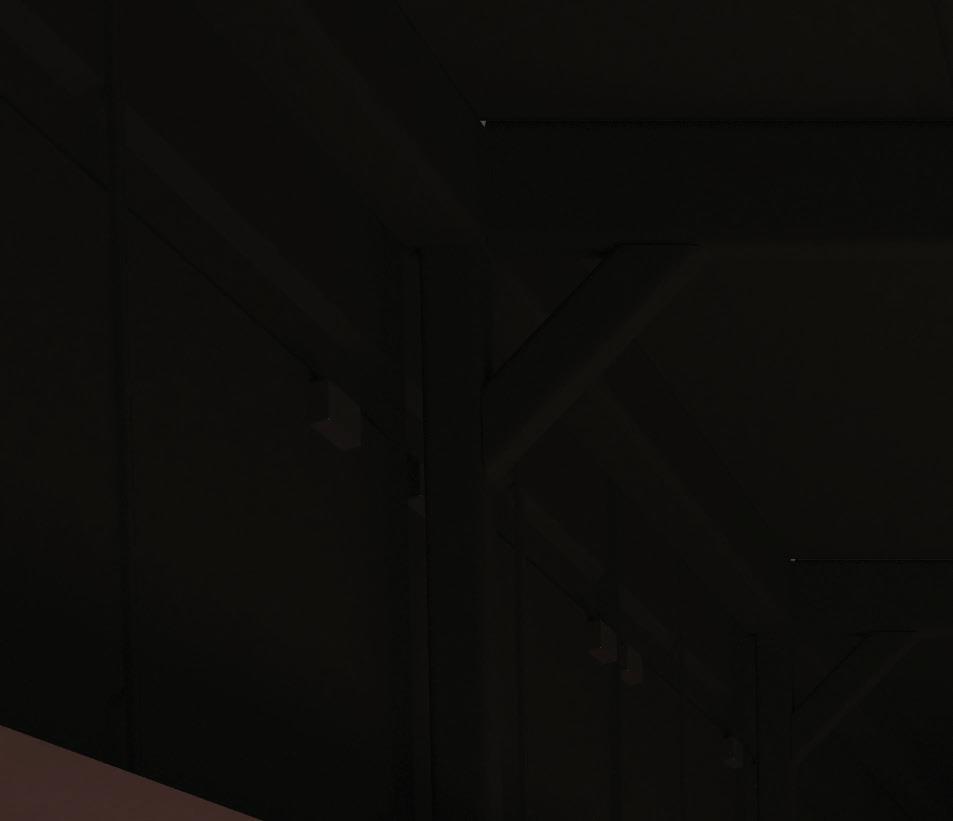
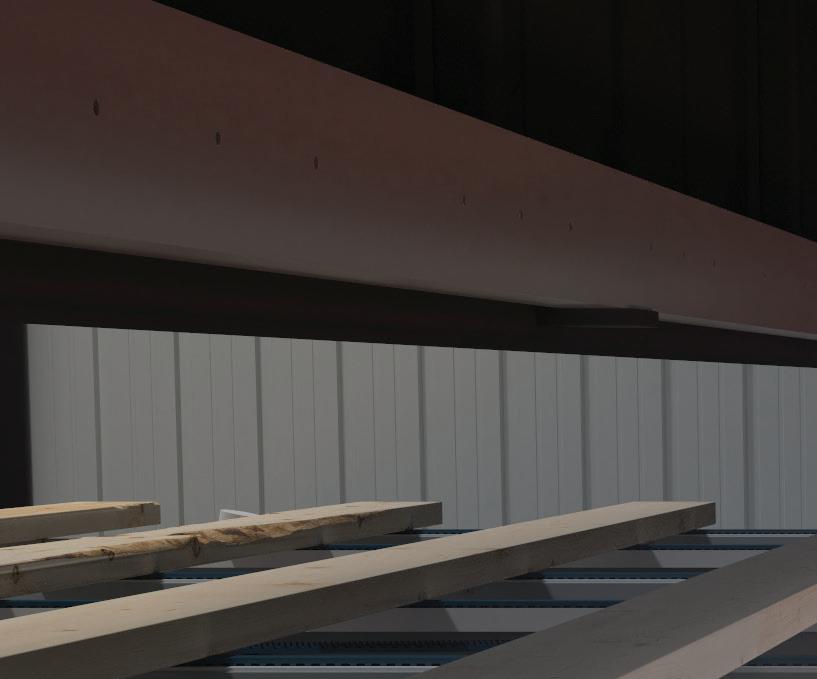
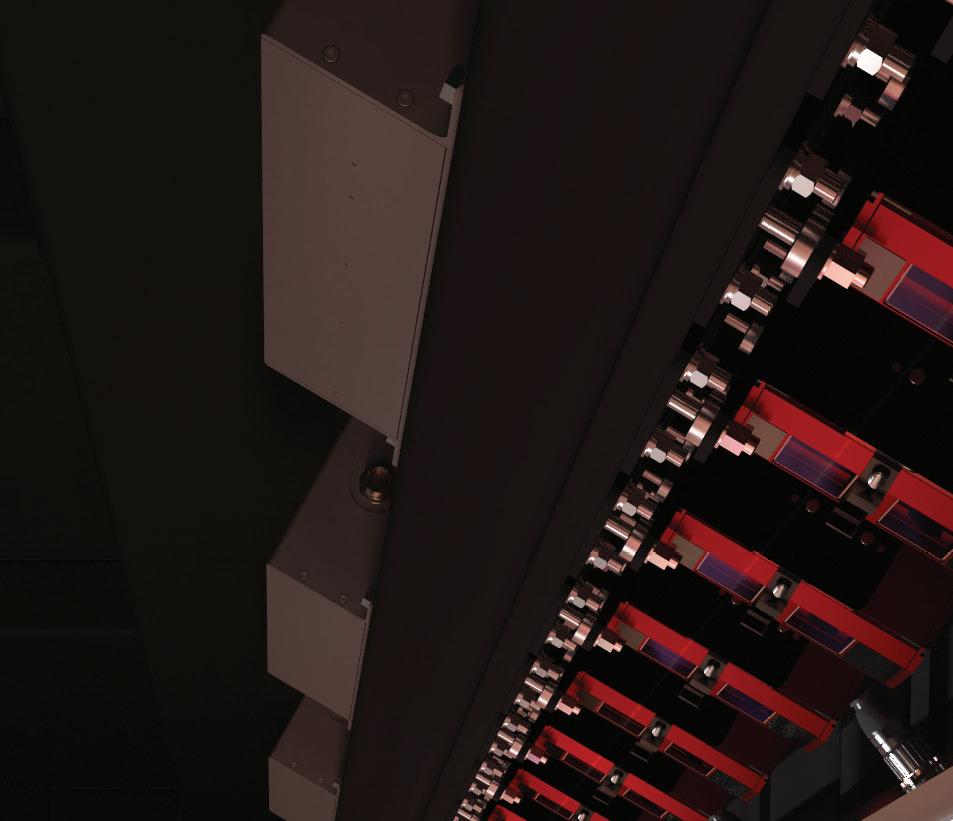
SAWLINES
Shredders & Grinders
Skidders

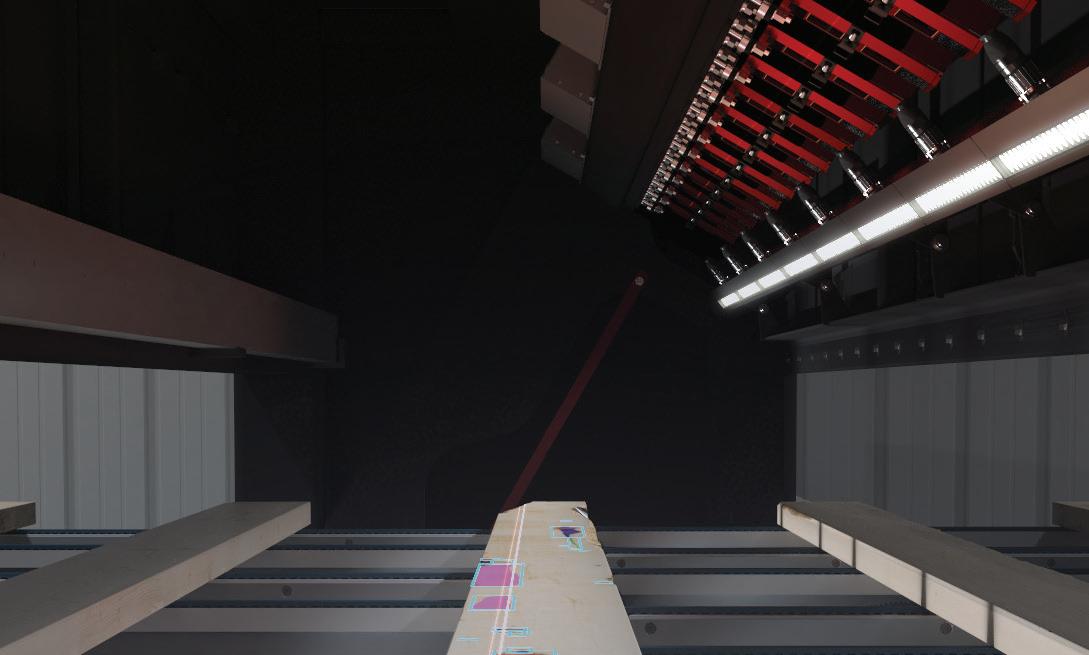
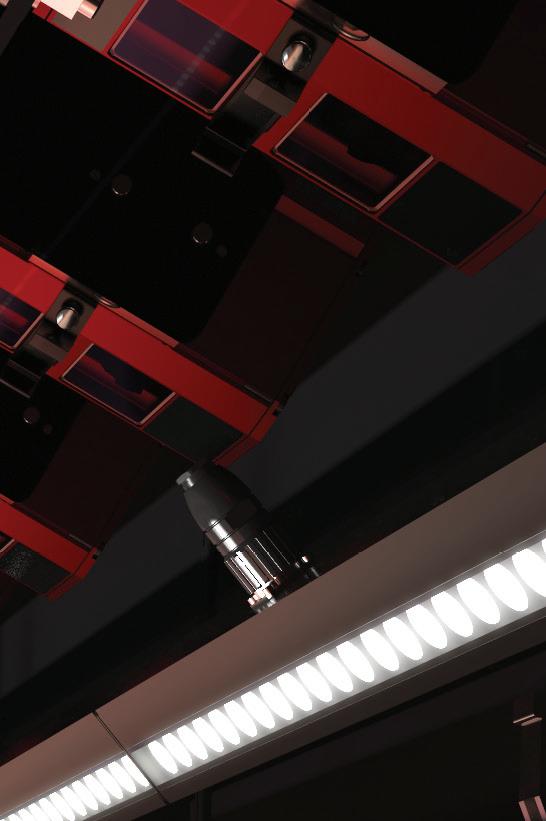
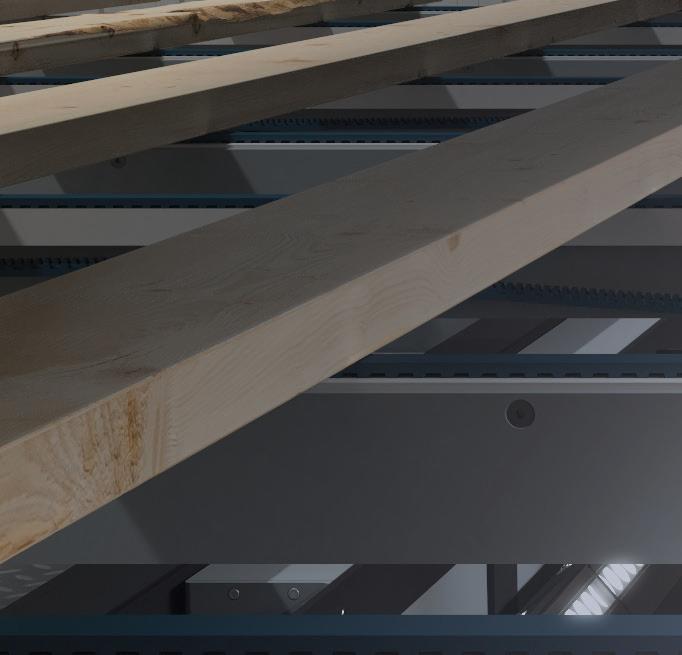
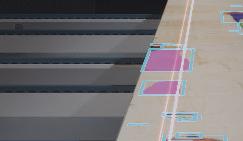
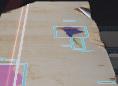

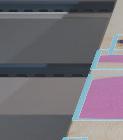
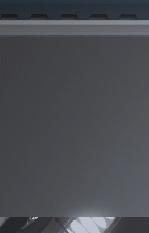
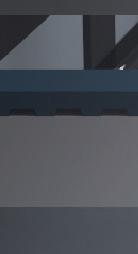

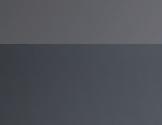

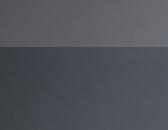

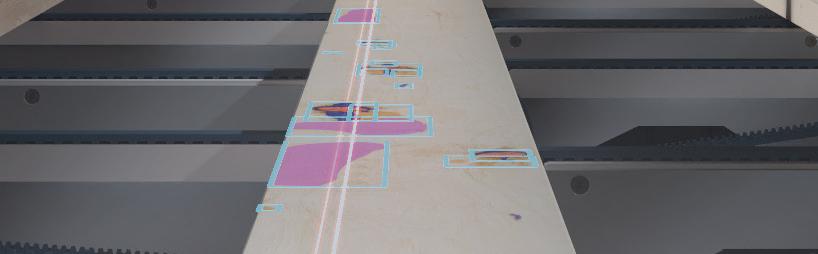
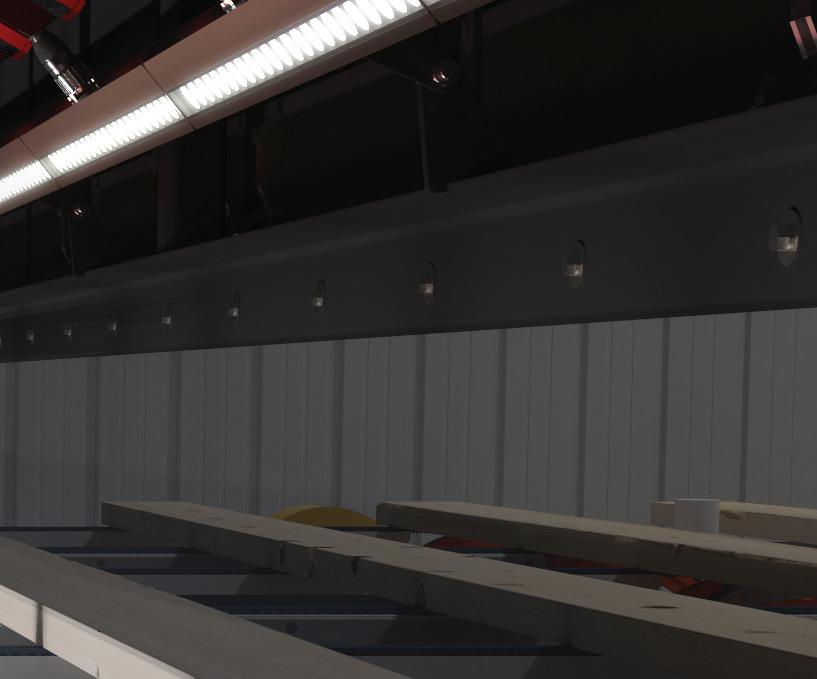



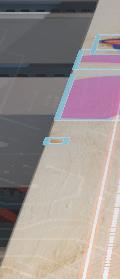
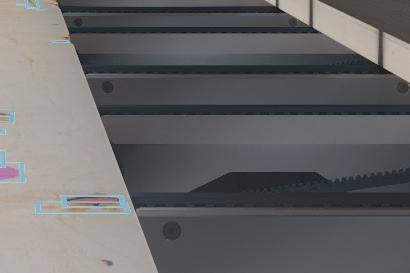

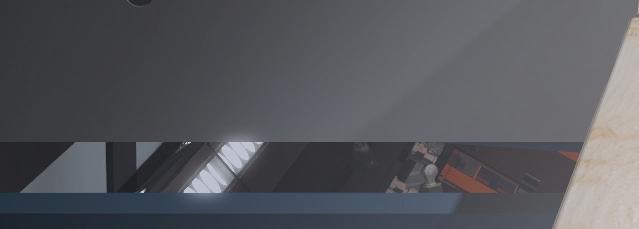
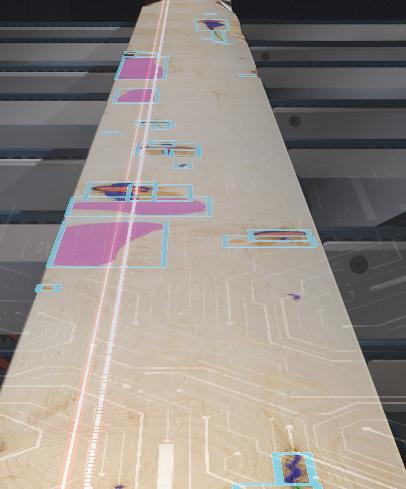
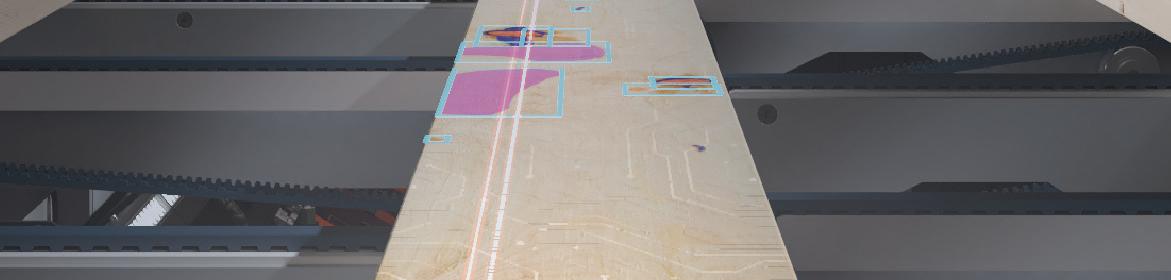


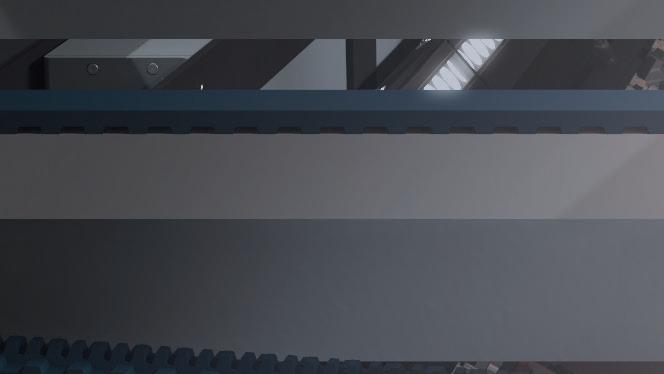

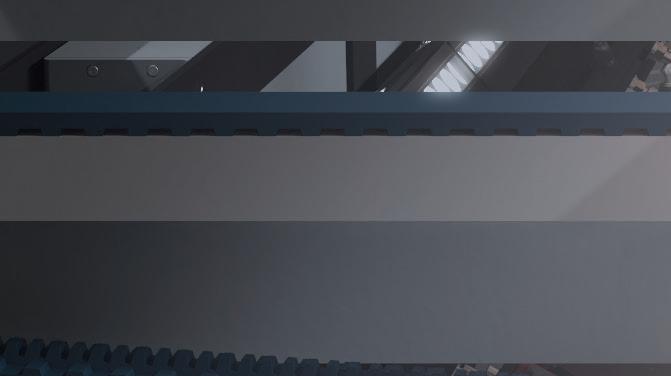
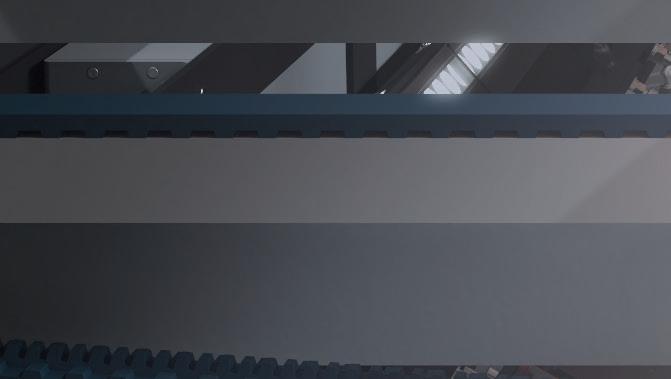
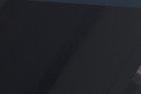

