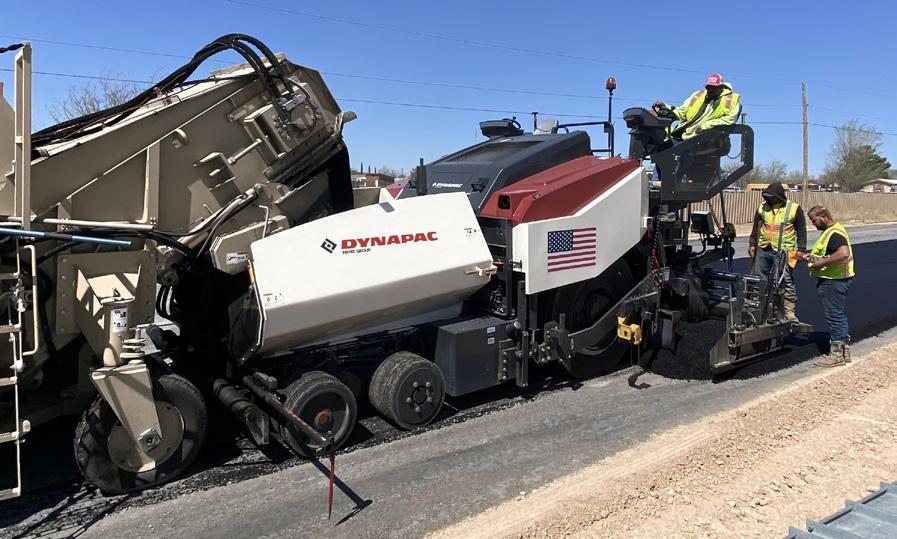
33 minute read
Road Building
Dynapac Highway Class Paver Line Up
The Dynapac range of highway class pavers and screeds includes four models of tractors, D30T – 10 ft. Track, D30W – 10 ft. wheel, D25T – 8 ft. Track, D25W – 8 ft. wheel and two models of screeds Mat Master 16R (8 ft.-16 ft. screed), Mat Master 20R (10 ft.-20 ft.)
•High transportation speeds, up to 10mph, allows fast repositioning of machine •iTrack ultra duty rubber track design offers performance with low maintenance costs •Dynamic suspension control (DSC) on wheel pavers offer tractive effort with lower investment and maintenance costs •For thin overlays on highways, Mat Master screeds are equipped with DiveStop and Active Screed Assist technique •Smart dashboard and HMI design on the tractor and screed allows operator to focus during long paving hours Read more at https://eqtoday.co/jknvfa
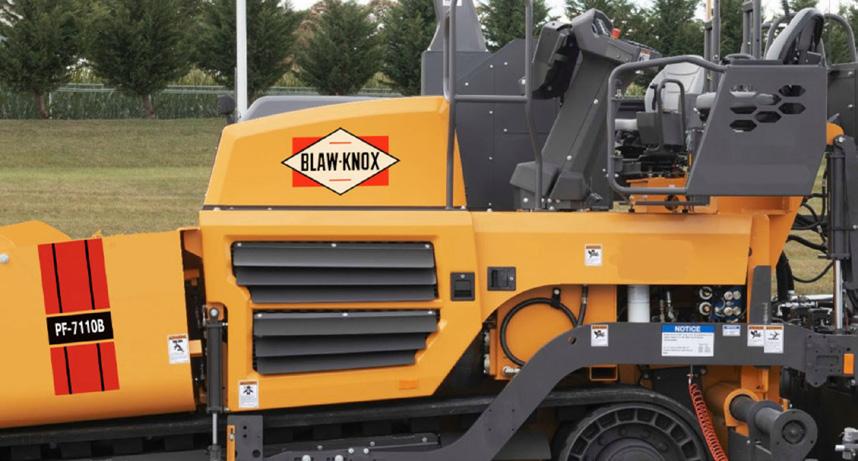
Blaw-Knox PF-7110B Asphalt Paver
Blaw-Knox’s Tier 4 Final D8 235 horsepower engine in the PF-7110B Blaw-Knox Tracked Paver improves fuel efficiency by up to 5% and provides reliability and ease of operation.
•The PF-7110B is a highway-class paver with an independent auger and conveyor system, and stable hydraulic screen extensions for delivering placement of bituminous base, binder, or surface mixes •Tier 4 Final engine meets emission regulations and fuel efficiency needs •All-around visibility with rotating and extending operator seats for a full view of the paving process •Basic width: 10 ft. •Engine power: 235 hp •Max width: 26 ft.
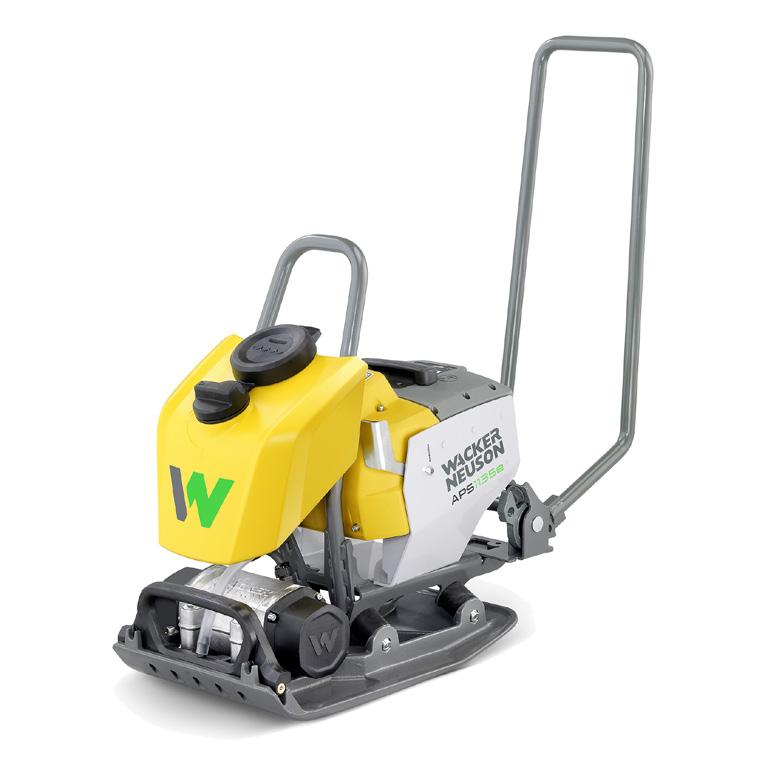
Read more at https://eqtoday.co/45793z
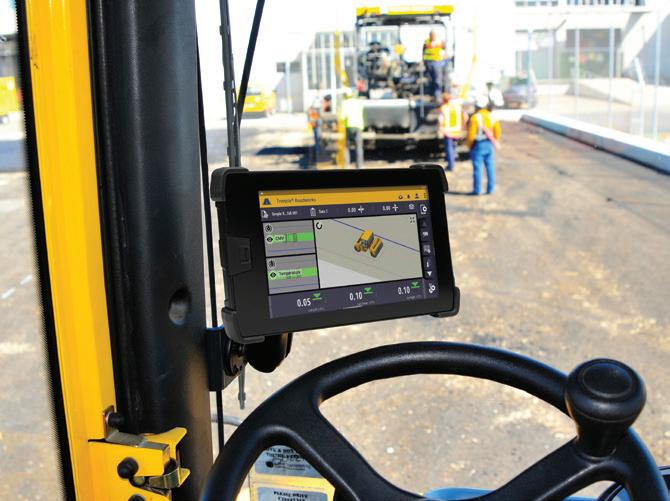
Trimble Roadworks Paving Control Platform
The Roadworks Paving Control Platform for Asphalt Compactors enables operators to accurately control the compaction process, while reducing unnecessary passes.
•Intuitive Android-based software maximizes ease of use •Asphalt temperature mapping provides color-coded data to allow operators to compact at correct temperature •Compatibility with Trimble WorksOS and WorksManager software enables construction-ready models to be sent from office to machine and remote monitoring of jobsite progress •Productivity data collected from the machine is automatically synced back to the office
Read more at https://eqtoday.co/w8gtfu
Rosco NB25 Three Wheel Broom
The Rosco NB25 Three Wheel Broom features an optimized hydraulic system with oil cooler.
•25 hp Kubota V1505 (canopy machine) •25 hp Deutz D2.2 engine (climate-controlled cab machine) •Wheel lift or wheel down tow options with warning system •8-ft. heavy duty brush with variable down pressure controls •-ROPS certified
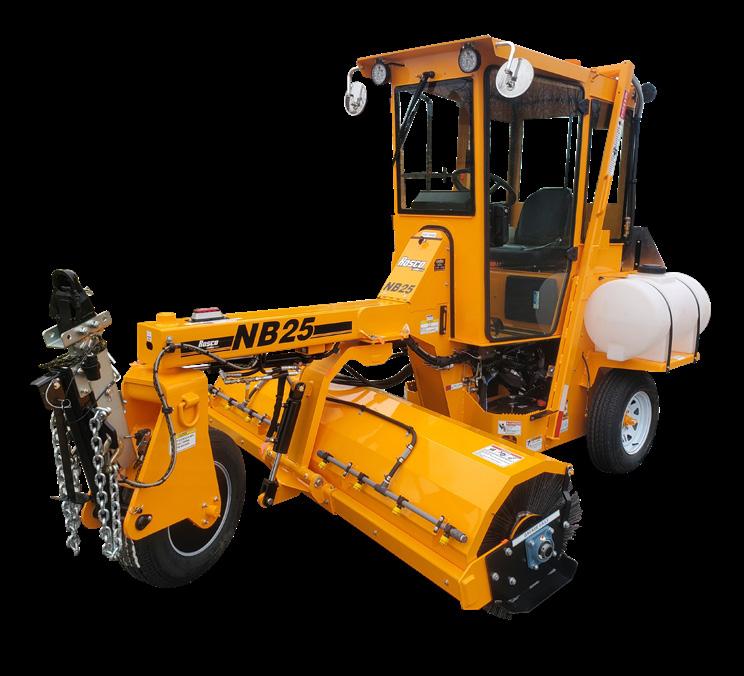
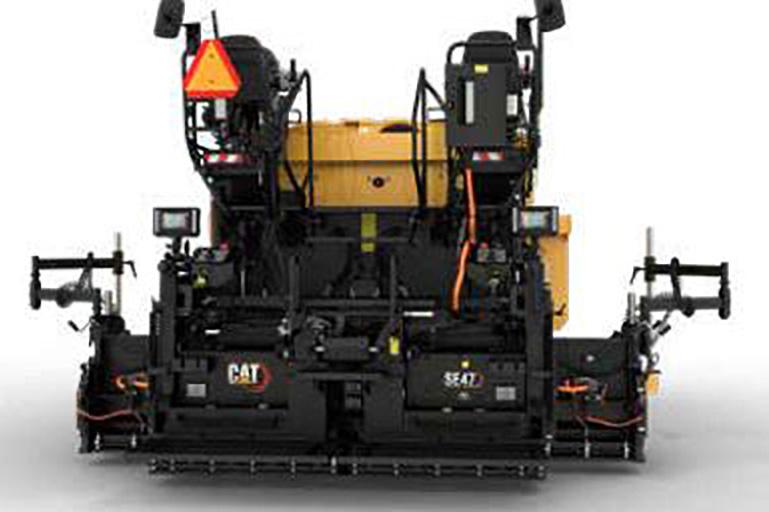
Cat SE47 FM Asphalt Screed
The SE47 FM screed is equipped with extenders in front of the main screed and offers smaller footprint that reduces handwork at the start of the paving pass.
