
69 minute read
BAUMA PREVIEW
October’s fest
Taking place in a new season and with new focus areas, Bauma 2022 will set the scene for the next three years of construction and mining equipment developments. Dan Gleeson looks at what we can expect to see
Advertisement

Bauma 2022 is set to, once again, set a benchmark for all construction fairs across the globe.
Taking place on October 24-30, the organisers, Messe München, are expecting around 3,000 international exhibitors to attend, spread over 614,000 sq.m of space at the ICV.
Construction remains the main target market, yet there is plenty to get excited about from a mining perspective, as IM reveals. Bauma 2022 organisers, Messe München, are expecting around 3,000 international exhibitors to attend, spread over 614,000 sq.m of space at the ICV (credit: Messe München GmbH)
Liebherr’s new generation 8
Among its booths at Bauma 2022, Liebherr is set to unveil a brand-new mid-size-class hydraulic mining excavator with the exhibition of a preseries model.
As the second machine within the Liebherr mining portfolio to receive the “Generation 8” label after the R 9600 excavator, which was launched in 2021, this new model comes equipped with the latest Liebherr technology products, the company says.
The hydraulic excavator to be displayed at Bauma 2022 has already entered the testing phase, with the company planning the start of serial production in early 2024.
The T 274, a 305-t mining truck, will also be on display at the show, featuring what Liebherr says will be “an impressive demonstration of the Trolley Assist System”.
This truck bridges the gap between the T 284 (363-t payload) and the upgraded T 264 (240-t payload) and was launched last year with the Liebherr Trolley Assist System available as an option.
The trolley assist system uses an overhead pantograph to connect the electric-drive system to a mine site’s electrical network, powered by the customer’s energy source of choice. It offers
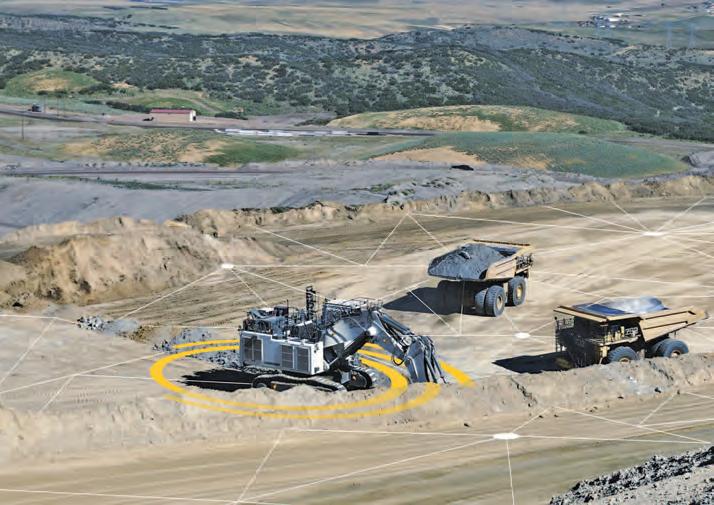
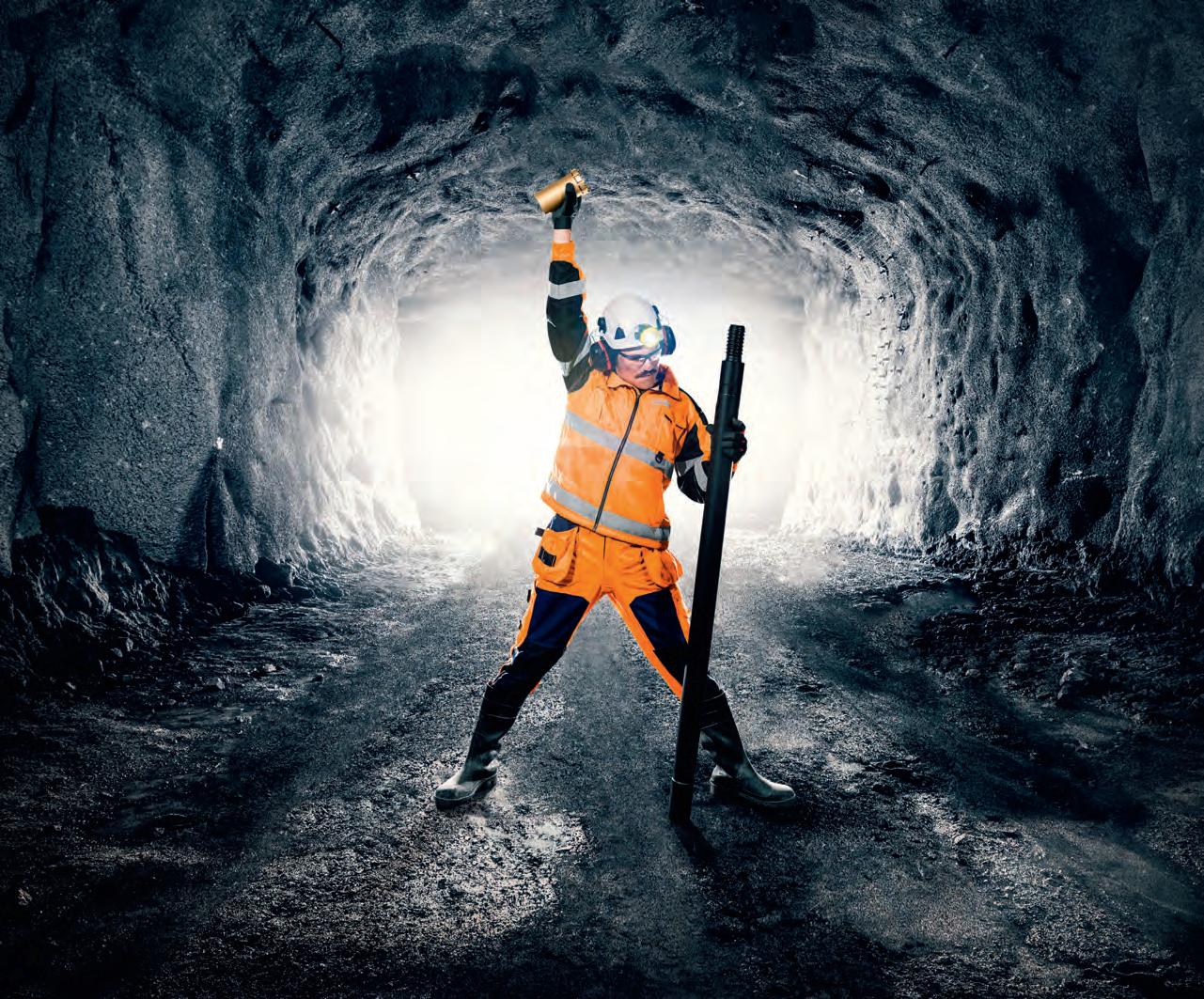
AUTOBIT THE DRILL MUST GO ON
The key to productive mining operations is to always keep your machines busy.
Autobit has an extended first grinding interval, lasting up to three hours. It enables your automated rig to drill during shift changes. The result is several hours of extra productivity every day.
Ready to minimize your downtime?
Read more at www.rocktechnology.sandvik/autobit
increased truck fleet productivity and the potential for a reduction in fleet size while retaining the same productivity compared with the use of standard trucks, according to the company.
The potential for a significant reduction of diesel fuel consumption and a smaller carbon footprint by decreasing the truck fleet’s CO2 emissions confirms the Trolley Assist System as an effective first step on the road to zero emission mine sites of the future, according to Liebherr.
Liebherr already has 56 trucks fitted with the system operating out in the field across three mine sites.
The company’s recently launched Technology Product portfolio will also be showcased in Munich, with the Truck Loading Assistant, Performance Monitoring and Application Severity analytic products among the list of solutions on show. Liebherr Power Efficiency and the Bucket Filling Assistant, the latter of which offers the first step towards excavator automation, will also be presented.
Mining company attendees will also gain some insights into the OEM’s hydrogen strategy, with Liebherr Components’ first hydrogen engine, the H964, being highlighted at the event.
Liebherr will also discuss its recently announced tie-up with Fortescue Metals Group, which has a hydrogen element to it.
Back in June, the two companies signed an agreement for the development and supply of mining haul trucks integrating zero emission power system technologies being developed by Fortescue Future Industries and Williams Advanced Engineering.
The phased supply of haul trucks as part of this agreement is anticipated to commence following a two-year joint development period. This is intended to enable the development and integration of Fortescue’s proprietary-owned battery electric and fuel cell electric power system into Liebherr’s proprietary-owned base truck.
Electric-drive and smart solutions
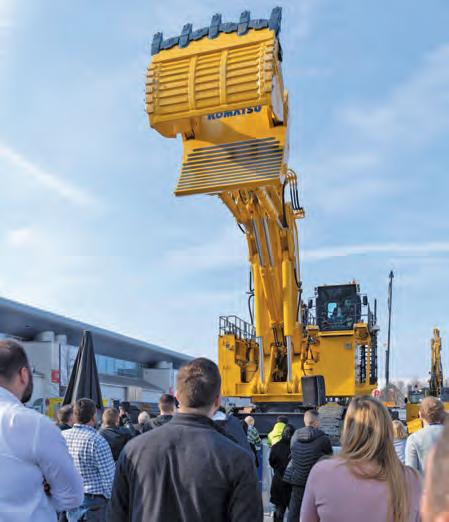
Across its plus-7,000 sq.m of Bauma space, Komatsu is set to present attendees with a record number of machines – 42 – that are new or well-recognised products and services that, it says, improve total job site efficiency and create real customer value.
The standout among these will be the PC400011 electric drive excavator, which, with its 22 cu.m shovel capacity, is a match for 150-240 ton (136218 t) trucks. It is also representative of the company’s knowledge and experience in developing, manufacturing and maintaining electric driven hydraulic excavators.
Komatsu Germany Mining started to build the first electric-drive hydraulic mining excavator in
The standout on the Komatsu stand at Bauma 2022 will be the PC4000-11 electric drive excavator, which, with its 22 cu.m shovel capacity, is a match for 150-240 ton (136-218 t) trucks
Torque of the town
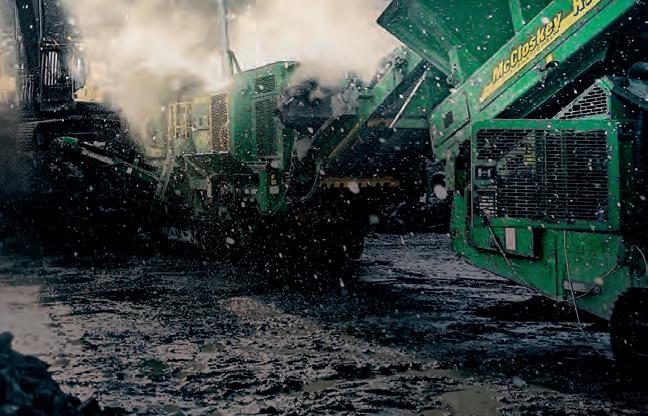
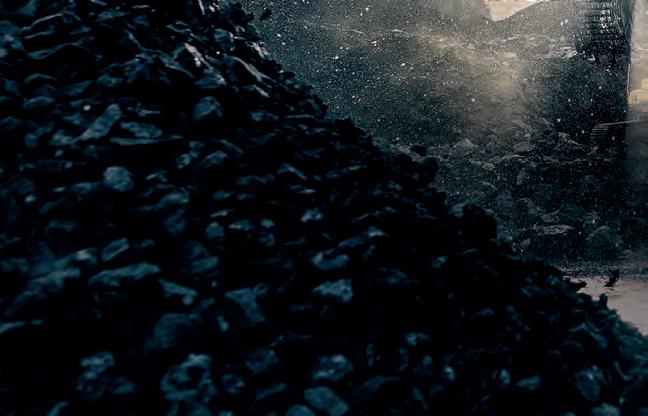
Machinery operating in the hostile conditions of mining, quarrying and construction requires an engine that
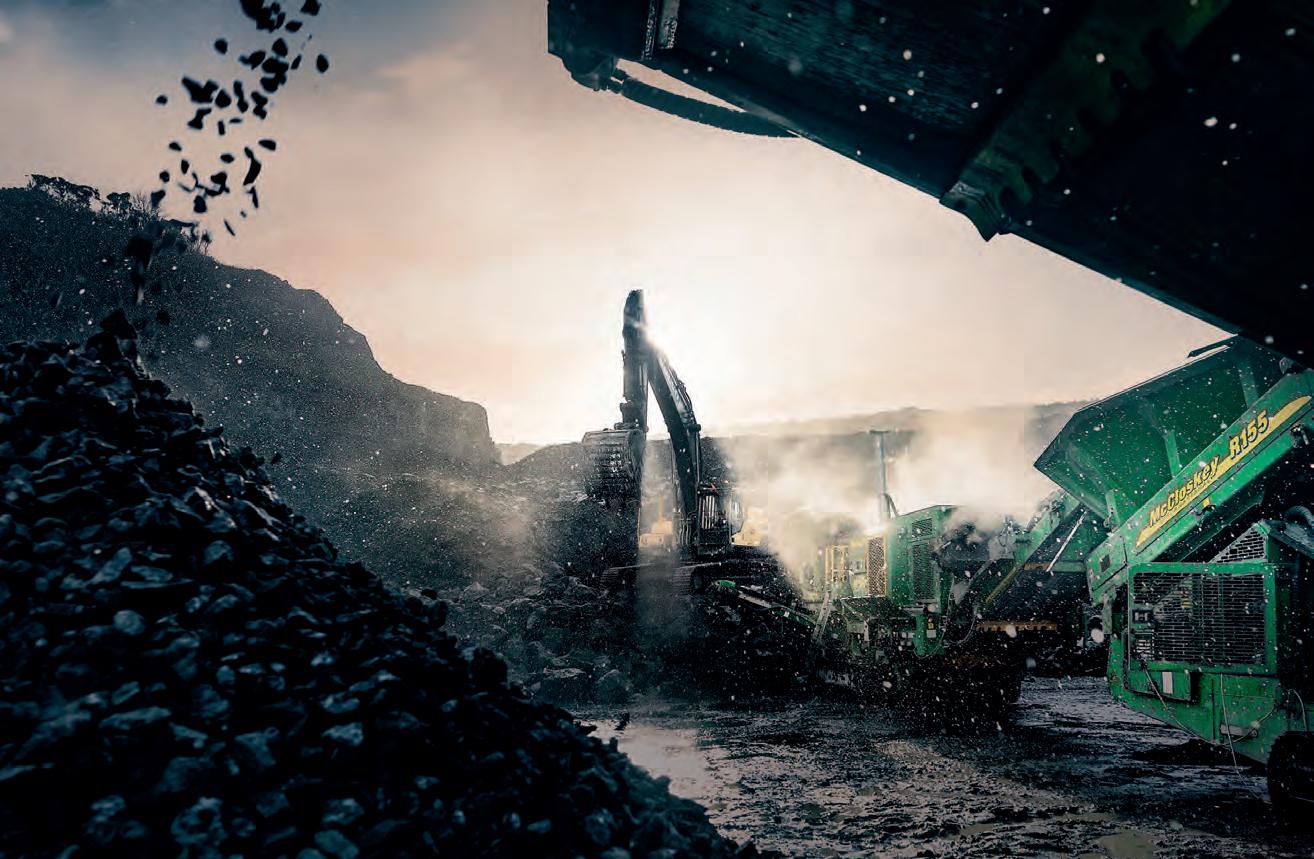
the early 1980s. Now, almost 40 years later, Komatsu has delivered more than 250 of them worldwide.
