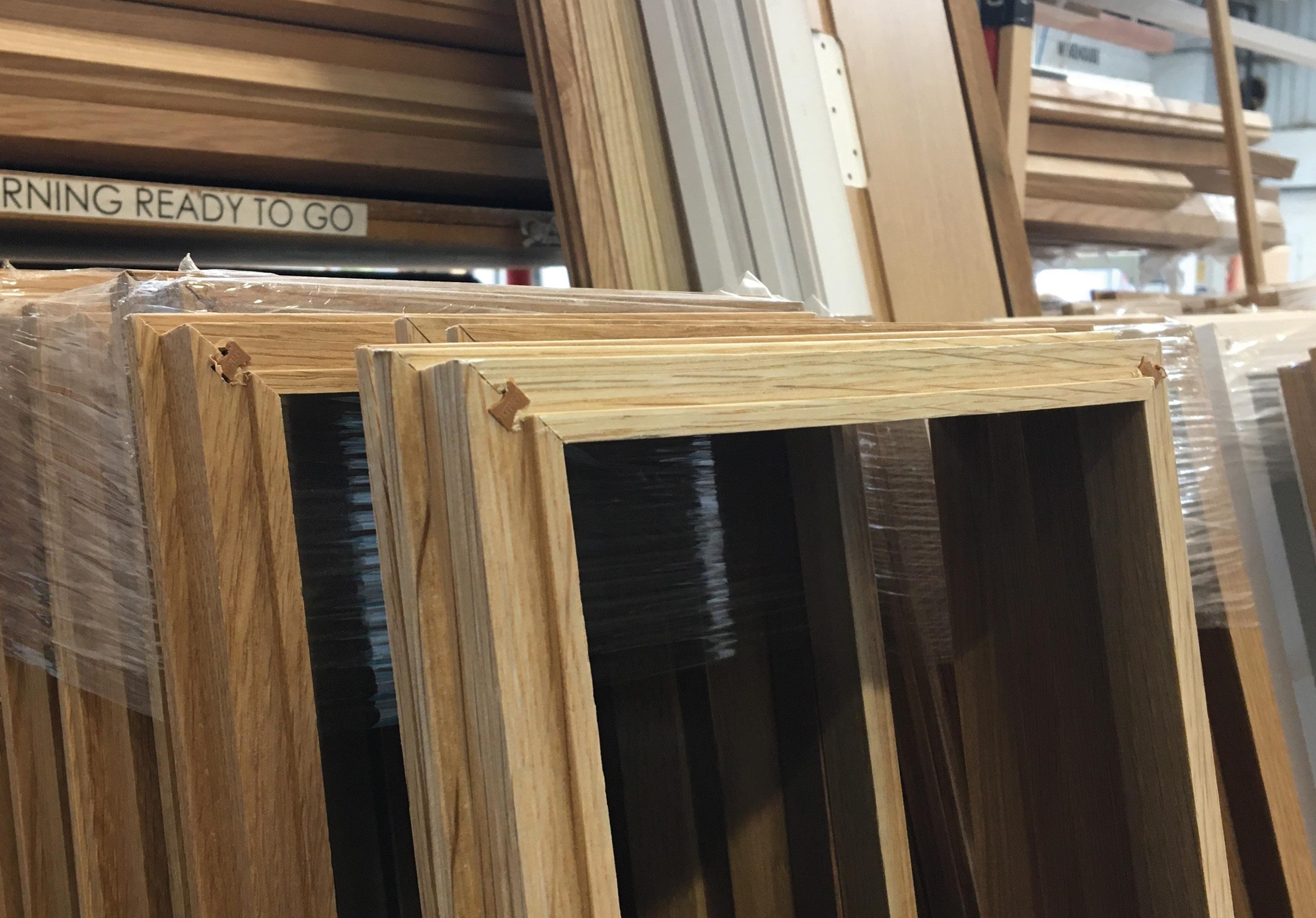
18 minute read
Installations
Ahmarra Door Solutions manufactures performance architectural doorsets across all sectors including education, commercial, hotel, airport and luxury residential. To deliver the quality expected at this level, the company looked to Lancaster-based Hoffmann Machine Co for a premium technology solution …
Ahmarra Door Solutions specialises in manufacturing performance doorsets for projects where complex fire-resisting, acoustic and security requirements exist – including timber-glazing bead cassettes for fire-rated doorsets, and timber panel mouldings for its range of bespoke Artisan Panel Doors. A combination of precision machinery and fine craftsmanship enables Ahmarra to meet the highest quality, performance and certification requirements. One of these precision machines is the Hoffmann MS 35-SF combination double mitre saw and router.
As an definitively innovative solution, the Hoffmann MS 35-SF delivers two clean, precision mitre cuts without break-out, to an exact length in one machine cycle. When both pieces are to be joined together or in a frame, then they can be prepared with one or two dovetail slots in precise positions in the cut faces, for jointing with Hoffmann Keys (suitable for workpiece sizes to a maximum of 90 x 90mm).
The machine can be fitted with router cutters for processing Hoffmann Key sizes W-1/2/3, making it ideal for cutting profiles for glazing beads, cornices, plinths, etc, in wood, aluminium or plastic at 45°. It can also be used solely as a double mitre saw.
High-precision cut
The technology, developed by Hoffmann for damping vibrations of the blades, ensures the high-precision cut of the MS 35-SF, and the almost vibration-free running of the machine means that no further work is required prior to joining.
“Our Hoffmann MS 35-SF has been extremely reliable and efficient,” explains Ahmarra’s managing director, Tim Doran. “Over the many years of manufacturing, many of our machines have required replacing and updating as expected, but the Hoffmann MS 35-SF has continued to manufacture a precision product with only routine maintenance required, and we see no reason to replace it in the near future.
“This combination machine not only cuts the perfect mitres, but simultaneously routers the dovetail slots for the Hoffmann Keys. Ahmarra has a long relationship with Hoffmann, and our current Hoffmann MS 35-SF has been in operation for over 20 years, and still performs with the expected accuracy and precision that it did the day it was installed,” enthuses Tim.
Ahmarra works very closely with architects and interior designers to meet their requirements, allowing flexibility in design while retaining comprehensive fire certification in accordance with Building Regulations. Hoffmann Dovetail Keys are all accredited with FD30/FD60 ratings.
Latest technology in design and production
As a leading manufacturer of fire door solutions, Ahmarra believes in maintaining the traditions of its craft by preserving the skills and value of time-served, traditional bench joiners, while
utilising the very latest technology in design and production methods. This way, its customers get the best of both worlds.
“Our many years’ experience of manufacturing timber doors has led us to produce a number of sector-specific product ranges, to include education, hotel and panelled doors,” points out Tim. “We specialise in working with clients who recognise the importance of developing doorset standards throughout their facilities. Significant client cost savings can be made by eliminating the need to redefine doorsets and ironmongery for each new project. We offer intelligent advice on how to make this process cost effective, simplifying what can be a very complex issue.”
