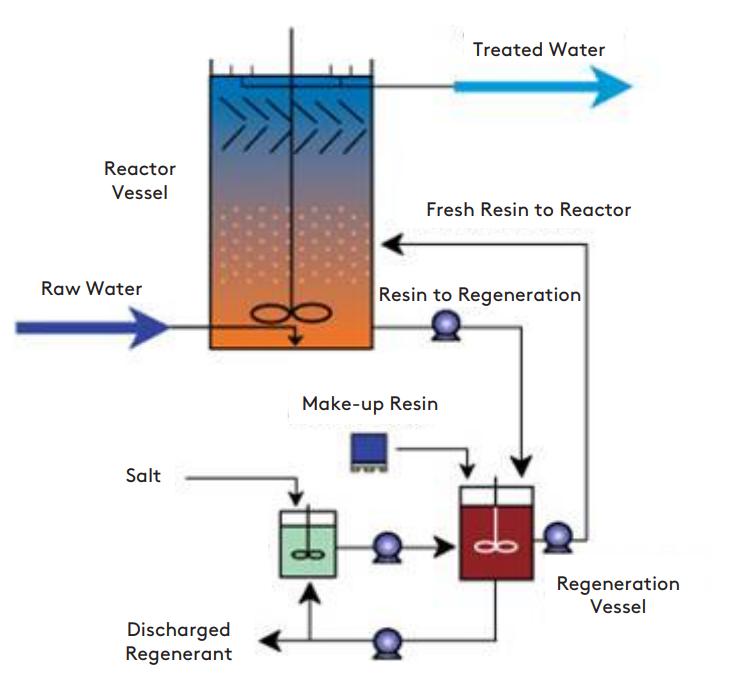
18 minute read
Three Ion Exchange Technologies, One Tough Decision for Florida Utilities—Tyler Smith, Chris
FWRJ Three Ion Exchange Technologies, One Tough Decision for Florida Utilities
Tyler Smith, Chris Reinbold, Vinnie Hart, and Larry Elliott
Advertisement
Over the last decade, the ion exchange (IX) process has increasingly become a technology of interest for the removal of natural organic compounds in Florida source waters. Three IX options for municipal treatment plants include: S Fixed bed vessel, which is commonly used throughout Florida and the United States. S Fluidized bed, such as magnetic ion exchange (MIEX), which has seen limited use in Florida and the U.S. (about 12 installations). S Suspended ion exchange (SIX), which has four installations in Europe and is on the verge of its first U.S. installation in Tampa.
Considering Florida’s variability in source water composition and other site-specific considerations, one IX process does not fit all, and each type of IX should be evaluated, considering, among numerous other factors, a utility’s project goals, facility size, operation and maintenance (O&M) aspects, and costs.
This article dives into the primary differences, similarities, and pros and cons for the three IX options so that Florida utilities can consider the most optimal solution for their water quality challenges. Case studies from pilot- and full-scale installations across Florida, varying in size, capacity, and water quality characteristics, were considered.
The MIEX is the only patented fluidized bed process (owned by IXOM Watercare Inc.) and uses a magnetized strong base anion exchange resin that is proprietary (the resin and process are both patented). The process was primarily developed to remove dissolved organic carbon (DOC) and the resin’s magnetic properties help facilitate settling (to avoid carryover to downstream processes). The MIEX resin has a mean particle size of 180 to 200 micrometers (µm). The small particle size and macroporous nature increases the available surface area, compared to traditional ion exchange resins.
The MIEX process allows water and IX resin to flow through a contact tank with mixing, in which DOC and other negatively charged ions are exchanged for chloride ions. Figure 1 shows the general process flow of MIEX. Raw water flows upward from the bottom of the fluidized
Tyler Smith is senior project engineer with Carollo Engineers Inc. in Phoenix. Chris Reinbold is a project manager with Carollo Engineers Inc. in Palm Beach. Vinnie Hart is a project manager with Carollo Engineers Inc. in Denver. Larry Elliott was a vice president with Carollo Engineers Inc. in Orlando (deceased).
bed reactor/tank, where it’s contacted with resin. The resin ideally remains in suspension through the use of an agitator operating at low speeds. A series of tube settlers (or plates) at the top of the reactor vessel separate the resin from the water. Treated effluent overflows into collection launders to downstream treatment.
