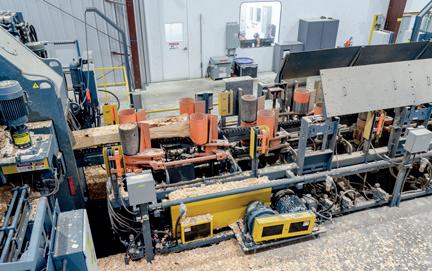
2 minute read
BID GROUP
BID Group’s SmartTool revolutionizes cant positioning
Optimal cant positioning can significantly increase production performance and profitability
Advertisement
During the primary breakdown, cant positioning is critical. The optimal position of the cant enables the execution of the optimizer solutions and ensures the best realization.
Occasionally, the mechanical components are unable to perform the required cant positioning. The challenge is to identify the causes quickly before they impact product quality or cause production problems.
Often, cant positioning problems are difficult to identify and are due to poor mechanical alignment, broken parts or components, incorrect settings or poor calibration.
The Primary Breakdown SmartTool, developed by BID Group’s team, is a software application that reveals unsuspected cant positioning problems in real time. This SmartTool empowers operators to intervene promptly before errors or defects impact quality or operations.
The main function of the Primary Breakdown SmartTool is to monitor cants and perform automatic adjustments to correct positioning due to visible or non-visible causes.
This closed loop system monitors and adjusts the face realization on sideboards and dimension offsets of all cutting tools, while dimension variation, taper along the length, skewed opening face, and bevel (nonparallel cut) are monitored. It also triggers an alert when a cutting tool error is identified.
Unique and revolutionary closed loop system
BID Group’s closed loop system is unique on the market. It is integrated directly in existing Comact optimizers so there is no need for third-party software, which makes technical support easier. Another advantage is that a PLC is not required for the installation.
Compared to other solutions on the market, the distinctive aspect of the Primary Breakdown SmartTool is that it uses scanner data (which provides the real and complete shape of the log) for the closed loop system. Therefore, operators obtain unsurpassed accuracy because the system uses the real faces which are compared to the theoretical faces to find the offset based on the real shape of the log (not simply a diameter measurement).
The closed loop system was developed based on BID Group’s vast primary breakdown experience. The system is now mature and has proven its effectiveness in the field.
In addition to quality control algorithms, the Primary Breakdown SmartTool has protective features to ensure constant precision and true size measurement. For example, if the dirt detected on the scanner could potentially affect dimension measurement, an alarm is triggered, and the closed loop system is turned off temporarily.
Dashboard, reports, and alerts for easy monitoring and analysis
A dashboard provides an overview of the primary breakdown operation status and a report can be generated for all defects monitored.
The configuration of alerts is done easily in the optimization software. In addition to the basic alert definition, operators can customize the alert message and include tips for troubleshooting or possible solutions. They can also define multi-conditions to avoid false alerts when the scanner is dirty.
Primary breakdown SmartTool and real sawline incidents
The Primary Breakdown SmartTool is installed on numerous sawlines in America and has proven to be indispensable to identify poor mechanical alignment, broken parts or components, and incorrect settings.
In one case, mechanical alignment was the cause of an unknown sawline problem. In fact,