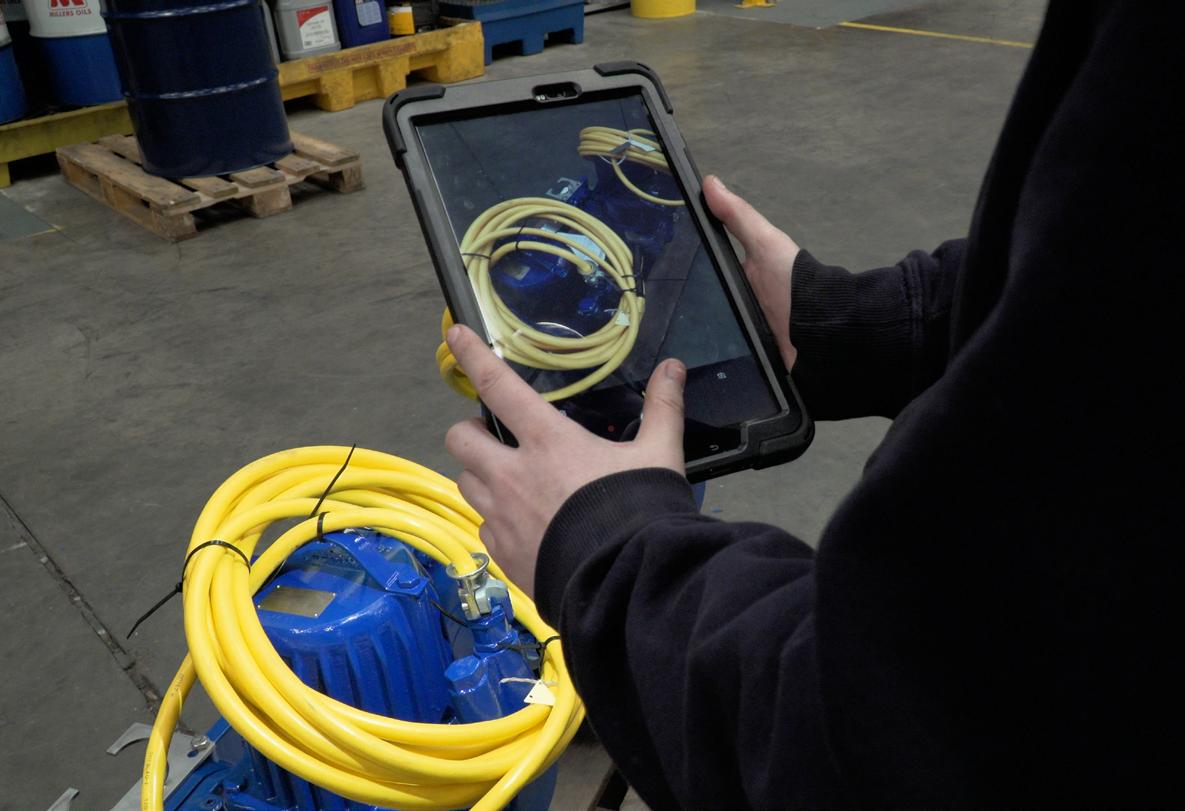
3 minute read
Improve repair efficiency
For organisations today, efficiency is critical. It is fundamental to being cost-effective, it enables a business to be competitive, and it supports environmental objectives, be they mandated or otherwise. Despite this, many companies still work with surprisingly complex paper-based systems. But they don’t have to, as flow found out.
Hidrostal, a Swiss pump manufacturer and repair organisation, had recognised the benefits of streamlining and digitising its processes back in 2013 when it installed EMiR (Electro-Mechanical Information Resource), a business management software solution designed specifically for the electro-mechanical industry by Solutions in I.T. Since then the company has been continually reviewing and improving its business processes, and in 2016 it removed all paperwork from its finance operation using the functionality in EMiR. When Hidrostal wanted to improve the efficiency of its workshop activities, it added the Smart Site extension to its EMiR package. Firstly, for each repair, the business was printing multiple documents to support the workshop activities. For example, a standard pump repair would include a damage report, a three-page job card, exploded diagrams of the item under repair and pages of parts lists that may or may not need replacing. This created a mountain of paperwork using valuable resources to create, distribute and manually update. Secondly, and most importantly for its client’s, to be more efficient in the maintenance of their assets, a request for greater detail was becoming the norm. The parts required and labour involved was only a small part of the required inventory to make informed decisions and take action avoiding unnecessary damage and inefficiency. Thirdly, while at capacity in the workshop, Hidrostal needed increased visibility of its operations, knowing the status of all repairs at every stage – production, stock availability and completed work – ready for invoicing. Using Smart Site, Hidrostal’s engineers can access information from EMiR via an Android and iOS app on ruggedised tablets, both in the workshop and when on site. Full job details are in the app including the damage report approved by the client at quoting, all necessary diagrams, records of parts used in the repair and the ability to make the job available for invoicing all without paperwork. Now, the site supervisor only has to print one piece of paper per job, which is for the repair component crate. This holds visual and barcode identification of the job, client and current status while the item is waiting for approval. Removing paperwork reduces the chance for human error. With Smart Site parts lists are all completed on the tablet and instantly available, meaning that no stock is ever missed or overordered. Customisable service checklists are also completed for a job, ensuring that every important repair procedure is actioned and recorded, meeting the requirements of any relevant quality standards. Text-based reports can also be backed up by labelled
Advertisement
The photos feature in Smart Site allows visual records to be easily captured
photographic evidence so that they have greater visibility and all the information customers need to make informed decisions is right in front of them. Another, somewhat unexpected, benefit of using Smart Site was the time saved in each job. Hidrostal’s engineers no longer needed to go to the office to collect and drop off paperwork because EMiR and Smart Site sync when connected to the internet. Since there are no more handwritten forms, the service coordinators don’t need to visit the workshop to clear up any handwriting issues, and terminology was now consistent thanks to the pre-created phrases and terminology that can be selected. Plus, detailed quotes can now be built quickly and easily using the information inputted to Smart Site, so the service coordinators no longer needed to write up the damage reports themselves. Hidrostal’s workshop staff have embraced the move to tablets since they have not had to change the way they complete repairs; it’s just faster with less paperwork. Hidrostal’s account managers have also benefitted. Any questions they receive from customers can be answered easily by accessing the job details in EMiR where they can see everything recorded in one place, and customers are no longer asking for more information on a job because they have already received everything they could need. Hidrostal’s move to a near-paperless workshop is almost complete three months after implementing Smart Site. With the help of EMiR and Smart Site, the pump specialist has saved time, eliminated human error, and improved customer satisfaction, all while reducing its carbon footprint. chevron-circle-right