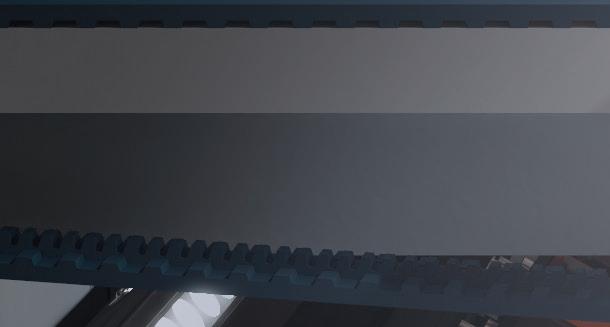
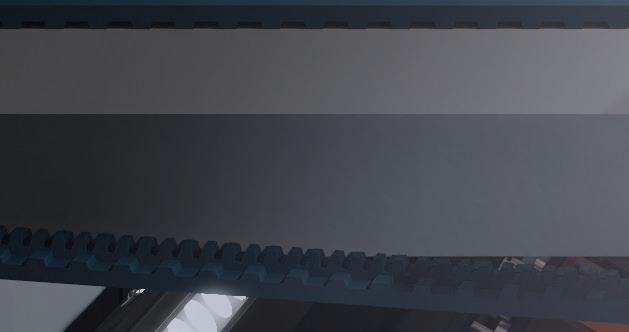




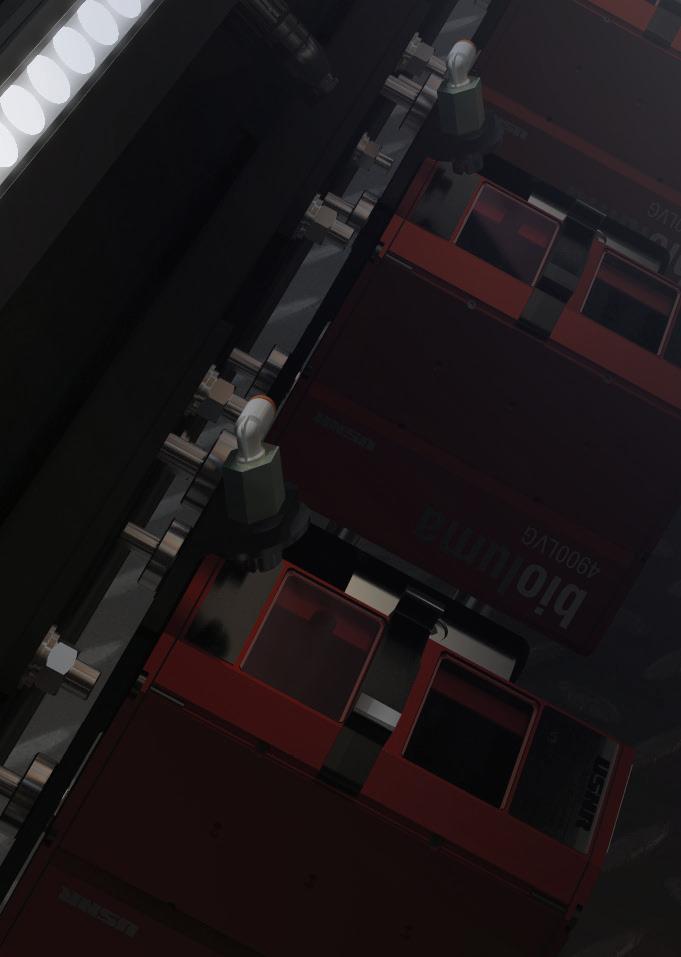

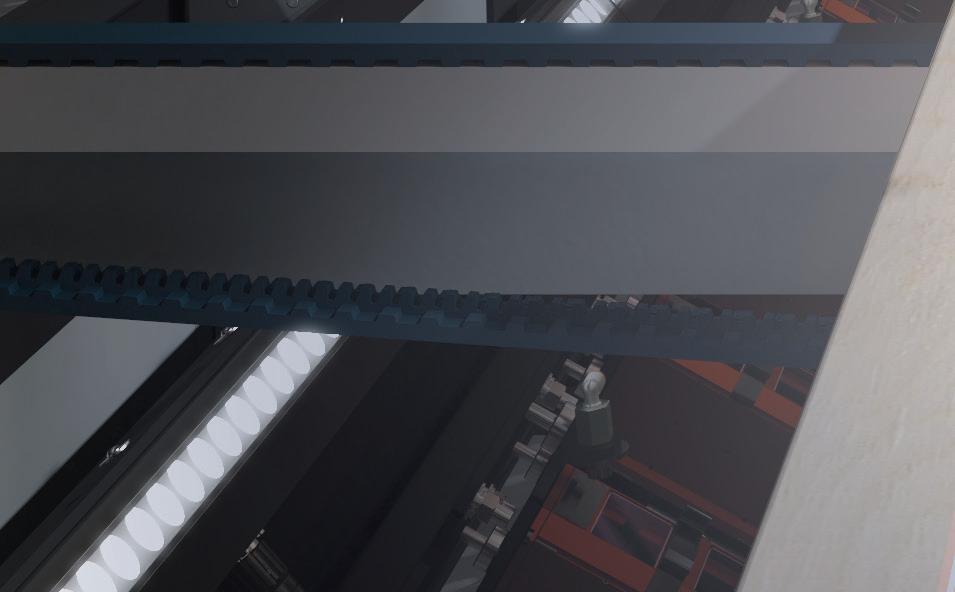
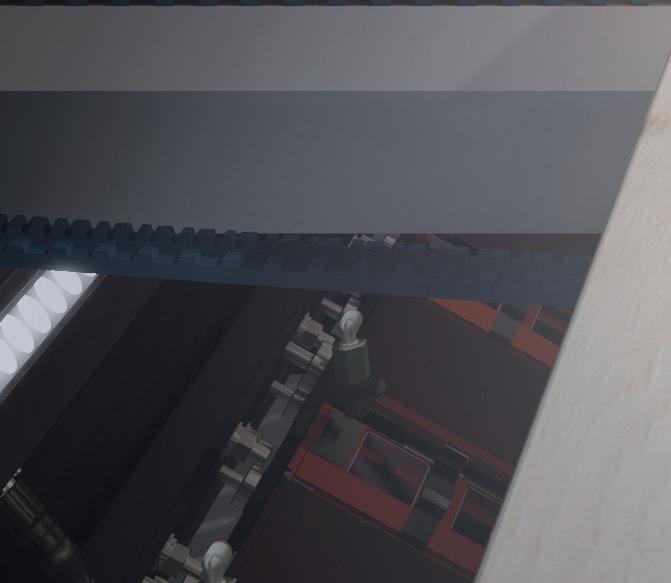
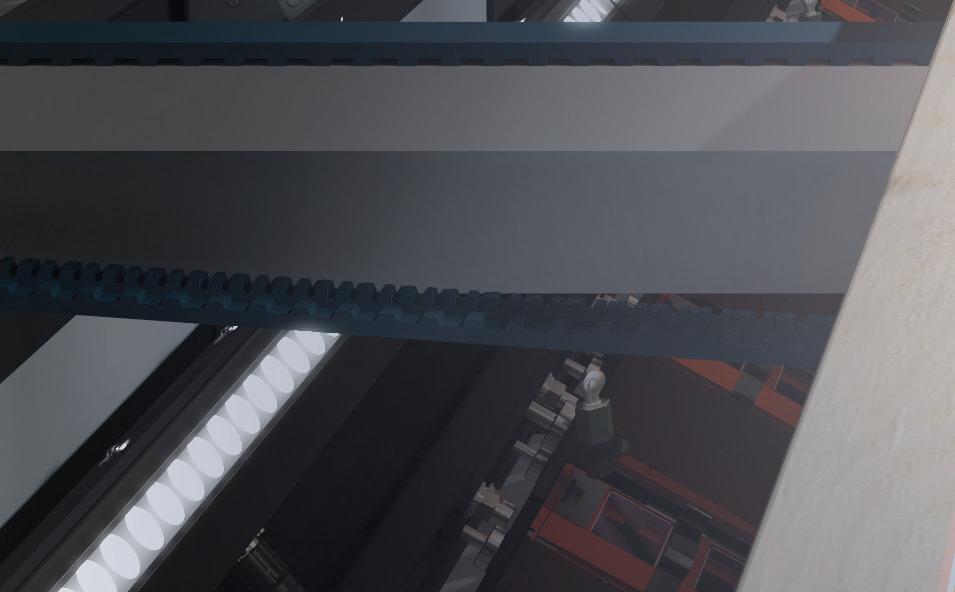

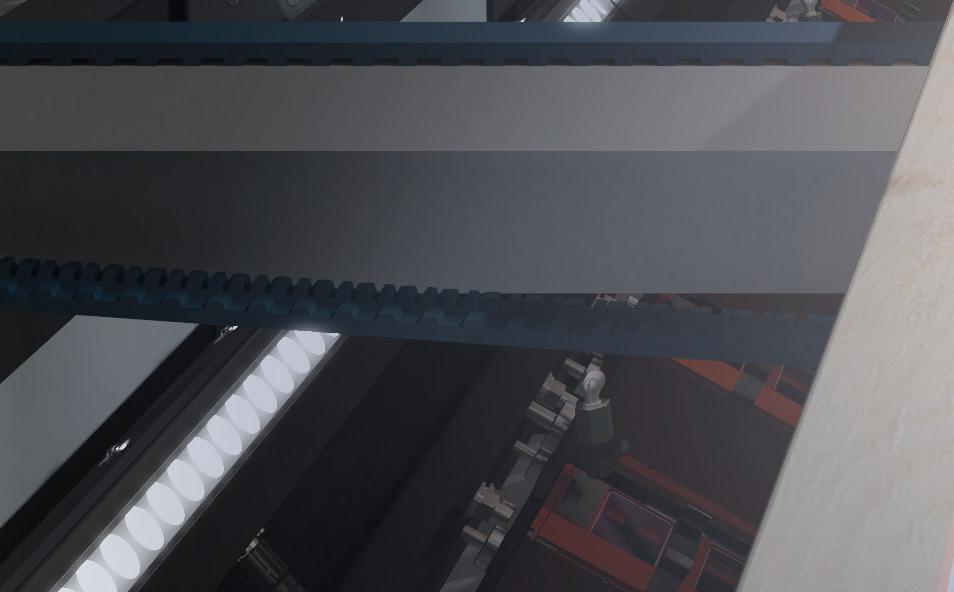

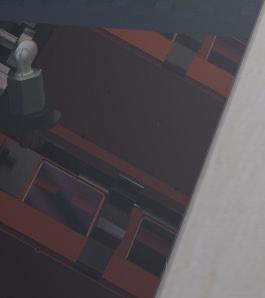
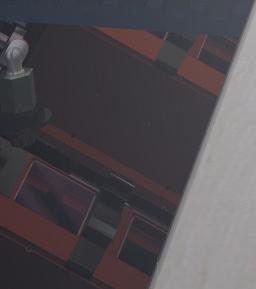

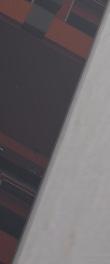
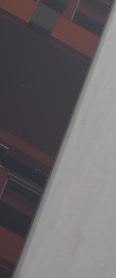
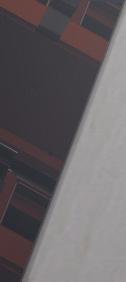
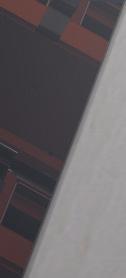
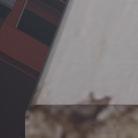
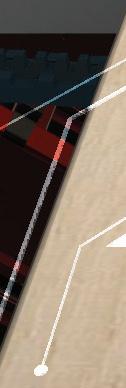
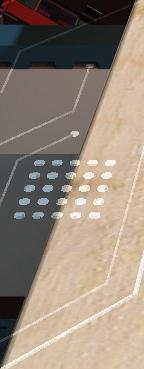
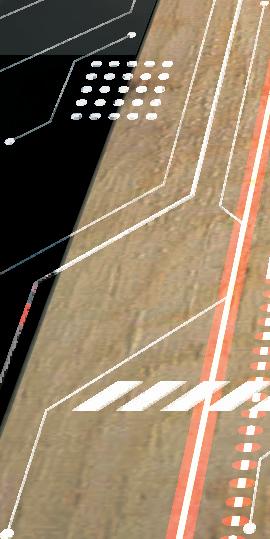

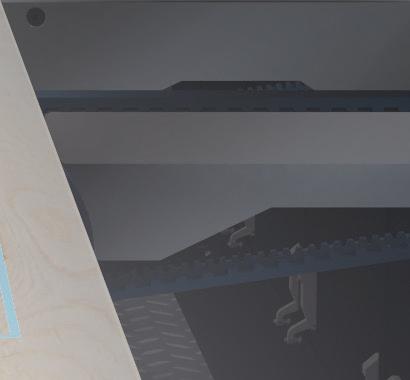
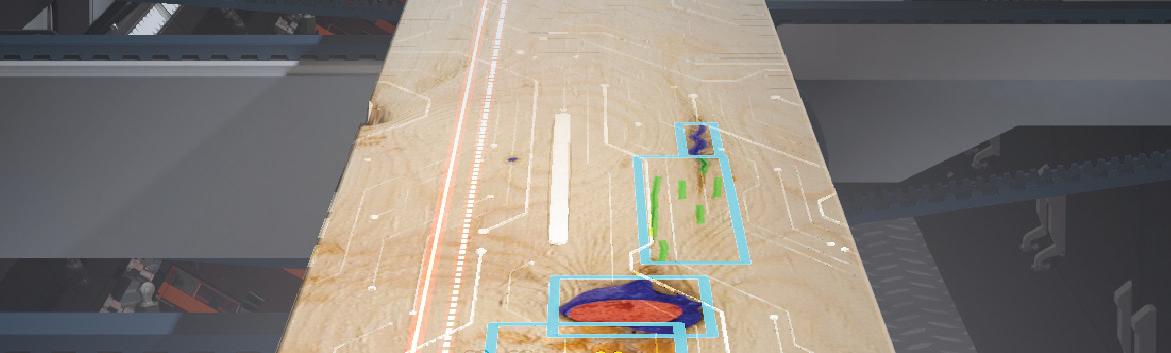



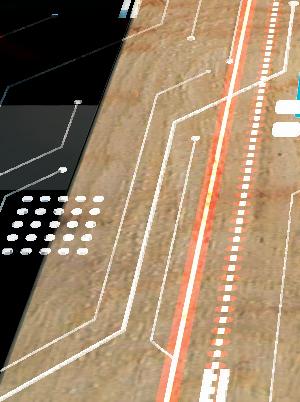
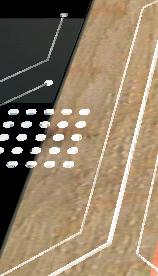
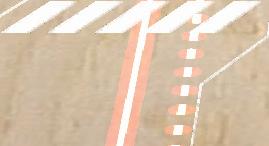

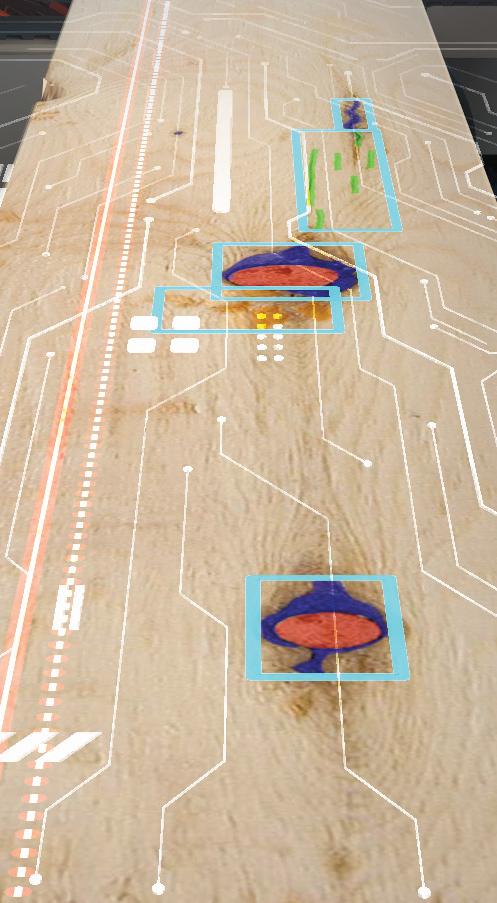
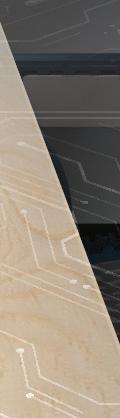
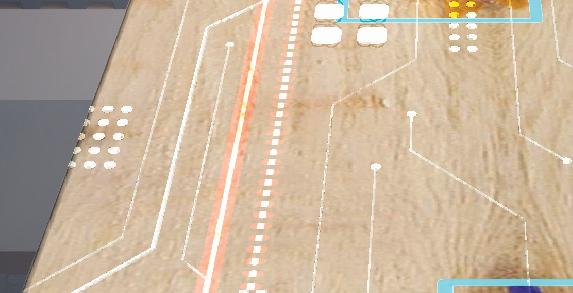




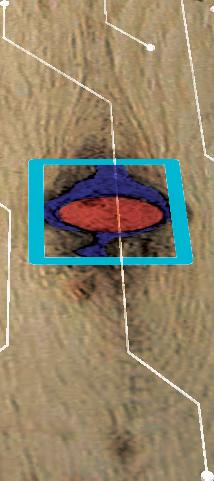
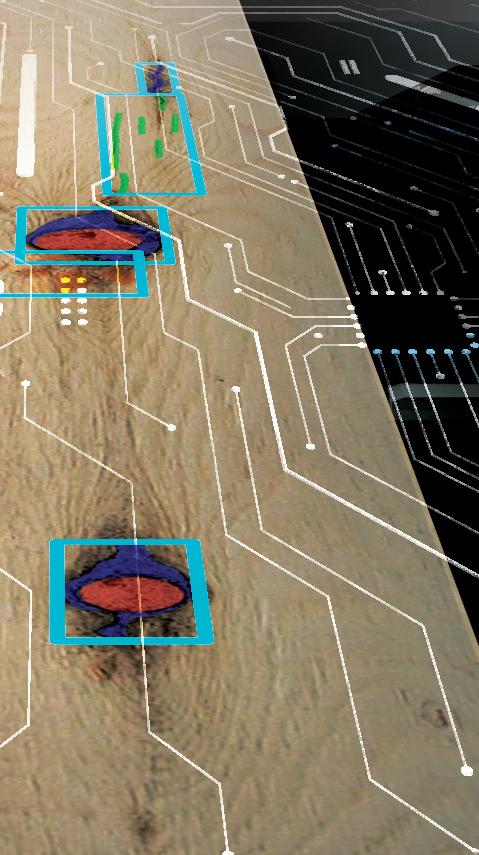
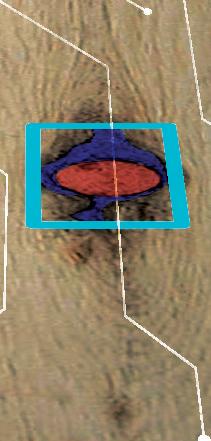
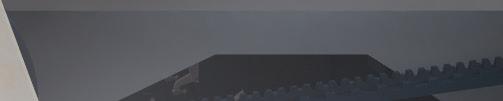
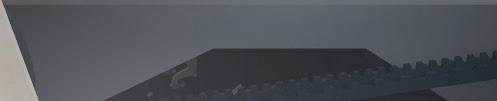
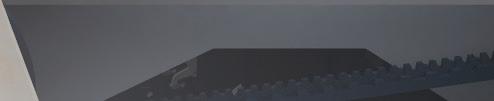
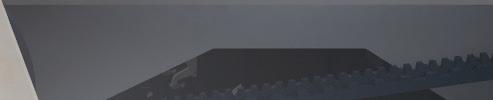
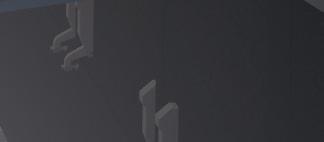



