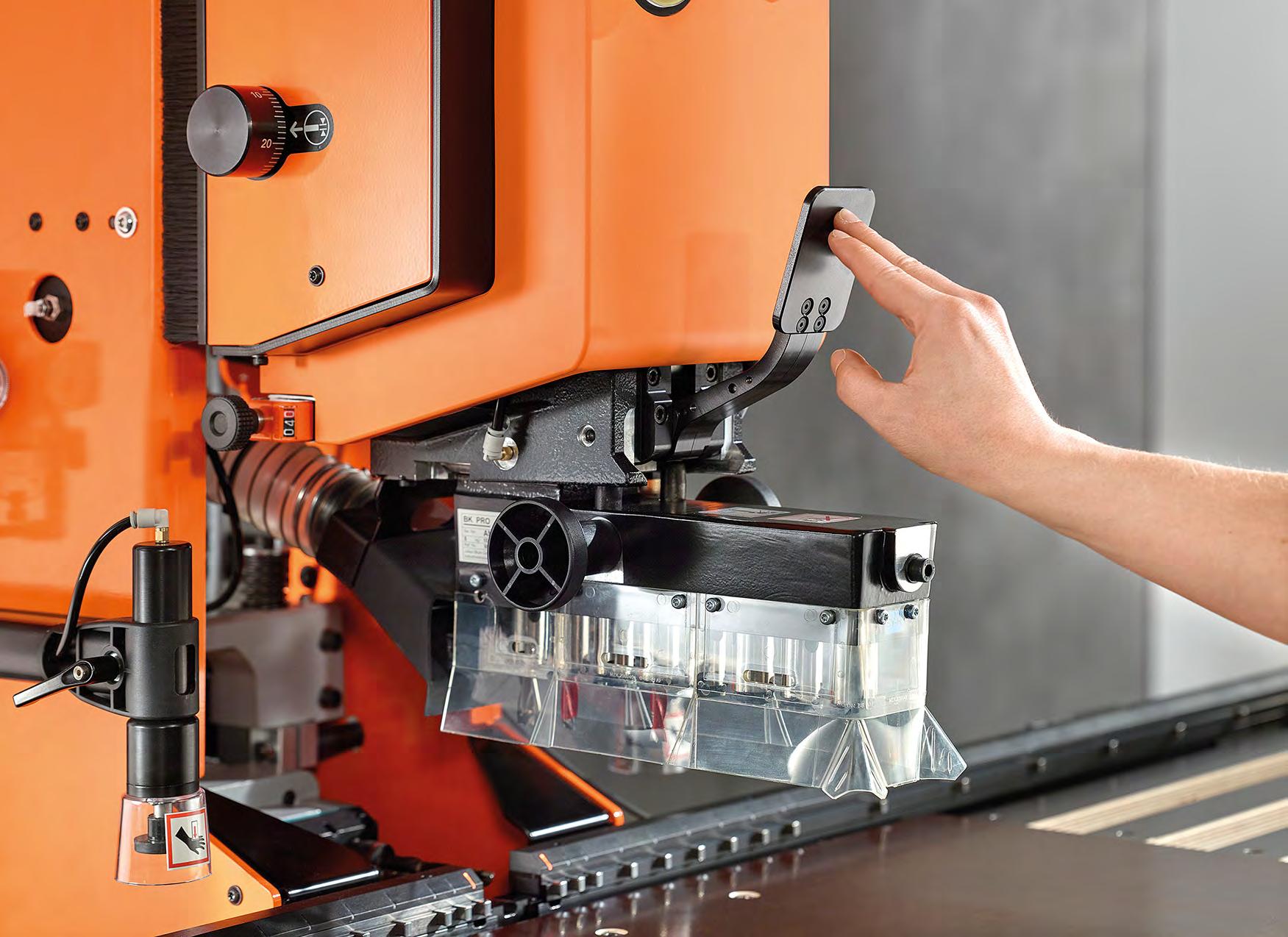
26 minute read
Products
Tortoise or hare, the MINIPRESS TOP from Blum has speeds to meet any needs
MINIPRESS top is now available in the UK, with even more features to aid all vertical and horizontal drilling operations within a single machine.
Blum launched the first version of MINIPRESS in 1984, but it has come a long way since then, and the latest version, available in the UK from September, is the most versatile yet.
MINIPRESS top means only one machine for all vertical and horizontal drilling operations. The horizontal drilling unit of MINIPRESS top allows precision drilling operations, making it useful for dowels and connectors. Speed and depth have been enhanced, with a new feature whereby, after breaking the drilling surface at high speed to avoid splintering, the drill will slow down to prevent burning, giving a much more precise, cleaner hole.
New features enable fast and accurate handling, helping the user optimise work processes for more precision, efficiency and quality. Combined with EASYSTICK for dynamic handling of the X and Y axes, the MINIPRESS top is “a perfect package” for all drilling operations on cabinets, doors and fronts.
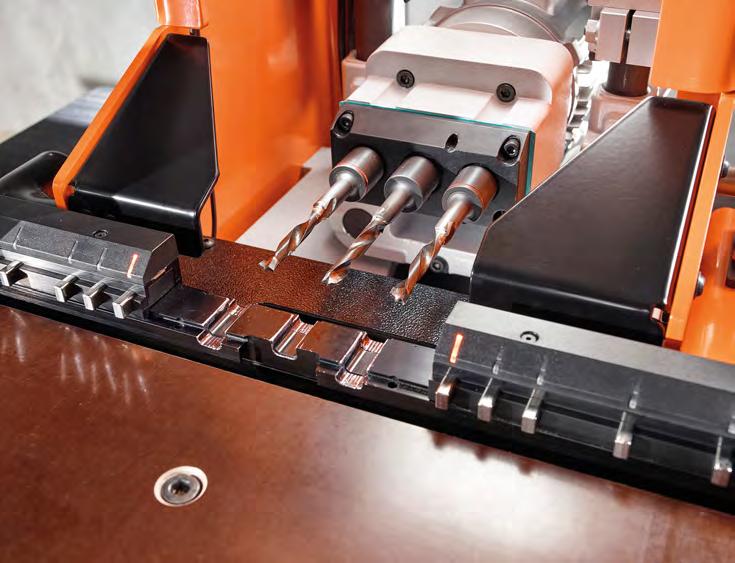
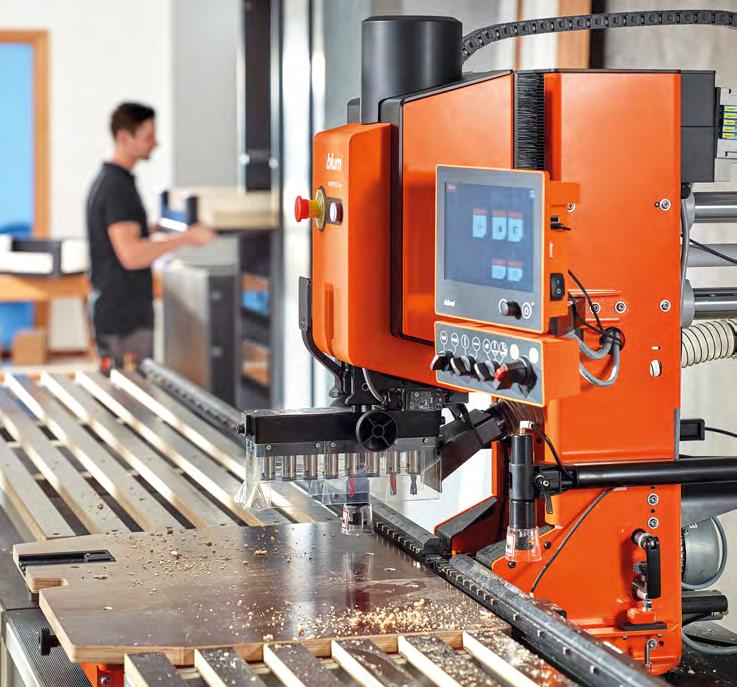
Services included
As always with Blum, service is of utmost importance, and the technical team is closely involved with the sales and commissioning process.
There are a number of set-up requirements, such as a three-phase power supply and pneumatic air supply, and the technical department will be in touch to ensure everything is in order.
The team is also highly involved in the training process, which, although relatively easy, is certainly necessary. Someone from the department will accompany the machine and help with set-up, and will customise the training so the MINIPRESS top is ready for use from day one.
As the machine is so versatile, it has an optional full suite of swappable heads that allow for different drilling patterns – customers may need additional training, which, of course, Blum is happy to provide free of charge.
Twelve-month, three-year and five-year services are included in the cost of the machine, as Blum recommends that it should be serviced regularly. If used and serviced correctly, the machine should last a lifetime – MINIPRESS version 1s are still in use today.
01908 285700 www.blum.com
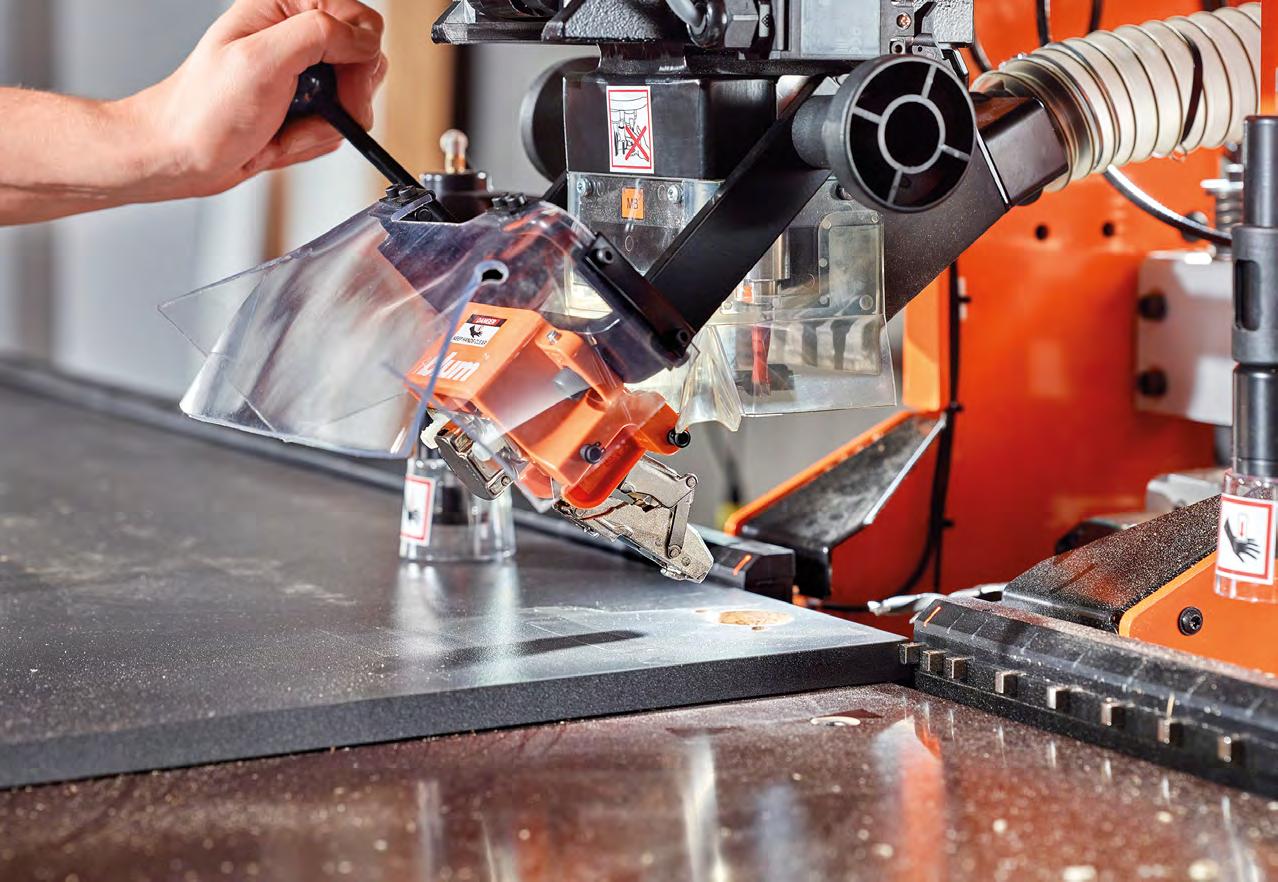
A blue world – colour in focus by Renolit
From oceans deep to skies high, blue symbolises life. So it comes as no surprise that it the most frequently quoted as a favourite colour. Currently blue is soaring high as it continues to be one the biggest colour trends for kitchens and interior furniture designs.
