KLEENOIL KEEPING KLEEN!


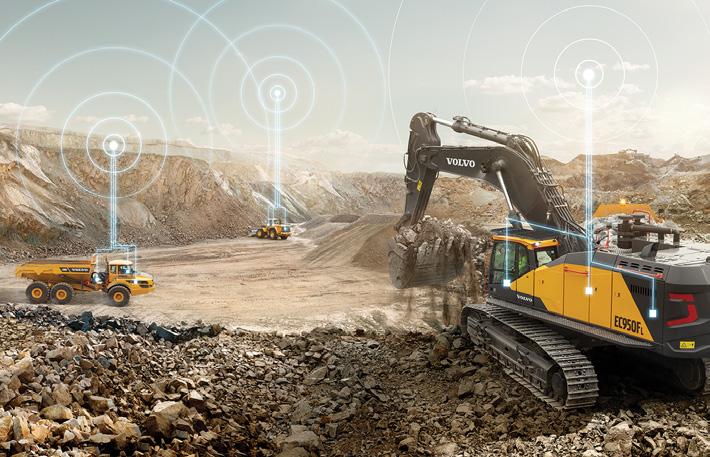
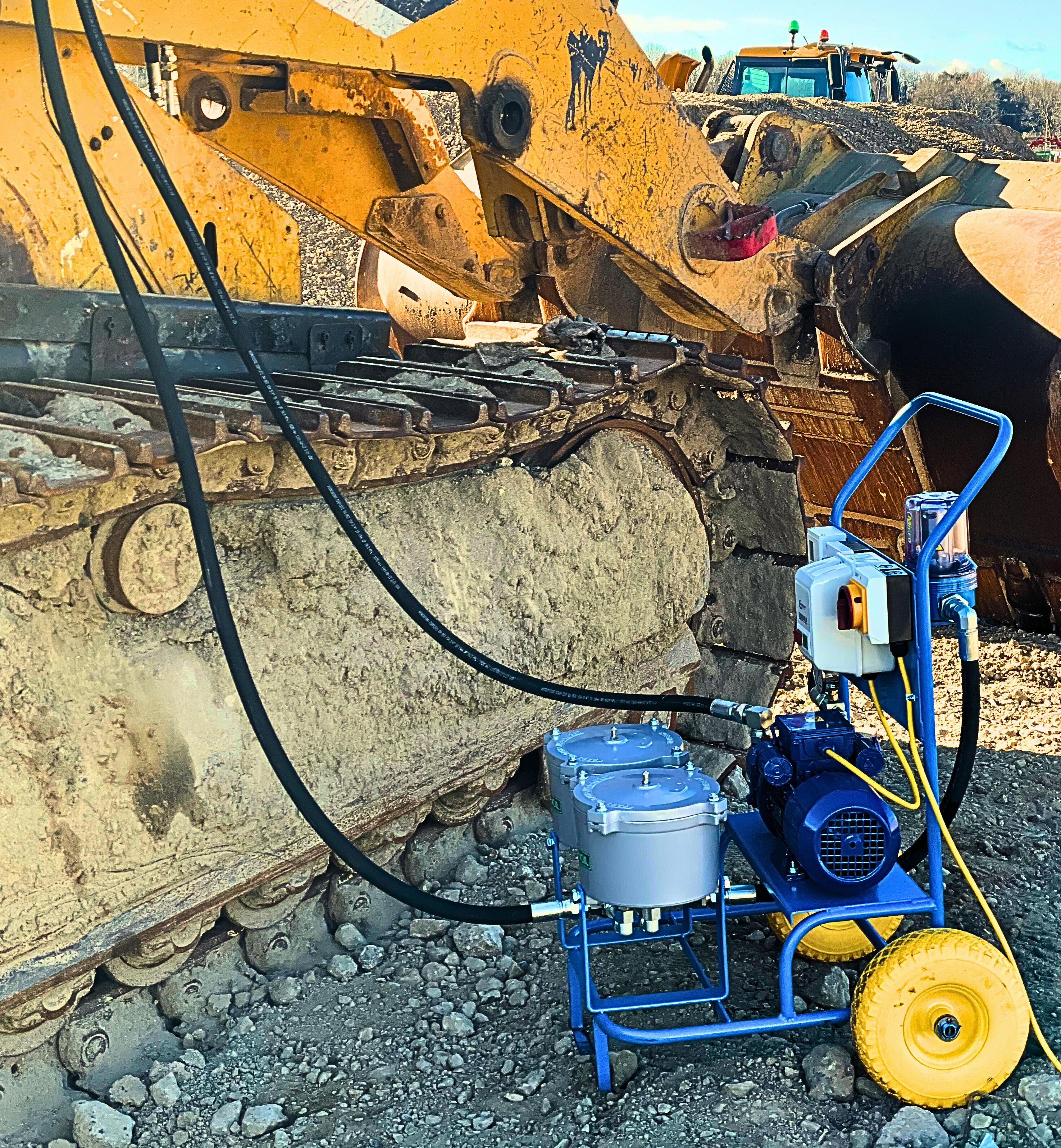
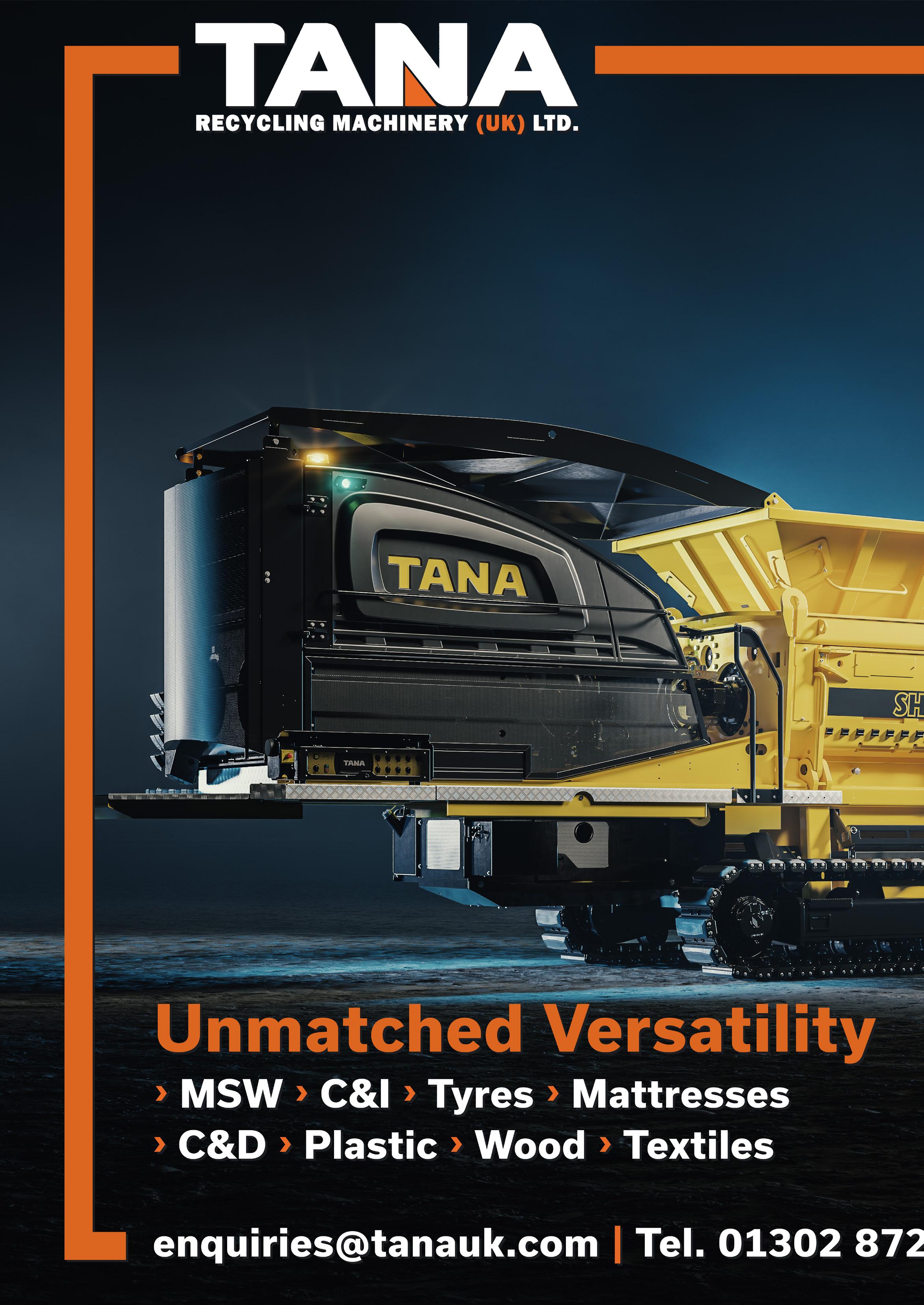
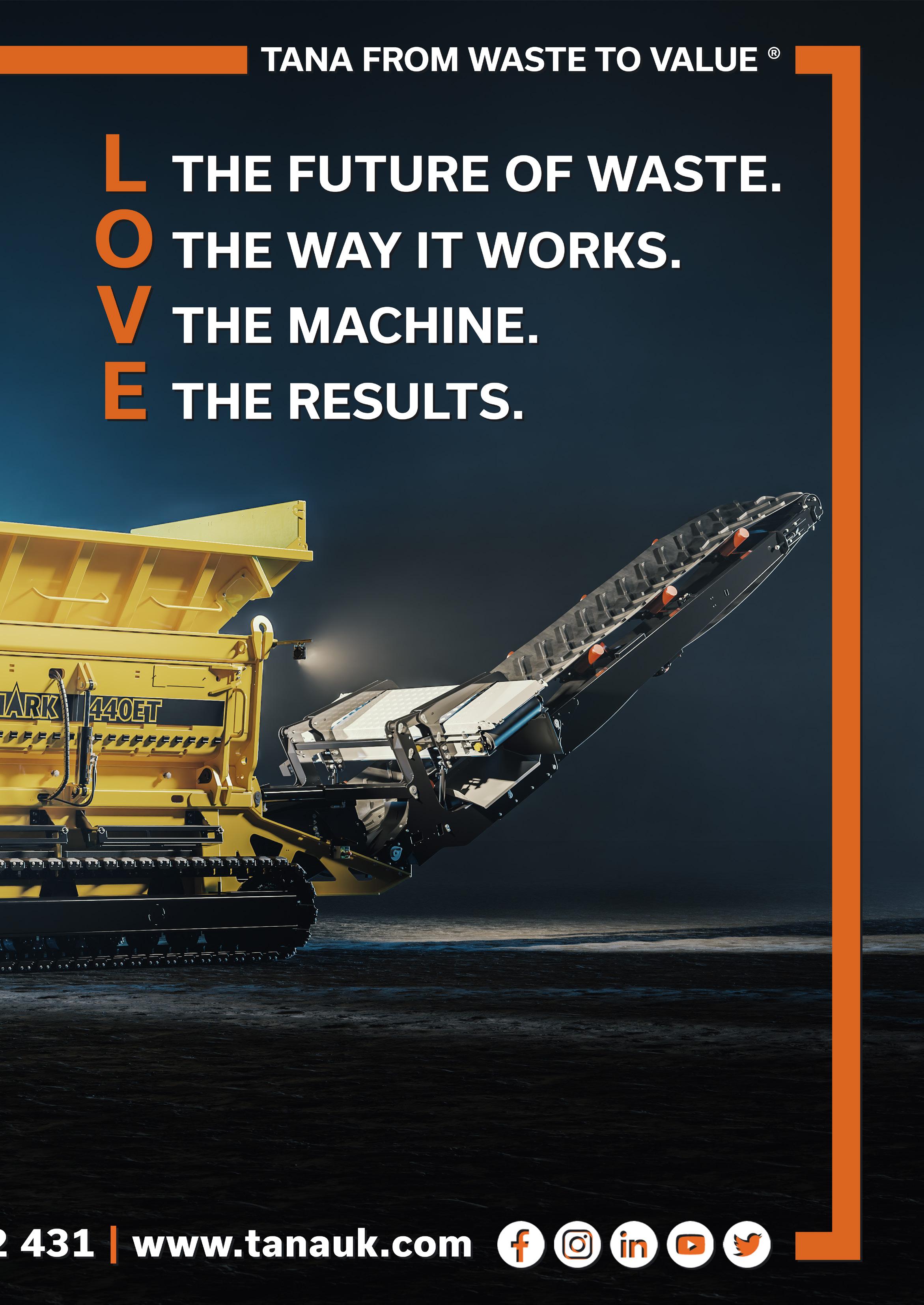
Well, what can we say? It’s been a glorious summer, dear readers, but now autumn has arrived and with it, the latest issue of Future Waste.
This month, we look back on all that the summer season had to offer, with plenty of wonderful tales from the world of waste as well as a review of the fantastic farewell show for Plantworx UK. Whatever the sun shone down on, we’ve got it covered.
