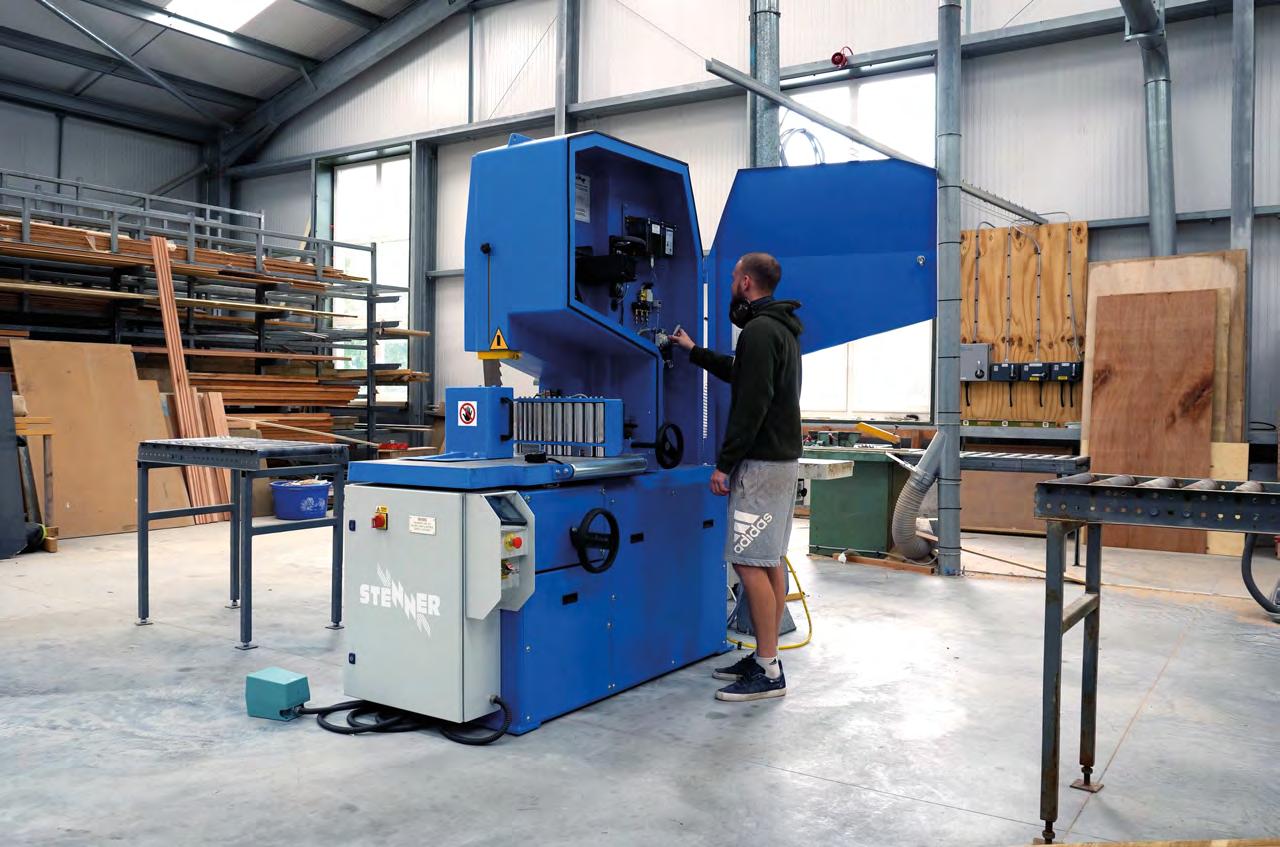
12 minute read
Installations
Bairds Windows invest in Stenner ST100R from Daltons Wadkin
Family run since 1994, Bairds Windows in Newton Stewart have developed an impressive windows and doors manufacturing facility, which has grown to over triple their original capacity.
Furniture & Joinery Production interviewed Malcolm Baird, fabrication director, about the heritage of Bairds Windows and the decision to invest in a new Stenner ST100R band resaw from Nottingham based machinery specialists, Daltons Wadkin.
What does Bairds Windows produce, and who for?
With over 20 years’ experience in designing and manufacturing high quality windows and doors, Bairds windows have now acquired a facility over three times the size of their previous workshop. Their customer base is varied, supplying PVC and timber products to domestic homes, commercial sites, and council buildings.
Why did you start looking for a new band resaw?
The old resaw started to show signs of ageing and inaccuracy. Limitations with cutting
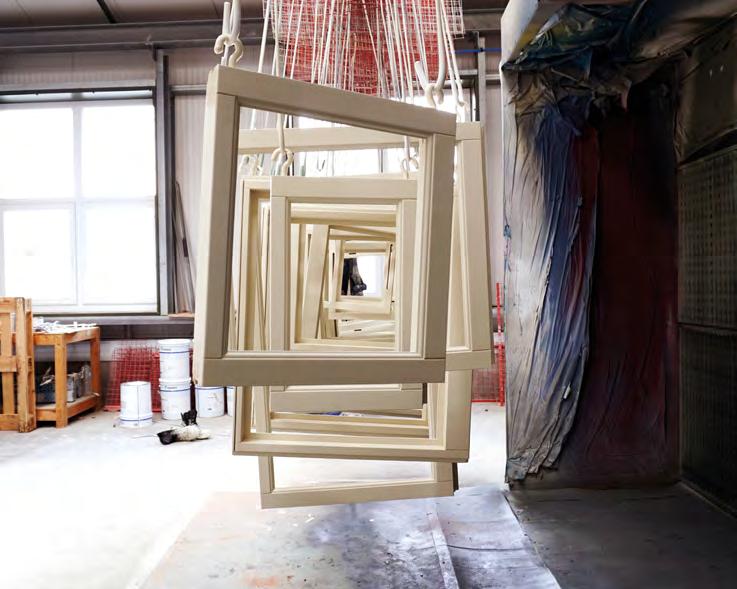
capacity, lengthy processing times and excess wastage prompted the decision to invest. “We had limited deeping facility on the old machine. We’re hoping to supply timber weatherboards, so that was one of the main reasons why we chose the Stenner,” explained Malcolm.