“With over 7 million operating hours, Komatsu is one of the most experienced and most successful companies developing, manufacturing and maintaining this type of machine,” it says. “The unique advantage of the electrically driven hydraulic excavator lies in the reduced operating costs, made possible by the elimination of diesel costs and the fact that they are not obliged to comply with any emission regulations.”
Equipped with the KOMTRAX Plus system, KomVision and Argus PLM, the PC4000-11 is digitally connected, benefits from constant monitoring, is equipped with safe operating mechanisms and offers efficient loading operations, the company says.
Other machines set to feature on the Komatsu stands include the 92.2-t-payload HD785-8 rigid frame off-highway haul truck and the 20.7-t capacity WA800-8 wheel loader.
Digitalisation is another essential element for improved productivity and, at Bauma 2022, Smart Construction/Earthbrain will show a new way of working, with unique solutions to support and improve customers’ businesses, Komatsu says.
Smart Construction is a solution for implementing highly productive, clean and safe work sites by connecting various site-based information via ICT. EARTHBRAIN, a new company setup by Komatsu, NTT DOCOMO, Sony Semiconductor Solutions and Nomura Research Institute, incorporates digital twins at sites based on its visualisation devices and applications for real-time remote monitoring, analysing and optimising of terrain, equipment, operators, materials, safety and environmental factors.
The Komtrax Next Generation and Komtrax Data Analytics booths, meanwhile, will explain how Komatsu’s wireless monitoring system can simplify decision making for all those who work to deploy equipment effectively or to improve fuel efficiency, to maximise productivity or to plan periodic maintenance.
SANY brings more products to Europe
SANY may be viewed by many in the Western mining sector as a China-only manufacturer, but the European arm of the company, SANY Europe, will be showcasing its international offering in October.
The European and Chinese arms of the group recently collaborated on the first 200-t excavator in China, the SY2000. The 200-t version is just the start, with plans in the pipeline to bring 400t, 600-t and 800-t versions to Europe, IM understands.
A mini excavator, the SY19E, powered by an alternative, environmentally friendly drive concept, will also be displayed, highlighting a potential electrification platform for larger-sized machines on SANY’s books.
In addition, SANY will introduce the first models of a new ground-up range of telehandlers developed especially for Europe – the STH1440 and STH1840 – and the recent extension of its wheel loader range with the 4-t-payload SW305K. The company also has plans to present a new drill at the show that has mining applications.
Back in March, SANY became the first Chinese company to list on Switzerland's stock exchange via global depositary receipts as it looked to diversify geographically. The construction of a new plant able to build 10,000 excavators a year in Germany, plus an R&D centre in the country, are also aiding this pursuit.
New ADT entrant
Hyundai Construction Equipment (HCE) is set to display 23 machines in Munich, with some of the display 23 machines in Munich, with some of the key highlights being a new articulated dump truck (ADT) and a hydrogen concept vehicle.
The company’s stand is 30% larger than in previous years, representing the ongoing growth journey it is on.
The entry of HCE into the ADT market involves the launch of two models, using proven, innovative design and technology to deliver high productivity and superior mobility on site, the
ROBBINS MDM5000

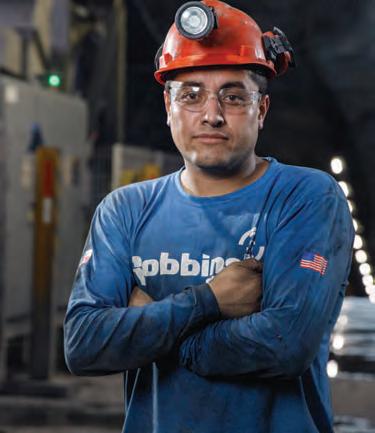
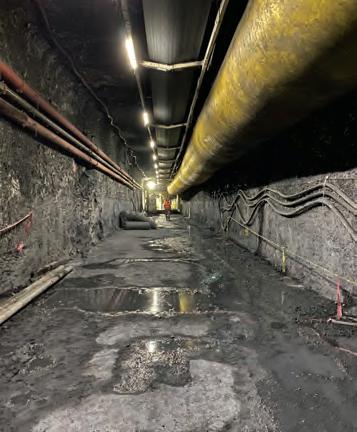
Twice as fast as conventional drill & blast
The world’s first successful rectangular tunnel boring machine
The Robbins MDM5000 is designed with mines in mind, capable of boring long drifts and access tunnels at 10-12 m/day in hard rock.

Hyundai Construction Equipment’s HA30A and HA45A ADTs are the first joint product developments between Hyundai Construction Equipment Europe and Hyundai Doosan Infracore, following the purchase of the Doosan business last year by Hyundai Heavy Industries Group
company says.
Aimed at the 30-t and 45-t sectors, the HA30A and HA45A are built around a full-time six-wheel drive concept, with front and rear limited slip differentials and a longitudinal differential that can be manually locked, for maximum drive and traction on difficult terrain.
The two ADTs are the first joint product development between Hyundai Construction Equipment Europe (HCEE) and Hyundai Doosan Infracore (HDI), following the purchase of the Doosan business last year by Hyundai Heavy Industries Group.
The trucks have a compact chassis design to aid manoeuvrability, with a sloping rear frame and a front-mounted differential integrated into the ZF transmission, allowing for a shorter front frame section.
This, the company says, results in the smallest turning radius in the sector, alongside outstanding stability.
Self-levelling hydro-gas suspension on the front axle further supports a comfortable ride, delivering maximum traction in tough ground conditions. The mounting of the turning ring in front of the chassis articulation point also provides increased stability and traction.
The HA30A and HA45A are equipped with a full hydraulic retarder, combined with an electronic engine brake as standard. This supports the oilcooled wet disc brakes to achieve an extended service lifetime of up to 15,000 hours. A hydraulically-activated mechanical parking brake, meanwhile, holds the machine when stationary.
The trucks are supplied with a gradient meter, with flip-over protection and a Body Over Centre of Gravity function, to assist drivers when tipping and operating on rough terrain. The sloping rear chassis section evenly spreads the load between the front and rear axles.
The HA30A has a 16.8 cu.m heaped body capacity that rises to 17.8 cu.m with the fitting of a tailgate. The larger HA45A offers a 24.4 cu.m heaped capacity, rising to 26 cu.m with a tailgate.
Hyundai has employed powerful EU Stage Vcompliant Scania diesel engines for both trucks.
HCE says the Hyundai HA30A and HA45A ADTs provide an ideal excavating partner for a wide range of crawler excavators and wheeled loading shovels and are designed primarily for major earthmoving and muck shifting projects, highways construction and mine and quarry operations.
The HW155H concept wheeled excavator, powered by a hydrogen fuel cell, meanwhile, features a 14-t payload that can offer eight hours of operation with a 20-minute refuelling time, according to the company. It is based on proven hydrogen commercial vehicle technology, HCE says, with the only emission from the machine being water.
ADT automation
As an ADT specialist, Bell Equipment is using the Munich backdrop to showcase its newest generation of the two-axle Bell B45E 4x4 ADT and a vehicle that comes with a width of less than 3 m (the B30E ADT).
Both machines offer a compelling advantage to customers with specific requirements, it says.
As a supplement to its range of seven “traditional” 6x6 ADTs, with payloads from 18 t to 45.4 t, Bell Equipment has, in the past six years, become the only articulated hauler manufacturer to offer a parallel range of two-axle ADTs, it says.
In the right applications, these machines outperform conventional rigid dump trucks that need good haul roads and three-axle ADTs designed for extreme off-road mobility to operative effectively, Bell claims.
At the upper end, the Bell B60E 4x4 – with a 55-t payload and 35 cu.m dump body capacity –is, Bell says, a benchmark for all-weather operations on undulating ground in open-pit mines or large quarries. At the bottom of the range, the Bell B30E 4x4 (28 t, 18.5 cu.m) is a compact and highly economical solution for sand and gravel pits, material handling or underground operations.
Driver-related assistance systems on board these ADTs include, for example, Hill Assist as well as loading and tipping routines that ensure productivity and safety in equal measure. All electronic assistance and status displays are based on real-time measurement data from the networked vehicle sensors (on-board scales, tilt and roll sensors, etc). Much of this information is also available for computer analysis and tracking using Bell’s satellite-based machine monitoring system Fleetm@tic® .
The digital advances for ADTs do not end there, with achieving an autonomous-ready platform a natural progression for Bell after it successfully integrated its ADTs with pedestrian detection systems (PDS) and collision avoidance systems (CAS), as standard, in 2019.
Bell Equipment’s Manager: Electrical and Software, Eben Lemmer, says: “We were first to develop our own telematics solution, Fleetm@tic, and to introduce onboard weighing, which is standard on our ADTs. When we introduced an inclinometer to improve our on-board weighing accuracy, we saw an opportunity to improve the safety of our trucks with our Hill Start and Tip Safe features that prevent rollback on slopes and rollovers due to tipping at unsafe angles. Similarly, by adding further layers on top of the existing PDS ISO standards, we have created an autonomous-ready platform that uses an open communication protocol principle to integrate easily with third-party suppliers.”
Bell Equipment’s focus is on the execution of instructions from those third-party suppliers.
Lemmer explains: “In the work environment, the guidance software processes all the sensory input, plots a path and sends instructions to the Bell drive-by-wire interface, which electronically controls the acceleration, braking and steering of the truck. Our communication simulator provides the ability to collaborate with service providers by allowing them to test communication and response in the desktop environment prior to going live in-field. This makes it easier to develop and test new software for controlling the Bell ADT.”
Bell first demonstrated that cost-effective remote control is achievable with the right building blocks when it successfully operated a B45E with a video game controller. Since early 2020, the company has been working with indurad and voestalpine on a lime quarry site in the Alps where the industrial radar specialist has fitted its iTruck autonomous haulage system (AHS) on Bell B30E ADTs with excellent results, the company says.
A collaboration with US-based safety and automation technology developer, Pronto AI, followed, with Pronto officially launched its product at MINExpo 2021 in Las Vegas in September. In the next few months, a fully-
fledged test site will also be open to the public near Orlando, Florida, where three autonomously-operated Bell B45Es and a Bell B50E will be working on an established sand mine using this platform.
“In most cases an autonomous operation will also need the end customer to set up their site to work differently; there may be special traffic control measures, berms or even different roads needed,” Lemmer says. “At this point in time, Bell has an autonomous-ready solution available for customers that are interested in doing proof of concept work in their application.”
New Hitachi platform
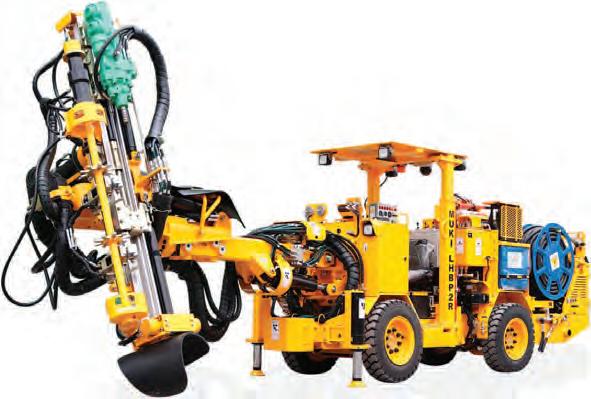
To demonstrate its expanding range of connected machinery at Bauma, Hitachi Construction Machinery (Europe) NV (HCME) is showcasing a Zaxis-7 medium excavator with a 3D machine control solution from Leica Geosystems. This has been fitted in HCME’s factory in Amsterdam as part of the new Hitachi Customised Solutions platform.
Adding Leica Geosystems machine control technology to the ZX210LC-7 increases efficiency on the job site while lowering running costs, the company says. It also enables work to be completed on time, on specification and to budget, safely and sustainably. From simple slope grading to blind and submerged cuts, the machine control solution provides operators with an easy-to-use system to rapidly excavate to the reference design. This ensures more uptime and operator satisfaction, according to HCME.
HCME Solution Linkage Manager, Ryo Kurihara, says: “By taking advantage of a factoryfitted Leica Geosystems solution, operators can start work immediately after machine delivery. Also, owners have peace of mind that the machine control system has been installed and tested to Hitachi standards, and it will be fully supported by their local Hitachi dealer in conjunction with the local Leica Geosystems specialists.
“We are pleased to offer this new turnkey option to customers, which will not only save them time, but also make their Hitachi excavators even more efficient, productive and versatile. By delivering customised solutions such as this we aim to become their first-choice solutions provider.”
The company will also display a Hitachi ZX8907 large excavator at the event. This machine, which has a backhoe bucket ISO heaped capacity of 3.5-5 cu.m, offers up to 20% reduced fuel consumption compared with previous models. This is on top of the enhanced efficiency that comes through using the HIOS V hydraulic system.
HCME will also be presenting a 5.5-t electric excavator im Munich. In addition to this, it will be highlighting more of its telematics capabilities as more clients look to automate certain functions –capabilities that can be fitted in Amsterdam as part of the Customised Solutions platform.
Excavator guidance advances
France-based iDig is readying a new tool in its own attempts to improve excavator guidance at construction, mining and infrastructure sites, with iDig 3D Connect set to launch in Munich, in October.
With the iDig system operators can manage distances, depths and desired slopes through a combination of advanced technologies that use no cables, are powered by radio communication and come with simplified installation and solar charging.
While iDig 2D successfully presented this guidance system concept to the market, iDig 3D Connect makes the process even easier to follow.
“True to iDig’s signature less-is-more concept, the 3D Connect has just one GPS/GNSS that’s easily removable for use as a rover,” the company said. “This feature marks a major breakthrough in excavator guidance because it enables contractors to easily stake out points and map a site just like surveyors.”
Traditionally, only companies with an in-house surveyor would stand to benefit from 3D guidance because most equipment is sold with one or more permanently installed GNSS receptors. This requires either an expensive, independent GNSS, or working with a surveyor to stake out the points that determine the boundaries of a site.
