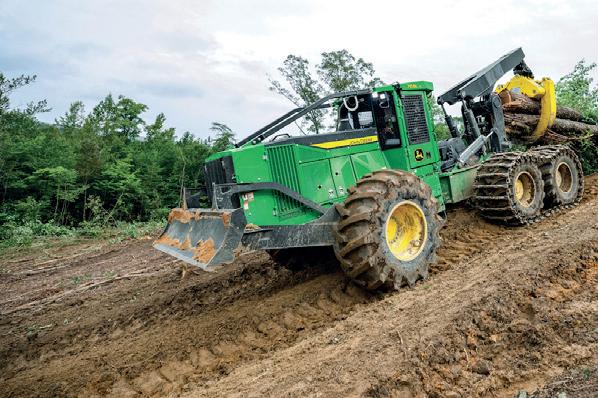
34 minute read
SKIDDERS
John Deere’s powerful new purpose-built 768L-II Bogie Skidder
John Deere recently introduced the new six-wheel 768L-II
Advertisement
Bogie Skidder, a true woodland warrior designed to conquer wet conditions and steep slope terrain. Incorporating the proven, durable features found on the John Deere L-II Skidder lineup, the new 768L-II maximizes productivity, performance, and comfort when carrying hefty loads over long distances in challenging conditions.
“Profitability and productivity are critical in the woods, and as loggers take to new areas for jobs, they need dependable machines that are built with these niche applications in mind,” said Matthew Flood, product marketing manager, John Deere. “With our new 768L-II Bogie Skidder, we’re delivering a purpose-built machine that navigates tough terrain, such as swamps or steep slopes. Providing distinct features, the John Deere bogie skidder helps loggers maximize their potential, regardless of the conditions.”
The 281-horsepower 768LII features heavy-duty bogie axles, which incorporate large components to maximize durability and stability for long axle and tire life. The heavy-duty axles are purpose-built for tough applications, effortlessly pulling heavy loads and maneuvering tough terrain. The smooth, stable operation results in reduced machine vibration, ultimately minimizing operator fatigue. Another key feature is the excellent tractive ability and floatation. When combined with the bogie axles, ground pressure is reduced, allowing the 768L-II to work in wet terrain not accessible with a four-wheel skidder. As a result, the harvesting window is extended, adding more working days to the calendar.
The new arch design provides the operator with an expansive rearward view of the grapple and work area, providing excellent visibility. Improving maneuverability, the long wheelbase and boom-arch envelope boost reach and lift capability for the boom and grapple, increasing dexterity in the woods. The tight turning radius enhances agility at the landing.
“The John Deere bogie skidder is hands down twice as good as a regular four-tire skidder. It’s just all-around better in my book for productivity and ground disturbance,” said Jason Dawson of Triple J Logging. “With the 768L-II, you can carry twice as much of a load, especially in wet conditions and on the steep terrain, without
Jason Dawson of Triple J Logging
tearing the ground up.”
The 768L-II retains the other customer-favorite features introduced on the L-II product lineup. Streamlined and redesigned electrical and hydraulic systems result in improved uptime and increase guarding and protection of key components. An increased
grapple squeeze force and twospeed winch further increase productivity, while articulation steering sensors improve the operator experience.
Highly regarded by customers, all L-Series II models feature a spacious cab, including ample storage space, configurable controls, and an effective HVAC system. Armrest-mounted electrohydraulic controls offer accessible, hand-finger operation of all machine functions, and joystick steering provides smooth control of steer, direction, and ground speed. The industryexclusive Continuously Variable Transmission (CVT) marries the efficiency of a direct-drive transmission with the smoothness of a hydrostatic drive. As a result, CVT provides more power to the ground by sensing the load, increasing torque and tractive effort as needed to maintain the desired speed.
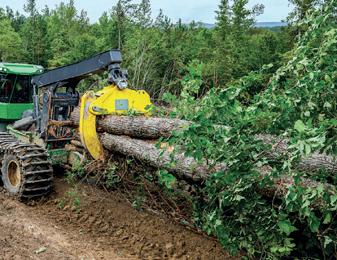
H-series skidders enjoy facelift
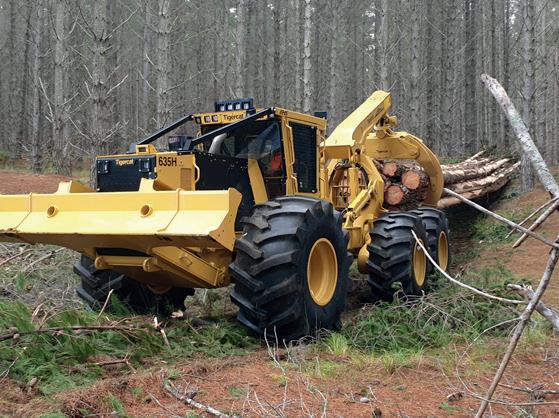
The 635H is built for extreme duty and super high production logging operations
Tigercat’s advanced, efficient and refined skidders just got a whole lot better
The Tigercat H-series skidders introduce a new, larger cab, while also improving serviceability, reliability, and efficiency. The new skidder line will see the release of the 620H, 630H, and 632H four-wheel skidders, as well as the 625H and 635H sixwheel skidders.
