
8 minute read
EWD
Overview of the “Optidrive” edger optimizer installation installed in December: From the right, the side material is fed from the pre-cut of the chipper line via the equalisers onto the cross conveyor in front of the enclosed control stand. After the end cross-cut and the scanning in the transverse pass, the board is aligned before the second scan in the longitudinal pass. Behind it, the closed feed (yellow cover) to the edging circular saw, at the back left of the image.
High yield, productivity and reliability
Advertisement
Holzindustrie Losheim (Hilo) has replaced its hard working EWD ‘Optimes’ edger after 28 years of service. In its place is the new EWD ‘Optidrive’ highperformance edger
With its processing speed of 28-30 bd/min, the EWD ‘Optimes’ board edger at Hilo Holz in Losheim, Germany, had become a bottleneck. Last December, in a first step toward upgrading the existing sawline, the Optimise unit was replaced by an ‘Optidrive’ board edger from EWD and its TAE edger with skew and slew function of for circular saws, giving higher performance and better yield.
Founded in 1992, the family business is managed by Thomas Perings. The sawmill cuts about 220,000 m3/y of logs, mainly Spruce, but also Douglas fir and a mix of the other softwoods available in the region for packaging lumber. The round timber is purchased as long logs and cut to lengths of up to 5.1 m and diameters of up to 55 cm. The company employs 45 people in the sawmill, operating an EWD chippercircular sawline, in single-shift operation.
Producing mainly green sawn Matthias Koch (EWD), responsible for the planning and implementation of the project, and the two owners Pascal and Thomas Perings (from left). Not pictured is Hilo production manager Rouven Schmaus
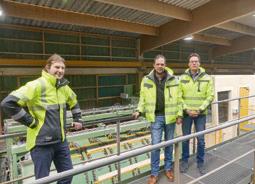
lumber for pallet and packaging, Hilo also offers KD lumber and value-added lumber, planed and available in numerous profiles. For garden and outdoor use, lumber is available impregnated.
Important customers for the company are packers and pallet manufacturers, horticulture and, increasingly, gluelam producers.
We have to continue to develop as a company
Pascal Perings, Hilo
Successful collaboration
For Hilo managing director Perings, the most important factors when deciding to invest in the future of the plant were the highest possible yield, the productivity and the reliability of the system, because one thing is very clear to him: “We have to continue to develop as a company.”
To this end, the reducer circular sawline had been partially updated more than 10 years ago. About one-and a-half years ago, together with EWD, they began planning the replacement of the Optimes edger supplied in 1993. It was clear that the new optimizing board edger should be located in the same place as its predecessor and that the loss of production due to the conversion had to be limited as much as possible.
That was achieved in close cooperation with the manufacturer, which was praised by the brothers Thomas and Pascal Perings: at the beginning of December last year, Hilo employees, with the support of an EWD technician, removed the old edger and then, without delay, the new optimizing board edger was delivered to the sawmill and installed for a smooth transition.
The hall roof had to be opened for this purpose and closed again in time for the onset of winter. Hilo was able to put the new edger into operation at the end of December after a total of three weeks of production downtime, even while taking the Christmas days off and not working on the installation.
The new EWD edger – model Optidrive TAE – has since been running without any problems, though at the still limited capacity of 30 bd/min. Limitations are centred on the downstream trimmer, which allows the company to run the OptiDrive at a feed speed of just 200 m/min.
Nevertheless, the new edger has already increased the edging performance. In the summer 2021, after a second conversion phase, the current trimmer behind the edger will be replaced so that the edger can be operated at full speed of up to 420 m/min, which corresponds to 50-55 bd/min depending on board widths and lengths.
The Optidrive edger is special, because of the skew and slew function of the circular saws, which can be moved and swiveled during the edging cut. In the process known as ‘skew and slew’ or diagonal edging, the circular saws are moved transversely to the feed direction by up to several millimeters per linear meter during the cut, mind you at a feed rate of up to 7 m/sec.
This way, the yield can be increased, especially in the case of irregular board contours. According to EWD’s experience with the edgers already installed, an increase in yield in the order of up to 2% over all is possible, depending on the products to be produced and the raw material.
