
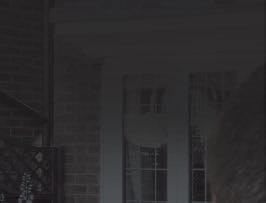
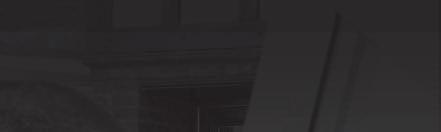
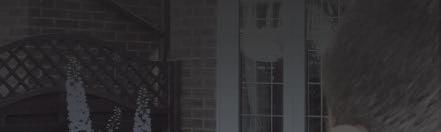
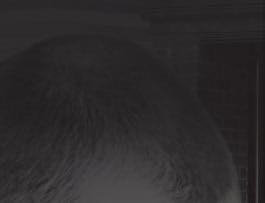
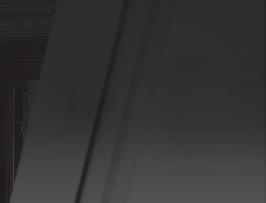
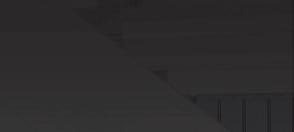
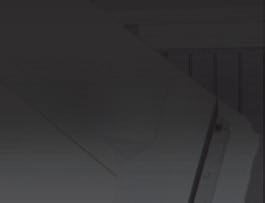
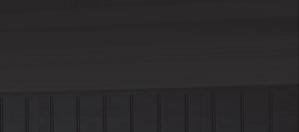
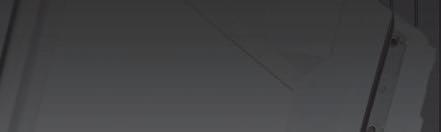
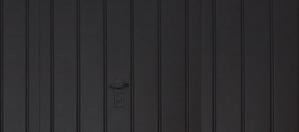
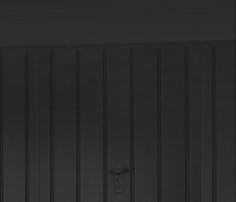
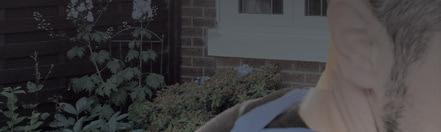

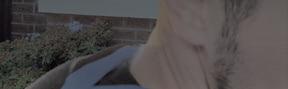
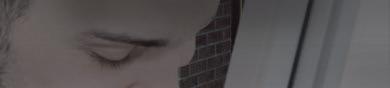
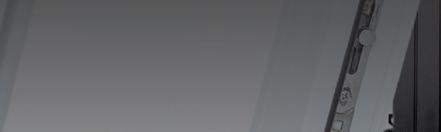
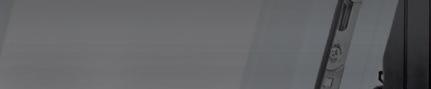
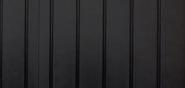
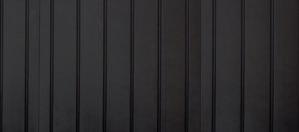
The persistent rise in theft from building sites has presented the construction sector with increasing difficulty in recent years, raising questions as to why, who’s responsible, and what to do about it.
Earlier this year, our UK Construction Crime Index revealed 7 in 10 construction workers witness theft as regularly as once a year, causing delays to at least one-third of projects.
The increasing cost of building materials is the primary factor contributing to the growing sophistication of theft from construction sites. The demand for commodities like copper, steel, and timber has increased due to global economic trends and supply chain disruptions, making them desirable targets for thieves looking to make quick cash. Our report shows copper and cable top the tables as the
most frequently targeted goods – delaying critical infrastructure, such as railways.
Technological advancements have also
Modern construction sites are equipped with sophisticated equipment and machinery, which, if left unsecured, become vulnerable to theft. Highvalue items such as excavators, generators, and power tools are increasingly targeted."
empowered thieves with new tools and tactics to carry out their illicit activities. Modern construction sites are equipped with sophisticated equipment and machinery, which, if left unsecured, become vulnerable to theft. High-value items such as excavators, generators, and power tools are increasingly targeted. Thieves are leveraging drones and GPS tracking devices to scout sites and identify valuable assets, enabling more strategic and coordinated theft operations.
A concerning trend is the rising level of organisation among criminals involved in construction site theft. Instead of opportunistic individuals, organised crime networks are orchestrating targeted heists on a larger scale. Last year, insiders orchestrated the largest copper heist in history, stealing 1 million euros worth of copper from Germany's Aurubis. Additionally, our own Construction Crime Index revealed that 1 in 3 construction workers, who are directly exposed to such crimes, believe that criminal tactics are becoming more sophisticated.
Continued on page 6...
Rapt /adjective/ definition
Completely fascinated or absorbed by what one is seeing
REALISTIC DETAIL
Foil laminate captures vibrant detailing
FAMILY FRIENDLY
Anti-slip, splinter-free & barefoot friendly
EASY INSTALLATION
Innovative swift easy
‘Quick Clip’ fixings with no visible screws
LOW MAINTENANCE
Stain-resistant, requires no painting or sanding
UV RESISTANT
Protected against weather & UV radiation
SUSTAINABLE
Contains recycled material & is fully recyclable
ROBUST
Will not warp, bend or decay
FULLY TESTED
Tested for slip & wear resistance
MADE IN BRITAIN
Designed & manufactured to BSI standards at our state-of-the art Denby HQ
Well, here we are in mid-May as I write this: two days of summer with warm to hot sunshine and now it’s back to rain. Is that it? Has summer come and gone in a mere two days? Those two days did, I must admit, raise my spirits and reading that the FTSE 100 index rose to 8,433.76 last week was another filip. Even the Bank of England has signalled that the first cut in interest rates may come as soon as next month, and growth in the first quarter ran at an annual rate of 2.4 per cent.
We’ve even been told that the recession that we were supposed to have been in at the end of 2023, and into the New Year, is now over although it was always suspected that someone had jumped the gun on the recession issue and, when the statistics are examined, it is doubtful that we were in recession at all! As ever the US markets lead the way but the rest of the world has started to catch up. The S&P 500 index is up by more than 10 per cent this year and the Footsie is not far behind with Germany’s DAX up 12 per cent. It is said that the UK’s GDP grew by 0.6 per cent in the first quarter such that an overall growth of 2 per cent this year is not out of the way.
Why, you may ask, is the old boy rambling on about statistics that may come to nothing? With my ‘half full’ hat on, this could mean cheaper money is on the way and, with that, more disposable income which, just maybe, could be heading into the coffers of those involved in the home improvement market. I’m not the only one with a ‘glass half-full’ attitude, Sternfenster’s Mike Parczuk has sent in an open letter that talks about the importance of being positive and he too thinks that interest rates will come down and that the economic prospects for the second half of 2024 are good. Mind you, he does indicate that an impending general election could have something to do with it. General elections are inclined to encourage politicians to spend money like there’s no tomorrow!
I always associate award ceremonies with the autumn/winter season and was slightly surprised to see one being mentioned in May. Nevertheless, it was nice to see, and it’s well deserved, that Sheerline is nominated in nine categories
in one award programme and, apart from products and the technology being nominated, Roger Hartshorn himself is nominated in a Director/Managing Director category – and good for him. I wonder if nine nominations is a record for awards in our industry?
It has been a composite door month. A visit to Comp Door at Newcastle Under Lyme and to see their manufacturing methods and then to the launch of Britdor, DoorCo’s new solid core composite door and the birth of what will be their new state-of-the-art manufacturing facility at Thorne, near Doncaster. All very educational and also enjoyable. We received a safety briefing from Doorco before attending the day with a request that we bring safety boots with us. I asked my son if I could borrow his as, fortunately, we’re the same size shoe. He sent me this picture, asking if they would do:
With apologies to Carslberg but if Thermoseal’s Mark Hickox did safety boots they’d probably look like this!
Business Pilot has held a ‘virtual round table’ on innovation in customer service and support: what has changed and what the installer support of the future would look like. Meanwhile, Glass Express Midlands held a high-level industry event in London – regrettably I couldn’t attend but I await news of the event in due course.
Pioneer’s Danny Williams, in his Cold Calling column this month, answers an installer querying whether the demise of Everest, and the likes of Safestyle, indicate difficult times ahead? Danny joins notable industry figures such as Emplas’ Ryan Johnson and Sternfenster’s Mike Parczuk in being positive about the future and, seeing the significant investment being made by many companies, the industry seems to be in good health or, at least, working hard and preparing for a better future.
‘TIME OUT’ WINNERS – MAY!
Sudoku:
David Horner, Trowbridge, Wiltshire
Eye Spy: Mrs W Bower, Grimsby, North Lincs
Spot the Difference: G Bradley, Cromer, Norfolk
Crossword: B Haith, Motherwell, Scotland
Congratulations to all our winners! Good luck in this months Time Out pages!
Christina Lazenby
Managing Director / Advertising Enquiries
M: 07805 051322
E: christina@glassnews.co.uk
Emma Champion
Advertising Manager
M: 07508 263262
E: emma@glassnews.co.uk
Justin Lazenby
Finance Director / Press Release Enquiries
M: 07711 828710
E: justin@glassnews.co.uk
Chris Champion
Editor / Editorial Enquiries
M: 07850 267223
E: chris@glassnews.co.uk
Kate Carnall
Graphic Design
E: kate@glassnews.co.uk
Deadline for copy:
16th of each
Your education and the subject or activity in which you excelled?
During my time at school, I found myself drawn to both Business Studies and Science. Science, in particular, captivated me with its problem-solving and innovation aspects. I enjoyed the process of unravelling mysteries and discovering new solutions to complex problems. On the other hand, Business Studies honed my strategic thinking skills. I didn’t pursue further education after school and pretty much jumped straight into the fenestration industry. But I do think both subjects equipped me with a diverse skill set that I can apply to various challenges.
Your favourite sports or interests?
As well as being a die-hard Newcastle United fan, I love following my son's grassroots football team, Jarrow Dynamos Blues. The highlights of the team’s success were winning a tournament in Blackpool and finishing 4th in an international tournament in Holland. Being a parent of a player who is involved in a grassroots team you have to give up some of your free time for fundraising etc.
Someone or Something that inspires you.
Sadly, I lost my sister in 2022 after a brave fight with cancer. The bravery, courage and how she faced everything head-on truly inspired me. This experience has made me stronger as a person and drives me every day to make her proud.
