
19 minute read
Updates
A staircase is often the best introduction to a home – if not the first piece of decor that attracts attention as soon as one enters a house. This is why it is essential for manufacturers, architects and designers involved in the production of staircases to pay close attention to every detail, and create a product that is as ‘custom-designed’ as possible and fully reflects a customer’s personality, and their practical and decorative preferences.
In response to these needs, SCM offers an integrated solution for the production of staircases. This involves a cell for the nesting cut, consisting of an automatic Flextore EL magazine integrated with two Accord 30 NST machining centres
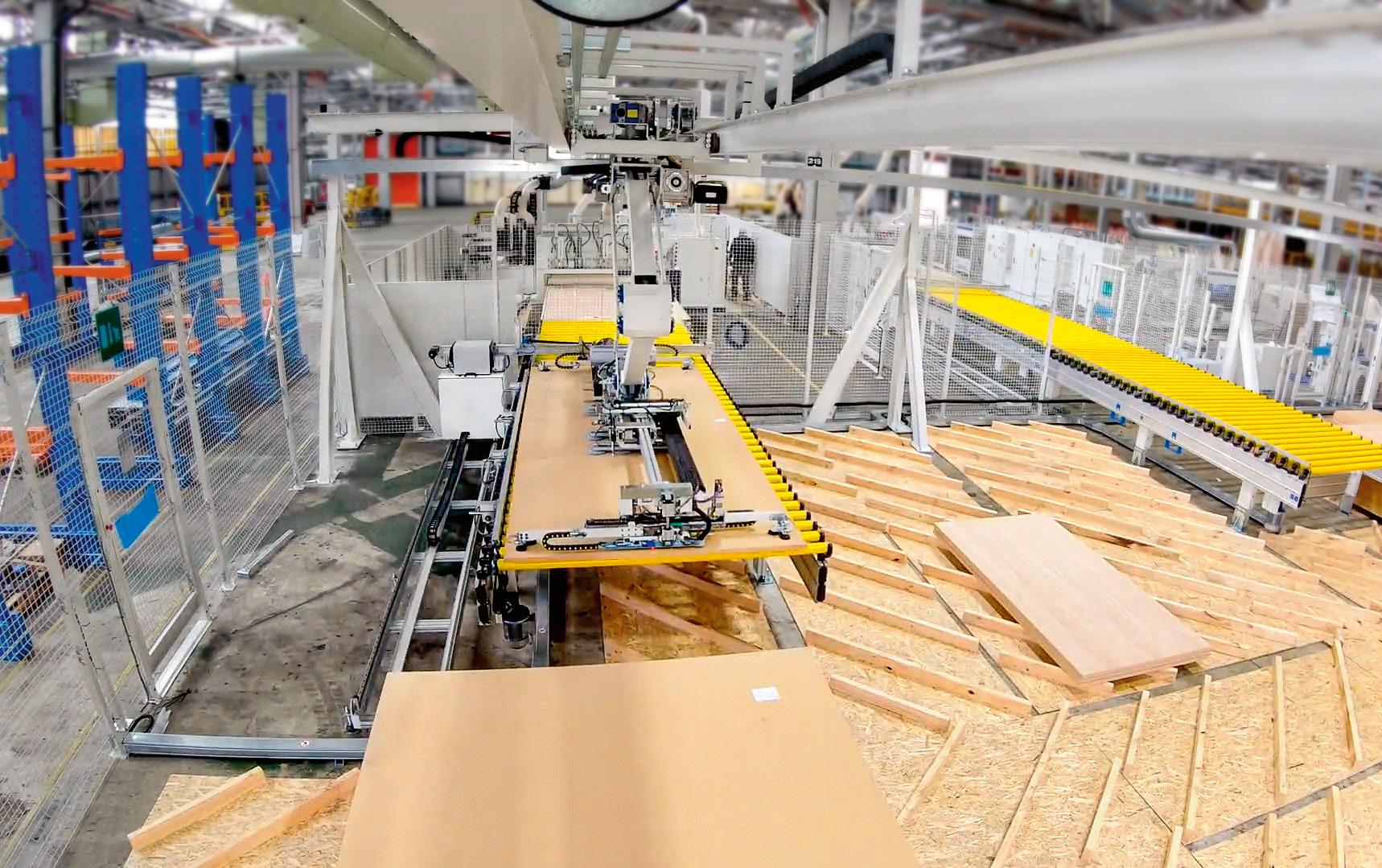
and a double Celaschi squaring line.
This engineering solution has already been successfully adopted by leading customers in the industry. It automates the machining process, increasing the quality and production capacity – which that can mean that 60
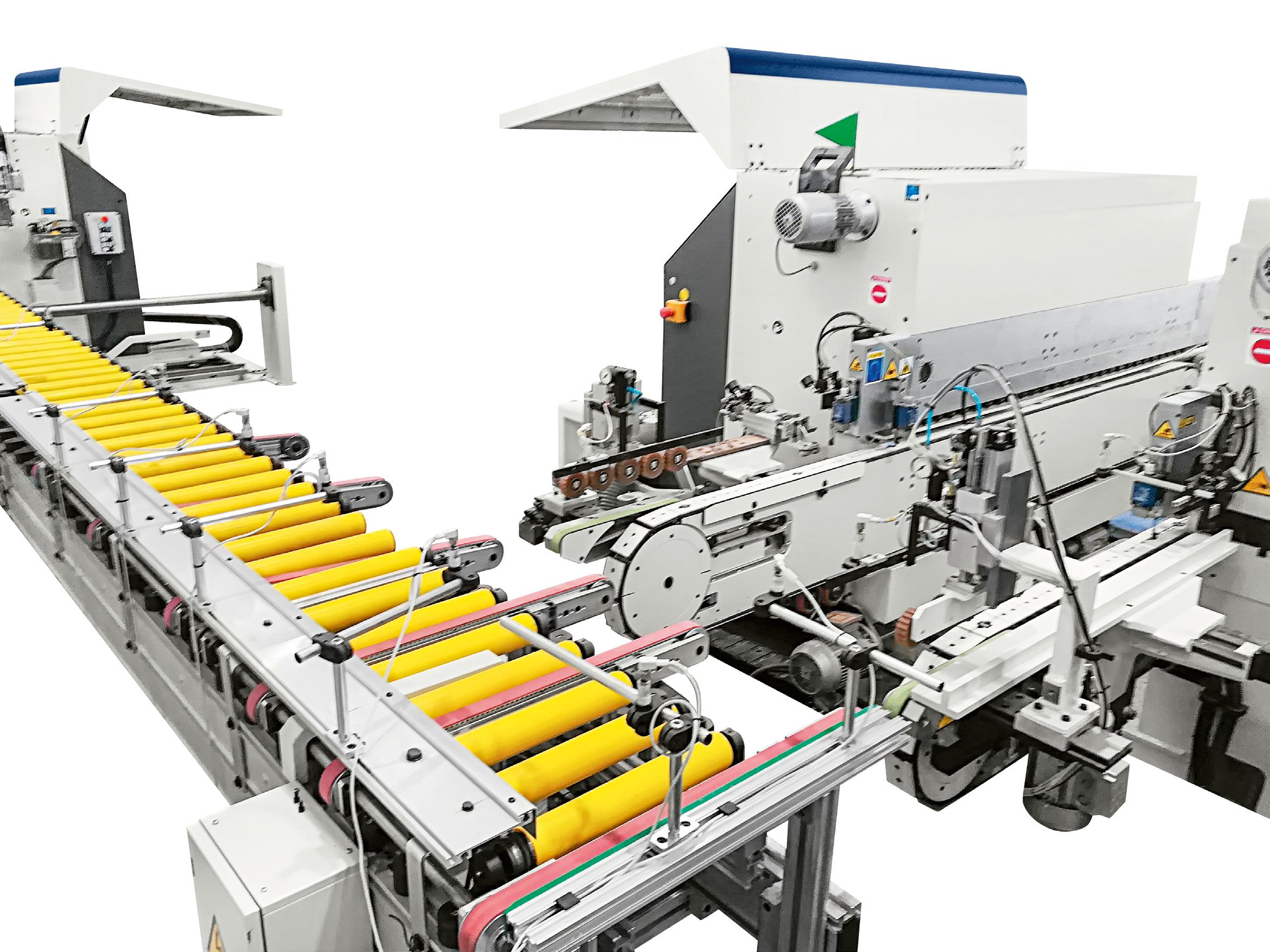
staircases, each with 16 steps and landings, can be completed in a single eight-hour shift.