Not to worry though; it’s not all lamenting the loss of the sunshine! We’re also looking forward to the months ahead, with a sneak peek at the exciting RWM show in mid-September, a show that demonstrates the industry’s commitment to sustainability.
SMT star in our company profile this month where they explain more about their Volvo support services. They tell us all about CareTrack, the Volvo Construction Equipment telematics system that gives customers access to a wide range of machine monitoring information.
ALEX COX SMT GB
TOM WORTHINGTON ALBUTT LTD
AARRON HUME INVICTA ATTACHMENTS
MARTINA SUSOVA SENSONEO J.S.A
JACK BARWISE
KENNY WASTE MANAGEMENT
partners with:
As for features, it’s all about connections, physical or technological. Future Waste gives you the inside scoop on the best waste handling attachments on the market, as well as the best fleet management apps. Whatever you need to work with waste, we have it well and truly covered. PART OF
Future waste is published by Kiwi Media and Promotions Ltd
2nd Floor, 41-42 Southgate, Chichester, West Sussex PO19 1ET +44 (0) 1243 345 323
Copyright
Kiwi Media and Promotions Ltd. © 2023 All rights reserved. Reproduction in whole or part is prohibited except with permission in writing from the company. Note to contributors: articles submitted to the Editor for consideration must be the original work of the author. Where photographs are included that are not the property of the company or contributor, permission to reproduce them must have been received from the owner of the copyright. Any views or opinions expressed within this magazine are not necessarily those of the company.
ISSN: 2631-4622
Registered in England No: 09910499
All advertisements are accepted subject to the Kiwi Media & Promotions’ standard of insertion. For a copy of Advertising Terms & Conditions, please write to Darren Shelton at 2nd Floor 41-42 Southgate, Chichester, West Sussex PO19 1ET
A round-up of the latest news from the recycling and waste sectors over the past few months.
Even though the 2023 event was, sadly, the last time Peterborough will host the show, it was the perfect farewell from the East of England Showground.
Rebecca Phillips has found the top three apps for managing your fleet… so you don’t have to!
Kleen Oil dispense with the corporate jargon and explain their process in layman speak.
A preview of September’s RWM event – the UK’s premier recycling show.
Turning Insight Into Action With SMT’s Volvo Fleet Support Services.
Rebecca Phillips speaks to two of the top companies for all of your waste handling attachment needs.
Westminster City Council and Veolia have announced the full-scale rollout of the UK’s largest electric refuse collection fleet. The vehicles are the next generation in electric Refuse Collection Vehicle (RCV) development and will deliver a cleaner and quieter service, powered directly by energy generated from the waste they collect. Housed in a specially designed depot, smart charging infrastructure will ensure they are always ready to go when needed.
Westminster Council has invested £20m in the 45 new zero emission trucks which will be introduced over the coming weeks in a ground-breaking initiative that will benefit residents by reducing vehicle noise, cutting air pollution and drastically reducing the borough’s carbon emissions. Westminster will gradually replace its entire 80-strong truck fleet, in the biggest decarbonisation programme of its kind by a UK local authority. Many of these vehicles will be housed at the new fully electric depot at Landmann Way, near Bermondsey. The electric vehicles will charge their batteries by drawing electric power from an adjacent energy recovery facility which uses the waste collected from homes and businesses in Westminster.
Westminster’s fleet, operated by its environmental partner Veolia, completes 50 million collections every year and each electric vehicle saves up to 89% CO2e compared to a diesel-powered fleet.
Veolia worked to procure, design and operate the new depot and charging infrastructure which will be capable of charging 54 vehicles simultaneously. Smart charging will allow the partnership to support the National Grid by receiving power at non-peak times to maximise local resources and strengthen the Grid’s resilience.
Pascal Hauret, Managing Director Veolia UK Municipal said:
“It’s fantastic to see our teams working together with Westminster City Council to deliver a cleaner, greener and quieter service for residents, businesses and visitors across the city.
“Using the waste we collect to power the electric fleet is an exciting innovation because that creates a local loop of energy, using local resources to run local services. I’m incredibly proud of the solutions Veolia and Westminster are pioneering together to build the sustainable municipal services we need, now and in the future.”
Cllr Paul Dimoldenberg, Cabinet Member for City Management and Air Quality, said: “By replacing diesel-powered refuse trucks with a £20m investment in UK-built electric vehicles, Westminster City Council is voting with its fleet.
“The trailblazing electrification will deliver an essential service that is quieter for residents, improves air quality in central London and reduces our fleet emissions by 50 per cent, or over 2,000 tonnes of CO2 per year. This is a significant moment in the evolution of sustainable council
services and we look forward to further expanding our zero-emission vehicle fleet in the future.”
The trucks, built by Dennis Eagle Ltd in Warwick, will be the mainstay of a zeroemission refuse fleet which also includes 90 electric street cleaning vehicles ranging from e-bikes to e-sweepers. The South East London Combined Heat and Power facility (SELCHP) will provide the site with 3.3GWh of electricity per year via a private wire to charge the e-fleet. This facility treats residual waste to create 265GWh of electricity, supplying enough electricity to the grid to power 48,000 homes, and generating heat for a local district heating scheme serving over 2,800 homes. Over 50% of the electricity generated by SELCHP qualifies as renewable under the Renewable Energy Guarantees of Origin (REGO) scheme.
The newest addition to the popular and proven TANA Shark shredder series, the TANA 440ET, uses electricity as its power source. Combining the benefits of cheap energy, long service intervals and near-emissions-free operations, the new model helps TANA customers succeed in public procurements and competition within the circular economy.
Soon, it will be possible to process various waste fractions into raw materials for the circular economy in an even more environmentally friendly way. Tana’s newest mobile shredder, the TANA Shark 440ET, shreds waste completely electrically.
“Electrification makes it possible to reduce local emissions from waste
processing to a minimum. This supports the goals of our customers working at the heart of the circular economy and makes the pre-processing of recycled raw materials and recycled materials even cleaner,” says Eetu Tuovinen, Product Manager for TANA shredders.
The TANA Shark 440ET is based on proven technology that has been tested extensively in real conditions. The design of the new shredder is based on the TANA Shark series that was launched at the beginning of the 2000s and who’s properties of durability, versatility and mobility have achieved almost iconic status among customers.
The development of the new shredder model was driven by feedback from customers. “Our customers have shown strong interest and a need for an electrically powered and mobile shredder. The TANA Shark 440ET is the first shredder model on the market that combines mobility and electric drive,” Tuovinen explains.
The TANA Shark 440ET completes the philosophy of the model series, according to which every customer can find a suitability powered and reliable shredder with the optimal performance for their particular operations. The TANA Shark 440ET is ideally suited for high-volume production facilities, where industrialgrade 1000-amp and 400/480-volt threephase electrical connections are available.
To learn more about TANA Recycling Machinery, please visit: www.tanauk.com
In recent years, the importance of the circular economy and locally produced recycled materials has also grown in terms of security of supply. A power unit based on diversified and decentralised electricity production supports not only environmental goals, but also the security of supply and predictability of operating costs for customers. Furthermore, the more the electricity production capacity increases, the more affordable the power source is. Although the shredding itself is powered from the electricity mains, diesel technology has not been completely abandoned. The new electric shredder is equipped with a small diesel engine that allows the machine to be driven independently from one processing point to another at the production plant or terminal.
Material composition in the recycling industry has been a longstanding challenge due to the complexity of mixed material streams, compounded by ongoing changes in consumer packaging. Operators have only snapshots of material composition gathered through manual waste audits and human observations once the waste arrives at the material recovery facility (MRF).
Understanding the material stream is key to making adjustments that influence the incoming material stream and recovered material reuse markets.
Artificial intelligence (AI) is the enabling technology essential for MRFs to generate and capture the data to optimise recycling operations. Visionbased AI software identifies and characterises objects in the waste stream in real time, digitising each item that passes by. These objects are captured as a new form of data, including object counts, packaging descriptions, and more, over time. At AMP Robotics, we’ve deployed hundreds of robots and sensors that process billions of objects on
conveyor belts in MRFs. This effectively enables automated and continuous characterisation of this material. We continue to expand our material categories by exploring and developing subcategories useful for MRFs as well as for downstream recyclers. The more AIbased robots and sensors we deploy into production, the more a network effect is created.
MRF operators can use the data this machine learning technology produces for analysis to support inbound, outbound, and product quality questions. It also allows operators, finance departments, and material auditors to do things like graphically compare material stream data to historical baselines; define material volume thresholds and create alerts triggered by movement above or below these thresholds, and more.
This delivery of real-time monitoring and analysis of material as it flows through a facility provides visibility into and feedback about material streams, helping operators to get ahead of mechanical or configuration-based issues and communicate with business partners or key staff in the facility.
The digitisation of scrap objects in the MRF opens up many potential applications. The first two that are deployed into MRFs today are robotic sorting and the descriptive and diagnostic analytics provided by standalone sensors. As the sensors become distributed throughout a MRF, we’re able to help the MRF become a more data-driven facility to reduce costs and increase revenue. As Extended Producer Responsibility (EPR) schemes emerge and mature, sensors growing in the fleet of MRFs can help satisfy the demand for reporting recovery rates.
To learn more about AMP Robotics, please visit: www.amprobotics.com
Latest data shows 58% carbon savings which will advance the transition to net zero through optimised vehicle performance, maintenance and operating regimes
The latest trials on yellow plant by leading resource management company, Veolia, have now demonstrated the potential to make major carbon savings of 58% across its fleet of over 660 site based machines. By working with vehicle manufacturers to optimise vehicle settings, training operators to maximise productivity, and lowering maintenance requirements through better operating regimes, the company is advancing the transition to net zero.
Set against a background of the limited availability of electric or other zero emission plant the programme shows the potential of lowering the carbon footprint of plant used in the company’s recycling, waste, construction and demolition operations.
The six month trial has focused on making key changes to the way vehicles are used, how they are set up for tasks, ensuring the vehicles are optimised, and implementing wide-ranging training programmes to enable vehicle drivers to limit fuel use
and vehicle wear. Results of the changes were logged through accurate telemetry monitoring across a wide range of yellow plant including articulated haul trucks, wheel loaders, tracked vehicles, dozers, and landfill compactors.
At Veolia’s main testing site in Rainham, the total time vehicles spent idling has been reduced by 50%, saving an estimated 12,000 litres of fuel a year. Other reductions in fuel burning rates are estimated to save a further 38,000 litres of fuel a year, and together, these can save an estimated 133,000kg of carbon emissions on this site alone.
To further cut CO2 emissions, arising from the manufacture of spare parts and maintenance, the company has developed new operating regimes based on conditions for operating on site, equipment configuration, job set up, vehicle optimisation, payload, and correct loading techniques. In combination these measures make a major difference to maintenance requirements and vehicle operating life and also improve the economics of these assets.
Following the success of this trial the Veolia optimisation programme will be introduced across the entire fleet of site machines, used on 83 sites, to increase CO2 savings.
Highlighting this latest achievement, Gary Clark, Veolia Fleet Director UK&I said: “The unprecedented carbon savings we have achieved during this trial have actively demonstrated how the industry can accelerate the transition to the net zero target, and meet our aim of ecological transformation.
“Through the hard work and engagement of our teams at all levels, supported by vehicle manufacturers, our optimisation programme has exceeded its aims. Together this has given us a greater understanding of the challenges, and can now be extended across all of our sites to make major cuts in carbon emissions.”
In becoming the benchmark company for ecological transformation, Veolia is committed to tackle climate change, resource depletion, biodiversity collapse, and pollution. By expanding the use of existing and new innovative solutions, the company is accelerating the process to radically change patterns of production and consumption and placing ecology at the heart of every process. This includes maximising the value from resources to effectively ensure a secure supply of energy, and easing resource scarcity challenges.
To learn more about Veolia, please visit: www.veolia.co.uk
Following a successful trial earlier this year, One Stop has partnered with global resource management company, Veolia with the aim of recycling over 380,000 milk bottles per year from their stores. Own Label milk bottles from the stores’ relevant vending machines and staff refreshments are collected from One Stop’s distribution centres by Veolia on a weekly basis and then the recycling begins.
Veolia takes the milk bottles to its Dagenham Plastic Facility where they begin their recycling journey. The bottles are washed, shredded and turned into pellets which can then be blown back into milk bottles and ready to use again!
Simon Futcher, Commercial Business Development Director at Veolia said: “Veolia is delighted to be working closely with One Stop to recycle their milk bottles, ensuring we reduce their carbon impact on the environment. “This partnership aligns with Veolia’s purpose of ecological transformation and demonstrates a closed loop recycling solution. Turning used milk bottles into fresh ones replaces the need for raw materials and saves 67% of carbon emissions at the same time.”
Amriene Kalsi, Sustainability Manager at One Stop said: “We’re so pleased to be working with Veolia on this new initiative. It’s certainly another key step towards our goal of increasing recycling within
our own operations, contributing to our target of meeting net zero by 2050.” The convenience retailer, which is transforming through its sustainable journey, has also recently replaced its green hard-to-recycle bottle tops on their British semi-skimmed standard milk with clear recyclable lids.
