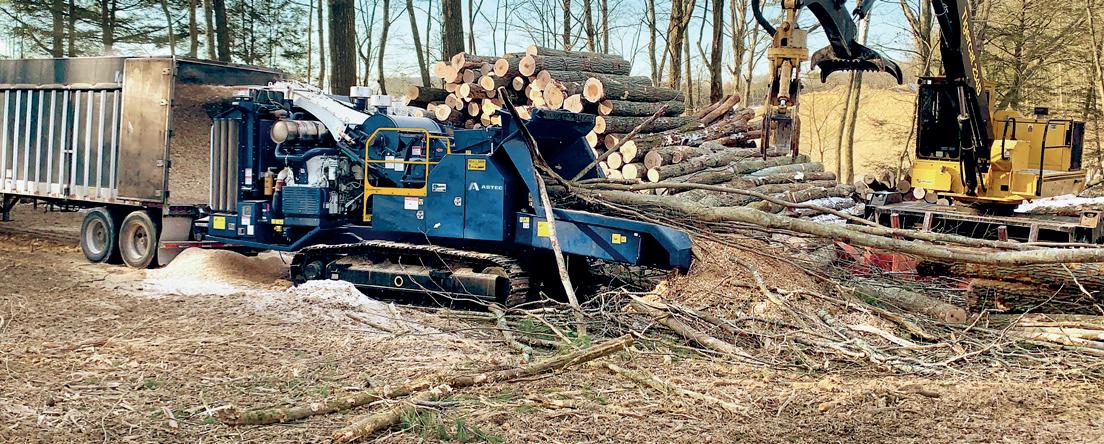
21 minute read
BIOMASS - ASTEC
Drop the Downtime
When the Peterson 4310B drum chipper came on the forestry scene 13 years ago it set a new industry standard for drum chipper efficiency. Not only does this machine process biomass materials at highly competitive rates, but the proprietary design also boasts excellent fuel efficiency. This power comes packaged in a compact and agile design that allows for optimum maneuverability in the field. Be it the machine or the end product, quality matters. There’s no question why this is the professionals’ choice.
Advertisement
The Hardware The Peterson 4310B drum chipper is suited for highvolume biomass producers who process a wide variety of feed materials from brush and small feedstock to logs up to 24 inches (61 cm) in diameter. At 58,500 pounds (26,535 kg), the track-mounted drum chipper is designed for operations requiring high production and frequent moves between jobs and is powered by the C18 Caterpillar engine (755hp).
The chipper utilizes a 36inch diameter by 44¾ inch (91 by 114 cm) wide drum with either six or 12 knife pockets. Chip length can be set from 1⁄8 to 1¼ inch (3 to 32 mm) depending on rotor and knife configuration. The chipper’s robust knives are the thickest in the industry, with a reputation for exceptionally long life. Three, 3/4” bolts clamp down each knife for superior strength and safety.
Other key features include a hydraulic clutch, a sloped feed deck for ease of feeding and wear-resistant AR 450 wear surfaces on the drum pockets

and shell. Optional materialsizing grates further reduce oversized twigs and branches in the chips. The machine can be further customized by adding on a chip accelerator to achieve maximum loading efficiency. The end load spout comes standard with an optional, top-loading spout available.
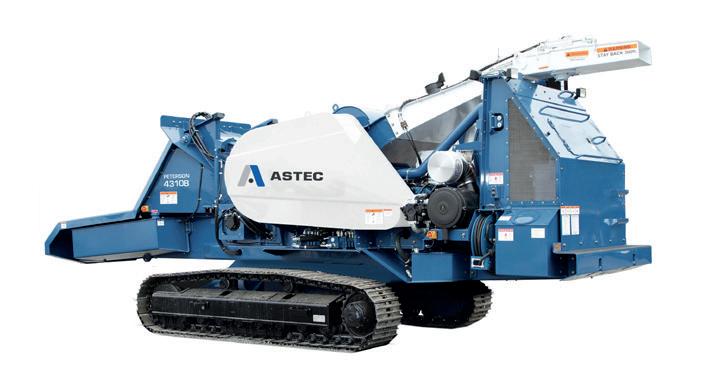
The Process It sounds simple. Materials are fed into the machine, processed into chips then blown out the other side. For those using the 4310B for the job, it can feel that simple as well. Engineered for maximum efficiency, there’s a reason so many rely on this specific machine to get the job done.
The process begins with the sloped feed deck designed to make for easier feeding of various species of feedstock. Unlike disc chippers that are made to process clean, straight logs, drum chippers are made to handle less uniform feedstock including limbs and bark. The design of the feed deck, along with the feed chains and compression roll, ensures a simple and smooth initial feed. As material is fed into the machine, the compression roller feeds the stems into the drum chipper assembly to be processed.
The drum in the center of the machine can be configured to run six or 12 knives (depending on the application). As the drum spins and materials fill the pocket below the knife, the knives cut the materials into a finely calibrated size. The resulting chips are then thrown through the grate, which prevents twigs and small-diameter stems from passing through. The chip accelerator forces air into the chip spout, increasing the velocity of the chips exiting the machine. This increases load density by packing the chips into a chip van, or if in a land clearing application, redistributing chips back into the forest. This is key to loading efficiency and can load up to an additional 10 tons of material into a container.