When did you first hear about Stenner Machinery?
“My dad had always wanted a Stenner, it’s just one of those things,” Malcolm shared his dad’s enthusiasm for Stenner machinery. After already investing in a Salvador automatic crosscut saw from Daltons Wadkin, it was a visit to the W Exhibition where Malcolm and his dad, Eric Baird, saw the Stenner ST100R in action. The ST100R is a ‘pitless’ resaw requiring no special installation other than the requirement for mains electricity, air supply and extraction. Established in 1875, Stenner is a British manufacturer renowned for its ‘bomb-proof’ range of band resaws.
How easy is it to use the Stenner ST100R?
The Stenner has simplified the job for the operators, saving time and material waste, enthuses Malcolm. “What we used to have was more complicated to work – adjusting blades, taking the tension off. With the Stenner you just have to flick a button.” The ST100 range of resaws all feature pneumatic blade strain, factory set pressure guides and automatic blade lubrication.
What are the key benefits of the Stenner resaw?
“The key benefits are the accuracy of the timber that’s coming off the machine, and minimising the amount of waste,” Malcolm explained the financial saving incurred through less waste has been significant.
To further increase productivity, included as standard equipment on the ST100R, is a pneumatically operated radial arm feed which is activated by photocell.
As standard the machine incorporates a hand wheel for fine adjustment and a foot pedal override facility is also available as an option. This allows the operator to control the feed remotely while simultaneously feeding lengthy timbers.
Would you recommend a Stenner ST100R from Daltons Wadkin?
“Bairds would recommend a Stenner from Daltons Wadkin. The service was great, everything the sales director, Andy Walsh, promised was delivered.” Malcolm concluded with: “It’s the Rolls Royce of resaws”. Daltons Wadkin worked closely with Bairds Windows to offer a machine which not only fitted their current requirements, but importantly would also grow with the business over the next twenty years or more.