The newly designed cab on the H-series skidders is 20% larger than the previous E-series design. Window area has been increased to provide unmatched visibility on all sides. The rear windows have been lowered, and front lower windows have been added to provide a better line of sight to all wheels. The updated interior uses a mix of molded plastic panels and removable steel panels. The
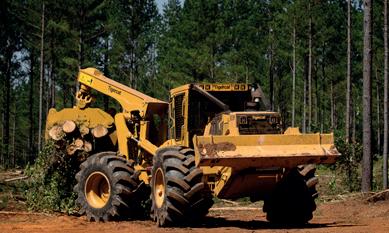
molded, easy to clean rubber floor mat has durable checkered aluminum plates at the high touch points.
The new and improved Turnaround system for H-series lets the operator rotate the seat 220°. “Effortless” pushbutton controls lock and unlock the seat in any position in the range, according to the manufacturer. The operator has full control of all machine functions including drive controls. The 220° seat rotation improves operator visibility, greatly reduces neck strain, and allows the operator to easily exit either side of the cab.
A durable, heavy duty air ride suspension seat with state-ofthe-art heating and cooling keeps the operator comfortable all day long. The reclining seat is fully adjustable with seat angle and seat extension adjustment. Tilt up adjustable armrests along with adjustable lumbar support all contribute to operator comfort. A secure five-point harness comes standard for improved safety.
A completely redesigned HVAC system provides greater cooling capacity and 50% more air vents for improved comfort. The larger intake filter keeps the cabin air clean. The fan speed control is now infinitely variable from zero to 100% and a new defrost option is available which cycles the A/C on and off automatically to keep the windows clear. A climate-controlled cup holder is connected to the system to heat or cool drinks.
Operator controls are located on the armrests and include many new features. Differential lock buttons are on the joystick and can engage front and rear separately. LED lights above the buttons illuminate when they are active. A cruise control button maintains the current engine speed allowing the operator to release the pedal. The grapple constant pressure button also turns on an LED indicator on the joystick alerting the operator that the constant pressure is activated.
Other features of the H-series cab include a tire pressure monitoring system, bright LED interior lights, a lunch box storage area, cell phone storage with charging port, and hooks for a
jacket and hardhat.
Horsepower has been increased on the 620H, 630H, 632H, and 635H models, and all H-series skidders feature load-sensing hydraulics with larger, more efficient valves. Hydraulic tank capacity has increased 20% for improved steep slope system performance, and includes improved level detection and more robust mounting. The 620H, 630H and 625H models have been equipped with larger arch, boom, and steer cylinders to better handle
large loads.
The new 635H swing boom skidder is the newest addition to the skidder line up. With a 210° rotation, the swing boom increases the working envelope of the skidder, which means the operator spends less time manoeuvring the machine. Tethering device set-ups are reduced due to the wider working range. Dual rotate motors and a large swing bearing make gathering and moving bunches effortless on steep slopes.
Engine enclosure doors have been reinforced to resist impacts and use T-style compression latches to keep them securely closed. The access doors are bolted on for easy replacement. Inside the engine compartment, an improved component layout locates all of the fuel filters on the left-hand side of the machine. A new high capacity crankcase ventilation filter is mounted on the right-hand side of the machine will all the oil filters. Front chassis hydraulic hose routing has been greatly simplified to eliminate leak points and improve serviceability.
All flat front chassis belly doors use a pivot bolt so they will swing to the side when service is needed. The angled belly door is keyed to prevent it from dropping when bolts are removed. Within the angle door is a small service cover which provides access to the engine oil, coolant, and hydraulic tank drain plugs.
When tilting the cab is necessary, new ‘quarter turn’ locking pins are used to lock the cab in the down position. To tilt the cab, simply loosen the locking plate bolts, slide the locking plate down, and turn the pins to the unlock position. Removing and installing the sweep bolts is easier with a new two-piece design. Fine adjustments can be made by loosening the additional sweep bolt. New keyed washers further simplify the assembly.
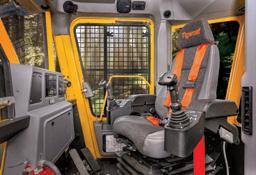
The H-series cab with 20% interior space and 19% more window area
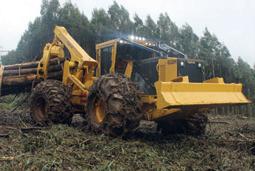
The 635H is the industry’s highest production four-wheel drive skidder
REVERSIBLE FANS FOR AUTOMATIC RADIATOR CLEANING | www.cleanfix.org
more Cooling more Power
more Productivity
less Downtime
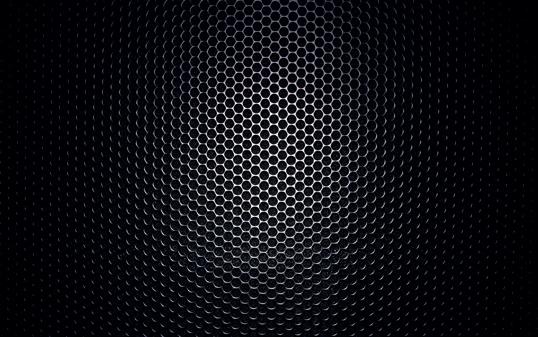
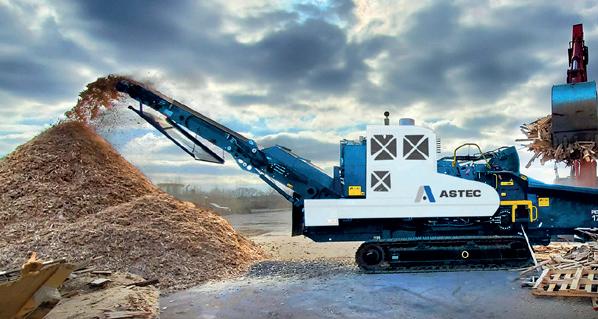
Shredders & Grinders
Size-reduction technology is looking more and more profitable as a secondary revenue stream or primary business
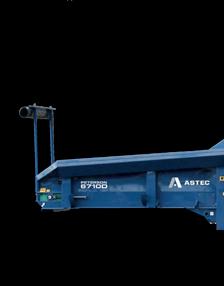
The argument goes that any forms of green product, particularly green and renewable energies, will be favoured as governments use increased stakes in enterprise to force the environment to the front of the business agenda.
