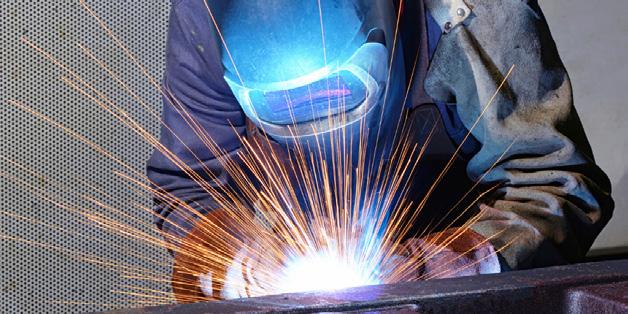
8 minute read
Let’s Talk Safety—Weld Well to End Well
This column addresses safety issues of interest to water and wastewater personnel, and will appear monthly in the magazine. The Journal is also interested in receiving any articles on the subject of safety that it can share with readers in the “Spotlight on Safety” column.
Weld Well to End Well
Advertisement
Safety is a critical consideration for any welding project. Arc welding is a safe undertaking when proper precautions are taken, but if certain measures are ignored, welders (and those around them) face an array of hazards that can be potentially dangerous, including electric shock, respiratory hazards, eye and skin injuries, fire, explosions, and more.
To help keep welders safe, organizations such as the American Conference of Governmental Industrial Hygienists, American Welding Society, and Occupational Safety and Health Administration (OSHA) offer safety guidelines to help control, minimize, or help employers and workers avoid welding hazards.
Here are a few to review before beginning any welding project.
Eye Injuries
Welding and cutting operations are a major source of eye injury. Related accidents occur when proper personal protective equipment (PPE) is not worn. The most common eye injuries result from flash burn, metal flying into the eye, and particulates falling into the eye. The only measure that will prevent eye injury is the use of appropriate eyewear and shields. It’s also important not to wear contact lenses while welding or near where welding is taking place. Welding helmet sand filter plates are intended to help protect users from arc rays and from weld sparks and spatters that strike directly against the helmet. They are not intended to protect against slag chips, grinding fragments, wire wheel bristles, and similar hazards that can ricochet under the helmet. Spectacles, goggles or other appropriate eye protection must also be worn to protect against these impact hazards.
When arc cutting and arc welding with an open arc, OSHA requires operators to use helmets or hand shields with filter lenses and cover plates. Nearby personnel viewing the arc must also be protected and the welder should always use a welding curtain or wall. Safety glasses with a shade 2 lens are recommended for general-purpose protection for viewers.
Skin Injuries
Injuries to the skin usually result from ultraviolet rays or from hot metal. The hot metal may be the material being worked on, or it may be part of the equipment. Unprotected skin is at risk for injury. In addition to burns, it’s easy for exposed skin to be cut during work with sharp metal. Proper safety shoes, clothing, and PPE will greatly reduce the chances of skin injury.
Respiratory Hazards
Without adequate ventilation, or when adequate PPE is not used, the threat of respiratory injury greatly increases. Before welding, the welder should know what the metal is and the potential effects of the fumes produced, which include carbon monoxide. Inhaling welding fumes or gas can produce metal-fume fever, the symptoms of which include a metallic taste in the mouth, fatigue, nausea, and muscular and joint pain. Depending on the metal or alloy, the results can be fatal.
Adequate ventilation (natural, mechanical, or respiratory) must be provided for all welding, cutting, brazing, and related operations, which means enough ventilation so that a person’s exposure to hazardous concentrations of airborne contaminants is maintained below the level set by federal standards.
Adequate ventilation depends on the following factors: S Volume and configuration of the space where the welding operations occur S Number and type of operations that are generating contaminants S Natural air flow rate where operations are taking place S Location of the breathing zones for the welder and other workers in relation to contaminants or sources
Natural ventilation is considered sufficient for welding and brazing operations if the work area meets these requirements: S Space of more than 10,000 square feet is provided per welder S A ceiling height of more than 16 feet S Welding is not done in a confined space S Welding space does not contain partitions, balconies, or structured barriers that obstruct cross ventilation
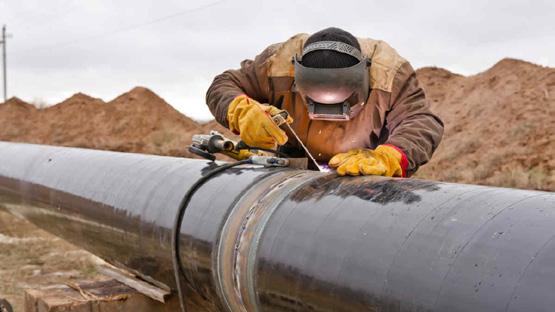
Whenever feasible, local and area ventilation systems should be used to remove harmful fumes and gases; however, in many cases, engineering controls alone cannot reduce exposure levels adequately. In such cases, it may be appropriate to use respirators. For most welding applications, an array of respirator options exist that offer specific benefits.
