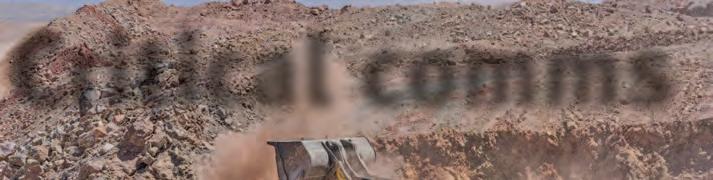
20 minute read
MINING NETWORKS
Critical comms
The increasingly autonomous mine is posing more challenges to comms networks – Paul Moore spoke to two of the market leaders in 4G LTE/5G solutions as well as the leading supplier of industrial wireless mesh in mining
Advertisement
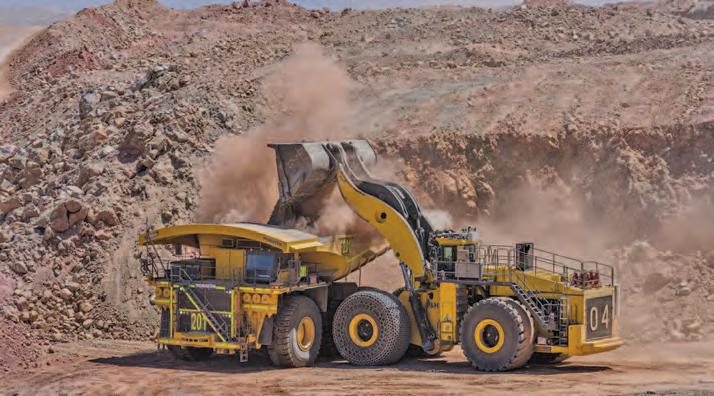
When it comes to connectivity, mining has a very distinct set of challenges. Jaime Laguna, Head of Nokia’s Digital Industries for Vertical Oil & Gas and Mining told IM: “These challenges are driving the need for mining digitalisation – or Mining 4.0 – to enable compelling use cases such as data-driven operations, predictive asset maintenance and autonomous drilling and haulage, among others. With the ability to send only machines into hazardous areas, workers are better protected, while productivity gains and costs savings are enabled by more predictable behaviour. But if autonomous equipment isn’t backed by reliable communications networks, issues can occur as they can disconnect from the network, halting productivity or even causing collisions.”
For this reason, many mining companies are turning to 4G/LTE and 5G private wireless networks based on the 3rd Generation Partnership Project (3GPP) cellular standards. “With the capacity to support thousands of connections at the lowest latency, private wireless enables a constant heartbeat link with connected machines offering the reliability, predictability and performance that WiFi just can’t deliver.”
By deploying a private wireless network, mining operators can consolidate operations. Traditionally, in addition to WiFi, mines use twoway radio systems, like Terrestrial Trunked Radio (TETRA) and Project 25 (P25), for mission-critical voice communications as well as other proprietary overlay networks. Laguna adds: “Using private wireless, they can leverage the Internet of Things (IoT) connectivity of low-power sensors, support the demands of mission-critical operations and allow teams to communicate via mission-critical push-to-talk (PTT) and push-tovideo (PTV) as well as video, while also supporting broadband data and video streaming. By converging operations onto a single private wireless solution, network maintenance activities can be reduced too.”
He adds that mining companies should first implement the Industry 4.0 capabilities that will have the biggest impact on their specific operational, safety and sustainability goals. “Talking to operations teams will help make that decision. Start with capabilities such as predictive maintenance which uses data collection of operational technology (OT) from sensors, combined with machine learning and artificial intelligence (AI) to reduce downtime and costs, and to extend equipment life.”
Automation is another use case that will deliver significant gains from the outset. Because of the predictability of movement, reduced acceleration and braking activity, and the constant monitoring of vehicle data, such as tyre pressure, a well-maintained self-driving haulage fleet will contribute to sustainability goals and costs by reducing fuel consumption.