We are all comfortable with blue, after all it is all around us, often representing serenity and inspiration, and it’s a calming colour that denotes reliability. Mid-night shades of dark blue such as Indigo Blue or the blue grey tone Oria Blue both from Renolit’s range of new Premier Matt solid colours create a so-phisticated and desirable kitchen, ideal as the centre of any household.
Combine with light woodgrains such as Natural Kendal Oak or Vicenza Oak with bronze accents for a sophisticated on trend statement.
Renolit Premier Matt is a decorative film that is treated with an innovative Physical Surface Technology (PST) to create a very desirable matt appear-ance which is also extremely functional and tough while also warm and smooth to touch. It exhibits a number of superior, advantageous properties including anti-fingerprint, scratch resistance, stain resistance, easy cleaning and thermal selfhealing. It presents a smooth surface with low light reflectance.
For further information and to order samples go to interiorcollection.Renolit.com or phone Customer Care on 01670 718222.
www.renolit.com
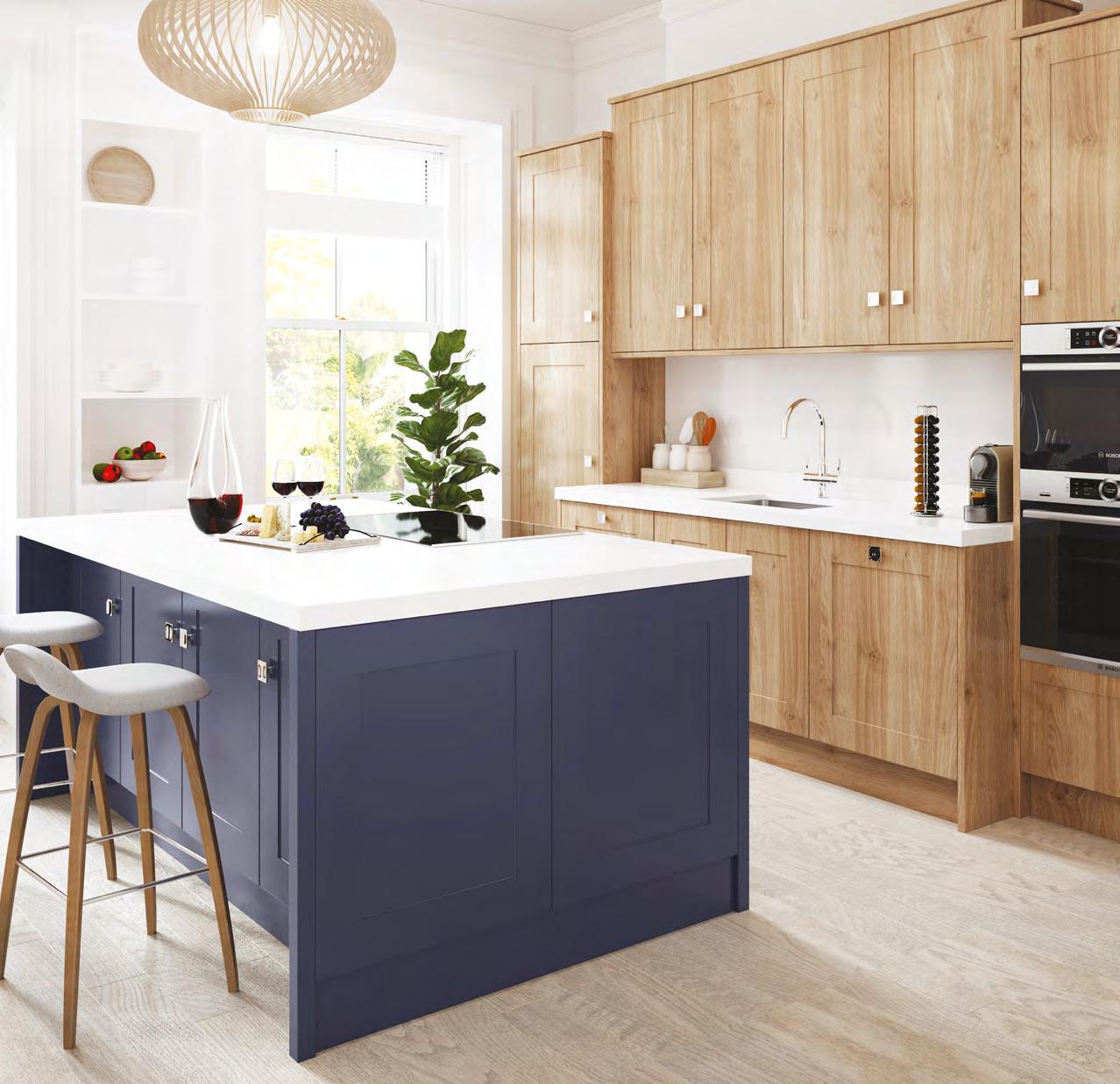
Ney’s most cost-effective solution for a seamless edge
Pre-glued edging with matching glue
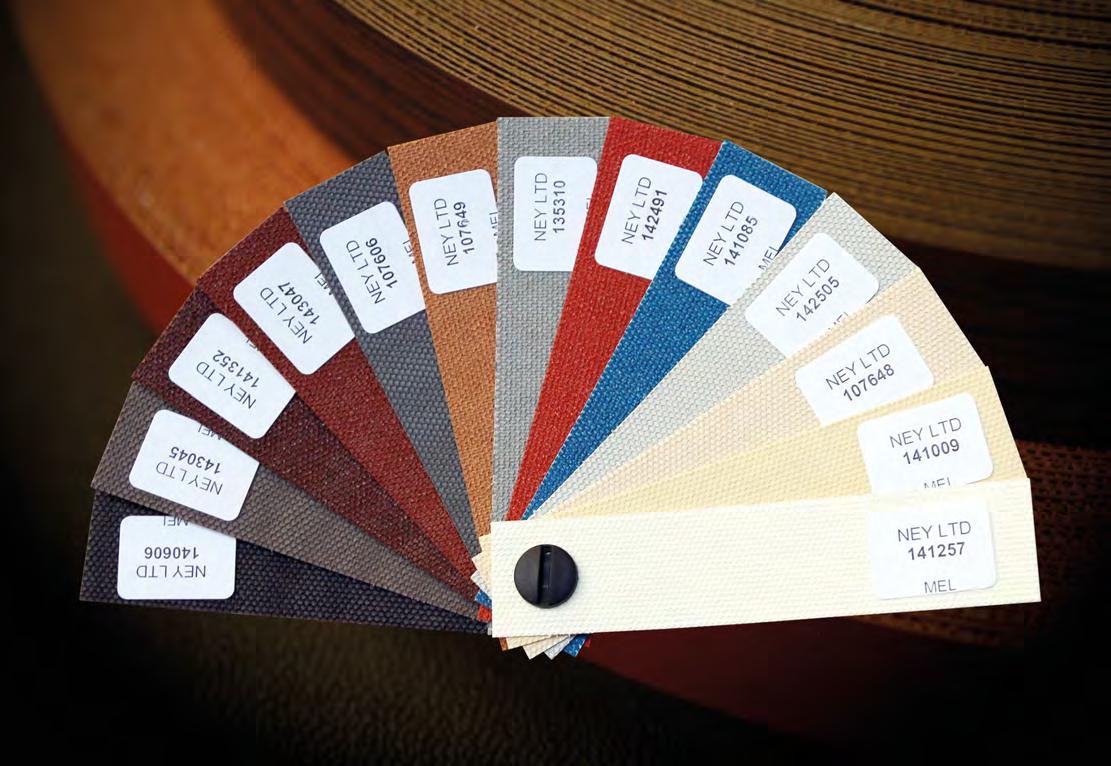
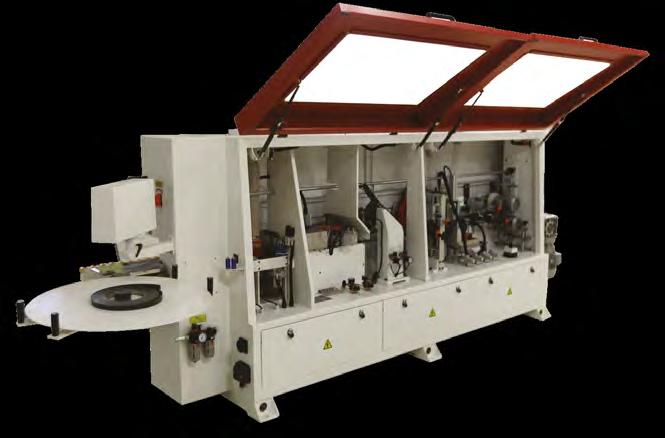
Ney is now offering a colour-matched glue when ordering pre-glued edging. By matching the glue to the edging and the panel, it will give a “never-seen-before” seamless edge, says Ney, therefore greatly improving the aesthetic quality of the finish.
Ney Airtronic edgebanding promises to provide a seamless edge while also providing some of the best bonding criteria for MFC and MDF. This is because the coated edgeband is knurled, and has an optimum adhesive gram weight which anchors deeply into the porous chipboard.
The EBM KDP 606 Airtronic uses hot air instead of a messy glue pot, and has all the premilling and finishing stations required for “the perfect edge”.
This unique coating process is prepared inhouse at Ney.
0247 630 8100 store.ney.co.uk
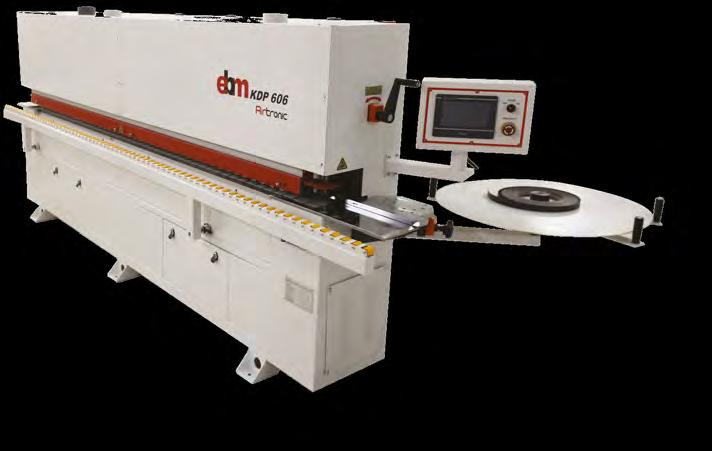
The significant optical quality makes Airtronic by EBM affordable for small- to medium-sized workshops
Cabinet hardware expert, Titus, has launched a second-generation range of its popular Tekform double-wall drawers. The new slimline versions feature a sleek and visuallyappealing design, and have 14mm side panels that maximise efficient utilisation of drawer space. They also incorporate the precision engineered Titus hydraulic dampers to ensure a reliable and consistent soft closing action, combined with low pull-out force.