THIS MONTH: Dean Pitcher Technical Director, Virtuoso Doors
Dean joined Virtuoso 25 years ago and looks after all aspects of the technical activity at the Company, including customer support and sales order processing.
When and how did you join this industry?
I joined the company just over 25 years ago as a Sales order processor for door panels, very quickly I moved into production management at a very young age. Most of my career has involved production management, but working for a small family business I was involved in some IT support and transport. After progressing through the company over the years my current position is Technical Director, which is really rewarding looking after all aspects of the Technical activity at Virtuoso as well overseeing customer support and sales order processing.
Your greatest achievement?
The progression and longevity at Virtuoso Doors, reaching the 25 year milestone and still enjoying every minute of it is a real achievement.
What would you like to do if you weren’t in this industry?
I have thought about this many times in my career and I can honestly say that even though this industry can be chaos and really challenging, it gets into your blood and doesn’t let you go.
A particular ambition
My ambition has always been clear: to lead Virtuoso Doors to become the premier Composite Door and Door Panel manufacturer in the UK. With our state-of-the-art manufacturing facility and a team of dedicated and skilled staff, I firmly believe that this goal is not only achievable but within our grasp. Our commitment to quality, innovation, and customer satisfaction sets us apart in the industry, and I am confident that we have the potential to surpass even our own expectations. Together, we will continue to push boundaries, set new standards, and strive for excellence, ensuring that Virtuoso Doors earns its place as the number one choice for customers across the UK.
The way you want to be remembered
I aspire to be remembered as a person who made a difference in the lives of others. Someone who approached life with kindness, empathy, and compassion, always ready to lend a helping hand or a listening ear to those in need. I hope to be remembered as someone who inspired others to pursue their dreams, to overcome obstacles, and to embrace life's challenges with resilience and optimism. Ultimately, I want to leave behind a legacy of love, kindness, and positivity, knowing that I've touched the hearts of those around me and made the world a little brighter in the process.
• Available in three door style ranges – Designer, Contemporary and Traditional
• GRP skins for a detailed wood-grain finish
• Hybrid timber-foam core to combine thermal efficiency and strength
• Aluminium sheets add rigidity and reduce moisture ingress
• Slab painted to order for a perfect finish in a wide range of colours
• Works with the award-winning Kubu Smart Security Sensors as standard
Continued from page 1...
These networks possess the resources and capabilities to plan and execute complex theft operations, employing diversion tactics and insider information. This shift towards organised crime has heightened the challenge of combating construction site theft for law enforcement and security teams.
To counter these evolving threats, construction companies are adopting new security measures and technologies. A popular approach is the implementation of surveillance systems equipped with video analytics and remote monitoring capabilities.
These systems detect suspicious behaviour in real-time and promptly alert security personnel, facilitating swift responses to potential threats.
Moreover, many construction firms are investing in physical barriers such as fencing, gates, and lighting to deter unauthorised access to their sites. Some are deploying security guards and K-9 units to patrol premises and conduct regular inspections. Additionally, marking and tracking high-value items with unique identifiers like RFID tags or serial numbers can aid in tracing stolen goods and enhancing recovery efforts.
Prevention is paramount in controlling this issue. To mitigate the risks associated with construction site theft, firms should adopt comprehensive security strategies that integrate technology, physical barriers, and vigilant monitoring.
Unfortunately, workers bear the brunt of poor security, with 1 in 4 surveyed in our report saying they’ve been left out of pocket after having to replace stolen tools. Despite this, 30% say security is seen as a “low priority” on sites they work on.
Rather than viewing security as an additional cost, it should be perceived as the best insurance policy to safeguard assets and project integrity.
In summary, combating theft from construction sites necessitates a multidimensional strategy that includes preventative measures, teamwork, and creative solutions. Construction companies can successfully safeguard their assets and maintain the integrity of their projects in the face of this growing problem by staying ahead of the curve and adjusting to emerging threats.
"Unfortunately, workers bear the brunt of poor security, with 1 in 4 surveyed in our report saying they’ve been left out of pocket after having to replace stolen tools.
Despite this, 30% say security is seen as a “low priority” on sites they work on."
Keystone Market Research is pleased to announce the release of the second edition of its quarterly UK Consumer Fenestration Trends report, sponsored by Epwin Window Systems, offering insights into changing preferences and homeowner buying priorities in the fenestration market.
The latest edition looks at the shifts in homeowner views compared to the initial survey, uncovering intriguing swings that are shaping the industry. To maintain a
balance between new content and tracking homeowner views over time to build up trends, each report presents the data results from a different angle to ensure that the information is as easy to understand and apply to your business as possible.
While the first report offered a comprehensive overview of overall results at a product level, the Spring edition takes a closer look at regional preferences. By examining each area in turn, readers gain valuable awareness of the unique needs of local audiences, highlighting both similarities and variations across regions.
As shown in the Winter report, online search and visibility are playing an increasingly crucial role in consumer decision-making. Therefore, this edition also features expert guest advice from Laura Trowbridge on maximising opportunities in this area.
Sheerline has revealed how vertical integration, internal communications, and a focus on providing an agile service have enabled it to achieve a world class OTIF (on time, in full) of 99.1% in February, followed by 99% in March – helping maintain high levels of customer satisfaction.
While benchmarking OTIF to assess performance is not uncommon for manufacturers, Sheerline tracks a particularly harsh standard, monitoring at full order level, not by item.
This means that if a single item is missing from any order (that may contain dozens of items), the full order counts against the overall OTIF score.
Delivery reports are sent the day before orders are due to be delivered and contain everything the customer needs to know. This includes an itemised list of the products being delivered, which is split by their orders. Not only does this give customers full visibility of what is being delivered and when, it also helps them to plan their production effectively, splitting everything down by individual customer projects if required.
Attention to detail and going the extra mile is something Sheerline has become known for thanks to initiatives such as this. The driving force behind this achievement is the key goal shared across all departments: customer satisfaction.
Alongside its single site, vertically integrated state of the art manufacturing, this enables Sheerline to offer incredible 5-day lead times on standard colours across its entire range.
Steve Musgrave, Sheerline Operations Director, commented: “Receiving an OTIF of just over 99% in February is an enormous achievement for the team, but we cannot let complacency set in. Our challenge now is to improve further and then maintain those levels, so customer satisfaction remains high.”
“We’re passionate about continuous improvement, striving for perfection and the highest possible standards across every element of the business, which is why our processes receive the same attention as our products. Ultimately, the result is happy customers, who know what they’re getting, when they’re getting it, and that they can depend on us,” he added.
To join Sheerline’s fabricator and installer network and receive exceptional customer service, contact the team on 01332 978000 to speak to them directly. Alternatively, email info@sheerline.com or visit the website: www.sheerline.com.
Charlotte Hawkes, Director of Keystone Market Research, comments: "Feedback on our inaugural report was overwhelmingly positive, with companies praising its strategic value and user-friendly format. Our annual subscribers are finding the Spring report to again be an invaluable resource, with comments on how interesting it is to see the changes in homeowner preferences quarter by quarter and how useful it is for generating installer support content. Building on the first edition results, we've packed this latest release with unique homeowner insights and practical guides to empower fenestration businesses and we’ll continue enhancing the format based on customer feedback to ensure we’re delivering ongoing value.”
Looking ahead, the Summer report will analyse results by homeowner profiles, aiding companies in gaining deeper insights into their target audience and enabling them to adapt their marketing efforts effectively. Meanwhile, the Autumn report promises to be the most thorough yet, drawing from the views of over 4000 homeowners by that point - the largest published dataset of its kind - to provide a comprehensive overview of UK homeowner views on fenestration products. Additionally, it will include the first look at anticipated homeowner-indicated spend levels on home improvement in 2025.
The second report is available now, with single report or annual subscription purchase options.
For more information, please visit www.keystonemr.co.uk.
"Our annual subscribers are finding the Spring report to again be an invaluable resource."
VBH, the hardware specialist behind the greenteQ range, has announced two new appointments this spring that have further strengthened the company’s technical and sales teams.
Daran Woodcock has joined VBH in the role of External Technical Sales Supervisor within the New Product Development/ Technical team.
Vastly experienced, Daran and his team of engineers provide hands-on technical support to colleagues and VBH customers, both on site and in the factory.
VBH advise that Daran’s skills surrounding new product fit-up demonstrations, test sample manufacture, problem solving and his general industry know-how are already proving to be an invaluable asset to the company.
Ollie Safhill also joined the company on the same day in the position of Regional Manager - North - England.
He brings much knowledge with him, gained during many years within the industry, including previous experience of hardware sales.
VBH advise that Ollie has ‘hit the ground running’, and is already proving popular with his customers across the north of England. It appears that the VBH team is getting bigger and even better!
VBH can be contacted on 01634 263263 or by email at sales@vbhgb.com.
Mark Frain has joined profine UK as national business development manager for WarmCore as interest in the unique hybrid window and door systems continues to rise.
WarmCore is much more than just a next generation bifold door, as there’s an impressive patio, flush residential and French doors in the range, along with casement, flush and tilt and turn windows, and a range of ancillaries too. profine are investing heavily in WarmCore and already there’s a new marketing campaign commenced which includes PR, advertising, direct mail, brochures, point of sale materials, web and social communications.
As a fenestration professional with a diverse background at Heywood Williams, aluminium systems and in supply chain management, this is an important new role for the business and indeed for Mark. He commented: ‘I’m delighted to be heading up the development of sales and business opportunities for WarmCore in the UK. It was incredibly well received at Fensterbau and we’ve already generated considerable interest in the UK since then.
He continued: ‘It’s a technically better product platform as is the Kömmerling and profine way, and with the investment planned for the product and brand moving forward I’m genuinely excited for the remainder of the year and beyond!’
For further information on WarmCore, visit: www.profine-uk.com/warmcore/
Leading colour coating specialist Kolorseal Ltd is introducing a new Quality Assurance Certificate for customers to pass onto the end user which will add further substantiation to the company’s existing 10 year quality guarantees.
As an award winning company, that is based in Huddersfield with multiple spraying and drying rooms, Kolorseal has an established reputation
for quality and reliability.
Customers state that the team’s understanding of the market, alongside the 5 day turnaround, product guarantees as well aspick up and delivery services provide a professional reassurance that stands out.
The launch of the Certificate of Authenticity takes guarantees to the next level for the homeowners as it reinforces the high standards associated
with Kolorseal and by association its customers.
Consumers trust the award winning brand and the standards they receive, which help to keep properties looking good year after year.
With most home owners prioritising quality when it comes to buying windows or doors, the assurance certificate will give Kolorseal customers a clear advantage.
