
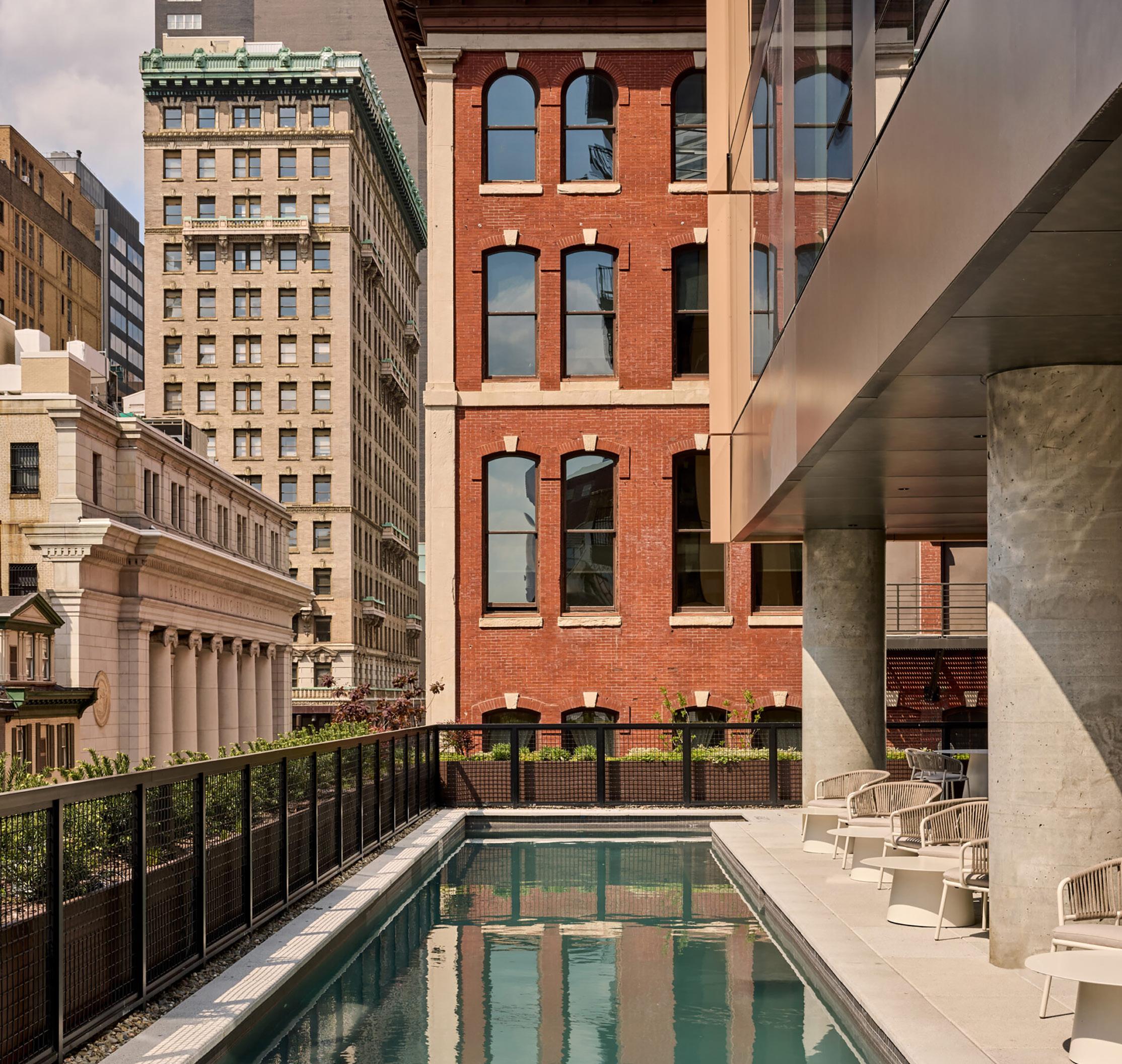
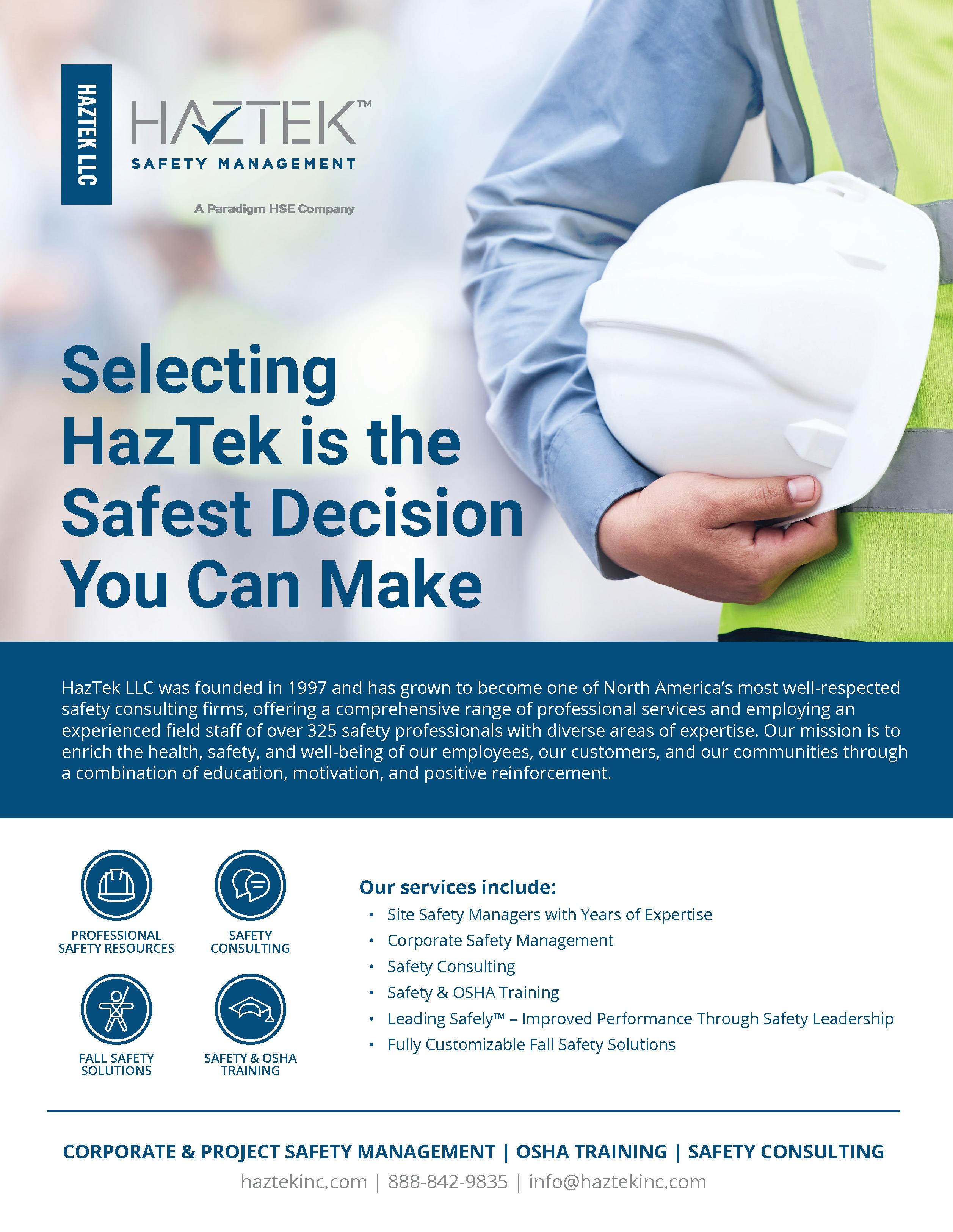
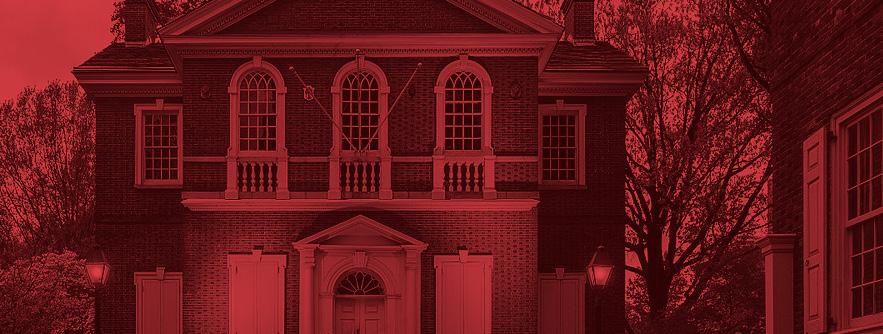
Life in the construction industry is fast-paced, ultra-competitive, and always changing. We’re constantly looking toward what’s next and how we can take everything we touch to the next level. Accomplishing things that have never been done before, bringing forward-thinking spaces to life, and driving progress that makes a real difference in people’s lives are big parts of what makes the industry so exciting. While we move full speed ahead, we owe it to ourselves to pause for a moment and celebrate.
As we recognize the incredible winners of GBCA’s 2024 Construction Excellence Awards in this issue of Construction Today, it’s a perfect time to stop and appreciate the excellence that’s all around us. This year’s honorees represent more than just remarkable projects. They embody the essence of what it means to build with purpose, precision, and passion. Moreover, they showcase the excellence in action that’s prevalent among all GBCA members throughout every stage and facet of construction. Continuing to elevate the exceptionally high standards we all uphold is no easy feat, but your hard work is paving the way for an even stronger industry and a more vibrant Philadelphia.
We also have several significant accomplishments to acknowledge two years into our association’s three-year strategic plan. When we designed this plan, we set our sights on ambitious goals across four strategic pillars to help ensure GBCA maximizes its impact where it matters most. With many wins already under our belt, we’re well on our way to successfully delivering on this plan.
Heading into the third and final year of executing this strategic plan, GBCA is well positioned to be exactly where we need to be to best serve you, our members, and the industry at large.
It has been an immense privilege to serve as Chairman of your GBCA Board of Directors for the past two years. Like you, I’m eagerly looking to the future and the great things we will continue to achieve under the bold leadership of our incoming Board Chair, Maura Hesdon.
Your support of our wonderful association is truly what makes all of this progress possible. Let’s keep it up!
Craig Melograno Chairman of the Board, GBCA President,
PDM Constructors, Inc.
"The future is already here—it's just not very evenly distributed." —
William Gibson
This quote resonates now more than ever in our industry. Artificial Intelligence (AI) is no longer a distant concept; it's a present reality transforming how contractors build and manage projects. Today, some contractors are integrating AI into their daily operations, leveraging its capabilities to enhance efficiency, safety, and productivity. Meanwhile, others view this technology as irrelevant or something to consider in the far-off future.
At the General Building Contractors Association (GBCA), we're investing in AI today so that we may be ready to help narrow the gap between contractors embracing this technology and those yet to explore its potential. Contractors are currently using AI for various applications such as predictive analytics to forecast project timelines, AI-powered project management software to optimize workflows, and safety monitoring systems that use computer vision to detect hazards in real-time.