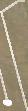



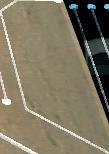

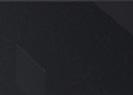
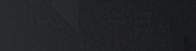
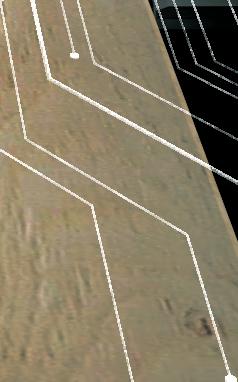
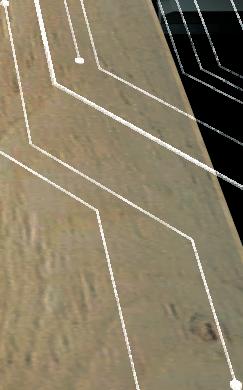
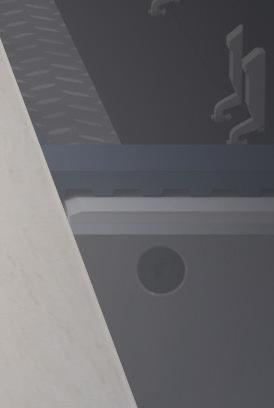
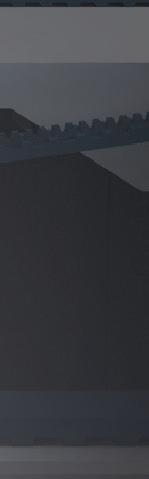

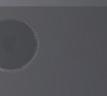

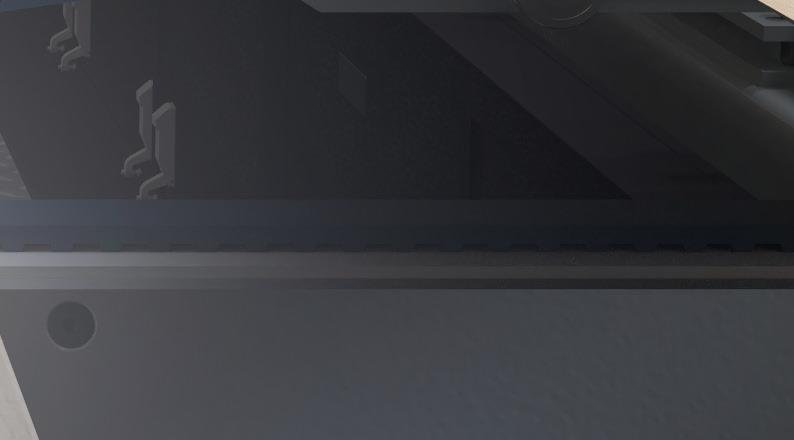
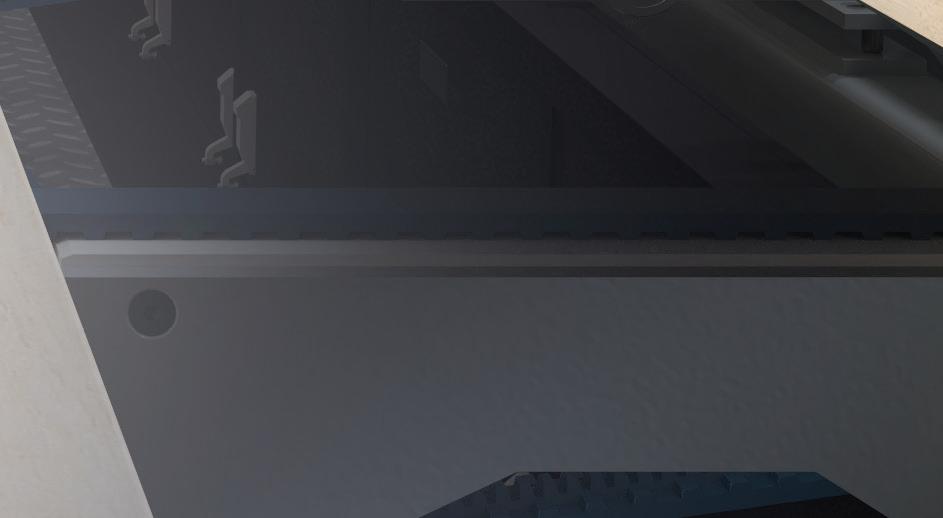

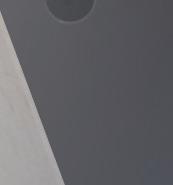
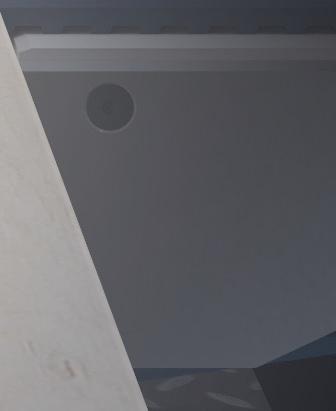
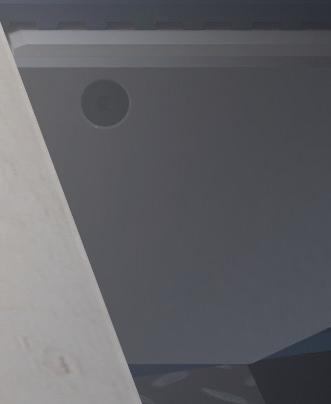
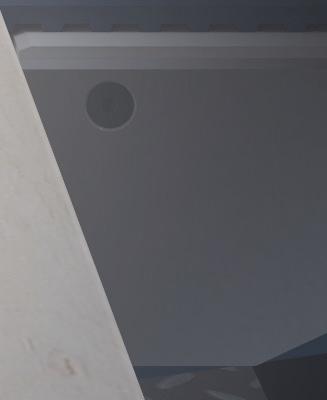
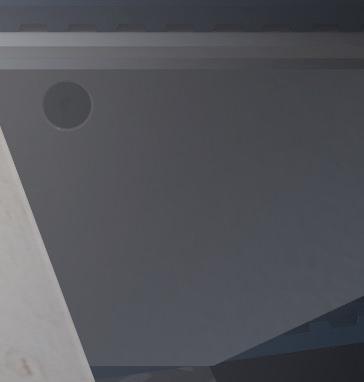
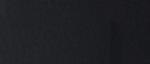
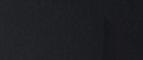



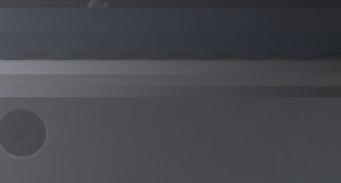
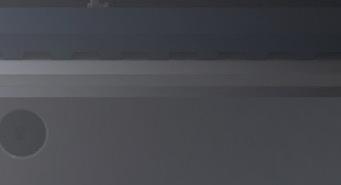


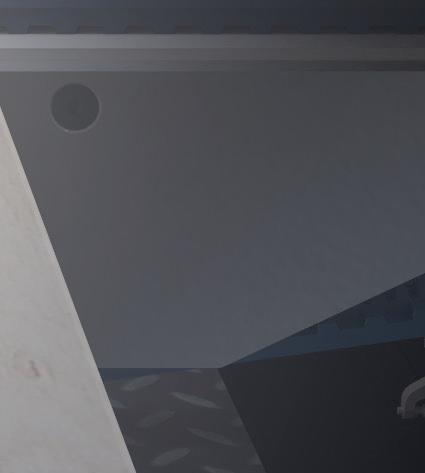
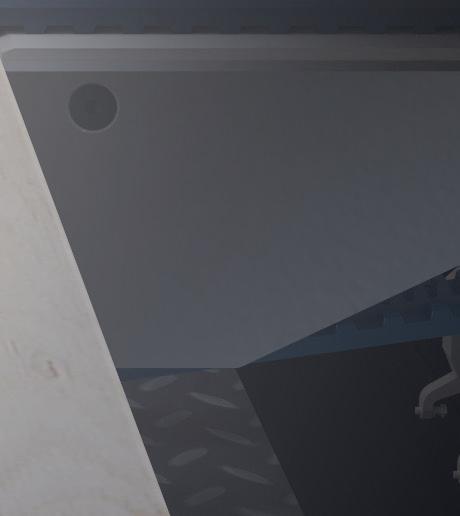

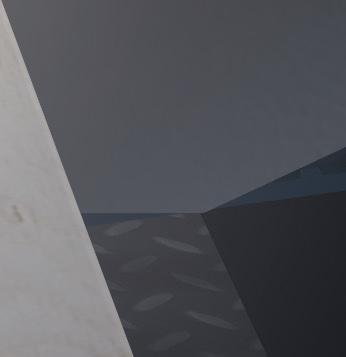
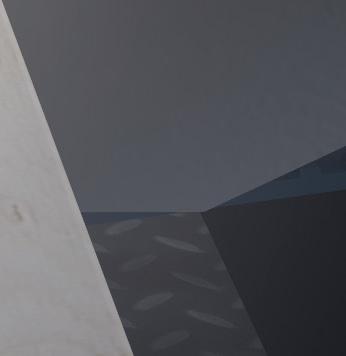
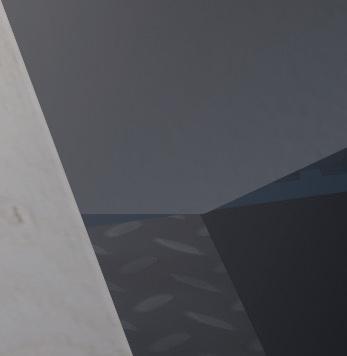
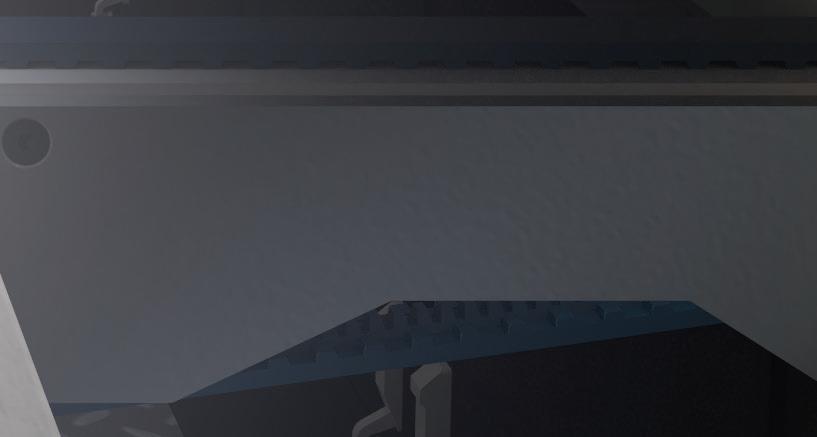



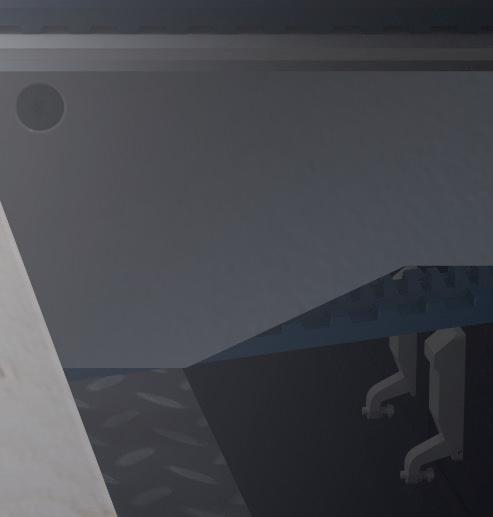
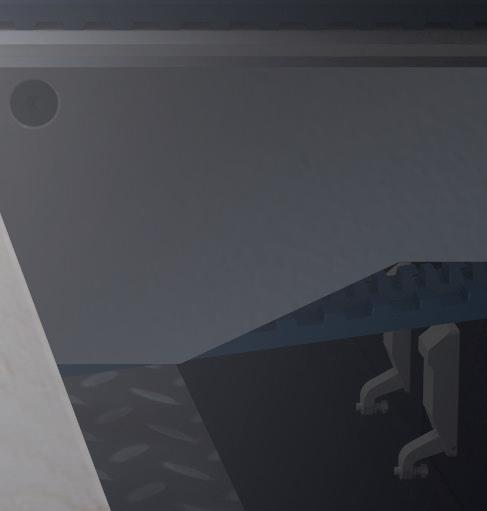
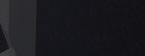
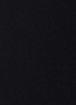
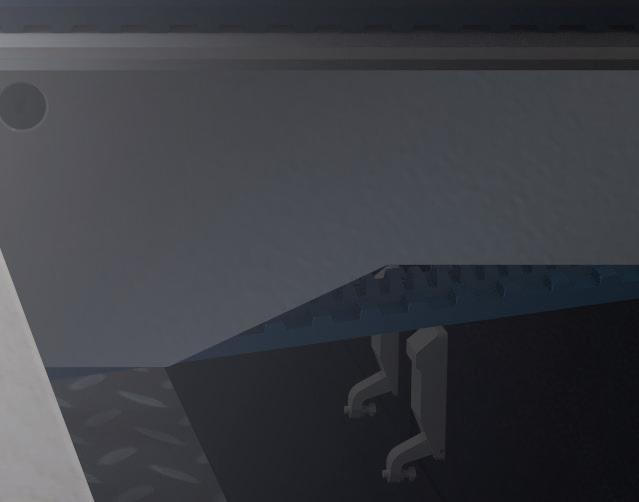

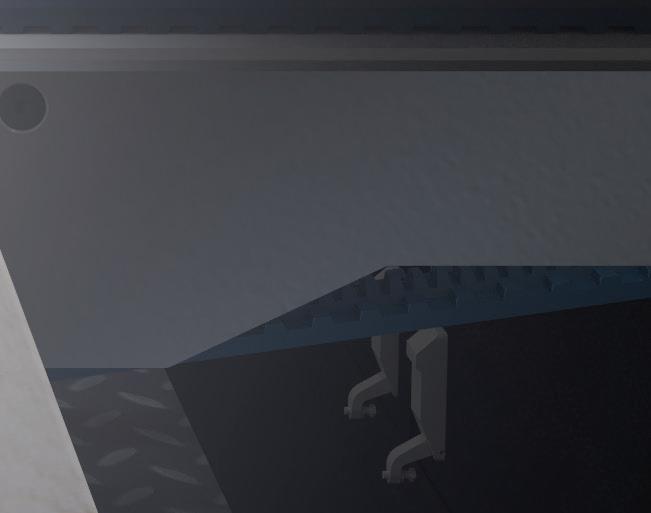

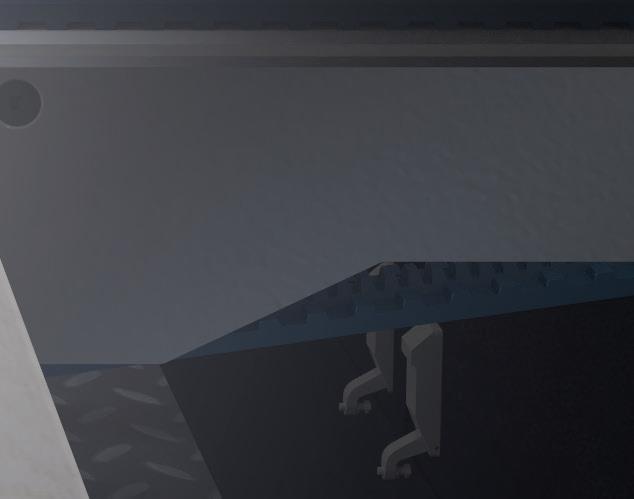
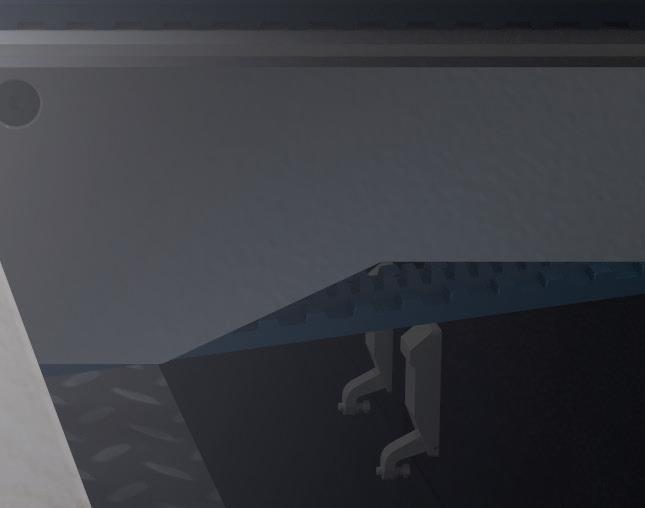
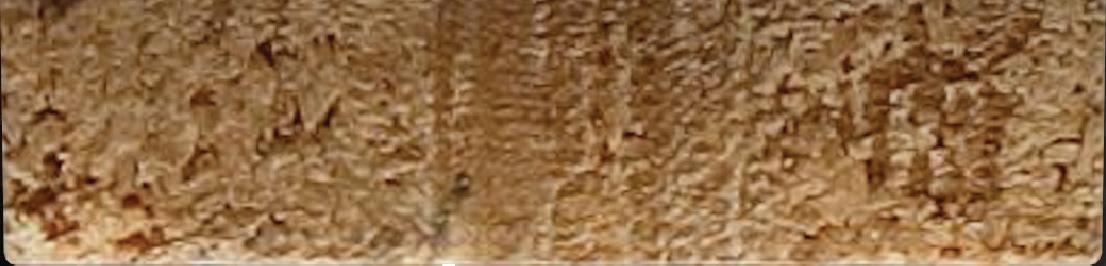