Deborah Hendry, Managing Director, Kolorseal comments, “Today, people have very high expectations when it comes to modernising their homes. Equally, when it comes to selling properties, homeowners are looking for advantages and assurance certification really helps.”
The demand for bespoke coloured coatings continues to be a fast-paced, growing
sector as consumers want to reflect lifestyle and at the same time add value in their choices.
Deborah continues, “Whether it is for an internal or external appearance on a window or door, or a roofline product that requires matching, it is important for consumers to feel reassured. As a brand Kolorseal is recognised for its quality, however it’s important for homeowners
As one of the capital’s busiest and most vibrant arteries, renovating the ageing steel windows within the frontage to a very popular events venue on the Edgware Road posed particular challenges for metal window specialist, Associated Steel Window Services (ASWS). This involved careful planning and flexible working, including some very early morning and weekend shifts.
In fact, Etc. Venues, at 86 Edgware Road, extends to four storeys with the ground floor being occupied by a Tesco store. Furthermore, the client’s business, which rents out different sized function rooms to multiple clients, was also required to remain operational throughout the contract, as ASWS carried out a variety of repair and maintenance tasks.
The existing windows are classic W20 style steel windows with either side-hung or pivot opening lights, ranging from 1.5m to 2m wide and up to 3m high. Although
subject to some corrosion and physical damage, ASWS’s skill and experience at insitu repairs proved very much in line with the client’s requirements.
Kris Bennell, Contract Director for ASWS, explained, “We had previously been involved with Etc. Venues in carrying out some carefully considered repairs to the upper level of County Hall on the South Bank, so this was a continuation of the relationship, but this time taking more of a maintenance approach to the building’s requirements. This included carrying out a number of repairs to frames and vents, as well as reglazing a lot of the units, putty repairs and replacing some of the original handles. This was done using refurbished handles and catches from our own stocks.”
“Aside from the client having daily bookings for meetings and other functions within a lot of the rooms - which can hold up to 100 people - the only time the street outside goes quiet is between 3-6am, which meant
getting our operatives there in numbers on a Sunday morning and cordoning off parts of the pavement. Ultimately, all of the work was carried out successfully, with our site management scheduling the work, sometimes at short notice – to suit the client’s bookings.”
Any of the fixed or opening lights which required reglazing were fitted with 4mm glass, including 4mm toughened where required for safety considerations.
The Head of Design for Etc. Venues, Franck Rosello, commented: “I choose ASWS for many reasons. First, their prompt quotation which included a survey, so the job was understood well from the early requests. Also, our needs, with regards to access and use of the building, were considered which meant we could continue to operate our business. Finally, the job was done with great care and safety in mind. We have had two large jobs done by ASWS and have been highly satisfied from a delivery point of view.”
to know that when choosing their ideal colour it will mean something."
www.kolorseal.co.uk
ASWS is a long-established member of the Steel Window Association and well recognised expert in the repair of metal windows, from the earliest wrought iron examples through to contemporary curtain walling. The family run business is frequently called upon to prepare condition surveys during the appraisal stages of a project, which then become part of the planning or listed building permission process. The company also maintains a very large stock of ironmongery and metal frame components to assist in its restoration work. For more information on ASWS, please visit asws.co.uk.
Leading systems house and PVCu extrusion company Liniar is renowned for design innovation - manufacturing a wide range of products for the fenestration and construction markets. It’s also the biggest supplier of PVCu and composite decking to the UK’s holiday parks, thanks to the development and manufacture of its high quality, maintenance-free deckboards and balustrades.
Mark Sims, Outdoor Range Sales Director, discusses the reasons customers choose Liniar’s PVCu outdoor range, and the company’s continued commitment to investing in new product development as they introduce a new foiled deckboard - Rapt.
Mark explains, “PVCu, composite deckboards have become an increasingly popular timber alternative for their low maintenance, durability and stylish appearance.
“What’s more, this is not just within the caravan industry, we’ve seen a huge spike in sales from homeowners across the UK with people increasingly wanting to add these products to their outdoor spaces. Many of our fenestration customers are now offering our outdoor range as an add-on to say a conservatory, or an extension. It makes perfect sense, why wouldn’t their customers want a beautiful deck installed at the same time?”
A subsidiary of parent company Quanex, Liniar enjoys high levels of investment which allow the business to continue investing in new product development.
Marks states, “Liniar is proud to be a British manufacturer and has been producing its decking in Derbyshire for over 25 years. However, we do not rest on our laurels and regularly bring new products to market, making sure we can always offer versatile solutions for a broad spectrum of construction projects and tastes.
“For example, we’re excited to be introducing the latest addition to our already market-leading decking range, Rapt, a premium foiled composite deckboard. This new product has been developed in response to both customer feedback and market trends and we’re looking forward to seeing how it is received.”
Discussing the latest addition, Mark says, “Rapt is finished using Renolit’s GEFOL foil, which enables the deckboards to mirror the natural aesthetic of materials such as timber in more detail than ever.
"The foil finish offers exceptional scratch and abrasion resistance, along with UV protection, making it perfect for enhancing outdoor spaces with a stylish decked area. It showcases our innovative design prowess while also reflecting Liniar's proactive approach to market trends."
Mark continues, “The detail in Rapt’s foiled finish means it appeals to those wanting to capture a timber aesthetic as accurately as possible but with all the benefits of composite PVCu.
“At Liniar we recognise the importance of offering our customers a choice of solutions and our existing SwitchBoard and SwitchBoard Ultra offerings remain as relevant as ever.
““SwitchBoard decking offers a versatile decking solution with a reversible design, allowing you to choose between woodgrain and grooved finishes for the creation of bespoke designs. Its 37mm thick boards (one of the thickest on the market) ensure durability, resistance to warping and bending.
“SwitchBoard Ultra is a premium, 3D embossed deckboard with a solid recycled core, and is also fully reversible. Premium capping technology has been used to ensure Switchboard Ultra’s core is protected from damp, decay and mould.”
Mark concludes with confidence, “We’re always looking for ways to improve and grow the business by prioritising customer feedback and support and keeping a keen eye on market trends. The high levels of customer retention and satisfaction we achieve are a testament to our successful approach.
Part of the Fortex® range, stunning Shadow Gap cladding looks and feels like painted pine, with a deep groove for a high-end finish. Low maintenance and durable, it’s also fully recyclable.
Fitted horizontally or vertically, its 7 shades can be colour-matched to roofline, windows and doors for an eye-catching façade on modern or traditional homes.
Call 0800 002 9903 to find a stockist and grow your business with premium cladding.
The UK-wide Steel Window Association members are the established, proven experts in the renovation and sympathetic refurbishment of steel windows and doors in both domestic and commercial premises; typically, those in listed buildings or properties in heritage and conservation areas.
One of the best qualities of a steel window or door is its longevity and this is where refurbishment and servicing are vitally important; this is where SWA members can help. Options range from a very basic ease and adjusting, where the windows and doors remain in-situ and are serviced, to a full in-situ overhaul involving significant paint removal and redecoration, where possible.
In a complete refurbishment, all the windows and doors are removed and taken to a factory environment for shot blasting, potentially galvanising, powder coating and servicing; then comes the reinstallation and reglazing. There is also the possibility, especially in heritage situations, of maintaining the original aesthetic of the original window by hand painting and reglazing.
The refurbishment has improved centuries, and, today, clients can expect an upgrade in usability and security as well as both thermal and acoustic performance through glazing and sealant enhancements. In addition, the windows are significantly more aesthetically-pleasing.
For owners of buildings or houses within listed or conservation areas, or those who would like to preserve the history of their own property, refurbishment is an invaluable and satisfying option. With this level of refurbishment, the SWA offers the ability to recycle, reuse and renew.
On-site servicing includes servicing, easing and adjustment of opening windows and doors for good operation; replacing or using draught excluder, replacement of defective
or missing ironmongery including hinges and pivots; removal of broken or cracked glazing; and replacement of lead lights.
On-site overhaul is as above but includes removal of visible surface paint; treatment of the visible steel substrate; tightening or replacement of coupled frame intersections and perimeter fixings; replacement of damaged weather seals; potential for upgrading of glass specifications; potential to modernise or refurbish existing ironmongery to include enhanced security; re-introduction of perimeter and window mastic seals; replacement of glazing beads, mastic and putty; and redecoration of painted surfaces.
Full off-site overhaul includes removal of existing frames, and possible temporary protection of apertures, shot blast to bare metal to remove all existing paint and priming material; fully recorded survey of necessary repairs and replacement section, hinges and couplings; full pre-treatment primer and re-painting of the steel sections to required specification; re-installation of frames to apertures, re-glazing with the possibility of thermal / acoustic upgrades; refurbishment and replacement of existing specialist glazing; application of new mastic and primary weather seals; and re-instatement of refurbished or new ironmonger.
For further information on the Steel Window Association, please visit www.steel-window-association.co.uk or call 020 3475 8049.
With the home improvement sector continuing to experience challenging trading conditions, Endurance® Doors is urging installers to consider additional ways of ensuring sales success.
In particular, the business, which manufactures solid, secure, and stylish composite doors, is highlighting the power of online reviews in converting leads into actual orders.
Scott Foster, sales and marketing director at Endurance® Doors, comments: “In today’s internet-enabled, hyper-connected world, consumers have a greater voice than ever before.
“Whether they’re looking to compliment or complain about a product or service they have received, they can now do so quickly, easily and to an audience that can potentially amount to millions.
“As a result, online reviews have become the ultimate form of word-of-mouth marketing. The buying process for all manner of products now begins online with purchasers looking at the experiences of other customers before making their own final and informed decision.”
He continues: “Endurance® Doors, in close collaboration with our network of professional installer partners, has gone to great lengths to develop an online reputation that can facilitate sales. As a prime example, Endurance® Doors has over 2,300 independent consumer reviews on Trustpilot, of which more than 87% award us the maximum five out of five stars.”
The composite door manufacturer is keen to point out that online research was important to consumers before the costof-living crisis and has grown even more
significant in the current economic climate where most households are seeing their budgets stretched.
Consumers at the mid to high-end of the market are still buying composite doors but, with disposable income in short supply, they are purchasing much more prudently and want the reassurance of knowing any expenditure will be money well spent.
“The positive online reputation enjoyed by Endurance® Doors has not happened by chance” adds Scott Foster. “Instead, it’s part of a wider and concerted effort to get closer to consumers and to help our installers sell.
“At every stage of the consumer journey, we are taking steps to turn prospects into advocates. This includes establishing our own bricks and mortar showroom as well as offering virtual design consultations, which enable people to explore different door options from the comfort of their own home.