A similar principle is held by Hoffmann Machine Company. When specifications such as optimisation, rationalisation and cost savings are essential aspects of a customer’s production, help can be found in its engineering services department.
The company can develop a package of measures that will result in a machine, designed to customers’ requirements, that offers efficiency, quality assurance and cost minimisation.
01524 841500 info@hoffmann-uk.com www.hoffmann-uk.com
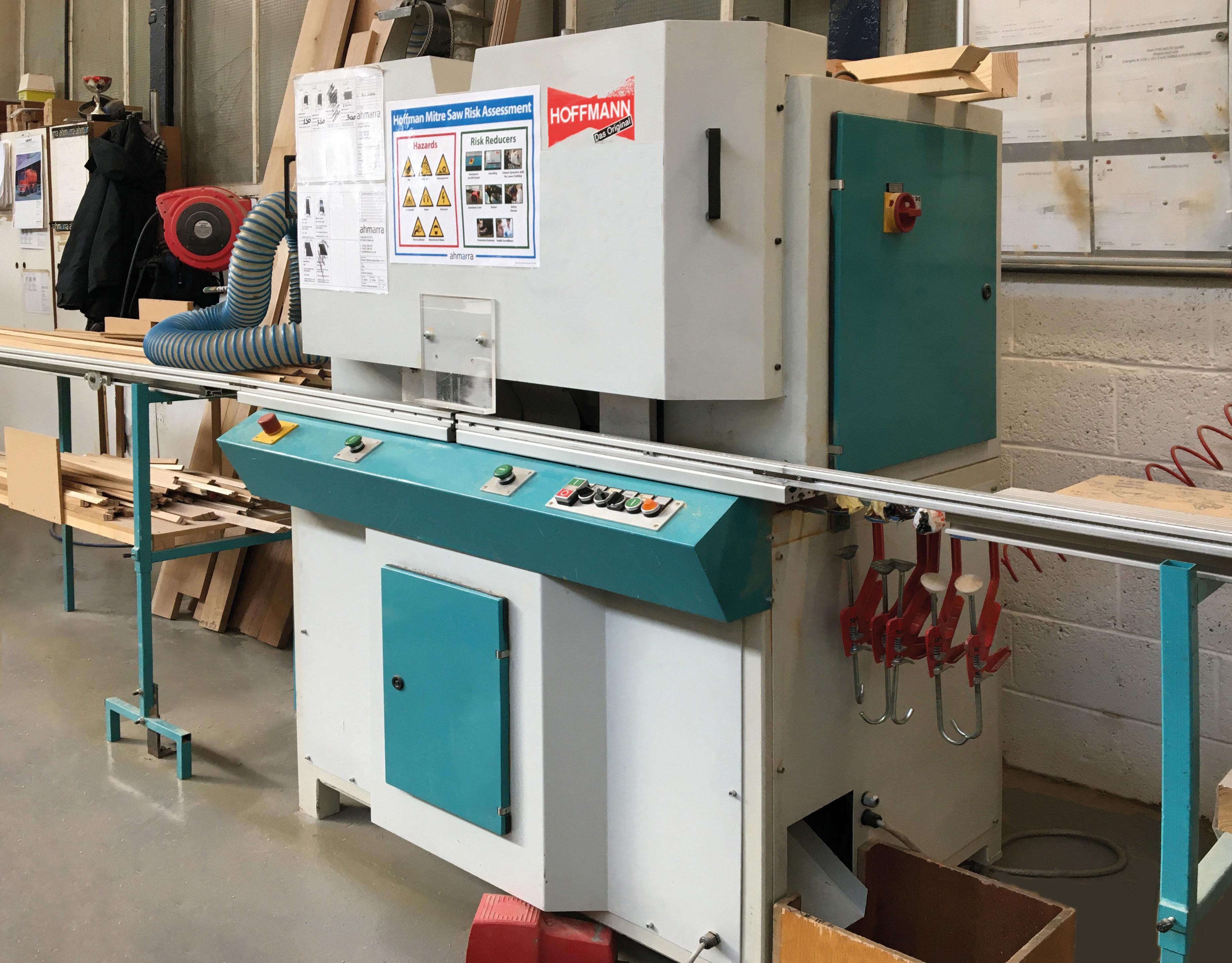
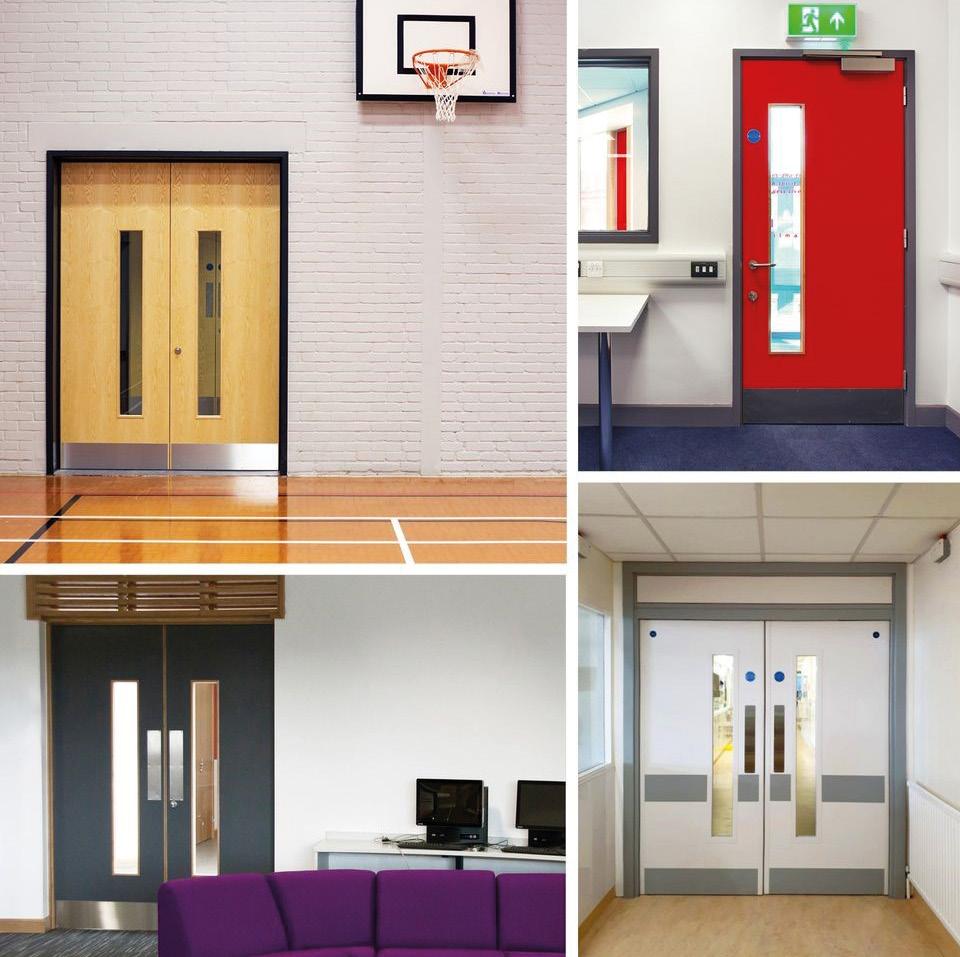
KWB London reaches new heights with Homag UK
KWB London specialises in bespoke kitchens, bedrooms, bathrooms and concierge fit outs for the London contract residential market. Founded in 2012 by joiner Kevin Behan, KWB’s focus on quality and service has given rise to rapid expansion. Since 2015, the company has been working exclusively with the large tier 1 contractors in London.
“We’ve been lucky to be invited to do some prestigious work, perhaps the most notable being Chelsea Waterfront which is our latest project,” explains KWB’s owner, Kevin Behan. He continues: “The gap in the market we fill is producing very bespoke joinery detailing in volume, something the larger outfits struggle to achieve.
“As our business began to take off, we realised we had to invest in better, larger CNC machinery. So, in 2016, we visited the Ligna show to research the market. That was a real eye-opener for us, and we were particularly impressed with the breadth and depth of the Homag presentation.”
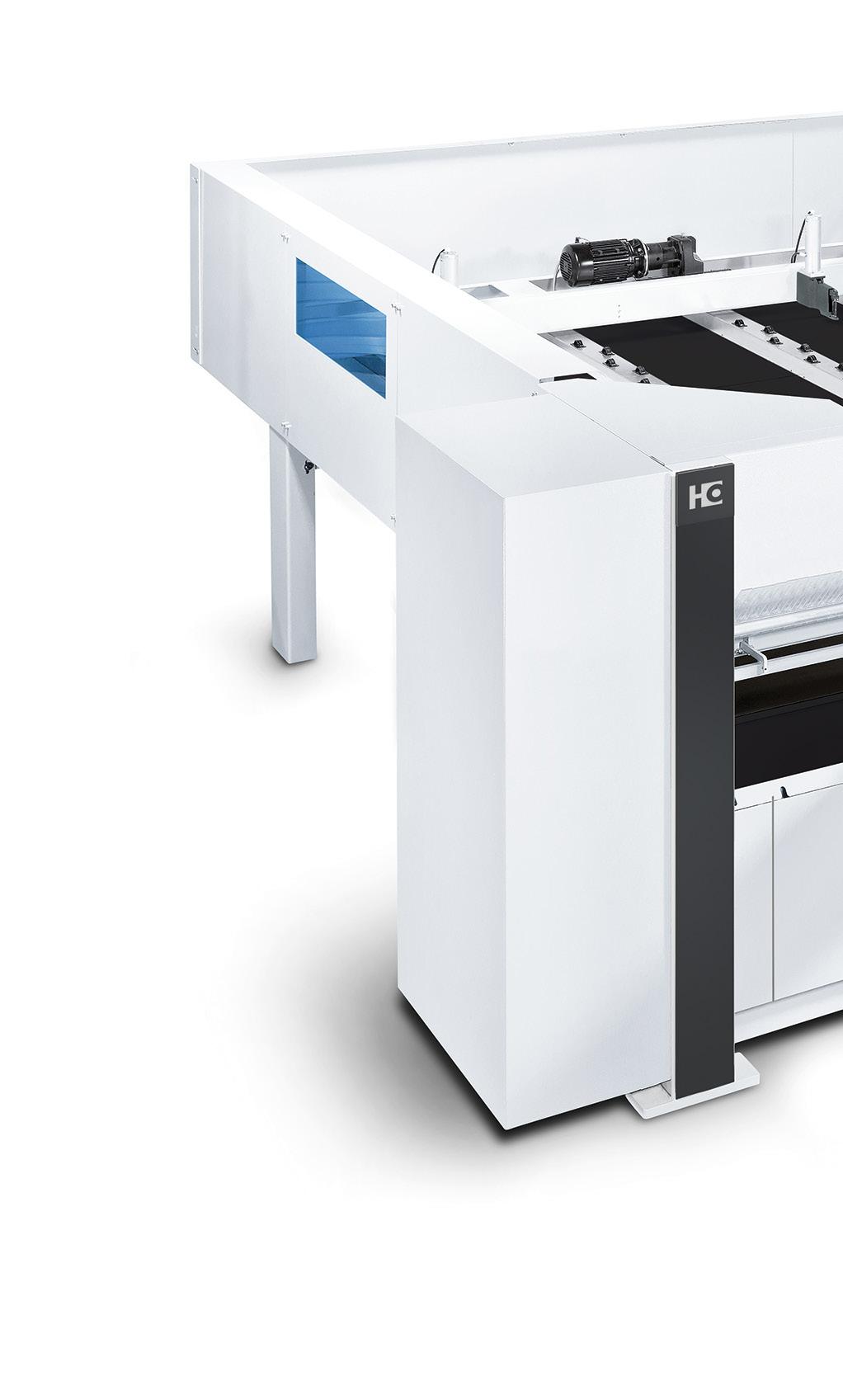
Swayed by price
“Despite feeling that Homag’s solutions were technically superior, we made the mistake of being lured by a lower-priced alternative. Unfortunately, we very quickly learnt the error of our ways. The cheaper machine ended up costing us dearly, as we suffered all sorts of issues and downtime which held back our progress.
“It was during the first lockdown period in 2020 that it became clear the time was right to make the next major investment in the business. Throughout the COVID crisis we kept operating, but many of our suppliers didn’t, and this exposed weaknesses in our supply chain. “Hindsight is a wonderful thing, but we weren’t about to make the same mistake again. So when it came to investing in new machinery and software to take us to the next level, we turned to the major players. Yet again, Homag came out on top and so we decided to partner with them.”
Specifying the right equipment
“Before approaching Homag we analysed our production processes. We highlighted the machinery we felt we needed to create a workshop that would not only produce the right volume and quality for our customers, but also enable us to grow the business.
“Our plant wish-list included a beam saw with an automated panel lifter, an edge bander, a vertical CNC drill and a carcass press. Working closely with the Homag team we finalised our order for a Sawteq B-130 with panel lifter, an Edgeteq S-300, a Drillteq V-200 and a Cabteq S-250.
“It’s very disruptive, changing your whole 10,500 sq ft workshop with new equipment, but Homag’s installation organisation and planning was excellent. From the moment we placed the order for the kit, they kept us informed of the delivery time frame. True to their word, their engineers installed all the machinery at the end of September, and I must say, they did an amazing job.
“The engineers weren’t precious, they just cracked on with installing the new machines.