For this reason, 3D excavator guidance is typically only called upon for large scale infrastructure projects, according to the company. iDig 3D Connect will disrupt all this, expanding the benefits of 3D to more companies, allowing even faster finish times on projects, the company claims.
For users new to 3D guidance, the main advantage is that the software works with a GNSS-generated site map, enabling precision digging relative to the area and making the process even quicker, simpler and ecofriendly than with 2D, which is already in use on large mining-sized excavators in Australia, IM understands.
More features will be revealed at the 3D Connect launch in Munich, including another aspect that is unique to the industry, according to iDig CEO, Albert Gamal.
A bit more life
Epiroc’s mining focus in Munich will be two-fold, highlighting the development of new drilling technologies and a two-component system for improved ground support.
Epiroc has frequently been viewed as a pioneer in the world of hard materials for drilling, and the introduction of Powerbit X rock drilling tools with diamond-protected buttons furthers this reputation.
The technology, called PCD (polycrystalline diamond), allows drill bits to work for longer – 10 times longer than existing bits on the market, Epiroc says – providing longer service life, fewer bit changes and less risk exposure for operators.
The 2-mm diamond layer can help improve workplace safety, reduce downtime and minimise CO₂ emissions, the company says.
Epiroc will also, for the first time, bring the New Concept Mining team from South Africa to Bauma to present a skid pump resin mixing and injection system.
The company, which acquired New Concept Mining in 2019, explains: “Rock bolting can sometimes be the bottleneck within the drill and blast cycle, leading to difficulties to predict work task scheduling. A recent development is the use of two-component pumpable resin for the anchoring of rock bolts and cable bolts.”
The two-component system is delivered by a pump unit and is injected through a nozzle. The mixed resin begins to gel immediately, setting into a strong solid mass with excellent mechanical properties, according to the company. When injected through hollow rock bolts, the viscous mix fills the annular space between the bolt and the borehole to create a full
Resemin is planning to bring its MUKI LHBP-2R to Bauma, a long hole production rig for sublevel stoping in narrow-vein mining. Boasting compact 1.05-m-wide-by-2-m-high dimensions, the drill rig is able to work in sections as small as 1.8 m wide, by 3 m high. In addition, this versatile rig can drill very close to the ribs, reducing dilution due to its two-unit rotations. It is capable of drilling 64-mm diameter holes up to 15 m – upwards and downwards. All these features make the MUKI LHBP-2R the most competitive rig on the market for narrow-vein mining, according to Resemin
column bond independent of the size of the hole.
The pumpable resin can be pumped into the borehole through an injection pipe prior to insertion of the cable or bolt, with the setting time adjusted to achieve a longer open time, enabling installation of a cable or solid bolt into a pre-filled borehole.
Once mixed, the set resin is unaffected by water, while the product is non-foaming and can even adhere to damp surfaces.
“The pumpable resin is available in different reaction times and requires a 1:1 volumetric ratio between the resin and catalyst,” Epiroc says. “Deviations from the ratio result in a reduction in cured resin strength.”
Epiroc developed this resin mixing and injection system for its Boltec rock bolting rigs, ensuring a quality resin mix for every installation. The closed loop system controls the flow rate of each component separately, ensuring the ratio is maintained and the volume of resin injected is monitored. The skid pump system is a replica of the Boltec resin injection system, allowing off-rig pumping and installation of pumpable resin rock reinforcement systems.
Bauma’s mining-focused attendees might also be interested in an update to an Epiroc product aimed at the trenching and quarrying markets.
In April, Epiroc launched its V-shaped drum cutter, heralding it as a brand-new way to work with rock, concrete wall and surface profiling, trenching, soft-rock excavation, frozen soil excavation and demolition. A patent-pending solution, it has been tested in all these applications.
Mounting the drums in a V-shape enables a cut with a flat base where no material is left untouched between the drums, according to Epiroc. Where a regular drum cutter would move from side to side to create an even trench – an approach that causes extra wear on the carrier arm – the V Cutter can reach the same result by going straight.
“This means the user can dig a more accurate trench much faster,” Epiroc says. “It basically works like a bucket, which makes it easier to use, friendlier for the carrier and a lot less energy and time consuming.
“A seemingly simple solution with extraordinary effectiveness, the V Cutter enables energy savings of up to 40%.”
In addition, compared with a chain cutter, the user saves more than 40% on picks and up to 50% on maintenance time; the investment is up to 25% lower than for a chain cutter and the lower weight makes it possible to use a smaller carrier, Epiroc says.
At Bauma, Epiroc will introduce the latest addition to the V Cutter range – a smaller model suitable for carriers of 15-28 t. PAUS’ forward-looking approach
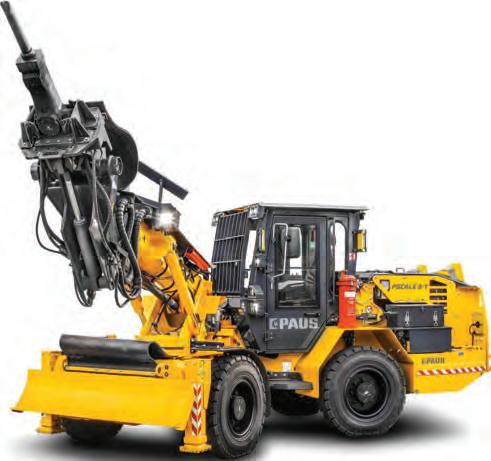
After already showcasing its battery-electric vehicle and corresponding electric driveline concept at Bauma 2019, PAUS is intending to bring even more new developments to the 2022 edition later this year.
The machines to be showcased in October include the PAUS Scaler PScale 8-T, the PAUS concrete mixer UNI 50-5 BM-TM and the PAUS dump truck PMKM 8030.
In addition to the brand-new designs and individual characteristics of the displayed machines, all of them will be featured with the latest technologies as part of PAUS’ general and forward-looking product developments.
Safety, performance, sensitivity and high durability are the design principles and values PAUS used for the development of its new PAUS Scaler PScale 8-T generation in order to provide what it says is a “unique scaling experience”.
“In underground operations rock falls could potentially lead to fatalities, injuries and damage to underground personnel and infrastructure,” the company said. “To ensure a higher safety working environment, any loose rock needs to be removed before the follow-up processes can be started.”
The highest performance possible is ensured thanks to the use of a high power output engine, 20° tiltable cabin, individual parameter adjustment of the hydraulic hammer, and operation and diagnostic display, which help provide higher reliability and quality of the scaling process.
The PScale series allows operators to adjust and check hammer parameters directly at the face instead of adjustments on the surface, while the operator’s cabin outperforms international ROPS/FOPS requirements. Other risks can be further alleviated by using additional configurations, such as plug-and-play for the remote control, 3P safety belts, a brake test button, hill start assistance and a pressurised cabin.
For working heights up to 10 m, Paus additionally offers the PScale 10-T.
The PAUS concrete mixer UNI 50 BM-TM offers a transport solution with a higher payload as well as safe and comfortable driving characteristics, even on rough terrain, PAUS says.
The larger UNI 50-5 carrier, which highlights the new chassis of the UNI series, comes with a payload of up to 17 t, increased ground clearance, a more powerful driveline and a spring-mounted fully suspended front axle, according to the company.
With an available volume of up to 7.5 cu.m, the PAUS transport mixer is a reliable partner for successful concrete works in underground mining, it says.
The UNI 50-5 carrier can also be provided with further superstructure such as fuel tanks, lubricant service, water tanker, fire tanker, loading platform with crane and
many more. Further to that, PAUS is offering a variety of customised configurations and options to meet the individual requirements of the different underground operations and conditions. The carrier can also be equipped with different types of changeable systems for carrying cassette- mounted superstructures.
PAUS delivers the UNI 50-5 BM-TM with an engine power of up to 173 kW with Deutz or Mercedes Benz engines. The machine can also be fitted with Stage V compliant engines.
The PAUS dump truck PMKM 8030, meanwhile, is designed for narrow-vein operations, with a compact yet powerful configuration.
The combination of the improved design and characteristics with the latest electronics and a preliminary setup for smart equipment will provide a future-oriented solution in terms of operator comfort and safety, but also efficiency, productivity and operating cost for haulage in narrow-vein mines.
The well-established sister machine, PMKM 8010, is designed with less width at increased length and height, but the new PMKM 8030 comes with a broader, shorter and narrower design at a reduced loading height and with improved driving characteristics thanks to the lowered centre of gravity, larger tyres and new axles with integrated oscillation, PAUS says.
With a payload of 16,000 kg, the machine is fitted as standard with a 8 cu.m dump box and can be further customised for transport of bulk materials with higher or lower densities.
The machine is also available with smart
PAUS’ PScale series allows operators to adjust and check hammer parameters directly at the face instead of adjustments on the surface
systems like a bird’s eye view camera, tyre pressure control and load weighing, all of which can be wireless monitored and displayed via PAUS CONNECT.
The PMKM 8030 comes with a rotating driver’s seat for long distances of driving backward at high speeds (bidirectional) and a spacious and comfortable cab.
It also comes with a choice of different Cummins and Caterpillar diesel engines complying with varying regulations and offering power of up to 190 kW.
The machine also includes the PAUS standard safety package for underground mining machines, eg SAHR brakes, a ROPS/FOPS cabin, enhanced LED lighting, etc.
PAUS concluded: “The multifaceted portfolio, the variety of options and the customised features available along with our machines will provide the basis for almost every task – it doesn’t matter how individual the solution needs to be.”
PAUS says it is already working on new solutions like a special mine rescue vehicle –currently being developed in cooperation with Dräger and a major European supplier for firefighting equipment. In addition to that, the “Scale Sense” project of the Germany-based RWTH Aachen University – for the detection of loose rock to use with PAUS scalers – is close to reaching the next development stage for extended field testing.
SBTi-backed initiatives
Volvo Penta’s commitment to supporting the current and future needs of mining and construction customers will be in sharp focus when it returns to Bauma in October.
Showcasing its plans to provide future sustainable power solutions to meet the industry’s net-zero ambitions, the company’s display will provide an overview of how its current portfolio of ultra-efficient D5 to D16 diesel engines – and EU Stage V-compliant models, in particular – has resulted in technological advances and market share gains that support its transformation journey.
The latest major innovation supporting Volvo Penta’s Science Based Targets initiative (SBTi)backed plans to reach net-zero value chain emissions by 2040 will take pride of place on its booth.
The electric driveline, which recently entered production in Rosenbauer’s RT and RTX fire trucks, was originally unveiled in 2019 as a proof of concept in a modified terminal tractor, highlighting the versatility and configurability of Volvo Penta’s electric solutions. This platform could possibly be scaled up for mining-class mobile equipment.
Morgan Blomgren, Director Strategy & Business Development for Volvo Penta, said: “We take a system-supplier approach which means that we can create a flexible, bespoke electric driveline solution for a specific vehicle and application. We are very experienced in a variety of different segments, so, by using that knowledge and combining it with the Volvo Group’s proven electromobility experience, we can build the best modular platform for our customer’s applications.
“With that as a base, we can optimise the design and adapt the complete electric driveline system for a specific vehicle, considering the exact application, usage, climate and environment it will operate in.”
Used in a wide range of machinery from crushers and screens to underground mining trucks, Volvo Penta Stage V-compliant diesel engines and gensets have been fully optimised to meet customer needs in terms of productivity, uptime and total cost of operations, the company says. Passive regeneration of the aftertreatment system has been maximised, for example, eliminating unplanned stops during operation, while fuel consumption has been reduced by up to 5% over the Stage IV-compliant models.
As one of Volvo Penta’s most popular engines for mining and construction applications, the new D16 received the 2021 Engine of the Year award. This was largely in recognition of its increased output (585 kW), which was achieved at the same time as an up to 10% reduction in fuel consumption. By incorporating water-cooled charged air, its dual-stage turbo engine delivers high performance right across the operational range, enabling maximum torque to be produced at both low and high engine speeds. A D16 unit will be taking pride of place on the Volvo Penta stand in Munich.
“In the short-term, the focus is still very much on internal combustion engines, and we will continue our development work in this area to stay competitive,” Blomgren concluded. “Our engines are already able to run on hydrotreated vegetable oil and biodiesel, and, to further support our transformation journey to zeroemission solutions, we are also looking into powering them with compressed natural gas, biogas and hydrogen, as well as the use of hybridisation – all of which are likely transitioning solutions for those markets that cannot yet support fully-electric solutions.”
All-in-one systems integrator
Yanmar, a provider of power solutions and industrial machinery, plans to introduce its electrification strategy for off-road vehicles and equipment at Bauma 2022.
The company will show its off-road product portfolio, commitment to customer lifecycle value and future vision for industrial equipment, which includes the electrification strategy for epowertrains; an electric equipment demonstrator; Yanmar/ELEO modular, highdensity battery system; and extended five-year warranty for its TN Series engines.
Through this presentation, Yanmar says it will establish itself as the all-in-one systems integrator for smart electrified power solutions tailored to the application-specific needs of individual OEMs. In its capacity as a systems integrator, it will implement system engineering, design and manufacturing of e-powertrains, while also providing control development, system evaluation, procurement, manufacturing and quality assurance.
Yanmar will show an electrified demonstration vehicle that shows the practical application of the company’s system integrator technologies. Powered by an electric drive and 48 V batteries with fast charging capability, the electric excavator is a quiet, zero-emission machine designed to meet the most demanding emissions restrictions, it says.
An important milestone for realising the urgent environmental challenges that must be overcome is Yanmar’s acquisition of battery-technology company ELEO, a developer and manufacturer of high-performance modular battery systems. This acquisition will further Yanmar’s electrified powertrain capabilities with versatile, customised solutions for off-road applications, it says. ELEO is building a new battery production plant, increasing its annual battery production capacity tenfold to 500 MWh – the equivalent of approximately 10,000 battery packs.
Yanmar is also launching a new five-year warranty (or 5,000 hours) offer, further enhancing sustainability and extended ownership of the current line-up of clean diesel solutions during the transformation to carbonneutral power solutions, it says. This extended warranty is free of charge and valid for TN Series engines sold in Europe and operating on European territory.
Berco to spin off Aftermarket division
Another company looking to make a statement in Munich is leading manufacturer and supplier of undercarriage parts, Berco.
The company has chosen the event to reveal the transformation it is undergoing, which will see Berco become a true global service provider that reaches far beyond the delivery of components for the undercarriage, it says.
Proximity to both original equipment and aftermarket customers is at the heart of this new strategy, with data management gathered through Berco’s latest digital applications, such as the Bopis Life cloud-based platform, playing a key role. This, ultimately, will further strengthen Berco’s technical expertise when creating tailored solutions for each customer around the world.