The original treatment scheme had two stages (contact, followed by settling) with resin concentrations in the 10 to 15 milliliter (mL)/L range, while the newer “high rate” systems combine resin contact and settling in the same tank, with increased resin concentrations in the range of 200 to 250 mL/L. Virgin resin is added to the process to make up for quantities of resin that may be inadvertently carried downstream or lost to attrition. At any given time, a small portion of the resin is withdrawn from the reactor vessel, regenerated in semibatch configuration, and returned to the reactor for reuse.
The MIEX has multiple full-scale and highrate installations in the U.S.; some of the larger installations include Palm Beach County Water Utilities Dept. (Water Treatment Plant 2; 16.4 mil gal per day [mgd]), Boynton Beach Utilities (20 mgd), and the C.B. Collier Water Treatment Plant in Gadsden, Ala. (24 mgd). Like the other IX technologies discussed, the resin itself has a high affinity for organics to facilitate their removal through ion exchange. In particular, the strong base anion exchange resin is effective at removing hydrophilics, humic substances, building blocks, and low-molecular-weight acids.
For Palm Beach County, its full-scale MIEX process was able to reduce raw water total organic carbon (TOC) from 13 to 4 mg/L. A MIEX pilot study conducted for the City of Tampa showed reduction of TOC from 24 to 9 mg/L. Overall, the process has been proven for organics removal in Continued on page 64
WATER MANAGEMENT. EVERYTHING IS INTERCONNECTED.
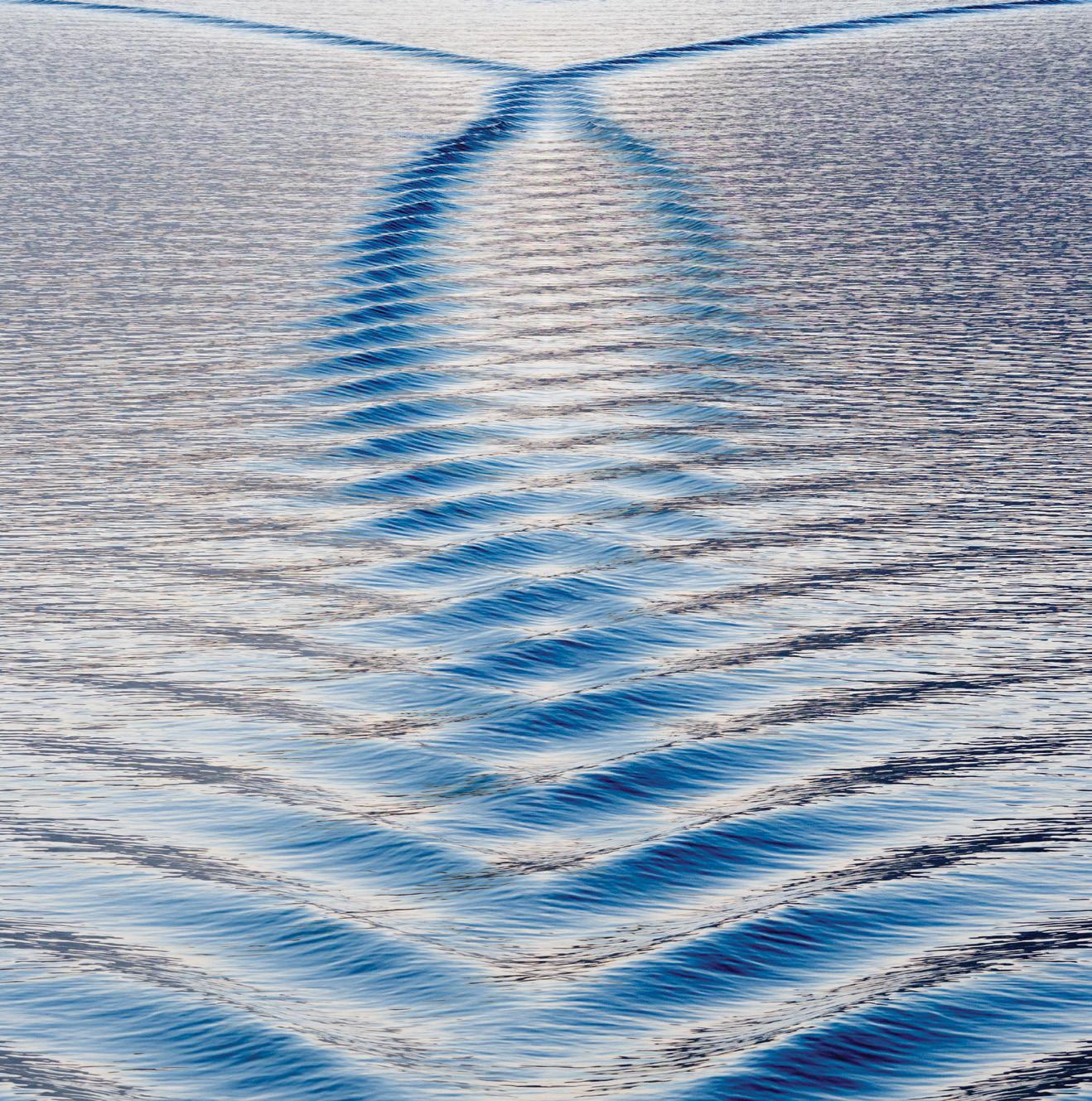
WATER
OUR FOCUS
OUR BUSINESS OUR PASSION Water treatment. Water reuse. Stormwater management. Collection and conveyance. They are not separate. They interact and affect each other every day. In today’s world, holistic water management is not a luxury, it’s a necessity. At Carollo, we ensure water at every stage in the cycle works together to deliver dependable, resilient water supplies for communities like yours. It’s all one water and for nearly 90 years, that’s how we’ve managed it. Interested? Inspired? Now’s your chance to make a splash! Join Carollo and make your mark.