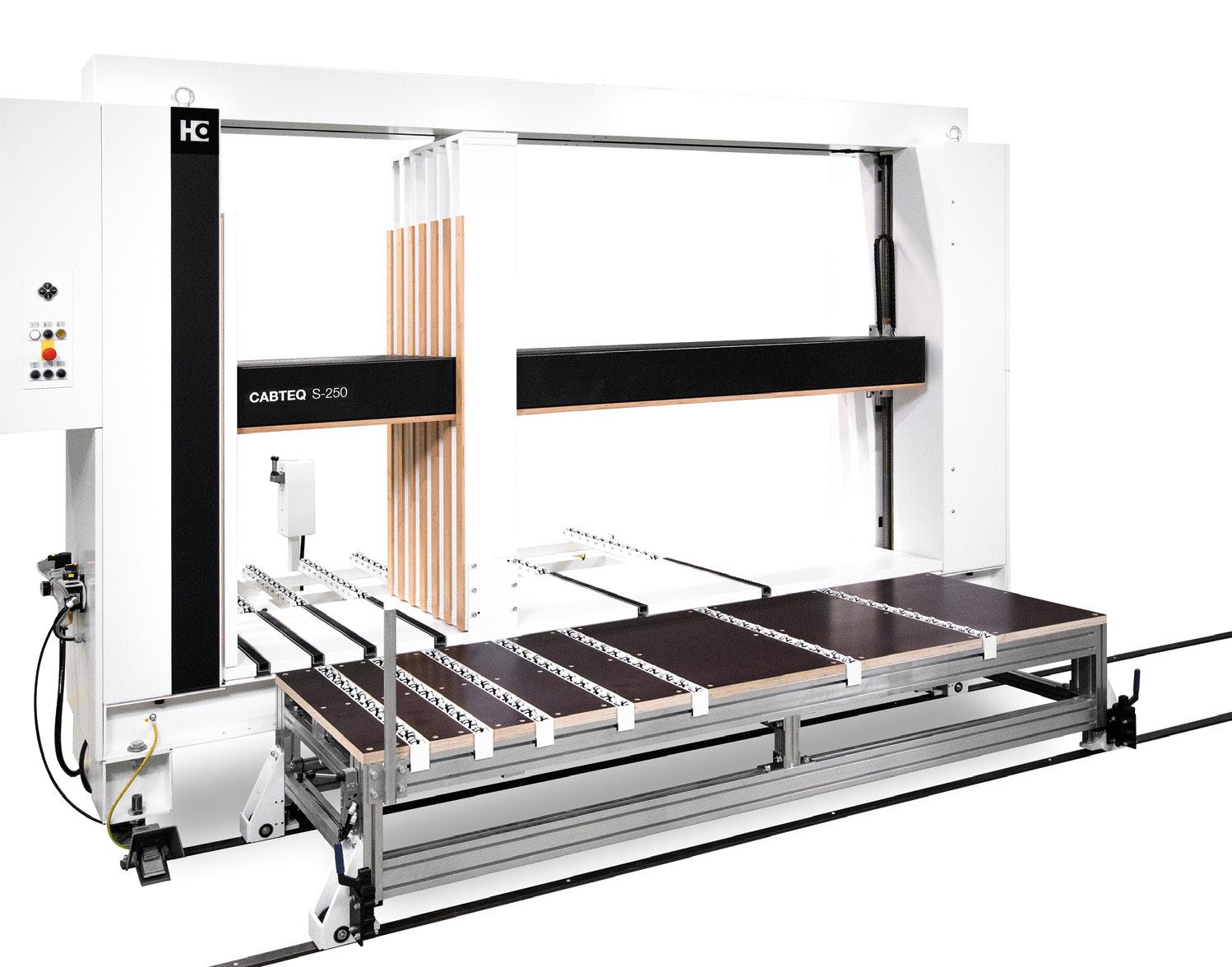
The Homag Sawteq B-130 beam saw
This enabled us to get on with our day-to-day production with minimal disruption; it really was a seamless process.
“Within a week all the machines were commissioned, and the engineers then trained our guys on site. This was supported by online training via Teams prior to the installation. Homag will also be providing refresher courses and advanced training online as and when we need it.”
Service and spares
“Aside from the quality and performance of the Homag machinery and easy to use woodWOP software, another deciding factor in partnering
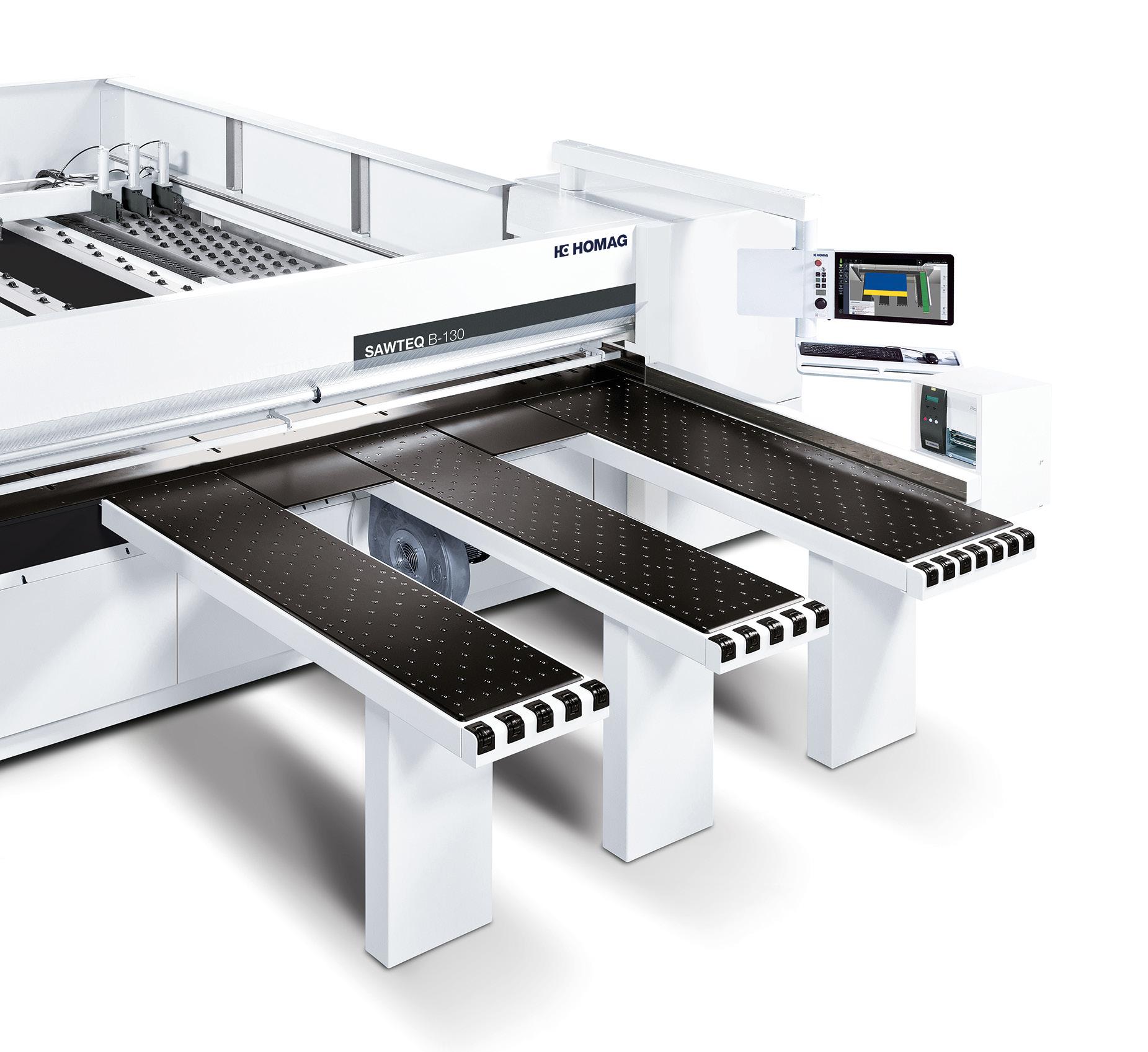
with them was the level of service and support they offer.
“Homag has its own team of engineers in the UK and consequently is able to provide an exceptional level of service. Not only that, but our research showed they also hold a comprehensive stock of spare parts. So, in the unusual event of a machine issue, they will be able to get us back up and running very quickly, and that is vitally important to us.
“Obviously, with five machines and software, this was a significant investment for a £5.5m business like ours, but again, Homag was able to help. They introduced us to Homag Finance, who made it very easy for us putting together an attractive investment package.”
The results speak for themselves
“The new equipment has revolutionised our production; we are seeing efficiency gains 30% higher than before, particularly with the automated Sawteq B-130 beam saw and the Edgeteq S-300 edge bander. For example, on the new edge bander, we can change between ‘When we invite potential customers to our facility the image the Homag equipment creates is hugely beneficial. It gives clients confidence that we can achieve the results they want and so it is definitely helping us to clinch contracts’
tape thicknesses, widths and diameter of radii without having to stop the machine; it’s all done at the touch of a button.
“There are hidden benefits too; when we invite potential customers to our facility the image the Homag equipment creates is hugely beneficial. It gives clients confidence that we can achieve the results they want and so it is definitely helping us to clinch contracts.
“Our employees too have gained in stature; they see they are in a truly professional environment and consequently have gained a deeper sense of pride in their work,” concludes Kevin Behan.
For a demonstration or more information on any of Homag’s machines or software, contact Adele Hunt at Homag UK on 01332 856424.