Operational accuracy is increased too for productivity gains. “Hang time reduction is one example of this. The accuracy enabled by autonomous operations means that a truck and shovel can be aligned perfectly the first time, reducing the time a shovel must hang idle waiting for a person to maneuver the truck into the correct position. Over time this delivers huge productivity boosts.”
Finally, mining operators need to take a holistic approach when adopting Industry 4.0 capabilities. For example, in the case of autonomous haulage, you need to provide the interoperability between the mining trucks, often built with legacy WiFi connectivity in mind, into the wireless network. “This means working hand in hand with all ecosystem partners to rigorously validate solutions before they are deployed. By partnering with companies experienced in delivering end-to-end communications solutions for mines, they can implement new use cases faster.”
Swedish miner Boliden is one company already experiencing the benefits of private wireless at its Kevitsa open pit mine in Sodankylä, northern Finland. A Nokia 4.9G/LTE private wireless network provides seamless indoor and outdoor connectivity across its facilities at Kevitsa, supporting tele remote vehicles and drilling, which the company plans to transition to autonomous drilling. The network also supports remote environmental measurements and quality control activities, for example, triggering alerts to a driver if they are about to dump materials in the wrong location. By monitoring equipment remotely, the company has also been able to implement preventative maintenance capabilities. Nokia has also been highly successful of late in introducing private LTE networks in Latin American copper mines to facilitate autonomous haulage fleet trials & pilots ahead of full automation implementation – recent examples include at Antofagasta Minerals’ Centinela mine plus at Codelco’s Radomiro Tomic and Minister Hales divisions.

Autonomous Komatsu 980E being loaded at the Minera Centinela Esperanza Sur pit
Mine connectivity moving up a level
The mining industry is getting well advanced with the rollout of connectivity for automation of large haulage trucks. That really took off in surface mines four or five years ago with 4G LTE and this technology still dominates in terms of live deployments and it is now well established globally in all the major mining hubs including Latin America and Africa. As discussed with Ericsson’s Jeff Travers, Customer Success Lead Dedicated Networks, what has changed is that there is now a big interest in taking the automation to the next level, and this is a dialogue firstly with the major equipment manufacturers. “Mines are an ecosystem and the mine needs to put a number of things together to
bring advanced automation into play, including the connectivity layer which needs to be supported by the ecosystem and the haulage and drilling equipment suppliers themselves have a role to play. These companies are looking at a different sort of automation – namely smaller and more widely deployed autonomous and remotely-controlled vehicles, including for the underground fleet as well. The mines are turning to the equipment providers saying we want more automation and remote control beyond the large haul trucks – what can you do for us? The OEMs need to be a couple of years ahead of the cycle, so they are building capabilities into their equipment now which they can then put into the market in the coming years.”
At the same time, workers will require new tools to augment their capabilities, to be effective in a digital environment and alongside new technologies in the field. Stepping up to the next level of automation for a mine and worker augmentation is also a big investment and business case to make – “one of the things we help them to do is de-risk that decision by engaging with the ecosystem including the OEMs so that when the time comes the miner knows that its equipment suppliers are both ready and capable. It is a key requirement that if a mine adopts a certain technology like 5G, that the main equipment suppliers can support it. And we work with the OEMs to ensure that as they build 5G into their machine, that it will perform to the specifications needed – that it can handle the uplink and latency and resilience. This also means we work with the device vendors who put gateways and modules into the equipment – we test them within Ericsson first in cooperation with the equipment OEMs.”
All of this means that you get to a point where connectivity is no longer just good to have, it is fundamental to the operation because we are moving from connecting just the haul trucks to connecting the whole mine operations. “You are getting into more advanced levels of automation, including the ability to use remote control to take over when needed, and remotely managed operations in general. Much of this has been sped up by economic and practical factors after the pandemic. Mines want the ability to be able to take control of equipment if there are any connectivity outages, significant labour issues, or other unforeseen events like pandemic related restrictions. It is already happening in other industries – in the logistics industry for example, some warehouses are moving towards remote control forklifts, where operators in one central control office will control forklifts at multiple warehouse locations. The same applies to mining, where Integrated Remote Operations Centres manage autonomy and remote control where applicable across more than one site.”