In addition, the entire system is designed to be subjugated, on the customer’s request, to an articulated robot positioned on a ‘seventh axis’, which increases the operating range to complement the integration of the two cells, automatically managing the nesting machine unloading and loading onto the Celaschi line, without the intervention of an operator.
The engineering project in detail
Nesting cell
Starting with the unfinished panel, the stair strings, landings, risers and treads are produced. This SCM solution is ideal for optimising and simplifying made-to-order productions because it handles both uniform and mixed stacks, consisting of panels of different sizes and colours, and unfinished panels and/or with a minimum ‘The Maestro Active Store software plays a dual role of manmachine interface for the Flexstore automatic storage, as well as acting as supervisor to the cutting cell, allowing control to be centralised and simplified.’
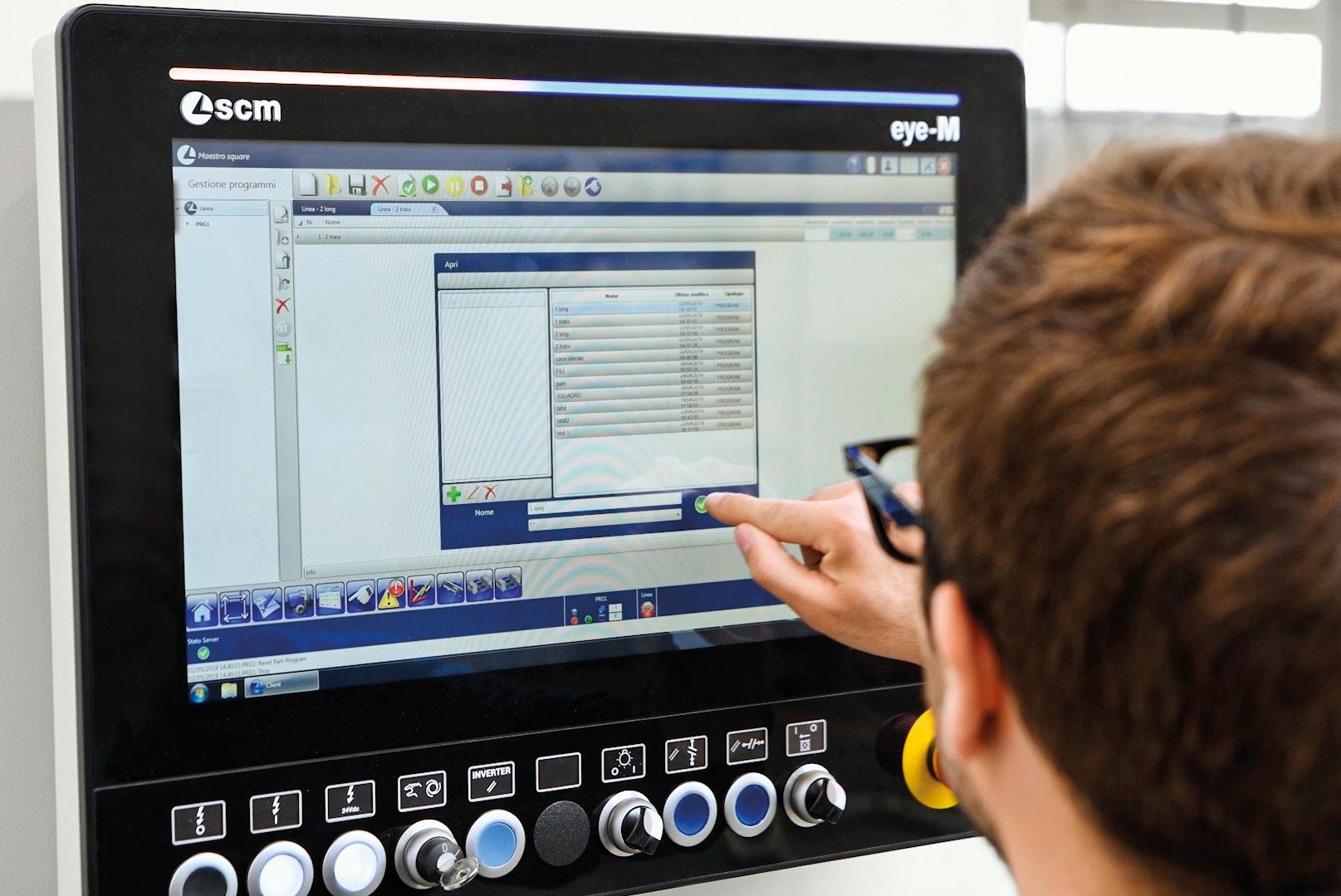

thickness of no more than 3mm, depending on the material.
The core of the cell is the three-axis Flexstore EL automatic magazine, which guarantees a considerable increase in productivity and a significant reduction in the cost of running the raw materials magazine.
The Maestro Active Store software plays a dual role of man-machine interface for the Flexstore automatic storage, as well as acting as supervisor to the cutting cell, allowing control to be centralised and simplified.
Furthermore, automatic panel labelling is done in this area, in accordance with the cutting diagram subsequently carried out by the operating machines. This operation is extremely important, as it means the panel can be constantly tracked during the integrated automatic processes, and the work programs associated with each element can be called up at later stages in the machining process.
Of the two Accord 30 NST machining centres, the first one is mainly used to manufacture the risers and steps, while the second is used for the stair strings on the staircases and landings. By maintaining the manual loading function, special one-off pieces can also be machined.
The main advantages of this solution are high-powered routing and intelligent programming, thanks to the Maestro software suite. This results in impressive
performance in terms of speed, as well as quality and implementation accuracy.
The main advantage of the cell lies in its modularity and scalability – indeed, even though each of the two machining centres are assigned to specific machining jobs, just one of them can be used if there is a reduced production capacity requirement. Equally, if there is a fault on one of the two machining centres, this solution ensures that production does not stop completely but that it continues on the other one.
Celaschi double squaring line
This line allows customers to trim lengthways and outline the risers and treads previously created. It consists of a manually powered automatic loading system, a longitudinal Celaschi P60 double squaring machine for profiling the long sides, a Celaschi TR 90 automatic transport system, a second transversal Celaschi P60 to trim and square the short sides, and unloading rollers.
The contribution from Maestro Active Watch software is also important for the supervision and control of the entire squaring line, which means program management can be optimised and simplified – as well as the worklists, machining commands and parameters, the process implementation, and all the work involved in diagnostics.
www.scmgroup.com

Second woodwaste heater for timber manufacturer as it expands into new premises
The owner of a Worcestershire export company has purchased a second woodwaste heater from Wood Waste Technology because the investment in the first heater delivered everything promised in helping to reduce operational expenses.
Rob Johnston, MD of IM Export Services in Redditch, manufactures ISPM export-grade timber products including bespoke timber cases, crates and pallets.
The business purchased its first woodwaste heater around 10 years ago from Wood Waste Technology. At the time, the business was operating from its 3500ft2 premises, and the heater helped save money on the disposal of waste wood while also providing the unit with free heating.
As the business went from strength to strength and continued to grow, it needed to relocate to larger premises to incorporate all the manufacturing, packing and dry-storage aspects of its business. The original woodwaste heater was relocated to the new building, and an additional heater, a WT15, was purchased to help heat the new 16000ft2 .
As Rob explains: “We generate waste wood as part of our dayto-day business operations, so it makes sense to convert this into free heating to warm the industrial unit for our 30 employees. It’s such a large space, with very high ceilings, I dread to think how much it would cost to heat if we had to pay for it.
“Fortunately, the two woodwaste heaters – as we have one at each end of the workshop – create a perfect workshop temperature. We’re delighted with our purchases. The heaters do everything we were promised they would, so have been a great investment. If we ever needed another, I’d be straight on the phone to Wood Waste Technology.”
Kurt Cockroft, MD at Wood Waste Technology, says: “We’re thrilled that IM Export got back in touch when they moved to larger premises. We’re proud to say that most of our business comes from client recommendations, as well as from existing customers needing additional units as a result of business growth. We’re also delighted that every woodwaste heater ever sold by us is still in operation today.”
WWT offers a full range of woodwaste heaters, from small, hand-fired units to larger, fullyautomatic systems, and offers site survey and design, as well as manufacture, installation and ongoing maintenance. The company also services all types of woodwaste heater, and supplies genuine spares up to 60% cheaper than other suppliers.
In addition, the company is the UK’s official distributor for Gross Apparatebau, a German manufacturer of dependable, precision-engineered shredders and briquetters. The company is also a distributor for Putzmaus boiler tube cleaning systems – a powerful but gentle routine maintenance solution that is quick and easy to use, and helps to increase boiler efficiency and lower operating costs.