www.homag.com
The Homag Edgeteq-S-300 edge bander
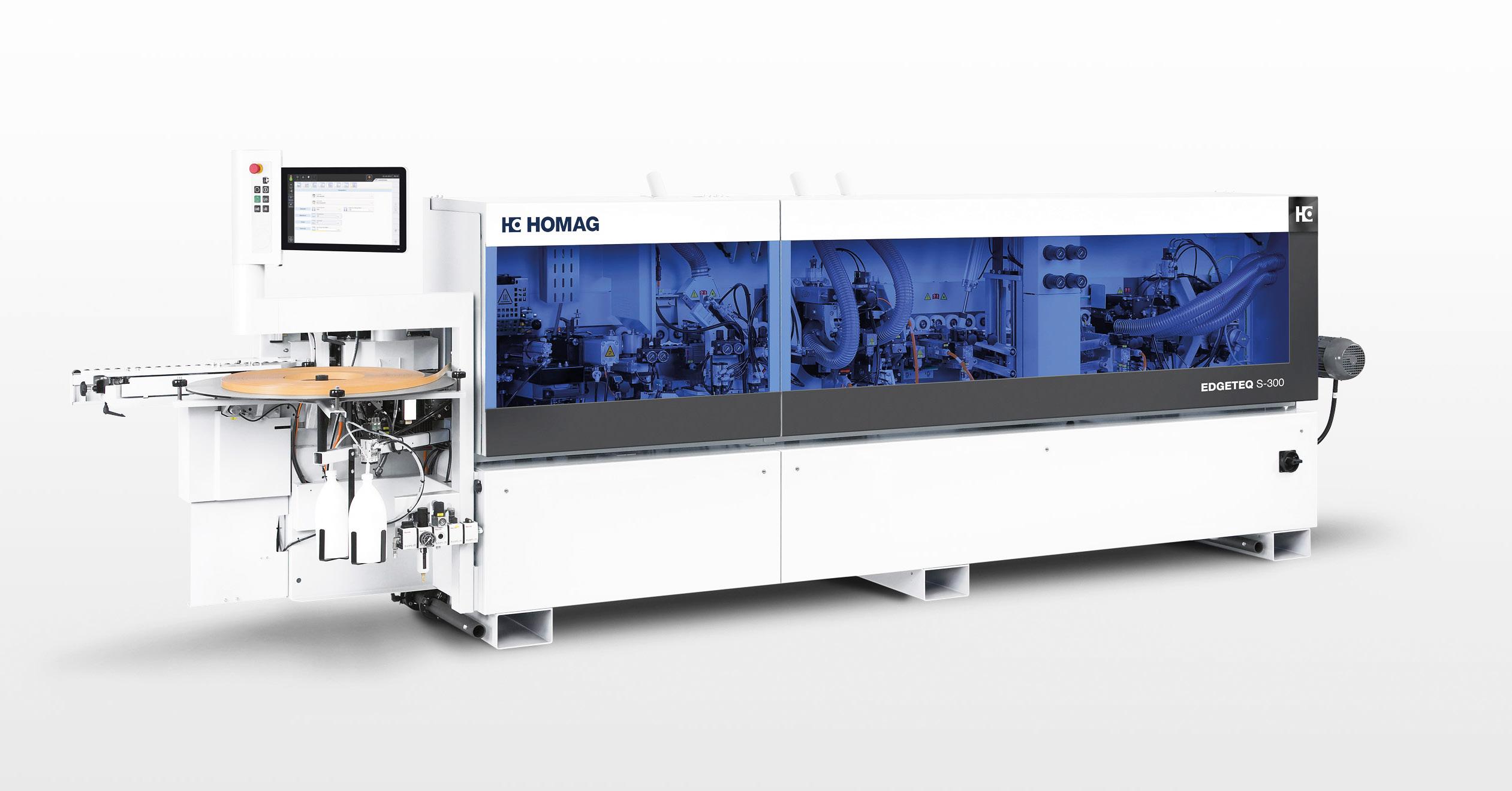
MB Maschenbau’s Fentech scores for Birmingham Veneers
Birmingham Veneers in Tyesley, Birmingham, has a reputation for high-class joinery and doors, working with some very esteemed clients and projects across the UK. Birmingham Veneers approached Dean Grimbley of John Penny Woodworking Machinery to find out more about its MB machine range and its unique features.
Birmingham Veneers has been supplying factoryfinished doorsets and bespoke joinery for years, and has tried several brush sanders in the past. Its experience of brush-sanding machines with smalldiameter heads was that the sanding paper life was poor, and it was difficult to achieve a quality finish on harder materials.
Following discussions with Dean Grimbley from John Penny Woodworking Machinery, the Roba Fentech fully-automated sanding machine – manufactured by MB Maschinenbau – was suggested as an ideal solution for Birmingham Veneers’ requirements.
The Roba Fentech carries large, 400mm-diameter oscillating sanding heads, putting more sanding paper in contact with the workpiece – and the oscillation of the sanding heads over the workpiece prevent wear in one area, thus ensuring the quality of the finish.
For Birmingham Veneers, the Fentech’s main unique feature was the way the machine could deal with small batches. The parts are laser-scanned on entry to the machine with the shape measured – the machine sets everything for the profile automatically from this data.
The machine sets almost instantaneously, with the parts being transported through the machine on a vacuum transport belt. The operator has the choice
A program-controlled swivel axis brings the top sanding unit in position
of working in one-man operation with components returned through the machine, or, for higher capacity, an operator can stack at the outfeed of the machine.
This was enough of an incentive for Birmingham Veneers to conduct sanding trails and visit MB Maschinenbau at its headquarters in Herford, Germany, for a demonstration – and, shortly after that convincing visit, an order was placed.
Birmingham Veneers has now had the MB Fentech
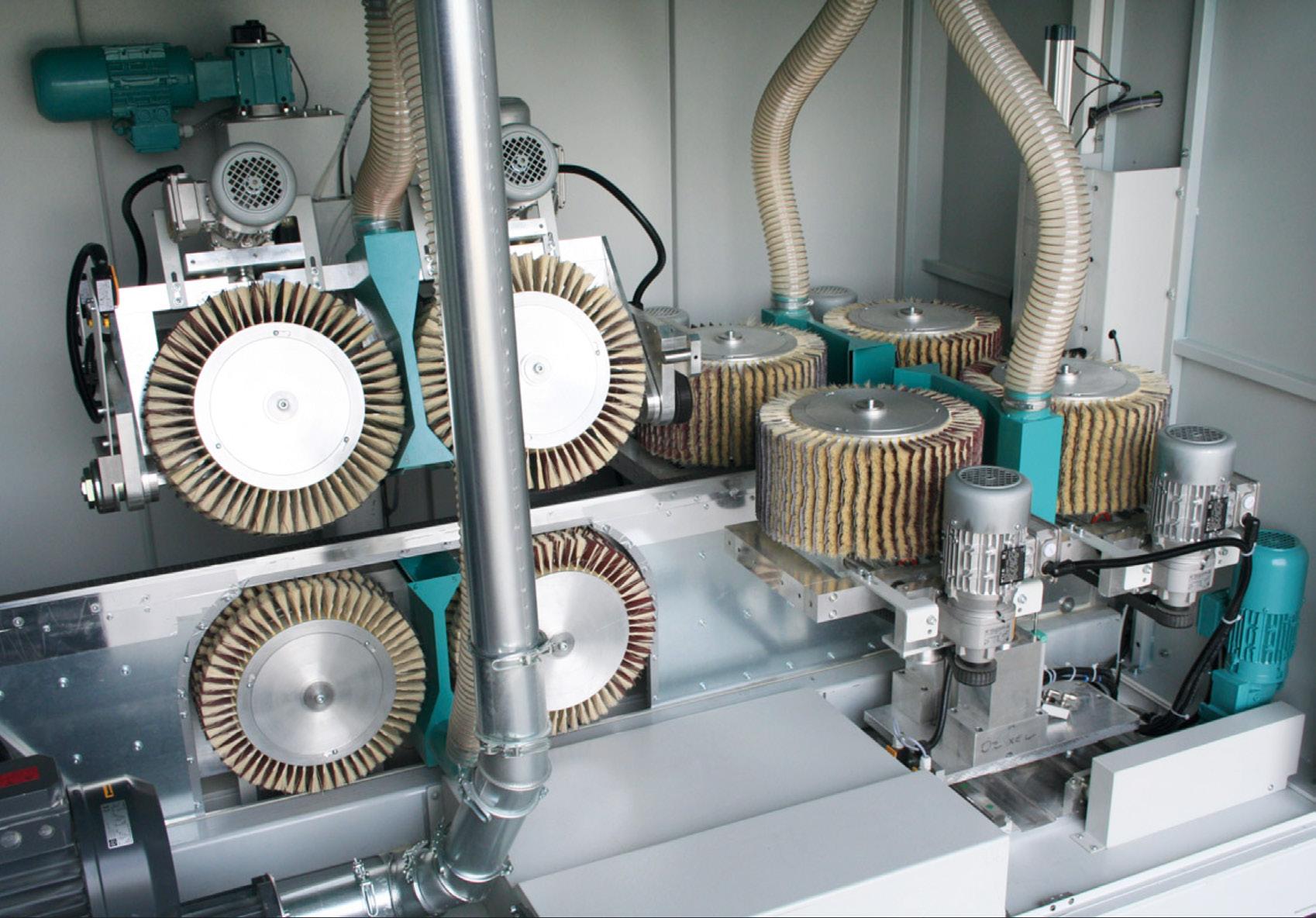
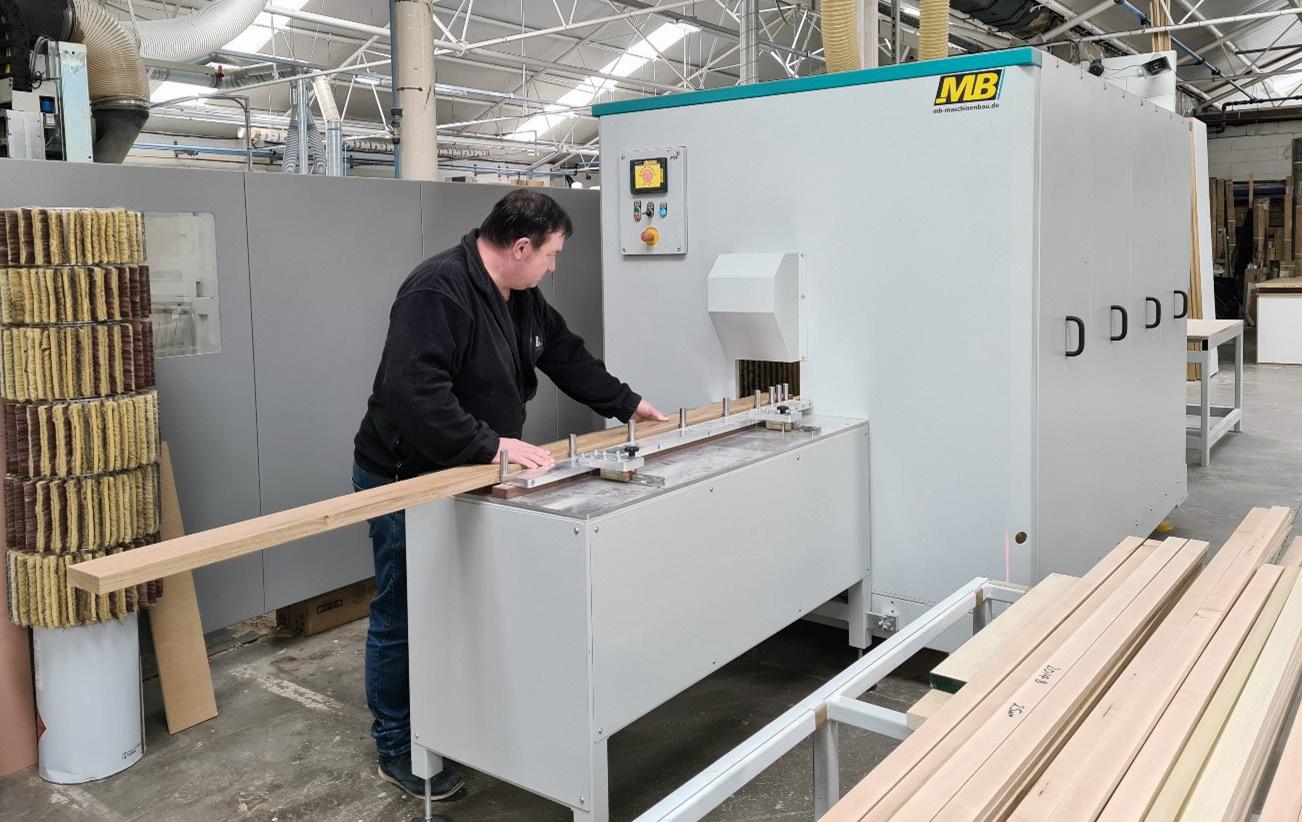
RIGHT Typically, high-quality sanding is required for Birmingham Veneers’ demanding clientele