FOR FURTHER INFORMATION
To learn more about Veolia, please visit: www.veolia.co.uk
In the coming year, both DEFRA and the Welsh Government are expected to enact the provisions of the Environment Act 2021 and thereby make the separation of food waste from other waste streams a mandatory requirement.
The new regulations are expected to mandate that any business producing over 5kg of food waste will need to separate and recycle its waste through a registered food waste carrier service. Failure to do so could put businesses at risk of financial repercussions with fixed penalty notices starting from £300. This is, of course, a concern for businesses and it may feel like a tall order in the
current climate. However, food waste recycling is not a new concept in the UK. It has been mandatory in Scotland since 2014, which means that Scottish businesses producing more than 5kg of food waste per week already have a legal obligation to recycle it responsibly.
In Scotland, we’ve seen the opportunities that this can bring. Separating and recycling food waste has had a significant environmental benefit and we have been able to drive resource productivity by reusing food waste to create valuable resources, such as renewable power, gas or fuel.
In addition to this, businesses that recycle food waste can often be privy to significant economic benefits. In fact, our
recent survey found that businesses could save up to £7,000 per year by recycling their food waste instead of sending it to landfill.
So, what are the financial risks and benefits for businesses who send their food waste to be recycled, rather than to landfill?
The cost-of-living crisis, soaring energy bills, and staffing shortages have meant businesses across the UK have had lots to contend with, and deciding where to spend already stretched budgets is a difficult decision to make. So, it was no surprise that our research revealed that almost half (44%) of businesses do not see food waste recycling as a core priority.
Separating and recycling your food waste can have significant environmental benefits
Pledge2Recycle Plastics, part of RECOUP, the plastics resource efficiency and recycling charity, is embarking on a mission to shed light on the actual household plastic recycling practices. Through a short survey - Cutting the Confusion: How do you recycle your household plastics (2023) Survey (surveymonkey. co.uk) the team aims to identify the items causing confusion in recycling, while questioning citizens about their commitment to recycling bottles, pots, tubs, and trays.
Stuart Foster, CEO at RECOUP, states, “We understand that recycling plastics can be challenging for people. Our research shows that even easily recyclable items often don’t end up in recycling bins. Astonishingly, out of the 38 million plastic bottles used daily in the UK, 14 million remain uncollected for recycling. We are determined to comprehend the barriers preventing people from recycling, despite the availability of kerbside collection, and the reasons why some recyclable items aren’t being given a chance to be recycled.”
The survey has been thoughtfully designed to require only a few minutes for completion. RECOUP earnestly
requests everyone to participate and share the survey with their friends, family, and colleagues. The aim is to create a comprehensive nationwide overview of the items that confuse individuals the most when it comes to recycling. As an added incentive, Pledge2Recycle Plastics will draw one lucky winner of a £50 high street voucher from the completed surveys every month.
The data collected from this survey will be compiled and shared with the plastics industry, Local Authorities, and other stakeholders. The objective is to identify necessary changes that will support plastic recycling efforts.
For more information about RECOUP, the work they do and how to become a member, please email: enquiry@recoup.org visit: www.recoup.org or call: 01733 390021
The bottle statistic is taken from RECOUP’s UK Household Plastic Packaging Collection Survey 2022, free to download https://www.recoup.org/p/431/recoup-reports-policy-infrastructure
BioteCH4 is delighted to have been awarded the contract for the treatment of Newcastleunder-Lyme Borough Council’s food waste.
BioteCH4, the UK’s leading Anaerobic Digestion (AD) operator, will initially receive food waste collected from kerbside collections in the Newcastleunder-Lyme borough.
AD is the sustainable process of turning food waste into renewable energy which then goes back into the national grid. The process also produces biofertiliser, a nutrient-rich organic material used to fertilise farmland.
Newcastle-under-Lyme Borough Council is the first waste collection authority in Staffordshire to take up the service. BioteCH4 is one of four providers on a framework with Staffordshire County Council, so could deliver the service to other district and borough councils. Depending on the roll-out of those authorities not currently collecting food waste, the new county-wide framework could see up to 40,000 tonnes of food waste being recycled a year, potentially resulting in enough energy to power 7,000 homes.
To learn more about BioteCH4, please visit: www.biotech4.co.uk
Lead at BioteCH4, said: “We are really pleased to be working with Newcastleunder-Lyme to recycle its food waste.
“Mandatory food waste collection services will need to be implemented by all councils and this could be a daunting challenge for some local authorities. But securing the treatment site early will help councils understand what recycling capacity is available and enable them to plan vehicle procurement, service routes and other logistics accordingly.
“Staffordshire County Council moved quickly to secure a treatment facility for its food waste and are now in a good position to meet DEFRA’s deadline for all their other district and borough councils. We strongly encourage councils to follow Staffordshire’s lead and start implementing their treatment plans as soon as possible.”
Newcastle-under-Lyme Borough Council’s Portfolio Holder for Sustainable Environment David Hutchison said: “Providing residents with an efficient food waste collection service is one of our top priorities. Not only does it encourage our residents to consider their recycling habits, but recycling food waste can play an important role in reducing our carbon emissions. We are pleased to be working with BioteCH4 and will be working hard to expand our food waste collection services across the county in the future.”
Prolectric, the off-grid, renewable lighting, and power specialist, has unveiled an innovative new savings calculator to help companies fast-track and achieve their environmental and sustainability objectives by making the switch from diesel to solar.
Serving a wide range of industries from construction, housebuilding, and rail to major infrastructure, Prolectric’s new savings calculator has been specifically designed to calculate the potential carbon, diesel and cost savings that could be realised when switching from diesel powered systems to Prolectric’s solar and hybrid power solutions.
Rachel Preen, Managing Director, Prolectric, commented: “Our range of environmentally friendly, advanced performance products have been designed as direct like-for-like diesel replacements, making them a simple switch. The environmental case is clear,
but our new savings calculator provides a simple yet highly effective tool to support businesses to see the full benefits and build a commercial case to switch to solar. Since launching our first solar lighting tower in 2017, we estimate to have saved our clients 26 million kg of CO2 and reduced diesel usage by more than 10 million litres, – that’s probably saved our customers more than £9 million.
“We are committed to providing practical and commercially viable ways for businesses to stop using polluting fossil fuels to reduce carbon emissions. Our new tool offers another level of granularity for customers during the critical specification and procurement stages, with quick access to understandable data, so they can make informed decisions which in turn will help them achieve their net zero goals and save money.”
Prolectric was the first to introduce all-inone solar street lighting to the UK in 2011, with specialist technology specifically
designed and developed for UK weather conditions. As a market leader, the company has installed over 8,000 units across the UK, providing high-quality, reliable, low-voltage LED lighting to customers across Local Authorities, MoD, Commercial and Industrial sectors. The company’s solar lights, hybrid generators and CCTV, provide highperformance temporary and permanent site lighting, power, and security - with minimal environmental impact and low running costs. In particular, Prolectric’s lighting systems produce zero carbon, zero noise, need little maintenance, and require zero fuel.
Siemens provided automation and building technology to the recently opened Bustanica vertical farm in Dubai, the world’s largest of its kind. The $40 million facility is owned by Emirates Crop One, a joint venture between Emirates Flight Catering, one of the world’s largest catering operations serving more than 100 airlines, and Crop One Holdings Inc., an industry leader in technology-driven indoor vertical farming.
Technology from the Siemens Xcelerator portfolio has been integrated throughout the farm to ensure efficient production, reduce waste, and increase the farm’s overall sustainability. Siemens Smart Infrastructure’s building management system Desigo CC controls and monitors air-conditioning and ventilation, while Siemens Digital Industries’ SIMATIC automation and control systems deliver optimal growing conditions by controlling the lights and CO2 levels required by the plants. SINAMIC series variable frequency drives along with automation stations make sure plants receive the right nutrients and water supply. SENTRON electrical components distribute power to the grow racks.
Siemens SCALANCE components create a communication network connecting these automation technologies while protecting the facility with Siemens cyber security solutions. Siemens Xcelerator is an open digital business platform that enables customers to accelerate their
digital transformation easier, faster, and at scale. At its core is a curated portfolio of connected hardware and software, a powerful ecosystem of partners, and an extensive marketplace.
Bustanica’s system is designed to circulate water to the crops to maximise water usage efficiency. When the water vaporizes, it’s recovered and recycled into the system, saving 250 million litres of water per year compared to traditional outdoor farming for the same output. The 330,000 sq. ft. facility requires 95% less water than conventional agriculture, and provides an output of 1 million kgs of produce per year that are free of pesticides, herbicides and chemicals.
“We are proud to work with Emirates Crop One on a project that will transform agriculture and will allow people to eat fresher foods while reducing water consumption and transportation costs,” said Franco Atassi, CEO of Siemens Smart Infrastructure in the Middle East. “Bustanica uses smart infrastructure in its vertical farm that will allow it to sustainably scale operations and become a model for other vertical farms around the world. The infrastructure installed today will allow for the use of machine learning and artificial intelligence in future.”
Bustanica’s produce will initially be provided to airline passengers flying to and from Dubai. The company plans to sell leafy greens and other produce in local supermarkets, and because the greens are grown in a controlled
environment, consumers can eat them straight out of the bag.
“Emirates Flight Catering constantly invests in the latest technologies to delight customers, optimise operations, and minimise our environmental footprint. Bustanica helps secure our supply chain, and ensures our customers can enjoy locally sourced, nutritious produce,” said Kieran Dowd, General Manager of Emirates Crop One and Vice President, Sourcing Solutions, at Emirates Flight Catering. “The technology provided by Siemens enables the facility to bring food production closer to consumers, making our operations more efficient and sustainable.”
Vertical farming facilities are up to 100 times more productive than outdoor farms because they consume 95% less water and don’t require any use of pesticides or chemicals. This method allows farmers to control light, temperature, water, and carbon dioxide levels – maximising output and efficiency – so they can grow crops year-round and near consumers. The industry is expanding to mitigate challenges like food insecurity, limited arable land, labour shortages and to meet growing demand for pesticide-free produce.
To learn more about Siemens, please visit: www.siemans.com
The International Association for Agricultural Sustainability (IAAS) proudly hosted the highly anticipated International Agriculture and Innovation Conference 2023 (IAIC 2023) under the theme of “Agro-industrialisation and Sustainability.”
The conference took place on 1st August 2023 and brought together leading experts, scholars, researchers, and industry stakeholders to explore transformative solutions for the agricultural sector. The event delved into three key themes: “Agriculture Development in the Face of Change,” “Controlled Environment Agriculture,” and “Agriculture Innovation Systems,” alongside insightful panel discussions. The IAIC 2023 commenced with an inspiring opening speech by Prof. TzongRu Lee, chairman of IAAS, emphasising the critical need for agro-industrialisation that balances economic growth with environmental preservation. This was followed by a compelling keynote address from Prof. Ian Givens, who shed light on dietary transitions for sustainable diets in the UK and India. The conference placed a strong focus on the symbiotic relationship between agriculture and industry, striving to develop practices that promote sustainable growth and resilience in the face of global challenges.
To learn more about IAAS, please visit: www.iaas.org.sg
The conference’s first theme addressed the urgent need to adapt agriculture to a rapidly changing world. Experts from diverse backgrounds shared strategies for enhancing agricultural productivity, climate resilience, and sustainable land management. Distinguished speakers from the UK, US, and Taiwan, such as Dr. Lin Hsueh-Shih, Dr. Jonty Brunyee, Prof. John Healey, and Prof. Fedro S. Zazueta, presented best practices and successful projects from their regions, focusing on adaptive measures and climate change mitigation in agriculture. The accompanying panel discussion, moderated by Dr. Wee Liang Tan, Vice Chairman of IAAS, explored innovative approaches to address climate change, water scarcity, and other environmental factors affecting food production. The discussions emphasised community engagement, public-private partnerships, and the integration of traditional knowledge with cutting-edge technology to drive sustainable agricultural development.
Under this theme, participants delved into the realm of Controlled Environment Agriculture (CEA) and its potential to revolutionise food production. Esteemed speakers, including Prof. Genhua Niu, Dr. Jennifer Bromley, Prof. John E. Erwin, and Dr. Eri Hayashi, shared enlightening talks on CEA, greenhouse vegetable crops, the potential of vertical farming, and plant factory innovations. Attendees
were inspired to explore new frontiers in urban farming and contribute to building a healthier and greener world. Following the sessions, a stimulating panel discussion, moderated by Prof. Cheng-I Wei, Honorary Chairman of IAAS, delved deeper into CEA practices and encouraged collaboration between researchers, entrepreneurs, and policymakers to optimise CEA for sustainable food systems.
The third theme, Agriculture Innovation Systems, explored the role of technology and research in driving agricultural progress. Sessions focused on the integration of artificial intelligence, data analytics, and blockchain in agriculture. Insightful talks from Dr. Lava Kumar, and two speakers from FAO, Dr. Delgermaa Chuluunbaatar, and Dr. Hildegard Lingnau provided valuable insights into precision farming, biotechnology, and sustainable practices, fostering an environment where innovation meets sustainability.