The End Product Drum chippers are known for producing materials for use in specific applications. Depending on the goals of the project, producers may The Peterson 4310B drum chipper is suited for high volume biomass producers who process a wide variety of feed materials from brush and small feedstock to logs up to 24 inches (61 cm) in diameter
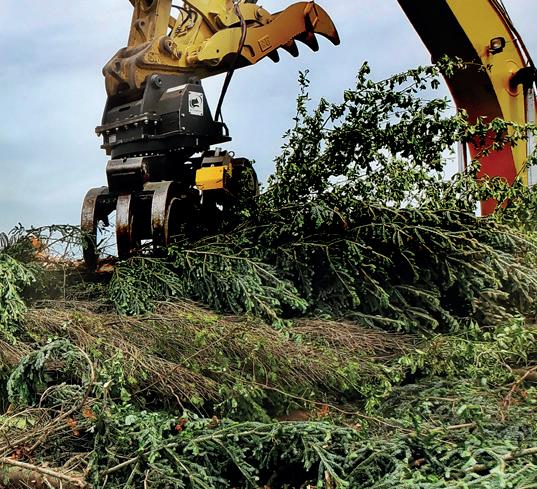
elect to simply blow the chipped materials back onto the property being cleared. Often though, there is value in other applications for these finely made wood chips. In these situations, the optional top-load spout can be added to allow for loading materials for transport.
The most common applications for biomass materials include various landscaping uses like erosion control, playground mulch or decorative mulch. These chips can also be specifically sized for use in filtration systems. However, the most common and dynamic application value right now is in biomass energy. As the world energy market continues to fluctuate, many producers of biomass materials are finding increased demand for use of their products as renewable energy. Operator Experience Every Peterson 4310B drum chipper comes standard with wireless remote-control capabilities allowing for single-person operation and total control in the palm of your hand. The IQAN control panel features a user-friendly, touch-screen design and allows for fine adjustments for maximum productivity. Remote monitoring is also available through Peterson+ Analytics, so you can stay on top of your project even when you are off-site. Users can wirelessly access machine location, rate of processing and error codes in real-time.
Key Features • Processes logs up to 24” in (61cm) diameter • Adjustable chip Length: 1/8” to 1 ¼” (3 to 33 mm) • High efficiency: 60 to 120 tons per hour* • High agility/mobility with a 15-degree slope rating • Proprietary fuel efficiency design • Quarter mile wireless remote pairing radius
*Actual production output may vary due to moisture content, material density and size, support equipment, and equipment options. Production rates are based on operating 50 minutes per hour.
With JENZ shredders through the energy crisis
JENZ biomass processors have always been designed to cover flexible areas of application for biomass as an energy source. Even more flexibility will be required in the future with increasing electricity and gas prices. On the one hand, the full use of wood as a raw material is becoming more and more important and on the other hand, in the wake of the gas shortage, electricity generation from biogas is to be promoted more strongly in the future. In order to actually achieve these two goals, JENZ biomass processors are equipped with various features or can be used for completely different processes by quickly changing tools and screen baskets. On the following pages, the production of biomass fuels and biogas substrate is presented in a hands-on manner.
