JUNE / JULY 2024

SAWMILLING • LOGGING • BIOMASS • RENEWABLE ENERGY
SAWLINES • Forwarders • Mulchers • Wood Drying Technology
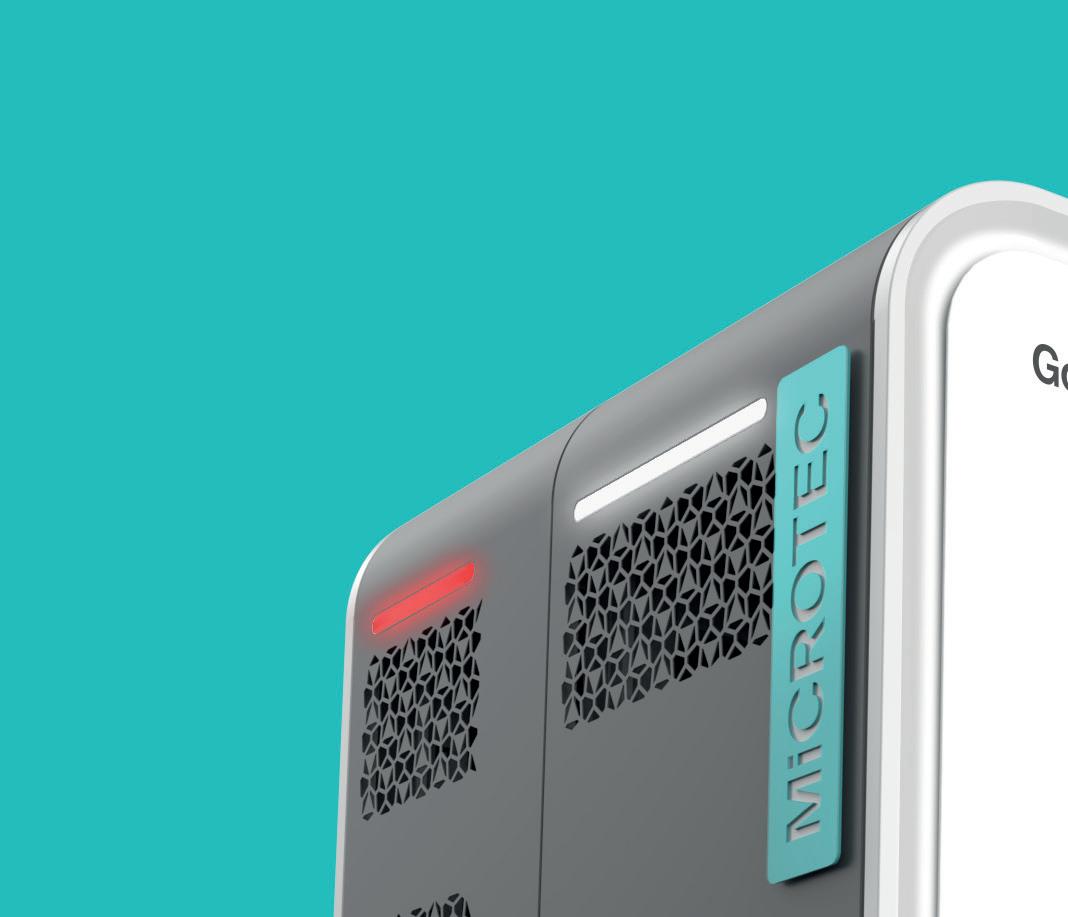
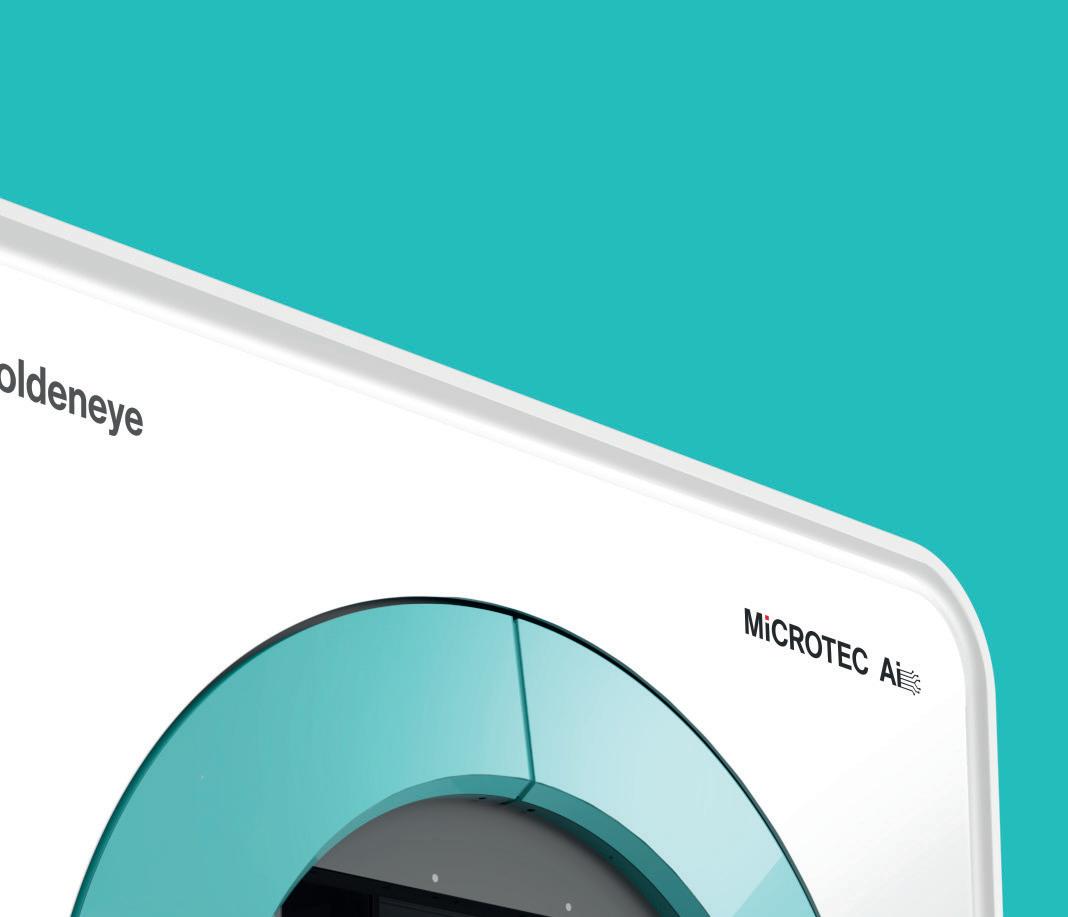
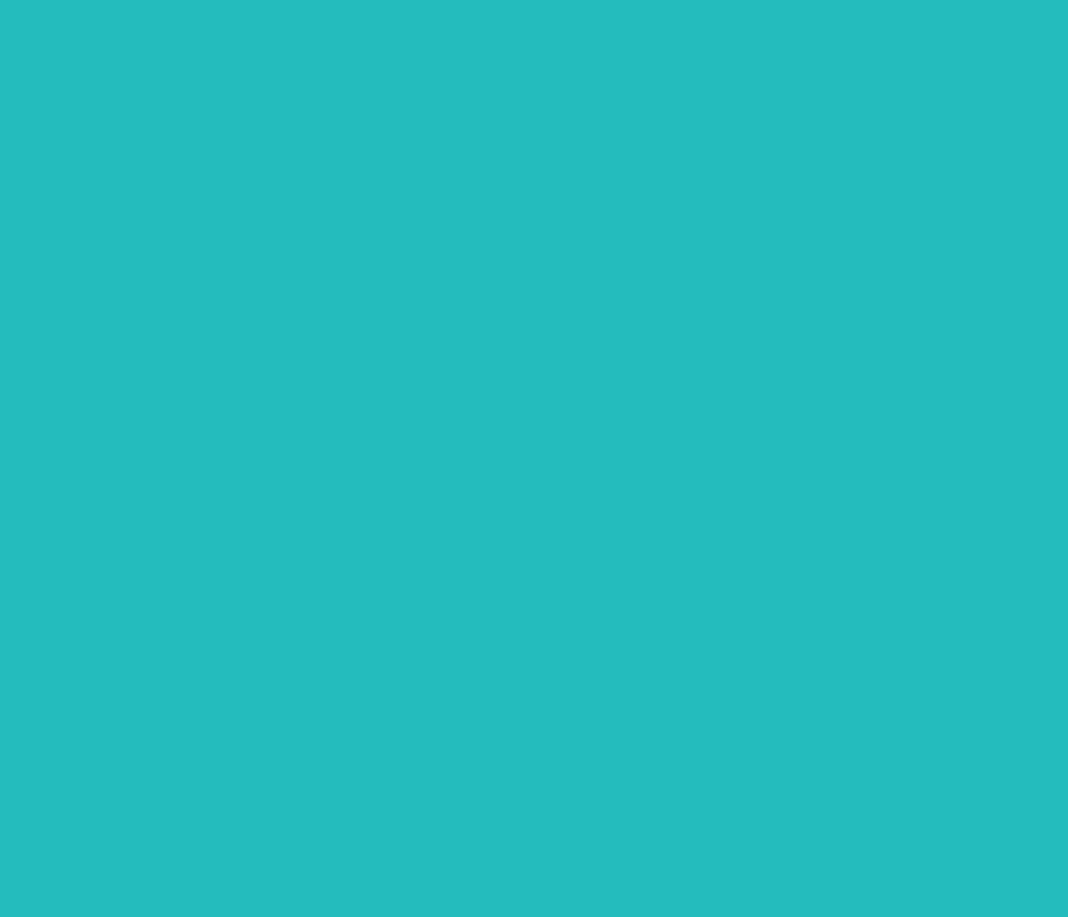

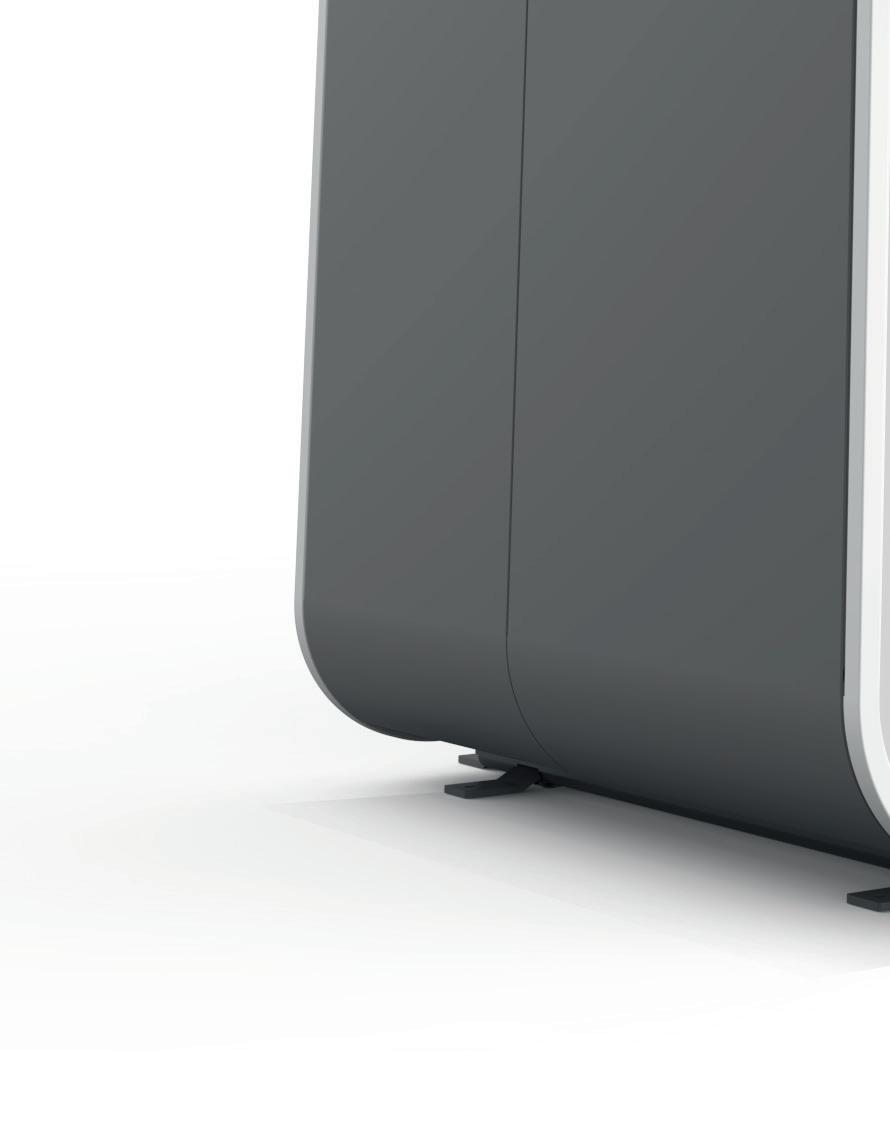


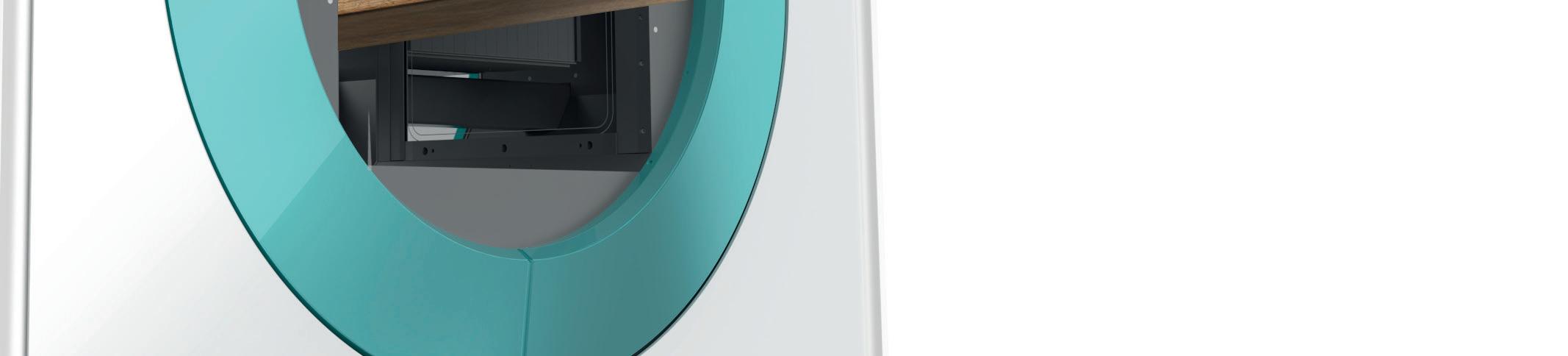

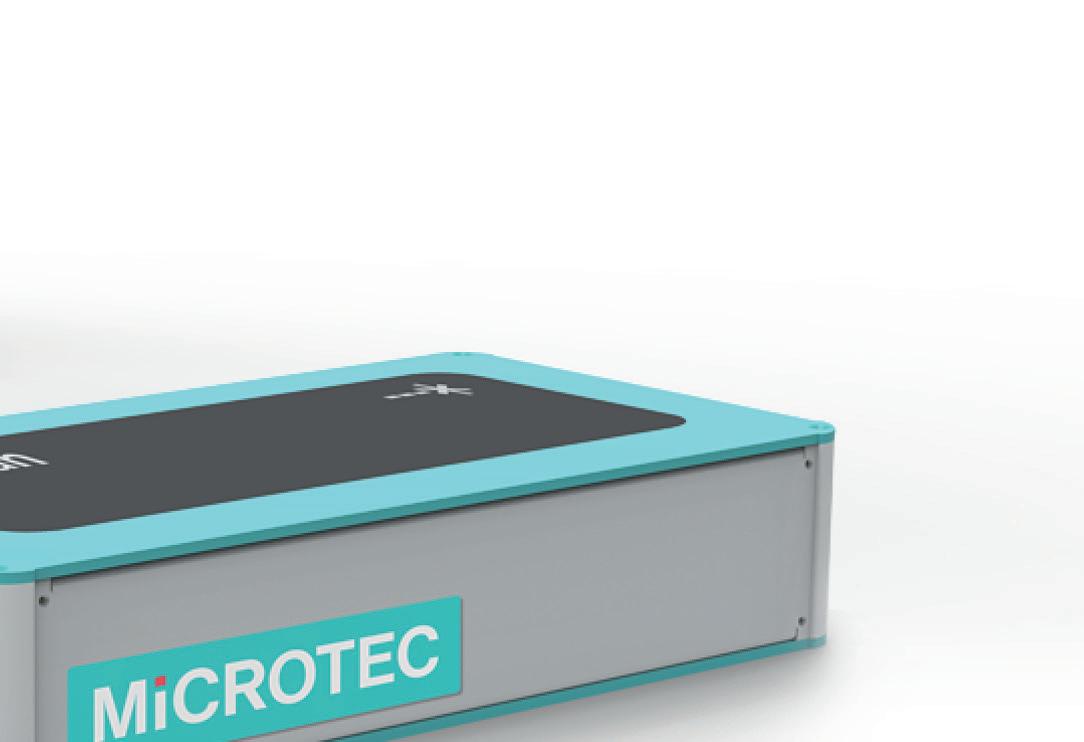

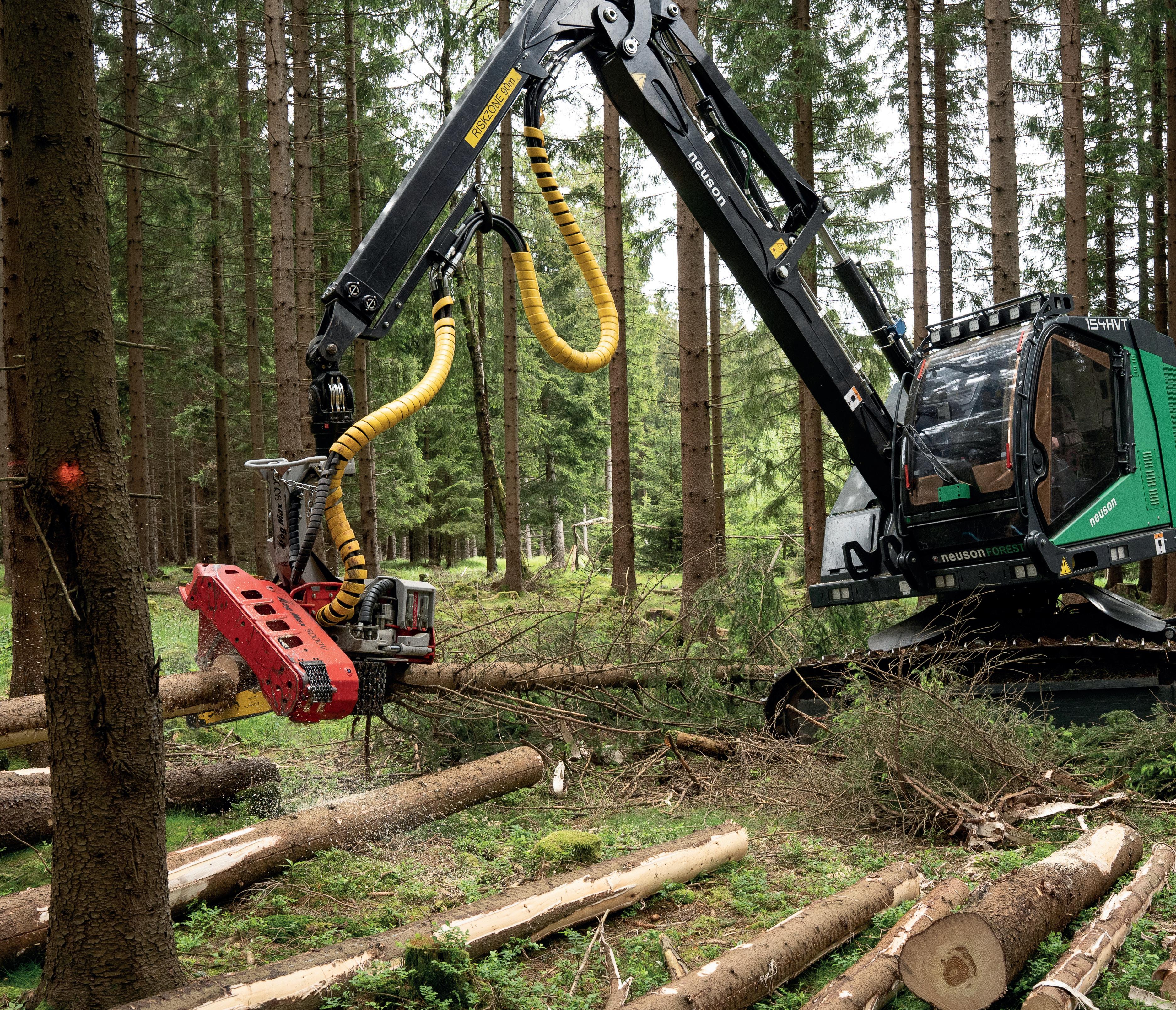
JUNE / JULY 2024
SAWMILLING • LOGGING • BIOMASS • RENEWABLE ENERGY
SAWLINES • Forwarders • Mulchers • Wood Drying Technology
The Log Max 5000V is a modern and reliable harvesting head that can handle a wide range of logging challenges. This is the perfect mid-range head for both thinning and final felling. The head can be equipped with a 82 cm saw bar and has a maximum cutting diameter of 74 cm. It also features Log Max’s Multi-stemming MK2, that is agile and lightweight, making thinning work easier. The Log Max 5000V is suitable for those who seek the perfect balance between agility, capacity, and durability.
What customers say:
“The cutting and feeding are brutally good and in combination with the new length measuring unit, Log Max is unstoppable ; )”
Goldeneye 706 is the combination of Goldeneye multi-sensor quality scanner including X-ray and Viscan. This strength grading solution localizes and recognizes every detail of your lumber with unbeatable precision and reliably determines MOE and MOR at the highest production speeds. Different grades can be determined for different parts of the board, so weaker parts can be removed allowing for a significant
increase in yield. With the approval of a speed up to 1200m/min it is the fastest strength grading solution worldwide. Furthermore, it has been certified according to the most relevant grading standards worldwide including EN 14081, MSR, and AS/NZS1748 standards.
microtec.eu
SUBSCRIPTIONS
SUBSCRIPTIONS
Tel: +44 (0)1442 877 583 emma@internationalforestindustries.com
Tel: +44 (0)1442 877 583 emma@internationalforestindustries.com
Annual Subscription
Annual Subscription