Investment in a Stenner resaw was not only a business decision for Bairds Windows, the personal goal of owning a new Stenner machine has now been reached. Furniture & Joinery Productioin and the team at Daltons Wadkin wishes Malcolm and Eric Baird all the best as they continue to develop their product range, and surpass their ambitions.
0115 986 5201 info@daltonswadkin.com www.daltonswadkin.co.uk
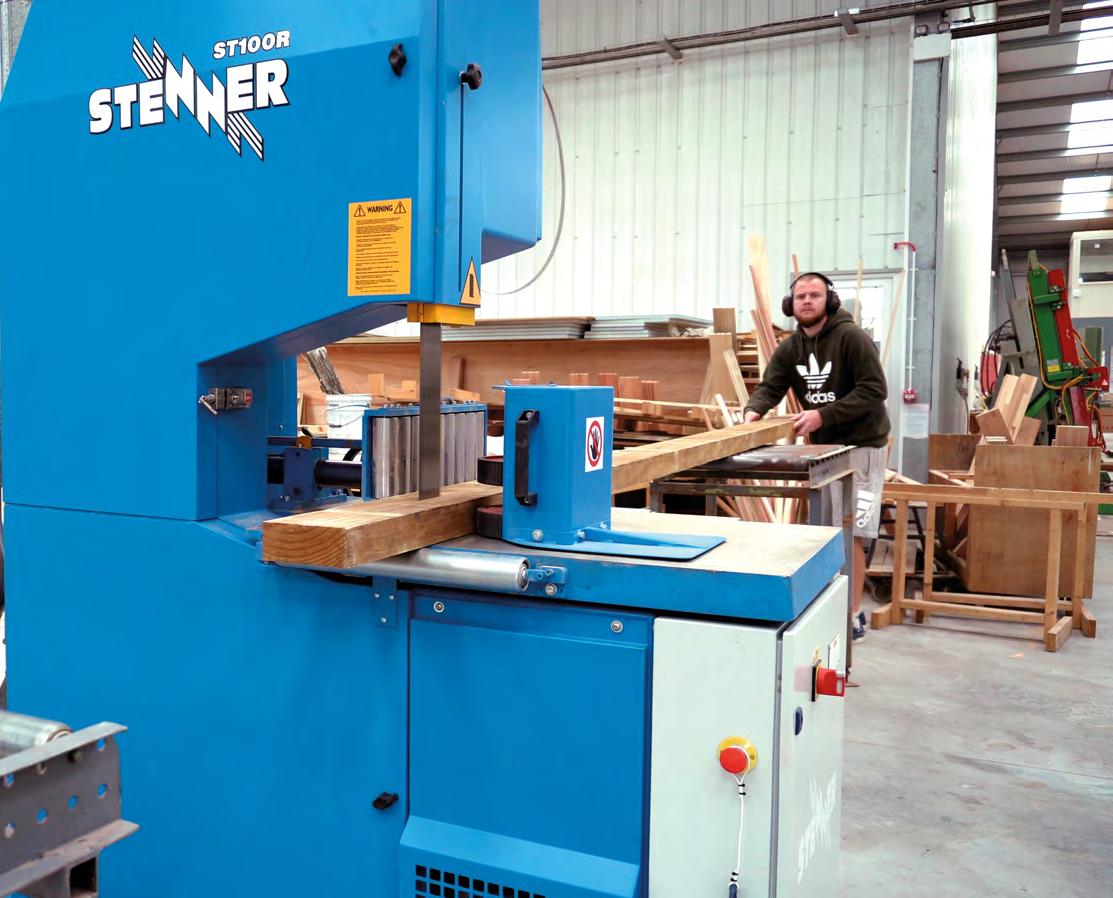
Alpha-Brush reduces time spent hand-sanding for bespoke furniture maker
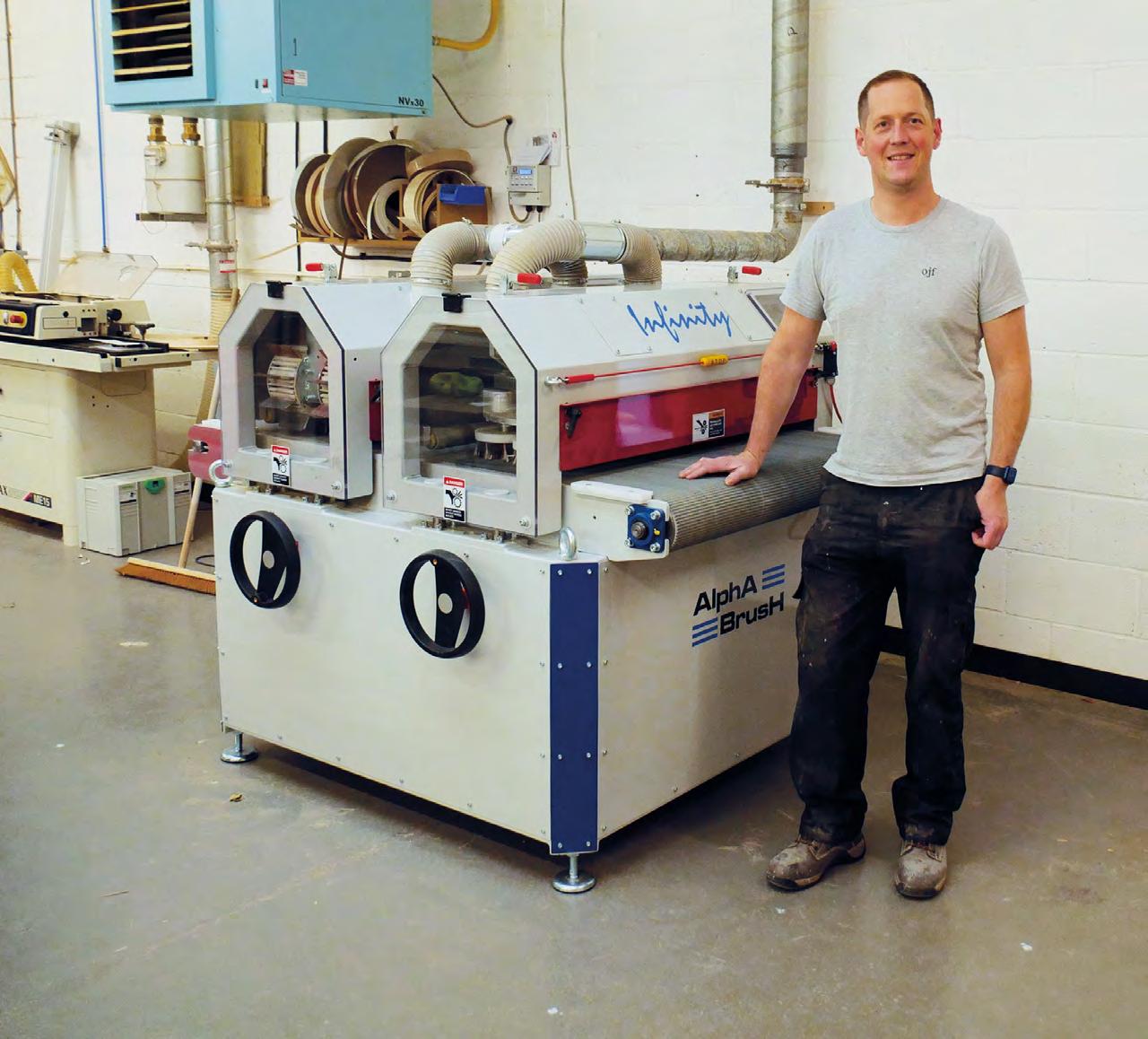
Based in Edenbridge, Oliver James Furniture designs and creates high quality bespoke furniture for the kitchen, bedroom or any room in the home and undertakes commissions typically all over London and across England’s home counties.
The company’s beautiful bespoke joinery is handmade and fully fitted by Oliver James Furniture. Whether it’s a fitted contemporary kitchen or a free-standing period bookcase, the company has the requisite bench skills to design practical, stylish and long-lastings solutions to its customers’ exacting requirements.
Oliver James Furniture’s managing director Gary Bishop says the company works closely with its clients to ensure each design is unique and reflects their individual style and personality. Each piece of furniture is hand-built by our craftsmen to exacting standards using only the finest quality materials.
“Our stylish designs are tailor-made to suit customer’s tastes, needs and lifestyle, be that traditional or contemporary. We pride ourselves on meticulous attention to detail,” says Gary, “and all our furniture is made on site in our modern, well-equipped workshop using a combination of traditional bench skills and a range of classical machinery all finished to our trademark high standards.”
