
9 minute read
MASTERING ELECTRIC POWER: Demolition Manufacturers Draw from Decades of Experience Engineering Electric Models
safer, faster ways to complete difficult, dangerous, labor-intensive tasks. Their solution was to mechanize manual processes and deliver a powerful but compact machine in an electric package. Today, these manufacturers have experience engineering electric equipment and have optimized machines for the best power and performance.
Remote-Controlled Demolition Robots doorway, fit in a passenger elevator or even climb stairs.
Demolition applications are demanding to say the least. They are dangerous. They often require the power of large equipment but pose a host of challenges that make it difficult to impossible to actually use it. Some of the common issues contractors contend with are limited access, confined spaces, low floor loads and nearby occupied spaces.
In the 1970s, there were not a lot of options for solving these kinds of problems. Confined access? Send in workers with hand tools. Confined access but overhead work? Put them on ladders or scaffolding with the hand tools.
But don’t let the compact size fool you. Demolition robots are engineered starting at the tip of the breaker for maximum hitting power. The result is that pound-forpound, demolition robots provide the highest power-to-weight ratios in the industry, delivering the same results as an excavator three times the size. Combine that with a three-part arm, an electric-powered demolition robot offers exceptional reach and power in all directions, providing maximum precision and accuracy while the operator works from a safe position.
Alternative powered equipment is a hot topic. You can’t pick up a magazine without seeing an article about electric excavators, skid steers, telehandlers, wheel loaders, cars and more. With the world paying attention, it’s easy to forget that other types of electric equipment have existed for years—and, in some cases, decades. As many manufacturers have proven, it’s not overly difficult to come up with an electric model. Virtually all the large and midsize heavy equipment brands have at least one. The real challenge is optimizing performance, especially in heavy duty applications. Does the product have the power to get the job done? Can it make it through a shift?
Decades before these questions entered everyday conversation, demolition equipment manufacturers were innovating to meet demand for
Too much noise? Deal with it. That’s the way it is. From the need for safer, more efficient demolition methods, the first remote-controlled demolition robots were born. While some diesel models are offered today, demolition robots started electric and remain electric more than 45 years later.
Today’s machines look like small excavators with a three-part arm that often wields a breaker, but can use a variety of attachments, including concrete crushers, scarifiers, shears, splitters, buckets, grapples and more. Robots range in size from 23.5 inches wide and 1,235 pounds to 84.65 inches wide and 25,133 pounds. The smaller robots can drive through a standard
A variety of attachments further increase the value of compact electric power. Equip the robot with a shears attachment and efficiently and safely tear out concrete reinforcement, sprinklers, conduit, wire and cables. Or use a concrete crusher for “silent” demolition. The crusher attachment “chews” down a wall as opposed to using the force of a breaker to knock it down, reducing noise and vibration. For top-down applications where noise and vibration are primary concerns, crushers allow contractors to work during the day, sometimes without neighbors noticing.
These capabilities have years of experience behind them, making electric demolition robots the go-to for everything from soft demolition to refractory removal, ladle cleaning, underground mining, tunneling and many unique applications, such as driving helical piers.
Hydrodemolition Robots
Hydrodemolition robots were not far behind demolition robots. They were first developed in the 1980s to provide a better, faster way to remove large amounts of concrete. Like demolition robots, the first hydrodemolition robots were electric models, with diesel models following.
If you aren’t familiar with hydrodemolition, it is a concrete removal method that uses highpressure water jets to penetrate pores and small cracks in the material and break it out. A significant benefit is that it can remove weak or damaged concrete while leaving good concrete intact. It is commonly used for repairs on bridges, parking garages, tunnels, dams and other concrete structures.
Back in the 1980s, hydrodemolition manufacturers were innovating to improve a slow, difficult process that took a lot of manpower and was very hard on both the workers and the concrete structure. By harnessing the power of water, they developed an impact-free process that eliminated the vibrations that cause microfractures—miniscule cracks in sound concrete that can compromise the structure’s integrity. The highpressure water jets also clean rebar and metal reinforcement without damaging it. And the process is much faster, with a single robot and operator achieving the same removal rate in a day as 20 jackhammer operators.