U K and Europe £160, € 230 Rest of the world US$270
U K and Europe £160, € 230 Rest of the world US$270
EDITORIAL
EDITORIAL
T: +44 (0)1442 877 583
T: +44 (0)1442 877 583
F: +44 (0)1442 870 617
Demo International Forestry Equipment show & Conference heads to Ottawa/Gatineau, Sept 17-21, 2024!
Registration open for premier industry event
www.internationalforestindustries.com
F: +44 (0)1442 870 617 www.internationalforestindustries.com
2 Claridge Court, Lower Kings Road Berkhamsted, Herts. HP4 2AF, UK
2 Claridge Court, Lower Kings Road Berkhamsted, Herts. HP4 2AF, UK
Editor
Robin Peach robin@internationalforestindustries.com
Editor Robin Peach robin@internationalforestindustries.com
Editorial Board
Kevin Lapham
J.P.Media Inc
Tel: +1 (630) 420 9752
OTTAWA/GATINEAU - The anticipation is palpable as DEMO International, the premier forestry equipment exhibition, gears up to make its mark in the picturesque capital region of Ottawa/ Gatineau from September 17-21, 2024.
offering attendees the chance to immerse themselves in a week-long celebration of forestry excellence.
Dr Patrick Moore – Chairman and Chief Professor Piotr Paschalis-Jakubowicz –Warsaw Agricultural University (Poland) Mr Kim Carstensen Director General Forest Stewardship Council
Fax: +1 (630) 420 9763
Eduardo Morales
Email: lapham@jpmediainc.com
South American Forestry Consultant
WEB OPTIMIZATION
Jo English
ADVERTISING AND PROMOTIONS
ADVERTISING AND PROMOTIONS
International Forest Industries Ltd
International Forest Industries Ltd
Advertising Manager
Advertising Manager
Organized by the Canadian Woodlands Forum, DEMO International is the quintessential event for forestry professionals, showcasing the latest innovations and technologies in action amidst the stunning woodland backdrop.
DEMO International is renowned for its dynamic demonstrations of cuttingedge forestry equipment, providing attendees with a firsthand glimpse into the future of the industry. From stateof-the-art machinery to groundbreaking technologies, exhibitors will bring their products to life, demonstrating their capabilities live in the woods.