The lateral movement of the saws, the ‘slew move’ during the cut exerts transverse forces on the circular saw blades. The thicker the boards, the higher the forces that occur. At present, Hilo’s side
Swiveling on the horizontal plane of the edger saw box, the ‘skew move’ avoids these lateral forces for all board thicknesses, thus eliminating wear and tear on the saws and loss of quality in the edging cut
Pascal Perings, Hilo
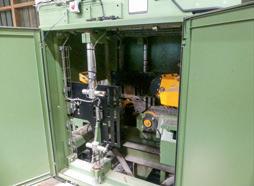
Integrated Microtec measuring system for longitudinal scanning
Cross-cutting station and measuring beam for board scanning in cross-feed (material feed in image from left
The two mobile mounted units of the “TAE” circular saw are swivelled on the horizontal plane for “shifting”. Photos: J. Härer
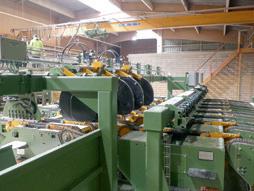


Two-stage board separation with intermediate screw roller conveyor for alignment at the zero line
boards have mainly thicknesses of 17-22 mm. In the near future, board thicknesses of up to 55 mm are also planned.
Swiveling on the horizontal plane of the edger saw box, the ‘skew move’ – not only of the saw blades but also of the entire swivelmounted machine unit – avoids these lateral forces for all board thicknesses, thus eliminating wear and tear on the saws and loss of quality in the edging cut.
Precision and high feed rate
To achieve a high yield with optimized quality at such high feed rates of up to 420 m/min and piece counts of up to 55 bd/min, additional components in the plant are indispensable.
This starts with the two-stage separation of the side boards coming from the reducer circular saw line. Via a first, S-shaped pre-unscrambler, the boards are fed onto a horizontally arranged screw roller conveyor, at which point they are already aligned with the zero line of the cross transfer system. The subsequent second unscrambler separates and transports the boards onto the chain cross conveyor in front of the control cabin, where they can be visually assessed by the operator and then transferred to the cross-cut station. The two-staged separation and the alignment to the zero line in that course, provides a good lumber flush line, allowing a faster charging of the boards onto the infeed system.
On the chain cross conveyor, the operator has the possibility of turning the boards for assessment, discharging unusable pieces downwards into the disposal area and removing slabs through cross-cutting. At the cross-cutting station, any length of slab can be cut off using a cross-cut saw on the zero line by moving the boards lengthwise on rollers that can be lifted. On the plant in Losheim, the cross-cut lengths 10 cm, 30 cm and 50 cm are predefined and can be started up automatically at the push of a button.
In the further process, manipulation time is gained by scanning the individual board twice: the thickness of the crosscut boards is scanned from above and below using optical sensors in the transverse pass and then automatically pre-aligned for the edging cut according to the contour determined before they go into the subsequent precision scan in the longitudinal pass – accelerated by way of lateral and top-engaging pressure rollers. Depending on the program specification or the operator’s choice, the boards can be aligned centrally, according to the ideal board axis or asymmetrically at the left or right wane.
An optical scanning system from Microtec is integrated into the line for linear scanning. Two cameras and four laser units scan the board on both sides. Some 800 scans per second and a width resolution of +/- 1 mm allow precise scanning of the board even at high feed rates. Pre-positioned pressure rollers and an upper pressure chain behind the scanning area enable the boards to be transported exactly lengthwise to the edging circular saw without changing their position. During the longitudinal transport, the scanning data is transmitted and the edger circular saws are positioned accordingly.
User-friendliness
Pascal Perings, who was the project manager at Hilo for this investment, was very satisfied not only with the performance of the plant but also with its operation: for an employee who has already worked on an edger, little training time was needed on the Optidrive unit. An aspect that is all the more important because there are no trained woodworking mechanics to be found and every employee in the company has to be trained for their jobs.
The plant operates at a high cycle rate in automatic mode. However, the operator can intervene from the enclosed control stand if necessary or adjust the settings. In addition to the relief for the operator in automatic mode, there are also clearly lower crosscutting losses during production.
Further conversion in summer
conversion phase. The edged boards will then run directly into the newly configured automatic sorting system, for which Springer Maschinenfabrik, has been commissioned.
The new grading will also include a Microtec wane scanner and a full trimmer. This then eliminates the bottleneck and the EWD edger can be run at its full capacity.
The rights of text and photos in this article belong to Holz-Zentralblatt
Pascal Perings, Hilo