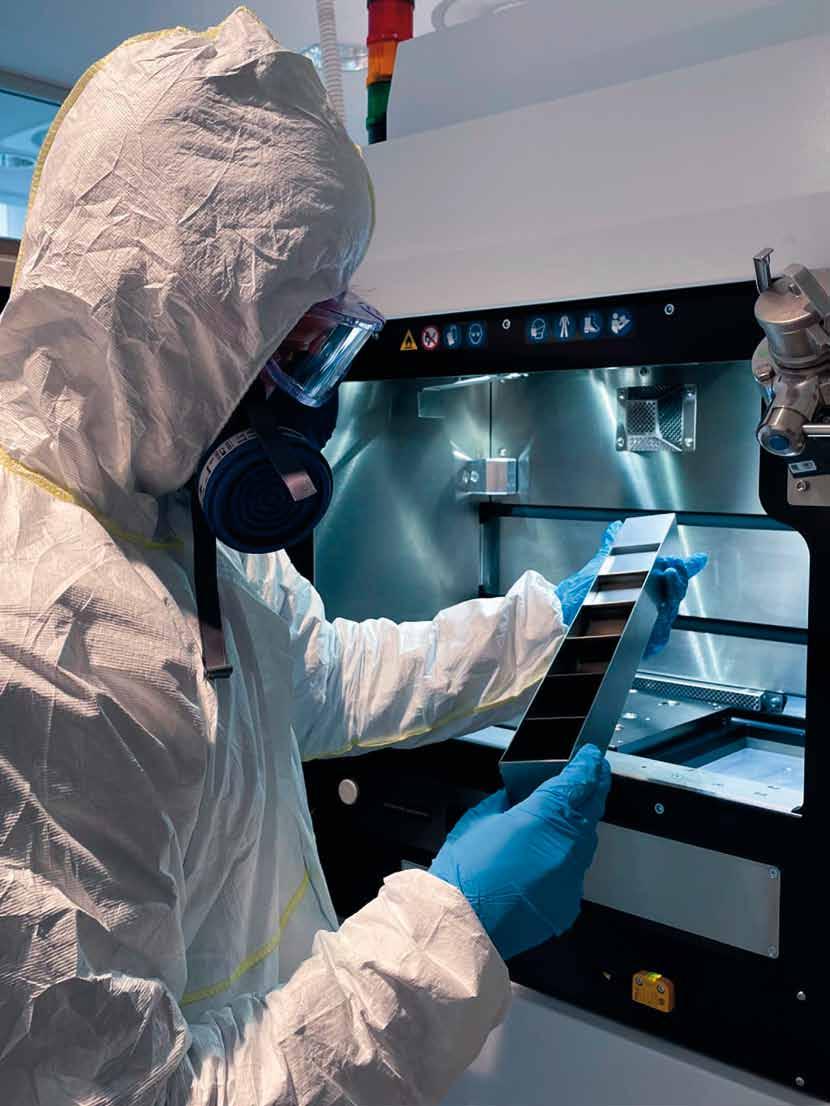
5 minute read
additive a portata di pmi
Il parco scientifico tecnologico Kilometro rosso ha investito in un nuovo training lab dedicato alla stampa 3d di materiali metallici. Si chiama Lisa Tech e vuole aiutare le aziende manifatturiere a gestire la tecnologia dell’additive manufacturing e integrarla direttamente nella propria realtà.
di Carlo Fumagalli
«sono arrivato qui lo stesso giorno della macchina» dice sorridendo Giuseppe De Marco, 26 anni, ingegnere meccanico fresco di specializzazione e ora Additive Manufacturing Engineer al Kilometro Rosso, il distretto dell’innovazione di Bergamo. La “macchina” in questione è una Eos M290, una stampante 3D per metallo a letto di polvere. Fa parte del nuovo investimento, di circa 1 milione di euro, del parco tecnologico che apre ora un punto di contatto tra aziende manifatturiere (Pmi in testa, ma non solo) e la tecnologia dell’additive manufacturing. Il progetto si chiama Lisa Tech. Acronimo che sta per “Living Space for Additive Technologies” e che ne descrive la filosofia: uno spazio pensato per sviluppare percorsi di formazione per aziende e professionisti, promuovere progetti di R&D, ma anche per dare la possibilità alle aziende di sperimentare. «L’idea è quella di aiutare le aziende a imparare a gestire questa tecnologia per integrarla direttamente nella propria impresa» spiega Giuseppe De Marco, «nel training lab si possono capire vantaggi e criticità di una produzione additive e poi sviluppare i propri progetti». L’additive manufacturing ha oggi la maturità per poter portare trasformazioni nel sistema di produzione, ma la sua diffusione in azienda non è sempre capillare. Ciò può accadere per specifiche barriere all’ingresso: «Spesso una questione di costi, che porta molte aziende ad affidarsi a service esterni» spiega Giuseppe De Marco, «ma non avere il controllo diretto sulla tecnologia non aiuta a formare le competenze necessarie». Un ostacolo legato all’esperienza quindi, più che alla tecnologia, che si può colmare sviluppando il proprio know how e prendendo consapevolezza del valore della stampa 3D, che non sostituisce, ma completa, quella sottrattiva. Il percorso formativo studiato dal Kilometro Rosso segue infatti una serie di step che puntano a trasferire le competenze in fabbrica: «La prima fase in cui affianchiamo le aziende è l’analisi dei componenti già prodotti, per imparare a selezionare quelli che potrebbero essere realizzati in additive» spiega De Marco, «da lì si passa alla realizzazione di un business case e poi alla parte tecnica vera e propria: prima con un training nella progettazione additive, e poi lavorando direttamente con la stampante». Nel laboratorio Lisa Tech i materiali trattati sono due: alluminio e titanio. «Entrambi i metalli non semplici da gestire per sicurezza e processo» spiega ancora Giuseppe De Marco, «ma sono stati scelti anche in base alle potenziali esigenze del tessuto manifatturiero del territorio». Ma come funziona, dopo la fase di progettazione, il processo di stampa vera e propria? Dopo aver caricato la polvere, nella macchina viene installata una piattaforma di costruzione, dove una lama stenditrice deposita strati di polvere che – in questo caso – possono andare dai 20 ai 90 micron (con alluminio generalmente si lavora a 30/60 micron, con il titanio fra i 40 e i 60). Subito dopo agisce un laser in fibra ottica nelle zone di interesse per dare forma all’oggetto, e in seguito viene recuperata la