Continued from page 62 the range from 50 to 70 percent TOC removal for both surface water and groundwater applications.
Due to the high loading rate configuration, the hydraulic retention time in the reactor is typically five minutes, and the resin remains in the contactor until it’s pumped to the regeneration system. Also, because of the high loading rate, the resin in the reactor is highly concentrated to achieve desired organics removal, with a typical concentration of 200 mL of resin per liter of water. Since only a portion of the resin is removed for regeneration at any given time, fresh (regenerated) resin makes up about 1 to 2.5 mL per liter of water in the reactor. This means the resin residence time can be up to a thousand times the hydraulic detention time.
The frequency of resin regeneration is quantified by bed volume (BV), which equals the volume of water treated divided by the volume of resin regenerated. Lower BV indicates a higher regeneration frequency. The MIEX process operates between 200 and 1000 BV (depending on source water constituents), where lower BV typically results in higher organics removal (since the resin is being regenerated more frequently).
The resulting salt use in the regeneration process is on the order of 300 to 800 lbs of salt required per mil gal (MG) of water treated. Lower BV treatment requires more salt, compared to higher BV treatment. Waste brine treatment options are offered by IXOM for salt recovery, thereby reducing overall salt consumption and waste brine volume disposal. Brine treatment options have unique challenges that require additional treatment steps and may or may not be viable, depending on the regeneration rate, salt use, and site-specific considerations.
