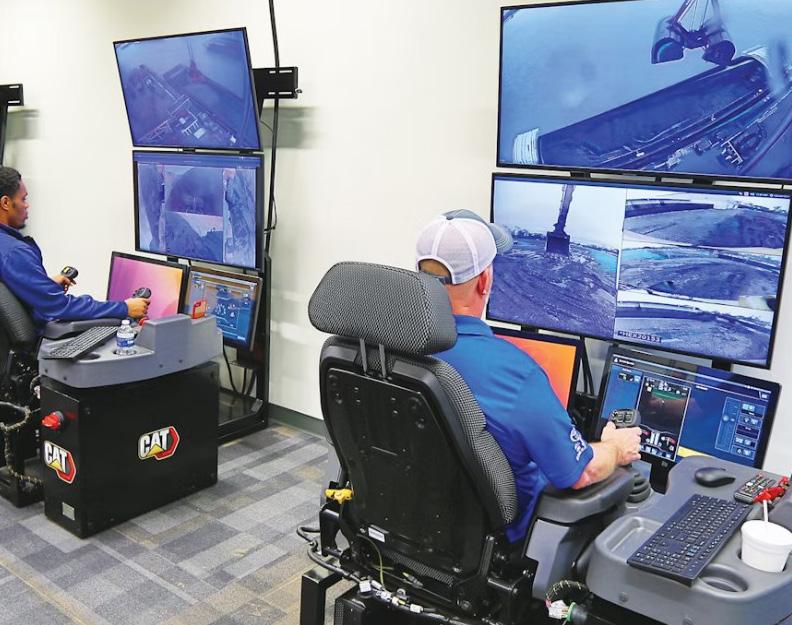
7 minute read
Four CRUCIAL TRENDS in Construction Machine Control
The Command console is a lightweight, portable console supported by a shoulder harness. Offering line-of-sight machine control from up to 437 yards away, it is suited for temporary or emergency remote operation with no on-site communications infrastructure required.
Longtime operators of off-road construction equipment may be extremely facile with travel sticks and pedals or levers for blades, booms and end effectors. But an expert operator in every cab is already hard to achieve, and demographic patterns and volume of work projected suggest it will get even harder.
Established and emerging machine control technologies can ameliorate this problem by:
˜ Enabling one operator to supervise and manage one or more machines remotely
˜ Lowering the barrier to filling positions with more intuitive controls
˜ Lowering the barrier to filling operator positions with automated operation
1. OPERATE ANYWHERE: REMOTE OPERATION
Technologies that enable an operator to control an excavator, wheel loader or other piece of equipment remotely have been on the market since Cat first began exploring remote operation in 2015, leading to the launch of Cat Command and regular expansions to more and more of the Cat product line from line-of-sight control Cat 988 wheel loaders in 2017 to loading, dozing and excavating operations in 2020 and excavating in 2021.
“One of the highlights is we have three different Command stations here, and that is our remote control offering where we are running seven different pieces of equipment in both our DNCs at Tenaha Hills, Arizona, and at Clayton, North Carolina,” Caterpillar Technology Marketing Manager Barry Littlejohn said from the company’s 1,500-square-foot technology hub at CONEXPO-CON/AGG 2023 (CONEXPO).
These technologies are supported and enabled by safety features like radar and camera systems in Cat Detect, ensuring that remote operation does not increase risk. Cat Command is sold in a package that includes:
˜ Line-of-sight remote control and can also be used in non-line-ofsight remote settings
˜ Dealer-installed field kits to make a machine Command-ready
˜ Multiple cameras for non-line-ofsite operation and stream on-site video feeds
˜ A microphone, cameras, indicator lights, a wireless receiver and antenna for mounting atop the cab
˜ Advanced features including Grade Assist, Swing Assist and E-Fence
While Cat Command and other, emerging remote operation technologies are coming to market first in mining and repetitive use cases, as the technology becomes more capable of sensing and responding to objects in the environment, they should become more and more applicable to busy construction sites.
