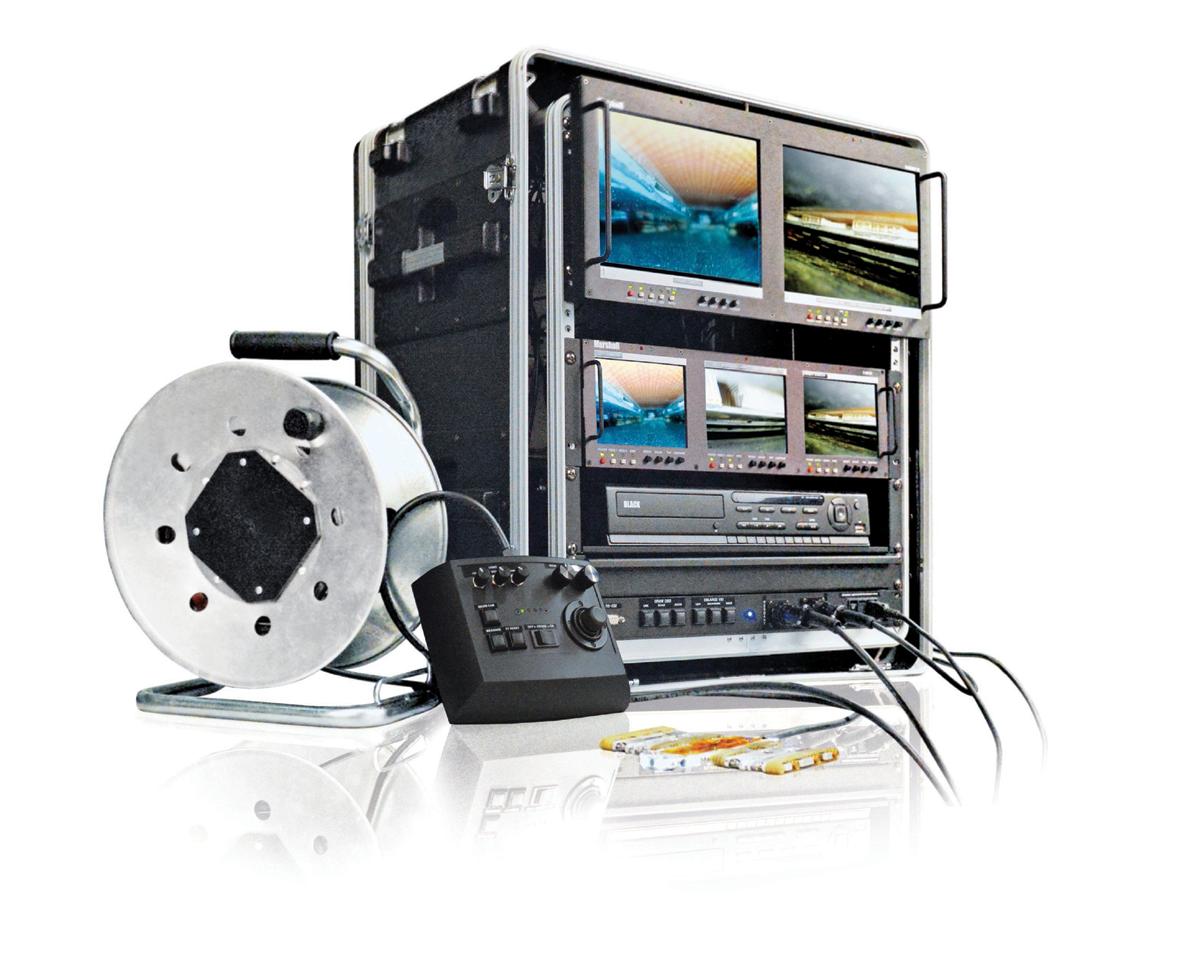
6 minute read
Adapting to keep industry moving
COVID-19 is forcing industries to think and react differently. From maintenance technology to witness testing of key assets, things are already starting to look very different. ABB’s David Hughes reflects on some of the changes that have happened since the pandemic restricted our normal ways of working.
Industries are saturated with pumps, fans and compressors – many of which are driven by large synchronous motors and generators. Today many of these assets are being asked to perform at unprecedented levels, with some being re-defined as critical assets used for pumping large volumes of water or compressing high volumes of oxygen. With many of these assets installed in the 1990s and earlier, their reliability is without question. However, such is the criticality of their applications today that greater focus is being placed on ensuring a robust maintenance policy, so that these machines never fail. The recommended maintenance program for ABB’s synchronous motors and generators, for example, consists of four levels, L1 - L4, each of which takes place throughout the life of a machine. For the classic motor/ generator installed around the 1990s, the most intense maintenance is L4 which is usually carried out after 80,000 hours or 12 years of operation. It is often at this stage where digital technologies are coming to the fore.