Another development in 360 degree mine connectivity is more intensive deployment of sensors. The whole sustainability argument is looking at how do ensure mines have less of a carbon impact – and to know about your Scope 1 emissions in detail and in real time for example, you need data about the mine environment and how your equipment is operating. “To ensure energy efficiency and sustainability you will only activate autonomous equipment when it is needed, and underground bring ventilation online when it is needed. Greater autonomy also means preventative maintenance becomes much more important.”
Travers added that automation does not mean there are no workers onsite, it just puts them in different places and with different roles. You have the mentioned remote operations centre autonomous controllers and remote control operators; but you also still have core maintenance teams on site who need to be able to interact with the autonomous equipment. Several studies are underway into how onsite workers will effectively and safely carry out their roles alongside diverse connected equipment and be empowered in largely automated mines.
So do technologies like WiFi and wireless mesh still have a role to play in the autonomous mine? “There is always a place for those technologies, it just depends what you want to do with them. But I would say that often they are not economic for wide area coverage and heavy capacities. Also for those who want a certain level of latency consistency and reliability they may not be enough. For remote control for example, you want a 75 millisecond round trip –say for remotely operating torque tools for remote maintenance, WiFi will not offer the required consistency as there will be latency spikes, then the remote operator will experience drops and freezes when the tool does not respond smoothly and instantly. Overall, mines will still use WiFi for the right use cases. But for the functionality they want to bring in now, they are looking to go straight to 5G.”
In terms of network capability and performance, Ericsson of course would emphasise that LTE and 5G are hugely powerful. “But there is another point to be made in terms of ecosystem support – you want to know that you current product and device gateway fit together, but there will be add ons – more products. What the whole smartphone world proved was that if you standardise certain technology and interfaces, which was done in the telecomms world with 3GPP, you open up things for very fast product development across many companies. So you quickly build a rich ecosystem to draw upon which gives you choice but also brings down the cost and the price. As mines becomes more autonomous ecosystem support will become an important factor.”
In terms of use cases, Travers referred to NEXGEN SIMS as a good example of what is
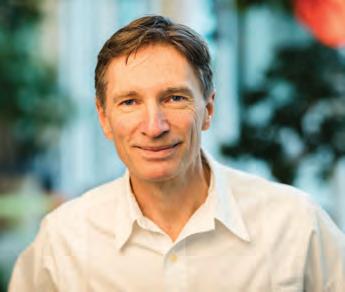
Jeff Travers, Ericsson Customer Success Lead Dedicated Networks
Zijin joins hands with MTN and Huawei
Nkwe Platinum Limited and South Africa Zijin Platinum (Pty) Ltd (wholly owned subsidiaries of multinational mining company, the Zijin Mining Group), have joined hands with African telecommunications giant MTN and global ICT provider Huawei, and signed a collaboration agreement to build what they say is the southern Africa region’s first 5G-enabled smart metal mine.
MTN and Huawei are to provide 5G-based ICT solutions for the smart mining requirements including, not only high-speed 5G broadband access, but also smart mining solutions like vehicle remote control, IoT, and enterprise digital transformation. “Once complete, the mine will mark a significant step forward in the digital transformation of the local mining industry. It will effectively demonstrate how a number of emerging technologies can be combined with 5G to improve functions across the mine.”
For more than 20 years, the Zijin Mining Group has regarded scientific and technological innovation as its primary driving force, becoming it says one of the few multinational mining companies in the world to be equipped with autonomous system technology and engineering management capabilities, with a well-established scientific research system and practice platform,” Fan Zhiyu, MD and CEO of Nkwe Platinum Ltd, said. “In May 2021, at the mine launch, we stated that we would build the Zijin Garatau Platinum Mine into a project with advanced technology, solid safety, and environmental protection practices. The adoption of this 5G smart mining solution will certainly enable the Zijin Mining Group to deliver on that promise, and to establish the mine’s technology-led global competitiveness.”