A compelling study from Boston Consulting Group, Harvard Business School and Wharton demonstrated the significant impact of AI on productivity. Consultants with access to AI tools completed 12% more tasks and did so 25% faster than their counterparts without AI. Moreover, the quality of their work was rated 40% higher by their supervisors. This underscores that early adoption of AI can provide a substantial competitive edge, one that may be hard to make up later.
Your GBCA is in the early stages of its AI journey. Since the public release of ChatGPT in November 2022, members of the GBCA team have been experimenting with AI technologies. Now, we're preparing to be one of the first Associated General Contractors (AGC) chapters in the country to participate in an AI training pilot program.
We believe that by embracing this technology, we'll not only enhance our services but also empower our members to leverage AI effectively in their businesses.
AI does not come without risks. Concerns such as data privacy, cybersecurity threats, and the potential for algorithmic bias are valid and must be addressed. However, we believe that by following some simple guidelines laid out in the works of Wharton professor Ethan Mollick, many of these risks can be mitigated.
• Start with an open and curious mind: Be willing to explore and learn about AI technologies.
• Use AI as a tool, not a replacement: Leverage AI to augment human capabilities, not replace them.
• Ensure data security and privacy: Implement robust security measures to protect sensitive information.
• Promote transparency and ethics: Be clear about how AI is used and ensure it aligns with ethical standards.
• Invest in training and development: Equip your team with the necessary skills to work alongside AI technologies.
Our role as your association is to help ensure that the future is more evenly distributed among all our members. We are committed to providing the resources, support, and guidance you need to navigate this technological evolution.
And yes, I must confess, AI was a partner on this letter.
Together, let's lay the foundation for an AI-powered future in construction.
Benjamin J. Connors, Esq., CAE President & CEO General Building Contractors Association
PUBLISHER/EDITOR
Nicole Catrambone
ADVERTISING/SALES Nicole Catrambone
CONTRIBUTING WRITERS Nathan Dennis / Jeremy Grey / Erik Highland / Ben Hofferman / Nick Jann/ Robert Landy / Jessica Matase Slattery/ Jim McGugan/ Jeff Shoaf/ Robert Smith / Karl Sorensen
DESIGN Punch Garage
ACCOUNTING Kristin DeFrancisco
EDITORIAL OFFICE
General Building Contractors Association, Inc. 36 South 18th Street Philadelphia, PA 19103
P: 215-568-7015 F: 215-568-3115
© Copyright CONSTRUCTION TODAY® registered in U.S. Patent and Trademark Office Copyright ©2004 by the General Building Contractors Association. All rights reserved. Submissions for editorial review should be sent to the editorial office address. Neither the publisher nor any individual associated with any branch of production, nor the advertisers will be liable for misprints or misinformation contained herein.
NATHAN DENNIS
President
Target Building Construction, Inc.
GREY
Executive Vice President of Industrial Development HRP Group
JESSICA MATASE SLATTERY
Director of Marketing
LF Driscoll
JIM MCGUGAN
GBCA Safety Consultant
Med-Tex Services, Inc.
ERIK HIGHLAND
Marketing Director
Superior Scaffold Services, Inc.
JEFF SHOAF CEO
Associated General Contractors of America
Training Director
Eastern Atlantic States Carpenters
Technical Centers
ROBERT SMITH
Training Director
Eastern Atlantic States Carpenters
Technical Centers
KARL
2024 CONSTRUCTION TECHNOLOGY EXPO
FALL PAC RECEPTION
EGGS WITH OSHA – L&I UPDATES
CLC VISITS MAYFAIR MIDDLE SCHOOL’S CTE PROGRAM
CLC LEADERSHIP SERIESTALENT WALK
AIA / GBCA EVENT- TECH INNOVATIONS CHANGING THE CONSTRUCTION INDUSTRY
BY JEFF SHOAF CEO | ASSOCIATED GENERAL CONTRACTORS OF AMERICA
One of the great things about this association is how much AGC and its chapters are like a family. This organization is where you meet up with your brothers, sisters, and cousins in the industry. It’s where you talk about your job and about making a difference in the world and in your family. This is why so many of you have given so much of yourselves to make the industry attractive to the next generation.
I have spent much of the past three decades helping support this family, first in running AGC’s government affairs operation and more recently serving as chief operating officer. Earlier this year, I had the honor to take over the role of administering this family when I became AGC’s chief executive officer. Serving as the new CEO is a challenge that I am eager to accept and anxious to fulfill.
It has been a real honor to work with our former CEO, Steve Sandherr, for nearly 30 years. For every one of those years, he operated as a leader who inspired the staff to deliver for the members. His leadership created a great team at AGC. That team is hard working, passionate and innovative.
One reason for that passion is the opportunity to represent an industry that positively impacts every person’s quality of life. The accomplishments inspire us to tackle the many challenges we face, including workforce shortages, environmental rules, regulatory burdens, and the actions (or more likely the inaction) of Congress.
My goals as your new CEO are to navigate the transition and achieve the goals contained in the AGC Board of Directors business plan. Those goals include continuing to successfully advocate for the needs of the industry, address the industry’s ongoing workforce shortages, find new ways to support member and chapter engagement, and improve the range of products, programs and services that we offer.
My first big decision was choosing the person to take my former spot. I selected Jimmy Christianson, the current head of AGC’s Government Relations Department as the next AGC Chief Operating Officer. His commitment to the organization, the members and the staff, will help keep the organization on track.
AGC is an exceptional organization with a great history and greater potential. Moving forward, we are going to continue advocating for you. We will continue our efforts to help develop the industry’s workforce. We will keep providing world-class education programs. And we will keep finding ways to make it easier for you to engage with your national
association and play an active role in helping build an even better industry.
To accomplish that, we are going to listen to members, work closely with chapters like the General Building Contractors Association of Philadelphia, and enhance our network of influence in Washington and across the country. You, the members, are constantly looking for ways to improve your businesses and deliver even better projects. Likewise, we are eager to keep finding ways to better serve the members and represent this industry.
That is one reason I have devoted quite a bit of time during my first few months as CEO to traveling the country, visiting many of our outstanding chapters and talking to members. Even though I have been with AGC a long time, it is still inspiring to learn about all that our chapters are doing. And I am always overwhelmed by the passion the members have for their work and this association.
I truly believe that the more we listen, coordinate, and broaden our influence, the better we will be able to anticipate the next big industry threats and the next great industry needs, and continue to have your back by figuring out how to turn the challenges of today into the opportunities of tomorrow.
As much as I want to, I haven’t yet been able to visit every chapter or talk to as many members as I would like. That is why I invite you to reach out with your thoughts and suggestions. If there is something we are doing you don’t understand, just ask. And if there are things we are doing you love, please let us know as well.
My goal is to make sure AGC continues to have a positive impact on the people like you who power the construction industry, and for the AGC family to remain strong, healthy and successful.
QA
Name: Branden Murphy
Title: Estimator and Project Manager
Age: 27
Company, City: Old Philadelphia Associates, Inc., West Chester, PA
Years in Field: 6
Education: Temple University
What inspired you to pursue a career in construction?
My family, particularly my parents and uncles, had a significant influence on my decision to pursue a career in construction. They have had successful careers in the industry, and I was always interested to hear them talk about the business. During high school, I worked as a laborer to gain firsthand experience. That is when I realized that I was drawn to the tangible results of construction work.
How has the construction industry changed since you started your career, and how have you adapted?
The pandemic was a time of uncertainty and dramatic changes. There were supply chain issues, project delays, new safety guidelines, and workforce challenges. We had to adapt in order to keep working throughout the pandemic. This meant providing new PPE and following the latest government regulations. Procuring material was difficult due to the supply chain issues, so we substituted materials with long lead times for materials that were readily available and ordered excess amounts of the materials that we use regularly.
What has been the most fulfilling moment of your career so far?
The most fulfilling moment of my career so far has been working on a Housing Authority apartment building for the elderly in Allentown. We were deck coating all the balconies and replacing joint sealant. The residents were all very nice and they appreciated the work that we were doing to fix their leaks and restore their balconies. We have since been back to the apartments for maintenance, and the residents still remember us and thank us for the work that we did.
What unique challenge do you face in your role, and how do you overcome it?
As an estimator and project manager, I wear a few different hats, and I find myself spread too thin at times. Sometimes I get overwhelmed when I look at my to-do list, but then I focus on starting small and checking off one thing at a time.
What advice would you give to someone just starting out in the construction industry?
I recommend to anyone starting out in the construction industry to take classes and learn as much as you can from more experienced colleagues and mentors. The GBCA offers a lot of continuing education classes both online and in person.
What leadership principles guide you in your professional life?
I was fortunate that my mentor had an open-door policy with me which allowed me to ask him questions. We also rode together for on-site visits and meetings where I could also pick his brain any time. Now that I am leading others, I use the same principles of being available at any time and always making others feel welcome to ask me questions.
How has being part of the CLC contributed to your personal and professional growth?
At the first CLC event that I went to, I felt like I barely knew anyone, and I was forced to get out of my comfort zone and meet new people. That was over two years ago. Since then, I feel like my networking skills have improved tremendously and I have made genuine connections and friendships with future leaders in the industry.
What’s a recent accomplishment or skill you’ve developed that you’re proud of?
I feel much more confident in myself, and my knowledge of the industry compared to when I first started. I’m proud to be a source of knowledge of my trade when I communicate with customers, engineers, and other contractors. I no longer second guess myself like I did early in my career.
How do you stay motivated and inspire those around you?
I try to lead by example with a strong work ethic and positive attitude. Collaborating with a colleague to achieve a common goal is also a great way to stay motivated because there are others relying on you.
What qualities do you think are most important for the next generation of construction leaders?
I believe that the most important qualities for the next generation of construction leaders are effective communication, networking skills, problem-solving abilities, and adaptability to change.
What’s your favorite CLC event or initiative, and why?
My favorite CLC event is the Phillies Outing event. I’ve been a huge Phillies fan my entire life, so I always enjoy going to a ball game. This past year was especially great because the CLC provided tickets to the game. We all sat together in the same section allowing members to casually network with each other while enjoying the game.
How has participating in CLC activities impacted your career?
As I mentioned earlier, the friendships and connections that I have made from CLC have been invaluable. GBCA is such a vast network from general contractors, specialty contractors, engineers, insurance, surety, and suppliers. The CLC members are the future leaders in the industry, so establishing these relationships now is incredibly important.
What makes GBCA membership valuable to you?
GBCA membership is so valuable to me because of the many resources that are offered such as continuing education and safety classes. Networking in the GBCA is extremely valuable as you are able to connect with the largest and most reputable companies in the area. GBCA also represents the Philadelphia area construction industry in Harrisburg and Washington D.C. to advocate for policies and legislation that encourage union construction in the area.