The subsequent panel discussion, moderated by Dr. Ravi Khetarpal, Executive secretary, the Asia-Pacific Association of Agricultural Research Institutions (APPARI), underscored the importance of cross-disciplinary collaboration and knowledge exchange to accelerate transformative agricultural solutions.
The conference’s interactive format facilitated networking and knowledge sharing among attendees from various sectors, including agribusiness, academia, and governmental agencies. With close to 300 scholars and industry professionals from 63 countries in attendance, IAIC 2023 set a new benchmark for knowledge exchange and collaboration in agroindustrialisation and sustainability.
The International Association for Agricultural Sustainability (IAAS) is committed to promoting sustainable practices in agriculture through research, education, and collaboration. IAAS strives to address global challenges while fostering eco-friendly solutions that drive positive change in the agricultural sector.
Three baby beavers (kits) have been born at two different beaver enclosures on the Holnicote Estate near Minehead, Somerset, where the National Trust re-introduced beavers for the first time in 400 years in January 2020.
One kit has become the sixth member of the family living at the National Trust’s ‘Paddocks’ enclosure at Holnicote, where Rashford became the first kit born on the estate in 400 years in 2021, followed by twins Russo and Toone last summer. All three were named after England’s football stars after the public were invited to help name the kits – with the final choices coming down to a public vote.
Yet to be named, the latest new arrival is already being shown the benefits of ‘eco-engineering’; how to make positive changes to the area through building dams and creating new pools to attract wildlife by its older siblings.
Jack Siviter, National Trust ranger working on the beaver project said, “The beavers at ‘Paddocks’ are a tight family team. We see them grooming each other, playing and working together to improve the site and create healthy habitats which can
support a broad range of species such as dragonflies and toads.”
George Layton, another of the National Trust ranger team at Holnicote added, “The habitat within the beaver sites is already much healthier than before their introduction and is absolutely brimming with wildlife. Beavers are brilliant creatures that through their ‘engineering’ create new ponds, leave standing deadwood – the rarest type of deadwood, where dead trees and branches remain rooted into the ground, forming vitally important habitats for invertebrates – as well as opening up fantastic glades where more light can hit the woodland floor so beetles, butterflies and even water voles can thrive.”
Another pair of kits have been born at Whiteman’s Moor – just a few miles away - to first time parents Lily and Bulrush. Here, the twins have been caught on camera playing and even hitching a ride on their parent’s backs as they work.
National Trust project manager, Ben Eardley said, “Beavers can play an important role helping to combat the climate crisis because their dams help restore dry and degraded wetlands. We’ve already seen the positive change beavers can bring to the landscape at
Holnicote and have recorded a dramatic change in water levels on the previously unmanaged woodland, as well as a change to vegetation and light.”
He continued, “The multiple dam complexes created over the last few years have helped to slow the flow of water through the area, create ponds and new channels to hold more water in times of flood, as well as in times of drought. These improvements they’ve made to the habitat are what have allowed wildlife to flourish, including fish, water voles, frogs, toads and otters.”
Due to the successful naming of the kits born to date by public vote, the conservation charity is once again asking the public for help in naming the three new kits with suggestions able to be made via the National Trust’s social media accounts, starting first on X and Threads with further opportunities on Facebook and Instagram over the coming weeks.
To learn more about the National Trust, please visit: www.nationaltrust.org.uk
Beaver kits snuggling at the Holnicote Estate, Somerset © National Trust Images/Barry Edward
SUEZ recycling and recovery UK marks the 10-year anniversary of its corporate partnership with Macmillan Cancer Support with Big 10 at 10 fundraising challenge.
SUEZ recycling and recovery UK is celebrating the 10-year anniversary of its partnership with Macmillan Cancer Support with The Big 10 at 10, a unique charity challenge that will see the business raise £101,010 for Macmillan Cancer Support. Between now and the end of the year, SUEZ is encouraging its people to get involved and take on a challenge.
To date SUEZ has raised over £550,000 to help fund Macmillan nurses, support centres and more. The company traditionally organises a ‘big’ fundraising event every two years. These events have become a popular feature in the staff calendar as teams around the country compete to walk the furthest, climb the highest and raise the most money to support people living with and affected by cancer.
This year, in honour of the tenth anniversary of the charity partnership,
SUEZ has committed to rallying its people for its fifth big event, The Big 10 at 10, to raise as much as possible, whilst having some fun and healthy competition along the way.
Colleagues across the business have already started taking on different challenges to raise money for this year’s big event, and on Friday 4 August the UK leadership team and colleagues embarked on an ambitious four-day journey from the national head office in Maidenhead to the global HQ in La Défense Paris.
Led by CEO, John Scanlon, the group committed to pedalling over 330 miles in just four days. The initial target of raising £10,000 was increased to £15,000 and the team is proud to have already raised over £14,000 of this target.
John Scanlon, Chief Executive Officer for SUEZ recycling and recovery UK said: “We’re incredibly proud of our partnership with Macmillan which has seen our teams raise over £550k in ten years. The sad reality is that many of us will be touched by cancer in some way at some point in our lives, so we’re pleased that the funds raised by SUEZ
help Macmillan provide vital practical, emotional and financial support to people living with cancer in the UK.
Our teams have embraced our partnership with Macmillan with the same drive and passion that they give to their day jobs, continually looking for new ways to raise money and reach our increasingly ambitious fundraising targets. This year, we’re excited to rise to the challenge for the Big 10 at 10, to raise as much as possible.
Our cycle challenge to Paris is just part of this year’s overall goal for the UK business to raise £101,010 for Macmillan. Giving something back to society is part of our People, Planet, Profit ethos at SUEZ and any donations at all that people can make, regardless of size, will have a positive impact for Macmillan in their support for people battling with cancer.”
To learn more about SUEZ, please visit: www.suez.co.uk
Celebrating 50 years in the construction recruitment industry, ITS Building People (ITS) now boasts 19 branches across England and South Wales. To commemorate this huge milestone, staff have pledged to raise £50,000 for the Sue Ryder charity.
Each ITS branch is taking part in various fundraising events, which include a charity skydive, The 3 Peaks Challenge, site labouring days, marathons, football matches and much more. The funds raised will provide hospice care for people with life-limiting conditions and their families.
“We are delighted to be celebrating our 50th anniversary by giving back to a fantastic cause,” said ITS Chairman Paul Knight. “Everyone at ITS is passionate about helping those who need it most, and I’m confident that our fundraising efforts will make a real difference.”
ITS Building People works with main contractors, developers and subcontractors across all sectors in the
industry, supplying trades and labour as well as professional construction staff on a temporary and permanent basis.
“We’re extremely proud of our legacy in the industry,” said Director John Bennett.
“Our success over the past 50 years has been down to our commitment to delivering quality service and solutions for clients both large and small.”
Along with the charity drive, ITS continues to push its diversity and inclusion focus to create employment opportunities for all. By tackling industry stereotypes and showcasing the benefits of working in construction, ITS are passionate about supporting sector-minority groups such as female workers and young people. As well as this, ITS is involved in several key mental health initiatives, which have seen company ambassadors co-ordinate and deliver mental health training to ensure all workers are supported in an understanding and friendly environment.
“With 1 in 4 people experiencing mental health issues, and high suicide rates
within the industry, we’re passionate about promoting a positive working environment that benefits everyone’s health,” said Director Callum McCartney. “As such, we work with constructionbased mental health charities (Mates in Mind and Man Gang) as well as national initiatives to understand the impact that mental well-being can have on people in the industry. We are constantly looking for ways to support workers both on and off-site.”
ITS are proud of what they’ve achieved over the past 5 decades and are passionate about continuing the growth of the business in the future.
To learn more about ITS Building People, please visit: www.itsconstruction.co.uk
Considered to be the pinnacle awards for the cleaning industry, Kimberly-Clark Professional is delighted to announce the return of the Golden Service Awards on Thursday 23 May 2024 at the London Hilton on Park Lane.
Created more than 30 years ago, the biennial Golden Service Awards are one of the most prestigious events and sought-after accolades in the facilities management (FM) and cleaning industry across a variety of sectors, including healthcare, retail, manufacturing, hospitality, education, leisure and office. “Behind the scenes, our cleaning and FM teams continue to make our workspaces and our public venues safe despite difficult times for all of us,” said Craig Bowman, General Manager for the UK and Ireland at Kimberly-Clark Professional. “We can go to work and attend events with our families and friends trusting that the many cleaners and FMs keep these locations safe. We are delighted to announce the launch of the Kimberly-Clark Professional Golden Service Awards 2024 where we will acknowledge and celebrate the achievements of our industry colleagues.”
Entries to The Kimberly-Clark Professional Golden Service Awards 2024 close on Friday 27 October 2023, with finalists to be announced on Monday 4 December 2023. Entries are welcome from all FM and contract cleaning companies across the UK and Ireland. There are 18 categories that recognise excellence and the achievement of the highest standards in the industry.
To honour the achievements of the industry in diverse and challenging times, Kimberly-Clark Professional has announced two new categories: a ‘Social Impact Award’ recognising positive impact on people and communities, and a ‘Cleaning Team of the Year Award’ for outstanding contributions.
The sponsors of the Golden Service Awards include a new gold sponsor, Kärcher, and returning silver sponsors, Nationwide, and Bunzl Cleaning and Hygiene Supplies, which are joined this year by a new silver sponsor, Soap20, and a new bronze sponsor, BioVate Hygienics. Welcomed back for the 2024 awards is the Irish Contract Cleaning Association (ICCA), event category sponsors for Inclusion and Diversity.
Kimberly-Clark Professional also welcomes returning media sponsors for the Golden
Service Awards, including Tomorrow’s Cleaning, Facilities Management Journal and Cleaning Matters.
To support all entrants, KimberlyClark Professional hosted a webinar on July 26 in addition to distributing a comprehensive ‘how to enter’ guide. The webinar featured support and guidance from the British Institute of Cleaning Science (BICSc), which independently oversees the judging process, and Suzanne Howe Communications, the awards’ organisers.
“We are very grateful to all our sponsors that support the Kimberly-Clark Professional Golden Service Awards and continue to help us make this special industry event possible. It is our flagship event in the UK and Ireland, and we look forward to discovering how the cleaning and FM industry continues to excel in reaching incredible new heights,” said Bowman.
Silver, bronze, category, and table sponsorships are still available. The sponsorship programme will run from the summer 2023 and culminate in the awards ceremony in May 2024. Sponsors benefit from extensive PR and social media coverage, excellent branding opportunities and top-level networking.
FOR FURTHER INFORMATION
To learn more about Kimberly-Clark, please visit: www.kimberley-clark.com
Showground in Peterborough has been bereft of the UK’s largest construction plant event. But no more!
Graced with glorious weather, Plantworx, which took place from 13th to 15th June, in every way lived up to its lofty expectations, showcasing industry-leading companies and innovative products.
A lot has changed since Plantworx was last in town, with the industry’s focus on sustainable power being as strong as ever. Considering that four years, a global pandemic, and Brexit have all unfolded since the last show, it makes sense that the construction and machinery industry would have different objectives this time around. Plantworx, if anything, served as proof that our world never sits still, and a post-pandemic world has forced everybody to adapt.
The construction industry is renowned for struggling to remain eco-friendly, but if this year’s Plantworx was anything to go by, the future looks a lot greener! Emailed tickets and water fountains were just some of the small, simple changes Plantworx made in contribution to our wonderful world, and many exhibitors made the change too, showing off a variety of technologies that put the planet first.
The east of England was blessed with the perfect weather for Prolectric to show off their high-quality solar panels. And in a fortuitous moment of foresight, they brought nearly their entire product range ready for demonstration!
The brand new 3-phrase solar power unit was particularly distinctive. Prolectric’s products clearly have a lot of TLC poured into them, and their strong position on the market is evidence that solar panels really are the way forward. “The quality of build and electrical engineering speak for themselves. We always make sure we never overpromise and underdeliver. Transparency is one of our most important attributes, and we’ll never make claims we can’t back up.”
Tucked away at the bottom of the Peterborough show ground was equipment giant, SANY, who showcased their new SW305 and SW405 wheel loaders in full force, which will no doubt make a significant impact in the world of waste management.
SANY UK, who were founded in 1989, have been long known as a trusted and reliable manufacturer. When asked about their brand, SANY stated: “You see our products in China and in America, and if you can break those markets, you know you’re doing something right.”
Leigh Harris, the Business Development Director for Sany UK was delighted by the response to their showcase. “We are thrilled with the overwhelming response and success we achieved at Plantworx 2023. The exhibition provided an invaluable opportunity for us to engage with industry leaders, establish new partnerships, and demonstrate the innovation and excellence that defines our brand. The positive feedback we received regarding our new range of wheel loaders has further reinforced our commitment to delivering top-quality construction machinery to our customers.”
We couldn’t help but get giddy over SMT’s VR headset! This device allowed us to experience their V-360 Expo technology, providing us with the chance to walk around a virtual warehouse and jump into the cabs of various machines. The company spoke about the role of AI in the industry, saying that the technology eliminated hurdles like location, conditions, and weather, whilst also providing real-world training to those in the industry. Their stand itself was totally in line with their use of such technology: sleek, modern and user-friendly. Such attributes are also proudly embodied by the company,
their ethos for the future spoken about with clear fervour and enthusiasm.
