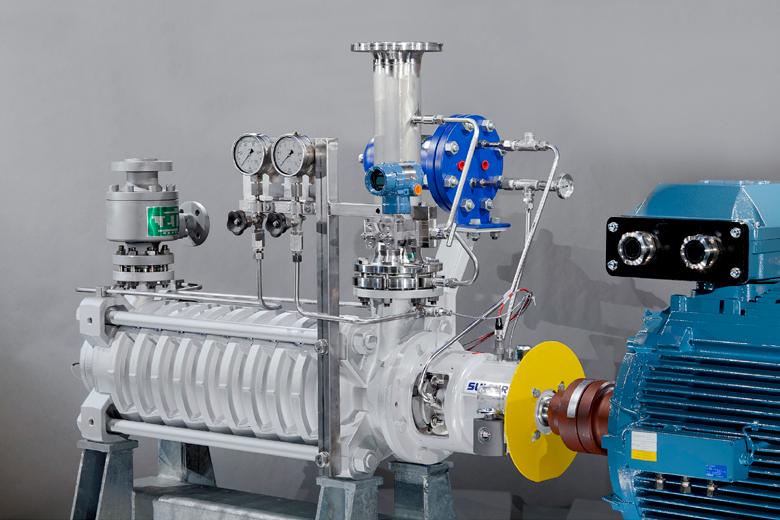
4 minute read
POWER & ENERGY SECTOR NEWS
CENTRE OF EXCELLENCE TO SUPPORT THE UK POWER GENERATION SECTOR
XYLEM HAS INVESTED IN WHAT IT is calling a European Centre of Excellence (CoE) serving the power generation sector.
Advertisement
Aimed at UK domestic power plants and UK customers building power plants outside the UK, but being designed here, the virtual CoE brings together a focussed team of experts with decades of experience in delivering complex powergen projects. The move aims to take the company’s customer support to the next level in terms of the customisation of customer solutions.
Expertise available through the CoE will cover core areas of a power plant such as the main pump packages and auxiliary pump packages, including cooling water pumps, condensate extraction pumps, and main heating pumps for district heating plants. Guy Fitzpatrick, General Manager, Industry & Infrastructure at Xylem Water Solutions explained: “We have expertise across the powergen sector from cogen (CHP), geothermal and district heating plants. Our custom pumps have one of the highest efficiencies in the market, and we are experts in customised and engineered to order pump packages, e.g. pumps with noise enclosures and surface protection. With this new CoE, our teams can now take on even larger projects – analyse, customise, engineer, and install a complete solution – helping our customers focus on core business, profitability and solving complex challenges.”
bit.ly/XylemCoE
EXPLORE YOUR PLANT IN AN ENTIRELY NEW WAY

COVERING VARIOUS PLANT TYPES, including conventional steam power, concentrated solar power and combined cycle power, Flowserve has created VirtualPlant to help take the guesswork out of product selection.
Built on actual use cases from its global customer base, the tool aims to help the company’s customers identify the most appropriate solutions from its pump, valve and seal portfolio. With particular benefits for those just starting in the industry or others who may have recently undertaken a new role or responsibility at their plant. Users of the tool start by selecting from one of the virtual plants, then using the aerial plant view, select the process area that they want to explore. From there, users can see a sector overview outlining vital information and challenges for that particular area and can click among the various Flowserve pumps, seals, valves and other solutions relevant to that specific process. Product literature, images, videos, manuals and training materials can then be accessed by selecting one of the products or services.
While VirtualPlant makes it easy to find relevant products and services by plant type or process area, the tool also delivers several benefits beyond product research. It can simplify the RFP process and reduce the time required for the discovery phase; users can quickly confirm that Flowserve has expertise in the specific industry application and then identify products to focus on in the RFP.
Customers that are already operating Flowserve pumps, valves, seals or support systems, can use the VirtualPlants to access a-growing library of information – including technical bulletins, safety data, instruction manuals, training materials and other supporting content – all in one convenient location.
VirtualPlant can also enhance the training of new employees. By exploring the 3D models and related information, they can learn more about the pumps, valves and seals they will encounter in a plant’s various application areas.
virtualplant.flowserve.com
BOILER FEED PUMPS REPLACED FOR THE COST OF REFURBISHMENT

A MAJOR UK WASTE-TO-ENERGY plant was experiencing considerable reliability issues with its boiler feed pumps. Routine maintenance involved a complete refurbishment every two years and the costs for this work were increasing. However, Sulzer was able to replace the pumps and achieve an impressive return on investment of just over two years.
The plant has six boiler feed pumps that have been operating since the site was commissioned over 45 years ago. Over the years, the pumps have been regularly maintained, but more recently, they have required major refurbishments to keep them operational.
Sulzer delivered a turnkey solution that included the removal of the legacy equipment and the installation and commissioning of new pumps. Having established the specifications of the old pumps, it was possible to source new pumps that would exactly match the original performance characteristics of the old pumps but with improved efficiency.
The proposal was to replace two pumps each year, allowing the plant to spread the cost of the project and also appreciate the benefits of the new pumps before committing to the next stage of the installation. The financial benefits were obvious from the outset. The cost of each new pump was only marginally more than the refurbishment costs of the equipment it replaced, giving a return on investment of just over two years.
Sulzer’s site services team only needed ten days on site to remove the old pump, modify the pipework slightly and install the new equipment. This ensured that the plant always had sufficient capacity, and no downtime was associated with the project.
So far, four of Sulzer’s MBN50 high-pressure 9-stage pumps have been installed, which are primarily designed for power generation applications and provide efficient and reliable service in this demanding environment. The performance of each pump has been tailored to the application to ensure optimum efficiency and reliability.
sulzer.com