BY NICK JANN, SENIOR MANAGER OF INDUSTRY RESEARCH | GBCA
Downtown Philadelphia retail has long relied on its daily population of commuters for business activity. The region’s commercial real estate market has experienced significant shifts in recent years, particularly due to the pandemic's longterm impact on work habits and urban activity. As hybrid and remote work models grew increasingly normalized, the city's retail landscape evolved, driven by changing consumer patterns and demographic shifts. These transformations are especially clear in Center City, where the demand for retail space is now largely resident-driven rather than dependent on daily workers.
Prior to the pandemic, Center City Philadelphia's retail market relied on commuting office workers and support staff. With firms increasingly adopting hybrid work models, the flow of these consumers has declined. Despite some employers, including the City of Philadelphia, mandating a full return to offices, many businesses still struggle with high vacancy rates. This decline in office-based consumer activity has significantly reduced the size of the city's retail trade area, shrinking from 2,500 square miles in 2019 to just 970 square miles in 2024.
Residents have now become the primary source of demand for retail in Center City. Data from 2024 shows that the percentage of pedestrians living within one mile of the city's prime retail corridors (Walnut and Chestnut Streets) has increased by 76% since 2019. This shift has reshaped the city's retail activity, with weekends—particularly Sundays— emerging as one of the busiest shopping days, driven by local residents rather than office workers. This change is also reflected in the types of retail establishments that are thriving, with experiential and lifestyle brands becoming increasingly popular in Center City. In addition to those already existing, a Formula One simulator and Five Iron golf simulator are coming online in downtown Philadelphia in 2024 as well.
The growth of Philadelphia’s residential population, especially in Center City, has played a key role in sustaining retail demand. Since 2010, Center City's population has grown by 27.8%, supported by a significant number of office-toresidential conversions. This trend has created a unique urban environment where mixed-use developments blend office, multifamily, and retail spaces. These developments resemble
the mixed-use projects in places like South Philadelphia and Fishtown. Recent luxury residential projects, such as The Josephine on Sansom Street and One Thousand One on Broad Street, have further intensified the residential presence in the city’s core. This multifamily growth has not only increased foot traffic but also reshaped retail offerings to meet the needs of a resident-driven market.
In Greater Philadelphia, the retail leasing market showed positive signs in the third quarter of 2024, marking the first time this year that the market saw positive net absorption. Grocery, discount, and experiential retailers have driven much of this demand. With limited availability of quality retail space, bankruptcies and closures of large retailers like Big Lots and LL Flooring have created opportunities for smaller, expanding businesses to enter the market.
Experiential retail is seeing considerable growth, with brands like Ace Pickleball and Five Iron Golf expanding their footprints. Additionally, discount retailers such as Ocean State Job Lot and Ross Dress-For-Less have opened new locations in the region, responding to a consumer base that has become more price-sensitive due to economic uncertainty.
Philadelphia’s commercial real estate market is undergoing a transformation, driven by the city’s growing residential
base, evolving consumer habits, and post-COVID-19 work adaptation. As office workers play a diminished role in retail demand, residents and experiential offerings are becoming the backbone of the market. This shift suggests that future retail spaces will need to cater more to residents, with a focus on experiential and community-centric developments.
For the construction industry, this trend implies an increasing demand for mixed-use developments that blend residential, retail, and recreational spaces. Developers will likely continue to decide the most cost-effective ways to repurpose older office buildings into multifamily units, a process that requires significant renovations and retrofitting. Additionally, the construction of new luxury multifamily buildings, particularly in Center City and surrounding areas, will continue to rise, driving demand for both residential and commercial construction projects. The growth of experiential retail also presents opportunities for specialized construction projects tailored to entertainment and lifestyle venues, further expanding the role of the construction sector in Philadelphia's evolving real estate landscape. In this changing environment, construction firms with expertise in adaptive reuse and mixed-use projects will be particularly well-positioned to capitalize on these new market demands.
BY JESSICA MATASE SLATTERY, DIRECTOR OF MARKETING | LF DRISCOLL
If there’s one thing Philadelphia does well (besides cheesesteaks), it’s museums. Modeled after the ChampsÉlysées, the city’s Benjamin Franklin Parkway boasts what is also referred to as “Museum Mile” thanks to the many cultural institutions located along the way. Philadelphia’s own LF Driscoll has led the construction of many of them, including the Barnes Foundation, Rodin Museum, Free Library, and the long-time master plan and Core Project expansions at the famed Philadelphia Museum of Art.
The team is now adding another cultural institution to this impressive list: Calder Gardens. Expected to open in 2025, Calder Gardens will serve as an 18,000sqft exhibition space for a variety of modernist sculptures created by famed artist—and native Philadelphian—Alexander Calder.
Designed by Herzog & de Meuron with Ballinger as architect of record, the planned building appears modest in size on the surface. However, as visitors enter at ground level, they will have the opportunity to descend two more levels that include galleries with a variety of art experiences. From a curved gallery that runs along the exposed concrete ceilings to a sunken gallery and smaller rooms at the lower level. “This building is like nothing else. Everything is custom,” says Jack Garrett, LF Driscoll’s senior superintendent. “We’ve assembled an expert team to make this kind of artistic vision a reality.”
The Calder Gardens building is designed to be built almost completely of exposed concrete—with walls up to 7 feet thick. That means all building systems, walls, windows, built-in benches, art displays, and other features had to be fully coordinated and meticulously planned before the concrete is poured. LF Driscoll is known for its ability to take on complex building challenges. For this project, the team leveraged virtual construction techniques and a close working relationship with the design team and subcontractors to align the many moving parts into one rock-solid plan.
“The collaboration level is very high. We’re working with our subs in almost a design-assist fashion to make this vision a reality,” says Garrett. “Everything we’re doing has required
detailed discussions and coordination before we begin because once the concrete is poured, it’s done.”
The structural concrete was only one of the many complexities of the project. The design is intended to keep a low profile to let the artwork shine, so every detail involves a unique approach.
Finishes and formwork. Between the different types of concrete and the wood finishes here and there, accomplishing how the different finishes meet up and work with the structural concrete was no easy task. “The windows have concealed sills and frames; they are recessed behind the concrete and finished walls,” says Garrett. “That is certainly unique, so we had to work with the design team to identify the exact thickness and specs for each one.”
And because the walls and ceiling of one of the primary staircases is being built from shotcrete-applied concrete, the design team was concerned about handrails having a rough finish. So, LF Driscoll brainstormed with the team to determine what could be applied there without detracting from the aesthetic. Just outside of the main galleries is the Vestige Garden where the textured finish of the exposed concrete walls was achieved by stripping the formwork several hours after placing the concrete so that it could be “scratched” with the claw of a hammer. This created a natural, geological appearance reminiscent of a rock formation.
“If you ask me, I would say with all of the custom finishes on this project, the scratched concrete would be the most unique. That was definitely a first for all of us,” says LF Driscoll’s senior project manager Andrew Klinger.
The project also includes other unique finishes such as wood siding, venetian plaster ceilings, polished concrete floors and walls, and a very custom stainless steel metal panel façade. A mockup was built prior to building construction in which several different wood species and stainless-steel metal panels were erected. The main lobby level and portions of the galleries will be clad with wood siding to complement the
board-formed cast-in-place concrete walls in the galleries. The main façade and entry canopy facing the Parkway is a custom #7 stainless-steel finish with a dulled reflection.
“The team went to great lengths to develop QA/QC guidelines for evaluating the custom stainless-steel panel finish due to the custom nature and specific aesthetic requirements of the design team,” says Klinger.
Gardens. As the name of the project would suggest, the gardens and landscaping are a main focal point of the design even beyond the artwork. The landscape was designed by world renowned landscape architect Piet Odoulf. The team has worked closely with the landscape architect and local nurseries to source the selected plantings. The dulled reflection of the custom stainless-steel façade provides a soft backdrop for the expansive gardens and almost makes the building disappear behind them.
Specialty lighting. The role of light on and around art is, of course, critical. The building’s design very intentionally balances natural light with subtle lighting fixtures to control the light specifically. But as with all MEP and security system infrastructure, the lighting design had to be worked into the structural concrete. Again, the team relied on the problemsolving powers of BIM to help fish the lighting conduit and boxes into the complex, rebar-laden walls, and elevated slabs to meet the exact specifications needed.
Protecting surfaces. Because all structural concrete for the project had to be poured early but is also the finished product, the team had to find ways to protect it as the rest of construction continued. This protection plan included wetcuring the floors, which the team tested first with a mock-up. “We used a curing compound on half of the mock-up floor and wet-cured the other half with a lawn sprinkler,” Klinger says. “The team preferred the wet so that process had to be carefully staged to allow for seven full days of wet curing in each area.”
Needless to say, this one-of-a-kind artistic sanctuary will be an art piece of its own once completed. And the LF Driscoll team is excited to be part of the process.
“Complexity is what we do best,” says Garrett. “We are here to figure out how to build this completely unique structure and help the City of Philadelphia add yet another world-class cultural center to its already impressive roster. We’re excited for the challenge. It’s what we do.”
BY KARL SORENSEN, DIRECTOR OF CONSTRUCTION TECHNOLOGY + INNOVATION | DAVIS CONSTRUCTION
With each passing year, the ever-growing gulf between labor demands and labor availability in construction continues to expand. In a recent survey conducted by Associated General Contractors of America and Arcoro, 94 percent of construction firms reported having a hard time filling open positions. With the median age of construction managers nearing retirement at 45.2 and industry growth estimated to reach a staggering $16.1T globally by 2030, labor shortage woes are seemingly here to stay.
Although we may understand the extent of the problem, the fix is a little more complicated. The best explanation of this disparity is twofold; construction’s unshakeable stigmas and the industry’s inability to engage the next generation of working professionals.
The stigmas surrounding construction are as damaging as they are ubiquitous. Any trip past an active jobsite or quick Google search will conjure up images of construction being little more than a dirty, time-consuming, sweat-inducing, old-school and dangerous profession. Whether it is high-rise or highway construction, residential or commercial markets, plumbers or electricians, all paths seem to be fraught with callous-handed difficulty. And if this is the perception, then it’s no wonder that younger professionals are looking elsewhere for gainful employment. Given the option between working with steel or working with code, working from the jobsite or working from home, or making a living or making money, the latter just seems more appealing.
What’s not immediately obvious, however, is that traditional industries and emerging industries aren’t mutually exclusive. In fact, when compared to tech-driven industries, construction offers on par or better opportunities, more disruptive innovation and a brighter professional outlook. These possibilities make construction a great first-choice career decision for recent graduates, instead of the traditionally perceived “back-up plan” when all else fails.
Wherever people live, there will be construction jobs available. As populations change, new leaders are elected and economic needs evolve, there will always be demand for construction. As humans migrate from state-to-state or country-to-country (and in the future, possibly planetto-planet), there will be a need for new or revitalized infrastructure. This reality was put on full display during the COVID-19 outbreak when droves of people vacated urban centers for rural economies — creating a flurry of new construction, revitalization initiatives and renovation/ repurposing projects in small- and mid-market towns. Not only that, but as contemporary life evolves, construction follows suit. Moreso today than ever before, there has arisen an increased dependence on sustainable living practices, teleworking and digital commerce, causing an unprecedented growth in construction for data centers, EV manufacturers, battery plants and microchip factories.
