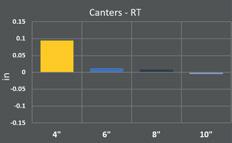
16 minute read
SETRA
Real-time display of the left twin thickness offset in the dashboard.
Real-time display of the canter’s thickness offsets in the dashboard.
Advertisement
one of the OLI cylinders had an offset of 0.400’’. Therefore, the cant positioning was not accurate, and this had a direct impact on the production value for one month. The mechanical alignment problem was identified once the Primary Breakdown SmartTool was installed. After fixing the error, the cant positioning resumed to an acceptable 0.010’’ automatic infeed offset.
In another incident, during production an OLI saw guide was damaged by a log. This caused the bandsaw to cut the wood two hundred thousandths off the dimension target, so it had a direct impact on the production quality. The problem was identified by the Primary Breakdown SmartTool and displayed in the dashboard, but it was not noticed by the operator. Fortunately, an alarm was triggered automatically, and the operator became aware of the situation.
In another sawline event, during the canter cutting tool cylinder calibration, the minimum cylinder position setting was defined at 2 in’ in the PLC and 1.9 in’ in the optimizer. This error caused the 4 in cants to be cut one hundred thousandth bigger. Since this pattern was not common, the problem was difficult to spot and lasted several months. It was only identified when the Primary Breakdown SmartTool was installed. The client was skeptical at first, but after investigation he recognized the facts and corrected the setting.
SmartTools: BID Group’s vision of operational intelligence and quality control
BID Group has created a complete suite of SmartTools with you in mind.
“Our goal is to raise sawmill operational intelligence and quality control to the next level based on the use of existing equipment, data, and cutting-edge technology,” the manufacturer said.
BID Group’s objective is to meet the client’s current and future needs “in an outstanding manner” with its brand portfolio and offer a return on investment unparalleled by competition. All of this is supported by BID Group’s renowned 24/7 service.
Setra makes major investment in Bergslagen
Setra is expanding drying capacity at Heby and Hasselfors – a decision taken by the Board of the wood products company at its latest meeting. “The investment is part of the development strategy for Setra in Bergslagen,” explains Setra’s CEO Katarina Levin.
The investment in both highcapacity drying kilns totals SEK 100 million.
“The new drying kilns will enable us to improve value optimisation and boost efficiency, which will strengthen Setra’s competitiveness,” says Jonas Fintling, Mill Manager Setra Hasselfors.
Setra Heby’s Mill Manager Jan-Erik Vik agrees, adding that the investment will also improve the work environment in Heby, as it will mean replacing some of the older equipment.
The increase in drying capacity at the sawmills in Heby and Hasselfors is an important element in the ongoing development of Setra’s operations in Bergslagen. Earlier this year, the decision was taken to invest in a new saw line in Skinnskatteberg, and last year a new rip saw was installed at the sawmill in Nyby.
“Setra is investing heavily in greater refinement of wood at resource-efficient production units in the Bergslagen area. This is positive from a sustainability perspective, as it helps to lower the climate footprint of our production and to ensure that we manufacture greener and more climate-smart products,” says Katarina Levin.
Examples of investments include CLT and components at Setra’s new factory in Långshyttan, planed construction timber from the new trimming and planing plant in Hasselfors and new x-ray technology in Kastet, Nyby and Skinnskatteberg. In total, Setra has invested more than SEK 1 billion in Bergslagen over the past four years.
Another example of green investment is the company Pyrocell, which Setra owns jointly with Preem. Pyrocell manufactures bio-oil from sawdust. The bio-oil is then used as a renewable raw material at Preem’s refinery in Lysekil, where it is mixed with petrol and diesel. Pyrocell’s facility is integrated with Setra Kastet in Gävle. Together, Setra and Preem have invested over SEK 400 million in this exciting venture.