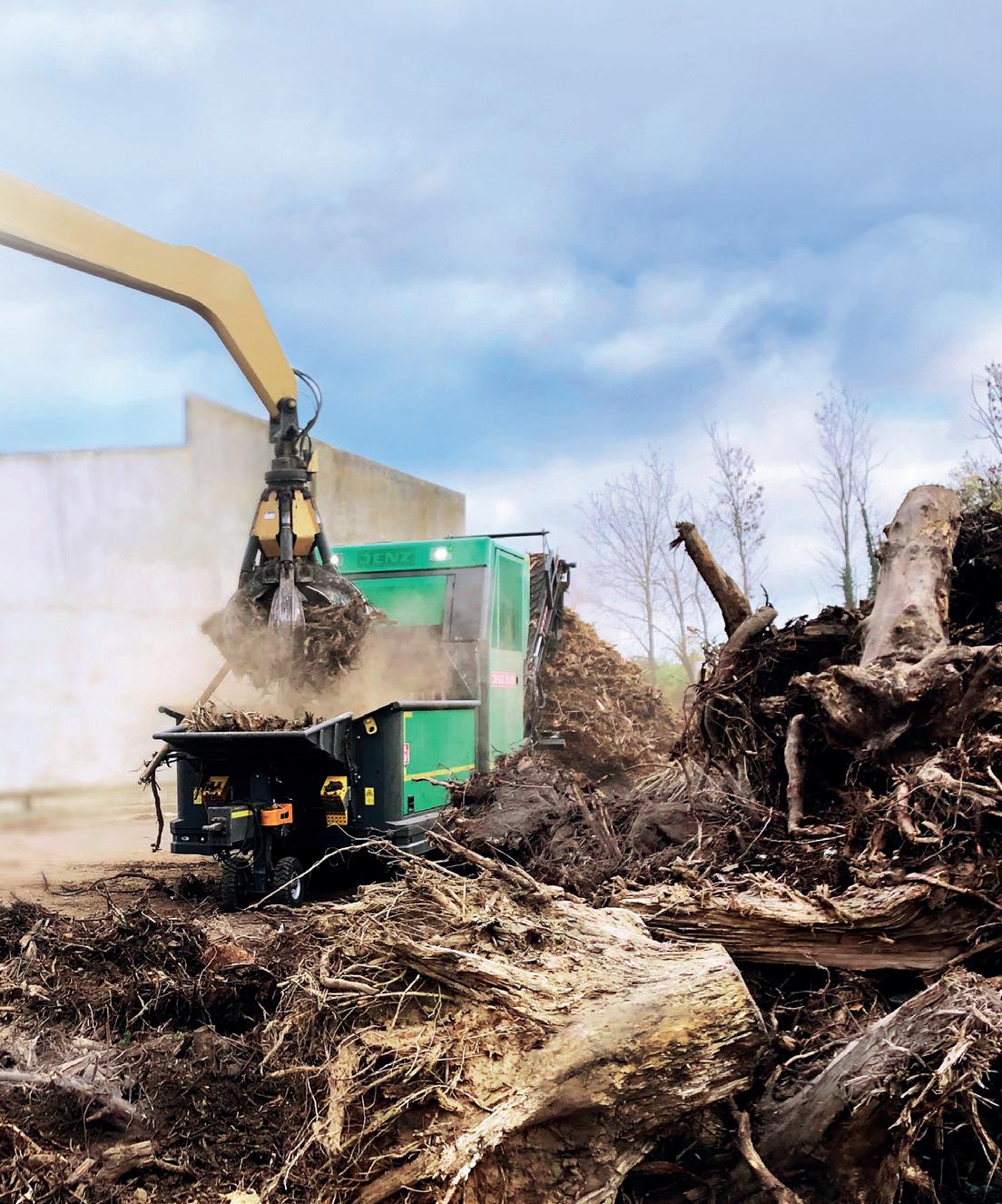
The importance of biomass fuels is increasingly coming to the fore as the price of fossil fuels rises. In addition to the highquality “premium woodchips” produced from round energy
What can be processed?
• Waste wood class I-III • Leftover wood from industrial wood processing • Crosscut wood • Bark wood, materials that are difficult to recycle can and must also be processed as fuel in the future.
• Branch and shrub cuttings • Woody components from green waste composting • Roots • Logs
And how?
BA 926:
The BA 926 is primarily the first choice for the permanent production of biomass fuel thanks to the TwinGear system. This unique system enables speed reduction to produce ligneous biomass.
BA 1016:
With 812 hp drive power and a particularly heavy rotor, the BA 1016 large shredder is the expert if you need to process particularly demanding material, such as waste wood, roots, cross-cut timber, etc., and you want to achieve enormous throughput rates.
BA 615 and BA 916:
Likewise good fuels can be produced from, for example, woody green cuttings or pre-broken roots with the two smaller machines by installing fixed tools.
Fixed tool easycut:
Converting to fixed tools with a blade makes it possible to achieve a defined and precise cut of the hard material when processing ligneous biomass. (Conversion time depending on machine type: approx. 2 - 2.5 hrs - No rotor exchange required)
“Biomass and Residual Wood XL” screen basket set
JENZ has developed a screen basket with slats especially for fuel production. This ensures the best chipping results without overlengths by holding back material which is too long and causing the material to be cut further.
Lower draw-in roller:
Adopted from chipper technology, an additional lower draw-in roller on the BA 926 and BA 1016 ensures controlled material feedin, e.g. with long logs or root end pieces. This in turn leads to good chipping results.
Practical example
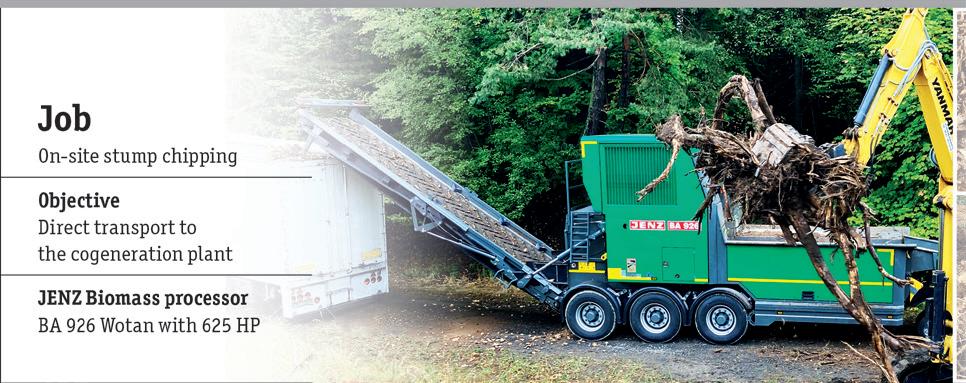
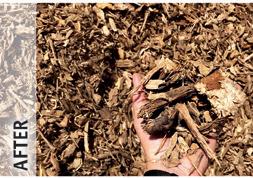

Biogas substrate
Biogas plant operators are facing the challenge this year that yields from maize as an energy crop are much lower than usual. At the same time, the biogas industry hopes for an expansion of biogas production to counteract the energy shortage. To ensure that biogas plants can also be utilised more efficiently with lower maize yields or overall, other interesting raw materials, such as maize straw or solid manure, must be considered as gas producers. Thanks to a total of four tool layouts, JENZ biomass processors can fibre almost any material and thus make the most diverse substrates available for the biogas plant.
