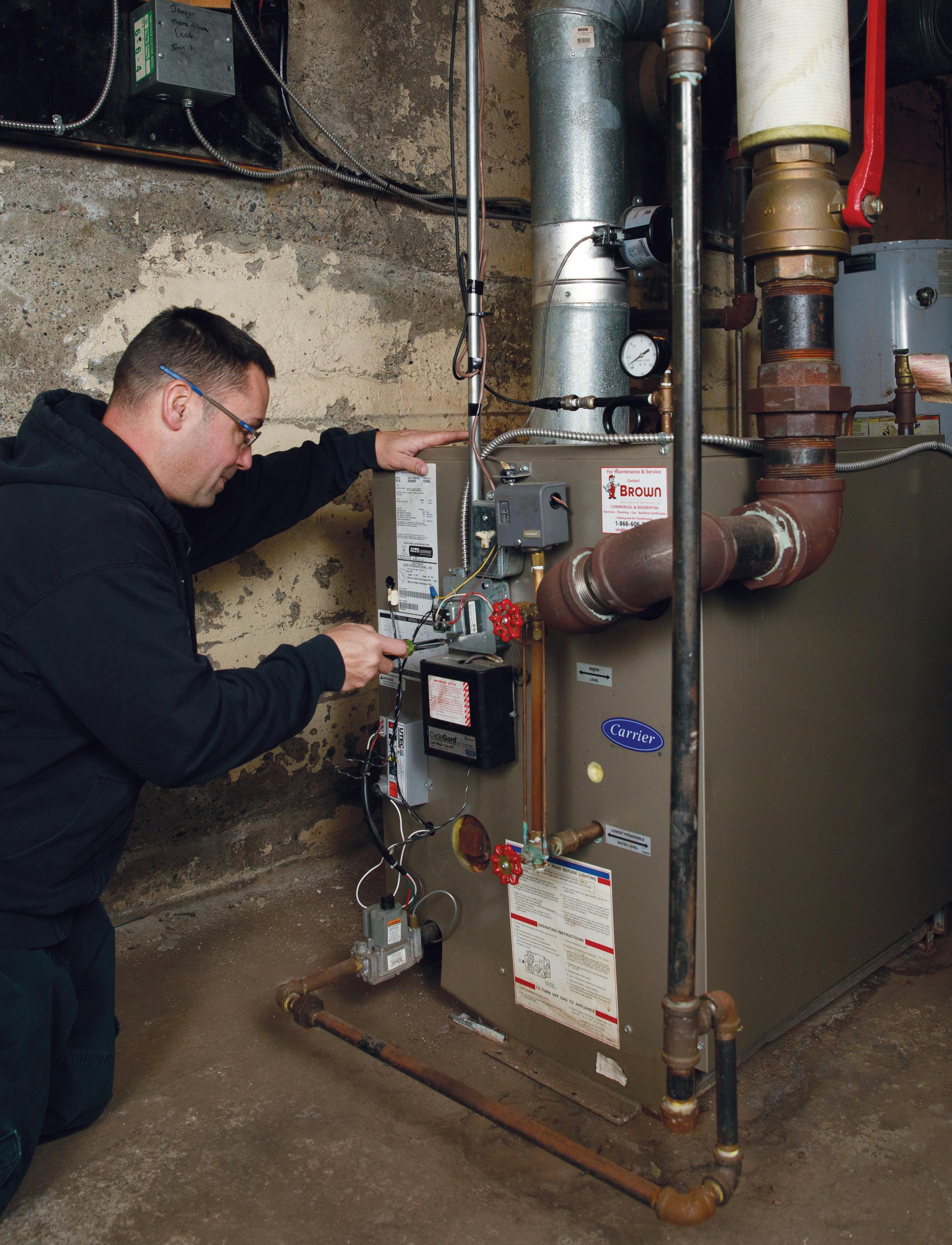
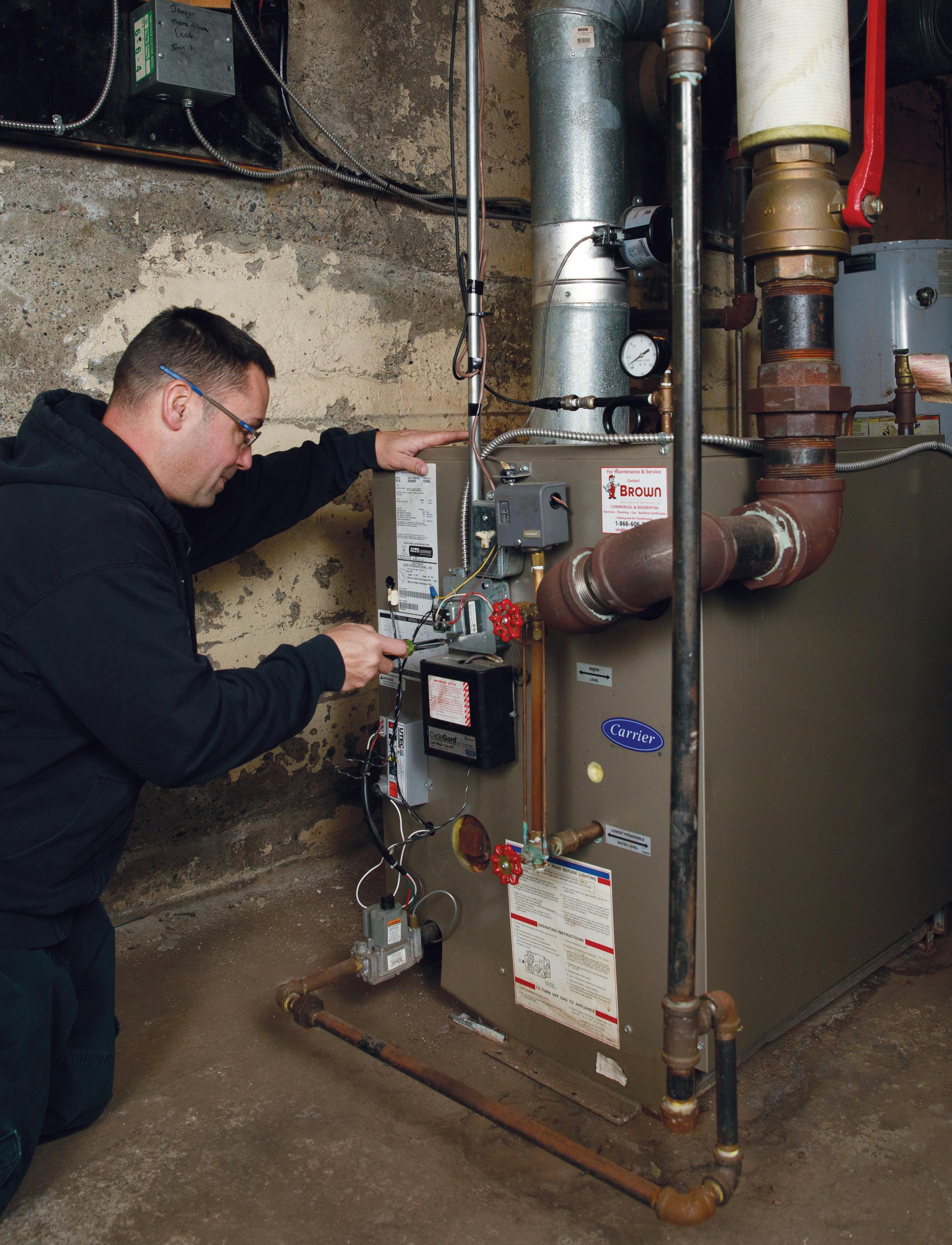
MODERN HYDRONICS
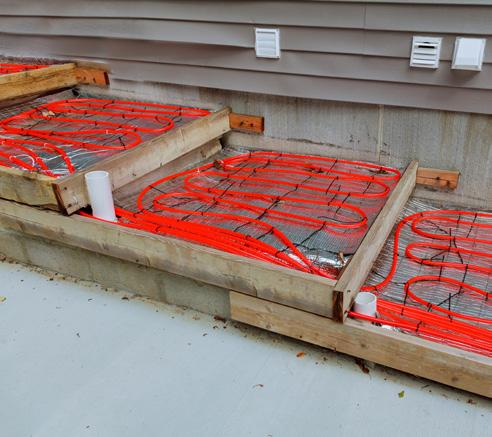
MH4 GLYCOL What's the Difference?
Exploring the changes that occur when antifreeze is added to the water in hydronic circuits.
By John Siegenthaler
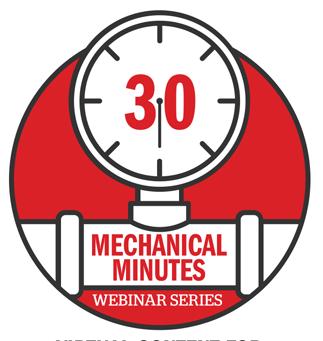
MH12
30
MECHANICAL MINUTES
Glycol and Hydronics
HPAC speaks with John Siegenthaler about how the addition of antifreeze affects performance, and he shares tips on system design and maintenance.
By Doug Picklyk

MH14 SNOW MELT
Frosty the Snowman
Melting snow can be a delicate situation.
By Curtis Bennett

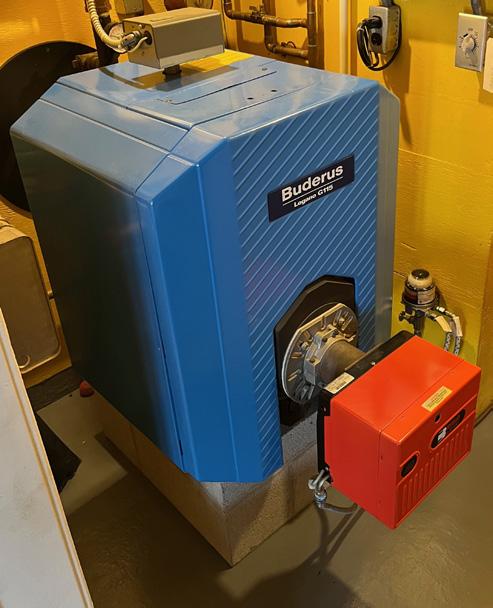
MH16 CONTROLS Haunted Theatre Receives Modern Upgrade
Historic site in downtown Vernon, B.C. retains its old-world charm while its steam heating system gets a boost with networked controls.
By Dan Vastyan
MH20 HYBRID SYSTEM
A Mix of Old and New
Making the case that new air-to-water heat pumps can still work effectively with older boiler systems.
By John Siegenthaler
EDITOR
ASSOCIATE PUBLISHER
NATIONAL ACCOUNTS
ACCOUNT COORDINATOR
MEDIA DESIGNER
CIRCULATION MANAGER
PUBLISHER
CEO
Doug Picklyk (416) 510-5218 DPicklyk@hpacmag.com
David Skene (416) 510-6884 DSkene@hpacmag.com
MODERN HYDRONICS
Amanda McCracken (647) 628-3610 amccracken@hpacmag.com
Kim Rossiter (416) 510-6794 KRossiter@hpacmag.com
Emily Sun esun@annexbusinessmedia.com
Urszula Grzyb (416) 442-5600, ext. 3537 ugrzyb@annexbusinessmedia.com
Peter Leonard (416) 510-6847 PLeonard@hpacmag.com
Scott Jamieson