Future Waste also spoke with them about their EcoOperator course, which aims to make operators’ lives more efficient and productive. It perfectly encapsulates SMT’s mission – to make the highestquality equipment and provide the best customer support they possibly can. “The business is always evolving and Plantworx is a great platform to teach new and existing customers what we’re working on.”
Pioneering in sustainability is certainly not something synonymous with the construction industry, but if Plantworx was anything to go by, that is set to change. The in-house awards night was a resounding success, and clearly demonstrated the industry’s commitment to mother nature.
KGP Automotive Intelligence sponsored the Best Environmental Initiative category, an award that championed those who were sustainability driven. Lifos took home the gold for their Lifos Fort PV power storage system, a complete renewable power system in a box. It’s not only compact and easy to transport, but also incredibly user-friendly. The included solar panels render it completely hybridisable, and it can even be used with genset or wind turbine. A well-deserved win for Lifos, as they’re
not only saving their customers money, but lowering energy emissions as a whole.
Innovative technology also took a key role in the awards night, with MachineMax picking up a highly commended award in the category of Best Use of Technology. Their sensor-based fleetmanagement system makes it easy for any business to not only track their vehicles, but also get the best performance from their vehicles and keep an eye on maintenance concerns. It saves money and fuel, as well as maintaining the longevity of the vehicles and cutting the constant need for brand new replacements. They even demonstrated their incredible technological pursuits in the ‘Simulation Zone’. Their latest collaboration with PLINX, a top safety equipment supplier was shown perfectly in the ‘Get Connected Zone’.
It may have taken four years for Plantworx to return, but the show didn’t miss a beat and it certainly delivered on all fronts. Future Waste was ecstatic to meet with, and talk to, so many fascinating industry professionals, as well as showcase our fast-evolving magazine, and what we can bring to the industry. It was sad to wave goodbye to the East of England Showground, but we can all expect Plantworx to be back with a vengeance at a new venue in 2025.
Future Waste has found the top three apps for managing your fleet… so you don’t have to!
How does the saying go? “Always plan for the fact that nothing ever goes according to plan.” Well, in the waste industry, a plan going awry can complicate things to a dangerous level. Due to the nature of the work, rubbish collection and waste hauling can have exceedingly serious consequences if something goes wrong.
Nowadays, we’re lucky enough that the pioneering world of technology is up to snuff. For the past ten years, mobile apps aimed at all sorts of industry professionals have become prevalent, and that includes those for waste management. So, when planning is so imperative, why overload yourself with tasks when you can get an app that does the majority of it for you?
Let’s look at this process as four easy steps.
Step 1: What are your fleet’s needs? What is it you want your app to tell you about your fleet?
Step 2: Consider the waste industry itself. What will ensure you stay ahead of the game?
Step 3: Identify the major software features you’re going to want? ie. Geofencing, onboard cameras, etc.
Step 4: Compare what’s on offer and choose the app that’s right for you.
Simple, right?
The big question is, which is the right app for you and your business? Well, Future Waste is here to help as we give you the lowdown on three of the top apps for fleet waste management.
Sensoneo claims to be the global leader in waste management solutions, and one look into its technology will demonstrate as to why. It provides a wide range of solutions to endless fleet waste management problems, as well as offering the opportunity to have them custom made to suit your individual needs given that ‘specific environments require specific solutions’. Say ‘yes’ to data-driven waste management!
• Valuable data and insights for informed decisionmaking
• High quality service which gives customers a competitive advantage
• Accurate and automated reporting to national authorities
• Quick verification of the recycling targets fulfilment We were lucky enough to speak to Martina Susova, PR & Communications Manager at Sensoneo who gave us further insight into their products:
“The Dashboard offers bin inventory, a digital interactive map, tools for qualitative analysis of
waste infrastructure (bin distribution, capacity, costs), record maintenance, collection records, and an overview of citizen feedback. The powerful cloud-based platform helps customers to configure, monitor and plan everyday waste management activities and belongs to one of the best waste management software systems on the market. The customer sees all the bins on a digital map and via street view including capacity, waste type, last measurement, GPS location, and collection schedule or pick recognition. A clear and accurate overview of all bin assets is the key and the very first step leading toward smart waste management.”
Alongside the regular use of data to improve overall safety, efficiency and cost, Sensoneo has several specialist products that enable you to get the most out of your app. The smart bin tags and stickers enable users to identify and record all bin assets. It gives you a clear overview of all bins on your
routes, as well as instant access to who owns them, quantity, location and more. This means that if there is unauthorised use of such bins, that your app will pick it up, as well as aid with you invoicing and overall communication with your clients.
Martina Susova goes on to explain more about RFID tags: “Sensoneo Asset Management solution allows cities and businesses to get a clear understanding of the complex bin infrastructure they manage. It combines RFID tags and stickers, Smart Waste Management System, Mobile App, and RFID readers. By tagging all bins and containers cities and waste fleet owners can identify and record all assets (bins) in a digital inventory in the Smart Waste Management System, a powerful cloud-based platform on Microsoft Azure cloud. The solution simplifies bin and container tracking, customer communication, and invoicing, and restrains unauthorised use of bins.”
The smart bin tags and stickers enable users to identify and record all bin assets
Safe Fleet is all about “end-to-end smart truck solutions for a safer, greener waste and recycling fleet.” Its website has a whole host of real customer reviews and insights into its products, all eulogising about the user-friendly technology.
Why Safe Fleet?
• Award-winning smart truck technology solution for waste and recycling fleets
• Integrated video and fleet tracking system for real-time route management
• Widest selection of truck and trailer tarping systems
As with any business, waste hauling will rarely run smoothly. There will always be accidents and errors, no matter how hard you try. Therefore, what you really need, is a way to find, review and resolve fleet incidents as quickly and as smoothly as possible. Not only does Safe Fleet offer on board computer systems and waste truck cameras, but its FleetLink Safety Dashboard also lets you manage the video evidence securely and successfully. You can search for incidents by alarm, date, time or even GPS location! The technology allows you to easily retrieve high-quality video evidence and additionally helps you to package it for third-party review, meaning everyone can access the live footage in real time.
Safe Fleet also has a Digital Video Recorder, which enables you to record events in and around your truck. This way, drivers are able to record their vehicle’s activity which can aid in exonerating drivers and resolving liability claims. In turn, this can be used to educate new drivers by using past mistakes of others or demonstrating best practice. Even if it’s needed to show possible dangerous behaviours before they become habit, the video recorder has so many helpful applications that will take your fleet management to new heights of efficiency and safety.
As a leading telematics platform that manages not only fleet costs, but also safety and sustainability, Geotab aims to increase efficiency through its open telematics platform. The fleet management software, MyGeotab, collects the data you need for you and transforms it into easy to read, useful information that you can act on and manage your fleet effectively. All fleets, no matter the size, have the same software foundation to grow their business from. With Geotab, businesses can even customise the software to meet their exact fleet needs with MyGeotab’s Software Development Kit (SDK).
As an example, fuel consumption is something that anyone managing a fleet has a vested interest in. Most, if not all, Geotab customers need to comprehend how fuel consumption is impacted by driving habits, time of day and how the particular make, model and age of a vehicle affects fuel usage. MyGeotab regulates the data to a common unit of measurement, making it easy to read and track trends.
The Geotab Advantage
• CNG fuel pressure and temperature check to properly measure fuel usage
• Monitor engine hours and PTO usage
• Geofencing and route optimisation
• Monitor large waste and recycle bins and curb side containers
• Integrations with multiple load or axle scale systems
Something else that sets it apart from other fleet management systems is the Geo Tab Marketplace. It is a veritable ecosystem of various thirdparty apps, collating the best apps for the job all in one easy to use location. Each market place helps you navigate your specific global location to find the specific app that is right for you. Additionally, MyGeotab is now available in 10 different languages! Chinese, Dutch, English, French, German, Italian, Japanese, Polish, Portuguese (Brazilian), Spanish.
To summarise, the key things an app can do for you are:
Improving vehicle utilisation – let your app show you how to use your vehicles to their fullest effect
Lowering fuel consumption and costs – quicker, easer routes mean you save time and money
Optimising maintenance and repair programs –get true longevity from your fleet by staying on top of your vehicle’s needs
Enhancing safety – for yourself, your customers and those around you, no matter where you are
Automating compliance – stay on top of health and safety at all times
Even in this day and age, using technology as the linchpin of your work day planning might seem a little scary. Afterall, paper and pen has worked for hundreds of years, so why break the wheel?
Apps mean you have a plethora of information at the touch of a button. Just below your fingertips sits a wealth of data that remains easily accessible at all times.
You know what they say: “An hour of planning can save you ten hours of doing.” So, if there is a handy portable device that can do that hour of planning for you, why not let it?
An ex-work colleague of mine, a successful truck salesman, often used to tell me the tale about a particular brand new DAF truck he once sold that went on to cover a million miles before eventually being retired. A feat in itself, but more amazing was that this truck was still on its original engine. What’s more, the engine hadn’t had so much as a rebuild, re-line or re-bore. In fact, the engine was so good, the operator scrapped the rest of the truck and sold the engine on to an eager buyer. The reason for the engine’s extended longevity, according to my source and endorsed by the operator of the vehicle, was put solely down to one thing. The truck had been fitted with a Kleenoil Filter from new.
The Kleenoil Filtration System is a bypass filter that works by continuously diverting a small amount of the engine’s oil through an additional ‘Kleenoil’ filter. The Kleenoil filter cartridge is contained within a remotely mounted aluminium filter housing and is made of ‘densely wound pure coniferous wood pulp paper’. It looks a bit like a roll of toilet paper!
As filtration manufacturers we often lose ourselves in our own jargon and sometimes it’s better for someone else to explain the process in layman speak, so over to Kevin!
A regular oil filter filters down to around 25 to 40 microns, too small to be visible to the naked eye, yet still large enough to do damage to your engine. The gap between any of the moving surfaces in your engine is around three microns. If you take a tiny 10 micron lump of muck that will have sailed straight through your genuine oil filter unnoticed and then try to squeeze it into a three micron space, what you’re effectively trying to do is akin to shoving a house brick through a washroom mangle. No wonder wear occurs in your engine. This is where the Kleenoil filter works its magic.
The Kleenoil filter has the ability to filter any contaminants in your oil down to less than one micron. Remember that an expensive ‘genuine parts’ filter can only work ‘at best’ down to approximately 25 microns. The Kleenoil system also scores over the standard filter by its ability to filter out one of the most harmful enemies of your engine’s lubrication system, namely water. The combustion process, together with the constant heating and cooling process of your engine, creates moisture that will react with the oil in your sump. Moisture reacting with the chemical additives normally found in any engine oil will lead to a reduction in the effectiveness of your oil, resulting in sludging, a build-up of corrosive acids, and a host of other nasties, ultimately leading to a premature end for your engine. We change the oil in an engine to purge the poor insides of your favourite lump of iron of the accumulated ‘cack’ carried by the old oil. By adding the Kleenoil filter to an engine, its ability to filter out even the tiniest particles means not only are you virtually eliminating wear on the moving
parts in your engine, the oil is now constantly being recycled as it passes through the high density Kleenoil filter element. This means your oil stays as clean and fresh as the day you poured it out of the can. Because you’re now running on clean oil all of the time, oil and filter changes can now be extended to up to ten times their regular interval. When your normal oil change is due, you simply change the Kleenoil filter element, and forget about changing the oil. I know it sounds like mechanical suicide, but you’re gonna have to trust me on this one!
In the increasingly cut-throat world of the transport industry, double-shifted trucks can soon rack up the sort of mileage in a single day the rest of us might take a month to complete. Therefore, it’s not uncommon to find a truck operator carrying out once a month oil changes. Take a large fleet of trucks, multiply the number of trucks by the litres of oil contained within a truck’s sizeable sump, add in a large number of oil filters, plus workshop down-time, and you can see why the Kleenoil system has found a loyal following within the industry.
One satisfied customer has driven over half a million miles without a single oil change. The Kleenoil system also lends itself to the typically ‘mucky’ world of plant and large off-road machinery. Many underground mining locomotives and stone crushers have Kleenoil filters fitted as standard equipment. I know it sounds like one of those ‘wonder products’ you see in the back of the Sunday supplements, but Yorkshire-based Kleenoil have been suppliers of the trucking and plant industry the world over for almost 50-years, so rest assured this is no ‘here today, gone tomorrow’ outfit. The system has been fitted to everything from locomotives, canal boats to wind turbines.