As always, the industry needs skilled workers to thoughtfully design and physically build these emerging spaces, but less discussed is the need for professionals that specialize in operations, finance, accounting, marketing and business development. Undiscussed, and maybe unknown to the wider world, is that there is a large and growing need in construction for technologists, hardware and software developers, researchers and innovators, virtual construction managers, data scientists, robot operators, 3D printers and drone pilots. The diversity, complexity and innovation of today’s construction projects are matched only by the diverse, complex and innovative characteristics of today’s construction jobs.
The success of the industry relies upon the success of today’s students and young professionals. It is imperative for the next generation look at the construction industry as a place to build; not just skyscrapers and roads, but new methodologies, new automations, new programs, new robots and new futures. This is where construction is headed, but it needs the expertise and guidance of those who can evaluate an impossibly difficult puzzle and propose complex, outside-thebox and innovative solutions.
Engaging with the construction professionals of tomorrow
DAVIS Construction has recognized that solving tomorrow’s construction challenges means first engaging with today’s most creative, most unencumbered thinkers. Being geographically near multiple prestigious universities, DAVIS has been able to provide an environment for homegrown student innovators looking to uncover unprecedented efficiencies in construction. Through our collaboration with George Mason University’s newly-minted Mason Autonomy & Robotics Center (MARC) or operating under the National Science Foundation’s (NSF) Industry-University Cooperative Research Center Programs with Virginia Tech’s Myers-Lawson School of Construction, DAVIS has found new solutions for aging construction challenges. Peggy Jones, a retired principal at DAVIS, says the collaboration at the MARC is critical. “The MARC connects academics, research, and experimentation between students, professors and local businesses.”
Ruichuan Zhang, Ph.D., is an assistant professor at the MyersLawson School and agrees on the critical need for connection with college students. "University academia plays a crucial role in addressing the construction industry's labor shortage by equipping students with the engineering and management skills necessary for modern construction practices,” he says.
It is our hope that through academic partnerships, not only can we find new solutions for inefficiency and waste, but more importantly, engage with the younger generation, demonstrating that construction is an exciting, innovative and viable industry worthy of exploration.
DAVIS’ nationally ranked internship program immerses students in the construction industry and prepares them for the professional world. Visit the DAVIS website to learn more.
Founded in 1966, DAVIS Construction serves the Washington and Philadelphia regions, building one billion dollars’ worth of construction a year. DAVIS has been recognized for 18 consecutive years as one of the area’s Best Places to Work by the Washington Business Journal.
The Eastern Atlantic States Carpenters Technical Centers (EASCTC),
Headquartered in Northeast Philadelphia and led by Executive Training Director Robert Smith and Training Director Robert Landy, the Eastern Atlantic States Carpenters Technical Centers (EASCTC) provide top-tier training to members and contractors associated with the United Brotherhood of Carpenters. Committed to providing students with stateof-the art training aligned with the latest trends in the construction industry.
This program has led the way for the past 75 years, always pushing the standard in the industry. EASCTC expects students to pursue excellence in the same manner as those who came before them, as the program was created to provide the tools one would need to reach their full potential.
At the Eastern Atlantic States Carpenters Technical Centers (EASCTC), we are proud to announce the graduation of our most resilient class to date, with an impressive 184 graduates from the apprenticeship programs at the Pennsylvania & Delaware campuses. These individuals began their journey at the onset of the COVID-19 pandemic, facing unprecedented challenges as they navigated uncharted waters in pursuit of becoming a Journeyperson.
The determination and perseverance demonstrated by this cohort is truly inspiring. Despite the disruptions and uncertainties brought on by the pandemic, these graduates remained committed to their training, adapting to new learning environments and safety protocols while honing their skills. Their ability to thrive in such difficult circumstances speaks volumes about their character and dedication to the craft.
Graduating during a time of global upheaval, these apprentices have emerged not only as skilled craftsmen but also as exemplars of resilience and adaptability. They have shown that with hard work and determination, it is possible to overcome obstacles and achieve one’s goals, even in the most challenging of times.
As we celebrate this milestone, we commend our graduates for their unwavering spirit and congratulate them on their achievements. The EASCTC is excited to support them as they embark on their professional journeys, armed with the skills and experience necessary to excel in the carpentry field. Together, we continue to build a brighter future for the next generation of skilled tradespeople.
We are thrilled to announce the remarkable success of the Carpenters Apprentice Readiness Program (CARP) 2024 cohort, the EASCTC flagship pre-apprenticeship program. This year, the program, conducted every Saturday for 10 weeks at our Philadelphia campus, has exceeded expectations, showcasing the dedication and hard work of both participants, instructors, partners & stakeholders.
Out of 32 eager participants, an impressive 23 have already secured placements or received promising job offers, highlighting the program's effectiveness in preparing individuals for a successful career in the trade. This achievement reflects the high-quality training and handson experience provided by our skilled instructors who are committed to ensuring that every participant is well-equipped for the workforce.
The CARP program focuses on essential skills such as safety practices, tool usage, and fundamental carpentry techniques, which are crucial for success in the field. Participants engage in interactive learning experiences, fostering teamwork and building confidence as they develop their craft.
As we celebrate this cohort's accomplishments, we extend our heartfelt gratitude to all involved, including our dedicated instructors, industry partners, and, most importantly, the participants themselves. Their determination and resilience have paved the way for a promising future in the construction industry.
We look forward to continuing this momentum and welcoming new cohorts in the future, ensuring that we remain a vital resource for aspiring craftsmen in our community. Together, we are building a stronger foundation for the next generation of skilled tradespeople.
We are excited to share that the Eastern Atlantic States Carpenters Technical Centers (EASCTC) has recently achieved accreditation across all seven of its campuses for its eight apprenticeship programs of study. This significant milestone, accredited by the Council on Occupational Education, underscores our commitment to providing topquality education and training in the carpentry field.
The accreditation has resulted in an impressive 42-65% increase in credit awards with our partner universities, which is a testament to the rigor and relevance of our programs. This enhancement opens new doors for our members, allowing them to earn valuable academic credits that can be applied toward further education.
EASCTC has secured articulation agreements with reputable institutions, including Rowan University, Thomas Edison University, and College Unbound. These partnerships mean that our members can expect to receive associatelevel credits or more upon the successful completion of their apprenticeship programs. This opportunity not only recognizes the hard work and dedication of our apprentices but also facilitates their transition into higher education pathways.
As we celebrate these achievements, we are proud to empower our members with the skills and credentials needed to thrive in today’s competitive job market. The EASCTC remains committed to enhancing educational opportunities and ensuring that our apprentices are well-prepared for successful careers in carpentry and beyond. Together, we are shaping the future of the skilled trades!
In an exciting collaboration, the Eastern Atlantic States Carpenters Technical Centers (EASCTC), Plenary Infrastructure Philadelphia LLC (“PIP”) and the Philadelphia Learning Collaborative will launch the CARP 3-1-1 Credential, a groundbreaking initiative aimed at transforming education and enhancing the status of skilled trades careers. This program recognizes and nurtures students who show a keen interest and aptitude in trades, providing them with real-world opportunities supported by engaging classroom instruction.
The CARP 3-1-1 Credential is inspired by the principles of Big Picture Learning, which emphasizes personalized, interestdriven education. By facilitating interest-driven internships, students gain hands-on experience under the mentorship of skilled professionals, fostering deep learning and skill development. The program is designed for all students, ensuring inclusivity and accessibility.
Participants in the CARP 3-1-1 program will spend three days a week working with women- or minority-owned contractors. They will spend one day on certification training, and one day volunteering on community projects. This structure not only results in practical skills but also builds vital connections between students and industry professionals.
Launching in Spring 2025, the program aims to recruit 10-15 rising high school seniors from West Philadelphia, offering them a clear pathway into pre-apprenticeships or apprenticeships in carpentry. By prioritizing diversity and inclusion, the CARP 3-1-1 initiative addresses the pressing need for skilled tradespeople in our communities.
Together, we are committed to empowering the next generation of skilled tradespeople, ensuring that they have the tools and support needed to succeed and thrive in their chosen careers.
BY JIM MCGUGAN, GBCA SAFETY CONSULTANT | MED-TEX SERVICES, INC.
In recent years, the construction industry has seen a significant shift in head protection with the introduction of a new style of safety helmet. While traditional hard hats have long been the standard, the newer helmet designs are garnering attention for their enhanced ability to protect workers from a wider range of hazards. This shift is driven by a deeper understanding of the diverse risks faced on job sites, beyond just falling objects.
The primary distinction between the old hard hats and the new helmets is in the scope of protection they offer. Traditional hard hats were designed with a focus on safeguarding workers from overhead hazards, such as falling tools or materials. In contrast, modern safety helmets are designed to address additional risks, particularly those associated with falls and "struck by" incidents. These helmets not only meet the ANSI Z89 standards required for head protection in the U.S., but many also comply with the European EN 397 standards, providing a higher level of safety assurance.
It is important to understand the two types of head protection commonly available: Type I and Type II. Type I head protection offers top-impact protection, designed primarily to shield the head from objects falling directly from above. On the other hand, Type II protection is more comprehensive, defending against both top and side impacts. Some of the newer helmet designs take this protection further, offering multi-directional impact resistance, making them more effective in dynamic environments like construction sites.
One of the key features of these modern helmets is the inclusion of a chin strap. This ensures that the helmet stays securely in place during falls, slips, trips, or when workers accidentally bump into stationary objects, such as when
crouching under beams or climbing ladders. This is a critical improvement, as traditional hard hats can often dislodge during such incidents, reducing their protective effectiveness.
The introduction of safety helmets in construction is aimed at reducing the number of fatalities caused by head injuries. A study conducted by the National Institute for Occupational Safety and Health (NIOSH) over an eight-year period found that more than half of all fatal falls in the workplace were attributed to head trauma. Between 2003 and 2010, there were 2,200 documented worker deaths due to traumatic brain injuries. In many of these cases, the hard hat came off during the fall, leaving the head unprotected upon impact. Helmets, with their secure chin straps, are designed to stay in place, potentially reducing these tragic incidents.
Another factor to consider is the nature of tasks workers perform on-site. For those frequently bending over, such as electricians or pipefitters, traditional hard hats may frequently fall off, leading workers to remove or improperly wear their head protection. This can be avoided with helmets that remain secure, making it easier for workers to stay protected.
Interestingly, younger workers seem more inclined to embrace these new safety helmets. Many in this generation are accustomed to wearing similar helmets in their personal lives—whether for biking, skiing, horseback riding, or other recreational activities. This familiarity makes the transition to helmet use on the job site more seamless and contributes to a culture of safety among younger employees.