This is likely to be a boon for forestry in general, but particularly for biomass production. And while high-level chippers may be the primary recipient of this new favour, all size-reduction technologies could potentially have an angle into new business.
Here, we present some of the leading products in this technology space that could turn forest waste into money for entrepreneurs.
Peterson, a brand of Astec Industries, is an industry leader producing a full line of grinders, disc and drum chippers, flail debarkers, and blower trucks. A history of innovation and reliable manufacturing has established a reputation for equipment of the highest quality. Peterson equipment is manufactured in Eugene, Oregon, where each machine is engineered and built to exacting standards.
KEY FEATURES
Peterson was the one of the first to develop portable horizontal grinders as wood waste recycling machines. This industry-changing innovation made sustainable forestry practices more attainable. Using horizontal grinders to process bark waste from in-field
1
4
2
3
1 Safety Guards
1 Safety Guards
Peterson horizontal grinders are built with safety in mind, including the projectile guard.
2 Sloped Feed Walls
Allow better visibility while loading and smoother feeding for more production in a wide variety of materials.
3 Feed Chain Conveyor
A robust feed chain conveyor efficiently feeds the rotor. A hydraulic drive motor synchronizes with the feed roll for near continuous feeding and massive throughput.
4 Adaptive Feed System
Monitors the grinding load and varies the speed of the feed system to keep the engine working at its optimal power curve.
It accelerates the feed when the engine load is light, slows when the load is high, and reverses feed when the load is excessive.
Peterson horizontal grinders are built with safety in mind, including the projectile guard. 5 Impact Cushion System Absorbs energy shocks and spikes to extend grinding system 2 Sloped Feed Walls component life and helps prevent catastrophic damage from
Allow better visibility while severe impact. loading and smoother feeding for more production 6 Rotor Placement in a wide variety of materials. Optimum rotor placement ensures positive feeding and reduces the potential of thrown material. Pinned or drum 3 Feed Chain Conveyor rotors are available.
A robust feed chain conveyor efficiently feeds the rotor. 7 Mobility Options
A hydraulic drive motor Astec horizontal grinders are available in wheeled, tracked, or stationary electric versions. Larger tracked grinders have synchronizes with the feed an optional tow dolly for easy transport, while the 1700D can roll for near continuous be towed with a dump truck. feeding and massive throughput. 8 Multiple Engine Options Available Depending on emission standards for your region, Astec offers both Tier II, Tier IV, and EU Stage V engine configurations.
4 Adaptive Feed System
Monitors the grinding load and varies the speed of the feed system to keep the engine working at its optimal power curve. It accelerates the feed when the engine load is light, slows when the load is high, and reverses feed when the load is excessive.
5 Impact Cushion System
Absorbs energy shocks and spikes to extend grinding system component life and helps prevent catastrophic damage from severe impact.
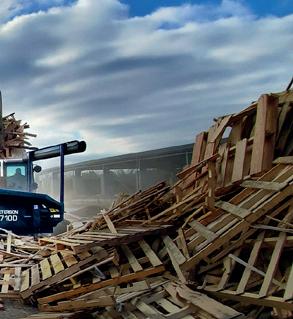
chipping into a value-added product means leaving less waste and site clean-up. Grinding slash into hog-fuel or nutrient-rich forest bedding can lessen logging impacts to an operation site. Reducing materials before it leaves the job site can increase payload and reduce truck traffic, fuel usage, and road erosion.
Peterson’s continued commitment to sustainability and innovation has developed specialized delivery and processing equipment that turns low-grade organic materials into high value products. The company’s strong foundation of innovations, one
5 8 9
11 13
Heavy duty and mobile, the 1710D Horizontal Grinder can readily reduce a wide range of materials
built upon the next, culminate into a premium product.
“Not only are they built to withstand the harsh conditions of forestry operations, but they also offer the lowest operating cost per tonne,” the company said.
Peterson’s three-stage grinding process starts with its patented upturn rotor, drawing material into the grinding chamber. The anvil is positioned for optimum sizing and the large grate area offers highproduction. The upturn process provides better material fracturing, and Peterson’s four-grate sizing system makes it easy to produce the size material customer demands.
This grate system offers unparalleled customization to tool the machine to fit output needs. Grates are removed through an easy-access door on the side wall. Combined with Peterson’s heavy-duty bits, and robust anvil, their horizontal grinders have an exceptional wear life and accurate product sizing.