01785 250400 www.woodwastetechnology.com www.grossuk.co.uk www.putzmaus.co.uk

AXYZ router proves a class act at leading furniture manufacturer
The latest AXYZ Infinite multi-purpose CNC combined routing/knife-cutting system from Telford-based AAG has recently been installed at one of the UK’s leading manufacturers of furniture and associated equipment supplied to the educational sector. The perceived higher performance capabilities and important new machining enhancements provided by Infinite were considered to be pivotal to the rapid business growth and commensurate increased productivity levels at the County Antrim, Northern Ireland-based Kindercraft.
The company employs mainly melamine-faced veneered MDF and birch plywood to manufacture a wide range of handcrafted, highend products. These include both standard and bespoke classroom desks, chairs and tables (including those covering special needs requirements), general storage, fitted washroom and kitchen units, computer suites and reception area furniture.
The company’s in-house design service works closely with school equipment specification and purchasing authorities in selecting products considered most appropriate for the different pupil age groups to be accommodated. These include products in a wide choice of different sizes, shapes and colours, enabling the creation of highly individualistic design themes.
Installation of the AXYZ Infinite could be described as the apogee in a long-running and highly successful business partnership forged between AAG and Kindercraft.
In 2002, the company installed an AXYZ 4008 twin-head router to undertake work previously carried out manually. This was followed in 2006 by a need to upgrade to and replace with the larger-format AXYZ 6010 router, in order to meet an increased customer demand, culminating in 2020 with the addition of the latest AXYZ Infinite 6010 machine (incorporating a seven-station Automatic Tool Change system for work requiring multiple tools) that was necessary due to a further exponential increase in production capacity that a single machine simply could not handle.
The AXYZ Infinite can be configured with a choice of single, dual or triple routing/ cutting heads to accommodate varying application requirements. It is available in a choice of sizes and incorporates an expandable processing bed area of up to 3251mm in width by an impressive 15.24m in length.
Key design features include the familiar solid steel frame construction to withstand the most vigorous machine operation likely to be encountered, and an aluminium t-slot vacuum material hold-down facility.
These are supplemented with a new carriage design to enable easier routine machine maintenance and the installation of future machine upgrades, an ultra-efficient dust-extraction unit for enhanced machine performance, and a new misting system to provide improved machine cooling and lubrication.
Other optional production enhancements include the AVS (AXYZ Vision System) for optimum routing/cutting precision, and the latest helical rack-and-pinion drive system. This incorporates a multi-teeth configuration that helps spread the workload more evenly, resulting in faster material throughput and reduced wastage and ultimately a longer-thannormal machine life.