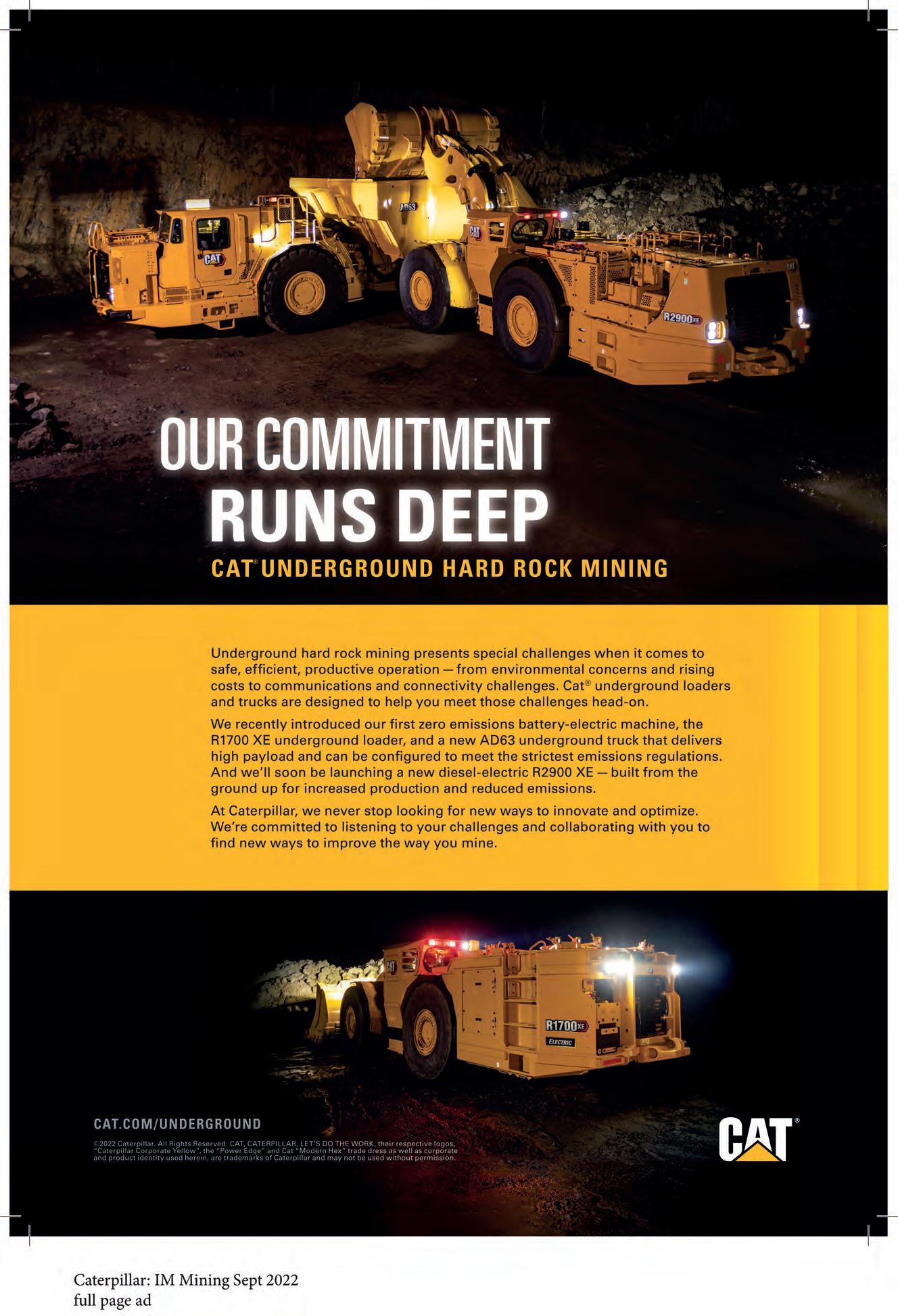
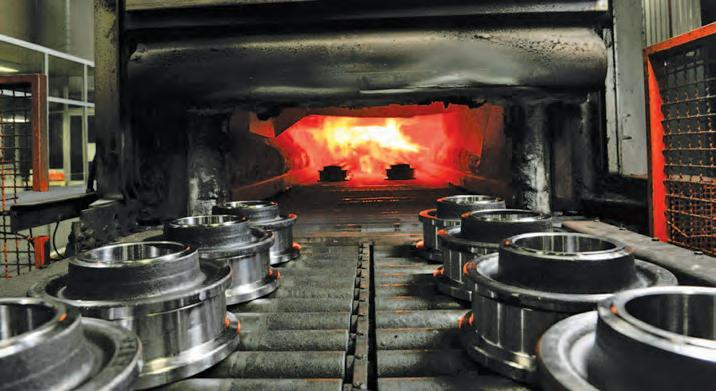
Berco says it plans to become a true global service provider that reaches far beyond the delivery of components for the undercarriage
Berco’s transformation is designed to satisfy market demand for increasingly customised solutions, and, to this end, it is looking to increase its technical presence in geographical areas closest to its customers.
The US, first, will receive additional focus, with Berco strengthening its level of support on the ground. This approach will soon be replicated in other important markets like Asia.
“In collaboration with our customers, our goal is to develop the best solution for each of their specific requirements and applications in any environment, wherever in the world,” Piero Bruno, CEO of Berco, said.
As part of this new approach, the Aftermarket business will be placed at the centre of the company’s development.
This has resulted in the creation of a spin-off solely dedicated to the Aftermarket, with all operations bundled together. The focus of this business entity will be a customer-specific service based on a new supply chain concept. This dedicated team is headed by Diego Buffoni and located in Bologna, Italy.
“The core impact of this transformation process, however, is the incorporation of 4.0 digitalisation standards,” Berco said. “With over 100 years of expertise in both development and engineering, Berco is now benefitting even more due to its approach to data management.”
Data generated in the field by Berco’s latest patented ‘Smart Undercarriage’ system or Bopis Life application are evaluated and processed through the company’s R&D department, with this data archive being the source for future systems solutions for both Original Equipment and Aftermarket, it says.
Back in November during the opening of Berco’s new R&D facility in Copparo, Italy, Buffoni said there was potential to address a market worth some €23 billion ($23.5 billion) in the future with key production additions and
developments backed up by a proactive and flexible Aftermarket organisation.
MTG’s digital first
MTG, a Barcelona-based specialist in the design and manufacture of high-quality wear solutions for earth moving machinery, is planning to present some major new innovations in October.
Among the mining-related launches due to be presented at the world’s biggest trade fair is VEEMET, a versatile system for excavators and loaders of between 20 t and 250 t equipped with plate lip buckets, and its ground engaging tool (GET) detection system called GET DETECTION.
As the successor to the STARMET system, VEEMET has been optimised for increased performance and user-friendliness, according to MTG. It offers improved stability due to its Vshaped fitting, which provides more resistance against torsional loads.
VEEMET, which will be visualised on the stand with a 3D printed model, also features an optimised locking option for quick and easy assembly and disassembly; reinforced pins; and a slim tooth design for enhanced penetration and increased machine efficiency, MTG says.
The wide range of self-sharpening teeth and plate lip adapter designs are suitable for any construction, quarrying and mining application, according to the company, providing a better digging performance. in terms of GET detection systems, MTG says it is the first major player in the industry that has developed its own in-house platform with GET DETECTION.
The launch follows successful field tests in Europe and Australia where the system – made up of magnetic field sensors and actuators integrated into the corresponding GET components, antennas, ECUs and an operator tablet – was able to show its ability to improve operational safety and avoid unplanned downtime, MTG said.
The system, which is embedded in the nose of the GET adapter instead of the teeth, can detect a detachment in less than three seconds, allowing direct action and a fast return to production, the company says.
The batteries on the sensors last for 5,000 hours, which means they can be directly aligned with maintenance intervals.
The first series of in-house developed digital solutions, GET DETECTION will be displayed on MTG’s stand for visitors to learn live how it works.
While still early days, the company’s next digital solution could be focused on the area of automation, IM understands.
ESCO buckets at Bauma
Weir ESCO’s offering of mining buckets, developed to meet demanding needs and the toughest applications, will feature all over its Bauma stand.
This offering includes a range of custom options to meet specific mine site requirements with full wear protection for severe abrasion and impact conditions. All tooth-style buckets come standard with ESCO’s Nemisys® tooth system for improved performance.
One of the company’s new dragline buckets set to be displayed is the ESCO ProFill® Delta dragline bucket, built using proprietary cast alloy construction.
While all ProFill buckets are built to deliver superior productivity and maximum durability under the toughest digging conditions, the new ProFill Delta bucket provides increased productivity and cost savings with the added benefit of reduced rigging complexity.
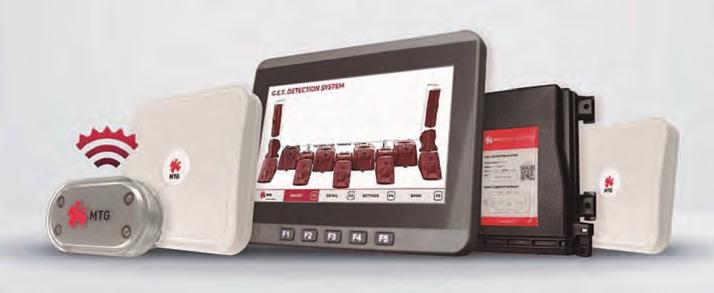
Meanwhile, eliminating the lower spreader bar and associated components reduces rigging weight by up to 15%, according to the company.
Alongside the ProFill Delta will be the ESCO Production Master® dipper lips – single-piece castings poured in premium alloys for toughness and weldability; a range of mining-class hoe buckets, designed using advanced finite element analysis tools; performance-driven face shovel fronts and backboards for 120-800-ton-class (109-726-t-class) machines; and a variety of wheel loader buckets.
The company also plans to showcase a range of wear material options that include Infinity® chrome white iron button and blocks, ESCO AR 400 and 500 plate, Infinity chromium carbide overlay plate, Kwik-Lok® II cast steel wear runners, as well as cast corner wear shoes and cast Nemisys and Toplok® wing shrouds.
Weir ESCO’s lip and GET systems are complemented by the ESCO ToolTek™ System for safer installation and replacement of Nemisys points and adapters.
The ToolTek system includes a boom crane mounted tool head that is remotely operated, well out of harm’s way during replacement of worn components. New parts are pre-staged on racks conveniently positioned on the flatbed truck outfitted with the hydraulic crane. The system can remotely engage and disengage the GET locking mechanisms during a changeout, making the process truly touchless and safe for mining maintenance personnel, Weir ESCO says.
“During replacement of parts on one bucket, a crew is exposed to hundreds of touchpoints which are eliminated with the ToolTek system,” the company explains. “Advantages of the ToolTek system include enhanced worker safety, fewer workers to replace GET components, all required parts and tools on one truck and safer disposal of worn parts.”
IM reported earlier in the year that the launch of ToolTek in Australia had resulted in two orders from mine sites.
Adhesives, IoT and washing
As a global leader with a history of innovative engineering and, like Weir ESCO, part of the Weir Group, Weir Minerals has an array of technologies to choose from for its Bauma presentation, with its booth set to feature several
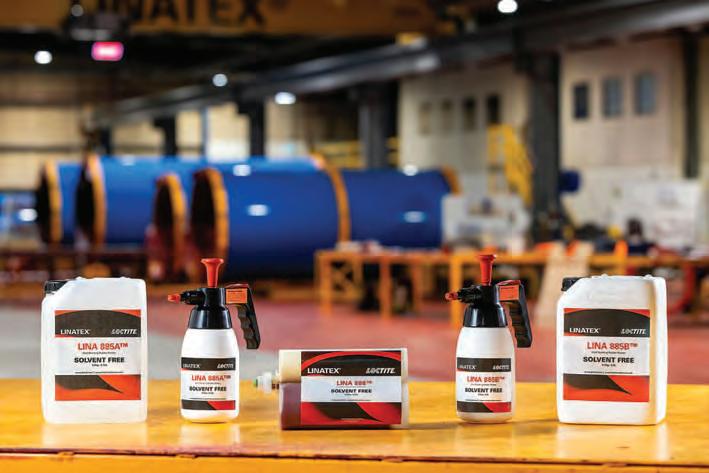
LINATEX LOCTITE - LINA 88 is a mining-industry-first, solvent-free adhesive range for rubber lining applications with zero volatile organic compounds
B2.524 B VISIT US AND LEARN MORE!
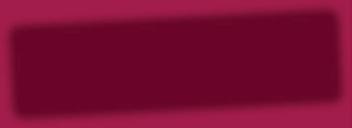
NEW RELEASE! AKOREL SOFTWARE INNOVATION

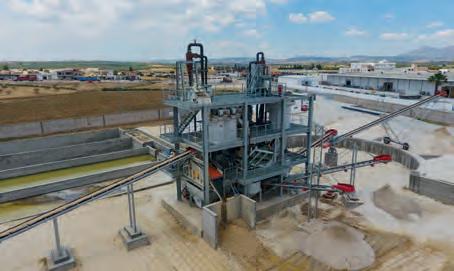
YOUR PARTNER FOR CUSTOMIZED SOLUTIONS
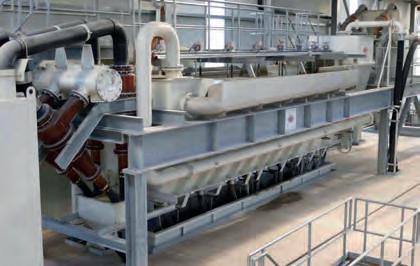
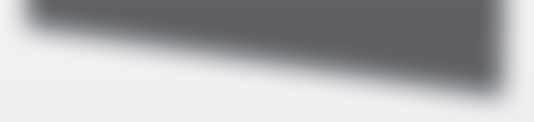
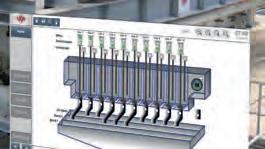

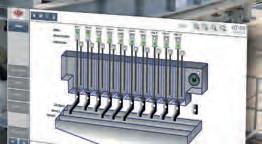
IN SAND BENEFICIATION, CD&E WASTES VALORIZING, FINE SAND RECOVERY AND PROCESS WATER RECYCLING
OUR CAPABILITIES
Technical Laboratory & Trials
Engineering
Equipment & Process Units
of its market-leading products and solutions.
One of these is LINATEX® LOCTITE® - LINA 88™, a mining-industry-first, solvent-free adhesive range for rubber lining applications with zero volatile organic compounds, delivering multiple environmental and safety benefits, as well as best-in-class bond strength, the company says.