Today, the smallest models are electric while the large models are diesel, electric or hybrid with the use of a hybrid kit. The benefits of hydrodemolition apply regardless what model a contractor uses, but there are certain situations in which an electric model is advantageous. A tunnel repair would be one of them. If diesel equipment is used, the contractor must provide a detailed plan for proper ventilation to win the bid and then implement the plan, which adds another layer of logistics and cost to the project. By using an electric hydrodemolition robot, the contractor eliminates concerns about air supply and ultimately saves time and money.
Solutions also exist for contractors who need the capabilities of a large robot but are unable to use diesel power. Maybe the project is inside a building. The market offers bigger robots with an electric-powered option for these situations. Just like a diesel-powered hydrodemolition robot, electric units can efficiently remove large amounts of concrete and reach horizontal, vertical and overhead areas up to 7 meters (23 feet) without support. On top of zero emissions, an electricpowered robot runs more quietly, making it an ideal option for projects with exhaust emission and noise restrictions. Some manufacturers also offer hybrid kits that allow a diesel hydrodemolition robot to run on electric power. The kit disengages the robot’s diesel engine, transforming it to an electric-powered machine, much like a hybrid car. This gives the contractor options, depending on what the project calls for, and provides a good back-up if the diesel power breaks down in the middle of a project. The contractor can simply plug in the hybrid kit to keep the operation moving.
Advancing Electric Technology
In the demolition world, electric solutions are nothing new. For many demolition and hydrodemolition contractors, it’s just another day on the jobsite. Manufacturers have developed generations of electric robots, mastering electric power and offering highly sophisticated technology that is used for major projects around the world. For them, the question isn’t how to come up with a workable electric solution. It’s how an already well-developed electric solution can further increase safety, productivity and profitability.
Electric-powered demolition robots offer reach and power in all directions, providing precision and accuracy while the operator works from a safe position.


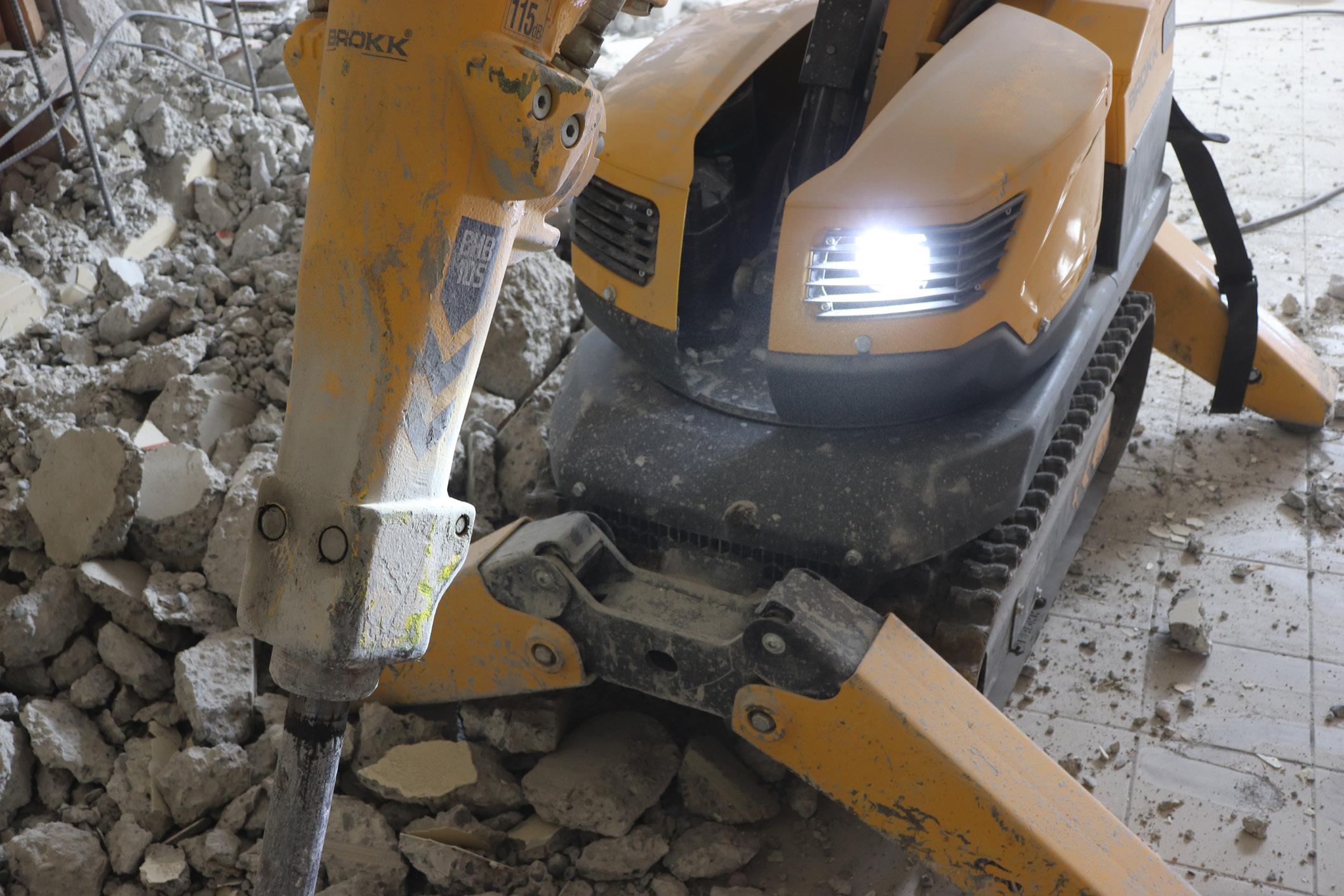
Read more at: https://eqtoday.co/x4fsct
Titan H/E Skid Steer Tire
The H/E deep-tread skid steer tire is designed for use in severe applications such as concrete planing, asphalt recycling, demolition, quarries, glass plants and scrap yards.
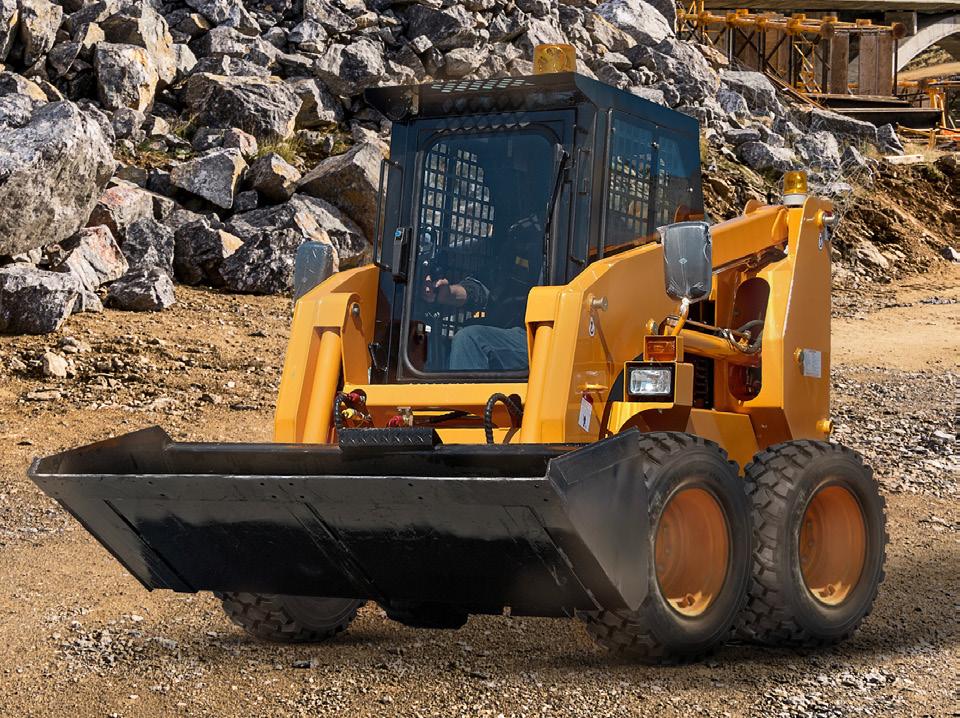
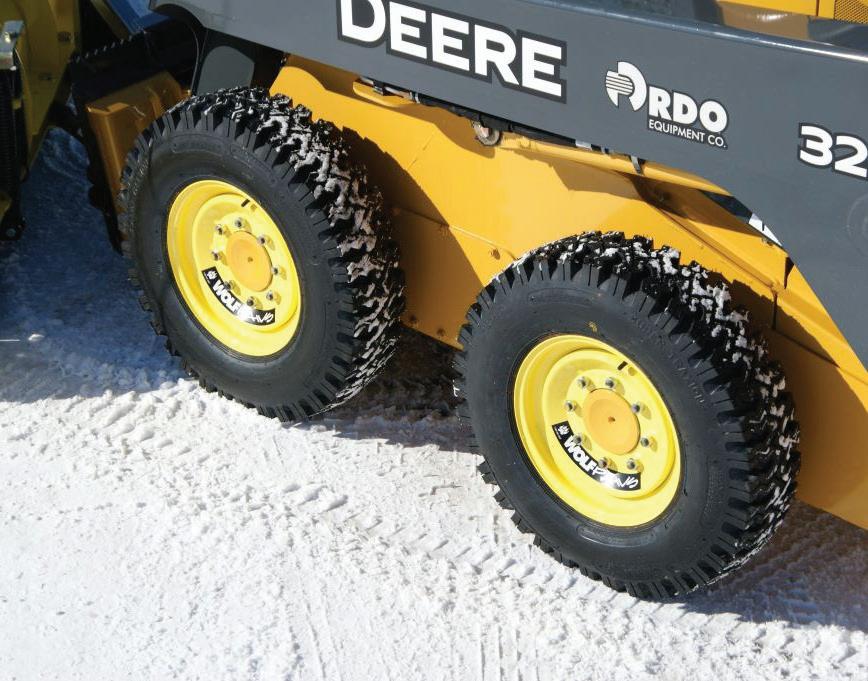
• Aggressive tread depth and diamond lug pattern provide optimal resistance to punctures and wear