In addition to the significant organics reduction, there are many benefits to the MIEX process, as it’s minimally affected by suspended solids, low concentrations of sand, or other colloidal particles; thus, it’s ideally suited as a pretreatment process for surface waters prior to conventional treatment. In this type of application, and as with suspended IX, the process provides great benefit as it serves as the primary treatment process responsible for removing organics, which can significantly reduce downstream chemical demand (i.e., coagulants or chlorine), sludge processing, and operating costs. Additionally, the magnetic resin is self-attracting, promoting the formation of large agglomerates that readily settle with hydraulic loading rates (up to 10 gal per minute (gpm)/sq ft).
The proprietary MIEX resin currently offered is manufactured in Australia and shipped to U.S. water plants employing this technology. Although the resin has an affinity for organics removal, it also has an affinity to remove inorganic containments, like sulfate, nitrate, and phosphate. Other utilities, like St. Cloud Utilities and Toho Water (both in Florida), have experienced issues with sulfide/sulfate, as the resin has a tendency to foster sulfide oxidizing bacteria growth and irreversible fouling of the resin. The biological growth decreases the resin’s specific gravity and can cause resin loss out of the reactor. Additionally, any iron present in the raw water must be oxidized before the MIEX reactor, as iron oxidation within the process will likely foul the resin.
Biological fouling has been observed in many full- and pilot-scale applications. A pilot study conducted in Tampa revealed the need to prechlorinate (up to 2 mg/L) the raw water supply prior to MIEX to discourage biological growth on the resin. Additionally, the long resin detention times, coupled with the level of organics loading onto the resin, likely causes the resin to become irreversibly fouled over time due to reduced desorption of organics during regeneration. In full-scale applications, this is shown by reduced organics removal over time, with mediation occurring through increased virgin resin additions. Fouling of the resin can result in resin loss, resin attrition, and a change in density that, in turn, impairs its ability to remain in suspension and fluidized during steady-state conditions. Further, air entrainment and pumping of resin can result in resin attrition, ultimately leading to loss and increased operating costs for resin replacement.
The suspended ion exchange (SIX) process is similar in some aspects to MIEX, but uses a nonproprietary resin in suspension. It flows in a plug flow regime, as opposed to a completely stirred tank reactor (CSTR) vessel. Virtually, any strong base, gelular, anionic exchange resin can be used in the process, given that it has the appropriate settling properties. These resins have similar affinity, selectively, as fixed bed IX and MIEX resins. Figure 2 shows the process flow diagram.
The resin is dosed into the process water (either as a pretreatment or post-treatment option) in low doses (10 to 15 mL/L), which then flows to the contactor (ideally with plug flow configuration). After the contactor, the resin is continuously separated from the flow stream using lamella (plate) settlers. Treated water flows over the plate settlers and is sent to the next treatment process. The collected resin is conveyed to a regeneration tank, where it’s regenerated in a batch process with a salt brine solution and continuously returned to the resin storage tank for reuse. Resin is regenerated after each passage through the approximately 30-minute contactor, thereby eliminating the compounding of resin residence times (via multiple passes) in the reactor and promoting a uniform resin loading.
