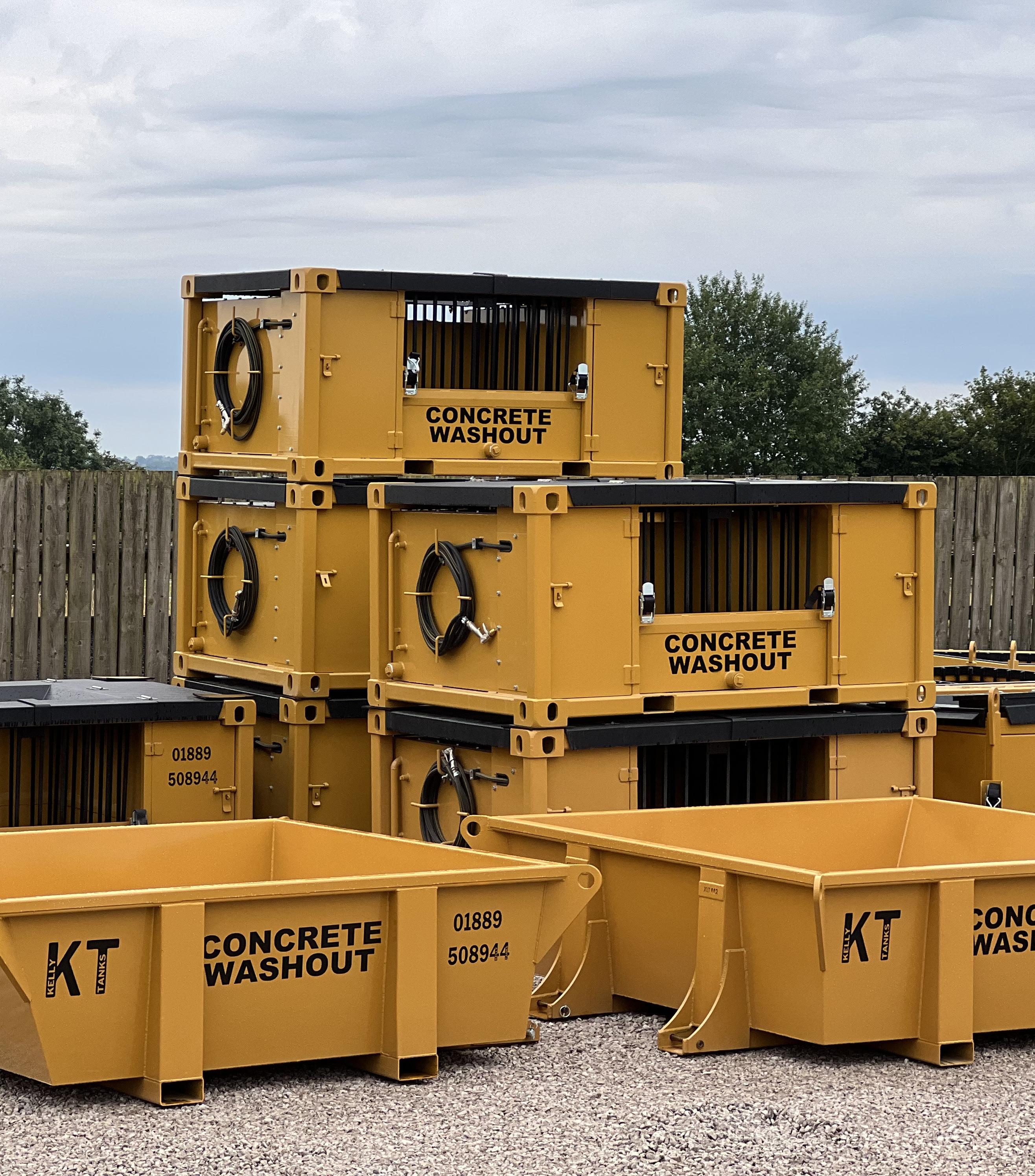


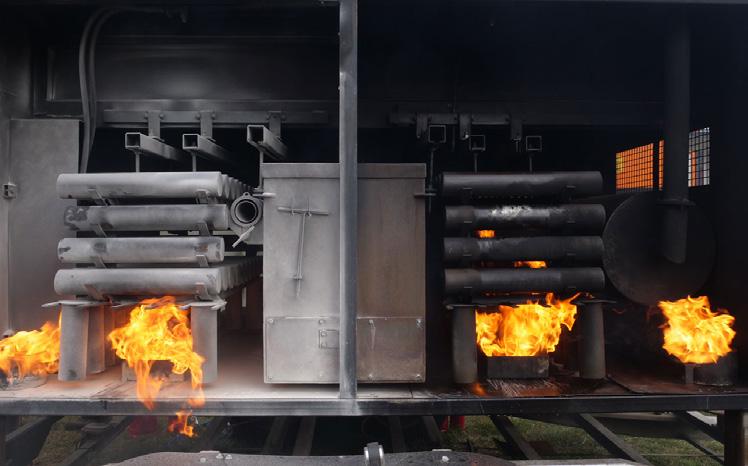
1. The Zonr system creates a virtual barrier around anything you attach it to using UWB technology.
2. If a worker enters the zone, they are alerted via a vibrating tag on their arm and an audible alarm.
3. The operator is alerted by an audible alarm and a flashing red light.
4. Incursion data is gathered and stored so you can monitor and manage how often incursions happen.
Zonr Base Unit
The Zonr Base Unit sits within the cab, typically beside the equipment operator. It provides an audible and visual alert to the operator if someone gets too close. The operator can also authorise incursions when needed.
The Zonr Tag is worn by your team and emits an UWB signal. If a user walks within the inclusion zone, it vibrates and emits an audible warning.
The Zonr Sensor ‘listens’ for UWB signals emitted by the Zonr Tags. If one gets too close, it alerts the Zonr Base Unit.
Zonr’s software gathers and stores data so that you can monitor the frequency of unauthorised incursions and improve over time.
Fastest to set up
Other solutions require specialist on-site support to deploy. Zonr can be deployed in minutes by anyone on your team.
The only wireless solution
You don’t want power leads and other cables getting under your feet. Zonr is the only fully wireless option on the market.
The most configurable Every site and job is different. Zonr’s custom exclusion parameters and authorised incursions make it the most configurable solution.
Zonr Tag Zonr Base Unit Zonr SensorZonr creates virtual safety exclusion zones that warn your workers when they’re getting too close to dangerous or moving equipment. Fully wireless Set up in minutes Easily moved from vehicle to vehicle Completely configurable exclusion zone
Keep your workers safe
Ensure duty of care to your employees and contractors.
Protect your reputation
Avoid HSE investigations and demonstrate health and safety compliance.
Reassure customers
Show prospects and customers that health and safety are in-hand.
Gather safety intelligence
Analyse incursion data to understand how often people breach exclusion zones.
Set up in minutes
Quickly and easily deploy or transfer exclusion zones as you work.
Set custom exclusion zone sizes and authorise incursions when you need to.
Welcome to our second issue of Future Waste! Future Waste had a successful launch at RWM & LetsRecycle Live as the all-encompassing UK show for the recycling and waste management sector returned for 2022 at the NEC Birmingham. You can read the full show review on page 44 of this issue.
This exciting November issue is full to the brim with over 80 pages, covering a wide range of news from the recycling and waste management giants, CIWM and Biffa, as well as a look at some of the great events of this year, including RECOUP’s plastic conference and The Big Sustainability Expo.
Be sure to check out our inspiring cover story from Kelly Tanks as Mark and Kelly, directors of Kelly Tanks, take us through the story so far and their ambitions for the future on page 56. Also in this issue, check out the impressive automatic fire suppression system for heavy machinery from Fireward on page 64.
Remember you can keep updated with the latest news via our website and social media pages and we look forward to seeing you for our next issue!
by Kiwi Media and Promotions Ltd
2nd Floor, 41-42 Southgate, Chichester, West Sussex PO19 1ET +44 (0) 1243 345 323
Kiwi Media and Promotions Ltd. 2022 all rights reserved. Reproduction in whole or part is prohibited except with permission in writing from the company. Note to contributors: articles submitted to the Editor for consideration must be the original work of the author. Where photographs are included that are not the property of the company or contributor, permission to reproduce them must have been received from the owner of the copyright. Any views or opinions expressed within this magazine are not necessarily those of the company.
ISSN: 2631-4622 Registered in England No: 09910499
All advertisements are accepted subject to the Kiwi Media & Promotions’ standard of insertion. For a copy of Advertising Terms & Conditions, please write to Darren Shelton at 2nd Floor 4142 Southgate, Chichester, West Sussex PO19 1ET
A round up of the latest news from the recycling and waste sectors over the past few months.
CIWM presents The Festival of Circular Economy and welcomes the new Modern Slavery protocols.
Future Waste takes a look into the effects of trade shows in the waste industry and how industry events are looking to take a more sustainable approach in the future.
CIWM presents The Festival of Circular Economy and welcomes the new modern slavery protocols.
resource efficiency and recycling charity, RECOUP, has published its 2022 UK Plastic Packaging Sorting & Reprocessing Infrastructure report, which found there is a clear bottleneck in the UK’s recycling infrastructure for plastic recycling.
The report, available to all RECOUP members, highlights the UK’s ability to sort both household and nonconsumer plastic packaging from other materials into separate plastic streams, and to reprocess it into raw materials and products.
RECOUP mapped the recycling facilities and researched the operational capacities in order to produce a number of scenarios to compare the requirements for recycled plastic packaging against the UK’s ability to produce the material. The scenarios looked at benchmarks set by both the UK Plastic Packaging Tax and if material export markets were no longer an option, something the UK relies heavily on to achieve its recycling targets.
This research found that significant increases are required for reprocessing plastic packaging in the UK. This includes the need to increase the current recycling infrastructure by five times for household-like plastic packaging and nine times for food grade plastic packaging. Unless resolving this reprocessing bottleneck is given the necessary priority and
investment, and ultimately, ownership, the UK will not be able to claim it has a world-leading recycling system.
RECOUP believes it is imperative that adequate funding through the reform of the UK’s Packaging Producer Responsibility System (otherwise known as Extended Producer Responsibility) goes to the right areas. The reprocessing infrastructure needs significant investment and support, particularly when these businesses are open to variable commercial conditions, such as increased energy costs and reduced material value.
Steve Morgan, Head of Policy and Infrastructure at RECOUP, commented: “The future of the UK’s recycling solutions for plastic packaging is in its own hands, but I’m afraid we
might let slip this perfect opportunity to channel appropriate funding into the high impact areas that could transform the UK’s infrastructure capabilities. Effective collection and material sorting to deliver high quality recycling outputs is essential, but we are at risk around not supporting the reprocessing sector. The capacity to produce the final raw materials to enable a circular economy to exist will just not be in place.”