Emma Smith emma@internationalforestindustries.com
Emma Smith emma@internationalforestindustries.com
jo@internationalforestindustries.com +44 (0)1442 877 583
+44 (0)1442 877 583
Publisher
Associate Editor
Robin Peach robin@internationalforestindustries.com
Robin Peach robin@internationalforestindustries.com
Advertising Production Enquiries
Advertising Production Enquiries
Emma Smith emma@internationalforestindustries.com
Emma Smith emma@internationalforestindustries.com
Studio Manager
Luke Evans luke@lecreative.co.uk
International Forest Industries is published by International Forest Industries Ltd,
Accounts
2 Claridge Cour t, Lower Kings Road Berkhamsted, Her ts. HP4 2AF, UK
Nicola Shukla nicolas@internationalforestindustries.com
International Forest Industries (ISSN 1755-6732) is published bi-monthly by International Forest Industries Ltd GBR and is distributed in the USA by Asendia USA, 17B South Middlesex Avenue, Monroe NJ 08831 and additional mailing offices. Periodicals postage paid at New Brunswick NJ. POSTMASTE R: send address changes to International Forest Industries, 17B South Middlesex Avenue, Monroe NJ 08831
© International Forest Industries Ltd 2007 – 2019 I FI uses, as preference, SI units throughout. All dollars are US unless otherwise stated.
International Forest Industries is published by International Forest Industries Ltd, 2 Claridge Cour t, Lower Kings Road Berkhamsted, Her ts. HP4 2AF, UK International Forest Industries (ISSN 1755-6732) is published bi-monthly by International Forest Industries Ltd GBR and is distributed in the USA by Asendia USA, 701C Ashland Avenue, Folcroft, PA 19032 and additional mailing offices. Periodicals postage paid at New Brunswick NJ. POSTMASTE R: send address changes to International Forest Industries, 17B South Middlesex Avenue, Monroe NJ 08831 © International Forest Industries Ltd 2007 – 2023 I FI uses, as preference, SI units throughout. All dollars are US unless otherwise stated.
As part of the festivities, the DEMO International Preconference will kick off at the Delta Ottawa City Centre on September 17-18, offering attendees an unparalleled opportunity to delve deeper into key industry topics. From presentations on research, automation, and digitalization to discussions on logging and trucking, biodiversity, and sustainability practices, the pre-conference promises to be an enriching experience for all participants.
Additionally, insights into international forestry outlooks from Sweden and Finland will provide valuable perspectives on global forestry trends and best practices. Mark your calendars as registration for both the preconference and the main DEMO International event is open,
Hosted by SBC Cedar, a prominent player in the forestry sector, this year’s DEMO International promises to be an unforgettable affair. Stay informed and follow along for future announcements and event information by visiting DemoInternational.com.
For further information, please contact: Becky Geneau Executive Director Canadian Woodlands Forum Becky.geneau@cwfcof.org
ROBIN PEACH EDITOR
Intelligent braking portfolio provides turnkey solutions for offhighway customers
• ZF’s electrohydraulic braking solution supports rapid transition to electric and autonomous vehicle applications
• Scalable technology offers ease of installation, adaptable brake pressure
ZF’s Industrial Technology Division is introducing its new brake-by-wire solutions. A global leader in hydraulic and electrohydraulic braking systems, ZF supports customers in the heavy duty, off-highway, construction, mining, and agriculture sectors with safe and efficient brake technology.
The company’s newest brake-by-wire solution is an important step change, as it provides vehicle manufacturers the ability to control deceleration via an electronic signal that adjusts brake pressure when needed, removing the need for hydraulic lines in the cab and evolving towards remote and autonomous operation.
As the off-highway market continues its transition from mechanical to intelligent braking technology, the new brake-by-wire system offers a universal solution that is easily scalable. Safety and vehicle architecture are key drivers for
ZF customers when designing their brake systems, and this new technology can help them achieve those goals.
The system is comprised of three components: an electronic pedal, electrohydraulic brake valve and a universal controller. Together, the system offers vehicle manufacturers ease of installation, electrohydraulic brake valves for precision brake control and adaptable pedal response/brake feel that can be customized to fit a vehicle’s brand identity. It also provides key operator benefits including reduced cabin noise, and passenger car-like comfort for brake feel.
ZF’s experience in motion control technology for passenger cars and commercial vehicles enables the Group to shape the future of electrification for these important off-highway market sectors. The intelligent braking portfolio not only provides turnkey solutions for customers in this sector today but also supports their shift to electric and autonomous applications in the future.
Introducing the Tigercat 573. A powerful, triangulated three-wheel drive harvesting head for fast picking, positive control, and precise measuring. Versatile for roadside processing and in-stand harvesting. Excellent performance and productivity in medium to large sized timber.
Match the power and performance of Tigercat carriers with an end-to-end Tigercat factory solution.
Ponsse turned 18 in Brazil in May and celebrated its anniversary by celebrating more than 500 pieces of equipment, including heads, harvesters and forwarders, delivered in the country during this period.
In the first quarter of 2024 alone, approximately 20 new Ponsse machines were delivered to customers and are already working in the country’s cultivated forests.
The company that began its activities in Finland in 1970, opened its Brazilian subsidiary in 2006. At the time, only Ponsse heads began operations, with assembly at the unit established in Mogi das Cruzes-SP. “Brazil is one of the largest forest producers and we believe it can become even more representative within our client scenario”, said Janne Loponen, director of Ponsse Brasil.
Hopscotch in the country
Since its founding in 2006, Ponsse Latin America, which is the corporate name of Ponsse Brasil, has sold more than 500 pieces of equipment, including harvesters, forwarders and heads, as mentioned above. Currently in operation, it is estimated that there are approximately 400 “hopscotch machines” (in reference to the color of the brand on the machines). Ponsse currently holds a share of around 35% of the forestry machinery market in Brazil.
The expectation for this year, according to Ponsse Brasil’s Commercial Executive Manager, Rodrigo Marangoni, is for a more moderate growth in the number of new orders, mainly due to the cellulose market. In the first quarter
alone, almost 20 pieces of equipment were delivered to Brazilian customers.
“The forestry machinery market in Brazil follows the same movement as the pulp market. The expectation is that the growth percentage will increase, as world pulp consumption also grows,” said Marangoni.
Relevance of Brazil for Ponsse
Brazilian forestry producers are more than just customers for Ponsse. The reality found in operations here is different from others in the world and challenges the creation of robust, effective and economically viable equipment. The director of Ponsse Brasil gave examples of equipment that had great participation from Brazilian producers in the development: the PONSSE H7HD Euca and PONSSE H8HD Euca heads are high-tech equipment with workload capacity, ideal for the country’s high demand.
Furthermore, there are Ponsse developments aimed at the Brazilian market, such as the Harbunk, which is the combination of a PONSSE Bear harvester with a ClamBunk clamp, ideal for cutting, dragging and processing in special areas, such as plots of up to 10 thousand tons of wood. ; and Multifleet by Ponsse, which is a system capable of integrated data management from various types of equipment and different brands on a single platform, facilitating data analysis and management of the forestry chain.
“Ponsse is a company that develops its machines listening to the real needs of the field. We work side by side with
customers to understand and bring solutions that really make a difference. Furthermore, our developments are driven by technology and aligned with sustainable development”, Loponen said.
The director adds that, even having started operations in 2006 with just head sales,
PONSSE H7HD Euca
PONSSE Mammoth
in just 18 years, Brazil has become a reference in the forestry market, adding not only harvesting heads, but purpose built machines , too. This demonstrates, according to Loponen, the gain of confidence in the Brazilian forestry sector, not only within Ponsse, but throughout the sector around the world.
“Today, the country is one of the great promises in the cultivation of sustainable forests and also has operational challenges that guide the development of new technologies.”
The new high-performance chain biolubricant for forestry applications
Engineered for full chain lubrication to provide an active barrier against sawdust and dirt.
Helping to protect your equipment for longer!
Granted since 1954, the iF DESIGN AWARD is one of the most significant and prestigious design awards in the world. The globally recognised iF DESIGN AWARD is considered a symbol of outstanding design. The award winners werecelebrated at the iF DESIGN AWARD NIGHT
2024 event at FriedrichstadtPalast in Berlin in Germany on Monday 29 April 2024.
The jury paid particular attention to the functionality and usability of the PONSSE Opti 5G information system. The user interface makes the forest machine operator’s work easier and
produces other harvesting information, including operator working hours, production, machine operation and fuel consumption.
“The Opti 5G system is designed to be easy to use to reduce the cognitive load of the forest machine operator and improve productivity. The user interface was completely rethought in our project to meet the users’ needs in the forest industry of today and the future. Design based on a user study and the large-scale testing of results are key factors behind the development of Opti 5G,” says Juha Inberg, Chief Technology and R&D Officer at Ponsse.
“During the project, we addressed the needs of forest machine operators, machine owners, maintenance services and sawmills,” says UX Manager Panu Johansson.
“This award is for everyone who has participated in the software development of the 5G system. Software development is almost always the result of the efforts of a large group of people. Software is at the core of modern forest machines to facilitate the use of the machine and make their operation more efficient. The user experience also plays an important role in improving efficiency, coping and comfort. Development at Ponsse focuses on understanding user needs,” says Inberg.
Further information: Juha Inberg, Chief Technology and R&D Officer, Ponsse Plc
Following the launch of five new models in its 25th anniversary year in 2023, Irish Materials Handling Specialist
Combilift has already announced the premiere of yet another innovation. The Combi-CLL (Container Log-Loader) was recently exhibited at EXPO Richmond 2024, one of America’s leading trade shows for the forest products industry.
The concept and operation of the Combi-CLL is based on that of the CombiCSS (Container Slip Sheet), which has been successfully deployed across numerous industries for the mechanised loading of long products such as packs of timber or steel into containers. This not only reduces the risk of accidents to the workforce and product damage but is incredibly fast compared to other methods – a 40’ container can be fully loaded by one operator in under 6 minutes.
The 30t capacity electrohydraulically powered CombiCLL offers the same benefits when it comes to speed, safety and product integrity. It was designed to address the requirements of exporters of softwood and hardwood logs, the nature and shape of which make them much trickier to handle than palletised or
packed products. Logs can be individually lifted and preloaded into a robust, highsided metal “tub” before the patented push-pull mechanism powers the tub into the container. Once inside, the hydraulic dropdown hatch is closed and locked into position to hold the logs securely in place, and the tub is retracted to allow the logs to settle within the container.
Once again, Combilift has come up with a customer-led solution that also has potential
for applications beyond the forestry industry.
Watch the video here: https://youtu.be/1H_78Oqtlvs ?si=26BQh095DnNQTHz_ For more information, please visit: https://combilift.com/ combi-css-log-loader/ www.combilift.com
BARAGA, Mich. — Pettibone offers the Extendo 1056X telehandler, providing a 10,000-pound-capacity machine capable of reaching lift heights of 56 feet.
This Extendo unit builds upon Pettibone’s tradition of rugged design while offering numerous performance improvements.
The Extendo 1056X features a 117-horsepower Cummins Tier 4 Final diesel engine. A Deutz 74-horsepower Tier 4 Final engine is optional. Mounted on a side pod, the engine offers easy service access while allowing excellent visibility and ground clearance of 18 inches.
Featuring a four-section boom, the 1056X delivers maximum lift capacity of 10,000 pounds, max forward reach of 40 feet, and max lift height of 56 feet, 6 inches. The boom structure’s formed plates
offer greater strength while reducing weight. The design also minimizes boom deflection for better control and accuracy when placing loads. Abundant boom overlap provides smooth operation and reduces contact forces on wear pads.
The Extendo 1056X comes standard with X-Command®, a Pettibone telematics program that offers real-time access to machine data, thereby saving time, money and hassle for rental centers and maintenance technicians.
To expand its range of wireless and radio remote controls, crane and hoist control specialist CP Automation has agreed a new partnership with Tele Radio in the UK and Ireland. After two years of conversation and negotiation, the two companies are now officially partners. Following the new agreement, CP Automation will now supply the Swedish original equipment manufacturer’s extensive range of radio controls, which can support various crane and lifting applications.
Following the new agreement, CP Automation will now supply the Swedish original equipment manufacturer’s extensive range of radio controls together with existing product ranges, which can support various crane and lifting applications. Tele Radio’s range offers reliable and flexible products customizable to all kinds of specific crane, lifting and hoisting needs. When installed, the Tele Radio remote controls can improve safety in industrial applications
by enhancing operator control from a safe distance.