What can be processed?
• Crop residues such as straw (maize, grain, ...) • Grass or maize silage • Dung • Sugar beet, potatoes, carrots, ... – Coarse shredding for silage heaps – Fine preparation for lagoon storage (pumpable) • Organic waste • Waste from the food industry (chocolate, wafers, bread, ...)
And how?
BA 615:
The compact shredder with 306 hp and an inlet opening of 615 mm is aimed primarily at smaller (contract) operations or local authorities. Thanks to its low tare weight of only 11.5 t and a low infeed height of 1.86 m, the BA 615 can be easily transported and loaded with small tractors such as tractors or wheeled loaders. With a rotor speed of over 1,100 rpm, the smallest JENZ shredder is ideally suited for substrate processing.
BA 916:
530 hp, 19 t total weight and 10.40 m transport length - that’s how the substrate and green waste specialist scores points. With a rotor speed of over 1,100 rpm, the BA 916 achieves particularly fine fibration, especially with difficult material (e.g. manure). The sideways swivelling outfeed belt and the standard tool box enable a quick changeover when changing material.
BA 926:
Anyone who focuses on the production of biogas in addition to the production of biomass fuels requires a multifunctional machine. The solution: the BA 926 with TwinGear drive. This unmatched system offers a total of four working speeds and thus a quick change between chipping and shredding operations. The BA 926 can be switched to substrate shredding at the touch of a button, where fast speeds are used for defibration.
BA 1016:
The largest JENZ shredder scores points above all for its outstanding throughput performance. For this reason, it is used where either hard, difficult material or particularly large quantities of material have to be processed. For example, over 200 t/h can be achieved when processing manure.
Practical example
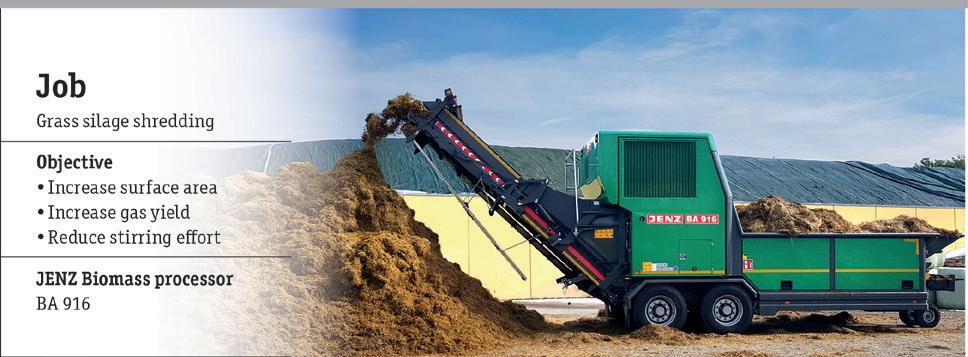
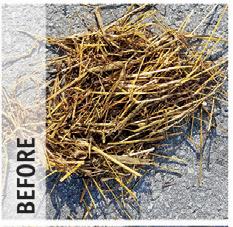
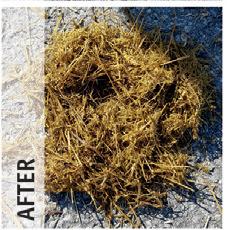
HEIZOMAT has developed a new rotor for the HM 14-860 K woodchipper. With an infeed width of 1200 mm, this newly developed chipping rotor has only 6 exchangeable blades. With this chipping rotor, wood chips can be produced for small wood chip heating systems as well as coarse wood chips for large heating plants. The 8 mm thick blades can be easily resharpened when installed.
Since the rotor speed has been reduced, a total number of 6 throwing shovels in the discharge fan now ensure smooth discharge of the woodchips. The rotor is driven in the usual way by the gearbox-independent power take-off (NMV) from Mercedes with subsequent speed and direction of rotation conversion by the proven elastic belt transmission from Heizomat.
The Mercedes Benz AROCS 3353 engine with a drive power of 530 hp ensures the fuel-saving drive of the woodchipper.