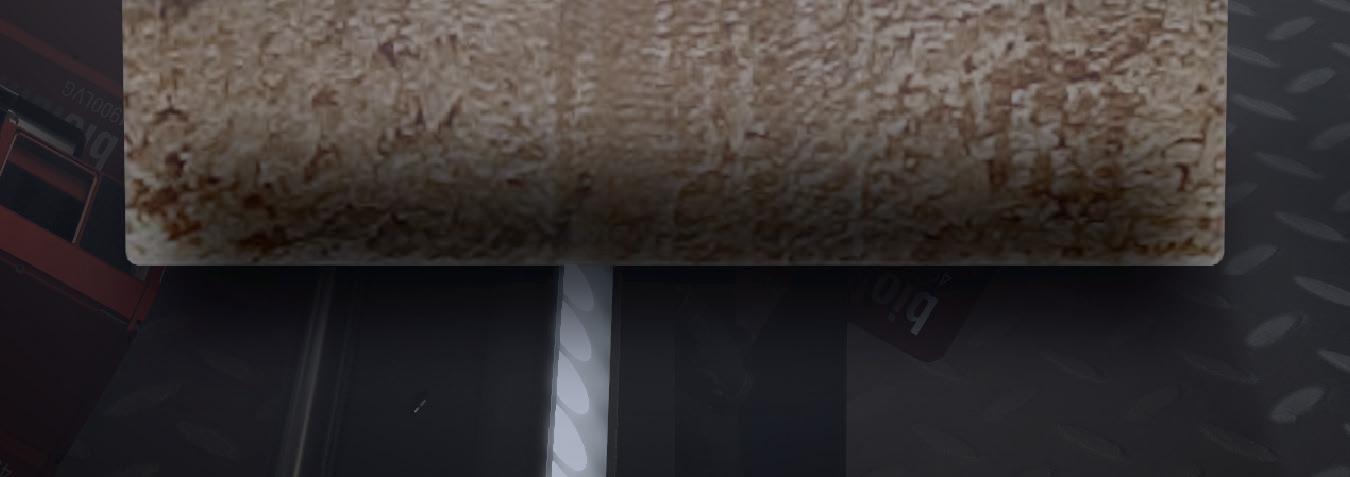
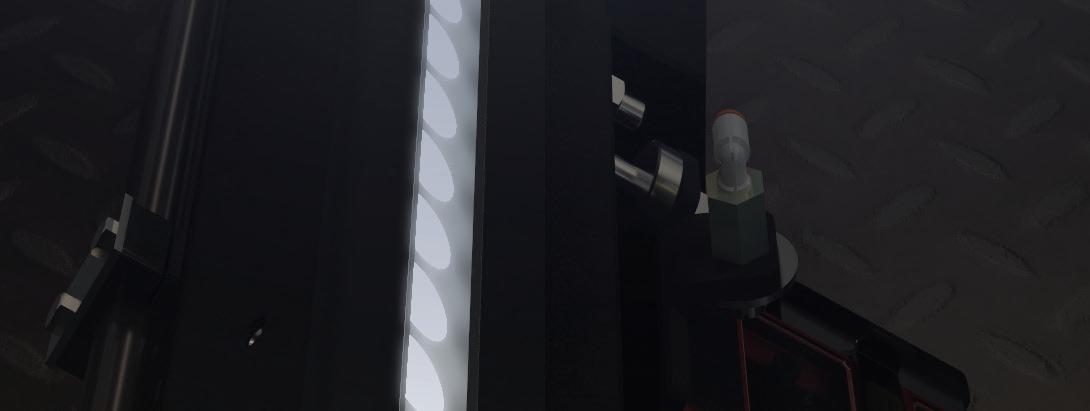
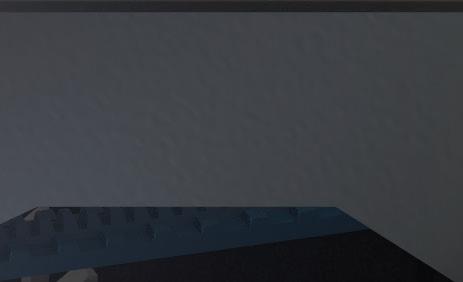
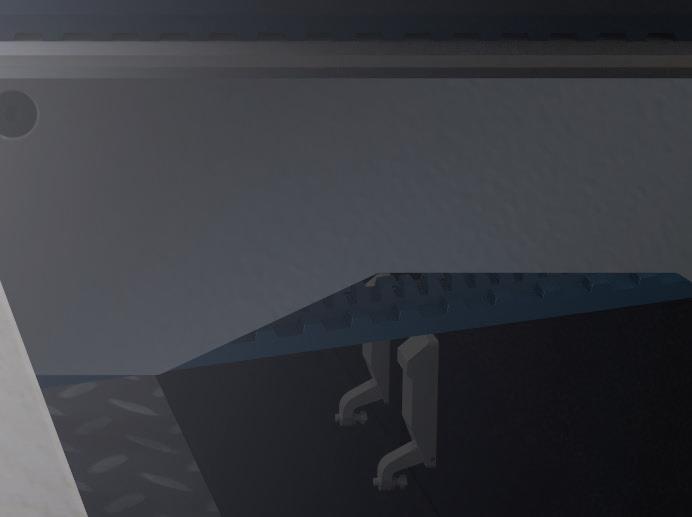

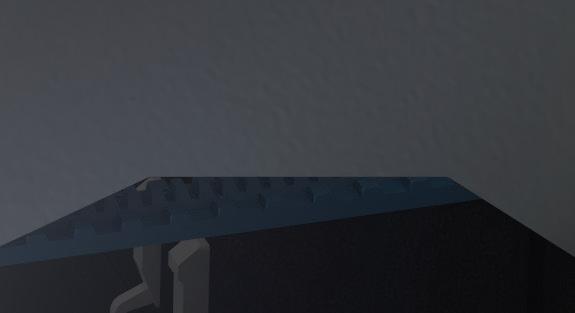
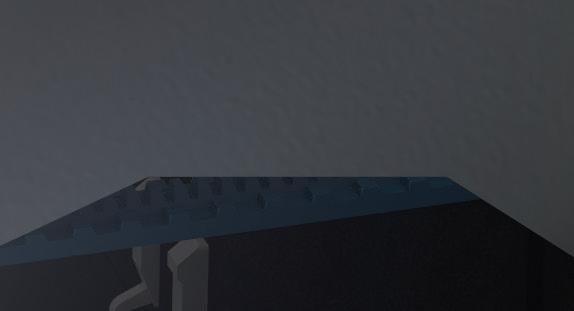


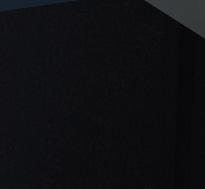
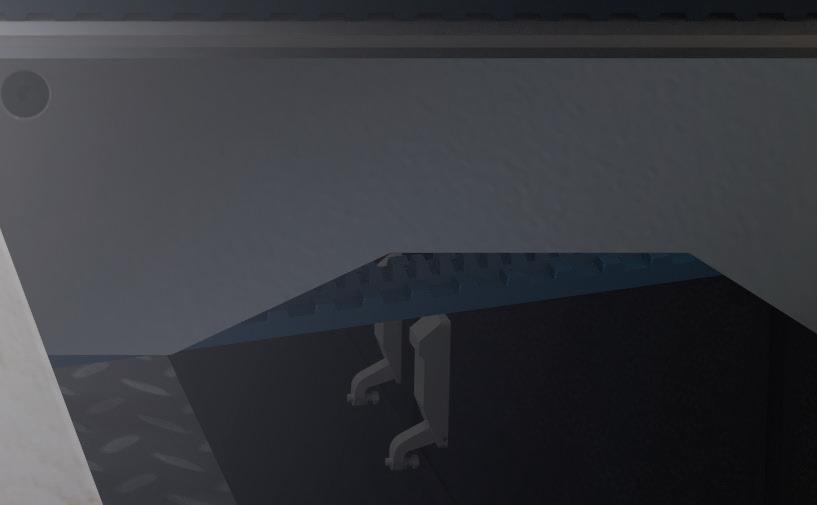
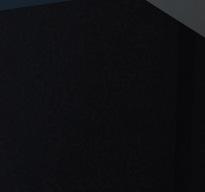

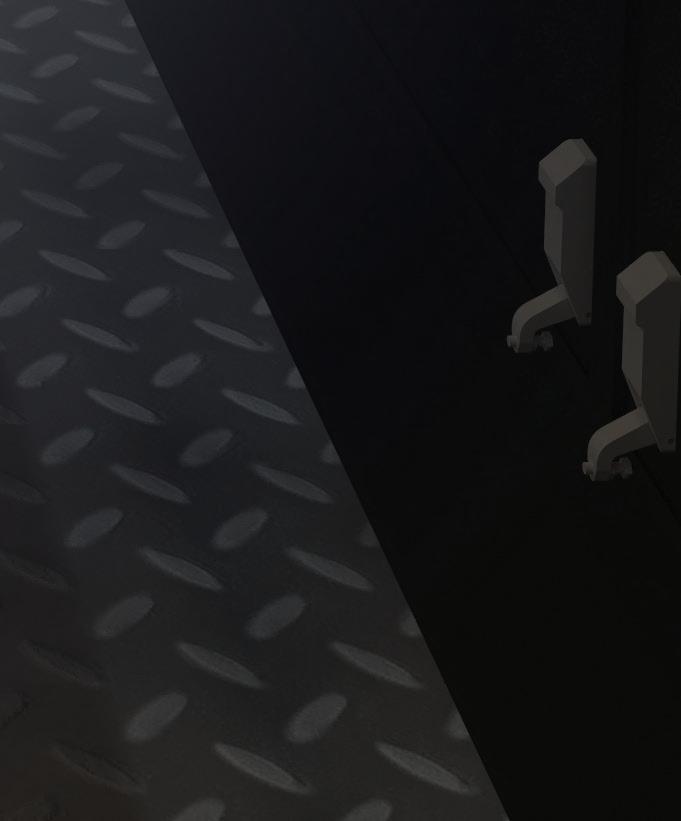
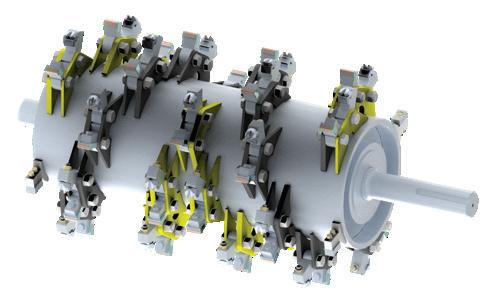

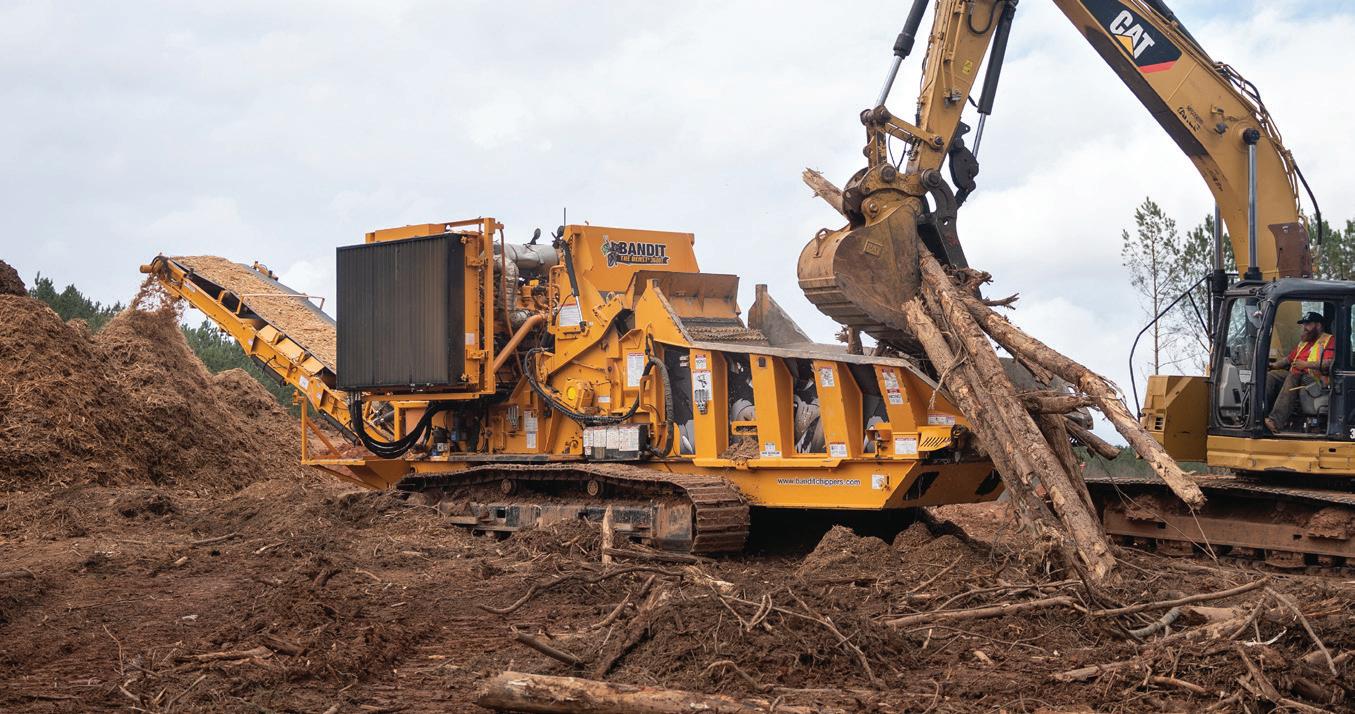
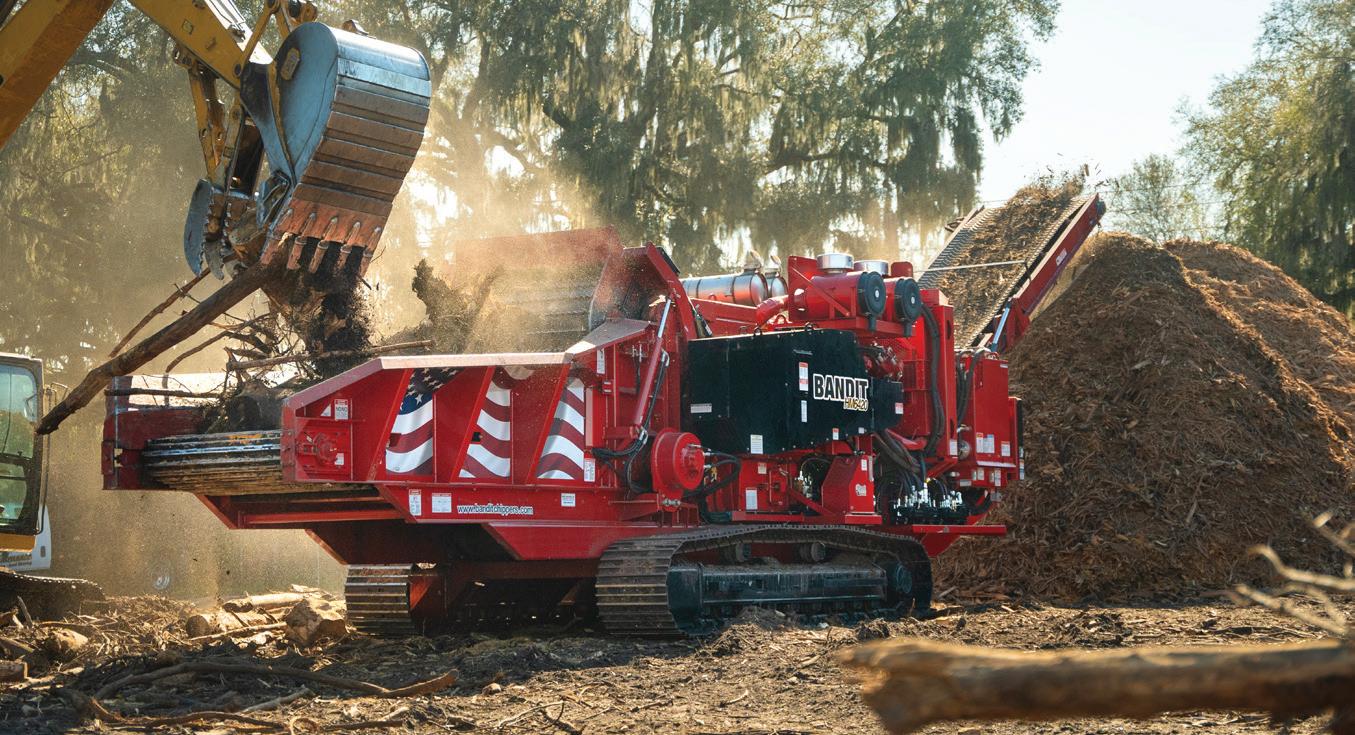
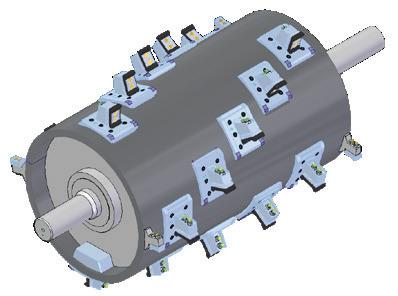
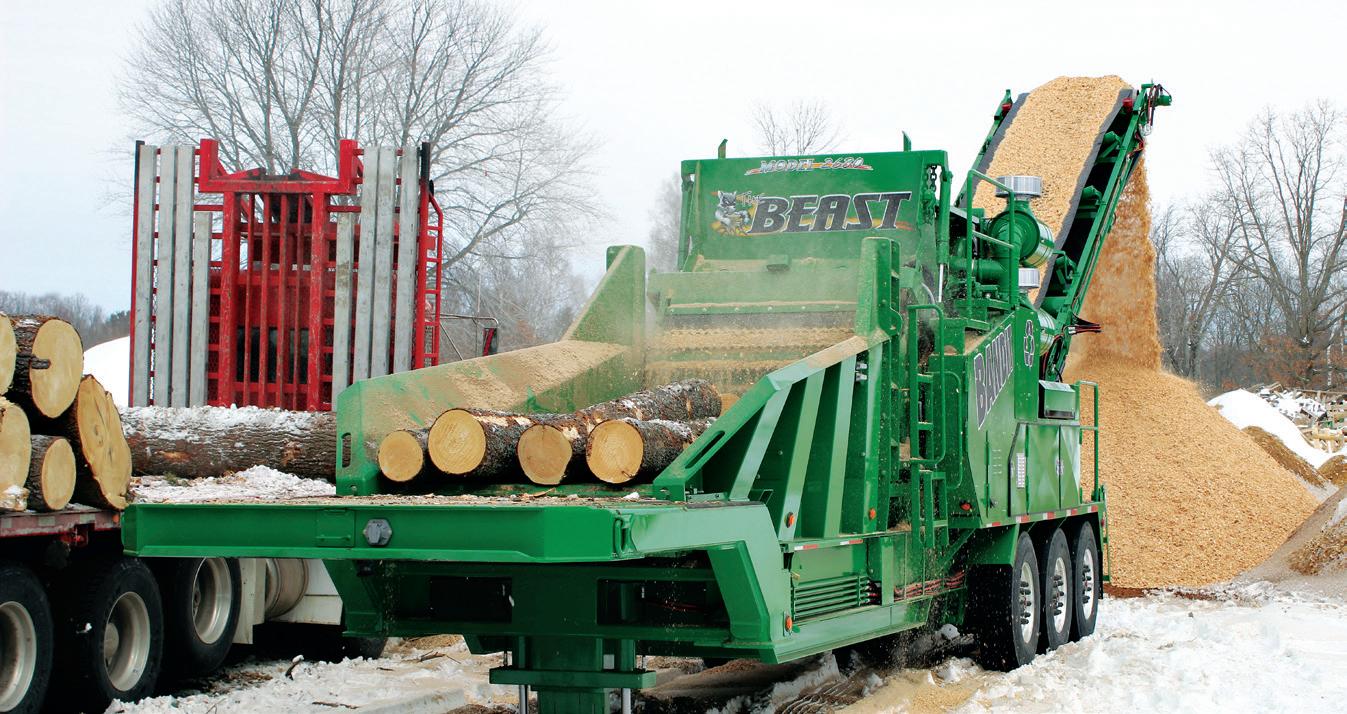