•Simple operation, proportional extender control provides smooth adjustment when transitioning paving widths •Screed plate heating in 25 minutes to 266 deg. F •Green light indication keeps operators informed of current screed plate temperatures •Durable heating elements combined with zone monitoring helps ensure even heat distribution and smooth asphalt textures •Smooth adjustment when increasing/ decreasing paving widths helps ensure smooth transitions around obstacles •Power controls for extender slope and height enables operators to quickly manage mat angles and surface textures •Inner and outer strike-off adjustments are connected to provide single point modification that ensures equal adjustment across the width of the screed Read more at https://eqtoday.co/dhv7rm
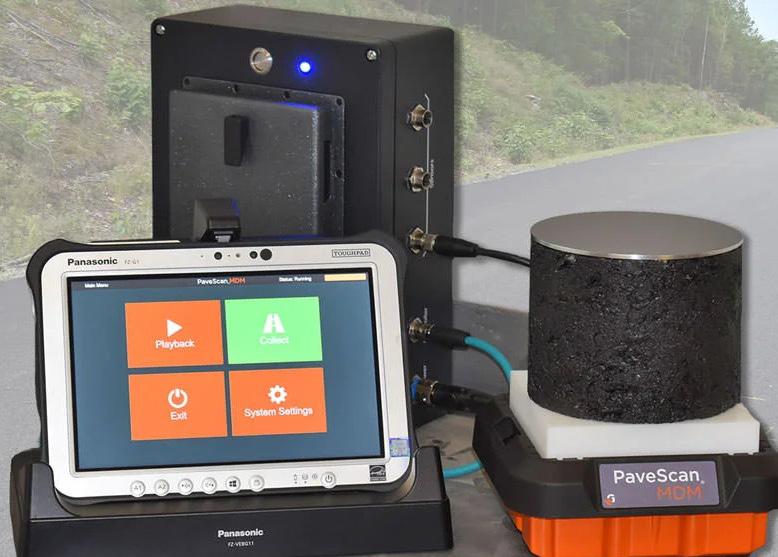
PaveScan Mix Design Module
PaveScan MDM is sensitive to subtle changes in aggregate, mix and moisture, comparing daily samples against approved mix designs. Makes any deviations apparent and helps to fix any problems before the mix is deployed in the field.
•With one five-minute lab test, users can accurately reveal problems before any need for silo dumps or other costly remediation •PaveScan MDM also turns our PaveScan RDM system into a powerful new Quality Control (QC) tool for asphalt density assessment •PaveScan MDM creates a correlation between the dielectric value of the mix at different percent voids •This correlation is used by PaveScan RDM to show accurate density variability within the asphalt mat •This degree of process control means bridge decks and longitudinal joints can now be rolled to specification in real-time Read more at https://eqtoday.co/rh5npz
Wacker Neuson Single-direction Vibratory Plates
This line of vibratory plates includes two models with Honda GX120 gasoline engines and two models powered by the BP1000 lithium-ion battery.
•Produce 2,473 and 2,923 lbs. of centrifugal force and have 13.8- and 15.8-in. baseplate widths •Optimized baseplate design with angular side edges •Responsive guide handle enables easy, comfortable operation while reducing hand-arm vibration •Includes large lifting eye and wide carrying handles •Available with a large-capacity water tank for asphalt applications Read more at https://eqtoday.co/9b7p8g
Caterpillar Pave Start Assistant Controls
Pave Start Assistant is a machine management tool that simplifies setup for performance on job sites with similar paving requirements.
•The integrated system records the functioning conditions of both the paver and screed including paving width, paving speed and towpoint position •When moving to a similar job site, the operator activates a previously recorded profile from the display menu, and the system matches machine setup specifications for reliable performance •This option is available on the SE50 V, SE50 VT, SE60 V, SE60 V XW and SE60 VT XW screeds.
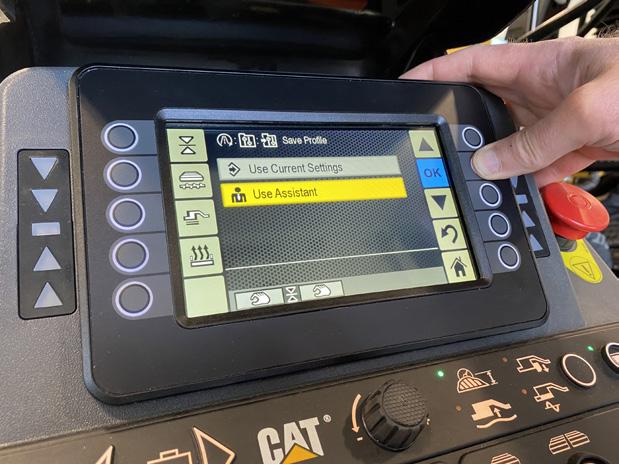
4 Ways Mobile Analytics Tools Drive Better Workflows

More data at your fingertips means you can make smarter project and business management decisions that lead to stronger profit margins.
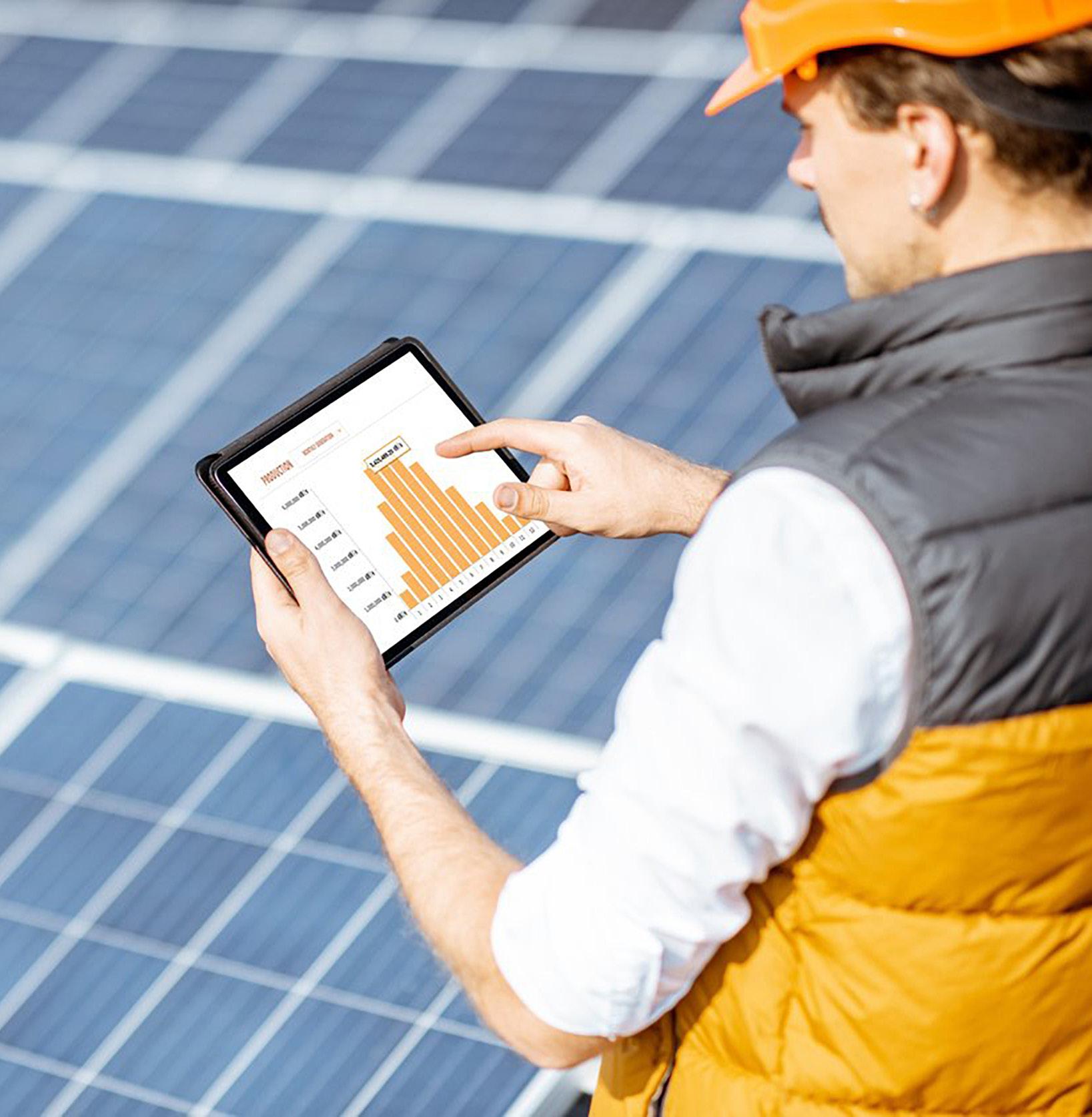
Construction projects have no shortage of data. From jobsite data collected in the field by wearables, mobile applications and sensors on equipment, to project management, accounting, job progress and HR and payroll data, most contractors are drowning in information.
With multitudes of data on hand, many contractors are sitting on an untapped gold mine of information with the potential to find more efficiencies and profit. Yet, because they don’t have the right software and workflow tools to parse and analyze the data in meaningful ways, many contractors are still struggling with consistent rework, project delays, data errors and other risks—all of which leads to profit fade.
Among contractors who have become increasingly comfortable with more modern construction data and workflow solutions, many have yet to harness the power of the connected construction software suite, where the combination of a hosted cloud environment and a single source of shared data across the organization can open the door to advanced data capabilities. Chief among these are mobile analytics, which makes advanced data easily accessible, editable and shareable on virtually any mobile device in real time, regardless of one’s location.
REAL-WORLD VALUE OF MOBILE ANALYTICS
The ability to access alwaysupdated data on projects means a much more connected construction operation, with data and collaborative communication flowing fluidly between the back office, field and extended project teams.
Analytic solutions, mobile technologies and cloud-based software applications can provide a clear, real-time picture of what’s going right and wrong across projects. With more data at their fingertips, contractors can make smarter decisions that lead to stronger profit margins.
For contractors unsure about the benefits of mobile analytics, here are four key ways they are improving construction workflows:
1. Instant Access to Data
and Reports. In addition to real-time access to data, mobile analytics solutions give users the ability to compare and contrast data to gain the specific insights they need to better understand their projects and roles.
Real-time data and connected project workflows provide project stakeholders with an accurate look at the latest information. Furthermore, data can be viewed in formats relevant to specific end users, from comprehensive reports to simple data comparisons to graphics and dashboards.
2. Democratized, Self-serve
Data. Mobile construction analytics tools help democratize data and decision making by expanding access to data across the entire construction organization and making it easy to retrieve and understand. This is especially helpful for empowering teams in the field with the data tools they need to work smarter.
Instead of complicated Excel sheet management, consistent calls between field and backoffice teams or drawn-out emails and memos, project teams in the field can visualize project information, tasks and workflows and directly pull the data most relevant to their roles.
3. Stronger Data Security.
One of the problems with construction data flowing through many channels and formats is that critical business data is ripe for security breaches. By operating in a connected, hosted cloud environment, today’s mobile construction analytics solutions not only deliver more powerful data insights in easily digestible slices, but the data and subsequent workflows can be securely shared and executed, all backed by the latest data security technologies.
Connected cloud construction suites and analytics solutions standardize and encrypt data while providing stronger permissions capabilities to ensure the right people have access to the right data at the right times.
4. Work Smarter, Saving
Time and Money. Access to advanced data analytics helps contractors identify areas for improvement to automate even more processes.
For instance, an equipment manager in the field can pull up data on a mobile device to see the average use of the company’s dozer fleet over the past six months and compare it to a sixmonth period from a year ago to view maintenance schedules. Or the manager can use data to set up alerts when certain usage numbers are triggered, without having to manually pull the data from each machine, enter it into a spreadsheet and compare figures.
MOBILE CONSTRUCTION ANALYTICS REQUIRES THE CLOUD
Today’s projects require realtime reporting, accurate data, quicker project cycles and other demands that make real-time data a necessity.
However, tapping into the value of advanced construction analytics applications can’t be done without connected cloud technologies that power real-time data collection, standardization, access and sharing. Those who haven’t moved to the cloud will soon be outpaced by competitors with updated technology. ET
Jenn Said is a freelance writer who covers the construction industry. Read more at: https://eqtoday.co/df7rm6
THE STATE OF CONSTRUCTION ANALYTICS TECHNOLOGY: The Industry Sticks its Toe in the Water

ABOVE: Construction industry contractors are finding out that project data holds real value, but are still aligning their systems, processes and staffing to take advantage of it with analytics, artificial intelligence (AI) and machine learning (machine learning) programs.
Contractors may be realizing the data that underpins their projects and businesses holds real value, but are still aligning their systems, processes and staffing to take advantage of it with analytics, artificial intelligence (AI) and machine learning (machine learning) programs.
Attendees at the Advancing Construction Analytics 2022 conference in Denver said they had not moved much further toward a mature analytics program since the last time they attended the event or previous events that like this one, convened in person. The event focused specifically on data analytics for the construction industry, with topics such as how to get buy-in from workers in the field, how to get started with artificial intelligence and overcoming technical roadblocks and challenges. Other topics included digital twin applications and data verification.
Attendees on stage during panels and over appetizers discussed the challenges of identifying which problems to solve, how to ensure data is structured and well-understood enough for analysis, staffing a data science department and the relative benefits of home-grown skunkworks projects versus packaged software.
GETTING BUY-IN
Getting both senior management and front-line workers to buy into analytics programs is one of the first hurdles in implementing programs to leverage
the tremendous amounts of data a construction contracting organization creates on a regular basis.
