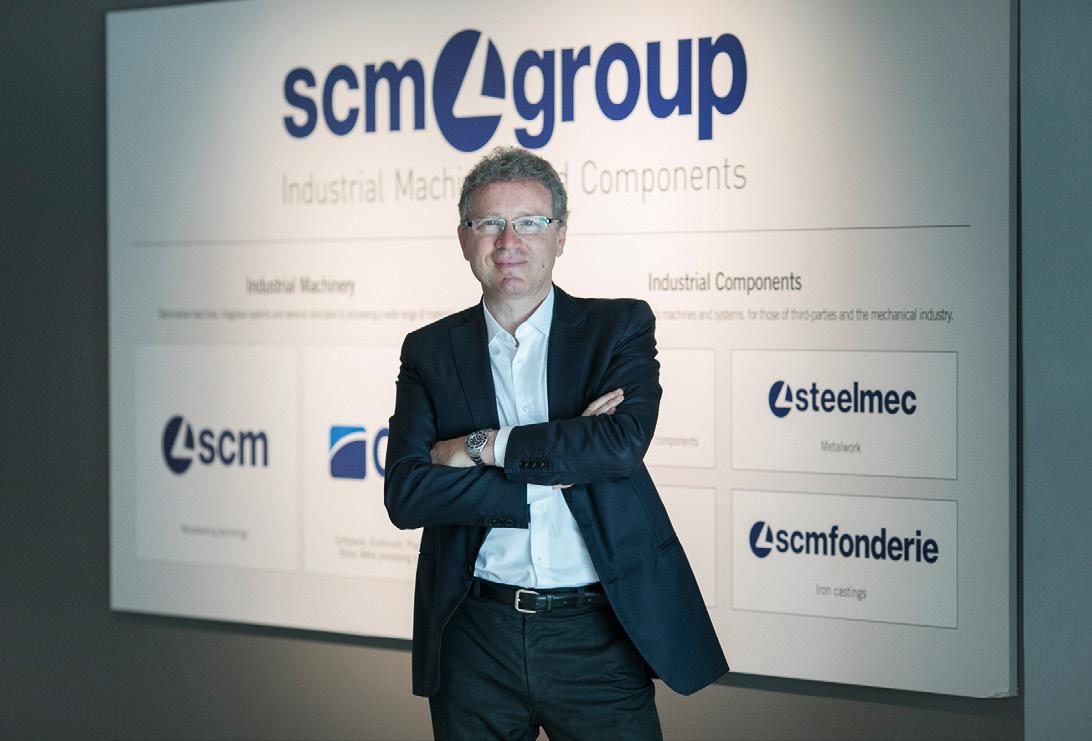
19 minute read
News
New board of directors at SCM Group
Marco Mancini has been appointed CEO and representative of the next generation are introduced, together with professional figures, to consolidate the Group’s governance.
Direct from Rimini, on the 17th March 2021 – a new board of directors has been confirmed at SCM Group SpA, a global leader group in technologies for furniture, construction and the processing of a wide range of materials and industrial components. On the 12th March, the shareholders’ appointed the new board of directors with Giovanni Gemmani (President), Marco Mancini (CEO), Andrea Aureli, Enrico Aureli, Valentina Aureli, Linda Gemmani, Martino Gemmani, Luca Franceschini and Filippo Corsini (board members).
The shareholders also reconfirmed Adriano Aureli’s appointment as Honorary President. Marco Mancini, who has been with SCM Group since 2015 and currently general manager, as
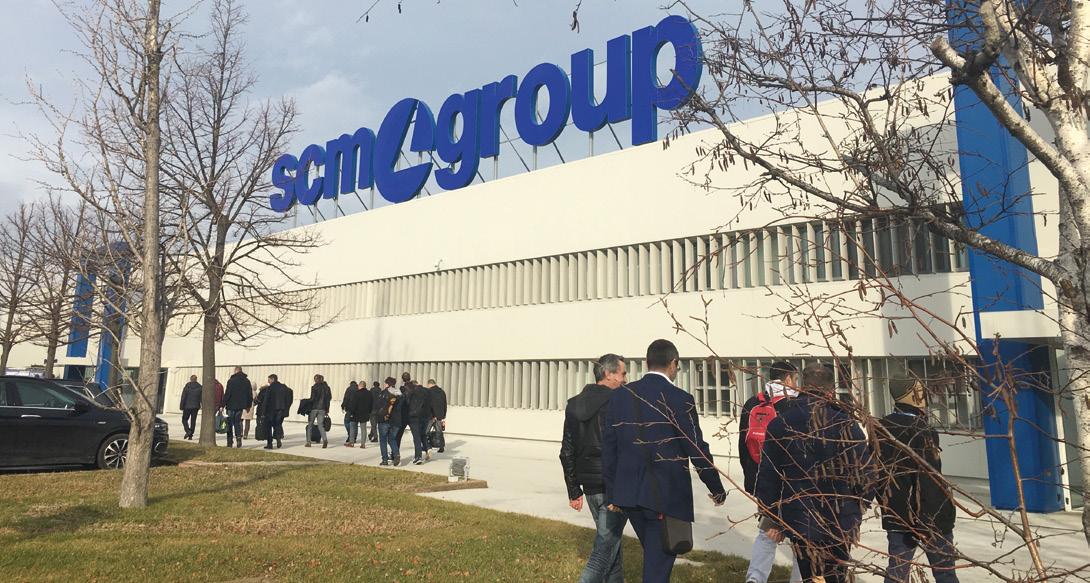
Marco Mancini CEO SCM Group
of 17th March, has taken up the position of CEO for SCM Group.
Shareholders thanked Alfredo Aureli for his significant contribution to the growth of the Group and the strong values he has imparted to all those who have worked with him.
The shareholders also welcomed the new board members who have joined the Group: Martino Gemmani and Luca Franceschini, fourth generation representatives of the two families at the head of the Group, and Filippo Corsini.
SCM Group coordinates, supports and develops a system of industrial excellence in three large highly specialised production centres in Italy, with a turnover of €700m, with around 4000 employees and a direct presence in all five continents.
www.scmgroup.com
New MD at Fein
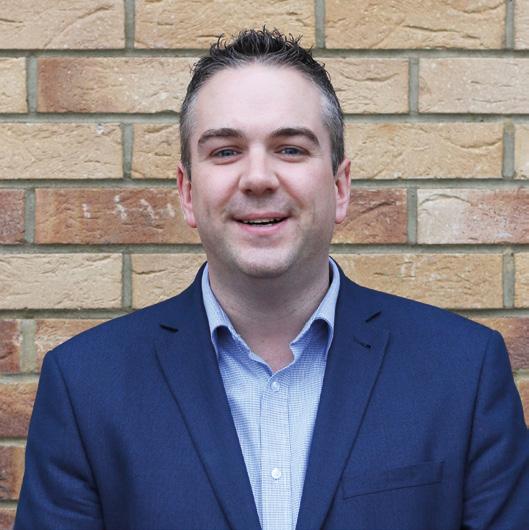
Power tools and accessories manufacturer, Fein, has promoted former national sales manager, Andy Mills, to UK managing director, with former UK MD Raphael Rudolph moving into the role of chief sales officer for the group.
Andy, who began his Fein career as an area sales manager in 2010 before becoming national sales manager in 2014, has ambitious plans for the next 12 months and beyond, with his primary focus firmly on driving forward the manufacturer’s solutions-focused strategy.
www.fein.com/en_uk/
British Woodworking Federation to leave CTI and go its own way
The British Woodworking Federation (BWF) has today announced that it will start the process to withdraw its membership of the Confederation of Timber Industries (CTI).
The Confederation of Timber Industries was established in 2015 by the Timber Trade Federation (TTF) and the British Woodworking Federation (BWF). It is an umbrella organisation representing the timber supply chain. Following its inception, the membership has increased to include the Structural Timber Association (STA), Wood Protection Association and the Trussed Rafter Association (TRA).