As the UK looks to navigate its way through the many changing environmental policies, RECOUP continues to provide expertise and guidance for the plastics recycling value chain and policy makers. For information about becoming a RECOUP member, please contact enquiry@recoup.org.
Dulux Decorator Centre has received a staggering one million paint cans under its can recycling scheme
Thanks to the initiative, Dulux Decorator Centre is improving the environmental efficiency of the industry one can at a time by reducing the amount of con struction waste that ends up in landfill.
Dulux Decorator Centre’s free of charge can recycling scheme, in partnership with Veolia, the UK’s leading resource management company, is designed to make it easy for tradespeople to dispose of empty paint cans in a responsible and suitable way. Professionals can arrange for cans to be collected from site or can return them to store themselves, depend ing on what is easier.
The Dulux Decorator Centre team will monitor customers’ recycling and send them a certificate each year to certify how many cans they have recycled as a percent age. This can then be used to showcase a best practice approach to improving envi ronmental efficiency and reducing wasteand can even help to win new business.
Duncan Lochhead, Commercial Sus tainability Manager at Dulux Decorator Centre said: “As a champion of sustaina ble building practices, Dulux Decorator Centre is incredibly proud to have received one million paint cans under its recy
cling scheme. With our customers’ help, we are striving to increase the empty can recycling rate significantly and reduce our impact on the environment. According to the Construction Leadership Council, the construction of our built environment pro duces the largest waste stream by tonnage, and recycling paint cans is an easy way for the painting and decorating trade to do its bit and reduce this figure.
“Our can recycling scheme means that tradespeople can drop their empty prod ucts into us on their next visit. Also, if customers have partially full paint cans at the end of a job, we will work with them to donate it to good causes such as Com munity RePaint - a UK wide paint reuse network, sponsored by Dulux, that aims to collect leftover paint and redistribute it at an affordable cost – so nothing goes to waste.”
“This is a great example of an industry coming together to make a real difference to improve recycling. To reach our net zero goals we must take every opportuni ty to cut climate-changing carbon emis sions. By recycling high-density Polyeth ylene (HDPE) paint pots up to 88% of the carbon emissions are saved compared with using virgin materials, and using
recycled steel and tin saves around 60% of the emissions against extracting new resources. This is just the beginning of the journey and I encourage all in the industry to utilise this service as together we can make a huge difference to deliver ecological transformation.”
DONALD MACPHAIL CHIEF OPERATING OFFICERTREATMENT AT VEOLIA UKDulux Decorator Centre accepts a wide range of dry or empty metal or plastic paint cans including Dulux, Armstead, Dulux Woodcare, Cuprinol, Sikkens, and Ham merite. Cans that have contained emul sions, gloss paints, undercoats and primers, floor paints, exterior paints, and masonry paints - and those that have contained water-based or solvent-based products - can all be recycled under the scheme. Plastic cans are shredded, washed, and sent back into the plastics market, and metal is remelted into new steel and returned to the general market.
For more information about Dulux Deco rator Centre’s can recycling scheme, visit: https://www.duluxdecoratorcentre.co.uk/ can-recycling.
As of 25 October, parts specialist TVH may call itself SDG Champion. In deed, the company reached the second level in the United Nations Institute for Training and Research (UNITAR) sustainability trajectory.
TVH − a global player in the field of parts for forklifts, industrial, construc tion and agricultural equipment - was one of the first Belgian companies to receive the UNITAR certificate of SDG Pioneer in 2020. This constituted international recognition for corporate sustainability. Specifically, TVH garnered the highest praise during the last audit for its recycling efforts, ergonomic work environment, and extensive electric vehicle fleet and in frastructure. Now, TVH has also reached the next level, i.e. becoming SDG Champion.
Anton Theunynck, Global Sustainability Manager at TVH: “To our compa ny, sustainability is of strategic importance. This clearly helped to convince the jury, as did our choice to commit to specific SDGs, through targets and measurements. A final convincing element was our policy to have key actors, such as the board, management and focus groups, take on a specific role, all the while providing the necessary cross-pollination. We were also given some homework: translating all of this into bigger strategic actions.”
UNITAR wants to offer governments and organisations a compass for corporate sustainability, based on 17 Sustainable Development Goals (or SDGs). To receive UNITAR certification in Belgium, a company must realise actions for all 17 SDGs and obtain the Voka Charter Corporate Sustainabili ty at least three years in a row. TVH meets both conditions.
Veolia launches its new PlastiLoop offer at this year’s K 2022, the World’s No.1 Trade Fair for Plastics and Rubber, held in Düs seldorf, Germany.
This brand-new offer is made possible by Veolia’s extensive network of experts and its 37 plastic recycling plants around the world. It provides its customers with a large variety of high-performance ready-to-use recycled resins: PET, PP, HDPE, PS, ABS, LDPE, and PC. These circular resins can be fed into production lines in multiple industrial sectors, including Packaging, Textiles, Agriculture, Home and Applianc es, Automotive, Industrial and Logistics, Building and Construction.
Veolia’s offer is customised to meet its customers’ needs and can cover all or parts of the global plastics recycling value chain: waste collection, sorting, washing, com pounding and production of ready-to-use circular polymers. These circular polymers allow clients to cut their environmental footprints with no compromise on product quality.
The new PlastiLoop offer brings together all our technical and commercial exper tise in recycled plastics to provide our customers with the best possible support with customized solutions. It offers the strength of the Group, through its experts and its various recycling plants, to ensure the best access to recycled plastic deposits. Choosing recycled plastic not only saves resources but also achieves a considerable reduction in CO2 emissions, up to 75% less than virgin plastic. As a global champion of ecological transformation, through this offer, Veolia is creating more outlets for recycled material and promoting the struc turing of this sector worldwide.
https://www.plastiloop.veolia.com/
PlastiLoop, the new
The second National Drainage Show and Floodex is upon us, with a few changes since last year.
The National Drainage Show is still run in partnership with the NADC and Drain Trader magazine and a host of other organizations, such as: LoDEG, British Water, Environment Agency, National Sewerage Assoc, Pipeline Industries Guild, Water Magazine, UKSTT, Cleantech Business News and British Water. Future Water Assoc will be presenting part of their ‘Networking No vember Sessions’ in the NADC Theatre.
The NADC will again have a dedi cated seminar theatre on site, with a programme of CPD accredited pres entations and will again be showcasing DrainSafe and the NADC Hydrant App, which looks like it is proving invaluable to many. There will also be a special net working opportunity for NADC mem
bers, which will be hosted by Frank Bruno MBE.
There is an interesting spread of exhib iting companies such as Rioned, RSM Lining Supplies, Bucher Municipal, DCR Inspection Services, JFC Civils, FM Conway, IMS Robotics, Naylor Drainage, Reinert-Ritz, Wavin, Spartan Tool and many others.
Jon Irwin said, “It’s been a fantastic response, especially when you think what has been going on the last couple of years.” He went on to say “Everyone involved hopes this will continue to grow and become a major, annual focal point for the industry.”
The National Drainage Show is a great opportunity to mix with peers, talk to experts and see what products and services are new in your industry, or coming to market in the near future.
“We are still looking for an asset fi nance company to be at the show, ready to offer financing advice and offer ‘in principle’ loans for people looking to buy vehicles, plant and equipment.”
In Floodex, SuDS continues to rise up the agenda and there is a two day SuDS Theatre hosted by CIRIA and susdrain, whilst the Environment Agency is host ing a day in the Floodex Theatre.
Whilst Floodex covers all aspects of Flood prevention, defence and mit igation, there will be an interesting addition in 2023. As part of the holistic approach to water and water level man agement, there will be a third part to this important event, in the Waterways Management Show (WMS).
WMS will be all about the management of inland waterways in the UK, from keeping the waterways working in har
mony with urban and built up areas, to controlling water level management in rural areas, especially the lowlands. WMS will be a showcase for all the plant, tools and services involved in maintaining, repairing and renovating the UK’s rivers, streams, lakes and fens, along with the surrounding flora, fauna and infrastructure.
The colocated Floodex show will also de liver a big crossover of interested parties, that includes exhibitors and visiting contractors, construction professionals, civil engineers, drainage engineers, plan
ners, developers and local authorities. Part of the promotional ‘crossover’ includes the visitors to Homes UK, which is on at the same time. We have reached an agreement with the organ izers to co-promote our events, so that interested parties will hopefully visit both shows, whilst at ExCel.
You can register for a free ticket in advance at www.drainageshow.com & www.floodex.co.uk or do it on arrival. f you need further info, visit www.drain ageshow.co.uk or contact Jon Irwin on 07748 150004.
Following the release of their 2021 Sustainaiblity report, Vaculug have continued to strengthen their portfolio of sustainable retread tyres with the recent launch of DTY1 suited to waste operations.
Designed for aggressive trailer operations, the DTY1 is designed with stone defence blocks to reduce rock packing and add further protection to the casing. The DTY1 also boasts Vaculug’s Protekt sidewall protection system offering the ultimate defence against kerbing damage.
Alongside their range of truck tyres, Vaculug also offer a wide range of off-the-road (OTR) tyres suited for waste operations. Their portfolio of OTR tyres consists of their own Mortrak and Kuantam range and tyres from longstanding partners Yokohama, Magna and BOTO. Vacu lug’s comprehensive portfolio offers tyres to suit all applications and budgets.
For more information on Vaculug’s tyre range please call: 01476 593095
Toughness is the reason why we’ve already sold over 500,000 wheel loaders world-wide and when it comes to toughness, our H-Series is as tough as it gets. The H-Series has genuine heavyweight credibility delivering the power, control, comfort and durability required to make light work of the heaviest jobs. Whatever your reason, discover the H-Series for yourself.
The new Alpha Sentinel range protects against some of the most dangerous respiratory hazards found in the workplace.
The UK’s largest PPE manufacturer, Globus Group, has launched a new range of face masks to protect workers against extremely hazardous substances found in the workplace. The new design provides improved comfort and fit to help encourage good PPE compli ance.
Prolonged exposure to hazardous substances over an extended period is known to be extremely harmful, with workers in the manufacturing industry at par ticularly high risk. It is estimated that each year an average of 33,000 workers suffer from illness caused or made worse by their current or most recent job in manufacturing.
The Alpha Sentinel range has been designed for supe rior fit and comfort for workers, especially those wear ing the masks for long periods of time. Lead Product Designer Josh Moffat said, “When it came to designing the Alpha Sentinel range we really tried to prioritise the end-user. We know that workers are often wearing
these masks for long periods of time, and so focusing on comfort and fit means that they are more likely to be worn correctly and workers can be confident that they are getting the right protection.