• Available in tread depths ranging from 1.375 in. to 1.5 in. and in 10-, 12- and 14-ply ratings
• 10-16.5NHS, 12-16.5NHS, 14-17.5NHS and 33x15.5-16.5NHS sizes
Trident Traxter Solid Skidsteer Tires
The Traxter range of solid, skid-steer tires features an extra deep tread and specially designed sidewall apertures for shock absorption.
• 100% flat proof with high damage resistance
• Supplied as ready to fit tire and wheel assemblies
• Extra deep tread provides three to five times the service life of pneumatic tires
• Available in a wide range of applicationspecific patterns
Trelleborg EMR1031 Tire
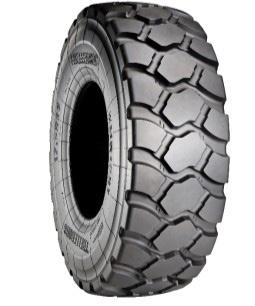
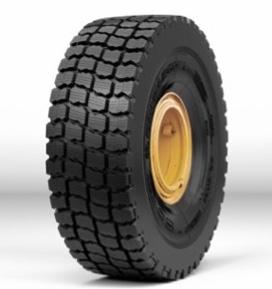
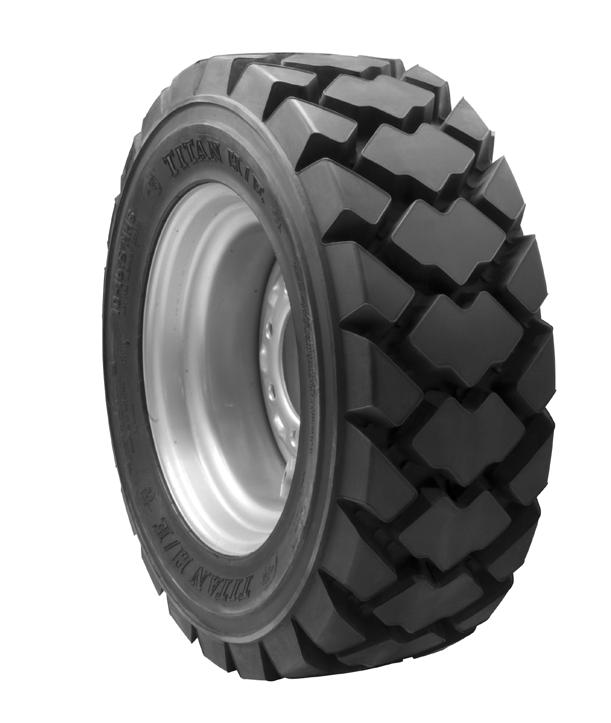
Trelleborg’s newest tire for earthmoving applications, the EMR1031, is designed to perform on sand, rock and other extra hard surfaces. Manufactured using a cut-resistant compound, the tire has a sidewall protector for damage protection and longer tire life, with a multisurface tread design for improved traction. Its cut-resistant compound is 20% more resistant to cuts and wear, reducing machine downtime and resulting in lower operating costs. The deep tread pattern offers longer tire life, enhanced grip and self-cleaning action during use, even on sandy or muddy terrain. To reduce environmental impact, the EMR1031 tire comes with a retreadable casing.
