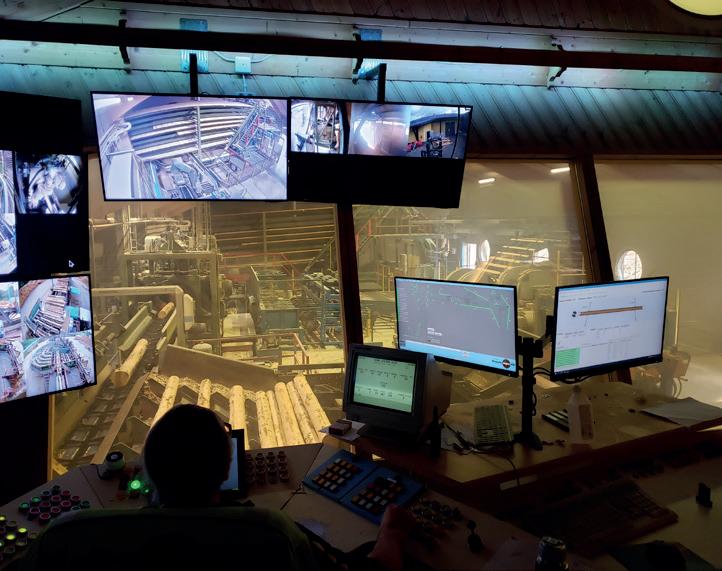
5 minute read
DELTA COMPUTER SYSTEMS
The edger controls failed at the worst time - in the middle of the pandemic’s high lumber demand and shortage of electronic controls

Advertisement
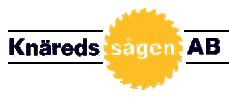
Swedish Sawmill Upgrades Edger with RMC Motion Controller
Can you tell us a little about the company Knäredssågen? Knäredssågen AB is a familyowned sawmill since 1969 in the town of Knäred in southern Sweden, which is run today by the second and thirdgeneration Mårtenssons with 10 employees.
Approximately 20,000 m3 (850,000 BF) of sawn timber is produced annually. The main product is short joists (2.4 – 3 m, 8 – 10 ft) which are planed and cut according to the customer’s requirements.
Knäredssågen has always been active in technology and development. At the end of the 1980s, we built our hydraulic servo actuators for the saw line. Today, all the automation, IT, machine design, and fabrication are done exclusively by ourselves.
I (Johan Mårtensson) am the son of one of the owners and have been working with automation since completing a three-year electrical installation/automation training at a local school.
RMC150E You performed a machine upgrade. Can you tell us about it?
Which machine? The Söderhamns Verkstäder (today USNR) Millomatic edging machine that measures, optimizes, and cuts away uneven edges on boards.
Sensors measure the boards with high resolution and the measurement data is processed in a powerful PC.
When the optimization is complete, the desired position of the blades and rotation of the board is sent to a PLC. The PLC processes the data and sends it to a Delta Computer Systems RMC150E controller that turns the board to the correct position and positions the two blades. When all three servos are in position, the board is fed through the blades at high speed. What problems did you have with the machine? In the summer of 2021, an electrical fault occurred
in a voltage supply to the measuring equipment. The optimizer computer was damaged and the measurement and optimization stopped working. With the high demand for sawn timber, we had to make some quick decisions. Neither spare parts nor help with repairs were available from the supplier, only new software and hardware were offered at a high price. Which goals did you want to achieve with the upgrade? The first goal was to get the edger up and running provisionally so that production in the saw line could continue. Once this was done we could focus more on what we really wanted in an upgrade. We concluded that full control over the various systems was most important. In this way, we can maintain and troubleshoot the system with our staff, which is a great advantage. Good support and service were also some of the main requirements. What areas did the upgrade involve?
Hydraulic-related:
Replacement of position sensor and motion controller
General controls:
New PLC with Ethernet communication for easier implementation together with Delta’s motion controller.
Optimization and sensors:
BoardProfiler 3D-T from LIMAB.
Structural:
Adaptation of the existing stand to the measuring frame for the new sensors.