Until recently, the Edenbridge-based firm used a variety of sanding techniques to achieve the desired finish on cabinet doors, including timeconsuming hand de-nibbing processing. Gary knew this was a situation which was important to be done well, but in doing so it tied up highly skilled craftsmen doing what is a fairly tedious and mundane task – a solution needed to be found.
Having seen a possible solution online, Gary reached out to Ian Brown, MD of Newark-based International Woodworking Machinery regarding an Alpha Brush Infinity Twin-headed sanding. Enquiries were made and it appeared that this was just what Oliver James Furniture was looking for.
But before going any further, Ian Brown suggested Gary dispatched some of his door frames and cabinet doors to be tested on the Alpha-Brush showroom machine – as he hoped, the samples came back in perfect order. Taking that on trust, Gary placed the order for a 1000mm wide 2S version which features two sanding units: the first unit was fitted with twin-railed longitudinal flap heads, and the second had unit twin rows of orbital flap heads to deliver an optimal finish – perfect for Gary to more efficiently deliver the high quality finish his customers demand.
In terms of what this means for Oliver James Furniture, Gary says: “Before we got this Infinity sander, we had two guys spending a considerable amount of time on and off doing this laborious task by hand. With the AlphaBrush machine it’s very simple to operate and maintain, and the work is done so much quicker.”
The Infinity machine is described as ‘the perfect solution for small- to medium-sized companies’ and is built with heavy duty frames, motors and components for years of demanding use. The Infinity is available in three sizes – 600,
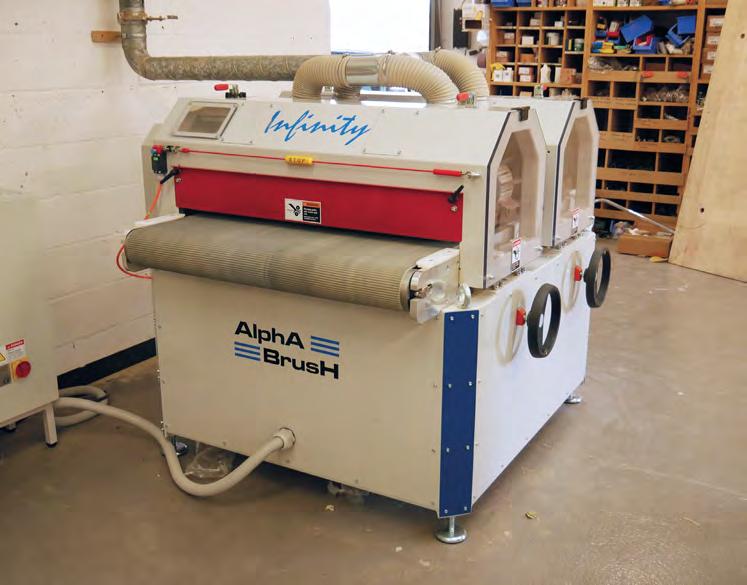
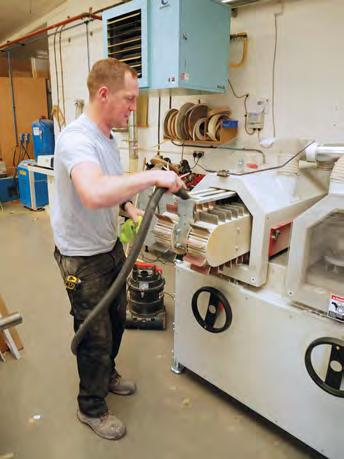
Above: Gary rates the easy access for cleaning, maintenance and to change sanding media
The Alpha-Brush Inifity sander is robust, performs well and boasts a compact footprint
1000 and 1350mm wide – and can be supplied with one, two, three or four sanding stations.
The machines have separate adjustable speed control for each unit as well as for the conveyor. The height adjustment is achieved by turning a hand wheel is measured down to 0.1mm with electrical counters. The Alpha-Brush machines come as standard with 2.2 kW motors, but can be upgraded up to 11kW, depending on application. They also come fully prepared with a vacuum table outlet so an external vacuum fan can easily be connected. The two sanding units are easily accessible for maintenance, removal and storage as required.
Asked what he liked about the machine, Gary said: “It’s already making a big difference to our business – it’s robust, straightforward to operate and maintain and doesn’t take up much room in the workshop – couldn’t imagine being without it! I would have no hesitation in recommending the machine – and Ian’s team at IWM.”
