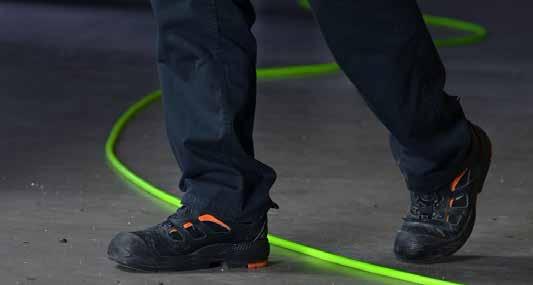
1 minute read
FWPCOA Online Training
Continued from page 60 S Make sure the trigger or operating valve on the tool is closed. Air supply shutoff valves should be located (as near as possible) at the point of operation. S Air hoses should be kept free of grease and oil to reduce the possibility of deterioration. S Check the run of the line to see that it’s
protected from possible damage and is not a tripping hazard. When possible, air supply hoses should be suspended overhead, or otherwise located to afford efficient access and protection against damage. S Be sure the valve is closed on the supply side of the coupling before changing the tool at the end of a compressed-air line. No
Advertisement
matter where the valve is—close it. Never simply kink the hose. S After closing the valve, pull the trigger or open the operating valve to release the line pressure; then you can make the required tool change. S Before the tool is disconnected (unless it has quick disconnect plugs), the air supply must be turned off at the control valve and the tool bled of air. S Static electricity can be generated through the use of these tools. This type of equipment must be grounded or bonded if it’s used where fuel, flammable vapors, or explosive atmospheres are present.
All components of compressed-air systems should be inspected regularly by qualified and trained employees. Maintenance superintendents should check with state and/ or insurance companies to determine if they require their own inspection of this equipment. Practice these safety measures when working with compressed air. Remember, there is power in pressure—and power means extra precaution. S
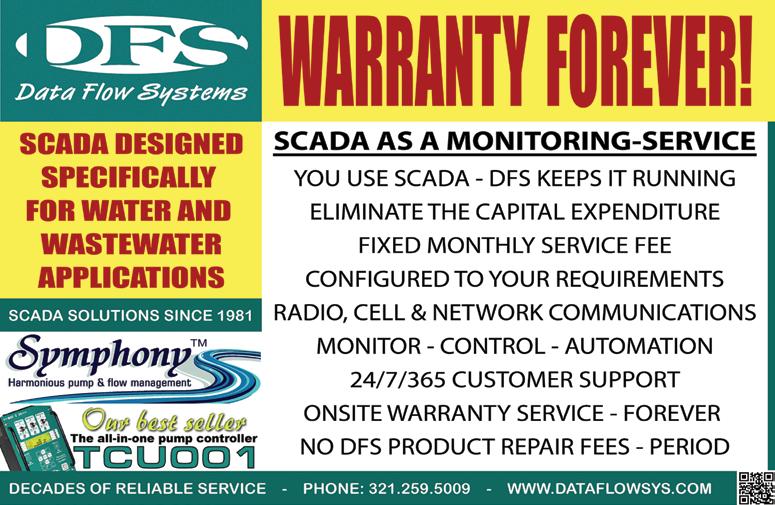