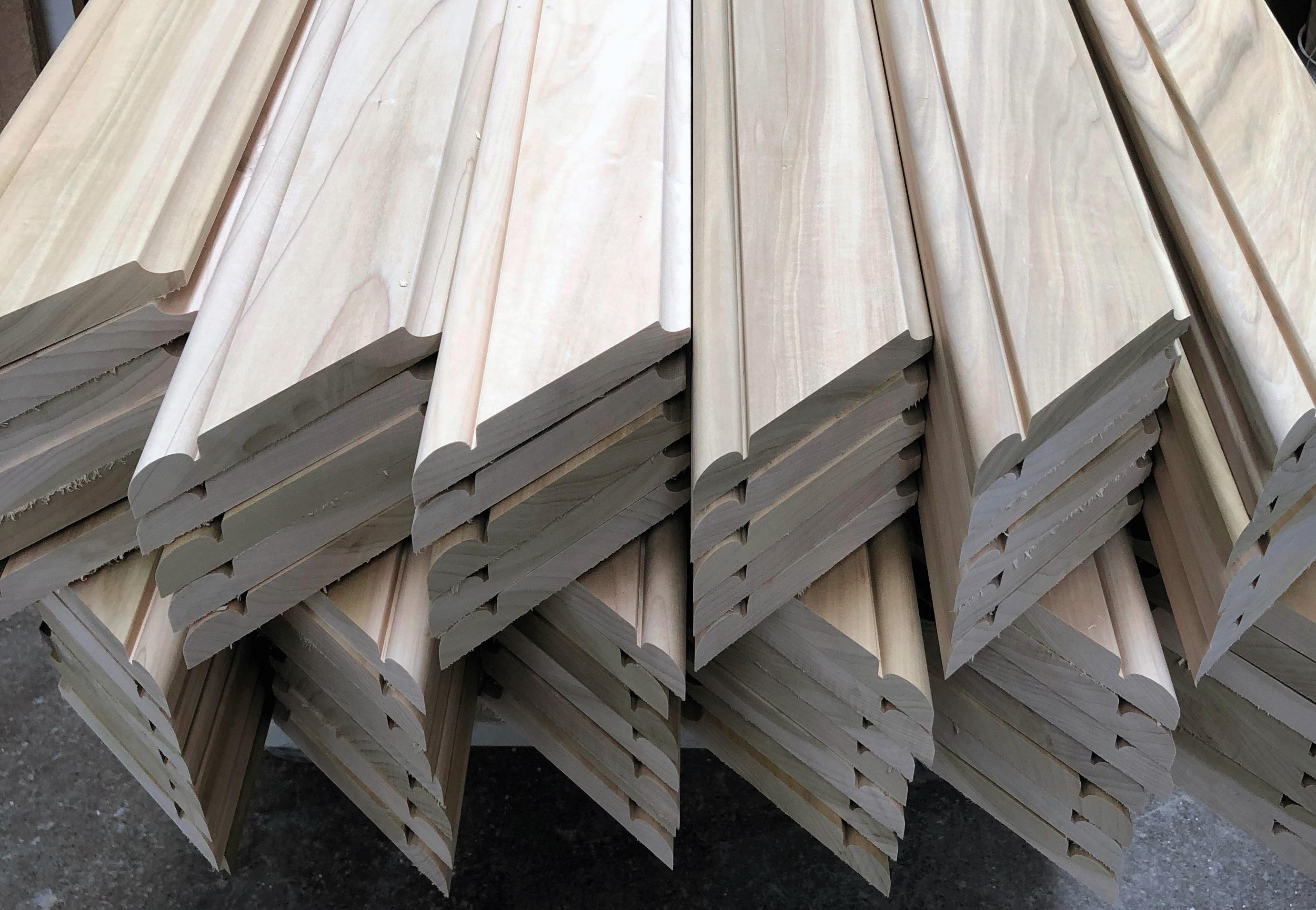
LEFT MB Maschinenbau’s Roba Fentech automated sanding machine, installed at Birmingham Veneers
BELOW Time-consuming setting is not required on the Fentech – instead, automatic part recognition at the inlet of the machine, and the subsequent motorised adjustment of all sanding units, take care of this
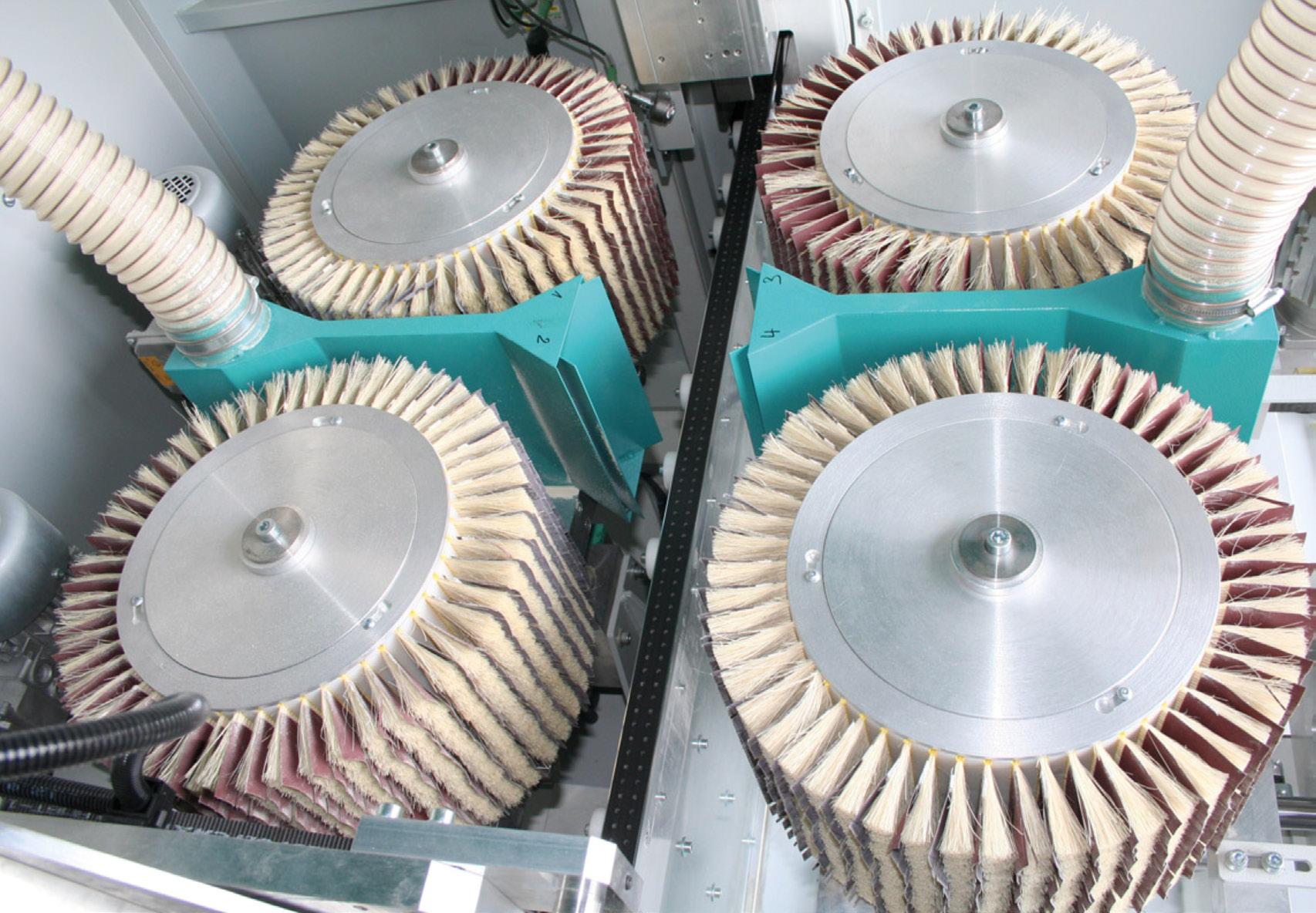
in production in Birmingham throughout the Covid-19 year. “The machine has performed to our expectation,” remarks production manager James Ferguson, “and has helped to complete some notable installations in London to a high and consistent quality very efficiently.”
From John Penny Woodworking Machinery’s Midland office, Dean Grimbley says: “For those interested in brush-sanding machines for flat surfaces and mouldings, call John Penny Woodworking Machinery
A large brush diameter optimises the surface quality – while a vacuum transport system also enables short part
and make your first step towards sanding perfection. Also, if you require high-quality joinery, call Birmingham Veneers for advice, quotation requests, or just to find out more about their services.”
For further details, contact Dean directly on 07973 851454.
www.john-penny.co.uk www.mb-maschinenbau.de www.birminghamveneers.co.uk
Kündig – the sanding Master
Established in 1945, Kündig is widely recognised as one of the most experienced and highestquality manufacturers of wide-belt and edge-sanding machinery. Kündig has two manufacturing plants: one in Switzerland, which is also its headquarters and where the R&D and special projects are developed; the other in Gotha, Germany, where the production of the standard wide-belt and edgesanding machinery takes place.
In today’s market, where manufacturers are facing all sorts of different challenges in generating the right surface finish, Kündig has the experience to respond, and to offer a solution to what is seen by many as near impossible.
Where first impressions count, manufacturers strive to achieve that ‘something special’ when it comes to surface finishing, and this is exactly why some of the world’s leading manufacturers of grand pianos have researched the market and commissioned Kündig to produce sanding machines to generate a perfectly flat surface and give intermediary sanding, building up to a high-gloss finish where any imperfection would stand out and not be accepted.