01636 918280 www.iwmachines.co.uk 01732 867 972 www.oliverjamesfurniture.co.uk
The Alpha-Brush Infinity sander significantly reduces the manual workload and achieves firstrate results
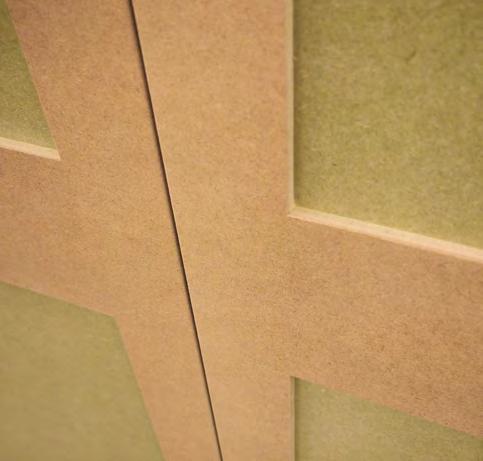
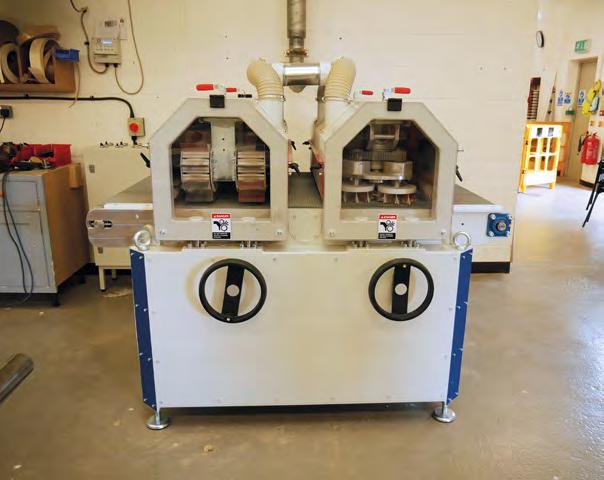
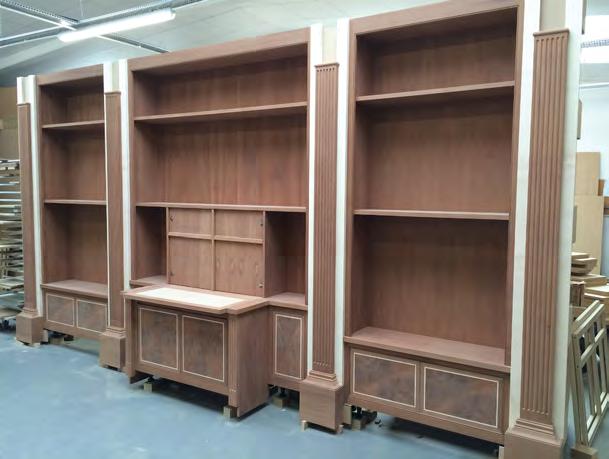
Sawteq B-130 panel dividing saw
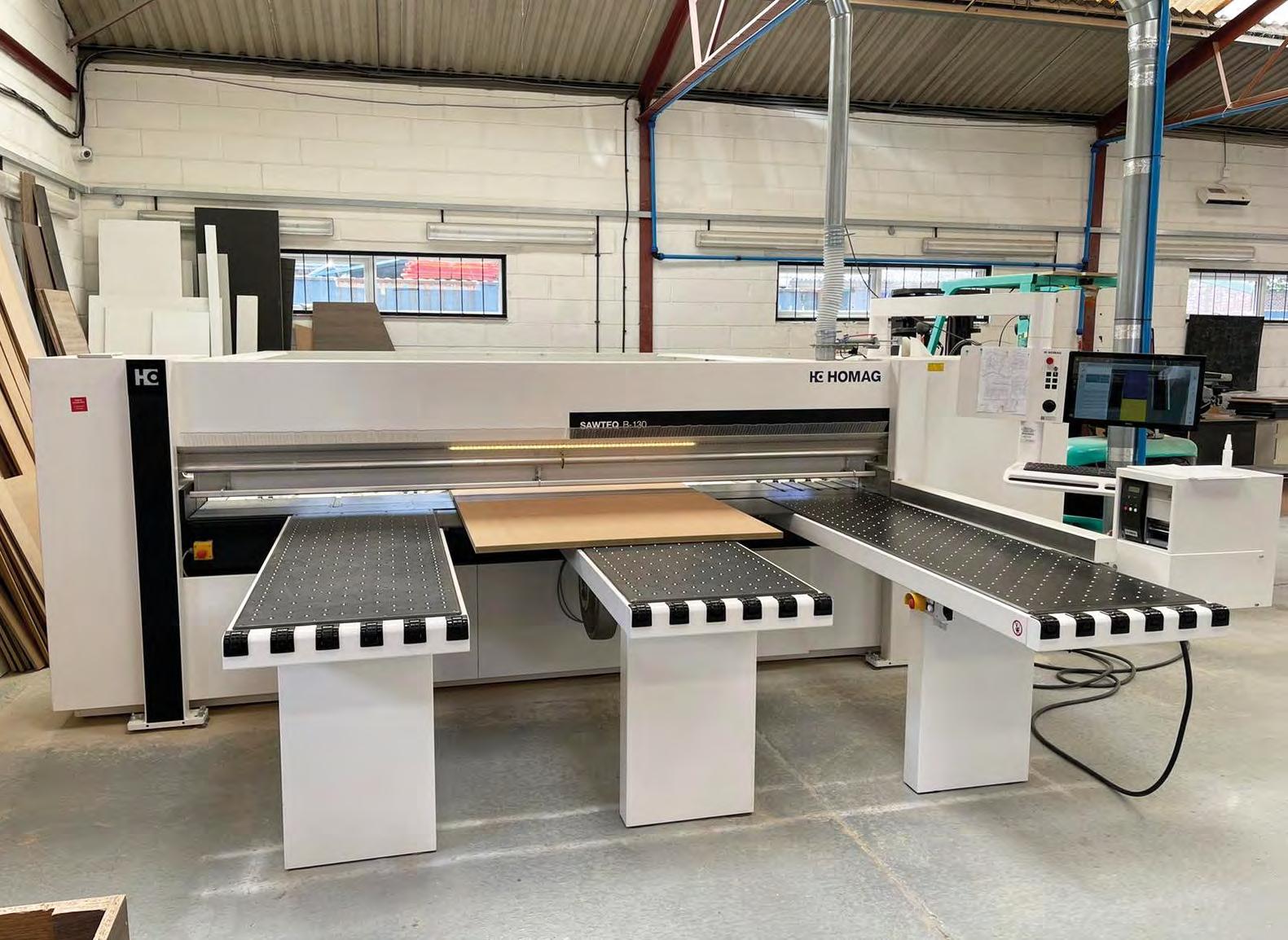
Evigol achieves a tenfold improvement in production rates with Homag machinery
Based in Clacton-on Sea, Evigol Ltd, a bespoke, luxury kitchen design and build company recently selected Homag as its preferred supplier to upgrade its wood processing machinery.