Electric Shock
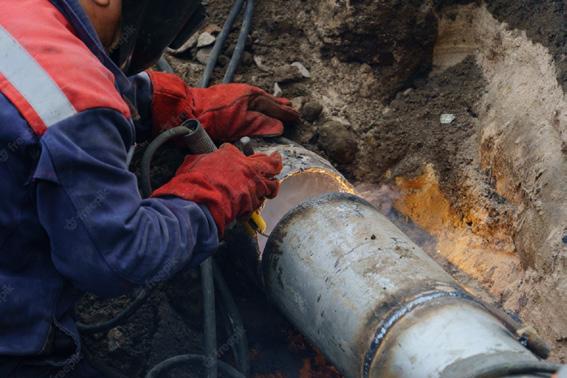
Electric shock is one of the most serious and immediate risks facing a welder. It can lead to severe injury or death, either from the shock itself or from a fall caused by the reaction to a shock.
Electric shock occurs when welders touch two metal objects that have a voltage between them, thereby inserting themselves into the electrical circuit. For instance, if a worker holds a bare wire in one hand and a second bare wire with the other, an electric current will pass through that wire and through the welding operator, causing an electric shock. Be aware that the higher the voltage, the higher the current, and thus, the higher the risk for the electric shock to result in injury or death.
The most common type of electric shock is secondary voltage shock from an arc welding circuit, which ranges from 20 to 100 volts. Bear in mind that even a shock of 50 volts or less can be enough to injure or kill an operator, depending on the conditions. Due to its constant change in polarity, alternating current (AC) voltage is more likely to stop the heart than direct current (DC). It’s also more likely to make the person holding the wire unable to let go.
Be sure all electrical equipment is properly installed, inspected, operated, and maintained. Before use, consider the following: S Placement of welding machines S Placement of cables S Load protection S Use of electrodes and holders
Fire Hazard
Welding and cutting should be done in designated areas that are free of flammable materials or conditions favorable to fire or explosion. If your utility has a hot-work permit program, make sure to follow its requirements. Before and during the welding operation, the welder and safety watch should do the following: S Inspect the area for flammable and combustible material before welding or cutting begins S Cover cracks or floor openings S Have fire extinguishers on hand
During welding, constantly watch for fires between walls, on opposite sides of metal partitions, or in any concealed place.
Personal Protective Equipment
Your utility’s PPE helps to keep welding operators free from injury, such as burns, which are the most common welding injury, and exposure to arc rays. The right PPE allows for freedom of movement, while still providing adequate protection from welding hazards.
Thanks to their durability and fire resistance, leather and flame-resistant cotton clothing is recommended in welding environments. This is because synthetic material, such as polyester or rayon, will melt when exposed to extreme heat. Welding leathers are especially recommended when welding out of position, such as applications that require vertical or overhead welding.
Avoid rolling up sleeves or pant cuffs because sparks or hot metal can deposit in the folds and may burn through the material. Keep pants over the top of work boots—don't tuck them in. Leather boots with 6- to 8-inch ankle coverage are the best foot protection. Metatarsal guards over the shoelaces can protect a welder's feet from falling objects and sparks.
Confined Spaces
Because of the small size and questionable atmosphere in most confined spaces, welding and cutting in such spaces requires very serious thought and planning.
There are very specific regulations from OSHA when it comes to welding in confined spaces. If the area can’t get proper ventilation without blocking the means of entry, welders must use respirators and be in constant communication with a coworker on the outside. Another OSHA rule states that safety belts, lifelines, and preplanned rescue procedures are required if the welding work has to happen in a space with a very small entryway (like manholes).
Always check the following before working in a confined space: S Make sure there isn’t any equipment blocking the exit S Test the air for toxic gases before entering the workspace S Remove all hazardous materials S Keep vents open and making sure valves are tight and leak-free S Have the means to immediately shut off gases, fuel, and power from inside the space if possible
Fire and Explosions
The welding arc creates extreme temperatures and may pose a significant fire and explosion hazard if safe practices are not followed. While the welding arc may reach temperatures of 10,000°F, the real danger is not from the arc itself, but rather the intense heat near the arc and the heat, sparks, and spatter created by the arc. This spatter can reach up to 35 feet away from the welding space.
To prevent fires, before beginning to weld inspect the work area for any flammable materials and remove them. Flammable materials are comprised of three categories: S Liquid, such as gasoline, oil, and paint S Solid, such as wood, cardboard, and paper S Gas, including acetylene, propane, and hydrogen
Other Safety Considerations
In any welding situation, the operators should pay close attention to safety information on the products being used and the safety data sheets provided by the manufacturer, and they should work with their employer and coworkers to follow appropriate safe practices for their workplace. Good common sense is key to a safe workplace when welding. If opening cans of electrode, keep your hands away from sharp edges. Remove clutter and debris from the welding area to prevent tripping or falling, and never use broken or damaged equipment or PPE. By following these safety practices, operators can stay safe and alive and keep production moving with no lost-time accidents. For additional information, go to the OSHA website at www.osha.gov, or the website for the American Welding Society at www.aws.org. S Florida Water Resources Journal • January 2023 33