“Not content to stop there, we even have a specialist consumer facing sales manager and a dedicated consumer phone line.
“Combined, these elements help to ensure the homeowner feels valued and front and centre in everything we do, rather than like an afterthought. This customer-centric approach is reflected in our online reviews and continues to pay enormous dividends.
“It’s been said that a good reputation is the most powerful form of advertising - and we’re inclined to agree.”
Garnalex is celebrating after the company was named the ninth fastest growing company in the UK according to the ORESA Growth Index 2024. The coveted index champions innovation, economic growth, and the inspirational business leaders behind the featured companies. Not only is it impressive to make the index, which only features the top 100 companies in the UK, but for Garnalex to enter the list for the first time in ninth place with a 171.07 per cent compound annual growth rate is a testament to the leadership team. In addition, while there were nine companies on the list from the East
Midlands last year, there are only six this year. When considering the timeframe includes the covid and post-covid recovery years, which saw many businesses struggling, it’s even more impressive.
One of the key trends from this year’s findings highlight the rise of sustainable businesses and initiatives. Garnalex prides itself on the sustainable processes it has woven into the very foundations of the business.
For instance, the company uses UK-sourced aluminium to keep its carbon footprint low, while also ensuring supply chain security, and recycles all its aluminium offcuts.
Roger Hartshorn, Garnalex’s CEO, said:
“To be recognised as one of the top ten fastest growing companies in the UK is a huge achievement in itself, but when you consider the context and climate in which we and other businesses are currently operating in, it’s fantastic.”
“It’s also proof of what you can achieve when you have the right strategic vision, ideas, investment, products, and people working together – all of which Garnalex has,” he added.
Find out more about Garnalex here: https:// garnalex.com or view the ORESA index here: https://growthindex.com/growth-index-2024/
CRL has announced big discounts on some of its most popular glass and glazing solutions, with Spring offers now available for a limited time.
Specifiers and installers can make significant savings on CRL’s best-selling products, including 10% off selected architectural hardware and 15% off its innovative frame systems for interior partitioning in on-trend matte-black.
Bathroom installers can also take advantage of 15% off many of CRL’s shower hardware systems.
With spring discounts on railing systems, including CRL Taper-Loc and CRL POSIone, plus tools and accessories, this is the ideal season to take stock ready for upcoming projects in the months ahead.
Orders are shipped daily from the CRL110,000 square foot warehouse and are generally received next day.
For more details call 00 800 0421 6144 or email crl@crlaurence.co.uk.
Permadoor, leading manufacturers of fire and security composite doors, has just launched its new brand identity.
Steve Jones, Managing Director of Permadoor, said: “Our new branding gives us a fresh new look and reinforces our status as a name you can trust.”
The new branding is part of a wider investment strategy designed to support Permadoor’s position as one of the UK’s biggest suppliers of composite doors to the social housing and New Build markets.
The investment includes a new vehicle fleet and inhouse paint line, as well as a new user-friendly pricing portal for its retail brand, Safedoors. In addition, a new FSC-accredited composite door offer will be launched this year, as well as an increased range of fire doors including more glazed options for both internal and external fire doors.
Other recent developments include the launch of a new solid timber core 48mm composite door. It is the only 48mm door on the market that can use both the chamfered and sculptured Profile 22 profile, giving it huge appeal in the social housing sector. The company has also introduced golden thread functionality to its fire doors by adding a fire data pin that can be updated in situ when maintenance works are completed, helping to ensure compliance with fire safety regulations.
Permadoor has over 30 years’ experience in the
affordable homes, new build and social housing markets, and it works with local authorities, housing association-registered providers and contractors on refurbishment and new build projects across the UK. Its product ranges include GRP doors, doors with canopies, solid timbercore doors, communal doors, outhouse doors and stock doors all with DDA accessibility options.
Part of the Epwin Group, Permadoor’s new brand identity celebrates its commitment to industryleading excellence and reflects its status as an established industry player.
As the industry strives to meet the ever-growing demand for high-performance solutions, Premier Arches recognises that exceptional manufacturing quality is no longer a nicety, it's the cornerstone of success. We speak to Managing Director Sean Greenall…
The UK fenestration industry plays a pivotal role in shaping the built environment. With a growing emphasis on sustainability, energy efficiency, and occupant wellbeing, the demand for high-performance solutions is reaching unprecedented levels, and in this dynamic landscape, quality manufacturing has become more crucial than ever.
Beyond aesthetics, meticulous production processes ensure components meet stringent performance criteria, contributing to energy-efficient buildings, occupant
comfort, and ultimately, a more sustainable future for the construction sector.
At Premier Arches, exceptional manufacturing quality is the cornerstone of everything we do.
We simply refuse to send products to our customers that are not manufactured to an exceptional standard. This philosophy isn't just a management decision, but a cultural principle deeply ingrained in our entire manufacturing team of over 20 skilled professionals.
At Premier Arches, we prioritise exceptional quality from the very beginning. Our
fabricators undergo a rigorous training programme, ensuring they possess the expertise required to work with complex arched and angled profiles. This translates to flawless results in every frame we produce.
Meticulous quality control is also paramount in our manufacturing process. Every frame undergoes a thorough inspection before it leaves our facility. This robust process leaves no room for error, guaranteeing that all our products meet the highest standards.
While efficiency is important, it never comes at the expense of quality at Premier Arches. Our company culture prioritises meticulous craftsmanship over rushed production, ensuring every frame we build is not only aesthetically pleasing, but also built to last.
Finally, we understand that the right equipment makes all the difference. That's why we invest in state-of-theart machinery and tooling specifically designed for working with arched and angled profiles. This guarantees precise fabrication and consistent results in every single frame we produce.
EMPOWER YOUR BUSINESS WITH EXCEPTIONAL
In today's competitive market, trust is paramount. By prioritising exceptional manufacturing, we offer fabricators and installers the confidence that they're receiving high-performance products built to the highest standards.
For fabricators, replicating the success they've achieved with square frames on arched projects often requires significant investment in specialised machinery and expertise. This lengthy and complex process might deter them from taking on lucrative bespoke jobs.
Premier Arches exists to bridge that gap by specialising in the "awkward products" others shy away from. When it comes to arched and angled frames, exceptional manufacturing is the foundation for trust, performance, and a successful project.
At Premier Arches, we are committed to delivering exceptional quality in every product we produce, empowering our clients to confidently shape the future of sustainable architecture.
www.premierarches.co.uk
Made For Trade, renowned for its innovative solutions, has been honoured with the King’s Award for Innovation 2024. This prestigious accolade shines a spotlight on the revolutionary Korniche Roof Lantern. It further cements Made For Trade’s progressive reputation and acknowledges its ground breaking contribution to redefining the fenestration sector.
Established in 1965, The King’s Award for Enterprise is the UK’s most distinguished business commendation. The award continues HM Queen Elizabeth II’s legacy and celebrates businesses that pioneer innovation, sustainable practices, and social mobility. Receiving the award is a testament to Made For Trade’s commitment to forging revolutionary solutions for industry products.
Made For Trade’s achievement demonstrates its commitment to excelling and pushing boundaries within the home building industry. Korniche has established Made For Trade as a national operation despite its base in the Northeast of England. It has moved from a fabricator of third-party systems to a business that designs, engineers, and builds its own products at scale. The Korniche Roof Lantern has set a new paradigm in design and functionality, raising standards in the industry.
With a triumphant message around forward-thinking, Bradley Gaunt, Managing Director of Made For Trade, shares his insights following this momentous milestone:
“As the managing director of Made For Trade, I’m delighted to announce that we’ve won the prestigious King’s Award for Innovation. At Made For Trade, innovation is our top priority. Winning this award validates our team’s hard work and dedication. It boosts our reputation and opens up new opportunities for growth and collaboration. Thanks to everyone at Made For Trade for their passion and commitment. Together, we’ll keep innovating and achieving success.”
Made For Trade’s creativity really surpasses industry expectations and reshapes customers' perceptions of their home spaces.
Exhibiting a cutting-edge design, swift assembly time, and seamless fitting, the roof lantern has disrupted the home building sector and had a revolutionary impact on installation, surpassing traditional roof products. Before
the introduction of the Korniche Roof Lantern, the market was saturated with inefficient PVC-clad aluminium systems that were not only thermally inefficient but also required extensive manual adjustments, such as drilling and cutting, which made their installation process cumbersome.
In stark contrast, the Korniche Roof Lantern is designed for streamlined installation, taking just minutes to fit and glaze compared to pre-existing and competitor products..
We take a look at the specific design features that enhance the product’s functionality and appeal and really demonstrate Made For Trade’s commitment to engineering excellence and user-friendly design:
• End Caps: For a sleek, refined appearance, these are installed with no visible fixings.
• Unique Glazing Retainer: The revolutionary design prevents glass from slipping and masks the glass edge, whilst simplifying the installation process.
• Assembling Mechanism: To ensure quick and reliable assembly, single fix bolts and die-cast aluminium components with steel helicoils are used to avoid crossthreading.
• Innovative Boss Design: A patent-granted design replicates a traditional timber "bird’s mouth" joint, allowing for a virtually seamless and aesthetically pleasing connection.
The Korniche Roof Lantern has really raised the bar for installation ease, thermal efficiency, and sleek design aesthetics, having tackled any previous industry limitations. It has emerged as a true beacon of creative thinking, appealing to a broad market of builders, roofers, and DIY enthusiasts. Due to its effortless installation, trade and end consumers benefit from increased efficiency and reduced costs.
Furthermore, the ‘KwikQuote’ online tool continues to amplify the customer experience, allowing Made For Trade to expand its operational reach. Trade clients can offer instant pricing, allowing improved sales processes and refined customer satisfaction.
The King’s Award highlights the power of transformation, innovative thinking, and Made For Trade’s steadfast dedication to excellence that can revitalise even the most established products.
The Glass and Glazing Federation’s (GGF) Training Academy has underlined its commitment to improving health & safety (H&S) standards with the introduction of a ground-breaking, industry specific training course that has been developed in collaboration with the Institution of Occupational Safety and Health (IOSH).
IOSH is an internationally recognised body that is responsible for setting national standards, advising government and facilitating H&S training in 130 countries.
The new IOSH Approved ‘Managing Safely in the Glass & Glazing Industry’ course has been designed to further bolster safety standards, empower businesses, and nurture a new generation of skilled professionals.
