
7 minute read
Profit Matters
Boldt Adds Tool to Lean CONSTRUCTION TOOLBOX
TouchPlan helps teams visualize workflows in ways that cut manpower peaks and fix schedule drift, plus it simplifies identifying process improvements.
©Blue Planet Studio – stock.adobe.com T he Boldt Co., which performed more than $1 billion in work last year, attributes a large part of its success to the company’s commitment to adopting a continuous improvement approach. This approach includes implementing TouchPlan, an enhanced management software system that allows project managers at the company to have improved access to data that keeps projects on schedule, while reducing labor demands and increasing efficiency. The software aims to provide project transparency to improve team communication and allows teams to manage projects from one place.
“Our focus has been on executing projects more successfully; by making our plans visible to more project stakeholders, problems come to the surface faster and help our teams focus on what will make the project better and improve every day,” said Nick Loughrin, group manager of project delivery services at Boldt.
TECHNOLOGY SUPPORTS STANDARDIZATION, IMPROVEMENT
since that organization’s early days. The company’s focus on improving production led to merging its experience with Lean principles to create The Boldt Production System with its roots in the Last Planner System.
“The Boldt Production System starts with a master schedule and progresses to the development of production strategies per phase. Each phase will then have a make-work-ready plan that leads to the weekly, daily and production tracking levels of project execution,” Loughrin said.
The contractor’s efforts for improvement are, as they say, continuous.
“One of our main strategic initiatives within our growing company is to develop better standards based on our best practices within our company. We know we will have successful outcomes if we are rigorous and disciplined in our approach to implementing the Boldt Production System. We see TouchPlan as a technology to help us with that.”
At the end of 2021, TouchPlan officially became a part of the standard technology used within the Boldt Production System, the company’s process for planning and managing projects. Boldt has about 30 projects already using TouchPlan, and the company has ample knowledge of its value. Loughrin relayed how applying the software to an ongoing Wisconsin project corrected schedule-drift.
“The team would have probably found a way to finish on time, but it would have cost exponentially more by working overtime and adding resources,” he said. “Working with the team to develop a production strategy based on flow, we were able to capture the plan in TouchPlan to further analyze and level out the resources and make the plan more efficient. We finished the project on time and with a lot less hours.”
SMARTER DATA AND EFFICIENCIES
Boldt’s commitment to TouchPlan is a step toward smarter project management data—not just “are we ahead or behind schedule,” but also production and performance data that brings the project to the current schedule status.
“What we've traditionally done is taken our master schedule, captured in P6 or Microsoft Project, and added layers of detail per phase that is hard for the team to follow and understand, or we create a separate Excel file that can become disconnected from the master schedule,” he said. “Then, we manage constraints in a separate file or board as they are identified by the team. All of these different platforms to manage the schedule and constraints creates a cumbersome process and adds non-productive time to the project teams' already busy days.”
It's a process that works on any given project, but each project is its own silo of stand-alone data and inefficiencies.
“Now, using TouchPlan, we are able to tie our master schedule and the production strategy together in a clear and visual way that the team understands, and constraints identified are able to be captured and tied right to the plan. It takes less time to manipulate the schedule for updates and changes. Another benefit we are starting to realize is the performance data we are able to see across all of our projects. TouchPlan makes it easier and faster for us to share best practices and problems from one project to another.” ET
Simulators in Construction: CONFESSIONS OF A SIMULATOR SKEPTIC
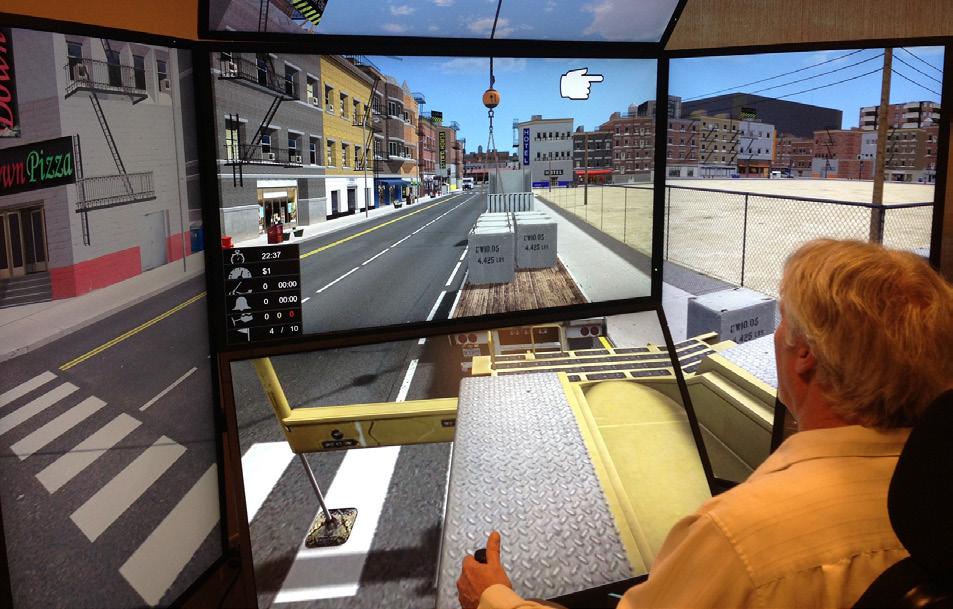
Experienced equipment operator opens eyes to simulator technology opportunities.