“There is more and more data coming in from the field,” Mortenson Construction Manager of Data Analytics and Insights David Grosshuesch said in a presentation on getting senior management buy-in. “We are still learning what stands out to people—what makes that light bulb go on.”
Grosshuesch said contractors should “focus on the business problems that matter—which is harder than it sounds. Grosshuesch said his efforts have benefitted from regular feedback and communications from Mortenson’s senior leadership. They have as a result prioritized hot button issues like safety, internal metrics and competencies, finance and process improvement. In estimating, for instance, they have been able to uncover insights that help estimators test their assumptions about where project elements should be priced.”
Sometimes though, buy-in comes after the technology proves itself. One presenter described an experience where a top executive at his company doubted the efficacy of the algorithms behind the AI trial the company was going through. The model proved that it could perform similarly to that same executive in the identification of high-risk projects.
“People don’t care how you get to conclusions in analytics projects,” Jones Brothers Construction Chief Information Officer Kevin Tuberville said. “Just find a balance on how much insight people want. And that is often a personal preference rather than something that is role-based.”

MAKE VERSUS BUY
A number of the contractors presenting were engaged in their own analytics projects, relying on in-house data science teams to construct beta projects. Robert Long, senior consultant at CPAIXCOM, presented on how contractors could construct proof-of-concepts using open source AI applications available for free online.
“There are a couple ways to do a Do-It-Yourself (DIY) proof of concept,” Long said in a discussion with ForConstructionPros prior to the event. “You can send them to an underlying open source system to see if that is good enough—at least if their data pipeline is decent and if they have someone in there that wants to learn this. If you have a data scientist on board, he is probably already doing something similar.”
Vendors at the event meanwhile had standardized software offerings for construction analytics, adding tension to the make versus buy debate. During one presentation on AI, Newmetrix CEO Josh Kanner presented a question from the audience on the desirability of growing your own analytics applications in-house versus buying a proven, packaged product.
Presenters tended to represent construction contractors rather than software vendors, which may explain the preponderance of DIY use cases. But Turner Construction Lean Manager Chris Davis shared the stage with his vendor, OpenSpace, to lay out the benefits gained from implementing that company’s computer vision and analytics solution. The application combines a 360-degree camera affixed to a hardhat or helmet with analytics and artificial intelligence tools for reporting, and AI tools to compare the images with the building information modeling (BIM) model, report on work completed and track durations and productivity.
“One area we have been able to benefit is in inventory management,” Davis said. “Visual inventory can settle months-old disputes. We had an electrical contractor that owed us 46 lift charging stations.
HERE FOR ANY JOB. ANYTIME.
Starting with the highest quality of equipment, the Compact Excavator Sales line of batterypowered excavators are built to handle jobs under unique and demanding conditions. Between the 2,375 lb. 9VXB and the 3,915 lb. 17VXB (with dig depths of up to 7 feet), CES offers a range of performance and maneuverability for the tightest workspaces. With batteries built for an uninterrupted work day, these machines minimize downtime and maximize profitability. CES, is a family-owned business, putting customers first. Knowledgeable product experts are always standing by to assist with any service or maintenance issues that arise and our streamlined parts distribution keeps projects on schedule. Call today to find out how Compact Excavator Sale’s superior service can helpyou achieve your goals.