The SIX treatment process originated from a utility, PWN Technologies in the Netherlands, but is nonproprietary and not patented. There have been many pilot- and bench-scale studies completed on a new SIX® process, including a 10-month pilot study just completed in Tampa. Organics removal through the SIX pilot was similar to fixed bed ion exchange and higher than MIEX, with up to 80 percent removal of TOC. There are currently few full-scale water treatment plants employing this technology in the world, and none currently in the U.S. The PWN Technologies owns and operates a 32-mgd surface water treatment plant in the Netherlands called Andijk III. This particular SIX installation, in operation since March 2014, is utilized to remove turbidity, organics, nitrate, and sulfate before the water is treated with ceramic membranes. In full-scale application, the plug flow regime necessary for the process is achieved through use of multiple and smaller completely mixed reactors (or basins) in series for even distribution of flow and contact time,
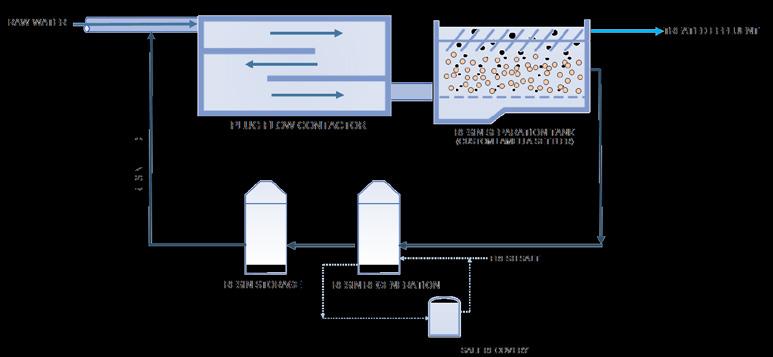
resulting in a maximum feasible train capacity of 10 mgd. Resin is kept in suspension through use of diffused air, as depicted in Figure 3.
In the SIX process, contact time and BV treatment directly influence the size and number of contactors since the resin and water experience the same hydraulic retention time. The BV can range from 20 to 200, depending on the resin dose (5 to 50 mL/L); therefore, the resin is regenerated more frequently than MIEX resin, and 100 percent of the resin that is dosed is regenerated after each cycle in the contactor. Since the resin is not heavily loaded with organics, previous studies have indicated that contact times up to 30 minutes will achieve adequate organics removal. Additionally, short regeneration times are needed and are more effective since the resin is lightly loaded with organics.
For SIX, the hydraulic detention time is equal to the resin detention time. The resin for SIX is subject to the same biological/algal, iron, and sulfide/sulfate foulants as other IX technologies; however, the shorter BV reduces the risk of long-term fouling via bacteria growth and resin blinding. Reduced risk of fouling and the type of resin used for SIX (less susceptible to shearing and abrasion) results in far less resin loss and attrition, compared to MIEX. This also allows for consistently stable adsorption kinetics and consistent high removal of organics long term.
Along with organics, because of the frequent regeneration, the SIX process also reduces bicarbonate (alkalinity). A Tampa pilot study found a reduction of alkalinity varying from 35 to 65 percent, depending on the influent water quality. This could be troublesome for utilities with limited alkalinity in the raw water and could require the addition of alkalinity downstream to avoid adverse impacts on distribution system water quality.
On the other hand, the reduction in alkalinity provides for a more efficient downstream coagulation process as coagulant and pH adjustment chemical demand is reduced. Although organic fouling is reduced in this process, any fouling requires treatment using caustic. Unlike the MIEX resin, the type of resin used for SIX is not chlorine-tolerant. This could require additional infrastructure and chemical use if a utility does not already use caustic.
Because the process operates at lower BV, and resin detention time is the same as the process water hydraulic dentition time, a larger inventory of resin is needed in order to achieve the same organics removal performance, compared to other IX technologies. Theoretically, the SIX process requires more salt solution volume, but at a lower concentration to regenerate since the resin is lightly loaded. In some applications, this results in a lower salt use, compared to other IX technologies; however, the Tampa pilot study found that the required salt use was three times the salt use, compared to MIEX. This is because the utility desired a finished water TOC target of 2 mg/L, so a conservative salt quantity was used to ensure full regeneration. Actual salt use would be dependent on the source water quality and finished water quality goals of the utility. Further, because of the required contact times and plug flow configuration, the SIX process requires a larger footprint, compared to MIEX.
Fixed bed ion exchange is fundamentally different in its contact mechanism, compared to SIX and MIEX, and typically consists of pressure vessels, complete with an underdrain, gravel, and sand support system, and resin. The resin is fixed within the contact bed and is not fluidized during treatment, nor does it flow with the process water. A general process flow diagram is shown in Figure 4.