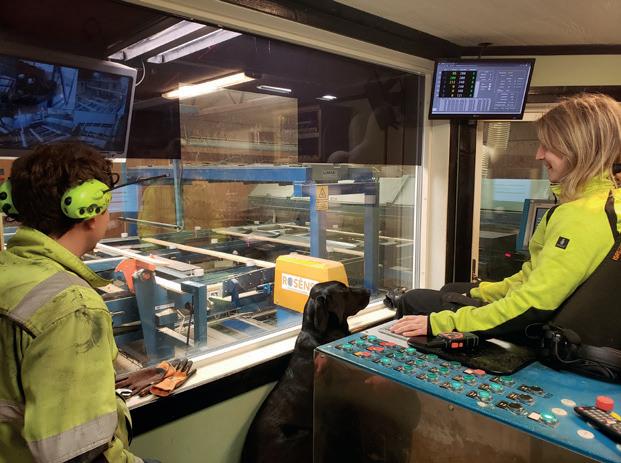
Did you encounter unexpected challenges? The delivery time for the sensors was almost 6 months. Such a long time without optimization on an edger is not a good deal. It was a challenge for production and sales as the saws yield is significantly worse without optimization. How did the planning proceed? The first step was to find a new motion controller that we could program ourselves. Once we had chosen the controller, we were able to
Cont’d on next page
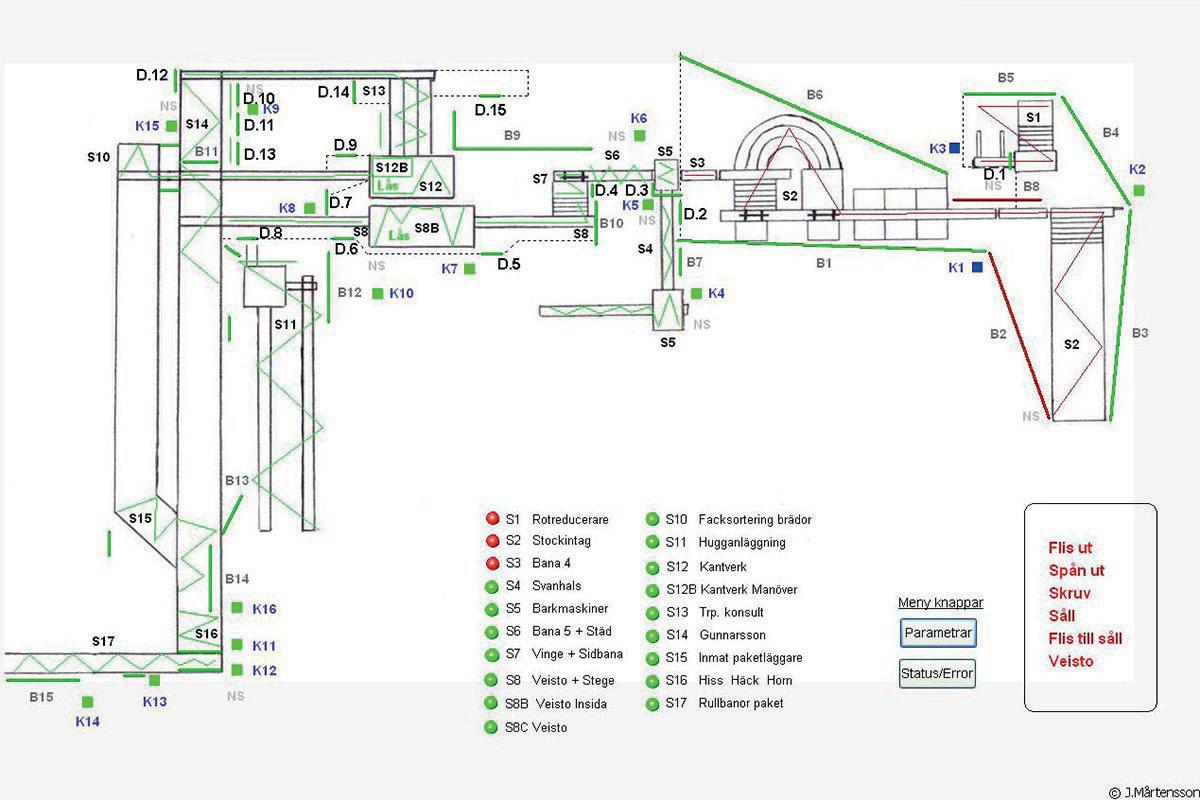
RMCTools was fast to learn, easily accessible with great support
proceed with choosing the optimization system. Early in the procurement of the optimization system, a long delivery time was pointed out. The installation of the systems and hardware was planned to be carried out when the saw line was at a standstill.