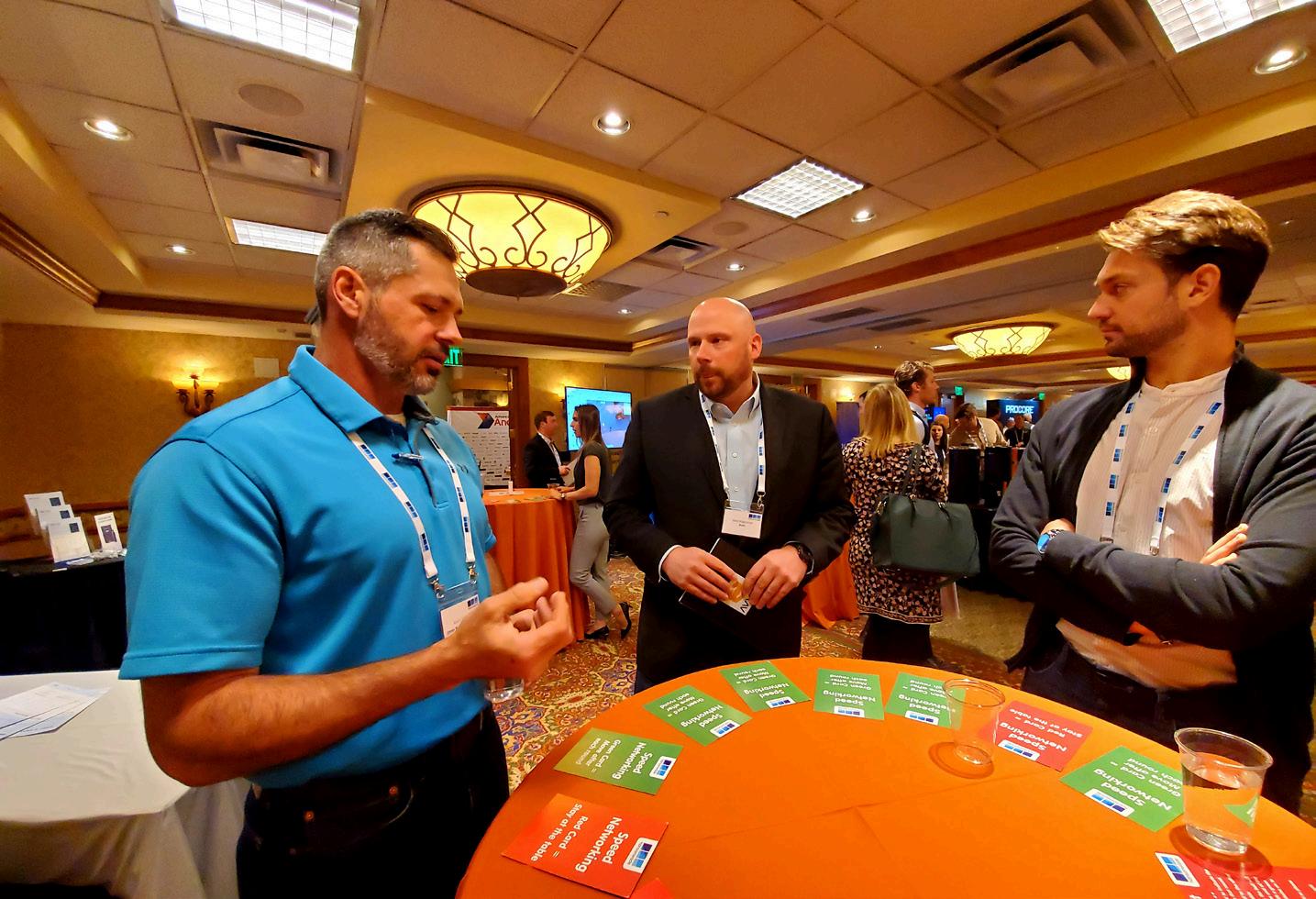
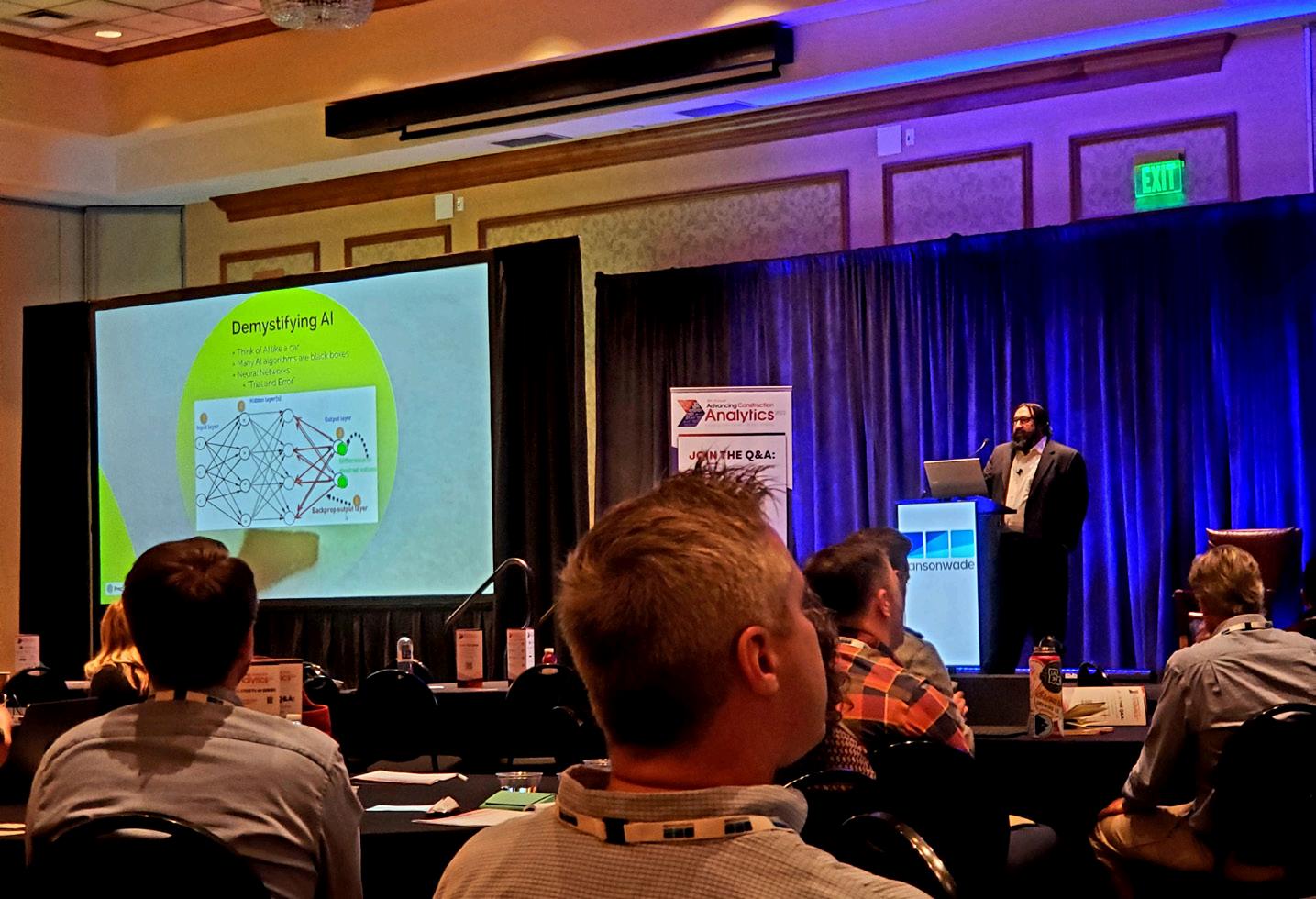
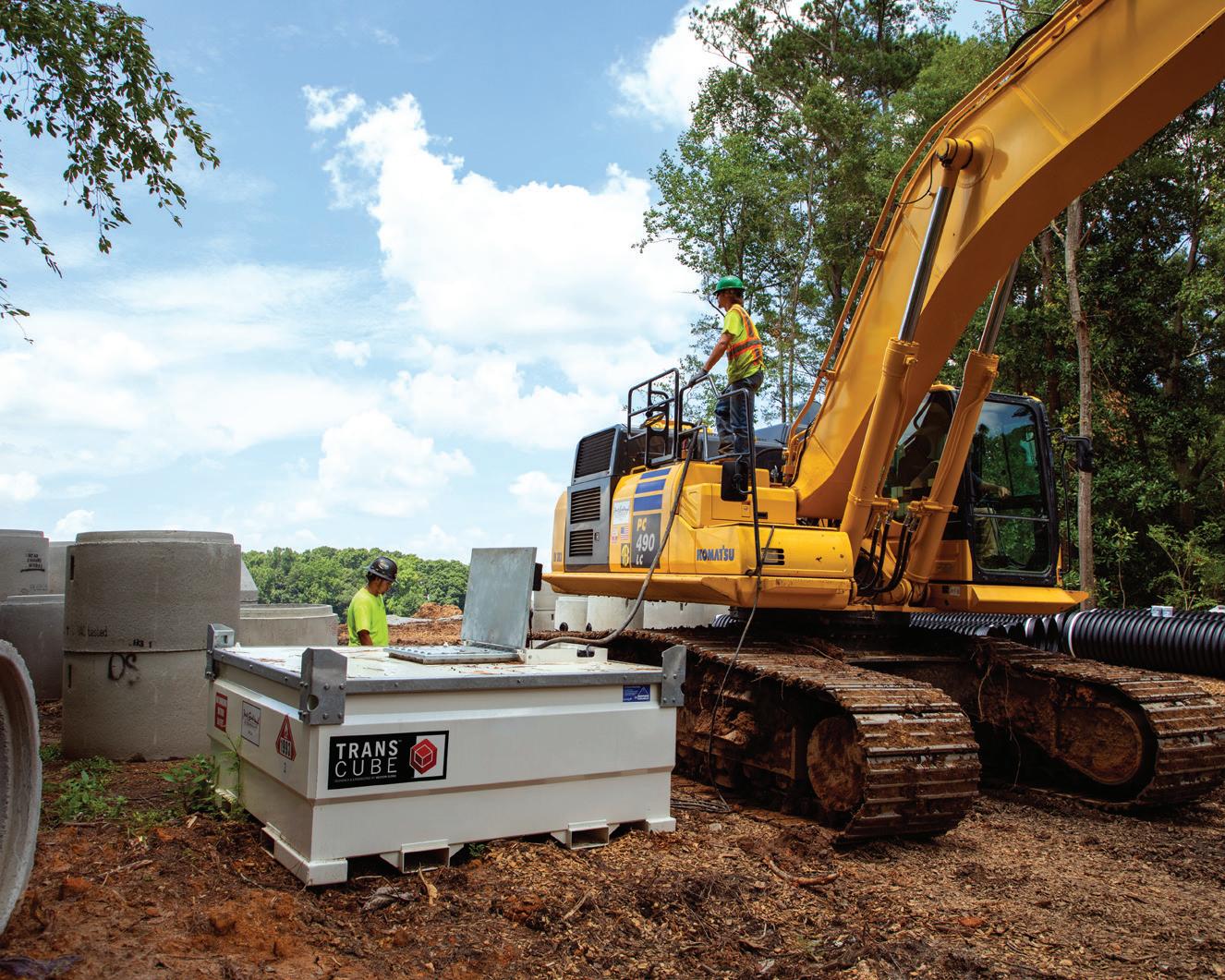
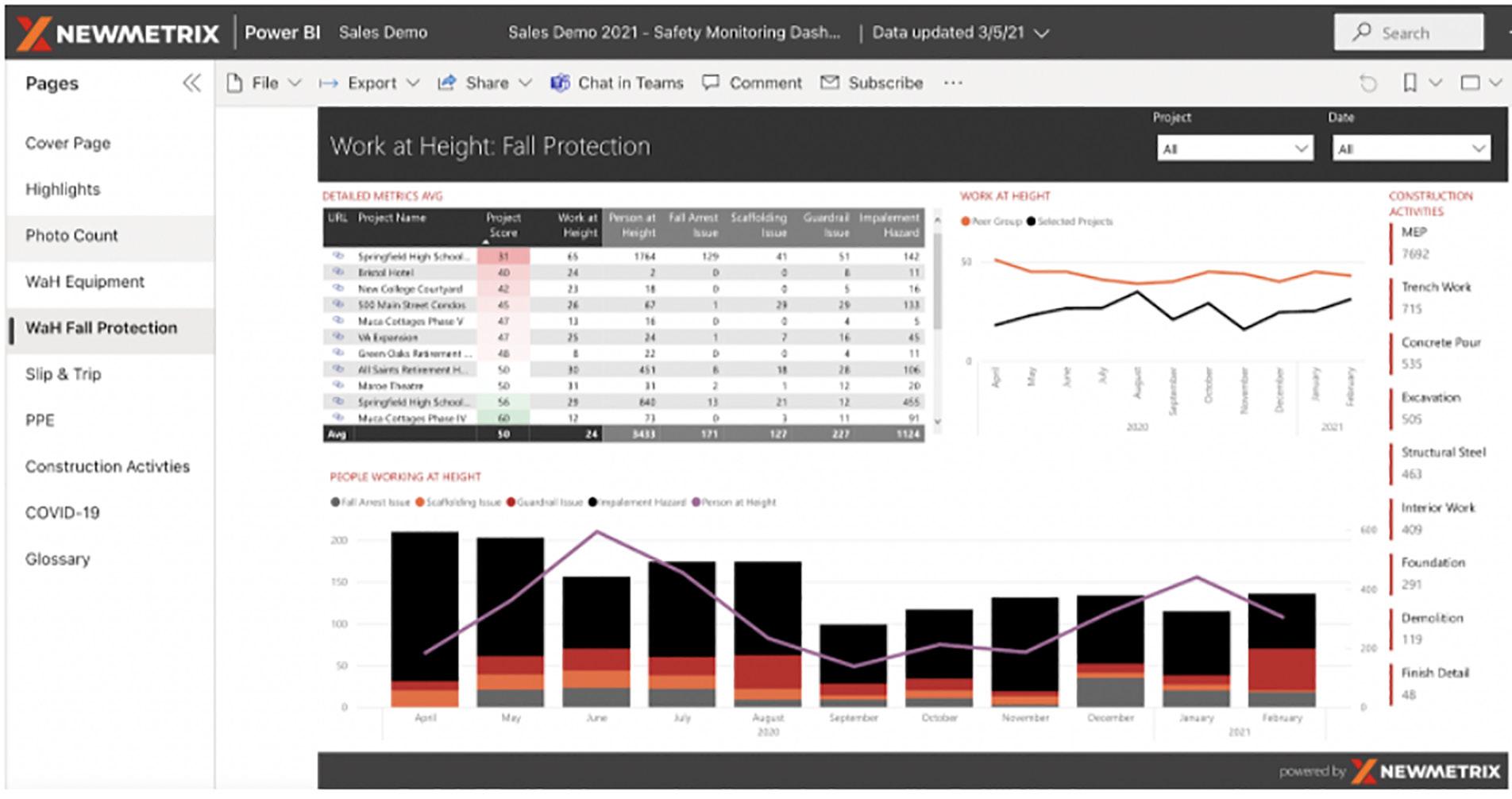
ABOVE: This Safety Monitoring dashboard from Newmetrix helps safety managers and executives identify up-to-date risk conditions that require attention. A construction-trained AI acts as a “virtual safety manager,” automatically detecting safety hazards on jobsites.
TOP LEFT: Attendees of the Advancing Construction Analytics conference in Denver participate in Speed Networking, rotating to a new table to meet new people at the sound of a bell. BOTTOM LEFT: Attendees learn about tartificial intelligence at the conference.
Charles Rathmann.
One day, me and the guy helping me do captures went and did captures at this site. As you are walking you can take a picture and field note—detailed photos of lift charging stations. You can see everywhere there are charging stations. On another job, we had too many lifts on the site. We took a snapshot of lifts across the job site to get a detailed, granular picture of the lifts, who owns them and if there was someone in there and when they would be needed, according to the schedule. Only 33% were in use. We could go back and tell our subcontractors about the quantities and the overall situation. The next day, we had a dozen lifts waiting to be picked up at the loading dock.”
In a briefing with ForConstructionPros later that day, Toric CEO Thiago Da Costa suggested there was a natural progression from home-built analytics solutions.
“There are different talents required of a contractor once there is packaged software,” Da Costa said. “From my experience, there is always going to be the need for people to take on the initiative internally, and for vendors to take on the technology, as there is a lot to build in common across companies. The buy versus build decision is a common topic in data analytics. At some point, commercial software overtakes internal software and it makes sense. It used to make sense for people to build their own distributed storage system. Now, if you’re not using a cloud storage provider you are wasting money — just save that and spend it on analysis instead.” In order to get to this crossover, where commercial software becomes consistently more desirable than homegrown tools, may come as contractors want to consistently rely on their analytics tools and see the value in always-on support of a product from a vendor. “In construction, contractors are still learning what vendors are providing and what are the right tools for them,” Da Costa said. “It is still a learning curve—some of the internal initiatives we see today started five to six years ago, and will continue to evolve. The difference between internal tools and vendor tools is that internal tools don’t have to work all the time, while vendor tools have to work all the time. That is why venture capitalists are investing so heavily in construction software companies.” ET
3 EMERGING EQUIPMENT AUTOMATION and Guidance Technologies to Watch For
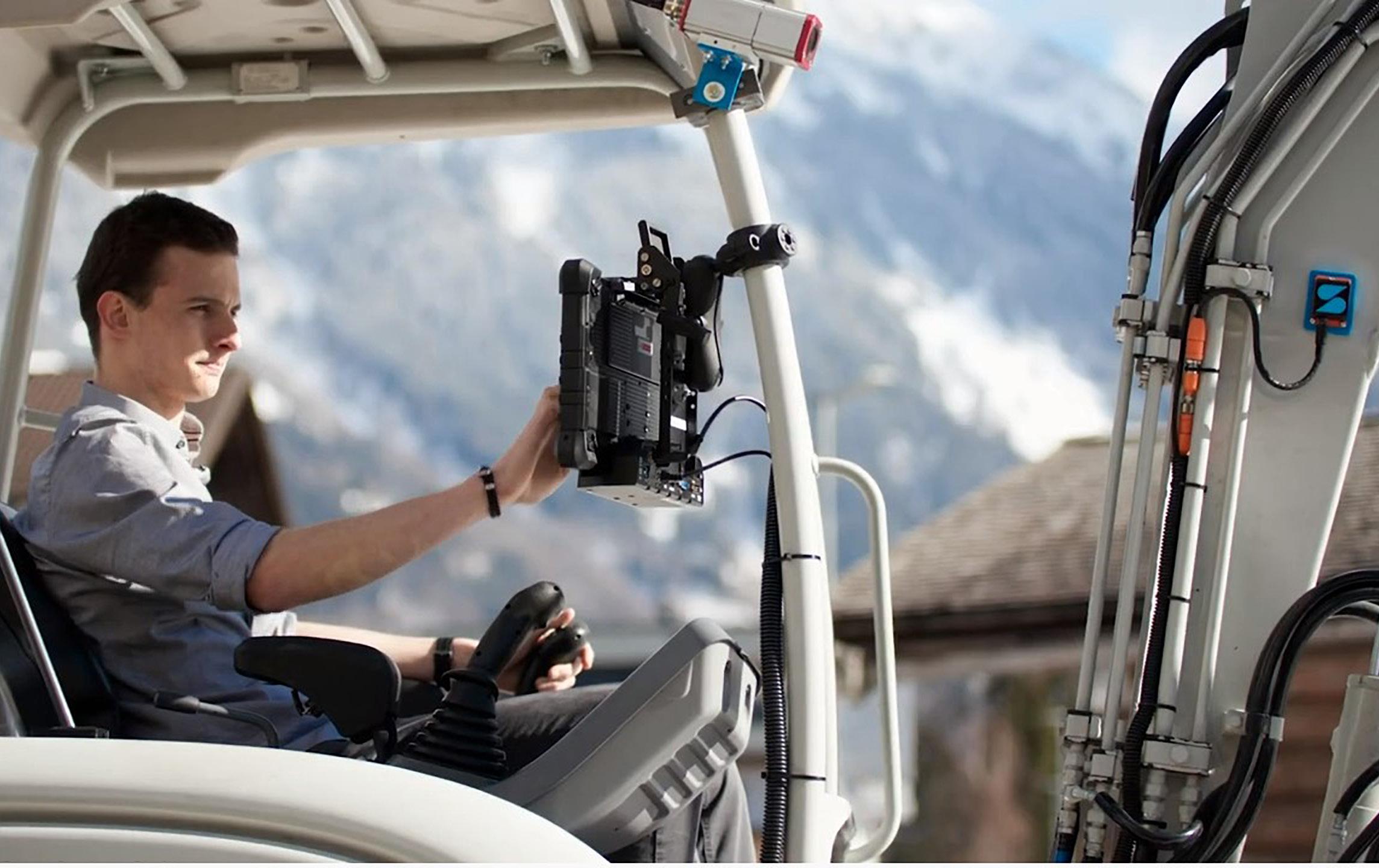
Sodex Innovations
While Trimble, Leica and Topcon own much of the market for equipment automation, these startups are offering novel or more affordable technologies that may either push the boundaries of construction equipment autonomy or enlarge the addressable market for equipment automation.
As more government infrastructure projects call for construction equipment automation, contractors involved in other types of work are attracted to the efficiencies delivered by technology that makes earthmoving and other equipment easier to use, captures production data or increases safety.