He continued, “Looking beyond fit and comfort, we know that another big reason for PPE non-compliance is masks getting too hot, so we have designed our unique large ex halation valve to minimise heat and moisture build-up. We really believe that the design innovations we have been able to make with the Alpha Sentinel masks are going to make a huge difference to the workers using these products every day.”
The Alpha Sentinel range comes with a range of changeable filters to protect against solid particulates, liquid particu lates, gases, and vapours, and are suitable for use in a wide variety of industry settings.
The Alpha Sentinel full and half face masks are the first Glo bus product range to be designed and manufactured entirely in the UK. Globus has committed to manufacturing as many of its products as possible in the UK.
To find out more visit: https://globusgroup.com/
Whether you work at a skip yard, a demolition site or a waste transfer station, if you work with demolition waste wood, it is your legal duty to identify potentially hazardous waste wood and action it accordingly under the Waste Wood Classification guidance.
Waste Wood Classification is the process of ensuring that waste wood is properly classified at its origin and is processed into appropriate end markets based on the Regulatory Positioning Statement (RPS) 250. By classifying waste wood, we can identify which items are hazardous in accordance with WM3 guidance and ensure they are dealt with appropriately.
Potentially hazardous items include fence posts, decking and certain types of waste wood from pre-2007 buildings including roof timbers, external joinery and tiling battens. It does not apply to materials such as railway sleepers and telegraph poles, which are already known to be hazardous and require specialist hazardous waste treatment.
As per RPS250, you should first IDENTIFY the type of wood using the RPS250 quick guide. Once this is done, a sample of the whole piece of the item should be taken (a cross-section from the middle no smaller than 150mm long) which can be sent to an accurate and reliable laboratory for TESTING. Only after this should you determine whether you should ASSIGN or CONSIGN your materials.
If your waste wood is deemed Hazardous, it must be consigned using a Hazardous consignment note. This needs to be completed fully, detailing the weight of the specific items. These items should be segregated and only when segregation is not practical can they be blended within a nonhazardous wood load.
As the leading testing and inspection company for the solid fuels sector, Alfred H Knight (AHK) has a wealth of experience in the analysis of waste wood, providing dedicated fuels and process residue testing services to major clients within the processing and recycling sectors.
AHK’s highly-skilled experts carry out analysis entirely in-house from ISO17025-accredited laboratories, strategically located throughout the UK. This ensures that clients get a swift, accurate and reliable service that is tailored to meet their individual needs and requirements.
If you would like to get in touch with an AHK expert to discuss best practice Waste Wood Classification and see how comprehensive analysis can support your operations, visit: www.ahkgroup.com/markets/solid-fuels/waste/
Yorkshire-based waste management and recycling business, MYGroup, has had its application for an environmental permit to recycle clinical waste approved by the Environment Agency.
The new permit means the company can now process a range of clinical waste items, such as used syringes, surgical dressings and personal protec tive equipment (PPE) from various settings, including hospitals and GP practices, dental surgeries, veterinary clinics and pharmaceutical facilities.
MYGroup is looking to build on its success in processing hard-to-recycle non-clinical waste discarded during the COVID-19 pandemic. The compa ny has recycled over 20 million such items, including used PPE, swabs and lateral-flow testing equipment, all while avoiding incineration or sending material to landfill.
Following these efforts, MYGroup is already speaking to a number of NHS and private providers about the commissioning of collection and processing services.
The company will process clinical waste at its Hull facility, where it has invested in the latest autoclave machinery from MACS International. The MACS 800 machine installed at the site is the first of its kind in the UK, allowing clinical and hazardous waste to be sterilised and shredded on site, with zero emissions and low water consumption. MYGroup expects the company to process up to 63 tons of clinical waste a week using the ma chine.
The resulting safe residual waste product will then be broken down through MYGroup’s other innovative separation and recovery processes. Any re maining plastic material will be converted into ‘Stormboard’ – a material similar in consistency to plywood – which can be used for construction, shop fitting and joinery, as well as the manufacture of products for re-sale and use in community settings, such as benches and desks for schools.
The company aims to expand its clinical waste processing capabilities over the coming years, including offering a mobile waste processing service in partnership with MACS, with additional markets outside the UK un der consideration. In addition, an even larger fixed autoclave machine is planned for the Hull site, together with the establishment of a ‘working showroom’ for prospective clients and partners.
Steve Carrie, Director, MYGroup, said: ‘After a rigorous application process, we are delighted to receive the clinical waste permit, which broadens our arsenal and reach in the ongoing fight against waste, and opens a host of new markets for the company.
‘It’s high time we stop accepting that the only solution for certain types of waste – particularly from healthcare settings – is incineration or landfill. MYGroup has proven time and time again that the “unrecyclable” is in fact recyclable, so we welcome this endorsement from the Environment Agency in us as a provider trying to overturn this status quo.’
LondonEnergy sponsors exciting local event as part of its programme to celebrate Black His tory Month.
Throughout October, LondonEnergy has once again celebrated Black Histo ry Month which this year adopted the theme - Time for Change: Action Not Words.’
Over the course of the month, Lon donEnergy organised and participated in several initiatives to raise awareness and celebrate the continued achieve ments and contributions of Black people to the UK and around the world. These included:
• A Food Tasting Day of African and Caribbean inspired dishes - served across all sites
• A Black History Month visual display at LondonEnergy’s ReUse shop in Chingford
• Updating the LondonEnergy logo with the BHM colours on its web site and social media
• Featuring employees from across the business on the website, social media and intranet.
One of the highlights however came this weekend when LondonEnergy support ed the ‘More Than History’ fashion show. This high energy event was curated and hosted by one of the company’s Site Su pervisors, Shane Campbell, and featured 5 collections including the Camouflage Project collection by Julie Corion, which was inspired by the Covid pandemic and people hiding their fears and feelings during this time. Other collections included the use of upcycled fabrics to create designs around the theme of ‘play’ and ‘Nothing goes to waste’ with models wearing jewellery sourced from Lon donEnergy’s ReUse shop.
LondonEnergy’s HR Director, Viv Morris, commented on the company’s support for Black History Month saying: “Black History Month gave us a great opportunity to celebrate black culture and the broad diversity of our local community and business. While we shouldn’t solely focus on the past, we can learn from it to improve the future. We’d like to thank everyone who took the time and made the effort to organise or participate in so many interesting and fun events over the course of the month.”
Fashion is inherently circular and the industry is coming to the forefront of the drive for a more sustainable economy. We were therefore delighted to be able to sponsor the’ More Than history’ fashion show and support local designers in showcasing their creativity and skills –congratulations to everyone involved.”
Find out more at: https://www.londonenergyltd.com/
South West-based J Witt Waste Recycling will use on-site biotechnology to convert more than 3,600 tonnes of unrecyclable waste into Solid Recovered Fuel (SRF) each year, in a move that will benefit the circular economy by reducing and reusing waste that would otherwise go for incineration.
The eight-year contract with biotech nology business Advetec is the latest in a long line of waste innovation activities from J Witt – which was the first waste handler to establish a dedicated food waste collection service in Bath.
J Witt plans to use Advetec’s largest aerobic biodigester machine the XO22 at full capacity, which means it will process up to 10 tonnes of unrecyclable waste on-site per day.
Advetec’s technology reduces the mass and volume of waste by 50% and 70% respectively and offers a sustainable and highly cost-effective alternative to land fill and Energy from Waste (EfW). For every two tonnes of unrecyclable waste that go through the machine, 1.2 tonnes of CO2 are saved, as the process digests the organic fraction of the waste using unique blends of bacteria. The floc that’s left will be used as a coal replacement product – each tonne of floc used as SRF will replace 0.5 tonnes of carbon-emit ting coal.
This technology will help J Witt offer greater environmental gains to its 1,000 customers in Bath, Bristol, Somerset and Mendip, which include retailers, restaurants, industrial estates, veteri nary practices, holiday lets and offices. In particular, processing unrecyclable residual waste on-site will save almost 500 road miles each week – as this waste will no longer need to be sent to the Energy from Waste incineration plant in Avonmouth.
Jamie Witt, director at J Witt Waste Recycling said: “This technology is a game-changer for us operationally and environmentally, and for our customers too. We’ve invested in Advetec to reduce and stabilise our costs and future-proof the business, as well as to give custom ers a more carbon and cost friendly alternative to landfill and EfW for their unrecyclable waste.
“At the moment, we have to transport this waste across the region which is costly and time intensive. An on-site solution will dramatically reduce our lorry journeys, which means less cost as well as significantly reduced road related carbon and congestion.”
Jamie added: “We’ve always been com mitted to actively reducing waste but now we’ll have the technology to amplify
our efforts. Crucially, we’ll be turning local waste into a commodity that ben efits the circular economy and helps our customers accelerate their journey to Net Zero.”
Lee Knott, Chief Commercial Officer for Advetec, said: “Jamie and his team are what we call waste innovators and for the businesses they serve, they’re waste heroes too. Their decision to invest in our technology reflects the increasing commercial and political impetus for change and shows their appetite to em brace more environmentally friendly and cost-effective methods.
“The Advetec XO22 will give J Witt greater control over cost and carbon and build greater waste handling capacity into their own operations – all of which will benefit their customers greatly. We’re delighted to count them among our clients.”
Earlier this year, Max Recycle in Houghton-Le-Spring became the first waste handler in the UK to create SRF on site with Advetec. Several of Advet ec’s smaller aerobic digester machines –the X06 and X03 – are also in operation across the UK.
To find out more visit: www.advetec.com or call 01225 777484.
the circularity gap report from Circle Economy revealed that only 9% of the global economy is circular. In addition, the Ellen MacAr thur Foundation reports that the circular economy “tackles the root causes of global challenges such as climate change, biodiversity loss, and pollution, creating an economy in which nothing becomes waste and which is regenerative by design.”
To accelerate the world’s transition to circularity, and move to a world beyond waste, CIWM is hosting the 2nd annu al Festival of Circular Economy in late November.
The Festival of Circular Economy (FoCE) is a global celebration of circularity, tak ing place online between 28 November and 1 December, with four hours each
day of motivational sessions that bring the circular economy to life. The FoCE event will focus on accelerating the move towards sustainability and net zero, tak ing the circular revolution forward both in the UK and worldwide.
With 23 countries participating and 60+ inspiring speakers – including big brand names such as Amazon, Diageo and L’Oréal, FoCE is the must-attend circularity event of the year. It also features a stellar line-up of keynote speakers, including environmentalist, author and sustainability advisor, Tony Juniper; global speaker and author, Marga Hoek; and architectural designer and TV presenter, Charlie Luxton. The event will be hosted across all four days by Mark Shayler, Founding Partner of Do Lectures.
FoCE is a unique, ground-breaking virtual event where people who are pas sionate about creating change can come
together to share ideas, innovations and inspirations, network and bond, challenge, collaborate and co-ordi nate. Over the four days, speakers will transform the way that businesses and individuals think about how we use the world’s precious resources and move further towards the goals of reuse, repair and refurbish.
