
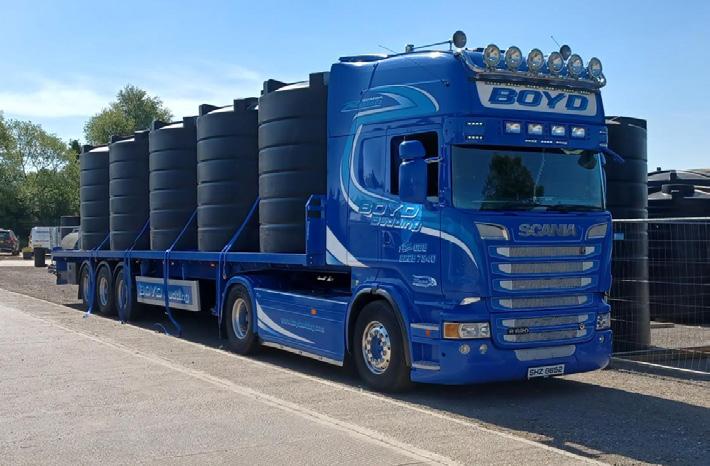
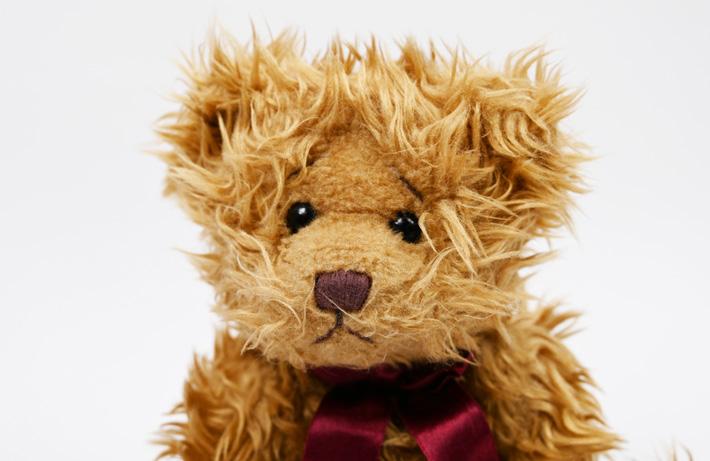
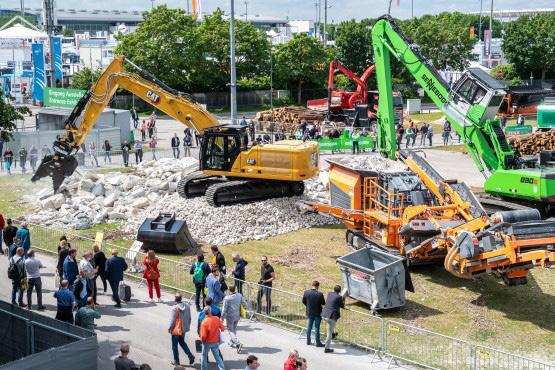
AUTHENTIC
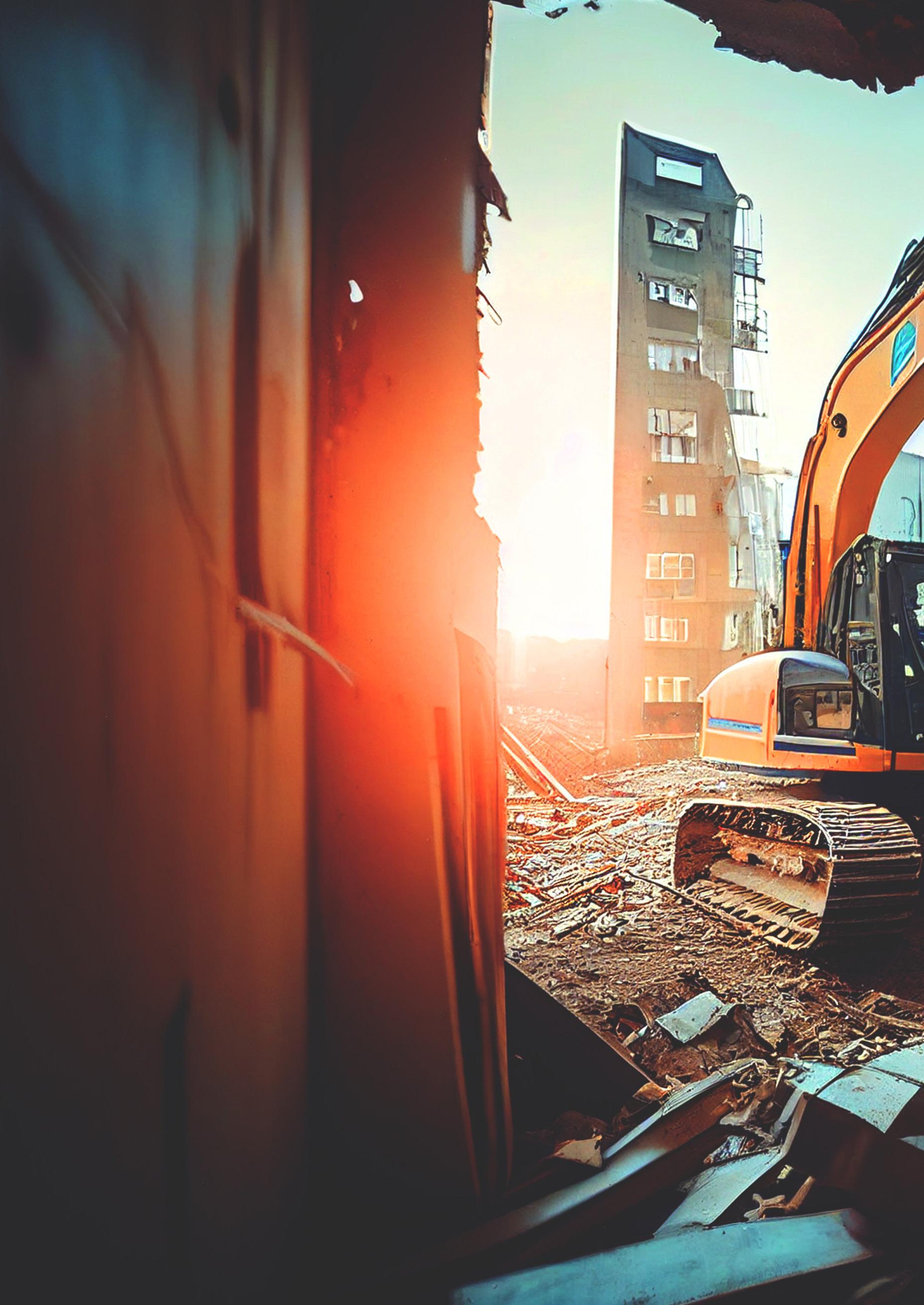
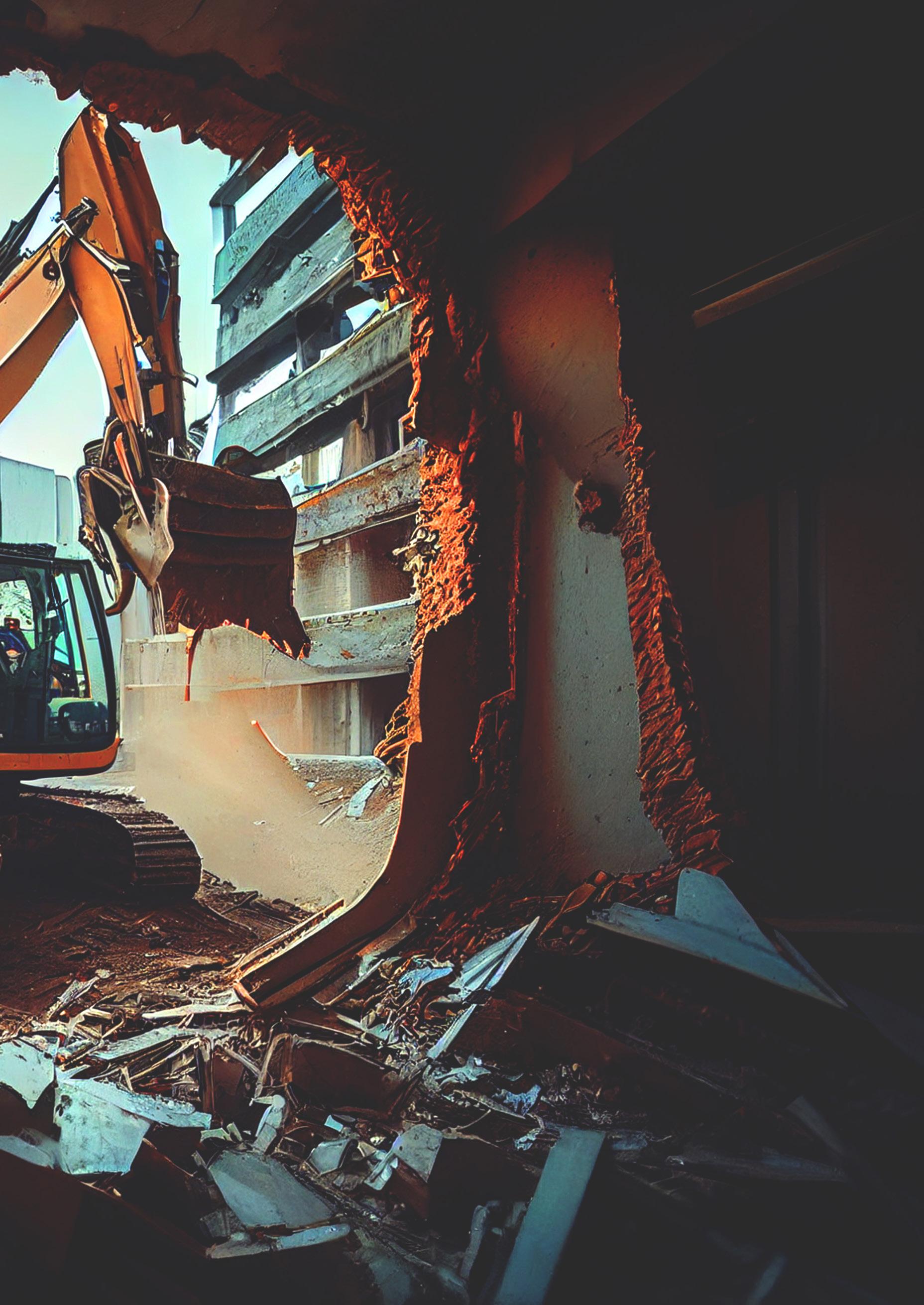
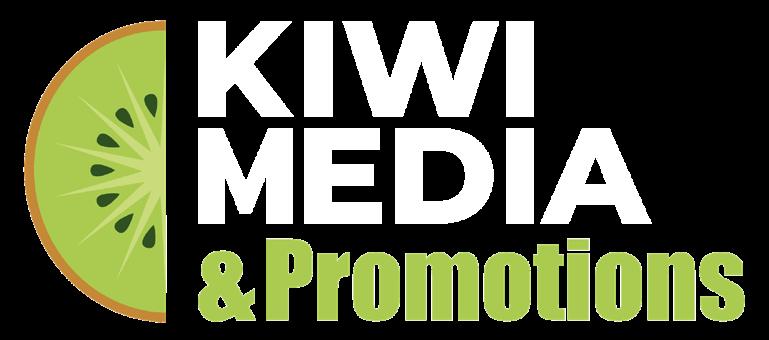
AUTHENTIC
The sun is finally shining, dear readers, and along with the banishment of all that rain comes another spring issue of Future Waste! As always we have a jam packed issue ahead, with this month’s main focus being the big bad wolf of the waste management industry: construction.
Not to fret, as we’ll be taking a look at how the industry is changing for the better! Both our feature articles look at exactly how the construction industry tackles the green issue, with all the tips and tricks you’ll need to stay in the know how. Our preview for IFAT 2024 also gears up for all of the wonderful green solutions the world has to offer, congregating in Munich this May!
And speaking of those in the know, BlakerTech adorn our front page, riddling us all things metal recycling in their fabulous spread. We also have two company profiles: Enduramaxx who make storage tanks, and Blazequel who pave the way in fire safety.
We also take a little detour from the world of construction for our Conscious Companies, with perhaps the cutest article this mag has ever seen! We speak to Charlotte Liebling, the founder of Loved Before Ltd, who details us everything her company does to ensure that not only do cuddly toys get a fresh start, but also just how important that change is to landfill capacity.
Happy reading everyone!
Rebecca Phillips EditorCHARLOTTE LIEBLING LOVED BEFORE LTD
KATE RUSSELL BLAKERTECH
CHESTER GILBERT ENDURAMAXX LIMITED
KEITH PICKTON BLAZEQUEL
DARREN SHELTON BUSINESS MANAGER
PHIL EVERY SENIOR SALES EXECUTIVE
REBECCA PHILLIPS EDITOR
REBECCA BURRELL SENIOR SALES EXECUTIVE
CHARLOTTE WALSH SENIOR SALES EXECUTIVE STEVE
LORNA COWLIN CONTENT CREATOR
MARTINA TONELLI MARKETING CO-ORDINATOR
DESIGN MANAGER
Future waste is published by Kiwi Media and Promotions Ltd 2nd Floor, 41-42 Southgate, Chichester, West Sussex PO19 1ET +44 (0) 1243 345 323
Kiwi Media and Promotions Ltd. © 2024 All rights reserved. Reproduction in whole or part is prohibited except with permission in writing from the company. Note to contributors: articles submitted to the Editor for consideration must be the original work of the author. Where photographs are included that are not the property of the company or contributor, permission to reproduce them must have been received from the owner of the copyright. Any views or opinions expressed within this magazine are not necessarily those of the company.