All Peterson grinders feature an adaptive feed system. This system monitors the grinding load and varies the speed of the feed system to keep the engine working at the top of its power curve. A patented Impact Release System allows contaminants to be ejected from the grinding chamber to reduce the risk of catastrophic damage from ungrindable objects like rocks and metal, a system unique to Peterson.
13 Optional Cross Belt
Magnet
Powerful cross-belt magnets pull tramp metal off of the conveyor, producing cleaner, profitable material. Earn additional income from scrap metal!
14
10 12 15
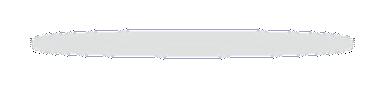
Absorbs energy shocks and spikes to extend grinding system component life and helps prevent catastrophic damage from
Rotor Placement
Optimum rotor placement ensures positive feeding and reduces the potential of thrown material. Pinned or drum
Mobility Options
Astec horizontal grinders are available in wheeled, tracked, or stationary electric versions. Larger tracked grinders have an optional tow dolly for easy transport, while the 1700D can be towed with a dump truck.
Multiple Engine Options Available 9 Telematics gives connectivity
New D-Model grinders feature Remote Monitoring
Analytics, including a wireless display for operators and offsite analytics.
10 Continuous Discharge Conveyor
One continuous discharge conveyor reduces materiel loss, increases uptime, and lowers maintenance.
11 Guard Rails
With safety in mind, guardrails are high-visibility yellow, reducing potential slip & fall hazards when servicing the machine.
12 IQAN Operating System
Fine-tune adjustments for maximum productivity.
13 Optional Cross Belt Magnet
Powerful cross-belt magnets pull tramp metal off of the conveyor, producing cleaner, profitable material. Earn additional income from scrap metal!
10 14 Optional Magnetic Headroll
Peterson grinders feature a magnetic headroll that allows for effective metal separation and high capacity production.
15 Optional Tracked Stacking Conveyor
Add an optional Peterson stacking conveyor to pile material even higher.
12
6 Rotor Placement 13
Optimum rotor placement ensures positive feeding and reduces the potential of thrown material. Pinned or drum rotors are available. 14
7 Mobility Options
Astec horizontal grinders are available in wheeled, 15 tracked, or stationary electric versions. Larger tracked grinders have an optional tow dolly for easy transport, while the 1700D can be towed with a dump truck.
8 Multiple Engine Options Available
Depending on emission standards for your region, Astec offers both Tier II, Tier IV, and EU Stage V engine configurations.
9 Telematics gives connectivity
New D-Model grinders feature Remote Monitoring Analytics, including a wireless display for operators and offsite analytics.
10 Continuous Discharge Conveyor
One continuous discharge conveyor reduces materiel loss, increases uptime, and lowers maintenance.
11 Guard Rails
With safety in mind, guardrails are high-visibility yellow, reducing potential slip & fall hazards when servicing the machine.
12 IQAN Operating System
Fine-tune adjustments for maximum productivity.
14 Optional Magnetic
Headroll
Peterson grinders feature a magnetic headroll that allows for effective metal separation and high capacity production.
15 Optional Tracked Stacking
Conveyor
Add an optional Peterson stacking conveyor to pile material even higher.
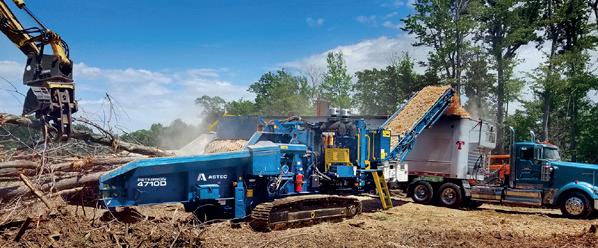
The Astec Industries Peterson 4710D Horizontal Grinder is a track mounted horizontal grinder designed for high-volume producers with very demanding end-product specification
DURABILITY & PERFORMANCE

3-STAGE GRINDING PROCESS
The machine uses an upturning rotor in combination with a down-force compression roll to grind the feed material in a three-stage process, resulting in more accurate and consistent finished products
1 Up Cutting Rotor
Opposing rotational forces create an aggressive shearing action. The upturn rotor draws material into the grinding chamber and minimizes bit wear.
Provides the first stage in material size reduction.
Available with pinned or drum rotors.
2 Anvil
Positioned for optimum sizing and production, the anvil provides the second stage in the sizing process.
3 Grate Area
The last step in the 3-stage sizing process, the large grate area results in high-production of a wide variety of materials and end products.
Peterson+ is a telematics system now available on all new Peterson grinders. It gives the owner and operator a live view of their equipment performance, and GPS location details. Loading operators can see common machine analytics right from their cab. Peterson+ includes a host of other features, including maintenance log, directions to the machine site, and historical machine data.
Optional features increase the grinders flexibility between jobs. Work lights, cold weather kits, magnetic cross belt conveyor. The company’s liquid injection system is a high-flow water option that’s great for mulch coloring and dust control, and an optional transportation dolly is available on many Peterson grinder models.
With an eye on innovation, Peterson has added several new models to the lineup.
1700 Series Horizontal Grinders
Peterson’s most significant addition to the of horizontal grinder lineup brings big power in a small package. This compact grinder has a 44 ft 1 in (1,344 cm) operating length but packs an impressive 455 hp (339 kW) Caterpillar C9.3B Tier IV engine and a large feed opening of 54 ft x 27 in (137 x 69 cm).