Yokohama Galaxy AT Grip Steel Radial Tire
Yokohama Off-Highway Tires has released new tires for skid steers. The new Galaxy AT Grip Steel steel-belted skid steer radial was designed from the ground up in consultation with skid steer operators and industrial tire dealers. There’s an extra sidewall ply on the tires to add thickness and stiffness. Immediately below the bead, a stiff flex-dampening layer directs sidewall deflection away from the rim, reducing damage from lower-sidewall movement. On the surface of the sidewall, twin rim protectors minimize impact and rubbing damage to the tire. The AT Grip Steel sidewall strikes a balance between stiffness and flexibility that allows the tire to reduce bucking and bouncing, while resisting damage and heat build-up.
SnowWolf WolfPaws
While most skid-steer loader tires are 10 to 14 in. wide, WolfPaws are 6.6 in. to 8.5 in. wide to provide nearly double the ground pressure.
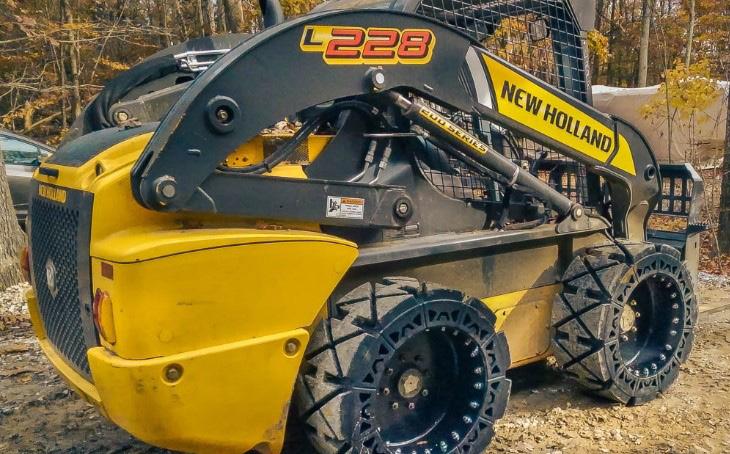
• Tread pattern designed specifically for use in snow
• Available for hundreds of different machines
• WolfPaws with studs available for extra traction
Alliance Galaxy Mighty Trac ND Skid-steer Tire
The Galaxy Mighty Trac ND all-season, nondirectional skid-steer tire is a versatile L-4 tire for use on loose soils, snow and pavement.
• Siped block tread design and 52:48 rubber-tovoid ratio combine enhanced traction on dirt and snow with wear resistance on the road
Open, non-aligned lug pattern on the shoulders provides extra grip in soft conditions and self-cleaning,
• Heavy, stepped centerline blocks ensure smooth roading and minimize wear
• Special cut, chip and abrasion-resistant compound and reinforced sidewall with a rim protector extend tire life
EVOLUTION WHEEL EWRS-HS HARD SURFACE SKID STEER TIRE
Evolution Wheel engineered the EWRSHS series for severe-duty applications where tire wear is the biggest concern. To do this they redesigned the tread pattern to maximize surface area. The EWRS-HS doubled the surface area of the EWRSAT Series to 66% to spread the weight of the machine out. This lowers the pressure per square inch on the concrete, while extending its wear life significantly. Additionally, the EWRS-HS series has deep tread, measuring at 52/32 in. The core geometry in these segmented tires allows them to compress like a pneumatic tire without the bounce.