In recent years, the CTI has focused on increasing the profile of the timber sector as a solution to help solve the UK’s housing and climate crises, with a heavy lean towards structural timber solutions. While the BWF has fully supported the work of the CTI and will continue to do so, the BWF Board and Council now wish for the BWF to step away from the CTI as a member, to focus on the primary objectives of the woodworking, joinery and manufacturing sector.
Helen Hewitt, CEO of the British Woodworking Federation said: “There are many challenges and opportunities for the woodworking, and joinery industry as we ease towards the Road Map to Recovery. We have seen the direction of the CTI change in the last few years and noticed there is a much heavier focus on structural timber solutions rather than the full timber supply chain and its products which has driven the decision to start the process to leave the CTI as a member association. We are fully confident that through our own PR strategy, intensive lobbying activities and our continued memberships of Trade Associations such as the Construction Products Association (CPA) and Build UK, we can continue to represent our members in the construction sector and with Government. She added: “We would like to thank Roy Wakeman the Chairman of the CTI and the CTI Board for their support and dedication over the last few years and shall look forward to continuing to work with our fellow Trade Associations to increase the use of timber as a preferred material of choice.”
www.bwf.org.uk
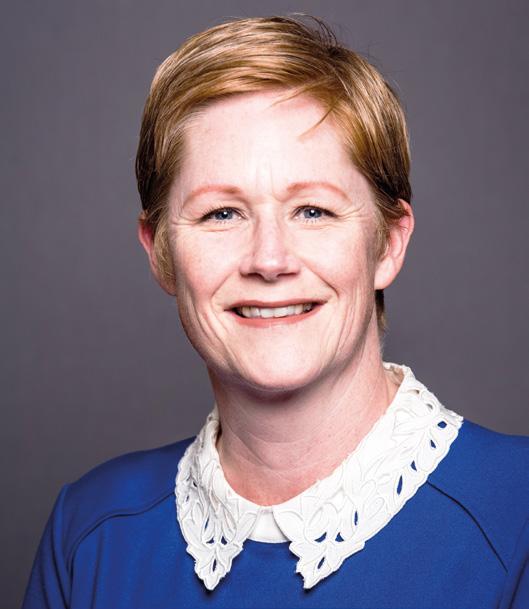
Softwood spearheads timber import resurgence in 2020
Softwood import volumes for 2020 saw a +3% rise against 2019’s totals, after falling -24% in Q1/Q2 of 2020, to reach 6,580,000m³, reports the Timber Trade Federation.
The cumulative volume for softwood in 2020 was up by 200,000m³, from 6.3 million m³ in 2019, following a surge in timber imports in Q3/Q4 2020 – primarily from Sweden, Germany, Latvia and Russia. Provisional full-year data for 2020 reveals total timber and panel import volumes between Q1/Q2 2020 were -26% below the same period in 2019. By the year’s end, improved second-half volumes had cut the deficit over 2019 to just under -3%.
Q4 helped lead the recovery, as volumes for all products were nearly +39% higher than over the same period in 2019.
A total of 4.9 million m³ was imported between August and December 2020, with the nextlargest volume over this period being back in 2006, when volumes reached 4.8million m³. David Hopkins, CEO of the Timber Trade Federation, says: “After the first lockdown in March last year, the timber industry, just like the rest of the UK economy, came to a near standstill, and the volume of timber being imported fell sharply. “Meanwhile, demand increased dramatically, both in commercial construction – which has managed to carry on during the pandemic – and domestic projects, as so many people were forced to spend more time at home, and spent their disposable income on refurbishment rather than holidays or other bigger-ticket items. It has led to timber becoming one of the most sought-after commodities in the UK! “The higher levels of import should help ease some of the pressure we have seen between supply and demand, though we do expect the tight conditions to continue well into 2021.”
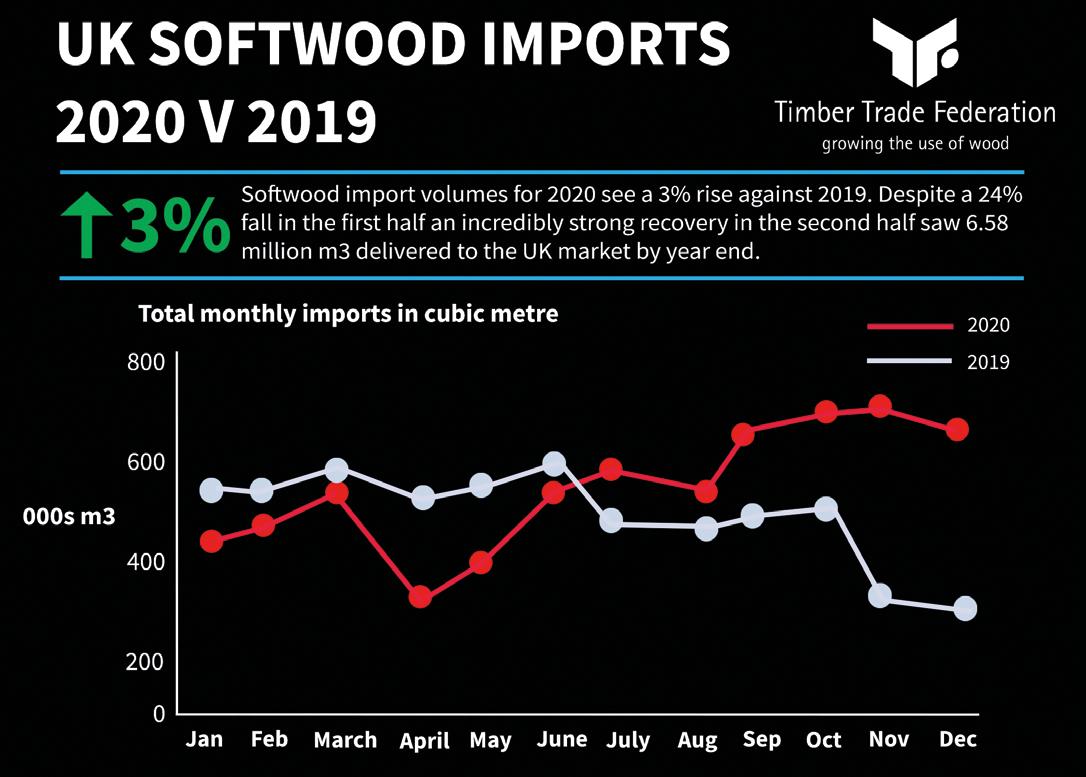
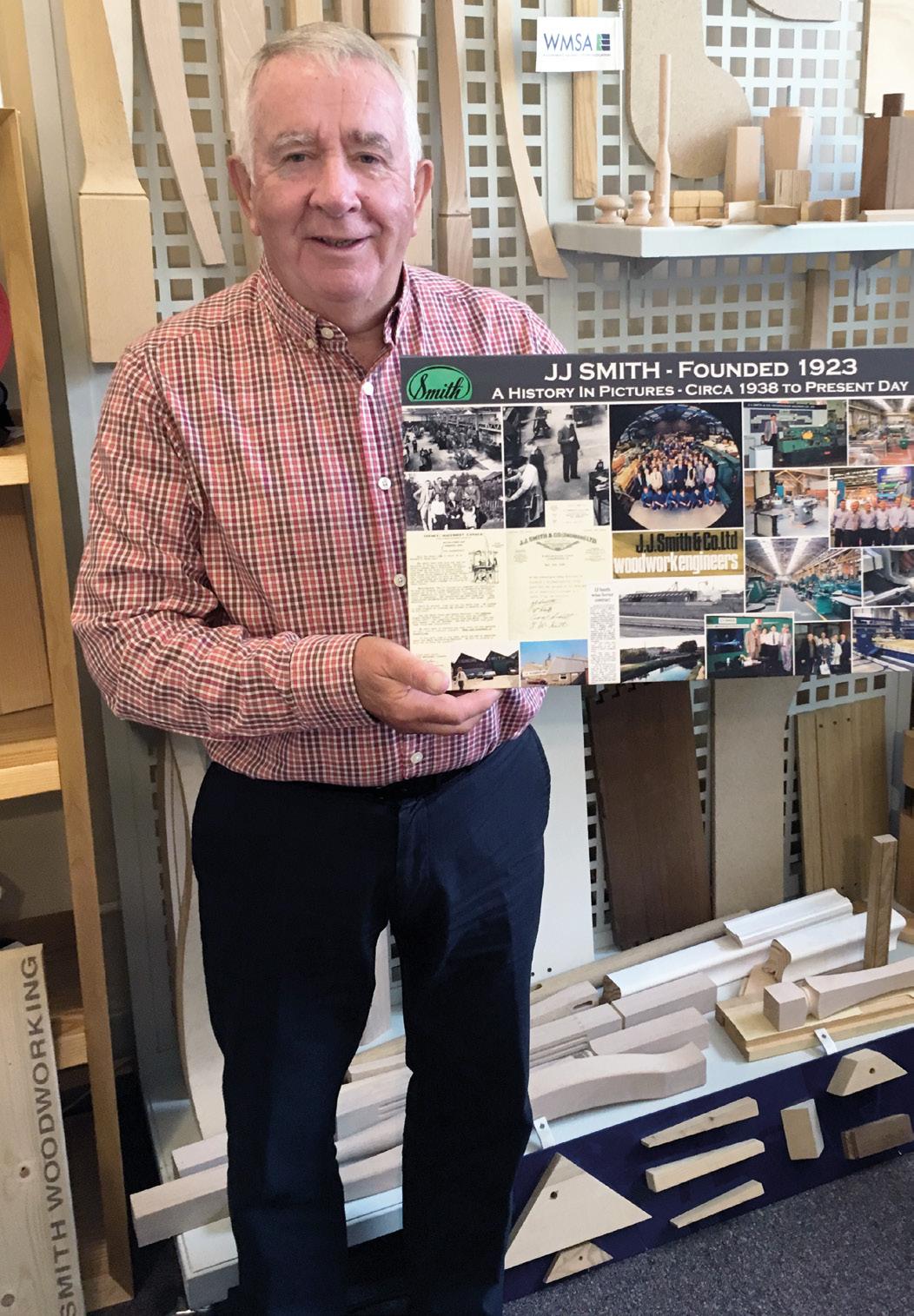
OBITUARY
John Smith
John Smith, former sales director of J J Smith Woodworking Machinery, and a well know figure in the industry, has died following a short illness.