When choosing a helmet for your workforce, it’s essential to assess the specific hazards your employees face during their tasks. Manufacturers provide detailed recommendations on how their helmets should be used, including guidelines on
care, warranty, type of protection, and electrical classification. Additionally, understanding the replacement schedule for components, such as the helmet’s suspension system, is vital to ensure continued protection. While the upfront cost of helmets may be higher, the longer lifespan of some models can offset the initial investment, making them a cost-effective solution in the long term.
Overall, the adoption of helmets in the construction industry is a significant step forward in enhancing worker safety. These helmets offer superior protection and are likely to
reduce fatalities and serious injuries. For employers, this translates into a safer workforce, reduced downtime due to accidents, and potentially lower insurance costs. By investing in modern head protection, the construction industry can prioritize worker well-being while also benefiting the bottom line.
In conclusion, the transition from traditional hard hats to advanced helmets is not just a trend—it’s a crucial evolution in safeguarding the lives of construction workers. As more companies adopt these helmets, the industry will see the long-term benefits of this enhanced protection.
BY JEREMY GREY, EXECUTIVE VICE PRESIDENT OF INDUSTRIAL DEVELOPMENT | HRP GROUP
The 1860s marked a pivotal era in Philadelphia’s industrial history, with the establishment of the Philadelphia Energy Solutions (PES) refinery, originally a whale oil refinery. Fast forward over 150 years and this historic site would become the focal point of HRP Group's acquisition and redevelopment, following a devastating explosion in June 2019 that led to the refinery’s bankruptcy. The process of purchasing this massive 1,300-acre parcel, covering nearly 2% of Philadelphia’s land area, was fraught with challenges, from navigating complex bankruptcy proceedings to conducting due diligence at the height of the COVID-19 pandemic.
“It was hard to believe that such a large asset existed within city limits, close to strategic infrastructure and a strong labor force” HRP Group noted. By leveraging its expertise in brownfield redevelopment, HRP Group was able to finalize the purchase in June 2020. The company’s experience with environmentally challenging sites, coupled with proactive stakeholder engagement and multiple pre-closing agreements, made the acquisition possible. Reflecting on the site’s legacy, HRP Group acknowledged that the last time a property of this magnitude was master-planned in Philadelphia was by William Penn in the 1680s.
The transformation of the former refinery site into The Bellwether District represents a monumental project. Envisioned as a 1,300-acre, multi-modal logistics park, The Bellwether District will be the future home for leaders in e-commerce, life sciences, innovation, and logistics. The scale is staggering: 15 million square feet of new development will reshape the region’s economy, delivering sustainable growth and driving change.
Since acquiring the site, HRP Group has embarked on an ambitious journey, undertaking demolition, decommissioning, master planning, environmental remediation, and vertical construction. A few key achievements include:
• Demolition & Decommissioning: The refinery’s closure has contributed to a 16% reduction in Philadelphia’s
carbon footprint. HRP has removed 920 miles of pipelines (equivalent to the distance from Philadelphia to Florida), dismantled 350 tanks, and repurposed over 200,000 tons of metal.
• Site Work: The extensive earthwork, expected to move 4 million cubic yards of soil, is raising the site above floodplain levels to ensure climate resilience. To date, 1.8 million cubic yards of earth have been shifted.
• Infrastructure: The plan includes 20,000 linear feet of new roads and 40,000 linear feet of new utilities to serve the logistics park.
The Bellwether District is expected to generate substantial economic benefits for the city and state. Over the lifetime of the project, HRP Group estimates the creation of 47,000 jobs—28,000 of which will be project-related and 19,000 permanent. So far, 2,000 workers have already been employed onsite. The projected tax revenue for the City of Philadelphia stands at $100 million annually, with another $120 million anticipated for the Commonwealth of Pennsylvania.
One of the crucial lessons HRP Group learned is the importance of stakeholder outreach during the early stages of such large-scale projects. “We needed a plan that was supported by the community” HRP Group emphasized. Early feedback indicated a desire to reconnect the formerly closedoff area to the city, leading to the inclusion of bike lanes and pedestrian paths, new roads, and public transportation improvements. Sustainability was another priority. Plans for The Bellwether District include 10,000 new trees, LEEDcertified buildings, solar-ready rooftops, and electric vehicle infrastructure.
Strategic planning and coordination have been essential in managing the many moving parts of this project. Aligning demolition, environmental remediation, and development workflows while accounting for contingencies, has been vital to progress.
Given the complexity of redeveloping a 154-year-old refinery site, HRP Group relies heavily on its contractors to creatively address unforeseen conditions. Sitework challenges, such as soil issues and underground obstructions, are significant and contractors are expected to propose innovative, costeffective solutions. Additionally, HRP Group values thoughtful approaches to reusing onsite materials and managing environmental remediation.
When awarding contracts for The Bellwether District, HRP Group prioritizes safety, proven track records, and local expertise with brownfield sites. Inclusion and local participation are also critical, particularly as it relates to hiring practices. The company is committed to ensuring the involvement of local contractors and workers in this transformative project.
HRP Group credits the City of Philadelphia with being a strong partner in The Bellwether District’s development. For future growth, they urge the city to continue issuing permits and approvals promptly to meet market demands and tenant requirements. Given the size and scope of The Bellwether District, the company also encourages the city to adapt some of its permitting processes and design criteria to better accommodate large-scale projects.
As The Bellwether District evolves, HRP Group remains focused on attracting a diverse range of tenants in sectors such as e-commerce, life sciences, logistics, and light manufacturing. Additionally, the site’s significant electrical infrastructure makes it ideal for data centers. HRP also anticipates strong demand from port users, marine industries, and air cargo businesses, given the site’s proximity to key transportation hubs.
HRP Group’s redevelopment of The Bellwether District is not just a project; it is a vision for Philadelphia’s future, blending sustainable growth with cutting-edge innovation to revitalize a historic site and create opportunities for generations to come.
BY BEN HOFFERMAN CPA, CITP, CHIEF CONSTRUCTION OFFICER | RKL ESOLUTIONS
Project managers in the construction industry fill a highly versatile role, handling various responsibilities throughout each project lifecycle, from overseeing construction activities to managing financial operations. Unfortunately, this variability often leaves employees overburdened with administrative tasks that take time away from strategic job functions. Accounts Payable (AP) is one of the most common functions fraught with administrative, paper-based processes and human error. However, with the emergence of advanced AP automation software solutions, construction accounting is witnessing a significant transformation, leading to streamlined functions and better employee job satisfaction.
Businesses automate their AP processes using a range of digital tools and integrated software solutions to manage the flow of invoices and payments in an organization. In construction accounting, this technology can be especially beneficial for several reasons:
1. Optimization of Invoice Management: In the construction industry, the influx of invoices from numerous suppliers and subcontractors can be overwhelming, so AP automation can be a critical factor
in streamlining the process. With the integration of Optical Character Recognition (OCR) technology, these systems can swiftly capture and interpret data from various invoice formats, significantly cutting down the hours otherwise spent on painstaking manual entry. This increase in efficiency accelerates the billing cycle and allows staff to redirect their focus to more productive tasks that contribute to the progress of construction projects.
2. Financial Savings and Incentive Capture: Automating accounts payable is a strategic move toward cost containment. By reducing the dependency on manual labor for invoice processing, companies can cut down on operational expenses. Moreover, the enhanced processing speed allows companies to take advantage of suppliers' early payment discounts while decreasing the likelihood of incurring late payment penalties. These financial advantages can contribute to considerable savings over time, boosting the company's bottom line.
3. Precision in Payments: The precision offered by automated systems is invaluable in the construction sector, where the margin for error is slim. Automated AP solutions meticulously validate details, ensuring that
payments are processed for the correct amounts and directed to the appropriate recipients. This meticulous attention to accuracy fortifies supplier trust. It reduces the risk of financial discrepancies that could lead to disputes or interruptions in the supply chain, often the precursors to costly project setbacks.
4. Strategic Cash Flow Oversight: Effective cash flow is the lifeblood of any construction project and AP automation offers a high level of control over this vital metric. With transparency in accounts payable, construction financial managers gain access to real-time data that is essential for informed decision-making. This visibility allows for meticulous financial planning and can significantly assist in aligning outgoing payments with the project's cash inflow, thus maintaining a healthy financial equilibrium.
5. Regulatory Adherence and Auditable Records: The construction industry operates within a complex regulatory framework, making compliance a top priority. AP automation systems are designed to securely document and catalog every transaction for quick access as needed. This digital record-keeping is vital not only for maintaining regulatory compliance but also for simplifying the audit process. In an inspection or audit, an organized and accessible audit trail is crucial for swiftly demonstrating adherence to financial regulations and industry standards.
Beyond the operational benefits, AP automation has a profound impact on employee job satisfaction, helping companies retain their top talent through times of uncertainty and hiring shortages.
1. Elevation to High-Value Activities: When routine and monotonous tasks are automated, employees are liberated from the drudgery of manual work. This shift allows them to dedicate their time and energy to high-value activities that require a strategic mindset and analytical skills. Contributing to the organization's success through meaningful work can significantly enhance job satisfaction. Participating in decisionmaking processes and developing innovative solutions gives employees a stronger sense of achievement and professional fulfillment.
2. Alleviation of Workload Pressures: Automating the processing of a high volume of invoices can significantly reduce the workload on employees. By entrusting repetitive and time-consuming tasks to software, the risk of human error is minimized, deadlines become more manageable, and the overall pace of work is more balanced. This reduction in stress levels can lead to decreased employee burnout, improved job satisfaction, and a healthier work-life balance, contributing to a more resilient and content workforce.
3. Opportunities for Professional Growth: Automation also opens doors for staff to further their professional skills. As the need for manual entry diminishes, employees can direct their focus toward acquiring new competencies and enhancing their expertise in more complex accounting and financial management areas. This upskilling leads to increased career opportunities, personal growth, and a more robust portfolio of skills, supporting the organization's succession planning efforts.
4. Empowerment via Advanced Tools: Modern automation tools are designed to simplify tasks, increase accuracy, and save time, allowing staff to make confident decisions based on timely and relevant data. Knowing that they are equipped to perform at their best and are integral to the company's innovation and competitiveness can boost morale and create a culture of continuous improvement and efficiency.
5. Fostering a Collaborative Culture: Accounts payable (AP) automation solutions often include features that enhance collaboration among team members. These tools may offer real-time communication capabilities, shared access to documents, and streamlined approval processes, which can strengthen teamwork and collective problem-solving. When employees collaborate effectively, it increases efficiency and fosters a sense of community and shared purpose, which can greatly enhance overall job satisfaction.
Implementing AP automation within construction accounting is both a matter of financial efficiency and a strategic investment in human capital, our most valuable asset. As construction firms embrace this technology, they pave the way for smoother operations and a more satisfied workforce, ultimately contributing to the overall success and growth of the business. With the construction industry's continuous push towards innovation and efficiency, AP automation stands out as a key enabler of both operational excellence and employee engagement.