At the time I fitted the Kleenoil filter to K3MUD it had done some 136,000 miles, still on its original engine. Arguably, 136,000 miles is not a good time to be fitting an engine lifepreserving device, as adding a Kleenoil filter will not ‘repair’ any damage already done internally. However, I had the fully stamped service record to prove it had been serviced from new up until the 120,000-mile mark when I took over ownership. From then on, it had been serviced religiously by myself with regular oil and filter changes every 5000-miles. The oil sample was taken at 151,000-miles having covered 16,000 since its last engine oil and standard filter change, way exceeding the recommended 6000mile oil change intervals. The Kleenoil filter had been changed, as recommended, in line with the standard factory intervals. The oil sample was taken from the filter head unit immediately after shut-down and although the sample oil was every bit as black as regular dirty engine oil, Kleenoil assured me this was quite normal in diesel oil.
Chunks of the sample results taken from the engine make for baffling reading with the use of words, phrases and elaborate graphs only a respected professor in chemistry would understand. However, the one thing I could decipher was the all-important summing up of the oil sample findings at the bottom of the very last page. The sample analysis was carried out by Moniton Ltd and the results read:
‘All additives are at the top of the range expected from a new oil...Viscosity at 82.9 centistokes at 40C is normal. Borom and Sodium levels indicate no coolant leak. This is confirmed by the absence of water. There is a low level of silicone which is a clear indication of oil and engine cleanliness and that the air filter is working correctly.’
It continues: ‘Wear metal traces are all low and indicate that very little wear has taken place during this oil change. Conclusion: Oil is still in good condition and fit for further use with an adequate additive reserve. Viscosity is similar to that of new engine oil. Extremely low contaminant level, no water present and no evidence of wear being shown’. Remember this was oil that should have been past its sell-by date. I think you’ll agree, having read the results, they are not bad for a 300Tdi that’s now showing 157,000 on the clock. Moreover, reading the results of the Kleenoil test, it looks like it’s set to be going strong for a few more miles. Thank you Kevin.
And whilst the demand for road transport engine filtration has dwindled over the years, the demand for by-pass filtration in hydraulics has accelerated – primarily down to the finer tolerances in pumps and production machines, resulting in the demand for offline filtration in the form of Mobile Filtration Systems; often better known as filter carts.
Remove DIRT & WATER in the same mobile application
Affordable and easy to change out replacement cartridges
Kind to the planet – as a natural, sustainable product
Save waste costs, replacement value and labour
Simple ‘plug and play’ application
Site permanently on a problematic machine or on a rotational cleanse across your fleet
Whether it be to tackle one off contamination issues, or as a permanent fix to heavy use equipment to protect pumps, valves & cylinders etc.. or as a rotational cleanse on off-hire equipment.
KLEENOIL offer a completely free trial at your site ; with before and after independent oil analysis.
Why Cellulose Depth Filtration still remains one of the best techniques in cleaning your working oils ‘to as good as new’
Generally, all filter carts are simply…
• a chosen filter, or multiple arrangement of filters,
• powered by an electric pump and motor,
• on a mobile or fixed framework,
• with feed and return pipe.
The complexity is in firstly the application, its oil type, temperature and dirt or moisture load; and then the choice of filters, followed by the choice of pump and its flow rates.
But not all carts are the same
• An off the shelf cart may give a reasonably fast flow – but to do this will not offer a fine level of filtration, usually as a spin on filter so may be around 20-40 micron at best. These are useful for quick fluid transfers and usually quite compact and light so easy to move around, but don’t expect fine levels of filtration.
• At the other end of the spectrum there are a variety of specific applications to which some carts are sold. These can become quite complex and large with staged filters, load indicators, particle counters and water sensors. These will cost tens of thousands and unless permanently fixed, become hard to manoeuvre and often, through their complexity, quite temperamental.
• Cellulose depth By-pass filtration sits neatly between these two extremes
By-pass or Kidney-loop filtration is by far the best method of offline filtering often fixed permanently to an application where current filtration is insufficient – usually in harsh environments or under demanding workloads and equally effective as a ‘quick cleanse’ to alleviate dirt levels or resolve unexpected water contamination.
An old but reliable technology; in this case, each metal vessel tightly holds the vital filtration cartridge. Made of tightly packed, long fibre cellulose, this allows the oil to travel up the centre and push down slowly through the entire thickness of the cellulose media. This ‘depth’ matrix is used to trap suspended particles, separating them from their carrying fluid. Working by adsorption and absorption, it has the unique filtration ability to not only trap the particulate, but also moisture. Depth filtration is most commonly applied in ‘polishing fluid’ applications as it takes filtration to a much finer level! But that is no reason to underestimate its ability and benefits in keeping any tank of oil continuously cleansed and dry. And with cellulose depth filtration, slow and steady is key to the best results… allowing fluid to move slowly through the DEEP media to optimise results, as opposed to forcing it at high flow which can open up channels and allow for by-pass. This means in correct operation it only has one level of filtration; down to 3 micron particulate.
The Benefits of cellulose depth filtration as a cart
• Removes dirt and water in the one same application
• A finer level of filtration to remove particulate down to 3 micron
• Removes water – emulsified or free
• Affordable and easy to change out replacement cartridges
• Kind to the planet – as a natural, sustainable product
• Use of filter tops as a visual test
• Can be used as a transfer unit
• Simple ‘plug and play’ application
• Situates easily next to the sump/tank to be cleaned – either permanently or on a rotational cleanse
Why would you need a filter cart?
• To simply clean new or used oil in transfer from storage to machine, or vice versa
• To clean oils used in test runs rather than wasting
• To offer rotational oil cleanses of machines in the factory
• To add as a permanent installation to a machine where OEM filtration is inadequate
• To resolve a one-off contamination or cleanse after repair work
• To clean old, stored oil for reuse – with sampling
Know what cleanliness level you want to achieve
The most important part of any filter or filter unit is which contaminants are being filtered out. Know what your oil cleanliness targets are (generally 3 microns for hydraulic fluid and 6 microns for gear oils) or do you have ongoing moisture issues?
In either case, it’s always best to determine the source of any contamination. Whilst filtration is always important even in clean systems, you may be masking an issue that needs addressing first. Some companies want to achieve a suggested ISO target, and this will be in your oil analysis testing or particle counting.
Consider the dynamic oil film thickness in gears, roller bearings and servo valves. They are all less than 3 microns. Hydraulic systems are particularly susceptible to dirty fluid problems because of all the moving parts that are often operating in the dirtiest, harshest conditions.
Any filter cart is purchased to clean oil – and all will do it in some way or another – usually as a ‘rock catcher’; entrapping larger 10 micron + particulate in a reasonably fast flow.
Yet for particle contamination, the big concern is silt-sized particles in the 1-micron to 10-micron size range. While tiny — less than 1/10th the thickness of a human hair — 3-micron silt-sized particles, which are no bigger than a red blood cell, are as much as five to ten times more likely to cause failure. That’s because many filters are not designed to remove such small particles, coupled with the fact that dynamic clearances (the separation between moving parts under operating load, speed, and temperature) in pumps and valves are typically in the 1-micron to 5-micron size range.
After hard particle contamination, water is the second most damaging contaminant found in hydraulics. Present in most fluids, even in the cleanest environments, water can increase failure rates 10-20 fold depending on circumstances.
Water causes problems in a number of ways – first, any iron or steel surface in contact with water will, of course, start to rust. This can induce premature failure due to corrosion, as well as introduce rust particles into the fluid.
New oil may look sparkly – but it is a rare test that sees it so.
And clean oil put into a dirty machine just gets dirty!
This oil sample result is from a refurbished baler machine – cleaned out and filled with brand new oil - first sample before first use. The high silicon is indicative of the work done and new seals etc, but contamination counts at 4, 6 and 14 are the crucial indicators of the levels of contaminant taken in a small sample!
New oil should have an ISO of around 18/16/13, yet this was at 22/20/16.
Hydraulic systems are typically subjected to hard use and feature very tight tolerances to help keep out the bad stuff. That means when dirt and debris from wear and tear get into the system, they can cause a lot of damage quickly. From pumps to valves, cylinders to motors, hydraulic systems depend on clean oil to keep running smoothly and even the smallest particle or drop of water can cause big problems.
The type of oil inside your machine plays a significant role in determining which oil filter cart you should buy. If you were to pump viscous oil quickly, you’ll encounter air bubbles forming inside the machine which could damage pumps and oxidise oil. Cellulose depth works on cleaning oil slowly and continuously and so can be more effective as a constant permanent install.
Hydraulic systems depend on clean oil to keep running smoothly
You will generally want to know how much oil will be cleansed per hour – and the rule of thumb on offline filtration is to pass it through 7 times to achieve best level if a temporary install or rotational cleanse. When you use a filter cart, oil cleanliness is diluted by the dirty oil in the sump, since you’re taking oil from the dirty sump, filtering it and returning it to the same. So, to combat this dilution, the amount of oil in the tank must pass through the filter the seven times to get the same cleanliness you would get from single-pass filtration.
As an example, a Twinset Cellulose filtration set up with the appropriate progressive cavity pumps on standard 32 or 46 sec hydraulic oils at 40’ temp will run approx. 500 lph; so a 2 hr cleanse would be more than adequate.
Some sites will use a filter cart to transfer cleanse out to an IBC, thus allowing for a scrub of the tank and then transfer cleanse back to tank. But, in doing this, never forget that sediment will be in pipes and cylinders so as a machine starts up this sediment will push back to tank and re-pollute the cleansed oil. So, in a transfer cleanse, it would be still advised to leave the filtration on to tackle this remaining contaminant.
Keeping a filter cart robust and simple is key. These machines are moved around in often harsh environments with heavy handling and challenging applications, so need to wear their workloads, and this is what they are built for.
So, making a Filter Cart purchase is a worthy investment in any location where oil cleanliness is key to efficient operation. The use of secondary filtration can save a lot of wasted time, frustration, and resources.
The application not only allows for higher efficiency and better utilisation of time and productivity, but also has an impact in lowering operating costs by reclaiming and extending the useful life of the oil and components, and lowering yearly waste oil handling.
And don’t underestimate a filter cart as a permanent application
It is all very well cleaning oil in an application – but if it’s just to get dirty again it’s still going to cause the wear and tear associated, so why not consider a permanent install ?
A machine with constantly cleansed oil is going to outperform its counterparts.
There are a huge range of filter carts on the market now, favouring many makes of filters, and our general consensus would be that ‘any’ extra filtration implemented must be an asset.
But, if you want to go that extra level –then Cellulose Depth filtration will take you there.
Free tickets are now available for the 2023 RWM Expo, the UK’s premier event for professionals working in the recycling, resource, waste, sustainability, and wider environmental services industry. Formerly known as RWM & Letsrecycle Live, the event provides a platform to connect with others, learn, and drive positive industry and environmental change via discourse on sustainable resource management. The exhibition takes place on: 13-14 September 2023 at the NEC, Birmingham.
You can secure your FREE ticket by visiting https://hubs.la/Q01-16780
Remember, one FREE ticket gains you access to all co-located events
This year will see RWM become part of the Environmental Services & Solutions Expo (ESS), forming the UK’s largest event dedicated to the environmental services industries. This massive show attracts an audience of 12,000+ professionals from diverse industries, making it the UK’s largest gathering focused on resource management, recycling, and sustainability.
The ESS conglomerate of events stems from a series of environmental B2B shows uniting under one roof at the NEC, giving rise to the ESS Expo. This overarching show now forms the ‘umbrella’ event for the following renowned exhibitions: RWM (Resource & Waste Management Expo), EFD (Energy, Fuels & Decarbonisation Expo), FWM (Flood & Water Management Expo) and CLR (Contamination & Land Remediation Expo). This represents 360 degrees of the environmental sector in land, water, air, and energy. By claiming your free ticket, you’ll gain exclusive access to all four co-located shows, along with a staggering 100+ events scheduled over the two days.
The trade show and conference brings together industry leaders, forward-thinking entrepreneurs, and eco-conscious professionals to collaborate, learn, and inspire one another towards a sustainable future through ground-breaking new technologies, strategies, discussion, and policy making.
Meet the sector’s most influential brands: Get ready to meet and do business with over 400 world-class suppliers, and take advantage of free consultations, product demonstrations, and tutorials that will leave you with powerful new connections, business partnerships, and actionable insights that truly enhance your operation. View the full exhibitor list and see who you could connect with this year: https://hubs.la/Q01-1xk50
World-class conference programme: You’ll have the chance to learn from 300+ expert speakers, keeping you updated on the latest trends and breakthroughs. Free-to-attend and all CPD-accredited, you can gain some truly unique insights into the latest and greatest strategies, technologies, and solutions for sustainable resource management - all from the sector’s leading minds. There are 6 dedicated theatres to check out – The Keynote Theatre, Local Authority Theatre, Materials Village Theatre, Circular Economy Theatre, Packging & EPR Theatre, and The Future Talent Hub, an area dedicated to championing the rising stars of the industry as well as exciting new startups and initiatives.
h
S t a y a t h e l a t e
e w o r l d - c l a s s , f r e e - t o - a t t e n d c o n f e r e n c e p r o g r a m m e i s f i n a l l y h e r e !
h e a d o f t h e c u r v e b y h e a r i n g f r o m i n d u s t r y v i s i o n a r i e s a s t h e y e x p l o r e s t t r e n d s , s t r a t e g i e s , i n i t i a t i v e s , e m e r g i n g t e c h n o l o g i e s , s u c c e s s s t o r i e s , a n d c h a l l e n g e s f a c i n g t h e s e c t o r . F e a t u r i n g s e s s i o n s f r o m :
JO PADWICK, COCA-COLA EUROPACIFIC
F R E E T O R E G I S T E R !