“This new agreement is the result of months of collaboration, negotiation, trust, and respect between ourselves and Tele Radio,”explained Andy Swann, global business manager for cranes & power transmission at CP Automation. “Like us, Tele Radio is a growing business of experienced engineers and specialists that put their customers first and pride themselves in the dependable products and support that they offer.
“Tele Radio was very open with us and, by its admission, cranes are not an industry that the company solely specialises in, so it was actively looking for a partner,” added Swann. “We’re a natural fit and, together, we can now provide greater technical support, back-up, and product choice for Tele Radio’s product customers, which CP Automation will manage using its market and product expertise.”
“Power and motion control is key to any material handling system or application — especially those involving overhead cranes and hoists,” added John Mitchell, global sales and marketing director at CP Automation. “As well as cranes, we’ll be introducing Tele Radio’s controls to our elevator customers and those working in our other core industrial markets, so that they can also benefit from the improved control these products provide.”
“Having had the opportunity to meet the team at CP Automation and to get to know them over the past two years, I know the word partnership means more to us than just a contract,” added John Suero, managing director at Tele Radio United Kingdom & Ireland. “It means that we are fully committed to each other’s success.”
Tele Radio Group is a multinational company that develops, markets and supplies universal, wireless remote controls and tailor-made wireless solutions for industrial use. The products contribute to a more comfortable and safer work environment.
Media contact Shietel Bhaggan | marketing@tele-radio.com
The Lifting Equipment Engineers Association (LEEA) has moved products, inspection, and training to the front of its Global Lifting Awareness Day (GLAD) campaign.
https://globalliftingawarenessday.com/
Introducing the Combi-CLL Log Loader, based on the highly successful Combi-CSS Container is incredibly fast compared to other methods. It can fully load logs into a 40’ container in under 6 minutes to a 30t capacity. The risk of accidents to the workforce is minimised and product damage is eliminated.
The Logs are pre-loaded into the robust, 40’ long high-sided Tub. The patented push-pull mechanism powers the loaded Tub into the container. Once inside, the Hatch is closed to hold the logs securely in place, and the Tub is retracted.
To find out how Combilift can help you unlock every inch of your storage space.
Tidewater Equipment’s third demo day was the culmination of years of careful planning. The event took place on a beautiful spring day at the Langdale farm outside Valdosta, Georgia, a key region where Tidewater has a strong support presence and a high concentration of forest industry customers.
Following previous demo days in 2015 and 2017, this was Tidewater’s largest and best attended ever. 1,600 visitors attended the one-day event that featured an allTigercat live demonstration, 21 Tigercat machines on static display, food trucks, and games and entertainment aimed at men, women and children of every possible age group.
The live demonstration was operated by Tidewater Equipment customer Sandlin Forest Products and featured a 620H skidder, 234B and T250D loaders, a 720G feller buncher and a 6900 grinder. In addition to the feller bunchers, skidders and loaders common to the US South, the static machines on display included the TCi 920 dozer, a 480B track mulcher, and the 865 and 875E loggers.
The Tigercat simulator, with its new track feller buncher program, was a big draw at the event and saw a constant flow of traffic by attendees of all ages.
Tigercat brought 57 people to the event including field representatives, product managers, designers, and key senior-level management personnel. It was an excellent opportunity to interact directly with customers, as well as Tidewater sales and technical representatives. Nothing beats first-hand feedback and an
exchange of ideas in a relaxed and welcoming setting. “I congratulate the Tidewater and Tigercat crews who worked diligently to set up this event, and of course, first and foremost, our customers,” says Tigercat founder and president Ken MacDonald. “Without them, there is no reason for the rest of us. This is simply the best way to meet and get to
know our customers.”
Tidewater president Jamie Young comments, “The turnout has been spectacular. The weather has been spectacular. It’s been a blessing to Tidewater and our customers, and we are very grateful to have the turnout we have. It was critical for us to show not only customers that we are different but our own team. We are trying to be the best dealer we can possibly be.”
“A venue of this magnitude takes years to plan, and I’ll say the Tidewater group certainly hit a homerun. Visiting and spending time with the team from one of our largest business partners and Tigercat customers from the five states they represent all at one venue was invaluable. This demo was probably the most impressive event I have attended in my 25year career at Tigercat. Thanks to the Tidewater team and our customers for making the demo a memorable event and a huge success,” says Tigercat US sales manager, Kevin Selby.
Modern forestry applications must first and foremost reduce fuel consumption and minimize emissions. No matter the power source, conventional or alternative fuels, hydrogen or electrification: ZF is contributing to reducing emissions from less to zero.
Efficient, tough, silent: this is how we envision future operation in forestry. With future-proof CVT technology, braking systems, and driveline solutions in the field of electrification, we are making this vision a reality today. ZF.com/construction
Acon Timber, the Argentinean sawmill of the Austrian HS Timber Group, celebrated the inauguration of its production site in Gobernador Virasoro, Corrientes, in April.
The plant designed for the processing of regional pine (pinus taeda and pinus elliottii) wood has an annual production capacity of 370.000 m3 dry sawn timber. The state-of-the-art sawmill operates according to the zero-waste principle, meaning that 100% of the raw material is used in the production process. This commitment to sustainability is supported by MiCROTEC solutions that ensure the best use of wood, which also reflects the continuation of the longstanding partnership between MiCROTEC and the HS Timber Group.
First Logeye including X-ray in South America
This project signifies a remarkable advancement in South America’s forestry industry with the introduction of the region’s first Logeye equipped with X-ray capabilities. The multi-sensor scanner combines the data from laser, color, and X-ray sensors to provide real 360° shape of the log. Based on this it measures a stable underbark volume of the logs throughout the variation of external conditions such as humidity or
seasonal changes and provides data for the sorting based also on the internal features of the logs such as the dimension of knots.
The Logeye works together with the Winlog sorting and control system that uses the data for accurate tracking and sorting of the logs. Additionally, it visualizes the infeed and sorting line according to personalized parameters and allows the management of stock targets, suppliers, shifts, and downtimes according to customized needs.
Extensive R&D efforts are rewarded with success
The Logeye underbark measurement has been made possible by the extensive research and development efforts involved in the project. Even training data collected by the unique MiCROTEC CT Log has been used to train the Logeye to reliably recognize the underbark diameter of
logs independently. This highlights the capabilities of the MiCROTEC Ai platform, showing the advantages of cross-learning.
Recurring trust in Goldeneye
Acon Timber’s planer mill is equipped with a Goldeneye Transverse scanner for accurate sorting and trimming from all four sides that runs at a speed of 200 boards per minute. With its multi-sensor approach the scanner integrates color, laser, and grain deviation images into one overlapping, multidimensional image, that allows the detection of defects such as knots, splits, bark, wane, and twist of boards.
The Goldeneye works together with the control suite Variosort and is fully integrated in the planer line provided by Springer. Additionally, an M3 Scan measures the moisture content of the lumber while a Warpscan measures its geometry to outsort nonconforming boards.
The Goldeneye has already been installed in previous projects with the HS Timber Group and although the wood species is different this time, the implementation has been going smoothly and the installation was completed rapidly so that it has been operational early on.
Introducing Sawbox: The innovative Wood Processing solution
Cutting capacity: Up to 8.5 million board feet of wood in two-shift operation.
Log diameter: 10 to 42 in, Lengths: 10 to 16 ft 2 in (20 ft on request)
100% self-sufficiency: Cut your own logs, optimize production costs.
Space-saving: Optimal use of operating area from 5,400 ft² to a maximum of 10,800 ft².
Long-term predictable prices: Own production ensures stable product prices.
Sustainability and regional value creation: Use of local wood, recycling of all wood waste.
Green footprint: up to 75% yield, maximizes log usage.
In the ever-evolving landscape of wood processing, it’s no surprise that efficiency and precision are paramount. Every mill operator seeks solutions that not only streamline operations but also enhance output quality. In this pursuit, BID Group presents two groundbreaking innovations revolutionizing sawlines and operations: the Mini Canter Profiler and the CETEC Twin Bandsaw featuring the new on-thefly maintenance system.
BID’s Mini Canter Profiler
Compact yet powerful, the Mini Canter Profiler stands tall as the pinnacle of efficiency in wood profiling and curve sawing, making it the ideal choice for space-conscious mills.
Features Driving Performance
The design of the Mini Canter Profiler combines the canter and profiler within a single module, along with a guillotine press roll feed module, creating a compact curve sawing system. This innovative setup not only saves space but also enhances efficiency by streamlining the cutting process. With three distinct feed modules providing a robust grip on cants during cutting, precision and consistency in output are ensured. Advanced hydraulic force control technologies further optimize performance by applying the optimal pressure on each cant, guaranteeing precise cuts, and minimizing waste. Sold with
Comact-branded secondary breakdown scanners, optimizers, and PLC systems, the Mini Canter Profiler offers a comprehensive solution for maximizing efficiency and output quality in wood processing operations.
Benefits at a Glance
• Seamless Integration: The Mini Canter Profiler’s ultracompact design ensures seamless integration into existing mill setups, minimizing disruptions and maximizing productivity.
• Enhanced Efficiency: By eliminating the need for boards to return to the edger, this innovation boosts sawmill efficiency, optimizing resource utilization and reducing processing times.
• Swift ROI: With its rapid results and tangible impact on operations, the Mini Canter Profiler ensures a swift return on investment, empowering mill owners to reap the benefits in record time.
BID Group’s CETEC Twin Bandsaw – Featuring the New On-The-Fly Maintenance System
Traditionally, changing a blade in a wood processing line meant halting operations entirely, a costly and timeconsuming endeavor. However, with the CETEC Twin Bandsaw, BID Group introduces a game-changing solution that eliminates downtime without compromising safety or quality.
Key Advantages:
• On-the-fly maintenance: Unlike conventional bandsaws, the latest CETEC Twin and Quad Bandsaw design enables blade changes during operation, thanks to its innovative saw change system. This feature not only minimizes downtime but also eliminates financial losses associated with production halts.
• Enhanced safety: With separate hydraulic units and a rear-opening bandsaw design, operators can safely perform maintenance tasks on one side while the other side continues cutting lumber, automatically shielded from potential hazards. While competitors may overlook such safety measures, at BID Group, safety is non-negotiable.
Bandmill changed during production
• Operational Efficiency: The ability to continue sawing while conducting maintenance tasks translates to unparalleled operational efficiency. Whether it’s checking lubrication, inspecting components, or replacing valves, the CETEC Twin Bandsaw keeps operations running smoothly. While it may require slightly more space and installation complexity compared to traditional bandsaws, the CETEC Twin Bandsaw’s ability to operate continuously without interruptions makes it a coveted asset in the wood processing industry.
More benefits of the CETEC include the following:
• Cutting-edge sensors continuously track the saw’s position on the wheels, automatically adjusting wheel tilt and strain to ensure precise blade tracking.
• Superior recovery rates thanks to thin kerf technology.
• Reliable performance ensured by its double column frame designed for high-strain tensioning and zero cantilever.
Both the Mini Canter Profiler and the CETEC Twin Bandsaw are not standalone solutions but integral components of BID Group’s offerings. Coupled with state-of-the-art PLC systems and optimization technologies, these innovations represent an approach to wood processing, where efficiency, precision, and safety converge to redefine industry standards.
As the wood processing industry navigates the challenges of modernization and optimization, BID Group stands as a beacon of innovation, offering solutions that not only meet but exceed the evolving needs of mill operators. With the Mini Canter Profiler and the CETEC Twin Bandsaw leading the charge, the future of wood processing looks brighter than ever. For more information, contact us at info@bidgroup.ca.
Sawbox - from debarking via scanning to stacking
The lumber industry is on the cusp of a technological revolution, and SAWBOX is leading the way with its groundbreaking ability to turn logs into lumber with just one operator.
his innovative sawmill solution is designed to meet the needs of modern wood processing operations, providing a compact, automated system that ensures efficient, high quality lumber production. Most importantly, the SAWBOX allows you to process diameters up to 42 inches that you would not be able to handle in your normal production operations. For businesses in North America the SAWBOX promises to be a game changer, delivering benefits that are too significant to ignore.
Key Benefits of SAWBOX
• Self-Sufficiency
One of the outstanding features of SAWBOX is its ability to make companies self-sufficient. By allowing companies to cut their own logs, SAWBOX helps optimize production costs and ensures a steady supply of raw materials. This level of control over the production process can significantly improve a company’s profitability and operational efficiency.
