
5 minute read
M y SMT NOW AVAILABLE
Following a meticulous design and testing process, SMT GB has now launched a brand new one-stop information, service and online parts ordering portal nationwide.
A core frustration faced by many fleet managers on a daily basis is the requirement to access multiple online or app-based portals and platforms to manage and maintain a modern fleet of machines.
Advertisement
To lighten this burden, MySMT offers a one-stop solution for SMT GB’s customers to manage their fleets.
Using a secure, web-based portal, customers can easily and quickly access, monitor and act on multiple aspects of fleet management, both from the office or on the move.
To ensure that the information stored on MySMT in a useful and usable manner, the platform is divided into the three distinct areas: “Company”, “Fleet” and “Parts”.
“Company” provides customers with visibility of financial transactions with SMT GB, all active CSA and Warranty contracts, oil sampling reports, ProCare recommendations and Service Inspection Reports.
“Fleet” provides customers with access to current fleet details, including location, operating hours, information of fuel consumption, productivity data, CO2 emissions and visibility of repair and maintenance data on all machines within a customer’s fleet.
“Parts” provides access to the newly launched SMT online parts store, allowing customers to look up and order all genuine Volvo parts 24/7, with access to technical drawings if required.
Another helpful feature of MySMT is ability to create multiple staff user accounts with varying levels of access and visibility to the system. This ensures that key decision making processes are preserved within the original arrangements of the customer’s management structure, while also providing staff responsible for the monitoring and administration of their fleet the ability to do so through MySMT.
Commenting on the launch of MySMT, Commercial Solution Manager Jack Kenny states: “MySMT provides a simple, user-friendly and secure portal for staff to carry out a wide range of monitoring, management and administrative tasks from.”.
Jack continues: “By combining information and the ability to take action instantly from a single, universally-accessible platform, staff responsible for fleet management and administration are offered the peace of mind from knowing that they are taking the best possible proactive steps to keep their fleet and operations running smoothly, all thanks to MySMT.”
Concluding, Jack states: “SMT are committed to bringing customer information into the digital age, and will continue to develop MySMT with our customers’ needs at the forefront of any new development”.
FOR FURTHER INFORMATION:
When using the right machine, waste can be transformed into valuable raw materials. Reducing, re-using and recovering waste to manage waste sustainably can be done profitably. Efficiently recycling waste by conventional means is notoriously difficult, and in most cases only a certain percentage of the waste ends up recycled. But what if there was an easier way?
We are lucky enough to have the most versatile machine on the market in regards to the TANA Shark Shredder. Be it general waste, mattresses, tyres, wood, plastic, C&I, C&D the Shark can handle them all and more. Pair that with excellence in service and you have a winning formula.
There are many applications to which the TANA Shark shredder can be used. The TANA Shark can shred all kinds of end-of-life tyres. These could come from cars, trucks, aircrafts and heavy-duty vehicles and can be really difficult to recycle. The TANA Shark uses hightorque to make it possible to shred tyres to an 80 mm particle size in just one pass and separates most of the metal wires directly from the shredded material flow on the conveyor. The steel wiring is removed in the shredding process and by an over-band magnet in the unloading conveyor. Once separated, shredded tyres and metals can be sold and reused in many ways.