ISSN: 2631-4622
Registered in England No: 09910499
All advertisements are accepted subject to the Kiwi Media & Promotions’ standard of insertion. For a copy of Advertising Terms & Conditions, please write to Darren Shelton at 2nd Floor 41-42 Southgate, Chichester, West Sussex PO19 1ET
09 Latest News
A round-up of the latest news from the recycling and waste sectors over the past few months.
36 Front Cover Story: BlakerTech
BlakerTech’s innovative technology is renowned and respected across not just the metal sector, but also the waste and recycling industries.
42 Company Profile: Blazequel
A fire in your process line can be transported through your entire facility in seconds, so effective process protection is so critical!
50 Can Construction Waste Really Go Green?
The issue of construction waste generation isn’t simply a UK-wide problem, but a global dilemma that has left the industry in a bind.
53 Company Profile: Enduramaxx
Enduramaxx details all about their amazing journey to producing the fantastic products they offer.
60 Conscious Companies: Loved Before Ltd
In a world of increasing consumption, the need to Reduce, Reuse and Recycle has never been more important.
68 Preview: IFAT 2024
A sneak peak at the world’s largest trade fair for water, sewage, waste and raw materials management.
72 The 5 W’s of Construction Waste
How does Local Authority tackle construction waste?
• Tyre Recycling
• Aluminium Recycling
• Cable Recycling
• Electronics Recycling
• MSW Recycling
• Fridge Recycling
• ASR Recycling
• Various Scrap
• Car Battery Recycling
• Conveyor Belt Recycling
• Solar Panel Recycling
• *NEWS* Optical Sorting *NEWS*
- Small Purpose Sorter
• State-of-the-art NIR technology
• E xceptional separation ratios
ince 1956, the world leading Danish company has manufactured recycling equipment known for high performance, low production costs and products with high output purity. Eldan systems and machines are developed based on ambient mechanical technique for size reduction and separation and require no melting or chemical treatment. The modular design enables their customers to expand or upgrade their plants as the market changes. By adding on new machines with Ai and Infrared Technology to their product portfolio, they are now able to offer even more sustainable recycling solutions!
In January 2024, Eldan announced a co-ownership with Picvisa Machine Vision Systems, a front-runner in optical separation technology. Integrating the optical sorting technology into the Eldan processes is a huge leap forward, and the co-ownership will result in the development of new lines of sorting equipment. The first machines, the Eldan MPS (Multi Purpose Sorter) and the Eldan SPS (Small Purpose Sorter), will be launched during Q2 this year. The SPS will also be on display, live and running for demos, at IFAT in Munich in May 2024. The two machines are tailored for efficient sorting in various applications, particularly in WEEE, NF and mixed metal scrap systems but also for different kinds of Polymers. Advanced technology, such as broadband infrared technology (NIR/ MWIR), Ai (shapes and appearance) enables innovative and sustainable sorting of colour and material. As a natural step, the name Eldan Sorting was established to build the brand for the sorting part of the company.
Toni Reftman, CEO, Eldan Recycling, is very happy about the co-ownership.
“This is extremely exciting, and the timing couldn’t be better! We are thrilled to bring these new products to the market and others will follow during 2024.”
In terms of what this co-ownership means for reaching new markets and segments, Toni continues:
“We will be able to reach out to new customers, but also give existing customers more possibilities than before which in turn will benefit them and their customers.”
Picvisa and Eldan have broadened their joint horizon by presenting each other’s solutions with amazing results of new combinations that offers the best of the best! Everyone is a winner in this new co-ownership, especially our planet and the next generation. This is a great step to save the scarce resources of the planet and make them all last at least a little bit longer.
To learn more about Eldan Recycling, please visit: www.eldan-recycling.com
Increasing environmental responsibilities and sustainability targets are driving the construction industry’s ongoing needs for cost effective, easy to use solutions for dealing with wastewater onsite. Sites also need quick replies, concise information, simple transactions, and deliveries without hassle.
Mark Stubbs, Director of Kelly Tanks, has been involved in Water Treatment for over 30 years, leading him to establish Kelly Tanks, alongside Kelly Bryant, over a decade ago. Mark and Kelly have been guided by customer demand to provide the UK’s largest, most diverse fleet of Concrete Washouts and have further developed their range of Water Treatment Solutions to include pH Control, Remote Monitoring, Flow Proportional Dosing and Renewable Energy.
Kelly Tanks’ product range and customer support is designed to ensure sites are equipped to:
• Comply with regulations
• Minimise waste and environmental impact
• Prevent contamination/pollution
• Promote responsible waste management
Kelly Tanks offer a selection of Water Treatment and Concrete Washout Solutions for hire or purchase and onsite set up and familiarisation training if required. Their popularity and proven track record is a result of providing the kit you need, in the manner you want, at a price you’re happy with. Match this with their eager to please attitudes and above and beyond aftercare and it’s easy to see why their customers keep returning.
KEY BENEFITS YOU CAN EXPECT FROM KELLY TANKS EQUIPMENT:
• Designed to meet the rigours of the construction industry
• Fast and simple to set up
• Small footprint equipment available
• Units can be linked to handle range of flows, pumps sizes and particle characteristics
• Easy to Maintain and Monitor equipment
• Reduce off-site disposal costs
• Reduce risk of pollution
• Easy to use equipment
Kelly Tanks take pride in the quality of their products and to customer service making them a real pleasure to deal with.
To learn more about Kelly Tanks, please visit: www.kellytanks.co.uk FOR FURTHER INFORMATION
Veolia, the world leader in hazardous waste treatment, is launching a new specialist facility based in Avonmouth, near Bristol, to meet the growing demand for the safe and compliant management of hazardous and complex waste streams in the South West.
Designed to be able to accept a wide range of hazardous wastes, it is expected to be operational in spring 2024.
With a capacity of 6,500 tonnes per year, the facility adds to the company’s seven existing hazardous waste transfer stations handling over 76,000 tonnes per year, and will provide a full range of services including a mobile chemist service to ensure wastes are safely segregated and compliantly packed and labeled ready for transportation.
Specifically designed to accept and store a wide range of packaged palletised waste including kegs, drums, IBC’s, the facility will manage wastes such as aerosols and gas cylinders, non hazardous materials, and materials categorised as flammable, toxic, corrosive, and oxidising. By acting as a local hub it will enable cost effective access to Veolia’s full range of recycling, treatment and disposal facilities.
The Avonmouth facility will serve a range of customers producing packaged oily wastes from vehicle maintenance and engineering sites, laboratory wastes from research and development facilities, production wastes from all types of manufacturing operations, and materials
from household waste recycling centres. The site will include a new laboratory and specially designed waste storage areas used to segregate each item based on its potential hazards, physical and chemical properties. These facilities will ensure correct identification, storage and movement of waste to the most appropriate recycling, treatment and disposal locations.
The transfer site will be supported by Veolia’s mobile chemist service, Chempac, for segregation, labelling, packing, collection and treatment and disposal of hazardous and laboratory chemical wastes, to ensure compliance and safety for customers. Waste streams will be tracked by Veolia’s end-to-end cloud based system that will ensure compliance and traceability through the complete cycle from enquiry to treatment or disposal, and is designed to cover more than 100,000 different waste profiles.
Nicola Henshaw, Director Hazardous Waste at Veolia UK said: “To ensure we protect people and the environment,
complex and hazardous waste streams need to have strictly controlled collection and treatment solutions, and our new facility will deliver extended depollution capabilities to the South West region. By using the latest cost-effective solutions, gained from our expert teams, we will be able to offer an advanced and compliant local service that will meet the growing need in the area.”
Veolia is the world leader in hazardous waste treatment, from collection and disposal to recycling and reuse. Today, Veolia treats and recycles around 6 million tonnes of hazardous waste for more than 100,000 industrial, commercial or public authority clients, and employs 8,000 people who operate a comprehensive network of more than 300 facilities on five continents.
To learn more about Veolia, please visit: www.veolia.co.uk
Adiamond doesn’t start out polished and shining, but as we celebrate our anniversary, we have certainly succeeded in growing out of pressure! After a record 2023, we stand here today as a global organisation, able to provide international clients with our Complete Solution. Demolish. Crush. Recycle.
Established in March 1964, Hughes and Salvidge has endured and overcome some tough times over the past 60 years, whilst continuously growing in stature. Working alongside our associated companies, K&B Crushers, H&S Metals, and H&S Asbestos, has ensured that Hughes and Salvidge, and our divisions, have continued to go from strength to strength. We are dedicated to demonstrating the continual development of our company and the people within it.
As we continue to grow, so does our responsibility to the communities in which we operate. We achieve this by monitoring, and evolving, our three initiatives supporting the Environment, Health and Safety, and Social Value. Safety and environmental awareness takes precedence on all our projects, and we are committed to delivering responsible and sustainable practices.
Our Green Hands Initiative is an internal environmental strategy and action plan
that includes seven key performance categories; COSHH, Waste, Sustainability, Procurement, Environment, Health and Wellbeing, and Community.
Each category covers one of the main targets currently identified through our existing Environmental Management System. Each performance category is made up of a series action points that allow us to see what we are doing well and provides us with steps for positive reinforcement, improvement and development.
Recent projects have required us to monitor our impact to water ph levels, ensure we do not impact floodplains, work over, and even in water. Specific mechanical demolition techniques are used to ensure minimal impact on the key areas identified during the scoping of the works.
Water is only one element we monitor as we factor in the individuality of each project. We also consider endangered or unique species of wildlife and monitor various areas of the environment, including air quality, noise, vibrations, and wind speed and direction. Pulling all this together with our waste control and recycling on-site, sets us on the right path as a business.
We continue to look for ways to develop this initiative, be it through new forms of fuel, such as hydrotreated vegetable
(HVO) fuel, or by innovatively looking into methodologies to limit our impact on our journey to become a more sustainable business.
We have successfully completed a vast portfolio of technically challenging projects, carried out for a valued client base including blue chip companies, developers and main contractors, local authorities, government bodies, health trusts and utility companies. We possess a wealth of experience delivering diverse projects. No project is alike, we regularly adapt our ways of working to accommodate this and surpass client needs and expectations.
We just want to take this opportunity to thank everyone who has supported Hughes and Salvidge. From our site staff to our Head Office staff, our UK and now our Global partners, we couldn’t have managed this without the hard work and dedication from you all.
Thank you, and here’s to the next 60 years!
Fornnax, a global pioneer in recycling machinery, was pleased to introduce the SR-200 HD Dual-Shaft Primary Shredder, a groundbreaking invention, at the prestigious India Rubber Expo (IRE) at the Bombay Exhibition Centre in Mumbai on March 20, 2024. The SR-200 HD marks a significant leap in recycling technology, demonstrating Fornnax’s dedication to engineering excellence and sustainability.
On this momentous occasion, the special presence of Mr. Ajay Shah, the President of Reliance Industries Limited, and Mr. Vishnu Bhimrajka, the chairman & chief convenor of India Rubber Expo 2024, along with a consortium of our prestigious clients, inaugurated the SR200 HD, marking a significant milestone in recycling technology. Led by Ravi Rathi from Rathi Rubber India Pvt. Ltd., Mr. Chetan Joshi from Tyre Collection Australia, Mr. Rajan Subramanian from Vinora Industries, Mr. Paras Barasara from Valencia Rubber Tech LLP, Mr. Suresh from Unity EcoGreen, Mr. Bipin Kumar Agrawal from Earthman Rubber Industries Pvt.
Ltd., Mr. Anil Rathi from Oyster Industries Pvt. Ltd., Mr. Manish Agrawal from Earthmet Resources Private Limited, the unveiling showcased the innovation and collaboration driving the industry forward. FORNNAX has always been aggressive about constant innovation and new product development. Based on growing customer demand for high-capacity pre-shredders from Fornnax, the SR-200 HD, the new HD model of the SR series that replaces the standard SR200 model, was developed. The Primary Shredder SR-200 HD is more powerful and has the highest input capacity model in the SR series of machines.
The SR-200 HD is primarily designed for tyre shredding applications. It can also be utilized for other applications, including high-volume municipal solid waste, wood pallets, industrial and commercial waste, and many more.
As a result of the stringent waste treatment policies in place, there is a growing global demand for competitive pre-shredders. The introduction of the SR-200 HD presents significant
opportunities for industries in the Middle East, Australia (due to full-tyre export bans from Australia and steel export bans from the Middle East) and Europe, where an increasing need for advanced recycling solutions is evident.
Primarily targeting large-scale recyclers and cement plants that require highcapacity machinery. We have secured six pre-launch orders from India, Australia, the Middle East, and Europe, reflecting the trust built in the global market over the years. Industries are seeking machinery with enhanced output capabilities that comply with industryleading standards to meet their recycling needs effectively.
Fornnax’s Objective is to Become a Leader in Recycling Technology
FORNNAX is focusing more on designing and developing new products that suit specific input tyre types that increase efficiency instead of providing standard models suitable for all tyre types.
FORNNAX is increasing its budget in R&D each year as we focus on new product development for customers’ specific
demands rather than continuing with the old standard products; in addition, CPCD-based, we are improving our standard models based on customers’ feedback. In the recycling industry, Fornnax focuses on various applications to achieve a broad range customer base and vision to become the world’s biggest shredder manufacturing company. For tyre, municipal solid waste, metal and cable recycling applications, the company has 14 new shredder models under development till 2030 designed to meet the heavy demands of high-volume applications and users.
The new shredders come with various proven knives developed by Fornnax to accommodate customers’ needs. With the robust cutting chamber design.