Double Coin REM-2S All-Weather/Snow Radial OTR Tire
Double Coin and CMA are pleased to announce the introduction of the REM-2S all-weather/snow radial OTR tire. This hard surface tire was designed for earthmover, loader and grader applications and will debut at CONEXPO in Las Vegas.
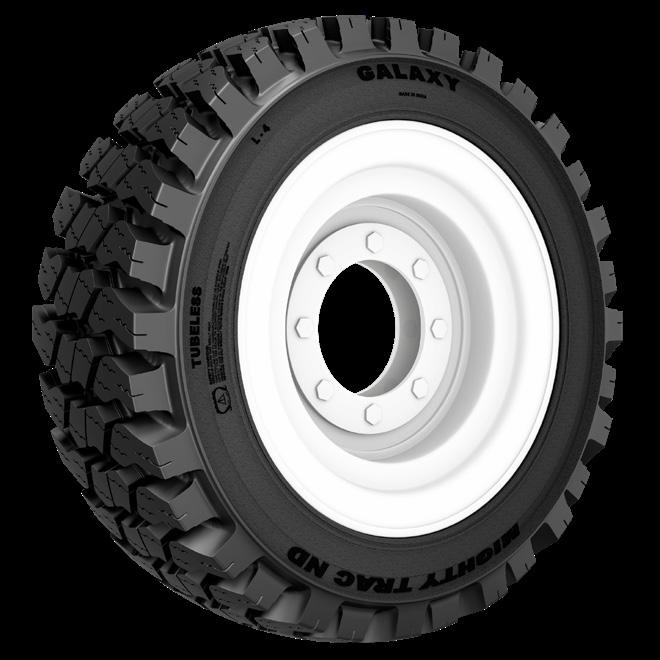
Features:
• Heavy siping with offset blocks for traction
• Advanced capability in snow, ice, gravel, and soft, sandy terrains
• Designed for year-round use
• Balanced performance on wet and dry conditions
• Great for snow removal, winter clean up, road clearing
Goodyear RangeMax RSDEV Tire
Goodyear has introduced the RangeMax RSDEV, Goodyear’s first electric vehicleready tire compatible with EV and gas- or diesel-powered regional work vehicles. Equipped to handle the high load capacities of EVs, RangeMax RSDEV was engineered to deliver low rolling resistance for fleets regardless of drivetrain. Engineered with Treadlock Technology to promote even wear and long miles to removal, RangeMax RSDEV is the first regional drive tire embossed with Goodyear’s “Electric Drive Ready” designation. Available now in size 295/75R22.5.
Bridgestone VZT Construction Tire and OTR Products
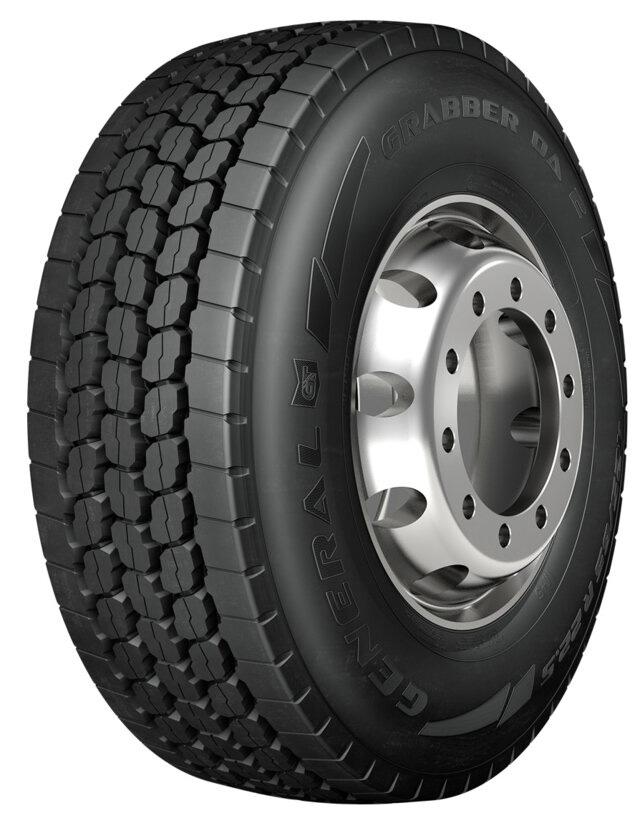
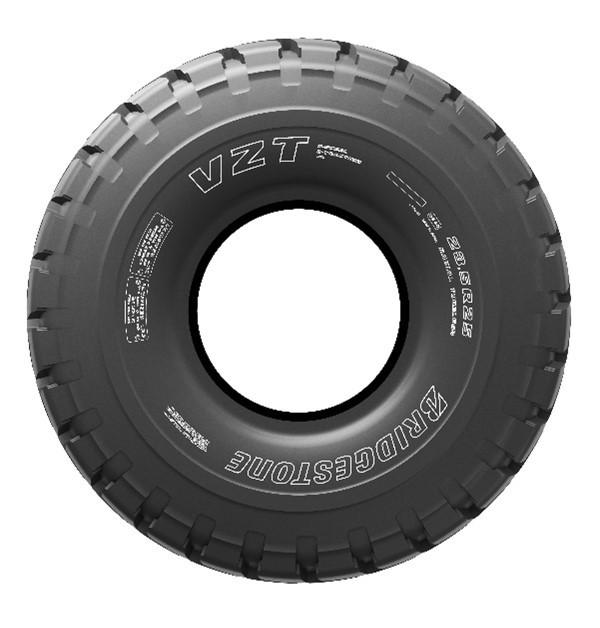
The new VZT 25-in. is the latest addition to Bridgestone’s construction tire lineup. Designed for loader and grader applications, the VZT supports performance attributes for traction and durability. The VZT’s sidewall design provides cut resistance. The VZT