The potential market for remote construction equipment operation is large enough that emerging vendors are also angling for a piece of the market. Founded in 2019, Palo Alto-based Teleo, for instance, raised $12 million in a Series B round in June 2022, in addition to a seed round in March 2020. The company employes 20, the majority of which are in engineering, according to co-founder and CEO Vinay Shet. At CONEXPO, the company announced new customer nameplates including John Aarts Group, Teichert and Tomahawk Construction. Perhaps more importantly for intermediate term success, they also announced dealer partners in the U.S., Canada and Europe.
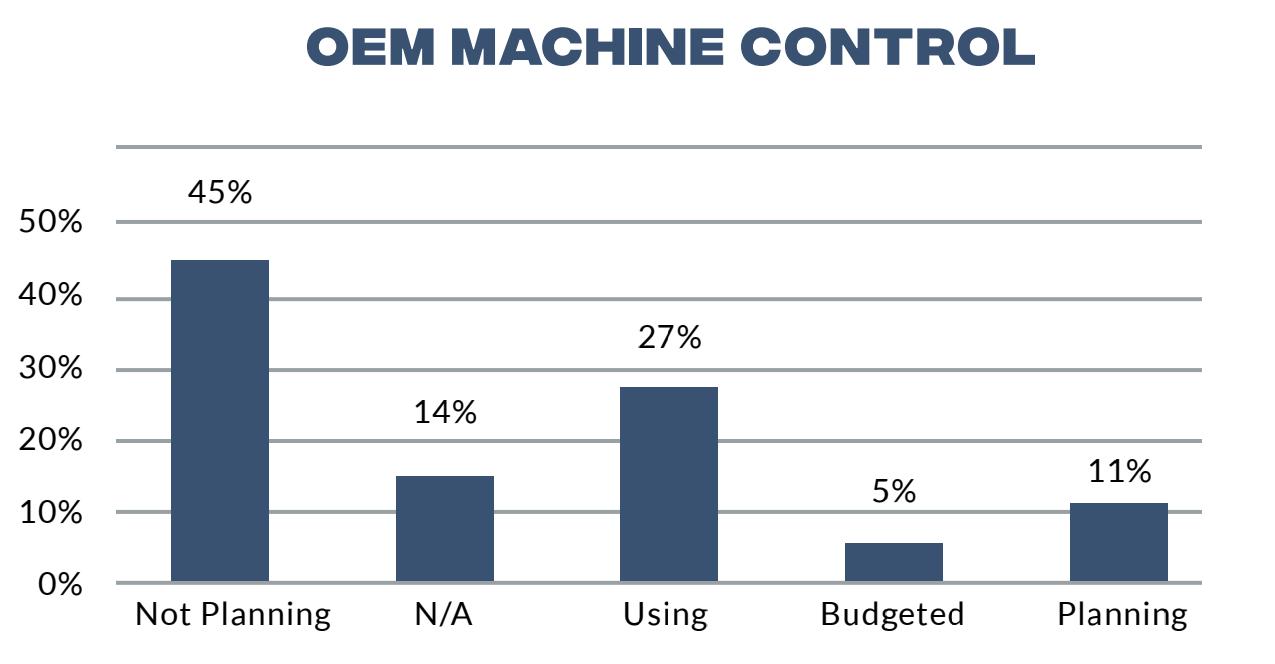
“What we offer our customer is all the layers—retrofitting for automation, the control station, network connectivity on site, AI algorithms and the cloud software to collect productivity data,” Shet said.
“We have a system around safety that means if connectivity for the machine is ever broken, we have a way to stop it if something in the way that is not supposed to be there.”
Safety is baked into Teleo remote operation solutions in a number of ways including unimpeded rear visibility, with Shet crediting cameras under the bucket, for instance, for unimpeded views of the work area for operators using wheel loaders and skid steers.
“Full autonomy is many years away,” Shet said. “What we deliver is supervised autonomy — we want to bring all the sensory queues from the machine back to the operator.”
While some remote operation solutions are geared more for line-of-sight control of the equipment, with an operator standing nearby, solutions like Cat Command and Teleo require a commercial internet connection with low enough latency to offer real-time control.
“Connectivity on the job site is crucial,” Shet said. “We have our own networking solution — it is critical for the machine that we deploy a mesh network on site.”