It is aimed at directors, managers and supervisors, and will deepen participants’
“Our new IOSH training course equips businesses with the tools to operate responsibly, safeguard employees, and distinguish themselves in a competitive market.”
understanding of H&S responsibilities in the workplace through a comprehensive 22-hour, 3-day program, featuring classroom-based learning and a rigorous end-point assessment.
Upon completion, delegates will possess the knowledge and skills to manage health and safety effectively, including risk assessment and legal requirements, incident response, the identification of hazards and the implementation of robust safety management systems.
Lauren Mawford, GGF Health & Safety Manager, commented: “This new initiative, which is the only IOSH approved course that has been specifically tailored for our sector, underscores our unwavering commitment to fostering a culture of safety within glass and glazing.
“By offering this exclusive course to the entire industry, and at discounted rates to our members, FENSA Approved Installers and BFRC customers, we are ensuring accessibility to essential training that promotes excellence and ultimately, protects our workforce.
“The safety of everyone who works in the glazing industry is absolutely paramount,” continued Lauren. “Our new IOSH training course equips businesses with the tools to operate responsibly, safeguard employees, and distinguish themselves in a competitive market.”
The course will be run at the GGF’s offices in London and will consist of seven modules that will explain: Introducing Managing Safely; Assessing Risks; Controlling Risks; Understanding Legal Responsibilities, Understanding Hazards; Investigating Incidents and Measuring Performance.
Course Costs:
• Full Price: £600 + VAT
• FENSA/BFRC Customers: £550 + VAT
• GGF Members: £500 + VAT
For inquiries and registration, please contact Lauren Mawford, GGF Health & Safety Manager, at lmawford@ggf.org.uk.organisation for companies involved in all aspects of the manufacture of flat glass and products and services for all types of glazing, in commercial and domestic sectors.
In 2022, the Double Glazing & Conservatory Ombudsman Scheme (DGCOS) carried out a mental health survey across the industry to understand the impact that daily challenges were having on both employers and employees. With Mental Health Awareness Week falling in May this year, the organisation is running a second survey and invites participants on an anonymous basis.
Faisal Hussain, DGCOS Chief Executive, explains, “I am still shocked at the conversation I had with an installer in 2022 in which he told me he had simply had enough of the pressures of the industry. Issues with late payments, supply chain issues, a lack of skilled installers, and juggling admin and sales had meant he had been unable to take a holiday or even go to his GP about an ongoing medical issue.
“It was this that prompted the first mental health survey that DGCOS did, and which returned some worrying results. It was obvious that there was a much wider issue to tackle,
and that many respondents had experienced adverse mental health and wellbeing. In fact, we launched a series of mental health podcasts last year as a way of offering focussed support.
“It’s now time to see how much progress has been made in the last two years so we are repeating the survey as a way of finding out if real life experiences have improved. I would urge anyone to take part, anonymously, so we can continue to assess the health of our industry. It only takes 5 minutes and the results could be invaluable in determining
where we are and what still needs to be done to make our industry better.”
“I hope that the last survey brought the issue of mental health out into the open and that it made people realise they are not alone. It seems Mental Health Awareness Week in May is an ideal time to find out how well we are all doing and whether things have changed for the better.”
To have your say and take part to help us gauge the mental health and wellbeing of our sector, visit: https://shorturl.at/ aqrQZ
Leading trade fabricator Dekko Window Systems has announced the appointment of a new Residence Collection Sales Manager.
Austin O’Carroll brings over 20 years of experience in sales, customer service, and product marketing to the role, where he will oversee the continued success of the popular Residence Collection brand within Dekko’s offering.
He comments: “Today’s consumers are looking for high-quality, beautiful, and functional products, and that’s exactly what they get with The Residence Collection.
“Dekko has been manufacturing their stunning windows for 10 years now, and I look forward to driving that relationship further by acquiring new customers, managing existing relationships, and ensuring seamless pre- and postsales support.”
The new appointment coincides with Dekko celebrating a decade-long partnership with The Residence Collection. In that time, the company has
manufactured over 61,000 Residence Collection frames, averaging a remarkable 130 frames per week across the R9, R7, and R2 ranges.
This success highlights the ongoing demand for Residence Collection products among fabricators and installers, and Dekko’s commitment to delivering exceptional quality and service.
Sales Director Kurt Greatrex comments: “We’re delighted to welcome Austin to the Dekko team.
His extensive experience and proven track record within the industry make him a valuable asset.
“This appointment further strengthens our
As the UK’s love for bi-folding doors continues, these stylish and space-saving solutions are transforming homes across the country, blurring the lines between indoor and outdoor living.
But with a growing market comes a crucial question: are all bi-folding doors created equal?
Michael Hewitt, Sales Director at AT Precision, believes the answer is a resounding no. The leading manufacturer of the precision-engineered Everglide range of bi-fold hardware is on a mission
to transform the UK bi-folding door market by demonstrating the importance of meticulous engineering in these increasingly popular home additions.
Michael explains: “While the visual appeal of bi-folding doors is undeniable, their smooth operation and long-term performance hinge on the quality of their unseen components, and it’s AT Precision’s focus on specific areas that ensures exceptional products.
“First and foremost is a focus on flawless functionality – our rigorously tested components, including rollers, tracks, and hinges, ensure bi-folding doors glide effortlessly, even for large spans. Precise tolerances prevent weather ingress and
guarantee proper door alignment, even when the elements rage outside.
“A second focus on uncompromising security sees robust locking mechanisms and high-strength materials built into products in order to deter potential intruders and meet the highest industry safety standards.
“Finally, AT Precision focuses on long-lasting value. Bi-folding doors are an investment, and our components are built to last. Minimal wear and tear translate to a longer lifespan for doors, saving fabricators money on repairs and replacements down the line.”
PARTNERING FOR BI-FOLDING DOOR EXCELLENCE
AT Precision isn’t just a supplier; they’re a trusted partner for bi-folding door
commitment to The Residence Collection and ensures we can continue to provide our customers with the very best in highperformance, aesthetically pleasing Residence Collection products.
“For ten years, Dekko has enjoyed a successful partnership with The Residence Collection, consistently exceeding customer expectations for R9, R7, and R2 windows. With Austin on board, we look forward to building on this success and further solidifying Dekko’s position as a leading Residence Collection supplier within the UK.”
www.dekkowindows.com
manufacturers, installers, architects, builders, and ultimately, homeowners. By prioritising precision engineering, the company empowers the creation of exceptional bi-folding doors that enhance the aesthetics, functionality, and security of UK homes.
Looking to transform your next bi-folding door project? AT Precision has the solution. Visit www.atprecision.co.uk to explore their comprehensive range of components and discover how they can help you create a bifolding door that stands the test of time.
Prefix Systems have just launched the revolutionary new SheerVent for their S2 glazed roofing system, bringing all the innovation from the award-winning Sheerline S1 lantern into their next generation system for conservatories and glazed extensions.
With more experience than most in first generation roof vents, this new innovation from Sheerline is a game changer for the glazed roof market, bringing an integrated solution that doesn’t suffer from water ingress thanks to an integrated muntin bar with installation directly into the ridge baffle.
S2 is re-defining the way in which glazed extensions look and perform, and now the dedicated SheerVent solution provides carefree long-term performance benefits and has been designed to seamlessly integrate with the S2 roofing system.
SheerVent’s sightlines are slimline and therefore it sits lower down than the traditional, clumsy looking first generation roof vents and is available in sizes up to 1.1 wide x 1.2m high. This new solution is fully thermally broken with 24mm glazing as standard and brings to market accessible 21st century automation through light, wind, and rain sensors for comfort and lifestyle benefits.
Chris Cooke, director of Prefix Systems commented: ‘The glazed and conservatory roof sectors have been plagued with poorly performing roof vents for decades. With the S2 SheerVent, we’re now able to offer our customers a next generation product that performs as well as it looks. The whole S2 glazed roofing system is already generating rave reviews from installation companies across the UK and this addition to the range will further support this view as we look to offer best in class solutions across glazed roofs, our award-winning WARMroof and through our outdoor living solutions, including Verandah.’
For further information on please visit www.prefixsystems.co.uk or contact the head office for a free brochure pack including details on S2 on 01254 871800, alternatively you can e-mail marketing@prefixsystems.co.uk.
You can also follow them on social media @prefixsystems.
Kömmerling have returned from what has been widely regarded as one of their best Fensterbau exhibitions with sales enquiries from across the globe and the opportunity to celebrate relationships with existing business partners under the new brand.
Alongside the Holz-Handwerk event, 973 exhibitors from 44 countries and around 75,000 trade visitors from 112 countries came together at the international trade fair held at the exhibition centre in Nuremberg. For Kömmerling, it’s their largest exhibition commitment across the group and took in excess of 12 months in the overall planning and execution.
Throughout the day and night Kömmerling celebrated with visitors with sustainability at the heart of everything that was presented, including the 100% recycled window, ReFrame and the revolutionary bio-attributed PVC. This ground-breaking development completely replaces fossil materials using a pine oil-based ethylene, which facilitates a 90% reduction in CO2 compared to conventional PVC.
WarmCore was highly prevalent on the stand both in the 70mm and 76mm variants with UK and international visitors highly interested in the unique hybrid window and door system. Other products in the 70mm, 76mm and 88mm platforms were on display including a preview of the new Kömmerling 70mm flush door sash, along with several Passive House and smart home solutions.
Kevin Warner, sales and marketing director of profine UK and Kömmerling enthused: ‘Fensterbau certainly did not disappoint. It was an epic event for a wide number of reasons and the feedback from visitors was immense. It was also fully reflective of our sustainable brand with Today for Tomorrow a theme throughout.’
For further information e-mail enquiries@profine-group.com or phone 01623 579200. You can also follow them on social media platforms @profineuk and @kommerling_uk.
Attending the launch of BRiTDOR and the birth of DoorCo’s new manufacturing facility at Thorne, Doncaster, Glass News’ Editor Chris Champion joined other trade publication editors to hear about, and see, where the new timber core composite door is being produced.
BRiTDOR, as the name implies, is a very British door. Although the timber core itself is imported, the construction of the slabs takes place entirely in the Thorne factory, finished with ThermoPlastic skins. Importantly, there is a standard slab size of 914mm x 2095mm, larger than the norm, that allows for the increasingly popular larger door spaces. It is also available in both 44mm and 48mm thicknesses and has over 15 colour availabilities. Styles include all the usual suspects but also two new and exclusive designs for this range, Enzo and Glenman, and one called Eaton Solid, which is also available now. While customers may be used to having DoorCo products painted in any colour, that facility is not available in the BRiTDOR. All the colours on offer are self-coloured but the range offered covers all the popular composite door colours, with more to come. BRiTDOR is available as a slab for fabricators to trim to size and CNC rout for any hardware options and to be fitted to any profile. Alternatively, a prepping service is offered at DoorCo’s Macclesfield facility and, again, prepped to any profile and hardware options.