Tekform slimline drawers are available in three heights – 70, 145 and 182mm – and can be supplied in a range of visually appealing finishes that ideally complement contemporary furniture designs. A further key benefit is that they use the same drilling pattern for runners as their predecessors, which facilitates mounting in existing products and designs.
Drawers are fast and easy to assemble, thanks to the EasyFix locking system used for the front-panel connector, which requires only hand insertion and a quarter of a turn with a screwdriver to lock the panel securely in place.
Reliable life-long ConfidentClose soft closing is assured by the use of the renowned Titus single-direction precision engineered hydraulic dampers, which smoothly slow down the linear movement of the drawer as it reaches the closed position but offer minimal resistance to movement when the drawer is being opened.
Installation of the drawers within the cabinet is fast and straightforward. Extended tolerances in cabinet construction can be accommodated without compromising accurate alignment, smooth and silent operation and excellent stability in the open position. In addition, variations of up to ±1mm in bottom panel width size are acceptable.
uk.titusplus.com
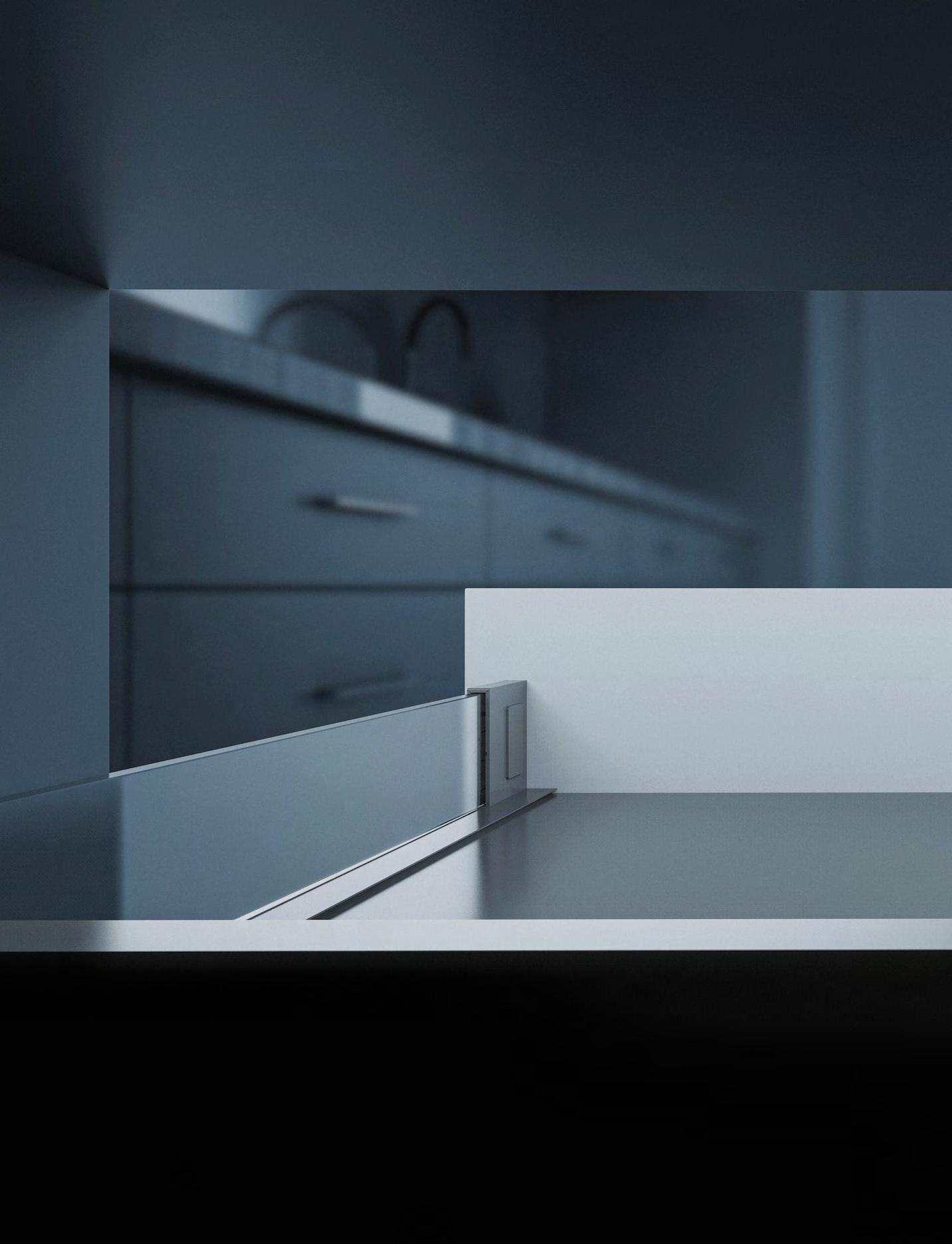
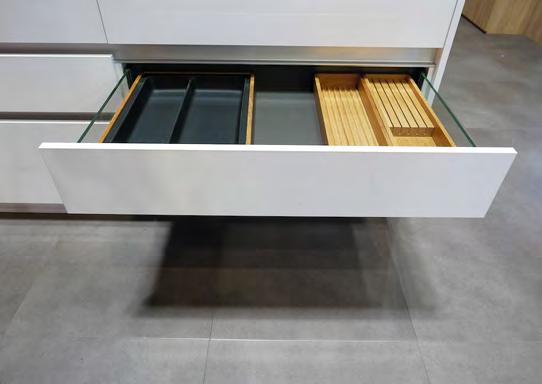
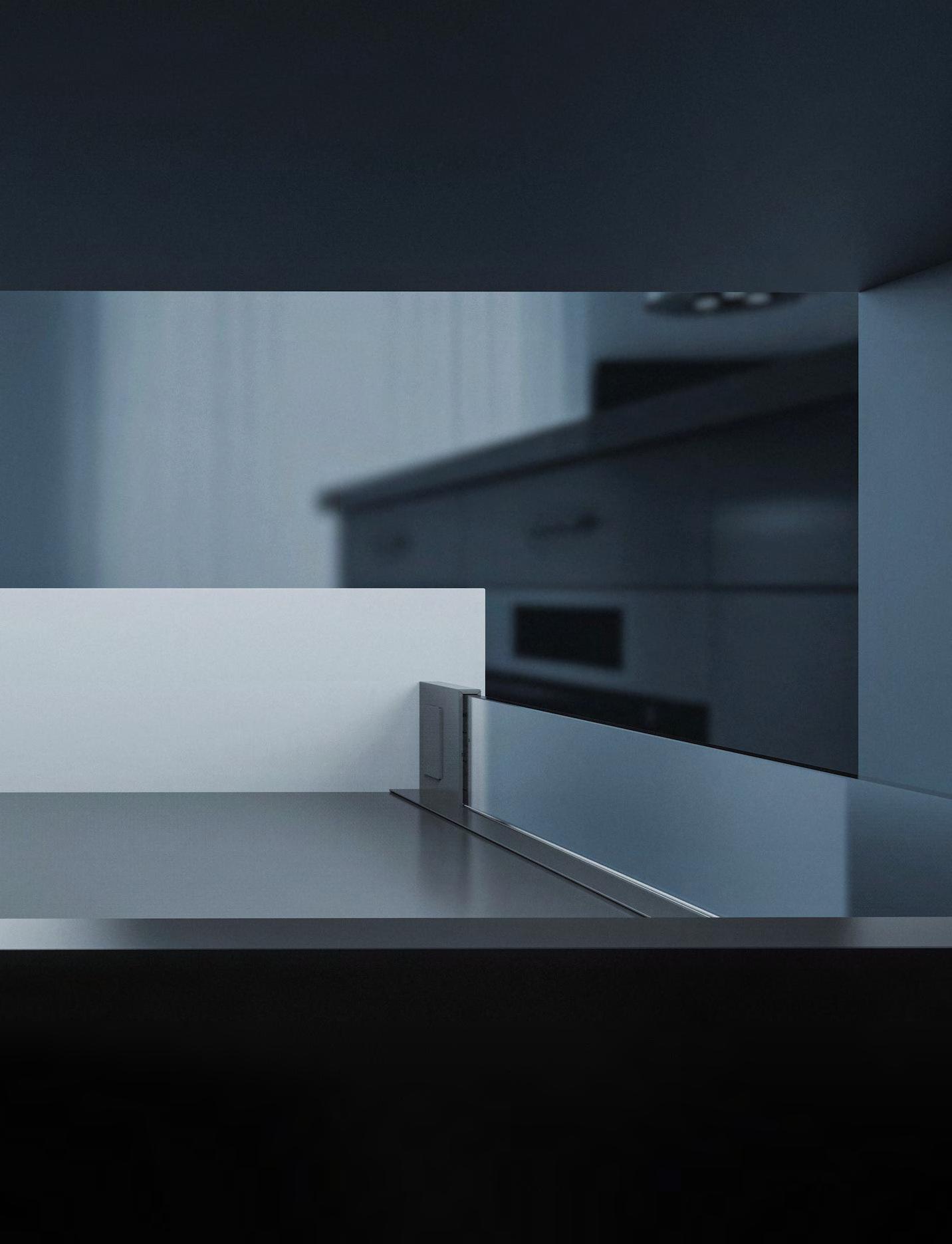
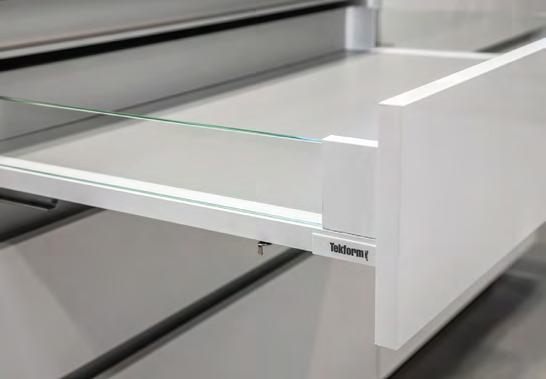
Ostermann with new surfaces – creative design for walls and furniture surfaces
Edging specialist Ostermann has long been established as an expert in other industryrelated fields, too. Their innovative furniture design products strike a strong chord with the market. Now, the assortment has been updated once more. The natural furniture and wall surfaces are versatile, lightweight and easy to process. Type in the search item #decorsinrolls on www.ostermann.eu to view all products and read up on their processing.
Whether in shopfitting and trade fair construction or in private interior design: thanks to Ostermann’s diverse surface assortment, furniture makers can swiftly endow rooms and furniture with an individual flair. A growing desire for natural materials is recognised here, combined with the benefits of a low-weight product. Applied to a workpiece or a wall, they can more than compete with their solid counterparts.
RollBeton Smooth: very smooth new concrete surface for furniture
To implement a loft look off-the-roll on furniture, Ostermann has just launched new colours of its concrete decor RollBeton smooth. The anthracite and light natural versions are distinguished by a particularly smooth and even finish with excellent colour consistency, suited especially for furniture surfaces.