The slow-speed shafts, which produce up to 2,000,00 Nm(newton meter) of torque,
allow the SR-200HD to work with the most challenging materials. This, along with a quick shafts change system, enables the end user to switch from working in one application to another. Overall, the SR200 HD is a high-capacity addition to our range and is already in high demand by our customers worldwide.
There are different variants available for different market standards. SR200 with disc classifier will provide 60 to 150 mm output sizes to feed downstream equipment. The SR-200 HD with a Trommel screen provides output sizes of 60-80 mm, which is called TDF alternate fuel for the cement industry. And SR-200 HD without a screen produces output sizes up to 400 mm, called single pass rough shreds. Due to the design of 750 mm diameter knives and a larger shaft centre, it has more discharge space to process bulky and high-thickness materials such as agricultural tyres, truck tyres and OTR tyres.
• The new HD model provides a low cost-per-ton with high reliability, ease of operation, and more flexibility for various types of tyres, as well as a design optimized especially for sites with a 25-ton per-hour production requirement.
• The SR-200 HD model provides higher capacity due to its high RPM and torque, resulting in less manpower, electricity, and wear costs.
• The new HD model is designed to focus on the TDF application (Tyre Derived Fuel). Cement plants usually utilize 3 to 4 lines to maximize production. The SR 200 HD is a single-line system that delivers a high output equivalent to 3-4 smaller lines.
Craig Walsh, a dedicated member of the Charles Muddle Ltd team, is preparing for a significant challenge, ‘Walking With Scrap in Mind!’, in support of mental health awareness and to raise money for the charity ‘Mind’. Craig aims to traverse over 100 miles, commencing from BMRA member, Charles Muddle Ltd, based in Adversane, West Sussex, on 24th May 2024, and concluding at the BMRA HQ in Huntingdon by dusk on 26th May 2024.
Motivated by his personal connection to the cause, Craig plans to integrate the ethos of recycling by collecting scrap
metal along the route for subsequent recycling. Since February, Craig has covered an impressive 234 kilometres (134 miles) through running, walking, or cycling, showing his dedication to physical preparedness for the upcoming trek. Surpassing the initial fundraising target of £1000, Craig has already amassed £1188, underscoring the generosity and support of donors.
With an average pace of 4mph, Craig anticipates covering a target distance of 35 miles per day, reflecting his meticulous planning and determination. Embracing the challenge with excitement rather than apprehension, Craig eagerly anticipates
the journey ahead, fueled by his unwavering commitment to the cause. Reflecting on the significance of mental health awareness within the recycling industry and society at large, Craig acknowledges his own struggles and the various outlets that aided his journey. He extends his heartfelt thanks to donors and expresses his appreciation for the support received from his employer, Charles Muddle Ltd.
Contemplating the possibility of documenting his journey through a video diary, Craig is actively exploring innovative ways to engage supporters and share his experiences along the way. For the first leg of his journey, Craig is toying with the idea of continuing through the night so he can witness London at sunrise. Keep a look out for him on social media!
To support Craig’s endeavour, donations can be made through his JustGiving page. Moreover, individuals and businesses interested in sponsoring the cause, or joining Craig along segments of the route, are encouraged to make contact with Craig to help foster a sense of community engagement.
For more information about Mind and their invaluable services, visit www.mind.org.uk
Craig’s JustGiving page visit: https://tinyurl.com/craig-walsh-mind
Recovery of high-value metals and minerals from non-ferrous scrap presents an attractive opportunity for processing plants to dramatically increase profits and reduce waste going to landfill.
Our SandFlo fluidised bed separator and MagThro eddy current system are durable, reliable, cost-e ective and environmentally friendly solutions, designed to save time and increase profits.
Both are built by hand at our UK premises, with full installation, training and support. For more information or to arrange a demonstration, please call or email our team.
Come and see us at Hillhead, stand C5, to see our MagThro and SandFlo in action.
l High recovery performance
l Easy to use, reliable and robust
l Dry process solutions, no by-products
l Individually built in the UK
l Installation and full training provided
l Products installed in 14+ countries worldwide
Thousands of companies are behind on key steps to tackle plastic pollution in their value chains, according to landmark data released today by CDP, the non-profit that runs the world’s environmental disclosure system. The data reveals, for the first time, the extent of companies’ awareness of their contribution to the plastic crisis, and presents a strong baseline for accelerating action at the fourth round of Global Plastics Treaty negotiations (INC-4) later this month, where mandatory corporate disclosure is on the table.
Findings show that almost half (42%) of companies took the vital first step of mapping where plastics were produced and used within their value chains in 2023. However, there are significant gaps in corporate understanding and action:
• Only 21% of companies were aware of risks associated with their plasticrelated activities, however
• 70% of companies have not yet mapped the impacts of their plasticrelated activities on the environment and human health; and
• 64% have not yet set targets for managing their plastic-related impacts, such as the use of plastic products and waste management practices.
These findings come from the disclosures of nearly 3,000 companies in 2023, spanning all regions and sectors, many of which have significant plastic-related impacts, including food and beverage, retail, and apparel. These high-impact companies are very likely to face tangible risks as a result, including supply chain disruptions, waste management fees, and regulatory risks, with more than half of G20 countries already having introduced plastic-related legislation.
Encouragingly, of companies not yet taking action, around half plan to map their impacts and set targets within the next two years. Greater visibility of plastic footprints, gained through consistent corporate data disclosure, will support companies to build strategies reduce their use of plastics and the pollution associated with it. Governments can accelerate this by including mandatory corporate disclosure on plastics in the Global Plastics Treaty being negotiated in Ottawa later this month.
CDP’s Head of Sustainable Business, Nathan Cole, said, “The fact that 3,000 companies disclosed voluntarily on plastics in this pilot year is an incredibly positive first step. Our findings show how much actionable data on plastics is needed.
Not just to rapidly boost corporate progress and translate awareness into action, but to assess our global progress towards reducing plastic pollution and its impacts. Governments must seize this once-in-a-lifetime opportunity and create the enabling environment companies need by agreeing an ambitious Global Plastics Treaty, with mandatory corporate disclosure as a core element. As plastic use continues to rapidly increase, our time to effectively limit its most dangerous impacts shrinks. We must accelerate action on plastics urgently by making plastics disclosure mandatory.”
Disclosure is the foundation of action. It’s a key tool for companies to understand their plastic-related impacts and know what they need to do to manage them. Disclosure is also a business necessity and increasingly required to secure access to capital and to compete efficiently in global supply chains.
Companies recognize this and have signalled their desire to see disclosure mandated. 37 companies worth more than US$ 270 billion in market capitalization value have signed CDP’s open letter to governments to this effect, asking them to create the regulatory certainty and level-playing field needed.
A spokesperson from Stella McCartney commented: “Since Stella McCartney’s debut as the first-ever luxury house to never use animal leather, feathers, fur, or skins, we have been on a mission to source and create cruelty-free alternatives that are less reliant on fossil fuels. Through the disclosure of our plastics data, we have been able to further assess our plastic use within our products and packaging – highlighting further reductions and opportunities for innovation and circular solutions. As a brand that proudly supports bio- and plant-based alternatives to petroleum products, we signed CDP’s corporate open letter calling for mandatory corporate disclosure within the Global Plastics Treaty as a call-to-action for other brands and business leaders to join us in defining their commitments on reducing their plastic use, whilst supporting and scaling their investments in sustainable solutions.”
Nathan Cole continues, “Companies must acknowledge the evidence: no
industry is immune to the massive risks associated with plastic pollution. CDP has prepared companies to start providing the data that they, investors and policymakers need to tackle plastic pollution and waste.
“Once agreed, CDP stands ready to drive market implementation of mandatory disclosure through our global disclosure platform. We have already started preparing companies and in 2024, we’re scaling this further, by encouraging all disclosing companies – 23,000+ in 2023 – to report on plastics through CDP. Heading into INC-4, we remain committed to putting our wealth of data, insight and expertise, and our trusted disclosure system, at the disposal of stakeholders during the INC process and once a Treaty is in place.”
CDP’s expansion to plastics disclosure is in partnership with The Ellen MacArthur Foundation, The Pew Charitable Trusts, the Minderoo Foundation and WWF.
70% of companies have not yet mapped the impacts of their plastic-related activities on the environment and human health
• Almost 3,000 companies, including listed companies with over US$25 trillion in market capitalization value, disclose on plastics through CDP for first time.
• Almost half reported mapping where plastics are produced and used within their value chains, a vital first step.
• However, only 21% reported plasticrelated risks within their value chains and just 1/3 taking key steps like mapping impacts on environment and health.
• Findings show major gaps in data needed to address the plastics crisis, boosting the case for mandatory disclosure, set to be discussed under Global Plastics Treaty negotiations.
• 37 companies worth $US 270 billion in market capitalization value, including Unilever, Stella McCartney and Superdry join calls for mandatory disclosure, recognizing the need for comprehensive, actionable data in tackling plastic pollution.
EDGE Innovate has been on a journey designing, innovating and creating. Our solutions are helping customers around the globe to shred, screen, separate and stack faster, safer and with greater efficiency than ever before. From advanced material handling solutions to state-of-the-art recycling equipment, EDGE Innovate is leading the way towards a better, more sustainable future.
Join EDGE Innovate at IFAT 2024, the world’s leading trade fair for environmental technologies to learn more about their journey and how EDGE’s environmental technologies can support you. The event is scheduled to take place from May 13th to 17th, 2024, at the Munich Trade Fair Centre.
IFAT Munich serves as the largest platform for water, sewage, waste, and raw materials management, attracting industry professionals and experts from around the globe. As a frontrunner in the field, EDGE Innovate is poised to showcase its latest advancements in waste processing technology, with EDGE’s popular VS420 waste shredder on display.
The EDGE VS420 represents our next generation of waste shredders, engineered for unparalleled versatility, durability, and resistance to contaminants. Boasting high capacity, reliability, and low running costs, the VS420 is set to revolutionize waste shredding, offering operators an efficient and cost-effective solution for their shredding needs.
Visitors to IFAT 2024 can experience the EDGE VS420 firsthand at Booth 205/304 in Hall B5. The company’s representatives will be on hand to provide demonstrations, discuss product features, and offer expert advice on selecting the right equipment to meet specific needs.
Key features of the EDGE VS420 include hydraulic hopper extensions, a large automatic tipping hopper with remote functionality, hydraulic height-adjustable twin-pole magnet, and EDGE’s innovative VS Status Lighting system, providing real-time communication between the machine and operator for optimal performance.
“We are excited to connect with waste professionals throughout the five-day show and demonstrate how EDGE Innovate continues to push the boundaries of waste shredding
technology,” Adrian Donnelly, EGDE Innovate Marketing Manager.
In addition to showcasing its latest product offerings, EDGE Innovate invites attendees to claim a one-day pass voucher for complimentary access to IFAT 2024. Vouchers can be redeemed by contacting EDGE Innovate directly via info@edgeinnovate.com.
EDGE Innovate develops, manufactures, and markets sophisticated technologies for shredding, stacking, screening, and sorting of primary and secondary raw materials in production processes and recycling. The company’s material handling and recycling range comprises reliable, durable, and cost-saving products, including mobile stockpilers, tracked stackers, tracked and mobile feeders, trommels, slow-speed waste shredders, picking stations, material classifiers, roll-sizers, and truck offloaders. With a commitment to innovation and sustainability, EDGE Innovate empowers its customers to shred, screen, separate, stockpile, and size a vast array of materials.
Key features of the EDGE VS420 include hydraulic hopper extensions, a large automatic tipping hopper with remote functionality, hydraulic height-adjustable twin-pole magnet, and EDGE’s innovative VS Status Lighting system, providing real-time communication between the machine and operator for optimal performance.
RECOUP, founded in 1990, is the UK’s leading independent authority and trusted voice on plastics resource efficiency and recycling. As a registered charity, our work is supported by a network of over 170 members who share our commitments including a more sustainable use of plastics, increased plastics recycling, improved environmental performance and meeting legislative requirements. We achieve these by leading, advising, challenging, educating and connecting the whole value chain to keep plastics in a circular system that protects the environment, underpinned by evidence and knowledge.
Originally set up in 1990 as an initiative called operation RECOUP, the organisation brought together major UK plastic bottle, machinery, and materials producers to promote plastic bottle recycling. The project was supposed to last for three years, but over 30 years later RECOUP is still going strong providing support on plastics recycling and resource efficiency to the whole plastics value chain. An ever-present challenge throughout RECOUP’s history has been to ensure plastic packaging design is aligned with the capabilities of plastics recycling infrastructure so that valuable materials are an output of the recycling process. To support the industry with this challenge, RECOUP has led the conversation around packaging recyclability and design through its flagship publication, Recyclability by Design. Updated annually, this essential document provides a set of guidelines to support the plastics packaging industry
make informed design choices. However, guidance on its own isn’t always a guarantee that packaging is going to be sorted correctly for recycling. RECOUP’s approach to this is to also carry out labbased testing of packaging or recyclability sorting trials in live recycling facilities with the co-operation of waste management partners. This provides direct information on how packaging performs during the collection and sorting phases of the recycling chain.
Testing in the RECOUP laboratory can form the first stage in a recyclability test, where packaging is assessed using near infrared (NIR) technology as well as a Fourier transform infrared spectrometer (FTIR). These machines are used to assess how packaging is likely to be detected at a materials recovery facility. The results of this can then provide initial feedback to packaging designers about improvements that can be made before a full site test is carried out.