BATTLE AX
LOW AND HIGH FLOW SKID STEERS & EXCAVATORS 10,000 LBS - 80,000 LBS
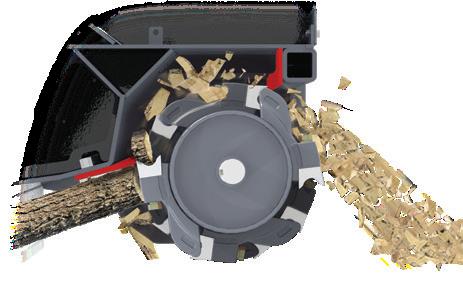
When it comes to training, today’s complex equipment requires an equally sophisticated learning environment. And while younger, tech-savvy workers are generally quick to embrace simulation-based training as an effective tool, many established operators remain convinced that nothing can replace on-the-job field training.
As a construction worker with more than two decades of experience under his belt, Gary James’ view of training simulators was tainted with a skepticism not uncommon among veteran equipment operators. He saw simulators as overly simplistic and unrealistic, only useful for novices, and in no way a reflection of actual jobsite conditions.
Throughout his career, James has operated a range of construction equipment and has trained others. Like many in the industry, his career literally began from the ground up. While slinging dirt with a shovel, an unexpected opportunity provided quick entry into the world of heavy equipment operation.
“One day an equipment operator showed up in let’s just call it a ‘less than ideal’ condition,” he commented. Long story short, the company was suddenly in need of an operator and James seized the chance.
Unfortunately, the training he received was less than ideal. “It was a classic example of baptism under fire,” he noted. “I was handed a shirt with a pocket and a receiver to keep in it. As I sat behind the controls, my supervisor walked me through the process shouting step-by-step loading instructions in my ear. This went on every day for weeks until I was able to operate the equipment on my own.”
This experience directly influenced James and his approach to training. “I learned in the exact wrong way. It was nerve-racking, intimidating and excessively long,” he said. “When I began instructing equipment operators, I knew that there had to be a better way.” MAKING THE CHOICE
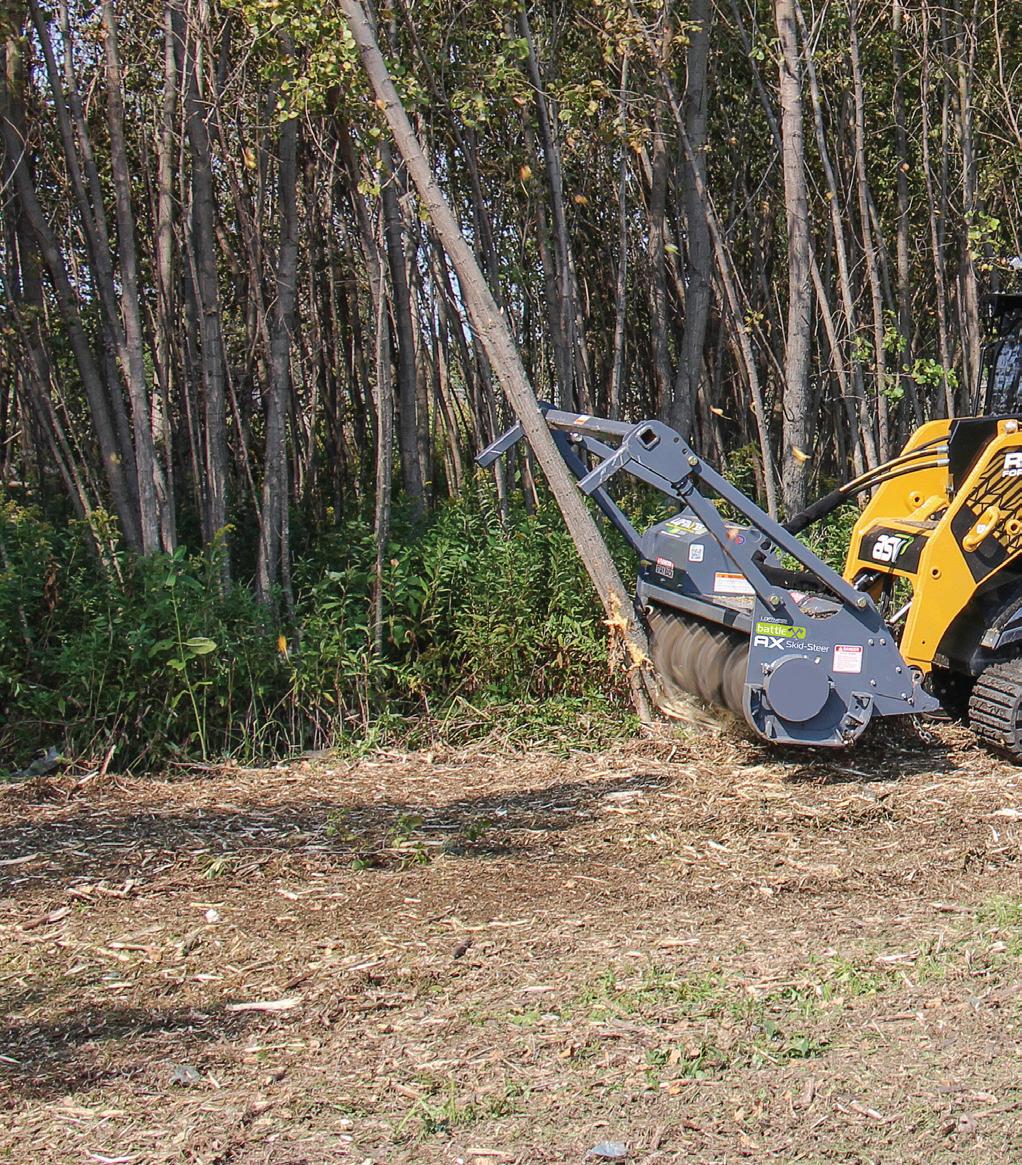
AN EYE-OPENING ENCOUNTER
Despite this realization, James had never considered heavy equipment simulators to be a viable training option. Things changed almost immediately when he encountered CM Labs’ line of Vortex simulators. With advanced graphics and algorithms, the simulators provide trainees with the look, feel and machine feedback of the real thing.