It's interesting how BRiTDOR has come about, DoorCo has thought very carefully about the naming of the product and certainly this solid core door is an important addition to the company’s portfolio completing the range alongside
ORiGINAL, the polyurethane foam filled and GRP skinned composite door; GRiPCORE, the insulated and engineered timber/foam/aluminium core door with a GRP skin, and the FIRECORE fire door. What makes BRiTDOR different from the other timber cored doors on the market?
The big difference is the look of the finished door and DoorCo Managing Director, Dan
Sullivan and his team have invested heavily in making the difference. Traditionally, ABS and PVCu skins that are vac formed tend to have a slightly bulbous imitation grain and differ greatly from the grain displayed on GRP skins. Moving to ABS or PVCu is a cheaper option than GRP, and tooling costs are very significantly different. However, Dan and his team have invested in tooling that makes the grain definition on the Thermoplastic CoolSkin replicate that of the graining on the GRP skinned composite doors. Indeed, putting them side by side it is pretty much impossible to tell the difference. A significant investment but one that, I’m pretty sure, customers will fully appreciate.
In talking with Head of Operations, Mark Towers, about the new manufacturing facility he was explaining how precise
routing was key to producing a high-end door slab, and they take a lot of trouble to ensure the routing matches the pressed skins so that no air is trapped when the skin is glued and pressed together. It’s clear they are aiming at producing a quality slab that matches the high quality the trade expects, and gets, from DoorCo products.
Mark has been responsible for setting up this new manufacturing plant and it would be fair to question the move across country from Macclesfield to Doncaster. The cost side is understandable with their being able to secure this large site for around a quarter what it would cost in ‘Premier footballer land’ being the Cheshire environs! But there is another reason: it’s right next door to DoorCo’s glazing cassette partner’s premises such that the Doncaster choice was a no brainer! But this is just the start of the Doncaster journey. The plan is to manufacture BRiTDOR here but, in time and after a three year plan to demolish the existing buildings and rebuild on the site, this will become a state of the art manufacturing facility for all the DoorCo products. So, what about DoorCo Korea? Korea is a facility that manufactures vast quantities of doors, and very efficiently, but design and development of products, something DoorCo is very good at, very much remains in the UK domain going forward. There is an element of future proofing here. With turmoil worldwide, the ability to
manufacture even the ORiGINAL GRP foam filled door in the UK makes sense. Equally, if GRiPCORE, BRiTDOR or any other new door created in the future becomes mainstream, as ORiGINAL has, quantity manufacturing can be backed up in Korea. Part of the reason for inviting the trade press to view Doncaster at this early stage is to involve us with the whole journey of this manufacturing facility and it will be very interesting to watch the progress of this substantial investment by DoorCo. Even now, manufacturing is taking place and the site’s development will run side by side the production of the BRiTDOR.
And what of Macclesfield, you may well ask? After all there are some 200 people employed at DoorCo HQ? The plan is straight forward, and Macclesfield will be the warehousing, prepping and glazing hub. The innovation Doorco puts into all its products has also covered FLiP glazing system, which can be used for the 44mm and 48mm BRiTDOR systems. Initially, DoorCo will prep all 48mm, but will not offer a glazing service due to the stock availability of thicker Glass units.
Dan Sullivan told us how the Doncaster team are well settled and manufacturing is in progress, indeed order taking is open now. The team are excited that they are officially open for business and Dan is happy that Mark, together with Senior Manufacturing Manager, Chris Mansfield and Doncaster’s Manufacturing Manager, David Wells-Burr, have everything in hand ready for the door orders through DoorCo’s ordering portal.
The team were keen to emphasise that BRiTDOR is a truly British product and the company’s Marketing Manager, Ellie Pool, talked about the naming of the product and the design options they looked at. “BRiTDOR captures exactly what this is – a British made door. No frills, no ifs, buts or maybes. BRiTDOR is a simple, solid choice backed by Brilliantly British Manufacturing.”
Dan Sullivan invited us all to visit regularly to watch the progress of this exciting development at Thorne, Doncaster, and I, for one, will take advantage of the offer as watching a development of this type, from scratch, is definitely compelling. Apart from anything else, it’s barely a half hour journey for me to make a visit!
1 stop delivery with product & glass
Fast online KwikQuote service
Step by step installation guides
Fitted in minutes, glazed in seconds
Enhanced thermal performance
PAS24 security as standard*
Standard single & dual colour ranges at no extra
Bespoke RAL or BS colours
10
Group, the UK’s leading manufacturer of bespoke, certified fire safety doorsets, is proud to have been recognised as one of the nation’s fastest-growing investment-backed businesses.
This prestigious accolade comes from a landmark report commissioned by BDO LLP to analyse value creation and understand supercharged growth within UK businesses.
Sentry Doors, which is owned by Cairngorm Capital, is a trusted partner for fire safety compliance across a diverse range of sectors, including social housing, education, healthcare, leisure, and commercial.
From their Birmingham and Doncaster sites, they manufacture a comprehensive range of fire safety and security doorsets that meet the most stringent building regulations. The company works closely with social housing providers to replace unsafe fire doors, a critical area of focus following the Grenfell tragedy.
The inaugural Private Equity Value Report written by Real Deals, on behalf of BDO, revealed that the 435 qualifying companies achieved an average combined EBITDA and Compound Annual Growth Rate (CAGR) exceeding 100% between the 2020 and 2022 financial years. Sentry has demonstrably surpassed these impressive benchmarks.
Within Yorkshire, Sentry stood out as a regional leader, ranking a remarkable number 15 among the 38 fastest-growing businesses. This recognition underscores
Sentry’s exceptional performance in areas like EBITDA growth and job creation over the last three years.
Moreover, Sentry secured the number 3 position within the Yorkshire manufacturing sector, further solidifying its position as a leader within the regional manufacturing landscape.
Since Cairngorm Capital acquired Sentry Doors in 2019, the company has witnessed remarkable growth. A £3 million investment has equipped them with state-of-the-art machinery and a new ERP system which has helped to optimise efficiency.
This significant investment was followed by the strategic acquisition of E. & S. W. Knowles & Company Limited (Knowles) in August 2022, which solidified Sentry’s position as the UK leader in fire safety and security doorsets, and expanded their footprint across two sites.
The Cairngorm Capital investment, coupled with the Knowles acquisition, has more than doubled Sentry’s production capacity, and their product ranges have expanded to include the specialist finishes used by the health, education and private sectors. This combined investment and acquisition strategy has not only enabled them to cater to new markets through Knowles’ expertise, but also positioned them to meet the growing demands arising from new fire safety legislation. As a result, these efforts have yielded a remarkable 100% increase in both turnover and profits, along with a 36% increase in EBITDA between 2020-2022.
This growth has translated into significant job creation, with employee numbers jumping from 28 in 2019 to a current
workforce of 200 across both the Doncaster and Birmingham sites.
As a leading, local employer, Sentry prioritises employee development and invests in its people through dedicated training programmes, ensuring a skilled and knowledgeable team. Over the years, Sentry has cultivated a supportive, family-oriented company culture that attracts and retains top talent. They also support the local economy by continuing to utilise trusted, local supply chain partners.
As well as following an impressive growth trajectory, Sentry has also begun its journey towards a more sustainable future, and the company recently hosted Ed Miliband, Shadow Secretary of State for Energy Security and Net Zero, who wanted to find out more about Sentry’s sustainability roadmap. They have already adopted a number of eco-friendly manufacturing practices including recycling waste sawdust and using an innovative heat generation system within their warehouse.
The Birmingham facility boasts ISO 14001 certification and FSC® Chain of Custody certification, reflecting a commitment to environmentally responsible practices. Sentry’s support for initiatives like Trees for Cities further demonstrates a dedication to sustainability.
Ty Aziz, CEO at Sentry Doors, commented: “It’s fantastic to be named alongside so many impressive businesses and is testament to the support of our investors and the hard work of our team. It’s important to shine a light on the positive impact that external investment can have on business’ ambitions and their contribution to their industries and the economy.”
“Our decision to partner with Cairngorm Capital in 2019 has proven instrumental to our success. Our initial growth plan aimed to double revenue and triple EBITDA. Today, we’ve surpassed those goals, achieving a fivefold increase across all criteria – revenue, EBIDTA, profit and production figures – since 2019. This signifies the remarkable impact of our strategic partnership.”
“We are passionate about delivering exceptional fire safety solutions, prioritising social responsibility, and investing in a sustainable future. While achieving significant growth, we remain committed to our core principles - a strong focus on family values and fostering a positive company culture.”
Nick Millward, Director at BDO LLP, added: “Despite the challenges of the past three years, this research demonstrates PE-backed businesses are a resilient and dynamic segment of the UK economy. There’s often a focus on the level of deal activity and headlines around exits but we should also celebrate the value created by investors and management teams working hard to deliver against their growth plans.”
To read the full Real Deals report, visit https://www.bdo.co.uk/en-gb/insights/ industries/private-equity/private-equityvalue-report.
Find out more about Sentry Doors by visiting https://sentrydoors.co.uk/.
*EBITDA stands for earnings before interest, taxes, depreciation and amortisation.
With a commitment to improving every area of the business, leading aluminium supplier AT Precision has made a significant investment in a brand new commercial truck, securing a seamless delivery service across the UK.
The Durham-based company, that’s been specialising in the manufacture of quality aluminium bi-fold hardware since 2020, has enhanced its operation with the new 18-tonne lorry, in a move that follows the recent introduction of the high-quality Everglide range of aluminium profile for bi-folds to its product portfolio.
Michael Hewitt, AT Precision Sales Director, comments: “We’re incredibly proud of our new bi-fold profile offering,
which gives us the ability to provide our customers with everything they need in order to manufacture a bi-fold door, but while we can make all the manufacturing upgrades we want, without effective investment in our operations, it will all be in vain.
“We’ve always prided ourselves on our next-day delivery service, and with our new profile offering, we’ve been seeing an influx of orders, so we needed to invest in order to keep up our reputation for quick and reliable service.
“The branded truck will be invaluable in continuing a stellar service nationwide, but I’m certain will also help to generate increased enquiries and sales for the company.”
The new truck is one of many investments made by AT Precision in the past year – in addition to a new profile range, the company has also moved into a brand new state-of-the-art 60,000 square foot factory, ramping up both storage capacity and production speed.