An example of how lab-based NIR testing can help guide packaging designers to understand how their packaging will perform is by producing colour maps. The colour map shows how different components of packaging affect detection through the MRF process. Taking a PET bottle with a PP label and PE cap as an example, areas detected as PET by NIR are shown in blue, with PP shown as green and PE in yellow. In some cases because NIR penetrates the label and the bottle material the result comes back with a mixture of both the PET and the PP signatures, so this is coloured in orange to represent a mixed result. This mixed area means that this portion of the bottle will not detect as either PET or PP. In the image shown the PP label (orange) covers 50% of the bottle with
50% showing as PET (blue), which means that there is a reasonable amount of PET visible to the NIR for detection.
Site-based testing enables the evaluation of the packaging throughout the entire journey from the entrance hall of the MRF, through to the final output location of the materials. Packaging is tracked as it makes its way through the facility to determine how it is identified and sorted by the process and whether it makes it into the target material stream. One of the first tests within a MRF is to determine if the item makes it through initial sorting due to factors such as its size. From there 2D and 3D packaging is separated with 2D items such as paper packaging and flexibles going one way and 3D rigids going the other. The 3D rigids stream is where most of RECOUP’s testing takes place, with the near infrared (NIR) equipment being used to detect and separate the rigid plastic packaging into segregated streams such as PET natural and HDPE natural. Alongside recyclability guidelines, understanding the journey plastic packaging takes through a recovery facility is crucial to ensuring it is recycled.
RECOUP have recently been involved in several new advances of recyclable packaging, such as Capri-Sun’s development of mono-material pouches to aid recyclability, and Lucozade and Ribena switching from full to partial sleeves on their drinks bottles to increase the ability of NIR systems to correctly identify them in the recycling process. The availability of recyclability guidelines and the ability to test plastic packaging recyclability in realistic scenarios provides a crucial support service to the industry to improve plastics recycling.
To learn more about Betonblock & CDT, please contact: Betonblock@wotmix.co.uk
Betonblock® and Wotmix are proud to announce the introduction of CDT® (Concrete Drive Thru) to the market. Having installed the first concrete drive thru in the UK at Wotmix plant towards the end of last year in 2023, we’ve witnessed a remarkable uptake with an average of 20 customers collecting concrete from the drive thru daily. This innovative solution has streamlined operations and elevated convenience for Wotmix customers, marking a significant milestone in the evolution of concrete procurement.
CDT® has also expanded its reach, with installations in Oxford and plans to install a third Concrete Drive Thru in Scotland. Additionally, CDT® has installed a drive-thru in Minnesota, USA, with plans for three additional installations in the coming months and is actively seeking opportunities for global expansion.
With CDT®, customers access fresh concrete with a simple touch of a button. Our modular system allows for easy configuration, tailored to specific requirements and local conditions. As industry experts in concrete, we provide unparalleled support, ensuring a hassle-
free experience for both you and your customers.
Empowering customers to select the exact amount of concrete they need, from 0.2m3, for various applications, our self-service solution streamlines operations. Simply drive the vehicle under the discharge belt, initiate the mixing process, and within minutes, fresh concrete is ready for transport. Safety remains paramount, with our system fully integrated into a UL certified and tested safety concept.
CDT® eliminates the need for a water connection, offering flexibility and convenience with a 1000L tank. Streamlining operations for building material suppliers, CDT® enhances customer satisfaction and loyalty. By expanding your service to include fresh concrete, you not only save time for customers but also secure the future of your business.
Our commitment to sustainability extends beyond convenience. With a dry-cleaning procedure promoting recycling and meticulous monitoring of system parameters, CDT ensures minimal environmental impact and maximum efficiency.
Moreover, Betonblock® has expanded its presence in the UK through a strategic partnership with Wotmix, Betonblock’s official UK distributor. With a warehouse at Wotmix, we can now deliver moulds in the UK without the need for extra paperwork and import duties.
Betonblock® stands as a beacon of innovation in the realm of concrete moulds, revolutionising the industry for over 15 years. Our steel moulds, meticulously crafted in-house, boast a lifespan exceeding 10 years. Utilising structural S355 steel sourced from esteemed producer ThyssenKrupp, and fortified with a rust-proof powder coating. We provide solutions to repurpose leftover concrete, minimising waste and promoting sustainability. Our moulds offer an economical and eco-friendly option for various industries, boasting a costeffective price per block.
In addition to our moulds, we furnish a comprehensive range of accessories, lifting, handling, and transport equipment, ensuring a seamless casting process.
Choose Betonblock® and CDT for innovative, sustainable solutions that redefine construction standards.
Harrow Council, has elevated waste handling efficiency at their Household Waste Recycling Centre by adopting the Atlas 200MH waste handler paired with the Promove SG 13.20 selector grab. This transformation represents a significant leap forward in operational comfort, safety, and productivity, setting new standards in waste management technology.
The Atlas 200MH has exceeded expectations, providing operators at Harrow Council with an unparalleled experience compared to its predecessor, the Fuchs equipment. The spacious cab design, excellent visibility, and ergonomic features offer operators a comfortable and safe working environment. Additionally, the offside blind spot camera ensures enhanced safety, meeting rigorous site safety requirements. The extended reach and optimised boom and stick configuration of the Atlas 200MH offer operators improved flexibility, enabling them to maintain a safe distance while ensuring a clear and secure work environment.
Operators praise the three different engine speed modes, allowing customised responsiveness aligned with individual operators’ confidence levels. The machine’s precise hydraulic response and intuitive controls have garnered acclaim for their user-friendly interface.
The Promove SG 13.20 selector grab, equipped with sealed self-lubricating bushes, significantly streamlines daily maintenance, reducing downtime and maximising operational efficiency.
In line with Harrow Council’s commitment to sustainability, the Atlas 200MH features advanced clean engines, reducing emissions and demonstrating a steadfast commitment to environmentally responsible practices.
The machine’s exceptional manoeuvrability, extended reach, and improved safety features contribute to a safer working environment by minimising operator proximity to materials being handled.
Notably, TDL Equipment offers an extensive range of Atlas Material Handlers and Promove Attachments, providing a diverse array of solutions tailored to various waste management requirements. The availability of this comprehensive range offers industry professionals unparalleled options for optimising their waste handling processes.
With the outstanding performance and exceptional service provided by Contract Plant Rental (CPR), who have provided Harrow Council the machine and attachment on contract hire, Harrow Council anticipates continued operational excellence without the need for further enhancements.
Reflecting on their experience with the Atlas 200MH and the Promove SG 13.20 selector grab, Harrow Council emphasizes the seamless integration and effectiveness of this setup, showcasing its unmatched efficiency and reliability in waste management operations. To learn more about Atlas Material Handlers and Promove Attachments available from TDL Equipment, please visit: www.tdlequipment.com
Asset finance is, for many firms, a form of funding they have used for many years. Yet still, for others, it’s not something they know much about. In this article Close Brothers Asset Finance takes a closer look at the different products and understand why it could be the perfect option when considering your next purchase.
In short, asset finance is an alternative form of funding used by businesses to obtain the equipment they need to grow or access much-needed cash. Asset finance makes the otherwise unaffordable affordable because it gives businesses access to the equipment they need without incurring the cash flow disadvantage of an outright purchase. Agreements can also be customised to the business’s needs, with flexibility on both the term and repayment schedule. There are various products that come
under the broad umbrella of asset finance with one of the key ones being Refinancing or capital release, as it’s also known; it’s a proven way to make your assets work for you and release cash back into the business.
It works by the finance company purchasing the asset and financing it back to you, with repayments calculated in line with the income the asset is expected to generate; at the end of the refinance term, you own the asset.
This offers several benefits to a business that just needs a cash injection, whether it’s for investment in additional business critical assets or to use in other areas of the business, including unexpected bills and invoices, salaries, VAT payments, diversification - the uses are almost endless. Funders can also look to take over a finance agreement with another provider and extend the term, ultimately reducing monthly payments and easing the pressure on cash flow.
Other examples of asset finance products are:
• Hire Purchase (HP) allows you to buy the equipment on credit. The finance company purchases the asset on your behalf and owns the asset until the final instalment is paid, at which point you are given the option to buy it.
• Finance lease: The full value of the equipment is repaid to the finance company, plus interest, over the lease period. At the end of the term, you can choose to:
• continue to use the asset by entering a secondary rental period
• sell the asset and keep a portion of the income from the sale
• return it
• Operating lease: Similar to a Finance Lease, an Operating Lease allows you to rent the asset from the asset funder while you need it. The key difference between the two is that an Operating Lease is only for part of the asset’s useful life. This means you pay a reduced rental because the cost is based on the difference between the asset’s original purchase price and its residual value at the end of the agreement.
Very
Construction materials giant, Breedon has slashed the amount of time it spends on tachograph administration by 1,300 hours a year – thanks to Webfleet, Bridgestone’s globally trusted fleet management solution. With 450 HGVs operating across more than 300 sites, the group provides asphalt, ready-mixed concrete and surfacing solutions within the UK and Ireland.
Webfleet’s Tachoshare Plus has helped Breedon re-coup the admin time by facilitating automatic daily remote downloads of both driver and vehicle tachograph data. Drivers and transport managers no longer need to travel to depots to complete vehicle downloads, saving them valuable time and maximising productivity by keeping the trucks on the road.
Truck-specific navigation is also saving time and boosting driver safety.
“With Webfleet’s HGV routing, we can set much more accurate routes avoiding low bridges, weight restrictions and narrow lanes,” said Sarah Scothern, General Manager, Transport & Logistics at Breedon Group plc. “It also means we can give more accurate pricing estimates for delivery jobs.”
With MANTIS camera integration on most trucks, the transport team can now access video evidence remotely, immediately after incidents, using the same Webfleet interface.
“Far from being a Big Brother intrusion, the in-cab technology means we can
support our drivers better,” explained Sarah.
“With Webfleet and the multi-camera system, we can see the full picture, confirming, for example, that a driver was braking sharply to avoid a car cutting in, rather than driving dangerously.”
Matt Vass, Director of Channel and Product Marketing at Mantis added:
“Imagine the peace of mind for Breedon knowing they can swiftly access critical footage without sifting through endless hours of recordings. With our advanced camera technology seamlessly integrated into Webfleet, moments like sudden braking trigger automatic uploads, ensuring Breedon can react promptly.
“Additionally, they have the power to stream or download any footage directly from any camera memory system, free from traditional constraints. This streamlined process enables Breedon to swiftly obtain video evidence, so decisive action can be taken when required.”
The company is analysing Webfleet data to identify incidents and event hot spotsand to gain insights into the root cause of problems.
The investment has resulted in a significant insurance premium rebate in recognition of lower anticipated accident rates.
Breedon has also set its sights on improving driver behaviour, leveraging Webfleet’s OptiDrive 360 driver feedback and reporting.
“As well as setting challenging KPIs, we’re planning to introduce a driver of the year and most improved driver award, to help
keep drivers incentivised to drive more safely and efficiently,” said Sarah.
“In addition, we’re planning to integrate around 800 owner-drivers into the system, so wherever you work in the business, everyone will be measured against the same benchmark.”
Webfleet’s powerful reporting suite will be integral to the company’s aim to achieve the Fleet Operator Recognition Scheme (FORS) Silver accreditation by the end of this year and net zero carbon emissions by 2038.
“Our large fleet presents a significant opportunity for CO2 savings and is a key focus of our sustainability strategy,” said Sarah. “With Webfleet’s certified CO2 report, we can now accurately measure our CO2 emissions, confirming not just how much our vehicles are emitting, but also why and where.”
Breedon uses Fleetcare for 100 HGV vehicles transporting cement, combining Bridgestone’s best-in-class tyre range and tyre management solutions with Webfleet fleet management.
Drawing upon connected tyre and vehicle data and reporting, Fleetcare provides smarter and more predictive maintenance solutions for the company, helping to reduce its total cost of fleet ownership.
Biffa, the UK leader in sustainable waste management, has strengthened its Resources & Energy capability following the acquisition of a business that transforms residual waste into fuel.
Biffa has acquired the entire share capital of Eco-Power Green Energy Ltd, a subsidiary of Eco-Power Environmental Ltd, along with a dormant plant in Hull and seven new members of staff. The plant has the capacity to produce more than 100,000 tonnes of solid recovered fuel (SRF) pellets each year from non-recyclable household waste. SRF pellets are a high quality, sustainable, alternative to fossil fuel used primarily by the cement industry.
Biffa will recommission the plant over the next few months.
Biffa’s Resources & Energy Division also transforms non-recyclable waste into renewable electricity for the grid, and organic compost for agriculture.
Mick Davis, Biffa’s Chief Operating Officer, Resources & Energy, said: “The recommissioning of the pellet facility allows us to further diversify our capability to divert more difficult-to-deal-with wastes away from landfill and help reduce customers’ carbon footprint.
“It’s an exciting opportunity for us to develop our expertise in the alternative fuels market and could potentially be a stepping stone to a broader strategy in this space.”
Louis Calders, Eco-Power’s Group Commercial Director, said: “We are delighted to finally complete the sale. The acquisition of the business is testament to the vision, hard work and commitment of the Eco-Power team for the past seven years.
“We believe that Biffa have all the necessary expertise and resources to take the business on to the next level and we wish them every success in doing so.”
To learn more about Biffa, please visit: www.biffa.co.uk FOR FURTHER INFORMATION
The deal includes a dormant plant which will be recommissioned over the next few months
The facility turns residual waste into ‘solid recovered fuel’ pellets, a high quality, sustainable, alternative to fossil fuel
Having been established for over 40 years, Kealshore has become a
Our location in Liverpool is geographically situated in the reach of the major roads and motorways, enabling us to supply aggregate throughout the NW of England.
