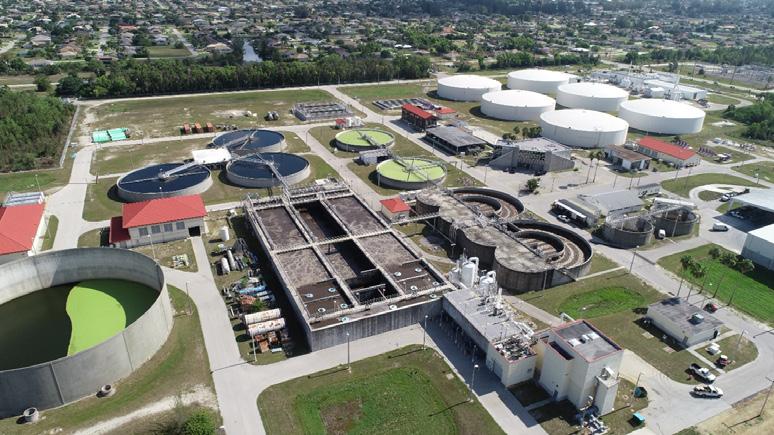
7 minute read
Process Page: Award-Winning City of Cape Coral’s Southwest Water Reclamation Facility: Optimizing Aeration Control Produces Multiple
Greetings from the FWEA Wastewater Process Committee! In 2020, the FWEA Process Committee conducted a thorough review of the historical Earl B. Phelps Award scoring criteria. After a detailed, line-by-line review, the FWEA Process Committee recommended updates to the criteria to reduce subjectivity and the potential for inspector bias. For example, instead of scoring points based only on carbonaceous biochemical oxygen demand (CBOD5) and total suspended solids (TSS) removal efficiencies, nitrogen and phosphorus removal efficacies were included in the scoring system, even for facilities not permitted for nutrient removal. Overall, a significant number of subjective scoring systems were refined and a detailed, treatment-based objective scoring system was implemented for the 2021 Earl B. Phelps Award evaluation. The evaluation criteria are now heavily focused on effluent quality, including nutrient removal. This allows treatment facilities to compete (in their respective size range and configuration) to earn the Earl B. Phelps Award based on objective, treatment-based excellence.
This month’s column highlights the 2021 Advanced Secondary Earle B. Phelps Award winner (City of Cape Coral Southwest Water Reclamation Facility) and the significant aeration control system improvements completed over the past year that resulted in substantial blower energy reduction, while consistently exceeding nitrogen removal regulatory requirements.
Advertisement
Award-Winning City of Cape Coral’s Southwest Water Reclamation Facility: Optimizing Aeration Control Produces Multiple Benefits
Matt Astorino and Matt Tebow
Background
The Water Independence for Cape Coral program was started in the late 1980s and was designed to reduce the impact irrigation has on the Mid Hawthorne Aquifer, one of the main sources for drinking water supply for the City of Cape Coral (city). The city has been recognized as having one of the largest municipal residential reuse water systems in the United States, with a daily average of 31.42 million gallons per day (mgd).
The city’s irrigation is supplied by treated wastewater from its two wastewater facilities, Southwest Water Reclamation Facility (SWWRF) and Everest WRF, and supplemented by freshwater canal water pumped from the city’s five freshwater canal pumping stations.
The city’s SWWRF was originally constructed in 1992 using a carousel-style oxidation ditch to treat an annual average daily flow (AADF) of 6.6 mgd. The SWWRF was expanded in 2008 to 15 mgd AADF and currently treats approximately 7 to 8.5 mgd seasonally.
Treatment System and Components
The headworks consists of two mechanical step screens and one manual bar screen, grit removal provided by four stacked trays, vortextype grit removal units, odor control, and two cyclone/classifier units, followed by a common influent mixing channel. The secondary treatment (activated sludge) process utilizes the anaerobicanoxic-aerobic (A2O) process. Although not a regulatory requirement, the A2O process is capable of biological removal of both nitrogen and phosphorus.
Three A2O process basins receive flow from the common influent mixing channel, with each basin having an anaerobic zone, followed by an anoxic zone and an aerobic zone. Each basin has four floating mixers, with two mixed liquor internal recycle pumps that pump from the end of the aerobic zone to the beginning of the anoxic zone. Mixed liquor from the three basins flows to a common reaeration channel; the combined flow is then split and gravity-fed to five secondary clarifiers (two at 100-foot-diameter and three at 120-foot-diameter) for settling.
The sludge pump station, with multiple return activated sludge (RAS) and waste activated sludge (WAS) pumps, discharges to the common influent mixing channel or sludge holding tanks, respectively. Effluent from the secondary clarifiers is gravity-fed to two sets of effluent automatic backwash (traveling bridge) filters. The effluent from the backwash filters then flows by gravity and is split between two chlorine contact chambers (CCC). High-level disinfection is provided by liquid sodium hypochlorite. The reclaimed water is then stored in three 5-million-gallon (MG) tanks, or due to wet weather or low demand, pumped into the deep injection well.
The SWWRF provides reclaimed water to the city’s reuse service area system, also known as the Water Independence for Cape Coral system. The SWWRF includes a 6.8-MG reject Continued on page 6
Continued from page 4 storage tank where substandard reclaimed water may be directed. Biosolids processing includes the carrousel oxidation ditches repurposed into four aerated sludge holding tanks and three centrifuges.
Aeration Control System Optimization
One of the major enhancements that the city implemented to optimize treatment efficiency and to reduce power consumption was to make changes to the aeration control system. Wastewater treatment aeration systems are one of the primary contributors to the overall cost of treatment. Typically, the longterm operational costs will significantly exceed the initial capital cost. Optimizing, retuning, and upgrading existing aeration control systems can provide operational cost savings for many treatment facilities, including savings in energy and supplemental carbon, if applicable.