Along with his brother Colin, John was one of the second generation to enter J J Smith which was established by their late father Bill and his three brothers back in 1923.
Joining the business in 1962 John initially worked on sales of the Smith range of classical machinery manufactured in the Liverpool factory, and was also involved in the purchase and sale of used/ reconditioned equipment.
In the 70s, John was credited with pioneering the import and sale of new machinery manufactured in Europe from companies such as SCM, Maweg, Klockner, and Balestrini, and this trend continues today with the company still importing a huge range from leading manufacturers in Italy, USA, Germany etc. John will be remembered across the industry as someone who always looked for the positive in any situation. He also has a phenomenal memory for people and faces, which was invaluable at exhibitions where he simply ‘knew everyone’. Retiring from full time work in 2002, John was appointed chairman and was still involved until 2017, having worked continuously for the company for 55 years. The business continues to be a leading player in the industry, and is still family run by the third and fourth generations. John will be sadly missed by all his colleagues at J J Smith and the wider woodworking machinery community. He is survived by wife Val and daughters Sarah and Kate.
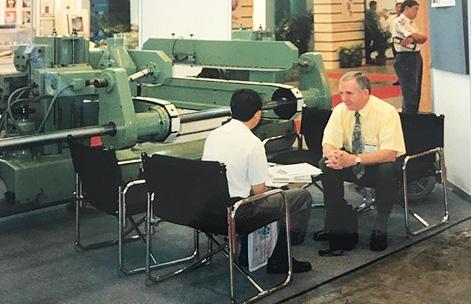
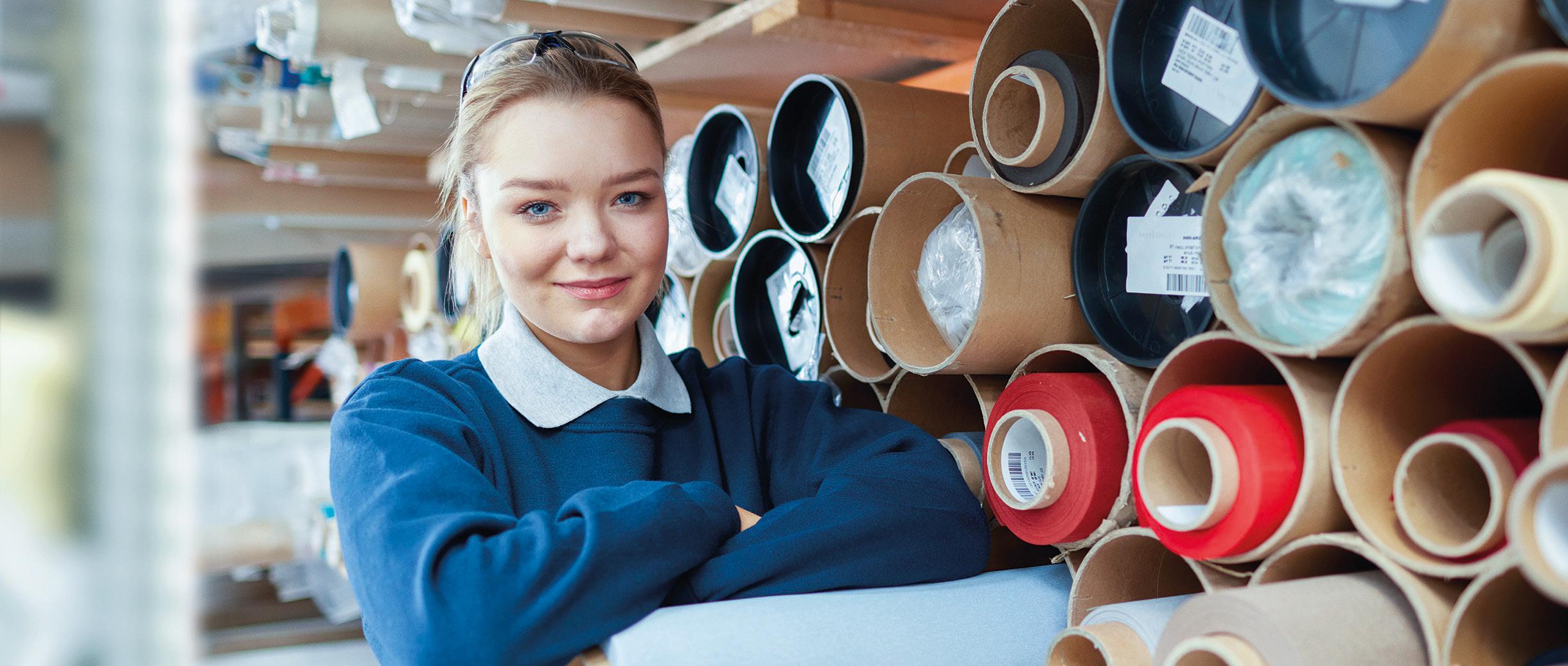
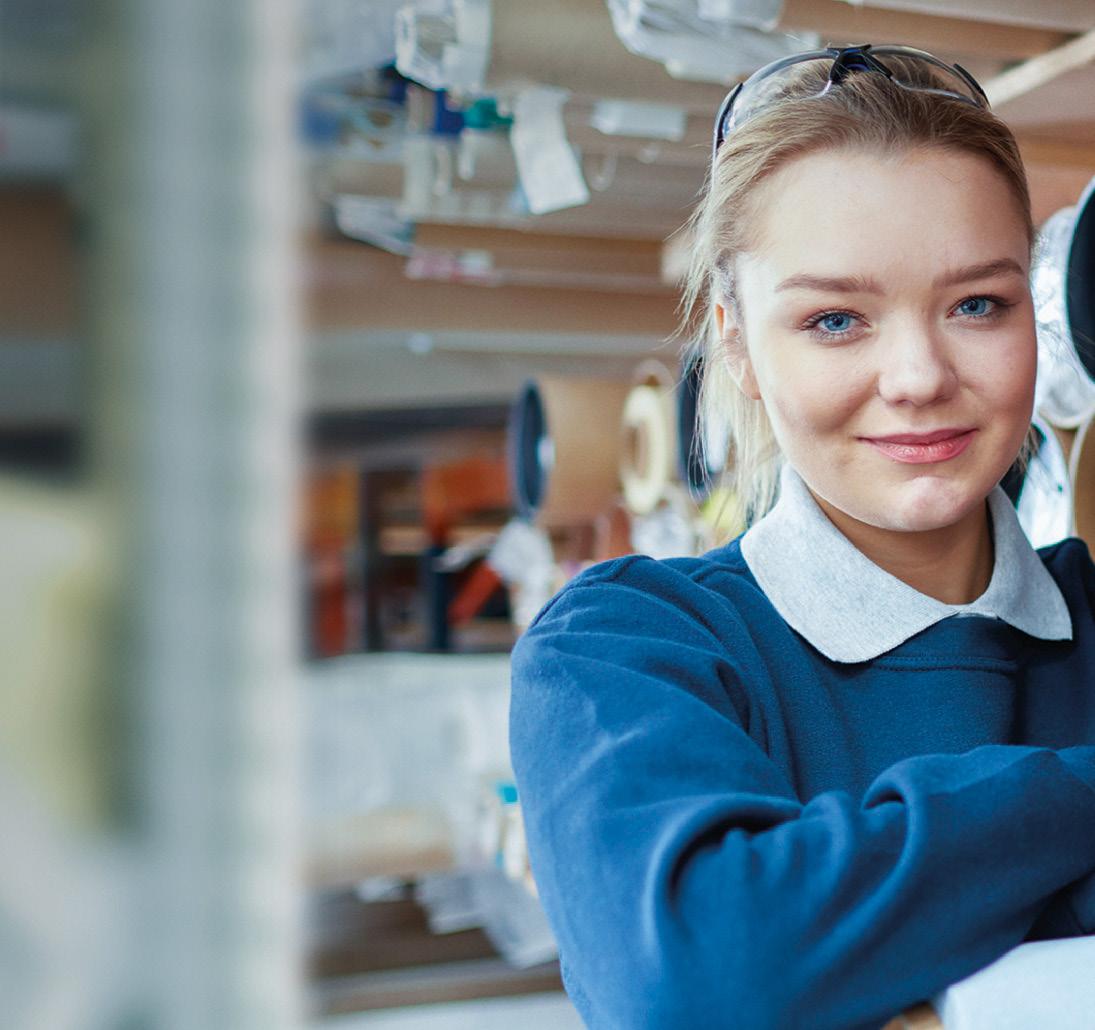
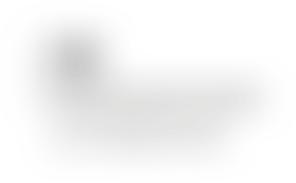
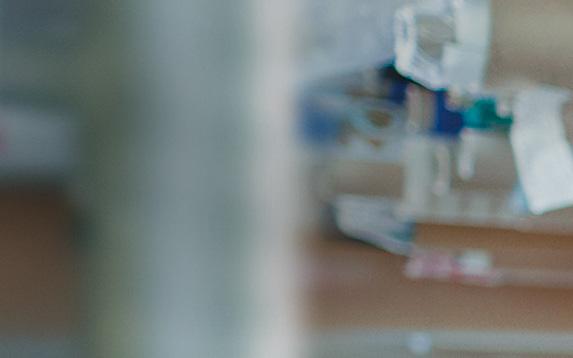
New temporary tax reliefs on qualifying capital asset investments from 1st April 2021
The Government has said that this new measure will temporarily introduce increased reliefs for expenditure on plant and machinery. For qualifying expenditures incurred from 1st April 2021 up to and including 31st March 2023, companies can claim in the period of investment: – a super-deduction providing allowances of 130% on most new plant and machinery investments that ordinarily qualify for 18% main rate writing down allowances; – a first year allowance of 50% on most new plant and machinery investments that ordinarily qualify for 6% special rate writing down allowances.
The measure also temporarily amends the rules covering expenditure incurred on plant and machinery used partly in a ring fence trade in the oil and gas sector.
Legislation will be introduced in Finance Bill 2021 to amend Part 2 CAA 2001 to bring in the super-deduction, an enhanced temporary 130% first-year allowance for main rate assets, and a 50% first-year allowance for special rate assets.
Certain expenditures will be excluded. The general exclusions at s46 will apply. In addition, there will be exclusions for used and secondhand assets and expenditures on contracts entered into prior to 3rd March 2021 even if expenditures are incurred after 1st April 2021.
Assets used wholly within a ring fence trade will be excluded from the super-deduction, as they already have a 100% allowance, with assets used partly in a ring fence trade temporarily qualifying for a 100% first-year allowance.
Plant and machinery expenditure which is incurred under a Hire Purchase or similar contract must meet additional conditions to qualify for the super-deduction and special rate relief.
The rate of the super-deduction will require apportioning if an accounting period straddles 1st April 2023. The rate should be apportioned based on days falling prior to 1st April 2023 over the total days in the accounting period.