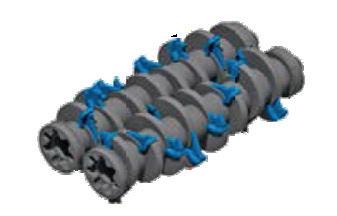
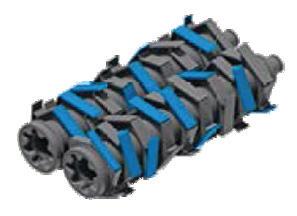
SAWLINES
Shredders & Grinders
Skidders
42 TIGERCAT - SKIDDERS
Tigercat H-series four-wheel and six-wheel skidders are designed for serviceability, reliability, efficiency, and operator comfort
/ SEPTEMBER
COVER - USNR
18 FAE - TRACKED CARRIER
FAE updates its top-of-the-line tracked carrier. Introducing the PT550
The world of automation is common today in the forest products industry, ushering in a new era of smart mill technology. And USNR is on the front lines of that effort.
From the use of deep learning AI in our highly innovative automated grading systems, to SAM’s on-the-fly machine adjustments that automatically correct cutting and positioning errors, USNR advancements lead the pack.
Artificial intelligence is now active on all our auto-grading platforms, delivering even more value and recovery while reducing startup times. We’ve also applied this advanced grading technology upstream in sawmill edger and trimmer applications optimizing for maximum recovery and value.
Visit TPEE booth #711
SUBSCRIPTIONS
SUBSCRIPTIONS
Tel: +44 (0)1442 877 583 emma@internationalforestindustries.com
Tel: +44 (0)1442 877 583 emma@internationalforestindustries.com
Annual Subscription
Annual Subscription
U K and Europe £160, € 230 Rest of the world US$270
U K and Europe £160, € 230 Rest of the world US$270
EDITORIAL
EDITORIAL
T: +44 (0)1442 877 583
T: +44 (0)1442 877 583
F: +44 (0)1442 870 617
Lwww.internationalforestindustries.com
F: +44 (0)1442 870 617 www.internationalforestindustries.com
2 Claridge Court, Lower Kings Road Berkhamsted, Herts. HP4 2AF, UK
2 Claridge Court, Lower Kings Road Berkhamsted, Herts. HP4 2AF, UK
Editor
aunched in 2007 as a sister publication to International Mining, International Forest Industries has grown to become a leading and influential voice in the global forestry sector.
Climate Change Policies: Introduction of policies aimed at reducing carbon emissions from deforestation and forest degradation, such as REDD+ (Reducing Emissions from Deforestation and Forest Degradation).
Robin Peach robin@internationalforestindustries.com
Editor Robin Peach robin@internationalforestindustries.com
Editorial Board
Kevin Lapham
Dr Patrick Moore – Chairman and Chief Professor Piotr Paschalis-Jakubowicz –Warsaw Agricultural University (Poland)
J.P.Media Inc
Mr Kim Carstensen
Tel: +1 (630) 420 9752
Fax: +1 (630) 420 9763
Director General Forest Stewardship Council
Eduardo Morales
Email: lapham@jpmediainc.com
South American Forestry Consultant
WEB OPTIMIZATION
Jo English
ADVERTISING AND PROMOTIONS
ADVERTISING AND PROMOTIONS
International Forest Industries Ltd
International Forest Industries Ltd
Advertising Manager
Advertising Manager
Over the years, it has earned a reputation for delivering comprehensive coverage on the latest trends, technologies, and developments in forestry and wood processing. With a focus on innovation, sustainability, and industry challenges, IFI serves as an essential resource for professionals, decision-makers, and stakeholders across the forestry supply chain, contributing significantly to the advancement of the industry worldwide.
I thought I would look at world issues arising across this period :
2016-2019:
Technological Advances & Trade Issues
Technological Innovations: Advances in sawmilling technology, including automation and improved efficiency in wood processing.
Trade Disputes: Tensions between major timber-producing countries, such as the softwood lumber dispute between the U.S. and Canada, impacting trade dynamics.
Emma Smith emma@internationalforestindustries.com
Emma Smith emma@internationalforestindustries.com
jo@internationalforestindustries.com +44 (0)1442 877 583
+44 (0)1442 877 583
Publisher
Associate Editor
Robin Peach robin@internationalforestindustries.com
Robin Peach robin@internationalforestindustries.com
Advertising Production Enquiries
Advertising Production Enquiries
Emma Smith emma@internationalforestindustries.com
Emma Smith emma@internationalforestindustries.com
Studio Manager
Luke Evans luke@lecreative.co.uk
International Forest Industries is published by International Forest Industries Ltd,
Accounts
2 Claridge Cour t, Lower Kings Road Berkhamsted, Her ts. HP4 2AF, UK
Nicola Shukla nicolas@internationalforestindustries.com
International Forest Industries (ISSN 1755-6732) is published bi-monthly by International Forest Industries Ltd GBR and is distributed in the USA by Asendia USA, 17B South Middlesex Avenue, Monroe NJ 08831 and additional mailing offices. Periodicals postage paid at New Brunswick NJ. POSTMASTE R: send address changes to International Forest Industries, 17B South Middlesex Avenue, Monroe NJ 08831
© International Forest Industries Ltd 2007 – 2019 I FI uses, as preference, SI units throughout. All dollars are US unless otherwise stated.
International Forest Industries is published by International Forest Industries Ltd, 2 Claridge Cour t, Lower Kings Road Berkhamsted, Her ts. HP4 2AF, UK International Forest Industries (ISSN 1755-6732) is published bi-monthly by International Forest Industries Ltd GBR and is distributed in the USA by Asendia USA, 701C Ashland Avenue, Folcroft, PA 19032 and additional mailing offices. Periodicals postage paid at New Brunswick NJ. POSTMASTE R: send address changes to International Forest Industries, 17B South Middlesex Avenue, Monroe NJ 08831 © International Forest Industries Ltd 2007 – 2023 I FI uses, as preference, SI units throughout. All dollars are US unless otherwise stated.
The forestry and sawmilling industries have faced numerous challenges and changes since 2007. These issues encompass environmental, economic, technological, and policy dimensions. Here’s an overview:
2007-2010:
Economic Downturn & Forest Management
Global Financial Crisis: The economic downturn led to reduced demand for wood products, impacting sawmill operations and forestry management.
Sustainable Forest Management: Increasing emphasis on sustainable practices to balance economic needs with environmental preservation.
2010-2015:
Environmental Concerns & Policy Changes
Deforestation and Conservation: Ongoing concerns about deforestation, especially in tropical regions, leading to efforts to promote conservation and sustainable forestry.
Certification and Standards: Growth in forest certification schemes like FSC (Forest Stewardship Council) and PEFC (Programme for the Endorsement of Forest Certification) to ensure sustainable practices.
Urbanization and Land Use: Increasing urbanization leading to land-use changes, affecting forest areas and management practices.
ROBIN PEACH EDITOR
September 25-27 2024
Timo Savornin has been appointed as Ponsse Area Marketing and Communications Manager, Europe & North America and member of the Ponsse global dealer development team as of 5 August 2024. In his role Timo is responsible for the marketing activities in Europe & North America, managing marketing and customer and
dealer communications as well as working for global dealer development.
Timo has 15 years of experience as Area Manager, North America and Sales & Marketing Director for several harvester head manufacturers, most recently at Nisula Forest. He has also worked as harvester and forwarder operator in Finland and France.
Timo has a degree in Forestry Engineering and Forest machine operator.
Timo will be located in Finland, and he will report to Jussi Hentunen, Area VP of Asia and Sales Excellence Team Lead.
Ponsse presents new functions that support the forest machine operators in their daily work and help the forest contractors to follow up the profitability and productivity of the machine park.
These new features are the PONSSE Scale crane system, which manages load data during all work steps, and the PONSSE High-Precision Positioning solution, which helps the machine operator know the exact position of the machine and harvester unit. They also present a material concept for a cargo space in fossil-free material. Ponsse is the first forest machine manufacturer in the world to be able to display a part of a forest machine made of fossilfree steel from SSAB.
At the factory in Vieremä, Ponsse have manufactured a cargo space for a PONSSE Buffalo forwarder made of fossil-free steel from SSAB. This is a material concept that investigates the processability, properties and behavior of the new material for use in the manufacture of forest machinery. The cargo area is designed for material testing only and does not correspond to the production models.
The material concept is part of the ecosystem project FORWARD27.
PONSSE Scale
PONSSE Scale is a crane scale system that weighs, sorts, saves and processes load data during all stages of work. Weighing data collected facilitates load management. Exact weight measurements ensure that the load is optimal at all times.
The system provides fully automated weighing during both loading and unloading with detailed load registration.
weather resistance, with accurate results both in hot summer temperatures and in freezing winter temperatures. PONSSE Scale can be installed on all Ponsse forwarders.
PONSSE High-Precision Positioning is a solution that helps the machine operator know the exact position of the machine and the harvester unit. This enables the efficiency of the felling operation to be maintained, even under varying
It does not affect the weighing results if the load is gripped in the middle or towards the edges. Load data, load logbooks and measurement accuracy data are available in easy-to-read reports. The PONSSE Scale has excellent
conventional positioning systems often cannot achieve.
By defining the exact position of the harvester unit and displaying it in a map view, High-Precision Positioning can greatly increase harvesting productivity. The solution clearly shows where the operator should cut and which areas should be avoided. The location of each felled tree is saved in the production file, and the paths created by the harvester are clearly displayed to the forwarder.
The new solutions improve productivity and safety in the business. They also ensure that the site is completed reliably and responsibly on time and on budget.
High-Precision Positioning is available in Finland, Sweden and Germany for all PONSSE harvesters equipped with Active Crane, also for retrofitting. Availability in other markets will be announced later.
For more information
Marko Mattila, Chief Sales, Service & Marketing Officer, marko.mattila@ponsse.com
conditions.
Using industry-leading navigation and positioning tools alongside Ponsse’s own advanced technologies such as Active Crane, High-Precision Positioning can raise the bar for reliability to a level that
Katja Paananen, Chief Responsibility Officer, Ponsse Plc, katja.paananen@ponsse.com
The Log Max 5000V is a modern and reliable harvesting head that can handle a wide range of logging challenges. This is the perfect mid-range head for both thinning and final felling. The head can be equipped with a 82 cm saw bar and has a maximum cutting diameter of 74 cm. It also features Log Max’s Multi-stemming MK2, that is agile and lightweight, making thinning work easier. The Log Max 5000V is suitable for those who seek the perfect balance between agility, capacity, and durability.
What customers say:
“The cutting and feeding are brutally good and in combination with the new length measuring unit, Log Max is unstoppable ; )”
Forico has invested in two New Generation Wagner L90 Logstackers for its mills in northern Tasmania, the first of the new generation machines to be commissioned in Australia.
The two new ‘Wagners’ arrived at Long Reach Mill in the East Tamar and Surrey Hills Mill in Hampshire, Tasmania in May 2024. After assembly and training by the North American manufacturer Allied Systems and specialist cargo handling company Quality Marshalling of New Zealand, the machines were commissioned and put into use in the log-yards in early June.
Recognising the need to update their fleet, the Forico Board had approved the purchase in April 2022, a significant capital expenditure outlay and investment in supply chain. The machines in use until that time had been purchased in 2015 and had been in service for in excess of 26,000 hours.
“The Wagners are also considerably more fuel efficient and have lower overall maintenance costs compared to front end loader machines used over the same operating period,” said Tim Duncombe, manager at Forico’s Long Reach Mill.
The New Generation L90s were transported from America by sea and road after a lead time of around 18 months on delivery due to demand for machines and worldwide challenges on the availability of components. Making the journey from Portland USA to
Melbourne, on to the port at Devonport and then on to the mill sites by road, the unique machines would have caused some ‘head scratching’ as they were driven under escort to their final destination, said Mr Duncombe.
Manager at Forico’s Surrey Hills Mill Paul Sturzaker said the operational teams had identified the need for additional handrailing to protect operators exiting the cab, but beyond that the newly designed Wagner unit would significantly improve visibility and handling.
Forico is the largest private forestry and asset manager in Tasmania, managing 89,000 hectares of plantation forest for wood fibre production, and 77,000 hectares of natural forest for conservation, biodiversity and cultural values.
2020-2021: COVID-19 Pandemic
Supply Chain Disruptions: The pandemic caused significant disruptions in global supply chains, affecting the availability and price of wood products.
Labor Shortages: Restrictions and health concerns led to labour shortages in both forestry operations and sawmills.
Increased Demand: A surge in demand for wood products, particularly for home improvements and construction, leading to price volatility.
2022-2024: Environmental Policies and Market Dynamics
Policy Developments: New policies and regulations aimed at combating illegal logging, promoting sustainable trade, and supporting forest-dependent communities.
Key Issues and Trends
Sustainable Practices: Increasing emphasis on sustainable forest management to ensure long-term ecological and economic viability.
Climate Change Mitigation: Forests play a crucial role in carbon sequestration, making their management vital for climate change mitigation efforts.
Technological Advancements: Innovations in sawmilling and forest management technologies are driving efficiency and sustainability.
Sustainability and Carbon Sequestration: Enhanced focus on forests as carbon sinks, with policies promoting afforestation and reforestation.
Wildfires and Pest Infestations: Increased frequency and severity of wildfires and pest infestations (e.g., bark beetles), driven by climate change, affecting forest health and productivity.
Technological Integration: Continued integration of advanced technologies like remote sensing, GIS, and AI in forest management and sawmilling for better resource management and efficiency.
Economic Recovery: Post-pandemic economic recovery influencing market demand and investment in the forestry and sawmilling sectors.
Global Trade Dynamics: Trade policies and disputes continue to shape the global timber market.
Environmental Challenges: Addressing deforestation, wildfires, and pest infestations remains critical for maintaining forest health.
The forestry and sawmilling industries are at a crossroads, balancing economic growth with the urgent need for sustainable and environmentally responsible practices.
Its important the timber industry is seen to plant substantially more trees than it harvests. A positive note is the world will always need timber!
ROBIN PEACH EDITOR
in
The 6900 is a heavyduty up swing horizontal grinder designed for high production and maximum flexibility. The versatility of the 6900 makes it the perfect solution for grinding a variety of materials such as forest biomass from logging operation, trees, stumps and root mass from land clearing operations, demolition debris and scrap sawmill material.
The rotor is belt driven and uses a tensioner system to engage the drive belt, eliminating the need for a clutch. The tensioner system is hydraulically controlled and can be lowered while in service mode, so that the rotor may be turned manually when changing tips or knives. Another unique feature of the 6900 is the pivoting frame. The upper frame pivots on the undercarriage, allowing the operator to adjust the infeed angle and discharge height. The infeed pivots down 4 degrees for feeding long trees and allows the discharge to clear large piles. Pivot the infeed up 7 degrees to act like a hopper which helps in
feeding branches and brush. With the infeed in the up position, it also brings the height of the machine to under 3,6 m (12 ft) for shipping, eliminating the need for a troublesome folding discharge conveyer.
Thick steel plate infeed walls are tapered to assist in directing the feedstock into the hog box. The discharge uses a 510 mm (20 in) head pulley that is available as magnetic or non-magnetic. The large diameter allows the use of a more durable three-ply discharge belt. It also holds onto the tramp metal longer so that it drops away from the discharge pile. For increased metal removal, an optional over band magnet is available. The entire underside of the discharge is open to prevent buildup of material.
The split hog box design on the 6900 opens fully for easy servicing of the rotor and grates. The grate assembly consists of three separate liner sections that sit in the grate frame. The grate frame hydraulically retracts for easy removal and installation of the liners. Optional liners are available for a variety of grinding applications.
The 6900 features an impact detection system that is designed to mitigate damage to the machine in the event that tramp metal enters
the hog box. When a foreign object enters the hog box, an accelerometer detects a change in rotor speed. When this occurs, the feed chain and feed wheel reverse direction, and the grate frame retracts.
If the foreign object remains, shear pins will break, allowing the grate frame to open further. A large enclosed control panel located on the side of the 6900 houses the machine computer control display, start/stop switch, diagnostic ports and remote control with charging cradle. When operation is transferred from the computer control display to the remote, operation from the display is removed. A tethered control is stored in the toolbox and allows the machine to be moved forward and reverse, and pivot the discharge up and down.
The upper frame pivots on the undercarriage, allowing the operator to adjust the infeed angle and discharge height.
Introducing the Tigercat LS857 – a high performance shovel logger with increased leveling capability.
The unique sloped tail of the LS857 allows greater leveling angles and provides winch assist chain clearance. Optimized weight distribution, along with Tigercat’s legendary super duty leveling undercarriage, delivers exceptional stability on steep terrain.
With several boom options, the LS857 can be equipped with a variety of grapple styles, or the Tigercat 5195 directional felling saw for felling and shovel logging with a single machine.
Bandit’s HM6420 is available with screens up to 7 inches and includes an impact detection system that shuts the system down gently if a contaminant is struck inside the grinding chamber. (Photo courtesy of Bandit.)
system to attach the holders to the mill, and each holder recesses into the mill pocket to enhance durability.
The recently introduced Bandit HM6420 tracked horizontal grinder is a heavy-duty workhorse. It features a 50-inch (127-centimeter)-diameter by 66-in. (168-cm)wide hammermill that incorporates 1.75-in. (4.4-cm) drum skin formed from rolled plate. The machine’s Cat C32 engine is rated for 1,200 horsepower (895 kilowatts).
Bandit showcased the HM6420 at the recent Compost2024 trade show in Daytona Beach, Florida.
Bandit says the HM6420 is well-suited for grinding material that may contain contaminants, thanks to its standard impact detection system that idles the grinder down and disengages the clutch if it detects an impact event.
Bandit’s HM6420 Hammers It
The HM6420 joins a Bandit lineup of horizontal grinders comprising machines designed to either “cut it,” “chip it,” or “hammer it.” This latest
“hammer it” solution has a 40- by 64-in. (102- by 163-cm)wide mill opening and a 7-in. (17.8-cm) main shaft that Bandit constructs of alloy steel and tests ultrasonically. The grinder’s pockets feature high-strength A-514 steel construction.
The HM6420 also puts to work 20 carbide-infused hammer inserts that Bandit says can stand up to the toughest material. The company uses a patentpending quick-change pocket
The HM6420’s combination of a directly driven doubleslat, track-type steel infeed conveyor, which measures 16 feet (4.9 meters) long by 64 in. (163 cm) wide, and a directly driven 64.75-in. (164-cm)-wide floating feed wheel allows it to grind huge quantities of material at once. The conveyor can generate over 18,000 pounds (8,165 kilograms) of pulling power, and the feed wheel adds another 17,000 lbs (7,711 kg) of pulling power and 8,650 to 17,300 lbs (3,924 to 7,847 kg) of downforce when using hydraulic pressure.
Bandit says the HM6420 has one of the market’s fastest feed rates at 82 to 132 ft (25 to 40 m) per minute. The grinder’s proportional feed system lets operators adjust the feed according to the material they’re processing, and they can do so using the machine’s radio remote with tether backup. The machine has a 56-in. (142-cm) dual-discharge system with a 16.6-ft (5.1-m) stacking height.
Introducing the Combi-CLL Log Loader, based on the highly successful Combi-CSS Container is incredibly fast compared to other methods. It can fully load logs into a 40’ container in under 6 minutes to a 30t capacity. The risk of accidents to the workforce is minimised and product damage is eliminated.
The Logs are pre-loaded into the robust, 40’ long high-sided Tub. The patented push-pull mechanism powers the loaded Tub into the container. Once inside, the Hatch is closed to hold the logs securely in place, and the Tub is retracted.
To find out how Combilift can help you unlock every inch of your storage space.
Carbotech Group has announced an agreement with Woodtech, marking another important step in the sale of advanced technological solutions for the forest industry. Under this agreement, Carbotech Group will become the exclusive representative and manufacturer of Woodtech’s innovative Logmeter. Carbotech Group, with its Autolog unit, will also provide technical support during and after the start-up of the Logmeter.
Logmeter is an automated system that provides high-precision volume measurements and biometric assessments of logs or stems in real time, as they are loaded onto trucks before entering the sawmill sites. By delivering accurate and timely data,
Logmeter enables informed decision-making that improves operational performance, strengthens supplier relationships, and enhances product quality. This leads to significant cost reductions and increased profitability. Logmeter is already used by several customers in USA, including T.R. Miller and Shuqualak.
Woodtech, the owner of Logmeter, is a high-tech company specialized in the design, development, and maintenance of cuttingedge industrial solutions. Its innovative products digitize, interpret, and measure industrial processes in real time, offering unparalleled advancements in accuracy and efficiency. Backed by its extensive knowledge and
experience in the forestry industry, Woodtech ensures that Logmeter is an invaluable tool for any sawmill.
“We are excited to collaborate with Woodtech and increase the use of the Logmeter system in the U.S. and Canada,” says Eric Michaud, VP Sales & Marketing at Autolog/Carbotech. “This partnership once again shows our commitment to providing cutting-edge technologies that enhance operational efficiency and accuracy in the forest industry.”