Only natural sand is used as a raw material in the production of Ostermann’s RollBeton. Some air pockets add depressions to the look. The decor surface on a roll RollBeton smooth is available in dimensions of 3000 x 1000 mm and with a thickness of 2mm.

RollBeton with boarding: striking eye-catchers for shopfitting
The industrial or loft look can be described as positively ‘uncouth’. A little rough around the edges, the raw concrete look remains a preferred stylistic element in modern interior design. There are even two striking RollBeton variants with boarding for eye-catchers in shopfitting or trade fair construction: with plank widths of either 100 or 200 mm. A mineral substance is used to apply the handmade structures of rough sawn planks onto a thin fibre glass matt. The one-component mineral material is flexible, tear- and waterresistant. The decor surface on a roll RollBeton with boarding is available in dimensions of 1000 x 3000 mm and with a thickness of up to 4mm.
RollTravertin: industrial chic from limestone
The decor surface on a roll, RollTravertin, was freshly added to the range. Its dark-grey colour fits the style of the popular RollBeton surfaces. Unlike these, however, it is not a concrete surface but an imitation of limestone, more precisely the imitation of Roman travertine – porous stone that forms in freshwater springs.
Back in antiquity, this travertine was already used for numerous buildings in Rome and other Italian cities. The new surfaces are available at Ostermann in rolls of 1200 x 2800 mm, and with a thickness of only 1.5mm.
Furniture linoleum offers a wide array of design options. A new video on OstermannTV shows how to process the natural furniture surface.
Furniture linoleum: suits all requirements
Furniture linoleum is a traditional material from plant-based sustainable raw materials. It is an ideal furniture surface: easy-care, resilient and available in many colours. Lately, soft pastel shades and muted earth tones experience an upward trend: they induce a friendly and cosy impression.
Furniture makers can obtain the material from Ostermann in three different production levels that suit all requirements. For those looking to make their work very easy, customers can order furniture fronts with a linoleum surface ready for assembly via the Ostermann configurators.
“If you want to press the material yourself, but prefer to avoid the cutting effort, the Ostermann configurators are still the way to go,” explains Ostermann UK MD, Stephen Parsons. “Here customers can order customised linoleum cuts online. If you want to do all processing steps yourself, you can order all linoleum decors from Ostermann in rolls and by the metre.”
01905 793550 s.parsons@ostermann.eu www.ostermann.eu
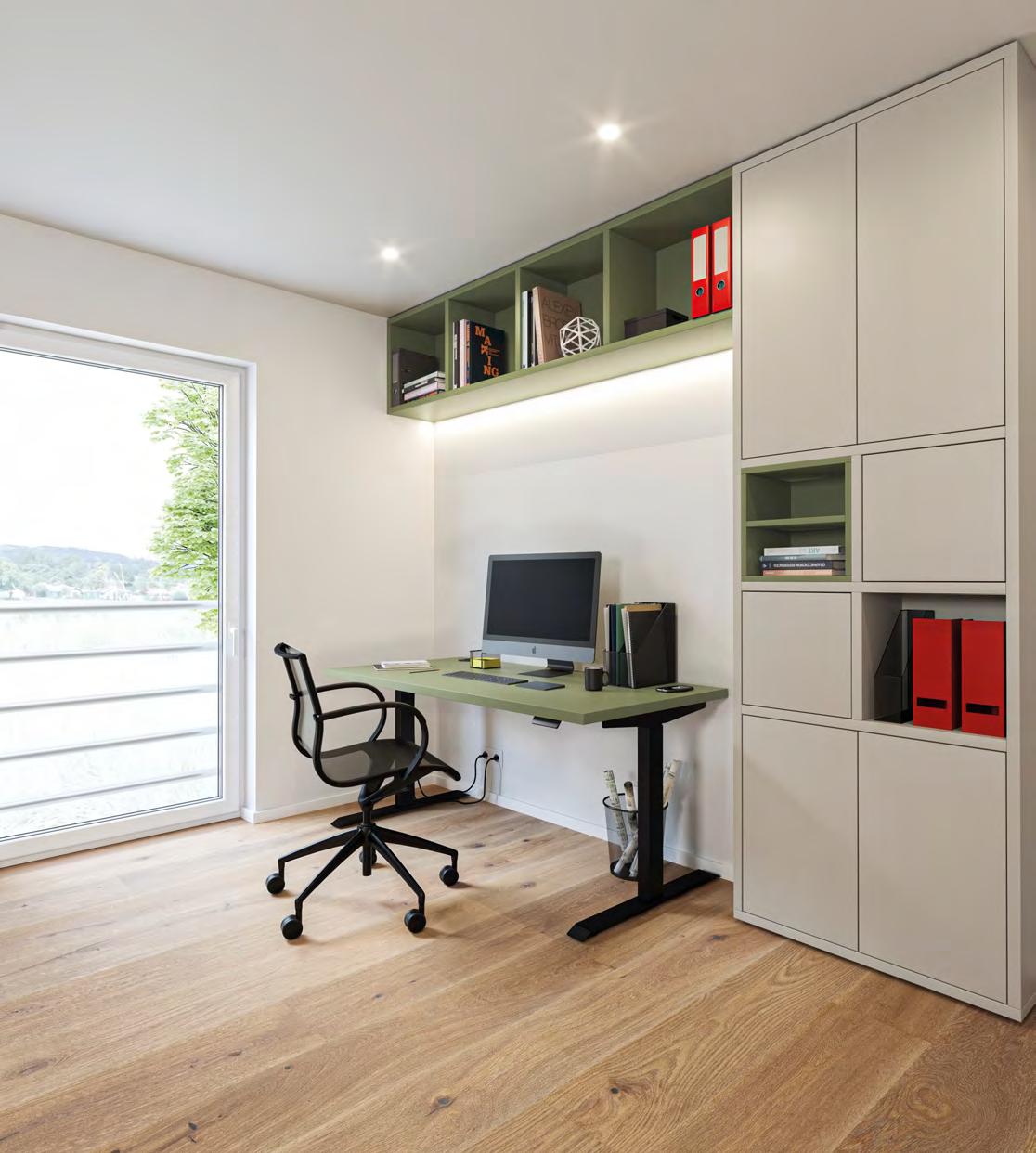
Fletcher Wood Products uses Cabinet Vision automation to simplify complex repeat commercial projects
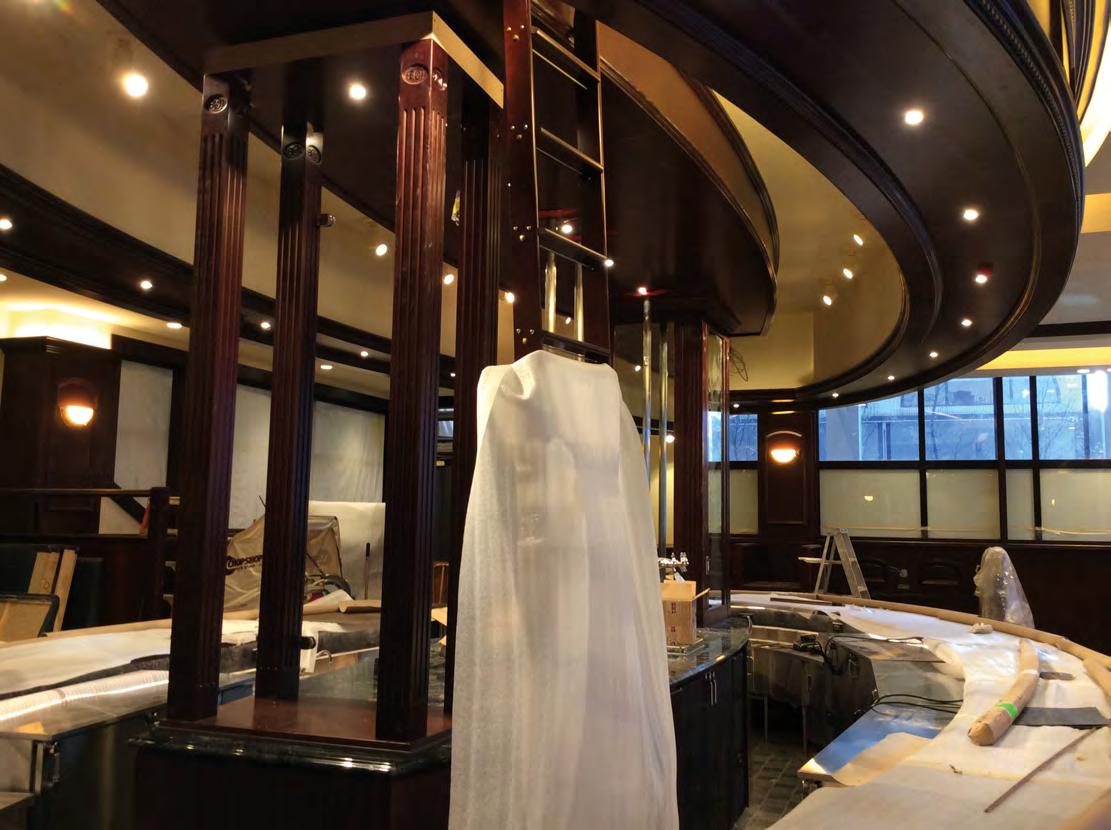
Making manufacturing smarter is all in a day’s work at Fletcher Wood Products, a 59-year-old custom commercial case and millwork company that has thrived for nearly six decades by continuously improving its processes.
Located in Fort Dodge, Iowa, the company was founded in 1961 by Bill Fletcher, an experienced craftsman who built a business on turning out high-quality, custom products. His son, Clark Fletcher, is now at the helm of the company – he utilises modern technologies to remain competitive, while continuing the company’s legacy of manufacturing top-notch goods.
A firm believer in the power of technology to help increase efficiency and reduce error, Fletcher implemented the Cabnetware solution for cabinetmakers in 1986 and, being an early adopter of CNC technology, acquired his first CNC router in 1993.
While Cabnetware helped Fletcher and his staff drastically cut time devoted to manually creating cutlists, shop drawings and assembly sheets, the integration of CNC machinery was a significant game-changer.
In 2007, Fletcher made the switch from Cabnetware to the Cabinet Vision Screen to Machine (S2M Center) solution, which delivers more robust design and project-planning functionality, as well as the ability to generate accurate NC code at the click of a button.
“The challenge is different today than it was when my father started the business,” says Clark. “For me, the challenge has more to do with the introduction of computers and software. You can tell when it’s time to change the way you do things – and today you need to use technology to stay in business.”
To begin a project in Cabinet Vision, the team at Fletcher enters the dimensions of the space in which the final product will be installed, and then virtually builds the project within that space. Once the project is drawn, shop drawings, cutlists and assembly sheets can be generated based on the design.
Among the Cabinet Vision functions utilised most often by Fletcher Wood Products is the ability to apply its own object intelligence to completed designs. Object intelligence eases the process of making design changes, including the ability to resize parts – even when they are included in assemblies. When part of an assembly is changed, the rest of the assembly will automatically adjust to that change.
“You add a part to the system, and you automatically add intelligence so that you can grow or shrink the part as the design progresses,” Clark says. “You can reuse it and change the overall dimension, and the other parts change with it.”
Cabinet Vision allows users to save and reuse any process, including those that include object intelligence. Reusing processes is especially helpful for parts that are very similar or identical, but any process can be edited and saved as an additional version of a previously saved process.
Keeping a process library makes it simple to save and select processes as needed.
“The most immediate return on being able to reuse parts and projects is that, for 75% of projects, you have to go back and change something,” says Clark. “The little bit of time you have to spend adding intelligence will save you time – without a doubt.”