Advertisement
ROBOTIC AIR-GAP CRAWLERS Recently, ABB’s UK service engineers were asked to carry out a planned preventive maintenance inspection of a critical compressor, driven by a large synchronous motor. The team deployed the air-gap inspector – a miniature, video robot that crawls in the air gap between the stator and rotor of large synchronous motors and generators. The robot traverses the stator core laminations using modular, magnetic tracks. The inspection revealed that the rotor winding’s V-block support mechanism had lost its pre-tension. This required the rotor removal and replacement of critical components. While the robotic crawler had clearly saved the day by identifying an imminent failure, the age of the motor and its critical application was about to test the flexibility and ingenuity of ABB’s engineers. Planning and manufacturing the required materials for a synchronous motor of this vintage can typically take ten weeks. However, such was the urgency to put the process back into production that ABB managed to fast track manufacture and supply of the materials within one week. The feat is even more remarkable as the motor’s age meant that, while most components were in stock, the more critical rotor insulation plates needed to be purposely cut. The challenge was further compounded by the fact that these project-specific insulating plates were not fully or accurately set up in the SAP ordering software, thereby missing critical drawing references. Experience of the engineers involved ensured that they rapidly determined the insulating plate data. With the correct information now entered in SAP, the motor factory’s production planning ensured that the right plates were cut in advance, thereby avoiding losing valuable time.
ABB Air Gap Inspector
ONLINE FACTORY ACCEPTANCE TESTING Meanwhile, other customers were facing a different dilemma. With the motors and generators they have ordered now built, it is normal for customers to visit the manufacturer’s facility to carry out an intensive factory acceptance test (FAT). The social distancing rules of many countries, however, made such an event impossible. To help overcome this, ABB’s factories in Finland, China and Estonia are now embracing the world of live video feeds to let their customers witness test machines before delivery. A camera system provides a live video feed of the FAT, giving a complete overview of the testing floor arrangement and the machine’s running status. Intermediate results from the testing software are shown on the video feed, including temperature graphs, voltage and current. The online FAT application works within web browsers without any special IT requirements. To take part, the customer needs an internet connection and a link to the FAT web browser application. The necessary login address, username and password are sent by email, enabling customers to watch the FAT on either a computer or mobile device. This avoids the need to travel to the manufacturing sites, as the online FAT can be viewed remotely from virtually anywhere in the world. By eliminating travelling time and associated costs, online FAT offers extra flexibility in customer schedules. Following successful completion of testing, final inspection of the completed machines is achieved by means of a client agreed checklist. Inspection photographs are also issued as evidence of quality so that customer release documents can be issued.
SMART SENSORS COME OF AGE There is also a growing interest in the use of smart sensor technology for pumps. Keeping pumps running is vital to ensure that critical production continues uninterrupted. However, getting personnel on-site to monitor and maintain assets can be a challenge, and particularly so in the current climate. In the past few years, the traditional industrial powertrain has undergone a transformation. A typical powertrain comprises variable speed drives (VSD), motors, bearings and a driven load, such as a pump. Until recently the only truly digital component of the powertrain was the VSD. Acting as a virtual sensor, the VSD can track, monitor and feedback lots of data on the health of the powertrain, particularly relating to the performance of the motor and the energy consumption patterns. However, digital technology has rapidly migrated throughout the powertrain by way of smart sensors. Today, smart sensors can help facilities remotely monitor the condition of various assets such as motors, mounted bearings and pumps. The smart sensors are attached to these assets and track parameters like temperature, vibration, noise and energy consumption. The data is harvested via Bluetooth before being transmitted to the cloud, where it is analysed. The results are then displayed via a portal, revealing the health and performance of the powertrain, enabling any potential issues to be spotted and fixed, long before they lead to faults. REMOTE MONITORING This opens new possibilities for remote monitoring and predictive maintenance using in-house maintenance teams working from home or outsourced to the asset manufacturer. Having the ability to track the status and condition of a company’s entire installed base of VSDs, motors, bearings and pumps in one place, “Keeping pumps running is vital to ensure that critical as well as being able to access this information production continues remotely, has many benefits. It means less uninterrupted. ” time spent on visual inspection and manual measurements, as users no longer need to physically access equipment to determine its condition, reducing risk and keeping personnel safe. Remote monitoring ensures that maintenance is carried out precisely where and when it is needed, based on how hard assets are working. This lowers maintenance costs while allowing personnel to be deployed more efficiently. Overall, the use of smart sensors generally offers up to 70% less unplanned maintenance, up to 30% extended motor lifetime, up to 30% reduction in operating costs and up to 10% higher system efficiency. chevron-circle-right
www.abb.co.uk/energy
DO YOU MAKE, SELL, INSTALL, REPAIR OR ASSEMBLE PUMPS AND SYSTEMS?