In some cases, these technologies are fresh off the drawing board, still nailing down distribution in the United States, or are just coming to market. But today and increasingly in the months and years ahead, contractors interested in equipment automation will have more choices with a broader swath of capabilities than they do today. SODEX EXCAVATOR AUTOMATED MEASUREMENT
An Austrian company, Sodex Innovations, came to market in March 2022 with an automated measurement tool targeted at small excavators. The company’s technology automates the surveying, documentation, and billing of excavated material on construction sites through continuous measurement of the three-dimensional terrain. To accomplish this, Sodex combines a camera and laser technology with several sensors to record and measure the environment in the excavator’s working area, georeferencing all measured points through a GNSS/GPS system to determine their absolute position. This creates a digital record of volume of material removed or inserted in a format that other software applications can use for billing and real-time analysis.
The SDX-4DVision is designed as a retrofitting solution that can be directly upgraded to any excavator regardless of brand, size, or age without major conversion work. Contractors can integrate the SDX-4D Vision System with conventional GNSS systems, such as those from Leica Geosystems, to automate production recording and billing.
According to Sodex Research and Development Hardware Engineer Markus Haftel, the product is in distribution in Europe but Sodex is looking for distributors in North America, including rental organizations that can retrofit their fleets as a differentiator in the market.
“If a distributor already has a fleet of excavators, they can mount our system on it and rent them out,” Haftel said. “It is also possible the distributor can sell our product independently to the fleet owner and mount it into the excavator. But in the rental channel, we anticipate they will be renting the excavator with our system installed. Our current distributors focus on small excavators between 2.5 and 15 tons. Sometimes we can retrofit larger excavators, but our main use case is in landscaping and sometimes in quarries.”
RIGHT: The automation delivered by an excavator equipped with Built Robotics technology helps the robot know what it needs to produce, so the technology enables ingestion of a design, along with GPS coordinates so the excavator can know its position and localize on site.
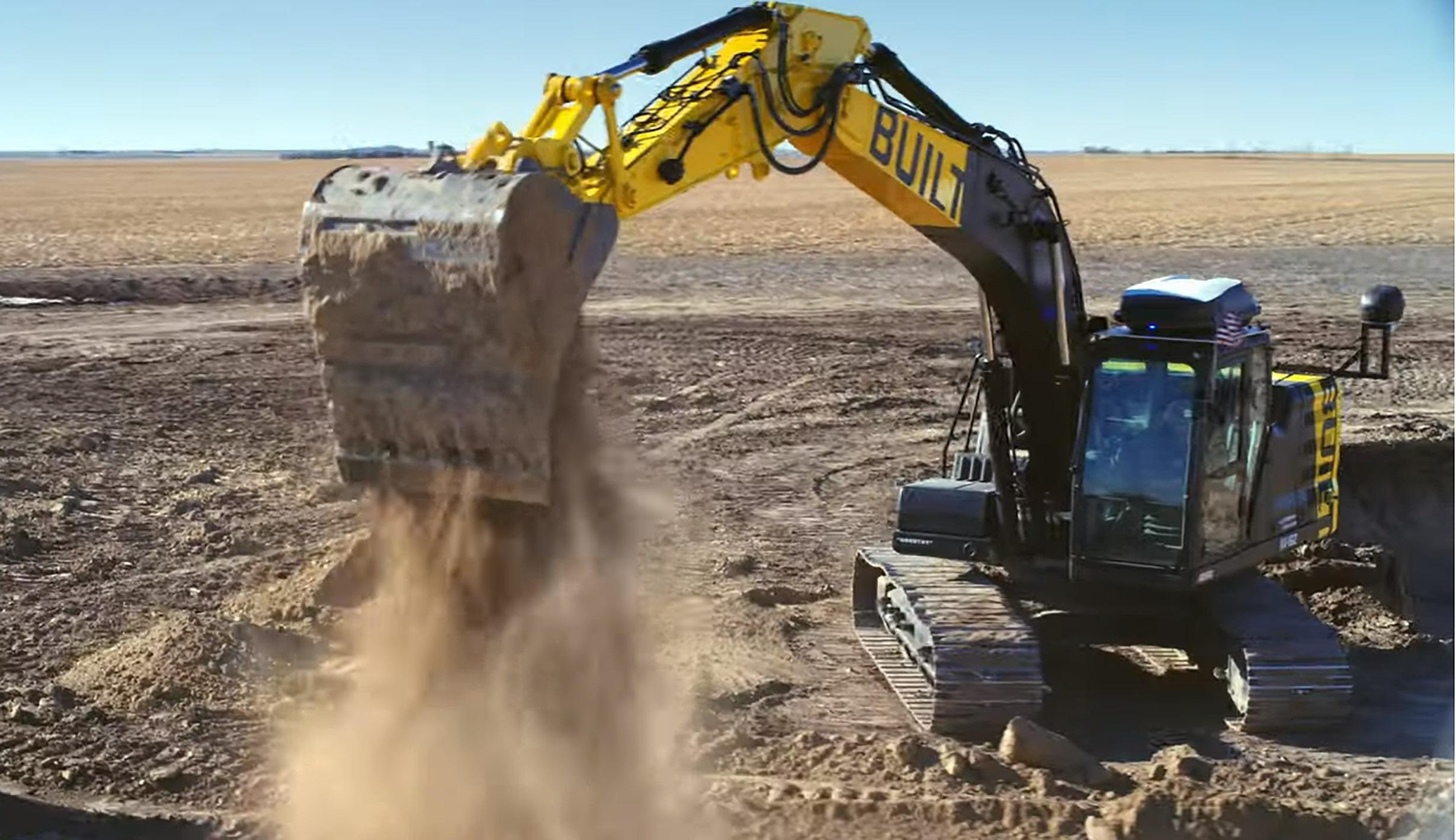
SMALL BUT GROWING
Sodex, founded in 2021, employed about a dozen at the time of ForConstructionPros’ discovery call with them. The firm at that point was primarily focused on formalizing its European distribution through a team of partner organizations and then establishing a foothold in North America. In both geographies, their ideal customer is the same.
“We are looking for customers who are medium-sized excavation companies interested in retrofitting their excavators,” Haftel said.
Installation, according to Haftel, takes about 10 hours of shop time.
“You need not that high a level of skill, but some basic mechanical skills and skills in electronics,” Haftel said. “You have to mount the contour cabinets to ensure everything is connected correctly—not just physical mounting of some sensors.”
Many of the new companies in construction equipment automation and technology are venture-funded, which can make a company vulnerable to investors’ wish for a liquidity event at some point. Sodex benefits from two principals who are invested long term—both of whom have capital from the sale of the Austrian Shpock resale app. Sodex has also received investment from the Austria Wirtschaftsservice (AWS), through the AWS Capital Initiative. This long-term funding should provide Sodex with added stability to scale its operation.
SODEX TECHNOLOGY STACK
While technology is coming to market to automate functions of excavator operation, Sodex focuses on data capture, measuring the dimensions of surrounding material around the excavator and detailing the volume of material moved.
“Our users get a detailed map afterwords of the surrounding area, including scans by time. The camera can see below grade, and based on the changing dimensions, can calculate the volume of earth moved. The technology can perform a billing calculation based on this data, based on the volume excavated, along with documentation of the work.”
A machine operator would still need to provide documentation on the type of earth moved—gravel, sand, topsoil or other material. But the technology eliminates the need for surveying for invoicing, and harnesses automated data capture on productivity to streamline the billing process further.
What Sodex is offering is a licensed software and hardware product, centered around an 800,000-points-per-second laser scanner capable of creating a very detailed and continuous map of the ground surrounded by the excavator.
“The worker inside will still dig, and can focus on his or her digging work and not the billing or surveying or other things,” Haftel said. “They don’t have to worry about the documentation of the work.”
Currently, the Sodex technology does not communicate with the cloud, connecting instead to a tablet computer in the cab through Bluetooth.
“We are developing a cloud solution so you can have an app and look up the data on the excavator,” Haftel said. “Right now, everything is stored locally and just a fraction will be sent frequently to the connected computer. Not all the data is sent. Our sensors are directly connected to the control cabinet and the tablet is connected by Bluetooth.
Features on the product roadmap include additional integrations with third party software that can consume the data and AI tools for differentiating various types of subgrades. In time, more and more data will be exposed and make consumable by external systems dedicated to tracking productivity, including enterprise resource planning (ERP) software.
BUILT ROBOTICS AUTOMATED EXCAVATION
Funded by a who’s who of construction venture capitalists, San Francisco-based Built Robotics has aftermarket solutions to automate 15- to 60-ton excavators, and in April secured an additional $64 million in Series C funding in a round lead by Tiger Global. The company in 2019 announced a partnership with Sunstate Equipment designed to funnel automated light excavators into the rental channel.
But in a briefing call with ForConstructionPros in March, Built Robotics Vice President Guarav Kikani suggested equipment in the rental channel seemed a ways off, despite a partnership with a major rental industry player. Instead, the company seems to be pursuing trenching on large infrastructure projects including solar farms.
“Today, most of our work is direct with the customers,” Kikani said. “We are working with large contractors who run a lot of equipment and have large fleets. That has been the most expedient way to go to market and to build the operational playbook. As we grow, our partnership with Sunstate Equipment and other equipment rental houses will become a critical part of our strategy to scale.”
While eventually automation technology from Built Robotics could be offered by OEMs, the focus into the foreseeable future will be aftermarket installation
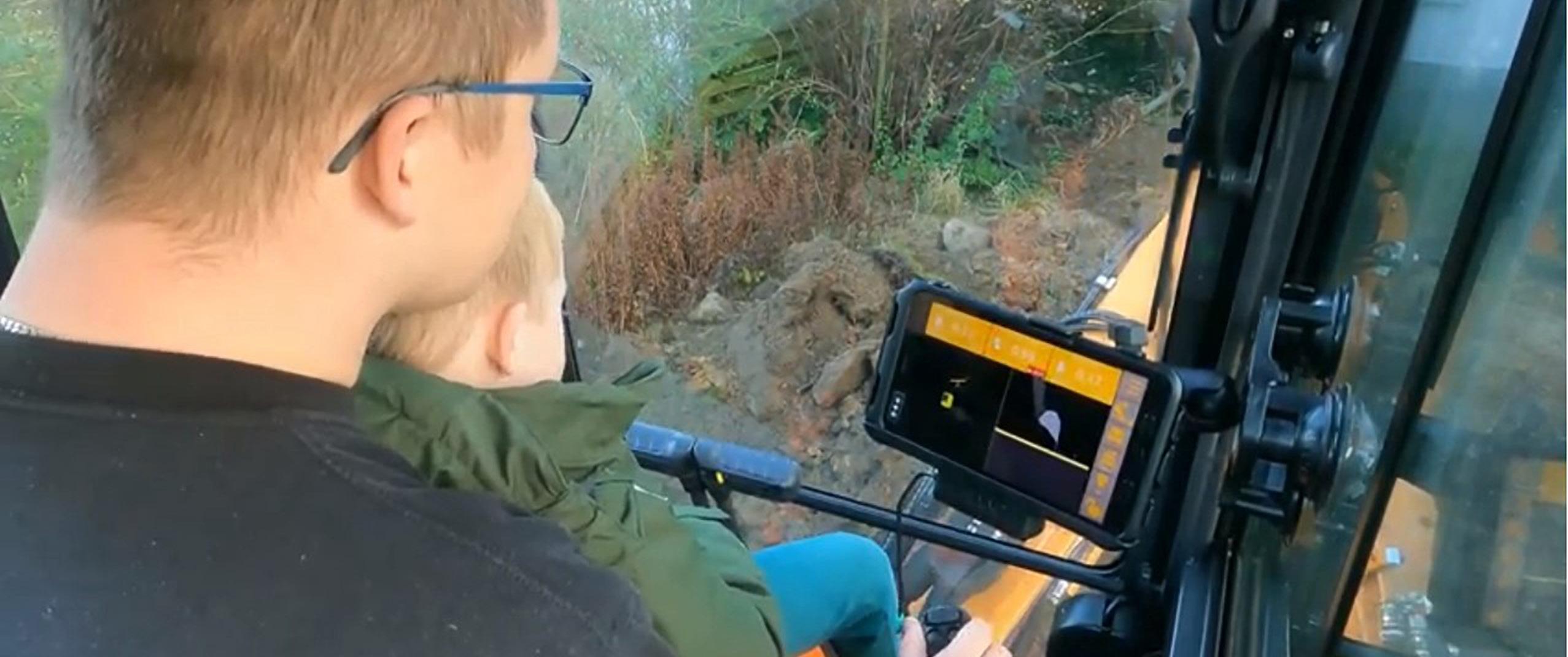
due to the long timeframe it takes for equipment already in the field to turn over. The tech will automate both electronically and pilot hydraulic systems. But since electronic controls are standard on more current equipment since about 2018, and since that is the direction the industry is going, installation will get easier and easier going forward.