Amendments will be made to Chapter 5 to bring in new disposal rules that will apply to assets that have been claimed to these allowances. Disposal receipts should be treated as balancing charges (taxable profits), instead of being taken to pools. The calculation includes rules which treat only part of the disposal receipt as a balancing charge, if part of the original expenditure is claimed by these temporary allowances, or part is claimed by other capital allowances.
Further, for assets that have been claimed under the super-deduction, the disposal value for capital allowance purposes should take the disposal receipt and apply a factor of 1.3, except where disposals occur in accounting periods straddling 1st April 2023, resulting in a factor lower than 1.3. This rule does not apply to the 50% first-year allowance for special rate expenditures.
Anticpated business stimulus
Commenting on the introduction of super deductions on businesses’ capital investment, Portia Pierrel, director, PwC said: “The super deduction represents a new increased temporary tax relief for companies who invest in certain qualifying capital assets from 1st April 2021, and is anticipated to stimulate £25bn in business investment in the UK. It is expected to benefit capital intensive businesses, such as manufacturers and utilities companies in particular.
“This measure will allow a temporary first-year allowance; including a super-deduction of 130% on most new plant and machinery investments which would have ordinarily qualified for 18% relief, and a first year allowance of 50% on most new plant and machinery investments which would have ordinarily qualified for 6% relief. This will provide not only an accelerated timing benefit but additional tax relief on expenditure incurred. For example, we anticipate a manufacturer incurring £10m of expenditure on a new factory to receive an additional £1m of cash tax saving over the two-year period the measure is in place.”
www.gov.uk www.pwc.co.uk
What industry suppliers have said …
TM Machinery Sales
“The new super deduction has made it the best time to invest in new machinery. The new incentive offers customers looking to purchase a new Striebig vertical panel saw significant tax savings. This, plus the added benefit of favourable exchange ranges and low finance rates, is making woodworking machinery more affordable than ever. “We’re already seeing increased machinery sales enquires since the budget earlier this month and we’re expecting to see a rise in sales over the next 12 months off the back of the announcement. This is great news for machinery manufacturers and the woodworking sector as a whole.”
SCM Group UK
“SCM are very pleased with the Government’s decision to spur capital asset investment to modernise UK production. “All manufacturers should look at keeping their equipment up to date to improve their competitiveness and achieve superior levels of safety and workplace welfare. This regardless of fiscal stimuli. “The Government incentive adds the extra encouragement to do so immediately. Looking beyond the mere substitution of obsolete equipment, the opportunity should be taken to aim towards revisiting the production process, increasing flexibility and customisation, delivering outstanding finish, improving sustainability and the adoption of Industry 4.0 solutions to drive performance supported by readily available data. “Only a handful of superior equipment suppliers like SCM can offer all of this, and the added benefit of a 130% temporary tax relief on qualifying capital asset investments eliminates logical justifications to wait any longer to do so. It’s temporary: catch the benefit while it is here!”