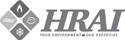


WHAT’S THE DIFFERENCE?
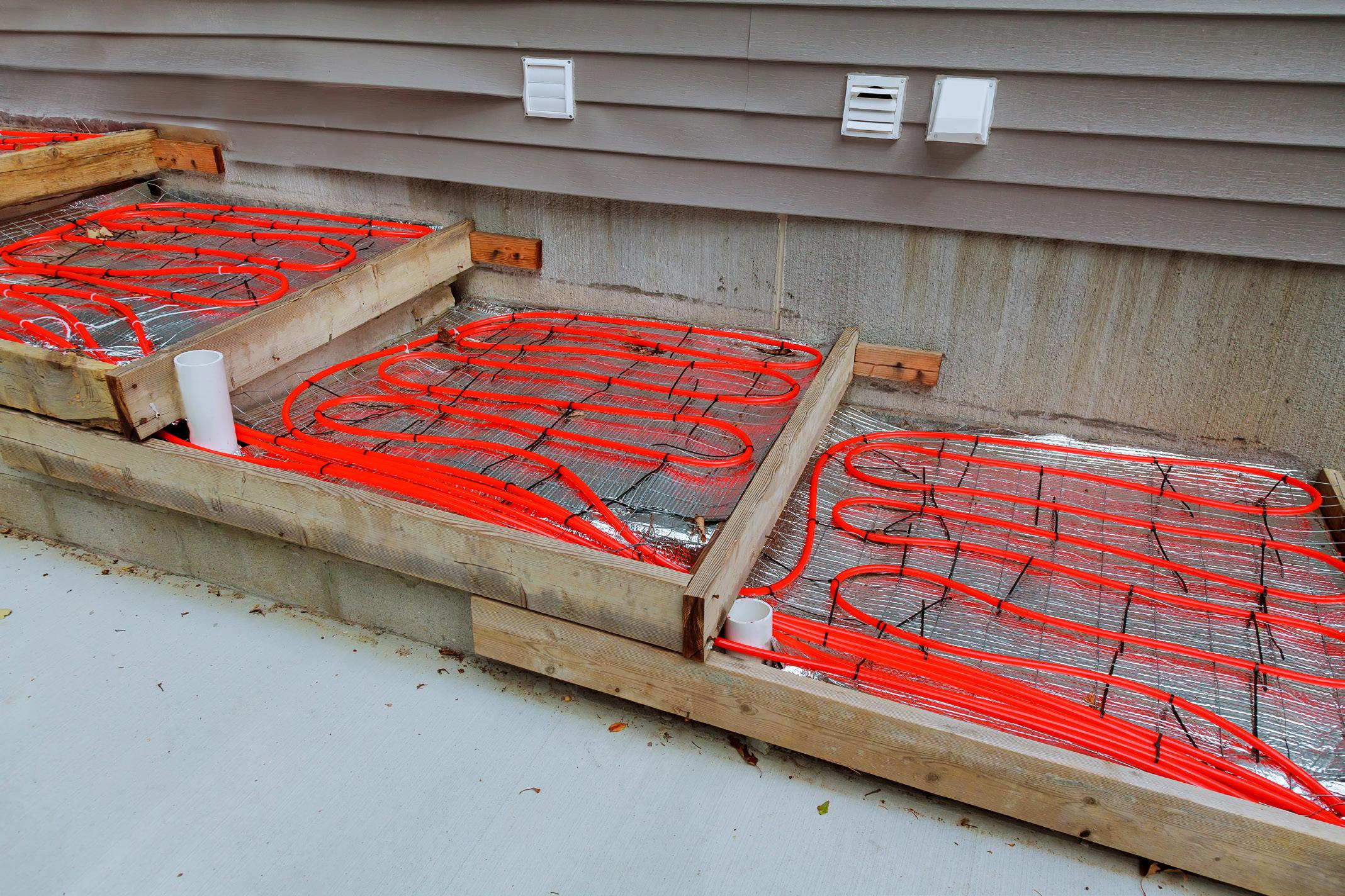
Exploring the changes that occur when antifreeze is added to the water in hydronic circuits.
BY JOHN SIEGENTHALER
I’ve been known to throw out a rather sarcastic comment when the subject turns to using antifreeze in hydronic systems: “The only good thing about antifreeze is that it doesn’t freeze.”
That quip was based on the facts that using antifreeze in a hydronic system: a.) adds to the cost of the system; b.) increases the pumping power required to achieve the given rate of heat transfer, relative to water alone; c.) decreases the heat storage ability of the system fluid;
and d.) needs to be periodically checked for chemical stability.
Still, when it comes to worst case conditions (e.g., subfreezing air temperatures for hours or days, no electric power, and no one available to open drain valves in the system), an antifreeze solution in the system is the only way to prevent freezing.
ULTIMATE RESILIENCY
One concept that’s getting increasing attention among HVAC engineers is “resilient design.” It refers to approaches that “ideally” allow systems to remain operational under very abnormal conditions or minimize effects that could cause major damage to systems when and if they are rendered inoperative.
The methods used by designers to
achieve resilient design vary. For example, one might think including an automaticstart emergency generator for a building with a hydronic system provides sufficient protection against freezing during a utility power outage. It would, if the generator starts when it’s supposed to and has enough fuel to keep running for the duration of the outage. A more conservative designer might specify antifreeze in the entire hydronic system to ensure that freezing would not occur, regardless of the duration of a power outage.
DIFFERENT BREWS
Over the last several decades there are several fluids that have been mixed with water to produce antifreeze solutions. They include inhibited ethylene glycol, in -
Outdoor snow and ice melt circuits are common applications for using antifreeze in a hydronic heating system.
hibited propylene glycol, methanol, ethanol, calcium chloride and other salts.
All these solutions have pros and cons. For example, methanol solutions, which have some acceptance in the geothermal heat pump industry, have lower viscosity and better specific heat that glycol solutions. But methanol is both toxic and highly flammable.
Ethanol (the alcohol used in “booze”) is a controlled chemical. It typically requires a license to purchase. There are also government restrictions on how these flammable materials can be legally transported. You can’t just put a 55-gallon drum of methanol in your pickup, throw on a couple of straps and legally head down the highway.
Salts such as calcium chloride can depress the freezing point of water, but their “Achilles Heel” is corrosion, especially on ferrous metals.
The most used antifreeze fluids used in HVAC systems are ethylene glycol and propylene glycol. Ethylene glycol, although having more desirable fluid and thermal properties compared to propylene glycol, is toxic in relatively small amounts.
My preference for antifreeze is inhibited propylene glycol. I would wager that everyone reading this article has, at times, ingested some amount of “food grade” propylene glycol. It’s used in eye drops, candy, soft drink, acetaminophen, aspirin, and the list goes on.
However, “food grade” propylene glycol is not an ideal antifreeze fluid for hydronic systems. It can degrade at elevated temperatures, support microbes, and eventually become acidic with age and elevated temperatures.
That’s where the word “inhibited” comes in. Inhibited propylene glycol contains chemical additives to better stabilize the fluid and reduce corrosion potential between the fluid and specific metals in the system (copper, iron, aluminum etc.).
THERMAL CONSIDERATIONS
The rate at which any single-phase fluid conveys thermal energy can be determined by formula 1 illustrated below.
Formula 1:
q = 8.01 Dc (f )(∆T )
Where:
q= rate of heat transport (Btu/h)
D = density of the fluid (lb/ft3), which depends on the fluid’s temperature.
c = specific heat of the fluid (Btu/lb/F), which also depends on the fluid’s temperature.
f = flow rate of fluid (US gallons per minute)
∆T = temperature change of the fluid as it absorbs or releases heat though some device. (F)
8.01 = a constant needed to make the units work out correctly.
LEADING THE WAY IN FULLY FORMULATED INHIBITED GLYCOL-BASED HEAT TRANSFER FLUIDS
Today we are proud to announce the merger of KOSTChill and RECOFREEZE brands into a single global brand, S OLUTHERM™ . As the global industry leader in vehicle antifreeze+coolants with our iconic brand Prestone® and as the top manufacturer of fully formulated INHIBITED GLYCOL-BASED HEAT TRANSFER FLUIDS; we offer a range of aluminum safe, food grade and LEED certified formulations specifically developed for optimal thermal management in HVAC applications.
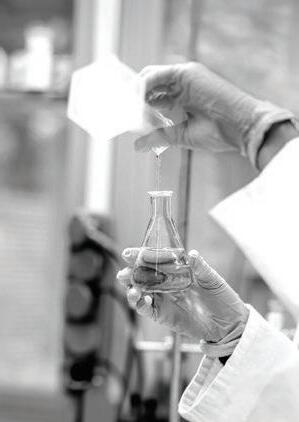
S OLUTHERM™ Services is an array of services that we offer to our customers to meet their needs.
• Formulation selection specifically developed for your application In-use testing and remediation
• Industry specific technical guidance
• Tailored trainings & sessions
• Education material (webinars, newsletters, video capsules, whitepapers, etc.)
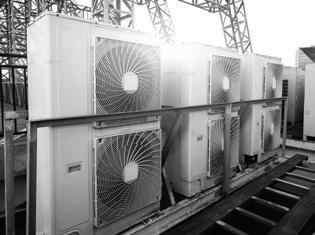
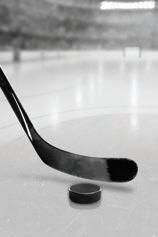
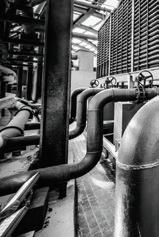
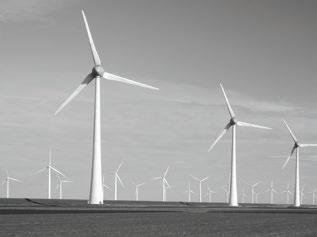
Formulations specifically developed to be environmentally safe and ensure an excellent performance.
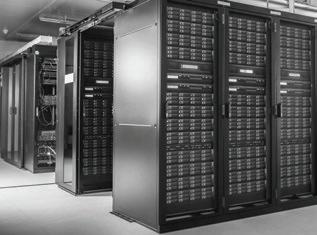
The higher the fluid’s density, and the higher its specific heat, the greater the rate of heat transfer for a given flow rate and given temperature change. The graph in Figure 1 shows the density of water, along with that of 30% and 50% solutions of one commercially available inhibited propylene glycol (PG).
Figure 2 shows the specific heat of these same fluids. The density of all the fluids decreases as temperatures rise, while the specific heat of the two glycol solutions increases with increasing temperature. The specific heat of water varies insignificantly over the temperature range shown in Figure 2
The multiplication of density (D) times specific heat (c) represents the “net effect” of how different fluids effect heat transfer. The chart in Figure 3 shows a relative comparison of this multiplication at three different temperatures 50F,100F, and 150F. In each case the multiplication (D x c) for the glycol solutions is given as a percentage of that for water. This allows for a comparison of the heat storage ability of antifreeze relative to that of water.
These numbers show that the heat storage ability of glycol
Relative heat storage ability compared to water
solutions is not as good as that of water. This is especially true at lower fluid temperatures and higher glycol concentrations. Still, at reasonably “hot” temperatures such as 150F, the heat storage ability of a 30% solution of propylene glycol is only about 3% lower than that of water. This would imply that a storage tank would need to hold about 3% more 30% PG solution compared to water to store the same amount of heat and while undergoing the same temperature change.
IT’S A DRAG
Another characteristic of glycol solutions is they have higher viscosity than water at the same temperature. This property, in combination with higher density compared to water, results in more head loss (and associated pressure drop) through any hydronic circuit, and at any given flow rate. Higher head loss implies that more pumping power is needed to achieve and maintain a given flow rate through a circuit compared to operating the same circuit with water alone.
The table in Figure 4 shows another relative comparison of
Relative head loss compared to water
Figure 1: Comparing density of water with that of 30% and 50% glycol/ water solutions across a temperature range.
Figure 2: Comparing the specific heat of water and water/glycol solutions across a temperature range.
Figure 4: Head loss is most significant with a high percentage glycol solution at lower fluid temperatures.
Figure 3: Heat storage ability is most affected at lower temperatures and higher glycol concentrations.
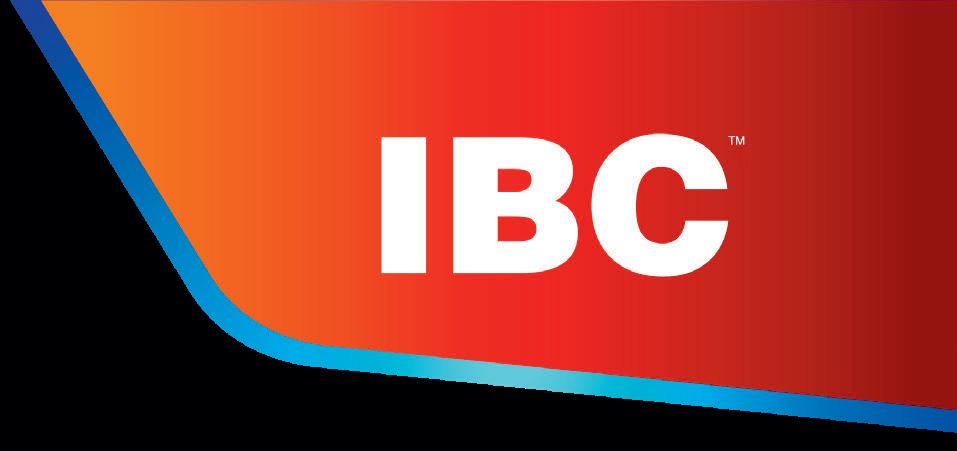
ULTIMATE EFFICIENCY DUO.
Backed by industry leading technology, The HPX™ Air-to-Water Heat Pump is the perfect solution to year round comfort. Pair it with the SKy-35 control to optimize your comfort, operating costs and energy consumption.
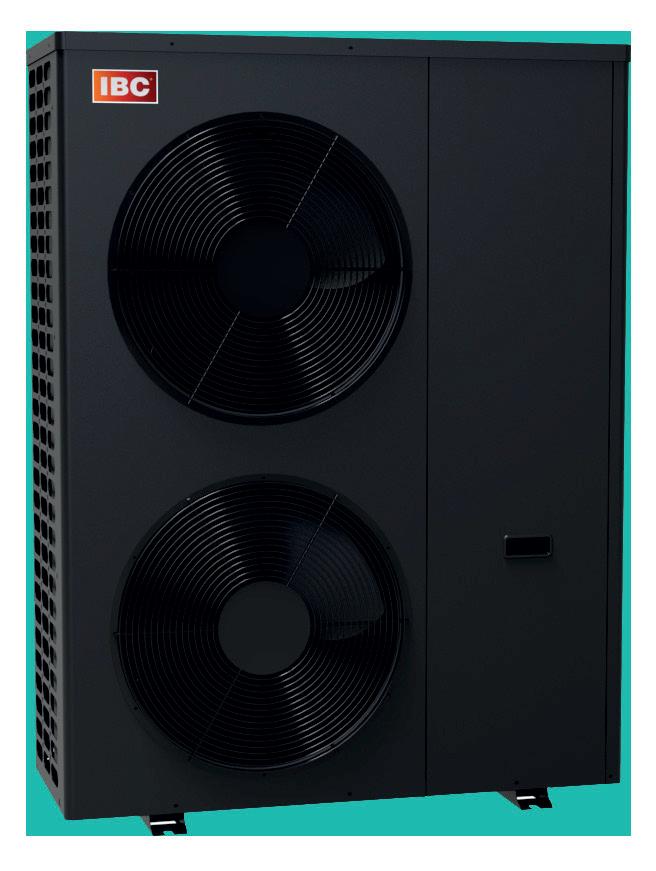


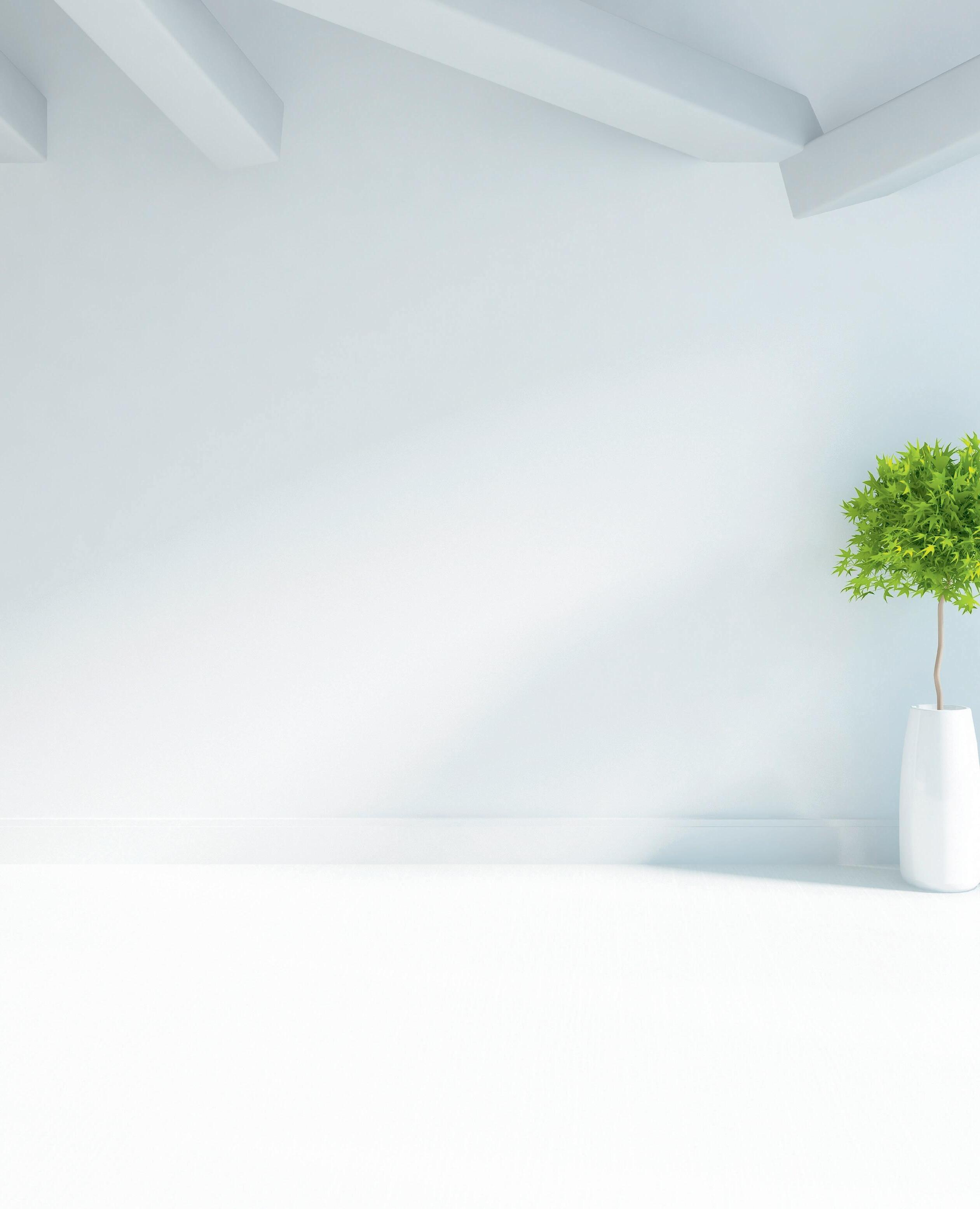
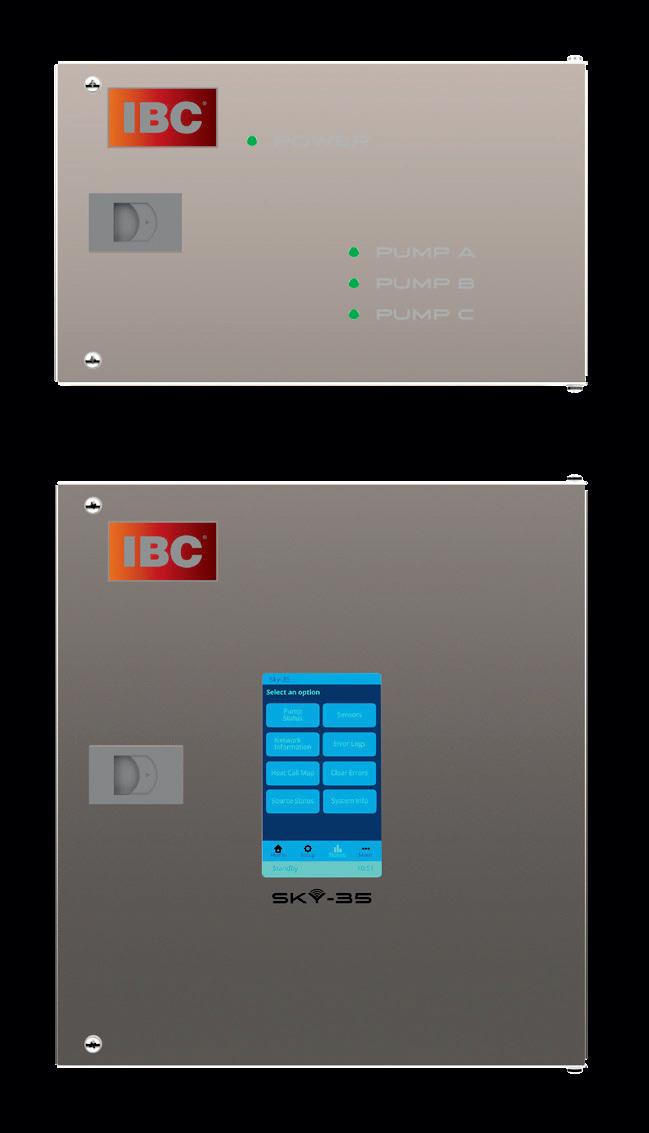

160 ºF supply temp.
Taco 007 circulator
3/4" copper x 200 ft equivalent length circuit
70 ºF surrounding air temp.
100 total ft. of residential baseboard
the head loss of 30% and 50% solutions of propylene glycol at the same three temperatures used in Figure 3
For example, the head loss of a 30% solution of propylene glycol at 100F is 1.24 times higher than for water at 100F in the same circuit and at the same flow rate.
The head loss of a high percentage glycol solution relative to water is very significant at lower fluid temperatures. A good example is the use of a 30% solution of propylene glycol in an earth loop for a geothermal heat pump system. At a fluid temperature of 32F, the head loss of a 30% PG solution is approximately 40% higher than that caused by water. Some earth loops can operate at temperatures down to around 25F, which would push viscosity and resulting head loss even higher. This must be considered when sizing earth loop circulator(s).
The combined effects of lower specific heat and higher viscosity imply both higher flow rates and higher head loss to create the same heat transfer ability of a given circuit operating with an antifreeze solution compared to that circuit operating with water. The combined effects are easily evaluated using software such as the Hydronics Design Studio.
To demonstrate the “net effect” of using propylene glycol solutions I created a simple circuit consisting of 100-ft. of residential fin-tube baseboard, a total circuit equivalent length of 200 feet of ¾-in. type M copper, a Taco 007 circulator, and a supply fluid temperature of 160F. Figure 5 shows the simple circuit.
Figure 6 shows the flow rate and heat output of the circuit when the fluid is changed, with all other operating conditions remaining identical. The red numbers in parentheses indicate the percentage change in flow and heat output relative to using water in the circuit.
The drop in heat transport rate using a 30% PG solution isn’t
too bad - down just over 3%. However, the drop in heat transport rate using a 50% solution is almost 10%. That’s certainly significant.
That loss of heat transport capacity could be compensated for by 1) using a more powerful circulator or a higher speed on a multi-speed circulator, 2) increasing pipe size to reduce head loss, 3) looking for any component substitutions that could reduce head loss.
EXPANDED THINKING
The changes in density of propylene glycol solutions with temperature is greater than that of water. This means that expansion tanks used in systems with glycol solutions may need to be larger to operate with the same pressure limits.
I used the Expansion Tank Sizer module in the Hydronics Design Studio software to calculate the minimum expansion tank volume for a system containing 50 gallons of fluid, with a temperature cycling range from 60F at cold fill, to 180F at maximum temperature.
The top of the system was assumed to be 10 feet above the expansion tank connection, and a 30 psi relief valve was assumed. The calculated minimum expansion tank (shell) volumes for this scenario are listed in Figure 7
In this case the expansion tank volume requirement for a 30% solution of PG is about 25% greater than that required if the system operated with water alone.
I support the idea that reasonable oversized expansion tanks are useful in hydronic systems, especially those operating with antifreeze. One benefit of oversizing is that the tank can store a “reserve volume” of fluid that can flow into the system as air is captured and eliminated following initial startup.
In a typical space heating system the temperature of the fluid is unlikely to drop below the temperature at which the sys -
Figure 5: A simple circuit consisting of 100-ft. of residential fin-tube baseboard
Figure 7: Minimum expansion tank volume calculations.
Figure 6: Changes to flow rate and heat output of the circuit when the fluid is changed.
REGISTRATION NOW OPEN!