01952 291600 www.axyz.co.uk
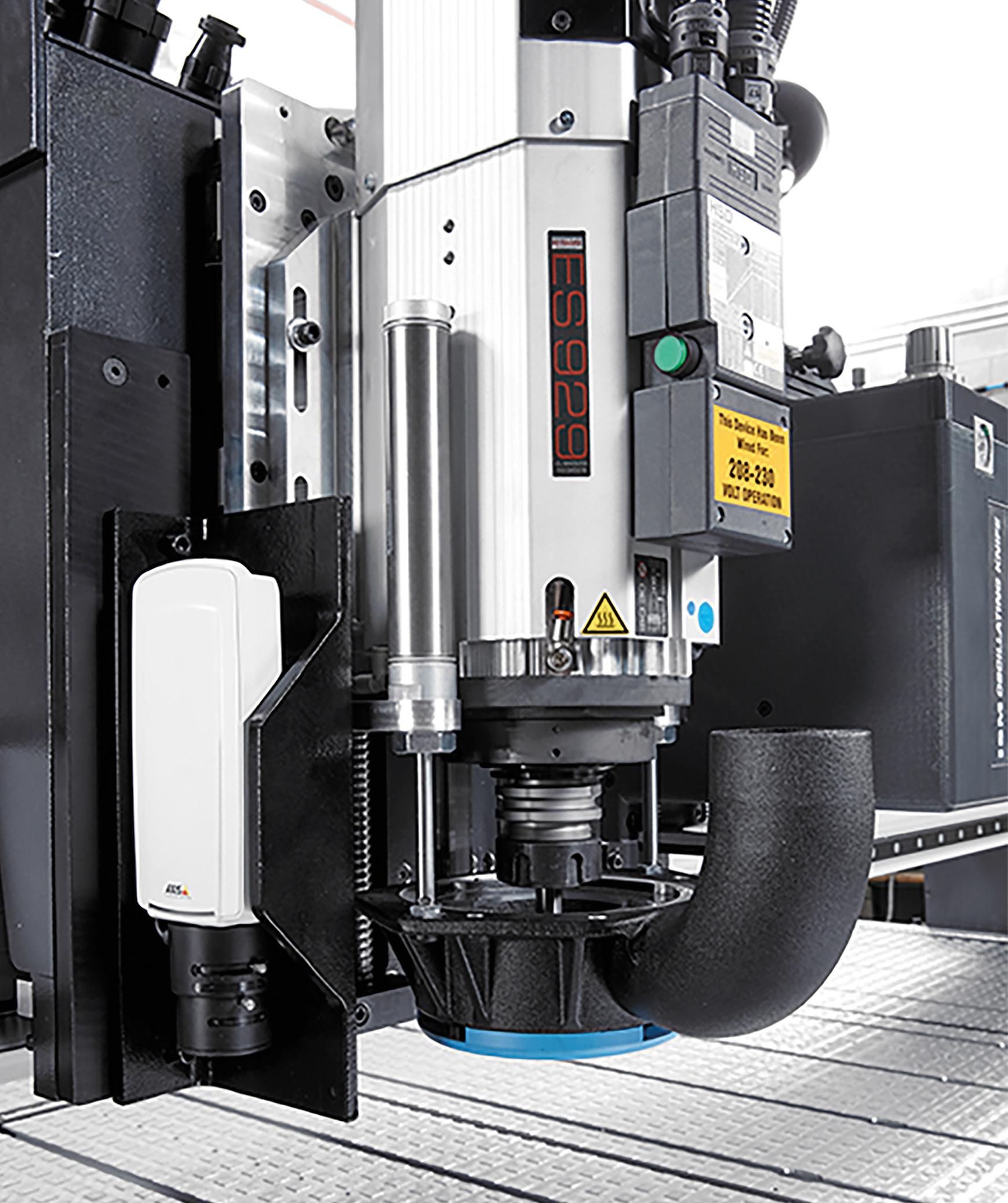
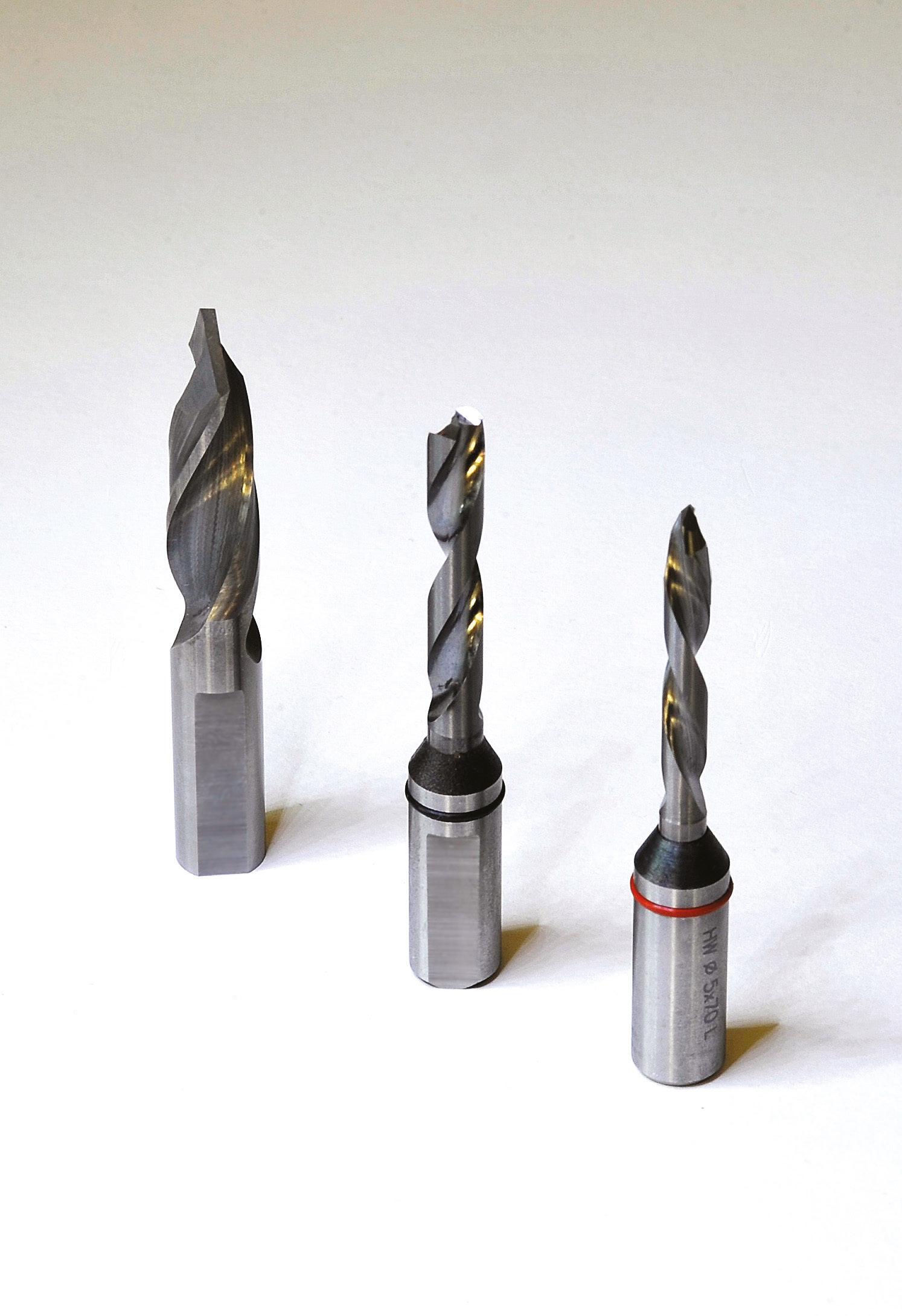
Coated d AbrasivesAbrasives ForFor Any Any KindKind OfOf Surface Surface
UK K ManufacturedManufactured Abrasive Abrasive SandingSanding BeltsBelts inin 3-53-5 days days
FullFull TechnicalTechnical Coverage Coverage ThroughoutThroughout TheThe UK&UK& Ireland Ireland
MarketMarket LeadingLeading Innovative Innovative Products Products
Immediate Response to Quotation Requests Immediate Response to Quotation RequestsGABBIANI G2 30% MORE PRODUCTIVITY
The new range of Gabbiani G2 beam saws features the new “EASY & RESPONSIVE” production system, employing flexible advanced technologies in compliance with “industry 4.0” principles. For r more information, please 5%OFFmore information, please OFF • A new intuitive operator INTERFACE, packed with functionalities Maestro Cut is the exclusive SCM software for panel saws which ensures every cutting operation is conducted at the lowest cost and is fully integrated with the rest of production. • A new CUTTING OPTIMISATION ALGORITHM contact t us on: 0116 258 1900.us on: 0116 258 1900. A new algorithm reduces machining times and waste, resulting in a 30% increase in productivity.
• FLEXCUT modular systems
Highly complex cutting schemes easily achieved in significantly less time.
• SAW SET, rapid and precise tool changes
The scoring saw is adjusted automatically in just a few seconds by detecting the position of the main blade.
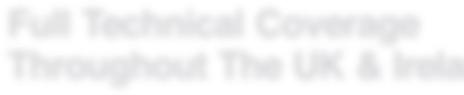


Bibielle e UKUK Ltd Ltd www.bibielle.co.ukwww.bibielle.co.uk sales@bibielle.co.uk sales@bibielle.co.uk
01707 386111 sales@calibretooling.co.uk
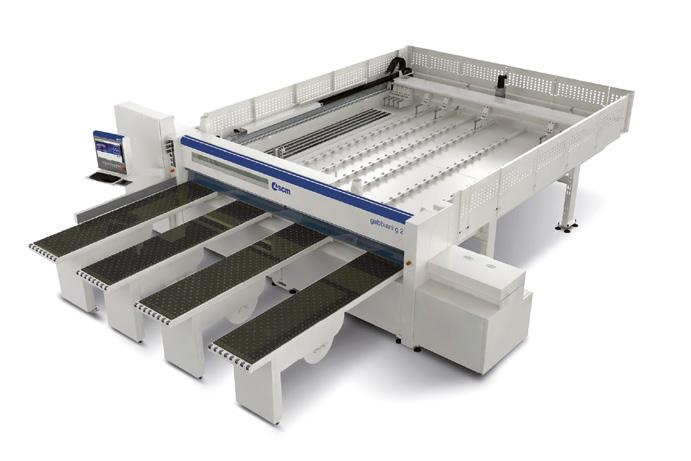
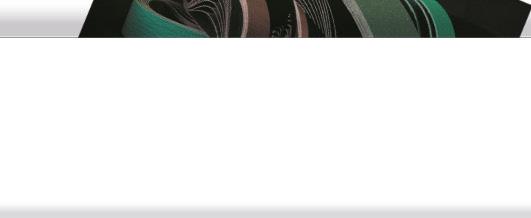

Unit 11, The Welltech Business Centre, Ridgeway Welwyn Garden City, Hertfordshire AL7 2AA
Download our new catalogue from www.calibretooling.co.uk
1/4 page vertical.indd 1
SCM Group UK
Tel. +44(0)115 9770044 - scmgroupuk@scmgroup.com - www.scmwood.com 10/03/2021 09:44Calibre326indd.indd 1
LHW Machinery providers of New and Used are pleased to announce for 2021 a new partnership with world renowned Italian manufacturers, SCM
QUALITY USED MACHINERY WANTED, SINGLE ITEMS TO COMPLETE WORKSHOPS
IN STOCK NOW ME28-t Pre-milling Edgebander T120 Class tilting spindle moulder Nova Ti105 Tilt arbor Spindle moulder Si400 EP Nova Panel Saw Si400 Nova Panel Saw Si300 Nova Panel Saw FS410 Nova planer thicknesser with tersa 2015 SCM si300 Nova 3.2m Panel saw - £5500 + VAT 2015 SCM Startech Multi-tech Boring Machine
Minimax S45n Bandsaw 240v / 3 phase SC 4e 2.6m Panel Saw FS 41e planer thicknesser tersa T 45c Spindle Moulder 240v TW 45c Tilting spindle moulder 2014 ME25 Hot Melt Edgebander - £6750 + VAT
09/03/2021 11:17
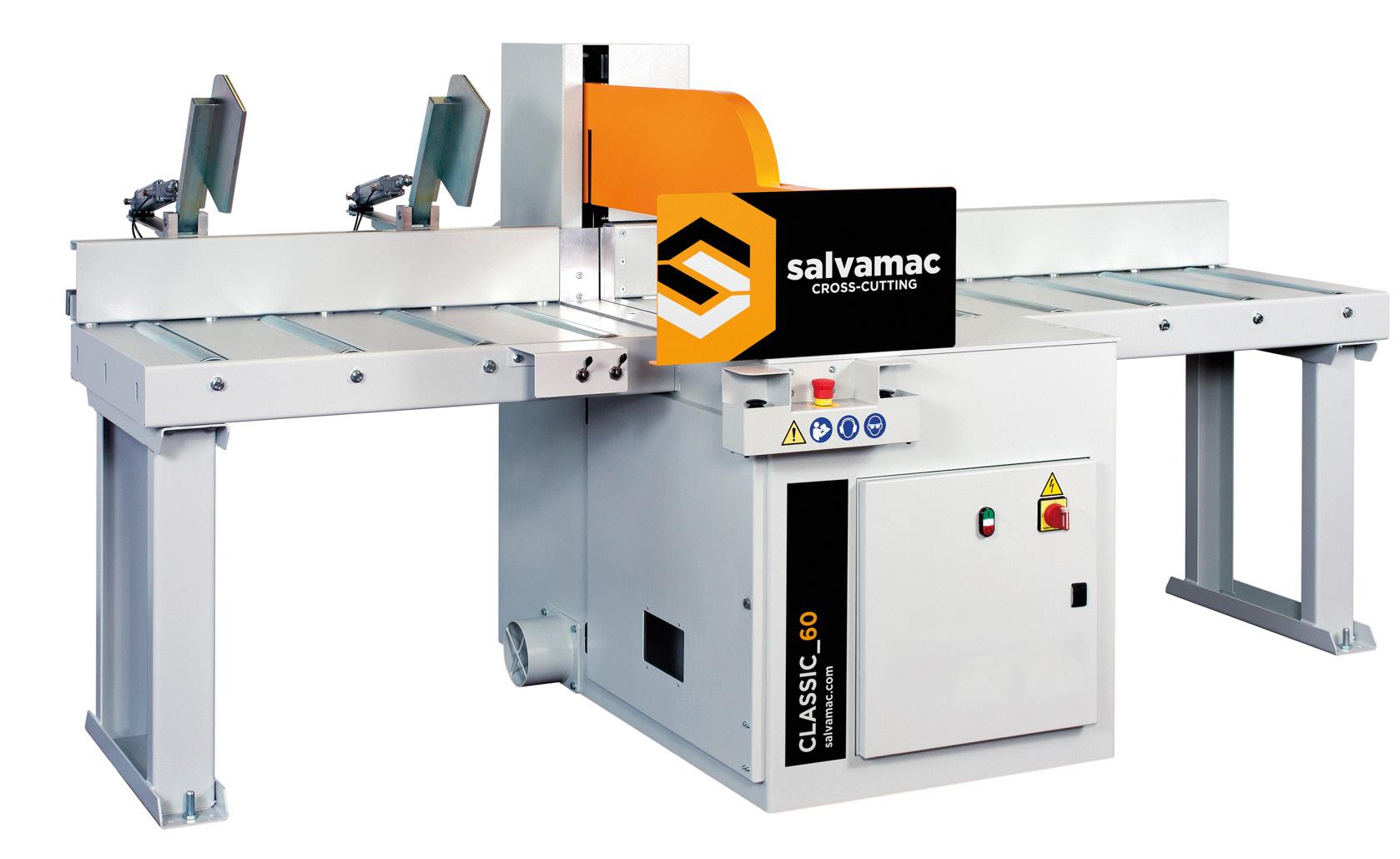
Salvamac – solid, simple and safe cutting
Christian Salvador comments on the presentation of Salvamac’s Q1 2021 results: “The event of our anniversary in March 2021 has been the occasion not only to confirm our choices, show our machines, share our ideas and meet our partners (mainly virtually) as we have done in the past and how we will do in the future, but also to celebrate our results, that are positively surprising us every month.”