Katarina Levin Setra’s CEO Jonas Fintling, Mill Manager Setra Hasselfors
Jan-Erik Vik Mill Manager, Setra Heby’s
Astec Peterson Equipment Leads in Biomass Energy Efforts
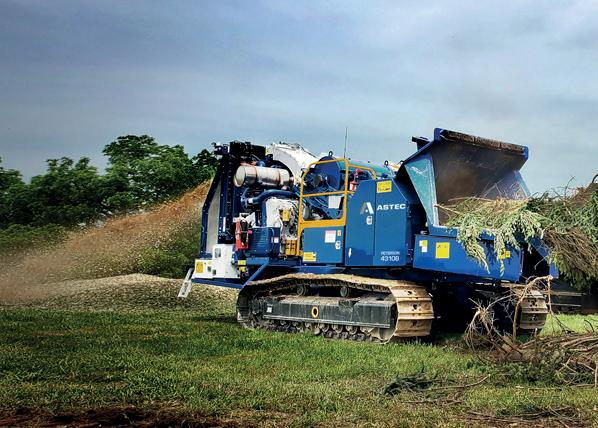
Equipment manufacturer Astec rebranded its Oregonbased forestry brand Peterson Pacific Corp., along with its many other subsidiary brands. Now united as Astec, Peterson forestry products will continue to be a priority for the company as the need for innovative energy solutions soar.
Energy challenges are increasingly more prevalent with the shortage of common fuels such as natural gas looming. As a result, many markets are looking for alternative fuels to better serve the energy industry. What was once a developing sector within the forest industry, biomass production has gained traction as a necessary and valuable clean energy solution and an alternative to coal which emits higher fossil fuels.
Astec forestry products, including horizontal grinders and chippers, have played an essential role in biomass production for over 40 years. Approximately 56% of Astec customers are currently using their Astec Peterson products
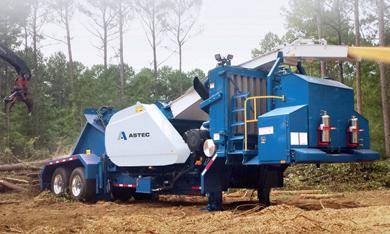
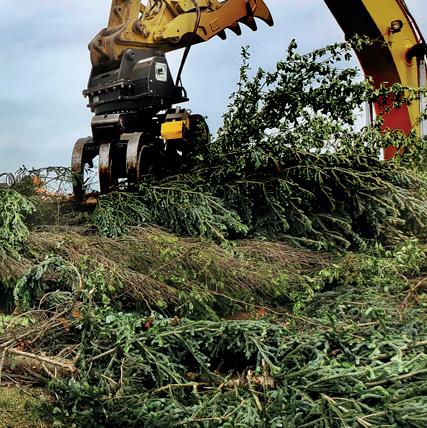
Astec-Peterson-4310BDrum-Chipper
to create biomass for various markets, and biomass production is expected to continue to increase in popularity as a more carbonneutral energy solution.
Biomass Equipment
In one of the beginning steps of biomass production, Astec horizontal grinders and drum chippers are highly effective for processing woody materials into biofuel or metallurgical chips to be hauled or conveyed to biomass facilities to be converted into energy.
There is a variety of materials that can be used in this process, including forest debris, scrap lumber, agriculture waste and more. This diverse source of fuel allows for not only biomass creation but also the recycling of otherwise wasted material.
The industry-leading and innovative horizontal grinders by Astec are utilized for many forestry and recycling applications, including biomass. Offered in five models of different sizes and capacities, the Astec Peterson horizontal grinders are designed to operate with the highest production rates and the lowest cost per ton.
Featuring many advantages for biomass producers, the unique three-stage grinding process uses an upturning rotor with a downforce compression roll to grind the feed material, delivering accurate fracturing and a more consistent product.
Another essential feature is
Astec-Peterson 4310B
the impact release system and cushion technology, unique to Astec Peterson equipment. These features help prevent damage to the machine when hazardous material enters the feed. The impact release system technology is a vital cost and time-saving feature, allowing for non-stop grinding and decreased downtime.
For customers looking for a stationary electric solution, Astec offers electric versions of horizontal grinders that cost less to operate and produce less noise. The electric grinders have unsurpassed uptime and burn clean energy. Without sacrificing power, electric grinders are equipped with crusher-duty motors ranging from 400 to 1,300 horsepower.

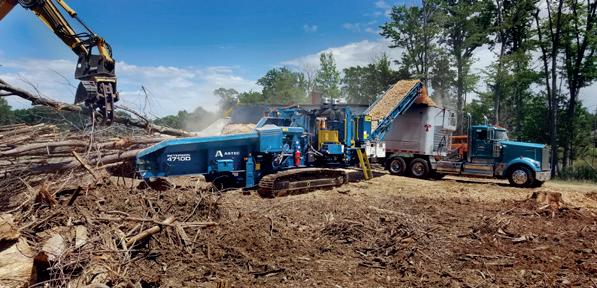
Astec-Peterson-4710D-Horizontal-Grinder
Drum chippers, such as the Peterson 4300B or 4310B, also have their own specific benefits for biomass. These highly mobile machines are available in end-load or top-load spots for loading trailers. In addition, a built-in chip accelerator packs wood chips tightly, ensuring maximum load capacity for increased efficiency.