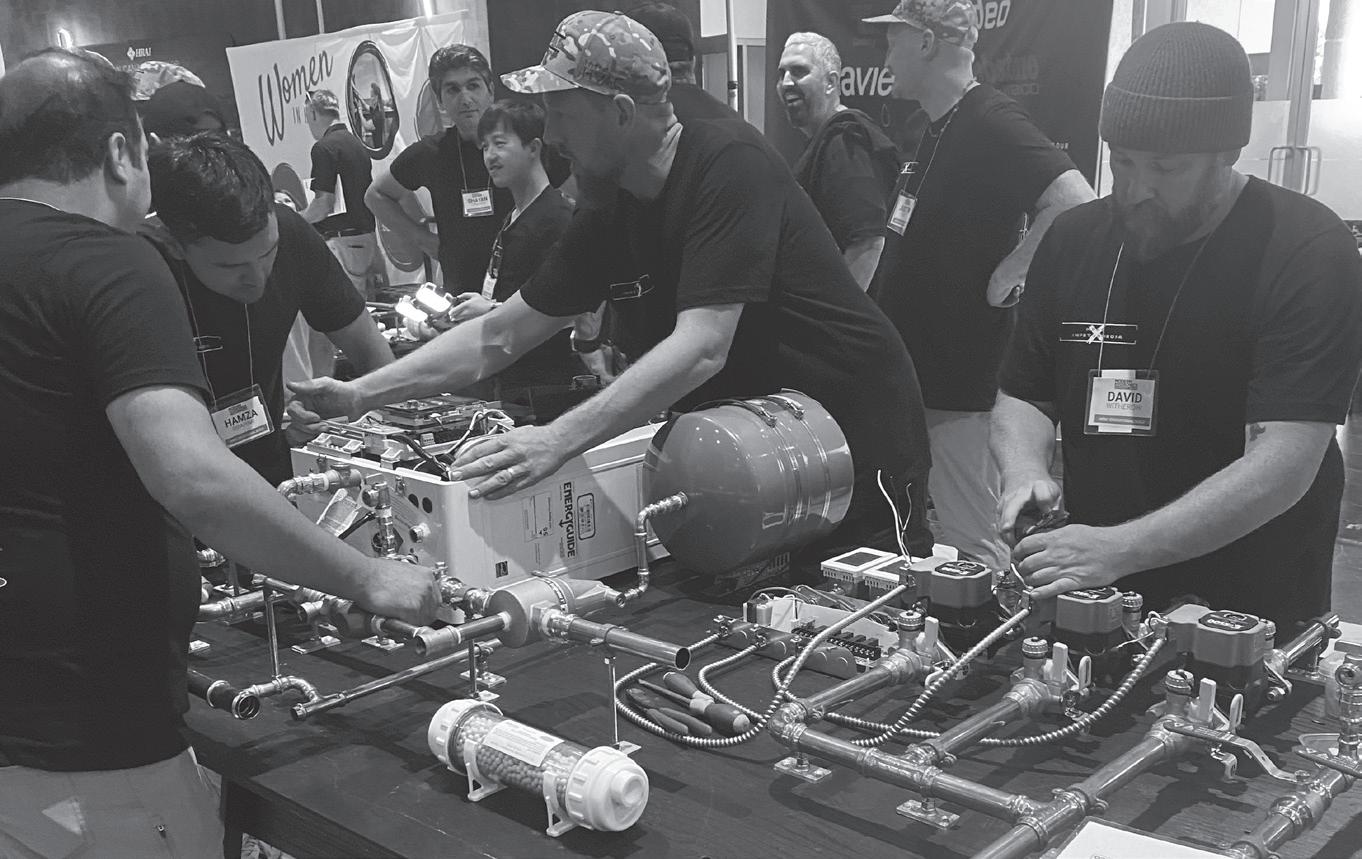

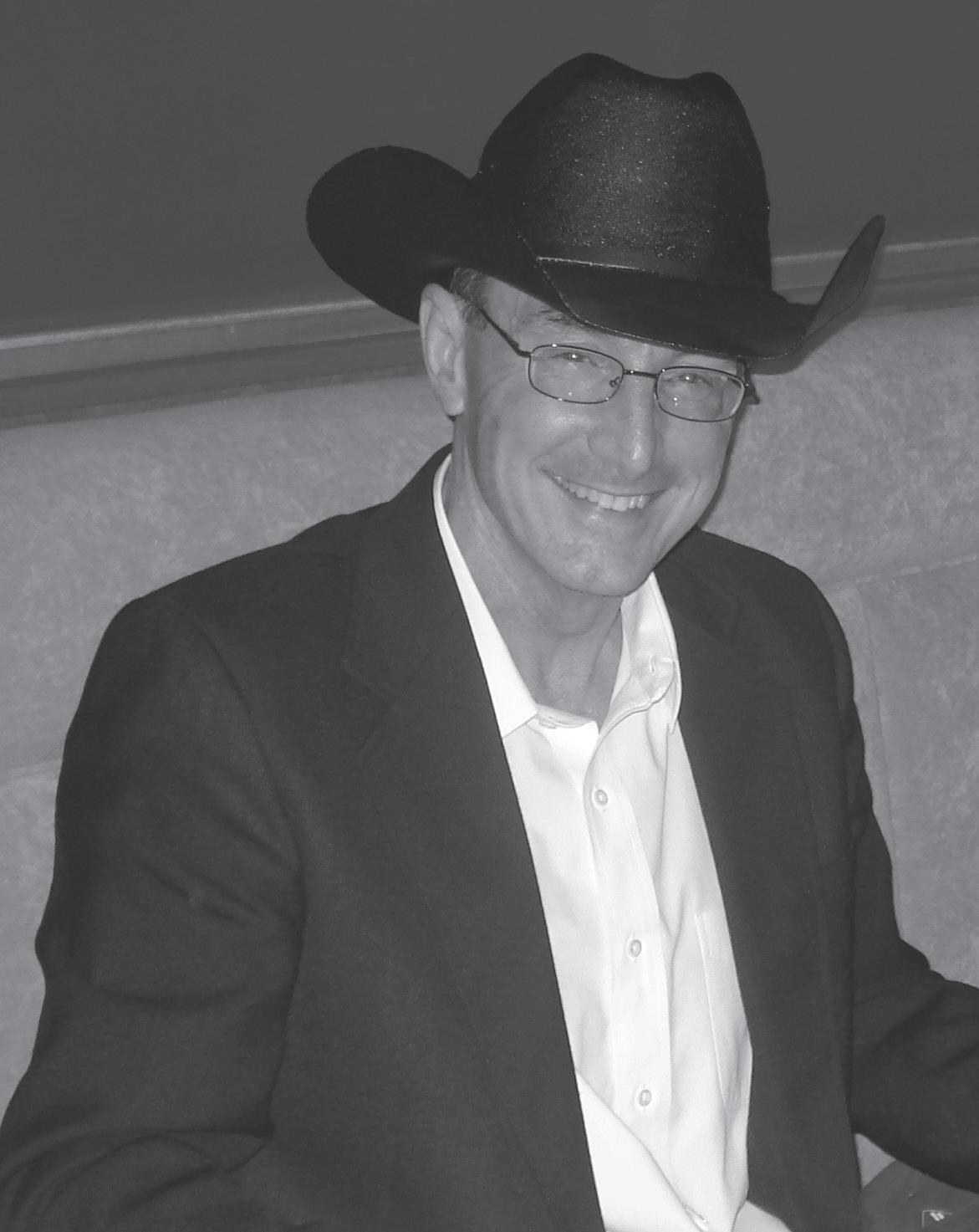
CALGARY, ALBERTA Glenmore Inn & Convention Centre
The Summit will host: • a full slate of excellent speakers • 40+ exhibitors demonstrating the latest technologies • and unparalleled networking with hydronics professionals.
Hydronics 101 sessions are sponsored by – perfect for newer technicians! For experienced pros, Master-Class sessions sponsored by, featuring John Siegenthaler and friends.
Lots of prizes including test instruments and Calgary Flames tickets will be won!
SPONSORS INCLUDE
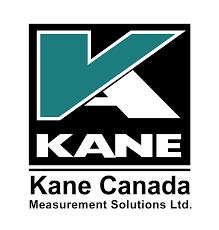
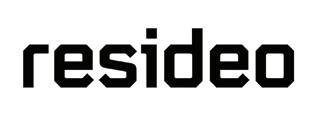
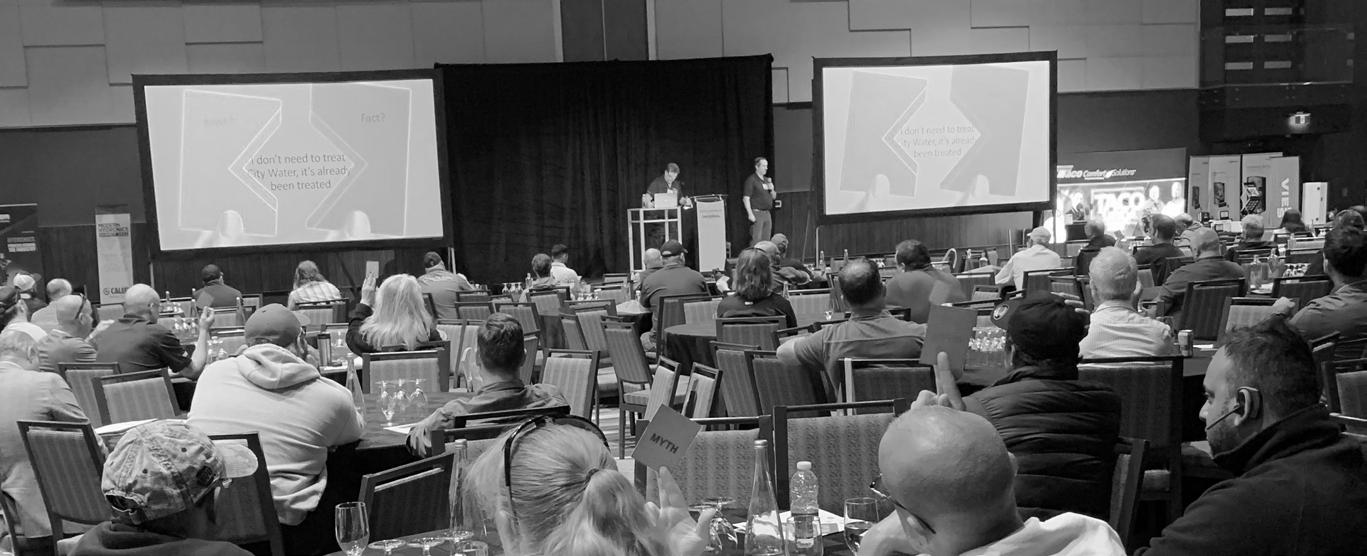

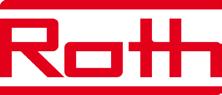
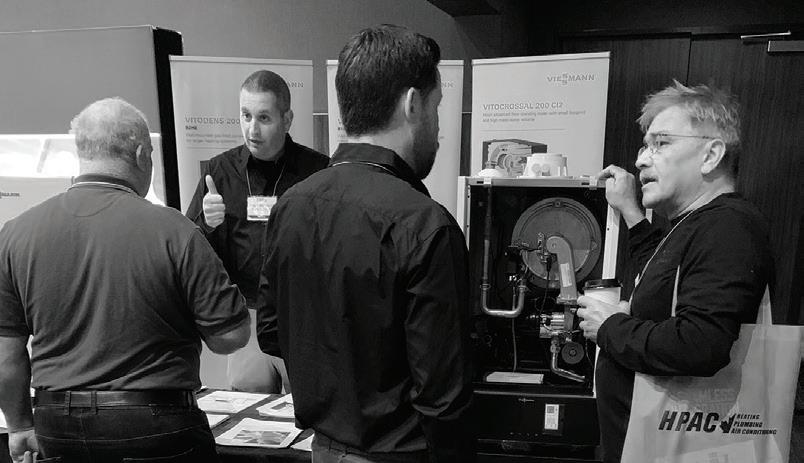
tem was filled and commissioned. However, in systems such as geothermal earth loops, solar thermal systems, hydronic cooling, and snowmelt systems, the fluid temperature will often drop below that at which the system was filled and commissioned.
In such situations it’s undesirable for the diaphragm inside the expansion tank to be fully expanded against the tank shell. If this occurs there’s no way the expansion tank can release more fluid back into the system as the temperature continues to drop and the fluid continues to shrink.
This might lead to sub-atmospheric pressure at some locations in the system. Devices such as automatic air vents or air separators at such locations will act as vacuum breakers allowing air into the system.
Although there are ways to calculate the extra fluid volume needed to avoid this situation, oversizing the expansion tank by 20-25%, and pumping up the system pressure an extra 5 psi at commissioning is generally sufficient to ensure that some residual fluid volume is available when temperatures drop below the cold file temperature.
WATER QUALITY
Glycol-based antifreeze should not simply be mixed with whatever water is available on the site. Ideally, solutions should be combined with demineralized water to minimize any chemical interaction with chlorine, minerals, microbes or other contaminants in the site water. Several companies now offer equipment to create demineralized water on site.
Don’t assume this mixture can then be pumped into a newly constructed system or an existing system that has been drained. New systems often contain residuals amounts of soldering flux, oils from manufacturing processes or other debris. Existing systems may contain iron oxides, or residual amounts of older antifreeze solutions.
Best practice is to use a “hydronic detergent”, which is available from several suppliers in North America, to internally wash the system prior to adding the antifreeze solution. Doing so prolongs the service life of the antifreeze and reduces the possibly of chemical interactions.
CONCENTRATION
Companies that supply glycol-based antifreeze often list two temperatures that apply to a given percentage concentration of their antifreeze. The “freeze point temperature” is the lowest temperature that prevents the formation of ice crystals in the solution. The solution can operate at or above the freeze point temperature, indefinitely, without ice crystal formation.
The “burst point temperatures” is the lowest temperature at which expansion of the solution as it changes from liquid to solid will not cause pipes or other components to fracture. The
burst point temperature is significantly lower than the freeze point temperature.
Figure 8 (above) shows how the freeze point temperature and burst point temperature of one commercially available propylene-glycol antifreeze vary with temperature.
IT WORKS
Antifreeze solutions are the only way to protect unassisted hydronic systems from freezing. They are essential in geothermal earth loops, solar thermal systems, and snowmelting systems. Most manufacturers of monobloc air-to-water heat pumps also require that antifreeze be used with their units. It protects them from freezing in winter, as well as against the formation of ice crystals in the heat pump’s evaporator during cooling mode operating under lower outdoor temperatures.
Adjust your designs to compensate for the differences in head loss and heat transfer capacity of antifreeze solutions and upsize expansion tanks when necessary.
Don’t use concentrations that are significantly higher than required. Check water quality against the specifications given by the antifreeze manufacturer, and be sure to test the solution periodically for both freeze point and inhibitor reserve levels. Finally, sleep well on cold winter nights knowing that chemistry is at work to protect your systems. <>
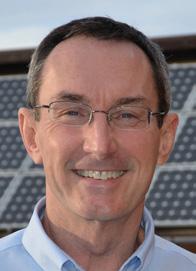
John Siegenthaler, P.E., has over 40 years of experience designing modern hydronic heating systems and is the author of Modern Hydronic Heating (4th edition) and Heating with Renewable Energy (visit hydronicpros.com).
Figure 8: Example of how freeze point and burst point varies with concentrations and temperatures for a propylene-glycol antifreeze.
Built for the PRO, by the PRO™
The NEW I-SERIES Plus™ line of Solo and Combi Condensing Gas Boilers offers unmatched value and performance with an expanded product line of 14 models that range from 60-199k Btu.
Now you can Rely on Rinnai for all your Residential Heating projects no matter the size or complexity.
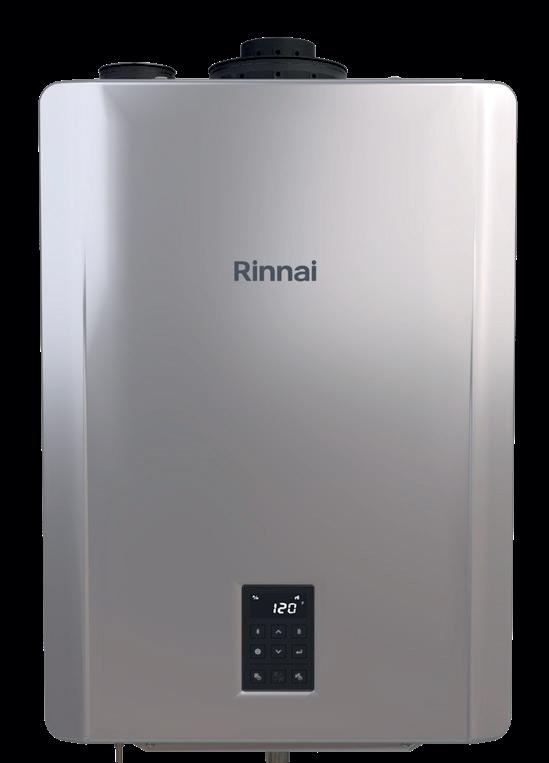
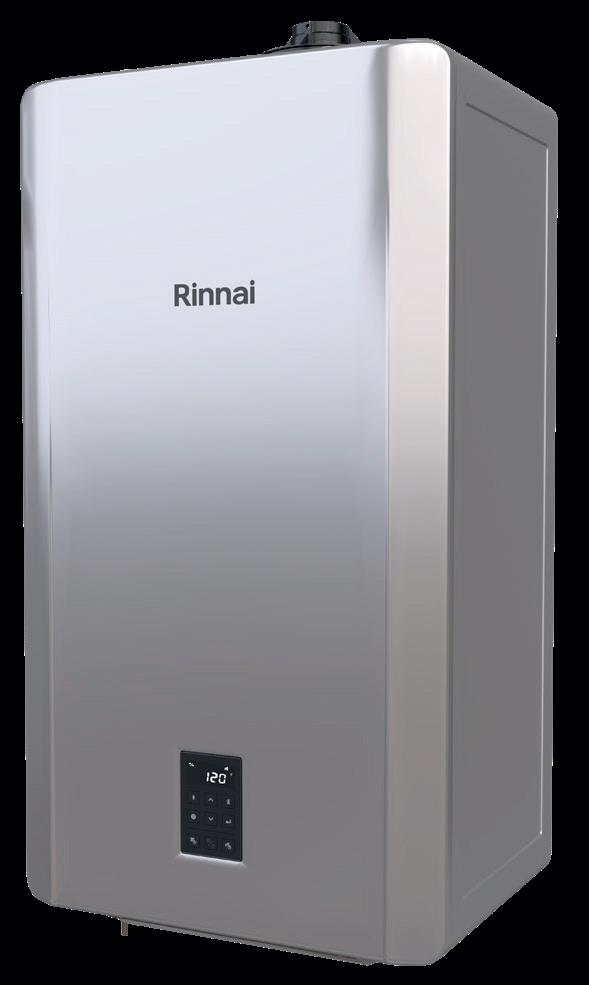
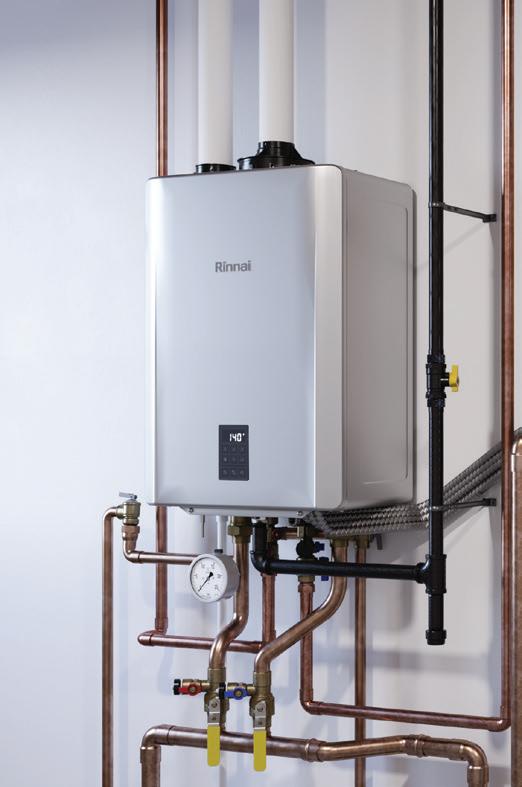
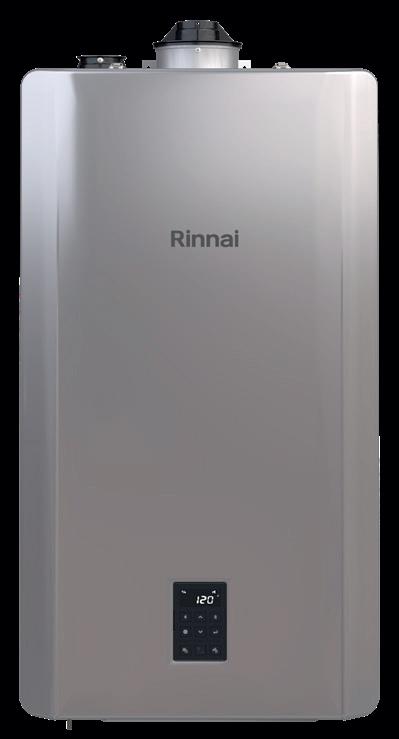