will be available beginning in the first half of 2024 in five sizes: 17.5R25, 20.5R25, 23.5R25, 26.5R25 and 29.5R25. Bridgestone will manufacture the VZT in North America at the company’s Bloomington, Ill. OTR plant, as well as in facilities in Japan and Thailand to serve Bridgestone’s global customer base.
Continental General Grabber OA 2
The General Grabber OA 2 on- and off-road, all-position tire features 22/32-in. and 24/32in. tread depth and a sidewall profile with curb rib to minimize damage from curbing, cuts and abrasions. The patented groove technology leads to minimum stone retention through a stone ejection system and extends casing life. The tire casing is constructed with four belts and a closed-shoulder four rib tread design, supporting all wheel positions. Drivers should see up to 19% mileage improvement and up to 5% chip and chunk resistance with the new General Grabber OA 2 when compared with its predecessor. This tire can also be sold with a sensor, which connects many of Continental’s tire pressure monitoring systems including ContiConnect Live and ContiConnect Yard Reader to read tire pressure and temperature. These heavy-duty tires can be used on coal or waste haulers, logging, construction, school buses and any on- or off-highway fleets. The General Grabber OA 2 includes a full warranty which guarantees three retreads or six years, whichever comes first.
Bkt Ridemax Fl 615
BKT has developed the RIDEMAX FL 615 radial flotation tire is designed for free rolling wheels of trailers, tankers and spreaders.