Whether utilizing a chipper or grinder for biomass applications, an equally important consideration is material screening. Precise sizing is critical to producers because inconsistent material could jam the conveyor at a biomass plant. Screening systems such as a trommel screen are essential to removing un-merchantable products and classifying materials into accurate and sellable products.
Both horizontal grinders and drum chippers provide a top-of-theline operator experience, including wireless remote-control operation, IQAN control touch screen panels and powerful Caterpillar engines. Safety is also a priority for Astec; all equipment is designed for high visibility and maximum safety.
Many grinders and chippers by Astec can also be optionally equipped with Peterson+ remote technology that allows producers A Sustainable Future
The world is headed in a more sustainable direction as energy sources are being diversified to reduce the depletion of natural resources and offer more environmentally-friendly solutions. Astec forestry equipment is an essential partner in advancing the biomass markets globally as a clean energy solution as the demand for energy surges.
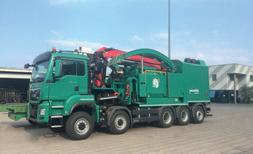
PTH 1400/1000 chipper ready for delivery – driven by CATERPILLAR C27, 12 cylinder, 1050 Hp engine. to monitor and address any machine issues in real-time. This feature connects with Astec customer support personnel for fast and easy machine assessments. Peterson+ machines can also be monitored remotely on internet-connected smartphones and tablets.
Often used in tandem with grinders and chippers are stacking conveyors. Designed for efficient material handling, stacking conveyors are used to pile wood chips or other biomass products to store the material in stockpiles or convey the material to processing plants. Astec Telestack conveyors can increase the bottom line for producers by eliminating the need for double material handling with traditional wheel loaders.
The chipper has been mounted on a MAN TGS 50.110 truck with 5 axles and is equipped with a Palfinger Epsilon Q130LD104 crane It is the first 1050 Hp CAT engine that meets Stage V emission limits.
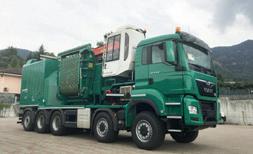
Even after half a century, industry leader Precision Husky never stops innovating its line-up of whole tree chippers, flail debarkers and knuckleboom loaders.
“Most of us came up in the logging industry and we know what it takes to win at this game. Customers all over the world recognize this commitment in the equipment we sell,” Smith said.
The latest achievements in Precision’s quest for forest industry perfection are accomplished with the remarkable design experience see production from the top or at insertion in real time and adjust accordingly. That’s like having an extra man in the crew. Complete system diagnostics come at the touch of a button, making trouble shooting simple when it used to take hours of downtime.
The new 2366 chipper brings 25% more anvil control to the table to prevent slapping and turning. This results in smoother slicing and more uniform chips, with less feed speed of up to 200-plus linear ft (61 m)/minute. An operator can generate over 100 t/h of clean chips.
The 2600-4 is also highly flexible. Because it allows for multiple individual solutions, it consistently receives the highest efficiency rates in the world. It
The new 2366 chipper brings 25% more anvil control
Scott Smith, Precision Husky
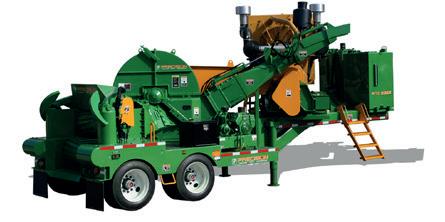
and application of ever-changing technology in the digital age.
From the top down, the Precision line is better engineered, built heavier, smarter and stronger for more fruitful logging and less costly downtime than previously.
“Precision is more than our name. It’s our number one goal.”
Precision Husky did not invent the whole tree chipper but it does make one of the best chippers available today as the more than 5,000 crews that use Precision products every day and have access to an unbeatable parts inventory and service technicians would likely attest.
The latest generation of Precision-built chipper pushes the envelope of technology to include a 66 in, five-knife option, which allows the chipper disc to operate at a slower rate. This not only saves wear and tear, it produces the most valuable chip quality available. Year after year, Precision chippers, operating with the 2600-4 flail debarker gives operators the highest production, lowest bark content and cost per tonne in the industry.