New rotor for the HEIZOHACK woodchipper
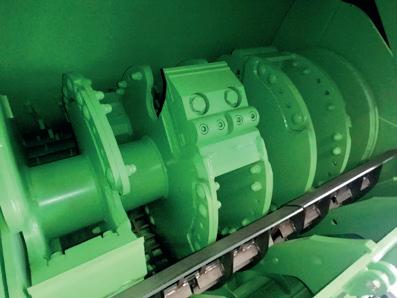
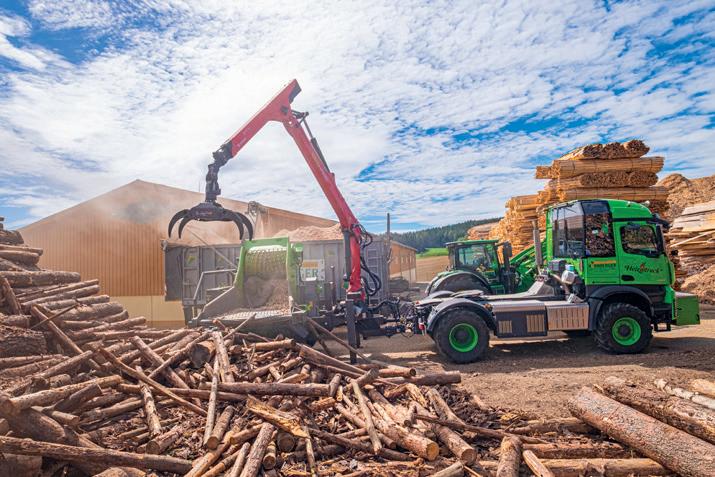

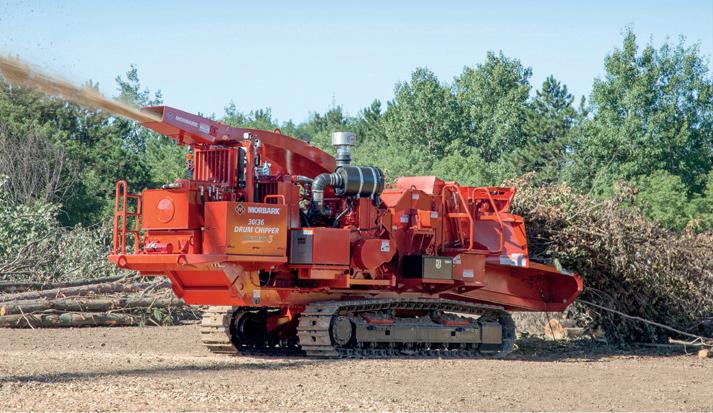
30/36 Track Whole Tree Drum Chipper
Morbark offers a full line of whole tree Drum Chippers in a range of sizes and in several configurations – with cab and loader (WCL) or no cab and loader (NCL), on tracks or tires, diesel or electric powered

Morbark Drum Chippers for Biomass
Add to these choices a wide variety of available options, and you’ve got the flexibility to customize the perfect chipper for your particular needs. With their rigid structural frame and powerful internal-drive, singlefeed-wheel infeed system, Morbark chippers are the best you can get. They can chip small, unmerchantable material, giving you access to more markets – and higher profits. These are just some of the reasons that Morbark is the largest and most respected name in chipping. 50/48x whole tree drum chipper
The Morbark 50/48 whole tree wood chipper is the largest, most productive drum chipper on the market.
The 50/48X was updated to a similar design layout as Morbark’s other industryleading industrial drum chippers with a sloped infeed, externally adjustable anvil and large work platforms for easy access for routine maintenance.
The reverse pivot yoke produces more down pressure than the conventional style yoke for aggressive feeding of a variety of material.
Morbark’s Advantage 3 Drum produces more consistent chips, while the heat-treated, AR-450 steel drum skin provides longer wear life for lower replacement costs and less downtime. The Advantage 3 drum assembly can come as 10-knives for fuel chip or 20-knives for micro-chip application .
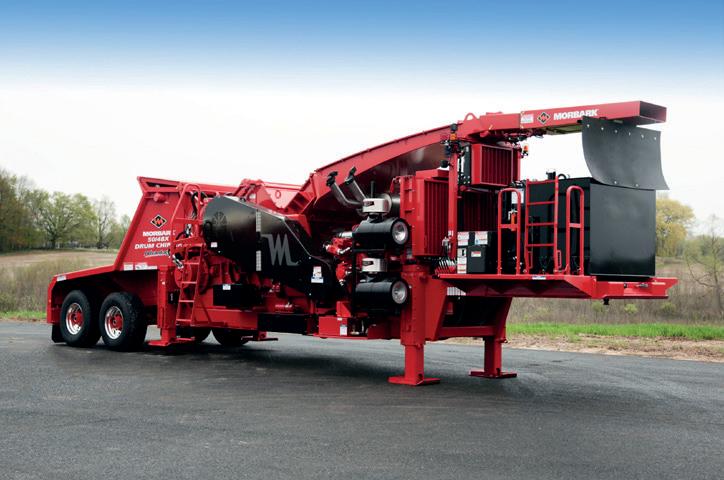
40/36 Whole tree drum chipper The Morbark 40/36 Whole Tree Drum Chipper is a compact, affordable, productive drum chipper designed with the biomass industry in mind.
Equipped with the same internal drive perfected on Morbark horizontal grinders, along with an extra wide feed opening, the 40/36 aggressively feeds brushy tops and limbs, quickly and effortlessly filling a chip van to maximum legal load capacity.
Morbark’s Advantage 3 Drum produces more consistent chips, while the heat-treated, AR-450 steel drum skin provides longer wear life for lower replacement costs and less downtime. The feed system is more efficient due to a staggered knife configuration and contains fewer moving parts, reducing maintenance.