Fueled by venture capital, Built Robotics has built a team of about 35 people in San Francisco and Australia. About a fifth of that staff is devoted to customer success, indicating a growing ability to ensure customers realize value on an investment in Built Robotics technologies. Another 50% to 60% of the team is software and robotics engineers— creating new features and tools based on feedback from the field. That team will work initially with major engineering, procurement, construction (EPC) contractors and smaller contractors focused on utilities and trenching—anyone, according to Kikani, focused on digging trenches with excavators.
“We are also seeing interest in our tech outside of the contractor community,” Kikani said. “Developers are interested in this tech—and we could see more of a mandate for their contractors to use automation like this. But when we think longer term, I see us working directly with rental companies and OEMs to integrate our automation technologies with equipment.”
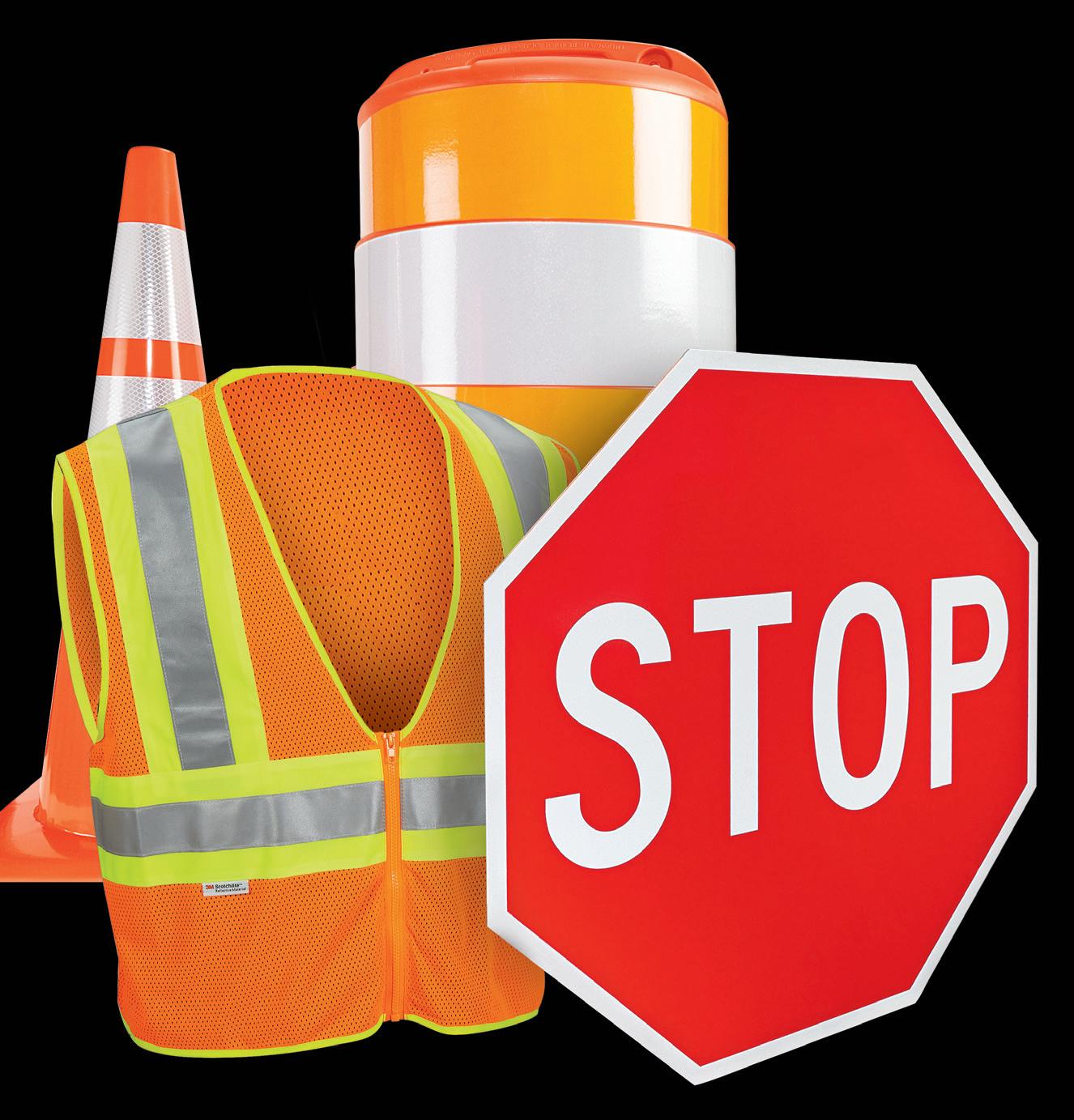
Unicontrol
BUILT ROBOTICS TECH STACK
The company has raised $112 million in venture funding to date, and according to Kikani, this is necessary to fuel the company’s ongoing research and development efforts. This in turn will pay dividends to investors as the technology matures, becoming more useful in redevelopment and urban environments.
“First, even if we just do greenfield projects like we are now, that is still a massive market,” Kikani said. “Our focus now is getting the technology out there, into customer hands, and then building that operational playbook. There is a lot of work to be done. We do intend to handle more corner cases and urban environments, but for now we are pursuing the safest and more prudent projects. This is not just a science experiment, we have been driving customer value since Day One. So yes, we are doing trenches now, but getting into site-level orchestration of job sites in the future.”
The automation delivered by an excavator equipped with Built Robotics technology first of all helps the robot know what it needs to produce, so the technology enables ingestion of a design, along with GPS coordinates so the excavator can know its position and localize on site. A series of sensors collect information on its orientation in space, including tilt and velocity.
“The excavator takes all of these data points and uses them to pinpoint the end effector—the tip of the bucket teeth— by knowing exactly where it is digging, comparing it to what it knows about the site,” Kikani said. “It can turn the existing world into the design it has been given.”
An edge computing device on the excavator runs the algorithms that direct production, collecting insight from the environment including resistance from the ground and track slip as it goes that results in modified tactics and approaches. Built Robotics also includes camerabased machine vision, used primarily for pedestrian detection. High fidelity radar meanwhile helps the excavator avoid buried infrastructure.
Roadmap items include capabilities for backfill and compaction and loading trucks, which has been a challenge for researchers working to help an automated wheel loader identify the truck where material is to be deposited, resulting in efforts to teach the machine learning algorithm using videos of scale models.
“There are some sophisticated, yet reliable, ways to do that,” Kikani said. “I would argue one of the harder things to do is not recognizing the hopper but to see the material to scoop. Spoil piles change as you move them. That requires a lot of sophistication.”
Also on the roadmap, according to Kikani, are capabilities for pile driving— in demand due to the construction of solar power infrastructure, and grading.
π
SHIPPING SUPPLY SPECIALISTS
OVER 2,850 SAFETY PRODUCTS IN STOCK
ORDER BY 6 PM FOR SAME DAY SHIPPING
COMPLETE CATALOG 1-800-295-5510
uline.com
MOVING TOWARD COMMERCIALIZATION
While still addressing specific and repetitive use cases, Built Robotics is securing sales and shipping product. They will not disclose unit numbers sold but are according to Kikani finding some commercial success. And at the time of Kikani’s debriefing call with ForConstructionPros in March, hardware was available and installations were scheduling about a week out.
“Last year was huge in that we did ship a lot more units and handed them off to customers,” Kikani said. “Now, it is about getting more numbers out there.”
To help the company scale from a sales perspective, and to streamline installations, Built Robotics is assembling a channel and service partnerships.
“Installation, if it is customer owned, takes one to two hours to do the hardware and another hour to do calibration,” Kikani said. “Today, Built Robotics does the installation. Over time, we will provide training and certification to make sure customers and workers can successfully operate automated equipment. We are partnered with International Union of Operating Engineers to train their members on how to run robots in the field. We have a couple already certified.”
ROOM FOR GROWTH
Some end customers who have experienced Built Robotics’ technology in the field report that the excavators still require a good deal of oversight and stop frequently due to conditions in the site. The robots also exclusively rely on cell signals for communication, apart from a USB port for updates and loading models. In time, other communication modalities, including satellite, could be added to the product.
“For updates, we can do it the oldfashioned way with a USB stick,” Kikani said. “Connectivity is very helpful for streaming video feeds and other nice features, like pushing data to the cloud. But all of the computation happens on the edge and on these robots—that is where the data hungry stuff happens.”
UNICONTROL MACHINE GUIDANCE
Founded in 2018 in Odense, Syddanmark, Norway and with boots on the ground in North America as of early 2022, Unicontrol has launched Unicontrol3D, a straightforward guideon-the-side interactive tool to make excavation easier. In a March call with ForConstructionPros, Unicontrol Chief Commercial Officer Ehsanullah Ekhlas described how the company is offering a software-centric approach that makes using excavators, wheel loaders and backhoes more intuitive, putting technology in the hands of small contractors and potentially making equipment easier to use.
AFFORDABLE EXCAVATOR TECHNOLOGY
While dominant excavator technologies focus on automating operation of components including the arm, dipper arm, bucket cylinder and that swing gear that controls the turret—plus forward motion of the vehicle itself—Unicontrol is focused on improving operator effectiveness and efficiency, eliminating the need for site surveyors because the operator can see the project plan superimposed on represented on a screen in the cab. The Unicontrol3D system includes sensors for the boom, dipper arm, swing arm and on the bucket to sense tilt. Also included is a GPS receiver and control box, GPS antennae and tablet display. Operators can share design files between multiple machines equipped with Unicontrol3D, orient and execute a design with GPS guidance or operate in 2D mode when not connected to GPS by zeroing out the height of the bucket each time the machine is moved.
Unicontrol3D is a product for companies or individual owner-operators who want the ability to dig more effectively and collect productivity information for billing without plunking down the pile of money required for automation.
“The contractor is asking for help because they have to document everything they are doing,” Ekhlas said. “Some need GPS to get the job. For them, getting into a bigger brand has been quite expensive and quite complicated. They may be afraid of machine control.”
While Unicontrol does not automate production, it does automate data collection for production reporting and as-builts. This, along with eliminating the cost of a third-party surveyor or flag man, makes for rapid ROI.
“We help operators avoid rework, avoid surveyors telling you where to dig,
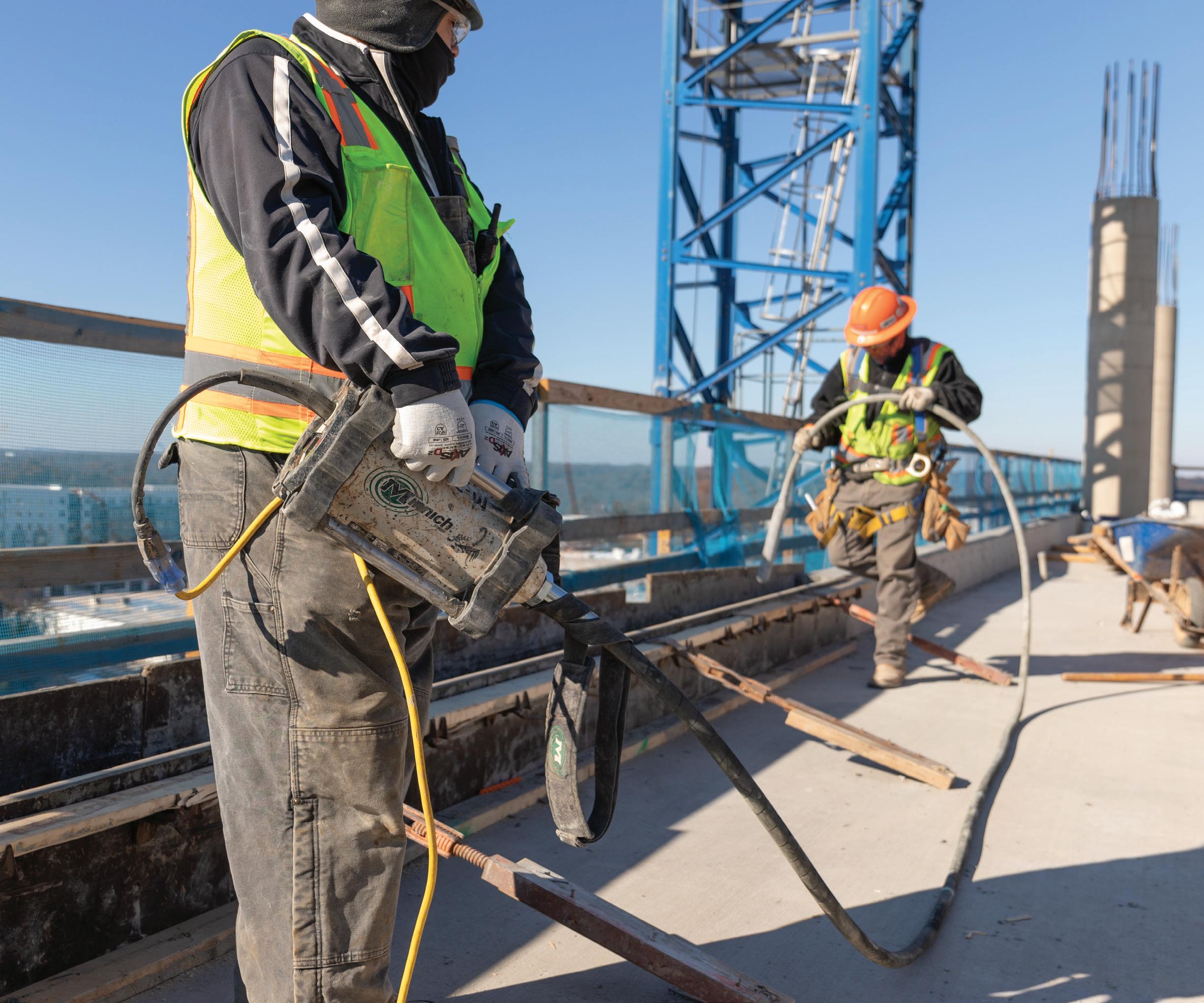
THE STINGER
The Stinger electric flex shaft vibrator is rugged, lightweight, and powerful. The 115v electric motor has been designed to run cool with the power and torque to handle todays concrete loads. The stinger attaches to competitor core and casing with quick disconnect adapters.