Allows you to connect your smart phone or tablet to the SENSEI® RX Series via Bluetooth®
Use the Rinnai Central™ App for quick, simplified boiler set-up and registration, significantly reducing your install time.


Rinnai’s Adaptive Gas Valve Technology lets you select your fuel type with the touch of a button on the unit controller or your smart phone. Conversion Kits not required. Smart Sense™ is only available on 60-150k BTU units
4 Built-in Zones for better comfort and savings.
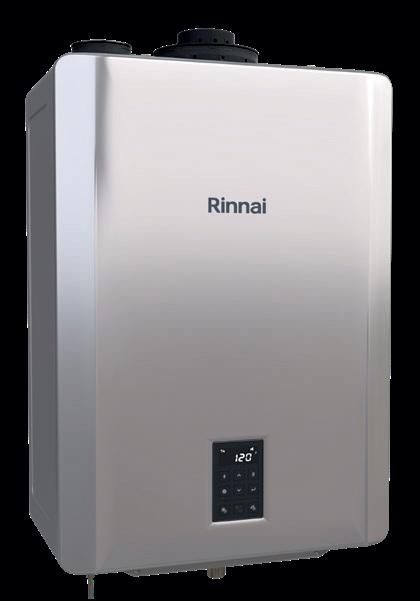




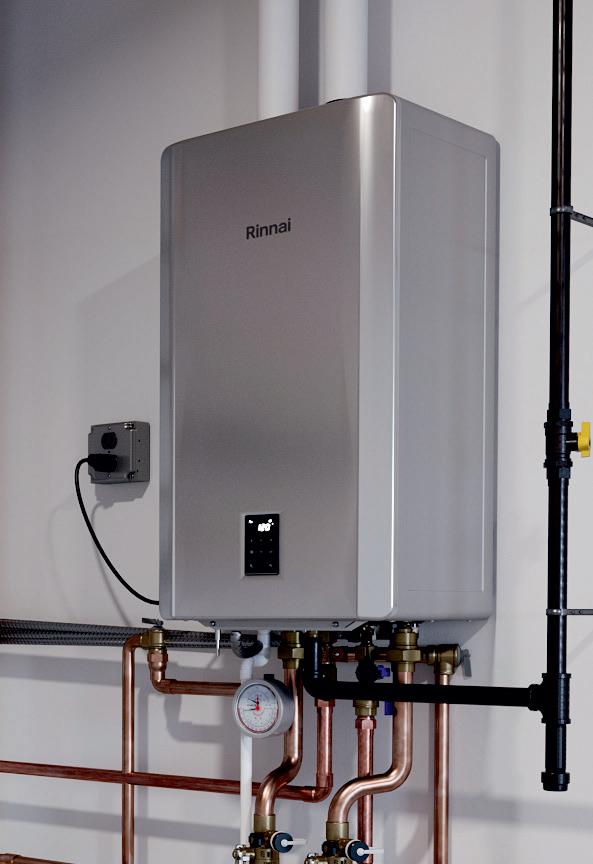
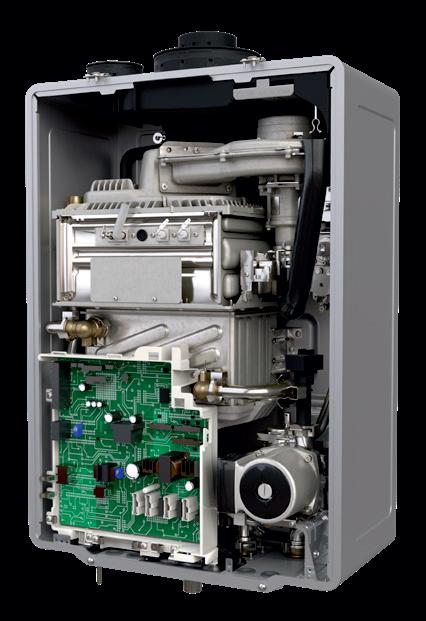

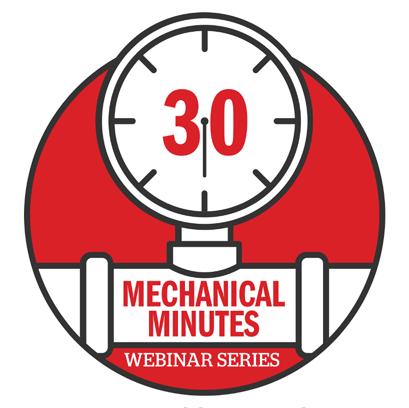
GLYCOL AND HYDRONICS
John Siegenthaler shares lessons learned when designing systems where glycol is used. BY DOUG PICKLYK
In January, HPAC magazine hosted a free 30 Mechanical Minutes webinar with John Siegenthaler covering the use of antifreeze in hydronics systems. Siegenthaler shared how the addition of inhibited propylene glycol affects the heat transfer and density of the fluid (see previous article). When designing a system, he strongly recommends compensating upfront for these changes.
He outlined the typical applications that use glycol: snow melt, garage addi -

Z-Vent
tions, monobloc air-to-water heat pumps, and whole house systems in climates where the temperature often gets below freezing and power outages are frequent.
He shared an example of a highway garage project in upstate New York, a 10,000 sq. ft. slab on grade building with floor heating. “If we had a long-term power outage, the antifreeze in the circuit would keep that system from freezing. But we also found out the garage had an automatic-start emergency generator. With
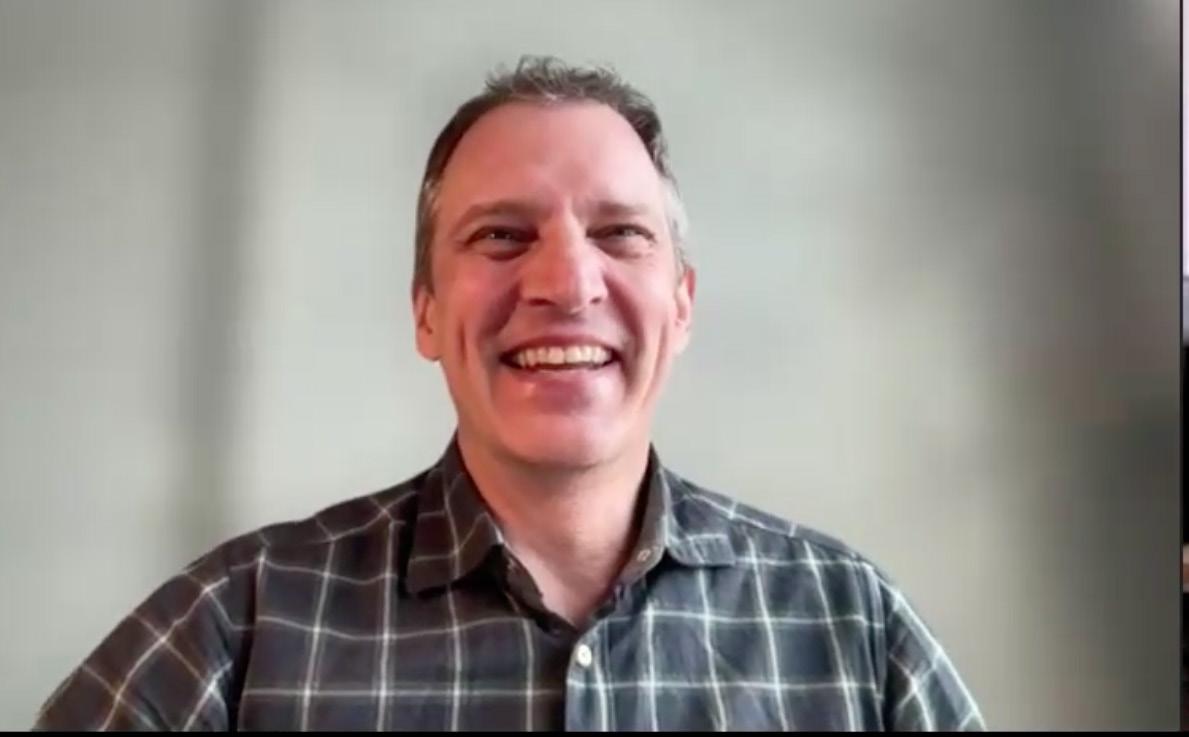
the generator, we could maintain circulation through the slab, which would buy several days’ worth of freeze protection, as long as that water was moving.”
“So, there’s an application where we didn’t necessarily need the antifreeze protection.”
He noted that most modern monobloc air-to-water heat pumps will automatically start their circulators if they sense that water in the outdoor unit is approaching freezing to scavenge heat from inside the building.


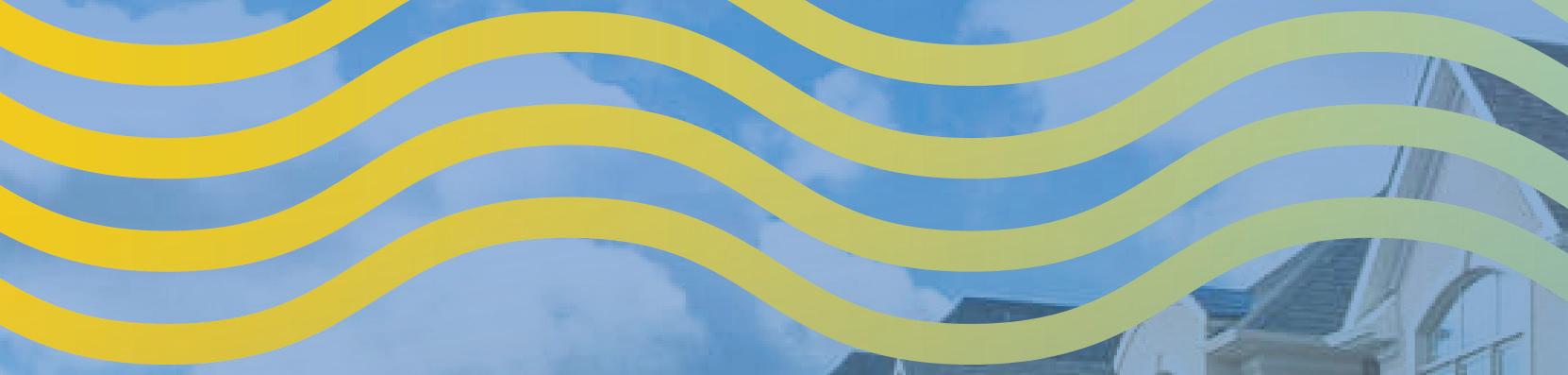
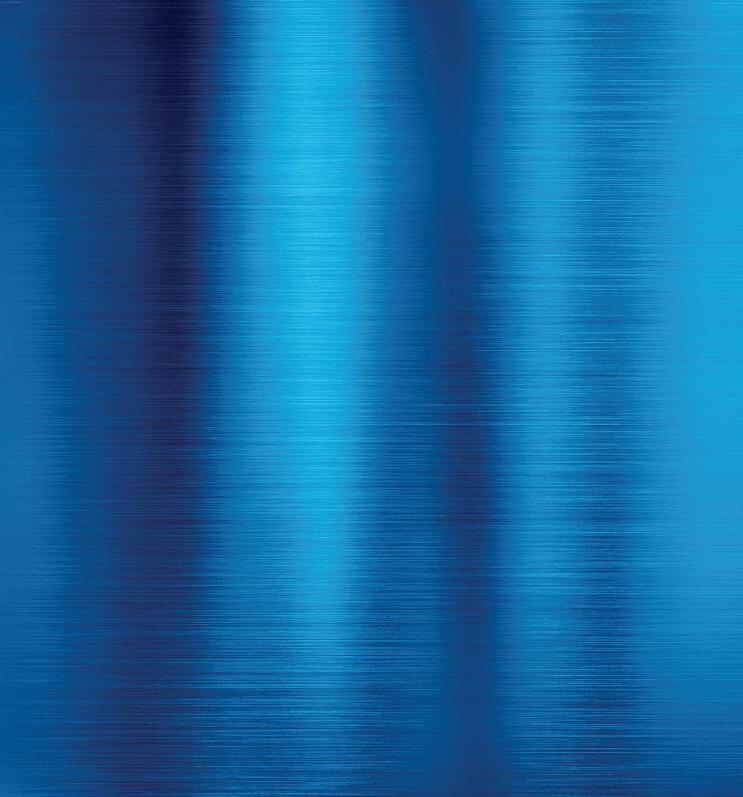
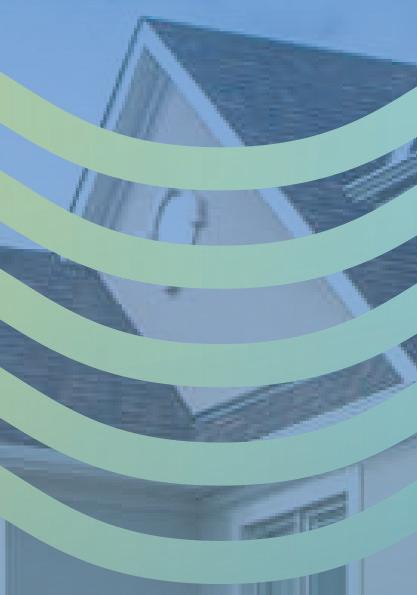
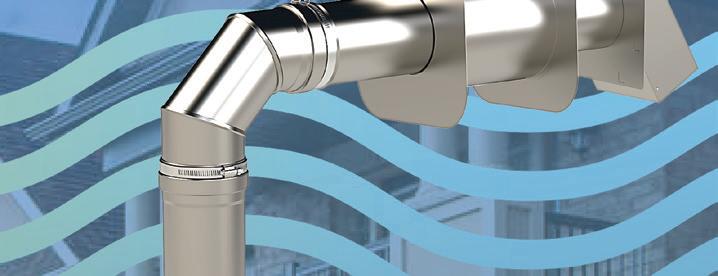
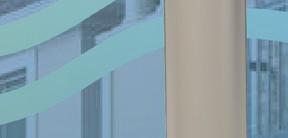