Continued over Kündig Technic
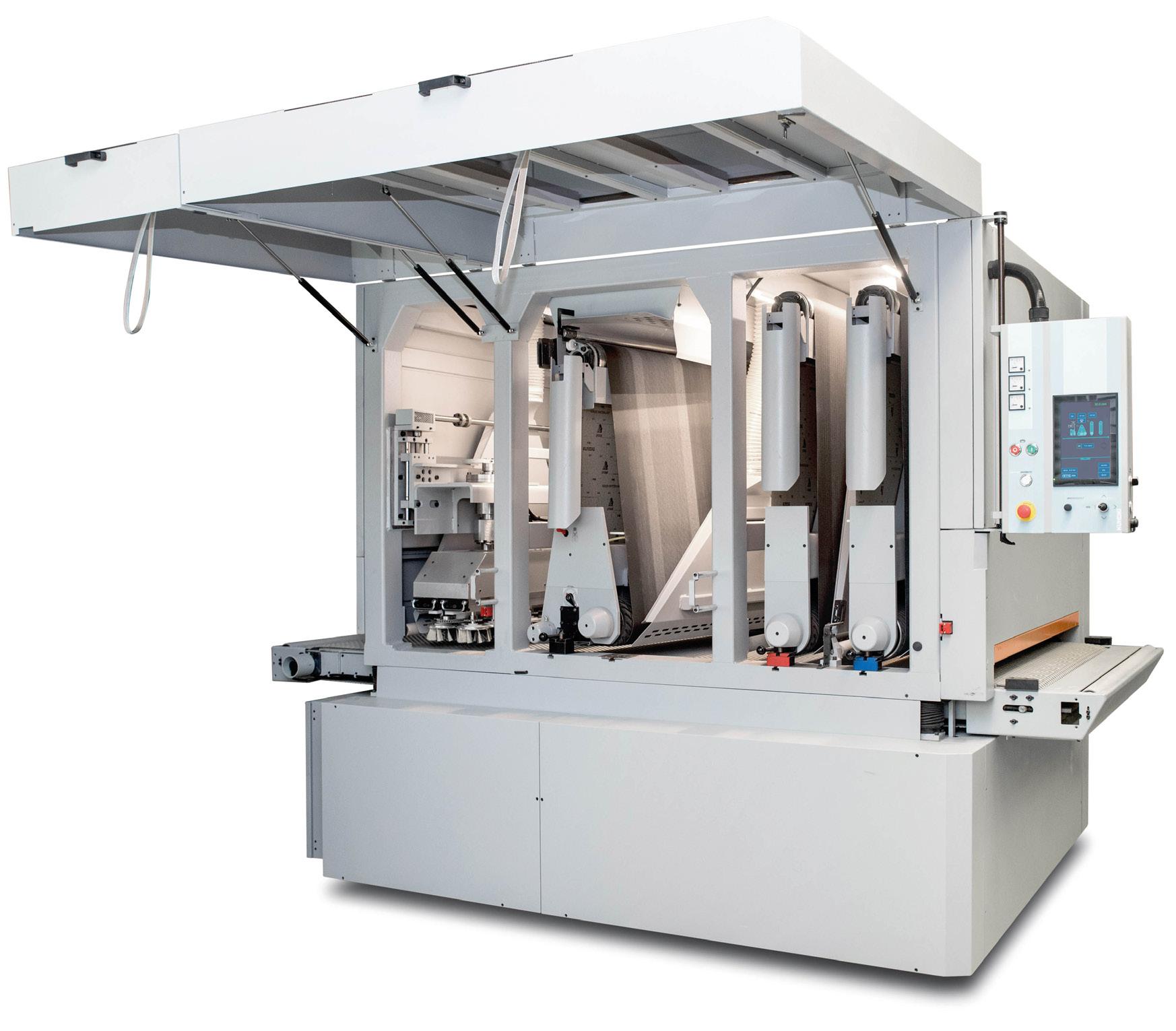
Below: Kündig Uniq Flash, front and rear
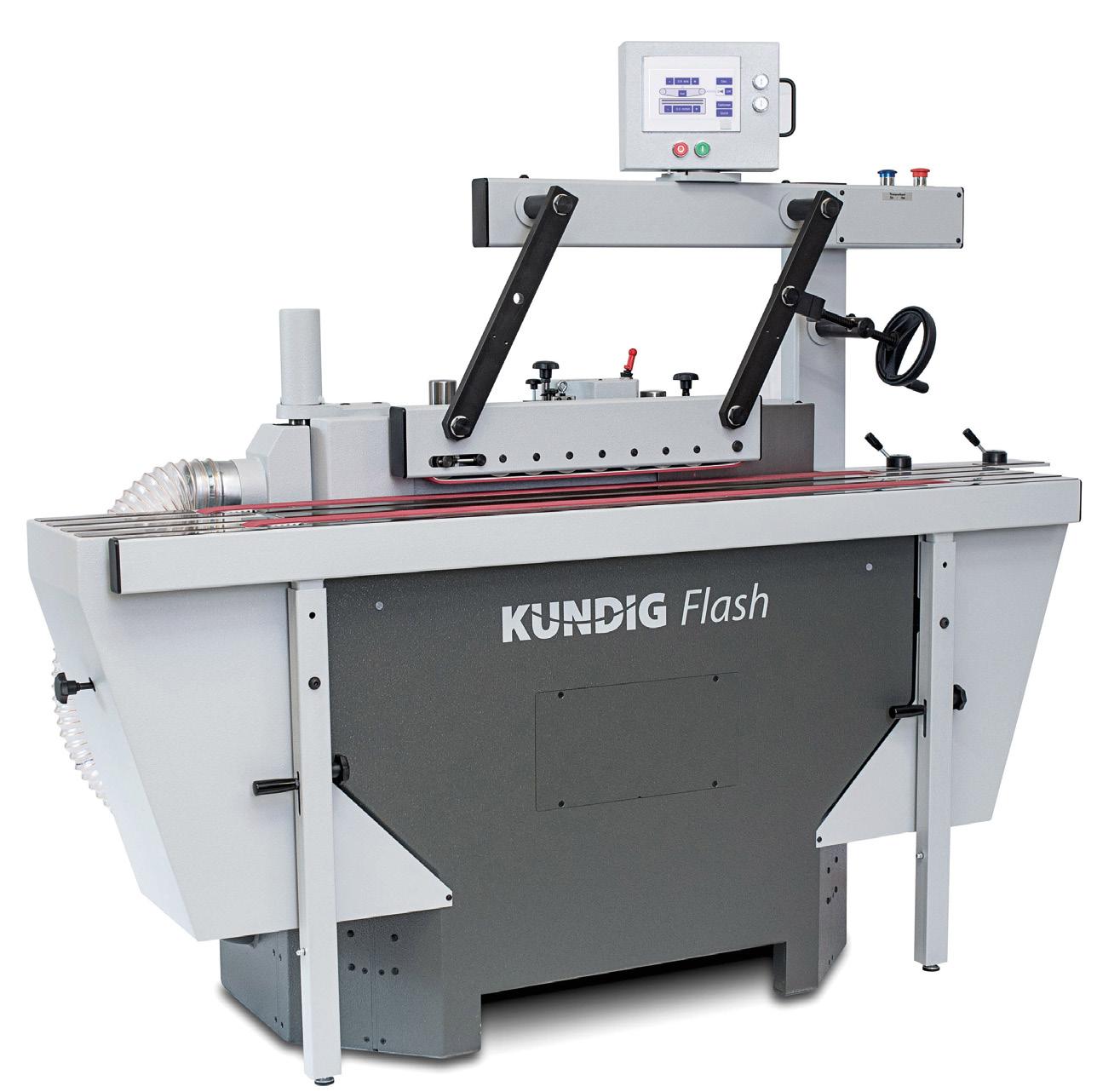
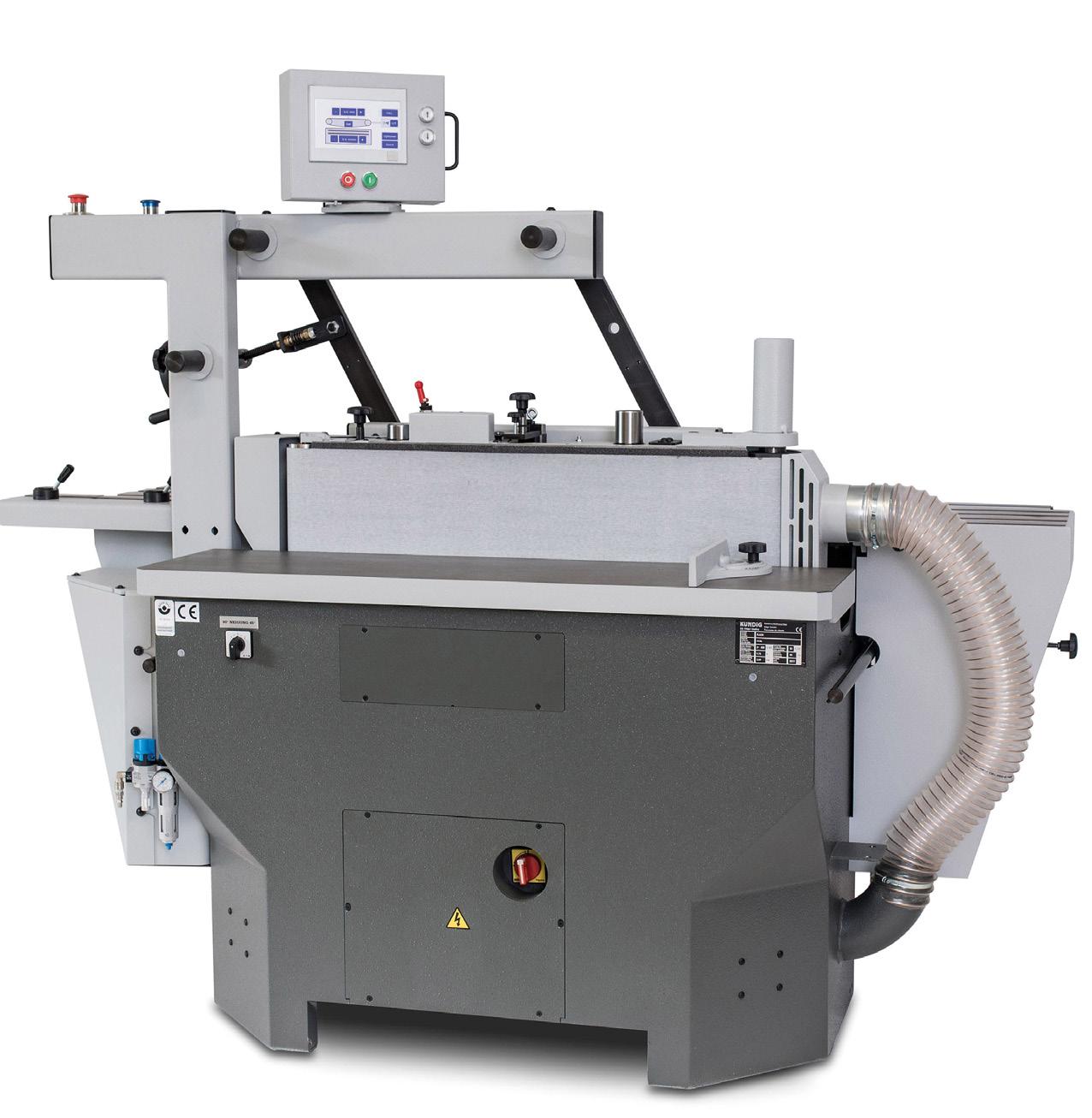
Kündig’s impressive Master – working width of 1350 mm and is equipped with a calibration roller as well as a fine sanding pad unit and features the proven, robust construction that guarantees decades of high sanding precisio
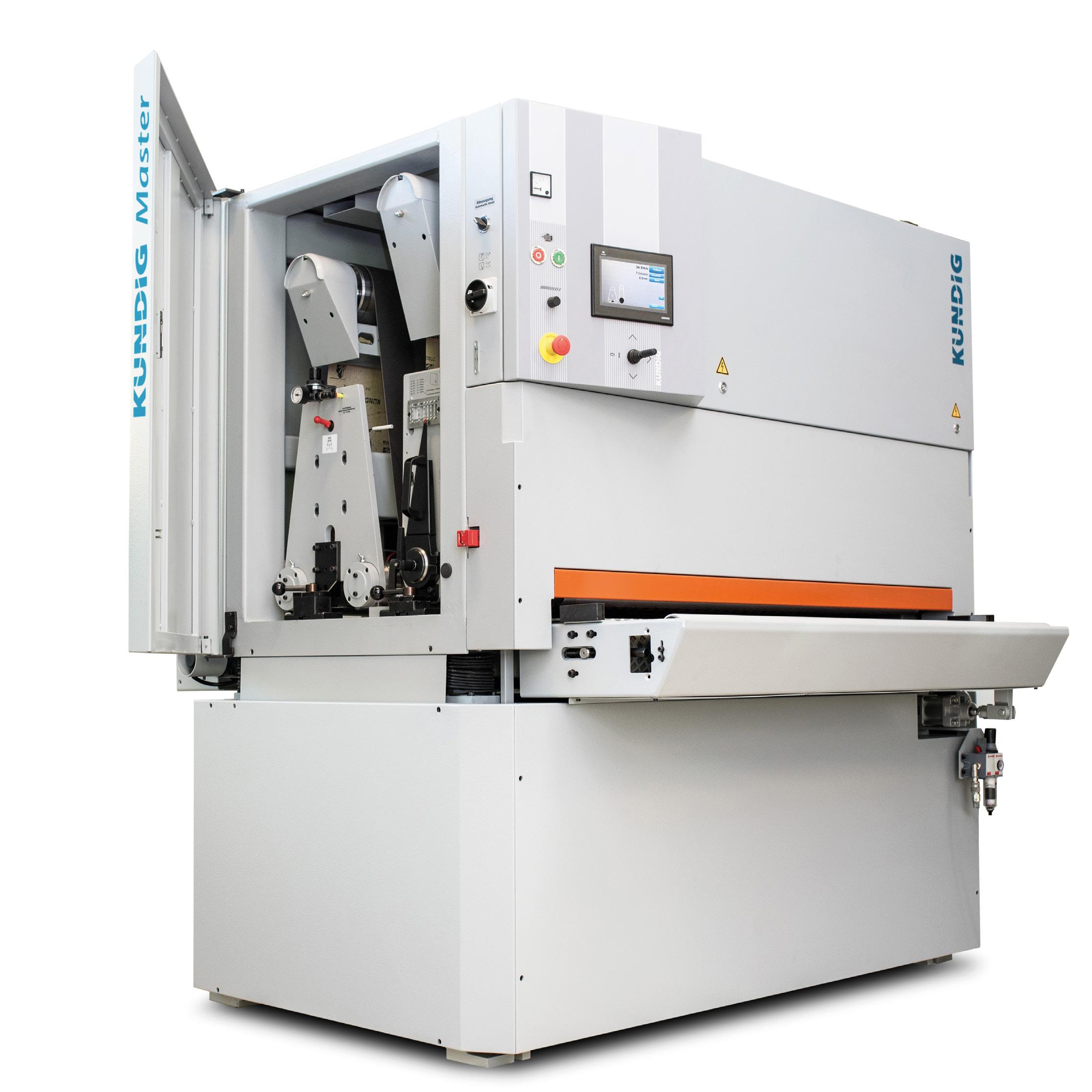
Other companies which have faced challenges have needed sanding accuracy to +/- 0.02mm, and turned to Kündig to meet the tight tolerances for final product. These machines are typically used in the automotive industry, but have also been installed for manufacturers looking to calibrate brake discs for commercial aircraft, insulation materials, plastics, etc.
Of course, the more familiar application for Kündig is in the woodworking industry, where its fixed-bed design has proven to give longterm accuracy – being fixed to the machine frame, with a sanding group that raises and lowers. This system has proven to be especially beneficial for calibrating heavy components – typically fire doors, where the fixed bed cannot move despite the weight of the door or the amount of pressure generated during sanding.
This fixed-bed system is also a huge benefit for veneer sanding, where veneer-cutting technology has increased, making the thickness of veneers smaller and smaller, hence making sanding accuracy more important than ever.
To cater for a wider part of the market, Kündig recently celebrated its 75th anniversary with the introduction of the new Kündig Master, which offers an ‘out-of-the-box’ solution. The idea behind it was to produce a more cost-effective machine while still keeping to all the traditional values associated with Kündig.