Every sector and industry that has something to contribute to the circular economy will benefit from attending FoCE. Manufacturing, architecture, design, energy, fashion and construc tion will all be represented, and their successes and wisdom captured and shared.
FoCE’s dynamic programme provides circular insights through interactive discovery workshops, changemaker case studies, group discussions, virtual head-to-heads and networking oppor tunities. You will meet like-minded people who are making a difference by thinking and doing things differently.
Sessions are short, sharp, incisive and bite-size so that you can dip in and out of the programme as it suits you. And if you miss out on any session due to another pressing priority, you can catch up online at any time during December.
FoCE will celebrate the great work in and around the circular economy. Our agenda covers all aspects of a circular economy, providing a forum for all.
The programme has been carefully put together to provide the ground-breaking content that delegates have come to ex pect from an event presented by CIWM.
Highlights include:
• Three big questions on how to achieve a truly circular economy
• How the circular economy could change the planet
• Achieving circularity in construc tion
• Why the circular economy is the future of business
• Why design is crucial to enabling the circular economy
With over 400 attendees expected, CIWM will bring together big names, big content and big ideas to make things happen.
From start-ups and scale-ups to mul ti-nationals, from government to academia – FoCE will bring together a breadth of knowledge, understanding and experience from all areas of the circular economy.
Anyone enthusiastic about circularity is encouraged to attend. Ambitious circular pioneers are especially welcome, to contribute their experiences and share how ideas are being turned into actions.
For more details, and to book a seat at this exciting event, please visit the website: https://www.circulareconomy festival.com/
Marking 2022’s anti-slavery day on Tuesday 18 October, CIWM hosted a webinar on behalf of the Indirect Procurement Human Rights Forum (IPHR) to launch the brand-new IPHR Waste & Recycling Modern Slavery Protocol.
In July 2021, CIWM and ESA an nounced a joint commitment to tackle slavery, forced labour and human traf ficking across the industry. Since the launch, CIWM has been supporting a number of orgnisations and initiatives to reduce the risk of modern slavery across its membership base and the wider sector.
The IPHR Modern Slavery Protocol is a voluntary agreement and public pledge of commitment of organisations to work collaboratively to tackle modern slavery and prevent exploitation or abuse of workers.
The six-page protocol sets out how organisations will take action to protect vulnerable and exploited workers and help build understanding of risks and embed responsible practices to improve standards.
To download the protocol, please visit https://bit.ly/3z4IZMj
Across the country organisations have surplus computers and technical equipment that could help raise vital funds to help the national Children’s Air Ambulance (TCAA) save young lives.
The ever-changing world of technology and an increase in hybrid working has led many companies to adapt and up grade their IT equipment. For most, the turnover of equipment is unavoidable, but teams are often unsure about what to do with the old equipment and face confusion about the destruction of data and potential recycling bills; that’s where the charity’s IT Asset Reuse department can help.
Donating IT equipment to the Children’s Air Ambulance is a free, convenient, and time-saving solution which helps the charity to continue its lifesaving service.
TCAA’s six-step IT Asset Reuse Process
01 - LIAISE
The TCAA team liaise with organisations offering a free collection service.
02 - TEST
Once collected they test all equipment for safety and the viability of resale.
03 - DATA WIPE
Destroy data contained in any form of media using Blancco binary data wiping software.
04 - DESTROY
Destroy any data bearing media that cannot be wiped
05 - CERTIFY
Receive tamperproof certificates for each item the charity was able to data-wipe along with a destruction report for any additional HDD’s, these can be stored to prove the safe destruction of your data.
06 - REUSE
Where applicable we refurbish equip ment ready for resale.
“Corporate Social Responsibility is high on the agenda for many. With organi sations reviewing the impact they have, both environmentally and within the community, we are keen to work with organisations who have a large amount
of redundant stock or who regularly update their IT equipment and are aware of the environmental impact this has. Our service is a great, cost-effective way to decrease your carbon footprint at the same time as supporting a charity.
The amount of WEE waste created each year is growing and whilst it’s great these items aren’t ending up in landfill, recy cling is an intensive, chemically lead pro cess which is often unnecessary, as these items still have plenty of life left in them, they’re just a little slow for corporate use, but they should be part of the circular economy. Why create waste when you don’t have to? We aim to reuse as much of each donation as possible and recycle what we can’t.” – Sam Frost, TCAA, IT Asset Reuse Manager.
The Children’s Air Ambulance is a national lifesaving high-speed transfer service – flying critically ill babies and children in clinically designed helicop ters from one hospital to another for specialist care.
The charity receives no government funding and relies entirely on donations to raise the £3,500 needed for every mis sion. Your support will help to keep hope alive for these patients and their families.
Donated technical items can include PCs, laptops, all-in-ones, servers, tablets and mobiles (restored to factory set tings), desktop printers, widescreen monitors, networking gear and more. Data wiped to MOD, InfoSec level 5 standards.
To find out more about TCAA’s IT Asset Reuse Services, visit: www.childrensairambulance.org.uk, or call
0300 3045 999.
This time of year, sees varying levels of moisture appearing simply through changes in temperature causing condensation in the tanks. If oil becomes milky in appearance, the saturation limit at the oil temperature has been exceeded, indicating that both dissolved and free water are present.
Water contamination can cause fluid breakdown, reduce lubricating film thickness, accelerate metal surface fatigue and corrode components. It also accelerates oxidation, which leads to additive depletion, acid build-up, varnish formation, and sludge.
The main sources of water contamination are heat exchanger leaks, seal leaks, condensation of humid air, inadequate res ervoir covers, and temperature drops which lead to dissolved water (below saturation) becoming free water (emulsified or in droplets). Both free and dissolved water cause component and oil degradation.
The usual action is to change the oil, and flush, and change the oil again; because once that milky oil has filled pipes and cylinders – it is just not easy to clear out.
KLEENOIL
ISO 4406 Cleanliness Code – 14/9 NAS 1638 Class 6 KLEENOIL is affordable and simple to operate.
Cellulose filtration is a natural form that not only removes particu late but also moisture in one simple application.
Install for a permanent level of high filtration or use as a one-off application to solve moisture and contaminant issues.
Contact sales@kleenoil.co.uk for more information
According to a recent report by Smash Hit Displays, data found that the conference and trade show industry is among one of the largest producers of waste; attendees generate approximately 600,000 tons of waste each year. Further to this, of the estimated 60 million people who attend trade events each year, each individ ual person generates approximately 20 pounds of waste, resulting in more than 1 billion pounds of waste annually.
are a top priority for those looking to expand their market and con nect with likeminded people within the industry. Trade shows can also be a great place to strengthen existing customer relationships, allowing many to put faces to names they ordinarily do business with over the phone or via email. In terms of marketing and networking, trade shows are a major benefit, however, many of these events are responsible for a vari ety of single-use, or throwaway items which can result in a big pile up of waste, particularly as many of these events are no small feat. Trade events attract a large number of participants and visitors, usu ally occupying large venues and can re quire a large amount of energy, resulting in a lot of waste being generated. Howev er, as many look towards a clear sustain ability objective, organisations look to present their products and services in the best and most sustainable way possible. Here are just some ways that many shows and exhibitions are looking to embark on more sustainable initiatives, in which you as visitors or exhibitors can also partake.
While many use merchandise or promo products as a great way of increasing brand awareness and drawing people to their stand, some of these items can simply end up in the bin at the end of the day. When exhibitors are looking to create promo materials, it is important to choose carefully. Exhibitors could opt for biodegradable pens and reusable items, such as canvas bags, thermal mugs or water bottles made from recycled or recy
clable materials, which can last for much longer, rather than just the duration of the show!
Many shows try to embark on Sustain able partnerships to ensure a greener outlook is taken, with many trade show suppliers happily offering eco-friendly options.
Trade show exhibitor stands can also be made from sustainable materials. Many shows also employ contractors who promote eco-friendly practices when building their exhibition stands and shell schemes. Many companies offer envi ronmentally friendly exhibition displays, using materials from a recycled source that are 100% recyclable. Stands can also be built from a variety of materials, such as wooden alternatives, and even cardboard.
RWM show 2021 took the initiative to plant a tree for every exhibitor who joined the exhibiton to offset the carbon created from the show.
Some exhibitors may even incorporate climate-friendly elements, such as living walls, which not only are great for engag ing visitors, but also are a great sustaina ble way to decorate.
Many trade shows are now looking to promote sustainable initiatives, including the venues they are held in. For example, the Business Design Centre, London, is the first Carbon Neutral venue in the UK. The venue is known for hosting the ‘Future of Utilities Summit’, ‘Sustaina bility Live’, ‘Rail Power’, ‘Surface Design Show’ and more. The venue is now carbon neutral, achieved through send ing zero waste to landfill, using 100% renewable energy to power the building, and they are now looking at the next step in their sustainability journey to become Net Zero before 2030.
RWM 2021 participated in a “plant a tree” initiative, where they took the step to offset the carbon created from the building of the trade show. Once an exhibitor or sponsor joined RWM, a tree was planted in a dedicated space of woodland in the Lake District in their name.
Another way to also ensure your stand as an exhibitor is engaging but also eco friendly, is through the use of recyclable furniture. RWM show ensures that the carpet used throughout the NEC Venue for their show is repurposed and recycled once it has been used. For example, this Smurfit Kappa, leading paper based packaging company, showcased their sustainable furniture at RWM 2022 show)
year’s carpet was directly reused into home and garden products such as bathroom mats, sofas, and armchairs.
Some exhibitors invest in recycla ble cardboard exhibition stands and furniture for an eco-friendly display throughout trade shows. All of these can be recycled, reused or are biode gradable, so once a show has finished, exhibitors won’t have to worry about waste.
Going paper free is one of the most popular choices when looking to take a more sustainable approach.
Many shows now adays get rid of
printed materials such as programs, flyers, and business cards, and instead opt for a mobile app or a digital option to prevent waste. You can find a variety of apps that can help you achieve what you want at the show, whether it’s to capture visitor data or to simply network – there’s an app for that!
Many shows now deploy a sustainable transport plan for those travelling to the venue, such as promoting electrical charging bays, encouraging those with electric vehicles to use them as a mode of transport to and from venues. Some venues also promote easy access to public transport, which provides visitors with a more environmentally friendly mode of transportation.
MOST POPULAR
open day took
place on the 29th of September 2022, a special event to immerse yourself in the GGR culture, explor ing their offices and workshop.
The business opened in 1995 as Glass Services, offering glass vacu um lifters for hire and is now one of the biggest lifting hire companies in the UK.
The open day boasted a layout to discover all the amazing machinery the company has to offer in full, with some sneak peeks of brand new machines which have not yet
been unveiled.