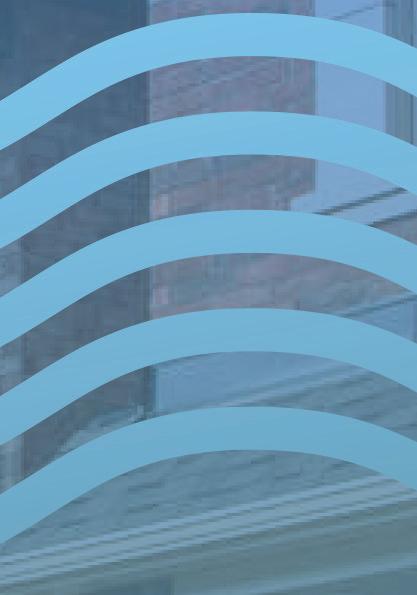

THERMAL PERFORMANCE

For the safety of both property and occupants proper venting of condensing gas-fired appliances is critical
Over time, scaling, poor combustion, elevated temperatures, and lack of maintenance can cause appliance fl ue gas temperatures to rise above safe operating temperatures of plastic vent material
For an added safety margin and peace of mind install Z-VentBLU®
Visit us at Booth 427
Z-VentBLU® a stainless steel vent independently listed by Underwriters Laboratories to UL1738 & ULC-S636 vent standards is rated for a maximum flue gas temperature of 550°F where similarly listed PVC is only rated to 149°F
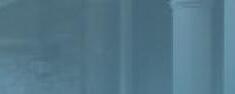
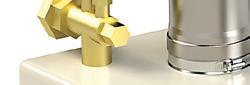

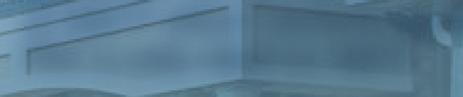


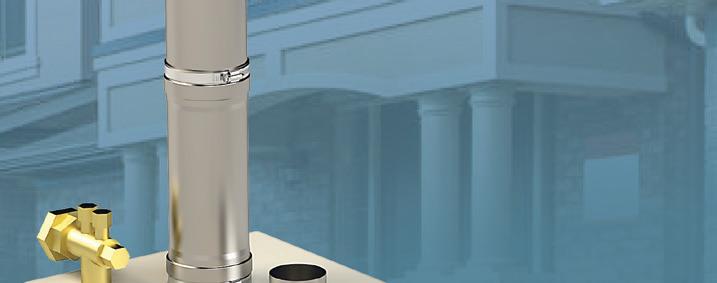
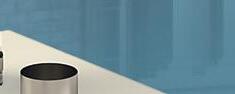
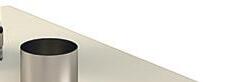
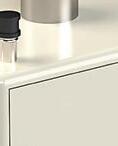
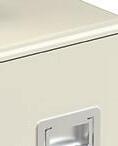


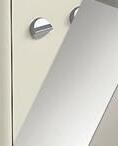
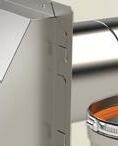
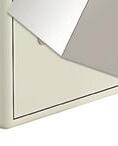
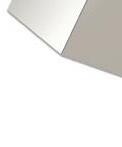

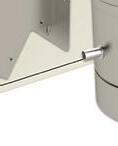
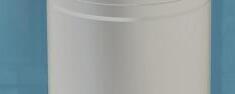
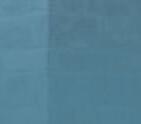
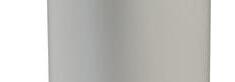
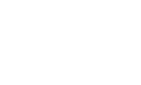
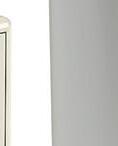

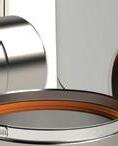



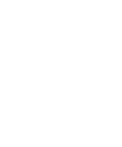
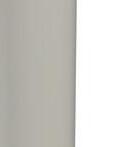
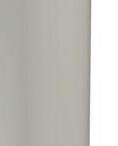
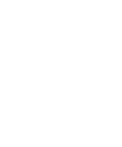

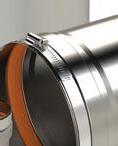
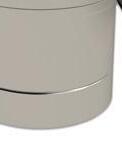
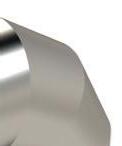
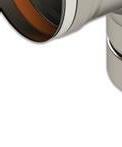
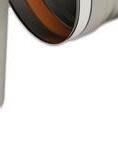

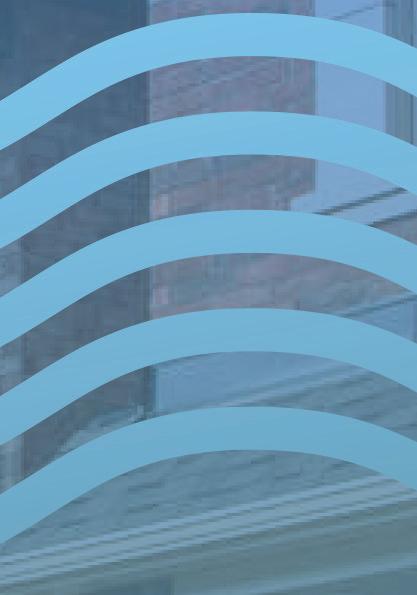

During a power outage that doesn’t work. “The ultimate freeze protection in hydronics is antifreeze. It’s going to work when everything else fails,” he says.
PERCENTAGES
The amount of glycol used in a system will be climate dependent. If you’re up in Northwest Territories, you’re probably going to be using a minimum of 50% possibly a 60% solution, says Siegenthaler. In milder climates you can still use a higher percentage to be on the safe side,

but remember that adding more will require more pumping power.
“It’s a trade-off. You don’t want to be excessive, but obviously you want to have enough to protect the system.”
Setting up the glycol mix, manufacturers have the option of premixed solutions. If the contractor is mixing, the initial water quality is very important. Ideally, use demineralized or deionized water.
Degradation of the glycol over time can be a function of temperature, notes Siegenthaler. “Generally speaking, high temp. applications (i.e. solar thermal) can cause glycol to break down faster.”
It was pointed out by one attendee that not all types of inhibited propylene glycols have the same specifications, there are differences in viscosity for example.
DE-AERATING
One attendee asked about the consequences of mixing glycol with non-
treated water. Not being a biologist, Siegenthaler deferred to following manufacturer instructions. But propylene glycol can react to organic materials in water, so start with demineralized water. It was suggested that concentrations above 25% propylene glycol should not experience bacteria issues in the fluid.
Another attendee asked if there was any difference in removing air from a hydronic system that is using a glycol mixture.
“It might take a little bit longer, but a micro bubble air separator and a good force will do it. It may take a little bit longer with glycol because of the viscosity, but I don’t know of any specialized equipment specific to de-aerating a glycol fluid versus water,” says Siegenthaler. <>
To see the entire webinar video, or any past episode of 30 Mechanical Minutes, visit hpacmag.com/webinars, or visit our YouTube channel, @hpacmag.
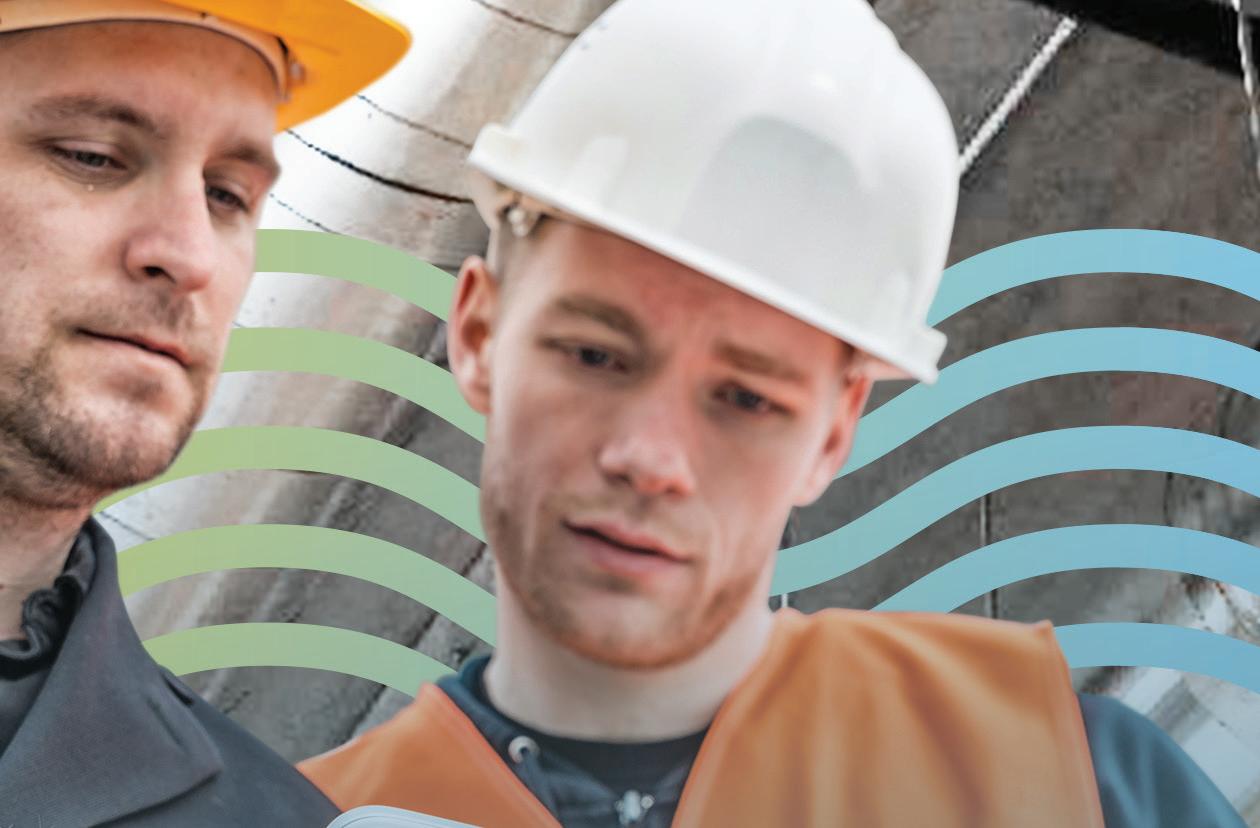


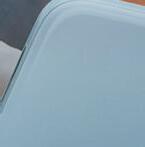
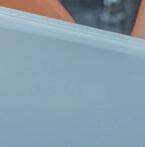
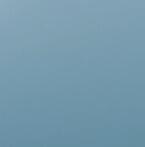
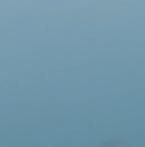
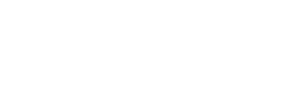
Flange to Flange ZV-Clamp™ outer connection
Factory installed Double Fail-Safe™ self-sealing FKM gasket connection

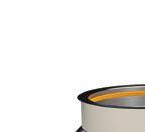

Precision factory formed pipe and fittings, with fusion welded seams


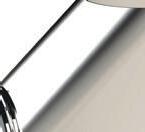
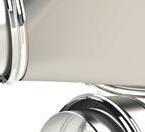
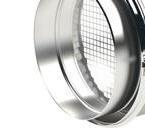
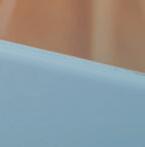
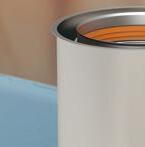


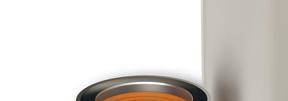
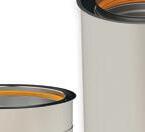
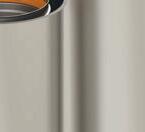
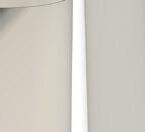
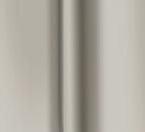
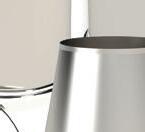


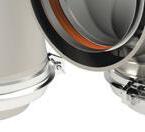

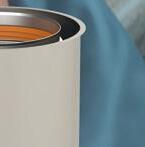


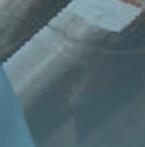
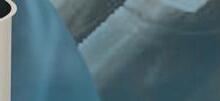
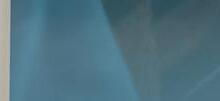
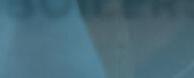
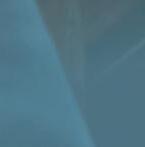
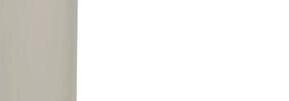
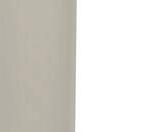
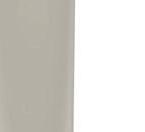
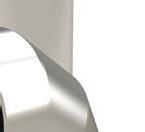
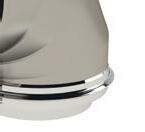
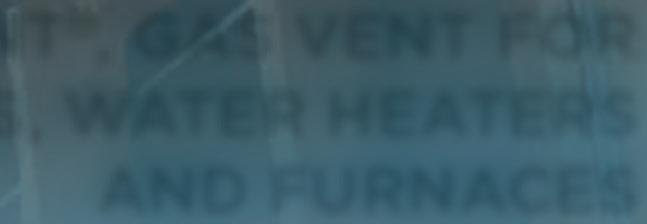