With over 40 years of dedicated experience in the field of earthwork, From Bulk excavation to waste management, site preparation to bulk material supply, we’re your comprehensive solution for every facet of earthworks.
Our fleet of wagons and plant machinery are fully equipped to effortlessly meet all your extensive earthwork demands.
Prepare your construction site with Kealshore’s expertise in site preparation, including land clearing, grading, and the setup of temporary facilities and utilities. We specialise in precision Reduce Level Digs, ensuring your well executed project designs.
Our Muck Away and Site Clearance services guarantee responsible waste removal, complying with regulations. For Bulk Aggregate Supply, trust Kealshore to provide construction essentials like Sand, Stone, Crushed Brick, MOT, and more – perfect for building roads, foundations, and various construction projects.
Kealshore provides construction aggregates for the needs of construction works – Products such as Sand, Stone, Crushed Brick, MOT and other materials used as a base for roads, foundations, and other construction projects.
Supplied in bulk bags or by wagon load, courtesy of our Aggregate Wash Plant facilities and fleet of wagons, we’re able to deliver aggregates conveniently and efficiently to your projects, whether it be domestic, trade, or commercial works.
K Sweep Road Sweeper Vehicles efficiently remove debris, dirt, and litter from road surfaces using mechanical brushes, vacuums, and water spray systems. These adjustable brushes cater to various surfaces.
Our regular road sweeper services prioritize cleanliness and safety, considering factors like traffic, weather, and regulations.
Aligned with environmental standards, we divert 85% of sweeper waste from landfills. Emergency cleanups after accidents or spills are also part of our services.
Bunzl UK & Ireland and social enterprise Amplify Goods, have joined forces for the groundbreaking launch of a new range of luxury washroom products.
The creation of a new brand, RE:MIND, has been designed to combine luxury hand and body care and social value, using a unique, high-quality formulation developed by Amplify Goods that uses carefully selected ingredients that are 9699% naturally-derived depending on the product. As a certified Social Enterprise, Amplify Goods donates at least 51% of its profits to charitable projects at the intersection of mental health and the environment, among many other initiatives that drive positive change in local communities.
Amplify Goods – which is based in Wimbledon, South West London - is an established social enterprise with a track record in selling net-positive washroom products to businesses looking to bring Net Zero ambitions into action within their supply chains as well as work opportunities to disabled, ex-homeless and underemployed groups.
Camilla Marcus-Dew, Amplify Goods’ co-founder, said: “Amplify Goods is proud to do things differently. The products have to be great, but we also work hard to design in a way that reduces waste, single-use plastic, and harsh ingredients whilst enabling bottle reuse, and putting more than half our profits into supporting the intersection between mental health and the natural.”
“We see this as a great opportunity for Bunzl’s various operating companies across the UK and Ireland, and their diverse customers.” added Camilla. “By the time we reach £700k turnover, we’ll likely be supporting 50-100 people a year, so imagine the impact that will have on the lives of those working on the front lines of climate breakdown.”
Simply by enjoying a washroom product, you’re jumping on board the burgeoning Social Enterprise and ESG movement and supporting both environmental and mental health projects. Thanks to this exciting collaboration between Amplify Goods and Bunzl, this can become a reality on a large scale.
“It’s this emphasis on social and environmental good in products and business practices that’s set to be the focus of RE:MIND’, said Amplify Goods’ co-founder Pasha Michaelsen ”which includes the support of the physical and mental health of ‘Quiet Changemakers’ –those working on the frontlines of climate breakdown”.
“As the founders of Amplify Goods, we know first-hand how important it is to avoid burnout - we’ve been there”, she adds. “That’s why we’re directly supporting these ‘Quiet Changemakers’ in ways they need, whilst also channelling funds into organisations working at the intersection of mental health and nature”.
Amplify Goods washroom products have been distributed by Bunzl Cleaning &
Hygiene Supplies for the past year, a relationship which has now been further enhanced with the development of RE:MIND.
RE:MIND is a first-of-its-kind partnership between social enterprise and distributor; bringing together Amplify Goods’ innovative approach to industry leading ESG product design and Bunzl’s mission to source and provide more sustainable, ethical, and socially responsible products to its vast customer base.
In this exclusive collaboration, the RE:MIND range launches as a small offering to enable all sectors to access affordable, high-quality washroom products. It includes a 5-litre Sweet Orange & Rosemary Hand & Body Wash, a 1-litre Sweet Orange & Rosemary Hand & Body Lotion, and Forever Glass Bottles
& Pumps for both the washes and lotions. These bottles can also be mounted using the RE:MIND single wall bracket or double lockable wall bracket.
The range is formulated to include luxurious essential oils and shea butter that both revitalise and nourish, with ingredients carefully selected to minimise negative environmental impact. They are Vegan Society-certified and Amplify Goods won’t work with any ingredients that are tested on animals. The products are also free from SLS (Sodium Lauryl Sulfate), synthetic dyes, and harsh surfactants. Users can rest assured that RE:MIND only offers products that are of the highest quality.
The packaging used for RE:MIND has also been carefully developed to minimise waste and harmful impacts
on the environment, with single-use plastic designed out where possible and upcycled waste cardboard utilised as a packing material. The majority of the packing processes have been considered with a view to utilising the skills of underemployed people, including ex-homeless, disabled people and those otherwise facing barriers to entry in the labour market.
Working in collaboration with Bunzl Cleaning & Hygiene Supplies, who have already adopted a similar 5-litre closedloop solution with other exclusive brands, Amplify Goods facilitates businesses in joining on their circularity journey. Through their pioneering container reuse programme, 5-litre bottles can be returned, cleaned, and refilled, reducing demands on virgin plastic and providing valuable work for people.
“Amplify Goods are the perfect partner for this collaboration; we love their ethos and commitment to purpose and we’re looking forward to the years ahead as we scale this ESG industry leading premium range” said Amy McLauchlan, Bunzl UKI Exclusive Brands Manager.
RE:MIND hand and body care products are now available from Bunzl Cleaning & Hygiene Supplies, and soon across many more of Bunzl’s operating companies across the UK and Ireland.
Elite karting is a sport measured in thousandths of a second, and drivers, engineers and mechanics will spend countless hours (and nearly any budget) to find those elusive fractions. At a recent round of the British Karting Championships, a single second meant the difference between qualifying in pole position or in 46th place. With tightly controlled technical regulations, arguably the single largest determinant of performance is tyre life. Although all drivers are on the same type, the lap time difference between qualifying in the morning and the final in the afternoon can approach one second, meaning this weekend’s race tyres are scrap by the end of the day. On any given weekend, there can be upwards of 500
drivers racing at circuits around the UK, almost all of whom will need a fresh set of ‘boots’ the following week. Many drivers race every week of a season that can extend to 35 weeks a year, meaning that the accumulation of waste tyres is vast and unmanageable without a structured and organised solution.
Twyford Recycling, through Junior Rotax driver Jack Price and his father, have begun the task of addressing this enormous and growing challenge, launching a pilot scheme with the Forest Edge Kart Club in the South East, seeking to collect and chip this waste pile efficiently and in an environmentally friendly manner.
The early signs are good - teams and drivers enthusiastically delivered dozens of old sets to the waiting van on the first
weekend - and the hope is that they can expand the initiative to more circuits across the country in the coming months. Improving the environmental credentials of the sport is a priority for the governing body, Motorsport UK, and tyre disposal remains the largest problem on the journey to a sustainable future sport. The team at Twyford Recycling, the organisers of the pilot scheme and the Forest Edge Kart Club community deserve credit for tackling the challenge head on.
To learn more about Twyford Recycling, please visit: www.twyfordrecycling.com
BlakerTech’s innovative technology is renowned and respected across not just the metal sector, but also the waste and recycling industries. Found in 14 countries worldwide, BlakerTech sets the industry standard with SandFlo™ and MagThro™, demonstrating design ingenuity and outstanding capabilities.
So, what is it that sets BlakerTech apart from the rest? Is it the rich, extensive history of this ostensibly British company? Is it their commitment to creating the very best products? Or is it perhaps their tireless commitment not just to their clients, but also to the surrounding community. In truth? It is the perfect blend of all these components that make BlakerTech the force that it is today.
Before there was BlakerTech, there was Blaker, a company well over 100 years old that began in the very heart of England. Starting life in Islington, North London, as Blaker Engineering Co. Ltd, specialising in Motor Aero and General engineering. After Mr A.A. Blaker’s Hallé Spring Wheel Syndicate Ltd won a gold medal at the Liége Universal Exhibition, Blaker continued to soar. It was even mentioned in the Daily Mail at the time:
“The first is the Hallé Wheel, the principle of which is three parallel rulers bound together with parallel links. The device is suitable for all kinds of motor work and is perhaps the most practical of all types of spring wheels that have been forthcoming so far.”
The 1930s saw the company rebrand as Blaker Specialist Welding Repairs Ltd and move to a new facility in Dial Post, West Sussex, as a new axle and chassis repair business. The second world war brought another change for Blaker as they contributed to the war effort. This included work on components for Hurricane and Spitfire plane engines, and even tank transporters and reconnaissance vehicles for Canadian Army units stationed nearby. Going from strength to strength meant a much larger facility was needed, and in the early 70s Blaker became a renowned welding and fabrication service specialising in vehicle, plant and heavy machinery repairs. Then in 2005, Blaker became part of the Charles Muddle Group, who excel in metal recycling in the South East, and made their move to the current premises in Billingshurst, West Sussex.
Separating the non-ferrous metals from dry recyclables realises a significant amount of money for metal recycling and processing plants
As the need for bespoke repair began to lessen, Blaker diversified and created BlakerTech, who are committed to the development of recycling of waste metals. Their decade long work with the waste and recycling industry, together with direct access to a live metal processing plant for R&D purposes, gave them the perfect insight to seize the opportunity to provide the sector with new technology to tackle the problems head on.
Sorting by hand, wet separation and x-ray fluorescence can, unfortunately, be problematic. Not only are they uneconomical and technical to operate, their methods can be environmentally problematic. Dust as well as contaminated water with wet treatments can lead to health problems.
Separating the non-ferrous metals from dry recyclables realises a significant amount of money for metal recycling and processing plants, on top of diminishing the growing costs that accompany waste disposal.
BlakerTech rose to the challenge and met the need for straightforward products whose process and operation remained simple, reliable and inexpensive to run. From these observations and extensive research, two incredible products were born: SandFlo and MagThro, both of which are handmade at the BlakerTech facility in West Sussex. The optimum process for the metal recycling plants is:
After magnetic separation of any residual ferrous material, mixed crushed scrap from a fragmentiser is screened to improve its uniformity. Non-metallics are removed using the MagThro eddy current separator and the mixed nonferrous metals are then fed into the SandFlo’s annular trough up-stream of the fluidised bed separator.
The MagThro with its eddy current technology is probably one of the most efficient in the marketplace. Despite this, BlakerTech has reliably kept its operation basic, and user friendly. Simple in its design, the MagThro is easy to maintain and highly efficient making it an excellent return on investment.
“That’s the idea behind it,’ says Robin Plater. ‘It’s remained pretty much unchanged for the 20 years since we first created it. As well as making the MagThro, BlakerTech also makes the equipment that feeds it. We make the framework, meaning we are able to create a bespoke design fit into a customer’s premises. For BlakerTech, it’s not a simple matter of installations, it’s about ensuring the customer gets exactly what they need.”
Made from high-grade components, the MagThro is fitted with 12-pole magnetic shafts and is made from exceedingly high-grade components. The high-performance Neodymium rare earth magnets are what create the continuous and strong magnetic force that reliably and efficiently separates the non-ferrous metals from mixed materials. Using a two or three-way splitter (subject to the client’s needs), the matter is then sorted through outfall streams into waste, fine/ smaller or larger non-ferrous metals.
Several areas of the framework are designed to facilitate fitment of service platforms. Hinged panels can provide quick access for routine maintenance. Standard belt widths are 500, 750, 1000 and 1250mm, and the main belt is fully adjustable and can be replaced without disturbing the rotor. The fully-adjustable eccentric rotor allows the separation and magnetic force to be altered as necessary to enhance recovery, which is protected from foreign objects by a sealed motorised drive drum and the conveyor belt is driven by Van de Graaff geared drive drums. Quality SKF or Nachi bearings are used for a high quality and smooth performance. Non-ferrous materials are evenly distributed onto a conveyor, which passes over the MagThro. The spinning rotor throws the non-ferrous metals (further than waste materials) into a splitter target, sending the sorted waste and non-ferrous metals downstream to their respective destinations. The MagThro has an eccentric rotor which can be adjusted to alter the separation/ magnetic force. Ideally, small fragments of non-ferrous metals, screened to 50mm, can be further refined by BlakerTech’s SandFlo system.
• Cost effective with high recovery performance
• An environmentally-friendly dry process
• Designed to operate in heavy industrial environments
• Multiple width options for tailored recovery applications
The SandFlo is completely unique in its design and is a dry operation separator. Its fluidised-bed system is perfect for the separation of secondary metals and minerals based on their density. It is low cost and highly efficient. It also has nearly zero emissions and absolutely no by-products. Unlike wet separators, the dry fluidity system creates no effluents, which are difficult and costly to treat.
Dubbed as ‘witchcraft’ by Robin Plater, BlakerTech’s Commercial Manager, the SandFlo’s technology has never been replicated or copied, and can be found in facilities all across the world due to its unique and easy to use design. Known to be highly robust, the SandFlo is a long-term answer to a metal sorting quandary.