Palamatic
“The super deduction on business investment by the Government will assist woodworking companies to invest in capital equipment that will result in productivity and process improvements and offer increased profitability.” “Vacuum Tube lifting has provided a solution to safe lifting and handling in the woodworking sector for many years. Companies soon realise after purchasing their first unit that the productivity improvements within that process offer additional financial benefits, they hadn’t previously been able to factor in and regularly proceed to purchase more units. “One operator can load, unload, rotate, inspect, re-load and finally palletise panels, doors and sheets of material. Applications we regularly provide equipment for include loading and unloading vertical panel saws, beam saws, dimension saws, flat bed CNC stations edgebanders, laminators, paint lines, and tilt tables”
Michael Weinig (UK)
“The new super deduction means for every pound our customers spend, their tax bill can be cut by up to 25%. This will make the UK capital allowance value the highest in the OECD - raising us from 30th to first – and making us extremely competitive internationally. “This offers huge potential for both furniture manufacturers and machinery manufactures alike. In fact, we’re already experiencing an uplift in enquires from people keen to benefit from the new allowance and invest in higher technology machinery – it is really a double bonus of paying less tax and getting your hands on the latest equipment. This is a really positive sign and Weinig UK expects to see industry growth in the next 12 months.”
AAG
“The announcement by the UK government of its super-deduction initiative will prove both a timely and much needed boost to future business growth in the wake of the devastation caused by the Covid-19 pandemic. “The initiative, which enables qualifying companies to benefit from significant tax cuts on capital equipment investments, will also be augmented by the already compelling inducements enshrined in ownership of an AXYZ machine and the tangible contribution made to business growth and profitability. AAG already provides a raft of customer support enhancements as part of a comprehensive and costeffective purchasing package and these are due to be further supplemented by important new developments to be announced shortly to mark the group’s 30th Anniversary.”
Thoughts on the 2021 Budget by JJ Smith
Last March, unprecedented times called for unprecedented measures, with the government announcing financial support packages to help both businesses and individuals as the Covid-19 pandemic hit. Fast-forward to this March, the 2021 budget delivered earlier this month highlighted that we are still in the emergency phase of the pandemic, with a focus on securing an economic recovery and ensuring business stability. JJ Smith managing director Martin Smith offers his point view …