PART OF THE UK'S LARGEST ENVIRONMENTAL EVENT
W W W . E S S - E X P O . C O . U K
Unrivalled networking opportunities: We all know how important social events are for facilitating unique and bespoke business opportunities, and there’s no shortage of them over the course of the two days at RWM. From AGMs, to industryspecific forums, to award presentations, breakfast briefings and private meetings, ESS Expo caters for all business needs. Read on to find out more about what’s on!
Vehicle & machinery demonstrations: If meeting the exhibitors in person wasn’t enough, get some up-close and personal live displays of cutting-edge machinery and sustainable waste management solutions to get a better understanding of how the apparatus works in its intended environment. The demonstrations are broken down into two distinct sections:
The Trucks in Action area focuses on collections, transport and street cleaning vehicles; showcasing the latest advancements in equipment, technology, and best practices for efficient urban cleanliness and sustainable waste management. Expect to see smart solutions for route optimisation to green, ecoconscious practices for reducing waste, improving recycling rates, and reducing pollution. The Live Demonstration Area focuses on larger, more industrial equipment involved in material processing, handling, dust suppression, fire detection and prevention, crushing, and heavy transport. Expect to see the cutting-edge machinery for effective and sustainable resource management that maximise efficiency, conserve resources, and reduce environmental impact.
Immerse yourself at the forefront of the environmental industry: Get ready to rub shoulders with thousands of key players hailing from across the waste and recycling sector. This is a golden opportunity to forge valuable connections and discover new perspectives. From influential thoughtleaders, to up-and-coming new startups, visitors will be able to meet and learn from the best and brightest the industry has to offer.
Four shows in one - drive positive change: Secure your free pass to ESS Expo, and you’ll also be able to walk between the co-located events - RWM Expo, EFD Expo, CLR Expo, and FWM Expo! The expo will be a melting pot for key discussions surrounding vital topics like achieving sustainable resource management, net-zero emissions, embracing circular economy practices, reducing your carbon footprint, material handling, and recycling strategies. Secure your FREE ticket by visiting https://hubs.la/Q01-16780
Visitors will be able to hear from more than 300 experts and key industry figures in the conference theatres, do business with over 600 world-class suppliers, see the latest innovative equipment and vehicles in the demonstration areas, and make powerful new connections at dozens of exclusive networking events designed to bring the industry together and spark meaningful change. Also featured will be an on-site pub, street food market, live music, and a host of special guest appearances.
Conference programme highlights
Key highlights for 2023 include headline speaker sessions from climate campaigners, environmental experts and numerous world-class thought-leaders in recycling, resource and sustainability. This includes interactive talks from Blue Planet II Executive Producer James Honeyborne, the Financial Times’ Moral Money Editor, Simon Mundy; and awardwinning environmental campaigner Tristram Stuart. Deputy Director of Department for Environment, Food & Rural Affairs (Defra) Chris Preston, environmental campaigner Natalie Fee, and EMEA President of Starbucks Duncan Moir will also be sharing their unique insights into the future of the sector, best practice, and mapping out a clear path ahead.
Other highlights include:
Leaders in Resource Management Panel at the Keynote Theatre with Gary Mayson; COO; SUEZ Recycling & Waste Recovery; Biffa; Neil Grundon, Chairman of Grundon, and Mike Maudsley, Chief Executive of Enfinium.
General Markets at the Materials Village Theatre with Paul Sanderson, Chief Executive of the Recycling Association and Chris Burton, Managing Director at IWPP.
IOSH Environmental Waste Management Group with WISH - including:
• The hidden dangers of lithium battery disposal with WISH and Newcastle University.
• Waste management for small to medium enterprises with IOSH and WISH.
• Workplace transport, site safety and waste collections with WISH, and WISH.
• Training and competence within the waste management industry with CIWM, SWITCH, IOSH EWMG and more.
• Mock Trial: Machinery incident investigation with WISH and WIllis Towers Watson.
There’s a host of exclusive and exciting free-toattend networking opportunities taking place within the expo over the two days; here’s just a handful of them. For more information on locations and timings, please visit the website.
Women in Sustainability Breakfast Meeting: Women in Sustainability is a networking platform for men and women in our industry. Explore factors that can positively influence or constrain a women’s career and work choices and share success stories from within the waste, recycling and sustainability sector.
The 35 Under 35 Awards: Letsrecycle.com’s 35 UNDER 35 is an exciting awards programme that identifies the rising stars and trailblazers in the waste and recycling industry who are striving for professional excellence, promoting industry innovation and giving back to their company or community. The scheme is open exclusively to those who work in the waste, recycling or organics industries and you can nominate yourself or on behalf of a peer. The shortlist and top three candidates will be announced live at RWM, in the Future Talent Hub. Free to enter and free to attend!
Zero Waste Recognition Scheme: The Zero Waste Awards is the UK’s premier recognition scheme for businesses and organisations that are committed to increasing the amount of waste they reduce, reuse and recycle. Enter free to join the network of sustainable thought-leaders that are reducing the amount of waste in their business operation, driving resources up the waste hierarchy, and contributing to a more sustainable society. Free to enter and free to attend!
BSI Group Net-zero Seminar: BSI Group will provide insights into their net-zero week - a weeklong program featuring a series of online webinars which delve into specific sectors; exploring the implications and opportunities surrounding the concept of net-zero.
Following the presentation, you will have the unique opportunity to engage in meaningful networking interactions with BSI’s team of sector specialists. During this session, you can connect with experts who possess an in-depth understanding of specific sector challenges and can provide valuable guidance on navigating the journey towards net-zero.
Broaden your network, gain industry insights, discover innovative strategies for reducing your environmental impact, and explore potential collaborations with like-minded professionals who share a common goal of achieving net-zero. Fleet Managers Forum: A premier networking event exclusively designed for independent waste operators and fleet managers in the waste and recycling sector. This session offers a unique opportunity to connect with industry professionals and discuss the latest trends, challenges, regulatory updates, and innovations in fleet management.
TO
Expand your network, forge valuable partnerships, and gain insights from experts in a collaborative environment. Don’t miss this chance to elevate your fleet management strategies and contribute to a sustainable future. Event partners include Dennis Eagle, LAPV Magazine and UROC. To attend, simply turn up on the day for a tea, coffee and networking!
RWM is the ultimate platform to engage in critical discussions and explore ground-breaking green technologies, acting as an international springboard for innovative waste and resource solutions that address the world’s environmental challenges. As the United Kingdom’s top meeting place for waste and recycling activities, in addition to land, air, energy and water services through the co-located shows, it is unmissable for anyone working with or selling into Europe.
In 2022, over 9000 professionals gathered to see industry innovation and hear updates from 200+ expert speakers. The event spans 3 exhibition halls and a large outdoor area for equipment, machinery, and vehicle demonstrations.
Organised in partnership with leading organisations including the Chartered Institutes of Wastes Management, Environmental Services Association and letsrecycle.com, get ready to connect with the biggest players and access need to know insights; all in one place over two action-packed days at the NEC, Birmingham.
The full programme of networking events, speaker sessions, workshops, talks, and live demonstrations will be released in the coming weeks.
https://hubs.la/Q01-1dCK0
Remember – one FREE ticket gains you access to all co-located events.
BE THE FIRST TO HEAR ANNOUNCEMENTS, REGISTER FOR YOUR FREE TICKET NOW
At SMT GB, this expectation is taken seriously, and made into a reality thanks to the essential efficiency and productivity boosting services and solutions available for all SMT GB customers.
The first essential tool made available to the modern Volvo machine fleet manager is CareTrack, which is the Volvo Construction Equipment telematics system that gives customers access to a wide range of machine monitoring information. Designed to save time and money, customers using Volvo CareTrack can reduce fuel costs, optimise machine and operator performance, and proactively manage services and maintenance to maximise uptime.
An advanced subscription to Volvo CareTrack is also available, which allows customers to view critical operational data from each machine in within their fleet, such as fuel consumption, machine utilisation and idling data, as well as productivity reports where customer machines are fitted with on board weighing technology.
The next essential tool available for all SMT GB customers is the ProCare advanced machine monitoring service, which aims to maximise individual machine uptime and performance, while minimising unscheduled maintenance, breakdowns and repairs, as well as their associated costs.
Possessing the ability to make data-driven decisions is a core expectation of the modern fleet manager, and having the ability to turn insight into action is more important now than it has ever been.
By combining multiple machine data sources and oil sample reports, SMT GB’s highly experienced and qualified ProCare analyst team can monitor the health and performance of individual machines within a Volvo fleet remotely, and flag any potential issues before they have the opportunity to develop into major faults.
If a machine fault is flagged, the SMT ProCare monitoring team will devise bespoke recommendations for customers, which are aimed at providing a solution to any of the issues flagged that will causes minimal disruption to site productivity, while also maximising the overall performance and uptime of the machine, with one such example being, where possible, to investigate or resolve the flagged issue during a scheduled service appointment, as opposed to arranging for the machine to be taken out of the production cycle unnecessarily.
Not only does this proactive approach provide considerable peace of mind to customers, but also helps to prevent breakdowns, leaving Volvo machine fleet owners and managers with more time to focus on core operations.
With individual Volvo machine and fleet performance well covered by SMT GB’s available solutions, next on the list of peace of mind providing solutions is SMT GB’s Customer Support Agreements, which are designed to suit the budgets and fleets sizes of all SMT GB customers.
With three levels of Customer Support Agreements available, maintenance costs are reduced to a fixed monthly payment, and machine uptime is maximised, as servicing is arranged and carried out proactively by SMT GB’s team of highly experienced and qualified team of mobile engineers.
This proactive approach provides considerable peace of mind to customers, and also helps to prevent breakdowns
To protect customer machine investments even further, SMT ProCare and an advanced subscription to Volvo CareTrack are included as standard in both the Level 2: Enhance or Level 3: Optimise Customer Support Agreements.
Designed to empower the modern fleet manager even further, SMT ProCare, Volvo CareTrack and all of the details and associated paperwork for all active Customer Support Agreements are also accessible via MySMT, which is SMT GB’s secure new customer selfservice portal that is freely available to all SMT GB customers.
Thanks to the secure, web-based portal, customers can quickly and easily access, monitor and act on multiple aspects of fleet management both from the office, out onsite or on the move.
Making sure that all of the information stored on MySMT is easily accessible, the platform is divided into the three distinct areas:
“Company”, “Fleet” and “Parts”. Company provides customers with visibility of financial transactions with SMT GB, all active CSA and Warranty contracts, oil sampling reports, ProCare recommendations and Service Inspection Reports.
Fleet provides customers with access to current fleet details, including location, operating hours, information of fuel consumption, productivity data, CO2 emissions and visibility of repair and maintenance data on all machines within a customer’s fleet.
Parts provides access to the newly launched SMT online parts store, allowing customers to look up and order all genuine Volvo parts 24/7, with access to technical drawings if required. MySMT also provides customers with their own ability to create multiple staff user accounts based on varying levels of access and visibility options.
This ensures that all staff responsible for the monitoring and administration of their fleet benefit from MySMT, and that key decision making processes are preserved within the original arrangements of the customer’s management structure.
When it comes to live data feeds, customers often rightly point out that it can be difficult for machine to obtain a strong enough signal to transmit data, especially in remote areas. However, to alleviate this issue, SMT GB have recently introduced Connect Support.
Utilising cutting-edge mobile data technology, Connected Support ensures that machines, fleets and their managers are kept in constant contact.
By employing IoT roaming, machines equipped with Connected Support are kept in constant two-way contact with the cloud via the strongest available network to their current position. Not only does this remove the risk of poor signal causing the loss of real time data insight, but also improves the reliability of Co-Pilot apps and ensures that the machine’s software is kept constantly up to date, ensuring that the customer is able to get the most out of their machine at all times.
Available with a choice of 12 or 36 month contracts, and with data allowances of 1Gb or 5GB, Connected Support can be tailored to the specific requirements of a customer.
Connected Support subscriptions include dedicated remote support from SMT specialists to help customers ensure assets and sites are connected and actionable insight is being communicated.
SMT GB is the exclusive dealer of Volvo Construction Equipment and K-Tec Earthmover products in Great Britain. In addition to delivering industry-leading product support, SMT GB also provides a range of end-to-end solutions, which ensure customer investments are protected and profits are maximised.
To learn more about SMT GB, please visit: www.smt.network/gb
Cutting-edge mobile data technology ensures that machines, fleets and their managers are kept in constant contact
With ProCare, SMT analysts monitor the health and performance of your machines remotely, creating bespoke recommendations if a machine intervention is required.
Multiple data sources are combined to identify hidden issues that together could potentially impact equipment productivity and performance. Taking a proactive approach helps to prevent breakdowns and leaves you more time to focus on your core operations.