Plus, through messagebased CAN bus platform with its easy to use three wire system, a remote operator can monitor infeed through the HD colour control panel. The operator can horsepower.
The unit comes with a fully adjustable hydraulic system, which provides limitless control of feed rate. The patented PT Tech HPTO Hydraulic Power Take-Off is a totally enclosed wet hydraulic clutch that requires no adjustment through its wear life. During a torque spike, the clutch will act as a torque limiter by slipping to absorb the shock load. A microprocessor controller provides remote operation.
The industry-leading XL-175 knuckleboom loader comes standard in the 2366 Precision chipper. They are professionally engineered to be highly responsive and balanced with a smooth, powerful swing. These workhorse loaders have central hydraulic pressure checks and are the largest available with super heavy-duty sub frames.
“With its 3-axle spring suspension, our Precison chippers are tough to beat,” Smith said. “Choose the engine strength that suits your operation – up to 1,200 hp. We also offer a popular new radio remote controlled trackdriven chipper that goes where the big rigs can’t and are favoured by many of our international recycling operations.
The new FD 2600-4 debarker can easily process logs from 3-26 in (76-660 mm) in diameter with a can operate along with our mobile chipper or as a stand-alone debarker.
Bark and limbs are removed in enclosed housing, protecting the system from damage. The 2600-4 flail removes waste with an oversized hydraulic pusher, keeping the chamber clean.
Precision Whole Tree Chippers
Capabilities
All four sizes of Precision Whole Tree Chippers have rugged frame construction, over-sized stabilizers, air compressors, trash separators and more powerful fans that pack more chips per van. Power options range from 400 to 1050 horsepower [298 to 783 kw]. Because Precision Whole Tree Chippers are built stronger, have more standard features, with a reputation of trouble-free service, it is the choice of experienced operators and owners.
The optional Husky Loader, manufactured by Precision Husky in the same plant as the Whole Tree Chippers, the Husky XL-175 is standard on the Model 1858 and 2366. The larger XL-245 loader is included for the model 2675 and 3084 Whole Tree Chippers. Husky Knuckle-Boom loaders are engineered to be highly responsive with a smooth powerful swing and perfect balance. Routine service is fast with an easy access design, like centralized hydraulic pressure checks and turntable bearing greasing from the operator’s cab. Husky booms are the largest available with super heavy-duty sub frames.
Performance
Precision is one of the best known chippers in the world. The Precision chipper design allows 25% more anvil contact, preventing wood slapping and turning. This produces a smoother slicing acti on ensuring uniform sized chips while using less horsepower. Knives are positioned in the disc in such a way as to allow 10 to 15% more roundwood capacity than others the same size. Our discs are made from high quality steel and stress relieved prior to machining and all bearings are heavy-duty double spherical rollers. For ease of maintenance, wear points are protected by easily removed and replaceable components.
Options
End Loading Discharge Top Loading Discharge Bed Infeed Chain Conveyor Knuckleboom Loader Trailer or Track Mount Radio Remote Control
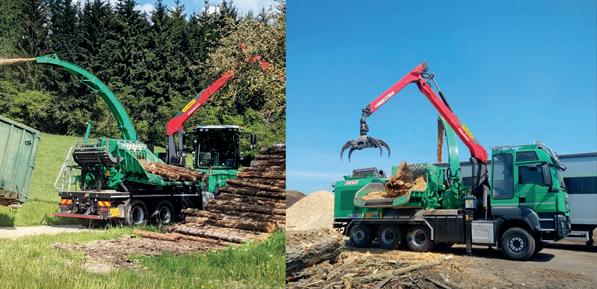
Also for large-scale chippers: The Professional Line add-on package has already proven itself with the JENZ Chippertrucks and has now been extended to the Chippertruck hybrid HEM 922.
All in one, everything done
Jenz has adapted and extended the additional ‘Professional Line’ package for its chippertruck series
Jenz presented the additional
‘Professional Line’ package for the first time at the end of 2019. Specially designed for the driver, it includes targeted solutions in terms of maintenance, ease of use and comfort.
The release found considerable success: the concept proved itself with the Jenz HEM 583/HEM 593 Chippertruck series and is now being extended to the HEM 922 series in the hybrid chipper-truck segment. Operators are enjoying the advantages of the individual equipment components and finding out what effects the changeover to the exhaust gas standard and the new MAN TG3 chassis have on the add-on package.