Ziemowit Dolkowski, co-founder of Salvamac, says: “Our growth has been more than +50% in recent months, and it was a success that we really did not expect – a success that has not only concerned traditional and already consolidated products, but the entire production range, and which has led us to the creation of something greater … Salvamac Group.”
Salvamac is the result of over 20 years of experience built by its founding partners, Christian Salvador and Ziemowit Dolkowski, who continue to invest their strong passion and deep knowledge for the woodworking machinery sector.
“All this, together with a continuous analysis of the reference market, has allowed us to create a network of contacts and skills, thus proposing our business as an ideal partner for those working in the woodworking sector,” Ziemowit continues.
Salvamac continues to move forward in its social and ethical approach to production and innovation, by creating a group based on the support of four production units in three countries –Italy, Poland and Turkey – to obtain a winning mix of Italian heads and hearts with the dynamics, advantages and competences of various other nations, all in a constant state of evolution. From this perspective, the Salvamac Group
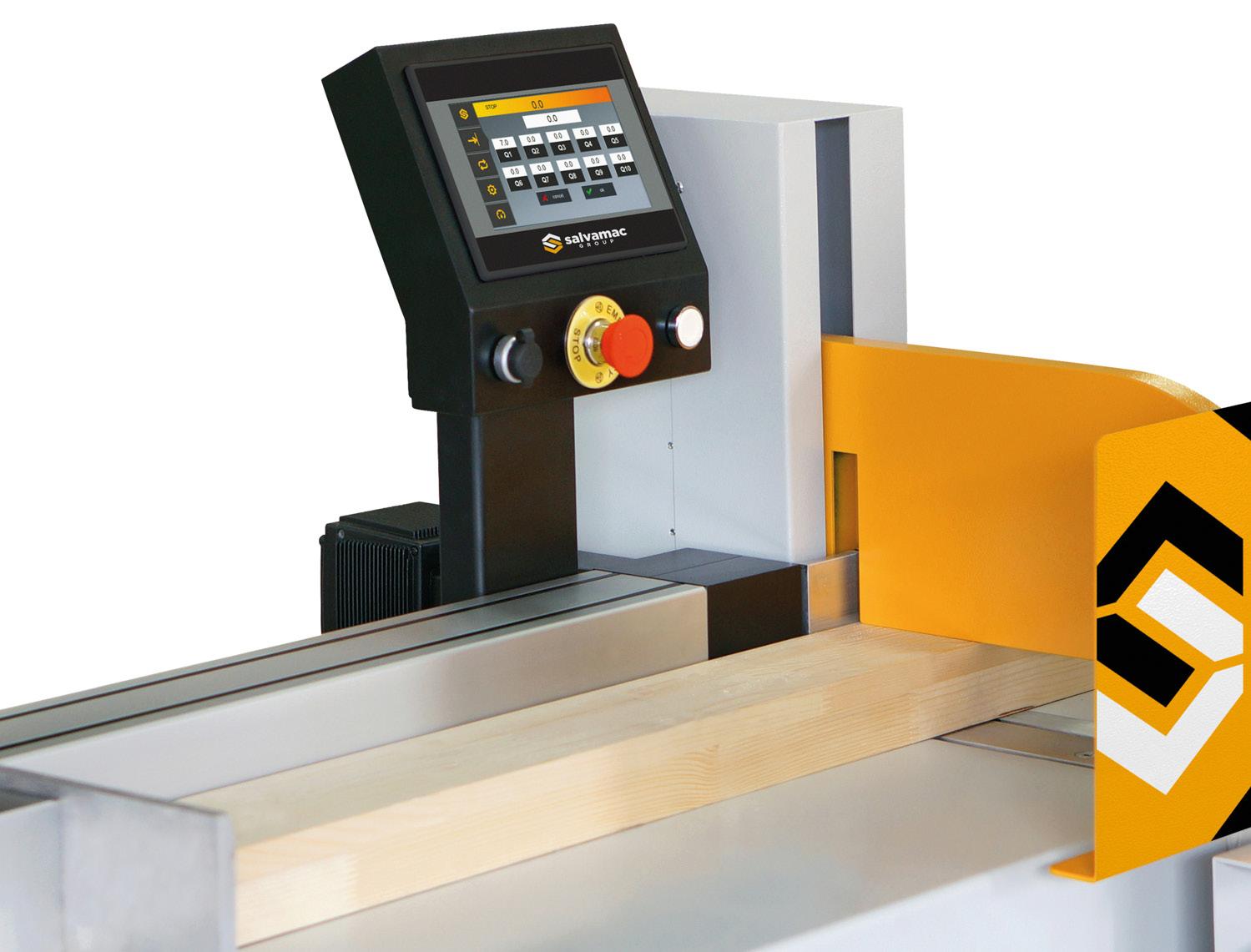

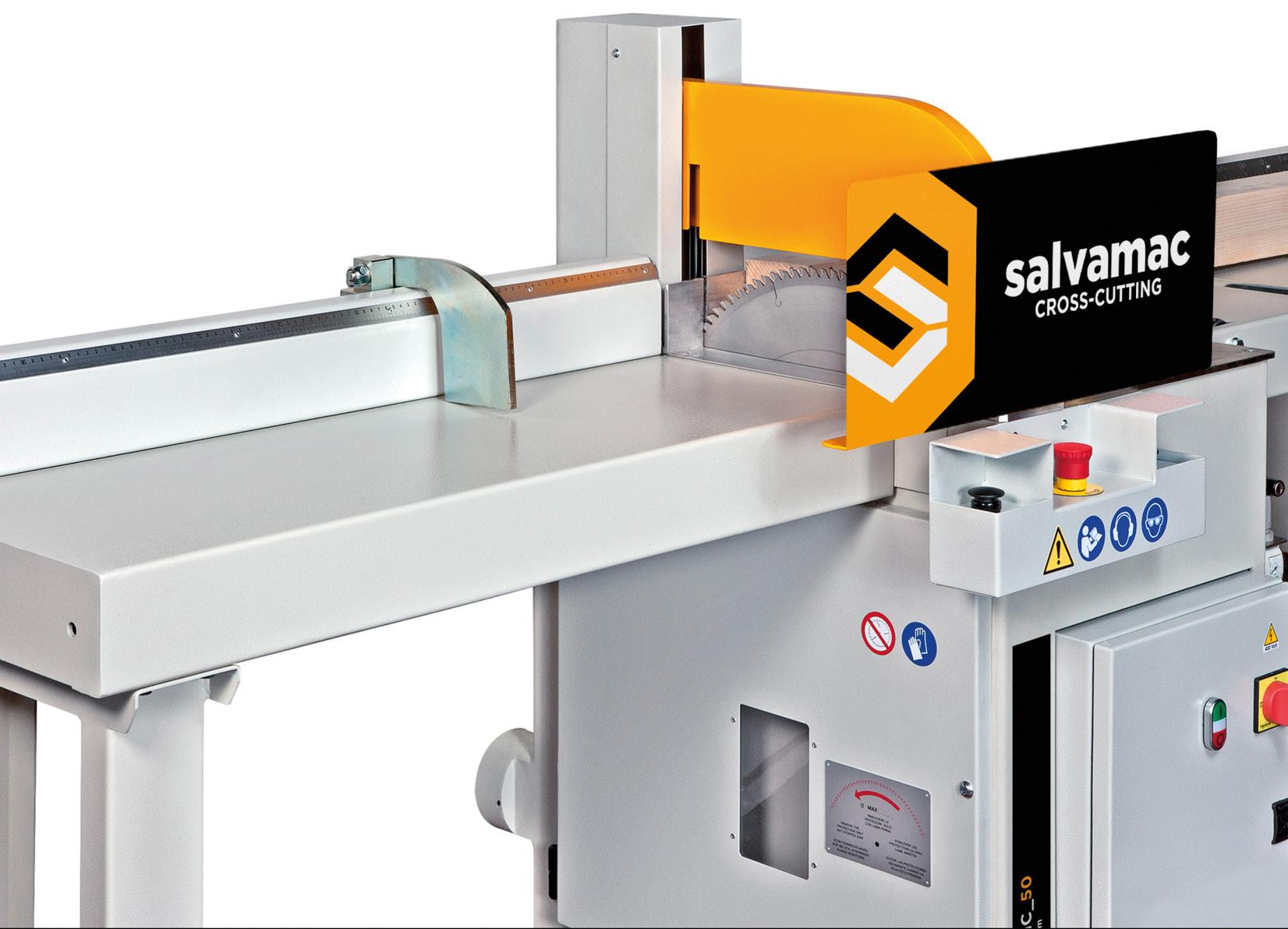
multiplies itself exponentially through three departments: the cross-cutting part, specialised in the cutting and optimisation of wood; the Air&Painting department, where the suction, air filtration and wood painting systems find a reference point; and the brand-new Salvamac Selection, an innovation that represents the natural evolution of the Salvamac project.