all in machine,” Ekhlas said. “This is a tech they know they need to use. If they don’t do it, they will not survive.”
While Unicontrol does not automate the machine itself, it’s more affordable than applications that do, coming in at around $3,000 per machine, including installation
“At the moment we are only guided, we are not in the automation space,” Ekhlas said. “We show where to dig and how deep, but the ability to control the machine is on our roadmap. A lot of operators are not happy with those construction equipment automation systems, they are working way too slowly for them. The biggest difference is simplicity.”
Unicontrol is also open to multiple non-proprietary file types when it comes to project models, including XML and DXF files.
FAST-GROWING STARTUP
The company employs about 40 and has its technology on about 700 pieces of equipment and is setting up distribution in North America. The company has 11 employees dedicated to customer success, and according to Ekhlas, there is a reason such a small complement can support so many systems in the field.
“The way we go about doing this is rather different,” Ekhlas said. “But we have built it differently, we see ourselves essentially as a software company, and most of our developers are in fact also somewhat customer facing. We go to market direct only in Denmark, and in the rest of the world rely on distributors to do the first and second level of support, and we train them. That is why there are not more customer success people. Our product does not require much, and then we go to market with others who sell and work directly with the customer.”
“Our system is built by equipment users for equipment users,” Ekhlas said. “Other systems are built by surveyors for surveyors. When we started, we reached out to equipment operators at all levels and got feedback and implemented that within short time cycles. We believe that is the right way to go.”
The technology offered by Unicontrol is designed precisely to make operating easier—not by automating the productive capacity of the equipment but by enabling the operator to see how what they are doing with the machine conforms to the BIM model, improving quality and consistency.
Unicontrol also should prove economically sustainable as they are already profitable and have internal funding
“We have three founders who got some soft money and then we brought two business angels onboard in April of 2020,” Ekhlas said. “And then we have another element that will help us—our technology is designed for mass customization. The system for U.S. is not the same as what we may sell in Australia, Poland or Denmark—we have a lot of features that distributors choose that determine how the system will operate—what screens you are seeing and what functionality is available.”