The company will also use the event to showcase its Synertrex® Intelligence Ecosystem, which continuously monitors and assesses equipment condition and performance. This information is then converted into actionable insights and recommendations, providing operators with unrivalled real-time decision support, according to Weir Minerals.
There will also be a sand wash plant solution on display. Designed to remove excess fines or coarse material, this solution provides exceptional washing results while delivering a clean, low moisture product for conveying or stockpiling, the company says.
Fossil-free steel
SSAB will be showcasing its fossil-free steel for people to touch in Munich for the first time.
The very first steel plate was produced with hydrogen-reduced sponge iron at SSAB in Oxelösund, Sweden, on August 18, 2021, and delivered to Volvo Group.
A cutoff of that steel plate will be on display at the show, with its sustainability experts explaining the unique HYBRIT technology and how fossil-free steel can be used as a platform for creating end-customer products that largely eliminate greenhouse gas emissions.
In 2016, SSAB, LKAB (Europe’s largest iron ore producer) and Vattenfall (one of Europe’s largest energy companies) joined forces to create HYBRIT. Using HYBRIT technology, SSAB aims to replace coking coal, traditionally needed for orebased steelmaking, with fossil-free electricity and hydrogen. It aims to be the first steel company in the world to bring fossil-free steel to the market.
Volvo Construction Equipment, part of the Volvo Group, recently became the first manufacturer to deliver a construction machine to a customer built using SSAB fossilfree steel.
The Volvo machine, an A30G articulated hauler, was handed over from Volvo CE to NCC earlier this year. The milestone came just nine months after Volvo unveiled the world’s first vehicle concept using fossil-free steel as part of testing the implementation in an ordinary production setup, and ten months after SSAB showcased the first steel ever made using hydrogen instead of coking coal.
SSAB’s Hardox® 500 Tuf wear-resistant steel and Strenx® high-strength structural steel will also be on display at the event as the company highlights its current commercial offering for multiple industries.
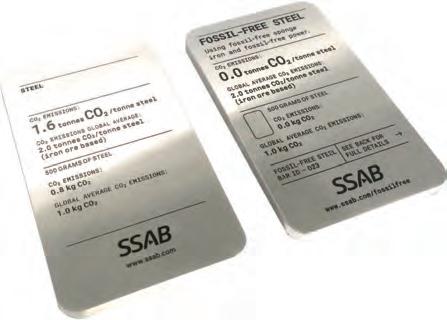
A new screen class
Haver & Boecker Niagara’s next-generation Niagara T-Class vibrating screen will be one of the highlights on the company’s Bauma stand.
The T-Class, Haver & Boecker Niagara says, retains the technical benefits the original concentric technology is known for while improving screening uptime and performance with new features. It provides producers with a cost-effective, maintenancefriendly solution to process a wide range of materials within industries including mining.
A cutoff of the very first steel plate produced with hydrogen-reduced sponge iron at SSAB in Oxelösund, Sweden, will be on display at Bauma
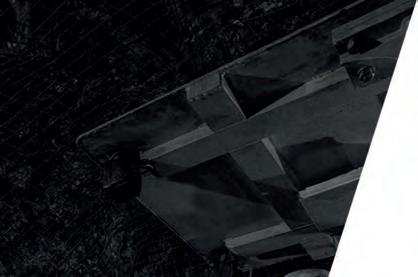
REDUCE DILUTION
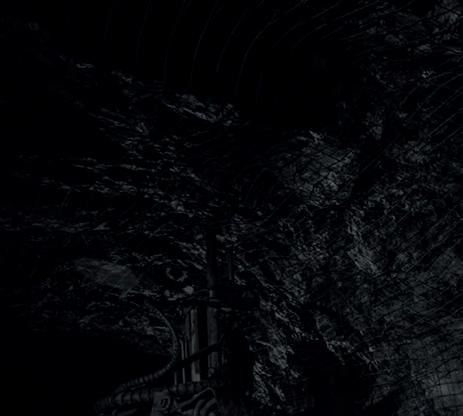
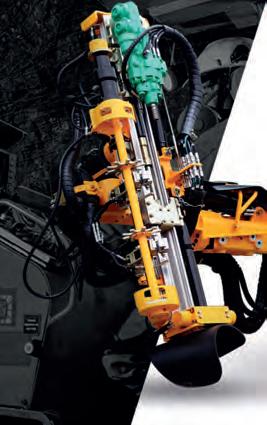
For miners is key to reduce dilution by drilling very close to the ribs. The MUKI LHBP 2R does it and has been doing so since its launching to the market in 2017. That´s why it is the preferred long hole drill rig for Narrow Vein Mining.
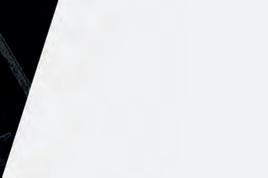
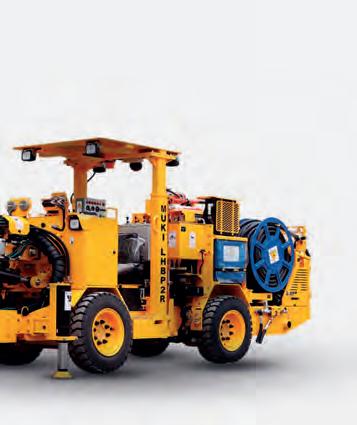
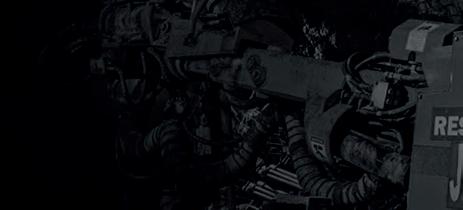
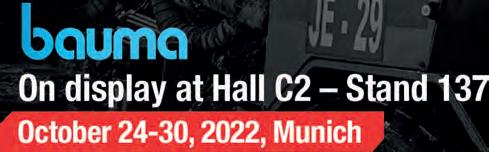
The T-Class, Haver & Boecker Niagara says, retains the technical benefits the original concentric technology is known for while improving screening uptime and performance with new features
The T-Class deck frame is now primarily lockbolted rather than welded to provide optimum strength, reliability and safety. Lockbolts have proven to be more effective in ensuring the machine’s structural integrity than welding in the demanding, load-bearing, high-vibration operation of a vibrating screen, the company says. The robustness of the machine also permits cross beams to be positioned and lockbolted every 1.2 m instead of every 0.6 m, allowing for better clearance and easier maintenance.
The new design allows producers to upgrade their vibrating screen with Haver & Boecker Niagara’s new Drop Guard system, further minimising maintenance. The liners provide 100% cross beam protection, both reducing wear and extending the life of the vibrating screen, according to the company. The system drops over the cross beam with no adhesive or tools required, making installation quick and easy, it says.
Additionally, Haver & Boecker Niagara redesigned the flat deck frames of the new TClass vibrating screen for simplified maintenance. The pin and anchor deck frame is adaptable to virtually any pin-style modular screen media. It features polyurethane anchors that are easy to replace and prevent premature wear on the deck frame. Additionally, the open design of the modular deck prevents material build-up on the bar rails. The cap and slide deck frame, meanwhile, is adaptable to virtually any groove-style modular screen media and features full rail protection.
The T-Class can be manufactured for sidetensioned or bottom deck end-tensioned screen media. Each new side-tensioned machine comes with Haver & Boecker Niagara’s signature TyRail™ quick-tensioning system, which cuts screen change-out times in half, the company claims.
Duncan High, the Product Manager behind Haver & Boecker Niagara’s new T-Class design, said: “The new, more robust T-Class was designed specifically to offer more strength in the middle of the machine – where it’s needed most. Each update was engineered with ease of maintenance in mind, to keep downtime low while providing cost efficiency.

Innovation in control software
AKW Equipment + Process Design’s AKOREL control software will be one of the major talking points on its Bauma stand. The company has been supplying the AKOREL freefall classifier technology for many years, offering a wet classification solution that corrects the sieve curve of raw sand ranging from 0-2 mm or 0-4 mm, in line with customer requirements. Even at high throughputs from 40-500 t/h (depending on the size), the AKOREL classifier consistently produces high-quality building sands with the same product quality, independent of the sand feedstock.
By decomposing the sand feedstock into six to 16 individual fractions, and re-blending them afterwards with the use of a user programmable control unit, the AKOREL can generate one or two quality sands with the desired grain size range.
In addition to the target of providing the customer with a robust, reliable and low-wear installation, much attention has been devoted in recent years to intelligent use of modern control technologies for data acquisition and processing. The objective of this has been to make classification more flexible and cost efficient, and, thus, contribute more decisively to the conservation of resources.
This focus has seen the company offer two different levels of control systems to its clients: the ‘Basic Standard-Control Option’ suitable for the production of simple and constant quality sand output, and the ‘Premium-Control Option’ for when the production requires flexibility in the handling of various input and outputs.
These software capabilities have gained significant market acceptance over the years, according to the company.
To offer customers even more convenience, AKW has made the software even easier to use through an optimisation process that factors in the need to accommodate throughput, operational, grain size fluctuation and product quality requirements from customers. This will mean customers, in the future, can benefit from: n Maximum user-friendliness; n A simplified, clear arranged software display and interface; n State-of-the-art technology including the newest features; and n An automatic recipe adjustment to raw material fluctuations, without operator intervention.
This updated software can be retrofitted on existing AKOREL classifiers, ensuring customers can leverage these benefits for many more years, the company says.
Enerpac to do the heavy lifting
Enerpac, a leader in high pressure hydraulic tool, controlled force products, portable machining, on-site services and solutions for precise positioning of heavy loads, plans to use the upcoming fair to showcase not only its construction-focused offering, but solutions for handling and maintaining mining equipment.
The centrepiece of the Enerpac stand will be the new SBL600 telescopic hydraulic gantry, along with the company’s entry-level gantry system for handling mining equipment – the ML40 Mini Lift Gantry. The new E-mover batterypowered load skate will also be demonstrated
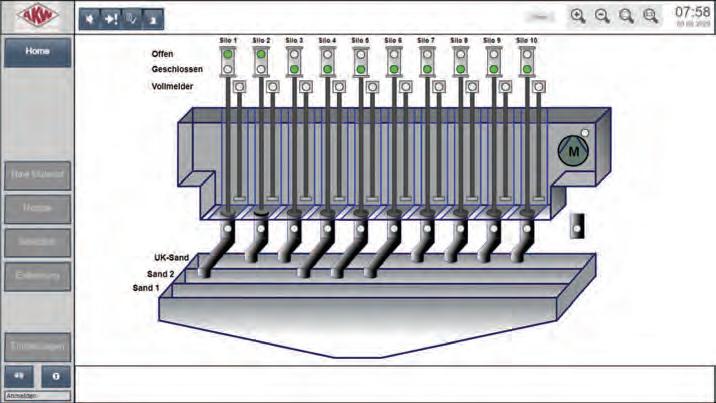
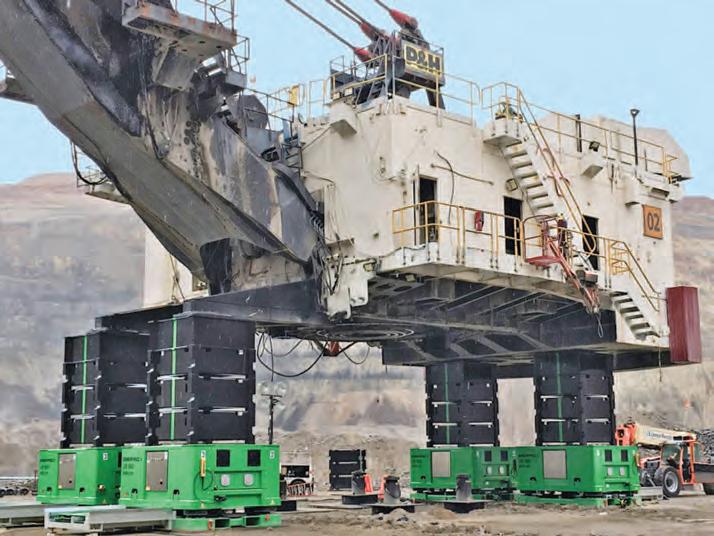
Capacities of Enerpac’s JS-Series Jack-Up range from the JS-125’s 125 ton capacity to the JS750,s 750 ton capacity, with each solution offering lifting heights from 6 m to 20 m, respectively
SBL600 Hydraulic Gantry
together with the SCJ-Series 50T Cube Jacks-Ups. It will also feature the Enerpac Power Riser for safe and mobile load lifting of mining vehicles.
In addition to the hydraulic gantries and cube jacks, the booth will feature a JS-250 Jack-Up, and multi-point lifting EVO system used to maintain mining shovels.
The SBL600 Super Boom Lift hydraulic gantry is a three-stage telescopic hydraulic cylinder with rectangular boom for increased capacity and first stage lifting capacity of 674 tons (611 t) and 416 tons at the third stage. The SBL600 fits in nicely between the SBL500 and SBL900 gantries, offering a lifting height of 10.6 m, compared with 8.6 m and 11.3 m, respectively. Jeremy Stubbs, Commercial Director, Enerpac Heavy Lifting Technology, said: “Ease of transportation is another key benefit of the new gantry. A foldable boom allows for shipping on standard flatbed trucks without special permitting and routing. In addition, with the self-weight less than 9,100 kg, the SBL600 allows for transport of two legs on a single road truck trailer.”
Enerpac Power Riser Lifting Jack
Riser Lifting Jack is a self-locking jack that performs automatic locking during lifting, lowering and holding. Available with 54-ton, 90ton, 136-ton and 181-ton capacities with either pneumatic or electric pumps, the Power Riser Lifter is supplied with 3.5 m pendant cord for airdriven units with pneumatic valves and 6 m pendant cord for electric-driven units, keeping operators away from the load. It is a readilyportable unit with 102 mm ground clearance for transport over rough terrain. A three-position handle, meanwhile, provides easy tilt back and transport, the company says.
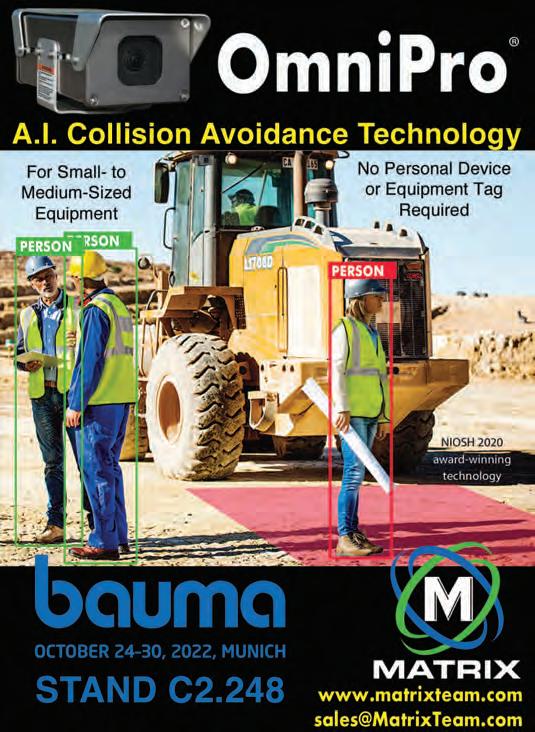
Synchronised lifting
Accurate synchronised heavy lifting is the hallmark of Enerpac heavy lifting systems, which, the company says, is exemplified by the SCJ-Series Cube Jacks and Enerpac’s larger JS-Series Jack-Up.