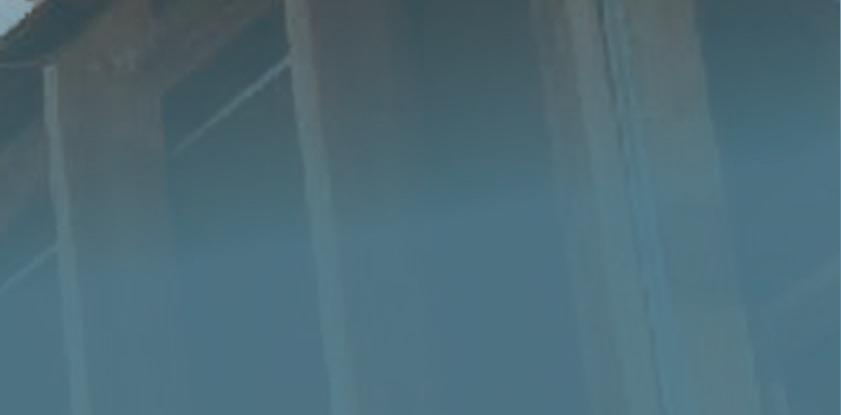




FROSTY THE SNOWMAN
Melting snow can be a delicate situation. BY CURTIS BENNETT
Iam a sucker for ingenuity. I’m that guy that goes on Facebook (not a regular) to watch 5-axis CNC machines work. I love how people problem solve. My favourite shows are about mining, especially Outback Opal Hunters, basically 60 minutes of pure problem solving. I don’t even care about the opal, I care about how they fix things in the middleof-no-where Australia. The ingenuity is OUTSTANDING. One of my favorite characters is 73 years old and he can fix anything, and fix thing fast. Time is money. I am amazed at things like that.
How does this tie into today’s topic. Well, I am sure the first snow melt system ever was just a guy that was like, “man, I hate shoveling,” and so he came up with this ingenious way of how not to shovel. “I’m going to just melt this snow off my driveway somehow!”
Snow melt, as I have said before, is my least favourite control. Not only is it the most problematic system out there, but our industry builds products for efficiency, and snow melt by all definitions is 0% efficient.
The by-product of heating the outside world is you melt the snow off the concrete. I know we need it for ramp heating and safety, but it’s the driveways that “drive” me nuts. But I digress, let’s talk snow melt.
Snow melt controls are kind of just glorified mixing controls. Yes, it’s true. Albeit they have way more inputs than a run-ofthe-mill mixing control, the basis of what they do is the same. The snow sensor tells the control that there is snow, this is our
demand to the control to start doing things.
We have a high temperature device, usually a boiler, and we mix that higher temperature down and push it to the slab. As important mixing can be in a house, it becomes ultra important in a snowmelt control. Why? Good question. What happens to that extra-large ice cube that you throw into your room temperature old fashioned? [Jeopardy music] …. It cracks.
With the ice cube it’s cool when it happens, with a slab of concreate, not so much. Controlling the temperature going out the slab is not based on a reset curve or a setpoint, it’s based on a Delta T. The reason we base it on a Delta T is so we don’t crack the slab.
Let’s go back to our ice cube demo. If you were to put that drink in the freezer for a bit, cool down the liquid to just above freezing, when you drop the ice cube in it won’t crack. There is no thermal shock to the ice cube.
The same applies to our slab. If we keep the supply water “fairly” close to the return water temperature, usually 20F to 25F, then like the second example of the old fashioned, the slab won’t get shocked.
Controlling this mixing can be done a couple of ways. The first is 3 or 4 way mixing valves. The main reason these systems are used is volume. In snowmelt systems “we” usually run about 50% glycol. What does glycol do to water? It makes it thicker. So, we need bigger pumps to push it around, that is also on top of the fact that we need way more
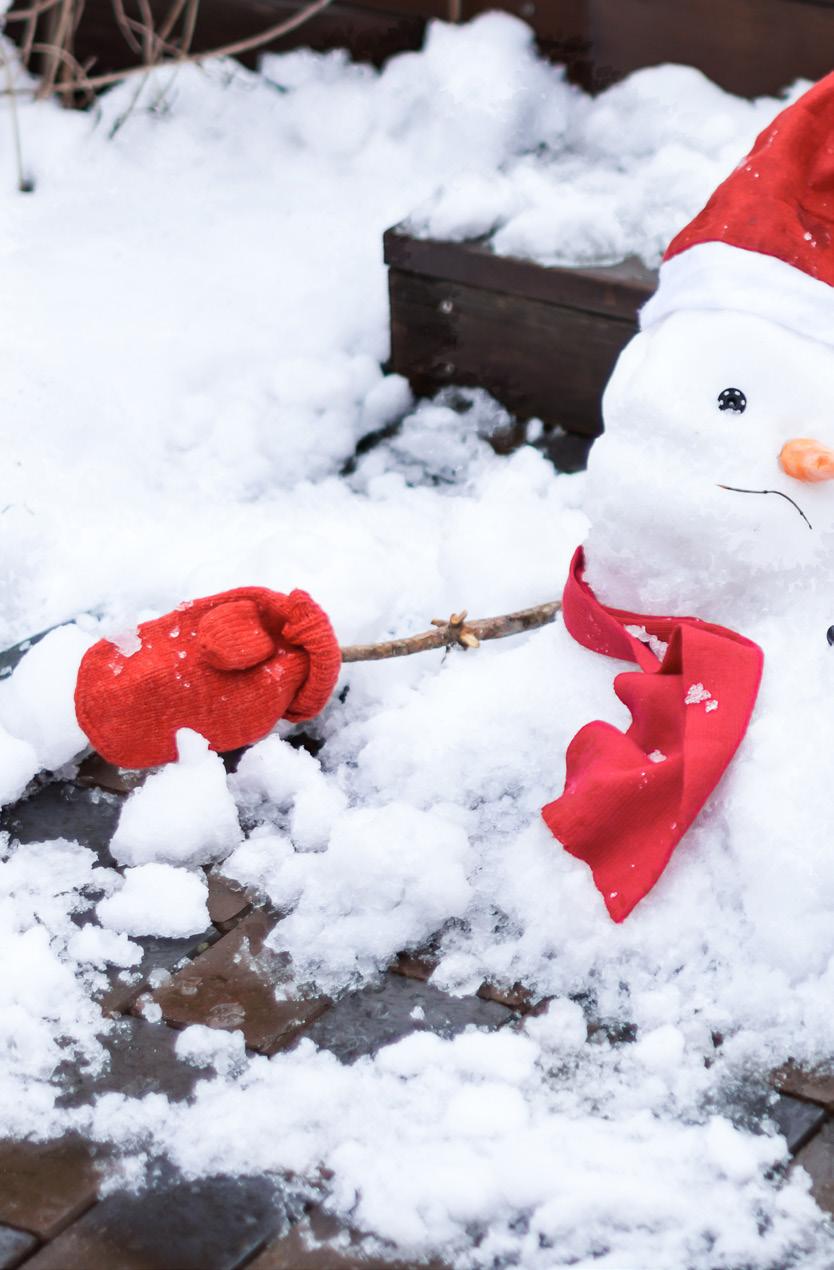
Btus per square foot for snowmelt. Remember these systems are outside. Both of those requirements equate to big pumps. This also means big heat exchangers. In snow melt systems we always keep the two portions separated with a heat exchanger. This way we don’t run 50% glycol through the portion of the system inside the building. We mix off the secondary side of the heat exchanger in this case carefully mixing the water temperature to achieve the consistent Delta T for the slab.
The signal to the mixing valve is the portion that gets “mixed” up the most. Everybody calls them both modulating valves. This is true, but to a controls guy like me they are very different. There are two types of mixing valves: floating action and 1-10VDC. Now both valves modulate up and down, and I think that is where the hangup usually is.
A floating action valve takes two 24VAC signals and one common. You hit one side with 24VAC “R”, and the valve opens, hit the other and it closes. It also stops if you take off both signals. This is how it “modulates” (see how I put that in quotes).
When it finds just the right mixing point to achieve the temperature output it can stop there. The second type is the
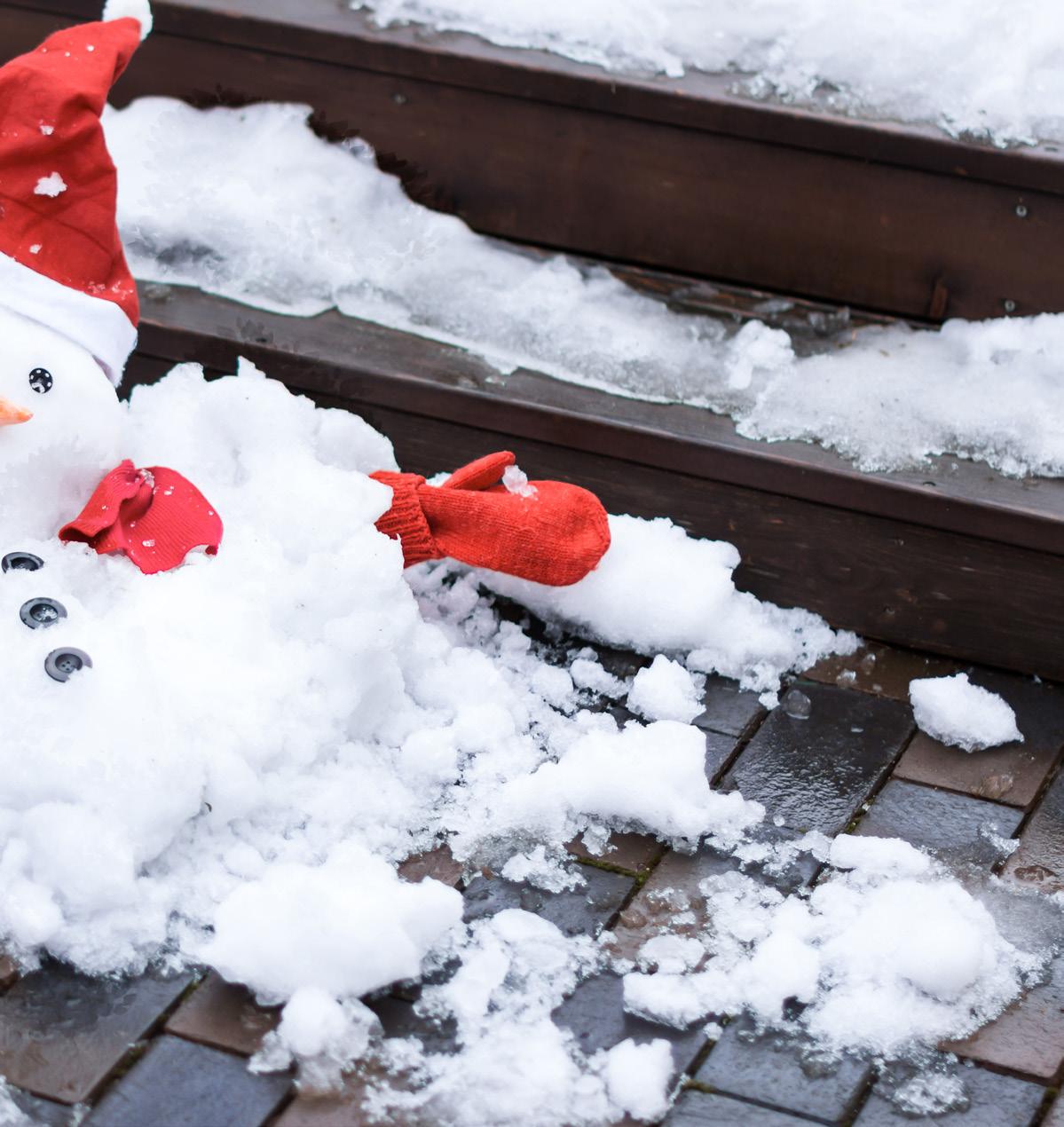
1-10VDC mixing signal. This valve is powered with 24VAC and a +1-10VDC signal to modulate the valve. As the signal goes up the valve opens more, to stop the valve where it’s at, the signal just stays where it was at and the valve won’t open or close any more.
The second type of mixing is injection. Good ole primary secondary injection! Taking a “hydraulically” separated fluid (I’m sure you already know this) and pumping it into a main system loop using closely spaced t’s. In this scenario you can get away with some smaller equipment.
By using higher Delta T’s on the boiler side you can use lower flow rates. This article is about controls, not mechanics. LOL. Back on track. There are a lot of pumps out there now that take a 1-10VDC signal to use as injection. These are a good choice to do the job right. ECM pumps are kind of everywhere now, and all manufacturers have them. This way you can have good and tight control of the Delta T.
Remember we talked about shocking the slab, so control of your Delta T is important. The setpoint for the system temperature on a snow melt control is determined by the return temperature coming back from the slab. We add our desired Delta T on top of that to give us the target for the system temperature. This temperature is moving, as is the boiler temperature on the other side of the heat exchanger, so we need to have accurate mixing to hit it properly.
One other aspect of mixing out to the slab is that we can protect the boiler as well. Protecting the boiler doesn’t seem to make sense most of the time, but it is possible to freeze the boiler in a snowmelt system. It freezes the condensate inside the boiler. I think we all know that’s a bad thing!
The return water can be below freezing—remember that the slab (using a glycol mixed fluid) is usually kept well below freez-
ing until snow is sensed. If you don’t keep the slab temp low when there is no snow, the slab won’t be the only thing that can get shocked!
So, by using a mixing device you can shut off the temperature going out to the system, which in turn stops the possible freezing return water temperature coming back to the boiler. You can essentially give it bumps of hot water into the system until the return water temperature is above the freezing point.
“Controlling” your Delta T is so important. The last thing you want is to damage the slab; by using some tried and true mixing techniques we can ensure a smooth temperature and Delta T. Nobody likes shoveling snow. Don’t lie to yourself, no you don’t. As for the safety aspect we also need good control to make sure no one slides into the garage door of a down ramp to a condo or industrial building. Smashed doors are also no fun for anyone. <>
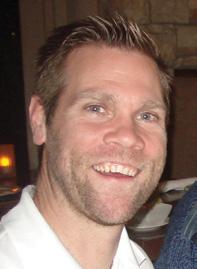
Curtis Bennett C.E.T is product development manager with HBX Control Systems in Calgary. He formed HBX Control Systems with Tom Hermann in 2002. Its control systems are designed, engineered and manufactured in Canada to accommodate a range of hydronic heating and cooling needs.

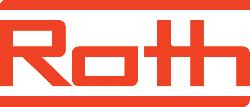
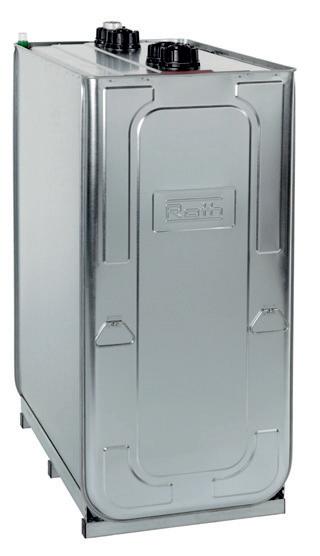
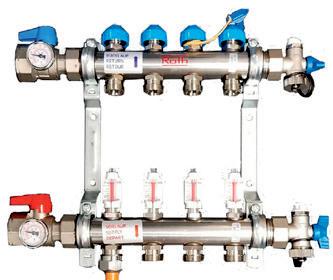
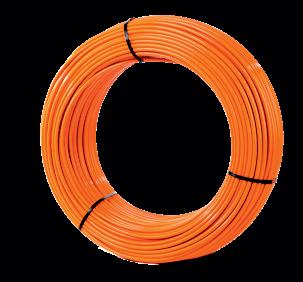

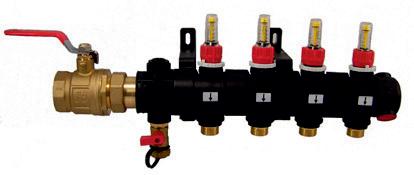
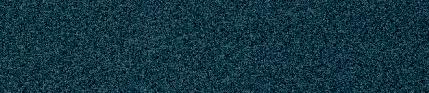
HAUNTED THEATRE RECEIVES MODERN UPGRADE