“Because it is so unique, nobody else has actually been able to copy it,” explains Robin. “It’s an aerated sand pit, and then it vibrates. It’s a circular dish, and in one part there’s a trough that goes all the way around. This dish vibrates at such a high frequency, the sand travels around in a perpetual circle. There’s an air bed underneath which blows air through the sand. So, if you touch the sand with it turned off, you could liken it to walking on a wet beach, as it will be compact, and you won’t move through it. As soon as you start to vibrate and turn the air on, you would just sink, like dropping into water.”
As the scrap is carried across the fluidised region by the continuously circulating sand, the less dense materials (aluminium and magnesium) remain near the surface and are conveyed out of the sand by an inclined perforated flight, fixed across the width of the trough. The heavier metals (zinc, brass, copper and any residual stainless steel) sink deeper as they travel through the fluidised zone and are conveyed out of the trough by a second lower perforated flight, downstream of the fluidised zone. The sand particles pass through the perforated flights and end up back at the feed point, re-circulating continuously around the annular trough.
Summary
• Cost effective with high recovery performance
• An environment-friendly, dry process with no contaminated effluent to treat
• A proven, commercial solution for upgrading nonferrous fragmented scrap
• Contaminated sand can been sieved / cleaned
• Requiring a single operator, the SandFlo can process 2-2.5 tonnes of material per hour
• By saving costs on manual pickers, SandFlo typically pays for itself in 18 months or less
Both products and associated accessories are handmade in the UK at BlakerTech’s facility in the South East of England. BlakerTech also provides full installation, training and support.
For more information, please contact robin@blakertech.com or call 01403 783634 Or visit the website, www.blakertech.com
Known to be highly robust, the SandFlo is a long-term answer to a metal sorting quandary.
Fires in MRFs are very much a fact of life in the recycling industry. The problem has only become worse with lithium-ion batteries and shows no sign of improving. This is very challenging for operators who have a high value recycling facility which they need to protect.
Keith Picton of Blazequel shares ways to make MRFs safer from the risk of fires.
A fire in your process line can be transported through your entire facility in seconds. That’s why effective process protection is so critical for ensuring your business continuity.
Take a typical MRF for example. Without rapid and effective detection, a fire risk such as a battery can be carried all the way from the primary shredder through your process in minutes (or seconds depending on the process speed), moving the fire risk from one part of your facility to another.
En-route, this fire risk could start multiple other fires as the material is separated into different fractions. For example, if a sparking battery has ignited some paper or cardboard this could end up in one bunker, whilst the battery continues to the heavies rejects or ferrous bunker. Perhaps too, a spark has been drawn into the dust extract system from a transition point.
Suitable detection and suppression is essential to prevent a fire being carried through your MRF with potentially devastating consequences. Here are some methods to make your facilities process lines safer, both by design and with automatic fire detection/ suppression systems - and some of the pitfalls to look out for.
There are plenty of excellent fire safety systems on the market, but good fire safety starts with good design of your process. Obviously, process design is very subjective and varies significantly with different material types and the commercial purpose of each facility. The following refers best to mixed wastes such as MSW or C&I material - where batteries, aerosols, gas cans, BBQ’s and all kinds of other ‘surprises’ may be mixed into the incoming material.
Firebreaks in your process:
Having witnessed various processes in operation and learnt of many fire-saves, I have become an advocate for having ‘firebreaks’ in your process. Firebreaks are simply any location in your process that can ‘store’ material as part of the process flow, for example:
• Dosing Bunkers (also known as metering drums)
• Feeding Hoppers
• Buffering Tanks
• A slow-moving incline / chain conveyor
• Or even just a loose waste storage bunker, from which processed waste is manually loaded into the next processing stage. (See Example 1, Concept 2.)
Benefit 1 Slow down your process, allowing material to self-quarantine. The benefit of a firebreak is simply that it can slow down the process after a high-risk activity, allowing material time to self-quarantine. And, if there is something ‘thinking’ about causing a fire (like a damaged battery) it can do so in this controlled and protected area. If something in your material is likely to cause a fire, it’s best that the fire occurs in an area that you have good risk controls over.
Benefit 2 Allow for safer controlled shutdowns of your process in the event of a fire.
Furthermore, firebreaks in your process may also allow you to run the ‘upstream’ conveyors and equipment clean into the firebreak zones in the event of a fire alarm and halt the process via a phased shutdown of equipment. If avoidable, it’s best not to have unprotected conveyors sitting with a load of combustible material on them in the event of a process-stop.
Benefit 3 Cost efficiency, allowing you to locate fire protection systems in the highest risk points.
It also allows you to position your fire protection systems in the locations where you are most likely to suffer a fire. It is rarely economically practical to install fire detection and suppression on every part of your process.
Firebreak Examples:
This simple graphic is a classic example of how we have used firebreaks before at other sites. This is after the primary shredder which is one of the highest risk locations at a waste recycling facility.
Simply by shredding into a dosing bunker (which in turn feeds the rest of the process), or by shredding onto the floor (from where it is loaded into a feed hopper by another grab), these sites have isolated the location of many fires, which could otherwise have been much more serious.
Diversion points in your process: All too often, fire safety is one of the last things to get designed. However, if you start to think about fire safety when you’re actually designing your plant you can even design some simple measures to clear fire risks out of your conveyors, and into a dedicated skip/ bunker. For example – by using detection inputs to your PLC with a bi-directional conveyor you can prevent fire risks from being stuck on your conveyors, and safely discharge ‘suspect’ material into a quarantine area. This is just another reason why we believe you should start talking to your fire protection consultant at the same time as you’re starting to design your new facility!
There are two main types of process line detection systems - flame detection and ember detection. Each method has its strengths, and a combination of both methods is often the correct approach.
Flame detectors are commonly used over high risk process points. Common install applications include shredder hoppers, highrisk conveyors and bunkers. However, they will not detect a threat unless there are visible flames. This is where ember detectors (as illustrated) are essential.
Choosing the right flame detector:
Not all flame detectors are created equal. Some flame detectors can take 5-10 seconds to activate - that’s no use on fast moving conveyors, where your risk will be in the next stage of the process by then! At Blazequel, we use flame detectors with an instantaneous response speed to detect fast moving fires and explosions.
Additionally, your flame detector won’t detect anything if it is covered in dust. There are two ways to protect against this:
• Ensure your flame detector can perform a ‘though-the-glass’ self-test periodically. Without the detector being able to selfverify the lens cleanliness, you have no certainty that your detector is actually in a working condition.
• Install an air-purge onto the detector lens, creating a wall of positive air pressure in front of the lens - this prevents dust and debris from obscuring the detector over time.
Ember detectors are much more sensitive than flame detectors. Monitoring your conveyor belts for hot particles such as tramp metal, faulty batteries and smouldering material, they are uniquely designed to detect fire risks in
transit (moving at up to 6m per second). This makes them extremely effective on high-speed conveyor belts. Such rapid detection allows them to contain a potential risk and reduce the threat to your facility.
Choosing the right ember detector: Ensure you don’t have issues with your ember detector performance by verifying:
• What temperature range does your detector operate over? Don’t confuse an ember detector with a spark detector. A spark detector works at a much higher temperature range and senses the light emitted from a spark or glowing object, rather than just the ‘black’ heat emitted from something suspiciously hot - which a true ember detector can identify.
• Air purge on the lens is often critical. If your detector is dirty, it can’t see anything.
• What is your process speed? Ensure it is within the operating range for your detector.
• If your conveyor has a heavy ‘burden depth’, it is still possible for a fire risk to be obscured under a layer of material. That’s why it’s often wise to have multiple detection points on your process.
A tale of two “fire-saves” –ember detector case studies: Here’s why detecting hot particles is so important...
In one case, an ember detector on a dosing bunker outfeed spotted a 18v lithium-ion battery which was sparking off just before it entered the plant. Our system detected the risk, stopped the process and deluged the risk area with water mist to neutralize the risk. Flame detectors over the dosing bunker didn’t see this risk, as there were no flames at this stage.
In another scenario, our ember detector on a shredder outfeed spotted a ratchet strap which had become tangled and crushed on the shredder drive shafts, with the friction creating a lot of heat. The detector spotted the hot object and stopped the belt, preventing it from being discharged onto a large pile of shredded material.
For the protection of process line risks, we recommend the use of water suppression. There are multiple terminologies used for these systems (deluge, water spray, water mist, spark suppression) and different flowrates or design principles applied. Fundamentally, the principle is the same - get water onto the fire FAST, by means of a set of fixed pipes and open spray nozzles across the risk area. In the event of a fire, the control valve is opened to allow water to flow from all the spray nozzles simultaneously.
Each system needs to be engineered for the specific application, considering for:
• Extent of suppression coverage required.
• Worst-case flow rate and water storage required.
• Dual power supply to pumps if appropriate.
• Monitoring of any critical failure points on the pumps and critical valve positions.
Stopping the process is a key part of containing fires on process lines. Once a fire has been suppressed, the area should be a manually checked to ensure that the risk is safe before starting up again. This is more important than ever now with the presence of lithium-ion batteries in the process which could suddenly reignite without warning. When setting up your process stops consider:
• Do you want to raise a general fire evacuation at the same time – or is a phased alarm more appropriate, allowing site operatives time to investigate then escalate to a general evacuation if necessary?
• Do you want to E-stop all the process simultaneously, or have a phased shutdown to minimise downtime when starting the process up again?
• Similarly, it may be wisest to allow any conveyors ‘downstream’ of the detected risk to continue to run for a timed period – clearing the belts of flammable materials and risks.
As you’ve probably guessed by now, process line fire protection is a complex and very bespoke exercise. No two processes are the same, thus every plant requires its own risk assessment and approach.
If you’d like to discuss your process requirements with our team, you can contact me on keith@blazequel.com or 01234 357357.
We look forward to helping you make your facility safer!
Customised Usage: Collect only what you need, from 0.25m3 upwards
Recycled Materials
Rainwater Utilisation
Efficient Transportation: Small vehicles for collection/delivery, minimising emissions
Handling
Lifting
It’s no secret that the construction industry has had a rocky past when it comes to going green (that was a terrible pun, I apologise). The issue of construction waste generation isn’t simply a UK-wide problem, but a global dilemma that has left the industry in a bind.
According to Qflow’s (the sustainability data app) latest report in 2023, “the construction industry generates 62% of the UK’s waste and 32% of all waste sent to landfill. Diversion from landfill is sitting at 87% – but with 13% of all construction waste going direct to landfill, this is far below the 99% target.”
The impacts of improper disposal can be severe, leading to land, water and air pollution as a consequence, not to mention the green house gasses produced as a result of landfill. And the negative effects are not simply environmental. The Waste and Resources Action Programme (WRAP) reported that an estimated £1.5 billion worth of materials was wasted in the UK alone back in 2017. It also revealed that only 48% of construction waste in the UK is currently being recycled, which means we have a long way to go in terms of improvement. The UK government previously set a target to recycle 70% of construction and demolition waste by 2020, and statistics are still needed to see how successful that has proven.
So, what can businesses do to help action change?
Materials must be properly sorted and segregated to ensure they are then sent to the correct place for reuse and recycling. Materials such as metal, concrete and wood can not only be recycled for other use, but also directly reused in new construction projects, meaning that the need for brand new materials will diminish. It is also important to salvage as much as possible from demolition sites to contribute to waste reduction. Business owners should collaborate with waste management companies to ensure proper disposal and recycling of construction waste.
This is absolutely crucial in order to reduce the environmental impact of construction waste. Nowadays, there is a large number of better impacts options. These include (but not limited to) recycled materials, low-carbon concrete, and sustainable timber, all of which are viable alternatives that have a lower carbon footprint and help mitigate environmental damage. It is the responsibility of the business owner to seek these options and make this change for the betterment of both their business and the environment.
Developing a waste reduction plan is the first step towards effective waste management. This plan should include accurate material estimation, efficient procurement practices, and waste reduction targets. By carefully planning and monitoring the materials used in construction projects, businesses can minimise waste at the source. Data apps can be a great way to do this, and there are many out there in the mix that properly report and calculate all such data.
It is imperative to adhere to waste management regulations, and the best way to do that is to work with licensed waste management companies. Not only are businesses themselves then taking responsibility for proper disposal, but it means that once it leaves their site it will be in the hands of another company who wants the same. Either way, owners should familiarise themselves with both the legislation and procedures, as well as ensuring proper documentation of all waste disposal activities.
In order to work most effectively, collaboration between construction companies, suppliers, and waste management stakeholders is vital. Sharing best practices, exchanging knowledge, and developing innovative solutions collectively can lead to a more sustainable construction industry. Business owners should actively participate in industry initiatives and engage with their peers to promote sustainable waste disposal practices.
This is summed up perfectly by Co-Founder and CEO of Qflow, Brittany Harris:
“When we started this analysis, we knew it was going to highlight some pretty shocking practices, but I wasn’t prepared for this level of non-compliance! As an industry, construction consumes over 40% of the world’s raw resources and accounts for over 40% of landfill waste.
“Without good data on what’s happening to all this waste, we don’t have a chance of reducing it or improving material reuse and recycling.
“We hope that with the insights shared today, and by helping the industry get better data far more easily, we can work together with the regulators, industry bodies, developers and contractors to really transform construction from a linear and wasteful industry, to one that is circular and low carbon.”
Since 2007, Enduramaxx has being supplying England with the very finest of water tanks to support a variety of individual needs. For 17 years, they have continued to develop and seek new ventures in water waste, including rainwater harvesting.