Its primary products (and best known in UK) are the upcut saws, equipped with devices that make them true cutting centres – the Classic cutting saws characterised by Salvamac’s philosophy.
Christian continues: “Our professional crosscutting saws are solid, resistant, compact. We build them with high-quality materials and complete them with functional options to optimise performance and efficiency.
“But not only solidity – we firmly believe that safety comes first. With our double-button device that is placed in an ergonomic position, and with the protection on the blade, you can work safely – we take care of the precautions.
“Finally, we want to make the job easy, and therefore offer easy-to-use woodworking machines. You have just to choose the stop and press the two buttons to start the cutting cycle, without any adjustment.”
Salvamac’s semi-automatic cutting saws, principally the Classic 40, 50 and 60 models, require limited investment but are a decisive step towards faster, safer and more efficient production.
“It is a coherent catalogue to which it is possible to add new aggregates that significantly increase the performance of these undoubtedly simple machines,” explains Christian, “also by means of intelligent loading and unloading systems, as well as automations that allow even small businesses or sophisticated craftsmen to move towards a completely new perspective.
“ Among the aggregates recently launched by Salvamac is the Salvastop measuring-stop device, a system that electronically manages the stopping and positioning of the boards or profiles to be cut, regardless of the material, with high speed and absolute precision, thanks to a state-of-the-art brushless electronic motor.
“Furthermore, the mechanical system has been designed not to require maintenance over time, while ensuring a high degree of robustness and precision.”
Salvastop can be installed on the Classic 40, Classic 50 and Classic 60 models, transforming previously entry-level models into semi-automatic cutting centres, which can be interfaced with the company’s management software (it should be noted that the Salvastop can also be installed on other machines, adapting them to all those applications where it is necessary to provide measuring and cutting operations in an extremely effective way).
Ziemowit continues: “We have worked hard to create the exclusive software very easy to use, thanks to immediately understandable and effective, complete, powerful and flexible graphics.
“It includes five different sections and two different modes, stop or push. Also, it has a 7in touchscreen in an optimum position for reading and programming – not forgetting the included and installed internet teleservice software.
“Due to an innovative technological concept, we have also created a new anodised aluminium beam section of 100 × 100mm, reinforced and with a large thickness to the profile edge.”
This beam has three sides, with groves to adapt and install the structure. One side is a flat fence, to favour the sliding of the wood on the guide, so avoid wear and dust problems.
Thanks to the scale of this solution, the pusher carriage reaches a movement speed of up to 60m/min. The transmission system has a 32mm wide-toothed belt, with high-precision internal steel cables, ensuring a wide capacity and a very high positioning tolerance.
The machined steel heads are robust and independent, designed to have a long life, highly reliable and precise, while the compact Servo Drive electronic motor guarantees simplicity, reliability, durability and efficiency. With this innovative technology, customers can manage closed-loop positioning, checking the position at any time – even in case of heavy efforts and accidental external pressure.
The motor, which is mounted in a pulling position, has a power of 11Nm, and the electrical and electronic inputs and outputs are integrated upon the engine itself. Finally, the emergency and start buttons are ergonomically positioned, to better facilitate the operator’s work.