The machine is produced in the same factory as the Premium, Brilliant and Perfect models, but is manufactured to a standard configuration to allow serial production, hence reducing the costs to produce. The Master has a generous 1350mm working width, two sanding heads – first a contact roller, followed by a finishing pad, which is available for solid wood or as a segmented pad for sanding veneers.
The Brilliant series of machines is aimed at those looking to achieve the highest possible quality of surface finish. By simply placing the abrasive at a 10° angle eradicates the wavy scratch pattern inherently shown on traditionalstyle sanding machines. These machines are available in widths of 1100, 1350 and 1600mm as standard, and as either single- or multi-head machines.
In recent times, Kündig has seen a substantial increase in the demand for purpose-made machines throughout different industries. Typical of this is a recent delivery to a company which wanted a machine to calibrate five-piece doors ready to go straight to spraying, to then denib and also have the possibility of creating a rustic-style surface with a bandsaw finish.
The answer was a four-head sanding machine, having contact roller, oblique sanding pad and cross belt to sand the rails – or alternatively using a 16-grit belt to create the rustic surface, followed by a carousel brush unit to sand into the profiles and soften the edges.
Despite the situation last year, Kündig has seen growth in sales, both in the UK and in other markets, and, in other news, will be shortly relocating to offer better demonstration facilities … more to follow.
0845 833 0565 www.kündig.com
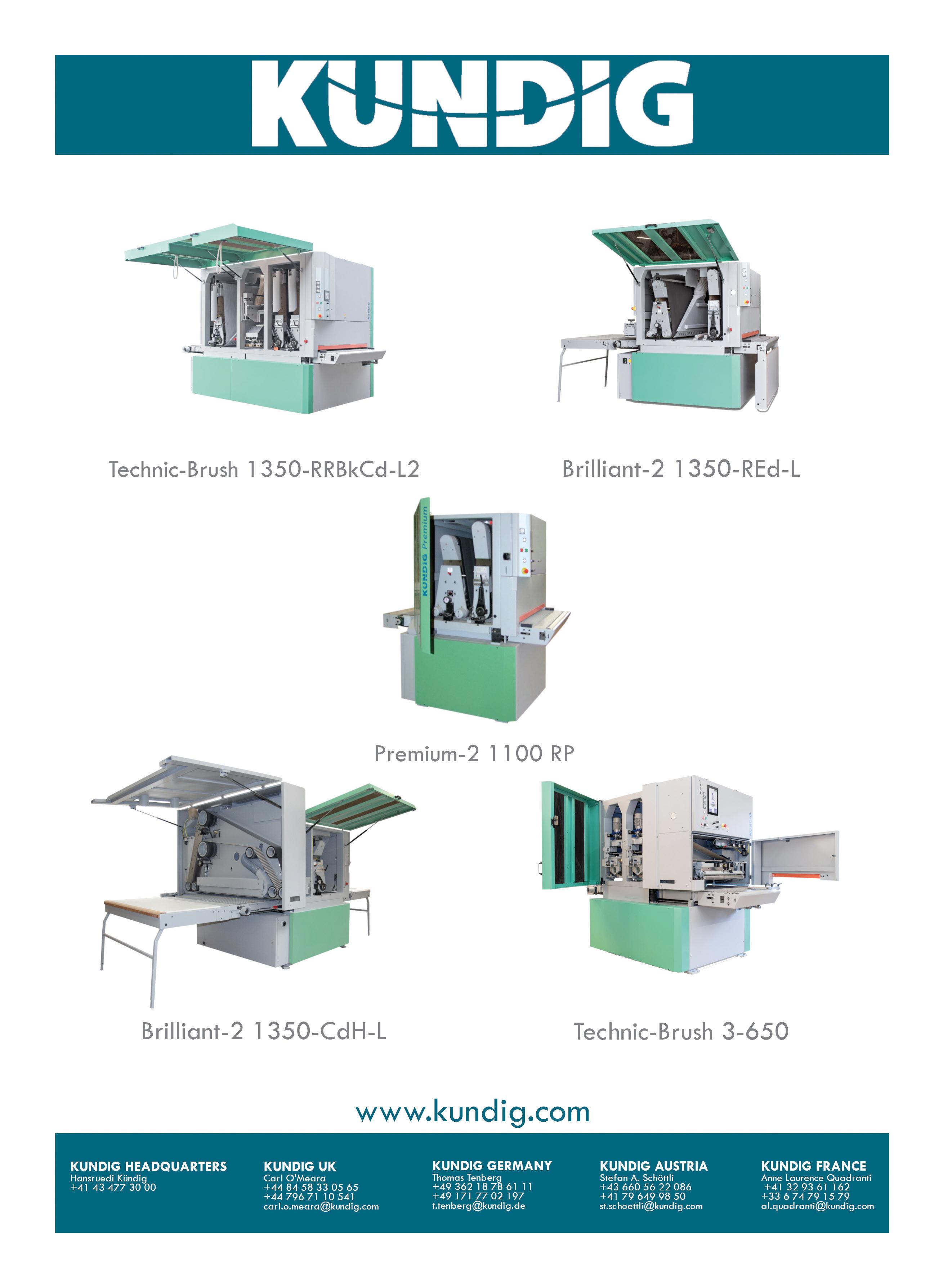
British-made woodworking abrasives – next day from stock and custom belts within 2-4 days
Bibielle UK Ltd was set up over twenty years ago to supply high quality abrasive solutions to a range of industries, including the furniture, joinery and panel production sectors. The company has built a long-standing industrial client base with its three respected brands: Bibielle, Nastroflex and ProGrind across the metal- and wood-working industries.