• Cost-Effective Investment
Setting up a SAWBOX is much more affordable than traditional sawing technology. The reduced investment costs make it possible for smaller companies to own and operate their own sawmills, paving the way for greater autonomy and financial stability.
• Increased vs Enhanced Yield and Efficiency
SAWBOX is designed to maximize the use of each log, achieving yields of up to 75%. This high level of efficiency not only reduces waste, but also increases the overall production, making the most of the available resources.
• Sustainability and Regional Added Value
SAWBOX supports the use of local wood and the recycling of all wood waste, promoting sustainability and boosting the local economies. By sourcing wood locally and minimizing waste, companies can reduce their ecological footprint and contribute to sustainable forestry practices.
• Predictable Pricing
With SAWBOX, companies can enjoy long-term stable product prices by controlling their own production processes. This predictability is crucial for maintaining competitive pricing and ensuring customer satisfaction in a fluctuating market.
• Impressive Cutting Capacity
The SAWBOX can process up to 8.5 million board feet of lumber in a two-shift operation. It accommodates logs from 10 to 42 inches in diameter and from 10 to 16 feet 2 inches (on request 20 feet) in length, available upon request. This versatility makes it suitable for a wide range of lumber dimensions.
• Space Efficiency
SAWBOX is designed to fit into spaces ranging from 5,400 to 10,800 square feet, allowing for optimal use of available space. This compact footprint is perfect for companies looking to maximize their production capacity without the need for large, sprawling facilities.
Embrace the Future with SAWBOX
For North American wood processing companies, the benefits of adopting SAWBOX are clear. Whether you are a sawmill, CLT or a gluelam facility, integrating the SAWBOX into your production line can lead to significant improvements in efficiency, cost savings, and sustainability. As the industry continues to evolve, staying ahead of the curve is essential. Discover how SAWBOX can transform your business, making it more competitive and resilient in a rapidly changing market. By investing in SAWBOX, you will not only improve your manufacturing capabilities, but also contribute to a more sustainable and economically vibrant community.
Explore the possibilities of SAWBOX and take the first step towards a more efficient and sustainable future for your wood processing business.
The family-owned company located in Austria (Europe), Greer (USA) and Nanaimo (Canada), plans, develops, and produces machines and state of the art solutions for the
wood processing industry. All processes, such as transporting, sorting, grading of wood, and automation, are implemented at the highest technological level. Special attention is placed on sustainability. The climate-
neutral company employs more than 500 people worldwide and is managed by the third generation of the Springer family, Timo Springer and Gero Springer.
www.springer-usa.com
Isojoen Saha Oy is constructing a new main sawmill line. The investment is one of the largest in the company’s history and continues the sawmill’s long-term development program.
The new modern main sawmill line will diversify and enhance Isojoen Saha’s production. For example, wood raw material can be utilized even better and more accurately in the future.
“Our product range will also diversify. The sawmill line enables more customer-oriented products and wider markets,” explains CEO Esa Hakamäki.
Construction work on the new premises for the sawmill line started in May 2024 and will be completed in early 2025. The sawmill line itself will be commissioned in stages during 2025. The new main sawmill line will replace the current one.
The investment brings positive employment effects to the region. Local companies, such as EP-insinöörit Oy and Rakennuspalvelut T Kiukkonen Oy from Kauhajoki, are responsible for the construction work, and several local subcontractors are involved in the project. The sawmill
line will be delivered by Veisto Oy. Other equipment suppliers are also mainly domestic.
“The multiplier effects of the new main sawmill line are substantial. The investment secures Isojoen Saha’s operations far into the future, which is significant for the entire region’s economy. We are proud of this investment in sustainable development and the vitality of our region. We want to be a reliable employer and partner for local forest owners and other stakeholders in the future as well,” says Hakamäki.
Isojoen Saha was founded in 1949, and the first logs were sawn at the same location 75 years ago. Production will continue on the current lines throughout the construction period, so there will be no interruptions in deliveries. The investment in the new main sawmill line is co-financed by the European Union.
new
line
• The area of the property to be built is 2,200 m2
• The property includes sawmill feeding, the new sawmill line, byproduct handling from sawmill production, and a feeding and intermediate storage system for green sorting of sawn timber
• Construction period 2024–2025
• The new main sawmill line will be commissioned in Isojoen Saha’s 75th anniversary year 2025
RemaSawco works with a partner in Canada who has now signed an agreement with a North American customer where RemaSawco’s order value amounts to approximately SEK 3 million
For several years now, RemaSawco has collaborated with a partner in Canada who has now signed an agreement with an end customer in the USA. RemaSawco’s part of the agreement concerns the licensing of RemaSawco’s world-leading system for board scanning, RS-BoardScannerQ, which can be used in all parts of the board handling process at a sawmill. The agreement also includes technical support during commissioning.
Delivery, installation and commissioning are planned for the third quarter of 2024.
“Just like in Sweden and the rest of Europe, North America has also suffered from limited availability of raw materials, which results in higher raw material prices. We now note
that more and more customers are discovering the benefits of our market-leading board scanner and what it can do for more efficient board sorting with higher yields using correct optimization” says Emilien Saindon, CEO RemaSawco AB
extensive experience in wood processing and treatment.
Frøslev Træ is one of Denmark’s largest timber suppliers. The company supplies timber and various processed wood products not only for the construction industry but also for retailers. Operating in southern Denmark, near the German border, the company processes timber and supplies processed wood products to its home country and to the German market, as well as to 12 other countries.
In 2016, Frøslev Træ decided to add thermally modified wood to its product range. Initially, the demand was low. According to Jørgen K. Johansen, the company’s operational director, the COVID-19 pandemic resulted in significant growth in the construction industry adding to an already prevalent trend of biocide free wood treatments, as a result of which demand for thermally modified wood surged. Frøslev Træ had bought thermally modified wood in smaller quantities from various suppliers and could no longer supply customer demand.
As demand for thermally modified wood skyrocketed, Frøslev Træ conducted a small market survey in the Danish market to understand the demand. The survey indicated a growing preference for environmentally friendly and aesthetically pleasing thermally modified wood material. Encouraged by this, the company began exploring opportunities to start its own production, leveraging its
Through these explorations, Jartek and Frøslev Træ entered into discussion. Frøslev Træ was convinced by Jartek’s experience in delivering industrial-scale production facilities. What was seen as an additional advantage according to Johansen, was that the thermally modified wood produced in Jartek’s kilns could be assigned the respected ThermoWood® product name. This ensures that the end product is of high quality and stability. ThermoWood® retains its dimensions and shape exceptionally well regardless of moisture conditions in comparison to, for example, classical biocidal pressure-treated wood.
Once Frøslev Træ decided to establish a production facility with Jartek’s equipment, the planning work began in collaboration. Jartek’s staff visited the site of the production facility. The production facility was planned in a way that the harmful gases generated during the treatment process are burned within the production facility rather than being released directly into the atmosphere. If released directly, these gases would cause unpleasant odor among other environmental issues.
ThermoWood® is treated only with heat, steam, and water and is therefore inherently more environmentally friendly than wood that has been treated with biocides. By not releasing
gases into the air, this process becomes even more environmentally friendly.
The first production facility began production in the spring of 2022, and shortly thereafter, a deal was made for a second production facility. Frøslev Træ’s customers prefer thermally treated wood to such an extent that currently one-fifth of the company’s turnover comes from
ThermoWood®. With its own production, Frøslev Træ has also improved its service level – being able to deliver from its own warehouses means that delivery times are shorter and transportation emissions have decreased.
Harri Puolanne, Jartek’s business director responsible for the project, believes that the high demand of thermally modified wood is also due to the beautiful appearance of it, as beautiful architecture and timber construction are valued in Denmark.
According to Puolanne, there were no difficulties during the construction of either of the thermal treatment kilns. The design and installation of the equipment went smoothly, and the kilns have been operating without issues in Denmark. Jartek stayed on schedule, and cooperation with Frøslev Træ and subcontractors was effortless.
Jartek’s own staff always oversee the installation
Jørgen K. Johansen, the company’s operational director
Harri Puolanne, Jartek’s business director
Thermowood Kilns at Jartek Invest Oy
and commissioning of the production facility – this time, Puolanne was present himself to ensure that everything went as planned. In Europe, Jartek also utilizes its own subcontractors for installation
work, while in projects conducted further away, local subcontractors are used.
Both Johansen and Puolanne state that the collaboration has been excellent. Johansen praises Jartek for managing the entire process from project management to maintenance support. Both Frøslev Træ and its customers have been satisfied with the quality of the end product. According to Johansen, the environmentally friendly ThermoWood® material with its excellent
properties is of interest to customers.
Frøslev Træ plans to further increase the share of thermally modified wood in its production and sales and to continue the fruitful cooperation with Jartek. Johansen sees the future of wood processing in environmentally friendly and sustainable processes such as the production of ThermoWood®.
Battle Ground, Washington
— All three of the Rockwell Automation ControlLogix analog motion modules, 1756-HYD02, 1756-M02AS, and 1756-M02AE, have reached end-of-life and, as of December 2024, will be discontinued and no longer
connect to all of the same field devices as the ControlLogix analog motion modules. Delta Motion’s sales and support team also has the expertise to support customers in converting from these modules to RMC motion controllers.
RMC User Programs can offload critical motionrelated tasks from the PLC
• Easy-to-use and powerful RMCTools software (freely downloadable)
• Analog and load cell inputs for position, pressure or force feedback
available for sale. Rockwell does not have a replacement option, which leaves a need for a motion solution that Delta Motion is uniquely positioned to fulfill. Rockwell Automation recommends that OEMs and system integrators consider RMC Motion Controllers as a replacement for these modules.
Delta’s RMC Motion Controllers can duplicate the function of the discontinued motion modules. They have the same I/O signals, communicate efficiently with Allen-Bradley PLCs via EtherNet/IP, and
Features of Delta Motion’s RMC Motion Controllers include:
• ±10V outputs (some RMCs also have ±20mA and 4-20mA options)
• Connection to feedback devices: Quadrature, SSI, PWM, Start/Stop (analog options are also available)
• Single and multi-axis: RMCs are available from 1 to 50 axes for tightly synchronizing axes
• Command-based programming keeps most control in the PLC, or the
• Extensive control algorithm options, including dualloop position-pressure or position-force control
• Knowledgeable and responsive technical support 24/7/365
To help get the word out about this replacement option, Rockwell Automation welcomed Delta Motion as a Technology Partner in the Rockwell Automation PartnerNetwork™ and arranged for a booth at the Automation Fair in Boston in November.
September 25-27, 2024
PORTLAND, OREGON
Additionally, Delta continues to develop and release information designed to make a smooth transition for all applications. With the announcement, Delta has released a complete set of details of using the RMC with an Allen-Bradley PLC, step-by-step instructions, and a video on setting up the communications between ControlLogix and the RMCs.
For more information regarding the transition from ControlLogix to the RMC, please contact Delta Motion’s technical support at technicalsales@deltamotion.com or call +1 360-254-8688.
Delta Motion and Rockwell Automation already share many customers. Rockwell Automation, as a leading global automation company, has a large installed base of its AllenBradley Logix platform. Delta’s RMC industrial hydraulic motion controllers are used extensively in conjunction with these PLCs, providing easy integration including exporting of tag names for import into Allen-Bradley PLCs.
Now, as a Technology Partner, Delta looks forward to working with more Rockwell Automation customers to achieve the best in industrial motion control.
Keitele Group, one of Finland’s largest mechanical wood processing companies, has announced that it was investing more than EUR 40 million to increase annual sawn timber capacity at its sawmill in Keitele, Finland reports FEA.
With the expansion, the Keitele Timber Oy sawmill will be capable of producing 600,000 cubic meters of finished sawn timber. The investment is planned for 2025–26.
According to the press release, the investment will increase net sales by EUR 60 million, while production at Keitele will increase by almost 50%. The investment includes a new packaging plant, additional drying capacity, a processing warehouse and batten load handling equipment, as well as 6 hectares of land and new storage buildings for end products.
The use of logs at Keitele will increase to almost 1.3 million cubic meters per year. The majority of the increasing use of wood is spruce logs, which are procured not only from North Savo but also from nearby regions.
The Finnish timber market, which has become skewed as a result of the end of Russian pulpwood imports and the increased energy use of wood, will be balanced thanks to the increased use of logs. This creates a market for longcycle raw material, which is processed into sawn timber and wood products to store carbon.