How did you choose components? First, we needed to be able to control the servos from our PLC. After some searching (we also asked Hewsaw) a Delta Computer Systems motion controller was the obvious choice. Then it was time for new sensors and optimization programs for the edger system. We chose a local supplier who had delivered similar systems to us before. The choice of a Mitsubishi PLC was obvious as we always use the same manufacturer. work. We have lost a lot of money due to the lack of optimization for 6 months. The repayment period will therefore be very short, perhaps weeks.
The payback period for the motion controller is more difficult to calculate as it does the same task as the old one. But now we have full visibility into its operation and in the event of an error, we can very easily read error codes. Production stoppages in the event of errors will now be significantly shorter with the new motion controller.
How was the result? Did it go as planned within the schedule? The result was very successful, upgrading a more than 20-year-old machine with today’s controls. Better interoperability, a clearer user interface for operators, tools for troubleshooting, and the possibility of increasing production are just some of the benefits. The schedule slipped when the delivery of the sensors was delayed by another 2 months.
Which parts went particularly well? I thought the change from the original motion controller to the Delta RMC150 would be a very complicated job. But the RMCTools software was quick to learn, as was the RMC’s communication to the Melsec IQ-F PLC. It is very easy to get support from Delta through technical support, YouTube, the forum, and the website. Do you have plans for other similar projects in the future? In the planer, there are saws (trimmers) that cut the pieces of wood to the right length, and hydraulically position them. A motion controller fits perfectly here.
The main saw line today has 14 hydraulic servos. The machine positions the logs, tools, and all the auxiliary wheels to the desired locations between each log. Today we have independent analog servo boards that work, but with a modern motion controller, we foresee the advantages of troubleshooting, adjusting speeds, etc. In this application, both position and position/ pressure will be used.
Delta Computer Systems
has 40 years of experience in manufacturing motion controllers with specialized expertise in hydraulics and sawmill machines. To learn more, visit www.deltamotion.com
What was the cost and estimated payback period? Approximately SEK 1.5 million (approx. $150,000) included Reconnect with the entire wood products optimization software, sensors, manufacturing community. motion controller, PLC, and

SAVE THE DATE
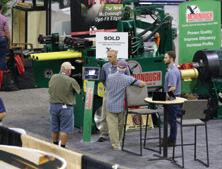
NOW
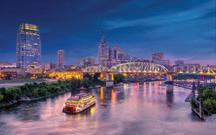
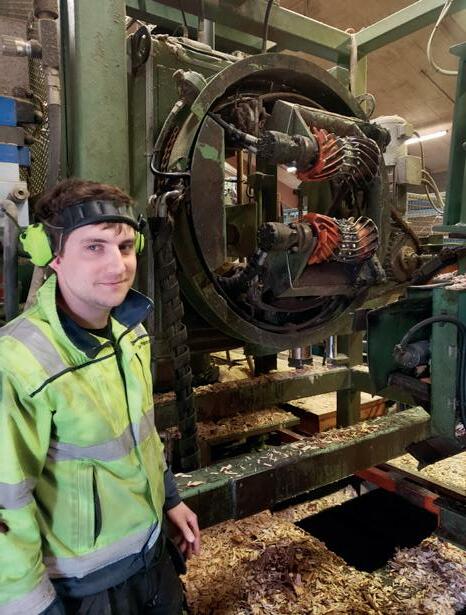

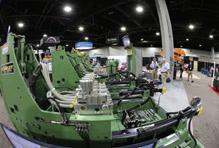