The tablet application is updated from a cloud application running on AWS.
“At the start, we were updating every two weeks,” Ekhlas said. “Now, we are on a cadence of every two to three months. The bigger we get, the more features that will change, leading to more frequent updates.”
The cloud application also enables the operator to upload projects, and the computer guidance technology then assists the user in executing against that project plan or model. There is also a diagnostic tool that enables the Unicontrol to support team to see operational data from the last 30 days—a valuable trouble shooting tool.
“Based on that, can see if there is a cable loose, or what the root of a problem is,” Ekhlas said. “About 95% of challenges are solved from the office.”
To be clear, Unicontrol3D includes both hardware that collects data from the equipment and the software, which is their main focus, but they source the hardware components. And the fact that the hardware is not proprietary may help them deliver products during a time in history characterized by supply chain constraints.
“We are not manufacturing,” Ekhlas said. “We are an open system. So while we deliver the full system, we are working with those that deliver the hardware. What that means is that we can deliver— more so than some other people. With the standard components, you get the luxury of double or triple suppliers of the same part, which makes it more available in the market.”
#1 Contractor’s Choice for Mechanized Cutting Solutions!
ADDING VALUE TO YOUR EXCAVATOR
TRENCHING, DEMOLITION, ROCK EXCAVATION, SOIL MIXING and more
ROCK AND CONCRETE GRINDERS ROCK TRENCHING ATTACHMENTS Founded in 2018 in Odense, Syddanmark, Norway and with boots on the ground in North America as of early 2022, Unicontrol has launched Unicontrol3D, a straightforward guide-on-the-side interactive tool to make excavation easier.
Unicontrol
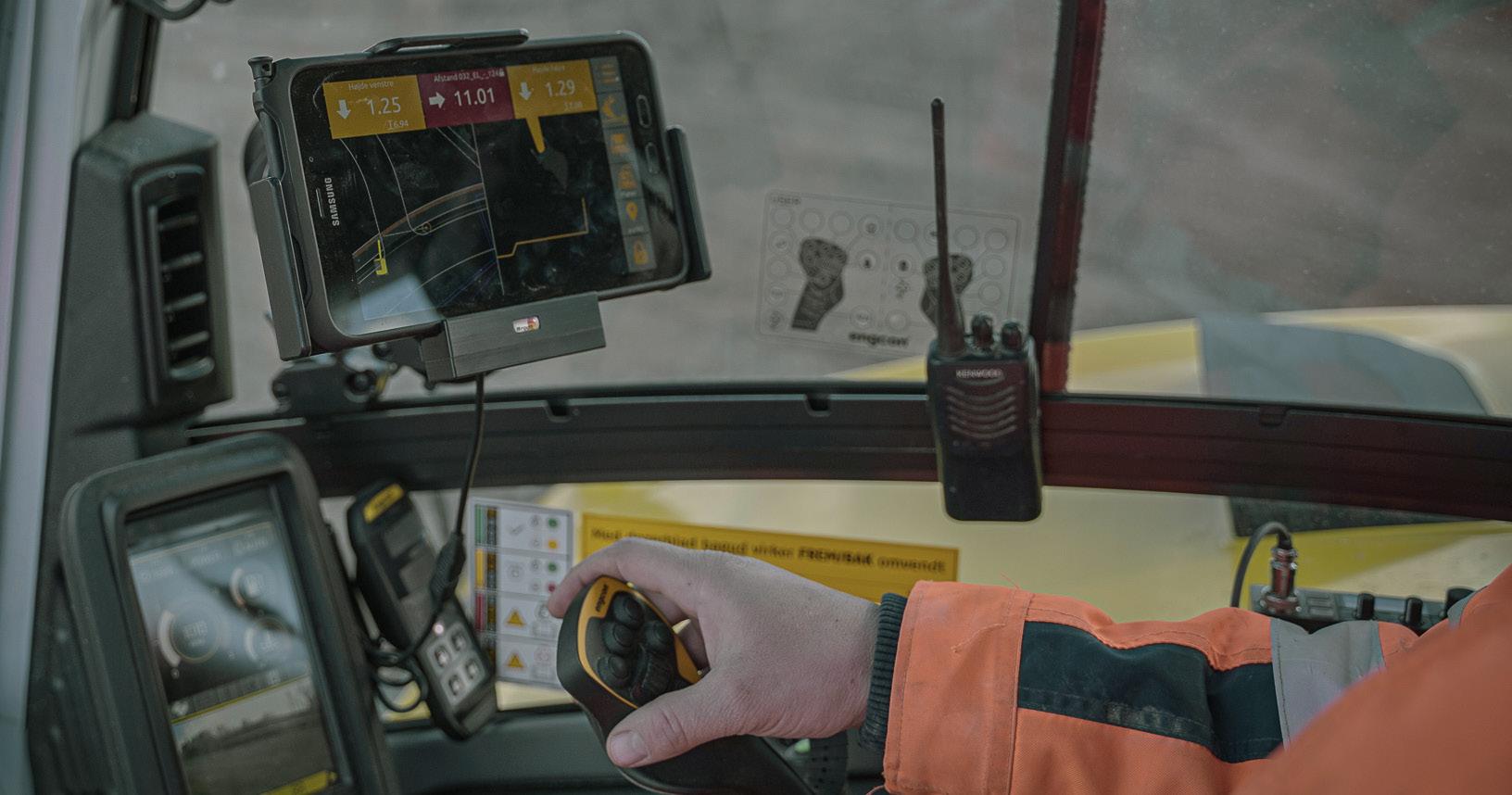
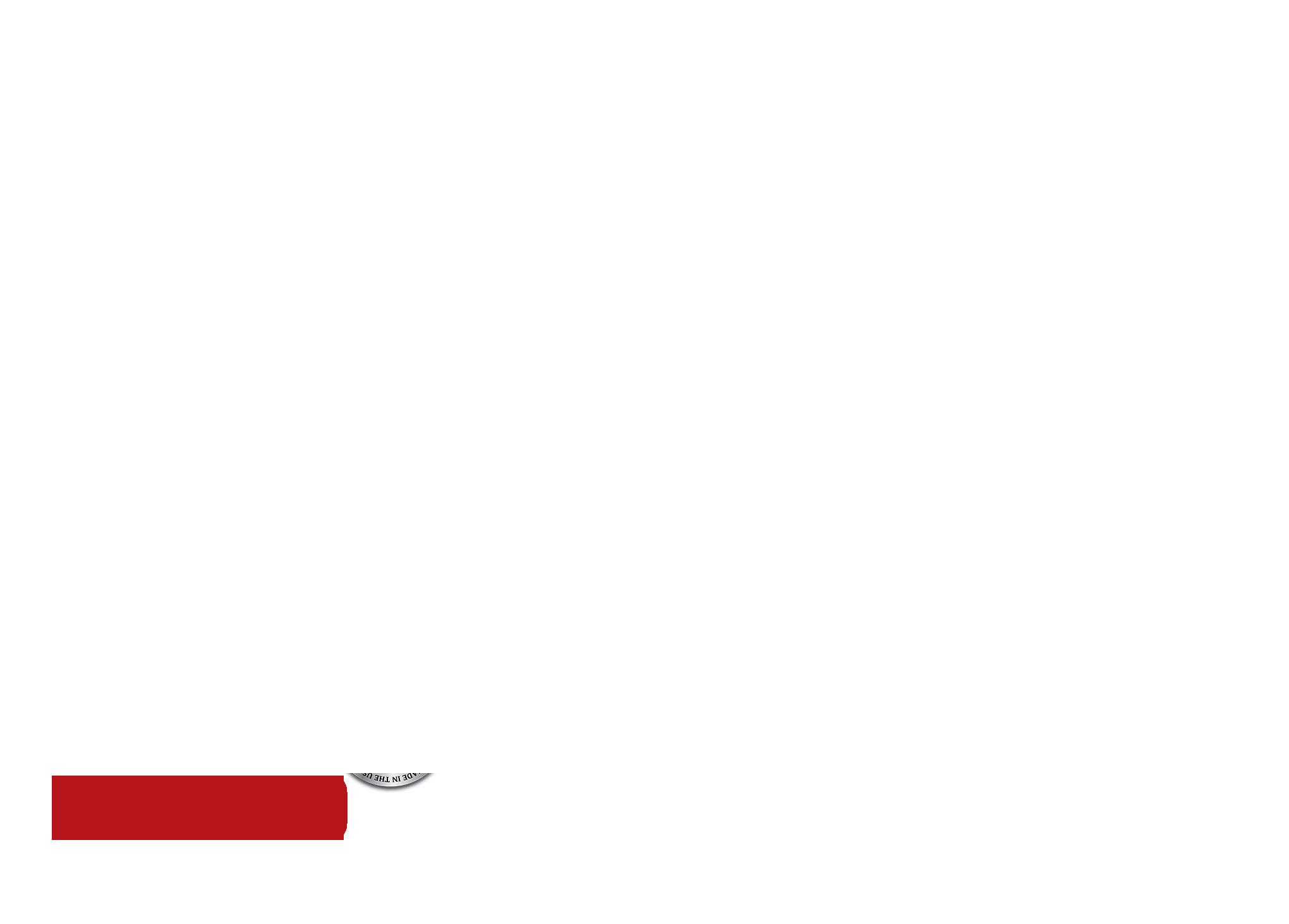
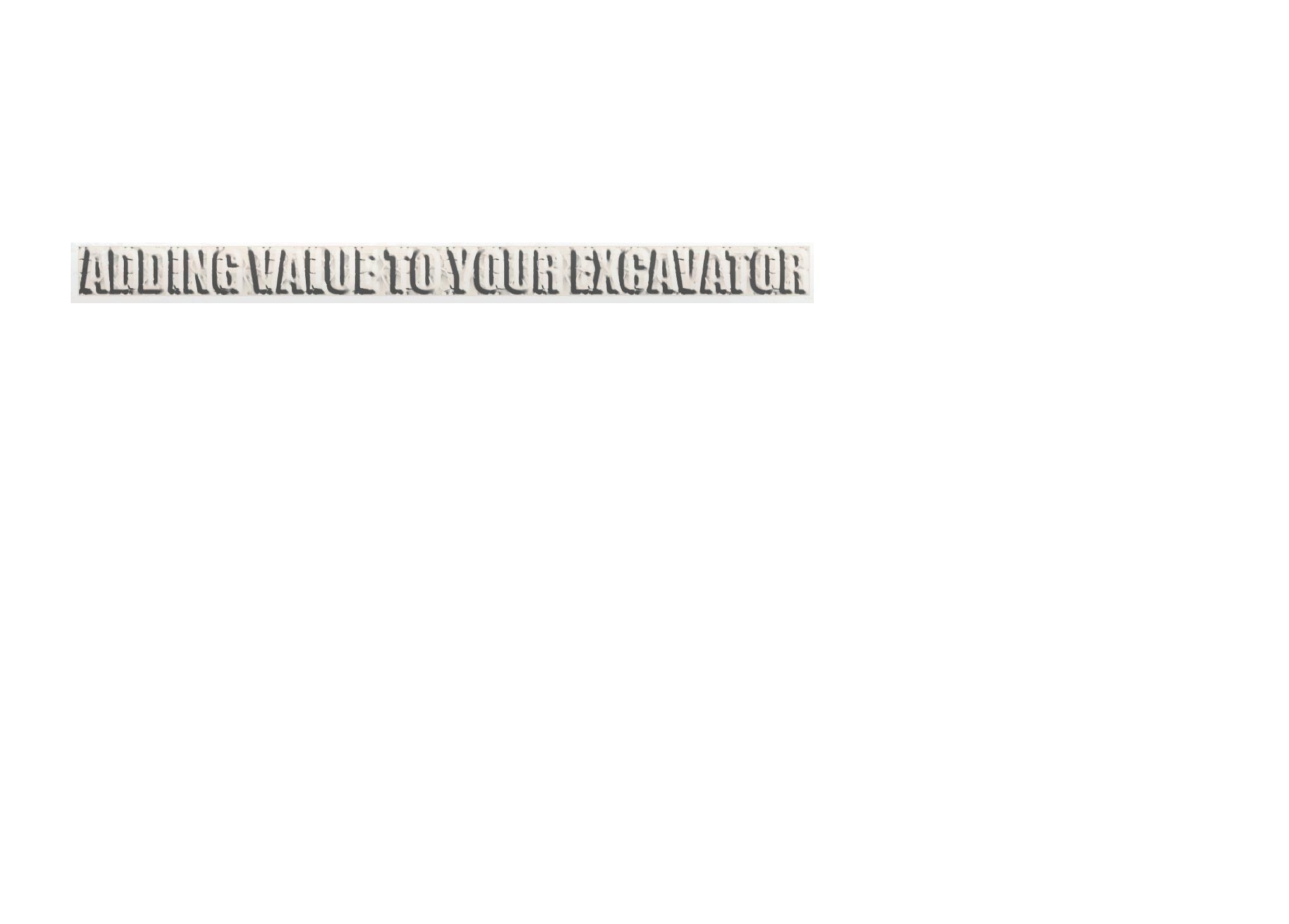
www.antraquip.net info@antraquip.net
For Additional Information Call 301-665-1165 NEED TO INCREASE PRODUCTION?
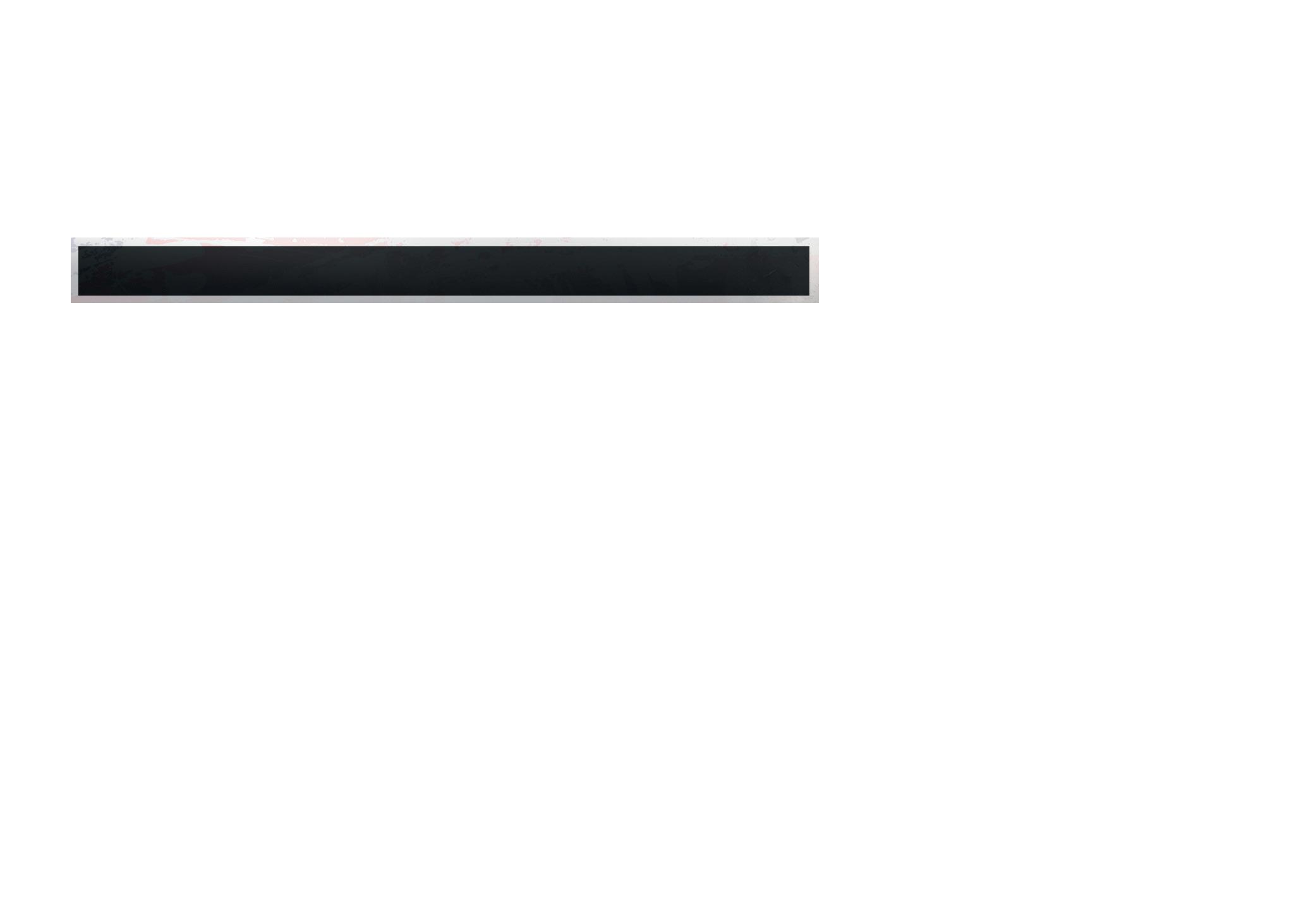
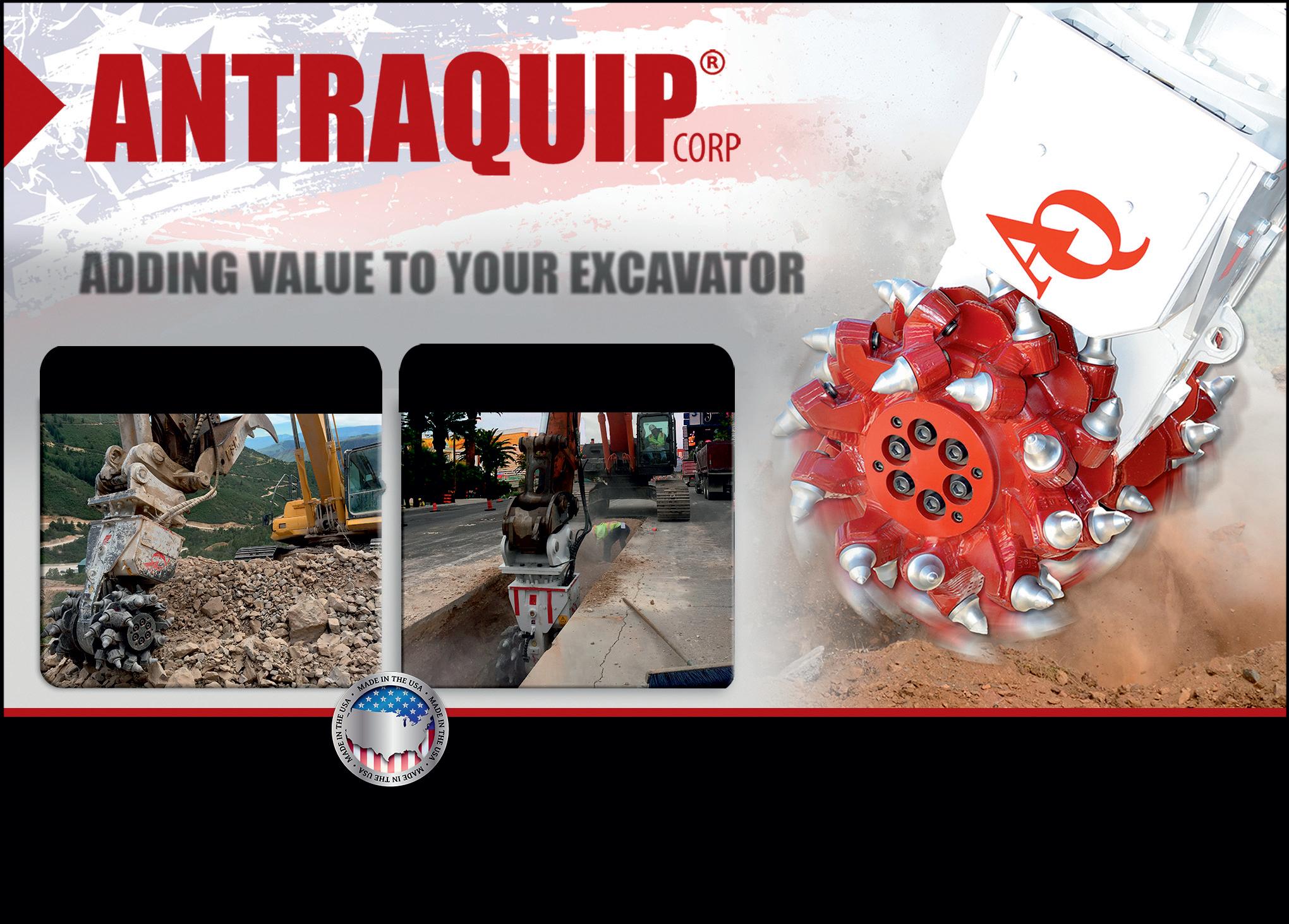
UNICONTROL ROADMAP
While the primary goal right now is for Unicontrol to penetrate the North American market, they also have additional solutions waiting in the wings.
“We are trying to work on different solutions and have a solution in addition to the excavator and wheel loader. We have a handheld GPS solution coming to expand our product portfolio. We know that there is a large market for dozers in the United States, and we are working on that, as well as a skid steer and a grader solution.” ET