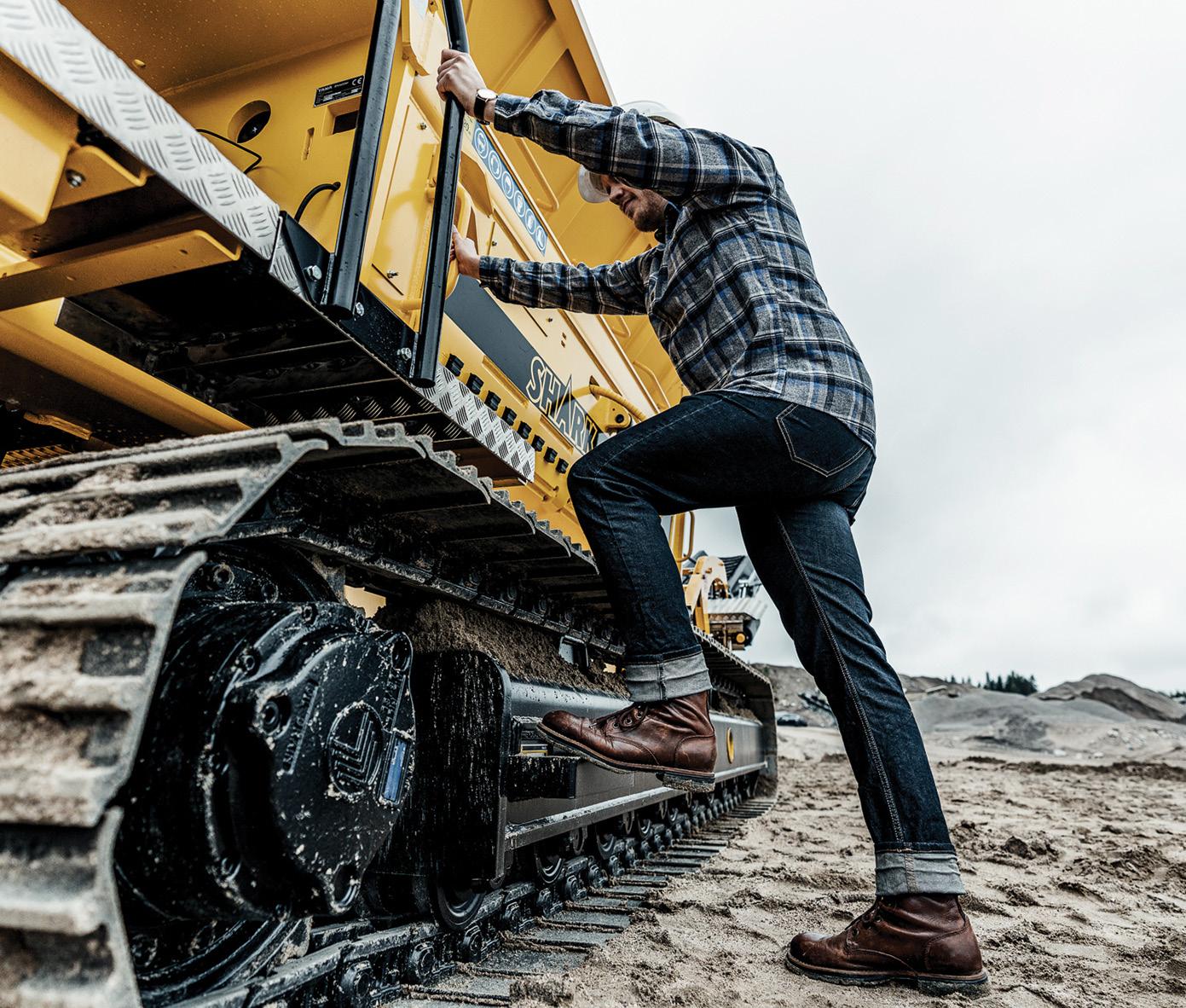
For packaging materials such as hard and soft plastics, cardboard, paper, wires, paper rolls, containers, aluminium, gypsum or any reject from the production line of a manufacturing process can all be shredded using the TANA Shark. TANA Shredders are well utilised in the treatment of this variety of material. Many complications arise from commercial and industrial waste depending on the recollection process of the materials. TANA shredders are slow speed and use a single shaft with high torque that optimises the machines functions. Because of TANA shredders unique features downtime is minimal as processes are in place to ensure the treatment process runs smoothly and efficiently without breaking down or requiring a ‘cool off’ period.
Get more out of your investment with the TANA Shark’s low-rev and high torque process. This makes light work for difficult materials such as mattresses, cables and wires, and ragger wires. Some of these materials are loathed by landfill operators as especially mattresses contain a mixture of complex materials such as textiles, latex, foam, springs and wood that are difficult to recycle. The magnetic separation of metals can generate additional income, as it can be sold on for recycling purposes. As cables and wires come in a plethora of shapes, sizes and contents, they can be classed as almost impossible to separate. However, the high torque capabilities of the TANA Shark enable this process to be possible.
Is Contamination
Still The Leading Cause Of Hydraulic Failures That
IS SO OFTEN QUOTED; AS ACCOUNTING FOR 70 TO 80% ?
If 80% of premature failures attributed to contamination was backed by definitive evidence 40 years ago; we would doubt it would still be the same today! –wouldn’t we?
Surely things have improved by now?
But we still operate those huge, old reliable balers & shears, or large plant equipment designed to last 30 years plus.
The OEM hydraulics of then didn’t really consider contamination so we see a lot of equipment without any filtration at all, or with so many inadequate systems ‘added on’ through the years; considered little more than ‘rock catchers’. Many older systems only used screens to trap the large particles of over 50 micron, whereas tolerances between moving parts these days are into single number micron.
Today’s new systems use filters that outperform those of 30 years ago, so shouldn’t we expect the frequency of contamination-related failures to be lower now?
NO! the level of tolerance in machinery is incredibly finer than ever before & many components are even more sensitive to contamination, so increasing that need for yet even finer filtration… & yes the filtration & awareness of the importance of fluid cleanliness has improved – but in essence the relationships are still the same! ; even more so with the increasing workload demands & crucial uninterrupted performance needs.
Contamination issues remain the same; being just anything that shouldn’t be there; dirt, water, rust, air, & wear debris - & the root causes remain persistent as general ingress, faulty pumps, system breaches, wearing cylinders, perishing seals, moisture or temperature issues, alongside the harder workloads we inflict on the equipment these days.
SO YES ! – The claim remains the same; So what is the best solution?
Without condemning the virtues of standard pressure & return filtration – it generally just can’t get down to the finer levels when it must meet the high flow velocities & pressures of the main system forcing those particles through the media.
Oil is the life blood of your machine & much like kidney dialysis; a By-pass or Off-line filtration system enables slow, continuous, multi-pass filtration at a controlled flow velocity & safe pressure drop, which results in the far higher filtering efficiency.