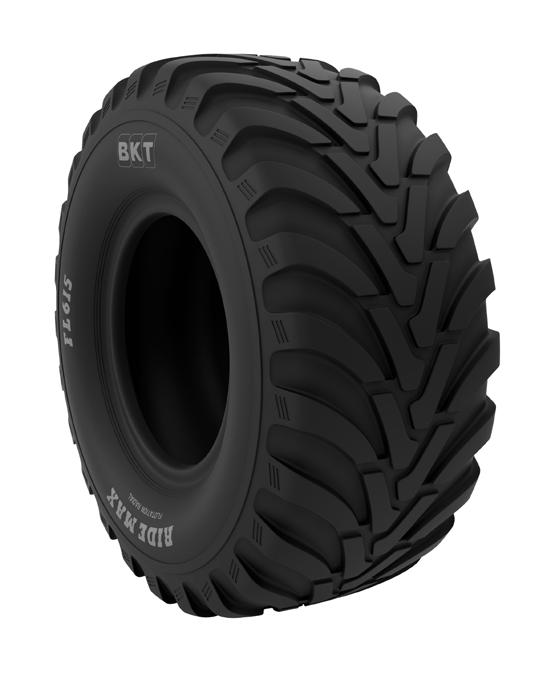
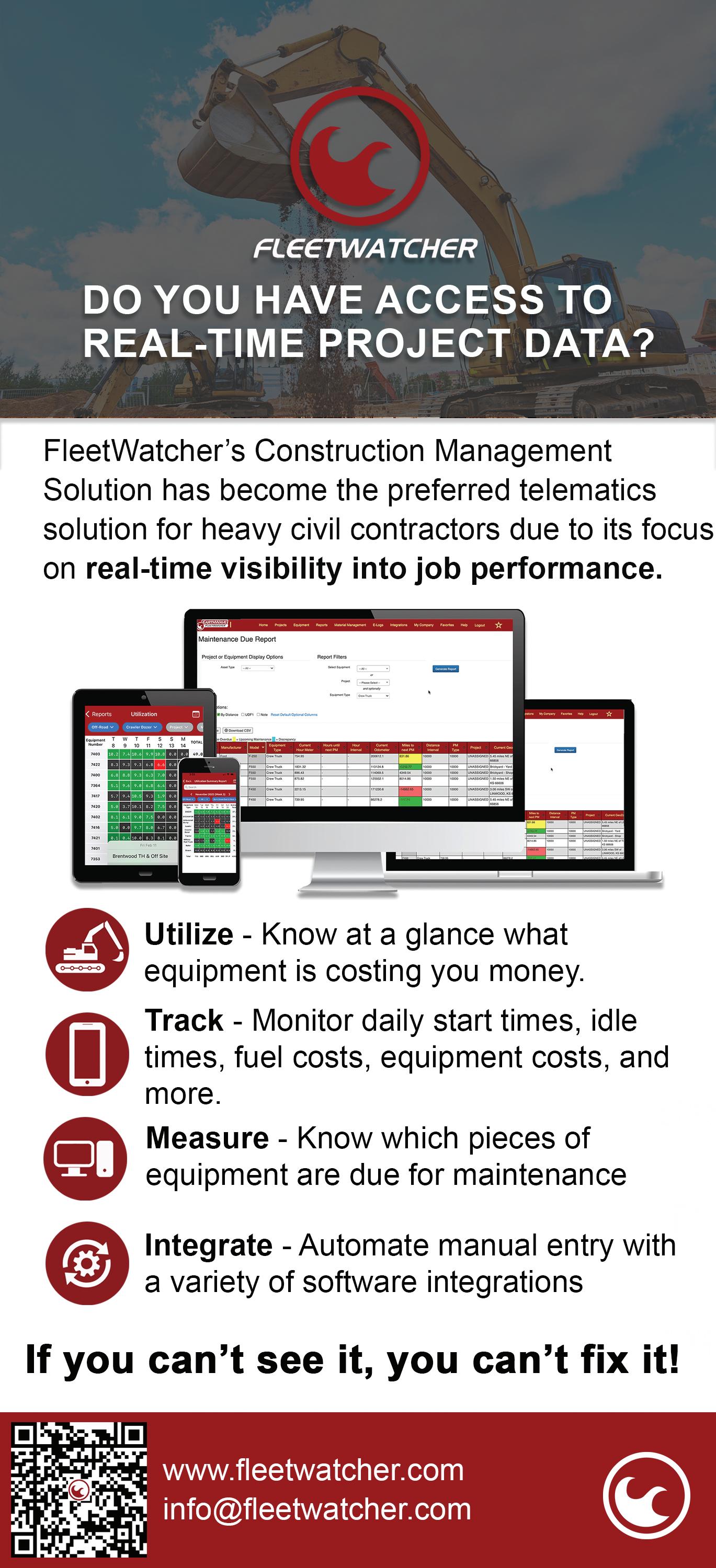
Battery, solar and drone systems are changing how operators see the jobsite.
As the construction industry moves toward zero emissions with large equipment, pressure to minimize or eliminate the use of diesel generators is increasing, including decreasing or eliminating their use for site lighting.
As with diesel internal combustion engines, these generators will continue to be used for the near future. However, for lighting jobsites, other options are available that can help contractors begin the move away from diesel lighting solutions. This