The event saw interesting presentations from some big partners of the company such as the CPA and Radius, who dis cussed their new Aviation lifting and the perks in comparison to the cranes, and GGR them selves discussing innovation and bespoke lifting solutions. The key topics were focused on many aspects of lifting, loading, lower ing, training, people plant, vehicle interface, new and improved methods of working, and areas of innovation.
THE COMPANY HAS TO OFFER IN FULL
Visitors had the opportunity to take a tour inside the facility and view a variety of product demonstrations, including GGR’s pioneering lifting equipment, glass vacuum lifters, glazing robots and UNIC mini spider cranes. Other innovative equipment on display was the new Sky Robot 1500, electric and diesel telehandlers, new overhang beams, and other specialist lifting equipment.
Around the showroom, you could find stands of businesses in partner ship with GGR, Ainscough being one of them, promoting their new crane with innovative features like moving the utility box at the back of the crane so that it is much more accessible - a modern design for 2022 machinery.
GGR is committed to helping customers to reduce their emissions during lifts. As a member of the Sustainability Supply Chain School, GGR has dedicated nearly three decades to this mission. As a part of this, GGR Group has a dedicated ‘Green Lifting Range’.
With over 90% of GGR Group’s range of lifting solutions being zero emissions, they are sure to have the perfect selection of equipment that is ideal for any project that is being completed in zero-emis sion or other clean zones. Legislation is constantly changing, and more and more clean air zones are popping up. Because of this, it is important for businesses to keep up and make sure that they have the correct lifting equipment, regardless of any changes that may arise in the future.
The Green range varies from:
• The vacuum lifter; there are 60 dif ferent vacuum lifters with capacities that range from 70kg to 600kg. With cladding lifters that range in capacity from 320-1000kg and a stone lifter range with 100-4600kg capacity, you can be sure that you will have access to the lifting equipment you need whilst still reducing your carbon emissions.
• GGR has a range of award-winning glazing robots with a variety of ca pacities that range from 280-1400kg. Glazing robots are the perfect solu tion to several different lifts, as with them, you could tackle inside-out glazing, curtain walling and more with ease. They are all 100% battery powered, which will give you the
opportunity to work in enclosed or noise-sensitive environments.
• A variety of Pick & Carry Cranes range from 2t to 25t. These are perfect for lifting and shifting materials on site. Along with this, they are also a perfect alternative to a forklift and many other industrial cranes. They are fume-free and do not require the use of outrigger mats, making them one of the best solutions for eco-friendly lifting and shifting.
• The Tracked Carriers, ranging from 1t to 6t capacity, offer users maxi mum manoeuvrability and control when operating on busy construc tion sites and in narrow areas. The Tracked Leveller range of Tracked Carriers come with an automatic
self-levelling load deck, ensuring optimum control and safety.
• MCC1004 Mini Crawler Crane has a huge 10t capacity and a maxi mum working height of 21.5m. The 2800mm wide base and solid tracks make it the ideal solution for travelling over uneven and rough terrain. This powerful crane can also operate in London’s Ultra Low Emission Zone thanks to its Euro Stage V engine.
• The latest in Mini Spider Crane engineering, the UNIC battery powered Eco-UNIC models provide fume-free lifting for sensitive envi ronments. Ideal for food processing plants and listed buildings, airports, and clean environments, these
THE KEY TOPICS WERE FOCUSED ON MANY ASPECTS OF LIFTING, LOADING, LOWERING, TRAINING, PEOPLE PLANT, VEHICLE INTERFACE, NEW AND IMPROVED METHODS OF WORKING, AND AREAS OF INNOVATION.
unique spider cranes are powered by a rechargeable 48v battery with no diesel emissions impacting the surrounding area.
• The world’s first electric telehandler, the F6.26 with a 2.6 maximum working capacity and a 5.9m max imum lifting height, gives users the best eco-friendly telehandler option in the UK. With up to a 6-hour bat tery life (depending on usage), the ability to opportunity-charge and a multitude of attachments available, this modern and effective tele handler can work in a wide variety of sectors and industries.
We want to thank GGR for the amazing opportunity given to be able to explore the machinery and find out more about the culture of the business.
To find out more, visit: https://www.ggrgroup.com/
WITH OVER 90% OF GGR GROUP’S RANGE OF LIFTING SOLUTIONS BEING ZERO EMISSIONS, THEY ARE SURE TO HAVE THE PERFECT SELECTION OF EQUIPMENT THAT IS IDEAL FOR ANY PROJECT
Hosted by national recycling campaign Recycle Now, Recycle Week is an event celebrating all things recycling, which took place this year between 17-23 October. As governments, trade associations, retailers, brands and waste manage ment companies come together for the event, they try to realise their joint goal of educating the public on the need for recycling. Their message this year? Let’s get real about recycling.
The event seeks to answer three of the following questions that arise most often when it comes to recycling:
• Does my recycling really make a difference?
• One item in the bin can’t hurt, can it?
• Recycling is so confusing, Isn’t it?
The mind behind the annual event, Recycle Now, is one of the citi zen-facing brands managed by WRAP, a charity working across six continents with governments, busi nesses and citizens to create a world where resources are sourced and used sustainably, through product design, waste minimisation, re-use, recycling and reprocessing of waste materials.
First staged in 2004, Recycle Week is now the UK’s largest national annual recycling campaign. Last year, Recy cle Week saw over 29 million digital impressions, and 82% of people who
interacted with the event reported that they had changed their behav iour as a result of seeing Recycle Week 2021 content. Expectations for this year’s event were high.
This time, to shed light on things we can recycle that often get missed, Re cycle Week built a giant hand-painted QR Code in Birmingham town cen tre out of recyclable items that people nationwide often forget to recycle, such as empty aerosols, perfume bot tles, and clean foil. Once scanned, the sign takes people to Recycle Now’s website, answering common recy cling questions and demystifying the process to the public. With their own Recycling Locator, information on contamination, and visualisations of how our recycling makes a difference, Recycle Now has all the information people could need to make smart er recycling decisions. Visitors can enter their location and the item they wish to recycle, and the website will recommend the most convenient way to do the recycling.
Iconic buildings across the UK, from the Blackpool Tower to Titanic Belfast, have also lit up in green in support of the event, and celebrities including former Olympic swimmer and keen environmentalist, Mark Foster, have joined the campaign as ambassadors to spread the message.
“We’ve seen a lot of things come through – iPhones, wedding rings, money, pheasants. We’ve actually had a snake come through as well – a py thon,” shared a worker at a recycling centre, shedding light on the extent of the miscategorised waste that ends up in the centres. Watch Recycle Week’s video that takes you on a jour ney to what exactly happens after we drop our items in the recycling bin.
According to data shared by Recycle Now, recycling is now a widespread practice in households across the UK, with nearly 9 out of 10 regularly recycling. The nation already saves 18 million tonnes of CO2 a year by recycling, and talking about it more often is working – 52% of people across the UK say they recycle more items more often, compared to last year. Yet whilst 87% say they recycle everything that can be, the 72% UK average shows there is still work that needs to be done to reach our goals.
Alongside this, one of the key issues that has arisen with the increase in recycling rates is contamination. Called ‘wishcycling’, the misguided belief that certain things should be recycled when they should not can
A SURVEY FROM EARLIER THIS YEAR SHOWS THAT 84% OF THE UK CONTAMINATES THEIR RECYCLING WITH MORE THAN ONE MATERIAL”
lead to whole lorry-loads of rubbish becoming unrecyclable. The most common contaminants include drinking glasses at 33%, followed by food and drink foil pouches at 29% and toothpaste tubes at 26%. A sur vey from earlier this year shows that 84% of the UK contaminates their recycling with more than one materi al, with an average of four items that UK households recycle incorrectly. Whilst recycling is done with good intentions, not doing it correctly can cause significant harm, highlight ing the need for more nationwide informational campaigns such as Recycling Week.
Furthermore, an astounding 80% of households put one or more things in the rubbish bin that could have been recycled, which is why the public is being encouraged to use the Recycling Locator and check what items are recycled at their local au thority, during Recycling Week and beyond.
To find out more about this years Recycle Week and how you can get involved next year, visit: https://wrap.org.uk/taking-action/ citizen-behaviour-change/recy cle-now/recycle-week
TThe return of RWM & LetsRecycle Live, the UK’s leading event for waste, resource, and sustainability profes sionals, saw over 12,000 visitors and over 500 exhibitors return to the NEC in Birming ham for an action-packed two days of waste management solutions, live action demonstrations and in-person network ing. It took place from the 14th-15th September 2022 with a total of four halls and 10,000 m2 of outdoor space.
Featured in the mass of industry leading exhibitors were names such as: Blue Group, Doyle Machinery, Air Spec trum, BOMAG, CIWM, Fireward, Hiab, Kelly Tanks, Keenan Recycling, Tana Recycling Machinery, JCB, Reconomy Group, SENSONEO, Ulster Shredders, Ward Recycling and more. Also joining the exhibitor line-up was the launch of Future Waste Magazine!
With this year’s RWM and LetsRecycle Live co-locating for the first time at the
Birmingham NEC, the show was bigger than ever! This year’s show was spread across four indoor halls as well as a bus tling outside area, which saw a variety of heavy machinery and recycling solutions, including the Doyle Machinery VZ 950
Titan Shredder. BOMAG showcased their BC 973 RB-5 landfill compactor, designed for use on landfill sites of all sizes. Also on site was the DOOSAN DX300 LC Hydraulic Excavator and DX 160W-7 Wheeled Excavator. JCB also
had an impressive line-up of machinery on display at their stand. This included their JCB Waste Master, designed to in novatively tackle issues facing the waste and recycling sector, as well as wheeled loading shovels, telescopic handlers and electric forklift trucks also joining the line-up.
The Trucks in Action demonstration area, sponsored by Refuse Vehicle Solu tions, allowed visitors to get “up close and personal” with the newest electric and low emission vehicles on the mar ket helping to reach net-zero targets. This year’s vehicles on show included refuse collection vehicles, skip, and hook loaders, street sweepers and grab loaders. This year’s participants in the line-up included Aebi Schmidt’s eSwin go 200+, a fully electric compact sweep er. Dennis Eagle also demonstrated the eCollect and Elite+ during the trucks in Action arena. Terberg Matec UK also joined the line-up with demonstrations of the Kerbloader EV and PBUV, with HIAB, Scarab Sweepers, and more also taking up the opportunity to demon strate their new trucks in action.
The Live Demonstration Area, spon sored by Zappshelter, ensured there was plenty to see throughout the day, with Peter Haddock leading the demon strations in the live demo area which showcased a range of machinery.