Conversion of the exhaust emission standard has no consequences
The Euro 6d emissions standard has been in force since September 2019. Until recently, exemptions allowed the deployment of 6c vehicles, but this is now a thing of the past. “The change in the emissions standard has no consequences for the Professional Line package,” says Hans Heinrich Hermeier, Jenz CEO.
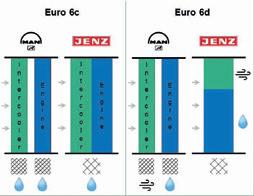
No big deal: The cooling system modified by MAN has been adapted to the requirements in the chipper sector and continues to ensure low maintenance and sufficient cooling capacity
Lars Egbers, Chippertruck designer at Jenz
Only the combi cooler had to be modified, as the standard MAN cooler is not suitable for the dusty environments in the chipper area due to its closely-meshed slats. Changes in the cooler area had been necessary from time to time in the past.
“MAN is using a modified cooling system for the current changeover to Euro 6d,” explains Lars Egbers, Chippertruck designer at Jenz.
“Our solution: water and intercooler air coolers with coarse slats sitting on top of each other ensure sufficient cooling capacity as well as low maintenance since the slat is continuous.
“During development, we benefited from a lot of experiential knowledge from the past.”
You can’t get more professional than that
A new intelligent cab concept, power-packed 510 hp and lower fuel consumption – these are all points scored by MAN’s new TG3 chassis.
An air-conditioned driving and working position, as well as additional storage and stowage options, will provide more comfort in the future. At the same time, assistance systems such as the distance-controlled cruise control integrated at the works increase safety on the road. The reduced fuel consumption is a clear plus in terms of economy.
“From the manufacturer’s perspective a consumption advantage of up to eight percent can be seen in the TG3 compared with the TG2,” says Egbers.
“If we combine the advantages of the new TG3 with those of the Professional Line package we can quite clearly say: you can’t get more professional than that,” Hermeier said.
“When we launched the Professional Line package in 2019, we only wanted to offer it in conjunction with the tried-andtested centric blower,” explains Hermeier, relaying that this was because the practical ladders and the sieve basket holder at the rear would otherwise have to be omitted. The latter in particular offers more flexibility and greater application possibilities.
“However, the customer base that continues to insist on the arrangement of the blower at the rear is larger than we originally assumed,” he said. Consequently, the Professional Line package has been restructured so that both chipper trucks in the HEM 583/ HEM 593 series with centric blower and with rear blower benefit from the advantages of the package.
The sales manager pointed out the minimal changes: “Use of the rear blower does mean that the screen basket holder takes up a different position and the climb to the screen basket housing is also somewhat less comfortable.
“Nevertheless, the combination of rear blower and Professional Line package works very well. True to the motto ‘all in one, everything done’, the customer doesn’t have to make any compromises and the driver doesn’t have to do without anything.”
The Professional Line package on the Chippertruck hybrid is excluded from this subject since only the centric blower is used here.
“We are professionals – our customers are professionals. The professional package will be successful if we listen to our customers and adapt it accordingly when necessary,” Hermeier said.
Hans Heinrich Hermeier, Jenz CEO
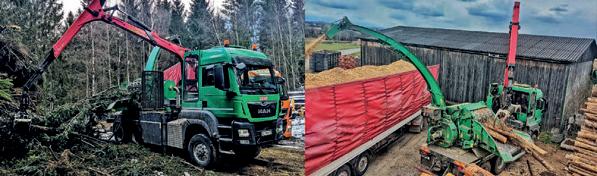
No compromises: The Professional Line add-on package is now also available for machines with a rear blower. However, thanks to repositioning, there is no need to do without the sieve basket holder
REVERSIBLE FANS FOR AUTOMATIC RADIATOR CLEANING | www.cleanfix.org
more Cooling more Power
more Productivity
less Downtime
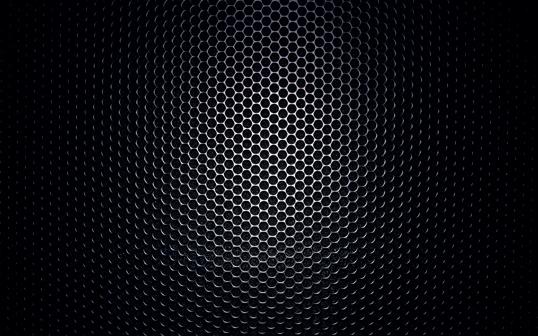