Keitele Timber Oy’s total sawn timber production capacity will increase to 1.25 million cubic meters of finished sawn timber. The company’s other production facilities are located in Alajärvi, South Ostrobothnia and Kemijärvi in Lapland. The three modern plants use a total of nearly 2.7 million cubic meters of high-quality Finnish conifer logs per year, and the wood procurement of Keitele Forest Oy, the Group’s parent company, covers more than 60% of the need.
BID Group, a pioneer in wood processing solutions, has announced that it has been bestowed with a distinguished award as OEM Partner of the Year from Rockwell Automation.
The award, presented during The PartnerNetwork™ Conference, hosted by Rockwell Automation, recognizes BID Group’s outstanding commitment to ensuring customer success. Rockwell Automation, a global leader in industrial automation and digital transformation, uses its PartnerNetwork™ Awards to commend organizations that exhibit exceptional performance in implementing transformative solutions, thereby fostering collaboration and innovation within the industry.
“We are deeply honored to receive this award from Rockwell Automation,” said Simon Potvin, President of Wood Processing at BID Group. “Our relationship with Rockwell has transformed from a provider to a partner
status, enabling us to deliver unmatched support and solutions for our customers. Through this collaborative journey, we’ve identified and implemented innovative solutions specifically tailored to address the demands of the wood processing industry.”
The award highlights BID Group’s ongoing efforts to leverage advanced technologies, including artificial intelligence and digital automation, to revolutionize wood processing workflows and optimize production efficiency. By partnering
with industry leaders like Rockwell Automation, BID Group continues to push the boundaries of what’s possible, delivering unparalleled value to its customers and driving positive change in the wood processing industry.
“We extend our heartfelt gratitude to Rockwell Automation for this honor, to our dedicated team whose hard work has made this achievement possible, and, of course, to our highly valued customers, regarded not only as clients but also as partners,” commented Simon Potvin.
JS-50 X6B CARRIAGES & SHORT-INFEED EDGERS
JS-50 TRIMMERS
JS-50 Z8 END-DOGGER, C FRAME & HI SPEED SNAPSHOT
Kalesnikoff has announced it will construct a third location this year. While the exact location of the new facility won’t be announced for a few more weeks, a Kalesnikoff recent press release says it will be located near the existing mill and mass timber facility in the NelsonCastlegar corridor.
The building itself will be constructed in part using Kalesnikoff’s own mass timber components. Groundbreaking is anticipated soon with a targeted opening by the end of 2024.
Once complete, the new facility will create up to 90 new jobs. The company says the new offerings will complement existing Kalesnikoff products and will be used for walls, flooring and full modular construction mass timber projects.
“We have experienced consistently strong interest and demand in our initial mass timber investment announced almost exactly five years ago,” Chris Kalesnikoff, chief operating officer of Kalesnikoff Mass Timber, said in a release.
“This additional offering of leading mass timber products and services for the North American construction industry will support mass timber buildings including student
Slocan that produces prefabricated engineered building products in the form of gluedlaminated beams and crosslaminated timber. On opening, it created 60 new jobs, but now employs 160.
Products and services at the new facility will include modular construction, prefabricated mass timber and light frame components,
and workforce housing, prefabricated housing and other mass timber projects.”
In 2019, Kalesnikoff expanded into the mass timber market with a $35-million manufacturing facility in South
and custom installation-ready products to meet customers’ needs. It will also increase Kalensnikoff’s glue laminated timber capacity.
The HCK continuous kiln dryer is BrunnerHildebrand´s answer to the increasing demand for continuous kiln drying technology, especially in the expanding marketplace of the softwood industry. The HCK operates in unidirectional mode with lumber package motion through the kiln in longitudinal orientation. This comes as a big advantage in terms of mill workflow with a clear distinction between wet side and dry side. Forklift transport is reduced to a minimum, no mingling of wet and dry lumber storage any more!
loss over time. The benefit is a much tighter mc control with hundreds of boards or more determining the current average mc.
Brunner-Hildebrand´s HCK is divided in length into several drying zones. The number and size of these drying zones are designed according to the customers´s desired KD output. The kilns are rail-loaded and may operate on a single rail or with up to six rails depending on customer specs. Roofings may be added in front of the HCK and behind to shelter lumber from rain and snow.
With some degree of simplification, the HCK dryer may be regarded as a number of batch kilns placed next to each other with lumber flow breaching through the side walls of the individual chambers. Each drying zone is tightly controlled in terms of temperature, air speed and relative humidity – all of these parameters adapted to the actual level of lumber moisture content.
Air speed generated by heavy-duty axial fans is controlled by VFCs with periodical reversal of flow direction. This eliminates wet spots and results in homogenous final moisture content of the lumber load.
Brunner-Hildebrand´s HTT (Hildebrand Turbo Technology) system raises airspeed to the maximum without the necessity of installing overly large fans with high power consumption. HTT consists of
aluminum baffles which are periodically moved in vertical direction, thus shutting certain sections of the lumber stacks off from the air flow. This increases air velocity in the sections that are still exposed to the air flow while air speed is reduced to almost zero in the baffled sections. This brings about a recurring conditioning effect which results in minimized spread of final mc distribution.
Kiln carts are moved through the HCK by powerful hydraulic pusher units inserted into the concrete foundation at the kiln entrance. Hydraulic power is sized for pushing the entire lumber load forward throughout the kiln. Indexing of the kiln carts is performed in full automatic mode, with surveillance by a comprehensive set of photoelectric sensors and end switches.
As an integral part of the kiln carts, Brunner-Hildebrand installs their revolutionay HWPT (short for „Hildebrand Weight Precision Technology“) system. With these wireless weight measuring bars, customers are capable of measuring the weight of the entire lumber stack resting on top of the kiln cart and record the weight and moisture
With a multi-rail HCK, the customer is even given the opportunity of drying several lumber dimensions in one continuous kiln by simply running different throughput rates for each track. With Brunner-Hildebrand´s special feature, the Kiln Prime Zone (KPZ), this even works for lumber dimensions with differing final target mc.
With Brunner-Hildebrand´s game-changing GreenKilns technology, the individual drying zones of the HCK cooperate in a thermal compound system. Excess heat from one drying zone will be extracted and guided to another drying zone which is in actual demand of additional heat. This way, up to 25% of thermal consumption may be saved and reused for lumber drying in an ecofriendly way.
In 2024, PATA - the leading forest management, lumber production, logistics and trade company in Latvia – finished commissioning the last of four Hildebrand HCK continuous kilns for their greenfield project at Jekabpils, about 85 miles southeast of the capital city Riga. All of these kilns feature GreenKilns, HTT, HWPT and individual zone control as described above. Customer feedback has been highly positive with kiln capacity exceeding sawline output considerably and lumber grade exactly at the desired level.
For more information on Hildebrand Continuous Kilns and various other types of kiln dryers, please contact andreas. mueller@brunner-hildebrand. com or visit www.brunnerhildebrand.com.
Virginia Carolina Forest Products in Lawrenceville, VA, is using just one USNR lineal grader to grade both a pine and a mixed rough hardwood lumber line in a new, more efficient application design.
The production lines run parallel to one another and the scan frame is placed on a rail system that intersects both. At the flip of a switch, the scan frame can easily move between the more heavily used planer line and
the hardwood line. As each board reaches the landing table, an overhead board tracker projects the grade onto each board to be screened by a quality control technician.
This quick-switch setup will allow both lines to receive
faster, more accurate grading for increased value.
USNR is grateful for the opportunity to apply this new technology to the production lines at Virginia Carolina Forest Products.
USNR recently implemented several upgrades to the batch kiln at Toney Lumber in Louisburg, North Carolina. This project included reskinning the kiln, replacing the doors, and upgrading to more efficient materials. The all-aluminum door panels and skins with wrap-around style corners minimize leaks, improving drying times and providing
better structural integrity to produce top-quality lumber products.
USNR works closely with Toney Lumber in Louisburg on these essential maintenance and upgrade projects.
Visit their web page or contact a USNR representative to learn more about the complete lineup of lumber drying technology.
In Masterton, New Zealand, Kiwi Lumber is streamlining their operation with a new MillExpert Log Sorter system to identify badly shaped or oversized logs for removal prior to entering the sawmill log breakdown line.
Comprised of four Bioluma 3900L sensors and USNR’s
MillExpert software, this log sorter system immediately improves throughput by keeping logs flowing steadily into the sawmill while also helping prevent log jams.
USNR is proud to be part of this project to improve Kiwi Lumber’s operation.
Sensor
In 2019 Pleasant River became the first North American company to invest in Valutec’s drying technology
“They are the best kilns out there!”, said Chris Brochu, co-president of Pleasant River sawmill group, when he, together with his brother Jason Brochu, received the prize as Timber Processing’s sawmilling person of the year 2023. In 2019 Pleasant River became the first North American company to invest in Valutec’s drying technology.
“The best kilns out there!”
Since then they’ve invested in another three Valutec TC continuous kilns. Other notable North American companies that have invested in Valutec kilns are JD Irving, Hampton Lumber and Spruce Products.
As the leading developer and world leader in continuous kilns Valutec has delivered more than 1 500 continuous kilns to sawmills around the world. The latest development is the “TC continuous kiln”. A sustainable state-of-theart kiln that combines high capacity and flexibility with excellent quality and low energy consumption.
Valutec kilns are probably the market’s most sustainable timber kilns. Constructed in stainless steel, resistant to thermal expansion and fatigue, the kilns have superior longevity (minimum 40 years), require no reskinning and minimal maintenance. The kilns are equipped with efficient IE5 fan motors,heat recovery systems and many energysaving functions in their control system which make the kilns
very energy efficient. Studies shows that Valutec’s stainless steel TC continuous kiln emits 23 tons less CO2 per year than the correspondent kiln built in aluminum. 23 tons of CO2 is about as much as three hectares of coniferous forest absorbs in a year.
The TC Kiln
Valutec is the only company offering TC kilns. A kiln type that comes with distinguishing features such as low energy consumption, high flexibility and superior capacity. It gives the operator the possibility
to create the ultimate drying process with freedom to mix dimensions, minimal moisture content variation and reduced risk of checking. Annual capacity can reach 150 MMBF with target moisture contents down to around 12-18% with a standard deviation of 1%. The principle is based on the timber package being fed length-wise through zones in which the air circulates laterally across the drying channel. This enables the separate regulation of the climate in different zones according to a schedule that comes very close to the ideal schedule of a batch kiln.
“The leap in technology has fundamentally changed the way of working at many sawmills. Higher flexibility creates significant advantages,
Since the beginning of 2023 Robert Weithofer is Valutec’s North American sales representative particularly when it comes to planning. Competition is extremely tough in the sawmill business, where margins are tight. So, customers in this sector rely on high efficiency and quality,” says Robert Larsson, Managing Director, Valutec.
Valmatics 4.0
Valutec’s control system
Valmatics 4.0 allows sawmills around the world to automate
Pleasant River Lumber
Pleasant River Lumber owns and operates 2 lumber manufacturing facilities, multiple log purchasing yards, two saw filing shops, and a trucking company spread out across the State of Maine. They operate two SPF Spruce/Fir framing lumber mills.
The SPF Mills current capacity is 300 million board feet annually. The SPF product line consists of 2×3 through 2×10 dimension lumber and 1×3 through 1×6 boards 6’ to 16’ long.
The company has invested heavily in modern sawmill, drying, and planing technology to ensure maximum yield and consistent quality.
and optimise drying in all types of lumber kilns. High process quality is guaranteed by simulators programmed with data from hundreds of thousands of measurements that enable the calculation of drying processes with unbeatable accuracy from beginning to end. Valmatics 4.0 means modern TC continuous kiln functions can be put to full use. All the kiln operator needs to know is the incoming and desired outcoming moisturecontent – the system does the rest.
ValuSim, the calculation program for moisture content in Valutec’s control system “Valmatics 4.0” is based on a physical model for the diffusion of water from a wooden surface. The calculation model has been refined over many years and can today calculate moisture ratio with approx. 1% accuracy. As input data, temperatures measured for the
They ship their products in the Eastern US, using rail, flatbed trucks, containers, and dry vans. PRL prides itself on providing high-quality products and long-term consistent business relationships.