Based centrally in Wigston, Leciestershire, Bibielle UK boasts an enviable track record supplying the metal-working sector, and following the acquisition of the respected Sheffield-based Abacon Abrasives business some ten years ago, Bibielle UK has been successfully growing its woodworking customer base.
As the exclusive UK distributor for leading brands Bibielle Spa, Nastroflex and ProGrind, Bibielle UK has a substantial stocked product range in addition to its dedicated UK-based manufacturing capability – a rare asset in the UK.
As a proud family-owned business, Bibielle UK is has a comprehensive range of abrasive products for surface preparation, blending and finishing. From narrow and wide belts, discs, blocks, non-wovens, sheets and triangles – and a custom-made belt scenario – Bibielle UK has all the key bases covered and can supply stock items within 24hrs. Bibielle UK will manufacture belts to order from two to four days with the company responding to quotes within the hour.
When it comes of belts, its custom bespoke belt products – wide-belts for roller or pad sanders, narrow-belts for automatic or manual pad sanders, narrow belts for contact wheel or slack belt, and short belts for portable sanders are available with either paper or cloth, or combined paper-cloth. Sizes range from 4mm to 3200mm wide and up to 1700mm long, so the woodworking sector is optimally catered for in calibrating, denibbing and finishing applications.
As a manufacturer, with the COVID-19 pandemic situation in a constant state of flux creating a challenging situation for many suppliers and importers, Bibielle UK is local – it is a reliable and highly capable British abrasive manufacturer which is able to keep UK furniture and joinery manufacturers supplied with its abrasive solutions on short turnaround times. With service uppermost in Bibelle’s thinking, enquiries and orders for its bespoke belts are responded to within the hour and deliveries are typically executed within 2-4 days.
Being Wigston based, Bibielle is ideally located and can readily cover the heart of the UK furniture and joinery trade with many manufacturers within and hour or two. The company also boasts a very efficient distribution model for next day postal deliveries – for orders made before 4pm, or 3pm Fridays, Bibielle UK will despatch goods the same day. Using its distribution network, Bibielle UK also provides a full on-site service to help reduce process times for customers by increasing their productivity.
Being itself a family business, the company is also acutely aware of the current situation regarding the COVID-19 virus situation. Bibielle UK sales director, Tom Wright, explains: “I’m sure you don’t need me to tell you of the challenging situation our country – and the world at large – is currently facing. However, as a family-owned independent business, and being able to react positively in difficult times, I think it is important to spread news that not all is bad and that we are ensuring we continue to support and supply the UK like we have done for the past 20 years.
“With this in mind, we have significantly invested financially in raw material and finish stock of our abrasive products,” says Tom. “This has taken our normal 3-4 month stock-holding to around 6-7 months, which in turn will ensure that our customers’ businesses can continue to run like normal, despite the current problems we are all facing.
“Our passion has always been about providing a great service along with a great performing product. However, this has no meaning if the health of the Bibielle UK team is suffering. We have also implemented extensive bacteriafighting agents throughout the company and are carrying-out regular checks on staff to ensure this is being carried out.
“I will leave you with a final message that should you have problems with stock, please get in touch and we will try our utmost to help. This is a difficult time for us all, let alone the additional pressures of trying to keep your business running and customers happy. I sincerely hope that with the plans we have carried out, we can be a valued supplier to your operation not only today, but in the very distant future.”
0116 258 1900 sales@bibielle.co.uk www.bibielle.co.uk
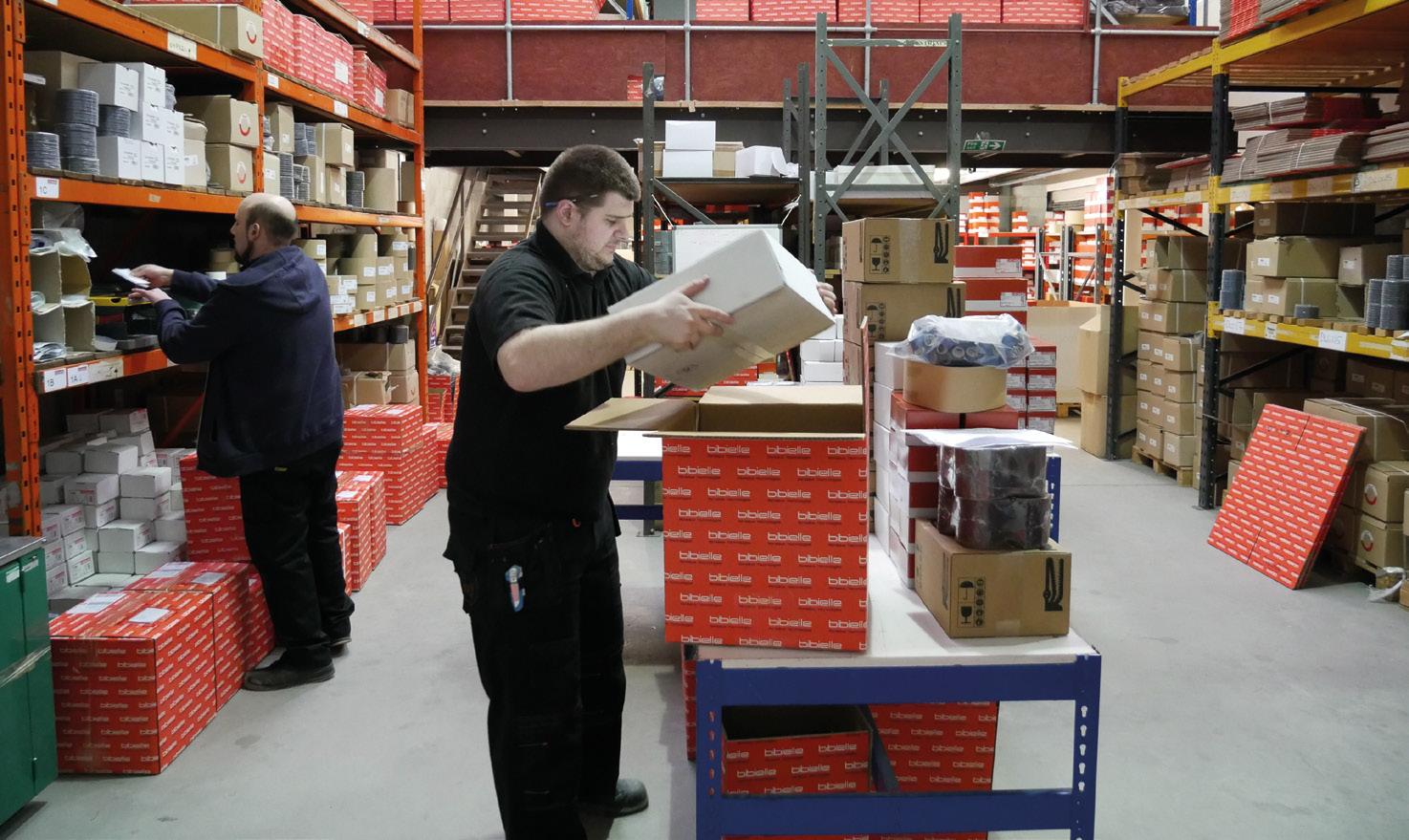
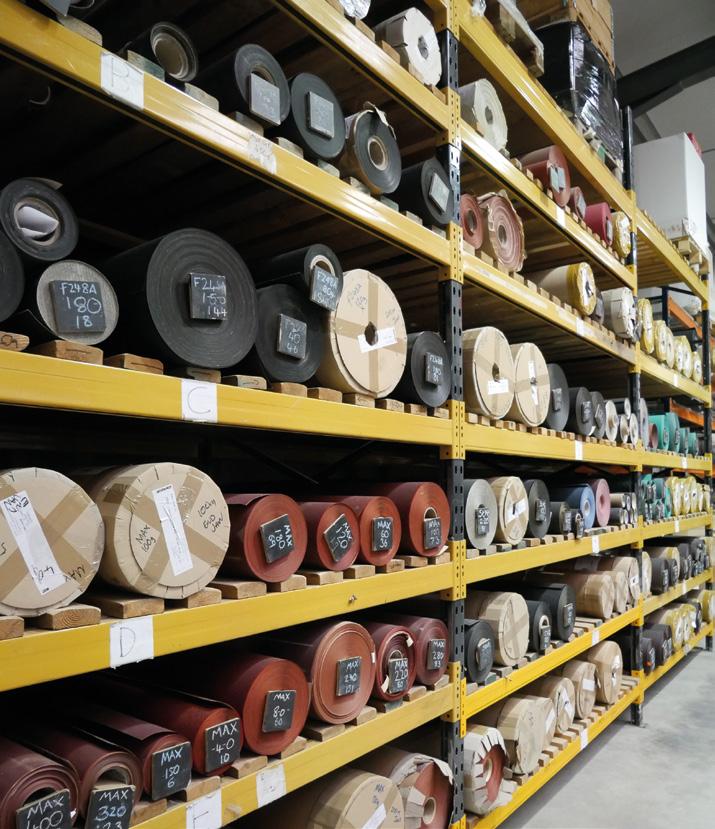