For Clark, the proof is, as they say, in the pudding.
Having utilised Cabinet Vision to varying degrees to complete projects for four new 801 Chophouse restaurant locations, he has saved and reused processes for several project elements.
As solution functionality and his knowledge of the software has grown, he has increased his use of the system to tackle the tougher project aspects. As such, 95% of his work on the last restaurant location was performed with Cabinet Vision.
“As Cabinet Vision continued to be developed, new features were added,” says Clark. “I think that kind of continued development is great, and shows that they’re listening to their customers.”
The four 801 Chophouse projects were completed in 2006, 2011, 2016, and 2019.
Cabnetware was used for cabinetry on the 2006 and 2011 projects, while Cabinet Vision was used in 2011 to produce only the panelling for the 2011 job. In 2016, Cabinet Vision was used to build both cabinets and panelling, and in 2019 its use was increased to include the production of cabinets, panels, moulding, booth assemblies, oval bar walls, a bar top, bar soffits, window shutters, wine tower-panels and display units, and applied arch frames.
“In 2016, we used Cabinet Vision to create custom wine cabinets with special operations, as well as wall-panel assemblies with the necessary machining operations, and saved everything to the Cabinet Vision library,” says Clark. “In 2019, we were able to use the work from 2016 and enhanced the previous Cabinet Vision work by adding mouldings to the wallpanel assemblies to aid in accurate accounting of moulding quantities.”
For the 2019 project, Clark created full booth assemblies that included wall framing, wall panels with intelligent machining, frame assemblies for glass panels, and all necessary moulding.
To design the restaurant’s intricate oval bar, the company used computer-aided-design (CAD) software, and imported the file into Cabinet Vision.
“We used the CAD import feature to create the oval bar and all related parts to create all shaped parts and assemblies, which included an oval bar top, shaped bar rail, bar face panels, and shaped soffit panels.”
He also used Cabinet Vision to create a sliding shutter system, and assigned object intelligence to its top and bottom tracks, side jambs, casing materials, and parametric shutter assemblies. The intelligent shutter assembly allows for changing the slat sizes, slat spacing and slat angles by using custom attributes.
“One big time-saver for us was creating assemblies for all of the applied wall moulding frames that we supply,” says Clark. “This project had over 150 wall frames with 16 different radius top pieces. The assemblies allowed us to account for all of the straight moulding needed for the frames.”
As each assembly included a shaped hardwood part for a curved upper rail, Clark saved a significant amount of time by sending those complex parts to the S2M Center, where true-shape nesting was used to efficiently nest the profiles.
“Those 150-plus frame tops were optimised and code created in minutes, versus the several days needed on our previous projects to draw arches, create toolpaths, and manually create nests on various material sizes,” he says. “I can’t say enough about the power of the tool that we have in Cabinet Vision and all that we can do with it. You’re only limited by your imagination.”
www.cabinetvision.com
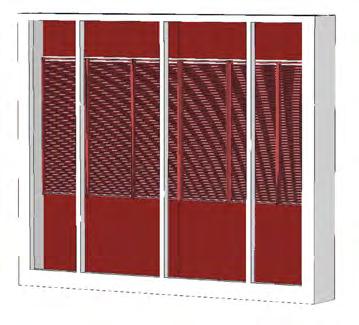
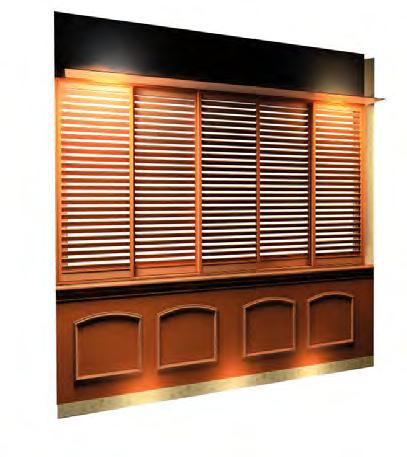
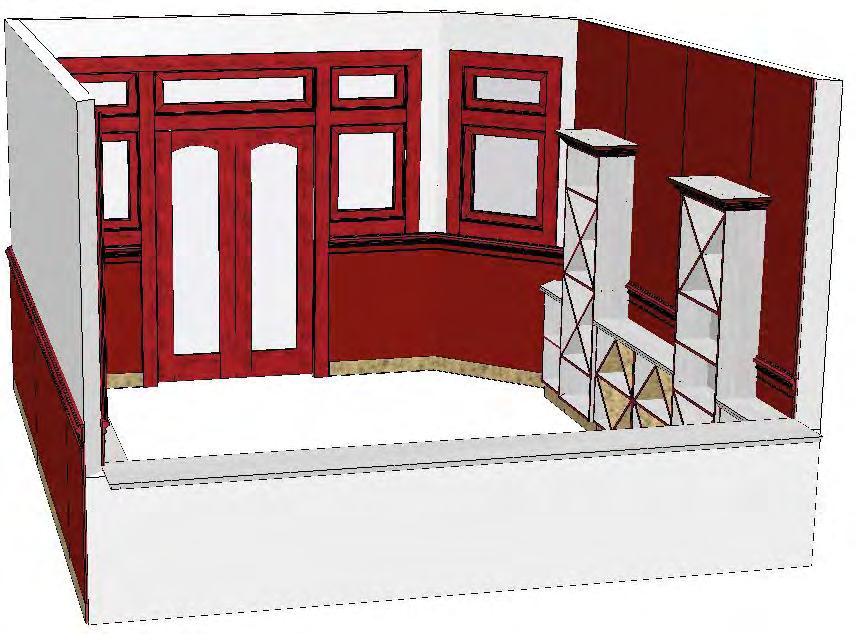
Among the Cabinet Vision functions utilised most often by Fletcher Wood Products is the ability to apply their own object intelligence to completed designs. Object intelligence eases the process of making design changes, including the ability to resize parts — even when they are included in assemblies
Specialist joinery and fit-out contractor looks to Microvellum software to solve efficiency challenges
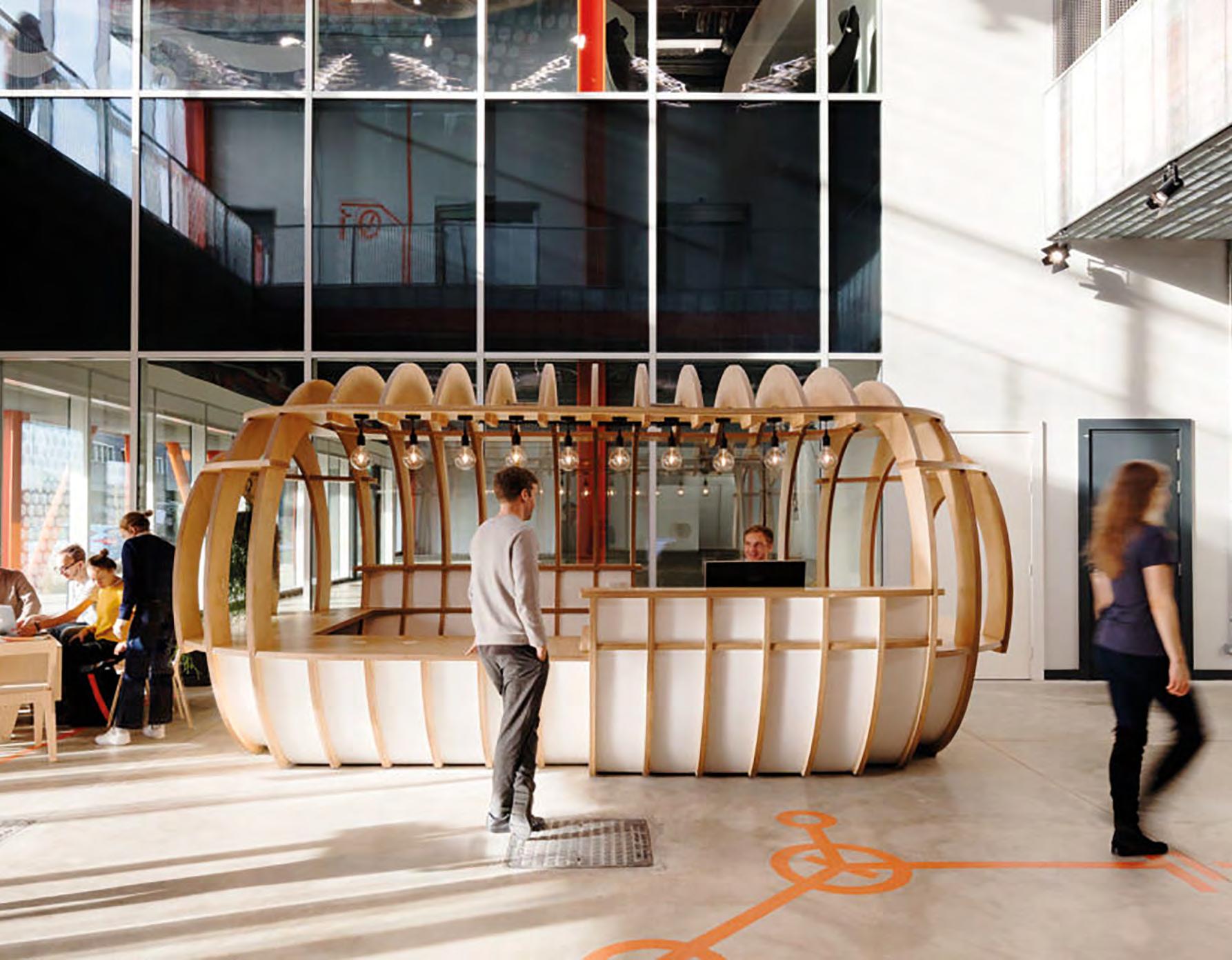
With a reputation as a professional joinery and fit-out contractor, Martek has been in the business of designing, manufacturing and installing bespoke joinery for nearly four decades.
The company, based in Croydon, specialises in high-end, commercial, healthcare and cinema interiors. Martek’s 40,000ft2 production facility, based in South London, combines the latest software and machinery for furniture manufacturing, combined with traditional skills and craftmanship.
Like many manufacturers today, Martek is faced with maintaining competitive prices while juggling the rise in material costs, project delays, and the high demands from architects to continually push the limits of manufacturing.
“In the early days, it became apparent that in order to take total control of quality and ensure we could meet deadlines, we needed a solution to manage the entire manufacturing process,” explains Derek Galloway, MD at Martek. “We work on a lot of high-profile projects, from penthouses to state-of-the-art cinemas, corporate offices and healthcare facilities. Having software that can help us handle the complexity of these designs and efficiently meet the demands of our ever-changing production requirements and schedules is key.”
One of the of the biggest challenges for Martek right now, related to the pandemic, is cost increases from suppliers.
“Nearly every cost is increasing. We are seeing an average increase of +20% across the board, yet our clients expect our prices to stay the same. For us, the solution to this problem is to focus on efficiency gains.”
To help combat these challenges, Martek, and its team of six drafters, relies on software from Microvellum, an AutoCAD-based design, engineering and production platform developed for woodworkers.