Carbotech Group was formed in 2021 with the acquisition of Autolog, a company that specializes in the optimization and automation of sawmill and planer mill processes. Many of its solutions now use artificial intelligence. Carbotech Group later acquired a company called Sawquip, which specializes in log breakdown equipment and sawlines; the brand now operates under the Carbotech name. With its three business units (including Carbotech, which specializes in the log and lumber handling area), the company can offer a comprehensive solution for
Eric Michaud, VP Sales & Marketing at Autolog/ Carbotech.
sawmills and planer mills. including installation on customers’ sites, start-up services, and tailored training and service plans. These business units have now been providing the industry with innovative solutions for 37 years.
For more information, please contact:
Eric Michaud VP Sales & Marketing Carbotech Group eric.michaud@carbotech.ca
The new high-performance chain biolubricant for forestry applications
Engineered for full chain lubrication to provide an active barrier against sawdust and dirt.
Helping to protect your equipment for longer!
FAE updates its top-of-the-line tracked carrier. Introducing the PT550: the tracked carrier for big challenges.
FAE has completely updated its top tracked carrier, introducing the PT550 to replace the PT475. The PT550 is the FAE tracked carrier for big challenges, ideal for major jobs in large, wooded areas and along oil and gas pipelines. Capable of working on large areas of soft, uneven or swampy ground, this vehicle can handle longitudinal slopes up to 45° and transverse slopes up to 32°. All this thanks to a low ground pressure of 0,41 kg/cm2.
This new vehicle has many updated features, from design changes to technological upgrades, starting with the completely redesigned cab for added operator comfort and safety. The PT550’s Cat. 2 ROPS/ FOPS/OPS approved cab has a new configuration and an integrated cabin pressurization system, an industry benchmark. Other improvements for added operator comfort and productivity include large Lexan glass windows, ergonomic joysticks, a pneumatic seat, a large 10” touch screen display to control all operating functions, a 360° camera system and display, and a heated and refrigerated compartment with cup holder.
The Caterpillar C13B sixcylinder engine in the FAE PT550 guarantees strength, reliability and global support. Equipped with a turbocharger with after cooler, the Tier 4 Final/Stage V engine delivers 536 hp. The combined diesel particulate filter (DPF), selective catalytic reduction (SCR) and diesel oxidation catalyst (DOC) guarantee compliance with Tier 4 Final/ Stage V. The PT550 is also available with a Tier 3/Stage
most demanding conditions. The lubricated track chains last longer than conventional chains and provide a smoother ride. When combined with the reliable dozer-type rollers and oscillating undercarriage technology, the PT550 offers superior grip and comfort. There are two roller guard options to adapt perfectly to different environments. The conventional geometry means a low center of gravity and optimal contact between the chain and the drive wheel, two fundamental elements that provide the best performance, even on slopes. The FAE PT550 wheelbase also extends the load distribution area, which means lower specific pressure against the ground. The undercarriage frames are designed to withstand major stresses and make maintenance easier.
The PT550 can be equipped with a forestry mulcher or a multitask head to crush stone and till soil. Each machine can benefit from Active Power Management technology, which combines the Floating System function with the Load Control function, ensuring that the head always precisely follows
III A engine for emission-free markets, rated at 475 hp. The large 12.5-liter displacement and the electronically controlled proportional and reversible fan cooling system, designed specifically for the FAE PT550, guarantee superior performance for heavy jobs and in tropical climates.
The FAE PT550’s heavy-duty undercarriage is designed to provide superior performance and reliability, even in the
along the ground and that the power is managed effectively during operation. Combined with the 300/U/SONIC and 500/U/SONIC forestry mulchers, FAE’s exclusive Sonic technology enables the head to work at maximum capacity at all times. Sonic technology adjusts the torque in real time according to the force required, for up to 30% higher productivity.
BATTLE CREEK, MICH —
Opticom Tech, a leader in industrial video monitoring solutions, has announced a groundbreaking advancement in industrial camera technology. Opticom’s cameras now offer the unprecedented ability to deliver 10 simultaneous video streams from a single camera, setting a new industry standard.
Opticom Tech cameras can now pull 10 video streams from a single unit—a significant leap from the industry standard of three streams. This capability is a game-changer for industrial facilities, allowing multiple stakeholders—such as operators, managers, supervisors, and security personnel—to access real-time footage simultaneously without
having to access the software. Each team member can monitor critical areas without any delay or interruption.
“We are incredibly proud to introduce this innovative feature that our customers have been asking for,” said Heidi Schmidt, Global Sales Manager at Opticom Tech. “Our new 10-stream capability not only enhances security and operational efficiency but also demonstrates our dedication to hearing feedback from customers and developing products based on their needs. This advancement will undoubtedly set a new benchmark in the industry.”
Opticom’s cameras are designed to meet the rigorous demands of industrial environments, providing reliable and high-quality surveillance. This new feature will be available across all Opticom camera models, ensuring that every customer can benefit from enhanced functionality and improved operational oversight.
Heidi Schmidt, Global Sales Manager at Opticom Tech
Founded in 1973, Opticom Tech provides integrated video monitoring solutions for industrial applications, including sawmills, mines, food processing facilities, and more. Built to withstand harsh environments, Opticom’s rugged cameras and equipment stand the test of time.
www.opticomtech.com
Efficient, clean and safe: this is how we envision future off-road operation with intelligent system solutions.
As a full-range supplier, we supply comprehensive drive systems for off-road machinery from one source. We develop axles and transmissions with advanced software functions and combine them with state-of-the-art braking technology, connectivity and safety solutions. Our answer to meeting the industry’s challenges: comprehensive and intelligent system solutions, thoroughly matched to each other. In doing so, we always keep an eye on reducing emissions and remain on our path to Vision Zero. ZF.com/construction
September 25-27
USNR - Leading advanced technology solutions for lumber production
USNR - Blades, knives, and tooling; automated sharpening and levelling systems
Booth # 711
Booth # 725
BID is a leader in operational lifecycle excellence, transformational wood processing technologies, and integrated solutions.
MiCROTEC is one the most trusted scanning & optimization providers for the sawmilling and wood processing industry.
State of the art wood conveying, sorting, grading, and automation processes.
Today’s sawmills require dependable, easy-to-use 3-D scanning – that’s why mills rely on JoeScan scanners for bucking, carriages, sharp-chains, edgers, gangs, trimmers and more.
A global leader in 3D scanning and inspection, LMI Technologies works to advance quality and productivity with 3D sensor technology.
Leading manufacturer of precision motion controllers for servo-hydraulics and servo-electric motion.
The Largest Manufacturer Of Multidirectional, Sideloading And Articulated Forklifts Globally.
Booth # 627
Booth # 409
Booth # 309
Booth # 337
Booth # 527
Booth # 841
Booth # 1025
A market leader in all aspects of the CCTV industry. Booth # 151-1
With over 45 years of experience creating wood hogs for the forest and sawmill-related industries, Rawlings consistently demonstrates a reputation for durability, performance, and reliability.
HALCO Software’s business is computer simulation and off-line optimization of forest industry operations.
Booth # 237
Booth # 960
Microtec CT Log X-ray scans all logs entering the sawmill
New X-ray technology at Norra Timber’s sawmills in northern Sweden will be able to identify the internal properties of logs, such as knots and other imperfections.
“Our investment amounts to a substantial total of SEK 400 million”, says Norra Timber’s Industry Manager, Henrik Jönsson
The sawmill in Sävar bought its first X-ray equipment back in 2017, which led to an increase in production of 6,000 cubic meters of timber planks a year - equivalent to 100 fully-loaded truck trailers. Now Norra Timber has bought even more advanced equipment, which it hopes will lead to an additional increase in profits.
In addition to providing information on how the logs should be turned to produce more planks, the new equipment utilizes AI to provide information on the
quality of the log and the type of products that different parts of the log are most suited for.
“The equipment produces X-rays just like in a hospital. The difference is that this scanning is faster. Each log only takes two seconds to process”, says Jönsson.
Norra Timber is investing a total of SEK 400 million in the new equipment being installed at its sawmills in Sävar and Kåge in northern Sweden. The new X-ray technology, which should be completely operational by the autumn of 2025, will be utilized at the very beginning of the production process. As trucks arrive with the logs, each log will be scanned to calculate dimensions and provide an overview of the log’s internal properties.
“By scanning the logs from the outset we can sort them according to their quality and unique internal properties. If a customer wants highquality planks for furniture without knots that are suitable for undergoing the special drying process required, we can identify which logs would be best before we even start sawing them”, says Jönsson.
He adds:
“Thanks to the X-rays we can also calculate the optimal number of planks we can generate from each log, which reduces wastage. We can therefore extract the maximum value from each log. A log with a large branch can be turned with the help of the X-ray machine so that the branch only ends up on one plank and the next plank is free of
imperfections. Logs account for 75 percent of our costs, so we want to get as much value from them as possible”.
The primary purpose of the investment is to be able to assign production data to each individual log. In the future each log can also be marked with a unique ID number - a kind of ‘log fingerprint’.
“The ability to trace our products and get data about the timber’s environmental impact will give us a competitive advantage. It will also be a driving force in how we can improve our environmental credentials”, says Jönsson, who concludes:
“By mapping each plank we can easily go back and see if something has gone wrong during the production process. We can also see how much energy was used for each product, which gives us much better control over costs and our environmental impact”.
This latest investment will ensure Norra Timber’s sawmills continue to be at the technological forefront of its industry and remain competitive in the years to come.
Norra Timber is a wood processing company that manufactures and delivers products to markets with high expectations concerning quality, capacity and accurate deliveries. Their sawn and added value products come from unique, slow-grown trees that have matured almost 100 years in the forests of northern Sweden.
Cutting capacity: Up to 8.5 million board feet of wood in two-shift operation.
Log diameters: 10 to 42 in, lengths: 10 to 16 ft 2 in (20 ft on request)
100% self-sufficiency: Cut your own logs, optimize production costs.
Space-saving: Optimum use of floor space from 5,400 ft² to a maximum of 10,800 ft².
Long-term predictable prices: Own production ensures stable product prices.
Sustainability and regional added value: Use of local wood, recycling of all wood waste.
Board dimensions: Wide range possible through chipper head, band and rip saws.
Green footprint: up to 75% yield, maximising log utilisation.
In the ever-evolving landscape of wood processing, a profound transformation is underway, driven by Artificial Intelligence (AI). This revolution is reshaping traditional methods and unlocking remarkable efficiency and quality across various sectors, with wood processing standing out as a prime example. At the forefront of this transformation stands BID Group, spearheading innovation and progress in the industry.
BID’s
AI’s integration into wood processing is far from being a fleeting trend; it represents a fundamental shift in how we approach wood grading, robotics, production line operations, and optimization decisions. What distinguishes BID’s AI from others is not just the technology itself but the expertise and dedication of the
team behind it. BID boasts an integrated team of specialists, including AI experts, who collaborate tirelessly to push the boundaries of what’s possible. This multidisciplinary approach ensures that BID’s solutions are cutting-edge and tailored to meet each client’s unique needs, delivering exceptional results and ensuring the fastest ROI in the industry.
BID’s Smart Vision technology is a prime example of this innovation. Designed to help sawmills and planer mills streamline their operations and prevent costly jams and breakages, Smart Vision harnesses the power of AI to analyze images and identify
Safety is paramount in any industrial setting, and wood processing is no exception. Despite measures to ensure safety, accidents can still occur. BID’s Smart Vision technology addresses this critical aspect by stopping operations before accidents happen, thereby enhancing safety without compromising production. By minimizing the reliance on human intervention, Smart Vision reduces the likelihood of accidents and creates a safer working environment.
objects of interest in real time. This results in decreased downtime, improved process flow, and better resource allocation, ultimately driving productivity and efficiency to new heights.
The Smart Vision’s versatility allows it to be applied across various stages of wood processing. For example, at the trimming line infeed, it can detect stacked boards and distinguish them from timber or single boards, triggering mechanical actions to unscramble board stacks and reduce human intervention. This capability extends to the trimmer lug loader, where it helps control problematic boards that can cause downtime due to improper loading. The system identifies issues before the boards are loaded, allowing for adjustments in loading speed or board feeding to ensure smooth operations.
On the trimming line, Smart Vision detects anomalies such as skewed boards, broken
boards, and double boards in the same lug, replacing the need for photocell sensors and manual intervention. Similarly, at the trimmer outfeed/ sorter infeed, the technology identifies problematic situations like skewed boards and boards that remain on chains after being cut, ensuring efficient transition to the sorter infeed.
BID’s Smart Vision extends its capabilities to the stacker infeed/outfeed, where it detects anomalies such as gaps between boards, overlength boards, and broken boards. It also counts the number of boards in the stacker, reporting any missing or fallen boards to prevent production delays. All applications are linked to the PLC, sending alarms to notify issues and avoid stoppages and equipment breakages.
The Smart Vision’s Gap Control for Log Singulation application immediately identifies logs that are too short or too small, eliminating the need to wait for the scanner to detect them and preventing the potential ejection of good logs from the line. It solves issues such as lasers being obstructed by debris, ensuring continuous and accurate monitoring. The system provides realtime measurement of log position and size in the wave feeder, monitors deck and step accumulation, and
detects double log loading and skewed logs. It optimizes line feeding, adjusts the singulation and accumulation deck’s speed on-the-fly, and detects off-standard logs before they reach the sawline, raising alarms and stopping production for problematic logs. This proactive approach enhances operational efficiency and safety, offering advantages like more accuracy than photocells, predictive gap control based on log diameter, and comprehensive flow management. By ensuring minimal gaps and preventing downtimes, Smart Vision significantly increases productivity and ensures smooth, reliable operations without the need for photocells in the outfeed conveyor.
One of the standout features of BID’s Smart Vision is its user-friendliness. There is no need for AI-specific knowledge, making the startup process seamless. BID’s large team of wood specialists and data scientists runs extensive pre-startup tests and quality control checks to ensure a fast and effortless deployment.
BID’s commitment to constant innovation ensures that its AI-enhanced technologies are the most powerful and reliable solutions on the market. This dedication to excellence is evident in BID’s ongoing efforts to expand its digital transformation offerings with new applications of Smart Vision, covering all stages of wood processing.
Artificial Intelligence is revolutionizing the wood processing industry, offering unprecedented opportunities to improve production flow and increase profitability. BID’s AIpowered Smart Vision promises the fastest ROI in the industry, peace of mind with integrated solutions, reliable service, and consistent production quality.
Stay tuned as BID Group continues to push the limits of technology, offering evolving solutions that ensure the best results throughout the operational lifecycle. For more information on how Smart Vision can enhance your operations, contact BID now or visit www.bidgroup.ca.
Battle Ground, Washington
— All three of the Rockwell Automation ControlLogix analog motion modules, 1756-HYD02, 1756-M02AS, and 1756-M02AE, have reached end-of-life and, as of December 2024, have been discontinued and no longer available for sale. Rockwell does not have a replacement option, which leaves a need for a motion solution that Delta Motion is uniquely positioned to fulfill. Rockwell Automation recommends that OEMs and system integrators consider
RMC Motion Controllers as a replacement for these modules.
Delta’s RMC Motion Controllers can duplicate the function of the discontinued motion modules. They have the same I/O signals, communicate efficiently with Allen-Bradley PLCs via EtherNet/IP, and connect to all of the same field devices as the ControlLogix analog motion modules. Delta Motion’s sales and support team also has the expertise to support customers in converting from these modules to RMC motion controllers.
Features of Delta Motion’s RMC Motion Controllers include:
• ±10V outputs (some RMCs also have ±20mA and 4-20mA options)
• Connection to feedback devices: Quadrature, SSI, PWM, Start/Stop (analog options are also available)
• Single and multi-axis: RMCs are available from 1 to 50 axes for tightly synchronizing axes
• Command-based programming keeps most control in the PLC, or the
BID Group has announced a strategic partnership with Tough By Nature (TBN) to distribute the revolutionary WonderCoat kiln sticks across North America. This collaboration sets a new standard in the lumber industry, providing mill operators with longer-lasting, more durable kiln sticks that enhance efficiency at the stacker and significantly reduce operational costs.
Over the past six years, TBN has developed a patented coating and process for southern yellow pine, enhancing its
natural properties to exceed industry standards in strength, durability, elongation, compression, and warp resistance. This free of Volatile Organic Compound (VOC) product, applied to kiln sticks to increase their resistance, represents a groundbreaking innovation set to transform the sector.
This partnership enhances BID Group’s ability to support its customers with solutions that drive efficiency and reliability. “We are excited about this partnership,” said Simon Potvin, President
RMC User Programs can offload critical motionrelated tasks from the PLC
• Easy-to-use and powerful RMCTools software (freely downloadable)
• Analog and load cell inputs for position, pressure or force feedback
• Extensive control algorithm options, including dualloop position-pressure or position-force control
• Knowledgeable and responsive technical support 24/7/365
Now, as a Technology Partner, Delta looks forward to working with more Rockwell Automation customers to achieve the best in industrial motion control.
of Wood Processing at BID Group. “The integration of Tough By Nature Sticks into our product offerings aligns perfectly with our mission to provide innovative and efficient solutions to our clients.”
Jeff Yurk, Managing Partner at Tough By Nature, expressed his enthusiasm for the partnership, stating, “This partnership exemplifies the innovative spirit and commitment to excellence that both companies embody. We are proud to be working with BID Group as they have demonstrated innovation and
success throughout the years.” TBN’s relationship with BID Group is built on mutual respect and a shared vision for the future. The company’s extensive experience in the wood processing industry, combined with TBN’s pioneering product, ensures that customers receive the highest quality and most reliable products on the market.
Ever seen a log like this? Even with safety as a priority and measures in place to ensure it, accidents can still occur.
BID's Smart Vision can stop operations before accidents happen, increasing safety without compromising production.
• Detecting production irregularities to prevent significant interruptions and equipment failures
• Enhancing control mechanisms to optimize product singulation, maximize process efficiency, and minimize operational downtime
• Minimizing accidents through reduced reliance on human intervention
THE SYSTEM CAN BE DEPLOYED AT ANY STAGE OF THE PROCESS.
See how Smart Vision would have prevented this near miss.
Contact us to learn more.
+1 450-435-2121 | info@bidgroup.ca | bidgroup.ca
This project includes controls and comes only six weeks after the start-up of the first USNR autograder at the Enfield, ME, mill.
The performance increase at Enfield and anticipated return on investment quickly
justified replacing their existing optimization system in Dover. With this new lineal optimizer, the team at Pleasant River expects an increase in grading performance of about 10%.
The USNR VAB-brand lineal grader’s small footprint
Pleasant River Lumber Company has invested in a second USNR VAB-brand lineal optimizer that will be installed later this year at the Dover, ME, planer mill.
simplifies installation, making it easy to integrate into existing production lines. It uses measurable dimensions and AI for exceptional accuracy and can manage standard and custom grades. The lineal grader can handle a variety of species, including southern yellow pine, spruce, pine and fir, and hardwoods.
For the first time in many years, an industrial-scale sawmill will be built from the ground up in the UK.
This greenfield project is the result of years of planning and, as the main supplier, USNR is pleased to announce it to the public.
The new mill is designed for an annual capacity of more than 250,000 cubic meters of sawn goods. Its undertaking comprises the saw line and two edger lines – including optimization and controls.
All equipment will be delivered from USNR’s Söderhamn facility in Sweden.
USNR will also supply controls for the log handling and residuals handling equipment.
The saw line is designed for maximum yield, using the latest optimization technology and curve sawing capabilities.
The customer has extensive experience with USNR’s band saw technology, which is why three Sawmaster 1600 quads and an HBS 1500 horizontal band saw constitute the core of the saw line, adding up to a total of 13 band saw units.