It doesn’t matter what the job is; big, small, simple, ridiculously time consuming and fraught with difficulty… you’ll want the right tools for the task. But in the innovative world of technology, where we are lucky enough to have a wealth of options to choose from, how do you choose? Don’t worry, we’ve got it handled!
Future Waste has the scoop on two of the top companies for Waste Handling attachments. We were lucky enough to speak to both about what sets their companies and products apart from the crowd. No matter your worksite, task or waste material, Invicta and Albutt have you covered with their extensive range of attachments, industry knowledge and years of reliable customer service.
Albutt started life as a family business with roots in farming. In fact, over four generations of the Albutt family have been involved in agriculture. You might be wondering then, ‘why are they on a list for the top waste handling attachments?’
Well, speaking to Tom Worthington, General Manager of Albutt Ltd, he told us: “We work up to a standard rather than down to a price. If we wouldn’t use them on our sites, we wouldn’t expect people to use them on theirs.”
Albutt is well known as the heavy-duty option in the specialised industry of attachments, and this onus on building strong is what led them to delve into the world of waste. The Waste King range was a direct result of the 50 years of work Albutt has contributed to agriculture. The Waste King Bucket Grab was the first of the waste products designed, and using their agricultural background, Albutt created the perfect tool for green waste handling solutions. This led them to design the Waste King range; attachments that can be used far beyond the farm and out in the global market.
In the waste attachment market, there is no product that can rival the strength and durability of the Waste King Bucket Grab. It’s use of high tensile materials such as Strenx and Hardox means that the grab is renowned for its heavy duty build quality. This is absolutely the reason it is used and trusted by some of the waste and recycling industry’s leading names. The sheer strength means that there is no chance of tipping due to heavy weighting on one side. The Waste King Bucket Grab is now also available in a compact form.
FEATURES
• Integral spill guard
• 50mm grab pivots with self-lubricating bushes
• Hydraulic rams bushed
• Armoured hoses
• Hydraulic rams protected by bolt on ram guards
• 3-piece HB500 bolt on reversible toe plate
• Split 2-piece grab
• Hydraulic rams cushioned
• Genuine Hardox grab tines
• Corner gussets
• Brackets included
• Rolled bucket profile
• Wear strips underneath bucket
Albutt is well known as the heavyduty option in the specialised industry of attachments
Waste King Composting Fork
The ultimate tool for green waste, compost and other types of loose waste. The solid back made with Strenx is designed for maximum strength at minimum weight, and the fork uses genuine Hardox tines, which are renowned for their resistance to bending, meaning a long operating life for your attachment.
FEATURES
• 1650mm long genuine Hardox tines
• Brackets to suit your machine
• 200 x 100mm heavy duty tine holder
• Wear strip to underside of fork tine holder
• Hardox side tine on each side
• Suitable for loading shovels and telehandlers
• Solid fork back protects headstock and hydraulics
• Cut outs in fork back for visibility
Waste King Fork and Grab
Albutt is well known for strength and durability being its winning factors, and the Fork and Grab is no exception. Performance will always be the deciding factor, and the Fork and Grab has been designed with this in mind.
FEATURES
• Genuine Hardox tines
• Grab pivots bushed with self-lubricating bushes
• Hydraulic rams bushed
• Open grab dimension 1980mm
• Wear strip under tine holder
• Welded fork tines
• High-capacity hydraulic cylinders
• High grade pins throughout
• Solid fork back with strategic cut outs for visibility
• Weld on brackets integrated into fork
Designed for Loading Shovels working in high intensity environments, the Waste King GP Bucket has a shorter floor length than a standard bucket, making it ideal for more heavier, denser and stickier material such as sand or concrete.
FEATURES
• Sizes from 2.50m3 to 4.00m3
• 9ft wide (2743mm)
• Integral spill guard
• Bolt on reversible toe plate (boron 500)
• Heel pads (boron 500)
• 30mm underside wear strips
• Side stiffeners
• Quick attach brackets included as standard
Based on the same principle design as Albutt’s ultra popular Push Off Buck Rake range, the Push Off Fork utilises the trust strength of all Albutt attachments to make it suitable for a variety of applications, particularly when it comes to green waste.
FEATURES
• 1650mm genuine Hardox base tines
• Side tines
• Flow divider valve helps to prevent gate twists on uneven loads
• For use with Telehandlers and Loading Shovels
• 200 x 100mm base tine holder
• 60mm diameter main pivot pin
• Double profile gate mounting prevents arms bending
• 35mm diameter ram pivot pins
• 75mm ram bore size
To learn more about Albutt, please visit: www.albutt.com
As the UK’s largest mechanical forks and forklift attachments manufacturer, it is no wonder that Invicta has so much to offer in the world of waste management. Everything is manufactured in house, meaning they can provide you with your bespoke solution within a matter of days. Invicta attachments mean your worksite, irrespective of the size, can remain well maintained and looked after.
Aarron Hume, Sales Director at Invicta Attachments said it best: “With over 30 years of experience, we help businesses save time and reduce risk. Safe and efficient waste handling begins with the right tools for the job. Our team has monthly technical training on products, and we always ask about the working environment and application to make sure the recommended attachment is fit for purpose.
“We have an extensive range of attachments in stock and can despatch items immediately. When a customer is having trouble with a waste handling process, we investigate and design a bespoke product, like these rubber lined skips for handling brick waste or the window-lidded skips for collecting bi-product. No problem is too much trouble. It’s incredibly satisfying to solve a waste handling problem with an attachment that saves the customer time, money, and frustration.
“The durability of our attachments is important. Our products are British manufactured at our site in Leeds, and our ethos is to build once and build well. We reuse and repair forks and attachments, enabling customers to get longevity from the attachments they rely upon. Every product complies with industry standards, including LOLER guidance, to protect the safety of employees. We are committed to our customers having the very best experience when they trust us to solve their waste handling problem. It’s what we call ‘The Invicta Difference’.”
Combi Skip
The uniquely designed ‘4-way entry’ base makes the handling and disposal of material in confined spaces simple and easy. Manual operation is standard, but if needed, automatic tipping at high level can be achieved by ordering the conversion kit. This allows the forklift / telehandler operator to remain in the safety of their seat whilst tipping.
FEATURES
• Low loading height
• Reinforced leading edge and body sides
• 4-way fork pocket entry
• Secondary Locking Mechanism to prevent accidental discharge
• Fully seam welded for retention of fluids
• Manual handle override
• Maximum fork section 150 x 50 mm at 675 mm centres
• Zinc plated heel pins for safe attachment to truck
• Bright orange for safety
The Fork Mounted Sweeper
Otherwise known as ‘The Basil’, this wily attachment is the best solution for re-heaping loose granulated waste like grain, soil, sand and more. ‘The Basil’ is available in 4 width combinations and 2 brush row combinations.
The ECO Range - The 5-row sweeper for lighter duty tasks.
The Standard Range - The 8-row sweeper for heavy duty tasks.
FEATURES
• Interchangeable blue nylon brushes
• Facility to hang Fork Mounted Magnet from the frame
• Zinc plated twist screws for safe attachment to truck
• Bright orange for safety
Skip Compactor
Given that the content of most full skips is at least 40% air, it makes sense to have a tool on hand to maximise waste capacity. The Skip Compactor, filled with ballast, ensures that this percentage is dramatically reduced, meaning less time and resources are wasted.
FEATURES
• Adjustable height to suit up to 8ft deep skips
• Heel pin locking for the safe attachment to forklift truck
• Bright orange for safety
The Wheelie Bin Lifter
In waste management, wheelie bins are ever growing in popularity, so the need to deal with them efficiently is paramount. The Invicta Wheelie Bin Lifter was designed with safety in mind; able to lift, move and empty 660-1100L bins.
FEATURES
• 50 – 1 geared gear box
• 6 metres endless chain
• Ratchet tensioner strap to leading edge
• Zinc plated twist screws for safe attachment to truck
• Bright orange for safety
Fork Mounted Multi Scoop
Instead of a loading shovel, why not let your forklift become the multifunctional asset it’s destined to be? The Multi Scoop is perfect for the loading a variety of loose materials into collecting vehicles.
FEATURES
• Secondary locking mechanism to prevent accidental discharge
• Removable toothed leading edge to cut into product and protect scoop lip
• 4-way Fork Pocket Entry
• Operating mechanism fully enclosed to protect against impact
• Maximum fork section 150 x 50 mm at 675 mm centres
• Zinc plated twist screws for safe attachment to truck
• Painted bright orange for safety
To learn more about Invicta, please visit: www.invicta-attachments.co.uk
We specialise in arranging a wide range of Commercial Insurance products as well as offering several bespoke and unique policies for the Waste, Recycling, and Haulage sectors.
We can provide you with a competitive quote for:
Commercial Vehicles and Fleet Insurance
Public and Employer’s Liability Insurance
Plant / Engineering Insurance
Property Insurance
Additional Covers
Why not give us a go?
Direct Contact:
Richard Morris
t: 01392 715866
e: richard.morris@gm-insurance.co.uk
t: 01392 426799
e: sales@gm-insurance.co.uk
w: www.gm-insurance.co.uk
GM Insurance Brokers Ltd
6a Cranmere Court, Lustleigh Close Matford Business Park, Marsh Barton, Exeter, EX2 8PW
Authorised and regulated by the Financial Conduct Authority
Independent Insurance Intermediary
Registered in England No. 05058019
Proudly supporting
HELPING YOUNG HEARTS
Vapes and e-cigarettes are now a very popular alternative for smokers in the UK. Businesses of all shapes and sizes have quickly become familiar with these products, prompting new workplace changes to account for different smoking habits.
The product concept is fairly simple. Soak a cotton-wrapped, high resistance coil with e-liquid from a pre-filled pod, then heat the coil using a lithium battery to vaporise the liquid and simulate the draw of a cigarette.
Disassembling and safely recycling these devices, however, is a far more complex and labourintensive operation. As a type of WEEE (Waste Electrical and Electronic Equipment), vapes and e-cigarettes cannot be mixed with other wastes and require a separate waste container for disposal.
Due to the battery encased within the device, explosive chemical fires are caused by incorrect disposal of vapes and e-cigarettes. Put simply, these devices must not be placed in any skip or bin under any circumstances.
This is a UK-wide issue for the waste and recycling industry, and we are committed to being a part of the solution. Our safety flyer is available online and free to download.
Recycling vapes and their lithium-ion batteries is the best way to prevent fires and it also extends the lifespan of our planet’s limited resources, bringing us one step closer to a circular economy. We can only achieve this by working together across all UK sectors.
Website: www.kennywastemanagement.co.uk
The vapes and e-cigarettes market has seen dramatic growth over the past decade, leading to 1.3 million single-use vapes currently being binned every week. However, public infrastructure has not kept up.
Last year, according to research from our industry partners, over 50% of the UK public reported that they did not know how to properly dispose of these devices.
Domestic consumers are demanding a more straightforward route to disposal, but presently the only consistent route for UK households still relies on individuals taking their own vapes to their local HWRC (Household Waste Recycling Centre).
Businesses, on the other hand, can easily access reliable vape and e-cigarette waste management. Wherever you are in the UK, Kenny Waste Management offer a range of convenient recycling solutions to suit your project, budget, and space.
Our customers value our best practice approach to compliance and recycling. Based on your sustainability needs, we are working in partnership with a state-of-the-art Approved Authorised Treatment Facility (AAFT) to safely recycle all vape and e-cigarette types from anywhere in the UK. Whether you are a national construction company, a large retailer, or local organisation, we can help you stay complaint and keep your essential vape recycling within your waste management budget. Kenny Waste Management can provide secure, separate solutions for your vape, e-cigarette, and battery waste recycling. Act now and help us to eliminate fires by ensuring that your devices are safely recycled.
Vapes, e-cigarettes, and other devices that contain lithium-ion batteries pose a severe fire risk and must not under any circumstances be placed in any skip, wheelie bin, or non-specified container. As soon as the anode connects with the cathode in a discarded device, the battery undergoes an explosive process called thermal runaway. The resulting chemical fire is extremely difficult to extinguish.
As such, any vape or e-cigarette poses a serious fire risk as soon as it becomes damaged. This can occur in the compaction mechanism of a bin lorry, the shredding of mixed waste for further processing, or even in day-to-day situations where a vape has become compromised. Separate, secure storage is the only viable option. Common examples of other items include: Electronic toothbrushes, device chargers and powerbanks, shavers and trimmers, powertools, flashlights, handheld vacuum cleaners, gaming controllers, bluetooth headphones and earbuds, and other wearable devices such as smart watches.
Our most popular solution safely holds up to 12kgs of mixed vapes, which translates to approximately 750 units. We find that this option can be tailored to almost every scenario. Collections and deliveries are bespoke to each customer’s needs. This solution is fully inclusive of delivery, collection, treatment, and Hazardous Waste Consignment Note.
If for any reason these standard Vape Recycling containers are unsuitable for your site, project, or business, we can help you select another option from our range. Just get in touch — we are happy to assist and identify the perfect vape recycling solution for you.