“JJ Smith, the UK’s leading supplier of woodworking and off-site construction machinery, was particularly thrilled with the budget’s focus on new machinery investment. Beginning April 2021, the Government is investing £25bn in the UK’s future growth and prosperity.
“Through the 130% super-deduction, companies can cut their taxes by up to 25p for every pound they invest in new machinery. If a company was to invest £50,000 in new machinery, it would reduce their taxable income by £65,000.
“This provides a fantastic opportunity for UK businesses to invest in new woodworking machinery that will enable them to be more productive, innovative or efficient while simultaneously reducing their corporation tax liabilities. If companies use this incentive from the government to buy machinery from us, they know that they will be getting world class equipment with long-term support from a company that has been trading for nearly 100 years. This incentive could be a fantastic opportunity for a large number of our customers to take on new projects and we’re excited to see what they do with it,” says Martin.
“JJ Smith is also proud to supply machinery to the offsite construction industry and welcome the increased focus on this construction method. Liverpool City Region was highlighted as having an ambitious proposal for MMC in the budget, and as industry experts, they think this is a fantastic opportunity for the region as a whole.
“JJ Smith welcomes the focus in the budget on investment in the construction industry as a key driver for jobs and prosperity in the UK. In particular as a leading supplier through its subsidiary company Modular Building Automation of automated equipment solutions for the offsite sector. Being the only offsite construction machinery supplier in the UK, MBA company is well placed to assist businesses large and small looking to innovate in this sector,” says Martin.
Furthermore, JJ Smith is a family business based in Knowsley which strongly believes in the benefit of apprenticeships and is proud to provide employment and training opportunities to local people.
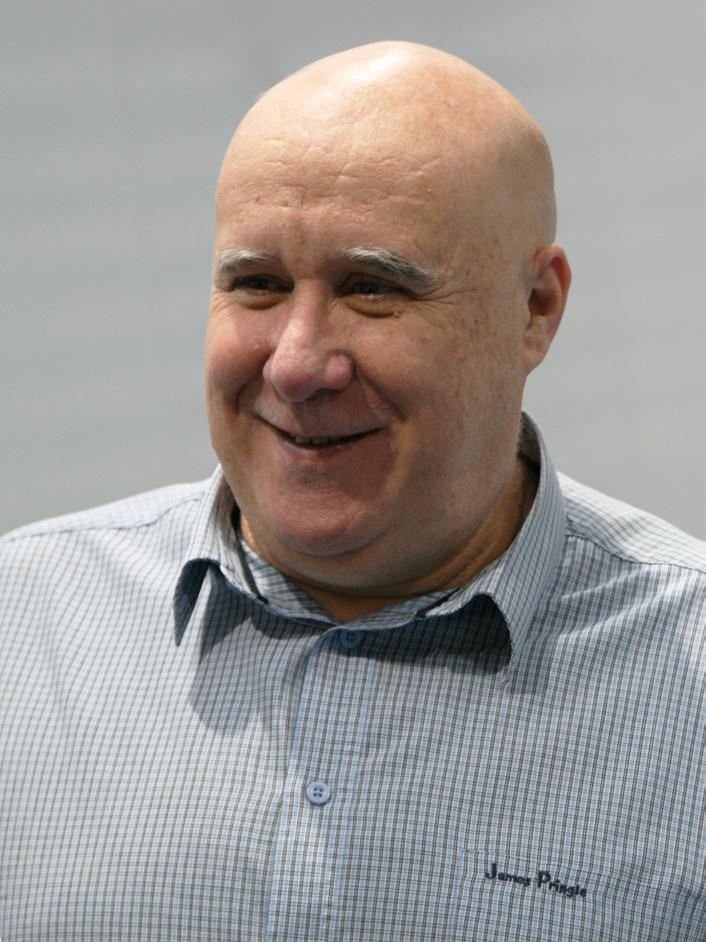
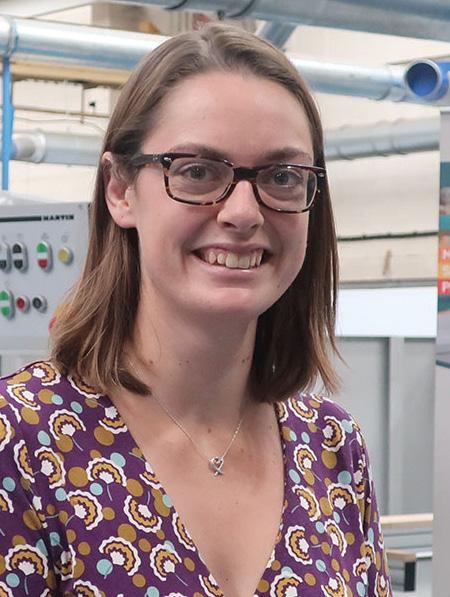
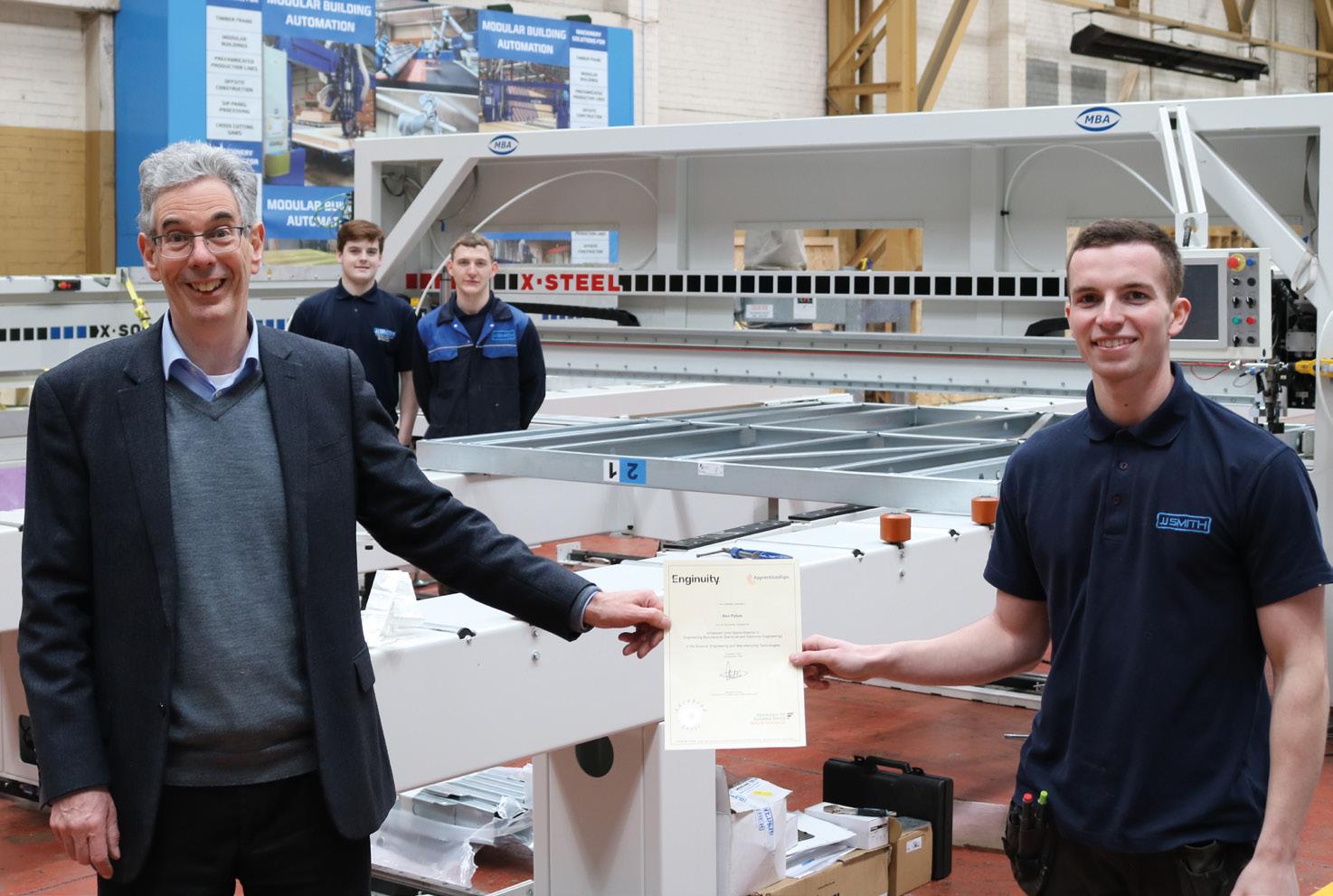
JJ Smith MD, Martin Smith, with former apprentice Ben Pybus
Pictured is rising star Ben Pybus who has just completed his apprenticeship and is now a fully qualified engineer. “Ben has shown a fantastic aptitude for engineering over the course of his apprenticeship and we’re very proud of all that he has achieved. He is a real asset to the company and he has a bright future ahead of him,” says Dave Moore, operations manager.