2. OPERATE MORE INTUITIVELY: HAND SIGNALS, JOYSTICKS
While Cat Command and emerging rivals aim to enable remote operation, other technologies aim to enable operation not just outside the cab, but through means that are more intuitive for an untrained operator. Work taking place at SRI International, a Menlo Park, California, nonprofit research institute aims to enable operation of an excavator by hand signals a joystick or even autonomously.
“The idea is to have a system that enables you to operate the excavator while not physically on the excavator,” SRI International Senior Robotics Engineer Reuben Brewer said. “The operator can work on-site or dial in from a different site. This is important because an excavator is often sitting idle during construction, and during that time, you can do something useful. Sitting in a warehouse or office, while waiting for the crews on site to be ready for the next digging task, I can dial into different jobsite.”
While much of this capability may seem duplicative of Cat Command, Teleo and other emerging vendors, there is more to SRI’s research than remote operation.
“We are looking at the system as a more complete package,” Brewer said. “Remote control of an excavator is not new — but we are the only system that includes active human detection. The excavator can stop, pause or slow if human is detected. We also focus on the immersive virtual reality environment we place the human operator in.”
More sensory inputs, according to Brewer, have proved essential to enabling effective remote operation.
“The virtual reality component is essential,” Brewer said. “When we first started, had dumpsters we were digging rock from, taking rock from dumpster A and putting it in dumpster B. Without the headset, we were missing the dumpster entirely 50 percent of the time. From 50 feet away, we did not have depth perception to do it properly. You put on the headset and suddenly it is a 100 percent success rate.”
Ensuring a remote operator has not only depth perception but the ability to see the entire environment is crucial for safe remote operation.
“We give you input to all of your senses,” Brewer said. “Because you cannot turn your head to see, we do additional sensing including 360-degree camera coverage. Rather than rely on a video feed that may not be useful if the human operator is distracted, we use machine learning to do detection. This is important for urban environments — if anyone gets near, we shut everything down. This may not work well on a busy urban sidewalk, but you can set zones behind the excavator so it can just not go in reverse if there is an obstruction.”
Once the operator is out of the cab, they can control the excavator either through a joystick control box or by using simple hand gestures, using the hand like a scoop to indicate the digging motion.
“The ability to follow the hand is something that helps get new operators up to speed addresses the labor shortage,” Brewer said. “When they get in the machine, operating the bucket with the controls is a left-right pattern and the brain cannot remember that because the boom goes front to back. We figured out a rolling pattern for the boom and the bucket.
“Working with a group of new operators with traditional controls, most could not scoop gravel off the ground. Five minutes in with our system and they were scooping and taking material from point A to point B. They were digging nicer-looking holes and not missing piles of dirt. If they were experienced operators but had not dug for a few years, the hand gestures were still more intuitive.”
3. OEM VERSUS AFTERMARKET MACHINE CONTROL
Regardless of whether machine control technologies consist of remote operation tools, grade control driven by GNSS signal, or reality capture tech that enables a machine to respond to its surroundings, fleet owners have two choices—they can rely on technology provided directly from their original equipment manufacturer (OEM) or solutions delivered after the sale by third parties.
The 2023 State of the Industry
Construction Technology Report lays out adoption curves for technology to automate operation of construction equipment is coming both from the OEM as a stock feature or as an aftermarket option sold by companies like Trimble, Leica, Unicontrol, Teleo or others. OEM machine control was the approach used most by study respondents, with 27% using it already, 5% budgeting for OEM-based machine control and 11% planning for it at some point in the future. Only 15% of respondents, meanwhile were using aftermarket machine control, 5% had it in their technology budgets and 12% were planning to roll it out in the future.
One reason contractors may opt for OEM machine control tools is the prospect of damaging the solution’s sensors will be diminished by thoughtful installation. Convenience during the purchasing cycle and potentially higher market value for OEM-equipped machines may also be factors. For these and other reasons, Caterpillar has been gradually making machine control features like grade control standard on some equipment classes, including hydraulic excavators. Case meanwhile offers a universal machine control option that makes each machine factory-compatible with all major suppliers of machine control technology, including Topcon, Trimble and Case precision partner Leica Geosystems.