“Our Microvellum software has been an instrumental component of our design and manufacturing process here at Martek for the
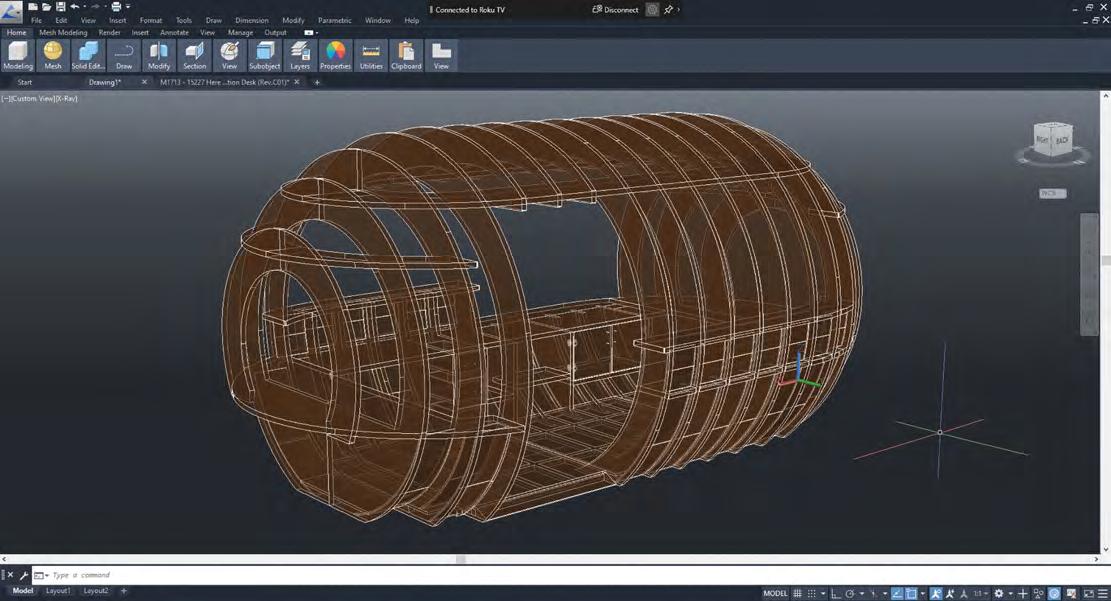
past 14 years. We work with a lot of architects, and the fact that Microvellum is essentially an extension of AutoCAD provides us with a seamless transition from the design and approval stage, right into the production stage of a project. “As you can imagine, our work is very bespoke. Whether we’re working on a custom reception desk, the one we built for the technology campus at Queen Elizabeth Olympic Park, a theatre display, or even the interior of a hospital, our projects can be quite unique. Microvellum helps us and our clients visualise product prototypes in 3D, which reduces errors and the time it takes to send those prototypes to production, since all the information needed to manufacture the product is contained within the drawing.
“Our customisable product library is a huge asset for us. It includes the latest hardware and materials, which makes ordering easy and efficient. Over the years, our engineers have grown our library in so many ways with new products and options to make it easier for our drafters to detail unique projects.
“Sustainability is important to us. With Microvellum, we can process multiple projects at once, optimising parts for our Biesse SKILL and Biesse Rover K FT CNC machines simultaneously. This helps minimise material waste and saves time for our production team.”
Through innovations in software, machinery, and processes, Martek has created a business model for success. Recently, this model has fuelled its expansion into yet another market, creating a division of the company that helps eliminate single-use plastic from the food supply chain, building flexible furniture products and displays.
“We expect the road ahead to continue to be challenging – it always is. Our success will be measured by the way in which we rise to combat those challenges. And for us, we can be confident that we’ve built business partnerships that will help us tackle anything that comes our way,” concludes Derek.
0800 680 0669 www.microvellum.com
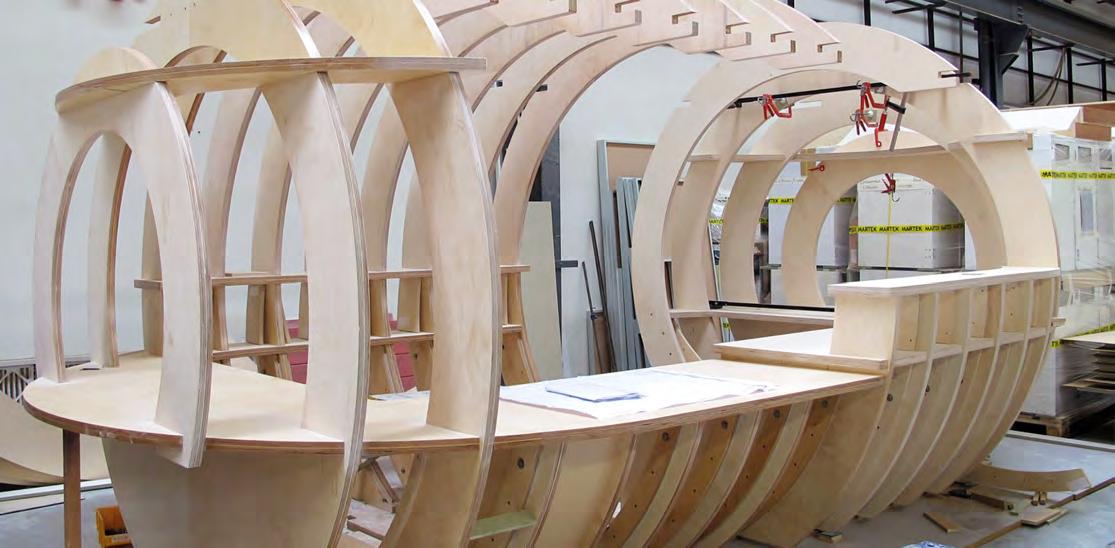
New range of SCM machining centres for solid wood
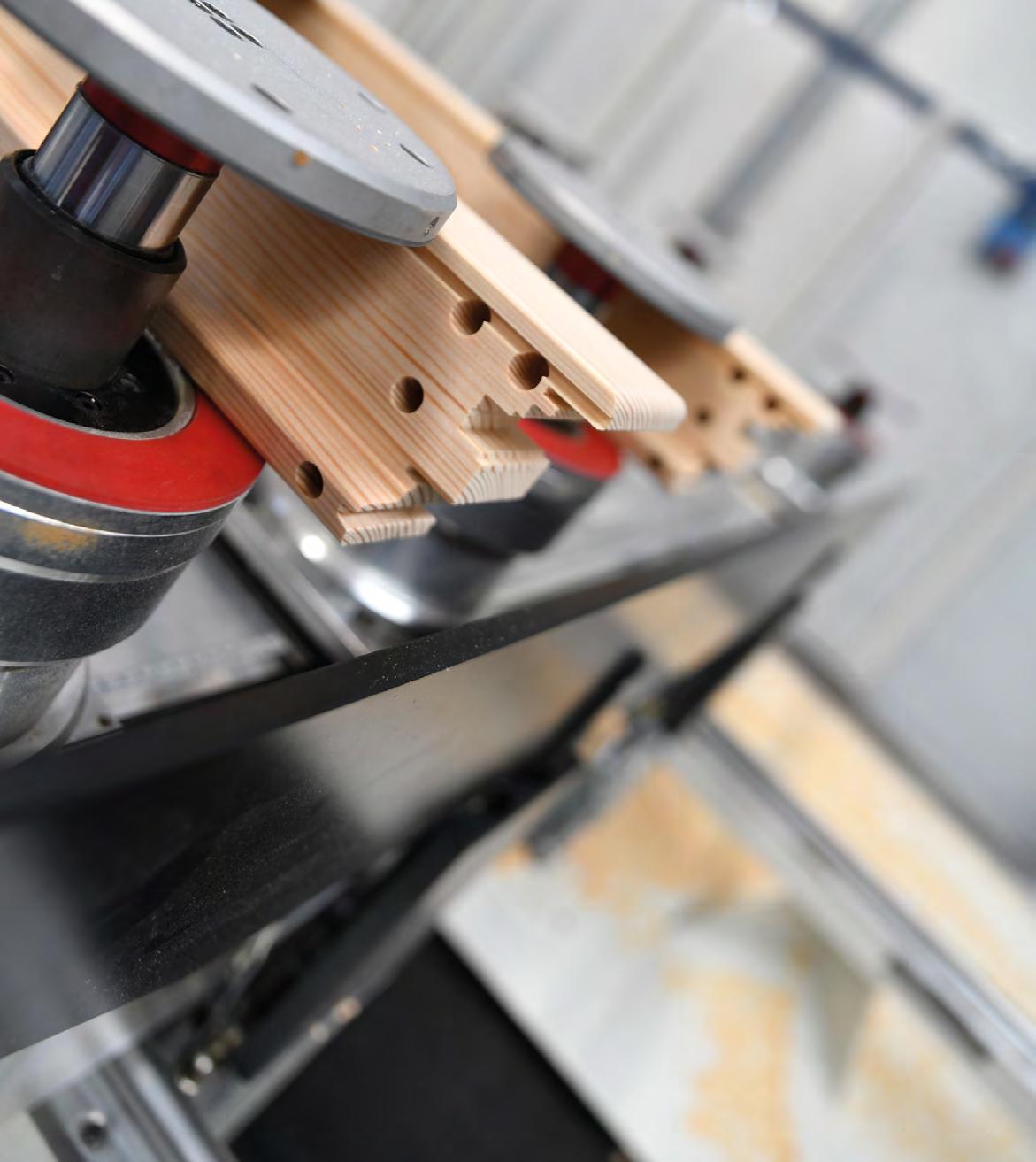
SCM says it is changing the rules of the game for machining doors, windows, stairs and solid wood elements. At the heart of the new Accord 500 and 600 models and the upgrade of the Morbidelli m200 lies the need for customers to regain control over their time, making significant gains in productivity while still achieving excellent quality on finishing.
Behind the claim chosen by SCM for the launch of its new range of machining centres for solid wood: ‘According to Wood’, lies the meaning and value of a project called upon to launch a new era in machining doors, windows, stairs and much more.
‘According to Wood’ describes SCM’s desire to provide a vast range of technical solutions that are even more effective and better performing, but above all designed by wood, because they have technical specifications and performances that are fully in line with market challenges.
At the same time, ‘According’ also brings to mind accord – a long history of successes and know-how like that of SCM’s range of machining centres for drilling and routing of the same name, which has been a benchmark for the industry for over 15 years. The same range is now being expanded and renewed from a completely new and strategic point of view, to stay abreast of the times and to rightly value customers’ time, by optimising and speeding up production processes, while simultaneously guaranteeing excellent finishing quality.
In fact, it has been time that has mostly led the revolution of SCM’s machining centres. Each technical feature is designed to save time at the most crucial stages for each industry manufacturer – from machine programming to set-up, from the machining process to maintenance. “Our aim was to give our customers, facing increasingly more complex problems when machining solid wood, an answer from specialists capable of finding precise solutions for each individual request. These new technologies considerably simplify the everyday work of operators, making it more efficient and, as a result, ensuring an even greater return on investment,” underlines SCM’s business manager for machining centres, Bruno Di Napoli.
>>
>> New Accord 500/600 machining centres
SCM increases productivity by +30% compared to market standards thanks to the ‘gantry’ structure with closed frame that, in line with the accord project, allows for sturdiness and precision to be achieved even at maximum advancement speed and with the most difficult machining jobs.
The routing speed is further increased and now exceeds 15m/min, with the new five-axis KPX machining unit with Hiteco 17 kW electrospindle, designed to always enable the most complex operations to be carried out rapidly and accurately.
Even the production cycle times are dramatically reduced with the exclusive BRC-S unit, which is even more flexible and compact, and allows the user to complete all the cutting, routing and drilling machinings typical of window components.