The announcement of the plan for additional £126m for 40,000 more traineeships in England is good news for young people. This will fund high quality work placements and training for 16-24 year-olds in 2021/22 academic year. As well as this there is an extension of the apprenticeship hiring incentive in England to September 2021 and an increase of payment to £3000.
JJ Smith currently employs five apprentices and endeavours to hire two new apprentices every year, so naturally welcomes the incentives for companies like theirs to continue to offer opportunities to young people to start their careers.
Commercial director, Rachael Baker says: “There are a number of announcements in today’s budget that we welcome. The Modern Methods of Construction Taskforce is good news. We are proud to supply machinery to the offsite construction industry and welcome the increased focus on this construction method. The super-deductions on capital investments in machinery assets provides a fantastic opportunity for UK businesses to invest in new woodworking machinery that will enable them to be more productive.
Rachael concludes: “We welcome the Liverpool City Region Freeport status and the possibilities that easier trading could bring to us as a company, and the increased apprenticeship funding is excellent too.”
0151 548 9000 www.jjsmith.co.uk
Historically, IMA (Germany) and Schelling (Austria) have always been close players in the industry, and worked under a network umbrella for many years, until some six years ago, when Schelling Anlagenbau of Austria bought IMA in Germany to form the IMA Schelling Group.
Since that time, ISG, as it is commonly known, has been busy on a global basis, consolidating the separate IMA and Schelling companies into one, to show a united front to all customers and be present as one group.
The appointed MD of IMA Schelling UK will be Markus Freuis, who has been part of the Schelling business in the UK since 1999. Andy Howell and Ashley Cooper, formally of IMA UK, remain on hand, lending their experience and expertise to supporting the newly merged business.
“We are therefore pleased to announce the merger of IMA Klessmann UK and Schelling UK Ltd into one company, with its new base being Wetherby, West Yorkshire,” confirms Markus.
“As well as the Schelling cut-to-size saws, and
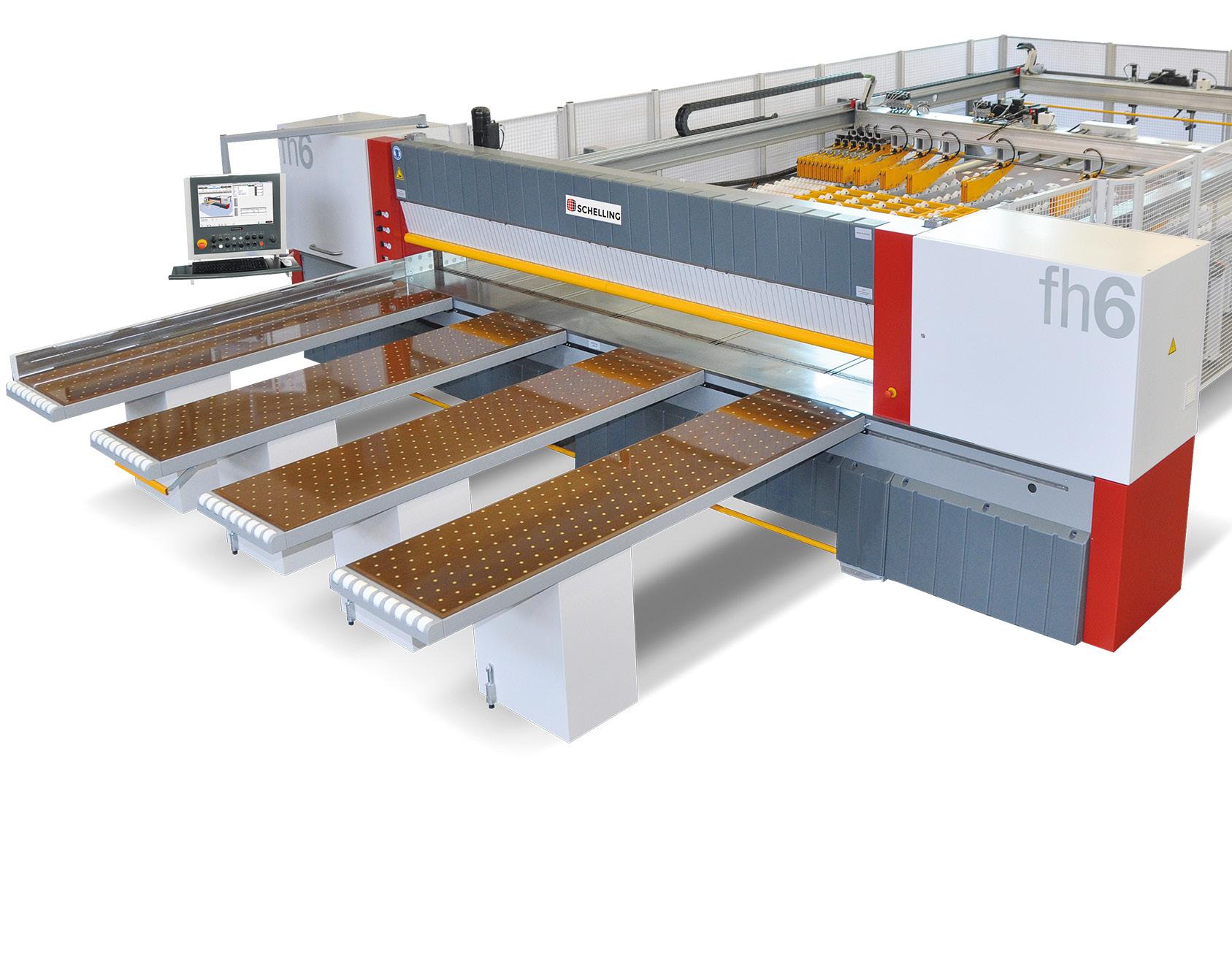
The fh6 cut-to-size saw
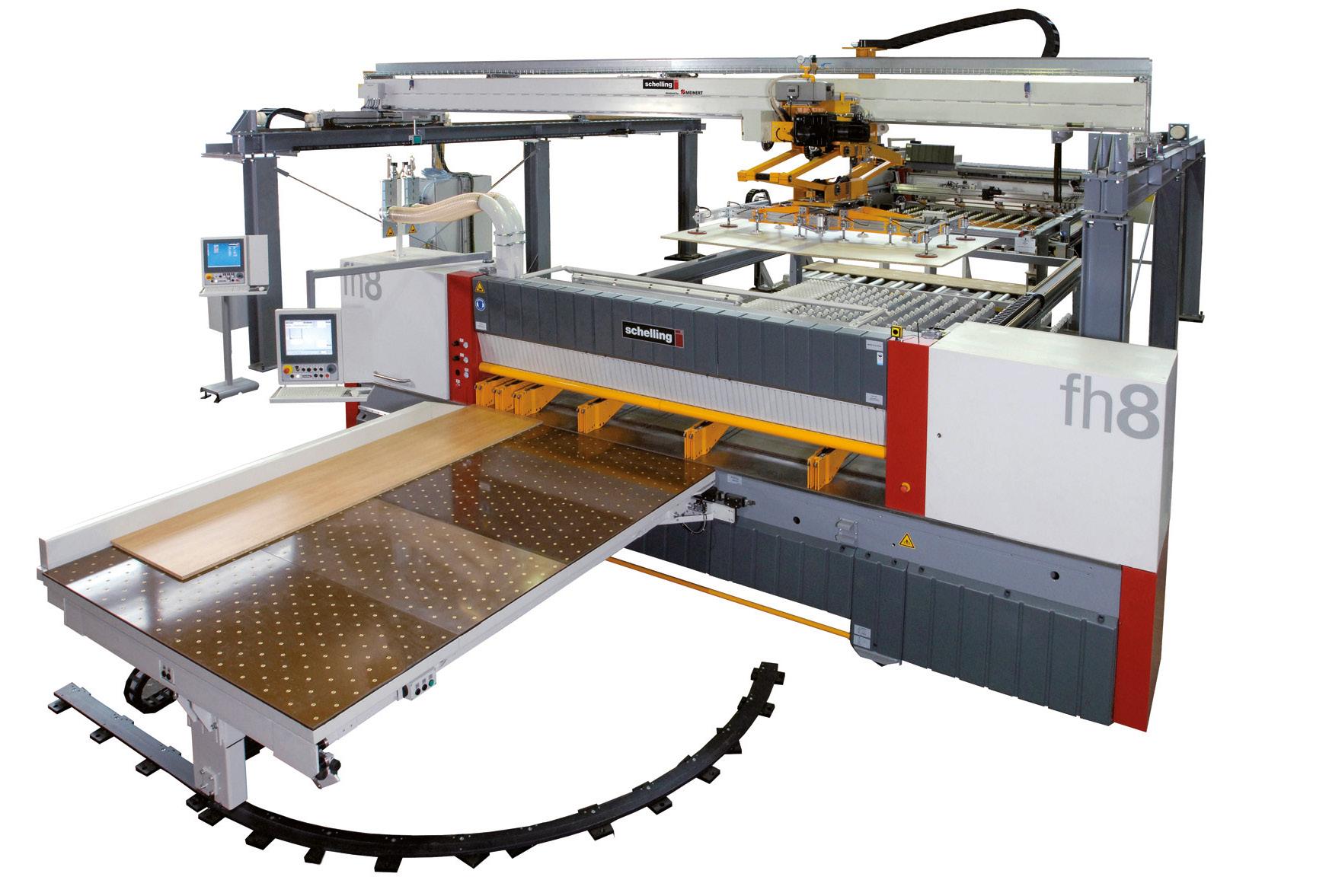
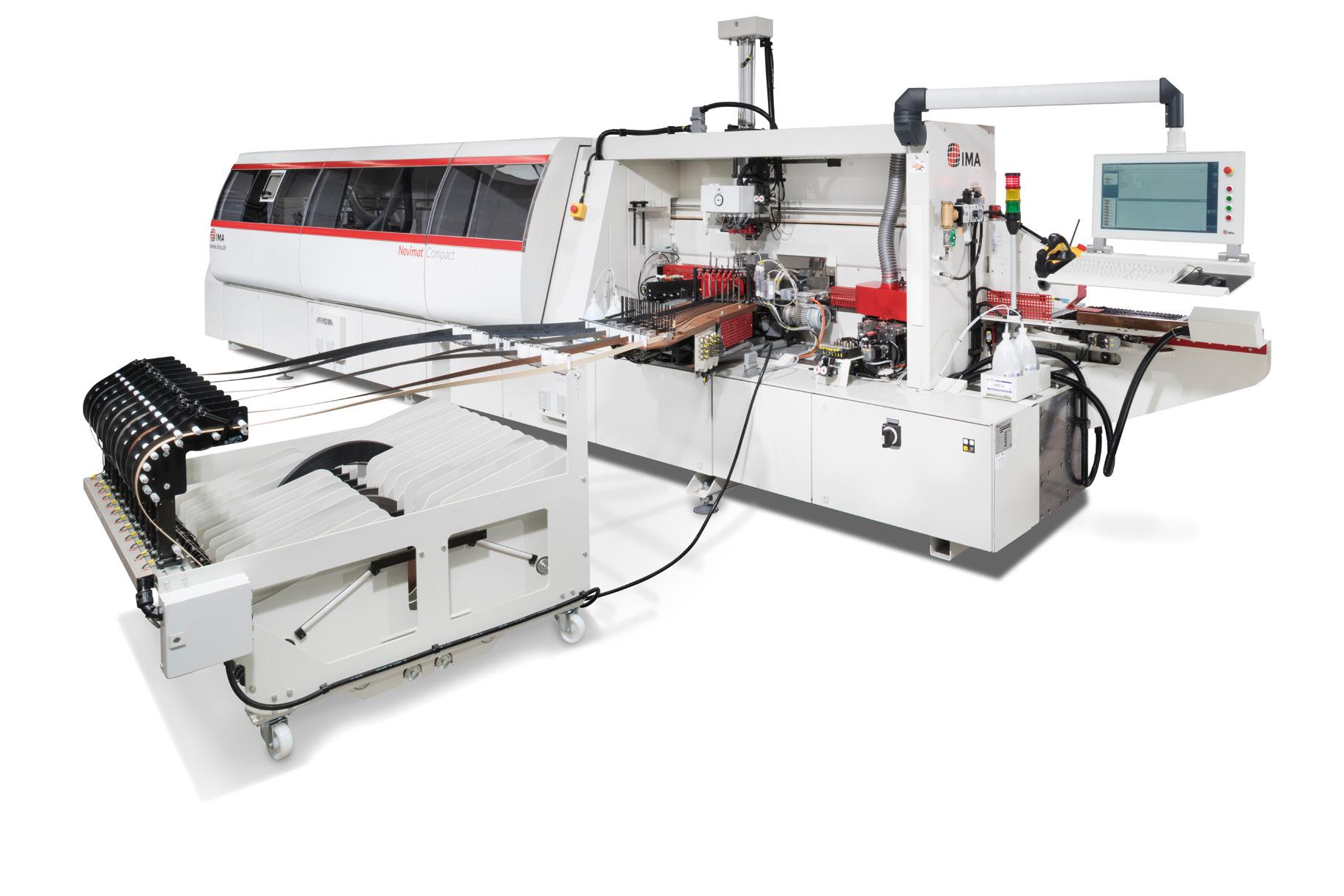
complementary equipment available from our head office in Wetherby, we are pleased to have with us the world-renowned manufacturers of throughfeed single- and double-sided IMA Combima edgebanding machines, running at up to 120m/min feed speed.”