Starting life in England’s South Coast, Enduramaxx began its journey in Portsmouth, the brainchild of Mark and Kate Gilbert. Still a family business, the board of directors has now welcomed Chester, Sales Director, and Peter, Operations Director. As the business grew, so did the need to move to another site. Given that everything is not only manufactured on site at Enduramaxx but also shipped out from there, it was clear that this thriving company had outgrown it’s southern site. With it’s sights set on a more prominent and central location, Enduramaxx moved to Peterborough in 2012.
With the first (STP 5.5m) rotational moulding oven up and running, the second was not far behind and made its debut in 2015. When the time came for a third to follow, it was clear that Enduramaxx had boomed into an even bigger operation. It was time for another move. Only this time, it wouldn’t be travelling far at all. Right at the end of 2020, the site directly opposite was purchased, giving Enduramaxx the brand new south side. South side became the centre for dispatching along with all alterations and final fits, and the North side remained the centre of production.
At the core of the company, is a family; a family with an ethos to keep thinking big and keep growing. With 67 employees, Enduramaxx is bigger than ever: a stalwart, thriving centre of production.
Enduramaxx make tanks in a range of sizes, from as little as 60L all the way up to 30,000L, so whatever the need, there’s a tank for that. All but one of the tanks is made on site, in Peterborough, and shipped out in one of their nine trucks all over the UK.
“Enduramaxx is proud to be a part of the ‘Made in Britain’ initiative, and investing in one of our plastic tanks is a direct investment in British manufacturing. All our tanks are constructed from either medium-density polyethylene (MDPE) or Polypropylene (PP) ensuring a robust and resilient tank fit for the product it contains.
“Our tanks are rotationally moulded at our factory in Lincolnshire. This method involves filling a heated hollow mould with a precise weight of polymer, followed by a slow rotation process. The result is a robust, long-lasting, and UV-stabilized tank that can provide many years of service, whether installed indoors or outdoors. Additionally, we source accessories, including fittings, flanges, and filters, to complement our tanks.”
Enduramaxx tanks and their uses fall into 3 main categories:
• Water Storage
• Rainwater Harvesting
• Chemical and Industrial
At the core of the company, is a family; a family with an ethos to keep thinking big and keep growing.
There are so many sectors that require good water storage systems, none more so that agriculture. In the agricultural field, a wide variety of tanks are needed for endless tasks, be it general water storage to liquid fertilizers and pesticides. Traditionally, it was steel or aluminium tanks that were used, though they certainly come with their setbacks. It’s best to look at each individual case and assess which tank is best suited for which application.
Steel tanks have been used the longest as they’re considered to be very dimensionally stable and safe, meaning they can be utilised for a wide variety of liquids. Despite this, and their large capacity and use above or below ground, a major disadvantage of steel tanks is their high weight, even if they are empty. That and the inherent risk of rust, which should always be taken into account. The moment rust sets in, contamination and leaks become an imminent problem. Regular inspections are necessary to maintain proper care.
Tanks made of aluminium are also sometimes used as they’re a relatively low weight compared to steel tanks. Aluminium is a soft metal, so it is subject to faster wear and doesn’t have the properties required for the transport and storage of food.
Plastic tanks, on the other hand, are suitable for many purposes and have long had a permanent place when it comes to safe storage or transport of water and other liquids. As a water container, they are generally suitable for liquids up to a density of 1.2 kg / L; plastic containers for liquids with a higher density, such as liquid fertilizer, molasses, glycerol or iron chloride, are usually designed for 1.4 kg / L. Plastic tanks are therefore extremely versatile and optimally designed for so many different tasks, just like steel, except they don’t come with the same issues of rust and weight. Modern plastic tanks prevent the formation of algae in the stored water even when the tank is outdoors. And given that plastic tanks can also be made completely opaque, it’s easy to check containment levels. Plastic tanks are light compared to other materials used making them easy to use when setting up or for mobile water bowsers.
Growing ever popular, rainwater harvesting is prevalent both domestically and commercially as not only will it save the consumer money, but will also make a huge environmental impact. For example, every millilitre of water that falls across a square metre gives you one entire litre of water in return! Think of all the many uses non-drinking water can be used for! Enduramaxx Rainwater Harvesting Tanks are designed for both domestic and commercial applications. Known as vertical storage tanks or water storage tanks, they provide the water storage element for Rainwater Harvesting Systems, and come in 40 sizes, ranging from 150L to 30,000L. All the tanks are made from one-piece, rotationally moulded medium density polyethene, which means minimal installation and assembly costs compared to traditional, sectional metal tanks, and are available as either above or below ground systems. The Enduramaxx rainwater harvesting filters prevent rubbish, moss and leaves from entering your rainwater harvesting tank, and are available as a basket filter or self-cleaning filter. Whatever you need, there is a filter to suit every roof size whether it is a domestic house, an agricultural barn or a commercial factory.
1) Agricultural
Harvesting from grain store, livestock and machinery shed run off e.g. for filling sprayer tanks with natural soft water, for pressure washing, for dairy wash down, for livestock watering.
2) Commercial/Industrial
Harvesting from commercial /industrial buildings to delivery greywater systems for flushing toilets and a number of applications for washing and cooling
1) Garden Watering
Above and underground water tanks fitted with a pump and filter can provide water supplies for dry spring and summer months.
2) Car Washing
A hosepipe will use around 10 litres per minute when washing the car, while a domestic bucket may hold 15 litres of water. A full 800 litre slimline home and garden water rainwater harvesting tank would wash a car approximately 8 times!
3) Filling Ponds & Other Garden Features
Chlorine-free rainwater is softer than mains water and kinder to wildlife.
4) Flushing Toilets
The most common use of rainwater is for toilet flushing. Toilets can use up to 13 litres per flush with modern ones using as little as 4 litres. Depending on the usage, the average person in the UK could flush over 30 litres down the toilet every day, which can soon mount up in households.
5) Clothes Washing
Harvested rainwater is excellent for washing clothes in hard water areas. Naturally, soft rainwater will use less detergent and prevents the build-up of limescale prolonging the life of the washing machine.
Modern plastic tanks prevent the formation of algae in the stored water even when the tank is outdoors. And given that plastic tanks can also be made completely opaque, it’s easy to check containment levels.
As they are lightweight, cost-effective and erosion resistant, Polyethylene and Polypropylene tanks are often used for chemical storage. Enduramaxx plastic storage tanks are manufactured to hold liquids with a specific gravity of up to 2 SG and are also available in 25 sizes, ranging from 50L to 30,000L. As they need to fulfil a variety of functions, these tanks are strong and non-reactive to be able to house the chemicals they contain.
“Therefore, when selecting a storage tank for a specific chemical, it’s essential to consider various factors such as the specific gravity of the chemical, the chemical composition, storage temperature, pressure, potential interactions between the chemical and the tank material as well as the type of fixtures and fittings required. Taking all these factors into consideration, the knowledgeable team at Enduramaxx also consult the Material Safety Data Sheet (MSDS), to advise on the best tank solution. Enduramaxx strongly recommend that you always prioritize safety and adhere to HSE advice when selecting storage solutions for chemicals.”
Plastic chemical tanks are manufactured with lifting lugs, overflow, inlet and outlet locations that can take up to 150mm fitting(s). Tanks can be specified with additional bulkheads, welded flanges and more.
Bespoke and specialist tanks are also something that Enduramaxx are proud to offer. Whether vertical, open top, cone bottomed or food grade, Enduramaxx tanks can be manufactured for a wide range of uses from tanks for aquaculture and foodstuffs to compost tea, brewer tanks, flocculation tanks and v-notch weir tanks. Tanks for acid picking, dipping tanks, brine tanks, settlement tanks and plastic silo tanks for granules and liquids as well as tanks for dispensing or mixing. As all Enduramaxx plastic rotationally moulded tanks are constructed as a one-piece moulded tank with no joins or seams, and they are UV stabilised to withstand many years of outside use. They can also be made in black, blue, natural, and dark green.
Remove DIRT & WATER in the same mobile application
Affordable and easy to change out replacement cartridges
Kind to the planet – as a natural, sustainable product
Save waste costs, replacement value and labour
Simple ‘plug and play’ application
Site permanently on a problematic machine or on a rotational cleanse across your fleet
Free on-site trial..
Whether it be to tackle one off contamination issues, or as a permanent fix to heavy use equipment to protect pumps, valves & cylinders etc.. or as a rotational cleanse on off-hire equipment.
KLEENOIL offer a completely free trial at your site ; with before and after independent oil analysis.
The power of social media is truly unmatched. Let it be known, dear readers, that my personal TikTok is not inclined towards my work subjects in any respect. It’s filled with ridiculous memes, Mads Mikkelson edits and horror book recommendations. Oh, and RSPB’s Bird of the Week segment. But waste management? Not a chance I’m afraid.
Then, low and behold, I was up early one morning (a rarity, it must be said), and came across an advert for Loved Before Ltd. Instantly, I was completely captivated, and ended up scrolling through their entire page to learn everything I could about the incredible work Charlotte Liebling and her team do; meet and greets with the new arrivals, a plethora of hilarious memes and the faces of the brand new owners of abandoned teddies had me writing an email asking for an interview through a veil of happy tears. Thank goodness that emotional mess wasn’t conveyed because Charlotte was gracious enough to say yes that very same day!
So a small warning for anyone reading this that attaches narratives and personalities to their teddies; this heartfelt enterprise will bring a tear to your eye. And it’s absolutely worth it.
Right, so what got you started on this venture? Where did the inspiration come from?
I was actually spending time volunteering in a charity shop, and I started to become very aware that a lot of people were bringing in stuffed toys as donations. The moment the doner handed them over was often really emotional! These toys held so much sentimental value, and honestly the process kind of broke my heart. These toys were either thrown into a box and sold for 50p or they were (unfortunately, because charity shops are just so overwhelmed) simply thrown away. As someone that has a real affinity for my own stuffed toys I couldn’t shake the image of them in landfill. I went home and sat up all night, covering the walls in post-it notes, trying to figure out how to save them. I knew I had to do something. Through piecing together the bits of research, I realised how many millions of stuffed toys were ending up in landfill. Then the moment truly hit me… this is it; now’s the time to launch this. I’m going to rewrite the rules. I’m going to change how we feel about these used toys; how we perceive them. I’m going to make a difference. And here we are!
It’s fantastic! Honestly, I’m one of those people. I remember my mum giving all my old teddies to a school tombola and it broke me! I know I’m 30 years old, but they have names and feelings and what if they miss me?
Don’t worry, I’m exactly the same. You’re in good company.
So how did the process get started? How did you take it from this mad idea and a room filled with post-it notes to what we see today?
So, at the very start, I worked to pilot it for couple of months with this charity. It was about offering donors a different option and seeing how much interest it gained. Once it got traction, I sat down with the charity, and we decided to kind of move away from each other. I wanted to set this up as a business, where I could still support charity (as we’re linked with MakeAWish) but it was time for it to be its own thing. I’m very much grateful to the charity though.
And how did you grow it from there?
It wasn’t easy. I probably had £5 to my name. So, then it was a case of working out, how do I turn £5 into £10, and then £10 into £100, and £100 into £1000 and so on. It started with an Instagram, which I set up and realised that if this was going to be successful, I needed to build a community before I built a business. After that came the website, designing packaging, how it would be sustainably manufactured… We’ve done it all ourselves, working it all out piece by piece. I still feel like I don’t really know what I’m doing!
It sounds like such a labour of love. Your brainchild has just grown and grown! I guess when most people come into a business, they deal with one specific area. But when you start a business, you have to do everything. It was a risk; I tell you that! We didn’t even have the toys either. I had maybe ten in a box which the charity had left me. And I work full time that’s another thing. I’d just started an internship when I launched Loved Before. I spent my nights brainstorming, posting leaflets through people’s doors on my weekends, going to charity shops to speak to them… it was a very, very intense period of my life. Not that it’s any less so now! Crikey! You’ve really got to believe in what you’re doing to do that full time. Starting a business is effectively a full-time job, whilst actually also working a full-time job. All credit to you, that’s incredible. Thank you. I really appreciate that. What was the exact launch date for Loved Before Ltd?
Actually, it’s a slightly blurry timeline, but we officially became a business at the very end of 2019. We did then have a bit of a break to rebrand after the initial working out. I realised I needed to rebrand it. I needed to come back and turn it into a proper thing. But I had the idea before that, while I was in my second year of university, working in the charity shop. Properly, I’d say we’ve been around for four years.
And you’re in Selfridges now, is that right?
Yes! Selfridges in London, Birmingham and Trafford. That’s huge! Is a lot of your client base from Selfridges? Or is it more online? I know your community obviously started in social media. So, is it still very online? Or has it gone more person to person?
It’s pretty balanced at the moment. This year, online, we have sold out within an hour or two of restock every single week, which has been amazing. You ride waves of viral social media so it goes up and down, but online is very strong. And in person, we did a pop up at Selfridges Christmas of 2022, and then a pop up in London for six weeks and we all realised, okay, customers really love this! So, then Selfridges invited us to have a more permanent space in London, in Birmingham and Trafford. Things are looking really good, especially when we have a video that goes viral, or something like. We’ve had a couple of instances of them selling out in store as well, which has been incredible.
And it all started from crazy post-it notes. I know, it’s still very strange to me.
I’m guessing it started a little bit more from this emotional attachment many of us have to our toys. I mean, who didn’t sob at Toy Story Three? I know I did.
Me too! But you’re also helping to reduce landfill by a quite significant amount… The emotional side is one part but you’re right, the sustainability is equally powerful and motivating to me. In the UK, over 8 million stuffed toys end up in landfill each year! Which is absolutely insane. Then on top of that, manufacturers are still producing millions of toys. Think of the greenhouse gases and water consumption of all of those things that go into producing them, when probably the 7 million of those 8 million in landfill just need a bit of love. It’s just a no brainer to me that this is where the industry needs to go. We’re starting to work with other brands to help drum the message into them so that they can close the loop a bit more with our support. I think people are starting to get that this is where it needs to go.