With low fuel consumption per ton produced, this unit is economical. At 8’6″ (2.59 m) wide this compact unit is easily transportable and requires no permits to move. 30/36 Whole tree drum chipper The Morbark 30/36 Whole Tree Drum Chipper’s high production rate lowers operating costs by increasing fuel efficiency.
The aggressive live floor feeding system with two strands of durable WHD-120 chain and a large top and bottom feedwheels ensure positive feeding of material, including brushy tops and limbs.
Morbark’s Advantage 3 Drum produces more consistent chips, while the heat-treated, AR-450 steel drum skin provides longer wear life for lower replacement costs and less downtime.
M20R forestry whole tree drum chipper The hard-working, aggressive M20R Forestry chipper provides optimal performance for in-woods chipping.
Easily filling a 53′ (16.15 m) trailer and sustaining up to four to five loads per day, this hardworking, aggressive chipper is the perfect option for those looking to enter the biomass market with low startup costs.
This machine features the Advantage 3 Drum and electronic flow control to The Morbark 40/36 Whole Tree Drum Chipper is a compact, affordable, productive drum chipper designed with the biomass industry in mind
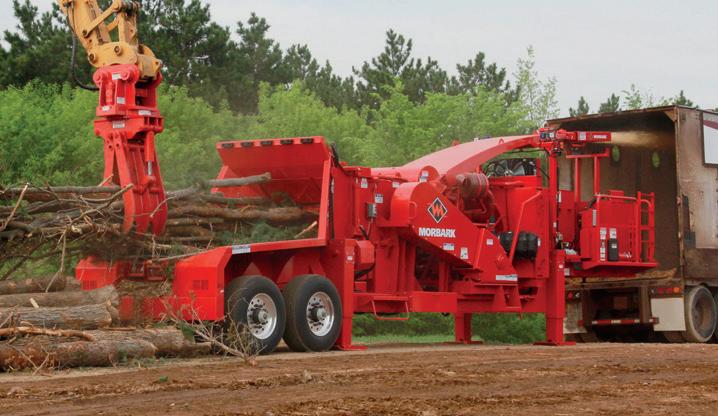
M20R forestry - Whole Tree Drum Chipper this hard-working, aggressive chipper is the perfect option for those looking to enter the biomass market with low startup costs

30/36 Whole tree drum chipper
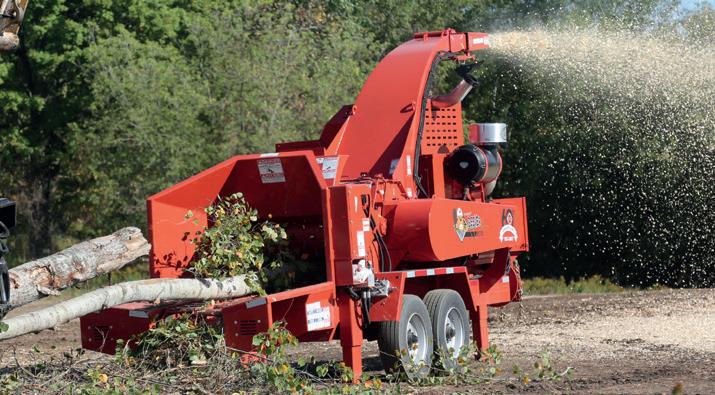
control feed speed from the remote. Tough, abrasionresistant AR-450 steel is used for the drum skin, replaceable belly band, discharge chute and wear strips beneath the bed chain, providing strength and long wear life.
Felling Heads
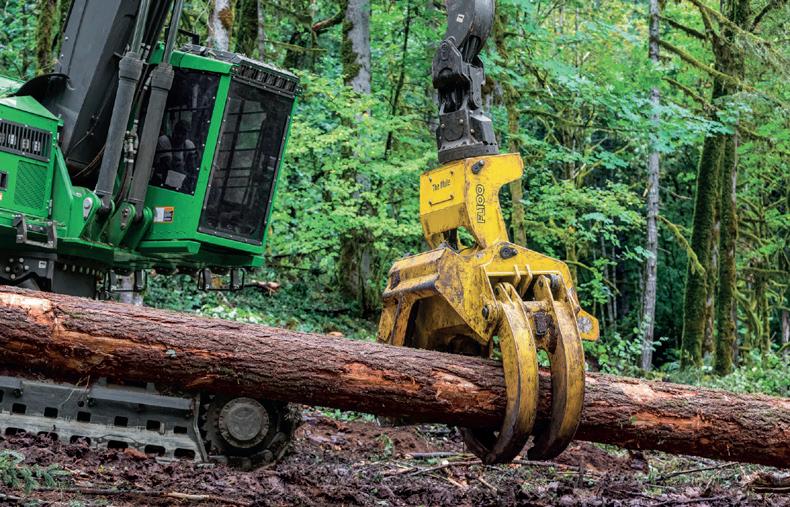
Deere’s new FL100 directional felling head for the steep slope market is a larger, more durable unit with increased grip strength, high grapple capacity, and excellent shoveling performance
Tracked Harvester 959MH Harvesting Head FL100
John Deere’s new large-class directional felling head FL100 model provides customers with a more comprehensive, more durable directional felling head solution. The robust, durable design of the new FL100 makes it ideal for steep slope, shoveling, and traditional felling applications. Featuring increased grip strength, grapple capacity and shoveling performance, the FL100’s grapple arm effectively handles both small and extra-large timber. The increased durability of the FL100 reduces potential downtime in tough conditions, while allowing excellent access to maintenance and service points. “Our customers are continuing to tackle more challenging terrain, and we want to provide reliable, durable equipment designed to meet their unique needs. As they seek purpose-built equipment for their operations, the FL100 will allow them to efficiently and safely fall in both unique steep slopes and traditional felling applications,” said Jim O’Halloran, product marketing manager for John Deere Tracked Harvesters and Feller Bunchers.