www.salvamac.com
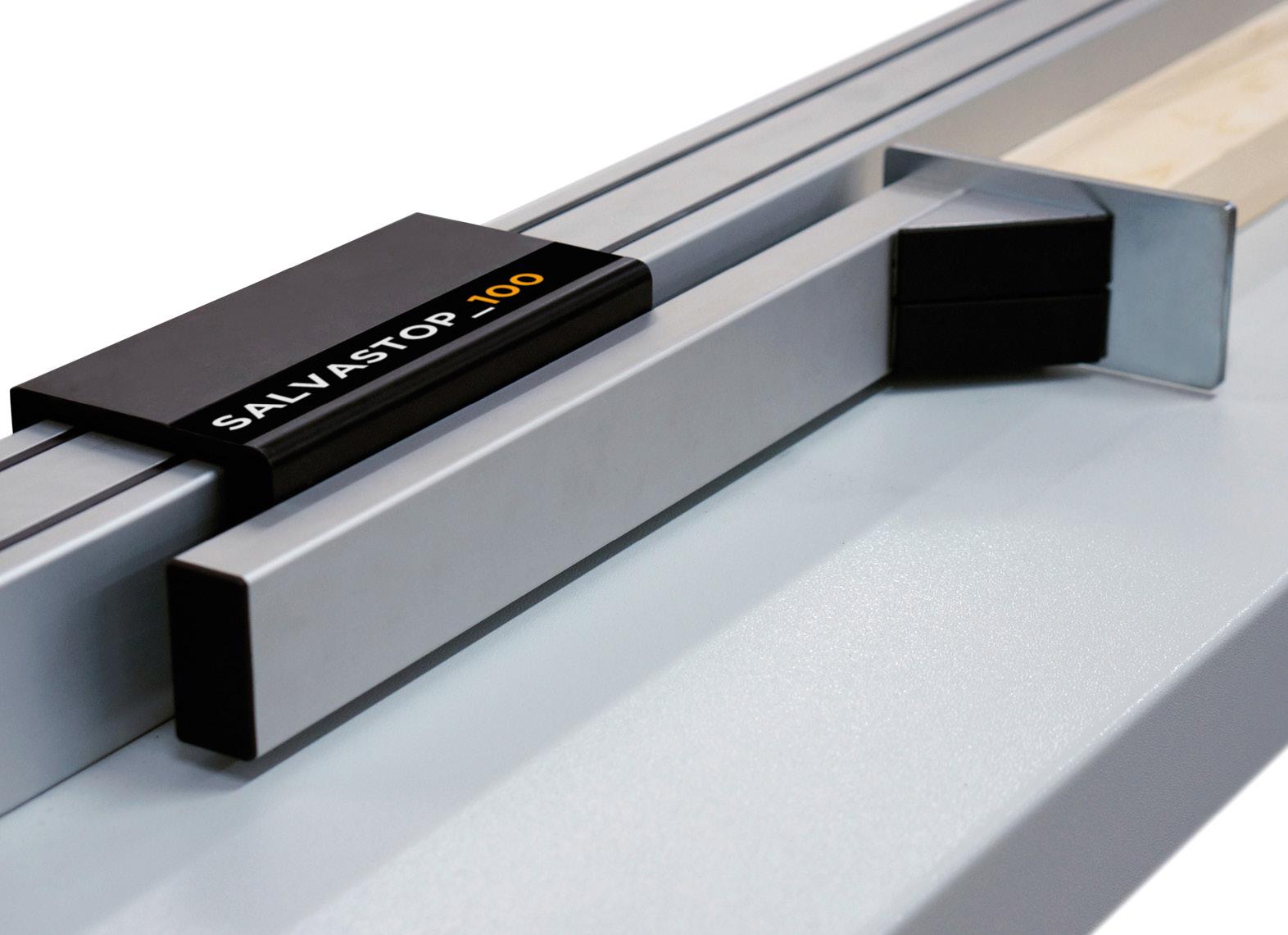
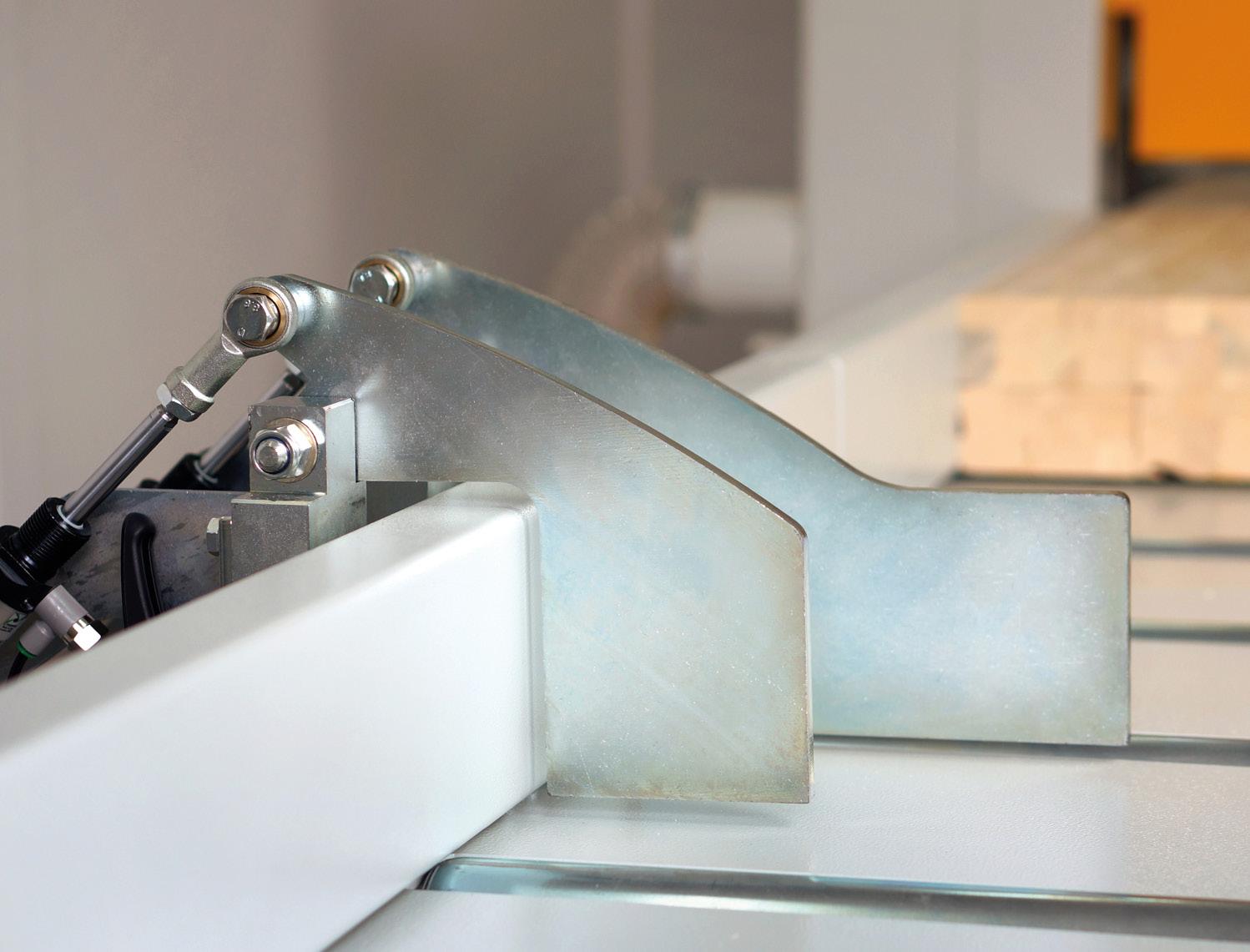
The COATIFY performance dashboard offers detailed, clearly structured and attractively presented reports for each integrated system. Current characteristic values – such as coating time, system status, number of coated parts or conveyor section – can be displayed and contrasted with characteristic values from comparative periods

Wagner expands its IoT platform with new functions and entry-level version, COATIFY.light
The system’s performance monitoring – including data on machine status, number of coated parts per minute, coating times, and much more – is presented in the form of clear diagrams
In 2019, Wagner successfully launched the COATIFY web-based information and management platform, which is used for the intelligent visualisation of coating systems. The IoT platform can be accessed via PC, tablet or smartphone, and enables secure access to production data from anywhere in the world, at any time. Additional functions, and a special entry-level version called COATIFY.light, are now available.
COATIFY provides clearly visualised key figures, live productivity monitoring, information on the exchange of spare parts, operating instructions with a spare parts list, and an interface to Wagner’s remote maintenance service.
The controls and sensors in the Wagner products provide the raw data, which is transmitted to COATIFY via a secure connection. The information enables reliable process control, short response times and anticipatory service measures. Everyone involved in the production process benefits from the high level of transparency provided by the COATIFY platform – whether operator, production manager, service employee, quality or process manager. System availability is increased, and productivity and quality are enhanced.
In addition to many other Wagner powder-coating systems, the SuperCenter powder centre and the ELine variant, which has the maximum control scope of this coating line, are now COATIFY READY – they can be connected to the platform. Soon, the entry-level variant of the E-Line and the SprayPackE automatic control unit will also be compatible with COATIFY. Plans are currently under way to also visualise liquid-coating systems in the future.
The platform has been enriched by several functions. The user can trace details of past jobs, including the used recipe, coating material and other parameters. Recording and tracing of application data of the EPG control units used, – for instance, the setting of the air or high voltage – is now also possible.
These new functions mean that certain parameter settings can be traced retrospectively. The production manager or quality manager, for example, thus receives even more valuable information on how quality can be optimised in future coating jobs.
Furthermore, one of the new features is that, in addition to automatic coating, the proportion of manual coating in the production process can also be displayed. In the Performance Dashboard, the data is no longer only displayed per day, but also per shift. The charts update automatically at regular intervals. This means that the most up-to-date data is always displayed without having to retrieve the status manually.
The user can now also choose between two COATIFY packages. In addition to the comprehensive complete package, which offers continuous data provision, the new version, COATIFY.light, is available as an attractively priced, entry-level package, with flexible billing models.
It has a reduced range of functions and displays all data from the last 365 days, retrospectively. Depending on requirements, companies can start with the lowerpriced basic version and have it expanded accordingly as soon as the demands on their own production monitoring increase.