Established in 2017, Evigol which trades under its brand name OOSI, has completed over 100 major kitchen refurbishment projects. The company has seen a significant increase in demand for its products and services following its investment in four Homag wood processing machines.
The technologically advanced, highperformance machinery which Evigol purchased comprises of a Drillteq V-200 vertical CNC processing centre, an Edgeteq S-240 edge banding machine, a Sawteq B-130 panel dividing saw and an Edgeteq T-200 shaped part edge banding post-processing machine.
Commenting on the selection process for the new equipment, Igor Profir, managing director at Evigol said: “From the reviews we had read we knew that Homag offered one of the best ranges of wood processing equipment on the market.
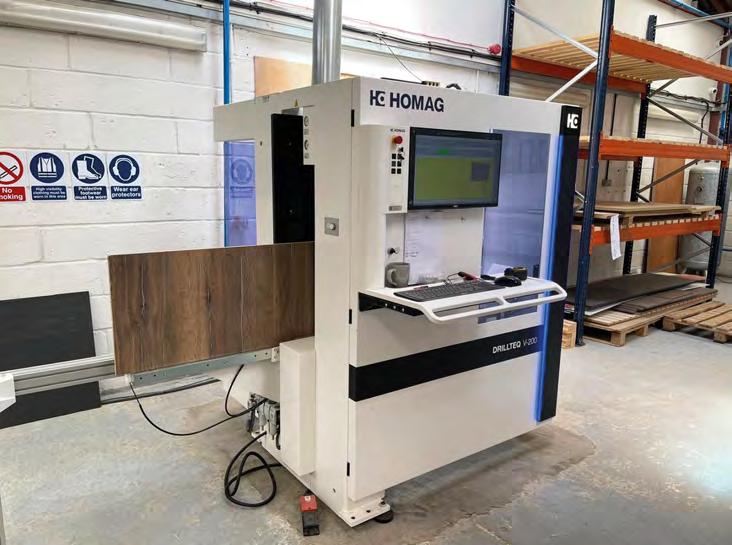
“To confirm our belief, we visited the Homag showroom in Castle Donington, Derby. At the showroom, our area sales manager, Charles Smith, guided us on the exact product specifications to suit our particular needs. His specialist knowledge gave us the added confidence that we were selecting the right equipment supplier.
“We had originally planned to purchase only one Homag machine but after reviewing our specific manufacturing requirements and capabilities with Charles, we confidently opted to purchase four machines instead.
“We were impressed with the manner in which our enquiries were handled and the outstanding treatment that we were given at the Derby showroom.
“The support and help Charles and the Homag aftersales support team have provided us with has been exceptional. When for instance we had a software issue with one of the machines, the Homag engineers resolved it quickly.” “The Homag equipment has also reduced production errors and wastage by 10%. As the machines’ software does all of the calculations for our wood processing, it has removed the human errors that we previously encountered”
Enhanced efficiency, competencies and customer acquisitions
Commenting on the productivity of the Homag machinery Igor went on to say, “The Homag equipment has automated a lot of our wood processing procedures, and improved our manufacturing efficiency and competencies.
“We are now able to complete big build projects ten times faster than we did previously. This additional production capacity ensures the timely delivery of our projects and has enhanced our ability to attract new customers with larger build projects.
“The Homag equipment has also reduced production errors and wastage by 10%.
As the machines’ software does all of the calculations for our wood processing, it has removed the human errors that we previously encountered.
“With the upturn in demand for our services, we’re planning to buy another Homag machine soon to supplement our range and further strengthen our manufacturing capabilities and efficiencies.”
For a demonstration or more information on Homag’s machinery or software, contact Adele Hunt at Homag UK on 01332 856424.