A&A Brochu Logging Operations (Pleasant River Lumber)
They are a cut-to-length operation using a Ponsse Scorpion King Processor and a new Ponsse Buffalo Forwarder that are running 2 shifts currently cutting 10 t/l’s of spruce per shift for their Enfield mill. They thin around 20 acres a week per shift.
current drying batch are used as well as information about the properties of the dryer together with the dimensions of the wood, wood species, etc. ValuSim is fully integrated into Valmatics 4.0 and can be used for both calculation of the current moisture content and to generate drying schedules. Valmatics 4.0 is the only control system on the market that combines simulator technology with adaptive control, and enables optimization based on capacity, quality and energy consumption. Simultaneous.
“It’s a faster and better way to dry lumber”, Jason Brochu co-president of Pleasant River sawmill group.
The TC kiln has reduced our energy consumption with more that 30%, states Mario Desjardins, General Manager, J.D. Irwing, CA.
“VIDA strives to have the latest technology at all times. It will be very interesting to evaluate how much the TC kiln can help us streamline our production,” says Jonas Axelsson, Technical Director, VIDA GROUP, SWE.
“We want to increase the drying capacity at our sawmills in Preding and Sachsenburg and saw that TC kilns were right for us. They offer a combination of high capacity and flexibility, without compromising on quality,” says Michael Fercher, CTO at HASSLACHER Group, AUT.
The TC kiln does a great job, in a lot less time than we’re used to and puts out a much better product”, says Fred Haigis, Lumber Yard Supervisor Moose River, US.
Ponsse Scorpion King Processor
Agility, power, ergonomics, weight distribution and economic efficiency – these are the features that set PONSSE forwarders apart. You can
choose from various models suitable for soft terrain and steep slopes alike. Power and some the best comfort features in forests are standard equipment.
This forwarder has what it takes to ensure productive operations even in the most demanding logging sites.
LOAD CARRYING CAPACITY
25 000 kg (55,116 lbs)
POWER
210 kW (286 hp) EU and North America
220 kW (299 hp) other countries
TRACTIVE FORCE
320 kN (71,938 lbf)
LOADER
K121 M/S
LOAD SPACE CROSS-SECTION
6.8 m² (73.2 sq ft)
VLA 8.0 m² (86.1 sq ft)
GROUND CLEARANCE
800 mm (31.5 in)
MINIMUM WEIGHT
28 500 kg (62,832 lbs)
TYPICAL WEIGHT
29 300 kg (64,595 lbs)
TIRES
28,5’’
All PONSSE forwarder models have more than enough power for changing conditions and difficult terrain types. The excellent weight to load-carrying ratio, the
smallest turning radius in their size classes and dimensions that distribute loads evenly to all wheels are prominent features. The extreme tractive force of their forwarders
Powerful engine, never-ending tractive force and 20-ton load-carrying capacity.
LOAD CARRYING CAPACITY
20 000 kg (44,093 lbs)
POWER
210 kW (286 hp) EU and North America
205 kW (275 hp) other countries
TRACTIVE FORCE
240 kN (53,954 lbf)
LOADER
K121 M/S, K111 S/M
LOAD SPACE CROSS-SECTION
5.8–6.7 m² (62.4–72.2 sq ft)
VLA 5.2–6.7 m² (56–72 sq ft)
GROUND CLEARANCE
800 mm (31.5 in)
MINIMUM WEIGHT
22 900 kg (50,486 lbs)
TYPICAL WEIGHT
23 700 kg (52,249 lbs)
TIRES
26,5’’
25T 20T
guarantees excellent comfort and efficiency, particularly over longer distances. Ponsse’s range has some of the most productive forwarders in the markets, both for thinning and regeneration felling.
Ponsse’s forwarders are the only forest machines in the world that use a continuously variable transmission (CVT). This enables higher fuel economy and tractive force, particularly in difficult terrain.
This workhorse gets the job done in conditions which often are too challenging for others.
LOAD CARRYING CAPACITY
18 000 kg (39,683 lbs)
POWER
210 kW (286 hp) EU and North America
205 kW (275 hp) other countries
TRACTIVE FORCE
220 kN (49,459 lbf)
LOADER
K121 M/S, K111 S/M
LOAD SPACE CROSS-SECTION
5.8–6.25 m² (62.4–67.3 sq ft)
VLA 5.2–6.7 m² (56–72 sq ft)
GROUND CLEARANCE
800 mm (31.5 in)
MINIMUM WEIGHT
22 000 kg (48,502 lbs)
TYPICAL WEIGHT
22 800 kg (50,265 lbs)
TIRES
26,5’’
18T
PONSSE forwarders, equipped with ultimate tractive force, guarantee efficient timber transportation – while saving the environment as much as possible.
A straightforward, yet extremely dependable tool with well-thought-out technical systems.
LOAD CARRYING CAPACITY
18 000 kg (39,683 lbs)
POWER
210 kW (286 hp) EU and North America
205 kW (275 hp) other countries
TRACTIVE FORCE
210 kN (47,210 lbf)
LOADER
K100+ M/S, K101 M/S, K111 M/S
LOAD SPACE CROSS-SECTION
5.2–5.8 m² (56–63 sq ft)
GROUND CLEARANCE
730 mm (28.7 in)
MINIMUM WEIGHT
20 600 kg (45,415 lbs)
TYPICAL WEIGHT
21 100 kg (46,517 lbs)
TIRES
26,5’’
18T
This forwarder goes where you want it to go, easily and effortlessly.
LOAD CARRYING CAPACITY
14 000 kg (30,865 lbs)
15 000 kg (33,069 lbs) with balanced bogies
POWER
210 kW (286 hp) EU and North America
205 kW (275 hp) other countries
TRACTIVE FORCE
185 kN (41,589 lbf)
LOADER
K90+ M/S, K100+ M/S, K101 M/S, K111 M/S
LOAD SPACE CROSS-SECTION
4.5–5.5 m² (48.4–59.2 sq ft)
VLA 4.5–6.0 m² (48.4-64.6 sq ft)
GROUND CLEARANCE
680 mm (26.8 in)
MINIMUM WEIGHT
18 600 kg (41,005 lbs)
TYPICAL WEIGHT
19 800 kg (43,651 lbs)
TIRES
26,5’’
An exceptionally fast forwarder that moves slickly in all types of terrain and even over longer distances.
LOAD CARRYING CAPACITY
16 000 kg (35,274 lbs)
POWER
210 kW (286 hp) EU and North America
205 kW (275 hp) other countries
TRACTIVE FORCE
210 kN (44,961 lbf)
LOADER
K101 M/S, K111 M/S
LOAD SPACE CROSS-SECTION
4.5–5.5 m² (48.4–59.2 sq ft)
VLA 4.5–6.0 m² (48.4-64.6 sq ft)
GROUND CLEARANCE
680 mm (26.8 in)
MINIMUM WEIGHT
22 000 kg (48,500 lbs)
TYPICAL WEIGHT
26,5’’ 14T15T 16T
22 600 kg (49,824 lbs)
TIRES
A powerful and durable forwarder with a first-rate load-carrying capacity.
LOAD CARRYING CAPACITY
13 000 kg (28,660 lbs)
POWER
150 kW (204 hp) EU and North America
145 kW (197 hp) other countries
TRACTIVE FORCE
175 kN (39,341 lbf)
LOADER
K70+ M, K90+ M/S
LOAD SPACE CROSS-SECTION
4.5–5.0 m² (48.4–53.8 sq ft)
VLA 4.5–6.0 m² (48.4–64.6 sq ft)
GROUND CLEARANCE
670 mm (26.38 in)
MINIMUM WEIGHT
17 700 kg (39,022 lbs)
TYPICAL WEIGHT
18 800 kg (41,447 lbs)
TIRES
26,5’’
An agile, lightweight forwarder with excellent power, visibility, and load-carrying capacity.
LOAD CARRYING CAPACITY
12 000 kg (26,455 lbs)
POWER
150 kW (204 hp) EU and North America
145 kW (197 hp) other countries
TRACTIVE FORCE
165 kN (37,093 lbf)
LOADER
K70+ M
LOAD SPACE CROSS-SECTION
4.0–4.5 m² (43.1–48.4 sq ft)
GROUND CLEARANCE
645 mm (25.4 in)
MINIMUM WEIGHT
16 300 kg (35,935 lbs)
TYPICAL WEIGHT
17 300 kg (38,140 lbs)
TIRES
26,5’’ 13T 12T
HWhen you step into the cab, you as a driver is greeted by a workplace that leaves nothing to chance
igh ceiling, a spacious airy feel, smart storage. Even a built-in food heater with timer function. A generous storage compartment that runs along the entire windscreen, part of the space is cooled by the machine’s air conditioning system. Perfect for storing your packed lunch. Large windows that give you a fantastic view around the machine. The air conditioning system with its automatic temperature control and efficient air filtration that also purifies the recirculating air ensures a workplace where you can be efficient throughout the shift. Even during the coldest and warmest days of the year. With main power activation via the door switch, the system starts up automatically and the operator starts safely at the touch of a button after entering their personal start code on the lever palette. The clean surfaces of the cab and few buttons in the side panels give a neat and modern impression.
All the important functions that are used continuously during the work shift are close at hand in the newly developed lever palettes, all to make everyday life easier for the driver. Color displays in the lever palettes provide the operator with the most important information, but also support for getting started with the machine for e.g. an inexperienced trailer operator who does not drive the machine on a daily basis. The phone is easily connected to the machine’s sound system with ‘Bluetooth’ and placed in the phone dock with built-in antenna amplification. The generous indoor lighting with a LED strip in the ceiling and at the floor both front and back makes it easy to take care of administrative tasks even in the dark hours of the day. When driving, the interior lighting switches to a color of your choice that provides a pleasant light when driving in the dark.
Rottne as a manufacturer values operator comfort highly. It is the operator who allows the machine’s performance to be fully utilized, and therefore it is important that the operator has good conditions. Part of this work is our cab suspension, Comfort Line. It has become even better. After many years of experience with cab suspension, we have taken it to a new level. The entire structure has been given a lift and become even more robust than before. Weak points have been improved, all to improve operational reliability. Better hose routing, newly designed cylinders with high-quality bearings and sealing systems designed for the tough task. The suspension has been given a new hydraulic solution with adjustable damping for different terrain conditions. With a simple push of a button, the driver can choose between
three different damping levels that can also be adjusted to each individual’s wishes. Informative menu for sensor calibration and possible troubleshooting.
On our largest forwarder models, the F18/F20E, we have a robust drive with substantial traction. Fully automatic three-speed gearbox with two hydrostatically driven motors delivering up to 27 kN. The machine’s software handles speed control and shifting using the operator’s instructions and an active load control that gives the machine efficient propulsion both with and without a load. The operator can easily adjust to the right speed using a potentiometer on
the lever palette along with ergonomically designed, highresolution accelerator pedals. For long forwarding distances or moving to the next object, a cruise control is available.
For the smaller forwarders, we use a transmission control from Rexroth. This gives us a safe and fast control of the transmission.
On our intermediate forwarder, XTF (Extra Traction Force) is now available as an option. It provides 12% better traction for the really tough offroad conditions. A good option together with a balanced bogie. All forwarders use a traction limiter that is managed by the software in the machine. This gives the machine a better behavior if the terrain requires maximum traction to perform the work.
All Rottne’s forwarder models have self-designed cranes. If, on the other hand, you choose a longer range, we have a good collaboration with Epsilon. The performance of the cranes is well balanced with the size of the machine and hydraulic system. RCA (Rottne Crane
Assistance) is available as an option on most variants. The system helps the operator to efficiently operate the crane throughout the shift.
With the E-model, we want to give you as a user a high level of comfort during many work shifts.
The 1055C is a heavy duty 14-tonne forwarder built to handle both selective harvesting and final felling applications. In order to meet the needs of a global market, the 1055C has two bogie choices, two transmission choices, two sizes of level-load bunk systems, and three wagon frame lengths. Crane choices include the standard Mesera M92FT100, and the Tigercat F135T85 hooked crane. Both are available with various grapple options.
With a 20-tonne capacity, the 1075C is designed for long distance forwarding, tough terrain and scarifying applications. The two Tigercat hooked crane choices are the F165T85 and the F195T85. With optional extreme duty Tigercatbuilt bogies, the 1075C excels in tough terrain and slopes and operates with minimal soil disturbance due to the extra-long 1,89 m (74 in) bogie walking beams. An optional
two-speed transmission is perfect for long forwarding and moderate terrain.