The Sawmaster band saws are known for their durability, low energy consumption and low maintenance costs. This
proven design operates in hundreds of sawmills all over the world.
“We have a long history of cooperation with this customer, and I believe our two companies share a common confidence,” says USNR’s European Sales and Marketing Manager Christian Winlöf. “This is one of the largest projects so far for USNR’s European branch and will strengthen our position as one of the biggest and most innovative suppliers to the sawmilling industry.”
Two Catech XT high-speed edger optimizers handle the side boards. These state-of-
OneFortyOne NZ Forests is building a new headquarters in Hope, Tasman. A key feature was to show how timber can be used to achieve a cost-effective carbon-neutral build.
All the components that you would normally make from concrete and steel have, where possible, a timber alternate – with the aim that they
sequester more carbon than was released.
The sheer volume of timber in this building is a real statement around what the company, and industry, stands for. Construction has been undertaken by Irving Smith Architects, Scott Construction New Zealand and Network Tasman Limited.
Design highlights include:
• Glulam posts, the equivalent of concrete in the design.
• LVL rafters, used like steel.
• The timber floor is one of the largest ever built in the region, and with the use of screw piles, construction time was cut down by almost a third.
USNR works closely with Pleasant River Lumber Company and looks forward to the benefits they will gain from this strategic investment.
Christian Winlöf
the-art edgers are fitted with the latest USNR optimization technology, offering the highest capacity the market has to offer.
Visit
https://youtu.be/_H0TbZzxKeE
In recent years, many machine suppliers in the sawmill industry have thrived, and Jartek is no exception. While nearterm investment levels may taper off, the outlook for the distant future appears promising, with investment levels poised to rise once again.
The use of renewable materials is on the rise, with lumber emerging as a particularly favourable option. Over these prosperous years, Jartek has grown steadily while maintaining its roots as a family-owned business, with a strong focus on building partnerships.
Although investment levels have been declining in Europe, Jartek anticipates that the market will return to its pre-boom state in the coming years, where customers are more focused on addressing specific bottlenecks in their processes. This shift is not unwelcome news for Jartek, as the company has been successfully managing such projects for the past 20-30 years. Of course, the company still hopes to see larger projects come to fruition as well.
“Our goal is to be as close to the customer as possible and to truly understand their needs. We don’t want to sell any devices or solutions that won’t provide real value to the customer,” says Kari Puustinen, head of sales and marketing.
Despite Jartek’s emphasis on constructing sorting lines with lifespans of up to 50 years or more, our on-site commissioning typically spans only up to two years, depending on project size,”
Our after-sales objective is to collaborate with customers on both minor and major investments to further enhance line productivity.
Kari Puustinen, Sales Director of Jartek
Jartek sees significant potential in these upgrade projects, whether it involves a single device or an entire production line—especially now that customers can
purchase both mechanical and automation solutions from them. “We have a wide range of equipment, and we work with the customer to select the best possible solution,” Puustinen explains. For automation, the company prefers using modern Beckhoff products, though other options like Siemens are also available, and in many cases, hybrid solutions combining different technologies within the same project are implemented.
Jartek doesn’t run any web shops or after-sales platforms. “We might lean towards tradition, but for us, building lasting relationships through human connections is key,” says Kari Puustinen. How does this align with our ethos of “More than Mechanics”? While expert mechanics lay the groundwork, they’re just one piece of the puzzle. We also prioritize cutting-edge automation and ongoing line development. Jartek is committed to providing state-of-theart automation solutions,
which our customers have enthusiastically embraced. These solutions are precisely tailored to industry needs, featuring intuitive interfaces, robust diagnostic capabilities, and seamless integration with third-party systems like reporting tools, whose importance is steadily increasing.
Looking to the future, instead of focusing solely on modern platforms, we’re enhancing our after-sales support through more
traditional investments to further boost line productivity. Finnish sawmills, known for their efficiency despite their age, have shown us the value of even minor improvements.
Therefore, we prefer terms like “service” or “partnership” over “after-sales,” highlighting the ongoing nature of our collaboration.
As a leading supplier to Finnish sawmills, Jartek encourages them to connect with our sales team to discover how we can work together to optimize line efficiency.
Roughly one year ago, Jartek commenced the installation of its largest project in Finland. This mill stands as one of the most advanced sawmills globally. Logs are seamlessly fed into the saw infeed by forklift, and the point at which the forklift touches the lumber marks the readiness for shipment to the customer.
Jartek provided a comprehensive supply package, encompassing green and dry sorting, along with stick and drying load moving systems and lumber feeding from sawline to greensorting, all of which operate fully automatically.
The layout was meticulously tailored to suit the site’s specific requirements, given its compact nature, making a fully automated process the only viable option. Collaboration with the Junnikkala team has been exceptionally fruitful, particularly in the conceptual planning phase.
The production lines feature a blend of standardized working solutions
complemented by customized fittings to adhere to the overarching concept.
This fusion ensures both high capacity and functionality, alongside an excellent layout. Currently finalising startup procedures, the mill is poised to serve as a benchmark, showcasing our capabilities to customers worldwide with pride.
Do you want to be at the center of the forest products community?
Are you ready to see how adaptive technology is influencing manufacturing decisions? Is your company part of the new manufacturing age at this critical moment for the industry?
If you answered yes to any of the above questions, don’t second-guess exhibiting or attending the 38th Forest Products Machinery & Equipment Exposition (EXPO). It’s the place to showcase your solutions for nearly every stage of manufacturing and network with:
• key decision makers who control major purchasing budgets,
• mill supervisors looking to improve efficiency,
• marketing experts seeking promotional vision, and
• young professionals making tomorrow’s decisions.
And they’re all looking to adapt to new markets, adjust quickly to increased demand, and bolster operations for the future!
EXPO 2025, set for August 6-8, 2025, in Nashville, offers solutions for nearly every stage of manufacturing. From raw material handling to crane operations; metal detection and scanning technologies; log optimization, drying, grading, sorting, packaging, and distribution, there are potential customers onsite to explore these solutions with you face to face.
The Southern Forest Products Association established EXPO to help advance the southern pine and greater lumber industry and provide
a forum for the exchange of ideas contributing to improved sawmill efficiency.
The three-day show provides a place to connect and reconnect with colleagues, connect with customers new and old, and explore opportunities. Both firsttime and returning exhibitors alike play a vital role in the continued progress of the lumber industry. More importantly, EXPO provides a place where in-person meetings are valued over emails and phone calls; where a handshake and a smile between colleagues communicate genuine respect; and where sharing ideas is best accomplished face-to-face.
Cont’d on Page 36
JS-50 X6B CARRIAGES & SHORT-INFEED EDGERS
JS-50 TRIMMERS
JS-50 Z8 END-DOGGER, C FRAME & HI SPEED SNAPSHOT
While the sawmill machinery show originated from leaders looking for a way to improve softwood lumber production, today’s EXPO showcases machinery and equipment for hardwood and softwood sawmills.
“Without a doubt, the hardwood lumber industry has long been represented at this show,” said SFPA Executive Director Eric Gee. “People come to EXPO with an exploration mindset, looking for opportunities to invest in their operations.”
A long list of manufacturers serving the hardwood
limited to, companies such as Corley Manufacturing, Oleson Saw, SII Dry Kilns, McDonough Manufacturing, TS Manufacturing, and WoodMizer.
Nashville was selected for several factors, but, most importantly, it is positioned smack in the middle of the forest action.
The surrounding areas, including the Eastern U.S. hardwood community, represent 42% of all lumber manufactured in the United States. And in case you’re curious, Nashville is within easy driving distance for 35% of Southern Pine sawmills and 73% of hardwood sawmills. That’s just a four-hour drive from more than half of Southern sawmills!
With 766 million acres,
more than $100 billion in forest products, the South’s variety of tree species and yearlong harvesting make the region a first choice for mills that rely on an available, affordable supply of sustainable wood products – and Nashville is right in the center of it all.
EXPO 2025 will be held at the Music City Center in downtown Nashville. Located in the middle of all the action, the MCC is the perfect home base for a fun-filled visit to Nashville. You’ll experience a modern business atmosphere in the new state-of-the-art facility surrounded by a thriving culinary, music, sports, and cultural scene, including the Country Music Hall of Fame, the historic Ryman Auditorium, and the always fun and famous
honky tonks – all within walking distance!
It’s Time to Get Down to Business: Face-to-face is Back
For nearly 70 years, this association-sponsored trade event has successfully connected the lumber manufacturing community. EXPO has a longstanding reputation as the place where connections are formed, relationships are strengthened, and deals are closed.
The forest products manufacturing community knows EXPO is the place to get up close to the materials, resources, equipment, and technology they need now.
What are you waiting for?
Plan your experience today at sfpaexpo.com!
After a major fire damaged several pieces of equipment at Evergreen Forest in New Meadows, ID, USNR is building new machines to get the mill running at full capacity again.
The initiative will take place over the course of several phases, some of which have already been completed. Evergreen has already received new edger scanning and optimization systems and a pony carriage with controls.
Later this year, they’ll receive a new headrig carriage.
They’re also slated to receive a new trimmer with MillExpert optimization and Bioluma 4900LV scanners.
Along with the new equipment, USNR is committed to helping Evergreen Forest bounce back with additional upgrades, training, and 24/7 support to tackle any issues that may arise.
USNR works closely with Evergreen to get production running even better than before.
With 21 years of industry experience, Norvin is excited to introduce the industry changing fingerprint system, MiCROTEC Connect integrated with CT technology for hardwood and softwood mills across North America. Norvin’s team serves the United States, Canada, Australia, and New Zealand markets, offering optimized wood scanning solutions
Norvin Laudon is the New Head of Sales at MiCROTEC based in Corvallis, Oregon. Norvin’s team serves the United States, Canada, Australia, and New Zealand markets, offering optimized wood scanning solutions. Norvin has 21 years of wood products industry experience, with beginnings in board scanning and moving into log scanning and optimization. Norvin has been with MiCROTEC for 16 years, where he was a key developer of the CT Log; using computed tomography technology to provide a complete reconstruction of a logs’ internal features and optimized cutting solutions.
With the new role, Norvin is excited to introduce the industry-changing fingerprint system, MiCROTEC Connect, integrated with CT technology
for hardwood and softwood mills across North America. The system offers massive benefits for mill-wide value & recovery optimization.
MiCROTEC Connect
MiCROTEC Connect is the real fingerprint system based on CT-scanned logs. Through the integrated and innovative scanner and software solutions and the implemented MiCROTEC Ai platform, each log can be traced from virtual to real boards. Likewise, the individual boards can be traced back to their original logs and recognized at each production step without any gaps. This modular concept offers huge benefits for mill-wide value & recovery optimization.
MiCROTEC is the only company offering scanning and optimization solutions from log to final board, providing
innovative scanning solutions focused on recovery and sustainability. MiCROTEC’s customer support is backed by a team of industry experts, including ex-graders, engineers, and specialized technicians. The scanning solutions offered by MiCROTEC allows logs to be graded and sorted by quality and optimizes the cutting solution with the highest value in real time. The company’s board scanning technology is well-known in the industry in the Lucidyne and Goldeneye scanners, revolutionizing automated defect detection and grading.
For more information on Norvin’s new role or MiCROTEC’s solutions, email norvin.laudon@microtec.us, or visit microtec.us.
TJames Jones & Sons Ltd, one of the UK’s largest and most progressive timber processing companies, chooses MiCROTEC Goldeneye scanners for their strength grading lines in Aboyne and Lockerbie for British spruce and larch timber processing.
he 5th generation family business installed the first Goldeneye scanner for strength grading in 2003 and has since relied on MiCROTEC, a company that looks back on more than 25 years of experience in the development of scanners for machine strength grading.
In 2021, James Jones & Sons decided to invest in two new Goldeneye scanners including X-ray for their strength grading
lines, one in their Aboyne location and one in the Lockerbie location.
This new generation of scanners is more compact, does not rely on water cooling, and is overall easier to maintain compared to the models from 20 years ago.
The Goldeneye allows James Jones & Sons to grade boards used for construction according to EN-14081 standards. The in-line moisture meter M3
Scan measures the moisture content of every single board. Boards with a moisture content outside the target range are automatically rejected.
The project applies the approach of double and triple virtual splitting, first introduced by MiCROTEC who is still exclusively offers the triple virtual splitting solution. Before sawing, the Goldeneye software utilizes a virtual board splitting mechanism, dividing a board lengthwise into two or three parts. This segmented data is then forwarded to the strength grading software, which treats each part as an independent board.
James Jones & Sons and MiCROTEC look back on a long-standing partnership. Reflecting on the collaboration, Tobbe Sandberg, Technical Manager at James Jones & Sons emphasizes the pivotal role of MiCROTEC’s Goldeneye X-ray grading technology in their operations, “James Jones & Sons Ltd has used Goldeneye X-ray grading for many years at its Aboyne and Lockerbie sites.When the time came to upgrade the strength grading in Aboyne and Lockerbie, we chose MiCROTEC Goldeneye again due to its reliability, good service and the longestablished relationship we have with MiCROTEC.”
Red Stag Timber is focused on growth and efficiency.
Red Stag Timber is one of the largest sawmill corporations in New Zealand currently producing over 600,000 cubic meters of Radiata Pine and Douglas Fir per year. The company recently started up a new USNR Bioluma trimline to further increase production capacity and recovery.
The trim line project went very well; good installation, machinery went together well, and start-up was smooth. We’re very happy with the result and performance.” says Andy Archer, Mill Manager.
Building on the successful installation of the USNR dual quad log line and dual edger lines, the decision was made to unleash the full potential of the sawmill by installing a second trimline and stacker line.
This new trimmer line in the Rotorua, NZ, mill features a high-speed multi-saw Clamshell trimmer to maximize trim accuracy and flexibility.
Bioluma 2900LV scanning sensors are paired with USNR’s new MillGenius trimmer optimizer for a powerful system that delivers high value, recovery, throughput, and reliability. Red Stag Timber is the first to use MillGenius software in New Zealand.
Upstream, a Revolver lug loader uses MillTrak cameras to manage the backlog as it deals boards into lugs ahead of the scanning system. The line also features the renowned all-electric and infinitely positional Multi-Track Fence to maximize trim saw accuracy and flexibility.
USNR provided the PLC controls, operator consoles, and HMI’s for the line along with a PLC-based safety system. The mill uses the WinTally Sorter Manager to setup sorts and manage bins, while the PLC and HMI systems generate alarms, messages, and downtime reports for the line.
Red Stag Timber saw an immediate increase in
production with the installation of the second trimline. The piece-per-minute bottleneck at the original trimline disappeared, and the log gap has been reduced to increase piece count. The mill has also seen a reduction in stoppages from board handling issues.
Andy Archer, Operations Manager: Sawmill & Secondary Processing
Investing in this line has increased Red Stag’s current capacity and it’s designed for further expansion. The next stage is to add a second sawline to the sawmill operation.
To watch a short video of the operation, click here.
This high-speed trimmer operates at 240 lpm and features a fulllength hinged top for exceptional access during saw changes, ensuring all maintenance can be accomplished from the floor level and up. Learn more about the Clamshell trimmer here.
Accommodating a wide range of products for sawmill, planer mill, and reman plant applications, the Revolver lug loader is very fast and its electric/pneumatic design reduces wear components. Read more about the Revolver Lug Loader here.
Tigercat builds the most advanced, efficient, and refined skidders on the market.
Tigercat H-series fourwheel and six-wheel skidders are designed for serviceability, reliability, efficiency, and operator comfort.
Tigercat skidders have large spacious cabs with generous window area to provide unmatched visibility on all sides. Lower windows on the front and rear provide a better line-of-sight to all wheels. The interior uses a mix of molded plastic panels and removable steel panels. The molded, easy to clean rubber floor mat has durable checkered aluminum plates at the high touch points.
The Turnaround® system lets the operator rotate the seat 220°. Effortless pushbutton controls lock and unlock the seat in any position in the range. The operator has full control of all machine functions including drive controls. The 220° seat rotation improves operator visibility, greatly reduces neck strain, and allows the operator to easily exit either side of the cab.
A durable, heavy duty air ride suspension seat with heating and cooling keeps the operator comfortable all day long. The reclining seat is fully
adjustable with seat angle and seat extension adjustment. Tilt up adjustable armrests along with adjustable lumbar support all contribute to operator comfort. A secure five-point harness comes standard for improved safety.
The HVAC system provides excellent cooling capacity and well-placed air vents for
operator comfort. The larger intake filter keeps the cabin air clean. The fan speed control is infinitely variable from zero to 100% and a defrost option is available which cycles the A/C on and off automatically to keep the windows clear. A climate-controlled cup holder is connected to the system to heat or cool drinks.
Operator controls are conveniently located on the armrests. Differential lock buttons are on the joystick and can engage front and rear separately. LED lights above the buttons illuminate when they are active. A cruise control button maintains the current engine speed allowing the operator to release the pedal. The grapple constant pressure button also turns on an LED indicator on the joystick alerting the operator that the constant pressure is activated.
Tigercat six-wheel skidders are field proven with 25 years of development and real-world applications in the most demanding extraction operations on the planet. The 635H is a Tigercat’s highest capacity skidder. With sixwheel drive and a massive grapple, the machine is built for extreme duty and super high production logging operations. The 635H swing boom skidder is the newest addition to the six-wheel skidder line up. With a 210-degree rotation, the swing boom increases the working envelope of the skidder, which means the operator spends less time manoeuvring the machine. Tethering device set-ups are reduced due to the wider working range. Dual rotate motors and a large swing bearing make gathering and moving bunches effortless on steep slopes.
The Tigercat 612 dual winch skidder was created to manage the extraction function in challenging terrain selective felling applications, while preserving the value and quality of the residual stand. The machine can be equipped with a dual winch, movable back shield fairlead system, as well as a crane and front blade tongs.
The Tigercat FPT N67 Stage V engine, 155 kW (208 hp) and combined with Tigercat’s efficient drive system, the 612 impressively handles adverse terrain while minimizing wheel spin.
The 612 is stable and robust, offering high ground clearance while maintaining a narrow stance, allowing easy navigation through tight trails and rough conditions. The moveable shield can be used as an anchor while winching. The dual winch and moving fairlead allows the operator independent control over two separate cables. The optional heavy-duty crane and blade tongs offer even more versatility for extracting, maneuvering and sorting logs.
The Tigercat 612 grapple skidder is designed to excel in tight selective harvesting applications.
A key design aspect of the 612 platform is the oscillating centre section. By allowing a fixed front axle, it narrows the stance of the machine, allowing easier navigation through tight stands.
Both 612 configurations feature stress-free serviceability. Easy access to daily service points, a tilting cab, and thoughtful layout of major components contribute to making maintenance smooth and uncomplicated.
Tigercat recently released the 630H silviculture carrier to address deficiencies that many forestry companies find with modified ag tractors for pre-planting site preparation applications.
Based on Tigercat’s skidder platform, the machine is equipped with hydraulic connectors and several drawbar receiver variations
to adapt to a variety of plow or mounding implement connection points. In addition, the carrier can be equipped with an optional winch and bolt-on fairlead system. The whole package is factory equipped and ready to work.
With proven results in gains in productivity and fuel consumption, the fleet of this forwarder in Brazil reaches 10 machines, in less than two years after launch
Ponsse’s Rodrigo Marangoni - Commercial and Marketing Executive Manager