BY NATHAN DENNIS, PRESIDENT | TARGET BUILDING CONSTRUCTION
Target Building has maintained a strong partnership with the Carpenters’ Apprentice Ready Program (CARP) for several years, during which the program has undergone significant evolution under the guidance of leaders Bob Landy, Ron Walsh, and Joe Lockley. Over time, several CARP participants have progressed to become journeypersons with Target Building. This year, we are proud to have hired two more CARP graduates as carpenter apprentices, Jashon Holland and David Wakeley Jr., who are already exceeding our expectations.
I recently had the privilege of attending the CARP graduation ceremony at the Philadelphia Museum of Art with our Director of Field Operations, Dan Hummel, alongside 30 students who graduated from the program. Speaking with the graduates, I was impressed by how prepared they were to enter the workforce. Their confidence and readiness were evident, a testament to the quality of the CARP program.
Bob Landy, who gave the commencement speech, made a significant impression with his passion and dedication to the students. His advice to the graduates was simple yet powerful: show up early, be the first onsite and the last to leave, and always come to work no matter the circumstances. He reminded the graduates that while there may be days when they don’t feel their best or have personal challenges, their union brothers and sisters will be there to support them, and it’s essential to take turns stepping up when needed. This sense of teamwork and responsibility resonated with me.
The Carpenters’ Apprentice Read Program is a 10-week training program that gives participants math and skills training and prepares them to take the Carpenters Apprenticeship Exam and begin careers in the union carpentry, but it goes beyond that. It fosters a strong work ethic and sense of responsibility, which is clearly reflected in the apprentices' dedication. The two CARP graduate apprentices currently working with us are excellent examples. One is contributing at the UPenn Stuart Weitzman Hall project, while the other is working at the SHIP Building 1 in
Springhouse. Both apprentices are showing up every day, working hard, and exceeding our expectations. We are excited to watch their continued growth as they progress through their apprenticeship and contribute to the success of Target Building.
During the CARP graduation, I gained deeper insight into the program’s holistic approach to supporting the participants. A representative from Everybody Builds Philadelphia inquired about a graduate who had missed his driver’s test, and when the graduate explained that he had no way to get there, the representative immediately took action. They arranged a new test date and provided transportation, ensuring that the young man would have his license and, therefore, a reliable way to get to work. This experience highlighted why the CARP program is so successful: it’s a team effort that goes beyond just technical training. They make sure the needs of each candidate are met, acting on their promises and ensuring results.
It’s essential to spread the word about the quality of the CARP program and its impact. I hope that more construction managers in Philadelphia have the opportunity to learn about this initiative and see the caliber of pre-apprentices that it produces. Attending the graduation was eye-opening for me;
the professionalism of the candidates was undeniable. These young men and women were dressed well, carried themselves with confidence, and greeted me with firm handshakes and direct eye contact. It’s clear that the program doesn’t just teach carpentry—it also emphasizes the importance of how to present oneself in the professional world.
I think a key aspect of the CARP program’s success is that it doesn’t rely on legacies, which helps introduce new individuals to the trades who may not have previous knowledge of the union trades. This approach is crucial for the continued replenishment of skilled labor in the city. If every union brought in even 30 new candidates annually, it would help lead to a steady infusion of qualified, skilled workers into the workforce, changing the landscape for the next generation.
During a recent visit to the CARP school, Bob Landy gave me a tour of the facilities, and I was deeply impressed by what I saw. The shop area, welding shop, and an underwater tank used to teach students underwater welding were remarkable. During the visit, I observed students taking their final exams, and the focus and intensity in the room was palpable. It was clear how seriously these students were taking their education and training. Some will likely go on to become foremen, superintendents, or even start their own businesses, creating jobs and further contributing to the construction industry.
At Target Building, we are proud of our partnership with CARP and look forward to seeing how the program continues to evolve. By helping to grow pre-apprenticeship programs like CARP, we’re contributing to the future of the trades in Philadelphia and ensuring that the next generation of workers is well-prepared to meet the demands of the industry. We
remain committed to supporting these efforts and look forward to seeing the positive impact they will have on our workforce and our city.
The Carpenters Joint Apprentice Committee of Philadelphia & Vicinity, the Eastern Atlantic States Regional Council of Carpenters, and the General Building Contractors Association, have partnered to offer the CARP. CARP is a Pre-Apprenticeship program registered with the PA Department of Labor
Everybody Builds Philadelphia works with existing Philadelphia Building and Construction Trade Union and Apprenticeship and PreApprenticeship programs to increase the skilled diverse workforce in the construction industry.
BY ERIK HIGHLAND, MARKETING DIRECTOR | SUPERIOR SCAFFOLD SERVICES, INC.
This one is hard to miss. If you are a regular in the Rittenhouse Square area – or were just passing through, St. Patrick’s Church has been a fixture here since 1839. When one of Philadelphia’s esteemed historic buildings needed major renovation, we were called in to help.
Superior Scaffold was proud to have been chosen to provide the scaffolding and access work on this historic landmark. Our extensive experience with historic and delicate structures made us a natural fit when Turner Construction took on the project.
Like any project this size, it involved a mountain of moving parts. Access issues, street closures, and adapting to the changes on how best to approach this giant endeavor were some of the challenges that were a part of the project.
If you were just walking through Rittenhouse Square and saw this, you’d probably think, “wow, that’s a lot of scaffolding for a renovation, but nothing special.” And that’s where you would be wrong.
Scaffolding this intricate and a delicate project was a big challenge.
These older structures require a special touch, so that everything remains as it was 150 years ago. That means using every bit of skill and knowledge we have to not to touch the building or leave a mark of any kind on this historic church. As you can imagine, erecting scaffolding in and around all of the geometric shapes and areas, like stained glass windows, columns, decorative cornices, roof lines, etc., was a huge challenge.
Our scaffold engulfed three sides of the old church. We used containment wrap around the entire structure to keep debris from slipping out.
One of the best examples of the detail and care we took in erecting thousands of steel and aluminum parts around sensitive materials can be seen in the main entrance around the columns and around the stained-glass windows. We had to get close enough for crews to be able to clean and repair everything. Our system scaffold works best for just this type of application. It allows us to erect scaffolding at odd angles enabling us to get to hard-to-reach areas while still providing the strength and stability needed for renovation workers’ safety.
We had a canopy, or overhead protection, around the entire perimeter and rectory to protect pedestrians while also
allowing the church to remain open for regular service during the entire renovation. This was very important for St. Patrick’s to remain open throughout the renovation process.
We had several 2,000lb material hoists on the South side and a Maxial hoist on the inside to help lift material. There were also multiple stair towers for access to every floor, and each level was decked in, so crews had full access to every inch of this restoration.
We needed to install shoring posts beneath the parking lot for support in the underground utility to help carry the added weight our scaffold was putting onto the area. We don’t have photos of that but it’s there.
Finally, we had scaffold on the roof area to access those hardto-reach areas and the beautiful cross at the top.
Of course, there are always challenges on a job like this and we worked closely with everyone at Turner to make sure there were as few wrinkles as possible.
For instance, the Rittenhouse Square St. side of the church where our scaffold runs the entire length of the building, needed the city to shut down a portion of the street. Easy peasy, you say? As you can imagine, shutting down even a portion of a busy street can be difficult.
With this in mind, we worked with Turner Construction Company and the Department of Streets, to submit drawings, right of way detour plans and changes to get Streets and L&I what they needed to close off the entire lane on the South side of the church.
In the end, we had crews completely around 3 sides of this massive structure to do the repair and renovation work and boy does it look fantastic!
We would like to give a shout out to everyone who made this project a success, particularly our crew, Turner Construction, who brought us along for the ride, The Philadelphia Streets Department and L&I. It’s not often those last two get any thanks. So, if you are in the area, walk on by and see the newly renovated St. Patrick’s Church – you won’t be disappointed.
Building a better Philadelphia demands the best— exceptional talent, unmatched craftsmanship, and the highest standards the commercial construction industry has to offer.
For over 130 years, the distinguished members of the General Building Contractors Association (GBCA) have set the benchmark for commercial construction in Greater Philadelphia. While their work is most visible in our iconic skyline, their influence extends to the places where we work, live, learn, and play, shaping the fabric of the entire region.
This year’s honorees represent more than just remarkable projects—they embody the essence of what it means to build with purpose, precision, and passion. Whether through groundbreaking technologies, sustainable practices, or unmatched craftsmanship, each winner showcases the very best in commercial construction. Excellence in Action emphasizes that it’s not just about the final structure, but about the commitment to quality and progress in every phase of the process, helping shape Philadelphia into a stronger, more vibrant city.
Check out this year's winners!
Battaglia's program focuses on five DEI initiatives: training/education, diverse partnerships, embedding DEI within the hiring process, social media/marketing awareness, and expanding its internal supplier diversity program. Through executive commitment and the company’s diversity program manager, the organization has increased the diversity of its suppliers and looks forward to utilizing these partnerships to support and further enhance DEI efforts. Other exciting achievements include developing Battaglia’s first DEI summit in 2023 and implementing its first DEI annual training requirement.
Oliver Fire Protection & Security showcases exceptional leadership in safety through a comprehensive program centered on continuous improvement and proactive hazard management. In the past 18 months, the company has significantly reduced its incident rate and earned the Highwire Gold Safety Award for 2023 and 2024. They prioritize mandatory OSHA certifications for all employees alongside robust training initiatives like Annual Safe Driver, Electrical Safety, and Fall Protection Training, demonstrating their unwavering commitment to employee well-being and community safety.
Skanska USA Building's Community Action Committee is dedicated to making a positive impact within the local communities it builds in. With a mission to promote community excellence and longevity, the committee plans four annual events that engage and encourage the participation of respective job sites. Notable highlights include Skanska's Day of Service, which is a marquee event that has been held for over a decade, and the Skanska Charity Challenge Golf Outing, now in its 15th year, which brings subcontractors and vendors together for a round of golf and to raise money for a charity of their choice.
WINNER
PROJECT DESCRIPTION
The CCORF is designed to produce 38,000 tons of Class A compost annually. The 103,000-square-foot processing building contains 18 240-foot-long bays where raw materials are loaded in one end, turned and advanced automatically by a rail-guided agitator, and removed as finished compost at the other end. The key project requirement was to construct the 8-foot-high concrete bay walls within a 1/16" tolerance in every direction and relative to adjacent bay walls so the agitator can travel unimpeded. The CCORF project concrete construction means and methods will become the standard for future composting facilities.
OWNER
Synagro Technologies, Inc.
GENERAL CONTRACTOR
Bittenbender Construction, LP
ENGINEER
On-Board Engineering
GBCA MEMBER COLLABORATORS
• Oliver Fire Protection & Security
WINNER
Geppert Bros., Inc.