The Enerpac Cube Jack has set the standard for ease-of-use and productivity for compact, portable lifting solutions, according to the company. It uses a base lifting frame and selfaligning, lightweight steel cribbing blocks –together with automatic incremental locking – to provide high-capacity and stabilised lifting. It is a safer, controlled, more efficient and environmentally friendly alternative to climbing jacks with tropical hardwood cribbing, Enerpac says.
Enerpac JS-Series Jack-Up Systems, meanwhile, are transforming the way many heavy-lift projects are executed, Enerpac says.
The Jack-Up is a synchronised lifting and lowering system with self-contained hydraulics in each unit for uncluttered work areas. Loads are lifted in increments as steel boxes, called “barrels”, and are stacked together to form lifting towers to mechanically hold the load. The JS-250 Jack-Up system uses computer controls for seamless synchronous control, raising and lowering all towers at the same time.
Capacities of the JS-Series Jack-Up range from the JS-125’s 125 ton (500-ton lift with four towers) capacity to the JS-750, 750 ton (3,000ton lift with four towers) capacity, with each solution offering lifting heights from 6 m to 20 m, respectively.
These flexible solutions can be moved in and out of sites and – importantly – are classified as intrinsically safe, meaning they can be used in the Australian market.
Heavier lifts
Enerpac strand jacks pack tremendous lifting capacity into a small footprint, acting like a linear winch.
This sees steel cables or strands guided through a hydraulic cylinder; above and below the cylinder are anchor systems with wedges that grip the cables or strands. By stroking the
cylinder in and out while the grips are engaged in the anchors, a lifting or lowering movement is achieved. The motion of the cylinders is driven by hydraulic power packs, with the Enerpac SCC software program synchronising the motion of the strand jacks and adjusting the motion to the loads per lifting point.
An Enerpac EVO multipoint synchronised lifting system is used to simultaneously control up to 12 cylinders, creating an accurate and synchronised lift. Operated using a PLC, hydraulic cylinders connected to an EVO Synchronous Lifting Pump enable each lifting point to be monitored and controlled by a single operator. The EVO pump maintains accurate positional control within 1 mm between lagging and leading cylinders and includes built-in warning and stop alarms for optimum safety, the company says.
Enerpac’s EVO synchronous lifting system recently came to the rescue of WesTrac in Western Australia, providing an efficient, portable and safe solution to lift its 200 t Cat® 994K wheel loader.
Bosch Rexroth’s myBODAS on trial
Bosch Rexroth says it is opening its mobile electronics software, BODAS, to all manufacturers and partners as part of a move to accelerate the launch of new machines and functions by OEMs.
The company plans to offer manufacturers of off-highway machines free access to the entire standard portfolio of BODAS software for controlling mobile machines, with Bosch Rexroth set to highlight this at the upcoming event in Munich.
Via the digital myBODAS platform, OEMs can download validated software packages for a range of applications, free of charge, to test and adapt them to suit their own requirements.
Proven modules within the platform minimise the time, investment risks and costs involved, with the service only billed via a payment model based on credits if the software is used during series production. The modules are developed in accordance with current standards and already meet functional safety requirements, the company says.
“Whether it be hydraulic control, automation, connectivity or electrification – software plays a central role in the highly dynamic off-highway market,” the company says. “In order to achieve
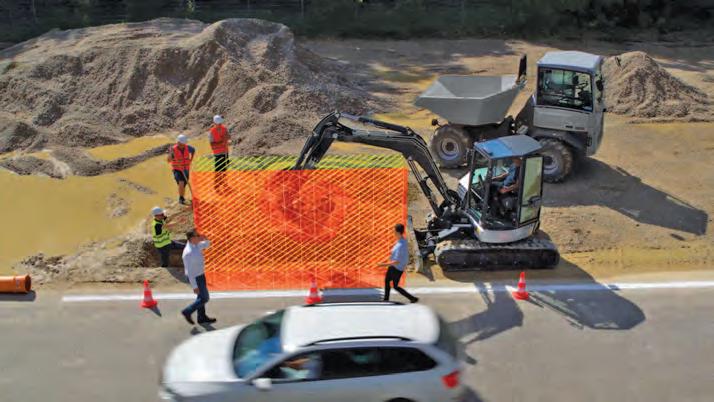
Bosch Rexroth will present an integrated portfolio for needs-based automation of offhighway machines, such as excavators, wheel loaders and telehandlers, at Bauma 2022 with the assistance functions covering, among other elements, virtual walls and emergency braking assistants for greater work safety

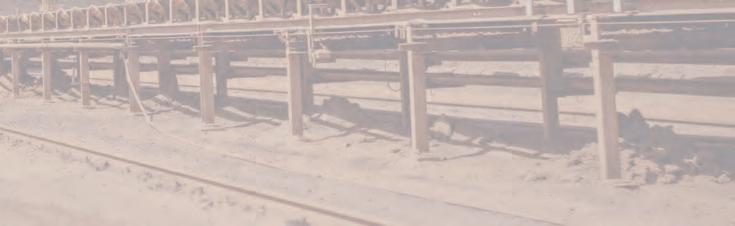
3,500 t/h TAKRAF stacker for iron ore in Australia TAKRAF is recognized as a leading global technology brand when it comes to handling high capacity run-of-mine and bulk material handling. Stackers form only a part of our portfolio and we supply the complete range of machines for the heaping of circular or longitudinal piles, as well as for the homogenizing and blending of bulk material. Innovation out of tradition - It pays to talk to a specialist!
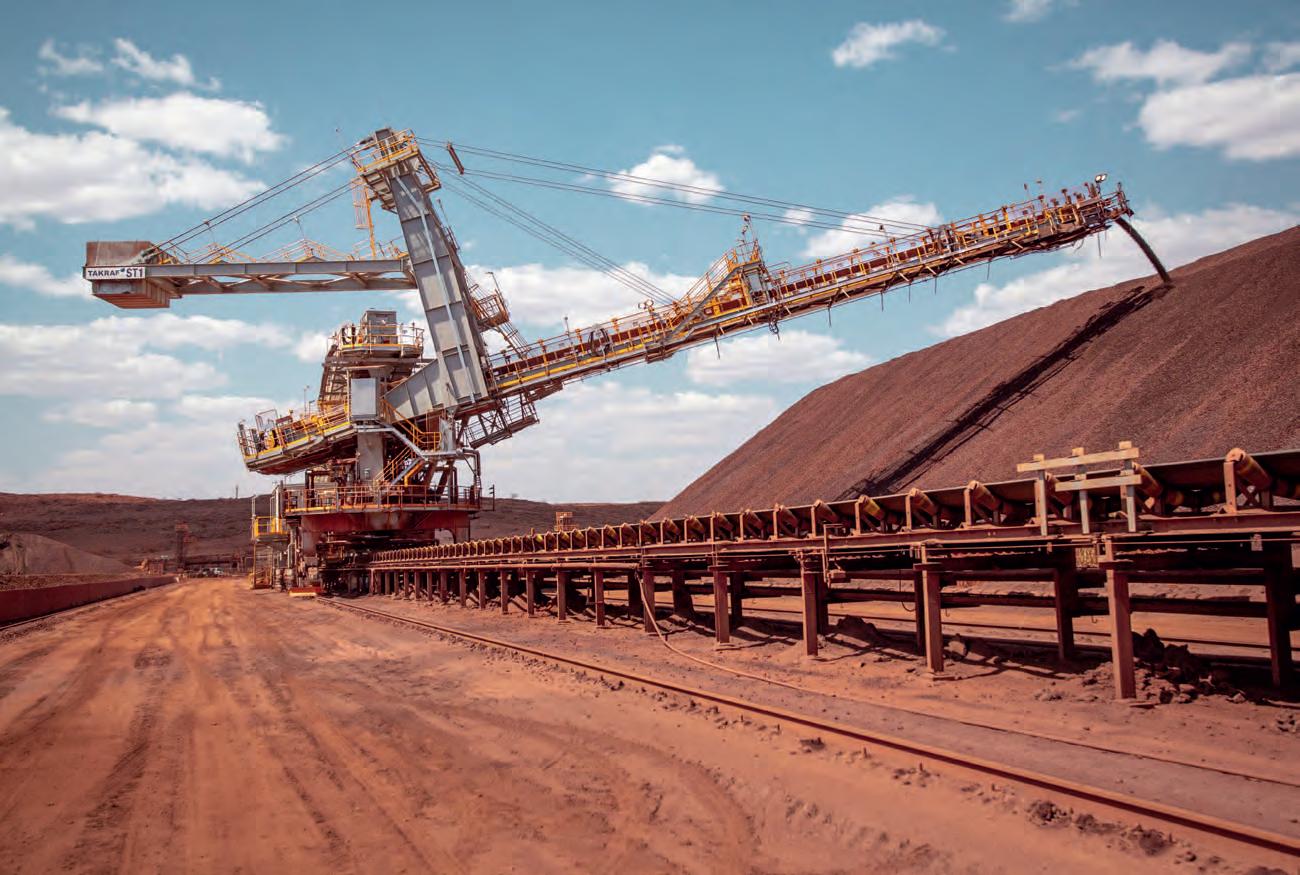
success with their mobile machines, OEMs must reduce the development time in a cost-effective manner while reducing functional and financial risks.
“This way, the OEMs’ software developers can concentrate on selected customer values and speed up the launch of new functions and machines. They can also scale their own offering more quickly with software modules validated for Rexroth hardware.”
The open ecosystem of BODAS is being expanded constantly with standardised, extensively-documented modules. myBODAS, thus, offers an updated toolkit for various control tasks involving mobile machines, the company explains.
Related to this, the company will present an integrated portfolio for needs-based automation of off-highway machines, such as excavators, wheel loaders and telehandlers, at Bauma 2022.
The assistance functions cover advanced sensor systems and intuitive operating devices, including driver assistance for more efficient working and virtual walls and emergency braking assistants for greater work safety.
And, as a hardware platform for higher automation levels, Bosch Rexroth will announce a microprocessor-based, ROS2-compatible robotic control unit.
For object recognition and terrain mapping, Bosch Rexroth is working with Bosch to develop a ROS2-compatible perception stack. On this basis, Bosch Rexroth plans to offer complete function packages in the future – from sensor integration and object recognition to machine intervention.
The new control platform is currently being developed, with prototypes for pilot projects available from the middle of 2023.
This entire automation portfolio will be based on the BODAS platform for hardware, software and telematics.
ABB partnership model on show
At Bauma 2022, ABB will take visitors on a journey to the reality of tomorrow, presenting not only its industry-specific portfolio, but showcasing its approach and methodologies.
The mining experts at ABB, made up of specialists across digital, automation, electrification, grinding, motors, drives, conveying, material handling, automotive wiring harness protection and traction, have a hand in most of the exhibition’s themes. They will discuss the importance of mining in ensuring a ready supply of the materials needed for the energy transition, including metals and minerals for modern technologies such as wind turbines, smartphones, electric vehicles and medical devices.
ABB’s latest solutions use products and methodologies as part of a wider integrated system and the company has taken decisive industry actions to partner directly with customers, original equipment manufacturers (OEMs) and technology innovators, enabling mining leaders to move towards their zero emissions targets more quickly while ensuring efficient, reliable and profitable operations, it says. This has been facilitated by working together and making a world of difference in every area where ABB is well placed to influence. This includes digital, electrification, motion, charging, energy storage and component protection systems for both onboard batteryelectric vehicles and around the mine site.
ABB will showcase its digital portfolio, including ABB Ability™ MineOptimize solutions and the ABB Ability eMine™ suite of electrification and digital systems designed to accelerate the decarbonisation of the mining sector.
In 2022, the ABB Ability eMine portfolio has continued to emerge as one of the industry’s foremost electrification strategies, with a successful project commissioning for the eMine Trolley System at Copper Mountain’s operation in Canada and ongoing testing of pilot eMine™ FastCharge. The latter, part of the eMine Charging Systems family, is set to become the worlds’ fastest and only fully automated charging system for mining trucks, offering up to 600 kW of power, ABB says.
Meanwhile, the company has designed and manufactured Harnessflex® Specialist Conduit Systems. These include flexible conduit systems and connector interfaces, protecting critical electrical and electronic wiring assemblies on automotive machinery from mechanical abrasion, liquid ingress, dust and salts.
ABB’s team will discuss how everything fits together in the all-electric mine, powered, managed, monitored and protected through automation and digitalisation. Lighting up the site
Just one of the Continental launches slated for Munich is its NightViu lighting series, developed specifically for applications in the construction and mining sectors.
With perfectly uniform illumination at automotive level, the series provides much better visibility in the work area, improving safety and efficiency on sites, the company claims.
The unique modular housing concept has a minimum level of component complexity and offers users the flexibility to cover a wide range of lighting requirements, according to Continental. It also boasts highly increased lighting efficiency when compared with systems previously available on the market.
The work lights in the NightViu series feature an efficient reflector lens design with six powerful LEDs and four cover lenses. Offering approximately 100 lumens per watt, these LED lights have an enhanced light efficiency level when compared with other LEDs for construction and mining machinery – protecting sensitive vehicle electronics and preventing short circuits caused by excessive power consumption.
Luminous flux options range from 1,500-3,500 lumens, with the light beams covering a wide variety of lighting scenarios for the work area around the vehicle; from close-range to far-field illumination. These beams have different lighting patterns, ranging from highly focused spotlight illumination to floodlighting, and from a wide to extremely wide illumination field.
“In Ultra-Wide mode, we still achieve a light intensity of one lux at a distance of 90 m, and that’s absolutely unique,” Chris Kosmala, who is responsible for lighting system development at Continental, said. Overall, this increases the brightness in the corners and sides or at the end of the illuminated area away from the spotlights.