www.homag.com
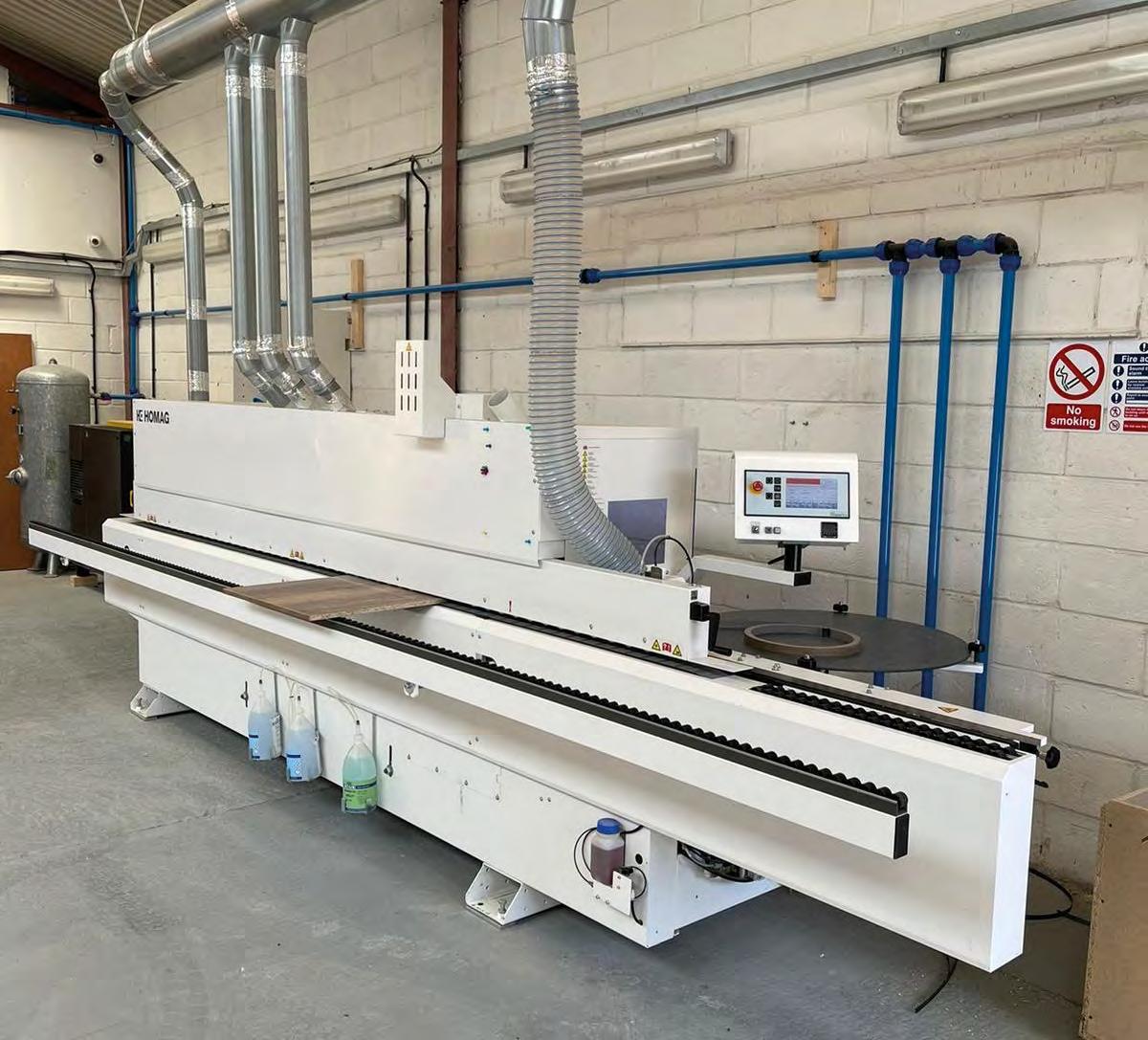
A Buckinghamshire furnituremaker has purchased a woodwaste heater from Wood Waste Technology to save money on heating and waste disposal costs.
Simon Taylor Furniture in Aylesbury is an award-winning company specialising in bespoke projects such as designing and making luxury fitted kitchens, bathrooms and bedrooms, as well as offering full interior project management solutions for every room in the home.
Having seen a woodwaste heater in use at another business, MD Simon Taylor realised that such an investment would be beneficial in helping him reduce energy and minimise waste in his own business.
Simon is very conscious about sustainability and his business’ carbon footprint, so did more research on woodwaste heaters and spoke to Kurt Cockroft at Wood Waste Technology.
He liked the idea of being able to recycle the MDF and chipboard offcuts into energy, rather than disposing of them in skips to go to landfill. There was also the benefit that the woodwaste burner would provide free heating to the workshop, making the current oil-fired heating redundant, saving the business money on both heating and waste disposal.
Simon received a grant from Low Carbon Workspaces for the woodwaste heater, and invested in a WT10 which was installed last year.
Simon says: “I’m delighted with the woodwaste heater from Wood Waste Technology. In my mind, companies that produce woodwaste can’t afford not to buy one! Especially as we’ll have had payback on the investment in less than 12 months!
“I’m very proud of the sustainable improvements I’ve made to my commercial property, including investing in a woodwaste heater and also in solar panels. Where we can, we avoid putting anything into landfill.
“All our timber offcuts are now used to heat
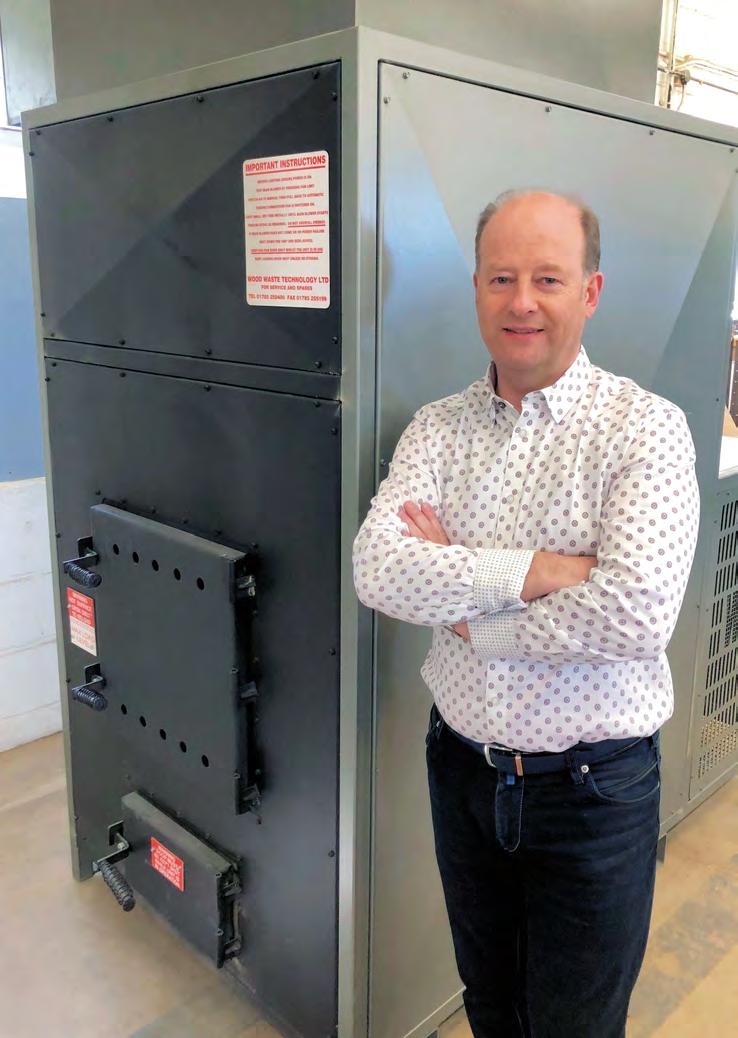
the building, saving on heating bills and the cost of skips. I now have a certificate on the wall that tells me I am saving 26.6 tonnes of CO2 a year – that’s the equivalent of four African elephants! I’m also getting a great payback on my investment. Investing in a woodwaste heater makes both economic and environmental sense!“
Wood Waste Technology’s years of expertise in woodwaste solutions have helped many companies reduce their waste disposal and heating costs.