John Deere FL100 Directional Felling Head is compatible with the John Deere 959ML Shovel Logger delivers outstanding grapple strength, arm durability, and rotate/tilt power, plus ease of daily and routine service. The FL100 improves productivity with enhanced flexibility in operation and more capabilities to properly position timber compared to previous models.
To learn more about the FL100 Felling Head, as well as the full line of John Deere Forestry equipment, visit a local John Deere Forestry dealer or www.johndeere.com Jim O’Halloran, product marketing manager for John Deere Tracked Harvesters and Feller Bunchers.
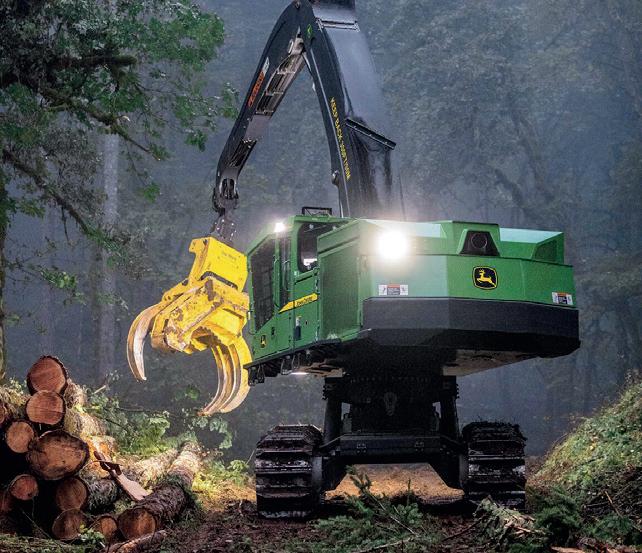

3000L Series Felling Head
Gilbert 3000 Series felling heads are recognized across Canada and the United States for productivity, durability, and reliability.
Increase your productivity with a felling head offering an above standard accumulation and an impeccable grouping of trees.
Intended for a full range of logging operations including thinning, blow down, select and final cut applications, the 3000L Series is available in 18, 22, 24 and 28 in cutting size with the most recognized high rotation wrists in the industry. Features and advantages
Heavy duty
The heavy duty design ensures maximum performance in hard wood as well as in multi-stem wood
Reliability
Gilbert unique and exclusive saw stops protect the saw drive system and the saw disc against impact and gyroscopic deflection. Hydraulic components and STRENX steel offer superior strength under all operating condition
Simplicity
Gilbert unique bolted saw drive system and the easy access to hydraulic components allows quick maintenance and increases uptime.
Efficiency
The conical base is designed to facilitate clearance for fast saw recovery. Moreover, Gilbert felling head ensures that the bunches are optimized for the skidder.
Versatility
The wide front throat opening accommodates butt flare and the innovative geometry allows an accumulation of more trees in tight, straight bunches. Moreover, the powerful 350 degrees wrist is strong enough
to handle any size of timber.
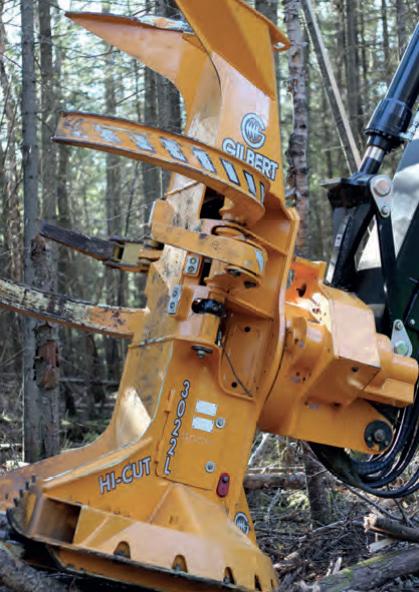
SÉRIE 3000L

TÊTES D’ABATTAGE
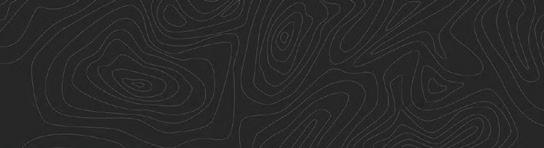
Tel. 1 418.275.5041 Fax 1 418.275.2624 info@gilbert-tech.com 1840, boul. Marcotte Roberval (Qc) G8H 2P2
www.gilbert-tech.com
• The new FR27 Disc Saw Felling
Head offers increased cut and accumulation capacity compared to previous models. • The FR27 is now standard on the 953M and 959M models and is available as an optional enhancement on the 853M, 859M, and 903M with special boom and track option configurations.