Continental has also designed a unique housing concept that, it says, enables the three
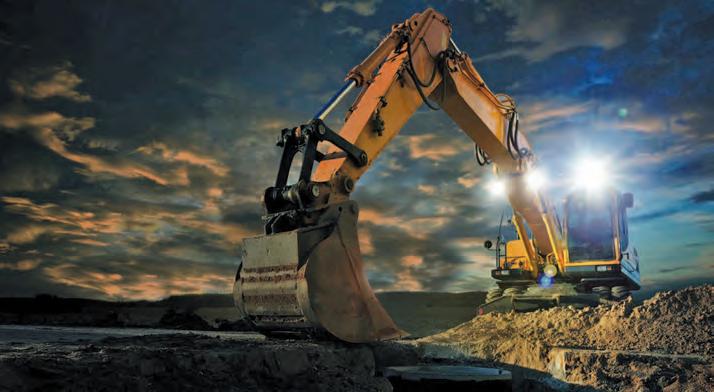
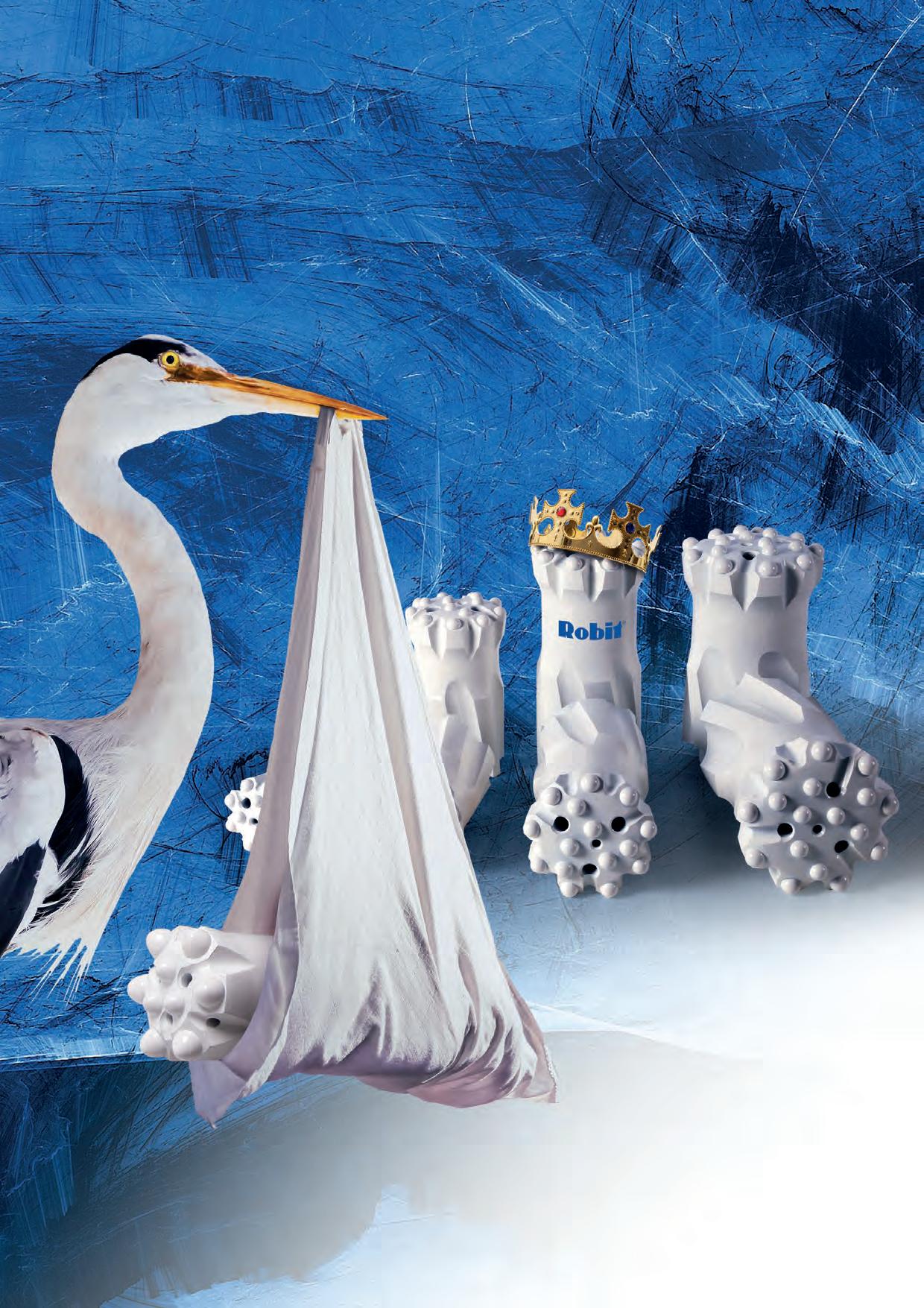
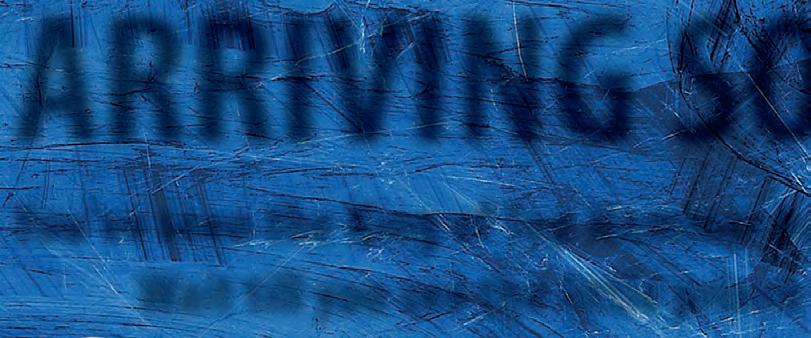
different luminous flux options and four different light patterns to be freely combined without needing more than one housing design.
“In this way, the complexity of the NightViu series is kept in check, but we can still meet every conceivable requirement of our customers,” Kosmala said.
The modular approach also allows different light cones to be combined, reducing the number of lights required but still ensuring a highly uniform illumination and the avoidance of shadows, according to Continental.
The aluminum housings are designed for hard off-highway use and are protected against water and dust in compliance with the IP6K8 standard. The lights also withstand temperatures between 40°C and +90°C and pass vibration tests of up to 12 g RMS – verified through tests in Continental’s certified quality laboratory.
The lights’ flexible installation system for standard or heavy-duty mounting also enables retrofitting in many different positions on vehicles, the company says.
BEUMER Group bulks up
There has plenty of change at BEUMER Group of late, with Rudolf Hausladen installed as the new CEO, succeeding Dr Christoph Beumer, the FAM Group joining the company and the launch of new conveyor technology.
BEUMER Group, an international leader in the manufacture of intralogistics systems for conveying, loading, palletising, packaging, sorting and distribution, has held a stable position in the bulk materials technology market for decades, and, with the acquisition of FAM, it has significantly strengthened its market position in the minerals and mining sectors.
The FAM Group, headquartered in Magdeburg, Germany, is a manufacturer of conveyor systems and a leading supplier of full-range bulk handling and processing equipment for applications such as in-pit crushing and conveying. It plans, designs and manufactures turnkey plants and systems for mining, extracting, loading and storing minerals, raw materials and goods.
BEUMER Group has also recently responded to the changing demands of dry bulk customers with two new products that leverage its existing expertise in pipe and troughed belt conveying technology.
Speaking at a recent virtual media event, Andrea Prevedello, CEO of BEUMER Group Austria, announced the new additions under the U-Shape conveyor family.
Leveraging the advantages of pipe conveyors and troughed overland belt conveyors, U-Shape conveyors enable environmentally friendly and efficient operation in port terminals, BEUMER Group says, allowing the implementation of more narrow curve radii than a troughed belt conveyor with higher mass flows than a pipe conveyor, all with dust-free transport. BEUMER Group explained the hybridisation of the two: “The troughed belt conveyors allow high mass flows even in case of heavy and robust materials. Their open design makes them suitable for coarse materials and very large volumes. “The pipe conveyors, on the contrary, present other specific advantages. The idlers form the belt to a closed tube protecting the material transported against external influences and the environment from emissions such as material loss, dust or odours. Partition plates with hexagonal cuts and idlers in a staggered arrangement keep the tube shape closed. The pipe conveyors allow the implementation of more narrow curve radii and larger angles of inclination than open troughed belt conveyors.”
With requirements changing – the quantities of bulk materials growing, conveyor routing becoming increasingly complex and environmental considerations rising – BEUMER Group found the need to develop the U-Shape conveyor.
Within the family are two products that offer higher curve flexibility, higher capacity, bigger lump size allowance, no spillage and reduced power consumption, according to Prevedello.
The T-U-Shape conveyor is a U-shape conveyor designed like a normal troughed belt conveyor with a 30% reduction in width, allowing the ability to take on tighter curves, Prevedello says. This looks to have many applications in tunnelling.
The P-U-Shape conveyor, as the name would infer, is derived from the pipe conveyor, but offers 70% higher capacity within the same width and 50% higher lump size allowance, Prevedello says, explaining that it could allow BEUMER Group to consider the use of pipe conveyors in space-constrained environments.
New installations will obviously be targeted as part of this new product launch, but Prevedello says there are both greenfield and brownfield application possibilities.
The T-U-Shape conveyor has more ‘new’ installation opportunities in tunnelling applications, he said, with the tight turning radii benefits allowing for small installations in tunnels.
With many ports shifting focus away from coal to handle different materials, the P-U Shape conveyor’s increased capacity and higher lump size flexibility could be of benefit in brownfield applications, he added.
Radio-controlled Tunneling Excavator
For tunnel cross sections from 6.2 m²
Entrance height 2.3m, Operating weight 12t
High breakout and tear force wimmer.info | mini-badger.at

Wirtgen’s ‘all-rounder’
With the new 280 SM(i) surface miner, Wirtgen says it has developed another efficient and practice-oriented solution for the extraction of primary resources, with innovative technologies that enable high machine utilisation rates and maximum productivity.
The 280 SM(i), which will be on show in Munich, is designed for the reliable and selective extraction of primary resources by direct loading, sidecasting or cut-to-ground. Raw materials are extracted and crushed in-situ in the purest quality in a single operation – without drilling and blasting, and with minimal environmental impact.
The 280 SM(i) is driven by four steerable and height-adjustable crawler units. This makes the machine highly manoeuvrable, able to quickly turn at the end of a cut, according to the company. The LEVEL PRO ACTIVE automatic levelling system maintains the specified cutting
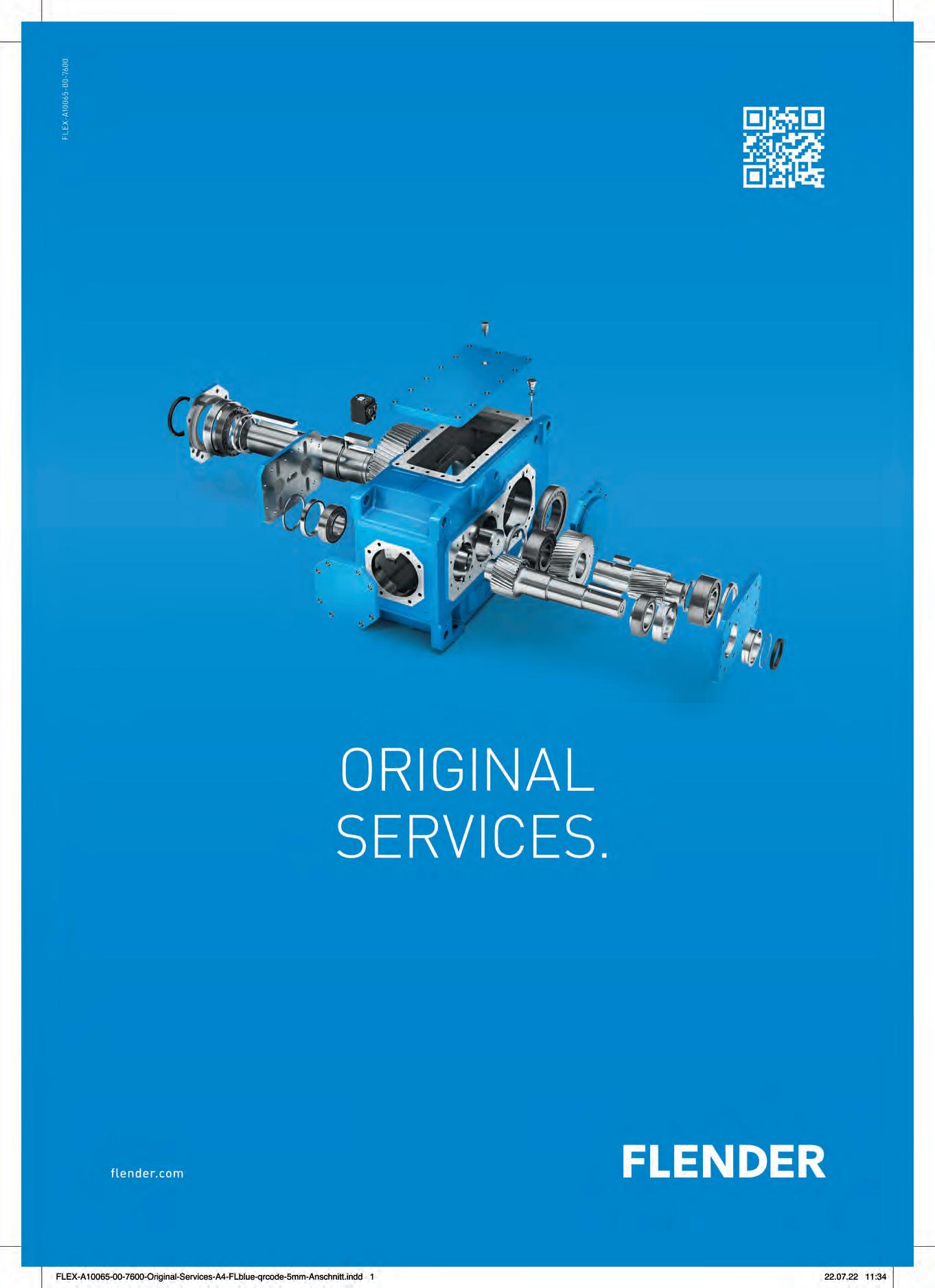
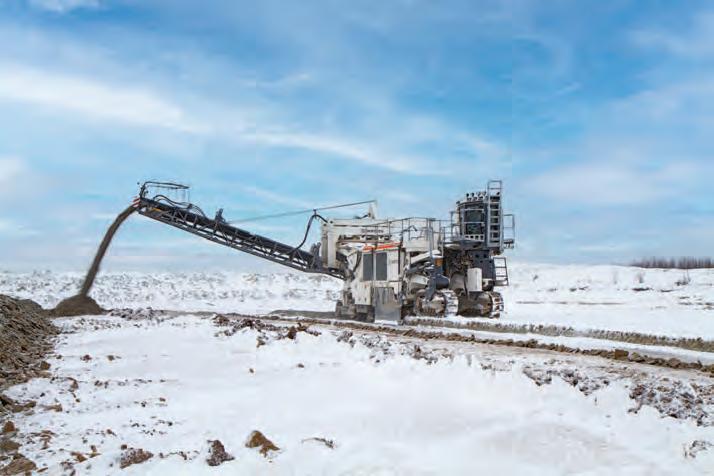
The 280 SM(i) is an “all-rounder” for all rock hardnesses and applications, Wirtgen says
depth with consistently high precision and without further aids.