Herd of Mammoths invades Brazilian forests. Perhaps this would be the most creative call for this text. The truth is that 10 PONSSE Mammoths are already in operation in Brazil, Ponsse’s largest forwarder. There are 50 machines spread across the world that have been gaining ground and showing what they came for: great efficiency and productivity.
There are already three companies that are betting on the results of PONSSE
Mammoth, one of which already has a fleet of eight of this forwarder model capable of transporting 25 tons of wood in a single trip. Designed to support high extraction volumes, even over long transfer distances, this machine stands out for its high energy efficiency. It has already demonstrated significant advantages in optimizing fuel consumption and wood extraction capacity per work cycle.
PONSSE Mammoth was launched in 2022 and the first
machine to come to Brazil began operations in January 2023. Still in 2023, Ponsse released the first results of the equipment in Brazilian forests and since then this imposing forwarder has been gaining ground , especially where there is greater demand for wood transportation.
“This is a machine designed for high transfer demands, an important fact for Brazil, which harvests at all times of the year and in large volumes. Even with its robustness, we already have data that prove that the PONSSE Mammoth delivers greater efficiency energy, optimizing the cost per cubic meter harvested”, added Rodrigo Marangoni.
About PONSSE Mammoth
The PONSSE Mammoth forwarder, the brand’s largest to date, has a load capacity of 25 tons of wood. Equipped with the latest technology and CVT transmission, the model is ideal for the most demanding operations, long transfer distances and high volumes of wood.
“This transfer machine has demonstrated excellent acceptance by South American customers, mainly due to its load capacity, energy efficiency and high onboard technology. In addition to all the advantages presented previously, the PONSSE Mammoth is an important differentiator in reducing CO2 emissions in forestry operation”, concluded Rodrigo.
Gains in productivity and better energy efficiency are positive results for tire machines, compared to adapted tracks, for forest harvesting in flat areas
According to Ponsse’s Commercial and Marketing Executive Manager, Rodrigo Marangoni, the harvesting module equipped with ten PONSSE Cobra harvesters showed an average gain of 8% in productivity, compared to crawler excavator machines adapted with harvesting heads, under the same conditions of land. “Maintaining the same operating conditions in the compared modules, there were moments, throughout the year of data analysis, when machines and some operators of the Cobra Project achieved productivity greater than 30%, compared to the adapted machines”, he highlighted.
For Suzano’s Forestry Operations Manager, Gilmar Baldo Junior, the results obtained in the project are extremely relevant. “A positive point we highlighted was energy efficiency. In this case, fuel consumption was approximately 12% lower”, he stated. Furthermore, Gilmar highlights the gain in ergonomics for operators, as the tire machine (8x8) adapts better to terrain conditions.
To put the project into action, the two companies signed a technical cooperation agreement, and many of the challenges were overcome with alignment between the parties involved. Training the workforce and providing maintenance services for greater mechanical availability of the machines were the focus of the teams in order to explore the best of each piece of equipment and each professional in that module.
The main highlight of the project is the innovation in adopting tire machinery for flat areas, instead of adapted tracks, a very common scenario in Brazilian forestry operations. “The relevance [of the Cobra Project] is high, given that it is a hitherto disruptive test within the Brazilian forestry market. The initiative, in fact, meets the concept of Innovability that we have here at Suzano, where the
search for solutions innovative and sustainable solutions has guided our actions for a hundred years. The Cobra Project represents a significant step in this direction, demonstrating Suzano’s commitment to exploring new approaches and technologies to optimize our operations and promote the sustainable development of the industry”, said Caio Razzano Rossmann, Manager of Suzano Operational Excellence.
Caio Razzano Rossmann Forestry Maintenance and Materials ManagerOperational Excellence
Suzano’s Forestry Operations Manager, Gilmar Baldo Junior
strongly believes that we can change this scenario by gaining productivity, ergonomics and energy efficiency by adopting tire machines manufactured for forest harvesting activities”, added the executive.
Other factors must also be evaluated before a total conversion of a forest
Marangoni explains that due to past situations - cost of acquisition, maintenance and support, local regulations, flexibility of use -, harvesting in flat areas using excavators adapted with a forestry head still prevails in Brazil. However, the market is dynamic and these same reasons need to be reevaluated. “Ponsse
harvesting fleet, but the results of the Cobra Project bring yet another solution option to be evaluated. “In view of the tests and scenarios applied, we, at Suzano, understand that this equipment model (tire harvester) will be considered in future acquisitions for forest harvesting in flat areas”, concluded Rossmann.
TEarlier this year Vermeer unveiled the LS3600TX low speed shredder. This single-shaft shredder incorporates exclusive innovations that efficiently process contaminated waste streams and help safeguard critical machine components
he Vermeer LS3600TX is specifically designed to excel at processing various materials, including light construction and demolition waste, wood waste with contaminants, and municipal solid waste. It is well-suited for waste facilities and land clearing operations, as well as compost, mulch and biofuel producers.
“For 30 years, Vermeer has been a leading manufacturer of high speed grinders,” said Jeff Bradley, Vermeer Recycling and Forestry product manager. “During that time, recycling has become a common practice at public and private waste handling facilities and has become another source of revenue for many organizations. To help our customers optimize their processing capabilities and handle a wider range of incoming materials, we have developed the LS3600TX low speed shredder. This shredder allows companies to process contaminated materials not suited for a tub or horizontal grinder.”
Vermeer has designed the LS3600TX shredder with a strong focus on maintenance and accessibility. The engine bay of the LS3600TX prioritizes ease of maintenance and serviceability, featuring large
comfort of the feed loader’s cab or a safe distance from the shredder.
The LS3600TX is equipped with a 10 ft (3 m) long rotor featuring wear-resistant plates for enhanced durability and dual-bolt tips to help maintain clamp load. It utilizes individual bolt-in
access doors, multiple ladder points and a spacious service platform. This thoughtful design allows for quick and efficient maintenance. Additionally, the LS3600TX is equipped with a hydraulically operated access system that provides full exposure to the rotor, comb, and belly conveyor, further streamlining maintenance procedures. Also, the belly conveyor can be easily removed without detaching the discharge conveyor, minimizing the invasiveness of service operations.
The LS3600TX shredder has a powerful 456-hp (340 kW) CAT Tier 4 Final/Stage V engine. It operates at a sound level of only 111.9 db(A). The shredder features a tracked undercarriage, which enables operators to reposition and maneuver it around a jobsite. It also comes with a full-function remote control, allowing operators to adjust the feed, access machine data, and diagnose fault codes from the
comb teeth, each with two usable edges, which extends their lifespan. The shredder is built with a fully mechanical driveline designed to optimize horsepower transfer to the rotor. To safeguard the driveline system against unshreddable objects, the LS3600TX includes a reversible mechanical transmission with an external torque limiter that will automatically disengage the drive when maximum torque is reached.
Vermeer offers an optional cross band magnet for the LS3600TX to further enhance its capabilities. This magnet effectively reduces steel contaminants from the end material, minimizing contamination in the final product.
The Vermeer LS3600TX joins a line of high speed tub grinders and horizontal grinders to deliver one of the industry’s most comprehensive waste processing and recycling equipment lines.
Rawlings Wood Hogs motto is “innovation not imitation.”
The company is constantly looking at ways to improve their equipment to make the machines more durable and easier to maintain. In response to recent trends, Rawlings is thinking outside the box and recommends systems that incorporate a combination of equipment. For example, utilizing horizontal high-speed and slowspeed grinders as the primary grinder for processing larger-size materials such as railroad ties, pallets, construction, demolition, and hurricane debris, while using the vertical grinders and hammermills to produce a smaller, more consistent particle size.
By splitting the material loads through different grinders and incorporating product screening, it allows the equipment to process the material more effectively while producing consistent feedstock,” says Judi Tyacke, Rawlings project manager.
The company’s solid steel Super Hi Inertia Rotor TM is designed from rock crusher technology, making it extremely tolerant of contaminants, rocks, and metal without catastrophic maintenance costs if metal enters the grinding chamber. The Rawlings rotor is also designed to maximize inertia while minimizing its weight.
“With the increase of inertia, our machine runs at lower rpms than competitor machines and half the speed of conventional hammermills, resulting in overall savings of electricity and maintenance costs. The cam profile of the Rawlings rotor prevents feed surges by keeping material closer to the cutting edge of the bits. This translates to better productivity as the in-feed conveyor is stalled less frequently, and less down time, as the increased energy reduces the number of motor drive stalls.
During Rawlings’ 45 years of designing wood grinding systems, our company has learned that most of its clients are asking for grinders to
rear of the machine, allowing full access to the hog’s internal wear components and rotor for ease of maintenance.”
obtain the smallest finished product on a single pass or one-stage pass through the grinder. We often suggest that this is not always the most economical option long term, running the grinder and related equipment at full surge capacity results in frequent equipment breakdowns, high consumption of spare parts and costly maintenance repairs. Incorporating several types of equipment into the system allows the customer to protect their investment while producing a highquality, consistent end product.
For that reason, Rawling’s engineers have made significant changes to the hog case that allow its customers’ maintenance teams easier access to the hog rotor, sizing grates and internal case liners. Over the years, several customers have wanted a Rawlings solid rotary hog but did not have the overhead clearance in their existing footprint to allow for a clam shell opening type of machine, Rawlings says. “Our engineering team took this feedback and did a redesign of the hog case. This new model opens hydraulically from the
More recently, a customer contacted the company looking for a 2-inch minus product, as his feedstock was 12-inch minus with approximately 40 percent of the material already sized to 2-inch minus. “After thoroughly looking over the project parameters, we suggested a vibratory shaker deck to screen off and separate the material, removing the 2-inch accepts prior to grinding it through a Rawlings vertical drop feed hog,” Tyacke says. “This is a common practice to reduce the amount of tonnage to the machine, resulting in cost savings of spare parts, maintenance, and overall electricity costs. Simply put, it’s less expensive to screen it than grind it.”
www.wastewoodhogs.com
Rawlings Vertical Feed Wood Grinder
UK, Europe, South Africa, US East Coast
CONTACT: Robin Peach
International Forest Industries Ltd
Tel: +44 (0)1442 877 777
Fax: +44 (0)1442 870 617 robin@internationalforestindustries com
Japan
CONTACT: Shigeru Kobayashi
Japan Adver tising Communications, Inc.
Star Bldg., 3-10-3 Kanda Jimbocho
Chiyoda-ku, Tokyo 101-0051
Tel: 81-3-3261-4591
Fax: 81-3-3261-6126
Email: Shig-kobi@media-jac.co.jp
Western USA (AZ, C A, NV, UT)
Australia, & New Zealand
CONTACT: Kevin Lapham
J.P.Media Inc
Tel: +1 (630) 420 9752
Fax: +1 (630) 420 9763
Email: lapham@jpmediainc.com
Western USA (MT, ID, OR,WA) & Canada
CONTACT: Kevin Lapham
J.P.Media Inc
Tel: +1 (630) 420 9752
Fax: +1 (630) 420 9763
Email: lapham@jpmediainc.com
US Mid-West, Central & Mountain
CONTACT: Kevin Lapham
J.P.Media Inc
1163 E.Ogden Ave, Ste. 705-359 Naper ville
I L 60563, USA
Tel: +1 (630) 420 9752
Fax: +1 (630) 420 9763
Email: lapham@jpmediainc.com
Bandit
www.banditchippers.com
BID GROUP
29 www.bidgroup.ca
Combilift 15 www.combilift.com
Delta Motion
www.deltamotion.com
Demo International 2024 �
4 & 19 www.demointernational.com
Franzen
41 www.franzen-machines.com
FAE
www.fae-group.com
Halco Software Systems 38 www.halcosoftware.com
Jartek �
31 www.jartek.fi
Joescan
www.joescan.com
www.LMI3D.com
www.logmax.com
The logging industry demands reliable and efficient equipment to tackle the toughest challenges in harvesting operations. Introducing the Log Max 5000V, a state-of-the-art harvesting head that combines durability, agility, accuracy, and intelligence to revolutionise logging worldwide. With its reinforced design, advanced features, and improved servicing capabilities, the Log Max 5000V sets a new standard for modern and powerful harvesting heads.
The Log Max 5000V boasts a reinforced frame designed to withstand the most demanding logging applications. The slimmed-down saw box enhances performance in snowy conditions, ensuring optimal cutting efficiency. Equipped with the new 318 MK2 - 30cc saw, this harvesting head delivers fast and troublefree cutting up to 74cm, guaranteeing exceptional cutting performance.
Accurate measurement results are crucial in today’s harvesting operations, and the Log Max 5000V meets this requirement
with its redesigned measuring unit. The length measuring unit incorporates smart features, including a contactless sensor, easier lubrication, and durable tapered bearings. Furthermore, the harvesting head’s improved accessibility, wellorganised hoses, and grease nipples facilitate simplified maintenance and servicing.
To enhance the Log Max 5000V’s durability and longevity, several updates have been implemented. The design of the measuring wheel hole has been improved, reinforcing the stoppers for the feed roller arms inside the frame, thus increasing strength and stability. The length measurement function has been significantly improved through the introduction of a new measuring wheel unit with a larger wheel, ensuring superior measurement accuracy.
The Log Max 5000V incorporates the enhanced saw unit 318 MK2 19 cc (True-Cut) or 30 cc, carefully designed to optimise work processes. Upgrades include a more robust saw bar mount with protective covers and rubber seals, ensuring protection against dirt and moisture. The saw bar holder now utilises premium-grade Hardox 450 material, offering increased strength and longevity.
Additionally, the placement of the “saw bar home” sensor has been optimised for easy access during maintenance. On the 30cc version the saw valve is mounted directly to the motor which greatly increases responsiveness.
The Log Max 5000V’s multistemming unit has undergone a redesign, resulting in reduced weight, increased lifespan, and simplified serviceability. The relocation of cylinders and improved hose protection increase durability and minimise the accumulation of snow and dirt.
The Log Max 5000V’s fourpoint measurement MK2 features new components and functions to excel in harsh conditions. The introduction of a contactless encoder in the lower delimbing knife enhances its lifespan and simplifies maintenance. The lower delimbing knife now incorporates an “Active Lower Knife” function, increasing lifting power and optimising tree holding capability. Additionally, the design modifications, such as a new axel nut and improved cable routing, enhance durability and reduce the risk of snow and ice packing.
The Log Max 5000V represents a groundbreaking advancement in the logging industry. With its unparalleled durability, cutting performance, precise measurement capabilities, and simplified maintenance, this harvesting head sets a new benchmark for productivity, efficiency, and reliability. Experience the power of the Log Max 5000V and unlock its potential to revolutionise your logging operations.
See page 6
Ponsse’s new solutions for increased productivity and profitability –Ponsse Scale crane system & PONSSE High-Precision Positioning solution
Visit us at Stand A20
See page 14
Bandit’s HM6420 is available with screens up to 7 inches and includes an impact detection system that shuts the system down gently if a contaminant is struck inside the grinding chamber.
(Photo courtesy of Bandit.)
Visit us at Stand A25
See page 42
Tigercat 6-wheel skidders are built for extreme duty and high production applications
See page 18
FAE updates its top-of-the-line tracked carrier. Introducing the PT550: the tracked carrier for big challenges.
Visit us at Stand S13
See page 49
Log Max 5000V: The ultimate Harvesting Head for unparalleled logging performance Visit us at Stand A24
As their old equipment started to lag behind what was needed for the business, Bright Wood turned to USNR’s AddVantage scanners for a solution. Bright Wood purchased eight systems with the plan to replace existing scanners and to add more locations.
The goal was to utilize the system’s AI defect programming to help reduce the amount of waste, create fewer cutbacks, and produce an overall better product for
their customers.
An outdated scanning system can be severely detrimental to any facility. From slow processing time to misallocated manpower to excess waste, it can be the weak link that costs a mill thousands of dollars every year. This is exactly what led Bright Wood to search for alternative scanner options.
The AddVantage uses AIdriven defecting technology that provides industry-leading
detection and classification of defects. But finding the AddVantage was just the beginning. Upgrading and refining their process has now led Bright Wood to new ventures and better product.
Read the full article here
To read other USNR related posts click here
USNR ‘s powerful history as a strong visionary leader has brought many important innovations to the industry, and it’s time to unveil our next groundbreaking product development.
Visit us at TP&EE Booth #711
We’re revealing a brand-new piece of equipment exclusively at this year’s Timber Processing & Energy Expo, September 25-27 in Portland, OR. We’re thrilled to introduce this latest product offering from USNR that is as innovative as you are.
We’ll also be showcasing new advances in optimization and panel technology. You’ll be able to see special displays from our parts and upgrades teams and meet our expansive network of experts so you can learn more about what USNR has to offer.
September 25-27 2024 Portland, OR
Join us as our special guest with this form and be one of the first in the world to witness this exciting moment!
TO read previous USNR posts click here.
See page 26
How BID Group’s AI-Powered Smart Vision Enhances Safety and Efficiency
Visit Bid Group at TP&EE Booth #627 September 25-27 2024 Portland, OR
See page 39 A Unique Approach to Strength Grading: Virtual Splitting at James Jones & Sons with the MiCROTEC Solution Visit us at Booth #409
September 25-27 2024 Portland, OR
The lumber industry is on the cusp of a technological revolution, and SAWBOX is leading the way with its groundbreaking ability to turn logs into lumber with just one operator.
This innovative sawmill solution is designed to meet the needs of modern wood processing operations, providing a compact, automated system that ensures efficient, high quality lumber production. Most importantly, the SAWBOX allows you to process diameters up to 42 inches that you would not be able to handle in your normal production operations. For businesses in North America the SAWBOX promises to be a game changer, delivering benefits that are too significant to ignore.
Key Benefits of SAWBOX
• Self-Sufficiency
One of the outstanding features of SAWBOX is its ability to make companies self-sufficient. By allowing companies to cut their own logs, SAWBOX helps optimize production costs and ensures a steady supply of raw materials. This level of control over the production process can significantly improve a company’s profitability and operational efficiency.
• Cost-Effective Investment
Setting up a SAWBOX is much more affordable than traditional sawing technology. The reduced investment costs make it possible for smaller companies to own and operate their own sawmills, paving the way for greater autonomy and financial stability.
• Increased vs Enhanced Yield and Efficiency
SAWBOX is designed to maximize the use of each log, achieving yields of up to 75%. This high level of efficiency not only reduces waste, but also increases the overall production, making the most of the available resources.
• Sustainability and Regional Added Value
SAWBOX supports the use of local wood and the recycling of all wood waste, promoting sustainability and boosting the local economies. By sourcing wood locally and minimizing waste, companies can reduce their ecological footprint and contribute to sustainable forestry practices.
• Predictable Pricing
With SAWBOX, companies can enjoy long-term stable product prices by controlling their own production processes. This predictability is crucial for maintaining competitive pricing and ensuring customer satisfaction in a fluctuating market.
• Impressive Cutting Capacity
The SAWBOX can process up to 8.5 million board feet of lumber in a two-shift operation. It accommodates logs from 10 to 42 inches in diameter and from 10 to 16 feet 2 inches (on request 20 feet) in length, available upon request. This versatility makes it suitable for a wide range of lumber dimensions.
• Space Efficiency
SAWBOX is designed to fit into spaces ranging from 5,400 to 10,800 square feet, allowing for optimal use of available space. This compact footprint is perfect for companies looking to maximize their production capacity without the need for large, sprawling facilities.
For North American wood processing companies, the benefits of adopting SAWBOX are clear. Whether you are a sawmill, CLT or a gluelam facility, integrating the SAWBOX into your production line can lead to significant improvements in efficiency, cost savings, and sustainability. As the industry continues to evolve, staying ahead of the curve is essential. Discover how SAWBOX can transform your business, making it more competitive and resilient in a rapidly changing market. By investing in SAWBOX, you will not only improve your manufacturing capabilities, but also contribute to a more sustainable and economically vibrant community.
Explore the possibilities of SAWBOX and take the first step towards a more efficient and sustainable future for your wood processing business.
The family-owned company located in Austria (Europe), Greer (USA) and Nanaimo (Canada), plans, develops, and produces machines and state of the art solutions for the
wood processing industry. All processes, such as transporting, sorting, grading of wood, and automation, are implemented at the highest technological level. Special attention is placed on sustainability. The climate-
neutral company employs more than 500 people worldwide and is managed by the third generation of the Springer family, Timo Springer and Gero Springer.
www.springer-usa.com