In addition to aluminium profile, the company manufactures the Everglide range of bi-fold hardware, the Everseal range of gaskets, security hardware, and a wide range of hinges, handles, and plastic ancillaries. AT Precision promises next day delivery on all orders made before 1pm, and free delivery on all orders over £250.
For more information, visit www.atprecision.co.uk.
Growth and success aren’t just around the corner. For Conservatory Outlet and its network of independent Premium Retailers, success is in the here and now, as Greg Kane, Conservatory Outlet’s CEO, explains.
For all the talk of doom and gloom, 2024 has been a year of opportunities - if you work hard for them.
The wider market may be slowing down as homeowners continue to be careful about opening their purse strings. Inflation remains high, though the rate has shown signs of stabilising. People and businesses alike are becoming accustomed to managing interest rates over 5%. It has been accepted that the days of interest rates of less than a percentage point are long gone, and everyone is planning accordingly.
People are still willing to spend money to improve their homes. That fact has never really wavered, even during the past 18 months when interest rates and finances began to rise month-on-month. People’s needs haven’t changed. Homeowners still need new, more energy-efficient windows. They still want new, safer and more design-led doors. They still want to add value and space to their home with a new or rejuvenated living space.
It’s just the ease at which they are willing to commit has changed.
If you look closely enough, leads, sales and the potential for smart, agile businesses to grow have remained. Fabricators and retailers across the country have to work smarter – and in many cases harder – to tap into it.
Those that do, have seen phenomenal results.
Over the first three months of the year, our Premium Retailers have grown by 17% year-on-year.
Sales have been incredibly strong, with several retailers recording their highest-ever monthly turnover.
As a fabricator, Conservatory Outlet plays an active role in helping our customers not only maintain their business but grow it. We do that by keeping ahead of the competition and adapting to the market, from both B2B and B2C perspectives.
I noted earlier that fabricators and installers have had to work smarter and at times harder to grow. We’ve provided our customers with fully-funded sales training sessions that were tailored to address shifting consumer behaviours. Over 100 sales professionals benefitted from this and our Retailers are clearly reaping the rewards.
In addition, through our leading in-house marketing team and partner digital agency, we have doubled our efforts to secure a stream of strong, convertible leads. Again, it’s all been about quickly adapting to consumer behaviour, rather than waiting for the dust to settle and then setting a course of action. We’ve been decisive with our advice and guidance.
And the result has been more leads and more sales.
I’ll touch on the new build sector and commercial sectors too. Our internal figures show a clear growth in contracts, sale values and tenders received. This is in no small part due to our size and ability to scale quickly in a way that doesn’t threaten our day-to-day operations.
This has been done by design, and with our commercial and trade partners in mind. That section of the market can harness Conservatory Outlet’s manufacturing and
operational capacity, one that’s built in a slightly different way to those fabricators who have run close to the bone, requiring a constant wave of low-volume orders to remain solvent.
We’ve secured several high-profile contracts by being able to step in late and complete plots - and in some cases entire developments - quickly.
As a business, we too have been making advancements.
In January, we rolled out our next generation of composite doors, allowing our customers to offer a growing collection of door designs and colours that are exclusive to them. We’ve also developed a new living space system and have further product lines in development, that we will be announcing shortly.
These will sit alongside and enhance our existing exclusive product ranges. These ranges are vital to the success of our Premium Retailers as they provide them with a clear competitive advantage.
Internally, we have invested further in our infrastructure, our staff and our processes. We have introduced multiple new production lines to expand our capacity, hired more people and we have further improved our already leading product quality.
Further opportunities are indeed on the horizon.
But why wait for them when there are opportunities today? There are plenty of them and Conservatory Outlet will deliver them to you.
If you're an installer that’s willing to work hard for them and work with an organisation that's forward-thinking and truly set up to help you grow month after month and year after year - no matter the conditions – you’ll thrive.
True authenticity comes from a blend of heritage styling and modern performance.
Single features may grab attention, but a true heritage sash window is designed to ensure the seamless integration of all its parts.
Everything has to work together: slim overlapping putty-line profiles, a 35mm midrail, heritage chalk finishes, seamless ornate sash horns, true mechanical joints, deep cills and innovative balance chamber covers, to name but a few.
Add to that a 1.2 W/m2k u-value without specialist glass, and you have a true conservation-grade sash window with outstanding modern performance.
Only Roseview’s Ultimate Rose sash window delivers all this. Because it’s more than a sum of its parts.
TuffX has become an official member of Made in Britain, joining hundreds of other British manufacturers in being eligible to display the distinctive and protected ‘Made in Britain’ quality mark of assurance on its goods and marketing.
‘Made In Britain’ is the official trademark for British manufacturing, signifying that products are manufactured in Britain and to the highest standards. The mark is protected and can only be used by members of Made in Britain, who must be transparent in their manufacturing claims in order to be eligible to join.
“The ‘Made in Britain’ mark is instantly recognisable and offers our customers at-a glance assurance that TuffX products offer
the best of British,” says TuffX’s Commercial Director Paul Higgins.
“It's a symbol of our craftsmanship, high standards and reliability, and it will help our customers make confident and informed decisions about what they are buying.
“For us as a business, being a Made in Britain member means we can showcase our products in the member product directory, the go-to place for consumers and trade buyers looking to buy and support British made goods. Made In Britain also supports its members with information and guidance on issues such as trading overseas and sustainability, for example, as well as working with government to give us, as members, a greater collective voice.”
The ‘Made In Britain’ mark began life as a logo competition for a commercial marketing campaign in 2011. Interest in the winning mark quickly grew until Made In Britain was launched as an independent non-profit organisation in 2013.
More than a decade on, the ‘Made in Britain’ trademark is now used by over 2,000 British businesses of all sizes across a broad range of industries, reflecting the diversity of British manufacturing. The trademark verifies that 100% of the labour that made the finished product carrying the mark is in Great Britain or Northern Ireland, and promotes British manufacturing.
www.tuffxglass.co.uk
CDW Systems is set to introduce a dedicated technical department for the first time in its history.
The specialist aluminium fabricator’s recent merger with its sister company, supplier and installer Clearway Doors & Windows has enabled the move to take place, in what is an exciting development for the business.
CDW Systems’ Gloucester headquarters will house all manufacturing and production and the newly formed technical department, comprising Technical Director Richard Smith, Technical Manager Nick Till, and Engineering Manager Luke Pemble.
Managing Director Jeremy Phillips said: “Our dedicated technical department is a significant step forward for
the company as it will give us a more cohesive approach to product development, solving any issues or problems customers get with products themselves, their installations, and complying with the latest building regulations.
“Richard, Nick and Luke bring together a wealth of indepth technical knowledge under one roof and it means that our customers have access to a dedicated team of experts that can provide them with the technical guidance and support they need.”
Clearway, which has become a division of CDW Systems, is continuing to be used for the supply and install side of the business, with all trade supply now coming under CDW and the merger brings together an impressive combined 73 years of fenestration industry experience.
“At CDW we’ve always provided exceptional customer service and merging the two companies will make
everything much more streamlined for customers, and our new technical department continues this,” added Jeremy. “The industry is constantly evolving with regulations and products, and we want to be at the forefront for customers, to refine existing products and anticipate customer needs.”
For more information visit www.cdwsystems.co.uk or call 01452 414853.
Pioneer Trading Company, which manufactures the Deceuninck range of windows, doors and conservatories to the trade throughout the UK, has renewed its membership with Secured by Design (SBD).
It has also added Gerda Engineered Entrance Doors, for which the Essex-based firm has exclusive distribution rights for the UK and Ireland.
Products covered under the agreement include Deceuninck doorsets, casement and flush sash windows, and Gerda Optima 60, Thermo Premium and Thermo Prime doorsets.
Tina Beal, Group Sales Director for Pioneer Trading Company, said: “We are delighted to continue our long association with Secured By Design, which ensures that we continue to manufacture and sell windows and doors that meet the highest standards of security and performance in our industry.
“Of key importance is the inclusion of Gerda Engineered Entrance Doors, on our Police Preferred Specification Accredited
"Pioneer Trading Company has been with us for 16 years with membership dating back to 2008.
I am delighted that they continue to feel that having the membership benefits them.”
Product List. With their aluminium outer frames and steel facings Gerda overcome the inherent problems of bowing and warping that composite doors suffer from and offer superior security. They sailed through the PAS 24 tests prior to us obtaining our SBD Accreditation.”
As well as high levels of security, Gerda Doors also offer superior U values, ranging from 1.3 W/m2K for glazed designs, as low as 0.74 W/m2K for the Gerda Altus door which exceeds Passivhaus standards.
For Secured By Design Lyn Poole said: "Pioneer Trading Company has been with us for 16 years with membership dating back to 2008. I am delighted that they continue to feel that having the membership benefits them.”
www.pioneertc.com
www.securedbydesign.com
Staff at Shelforce had another morning they will never forget after being presented with their King’s Awards for Enterprise certificate signed by the King and a unique domed glass crystal to immortalise their achievement.
The Birmingham window and door manufacturer received the King’s Awards for Enterprise in Promoting Opportunity (through social mobility) last year.
Established in 1965, the awards have propelled UK businesses onto the world stage with an internationally-renowned symbol of excellence. Previously named The Queen’s Award for Enterprise, His Majesty The King approved the Prime Minister’s recommendation that Shelforce be recognised.
Shelforce specialises in supplying highperformance PVCu casement windows, composite doors and its fully compliant Fireshel 30-minure fire, smoke and security resistant door to local authority building projects, including Birmingham City Council.
The business employs 31 people, of which 75% have a disability, and provides a place where people with mental or physical disability can thrive in employment.
Shelforce welcomed The West Midlands’ Lord Lieutenant, Sir John Crabtree, to its headquarters in Erdington. Sir John presented The King’s Awards for Enterprise engraved crystal winner trophy to staff and gave a short speech on what the award means for the West Midlands before meeting and congratulating the team. The event was also attended by members of Birmingham City Council, including Wayne Davies, Director of Asset Management.
The team were also able to view the official The King’s Awards for Enterprise charter, which was signed by King Charles and Prime Minister Rishi Sunak and recognises ‘the outstanding achievement of Shelforce.’ It will be proudly displayed, along with the domed glass crystal, in the reception at Shelforce’s headquarters.
Since 2021 Shelforce has scooped several awards, including being crowned the 2021 Greater Birmingham Chambers of Commerce (GBCC) Business of the Year off the back of winning the Excellence for People Development award at the same event and, in 2023, winning the ‘Most
Significant Service Improvement’ award at the first ever City Housing Awards and being named Business of the Year at the Great British Business and Community Awards.