John Deere has announced its newest forestry attachment offering with the FR27 Disc Saw Felling Head. Now standard on the John Deere 953M and 959M feller buncher models, and available as an upgrade on the on the 853M, 859M and 903M feller bunchers, this felling head attachment has a larger cut capacity compared to previous felling head models. Building upon the success of the FR24B, John Deere has successfully designed the durable FR27 as a solution aimed to increase productivity on the job.
“We are always looking for ways to enhance operator efficiency and machine capacity. By introducing a larger felling head solution to our line-up with the FR27, we are providing our customers with a larger, more durable attachment to help increase their bottom-line,” said Jim O’Halloran, global product marketing manager, tracked feller bunchers and harvesters & disc saw felling heads, John Deere. “The newly designed FR27 enables loggers of all experience levels to tackle even the most ambitious jobs with confidence knowing their machines are built to endure larger timber and excel in a variety of forestry applications.”
The FR27 Disc Saw Felling Head is designed to take on a variety of timber applications, from large single stem cutting to mid-sized accumulation, and boasts an all-new design and overall rebranding from previous John Deere felling head models. In addition, this robust, high rotation felling head features excellent cut and accumulation capacity, offering top-of-the-line productivity compared to previous models. The FR27 features an impressive cutting capacity of up to 27.2 in. and an accumulation capacity of up to 7.5 ft, improving capability in the woods.
Building upon the success of the field proven FR24B, the FR27 features an updated frame and wrist design, which includes a tall horn, long harvesting arms and continuous hose routings that promote easy machine clean-out. The hardened saw housing wear plates are now standard and offer improved saw housing wear resistance.
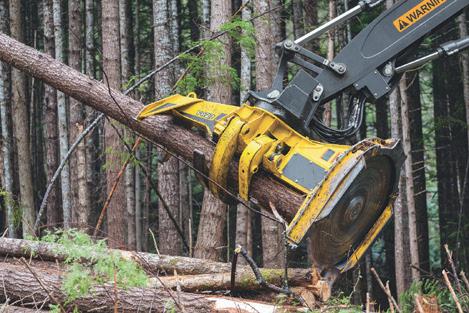

Jim O’Halloran, global product marketing manager
Additionally, the FR27 offers bolt-on saw housing for improved serviceability, with three separate saw housing sections with integrated skis getting you back on the job sooner. The incorporated large side chip exhaust chute minimizes build up and plugging, keeping your machine up and running. The side chip exhaust chute also includes a cover that can be added or removed depending on application.
Starting now, the FR27 are available for purchase on the 800 and 900 M-Series Feller Bunchers models. To learn more about the FR27 Disc Saw Felling Head or the full line-up of John Deere forestry solutions, contact an authorized John Deere dealer or visit www. JohnDeere.com/.
Black Bruin strongly involved in the development of Ponsse’s HH360 rotator
Forest machine manufacturer Ponsse is launching the new HH360 rotator which lets the harvester head freely rotate 360° degrees without limitations. The product has been developed in close cooperation with Black Bruin and Ponsse has exclusive rights to the product in forest machine use. The innovation was on show for the first time at the Expocorma trade fair in Chile on November 23-25, 2022.
According to Janne Loponen, Ponsse’s Product Manager for harvester heads, the 360° degree rotating harvester head speeds up wood processing, makes the operator’s job easier and reduces hose failures. “Compared to competing products, the rotator used in this innovative solution is strong, powerful and above all, energy efficient,” says
Black Bruin’s R&D Manager Tero Ylä-Mononen
Loponen. “The project with Black Bruin has progressed smoothly all the way and the cooperation has been highly productive.”
Black Bruin’s R&D Manager Tero Ylä-Mononen is also highly satisfied with the outcome of the cooperation and elaborates on the advantages that can be achieved with the HH360 rotator: “The HH360 is a combination of the wellknown and durable radial piston technology of Black Bruin’s harvester rotators and Ponsse’s innovation. Thanks to the structure, the torquetransmitting components are wear-proof and the rotator maintains a firm grip throughout the machine’s service life. The rotator is extremely accurate in use and responds precisely and consistently to the user’s actions. That’s what makes controllability of the harvester head natural and superior in all situations.”
Due to the radial piston rotator’s very high efficiency, just 20 l/min of oil flow suffices to operate – yet another factor contributing to the forest machine’s total economy. The rotator’s operating costs are low and it is easy to service if needed. This means that service life can be extended far into the future. “We are also pleased to make our own contribution to support the key properties offered by Ponsse’s harvester head solutions, that is, productivity and reliability,” continues Ylä-Mononen.
The powerful and exceptionally energy-efficient HH360 rotator is available for multiple Ponsse harvester heads when mounted as a loose head installation. The innovation was on show for the first time at Expocorma in Chile.