For James, and many who first experience these simulators, the difference is eye-opening. “If I were blindfolded, I wouldn’t know if I were on an actual piece of equipment or a CM Labs simulator,” he stated. “It blew my mind the first time I tried it. When engaging the hydraulics, swinging the arm or lifting the bucket filled with dirt, you can feel the reaction of the machine in the controls and in the seat. What’s more, the feedback is real time and accurate, not scripted. I couldn’t believe how close it was to the real thing.”
Training simulators are a cost-effective way to bridge the gap between the classroom and field training while allowing novice operators to learn in a safe and stress-free environment. Today, this self-described cynic has come to see the light and is a leading advocate for simulation-based training. In addition to measurable improvements with operator productivity and safety, James cites savings related to fuel consumption, equipment maintenance and employee screening. Contractors can save $60,000 to $80,000 or more each year in accident avoidance. As James can personally attest, it’s better to learn lessons virtually than on the jobsite. “I’ve personally been responsible for thousands of dollars in equipment losses,” he admitted. “Simulators allow students to make mistakes without associated dangers or costly consequences.” ET Read more at: https://myfc.pro/v47ckf
THE CLEAR ADVANTAGE.
Spend less time in the cold switching multiple blades with Brandt’s purpose-built 4-in-1 snow blade: More Adjustable side wings rotate 180° for Versatile maximum versatility in all conditions. Safer Two trippable edge configurations Operation deliver added safety & longevity. Low Blade hydraulics remain protected with Maintenance cover plates, reducing repair costs. brandt.ca | 1-844-328-2538
DON’T BITE OFF MORE THAN YOU CAN CHEW …OR LESS
EXCLUSIVE DEPTH GAUGE DESIGN
Maximize productivity by not biting off too much, or too little, material at one time. The new Battle Ax rotor has unique depth gauges that optimize the material feed rate for top efficiency.
TWO-STAGE CUTTING CHAMBER
Thoroughly process material with the exclusive two-stage cutting chamber featuring an adjustable primary shear bar.
Mulching Heads Flail Mowers Mechanical Trimmer LOFTNESS.COM