Other players in mining private LTE
While the market for 4G LTE and 5G in the mining industry is led by Nokia, Ericsson and Huawei – there are other players out there which have had successes in mining – two examples being NTT and Hytera.
NTT Ltd, a world-leading global technology services provider, announced in May 2022 it is working with Albemarle Corp, the speciality chemicals company with leading positions in lithium, bromine, and refining catalysts, to deploy a pilot private LTE/5G and WiFi network at Albemarle’s hard rock lithium mine in Kings Mountain, North Carolina. The 800 acre site sits on one of the richest spodumene ore deposits in the world. In addition, this site produces battery-grade lithium hydroxide, lithium bromide, lithium chloride, USP-grade lithium carbonate, high purity lithium carbonate, battery grade lithium metal products and lithium alloy powders.
Operating mining and manufacturing facilities across three continents, Albemarle needed a network that would allow its global engineers to connect with technicians for remote site surveys and assists. Previously, it was difficult for global engineers to visit Albemarle’s site due to COVID-19 travel restrictions, which significantly impacted the process of decision making and timing. The use of private LTE/5G will enable Albemarle to enhance its hybrid working process and reduce the amount of global travel needed to operate.
Utilising NTT’s global expertise in connectivity, Albemarle can now use integrated technologies to ensure that surveys, assists and maintenance activities can be conducted remotely. Albemarle is also looking at additional use cases to leverage wireless networking at their manufacturing sites. A private network provides the organisation with enhanced security, high technology performance, and coverage to enable IoT devices.
NTT worked closely with the manufacturer to determine the best use of connectivity dependent on the location or use case, always enabling the best possible coverage. Following the pilot in Kings Mountain, Albemarle plans to roll out the network to additional sites.
“To enable collaboration and digital applications at our mining and processing sites, we require widespread, high-speed connectivity,” said Chuck Holley, Global Manager of IT Network Infrastructure, Albemarle. “A private LTE/5G network is a great way we can do this costeffectively, and NTT was our first choice to pilot a design, prove the technology and show the value. With a private LTE/5G network, we’re able to continue to seek out innovative solutions to some of our most pressing challenges.”
“We’re incredibly proud to be partnering and consulting with Albemarle on this innovative pilot,” said Parm Sandhu, Vice President, Enterprise 5G Products and Services, NTT. “A private LTE/5G network will continue to transform business outcomes in mission-critical environments for Albemarle, and this is just the start of their journey. We look forward to working closely with the manufacturer as it continues to digitally transform its business for the future.”
Hytera's solutions have been successfully applied in the mining industry where they have helped customers solve their communication problems. For example, JSC AK Altynalmas has deployed a Hytera Hytalk (PoC) LTE platform and terminals in Kazakhstan, while the Letpadaung Copper Mine in Myanmar is using an integrated Hytera DMR and LTE solution.
Hytera's Intelligent Communications Solution for Mining it says provides instant voice, video and data communications to deliver team members the information they need to know to carry out their work. “Hytera's communications solution supports a rich ecosystem of real-time intelligence, which enables teams to work more efficiently, productively and safely.”
“The Hytera Intelligent Communications Solution for Mining can help the industry realise the benefits of digitalisation. It provides a highly transportable end-to-end broadband solution including terminals, network, data centre and command and dispatch centre. It is capable of supporting sophisticated automation, data analytics, and all the voice, video, data and M2M/IoT applications used in the mining industry.”
The fully 3GPP-compliant 4G/5G solution provides a complete wireless broadband network including radio access network (RAN), backhaul, LTE core, device and network management. Multiple services can be run simultaneously over the high throughput and resilient 4/5G network, including: Mission Critical Push-to-X (Voice/Data/Video); real-time video streaming; telemetry/SCADA; and M2M/IoT sensor monitoring. Low latency transmission rates (< 100ms) enable precise control of remote automated operations.