The 280 SM(i) is an “all-rounder” for all rock hardnesses and applications, Wirtgen says. The 2,750 mm cutting drum unit, with a cutting depth of up to 650 mm, is precisely adaptable to each specific application and achieves outstanding cutting performance with minimal pick wear, it added.
Wear-resistant toolholder systems ensure optimal pick utilisation and minimal downtime.
While the soft-rock cutting drum unit is designed for high material flows in soft rocks, the hard-rock cutting drum unit ensures maximum durability and long life in hard-rock applications, according to Wirtgen.
The hydraulically, height-adjustable rear discharge conveyor with a movable counterweight can be slewed to the right and left by 90° and enables the loading of mining trucks with payloads of up to 100 t. Whats’ more, the operator can continuously vary the speed of the belt independent of the engine speed to reduce belt wear dependent on the material volume and the size of the mined material.
Entirely new standards are set by the dustsealed and air-conditioned, positive-pressure cabin on the new surface miner with fresh air filtration. This, the company says, prevents the ingress of dust into the operator’s workplace.
Mounted on the front left chassis column, the operator’s cabin has all-round glazing and is decoupled from the machine body to offer 90° rotation in both directions. Up to six cameras can also be installed to provide even better all-round vision, while various automated functions further contribute to operator comfort. This potentially reduces the risk of fatigue, assists the operator in achieving high productivity rates and improves the overall efficiency of the process, the company says.
Thanks to the reduction of carbon emissions by low specific fuel consumption, an efficient water management system and effective solutions for the minimisation of dust pollution, the 280 SM(i) shows that ecological and economic considerations are compatible and closely interconnected, Wirtgen concluded.
Moving to drive mode
After launching Generation X.e in 2019, SEWEURODRIVE says it is once again setting new technology standards.
The helical and bevel-helical gear units of the X.e series cover a torque range from 6.8 to 475 kNm across 23 graduated sizes.
Digital data models and the latest calculation methods have laid the foundations for a further improvement in the performance of its Generation X.e series. Among the benefits that come with this update are a higher thermal limit rating, a longer bearing service life, and higher nominal and application torques. Moreover, larger application angles are permissible with the maximum overhung load.
One potential result of this optimisation is a smaller gear unit size. Besides reducing the oil volume, energy consumption and total cost of ownership, this also means the units are lighter and take up less space in the plant. Particularly in the case of drives that are subject to high loads, mechanical safety – and, thus, the potential for preventing damage – is also further improved. What’s more, a lower oil-bath temperature and a higher bearing service life mean reduced unplanned maintenance.
These same gear units, to be displayed at Bauma, are part of the company’s “Industrial gear units to go” program for shorter delivery times, aiming to supply SEW-EURODRIVE industrial gear units to customers even faster.
This sees standard drives from the X.e – up to 175 kNm – and P series – up to 360 kNm – leave the plant just five working days after receiving an order. Gear units that require design adaptations – such as special output shafts or preparation for use at low temperatures – are ready for shipping within 15 working days.
In terms of hardware, the company will also be talking up the introduction of new line-operated DRU.. series asynchronous motors in the IE4 energy efficiency class in Munich.
The new IE4 AC motors with 4-pole design will be available in a power range of 0.75 kW to 200 kW and can be combined either directly with SEW gear units, or as standalone motors in all footmounted and/or flange-mounted designs.
The launch takes place ahead of the July 1, 2023 deadline stipulated in the third stage of the European ecodesign regulations for motors, (EU) 2019/1781 and (EU) 2021/341.
Still along the lines of sustainability, the Bruchsal-based drive specialist recently introduced GearFluid, a premium lubricant for
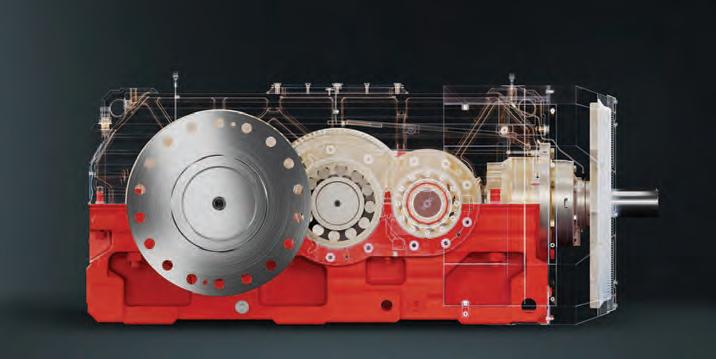
gear units made from sustainable biomass.
GearFluid Poly 220 E1 is the first CO2-reduced gear unit lubricant on the market made from sustainable biomass, with CO2 emissions at the end of the lifecycle of GearFluid Poly being 84% lower than conventional polyglycol oils, according to SEW-EURODRIVE. Consequently, this new premium lubricant helps customers reduce their overall corporate carbon footprint.
While offering maximum wear protection for the gearing and the rolling bearings, the premium lubricant’s low friction coefficients increase gear unit efficiency and, compared with conventional biodegradable oils, GearFluid extends the interval between lubricant changes by up to 300%.
Pump servicing workshop
Tsurumi, a dewatering pump leader, intends to lift the veil on its new safety pumps at Bauma 2022, offering visitors the chance to learn how to service a pump properly.
For the first time, the exhibitor is coming to the show with a workbench where visitors can demonstrate their skills. The task is to service a pump, especially in the sensitive areas of hydraulics and electrics, reinforcing the need to carry out regular maintenance to avoid pump failures.
Safety is also the focus of the new product presentation, which the Japan-based company has saved as a further treat.
The company will debut the KRDX, a model in its new series of safety pumps that are approved according to IECEx and ATEX standards.
The three-phase submersible heavy-duty pumps are designed for slurry drainage/pumping and have motor outputs from 3.7 kW to 7.5 kW. They are equipped with an agitator and an outlet of up to 100 mm to pass solids up to 33 mm in size. Tsurumi states a pumping capacity of 2,200 litres/min.
Completing the safety trifecta will be Tsurumi’s Connect system for monitoring of pumps and other machines, including those from third parties. Via a small box on the unit, the operator can determine the location, read out performance data and set alarm and error scenarios. The aim is to raise safety and efficiency to a new level, with the first systems already in use on the market.
The manufacturer will also use the show to provide information on many other pump models, including the LSC2.75S residue dewatering pump, and the KTZ and KRS pump series.
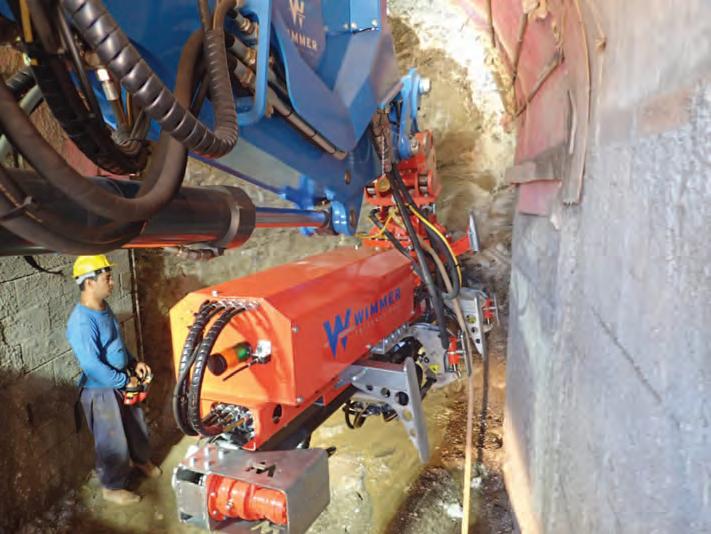
Mine development options
To this point, Austria-based Wimmer has set its sights on the tunnelling industry, with its flagship Blue Badger tunnel boring machine (TBM) being used around for tunnel cross-sections from 3.5 m in height.
Since the release of the original Blue Badger in 2018, the company has supplied around 20 machines to projects across the globe. One of these was for a gemstone mine owned by Suacuai Mineracao LTDA in Brazil where the machine was previously boring through rock that had a uniaxial compressive strength of 60-120 MPa.
The company has expanded this range with the miniBadger – for driving tunnels with a crosssectional area of 6.2 sq.m or more where the working height is 2.7 m – and the eBadger – a TBM driven by an electric motor that delivers up to 50 kW of power on battery for tramming and positioning and is connected to the mains infrastructure while tunnelling.
The introduction of the Yellow Fox is where the company could potentially find further mining applications.
Based off a Liebherr 914 Compact Litronic superstructure with a Liebherr 920 Compact Litronic undercarriage, the Yellow Fox can be used for working heights of 4.2-7 m. As with the Badger family, the excavator boom is custommade by Wimmer, offering high breakout and tear force alongside a boom that can be swivelled by 45°. All heads can also be switched out, changing from, say, a roadheader attachment to a drill, depending on the application.
The Yellow Fox is powered by a 90 kW US Tier 4 Final-compliant engine. For the first time, Tsurumi is coming to Bauma with a workbench where visitors can demonstrate their skills
Wimmer’s Blue Badger progressing through rock at a gemstone mine owned by Suacuai Mineracao LTDA in Brazil
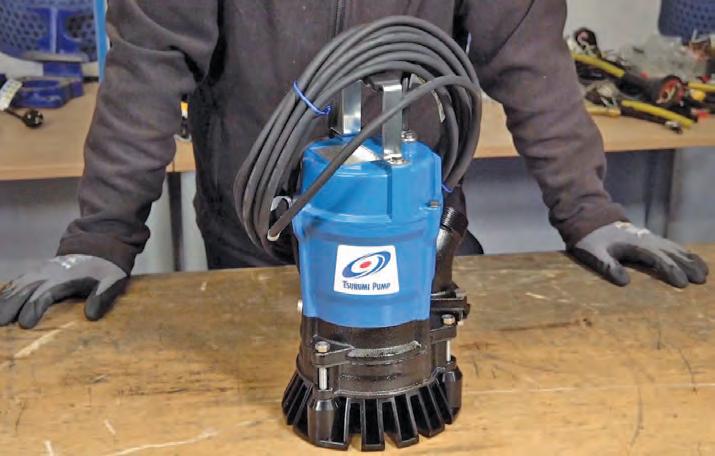
New products and direction for Hydreco
At Bauma, Hydreco Hydraulics plans to present its new range of directional control valves, the MS series, and the new multifunctional ergonomic handle, the MHC.
It will also use the event to display the most recent developments of the external gear pumps made in its new production site in Parma, Italy.
Designed in cooperation with Duplomatic MS, the new MS range includes central bypass, sixway, open-centre directional control valves for mobile applications. The range is designed for high performance with a wide range of configurations and options to meet customer needs.
Key features include compact and modular construction, with a single pump able to supply one to 12 services that cover pressures up to 350 bar.
The new MHC handle, meanwhile, has been designed to host a wide number of controls in a compact space. This sees the new electroproportional roller, as well as the full range of switches and devices, available on Hydreco handles.
Hydreco currently sells around 70% of its products direct to OEMs, with many of its CAN BUS-based joysticks used on underground mining machines. The company is also looking to provide a direct offering to the market through other channels.
Bauma 2022 offers a meeting place for Hydreco customers to find out about this new offfering, and will also provide the company with a chance to update the market on Daikin Industries’ plans for the wider Duplomatic Group, following its acquisition of the entity earlier this year.
AI-backed collision avoidance
Matrix Design Group, an ISO 9001:2015 certified manufacturer that designs, develops and markets safety and productivity technology for use in mining and industrial applications, will feature the OmniPro Visual A.I. collision avoidance system for small-to-medium sized vehicles at its Bauma booth.
This innovative application of visual artificial intelligence (Visual A.I.) and machine learning enables line-of travel and blind-spot pedestrian and vehicle alerting for mobile equipment, such as dozers and wheel loaders. Consisting of up-tothree 120° field-of-view cameras, the OmniPro system works without personal wearable devices or tags, and not only “sees” and identifies people and hazards, but also photographs and reports zone breaches.
OmniPro is an application of the Matrix technology that received the 2020 NIOSH Mine Safety and Health Technology Innovations Award, Matrix said.
Through its Visual A.I. object recognition technology, OmniPro has been taught to identify and report on a library of “objects”, including people, vehicles, equipment, stop signs and pedestrian signs. The user can select which objects will be included, whether to integrate with the machine or operate as alert-only, and whether the alert will be visual, audible or tactile. Additionally, depending on the operation’s needs, OmniPro’s wireless solution can trigger a stop sign, pedestrian light, voice alert or crossing arm. All incidents are recorded and can be reviewed to provide insights for additional safety training as needed.
OmniPro’s cost-effective and customisable solution can be adapted to match any operating environment through its programmable field-ofview zone grid configuration tool, which enables it to meet the safety requirements of different operations, Matrix claims. Rear-facing cameras can be used alone and, in multiple-camera systems, OmniPro will auto-switch to only monitor the vehicle’s direction of travel. Each system operates independently and is easy to install, the company added.

TTControl’s Autonomous Operation Cluster
One company talking up the use of autonomous operations at construction and mining sites at Bauma 2022 will be TTControl.
A joint-venture company of TTTech Group and HYDAC International, TTControl offers control systems and operator interfaces for mobile machinery and off-highway vehicles.
It recently helped initiate an Autonomous Operation Cluster (AOC) formed of Ammann, PALFINGER, Prinoth, Rosenbauer and TTControl, looking at collaborating on application-oriented solutions within this field.
The multinational companies will jointly develop key technologies for autonomous operation elements for series production of mobile machinery functions and off-highway vehicles, with the aim being to accelerate the development of advanced assistance functions through collaboration.
This year, the partners are focused on defining a technological solution and developing a proof of concept and initial prototypes. Further application implementation based on specific use cases will continue in 2023.
TTControl, for its part, is helping facilitate this automation collaboration through the provision of a new generation of electronic control units for vehicle manufacturers.
It launched the TTC 2300, the first member of its complete and scalable TTC 2000 series designed to meet the needs of automated and smart off-highway vehicles and mobile machines, earlier this year.
OmniPro is an application of the Matrix technology that received the 2020 NIOSH Mine Safety and Health Technology Innovations Award