Water is fed at the top of the vessel and flows through the resin for treatment. Treated water exits the bottom of the vessel and is conveyed downstream to the next unit treatment process. Unlike MIEX and SIX, the underdrain contains the resin and requires no additional downstream treatment due to resin carryover. During regeneration, the process water is diverted, and the IX vessel is removed from service. The resin is regenerated in-place, after which the vessel is returned to service. The resin is often fluidized during regeneration, which helps ensure fullsurface-area contact with the salt brine and helps decompact the bed to minimize headloss when placed back into service.
There are many fixed bed IX installations located across the U. S. and internationally, and widely available by competitive manufacturers, with installations in significant excess of MIEX and SIX. Since fixed bed IX occurs in a vertical pressure vessel, the capacity and footprint of each vessel is limited by transport size. Open-top and horizontal vessels have been considered, but not widely implemented. The largest vertical pressure vessels available can process up to about 1.5 to 2 mgd each, with loading rates between 8 and
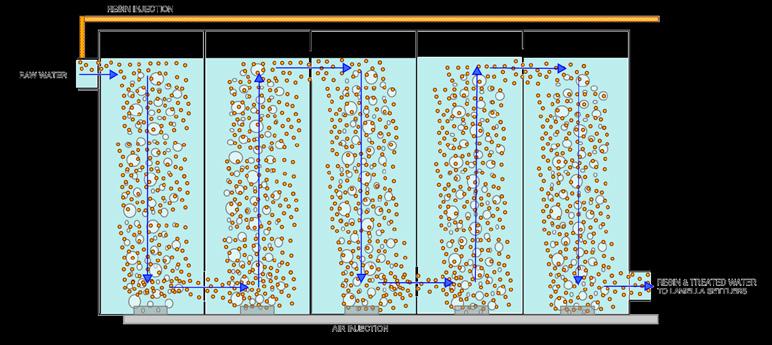
Figure 3: Cross Sectional Representation of the Suspended Ion Exchange Contact Process

Figure 4. Fixed Bed Ion Exchange General Process Flow Diagram
Continued from page 65 10 gpm/sq ft. Typically, these systems are used postfiltration as a polishing step for organics removal.
The fixed bed IX process requires any strong base anion exchange nonproprietary resin. Like MIEX, competing anions, such as sulfate, can cause reduction in TOC removal if the resin is not regenerated frequently. Because the IX system is often post-treatment, and bicarbonate is an anion, removal of alkalinity can be a significant consideration, and pilot studies have shown sulfate breakthroughs at 600 BV. Fixed bed IX systems typically operate between 1000 and 2000 BV, so it’s regenerated even less frequently than MIEX. Unlike SIX, the resin that is typically used can tolerate a small amount of chlorine if fouling is occurring.
In applications where water is exposed to chlorine and/or to the atmosphere before or within the IX process, oxidation/precipitation of iron and other species can occur and cause fouling of the IX resin. In addition, the presence of oxygen can promote biological growth on the IX resin and reactor (less so with SIX than compared to MIEX). The detrimental issues associated with oxygen are particularly of concern with anerobic groundwater, where the concentrations of highly soluble reduced metals (particularly iron) and aerobically biodegradable compounds are often high, and the associated scaling and biological fouling are also high.
Fixed bed ion exchange technology is another option for utilities with this type of source water. Due to the enclosed vessel, the fixed bed system does not expose the source water to oxygen, and as such, reduces the biological risk associated with changing the biological growth potential, offering substantial benefit for certain groundwater applications in Florida.
Fixed bed IX may not be a feasible option for larger installations since the vessels are limited to 2 mgd. For example, a 50-mgd facility would require 25 to 30 IX vessels, which can become costly, require a large footprint, and require additional maintenance due to the increase in mechanical equipment and components. It can also be aesthetically unpleasing in high population areas. Additionally, since the resin is regenerated in situ, it’s required to be placed out of service (when in regeneration mode), thus requiring more redundancy than MIEX and SIX. Since the fixed bed IX arrangement is similar to a filter, any particulates must be removed prior to the IX vessel, which may require an additional upstream treatment process.