The Live Material Processing Demon stration brought a collection of ma chinery from different manufacturers together for three displays throughout the day for the duration of the show. Visitors saw a variety of machinery such as shredders, balers, material handlers, wheeled loaders, and dust suppression equipment. Kicking off the demonstra tions was the Terex Ecotec TWH 228, supplied by Warwick Ward Machinery,
designed for more power, and reach in compact situations. The machine demonstrated its 129kW engine power, 30.6t max service weight and 13.2m max reach. CASE Construction were also found in the live demo area demonstrat ing their 621GXT wheel loader.
Also amongst the impressive machineries in the live demo area was the Willibald Shark V high speed shredder from Doyle Machinery. This was actually the first time the new machine has been shown off in the UK! The high-speed shredder also comes with a remote control to fur
ther enhance ease of use for the oper ator. The Shark V also boasts a built-in dust suppression, new Stage V engine.
Doosan also had two machines in the live area, the DL 420-7 Stage V wheel loader and DX160W-7 Wheeled Excavators. Also partaking in the live demonstration was the Solmec EXP DP5025, available from 8 to 12 metres reach, specifically developed for mate rial handling and demonstrated such in the live area of RWM & LetsRecycle Live.
Back inside the show halls, the nine theatres ran a programme of speak ers, committed to driving change in the waste and resource industry and covering important topics within the recycling and waste industries. Topics included combatting the impacts of waste crime, smart sustainable pack aging, energy from waste, as well as women in resource and sustainability. These seminars provided a platform for key industry knowledge sharing and learning. Continued on page 54→
2022has been a busy year for Keenan Recycling with its investment in its new hybrid vehicle which reduces CO2 emissions by 98%. As the first day of RWM kicks off to a busy start, Future Waste editor, Kate Hutchison, sits down with Fergus Healy, Head of Strategic Development and Net Zero at Keenan Recycling, to get a first-hand account of the ideas and development behind its newest innovation.
Fergus Healy is one of the senior team of experts at Keenan. Fergus kicked off the conversation by giving some background to the company.
“Keenan Recycling has been around for over 20 years now. It started as a com posting business, it’s got a large facility in Scotland, composting food and green gardenwaste. Around ten to fifteen years ago, it started to get into the actual col lection side of food waste recycling.
“We have expanded dramatically in the last three years from servicing just Scotland and its surrounding areas to now being the largest provider of food waste recycling nationwide. At Keenan Recycling, we take food waste from any business or sector that generates it, so, hospitality, restaurants, pubs, healthcare and hospitals, care homes, supermarkets, sporting arenas, wherever it may be, we can service it.
“We are a recycling business that solely focuses on food waste, in addition to collecting the waste we have a large ded icated de-packaging process that extracts value from the waste food. Organic ma terials recovered are then liquidised and blended forming a biofuel. This biofuel is then loaded into Anaerobic Digester tanks, in which it is broken down by micro-organisms over time. During this process, methane is produced through the activity of the colony or micro-or ganisms. This methane is extracted from the digester and is known as biogas. This biogas can be used for creating renewable electricity, cleaning up to biomethane and injecting into the gas grid, or even
compressed and used in road transport.” Fergus continued to discuss their ambitions for the future and their next innovation.
“Our aim is to take this to the next level and create a fully sustainable low-carbon food waste recycling business. To actually collect the food waste using a vehicle which is powered by a non-fossil fuel source. In this instance, hydrogen and HVO, which is a used cooking oil. Down the line, we’re aiming to have compressed biomethane vehicles, which will directly use the gas that’s being produced by the food waste to power the vehicle, allowing for a more circular approach which also drives greater resource productivity.”
When discussing the reasoning behind the choice of hydrogen and HVO pow ered vehicles Fergus adds:
“We’re on a journey to becoming a net zero business by the end of this decade and a large part of that revolves around decarbonising our fleet. With this, there
is a whole range of alternative fuels that we’re looking at. This particular one is hydrogen and HVO powered, but there’ll be others coming and towards the end of the decade, we will probably look to battery and fuel cell electric vehicles as well. However, right now, we don’t think battery electric vehicles are necessarily the answer. There are various reasons for that. For example, the cost of the vehicle in a non-urban setting, how far can you travel on one charge cycle, the weight of the batteries and all sorts of things preclude you from using them more generally. However, we feel there are a variety of other options out there.”
With the hybrid vehicle being unveiled for the first time at the 2022 show of RWM, Fergus comments:
“This hybrid vehicle is a new concept. It’s an innovation because nobody has put hydrogen and HVO together before. Although hydrogen technology exists, it’s never been configured in this way. We are genuinely trailblazing here. The
vehicle will be based in Aberdeen near a hydrogen refuelling site where we’ll trial it for six months in that location and, during that time, we’ll determine any obstacles, iron out any little details and then go from there.”
Fergus added: “We have a structured plan to assess all different components, including feedback from the driver. There are some very real psychological
issues surrounding someone driving a vehicle that’s got a flammable & explo sive gas on the roof! Hence all logistical, operational and technical issues will be considered as part of that trial process. We must also thank the team at Scottish Enterprise for their help and support in making our vision a reality”
The UK is highly motivated in its move towards a net zero future by 2050 targets set out by The Climate Change Act, with many businesses looking towards striv ing towards a greener and cleaner future, and Keenan Recycling is taking a leap in the right direction on the road to net zero with its new hybrid vehicle.
Fergus says:
“What we’re excited about is being the first to develop this.
“We’re using hydrogen from a green hydrogen source, which is zero carbon and we’re using HVO, which is very low carbon. Those two things together give you almost a carbon-zero emissions vehicle. It is this combination which we feel is real innovation and we’re very excited about that. This also kick-starts our journey towards Net Zero, the first of many milestones that we’ll go through in the next five, six, or seven years.”
Reflecting on what the future may hold for Keenan Recycling, Fergus explains: “For me, our roadmap displayed on our stand really showcases the story.
“We’re going to see how this trial goes. We’re pretty confident it’ll go well. Fur ther down the line, we’ll get some more of these vehicles. Eventually, a fleet of gas-powered vehicles that will run on gas
from the anaerobic digestion process. We certainly won’t run any new fossil fuel vehicles. For us, diesel is a thing of the past. We’re trying to create a low-carbon, fully sustainable food waste collection model here. And that’s what this new hybrid vehicle is about. For Keenan, this is the starting pistol fired on that journey to a net zero future.”
Keenan Recycling collects food waste from the public and private sector organ isations across the UK, and transforms it into compost, renewable electricity and gas, heat and fuel. Its ever-growing fleet of specialised food waste collection vehicles operate a 24/7, 365-day a year service, across 17 depots, offering private & public sectors clients an opportuni ty to segregate food waste for separate collection.
For more information, please visit https://www.keenanrecycling.co.uk/
Eversince 1971, TANA has been at the forefront of designing and manufacturing robust machin ery for the purposes of solid waste management. With a wealth of decades of experience on the needs and requirements of landfill and waste management operators, in the early 2000’s Tana expanded it’s machine selection with the TANA Shark mobile shredders.
Based in Bentley, Doncaster, TANA Recycling Machinery (UK) Limit ed is the sole UK distributor for all Tana products. TANA (UK) Ltd was established in May 2016 and has been at the forefront of delivering unmatched versatility to the UK recycling industry.
TANA’s main role is to provide the sales, service, and maintenance for it’s Recycling Machinery, and the company has an array of machinery from slow speed Shredders, Landfill compactors, Trommels and Disc screens. TANA has the responsibility to make sure that all their customers’ machines are always well serviced and maintained, ensuring that there is little to no downtime for the com panies that operate them.
Sales & Marketing Manager Brook lyn Walker commented, “The com pany slogan TANA From Waste to Value® is a symbol of Tana’s devotion to not only produce machinery that is unique in terms of its design and features, but also to provide our customers with solutions and ser vices for improved productivity. Our mission is to improve our custom ers’ businesses and enable them to
increase their revenue - from waste to value.”
The TANA Shark Shredder is a mobile and extremely versatile waste shredder, suitable for both pre-shredding as well as shredding of industrial waste, demolition waste, tyres, mattresses and green waste, and it can be adapted to any desired piece size. For the best job, the TANA Shark 440DT Eco is ca pable of producing high torque with the best cutting power, and Tana rec ommends this model as it is the best multi-purpose shredder available, and is capable of tackling anything that is required of it.
TANA is also the first brand to devise a waste compactor specially built for the landfill market. The new TANA H-series is the result of long-term product development and proven solutions that offer excellent user benefits, and the compactors are equipped with unique features that set them apart from other compac tors on the market.
The rigid frame provides optimum crushing force, so the TANA com pactor is built around a rigid articu lated frame which allows a crushing force of up to 100% on a single barrel drum compared to a four-wheel oscillating vehicle of similar weight. This guarantees a 10% better com paction rate and fewer passes.
To find out more, visit: http://www.tanauk.com/
Also featured in the RWM Exhibition was an art display entitled “The Art of Recycling” presented by Waste Care. The display featured incredible sculptures such as a recycled plastic shark model, made up of 801 plastic milk bottles, used to illustrate the importance of reducing our dependence on plastic and the 10 million tonnes of plastic that ends up in our oceans every year.
Other eye-catching pieces of art on dis play include a replica Portuguese man of war jellyfish, a vital part of our ecosys tem, as well as an octopus model made up of recycled and unusual materials. There were also many awards to be won at the show, with the excellence in innovation award being awarded to Hiab for the MOFFETT E5 NX eSeries, the world’s first all-electric moving mast and 4-way TMFL. Another winner of the excellence in innovation award includ ed Aebi Schmidt, for the noiseless and carbon-free cleaning Schmidt eSwingo 200+ at this year’s show.
The impressive and advanced innovative machinery on display at the RWM exhi bition made for a great return for both RWM and LetsRecycle Live, and the show will return in 2023 from 13th-14th September.
Register for the 2023 RWM exhibiton today: https://www.rwmexhibition.com/
In 2012, Mark Stubbs was running a successful contracting company specialising in land drainage when Kelly Bryant started as his administra tor. Mark introduced Kelly to working with water, creating balancing ponds, dredging rivers, creating wetlands and wildlife habitat. It was during this time the pair developed a long-standing
relationship with the wildlife trust, fur ther instilling in them the importance of protecting the environment, a value that has remained at the core of their business ever since.
Before this, Mark gained considerable experience working on pipelines in the UK, Russia and Southeast Asia. It was here Mark began to appreciate the work that could be achieved using natural resources and teamwork. When the pipeline days came to an end, Mark returned to the UK and began his groundworks contracting company. Mark’s determination and passion are evidenced not only by the successful businesses he runs, but also by the odds he overcame to build them. Hav ing suffered a near fatal accident, Mark spent eleven months in hospital and
was told he would never work again. Mark’s commitment, unwavering work ethic and conviction drove Mark to not only return to a working career but to excel in it, surpassing all expectations. By the time Kelly joined, Mark was already harbouring ideas about intro ducing water treatment systems into
MARK’S DETERMINATION AND PASSION ARE EVIDENCED NOT ONLY BY THE SUCCESSFUL BUSINESSES HE RUNS, BUT ALSO BY THE ODDS HE OVERCAME TO BUILD THEM.