Historic site in Vernon, B.C. retains its old-world charm while its steam heating system gets a boost with networked controls.
BY DAN VASTYAN
Known for its vintage charm and intimate atmosphere, the Vernon Towne Theatre, located on the main street in Vernon, B.C., offers a unique experience for moviegoers and event attendees.
With its classic marquee and art decoinspired interiors, the theatre maintains
an old-fashioned ambiance while showcasing both first-run movies and independent films, as well as hosting concerts and community events.
Rumors circulate that the old building is haunted. Some visitors are skeptical, but most of the staff believe the stories.
“The rumours go back many decades and have continued to current day with employees experiencing unexplainable phenomenon,” says Scott John, theatre manager. “It’s been featured in books and paranormal TV shows as one of the most haunted locations in Canada. There are documented cases of deaths in the theatre, that may have added to the legend.”
Strange, intermittent noises come from inside the walls. Troy Lehr, general manager at Brown Mechanical Services, the local contractor with the maintenance contract for the theatre, has his own theory.
“The noise is largely due to an old steam piping system, coupled with a wood structure that was built in 1929,” he explains. “The creaks that are heard when the heat is on are part of the building’s character that will likely be with it for life.”
Creaking, as Lehr describes it, is likely caused by the expansion and contraction of steam pipes, which rub on the wall studs. Steam hammer can also be
The Vernon Towne Theatre receives its regular service from local contractor, Brown Mechanical Services; both have been fixtures in town for a long time.
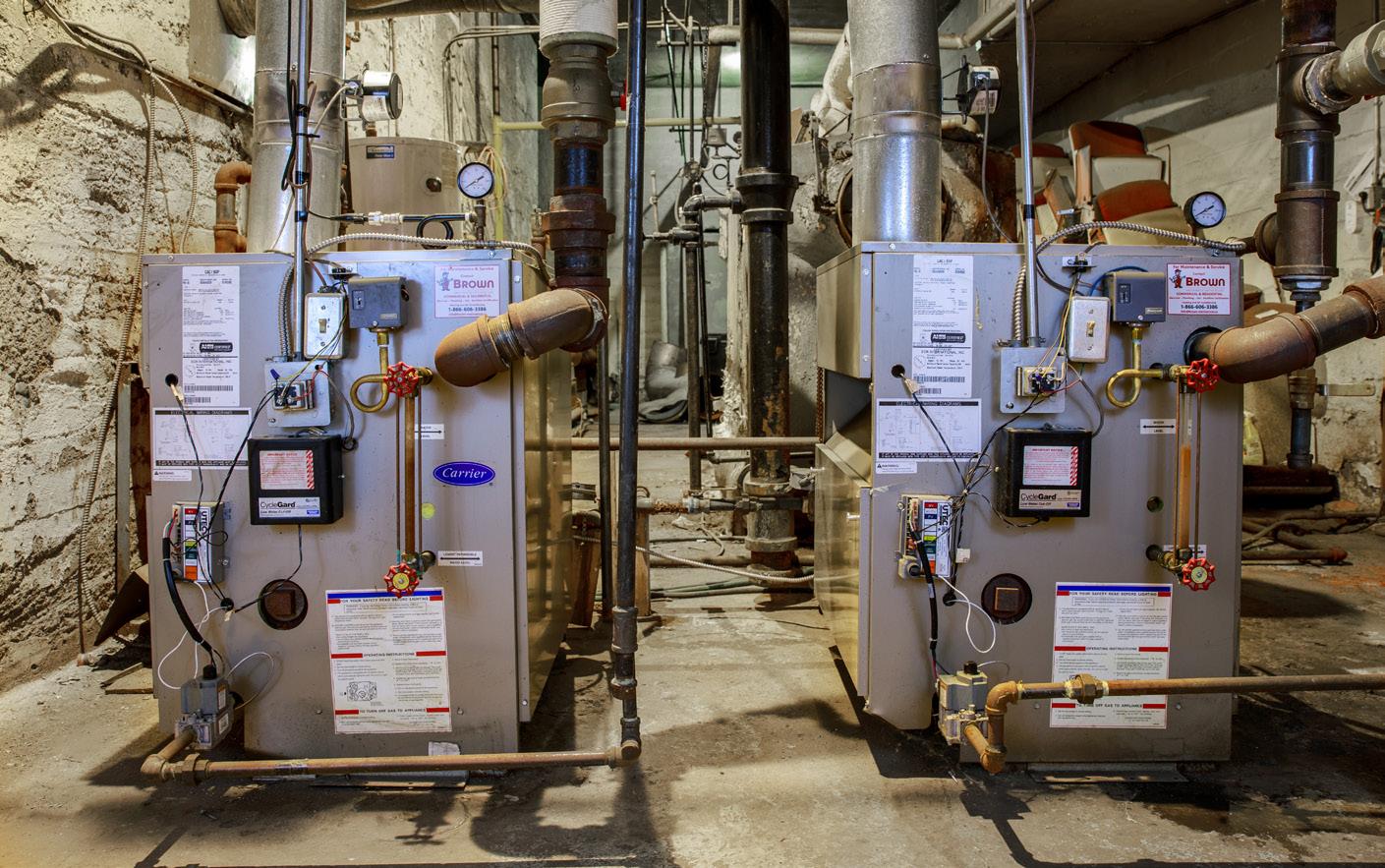
heard, which occurs when condensate water collects in the sagging return pipes. Steam pressure then throws the water down the pipe until it hits an elbow, creating a ghastly ring.
There are no plans to fix these issues, simply because and entire retrofit would be too costly and invasive. Plus, evicting the ghosts would detract from the build -
ing’s historical panache.
Phantom noises aren’t the only oddity at the cherished cultural venue. Originally a dance hall called The Capitol, the building was converted into a cinema in 1938, and the Vernon Towne Theatre is one of the few theatres in North America that still has its old 35mm film projector hooked up and useable—though a new
digital system is the workhorse of the venue. In the boiler room, the original Viking coal-fired steam boiler is also still in place, though it has long been abandoned.
MODERNIZATION
Brown Mechanical Services is a nine-person 40-year-old company based in Vernon, and the team has worked at the theatre for years, though they entered a service contract with theatre management only recently in the summer of 2024.
Since then, they’ve been improving the health of the two-pipe steam and plumbing systems. Steam traps and vents have been replaced and the two 299-MBH Carrier cast iron boilers have been cleaned and calibrated.
To combat winter conditions, which can drop as low as -35C in Vernon, the theatre has cast-iron radiators providing heat in the projection room, baseboard
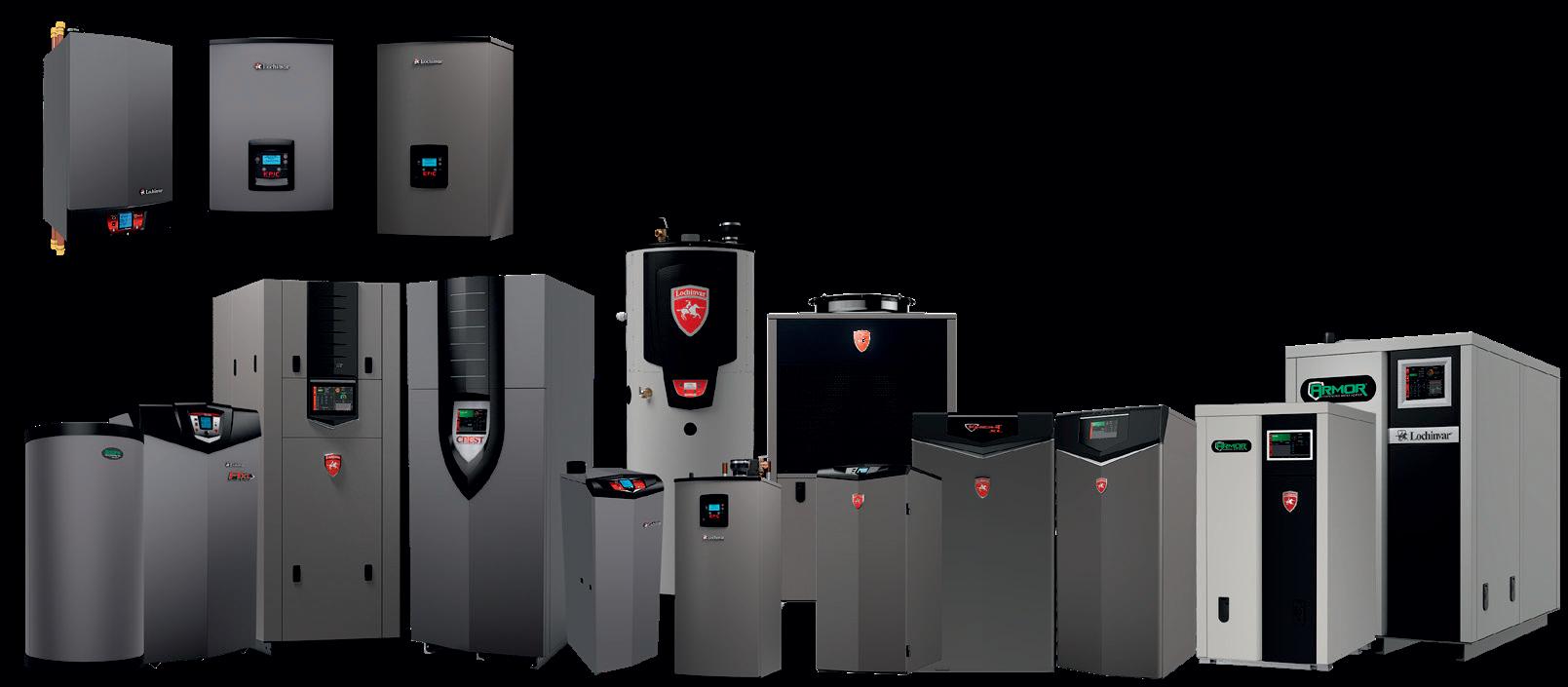
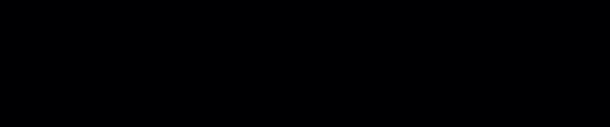
commercial and
residential space and water heating solutions that engineers, specifiers, builders and contractors can depend on. Turn to AQUATECH for heating and hot
Heat in the theatre is provided by two 299 MBH Carrier cast iron boilers and a two-pipe steam system.
heaters installed along the lobby, and an air handling unit with a steam coil conditions the auditorium.
Until the summer of 2024, the dualboiler steam system at the theatre has been “dumb.” There’s no building automation system, and both boilers fired when there was a call for heat.
To bring some modern touches to the system, before the 2024-2025 heating season began a tekmar Smart Steam Control 289 was installed to improve the efficiency and longevity of the system. It also helps to simplify maintenance for the Brown Mechanical team.
The new system is a web-enabled boiler control designed to operate up to two steam boilers on either one or two pipe steam applications. The control system can provide up to 20% energy savings through outdoor reset technology, indoor temperature feedback, and warm weather shutdown.
“Through the Watts OnSite mobile and web app, we can remotely monitor the heating system at the theatre,” says Lehr.
“The control notifies us of anomalies to ensure the system is operating efficiently and comfortably in the building. It also provides runtimes across the boilers so we can balance the system to ensure maximum life of equipment is achieved.”
With these new remote insights and a better understanding of what’s going on in the steam system, many issues can be identified and addressed before a noheat scenario arises. It also reduces the number of staff hours needed onsite.
The outdoor reset technology built into the control provides progressively longer boiler runtimes as the outdoor air temperature drops. And conversely, runtimes are shorter when the outdoor temperature rises.
“The control stages the two boilers based on pressure, using a pressure sensor,” explains Lehr. “It also rotates the two boilers to provide equal run time and helps point our techs to areas that may require attention. We can see all of
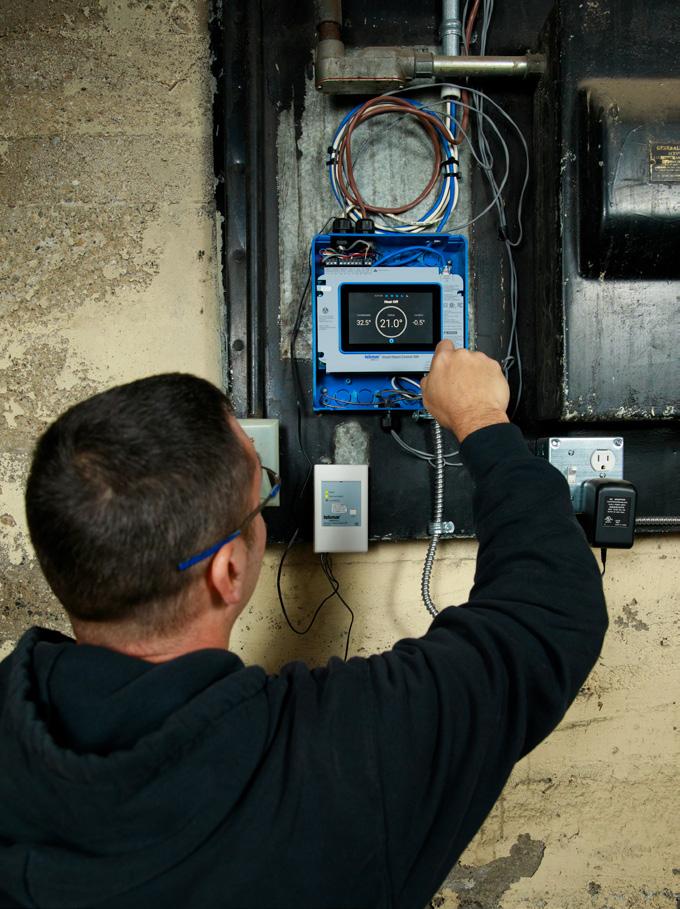
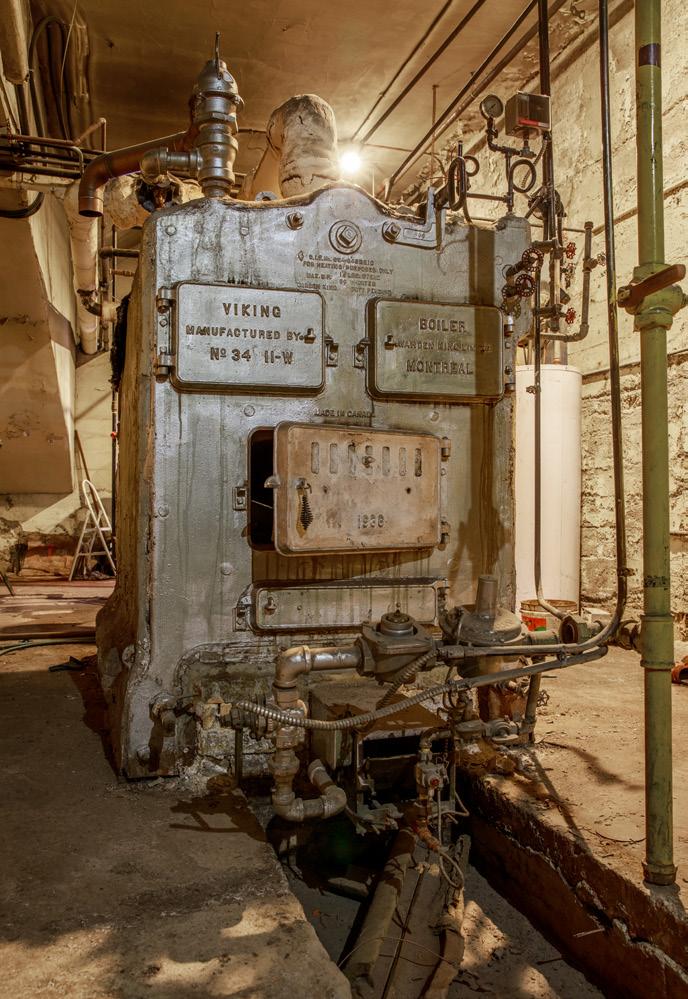
this and make many changes within the system through the app, without ever leaving the office.”
The new control has helped Brown Mechanical’s technicians care for the theatre heating system, but it’s also simplified the system for theatre staff, too.
“The ability to remotely control our system with the tekmar dashboard has been great,” says John, the theatre manager. “We can log on and see the status of the boilers and receive error or warning notifications. Our hours can be variable, so the ability to change the temperature and start the system via the dashboard and start warming up the theatre has been helpful.”
“We haven’t determined the exact energy savings from the addition of the new control, but we know our energy costs are lower. We have yet to account for variables like heating degree days and occupancy hours.”
This year’s heating season will provide a better picture of the energy savings provided by the new control, so long as a supernatural presence doesn’t take up residence in the boiler room.
“It’s exciting to see our Smart Steam
Control 289 bringing both efficiency and modernization to a historic landmark like the Vernon Towne Theatre,” said Mercedeh Fallahkhair, senior product manager at tekmar Control Systems, which also happens to be located in Vernon. “This project showcases how innovative solutions can enhance energy efficiency while respecting the building’s vintage charm. Our technology simplifies maintenance for service providers and delivers meaningful benefits to building owners and operators alike.”
The Vernon Towne Theatre demonstrates how thoughtful upgrades can breathe new life into historic spaces while preserving their unique character. <>
Dan Vastyan is president of Common Ground, specializing in marketing communications and serving the North American construction industry with a focus on plumbing, mechanical and HVAC markets. danv@seekcg.com
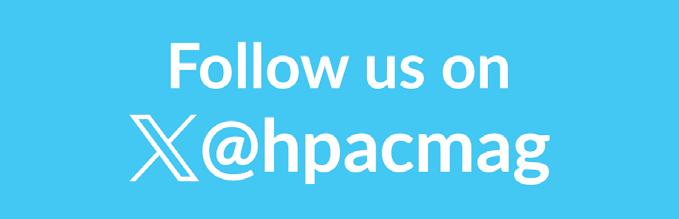
Brown Mechanical technician Chris Bibby installs the tekmar Steam Control 289 in the theatre’s mechanical room. It provides remote access to the theatre’s heating system.
The theatre’s original steam boiler, a Viking coal fired unit, remains in place although it has long been abandoned.

A MIX OF OLD AND NEW

Making the case that new air-to-water heat pumps can still work effectively with older boiler systems.
BY JOHN SIEGENTHALER
There’s a lot of interest in adding an air-to-water heat pumps to existing hydronic heating systems supplied by fossil-fuel boilers. I get inquiries on that subject almost every day.
An air-to-water heat pump is a state-ofthe-art device for producing heat. By comparison, a cast-iron boiler might be considered (by some) to be outdated technology. I’ve even been asked: “John, why do you still talk about cast iron boilers, they’re the ‘dinosaurs’ of our industry.”
That’s not my take. Although I strongly support the use of air-to-water heat pumps in applications where they can perform well, I don’t support doing so by
first ripping out a perfectly good cast-iron boiler that has remaining service life.
GRAY IRON IS GREEN
I’ve specified many cast iron boilers over the years and have had excellent results in terms of reliability, minimal service requirements and stable performance.
I have an oil-fired cast iron boiler in my home that’s 26 years old and still going strong. There’s another identical one in my office that’s 25 years old, and it still looks like the day it was installed. I fully expect to get another 10+ years of service from both boilers (assuming it’s still legal and affordable to purchase fuel oil).
Can you name an appliance in your home that has lasted 25 years or more? Refrigerator? Washing Machine? Dishwasher? Microwave? Mod/con boiler?
I’ll stop short of saying that cast iron boilers are “bullet proof,” but when properly applied and maintained they’re likely to outlast any alternative hydronic heat source.
When they do reach the end of their service life the cast iron is highly recyclable. About 90% of the cast iron used in a new boiler is recycled iron from scrap such as old fire hydrants, railroad car wheels, bathtubs, or recycled old boilers. Today, over half the boilers used in new North American hydronic systems are capable of operating with sustained flue gas condensation. When properly applied they can attain efficiencies in the mid-90% range.
WHAT TO DO?
This leads to a question that’s likely to come up when a client wants to add an air-to-water heat pump to their existing hydronic system, and they want to use a boiler as the backup to the heat pump: “Is it be better to remove the existing conventional boiler operating at an AFUE of say 85%, and replace it with a mod/ con boiler operating at an assumed AFUE of 95%?”
To help answer this question, consider the following scenario:
– Building: 2,500 sq. ft. house with design load of 20 Btu/h/ ft2.
– Building design load: 50,000 Btu/h at outdoor temp.= 0F, and indoor temp. = 70F.
– Average internal heat gain: (1 kW) or 3,413 Btu/h.
– Location: Syracuse, NY, 6,720 heating degree days.
– Heat Pump: 4-ton rated, low-ambient air-to-water.
– Distribution system: fin-tube baseboard requiring 170F water at design load.
– Existing boiler : 60,000 Btu/h oil-fired cast-iron, with AFUE = 85%.
– Alternate boiler : 60,000 Btu/h condensing boiler, with AFUE =95%.
– DHW load: 60 gallons per day, heated from 50-120F.
– Cost of fuel oil: $US 3.36/gallon*.
– Cost of propane: $US 2.70/gallon*.
– Supply water for space heating: based on outdoor reset.
– Defrost correction on heat pump performance in effect.
– Upper temperature limit allowed for heat pump: 130F, all heat required at higher supply water temperatures is provided by the boiler. (*prices from Fall 2024, upstate New York)
The existing system has an oil-fired cast-iron boiler. There are
no mod/con boilers that operate on fuel oil (at least at present in North America), so a decision to convert an oil-fired boiler system in a rural location to a mod/con boiler would force a fuel change to propane.
Using simulation software the estimated heating energy use for the above system is as follows:
– Seasonal space heating energy required by house: 110.6 MMBtu
– Yearly domestic water heating energy : 12.7 MMBtu
– Total heating energy required = 110.6+12.7 = 123.3 MMBtu (1 MMBtu = 1,000,000 Btu)
The delivered cost of heat from the existing oil-fired boiler operating at AFUE = 85%, and with the above fuel oil pricing (US$3.36/gallon) is US$28.22/MMBtu.
The delivered cost of heat from a mod/con boiler operating at 95% AFUE with the propane pricing (US$2.70/gallon) is: US$30.98/MMBtu.
Using the above assumptions the simulation software indicates that the nominal 4-ton low-ambient air-to-water heat pump would provide 114.1 MMBtu of the total heat, and the boiler would provide the remaining 9.3 MMBtu.
INTRODUCING
All New Commercial Boilers and Volume Water Heaters
Whatever your needs may be, you can trust that you’re installing a product that is produced to the highest standards. Both models offer our Peace of Mind Warranty Program. Choose Triangle Tube for efficient and reliable solutions for your heating and hot water needs.
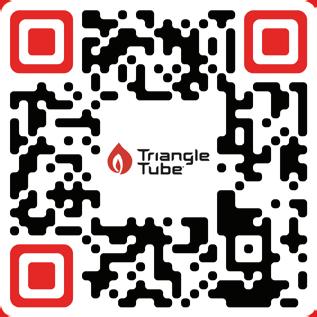
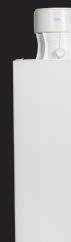
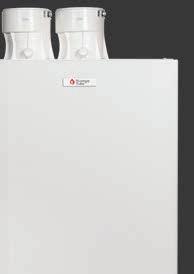