IMA is the universally respected manufacturer of the world-famous IMA BIMA range of CNC machining centres – both with and without edgebanding and finishing facilities – as well as being the designer and manufacturer of the IMAGIC range of throughfeed point-to-point drilling and dowel-insertion machines.
IMA UK and Schelling UK service engineers are all factory trained, with experience in mechanical, electrical and electronic fault diagnostics. All routine maintenance, machine repairs and servicing can be carried out without the expensive costs associated with overseas engineers.
“In the short interim, we will run both companies side by side to ensure continuity of business as usual for you, our customers, and we will start trading with immediate effect as IMA Schelling UK Ltd,” explains Markus.
“We would like to assure all our customers and suppliers that it’s business as usual, and there will be no changes to the support you receive and the customer service you have experienced in the past from both IMA Klessmann UK and Schelling UK.
“All the contact numbers, etc, will remain the same through this transition period, and any changes will be announced to all our customers where applicable. Please note the new email address – info.uk@imaschelling.com – if you have any questions, please feel free to contact us via this address. Here’s to a very exciting and prosperous future.”
www.imaschelling.com
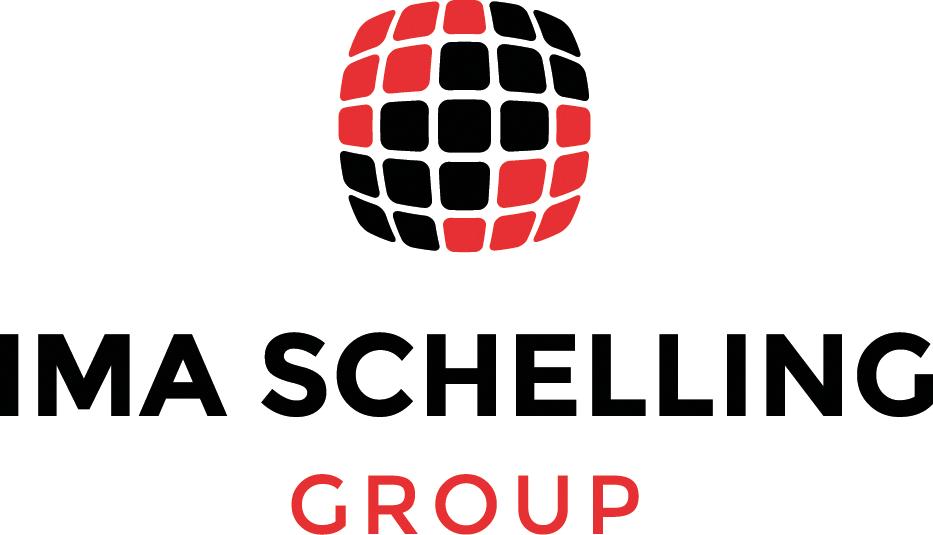
The Novimat Compact R3 edgebander
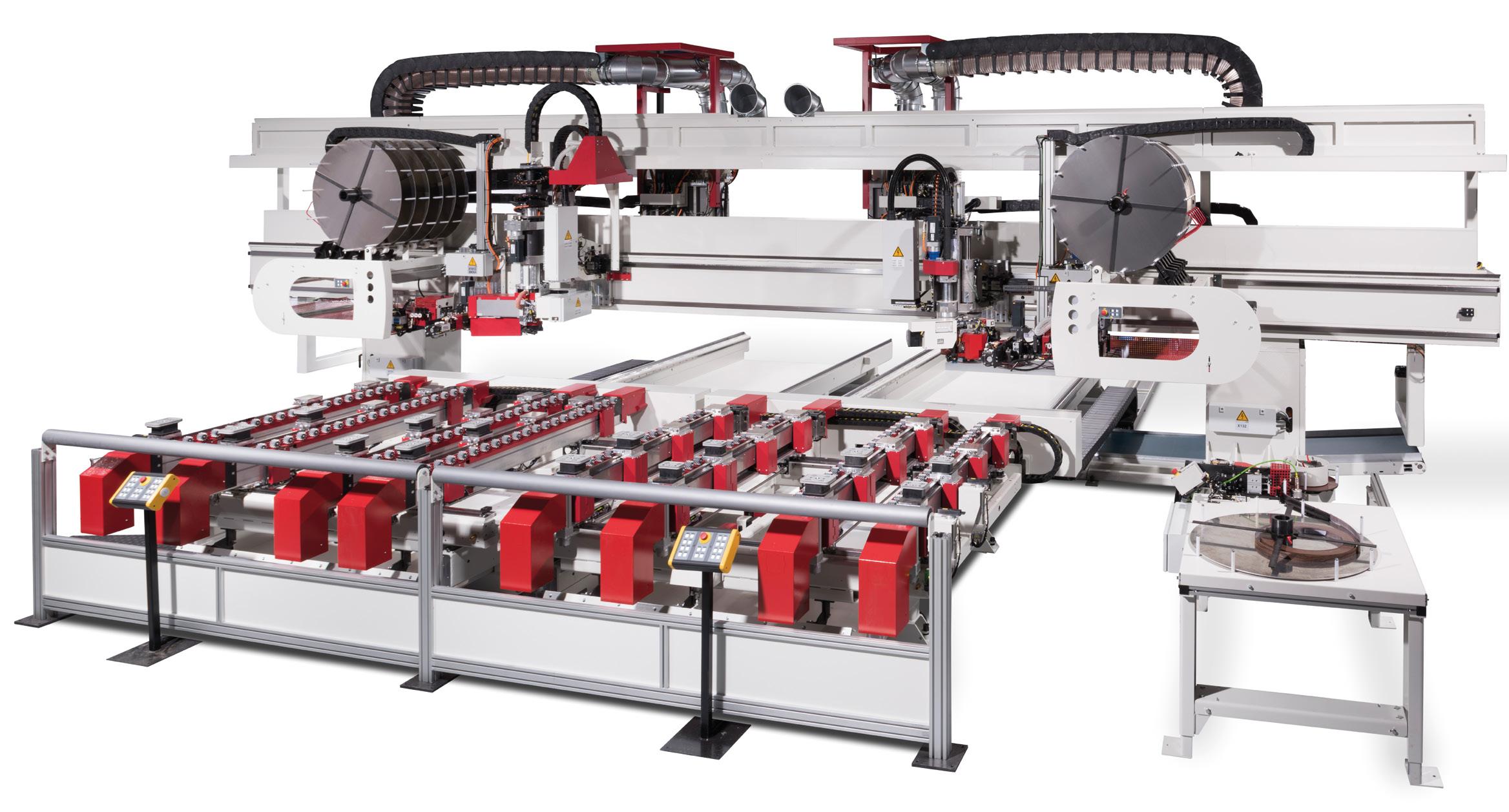