The 1085C has a massive 25-tonne capacity. It excels in severe duty, steep slope applications. An optional steep slope package includes a 25° rearward tilting crane, a moving reinforced gate, 21 tonne (23 US ton) rear frame tethering lugs, and an optimized steep slope bunk design. A baffle system in the fuel tank ensures a constant supply on steep
ground. The front bogie pinion and transmission are pressure lubricated. The Tigercat-built drivetrain provides torque that is unmatched in the industry. Tigercat’s WideRange transmission provides plenty of tractive effort to carry large loads on steep slopes and achieves a maximum working speed of 7 km/hr with a single gear ratio. The 1085C can attack and manoeuvre steep slopes under load with ease.
Hooked crane profile and lowwide bunks
Tigercat cranes are capable of heavy loads and tough duty cycles. The slew base has a tapered roller bearing system designed to last the life of the machine, and no plain slew bearings or spherical rollers often used in other cranes. The crane’s hooked profile is designed to increase the working envelope of the crane for reduced machine travel and improved productivity. But where the crane really shines is when used in combination with Tigercat’s new low-wide expandable bunk systems.
In addition to a conventional flat loading expandable bunk system, Tigercat has optional low-wide® bunks, which are inclined rearward to reduce overall gate height and eliminate the need for a vertically sliding gate. In combination with the hooked crane, the low-wide bunk system significantly reduces the chance of crane contact with the gate or bunk stakes. Operator visibility and productivity is enhanced. The operator enjoys a clear sightline to the top of the load, increasing log placement accuracy and decreasing cycle times. In addition, the grapple stays within the operator’s view through the entire loading and unloading cycle for reduced operator strain.
The low-wide system is available for both the 1075C and 1085C forwarders.
Operator’s Station
Crane control is very smooth and predictable with optimized flow sharing features so
crane movements are precise over a variety of loads and conditions. Tigercat forwarders are equipped with a modern, spacious and comfortable cab. Extended windows provide excellent visibility to the load area and the ground. Operators comment about an open feeling even after a long shift in the cab. A rear window guard provides more protection and comes standard on all forwarder cabs. A quiet environment is important for operator comfort and productivity. The forwarder cab is insulated and isolationmounted for reduced noise and vibration levels. A variety of operator convenience options is available. Each machine comes with a TPMS system for maximum tire life. LogOnTM comes standard on Tigercat
The Alstor 834 has a completely new front chassis where the removable belly plate creates very good serviceability. Operator ergonomics have been optimised with reduced cab noise levels and increased
storage. The traction is greatly improved with a 24 hp Yanmar engine. The new clutch provides better control and power in difficult and advanced
Cont’d from Page 48
forwarders and RemoteLog® telematics is optional, along with a data package paired to the warranty period purchased with the machine.
Tigercat forwarders the levelload bunk system are available with an optional payload scale system. Payload data is conveniently displayed in the cab, including a load counter and a tare weight reset button. Payload scales can also be integrated with the optional F30 productivity system. Actual load weight can be added to data uploaded from the harvester to make it easier to track productivity, maximize production, and provide load information for the mill. The F30 productivity system can
also generate StanForD classic or 2010 reports from the data Service
Tigercat forwarders have unsurpassed service access to all electrical, mechanical and hydraulic systems. Access to the engine, driveline, and pumps is through the tilt-out hood enclosure and tilting cab. Hydraulic valves and computer control modules are located in one compartment in the wagon frame. Easily accessed from ground level, hydraulic adjustments are simple to perform. Hydraulic cleanliness is easy to maintain with spin-on hydraulic filters and an electric oil-filling pump. Electrical reliability is excellent due to short wire runs between the control modules and valves located immediately beside them.
Tigercat Mulching Heads are an End To End management solution. They are well matched to the high performance and capabilities of Tigercat Mulchers including the M726G, 760B, 470 and 480B models.
The 4061 and 4054 mulching heads are manufactured to Tigercat’s exacting high standards for robustness and quality. The 4061-30 is a 3 metre (118 in) wide mulching head that can be used on the 480B and 760B mulchers. The 4061-25 is a 2,5 metre (98 in) wide head, best suited to the 480B and M726G mulchers.
The 4054-20 is a 2 metre (79 in) wide head best suited to the 470 mulcher.
The housing features reinforced side covers and abrasion resistant skis. The housing is optimized with debris door cylinders mounted internally for protection and contains position references to aid in ski alignment. Poly chain eliminates belt slip and provides efficient power transfer to the rotor, lowering maintenance time and costs associated with conventional v-belts.
Regular maintenance is a snap, maximizing uptime. Large removable side panels give
The 4161-15 mulching head, when paired with the LX830E is a highly capable steep slope mulcher
access to the drive belts and sprockets. Many removable panels on the head provide excellent access to all service points. Features such as bolt-in wear liner and reversible anvils all help to increase overall uptime.
4161-15 swing to tree mulching head
The newest addition to the Tigercat mulching head line is the 4161 swing to tree mulching head. The 4161-15 is a 1,5 metre (59 in) heavy-duty swing to tree mulching head is optimized
for use on Tigercat 800 series carriers.
The 4161-15 uses many field proven components common to other Tigercat mulching heads. There is a choice of standard drum rotor or feed control rotor with depth gauges in front of each tooth to control the cutting depth, reducing load on the machine. The rotor design is similar to 4061 series mulching heads. Tool choices include standard carbide, heavy-duty rock resistant carbide, and hardened steel knife style.
The 4161-15 pivots 130° (+/- 65°) left or right on a hydraulically controlled wrist. Hydraulic hoses to the head are routed through the open boom tip of the carrier and connected to a manifold in the wrist. This routing minimizes exposed hoses, aiding in reducing wear and damage.
When paired with the Tigercat LX830E, this minimal tail swing, leveling machine is highly effective at fuel load management and fire mitigation on steep slopes and tight areas.
The FAE BL1/EX range expands with a new model that eliminates the need for motor draining. The new model for 4.5-to-7.5-ton excavators, features a newly conceived gear motor, with easier and more costeffective installation.
The BL1/EX-75 can mulch light vegetation, shrubs, and trees up to 12 cm in diameter. It can be used to control vegetation along roadsides, railroad tracks, and the banks of canals, rivers and lakes, to manage and protect wildlife habitats, and to maintain commercial parks and sports grounds.
The new BL1/EX-75 model replaces the old, piston-motor model, and is complemented by the VT model, with the same operating width.
The Bite Limiter technology on this head is ideal for high-productivity vegetation management, with reliably efficient shredding. The Bite Limiter rotor uses special
FAE expands its line of forestry mulchers with Bite Limiter technology with a model designed for mid-range excavators: the BL2/S/EX for 11–16 ton excavators.
The BL2/S/EX can mulch vegetation, shrubs, and trees up to 15 cm in diameter. It is designed for forestry management, roadside and railway maintenance, maintaining the banks of canals, rivers and lakes, and managing and protecting wildlife areas.
The Bite Limiter technology on this head is ideal for high productivity vegetation management, with reliably efficient shredding. The rotor with Bite Limiter technology comes with special wearresistant steel profiles that limit the reach (bite) of the
teeth. This cuts down on power demand and promotes a consistent working speed, for excellent performance when mulching any kind of wood. Bite Limiter technology also minimizes rotor stalling and optimizes fuel consumption.
The sturdy steel frame is built to last, just like all FAE products. The toothed belt transmission provides optimal power transfer and long-term reliability. Interchangeable bolt-on Spike Pro counter blades and skids and a hydraulically adjustable hood are also major design features.
wear-resistant steel profiles to limit the reach (bite) of the teeth. This cuts down on power demand and promotes a consistent working speed, for excellent performance when mulching any kind of wood. The
Bite Limiter technology also minimizes rotor stalling and optimizes fuel consumption.
The new BL1/EX-75 can be equipped with BL/MINI blades or C/3/MINI teeth and is available in an operating width.
The BL2/S/EX is also available with FAE’s exclusive Sonic system, which keeps the operating carrier and the FAE mulcher completely aligned by automatically calibrating and constantly regulating the mulcher’s hydraulic parameters for a significant boost in productivity. The FAE app is also available for technical support and makes it possible to quickly and easily calibrate the Sonic system for fast and accurate connection to the operating carrier so you can get the highest level of productivity from your FAE mulcher.
The new BL2/S/EX can be equipped with BL blades or C/3 teeth and is available with a working width of 125.
www.fae-group.com
UK, Europe, South Africa, US East Coast
CONTACT: Robin Peach
International Forest Industries Ltd
Tel: +44 (0)1442 877 777
Fax: +44 (0)1442 870 617
robin@internationalforestindustries com
Japan
CONTACT: Shigeru Kobayashi
Japan Adver tising Communications, Inc.
Star Bldg., 3-10-3 Kanda Jimbocho
Chiyoda-ku, Tokyo 101-0051
Tel: 81-3-3261-4591
Fax: 81-3-3261-6126
Email: Shig-kobi@media-jac.co.jp
Western USA (AZ, C A, NV, UT)
Australia, & New Zealand
CONTACT: Kevin Lapham
J.P.Media Inc
Tel: +1 (630) 420 9752
Fax: +1 (630) 420 9763
Email: lapham@jpmediainc.com
Western USA (MT, ID, OR,WA) & Canada
CONTACT: Kevin Lapham
J.P.Media Inc
Tel: +1 (630) 420 9752
Fax: +1 (630) 420 9763
Email: lapham@jpmediainc.com
US Mid-West, Central & Mountain
CONTACT: Kevin Lapham
J.P.Media Inc
1163 E.Ogden Ave, Ste. 705-359 Naper ville
I L 60563, USA
Tel: +1 (630) 420 9752
Fax: +1 (630) 420 9763
Email: lapham@jpmediainc.com
Cont’d from Page 45
terrain. The new simplified powertrain provides better braking performance and creates better serviceability and reliability. The Alstor 834 now also has electrically lockable differential gears, which provide even better agility and accessibility and have a smaller footprint in the forest and land. The newly developed timber nest has sturdier bunks and a design that
facilitates loading and unloading. The new design also makes it easier to adapt to Alstor’s different load concepts and special adaptations.
SAWLINES
International Forest Industries Magazine (IFI) stands as a premier forestry publication globally, delving into timber harvesting, forwarding, haulage, and sawmill operations. From timber handling to cutting-edge technology and logistics, IFI provides comprehensive coverage. We also address biomass collection and processing, bridging the longstanding gap in forest-related industries for suppliers in timber harvesting, sawmill operations, and biomass management.
SAWMILLING • LOGGING • BIOMASS • RENEWABLE ENERGY
APRIL / MAY 2024
Thinning Harvesters • Chippers SAWLINES
FAST INSTALLATION
SIMPLE OPERATION
MAXIMUM VALUE EXTRACTION
FEB / MARCH 2024
SAWMILLING • LOGGING • BIOMASS • RENEWABLE ENERGY
FEBRUARY / MARCH 2024
SAWLINES
Planers & Edgers
Harvesters
Lifting & Loading
SAWMILLING • LOGGING • BIOMASS • RENEWABLE ENERGY Dec / JANUARY 2024
SAWLINES
Planers & Edgers
Biomass
Steep Slope
Harvesting
Felling Heads
SAWMILLING • LOGGING • BIOMASS • RENEWABLE ENERGY
OCTOBER / NOVEMBER 2023
SAWLINES
Harvester Heads Forestry Mulchers Track Carriers
AUGUST / SEPTEMBER 2023
SAWMILLING • LOGGING • BIOMASS • RENEWABLE ENERGY
AUGUST / SEPTEMBER 2023
SAWLINES
Skidders
Shredders & Grinders
Scanning & Optimisation
JUNE / JULY 2023
SAWMILLING • LOGGING • BIOMASS • RENEWABLE ENERGY
JUNE / JULY 2023
SAWLINES
Forwarders
Harvester
Head Launch
CVT Technology
New Harvester
APRIL / MAY 2023
SAWMILLING
SAWLINES
Chippers
Access to the Timber Stand Feller
Bunchers
Efficient, clean and safe: this is how we envision future off-road operation with intelligent system solutions.
As a full-range supplier, we supply comprehensive drive systems for off-road machinery from one source. We develop axles and transmissions with advanced software functions and combine them with state-of-the-art braking technology, connectivity and safety solutions. Our answer to meeting the industry’s challenges: comprehensive and intelligent system solutions, thoroughly matched to each other. In doing so, we always keep an eye on reducing emissions and remain on our path to Vision Zero. ZF.com/construction