The 1700D Horizontal Grinder is available with wheels, while the 1710D Horizontal Grinder is a tracked model. The 1700D has a pintle hitch and can be transported between job sites with a dump truck. 4700D Horizontal Grinder
The most recent model release, the 4700D Horizontal Grinder, is designed for high-volume producers with very demanding end-product specifications. The 4700D is powered by a Tier IV Caterpillar C18 engine rated at 755 HP (563 kW).
2750D Horizontal Grinder
Peterson’s new 2750D Electric Horizontal Grinder is powered by a single 600 HP (450 kW) electric motor. An on-site electric machine may be the answer for grinding mill residuals to increasing profits since electric power costs are typically much lower than diesel fuel costs.
With a feed opening of 60¾ in x 32 in (154 cm x 81 cm) combined with Peterson’s high lift feed roll for an optional opening up to 44 in (112 cm) high, the 2750D can reduce a diverse range of raw materials.
While Peterson brought the industry-changing horizontal grinder to the marketplace to process wood waste from in-field chipping operations, sustained growth and a focus on customeroriented products continues to keep the manufacturer at the forefront of the market.
Equipment manufacturer Rawlings describes itself as a “proven leader” in size reduction technology that specializes in helping business owners with the design of custom wood-waste recovery systems for specific processing needs and budgets.
Rawlings states it can handle every aspect of configuring, building, installing, and supporting a complete materials processing system. Its electric stationary systems come in all shapes and sizes – indoor/outdoor; from simple stand-alone vertical hogs for saw and paper mills, to complete multi-dimensional systems.
“Add a wide variety of available options, and you’ve got the flexibility to customize the perfect wood waste recovery system,” the company stated.
Each system can be designed with work platform decks, choice of belt, chain or vibrating in-feed and out-feed conveyors, metal or magnet protection, product screening and separation all customizable for specific operations.
Markets for wood waste start with feedstock for engineered woods, landscape mulch, soil conditioner, animal bedding, compost additive, sewage sludge, and boiler fuel. All these end uses have similar processing requirements in that the wood waste has to be separated from other wastes, cleaned by removing contaminants and fasteners, and, in some cases, processed through grinding or chipping. The final use of the wood waste often determines how clean and consistent the feedstock must be (California Integrated Waste Management 2001).
“During our 40 years designing wood waste grinding systems we have found that most of our clients are looking to get the smallest end particle size on a single pass, onestage pass through the grinder,” Rawlings said. “We often suggest that this is not always the most economical option in the long run.
“Running the grinder and related equipment at full surge capacity results in higher consumption of spare parts and maintenance costs. And depending if you’re using electricity or diesel fuel these costs add up over time.”
During the preliminary design there are many factors that should be considered. Such factors include species of wood, moisture content, diameter and length of incoming wood waste, metal contamination and most importantly the required end product size.
For high volume high capacity wood handling operations that typically receive a large variety of contaminated materials such as railroad ties, pallets, construction, demolition and hurricane waste, Rawlings recommends wood waste systems to incorporate a combination of equipment. This could include both horizontal and vertical feed grinders.
Horizontal grinders or slow speed grinders are often utilized as the primary grinder while the vertical grinders are used to produce a smaller more consistent particle size. Using metal protection, product screening and separation allows the customer to protect their investment while producing a high-quality consistent end product.
If the wood handling system is designed to receive a steady stream of bark or sawmill waste a vertical feed hog is the preferred option. Typically in this scenario most of the incoming material is preprocessed further upstream and it already sized to be processed through this type of grinder.
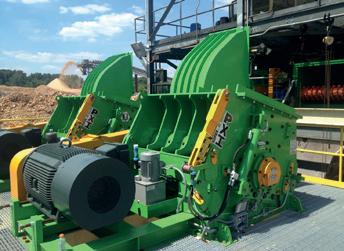
Rawlings Vertical Grinders
Each unit is equipped with the Rawlings Super Hi-Inertia Solid Steel Rotor. With the increased inertia of the solid steel rotor our machine runs at lower RPM’S than many competitors, resulting in overall savings of electricity and maintenance costs.
The Rawlings wood hog is recognized in the industry as a ‘Green monster hog’ and provides the crushing and shearing power needed to handle really tough jobs like green waste, cypress, redwood, cedar, black spruce, poplar and a wide range of other stringy and fibrous material. The machines are also tolerant of contaminants, rocks and metal without catastrophic maintenance costs if metal enters the grinding chamber.
“For over 40 years, we’ve assisted our customers in utilizing renewable resources while reducing and recycling a wide variety of wood waste into valuable wood fiber products,” Rawlings stated. “We offer a complete line up of seven different sizes of both vertical and horizontal hogs to fit any application.”