IN THIS ISSUE OF FUTURE WASTE, MARK AND KELLY, DIRECTORS OF KELLY TANKS, TAKE US THROUGH THE STORY SO FAR AND THEIR AMBITIONS FOR THE FUTURE.
his hire fleet. Kelly having also faced adversity, experiencing homelessness in her teenage years, was keen to prove her value. Crediting herself with resilience and compassion, she endeav oured to assist Mark in exploring new opportunities.
It was when a customer asked Mark if he was interested in buying a cylin drical water storage tank that things began to move forward. Mark accepted the tank, hoping that once refurbished it could be hired out. During the process of refurbishment Mark and Kelly began discussions about devel oping a water treatment system for use on construction sites. Their first ideas were to create a basic settlement tank and eventually, with some help, Kelly drew up a plan.
KELLY HAVING ALSO FACED ADVERSITY, EXPERIENCING HOMELESSNESS IN HER TEENAGE YEARS, WAS KEEN TO PROVE HER VALUE. CREDITING HERSELF WITH RESILIENCE AND COMPASSION, SHE ENDEAVOURED TO ASSIST MARK IN EXPLORING NEW OPPORTUNITIES.
Over the next year Mark and Kelly built more tanks, all the while learning more about water treatment, onsite requirements, and the drawbacks of systems already on the market. They came to understand that sites wanted systems that were simple to set up, sim ple to use and simple to empty. With this in mind, the pair designed the ‘WTS’, a settlement tank that includes a cage to housing flocculant blocks to enable simple flocculation, an adjust able oil skimmer, a compartment for lamella/coalescing media to optimise settlement and a hopper bottom and dump valve to easily remove settled solids.
Next, the pair introduced the ‘Sack Frame’ to house sacks that would further filter waste water and retain
THEY CAME TO UNDERSTAND THAT SITES WANTED SYSTEMS THAT WERE SIMPLE TO SET UP, SIMPLE TO USE AND SIMPLE TO EMPTY.
suspended solids, unfortunately they found existing sacks were essentially builders sacks with a felt liner sewn that quickly became blocked and ineffective. Rather than give up on the premise, the pair sourced a liner and created the ‘Adsorption Sack’, a sack specifically designed to enable solids to attach to the surface of the liner, even tually becoming heavy enough to drop into the sack leaving the liner clear to continue filtering.
Interest for the systems quickly grew and in 2013 they were asked to com mission systems for J Murphy & Sons and JN Bentley. At this point Mark decided to separate the growing water
treatment fleet from his contracting company and set up a new company. The company was to be named Kelly Tanks and Kelly was invited to become a director.
It wasn’t long before the pair realised the Adsorption sack could be used for many purposes, one of which being the retention and filtration of cementitious particles in concrete wash water. After much development, Kelly drew up plans and the CWS Concrete Washout was born. A cost-effective alternative to skips & suction wagons, the CWS is a ‘plug & go’ system that allows concrete equipment and wagons to be safely washed-off onsite by separating the
solids, recycling the water and neutral ising the pH. Demand for Kelly Tanks innovative and user-friendly systems grew and soon the brand was receiving recognition.
Kelly became a shareholder in 2017 and the pair continued to add products and systems to their fleet. Mark and Kelly went onto design pH treatment systems that would proportionally dose using a pH reducing liquid. They also discovered existing methods for re ducing pH levels were wasteful in their overuse of C02 and so designed sys tems that would only dose the required amount. This method can be found in their GWS and HpC system, designed
to retain the solids and neutralise the pH of the water captured in Hydro demolition, and again in their Modular pH dosing systems.
Whilst their fleet has grown, so have their facilities and team (teamKT). Now, almost ten years later, Kelly Tanks has become an industry leader in concrete washouts, boasting the UK’s largest hire fleet whilst continu ing to supply water treatment systems worldwide. Mark and Kelly consist ently release new products each year and their innovative product range is complemented by their ongoing commitment to excellent quality and customer service.
To find out more, visit : kellytanks.co.uk
MARK AND KELLY CONSISTENTLY RELEASE NEW PRODUCTS EACH YEAR AND THEIR INNOVATIVE PRODUCT RANGE IS COMPLEMENTED BY THEIR ONGOING COMMITMENT TO EXCELLENT QUALITY AND CUSTOMER SERVICE.
T u r n f o o d w a s t e i n t o r e n e w a b l e e n e r g y S t a y c o m p l i a n t w i t h U K l e g i s l a t i o n G r o w e n v i r o n m e n t a l c r e d e n t i a l s
R e d u c e c a r b o n e m i s s i o n s i n f o @ k e e n a n r e c y c l i n g . c o . u k 0 8 0 0 6 4 4 6 6 1 8
While heavy plant and machin ery continues to embrace the advance ment of modern technology to improve efficiency and drive standards, there continues to be one area of high risk that remains a ‘real and credible threat’ to all businesses within one of the UK’s biggest industries.
With a large proportion of fires orig inating from within the engine bay, more specifically, in and around the turbochargers and exhausts, these areas carry a potentially devastating risk to all businesses. Generating heat that is well over the temperature required for instant combustion, the engine bay flies a red flag 24/7. It only takes a machine that has not been cleaned or properly main tained to cause a devastating and costly fire. As well as destroying the asset, it is important to understand the additional destruction a fire can bring:
• Safety of people
• Total loss of the machinery • Bad press • Loss of revenue
• Delay to work schedule
• Risk of injury
• Damage to the surrounding environ ment
With the growing awareness and un derstanding of fire suppression, many
insurers are waking up to the benefits that effective systems can offer both customers and insurers alike. Many have gone one step further by refusing to insure high-risk machinery unless fire suppression has been fitted. By way of encouragement, certain insurers are of fering operators the advantage of lower insurance premiums and lower excess fees if they install a recognised and approved fire suppression system.
Our detection system consists of a pneumatic detection tube (which is routed around the hazard areas) and a predefined discharge network (various nozzles and hoses) to deliver the ex
tinguishing agent. In the event of a fire, the heat from the flame will burst the pneumatic detection tubing, causing the pressure to drop, which release the sup pressant agent. The initial knockdown from the dry powder is immediate, while the supplementary wet chemical agent has an increased duration of protection to completely cool the hot surfaces. The combined effects of the agents ensure that the fire is extinguished and the risk of reignition is reduced. Detecting the fire in under 5 seconds ensures that even when a fire occurs, the asset is capable of returning to full operation once the fire suppression system has been recommis sioned.
As an example of how our system has protected machinery, our engineers had a call out to a system discharge. Much to the customer’s surprise, there had been a fire in the engine bay. Our system suppressed it within seconds saving thousands of pounds. We installed one of our dual agent fire suppression systems onto a shredder used to process wood. Throughout its working hours, the machine experienced an accumula tion of sawdust between the door and the engine bay. A piece of molten metal had become encased in the 6 inches of sawdust, causing the fire to start. Even though the detection tube was buried within the build-up, the fire was detect
THERE
TO BE ONE AREA OF HIGH RISK THAT REMAINS A ‘REAL AND CREDIBLE THREAT’ TO BUSINESSES WITHIN MANY INDUSTRIES.
ed almost immediately. No damage was caused to the machine, allowing the busi ness to still operate as normal with no downtime. During these current times, to order new plant machinery the lead time could be months. By having our Fireward fire suppression system fitted, it saved the owner hundreds of thousands of pounds and the risk of catastrophic consequences to the business.
Our industry-leading dual agent system is the perfect solution to protect heavy plant and machinery used within a vari ety of industries. Dual agent systems are an outstanding fire suppression method due to the combined benefits of dry powder and wet chemicals in one solu tion. The dry powder provides rapid-fire knockdown and excellent coverage, while the wet chemical has significant cooling properties.
Fireward’s Dual Agent system is per formance and durability accredited to RI:SE P-Mark SPCR 199. This approval
ly recognised approvals. The systems are manufactured in a strict and controlled process, meeting a consistent, high level of quality. Not only did Reacton set an impeccably high standard with our approval, but the system is also the most economically sized and approved system on the market. This allows smaller machines the option of being fitted with an approved system, this provides the whole industry with regulated systems that were often only for large vehicles.
installation, service and maintenance has allowed Fireward to rise through the ranks to become a partner of preference for many within the industry.
Fireward, Protecting People and Assets 24/7.
is for our heavy plant and machinery fire suppression systems, tried and tested in the harshest of environments to prove their capabilities and performance under vigorous testing conditions. Reacton Fire Suppression (our manufacturers) achieved the highest possible score with an A + rating. Reacton supply systems to Fireward from their UK based ware house, which is recognised by Made In Britain, ISO 9001:2015, and other global
With customer expectations at an alltime high, it is not enough to simply install a fire sup pression system that works. Guiding cus tomers through the ‘customer journey’ from specification and proposal to
To find out more about Fireward’s Au tomatic Fire Suppression systems, visit www.fireward.co.uk or get in touch with us- 0800 151 0249 or sales@fireward.co.uk.
IT IS NOT ENOUGH TO SIMPLY INSTALL A
SUPPRESSION SYSTEM THAT WORKS.
LTI rate has fallen by 300% over ten yearsone of the best in sector.
Modules such as event tracking, incident reporting, risk assessment and audit management will help Biffa to achieve its mission: to continually reduce the likelihood and severity of workplace harm.
Gary Carvell, Biffa’s Group Health and Safety Director, said: “Nothing is more important than the health and safety of our key workers, whether they’re frontline operatives delivering essen tial waste and recycling services right across the UK, or office staff working hard behind the scenes.
“It is also vital we help keep our cus tomers, contractors and members of the public safe too.
Biffa, the UK’s leading sustainable waste and recycling firm, is launching a new health and safety platform that will be a “game-changer” in how it manages risk.
Already the recipient of a full Five Star rating from the British Safety Council, and with an improving lost-time injury rate, the company says nothing is more important than the health and safety of its key workers, customers, contractors and the public.
Biffa employs around 10,000 people and collects waste from thousands of businesses and millions of households across the UK each day.
As part of its ongoing digital transfor mation, Biffa has made a significant investment to introduce EcoOnline – the class-leading online platform for managing risk and health and safety –across its whole delivery portfolio.
“EcoOnline is a real game-changer. It will revolutionise the way we manage risk across the business and follows the launch of our Safer Together programme in 2020 that centres on an interdependent approach, working collectively to ensure the safety of our people and those we work with.