BPMA membership offers a wealth of information, advice and opportunities designed to help your business thrive.
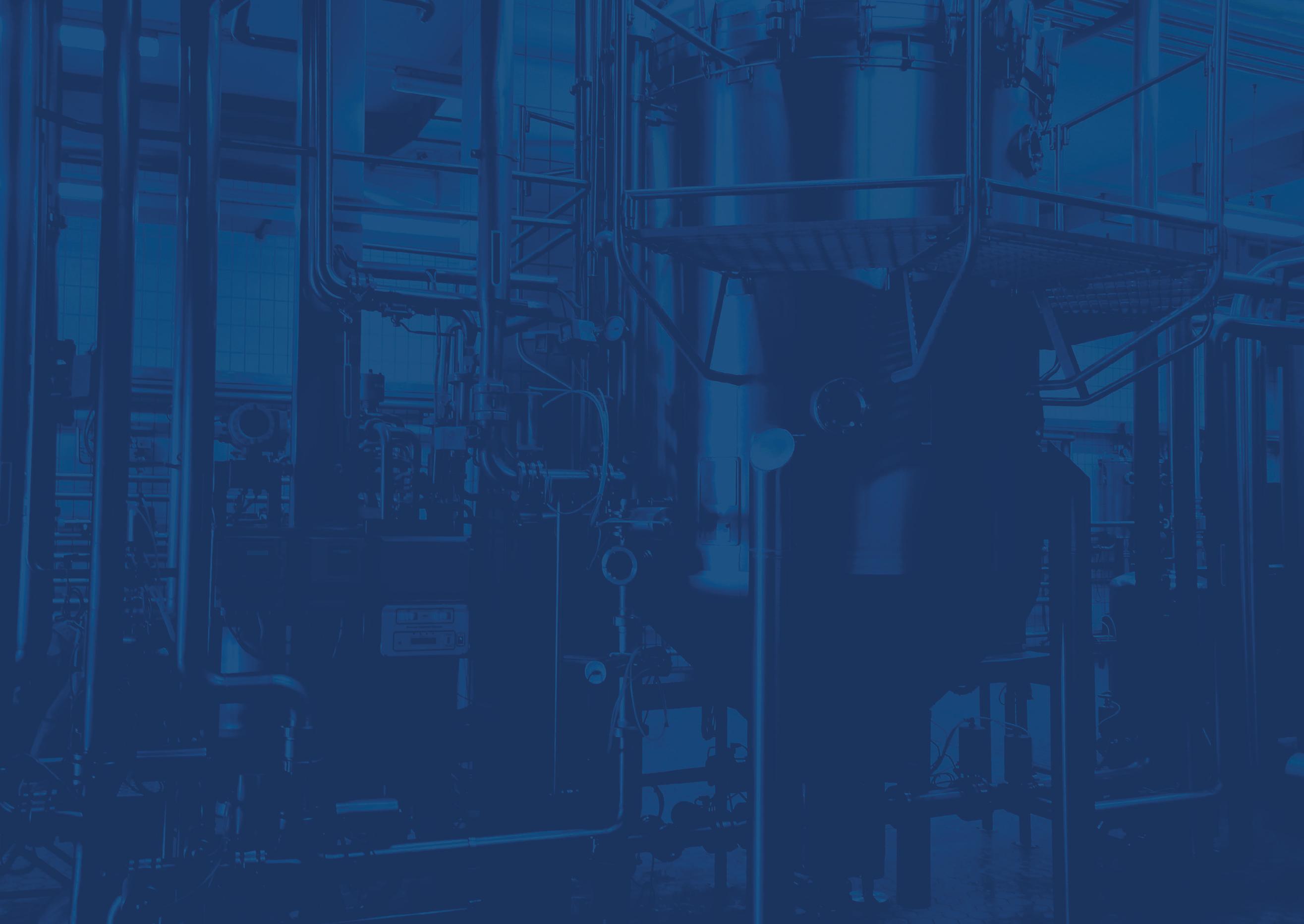
• Tender alerts • Free commercial, health & Safety and legal advice • Free and discounted technical and market insight guides • Expert advice on standards, legislation and technical issues • Discounted training • Energy auditing • Discounted insurance • UK and EU representation at political and executive levels • Exclusive promotional opportunities • Valuable networking opportunities