PROJECT DESCRIPTION
The Princeton Art Museum Demolition involved the demolition of several wings and additions of the existing Princeton University Art Museum, including the Marquand Library, CRAM Hall, and portions of McCormick Hall. The carefully planned removal of these structures was a key step in preparing the site for the construction of a new 150,000-square-foot Art Museum. The new facility will showcase modern architectural design while preserving the cultural heritage of Princeton. Once completed, it will house an expanded collection of artworks, enhancing the museum’s ability to serve as a cultural and educational hub for students, faculty, and visitors.
OWNER
Princeton University
CLIENT
LF Driscoll
ARCHITECT
Adjaya Associates
WINNER
PROJECT DESCRIPTION
As construction manager, C. Erickson & Sons, Inc. transformed The Franklin Institute's Wondrous Space Exhibit by merging two galleries into an immersive, interactive experience. Utilizing cutting-edge virtual and augmented reality technology, the redesign features advanced, sustainable materials and construction techniques for energy efficiency and structural integrity. The project simplifies complex astronomical concepts through engaging displays, reflecting Erickson's commitment to innovative educational design and STEM enrichment. By collaborating closely with architectural and engineering teams, Erickson created an inclusive space that enhances learning and upholds The Franklin Institute’s legacy in science education.
OWNER
The Franklin Institute
ARCHITECT
JacobsWyper Architects
ENGINEERS
Bala Consulting Engineers
Keast & Hood Structural Engineers
GBCA MEMBER COLLABORATORS
• Bell Supply
• Independent Contract Flooring, LLC
• Oliver Fire Protection & Security
PROJECT DESCRIPTION
Clemens Construction Company, in collaboration with Rebuild Philadelphia, revitalized Ziehler Playground, a 7.1acre public park in Olney, North Philadelphia. This green space project included installing new stormwater BMPs, modern playground equipment, safety surfaces, basketball courts, seating areas, shade structures, permeable paving, rain gardens, landscaping, and new concrete and asphalt walkways. The 3,800-square-foot Recreation Center also underwent a comprehensive remodel, encompassing new restrooms, a multipurpose community room, boxing gym, staff office, MEP upgrades, paint, and roof/awning restoration. Rebuild Philadelphia aims to build cleaner, greener, stronger communities one park, rec center, and library at a time.
Philadelphia Parks & Recreation
Rebuild Philadelphia
Ian Smith Design Group
Salt Design Studio
D’Huy Engineering
Mark Ulrick Engineers
Meliora Design
Miller Design Group
• Carr & Duff
• Eureka Metal & Glass Services, Inc.
• Geppert Bros., Inc.
• Liberty Flooring, LLC
• Unified Door & Hardware Group, LLC, Tru-Fit Frame and Door
WINNER
Turner Construction Company
PROJECT DESCRIPTION
Recognizing the need for comprehensive care and accessibility, this outpatient surgery center consolidates and integrates 18 specialty services. This ambitious endeavor reflects the growing trend of co-locating medical specialties to facilitate personalized care in a convenient and less stressful environment compared to traditional hospital settings. Central to the approach was the creation of distinct zones, or specialty pods, each signified by a vibrant color that reflects the brand and serves as a space planning tool. To transition from a single-point welcome desk to these zones throughout the 43,000-square-foot facility, meaningful adjacencies optimize patient flow and staff efficiency.
OWNER
Nemours Children's Health
ARCHITECT
NORR
ENGINEER
Barton Associates, Inc.
GBCA MEMBER COLLABORATORS
• ARC Document Solutions
• Belcher Roofing Corporation
• BrandSafway Services, LLC
• ClarkDietrich Building Systems
• Revolution Recovery, LLC
• WillScot
• United Rental, Inc.
• M. Schnoll & Sons, LLC.
• Milwaukee Electric Tool Corp.
• Sunbelt Rentals
WINNER
PROJECT DESCRIPTION
The Meadows Central Utility Building (CUB) is a singlestory structure featuring geo-exchange facilities that provide thermal energy for buildings in the new Meadows Neighborhood. The project includes two Thermal Energy Storage (TES) tanks, electrical transformers, and a natural gas-powered backup generator, all visually integrated with architectural screening and landscaping. The TES tanks store water for heating and cooling, designed for use during economically and environmentally advantageous times. Connected to 156 geo-exchange bores beneath the softball field, the CUB supports Princeton's goal of carbon neutrality by 2046. The building incorporates sustainable design strategies, aiming for LEED Gold certification from the U.S. Green Building Council.
OWNER
Princeton University Office of Capital Projects
ARCHITECT
ZGF Architects
ENGINEER
Introba
GBCA MEMBER COLLABORATORS
• All Trades Mechanical
• American Floors, Inc.
• Artisan Display, Inc.
• Berlin Steel Construction Co.
• DWD Mechanical Contractor, Inc.
• EDA Contractors, Inc.
• Frank T. Lutter, Inc.
• Fromkin Brothers, Inc.
• Independence Steel and Erectors
• National Glass & Metal Company, Inc.
PROJECT DESCRIPTION
To accommodate a growing student body, KIPP Hatch Middle School’s 1920s building and its three-story 1980s addition were completely renovated. The school, part of the KIPP Cooper Norcross family of public charter schools, serves students from educationally underserved communities. The 130,000-square-foot project introduced new basketball courts, a new kitchen, and a new auditorium featuring stateof-the-art A/V systems. The 1980s addition received a new CFMF roof truss system with new sheathing and roofing. The entire building received new finishes, including flooring, ceilings, lighting, and doors, as well as a new mechanical system for fresh air and energy recovery.
OWNER
KIPP Cooper Norcross Inc.
ARCHITECT
Strada
ENGINEERS
Alderson
IMEG Consultants Corp.
Langan
• Brock Industrial Services
• Creative Services Inc.
• EDA Contractors, Inc.
• Falasca Mechanical Inc.
• Joseph Dugan, Inc.
• Liberty Flooring, LLC
• Patriot Roofing Inc.
• M. Schnoll & Sons, Inc.
• Richard R. Pucci & Associates
• Southern New Jersey Steel Co., Inc.
• Suburban Enterprises Terrazzo & Tile Co., Inc.
WINNER
PROJECT DESCRIPTION
In 2020, PULLMAN embarked on an exciting, multifaceted historic preservation project on the third-oldest state capitol building still in use, the New Jersey State House. With the oldest part of the structure dating back to 1792, a full-scale renovation of the entire building was led by Daniel J. Keating Company to make the State House safe and functional for generations to come. PULLMAN was awarded a contract to restore the entire historic stone, brick, and stucco façade, and to stabilize and strengthen the original structural rubble stone walls of the building without disrupting interior finishes.
OWNER
Daniel J. Keating Company
ARCHITECT
Nelson
ENGINEER
Silman
CONSERVATOR
Preservation Design Partnership
GBCA MEMBER COLLABORATORS
• BrandSafway Services, LLC
• Hilti Inc.
• Sunbelt Rentals
PROJECT DESCRIPTION
Clemens Construction Company provided general contracting services for the high-end architectural overbuild of an 11,000-square-foot dining facility atop the historic Union League of Philadelphia. The new "Trumbauer's" Rooftop Restaurant features a commercial kitchen, indoor and outdoor dining, a large arched skylight, central bar, private dining room, wine storage, and new restrooms. The scope also included the extension/modernization of existing elevators and stairwells, and the replacement/relocation of hotel chillers and rooftop mechanical equipment. Clemens collaborated closely with the City of Philadelphia Historical Commission to ensure design intent and historic requirements were met, seamlessly blending modern amenities with the League's classic architectural style.
OWNERS
Quatrefoil Consulting
The Union League of Philadelphia
ARCHITECT
Chambers Architectural Associates
ENGINEERS
Bala Consulting Engineers
Next Level Design
O’Donnell & Naccarato
The Lighting Practice
• AEGIS Project Controls
• BrandSafway Services, LLC
• CDP Construction, LLC
• Cippco lnc.
• Crescent Iron Works
• Eureka Metal & Glass Services, Inc.
• Independence Steel and Erectors
• Liberty Flooring, LLC
• Maxim Crane Works LP
• Mega Construction Co.
• O’Donnell & Naccarato
• Oliver Fire Protection & Security
• Phoenix Contractors Inc
• Skyway USA, Inc.
• Tracey Mechanical, Inc.
WINNER
PROJECT DESCRIPTION
Gilbane Building Company provided preconstruction and construction management services for the exterior façade renovation of the historic complex of the Main, Randell, and Curtis Buildings on Drexel University's campus. This is the oldest building group on Drexel's campus at 131 years old. The renovation included cleaning, restoring, sealing, and repointing the terracotta façade, repairing and restoring original windows, and replacing degraded mortar in order to extend the life of the structures. This project required meticulous logistics to work around an occupied building in the middle of Philadelphia’s University City, extensive mockup approvals, and daily reviews with the architect.
OWNER
Drexel University
ARCHITECT
VITETTA Architects & Engineers
ENGINEER
DCI Engineers
GBCA MEMBER COLLABORATORS
• Joseph Dugan, Inc.
• United States Roofing Corp.
• Window Repairs & Restoration, LLC
WINNER
PROJECT DESCRIPTION
The Meadows Central Utility Building (CUB) is a key component of Princeton’s plan for carbon neutrality by 2046. This single-story facility, connected to 156 geo-exchange bores located under the softball field, provides thermal energy for the new Meadows Neighborhood. Equipped with two Thermal Energy Storage (TES) tanks, electrical transformers, and a natural gas backup generator, the CUB’s infrastructure is carefully concealed with architectural screening and landscaping. The TES tanks store water for efficient heating and cooling during optimal times for both cost and environmental impact. Designed with sustainability at its core, the building is targeting LEED Gold certification from the U.S. Green Building Council.
OWNER
Princeton University Office of Capital Projects
ARCHITECT
ZGF Architects
ENGINEER
Introba
GBCA MEMBER COLLABORATORS:
• All Trades Mechanical
• American Floors, Inc.
• DWD Mechanical Contractor, Inc.
• EDA Contractors, Inc.
• Frank T. Lutter, Inc.
• Fromkin Brothers, Inc.
• Independence Steel and Erectors
• National Glass & Metal Company, Inc.
• Berlin Steel Construction Co.
PROJECT DESCRIPTION
Superior Scaffold Services, Inc. designed a scaffold that allowed crews to play a giant game of Operation! The scaffold got workers close enough to the structure to remove, attach, lift up and out 500-pound pieces of limestone that covered the entire exterior so they could reseal and waterproof the structure. A two-foot gap was created, enabling a crane cable to be threaded in between the building and scaffold. Workers attached the stones and slowly hoisted them out, one at a time, carefully avoiding hitting the scaffolding and building. This was executed during one of the windiest, rainiest, and stormiest times of the year.
OWNER
Rowan University
GENERAL CONTRACTOR
Masonry Preservation Group, Inc.