polvere rimasta. Il processo è controllato da un tomografo ottico, uno strumento composto da una fotocamera a raggi infrarossi capace di scattare 60 fotogrammi al secondo durante la lavorazione. In questo modo viene digitalizzato il processo e attuato un monitoraggio real time dell’operazione, valutando così eventuali difetti e ottimizzando il progetto. Oltre al tomografo interviene anche il supporto di un Meltpool, che svolge un’attività supplementare di controllo lavorando sull’emissione della luce riflessa dalla polvere. Come ricorda il direttore del Kilometro Rosso, Salvatore Majorana, «L’additive manufacturing cambia il modo di guardare i sistemi produttivi. Non sostituirà sicuramen-
La macchina
Lisa Tech è equipaggiato con una macchina Eos M290, che utilizza la tecnologia di fusione a letto di polvere. Per mezzo di un raggio laser mobile, la polvere metallica viene fusa localmente in modo selettivo strato per strato, solidificando così una sezione trasversale del componente. La camera di lavoro misura 250 x 250 x 325 mm e possono essere stampati oggetti in alluminio o titanio.
spesso è una questione di costi che porta molte aziende ad affidarsi a service esterni, ma non avere il controllo diretto sulla tecnologia non aiuta a formare le competenze necessarie
il progetto
Lisa Tech nasce al Kilometro Rosso dal progetto Ircram 4.0, finanziato da Regione Lombardia per creare una rete di laboratori dedicati alla progettazione meccanica tramite l’utilizzo delle tecniche di additive manufacturing e robotica. È costituito dalla partecipazione di 5 partner, ossia Camozzi, D&G Impianti elettrici, Fae Technology, Istituto Italiano di Tecnologia e Kilometro Rosso, a cui è affidato il ruolo di dissemination e R&D. Lisa Tech è stato avviato nel 2020 in pieno lockdown, e lo scorso 8 febbraio ha presentato l’attività di formazione (a giugno il via al terzo ciclo), di prototipazione assistita e di stampa a disposizione delle imprese.
te l’intero sistema produttivo, ma in moltissimi casi ci regalerà un nuovo modo di vedere soluzioni per indirizzare i problemi che possiamo avere tutti i giorni». Per un’azienda meccanica, ad esempio, introdurre materiali “nuovi” può avere dei risultati importanti. Il titanio, per rimanere nel raggio d’azione di Lisa Tech, può garantire specifiche proprietà meccaniche a componenti oggi realizzati in altro materiale, come l’acciaio: un’azienda produttrice di valvole pneumatiche – spiegano nel laboratorio del Kilometro Rosso – ha potuto partecipare ad appalti con grandi contractor grazie all’introduzione della tecnologia additive in una serie di valvole. Da una variazione tecnologica, insomma, possono aprirsi nuovi mercati. «Credo che un’azienda oggi non possa permettersi di non studiare l’additive» spiega ancora il direttore Majorana, «probabilmente non la sceglierà come sua tecnologia principale, ma serve a tutti poter comprendere le tecniche, la progettazione in additive: offre possibilità straordinarie, non soltanto a chi è grande e capace di fare investimenti, ma anzi, soprattutto a chi è più piccolo o di taglia media e ha delle caratteristiche particolarmente ricercate da poter essere soddisfatte tramite l’additive manufacturing».
L’additive manufacturing cambia il modo di guardare i sistemi produttivi, non sostituirà l’intero sistema produttivo ma regalerà un nuovo modo di vedere soluzioni


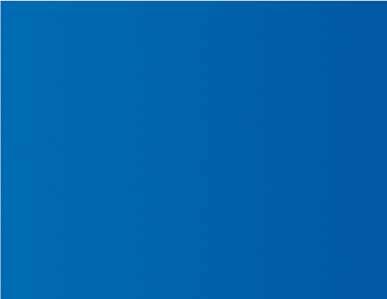
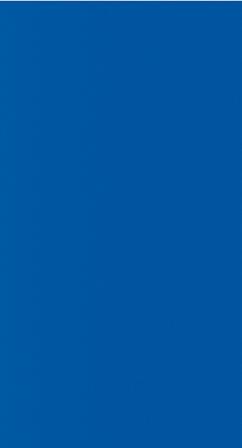
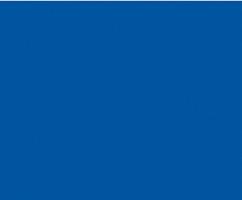