Another significant new entry is the more-than 100 tools readily available and easily ready for use with the new Caddy 35 storage, unique both for its capacity as well as its structure, because it is integrated into the machining centre without increasing the machine’s bulk.
Tool management is further optimised and simplified by the new Maestro Power TMS software, integrated with SCM’s Maestro suite. Thanks to this program, which maximises the ability of the storage and optimises programming, there is no need for the operator to waste time and energy in looking for the most suitable tool – the software will identify and indicate the tool’s exact position in the storage, thus minimising machining times.
Cleaning the surrounding area is another crucial matter when machining solid wood and, in order to deal with the problem, SCM has devised a new shavings conveyor, automatically positioned in accordance with the machining program, which can ensure maximum suction efficiency under any condition.
One range, greater demand
The ‘According to Wood’ project is offered to the market with a range that fully satisfies its various production needs.
Accord 500 combines tradition, simplicity and compactness, without sacrificing high technology, offering the “ultimate power for wood applications”, delivered by the new fiveaxis machining unit with 17kW electro-spindle and the possibility of choosing a Pro-Space configuration without perimeter protection, which is ideal for those who do not have a great deal of space available.
Accord 600 is the project solution that involves no compromise on performance – with a view to reducing production times as much as possible in any application field, it offers a completely new, hyper-performing machining unit, fitted with as many as three separate units.
The four-axis and JQX five-axis electrospindles, respectively from 21-13.5kW with separate on-board storages, allow for tool change while the machine is running and even during machining of the separate front unit, with BSC-S or head to drill, as required.
All is aimed at saving time – which is the key concept throughout the entire range.
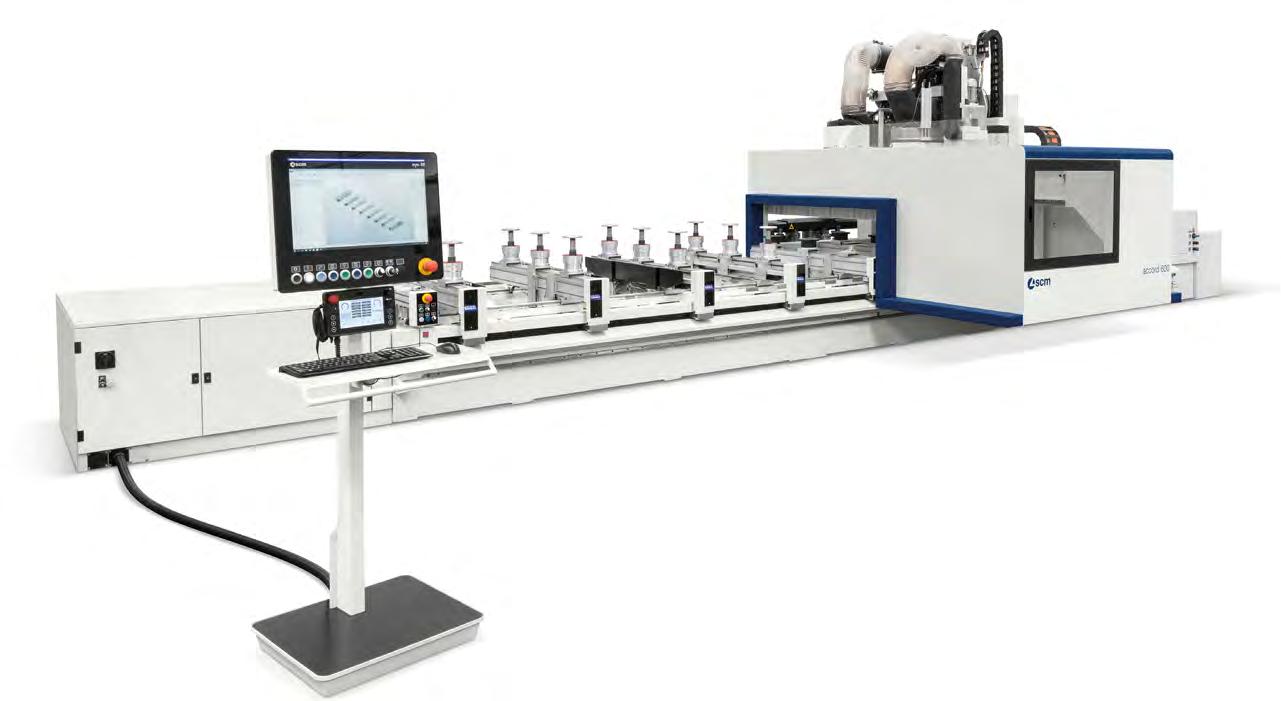
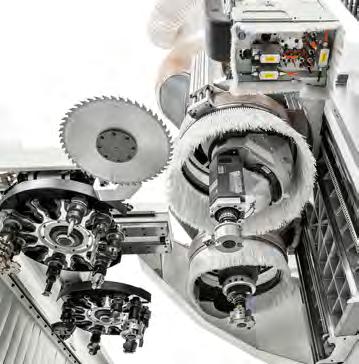
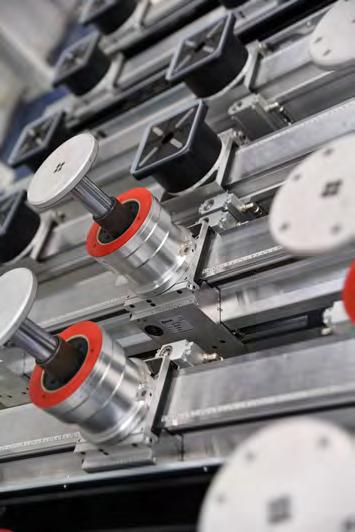
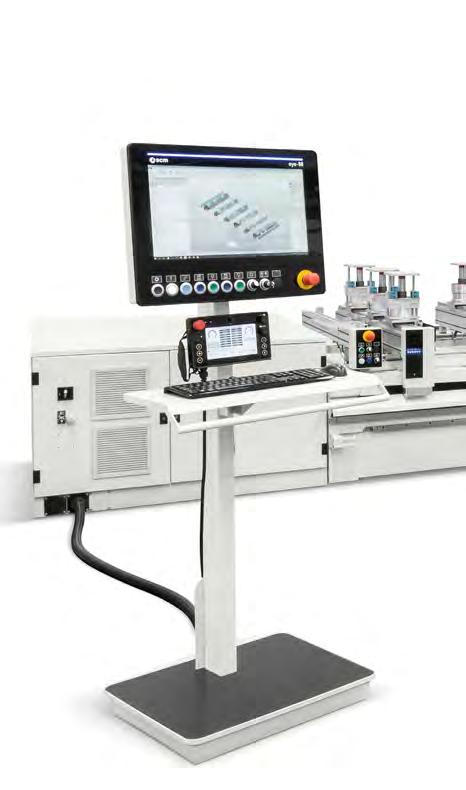
The upgrade of the Morbidelli m200 all-in-one technology machining centre
The morbidelli m200 range, a benchmark for CNC machining centres across the globe, confirms its technical features as the most popular on the market – like its solid structure, its 250mm component passage, its Prisma KT five-axis, and the FlexMatic table which ensures that all kinds of machining for panels can be achieved, but also those for solid wood.
This machining centre has now been enhanced with new features that are ideal especially for the production of window elements.
Cycle time reduction is achieved with the FlexMatic table, which becomes even more flexible when its movements are made simultaneously under the control of SCM’s Maestro CNC software. As well as this, the performance of the piece-gripping system has been further enhanced, thanks to the Multigrip
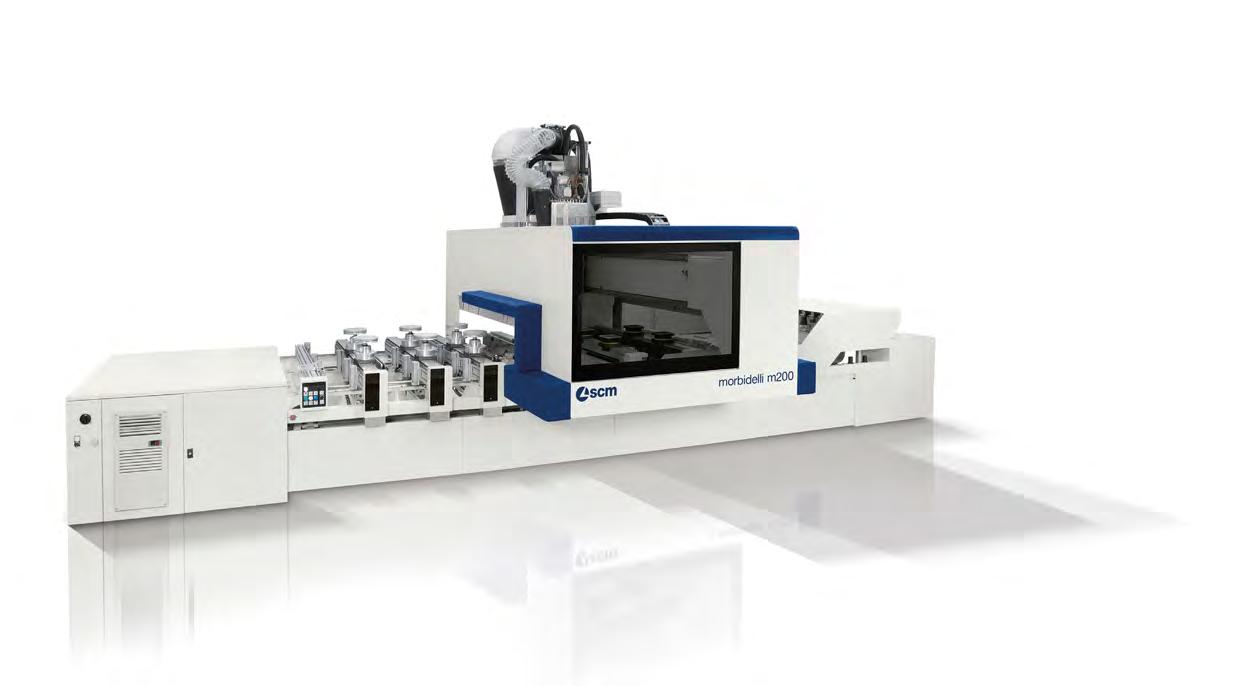
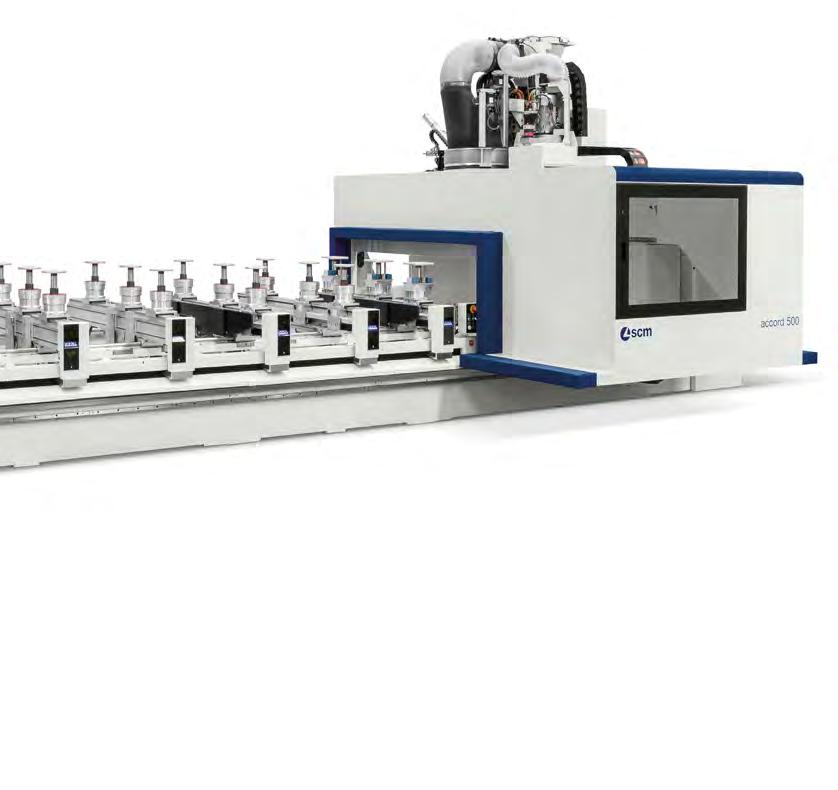
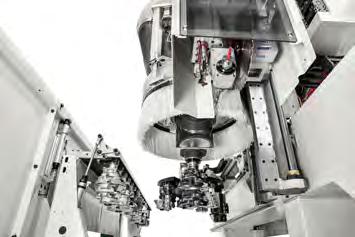
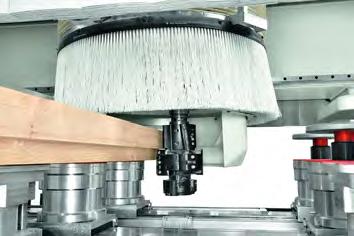


clamp, designed to specifically machine elements for windows and doors, which allows the workpieces to be positioned and blocked faster and more reliably.