ENGINEER
Alternate Design Solutions
WINNER
PROJECT DESCRIPTION
Originally constructed between 1936 and 1939, Princeton’s Palmer Square Post Office closed for official use in 2015. The building is listed on the State and National Registries of Historic Places, so a renovation to become a fully functioning restaurant and brewery required significant considerations for historical preservation. Years of neglect also meant the building needed extensive restoration and rehabilitation. The building was gutted and required new heating, cooling, electric, and fire protection systems to house the restaurant's kitchen, dining rooms, and bars. While some sections were entirely redesigned, many original historic details were restored in the new Triumph Brewery.
OWNER
Triumph Brewing Company
OWNER’S REP
Princeton Design Guild
ARCHITECTS
Gittings Associates, PC
Historic Building Architects, LLC
Richardson Smith Architects
ENGINEERS
Fisher Marantz Stone
JT Engineering
Princeton Engineering Group, LLC
GBCA MEMBER COLLABORATORS
• Central Salvage Company, Inc.
• Crescent Iron Works
• D.M. Sabia & Co., Inc.
• Eureka Metal and Glass Services, Inc.
• James Floor Covering, LLC
• Masonry Preservation Group, Inc.
• Oliver Fire Protection & Security
• PDM Constructors, Inc.
• Unique Scaffolding Systems LLC
WINNER
Turner Construction Company
PROJECT DESCRIPTION
This outpatient surgery center brings together 18 specialty services under one roof, addressing the need for accessible, comprehensive care. The project embraces the growing trend of co-locating medical specialties, offering a more personalized and less stressful alternative to traditional hospital environments. The 43,000-square-foot facility features distinct specialty pods, each marked by a vibrant color that both enhances the brand and aids in space planning. Designed with meaningful adjacencies, the layout ensures smooth transitions from a central welcome desk to the various specialty zones, optimizing both patient flow and staff efficiency.
OWNER
Nemours Children's Health
ARCHITECT
NORR
ENGINEER
Barton Associates, Inc.
GBCA MEMBER COLLABORATORS
• ARC Document Solutions
• Belcher Roofing Corporation
• BrandSafway Services, LLC
• ClarkDietrich Building Systems
• Revolution Recovery, LLC
• WillScot
• United Rental, Inc.
• M. Schnoll & Sons, LLC.
• Milwaukee Electric Tool Corp.
• Sunbelt Rentals
PROJECT DESCRIPTION
The Carson, a large-scale mixed-use project in Northern Liberties, spans an entire block bounded by 5th Street to the east, Spring Garden Street to the south, 6th Street to the west, and a private access street to the north. It features a 12-story residential tower with retail on the east and a box grocer space on the west atop a one-story underground parking garage. Amenities include a basketball court, fitness studio, and demonstration kitchen. The rooftop offers lounge areas, a dog run, and panoramic views, complementing the 370 residential units.
OWNER
R Investment Twenty One LP
ARCHITECT
Perkins Eastman Architects
Alderson
IMEG Consultants Corp.
Langan
• Artisan Display, Inc.
• BrandSafway Services, LLC
• Central Metals, Inc.
• Component Assembly Systems, Inc.
• Creative Surfaces Inc.
• D’Andrea Bros. Concrete Co., Inc.
• EDA Contractors, Inc.
• Guthrie Glass & Metal, Inc.
• Independence Steel and Erectors
• James Floor Covering, LLC
• MEG Glass Inc.
• Richard R. Pucci & Associates
• Roman Mosaic & Tile Company
• Schnabel Foundation Company
• Torrado Construction Co., Inc.
• Unified Door & Hardware Group, LLC, Tru-Fit Frame and Door
• Union Electric Contracting Co.
PROJECT DESCRIPTION
This 5,500-square-foot, LEED-certified interior renovation and expansion revitalized a workplace, prioritizing functionality, comfort, and sustainability. Sustainable practices were a priority, with recycled materials, low VOC products, and high-efficiency HVAC systems incorporated. Enhanced commissioning and energy optimization ensured efficiency. Additionally, merging an adjacent suite introduced modern amenities, including flexible workspaces, a work café, huddle spaces, and a lounge. The finished space fosters creativity, collaboration, and employee well-being. Transparent communication and regular updates with the client fostered trust and satisfaction, showcasing resilience and innovation in navigating the complexities of a postpandemic construction environment.
OWNER
T. Rowe Price
ARCHITECT
Gensler Architects
ENGINEER
WB Engineers + Consultants
GBCA MEMBER COLLABORATORS
• Oliver Fire Protection and Security
• Paul Rabinowitz Glass Co.
• PDM Constructors, Inc.
• Suburban Enterprises Terrazzo & Tile Co.
EXCELLENCE IN CRAFTSMANSHIP: $15 - $50 MILLION
For the high-end transformation of the Union League of Philadelphia’s rooftop, Clemens Construction Company undertook a complex 11,000-square-foot architectural overbuild. The new "Trumbauer's" Rooftop Restaurant boasts both indoor and outdoor dining spaces, anchored by a central bar and highlighted by a dramatic arched skylight. The facility includes a commercial kitchen, private dining area, wine storage, and updated restrooms. Clemens also modernized and extended existing elevators and stairwells, while relocating hotel chillers and rooftop mechanical equipment. In close coordination with the City of Philadelphia Historical Commission, they ensured the project preserved the League’s historic charm while introducing modern functionality.
OWNERS
Quatrefoil Consulting
The Union League of Philadelphia
ARCHITECT
Chambers Architectural Associates
ENGINEERS
Bala Consulting Engineers
Next Level Design
O’Donnell & Naccarato
The Lighting Practice
• AEGIS Project Controls
• BrandSafway Services, LLC
• CDP Construction, LLC
• Cippco lnc.
• Crescent Iron Works
• Eureka Metal & Glass Services, Inc.
• Independence Steel and Erectors
• Liberty Flooring, LLC
• Maxim Crane Works LP
• Mega Construction Co.
• O’Donnell & Naccarato
• Oliver Fire Protection & Security
• Phoenix Contractors Inc
• Skyway USA, Inc.
• Tracey Mechanical, Inc.
• United States Roofing Corp.
• Window Repairs & Restoration, LLC
EXCELLENCE IN CRAFTSMANSHIP: $50+ MILLION
PROJECT DESCRIPTION
The Jessup House is a 20-story, 371,000-square-foot mixeduse residential tower at 12th and Sansom Streets, bordering Market East and Washington Square West. It features 399 residential units, 11,000 square feet of future retail space, and below-grade parking. The lower two-story podium is clad in dark gray brick, with the upper set-back portion consisting of full-height glazing, balconies, and undulating copper-colored metal panels. Amenities on the second and third floors include coworking space, a fitness center, kitchen/lounge, game room, outdoor terrace, plunge pool, and dog run. The 20th floor features penthouse units, a clubroom, and a roof terrace with incredible center city views.
OWNER Greystar Residential
ARCHITECTS
Perkins Eastman Architects
Stokes Architecture + Design
Studios Architecture
ENGINEERS
Bala Consulting Engineers
Bohler Engineering
IMEG Consultants Corp.
GBCA MEMBER COLLABORATORS
• Aegis Project Controls
• Berlin Steel Construction Co.
• Carr & Duff
• DWD Mechanical Contractor, Inc.
• Eureka Metal & Glass Services, Inc.
• Guthrie Glass & Metal, Inc.
• IMEG Consultants Corp.
• Independence Steel and Erectors
• Liberty Flooring, LLC
• Madison Concrete Construction
• Oliver Fire Protection & Security
• Siemens Industry Inc.
• Southern New Jersey Steel Co., Inc.
• Unified Door & Hardware Group, LLC, Tru-fit Frame and Door
THANK YOU TO OUR 2024 CONSTRUCTION EXCELLENCE AWARDS JUDGES!
KEVIN CANNON
Senior Director, Safety & Health Services, Associated General Contractors of America
NAZIA SHAH
Director, Safety & Health Services, Associated General Contractors of America
KATHLEEN SHORT, PHD
Assistant Teaching Professor, Assistant Program Director, Drexel University Construction Management Program
XI WANG, PHD, P.E., LEED GA
Assistant Teaching Professor, Drexel University Construction Management Program THANK YOU TO THE 2024 CONSTRUCTION
PRESENTING SPONSOR
LF Driscoll
PLATINUM SPONSOR
21 Unified
Eastern Atlantic States Regional Council of Carpenters
Southland Industries
T. N. Ward Company
GOLD SPONSOR
A.T. Chadwick Company, Inc.
CBIZ CompuData
DCI Engineers
Geppert Bros., Inc.
Kieffer's Appliances
Marcum LLP
P. Agnes, Inc.
Rosenberg & Parker
Turner Construction Company
SILVER SPONSOR
Aegis Project Controls
Bell Supply
Cement Masons and Plasterers
Union Local 592
Cippco lnc.
Clemens Construction Company, Inc.
Cumby, Spencer & Associates
Financial Group
E.C. Fence & Iron Works, Inc.
EDA Contractors, Inc.
Foundation Building Materials, Inc.
Herman Goldner Co., Inc.
Kreischer Miller
Microsol Resources
Milwaukee Electric Tool Corp.
National Glass & Metal Company, Inc.
O'Donnell & Naccarato, Inc.
Patrick DiCerbo - Northwestern Mutual
Steven Kempf Building Materials, a GMS Company
Superior Scaffold Services, Inc.
Wouch, Maloney & Co., LLP
Shawmut Design and Construction
Alpha Infinity
DeWalt Industrial Tool Co
Essential Sealants Inc.
EVB Towing
Fidelio Insurance Company
Lechner & Stauffer Inc.
Nationwide Mutual Insurance Company
BUILDING MATERIALS
Bell Supply
See our ad on page 13.
Kieffer's Appliances
See our ad on page 13.
Tague Lumber, Inc.
See our ad on the back cover.
FINANCIAL
Rosenberg & Parker
See our ad on page 21.
Wouch, Maloney & Co., LLP
See our ad on page 13.
GENERAL CONTRACTORS
Clemens Construction Company, Inc.
See our ad on page 33.
E.P. Guidi, Inc.
See our ad on page 21.
HSC Builders & Construction Managers
See our ad on page 79.
LF Driscoll
See our ad on page 81.
P. Agnes, Inc.
See our ad on page 23.
Turner Construction Company
See our ad on page 39.
INSURANCE
Pat DiCerbo
Northwestern Mutual
See our ad on page 35.
SAFETY CONSULTANTS
HazTek Inc.
See our ad on the inside front cover.
SPECIALTY CONTRACTORS
Aegis Project Controls
See our ad on page 19.
CIPPCO Inc.
See our ad on page 19.
Component Assembly Systems, Inc.
See our ad on page 79.
Diversified PHL, Inc
See our ad on page 17.
E.C. Fence & Iron Works, Inc.
See our ad on page 13.
Herman Goldner Company, Inc
See our ad on page 27.
O'Donnell & Naccarato, Inc.
See our ad on page 29.
National Glass and Metal Company, Inc.
See our ads on page 27.
IMAGINiT Technologies
See our ads on page 29.
Microsol Resources
See our ads on page 33.
Milwaukee Electric Tool Corp.
See our ads on page 77.