Aeration control system strategies typically include the following: S Ability to meet aeration process set point (e.g., dissolved oxygen [DO]) quickly and maintain that set point under variable loading conditions S Minimize actuator starts/stops while consistently maintaining the process set points S Optimize energy usage by minimizing pressure loss in the system
The term “most open valve” (MOV) control is frequently used, but sometimes the exact meaning of the term is not always clear. Jenkins (2013) provides a useful definition:
“MOV logic is a technique developed to eliminate excess power demand created by constant pressure control...the fundamental principle is that at least one of the air flow control valves will be at the maximum position at all times.”
The SWWRF was originally furnished with a pressure-based MOV system, coupled with integrally geared, single-stage centrifugal blowers. The pressure-based control system attempts to minimize unnecessary pressure losses compared to a constant pressure blower system.
The control strategy for a pressure-based MOV system at SWWRF used three cascades of control loops: 1. The DO proportional-integral-derivative (PID) controllers calculate an air flow set point for each aeration control zone. 2. Flow/valve flow PID controllers calculate a valve position set point to meet the air flow set point calculated in the first loop. 3. A blower pressure PID controller modifies the blower operation to maintain a floating blower pressure set point calculation based on the
MOV position.
One of the challenges at the SWWRF with the pressure-based MOV aeration systems was the need to periodically “retune” the DO and pressure PIDs for optimal performance, depending on seasonal flows/loads, ambient conditions, number of operational blowers, etc. After looking at historical DO and air flow trends, the SWWRF staff developed a type of MOV “floating control” aeration strategy, rather than only PIDs. A disadvantage of the pressure-based MOV-DOPID control is that it assumes a linear relationship between DO concentration and air flow rate, whereas, in reality, the relationship is dependent on a variety of factors (temperature, oxygen mass transfer, and other process-related factors) that are constantly changing. The term “floating control” is similar to an “adjust/wait and see” approach, in that the control system waits for an operatoradjustable delay response, which gives the process DO concentration adequate time to adjust to changes in air flow.
The results of the new strategy, developed in-house, achieved DO measurements in the basins much tighter to the actual DO setpoint and reduced the blower aeration header pressure approximately 0.5 to 1 pounds per square inch (psi). After these changes, the WRF blower amp draw was reduced by approximately 100 amps, resulting in significant operational cost savings.
Other improvements this past year at the SWWRF include the following: S Installation of TSS probes in the WAS and aeration basins (mixed liquor suspended solids [MLSS]) to optimize and maintain consistent process control with solids retention time (SRT). S Installation of ammonia ion selective electrode (ISE) probes in the process tanks to record, trend, and optimize DO setpoints to provide sufficient aeration for complete nitrification, while minimizing “excess” DO concentrations, thus saving energy on aeration. S Installation of new, fine bubble, membrane diffusers for increased oxygen transfer efficiencies.
Moving forward, the SWWRF staff is developing a process-model-based control algorithm to calculate the air flow set points in each control zone based on oxygen uptake rate (OUR), utilizing the ammonia ISE data and coupled with the optimized MOV aeration control strategy.
The dedication and hard work of the entire SWWRF maintenance, electrical, and operational staff resulted in the SWWRF consistently producing exceptional effluent quality, exceeding all regulatory requirements, and reducing chemical usage and energy consumption.
The SWWRF is proud to be the recipient of the Advanced Secondary Earle B. Phelps Award for the second year in a row.
Matt Astorino is chief operator of the Southwest Water Reclamation Facility in City of Cape Coral and Matt Tebow is a water and wastewater engineer with Kimley-Horn in West Palm Beach. S

Back row, left to right: Anthony Rivoli, operator; Dakota Kayatta, custodian; Brad Trautman, operator; Matt Astorino, chief operator; Troy Charno, operator; Marcus Papp, instrumentation; Carlos Rodriguez, programmer; Zach Pentaude, laborer; and Joe Holowell, maintenance supervisor. Front row, left to right: Rob Tracy, operator; John Pitzer, operator; Igor Gutin, operator; Pat Long, water reclamation manager; Dale Kingsbury, maintenance mechanic; and James Thomas, maintenance mechanic.
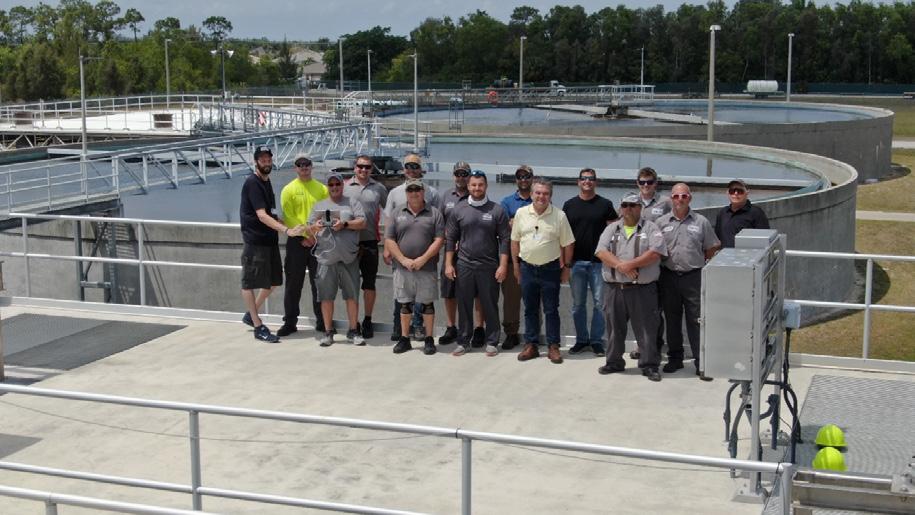