www.coatify.net www.wagner-group.com
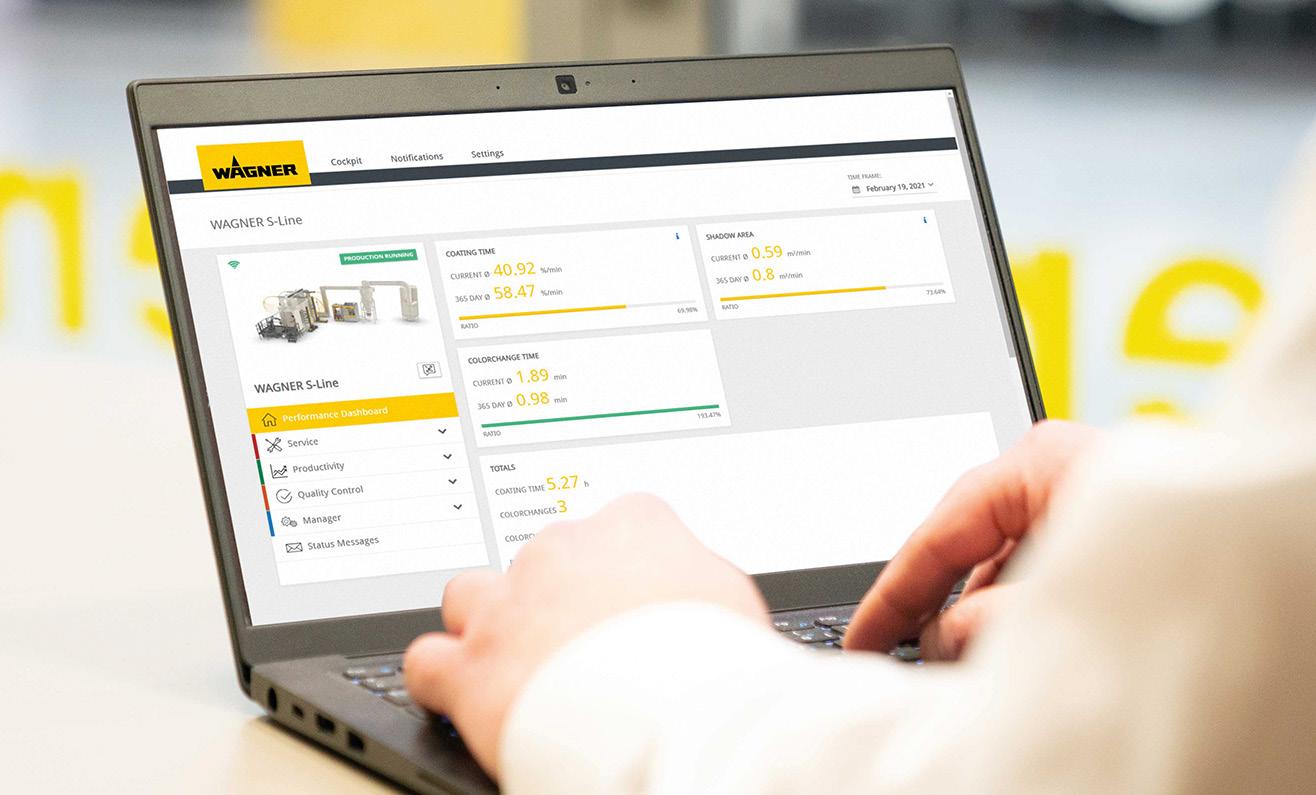

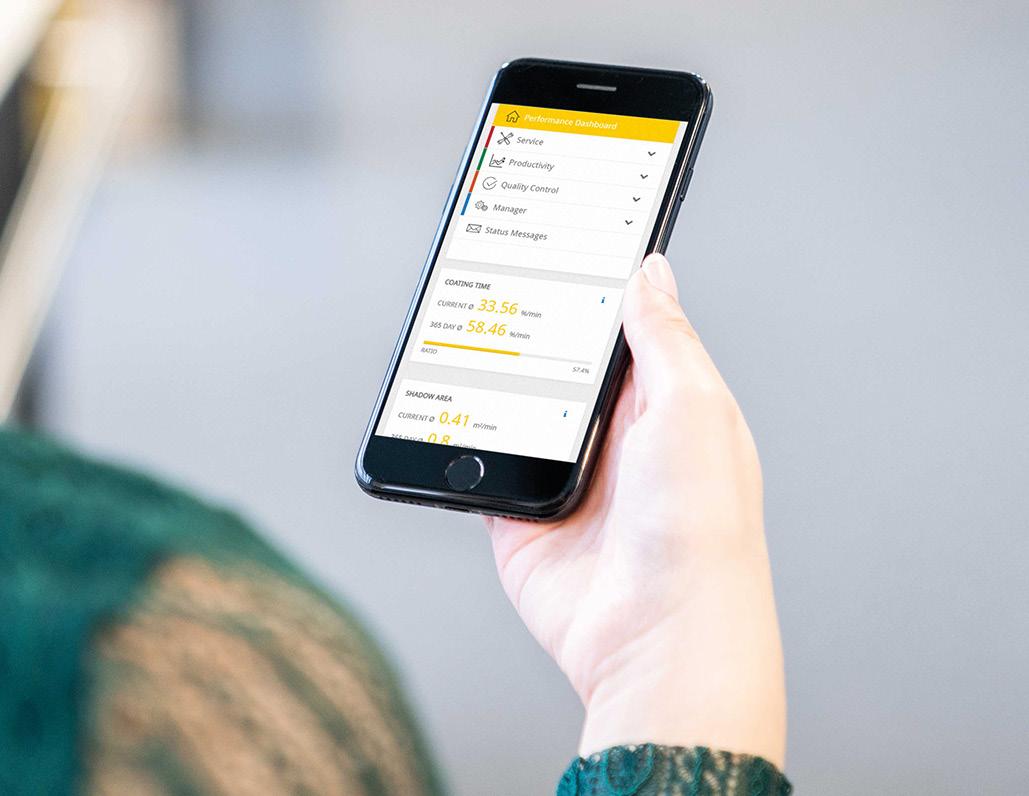
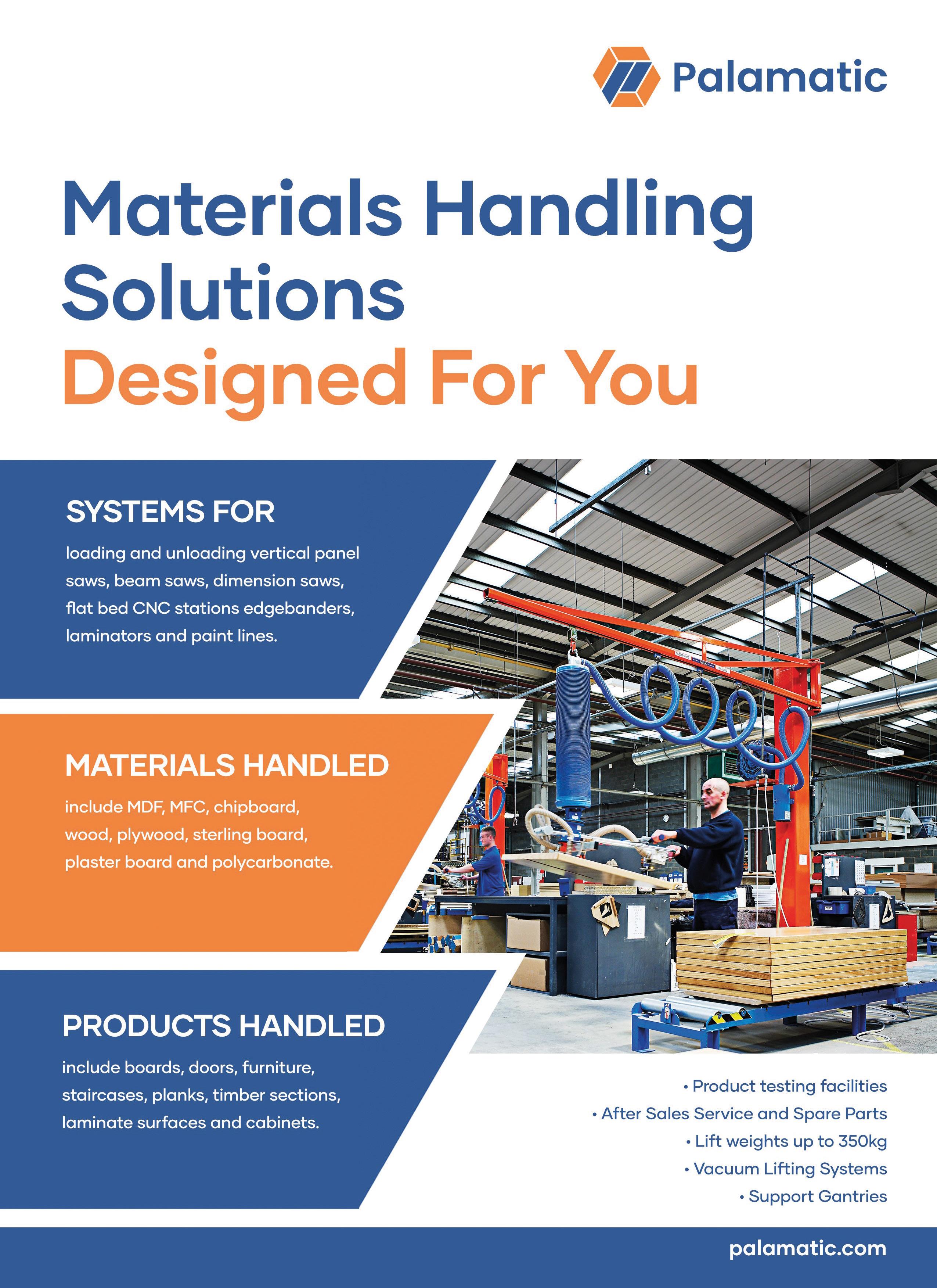