R
SALES PARTS SERVICE
COMPLETE LINE-UP OF THE MOST PRODUCTIVE AND COST EFFICIENT WOOD GRINDERS
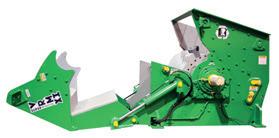
VERTICAL & HORIZONTAL MODELS AVAILABLE
Tub Grinder v Horizontal Grinder
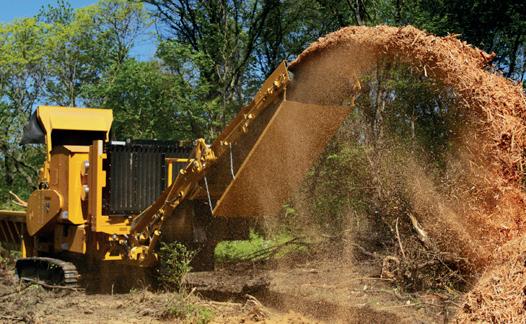
Built for land-clearing and pipeline right-of-way operations, the HG6800TX horizontal grinder offers a high-horsepower engine on a tracked machine with a compact design. Featuring 950 hp (708 kW) in a 92,000 lb (41,730.5 kg) class, and an infeed design designed specifically for feeding larger materials, the new grinder is built to power through tough materials with less operator interaction
Industry leading supplier examines the all-important question of what’s the right grinder for a given operation
When it comes time to add or replace a grinder in your equipment fleet, one of the first questions an operator should consider is: “Do I need a tub grinder or a horizontal grinder?”
It is important to compare the two grinder designs and features for yourself and then determine which is right for a given operation. Here is a brief overview of things to consider during the buying process.
Safety considerations
According to David Steege, recycling account manager at RDO Equipment, properly trained and experienced operators know that if they are working with material that may contain non-organic contaminants (i.e. metal), they need to spend a bit of time sorting and paying close attention to every load they feed into the grinder. This step will help mitigate the risk of thrown objects.
“With tub grinders, features like the patented thrown object restrain system (TORS) found on Vermeer models, can help reduce the amount and distance of thrown objects,” explained Steeg.
“The TORS system has a deflector plate positioned across from the hammer mill to help redirect loose material back inside the tub. Making sure the tub grinder’s bowl is filled to proper capacity – per your operator’s manual – also can help reduce the risk of the grinder throwing material. Since tub grinders use gravity to feed the hammer mill, a full tub can provide an additional layer of protection to help keep material where it belongs.”
To help mitigate the risk of metal contaminants cycling through with organic material, Vermeer grinders (tub and horizontal) can be outfitted with the optional Vermeer Damage Defense System. When a metal contaminant is detected during operations, the Damage Defense system will alert the grinder control and automatically initiate the shutdown process.
Space available
Some in the industry may have heard that tub grinders need a lot more room to operate. This is due to the distance thrown objects can travel, but Steege explained that there is more you need to consider on the topic of working areas.
“Tub grinders will often be used to process a lot of different types of wood waste, and possibly in a setting where the incoming material may not be the cleanest,” he said. “Tubs can handle that type of material, but it’s always advisable to have more open area surrounding the machine. Otherwise, the operational space needs for horizontal and tub grinders are similar.”
Material sizing
Next on your list of considerations is which machine is going to size your material more consistently. There are several factors to consider when thinking about this area beyond the basic tub or horizontal grinder design.
“Consistency of material sizing can be more related to the quality of the machine and how all of the moving parts work together than whether it’s a tub or horizontal grinder,” said Steege. “The Vermeer duplex drum system and screen configuration optimize the grinders’ performance to produce a quality end product.”
Steege went on to say that taking a look at the size of the incoming material is a more important consideration.
“When I’m in the field talking to contractors and facility managers about grinders, one of the first things I ask them about is the type and size of material they are going to be grinding. Horizontal grinders are more efficient than tubs at handling longer material because less cutting is required before it can be fed through the machine.
“So, if they are going to be running long branches and tree trunks, a horizontal grinder will
likely be their more efficient machine. However, if they are running a bunch of stumps and odd sizes of material, they are going to want a tub grinder.”
For loose green waste, Steege said either grinder is fine, but tub grinders may be more efficient for their operation.
“With horizontal grinders, the material is being force-fed into the drum, but tubs use gravity, so there are fewer moving parts involved with the process.”
Transportability
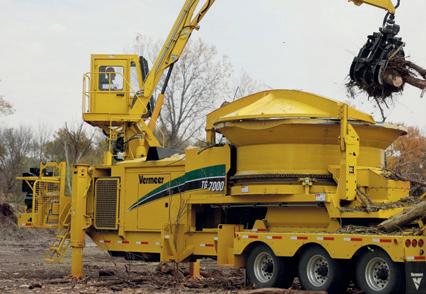
Depending on the line of work, hauling, or only moving a grinder around a facility is another factor to consider. If working on a big job or frequently needing to reposition the grinder, business owners are going to want to look at a grinder with tracks. If that’s a need, horizontal grinders like the Vermeer HG6000TX and HG6800TX are good options to consider.
If moving from one site to another, it is important to review any DOT size and weight restrictions in the area to see which unit will be more efficient to haul.
“The sides on Vermeer tub grinders fold in for transporting, which gives them a similar travel width as a comparably-sized horizontal grinder,” Steege explained. “However, tub grinders without a loader are considerably lighter than that same horizontal grinder, which can help reduce transportation expenses.”

The TG7000 packs innovation and power for large land clearing projects and organic/wood waste processing applications. It processes through wood waste quickly with the exclusive Vermeer duplex drum to minimize maintenance, a PT tech wet clutch with microprocessor to automatically limit torque when necessary, and a patented cutting system outfitted with 10 hammers and 20 double-bolt cutter blocks.
The TG7000
Preference
As can be seen, both tub grinders and horizontal grinders have helpful qualities to offer. So, when it’s time to add or replace a grinder in a fleet, it’s important to think about the needs and what type of grinder will deliver the best results for an organization.