The various technologies can all be managed using one unified command and visualised dispatch centre and a remote control centre, which receive and distribute real-time information from and to the field operations. The network infrastructure also supports intelligent data analytics and artificial intelligence applications.
NTT has deployed a pilot private LTE/5G and WiFi network at Albemarle’s hard rock lithium mine in Kings Mountain, North Carolina

being done. “At that R&D project we are working with total visibility. It has brought together OEMs like Epiroc and connectivity companies like Ericsson with major miners like Agnico Eagle, K+S, OZ Minerals, KGHM and Boliden. We are responsible for the connectivity part; specifically what connectivity is needed for next generation autonomous (and electric) equipment functionality. One focus area is intensive use of autonomous loaders and trucks to be able to work through post blasting downtime. Then you have the use of drones and sensors for monitoring for gas as well as visual observations. Another work program is focused on rock stress testing in a mixed human and autonomous environment.” The load and haul program is well advanced now, with technology vendors and OEMs looking to deploy the new capabilities into machines for commercial availability. The drones program is also advanced while the rock stress testing element is at an earlier stage.
As another discussion point, how does Ericsson operate effectively in country where mines are located? “It is important that new technology gets introduced consistently and commonly as there are multiple mine locations and diverse players. A lot of the dialogue we have had up to now with mines now is about ‘the pilot mine’ but now they are saying this is not enough, they want to talk about rollout in several of their mines across different countries. They want to know that they can be sure that the connectivity environment they have for the pilot mine will still apply for their mines in a different continent. They want to know from us that the tech applied will be the same and perform the same. This is another important discussion with the OEMs – making sure that the tech standard which the OEM expects and requires of the mine when it sells its latest autonomous equipment, is handshake with us and therefore will work in whatever countries it is required to.”
Finally, there is an important role telecomms partners. “Increasingly the major mining houses turn to the major telecom operators they trust, and work with them to design and architect a network blueprint for their mines, with our 5G technology at its heart. They then hand over network deployment and operations to the local in-country telecomms operator with the required spectrum, which may or may not be a subsidiary of the global telecomms company that designs the blueprint. We are often the middle trusted party in that dialogue. It works smoothly as the system has been designed centrally but with the local requirements factored in.”

Rajant gets key OEM autonomous validations for Kinetic Mesh
Corporation, the pioneer of Kinetic Mesh® wireless networks, has recently announced key validations for its connectivity solutions with two of the leading OEMs in autonomous mining –Epiroc and Komatsu. Rajant and Epiroc, the major equipment supplier & productivity/sustainability partner to the mining and infrastructure industries, have announced successful validation for both semi-autonomous and autonomous drilling. As part of the validation, deployment best practices guidelines were created to support the deployment of Epiroc drills with Rajant BreadCrumbs® .
Epiroc has a permanent deployment at their test facility in South Africa to demonstrate semiautonomous and autonomous drills using Rajant BreadCrumbs. Rajant is deployed on dozens of semi-autonomous and autonomous Epiroc drills globally, some of which include semiautonomous drills at Anglo American’s Sishen (iron ore), Mogalakwena (platinum) and Los Bronces (copper) mines plus autonomous drills at Exxaro’s Grootegeluk coal mine.
“Improving the operational safety and productivity of mining operations is the byproduct of Rajant Kinetic Mesh. It is the only industrial wireless network enabling machine-to-machine (M2M) connectivity and mobility in markets like open-pit and underground mining,” shares Geoff Smith, EVP of Sales and Marketing for Rajant.
“Unlike other wireless networks that are dependent on fixed infrastructure, Rajant mobile BreadCrumbs can communicate with each other allowing machines to interconnect which adds additional layers of connectivity and redundancy while Rajant networking software InstaMesh® is self-optimising to overcome the constant environmental changes, data loads, interference, and on-the-move requirements of modern mines.”
Adds Brian Doffing, Epiroc’s VP of Integration: “Rajant’s unique technology offering has been instrumental in allowing our joint customers to scale their autonomous solutions. This includes not only Epiroc drills but opens the door for all connected equipment at the mine site.”