The JQX machining unit has been enhanced by an innovative shavings conveyor, specifically designed to achieve maximum cleaning even in the presence of significant removals. This is controlled by NC not only in rotation, following the machining direction, but also in a vertical position – which means the conveyor can always position itself directly in front of the jet of shavings to capture it as effectively as possible.
Confirming the focus on the world of windows and doors, even on the Morbidelli m200, the new BRC-S unit that allows for horizontal blade cuts and drilling and routing is achieved as quickly as possible, leaving the five-axis spindle with just the main profiling and tenoning operations to do.
www.scmgroup.com
Artea: the art of edging
Introducing the Artea: Holz-Her’s brand new edgebander series. Furniture & Joinery Production takes a closer look at the latest entry-level edgebanding range from Holz-Her.
With a compact footprint, the Artea 1030 offers a competitive price/benefit ratio. Within a space of just 3700mm, operators can benefit from pre-milling, corner rounding and a full complement of finishing units including a radius scraper, flat scraper, buffer and sprayer.
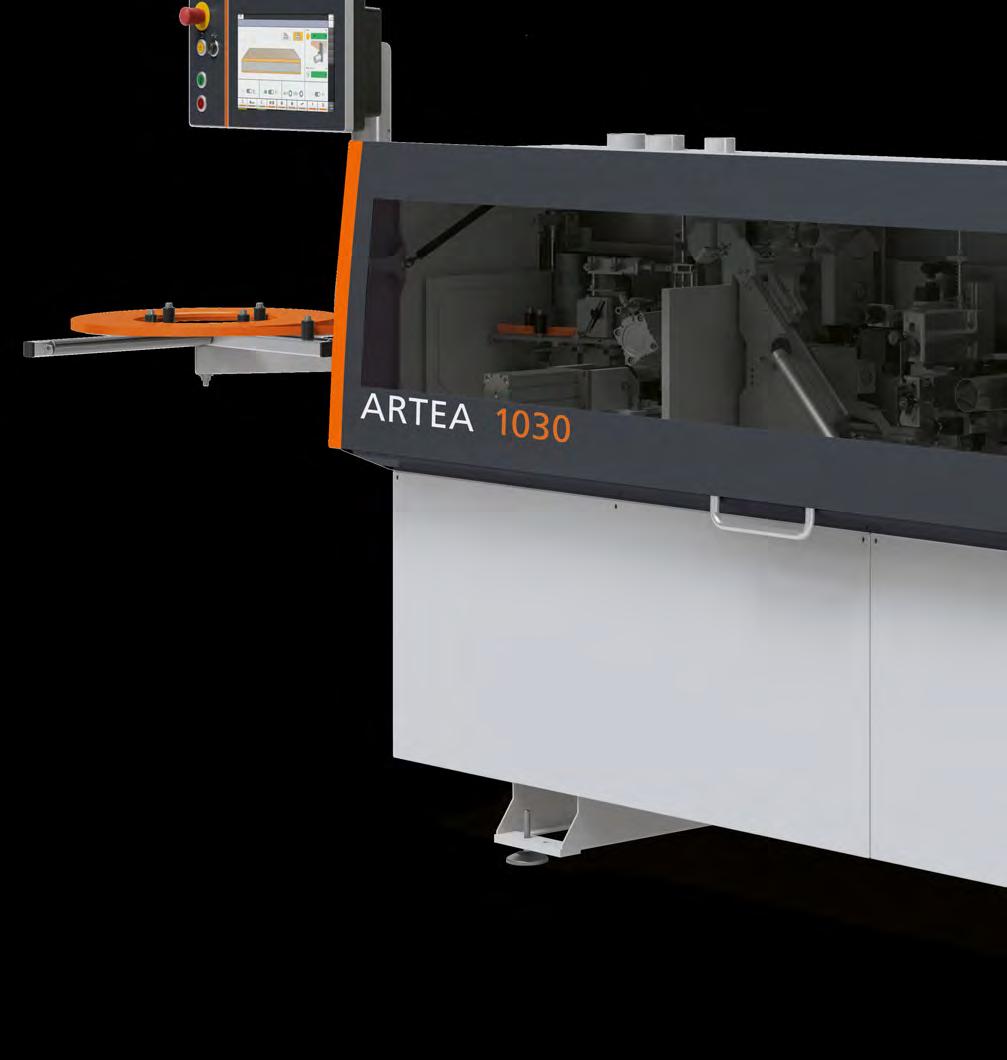
GLU-JET SYSTEM
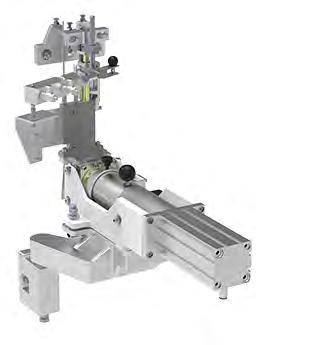
The Artea series comes equipped with Holz-Her’s patented Glu Jet system. The innovative adhesive application nozzle guarantees invisible joints on all material, making PUR processing quick, easy and cost-effective. Unlike dated models which feature glue pots and require lengthy heat-up times, the Glu Jet is ready to go in just three minutes, offering highly flexible batch machining and a reduction in energy costs. The Glu Jet can process glue cartridges and granulates – whether PUR or EVA - and even different colours. The patentprotected Glu Jet system facilities this with ease with a simple change of glue hopper.
The new Artea will be available to view at Holz-Her’s in-house event, Laser vs Glue, from the 14-16th September. To register attendance, visit www.holzher.co.uk or call 01235 557600.
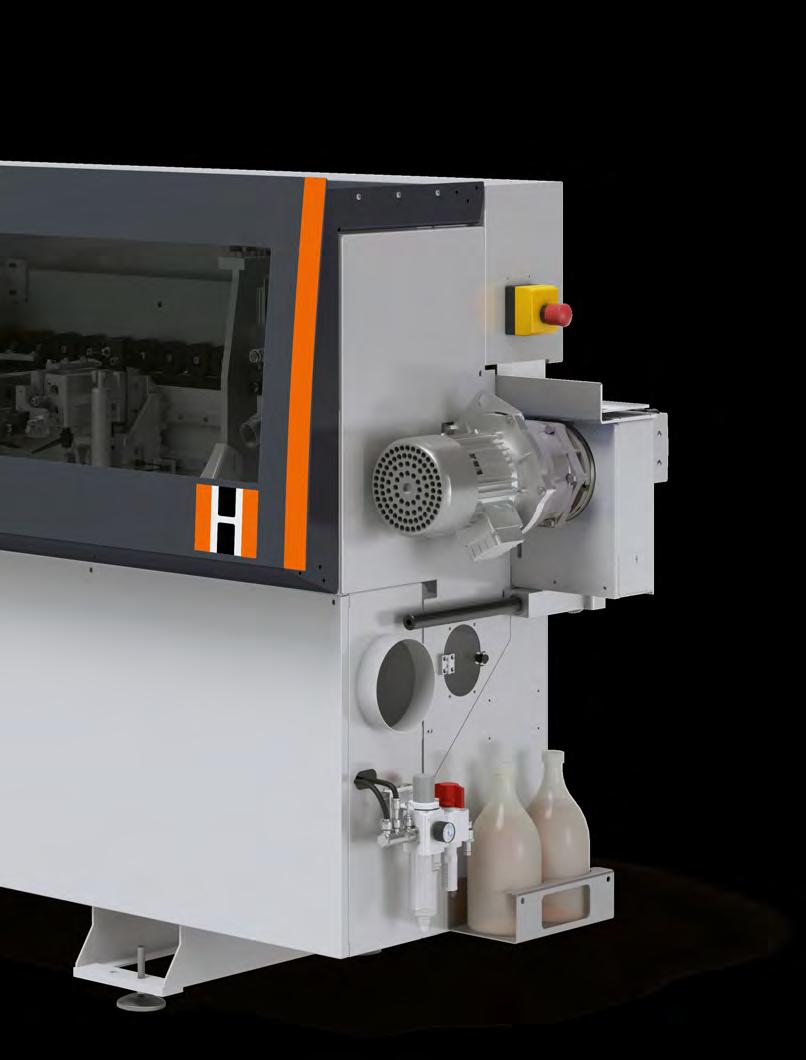
Paul Nightingale
National sales manager, Holz-Her UK

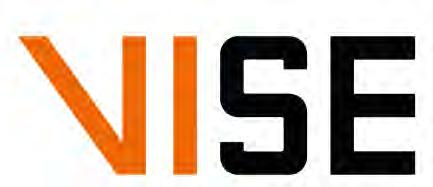
VISUAL SETTING DIGITAL LOGBOOK
The Artea comes equipped with a newly developed adhesive database – part of Holz-Her’s VISE (Visual Setting) digital logbook. This handy aid can store up to four different glue settings. This makes change-over from EVA to PUR fast and easy and takes all important parameters, such as processing temperature and pressure values, as well as the various glue viscosities, into consideration.
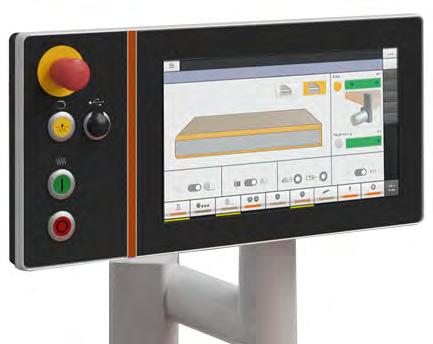
TOUCHSCREEN
The Artea features a high resolution 15.6in wide format, touch screen colour monitor which provides the HMI for a Beckhoff industrial computer, offering simple and intuitive operation.
ENERGY MANAGEMENT
The Artea features EcoMode, an intelligent energy management system. Designed to go into stand-by mode after six minutes of inactivity, it reduces energy consumption and running costs. Thanks to the Glu Jet system, the edgebander can go from zero to operating temperature in just three minutes.