Absolutely. We’re in the age of saying of reduce, reuse, recycle. And historically we had ‘make do and mend’. It’s an important mindset that manufacturers seem to ignore.
Well, that’ll never stop, but there is this climate for giving old things a little bit of love and selling it that way. And I want to work with as many partners and manufacturers as possible to work out how we can help them individually extend the life of their toys, and then help their customers have somewhere to properly part with them. I think for me, it’s beyond trying to save a few toys from landfill and what we can do on a small scale. Recycling is incredible, but what we’re trying to do with Loved Before is that bigger mindset shift. I always say, what you can teach a child through the medium of a teddy bear with Loved Before is more powerful than simply throwing your plastic in the right bin, because you’re telling them, and teaching them, with this one item that something used can easily be loved again. And actually, it doesn’t lose its value. If anything, it gains value just by being loved.
So, let’s implant that thinking into future generations to make a real, proper difference.
That way, the shift in mindset starts from the ground up, doesn’t it?
Because if you’re teaching the kids, they take that mindset and they grow with it. And like you say it, it’s an emotional issue, and looking after the planet should be an emotional issue. Absolutely. And that’s easily said through the medium of something as personal and lovely as a teddy bear.
I still have my stuffed bunny from when I was a kid. He’s reused forever!
I can’t get rid of him.
I have the same! It’s an amazing thing to push for, not only from a sustainable point of view, but to know that these things that we do get emotionally attached to, get another life. They get to have a different name written on the underside of their boot, so to speak.
Big question is, what’s the next step for you? I know you have these amazing ideas, so there’s got to be something in the pipeline?
There’s a few things that are next on the horizon. Getting some more retailers under the belt would be incredible. Really, the next thing involves global steps. We ship internationally as well as receive donations from all around the world. But in terms of carbon footprint, we don’t want to forever be operating solely from the UK and have people sending stuff. We want to encourage them to interact with the brand, and right now, they can’t do any other way. There’s a big demand for it, particularly in places like the US. We were in the Washington Post recently! But to stay on the sustainability side of things, we need to set up operation in places beyond the UK. A US hub would reduce the potential carbon footprint massively. We also want to start setting up our own spaces and stores eventually, probably a bit further down the road. But then we can offer additional services, like our teddy spa. At the moment, we use it to wash our toys that go out the door, but people very much ask to be able to send their toys to it.
They don’t want to give them up, just want them to have a clean, repair or refresh kind of thing.
I think a teddy spa might be the cutest business idea I’ve ever heard of.
It’s a winner, right?
I certainly wouldn’t bet against you. Everything you’ve achieved these past few years is an incredible feat.
Thank you. The support we’ve had has been amazing! I mean, don’t get me wrong, the Internet is a horrible place. Even I get trolled every now and again…
How would you be trolled?
You’re doing this lovely thing and people troll you?
They take a jab at the charity we work with or attention seeking, blah blah blah. If anything it’s entertaining.
At least you look at it that way, and can keep your head held high over the amazing work you’ve done.
Thank you. I really am so proud of it all.
IFAT Munich is once again presenting itself as a launch pad for innovative young companies in the environmental technology sector. From May 13 to 17, 2024, they will be presenting themselves to international experts in the Start-up Area, on the Green Stage, and on special guided tours.
“While startup activity has slowed down in other sectors of the economy, the dynamism of the startup scene in the environmental technology industry remains high,” says Stefan Rummel. The CEO of Messe München attributes this primarily to the longterm, existential importance of the topics dealt with.
“Solving global environmental problems – such as climate change and its consequences, polluted seas and water shortages, or growing mountains of waste and dwindling natural resources – is one of the major challenges facing humanity and offers virtually unlimited scope for innovative ideas and new business models,” Rummel is certain about that.
Consequently, young companies will once again be given a broad forum at IFAT Munich 2024. From May 13 to 17 of this year, the world’s leading trade fair for environmental technology will once again feature a Start-up Area in Hall C4. Around 50 young companies from over 15 countries will present themselves in the separate exhibition area. Among them will be, for example, the Norwegian company Renasys, which aims to revolutionize wastewater treatment with a new type of mechanical filtration.
“Our process offers unprecedented high flow rates for filtration levels from 40 down to 5 microns,” explains Christopher Sveen, Co-Founder and CEO at Renasys, and continues: “We are not only achieving outstanding efficiency in particle removal, but are also pioneering the recovery of resources, for example, organic matter from municipal wastewater or minerals from mining.” His aim is to forge further long-term partnerships at IFAT Munich in order to jointly tackle some of the world’s most pressing ecological challenges.
IFAT Munich 2024 also marks the market entry of Solar Materials. The Magdeburgbased startup has set itself the task of using its patented technology to completely recycle solar modules. “Not only glass, aluminum and copper are recovered, as has been customary in the industry to date, but also the critical raw material silicon and the precious metal silver,” explains co-founder Dr. Jan-Philipp Mai.
According to him, this added value reduces recycling fees for customers such as solar farm operators and module manufacturers. The company currently has an annual recycling capacity of up to 150,000 modules, which should already have been expanded to 500,000 modules by 2025.
At the moment, the plan for Metycle, a young company founded in Cologne in 2022, is to become the “world’s most efficient and trusted marketplace for secondary metals.” The digital platform enables sellers and buyers to trade in all types of metals and mixed metals. Metycle manages the entire trading chain so that scrap dealers and metal collectors don’t need to contact recycling companies and smelters themselves. The respective parties to the transaction can track the supply chain online in real time.
In addition to visiting the exhibitors in the Start-up Area on their own, trade visitors to IFAT Munich 2024 can also join guided tours. In the afternoon, from Monday through Thursday, selected companies in the special area will be visited with an expert guide.
As an additional information and networking offering, the Start-up Area will also include an activity area called “Green Stage” for exhibitor lectures, presentations by associations and partner institutions, and scientifically oriented discussion panels. On the mornings of the first four days of the trade fair, the program will include two hour lecture and discussion blocks on topics of particular relevance to the startup scene. The example of automated dismantling will be used to look at the end of the linear economy and the opportunities for industrial collaboration, while current approaches for an optimized circular economy will be presented and discussed based on the construction sector. Other focal points will be the technical implementation options from the bioeconomy and cooperation between startups and the public sector.
More startups on the rest of the exhibition grounds
“With the Start-up Area, we are making it easier for young companies to access the market, and offering a concentrated space for the startup scene, but of course there are also many more exciting newcomers among the other exhibitors in our 18 halls and the outdoor area,” as Philipp Eisenmann, Exhibition Director of IFAT Munich, stresses.
WeSort.AI will be there for the first time and directly as the main exhibitor in Hall B5, Stand 124. Founded in 2021, the Würzburg-based company has developed from a promising idea into a respected player in the recycling industry within just two and a half years. Specializing in the granular analysis and sorting of waste objects using artificial intelligence (AI) and object recognition, WeSort.AI is revolutionizing waste management.
“With our solution, we are opening up new fractions and achieving previously unattained levels of purity,” explains cofounder Nathanael Laier and continues:
“A highlight of our technology, the ‘BatterySort’ product, makes a significant contribution to fire prevention in sorting plants. We will also be presenting it in a lecture at IFAT Munich on the Green Stage.” The technology is already being used successfully by various recyclers in Germany, and further AI analysis and sorting machines will be installed in 2024. The example of Greyparrot shows the outstanding development that former young companies can achieve. The British company presented its innovative system, which uses AI and machine learning to optimize the waste sorting process, at the last IFAT Munich in 2022 – back then still as part of the Start-up Area.
Greyparrot will be back in Munich again this year, but this time as a “regular” exhibitor in Hall B4, Stand 137. “Over the past two years, we have made massive progress in many areas – from the expansion of our waste recognition library to more than 70 categories, and the installation of over 100 Greyparrot analyzers in 14 countries, to our recently announced strategic partnership with Bollegraaf, the world’s largest manufacturer of recycling systems,” says Mikela Druckman. And the CEO of Greyparrot is looking further ahead: “Progress in tackling the global waste and resource crisis can only be made if we work together. That’s why we are once again looking forward to IFAT Munich to find out how our system can support the international key players in the recycling sector even more extensively.” You can find more information about IFAT Munich at www.ifat.de/en
As fly tipping is a rampant problem, it’s only fitting that government bodies are stamping down on the disposal methods for construction waste. There have been a fair few changes to the pertinent legislation in recent years, and councils are certainly trying their best to inform the public.
But never fear, Future Waste is on the case and has a handy guide ready and raring to lend a helping hand.
So, who is responsible for the proper disposal of construction waste? This one is pretty simple. It is down to the site manager, contractor or relevant responsible party to properly dispose of their waste.
Waste disposal companies are the best solution to the proper disposal problem. They must be licensed with a Certificate of Registration under the Waste (England and Wales) Regulations (2011) by the Environment Agency. They are legally required to provide WTNs (Waste Transfer Notes) for each load removed from site, which should be held in company/personal records for proof.
According to NetRegs, a WTN should always include:
• A description of the waste
• Any processes the waste has been through
• How the waste is contained or packaged
• The quantity of the waste
• The place and date of transfer
• The name and address of both parties
• Details of the permit, licence or exemption of the person receiving the waste
• The licence or registration number of the person handing over the waste, if they have a waste management licence or are a registered carrier of controlled waste
• The appropriate European Waste Catalogue (EWC) code for your waste
• The Standard Industry Code (SIC) of your business
It is also a legal requirement that any waste produced by a business that is sent for recycling or disposal must be classified using an EWC code and that this code is included on the WTN.
For a thorough breakdown of the different types of construction waste materials, along with their waste codes, please visit https://www.gov.uk/how-to-classify-differenttypes-of-waste/construction-and-demolition-waste
So, what is construction waste? It might seem like a silly question, but let’s answer it anyway. Construction waste is any additional matter that is discarded/produced as a result of the following work:
• Construction
• Demolition
• Excavation
• Refurbishment
• Renovation
• Road works
• Site clearance
It is a legal requirement that any waste produced by a business that is sent for recycling or disposal must be classified using an EWC code, which should be included in the WTN.
EWC codes for construction and demolition waste include but are not limited to:
• Paints and varnishes – 08-01-11 to 08-01-11
• Adhesives and sealants – 08-04-09 to 08-04-10
• Packaging waste – 15-01-02 to 15-01-10
• Concrete, bricks, tiles and ceramics – 17-01-01 to 17-10-03
• Wood, glass and plastic – 17-02-01 to 17-02-04
• Bituminous mixtures, coal and tar – 17-03-01 to 17-03-03
• Metallic waste, including cable – 17-04-01 to 17-04-11
• Soil, contaminated soil, stones and dredging soil – 17-0503 to 17-05-06
• Insulation and asbestos materials – 17-06-01 to 17-06-13
• Gypsum – 17-08-01 to 17-08-02
• Cement (wet) – 17-09-03
The EWC code provides a standardised description of different wastes which enables waste to be recorded and monitored effectively. Classifying the waste will help to decide on the most appropriate treatment process. The primary purpose of identifying and following the prescribed movement and waste management options is to prevent harm to people and the environment.
All reputable waste management companies will require the inclusion of the relevant EWC code on the WTN paperwork when arranging for the disposal of waste materials.
Timings are a difficult one to pinpoint as it will vary from site to site. For instance, a bigger worksite might be able to store waste safely in a larger capacity than a smaller site. The general rule to follow is ensuring the amount of waste does not back up, and is regularly emptied and dealt with by the relevant party.
For hazardous waste disposal, there will be definite parameters of when to dispose of hazardous substances and materials. The best course of action is to double check these requirements with the service provider.
As there will be a variety of materials, there will be several different waste streams they must conform to. Waste and recycling centres will be able to take some of it, however due to the nature of the work, some materials will be classed as hazardous.
Hazardous materials are listed below but not limited to:
• Asbestos
• Batteries
• Chemicals, such as brake fluid or print toner
• Equipment containing ozone depleting substances, such as fridges
• Hazardous waste containers
• Oils, except edible ones, such as vehicle oil
• Pesticides
• Solvents
It should be noted that hazardous waste items fall under the Control of Asbestos Regulations (2012), the COSHH Regulations, and the Control of Lead at Work Regulations (2002) and require specialised handling. Special handlers will need to be employed for proper disposal, Kleenwaste (https://kleenwaste.com/)
For smaller amounts of construction waste, it is a good idea for contractors to hire a skip to dispose of their waste. There are, however, a number of considerations to keep in mind when choosing this option. Firstly, there are a number of common items that cannot be disposed of in a skip, including the list above. The skip company should be able to give proper guidance about any limitations they may or may not have.
Given the nature of construction waste, and the wide variance in materials, it can be really tricky to correctly dispose of correctly. It’s certainly an expensive business as not only is it heavy and difficult to transport from one place to another, but there are also many rules and regulations that surround the process. This, unfortunately, means a lot of illegal disposal takes place, meaning that stricter rules and legal enforcements are needed to ensure proper disposal.
Luckily, the rules and regs are actually seeing an improvement in figures.
Government statistics report (on the gov.com website): In 2022/23 there were 1.08 million fly-tipping incidents reported, a decrease of 1% from 1.09 million in 2021/22 (Figure 1). This is the second year in a row that a decrease has been seen.
It goes to show just how effective it can be when everyone plays their part.
For more construction waste statistics and recovery rates, please visit:
www.gov.uk/government/statistics/ uk-waste-data/uk-statistics-on-waste