As well as offering site survey, design, manufacture, installation and ongoing maintenance for new units, the company also services all types of woodwaste heaters and supplies genuine spares up to -60% cheaper than other suppliers.
In addition, Wood Waste Technology is the UK official distributor for Gross Apparatebau, a German manufacturer of dependable, precision-engineered shredders and briquetters, available in various sizes and specifications to suit all business applications.
01785 250400 www.woodwastetechnology.com www.grossuk.co.uk
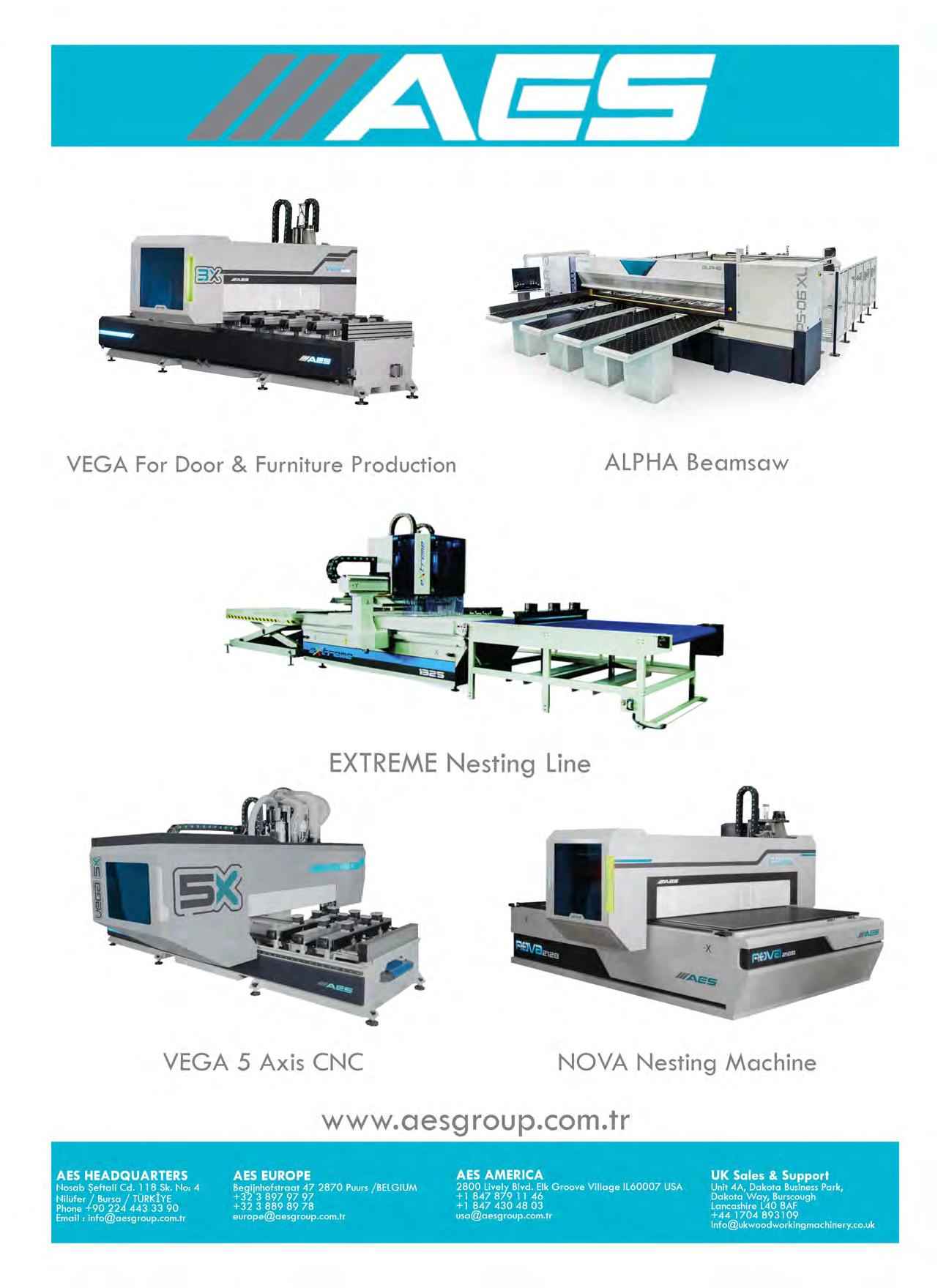