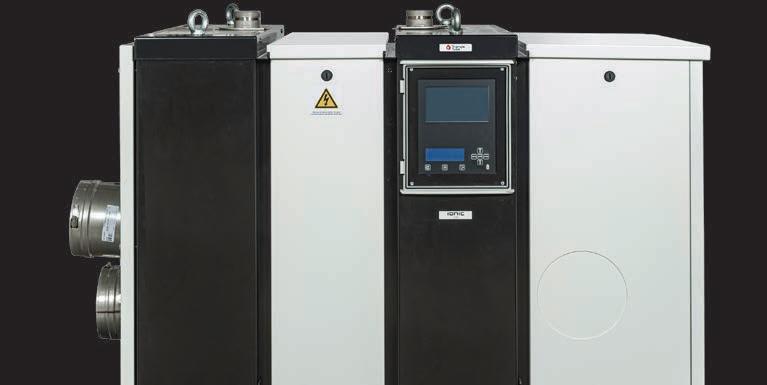
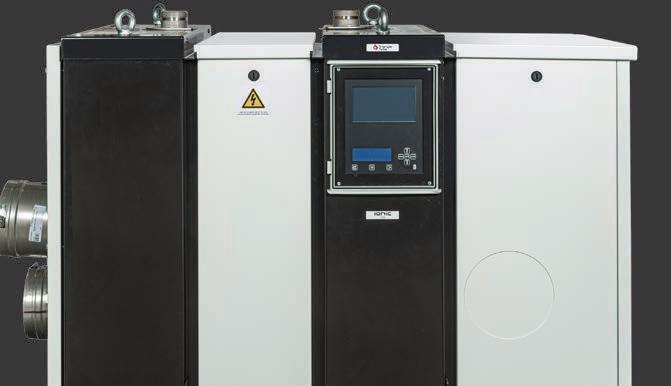
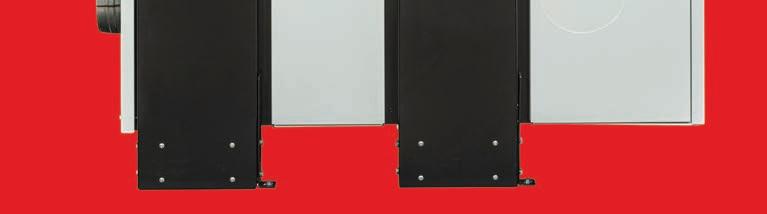
That 9.3 MMBtu is only about 7.5% of the total annual heating energy, and as you’ll see, this informs the decision about upgrading the exiting boiler.
The simulation software estimated the seasonal average COP of the heat pump to be 2.78.
If the existing oil-fired boiler remained in place the cost of the 9.3 MMBtu auxiliary heat would be: 9.3 MMBtu x US$28.22/MMbBtu = US$263 per year.
If a new mod/con boiler produced this heat it would cost: 9.3 MMBtu x US$30.98/MMBtu = US$288 per year.
Based on these numbers the cost of operating the 95% efficient mod/con boiler on propane (at the fall 2024 local price) would be about US$ 25 more than the existing cast iron boiler operating at 85% efficiency on fuel oil (at the fall 2024 local price).
These two costs are obviously very close, and different fuel pricing or thermal efficiency assumptions could make the mod/con boiler the lower cost option. The take away is that the installation cost of new boiler is definitely NOT justified based on fuel cost savings.
HOW ABOUT ALL ELECTRIC?
I also ran a comparison based on installing an electric boiler as a replacement to the oil-fired boiler. The cost of electricity in the same area was US$ 0.25 per kWhr. The 9.3 MMBtu of auxiliary heat would cost US$ 681 if supplied by an electric boiler (or other resistance heating elements). That’s US$ 418 per year more than if the heat was supplied by the existing oil-fired boiler, and US$ 393 more per year than if that heat came from the mod/con boiler.
WHAT ABOUT NATURAL GAS?
Suppose the existing conventional boiler was fueled by natural gas. The most recent data for pricing of natural gas in this region is US$ 2.32 / therm (1 therm = 100,000 Btu).
If an existing gas-fired conventional
boiler remained in place, and operated at an AFUE of 85%, the cost of the 9.3 MMBtu auxiliary heat would be 9.3 MMBtu x US$27.29/MMbBtu = US$ 254 per year.
If the existing gas-fired conventional boiler was replaced with mod/con boiler operating with an AFUE of 95%, this heat it would cost 9.3 MMBtu x US$24.42/ MMBtu = US$227 per year.
The annual savings would be US$254US$227 = US$ 27 per year. True, it’s a savings based on the assumptions, but hardly one that justifies removal of the existing boiler and replacing it with the mod/con boiler at an estimated cost of US$ 9,000.
The take aways from this example:
1. A properly sized and controlled air-towater heat pump is capable of providing just over 90% of the total heating energy required for the typical house, even in a relatively cold climate, and even with heat emitters that require 170F supply water temperature at design load.
2. The use of outdoor reset allows the “high temperature” heat emitters to be supplied reasonably well by the air-to-water heat pump on a seasonal basis, especially considering the simulation limited the supply water temperature from the heat pump to 130F. Any heating energy required above this would come from the boiler.
3. The underlying reason for these results, which probably weren’t intuitive, is that whatever auxiliary boiler is used in the system, it’s only supplying a small percentage of the seasonal heating energy. That’s going to produce economics that are far different from the more common scenario of replacing a conventional 85% efficient boiler with a 95% efficient boiler, where either boiler would provide all heating energy. It’s not just about efficiency; it’s about how much fuel gets processed though the boilers at those efficiencies.
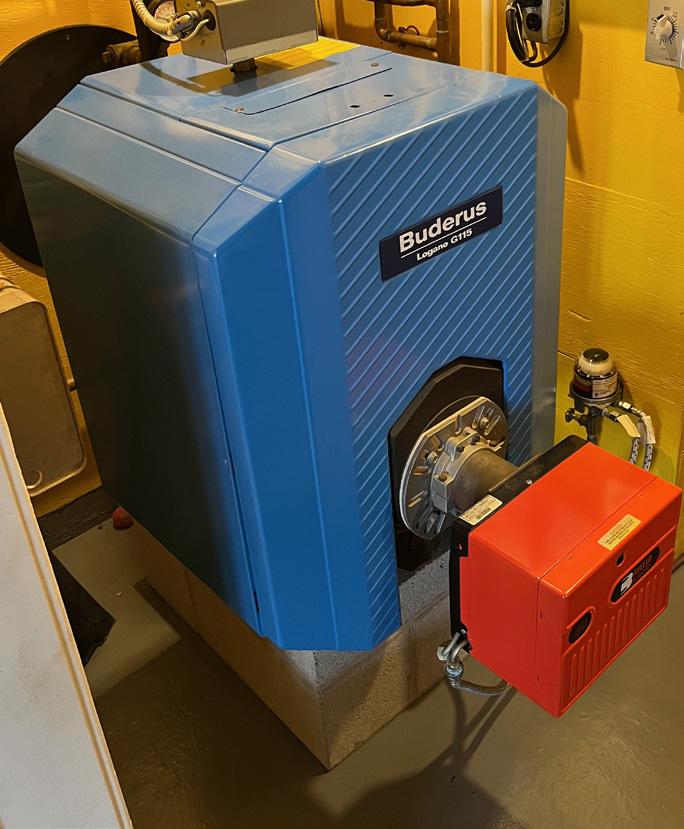
4. The cost of removing the existing oilfired boiler and its fuel tank, and replacing it with a mod/con boiler could easily be US$9,000 or more in today’s market. With little if any savings generated by a scrapping the exiting boiler and replacing it with a mod/con boiler there’s very little, if any, economic justification. Still, different clients have different goals. Some just want to rid themselves of anything that operates on fossil fuel. You may not agree with that goal, but you can make it happen, and profit from it.
NO GUARANTEES
Government (and global) manipulation of energy prices, or increases in carbon taxes, could significantly skew these comparisons. Still, for the recent prices used in this comparison it appears there’s merit in designing air-to-water heat pumps systems that retain existing boilers that have remaining service life— even those older cast-iron boilers. They’re not necessarily the “dinosaurs” that many claim them to be. <>
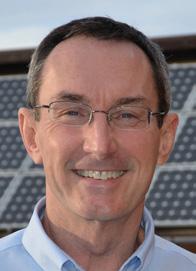
John Siegenthaler, P.E., has over 40 years of experience designing modern hydronic heating systems and is the author of Modern Hydronic Heating (4th edition) and Heating with Renewable Energy (visit hydronicpros.com).
No sense replacing an old cast iron boiler when backing up a heat pump if cost is the main factor.
PHOTO: JOHN SIEGENTHALER
CANADA’S HYDRONIC
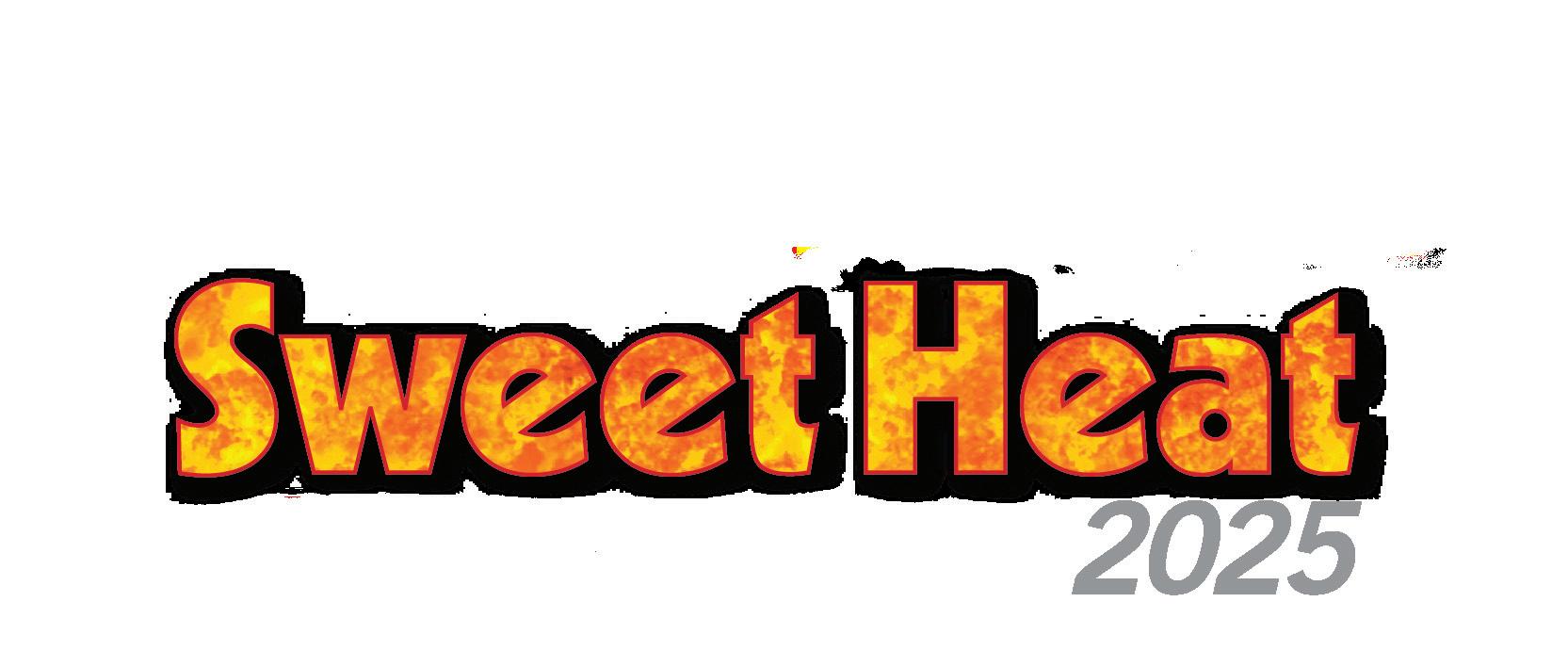
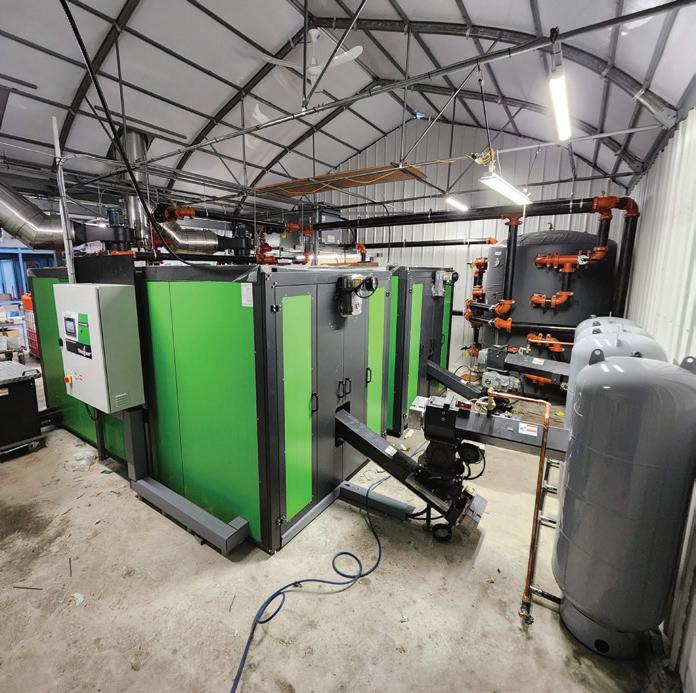

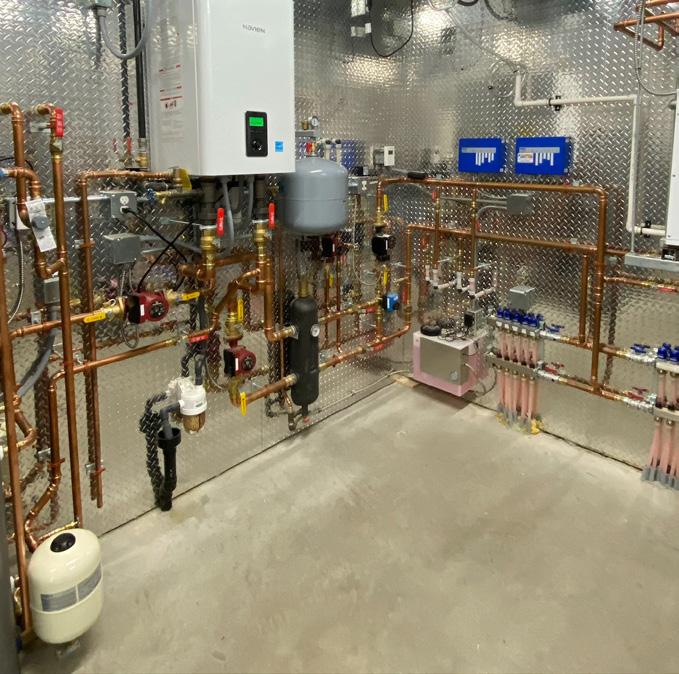
Proud of your work? Better than the rest? It’s time to bring it on!
THERE WILL BE A WINNER IN EACH CATEGORY: COMMERCIAL, RESIDENTIAL NEW-BUILD & RESIDENTIAL RETROFIT
ENTRY IS SIMPLE - send us pics of your installation. Include a brief description of the particular challenges that you faced with this installation and how you overcame the obstacles. Submissions are limited to one per contractor. Deadline to enter is July 31, 2025. The three winners will also be announced by John Siegenthaler at the Modern Hydronics Summit 2025. In addition to having your winning entry shared across our social media channels you’ll also be interviewed by HPAC’s editor and featured on the cover of the October edition of HPAC –
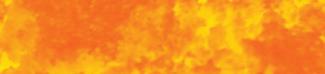
2024 Commercial Winner BT Energie – St-Joseph-de-Beauce QC
2024 Residential Retrofit Winner Farr Mechanical - Stouffville ON
2024 Residential New Build Winner Donaldson Plumbing & Heating - Kingston ON

The Perfect BALANCE
The ideal manifold and tubing for the distribution of heating fluid in radiant systems
Thanks to our ideal set-up for installers using our unique flow meters on each manifold loop, IVAR stainless-steel manifolds guarantee perfect system balancing, optimizing energy use, while providing premium thermal comfort.
Every manifold set is supplied with all components included in the box, ensuring a smooth commissioning process for radiant system installers.
Pair the IVAR Manifolds with our premium VIPERT™ (PE-RT) Oxygen Barrier Tubing, manufactured specifically for radiant systems, and you have a winning solution every time.
Take advantage of our in-house hydronic expertise, including LoopCAD design and layouts customized for each of your residential and commercial projects.