If a business needs a little help along the way, recycling and forestry specialists can help weigh the pros and cons of each grinder type.
ProGrind 5200 - T - The special double-bolt hammer tips provide more durability and grinding ease, assuring high production rates, less wear on the hammermill and easy maintenance. It’s been called the most powerful, easy to use tub grinder in the industry, according to the manufacturer
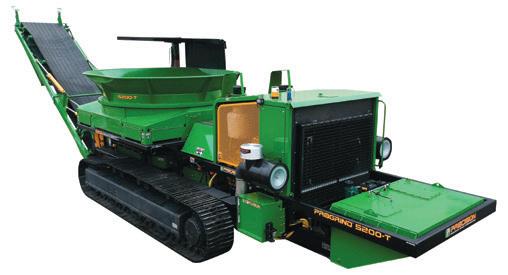
“Whatever side of the fence you’re on these days, be sure to have Precision Husky with you,” the manufacturer states with just a touch of bias.
“It’s one of those jobsite nobrainers; like wearing a hardhat. Why? Because Precision Husky has evolved into one of the world’s top providers of tough and tested forestry equipment. We keep getting better because we never stop to rest on our laurels. Our equipment is designed with your paycheck in mind and built to work as hard as you do.
“Today, our fuel-efficient, low maintenance and low noise grinders are being used all over the world to manufacture mulch, compost and boiler fuel and to clear and clean jobsites.
“In this day and age, at least everybody can agree on high-speed productivity. Our industry leading horizontal and tub grinders will make you wonder how you ever got along without them.”
The Precision Husky H-3045 is one of three horizontal grinders from the ProGrind range ProGrind Horizontal Grinders
For working with long limbs, Pecision’s high-speed ProGrind horizontal grinders are difficult to beat. There are three models (H-3045, H-3060 and H-4060) to choose from, each with a rugged diesel engine and offering from 520 hp up to 1,050 hp, depending on requirements.
The dual cutting surfaces at various depths eliminate frustrating jams. The 3045 offers a 30 in cutting diameter and a 45 in infeed width, the 3060 has a 30 in cutting diameter and a 60 in infeed width, and the 4060 has a 40-inch cutting diameter and a wide 60 in infeed width.
ProGrind horizontal grinders are built with a down cut design, which allows operators to switch out the hammermill for a two or four-knife chipper drum.
“Many of our customers find this feature a particular cost saver,” Precision said. “No need to buy a chipper when your grinder can do the job.”
ProGrind Tub Grinders
Precision Husky also offers six popular models of ProGrind tub grinders, each built with ease of operation, cost and productivity in mind.
“All of our tub grinders, from our PG 900 base model to our powerhouse PG 5200, offer industry-leading user-friendly controls, clutch protection and different hammer options for grinding versatility,” the manufacturer stated. “The tub tilts 90° for easy access to the hammermill, screens and lower auger area.
Feedback on the newest offering, the ProGrind 5200, has been “fantastic”. It contains one of the most aggressive hammermills in the industry. It can cut through mountains of green waste at production rates of over 100 t/h.
The special double-bolt hammer tips provide more durability and grinding ease, assuring high production rates, less wear on the hammermill and easy maintenance. It’s been called the most powerful, easy to use tub grinder in the industry, according to the manufacturer.
The 5200 also is a technological accomplishment. It is operated by
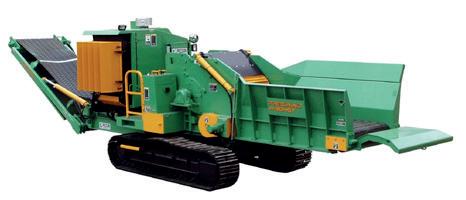
Precision Husky
a dust and water-resistant, shockmounted control box with a Sauer Plus 1 system, CAN+ radio remote controls and a smart display panel. The enclosed, wet hydraulic clutch is engaged from the control panel with fault indicators using a push button microprocessor.
Many customers have chosen the knuckleboom-loader option, complete with air-conditioned cab (standard) and state-of-the-art joystick.
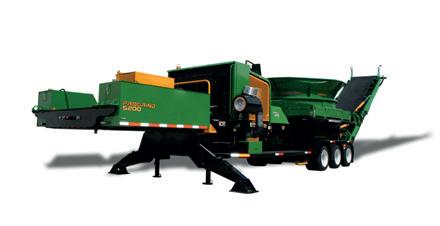
Profile
More than 100 experienced, highly dedicated and motivated employees, many of whom are former loggers and wood processors, work from Precision’s 165,000 sq.ft manufacturing facility Dual cutting surfaces at various depths help the H-3060 eliminate frustrating jams
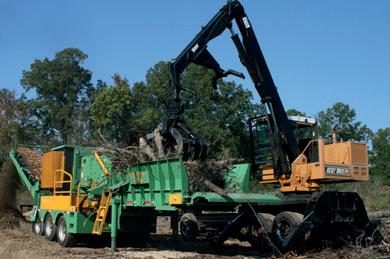
ProGrind 5200

ProGrind horizontal grinders are built with a down cut design in Leeds, Alabama. Inside the plant, the manufacture is constantly working to innovate and improve.
“Precision Husky is a clear example of the American Dream come true,” the company states. “Our President Scott Smith is a second-generation innovator like his father, company founder and CEO Bob Smith. Together they have seen Precision go from a small regional provider to a worldwide leader in timber processing technology, with customers in 120 countries.”