AS PART OF ITS ONGOING DIGITAL TRANSFORMATION, BIFFA HAS MADE A SIGNIFICANT INVESTMENT TO INTRODUCE ECOONLINE
“The system will be available on people’s hand-held devices and mobile phones and can be used by every one, from front-line operatives right through to the Executive team.
“The platform makes it even easier to report hazards, near misses and incidents, and will present the infor mation, accurately and quickly. It gives us an immediacy we didn’t have before, and a much greater insight into what’s going on in the business, turning that information into predictive
data that will help us make informed decisions.”
Biffa’s lost-time injury rate has fallen by 300% over a ten-year period, making it one of the best performing organi sations in its sector. Biffa has set itself a target of reducing LTIs by a further 50% by 2030.
Biffa will begin building the EcoOn line platform in November, with a launch date in early 2024.
Göran Lindö, CEO of EcoOnline, said: “This is a crucial first step in Biffa’s transformation towards a more efficient, compliant, sustainable and streamlined risk management system. EcoOnline’s digital software allows data to be centralised, tracked and moni
tored, making it easier for users to lo cate and understand safety guidelines.
“Consistent and regular reporting is at the heart of Biffa’s ongoing com mitment to full transparency, and the latest software can simplify incident management to help ensure that the company can continue to protect its employees.
“Biffa is leading the charge in reduc ing workplace safety incidents, and I’m looking forward to seeing how our innovative technology can help take them to the next level with a user-friendly interface and on the go access to key information.”
Visit EcoOnline | EHS, Chemical & Learning Management Software for more details.
Plastics recycling charity, RECOUP, again proves its position as the number one conference in the plastics recycling and resources sector with another outstanding day of debate and presentations.
Stuart Foster, CEO, of RECOUP in his address highlighted that “we live in a world demanding better environmental protection, circularity and sustainability whilst wanting to hold on to consumer ism, low cost, convenience, growth and economic prosperity.” Foster reiterated that RECOUP, would continue to deliver the organisation’s aims with balance, integrity and evidence. He continued to announce that Morrisons was the latest company to join RECOUP and “if you are thinking of supporting RECOUP, now is the time.”
Tom Heap, of ‘Costing the Earth’ and BBC’s ‘Countryfile’ commented that it was an interesting time both politically and legislatively. Heap referred to the importance of legislation in relation to plastics recycling and resources.
With Heap’s direction, plastic packag ing tax, tray-to-tray recycling, invest ment in chemical recycling, feed stock quality and circular economy principles were debated. All speakers repeated previous conference calls to increase and improve collaboration.
Hayley Lloyd-House, Head of Cor porate Affairs and Sustainability at Nestlé Waters (UK) Ltd highlighted the positive joint work with RECOUP and drew attention to the ‘The 5 -pillar strategy’ aimed to Reduce, Re-use, & Refill, Redesign and Rethink behav iours.
The panel debated the lack of consist ency in kerbside plastics collections and communications as well as UK recycling capacity. With mixed mes
saging and ‘wish’ recycling causing contamination and a call for the harmonisation of labelling.
Paula Chin, Senior Policy Advisor – Consump tion at WWF set the scene in session two by stating that it was important that the sector use the “right material, in the right place and with the right approach.” Chin highlighted products such as disposable vapes and ques tioned why such products are placed on the market when there is clearly no end-of-life solution. Chin once again called on the delegates to appreciate that the only way forward was to reduce consumption.
Rowan Byrne, Marine Plastics Global Lead at Mott MacDonald commented on the issue of plastics in the natural environment particularly rivers and oceans, “to manage something you have to measure it” however, “the challenge with plastics in the environ ment is the issue gets bigger as plastics get smaller. Just because you can’t see it doesn’t mean it isn’t there.” Byrne further highlighted that perhaps there should be a ban on wet wipes.
“the challenge with plastics in the environment is the issue gets bigger as plastics get smaller. Just because you can’t see it doesn’t mean it isn’t there.”
RECOUP launched a number of reports and projects at the event:
• A Best Practice Guide for UK Plastics Recycling Communications
• Recyclability by Design 2023 and case studies highlighting the importance of recyclability basic principles, material substitution concerns and work in the area of bacon and meat packaging.
• ESA Quality Standard for Recycled Plastics with support from the British Plastics Federation, Recycling Associa tion and RECOUP, to define a quality standard for post-consumer recycling.
To access these reports, visit: www.recoup.org
The afternoon panel was chaired by Sara Banning, Innovation Lead from Innovate UK – UKRI. The panel called for the importance of data to be used for accountability, the need for clear government signals and policies for reuse and prevention tar gets, a mindset shift towards circular economy and the common theme of the day, collaboration.
Recoup’s conference will return next year on Thursday 28th September 2023.
For more information about RECOUP, the work they do and how to join please contact www.recoup.org.
TThe Big Sustainability Expo was designed back in 2015 to serve organisations in sup port of their sustaina bility, environmental management and cor porate social responsibility strategies. This year, sustainability has never been higher on the corporate agen da, as organisations wake up to their environmental responsibility and what it means for their future, which is also a vital part of their sustainable economic model.
With the UK and indeed, the world, facing unprecedented economic chal lenges, businesses could be forgiven for considering kicking their environmental agendas into the long grass. However, if The Big Sustainability Expo’s 7th-year run is anything to go by, this is most certainly not the case. We caught up with the organisers, Lynda Daniels and Anita Potten, just days after the Expo took place to gauge their thoughts on why businesses are attending.
“Feedback from our delegates on the day was loud and clear,” they told us. A rocky financial climate is one of the reasons we are here in search of the solutions and experts that will help us tackle issues such as waste in all its many forms, in order to avoid unnecessary expenditure. “Yes, it’s about the planet and playing our part,” they are keen to add, “but this agenda really does save money too, and that is another reason we are supported within our organisation.”
This year’s Sustainability Expo featured over 100 different exhibition stands, all of which pledged to support the efforts of businesses as they navigate their own corporate sustainability strategies. Helping to catapult projects which lead to carbon reduction that will only serve to help our planet, this year’s showcased the latest products, services, technolo gies and innovations making their mark today. This year’s expo also featured a range of education workshops, as well as leading experts from across the country, a bigger than ever Speaker Platform, and much more!
EXPERTS CAN ADVISE US HOW TO TACKLE SUCH ISSUES AS WASTE IN ALL ITS MANY FORMS, IN ORDER TO AVOID UNNECESSARY EXPENDITURE”.
“To name just a few highlights on the show floor this year, we were pleased to host the Environment Agency as they featured their Preventing Plastic Pollution project,” the organisers shared. “We were also keen to showcase a new partnership between ThinkCarbon and Wastetrade - an artificial intelli gence-based carbon analysis tool de signed to minimise the carbon footprint of the waste sector and introduce more environmentally conscious practices into the industry. Of course, there is also the issue of disposing of unwanted items within our businesses, and exhibitor, Renewed Store, tackles this on our behalf by taking unwanted IT equipment and refurbishing it to BSI standards in order to offer it back into the marketplace with a 40% cost saving over buying new.
Alongside this, Pearce Compaction, from Dorset, provides a circular econo my approach to compacting and baling equipment in this year’s expo. They both sell and hire their UK-manufactured machinery, maintain it, and they will take it back at the end of its useful life
for that business only to refurbish it and send it back out again as good as new.”
“Overall, we were delighted by the types of organisations that came through the door again this year,” they summa rised. “We knew our numbers would be reduced with an unscheduled bank holiday in the same week, but once again, professionals from large corporations to SMEs and the public sector joined us and proved that reducing commercial carbon impact is as buoyant and as necessary as ever.”
The Big Sustainability Expo are already working towards their 2023 goals, and the Expo will open its doors once again on October 3rd.
To find out more, visit: www.southernsustainability.co.uk
With our current climate crisis, going green has never been more popular. With everyday items regularly stored in some variation of plastic con tainer, you’d think that these containers would be easy to recycle, but this is not always the case. It is important to know what to do with these containers when we’re done using the product contained inside.
Some everyday items can be easily recycled, such as:
• Chocolate and biscuit tubs and trays
• Dishwasher tablet / washing capsule tubs
• Non-black plant pots
• Pots, tubs e.g. yogurt, soup, butter and ice cream
• Trays or punnets, e.g. raw or cooked meat trays, Microwaveable ready meal bowls/containers, take-away trays and fruit & veg trays
Always check that your plastic food storage containers and lids are embossed with the recycling symbol before putting them in the recycling bin. The universal recycling symbol consists of three arrows in the shape of a triangle.
There is usually a number inside, so if you see a 1 or 2, then you’ll be able to recycle the container. Most recycling programmes also accept number 5, how ever, if you’re unsure, check with your local recycling service.
However, some containers aren’t as easily recycled and can end up causing issues when trying to dispose of them.
Containers such as large plastic storage boxes or Tupperware are not allowed in your kerbside recycling bin. Instead, there are alternative recycling ideas that you can do with these everyday items such as plastic water bottles, milk cartons and shampoo bottles.
Many storage containers can be upcycled and can be used for a variety of purpos es. For example, you can use containers stationery and crafts, or even fill them with soil to grow small indoor plants.
Containers and packaging are the main source of plastic waste, and in the UK accounts for nearly 70% of our plastic waste. Some main supermarkets such as Tesco, M&S Aldi and Lidl are attempting to take it one step further and eradicate them from many of their products or reduce plastic packaging and containers to a minimum. Some household brands are losing their containers all together, in an attempt to reduce packaging and container waste as well as their carbon footprint.
These include:
• Pot noodle – Pot noodle decided to ditch its famous pot container for the first time in its 40-year history, and branded its new - Lost the pot, Pot noodle. The new product was made with the idea to make the snack more environmentally friend ly, by removing the hard plastic pots.
• SMOL washing capsules have opted to ditch all plastic containers and wrappers and instead post their tablets direct to the buyer in one recyclable cardboard box. The dish wash plastic-free packs took over a year to develop and any branding on the packaging has been printed using vegetable-based inks.
• Oral B, Sensodyne, Aquafresh and Corsadyl scrapped the cardboard box that toothpaste and mouthwash products are usually packaged and sold in.
While some brands are scrapping con tainers all together, while this may not be possible for all, other brands such as Dove and Lenor washing liquid are also looking to reduce the size of containers and therefore the plastic used to make them by cutting the weight of packaging through better and lighter designs and ultra-concentrated formulas meaning less packaging is needed.
If you want to purchase a plastic storage container, there are many different options that you can make in a conscious effort to reduce your plastic usage. You could opt to buy a container made from recycled materials such as recycled con tainers constructed from materials like old car batteries. This small but adapt able change can contribute to everyone taking the small step to reduce their carbon footprint and contribute to the reduction in plastic waste.
Come and see us at RWM & Letsrecycle Live 2022 Stand R-N184, near to the Packaging Theatre.
truly sustainable world by conserving finite resources.