KLEENOIL By-pass cellulose depth filtration will affordably achieve these levels & maintain to a cleanliness target within the expected ISO 18/16/13 of new oil.
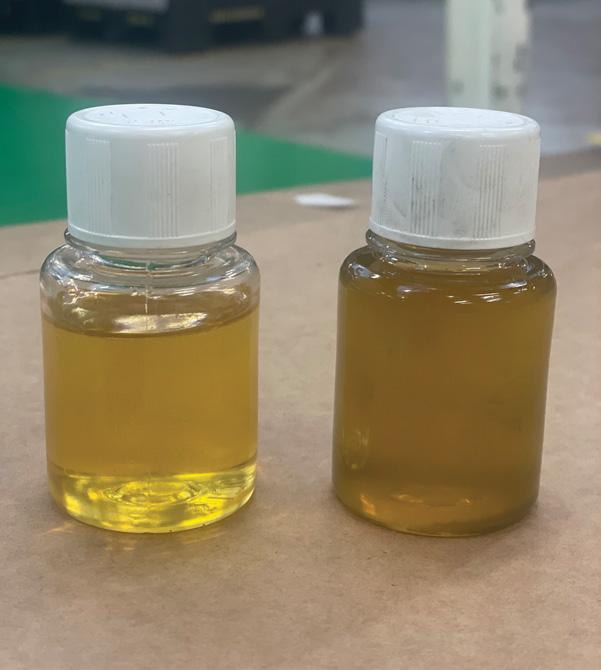
Controlling contamination to its absolute best improves hydraulic system reliability & longevity while reducing total cost of ownership of equipment. And with constantly cleaned oil; in conjunction with reliable condition monitoring; a company can eliminate the oil changes based on routine & move to essential changes based on assessed condition….. generally extending oil life by 5 times or more.
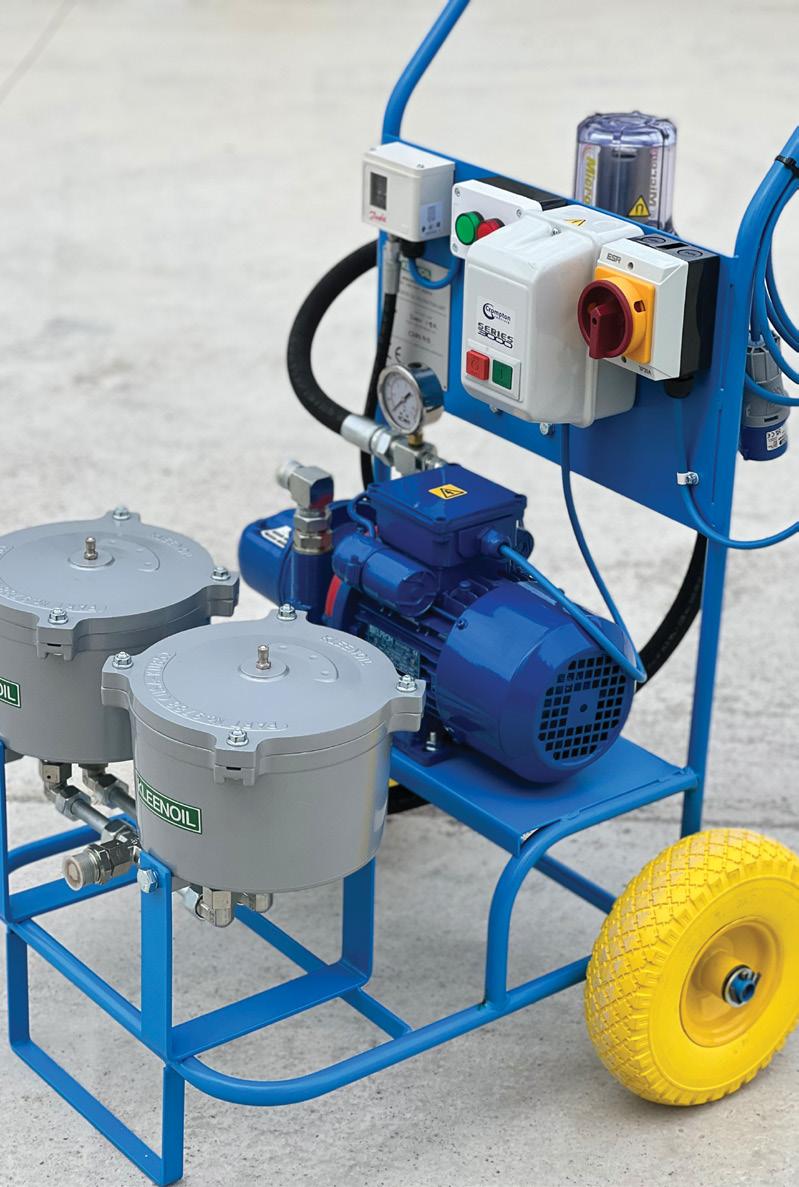
Minutes published by the Advisory Committee for Packaging (ACP) from the 1 November ACP meeting have highlighted that its members feel there is “no clear case” for interventions in the market, but compliance with packaging regulations is under review. (writes Joshua Doherty of Let’s Recycle)