BA 916 D and BA 926 D in comparison
JENZ launched two new machines on the biomass processor market last year. The BA 916 green waste specialist and the flexible multi-talent BA 926 are part of the new shredder generation.
But how exactly do the machines differ and which shredder actually achieves which end product best? We compare the two newcomers in detail.
BA 916 D The garden waste specialist BA 926 D The flexible one
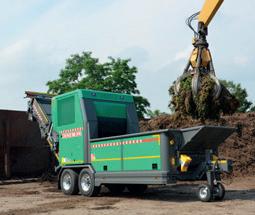
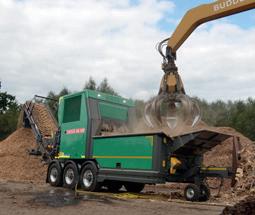
Chassis
• Extreme mobility thanks to 2-axle chassis and low total weight of less than 19 t • The total train length of less than 18.75 m allows transport by 3-axle truck with simultaneous use of a wheel loader. • Standard underrun protection and hydraulic propulsion drive • Hydraulic support winch as standard for quick coupling and uncoupling
Draw-in
• Free loading length of 4.40 m, extension to 5m is possible • Large intake opening of 900 mm • To avoid idle time: Speed function catapults bulky material directly under the draw-in roller • New hydraulic system: significantly increased cooling power and more aggressive draw-in behaviour
Rotor
• Choice of freely-swinging or fixed tools for optimum use depending on the material or desired end product • Two speed ranges: Eco and Power Eco (960 rpm): sufficient for most applications Power (1100 rpm): for even finer fragmentation
Chassis
• Quiet driving comfort and maximum stability thanks to heavy
3-axle chassis
• Standard underrun protection and hydraulic propulsion drive • Hydraulic support winch as standard for fast coupling and uncoupling operations
Draw-in
• Free loading length of 4.25 m, extension to 5m is possible • Large intake opening of 900 mm • Increased draw-in opening + aggressive high-speed intake = remarkable increase in throughput • Faster material feed due to more force and electrically-adjustable pre-tensioning pressure • Repositioning of the lower feed roller: more control when feeding logs and roots. Result: improved wood chip quality and additional machine protection
Rotor
• Choice of freely-swinging or fixed tools for optimum use depending on the material or desired end product. • Four working speeds thanks to the proven TwinGear drive system (400 to 1000 rpm) · Fast (hare) Eco and Power respectively · Slow (turtle) Eco and Power respectively
Maintenance
• Ergonomic maintenance access in standing position • Professional tool system as standard: - swivelling toolbox - incl. compressed air connection and working light - direct access to tools and spare parts • Screen changeover in under 10 minutes - by only one person - two-piece screen basket set (transport of additional screen basket set possible)
Outfeed
• Folding outfeed belt with discharge height of 4400 mm • Side-swivelling discharge conveyor (operation at the touch of a button) • Magnetic roller optional: for the selection of smaller iron parts
Control system
Innovative easy2 controller
• Smartphone-like operation via easy2TOUCH display • Additional easy2HOTKEY-Box key control panel for fast machine operation • Extended diagnostic options
Operator Info System
• New easy2CONNECT radio remote control - control and monitoring of all functions from the loading vehicle (integrated display with status indication) - loading and stowing directly at the machine - additional 12V charging cradle on the charging vehicle • LED status flashing lights on the engine housing roof signal the machine status to the operator from a distance
Unique assistance systems
• Set-up / dismantling assistant • GFA draw-in control system • Mode selecting system - factory-preset chipping modes for quick changeover when changing material - up to three programmes
Maintenance
• Ergonomic maintenance access with additional handles and steps • Swivelling discharge chute provides plenty of space for maintenance work on the shredding system • Screen changeover in under 10 minutes - by only one person - optional screen basket holder at the rear for additional two-piece screen basket set
The green waste specialist BA 916 presents itself as perfectly adapted to the operator with a more aggressive draw-in behaviour at the same time. The BA 926 is based on well-founded chipper know-how and, thanks to the unique TwinGear system, it can be used as a shredder or chipper.
Dominik Meden, Jenz
Outfeed
• Large screening area ensures unhindered material flow • Leakage belt as standard • Even more screening surface: optional installation of a screening floor with screening plates (recommended when processing woody biomass) • Hydraulically-adjustable over-belt magnet - height-adjustable from 150 mm (via easy2 control) - can be moved out of the material flow into a parking position
Control system
Innovative easy2 controller
• Smartphone-like operation via easy2TOUCH display • Additional easy2HOTKEY-Box keypad control panel for fast machine operation • Extended diagnostic options
Operator Info System
• New easy2CONNECT radio remote control - control and monitoring of all functions from the loading vehicle (integrated display with status indication) - loading and stowing directly at the machine - additional 12V charging cradle on the charging vehicle • LED status flashing lights on the engine housing roof signal the
machine status to the operator from a distance
Unique assistance systems
• GFA assistance system for controlling draw-in speed • Mode-Selecting system - factory pre-set chipping modes for quick changeover when changing material - uncomplicated changeover between chipping and shredding mode
Advantages:
• Professional tool system • unique driver assistance systems • ergonomic maintenance access Advantages:
• TwinGear System (enables chipping and shredding) • larger engine with 625 hp available (BA 926 D Wotan) • enlargement of the possible screen surface due to additional screen floor