Rajant and Komatsu, developer and supplier of heavy equipment and services for the construction, mining, forklift, industrial, and forestry markets, have achieved Rajant certification for Komatsu’s FrontRunner® Autonomous Haulage Solution (AHS). Validation for FrontRunner AHS was completed in just six months.
“Reliable communications networks that offer continuous mobile connectivity are crucial to successful autonomous haulage operations,” said David Haukeness, Komatsu’s Product Manager for autonomous systems. “Rajant’s low-latency Kinetic Mesh and support for LTE and WiFi make their network a key part of our efforts to help our customers achieve their autonomous goals.”
Komatsu’s FrontRunner AHS uses a wealth of onboard technology and requires continuous, reliable wireless communication with the central office. Rajant Kinetic Mesh machine-to-machine (M2M) InstaMesh technology provides autonomous solutions like Komatsu’s FrontRunner AHS with higher reliability and network resiliency with low latency, which is critical to maintaining ‘always-on’ connectivity for autonomous machines.
Rajant is already co-deployed on Komatsu mining equipment in more than 100 mines globally and is now ready to support Komatsu’s autonomous solutions. “Achieving Rajant certification with Komatsu reflects the work of many individuals and addresses a key request from our mutual customers to continue utilising both companies’ advanced solutions,” shares Sagar Chandra, Vice President of Sales –Americas.
Rajant and Epiroc have announced successful validation of Kinetic Mesh® wireless networks for both semi-autonomous and autonomous drilling
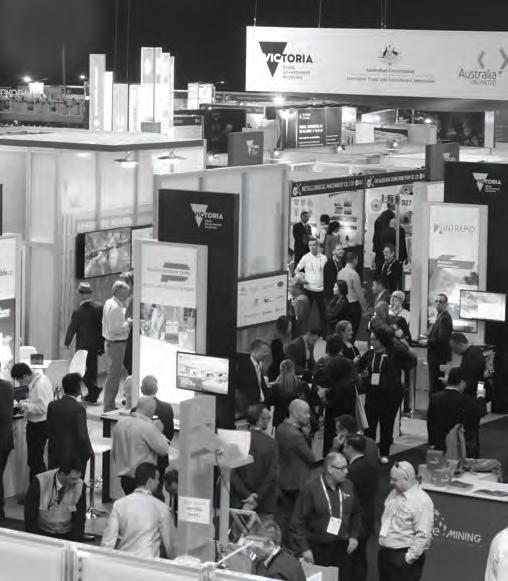
2 - 4 NOVEMBER 2022 | ICC SYDNEY
The International Mining and Resources Conference (IMARC) is where global mining leaders connect with technology, finance, and the future.
As Australia's largest and most influential mining event, IMARC creates a global conversation, mobilises the industry for collaboration and attracts some of the greatest leaders in the mining, investment, and technology industries for three days of learning, deal-making and unparalleled networking.
Learn from more than 450 mining leaders and resource experts with six concurrent conferences covering the entire mining value chain. Gain strategic insights from c-suite executives on minimising disruptions and building resilience, progressing ESG, accelerating mining’s energy transition and the future workforce. Whilst technical talks will delve into exploration, discovery and project developments, minerals processing, digital technology, and mining innovation.
Discover inspiration and new ideas, find practical solutions, and see demonstrations of the latest products and innovations from startups through to some of the biggest names in the mining industry with more than 470 exhibitors throughout the 17,000m2 expo floor all under the one roof.
Meet over 7,500 decision makers, mining leaders, policy makers, investors, innovators, and educators from more than 100 countries. As the largest gathering of mining professionals in Australia, IMARC provides unmatched networking opportunities, serving as the meeting ground for the mining industry.
Across three days, there are thousands of opportunities to network, brainstorm, and knowledge share, providing the perfect platform to obtain invaluable new business contacts, connect with the industry’s leading figureheads and explore new ideas.