Table 1 presents a comparison/summary of these three IX technologies. As shown, organics removal is similar to all of the options, but actual organics removal quantities will be site-specific. The fixed bed IX is the most limited in train size, making it impractical for large-scale installations, while the SIX process, ideally suited for larger installations, comes with the largest footprint. The MIEX only regenerates a small portion of the resin inventory at any given time, which results
Table 1. Ion Exchange Technology Comparison Table
Fixed Bed IX MIEX SIX Resin Type Nonproprietary Proprietary Nonproprietary
Strong Base, Type I, Anionic Exchange Resin Magnetic, Macroporous Resin Strong Base, Gelular, Anionic Exchange Resin Size Limitation per Train 1 - 2 mgd 10 mgd 10 mgd Footprint per Train Smallest Medium Largest Typical BV Treatment 1000 - 2000 200 – 1000 50 - 200 Regeneration Per Cycle 100%, based on WQ 1 – 10% 100% after single use Organics Removal 50 – 80% 50 – 70% 50 – 80% TOC Loading Medium High Light
Sulfate and Bicarbonate Competition
High Medium Low Iron Competition Low High (if oxidation of iron does not occur prior to MIEX system) Unknown
Chance for Long-Term Fouling
Medium High Low
Brine Concentration 10-12% 100% 2 – 6%
Brine Waste Production Volume
Moderate Moderate High
Demonstrated Performance
High Medium Low Capital ~$1.00 – 2.00 / gal ~$0.50 – 1.25 / gal ~$0.75 / gal
Operation and Maintenance
Lowest Highest (due to resin replacement) Moderate (due to salt use) Operator Interface Low High Unknown in its higher propensity for long-term fouling, compared to the other IX options. Capital costs for fixed bed IX are generally higher than MIEX and SIX, but lowest in O&M costs due to the lower salt use and less-frequent resin replacement. There is little available information on the O&M personnel requirements for SIX, and the demonstrated performance is limited to a few full-scale installations. Additionally, bicarbonate addition may be required with SIX, since the alkalinity is reduced due to the lightly loaded resin.
The MIEX has the most resin attrition and loss, and is a proprietary product, thus resulting in the highest O&M cost. Overall, MIEX and SIX are viable options in surface water applications as a pretreatment step, where fixed bed IX, depending on the plant capacity, can be better suited as a polishing step. Fixed bed IX is most beneficial in smaller-scale groundwater application, whereas a SIX and MIEX implementation should consider prior oxidation of iron and minimization of sulfide-reducing bacteria. The SIX and MIEX are more viable in larger-scale installations (more than 30 mgd), while fixed bed IX is more appropriate for smaller water treatment plants. Fixed bed IX may be preferred for utilities that have minimal staff, while SIX and MIEX require more operational oversight. As such, the choice of the most appropriate IX technologies is not one size fits all; the pros and cons of all of them must be weighed, which may vary among different utilities.
Conclusion
The primary differences and similarities among the three IX technologies are presented, and Florida utilities should consider these differences when selecting an anion exchange process for the removal of color and natural organic matter at their water treatment facilities. Any option could be extremely beneficial for existing utilities employing coagulation and wanting to reduce chemical demand and solids loading, looking for an organics removal system polishing step, or looking for a sidestream organics removal option.
Utilities should compare the technologies for their process footprint requirements, organics removal, resin acquisition, resin characteristics, O&M requirements, brine quality and quantity, fouling potential, capital and operating costs, and demonstrated performance (and risks) in the waterworks industry. The selection of the most appropriate IX will vary according to a utility’s needs, plant capacity, raw water quality, available budget, and more; however, common to all considerations should be bench- or pilot-scale testing, prior to full-scale implementation of the selected option. S