While factory-integrated machine control options are more popular than aftermarket according to the data, emerging products from vendors like Unicontrol, Sodex, Teleo, Stonex Machine Control, Moog Construction, Kiwitron, Built Robotics and others may increase the percentage of contractors and fleet owners retrofitting for machine control. Alternatively, as more OEM equipment comes with standard machine control capabilities, the balance could tilt further towards OEM options or stay the same. This bears watching as the market figures out if the simplicity of factory machine control is preferable to aftermarket options.
4. ADVANCING TOOLS FOR MACHINE CONTROL DATA
One final trend affecting machine control for construction is the proliferation of technology options to prepare data for consumption by machine control solutions, as well as those that harvest information for progress reporting, other reporting and as-builts.
Trimble Earthworks is probably the dominant solution for this application and relies on a USB stick and File
Flipper app to transfer files directly onto a machine in the field.
Other options for this and other machine control data tasks include InSite Elevation Pro from InSite Software, which has in recent years been completely reimagined in 2020 for ease of use and performance. New features continue to proliferate, including the addition in April of 2023 of RockAlert, which gives machine control systems data on the location of rocks, water and other strata.
Quantum Land Design meanwhile in April of 2023 launched Quantum Flight Pack, a utility that enables a contractor to use a GPS rover to collect ground control targets, launch an automated drone flight over the property and then process drone data and run volume calculations for takeoffs.
Read more at: https://eqtoday.co/gykin1
Aftermarket machine control could rise in popularity compared to OEM options as more technology vendors enter the market.
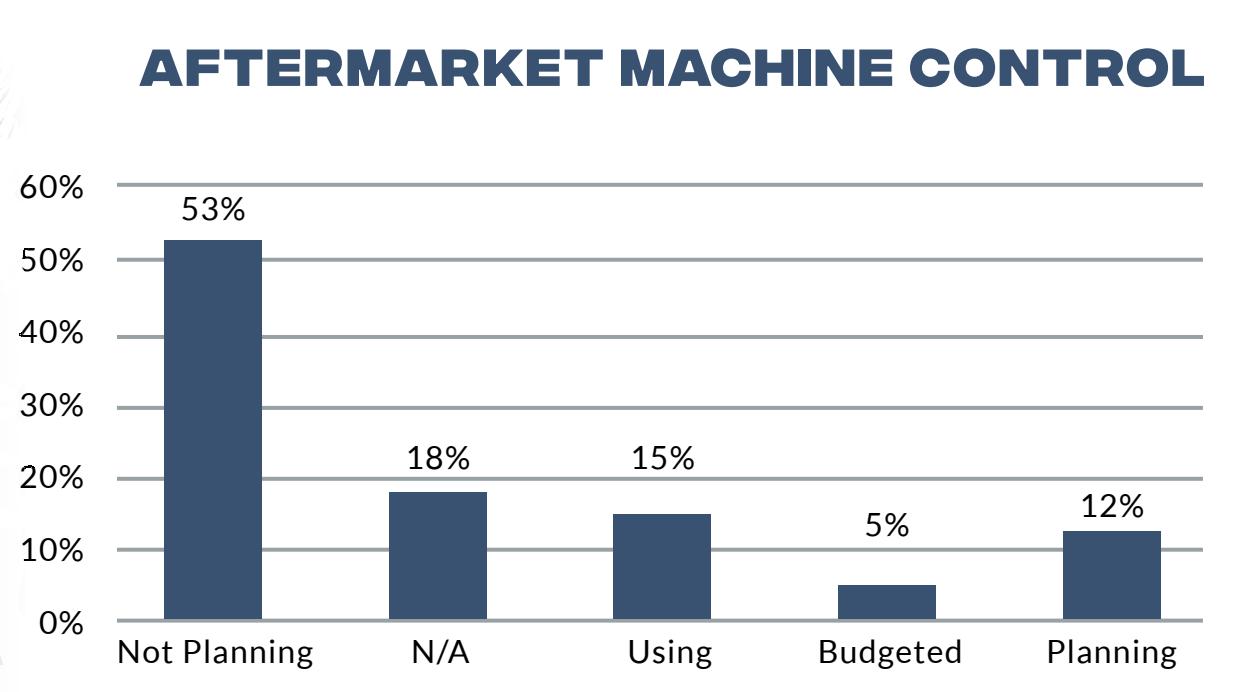