The King’s Awards for Enterprise, however, has been by far the biggest and Howard Trotter, Shelforce’s Business Manager, said: “It was a huge honour to welcome Sir John to the factory and it was brilliant for the team to be presented with the King’s Awards for Enterprise crystal and charter as our success is all down to them.
“Something like this really drives home to the team how well they are doing and how good they are at their jobs. When they hear that this comes from the King it gives
them even more drive and determination to succeed.”
New signage and a complete refurbishment of Shelforce’s reception and offices courtesy of long-term partner Equans have come off the back of the success, while three new team leader roles are in place to be filled and an investment in new machinery will increase manufacturing capacity and help the business meet ever increasing demands.
“The recognition and weight that the King's Award for Enterprise carries, signifying excellence in various aspects of business, has enhanced our reputation and attracted
positive attention from potential clients and has helped open the door to other councils and housing associations, whose social values and sense of social responsibility line up with our own,” added Howard.
“Eleven years ago, the perception was that Shelforce was broken, and we would not survive, so to get to where we have and to receive the highest honour in UK business, renowned across the world, is an unbelievable achievement.”
For more information on Shelforce's wide range of products and services, of if you would like to discuss your next project, please contact them on 0121 603 5262 or visit their website at www.shelforce.com.
Colin St John, Commercial
Director of Freefoam BuildingProducts Ltd, looks at the cladding market phenomenon; the designs and colour ranges, and European market trends affecting the UK.
In 2023, cladding topped the Rated People’s Home Improvements Trends – with demand increasing by an amazing 743%.
The market has shown little sign of slowing since, with our top cladding stockists (and their installer customers) seeing sales soar.
New cellular foam cladding in particular is not only challenging timber cladding, but being used to replace existing old-fashioned cladding colours, to renew tired white PVCUE cladding, and to transform unsightly render or replace outdated tiles. Low maintenance, long-lasting, easy to handle and install (and stunning), it’s the choice of design, colour, and long-lasting guarantees that is really driving this makeover market forward.
It’s an exciting prospect for installers and stockists – if they work with the right partner. A supplier that’s come late to the market with only one or two me-too products won’t allow you to compete effectively. It's vital to choose an established cladding manufacturer that offers a broad array of tried and tested products in thought-out finishes and colours that work with other elements, supported with print and online marketing.
Since the late 1990s and early 2000s Freefoam has grown with and invested in the cladding market, developing and creating a significant range of options in the UK – and for leading players in Europe too.
We now offer four ranges in the UK:
1 Fortex® Double Shiplap, traditional Weatherboard (or ‘featheredge’) and Shadow Gap, all available with an embossed finish in a wide range of attractive and on-trend colours including Sage Green and Misty Grey – and now the digitally printed Fortex® Natura
2 X-Wood premium 16mm boards, finished in stunning woodgrain.
3 Single Shiplap, available in white and smooth woodgrain
4 Slimline Open V cladding
Some of our ranges now feature up to 11 different shades – and Anthracite Grey is offered on almost all our cladding products. This popular shade is often specified for high-end bifolds, doors and windows, as is Agate, or Misty Grey, an up and coming on-trend colour. The availability of these shades in cladding means installers can easily upsell a full suite of products – and often higher value ones too. We offer RAL numbers (exact shade or nearest equivalent) so installers can enable homeowners
to match cladding to other building elements for total house transformations that can often lead to more sales in the neighbourhood.
Colour-matched fitting accessories offer further options for add-on sales.
The UK cladding market often follows in the footsteps of continental trends. The more mature European market was an early adopter of external PVC-UE cladding, especially in areas in Western Europe with temperate maritime climates. Here there is a greater need for robust building products that stand up to the ravages of moisture, which is unsuitable for timber cladding.
Aidan Harte, CEO of Freefoam, comments: “Freefoam has been at the forefront of cladding products in Western Europe for the past 20 years, expanding from the West coast of France (traditionally a strong market for PVC building products) to Spain, Belgium, the Netherlands, Germany and Scandanavia. We work with a broad range of customers including specialist stockists, and large/national builders’ merchants across Europe, including SaintGobain, the biggest building products distributor in France.
“The challenge on the continent has been to meet the demand for versatility in terms of ease of use and looks. The French and Benelux markets for example, are quite adventurous with colour so this has driven us to extend the options, while embracing new materials and designs to improve weathering performance in hotter and wetter climates (eg Spain) even for darker colours like Anthracite Grey.”
This research and development has allowed us to offer tried and tested market-leading guarantees on white and coloured products. Fortex® cladding, for example, is a longterm decorative cladding solution, designed to withstand many different weather conditions, with a 10-year guarantee in the UK on a variety of shades.
Some of the products we’ve recently added to the UK we’ve sold on the continent for a number of years. Shadow Gap was added to our high-end Fortex® range last year, having previously sold well in Europe. Co-extruded with a rigid foam core, Shadow Gap features
an embossed finish like painted pine, with a deep groove between boards, and can be fitted horizontally or vertically.
Meanwhile, market research led us to introduce a digitally printed wood-effect cladding in Fortex® Natura. This premium V-groove cladding was launched earlier this year. Like Shadow Gap, it can be fitted in various ways (even diagonally!) and is guaranteed to look as good in a decade as it does the day its installed. It’s a market disrupting product and virtually indistinguishable from quality planed timber – but unlike natural wood, it doesn’t fade.
Our continuous focus on new product development shows we take cladding – and the opportunities it presents – seriously. It’s this experience and expertise that means we can help UK stockists and installers grow and take advantage of the expanding cladding market with the widest range of design and colour options.
See Freefoam’s full cladding range at www.freefoam.com - or call 0800 002 9903 to boost your business and add cladding to your portfolio.
It’s good to talk! So says the Automatic Door Suppliers Association which has just launched its own podcast – Tech Talk.
The series will feature conversations on topical issues facing the industry and interviews with those who work in it.
The first episode focuses on changes to BS EN 16 005 - a standard that defines safety in use and test methods requirements for power operated pedestrian door sets. It teases out the main changes of the update and responsibilities that fall upon manufacturers and technicians.
The 10-minute discussion is hosted by ADSA MD Ken Price, in conversation with Technical Training Manager Darren Hyde and Head of Operations Fae Ellor.
“People consume media in different ways and at different times – from their daily commute to when they are exercising. By producing Tech Talk as a podcast, we hope to highlight important issues, break them down and examine them in detail but in a way that is easy to access and provides a different take on a variety of subjects.”
The monthly podcast is available through Apple and Android streaming services and can also be accessed through the ADSA website and social media channels. ADSA members can also access episodes through its online Academy.
Tech Talk has been introduced as an extension to ADSA’s existing communication channels and its availability on public streaming channels is intended to make it more accessible to “people on the go”.
Said Ken: “We felt that this was an ideal medium for many of our members, particularly technicians, who may be on the road travelling to different sites. Podcasts provide a bite-sized opportunity to raise awareness of key issues, in a way that can be informative and entertaining.
“People consume media in different ways and at different times – from their daily commute to when they are exercising. By producing Tech Talk as a podcast, we hope to highlight important issues, break them down and examine them in detail but in a way that is easy to access and provides a different take on a variety of subjects.”
It is planned that some episodes of Tech Talk will also be produced as video casts to incorporate visual requirements.
Leading manufacturer AT Precision has announced a significant surge in demand for its Everglide aluminium profile for bifold doors.
In the past year since its launch, an impressive 12 fabricators have switched to Everglide profile, having previously sourced their systems from alternative suppliers.
Everglide profile is manufactured in-house at AT Precision’s state-ofthe-art facility in Durham. This meticulous in-house production process allows the company to deliver exceptional quality at competitive prices, a key factor in attracting new customers.
“We’re delighted with the positive response we’ve seen to Everglide profile,” comments Sales Director Michael Hewitt. “Fabricators are recognising
the significant benefits it offers, not only in terms of cost-effectiveness but also in quality and performance.”
Everglide profile boasts impressive technical specifications, including a U-value of 1.5W/m²K and full Document L compliance, ensuring exceptional thermal performance.
With maximum sash dimensions of up to 1,200mm wide and 2,500mm high, the profile offers superior design flexibility, catering to a wide range of project requirements.
“Everglide profile caters to the growing trend for larger bi-fold door applications,” Michael explains. “The ability to support sashes up to 100kg in weight makes it ideal for projects demanding expansive glazed areas.”
Fabricators choosing the Everglide profile benefit from a true one-stop shop for all their bi-fold door needs.
AT Precision offers a comprehensive portfolio of products, including the Everglide range of bi-folding door rollers, guides, and hinges, the Everseal range of gaskets, and a wide range of security hardware, eliminating the need for multiple suppliers and streamlining the procurement process to save valuable time and resources.
For more information on Everglide aluminium profile and AT Precision’s complete range of bi-fold door components, visit www.atprecision.co.uk.
Spot three differences. Fill in your answer and your contact details below and send your competition entry to: FAO: Christina Lazenby, Glass News Competitions, 19 Heather Close, Tickhill, Doncaster, DN11 9UU or Email: christina@glassnews.co.uk. Entry deadline: 20/06/24.
As a nation we're too quick to talk ourselves down – you turn on the news, and it’s always bad.
This lack of positivity can be very damaging. For example, I think the economic prospects for the second half of the year will be better than the first. Inflation seems to be under control. We've got a general election, which normally means money is going to get thrown at everybody to try to win votes. And I think customers will be in a better position to part with their cash as interest rates come down, so there will be more consumer confidence in the market.
But I do think that our job as business leaders is not to talk everything down, and instead be a bit more positive. Yes, the market is tough, but we've been here before and we'll be here again. It just means that we must work harder and work smarter to win new business.
It’s a conversation we regularly have with our customers, because we have a range of tools that can help them win business and keep their operations running efficiently and profitably. For example, our EasyAdmin package can create professional looking quotes, track deliveries, and allow customers to have full oversight of their profit and loss.
We’ve seen that, since the start of this year, more of our customers are engaging with these tools, and they are doing better than those customers who don’t. Similarly, customers who want to learn more about our product ranges are engaging more successfully with homeowners, because they can more easily sell them a dream with a wide choice. You can’t sit and wait for the phone to ring and expect the leads to come flooding in.
In fact, it is this mentality that fuels the race-to-the-bottom on price. Where is the imagination?
We are very proud of the range and the quality of our products, but we are a fabricator, like many others, who make and sell PVC-U and aluminium squares.
The differentiation between us all shouldn’t be price, it should be the added value and extra services we offer. As I’ve outlined above, this can be much more effective at generating leads and winning sales than simply cutting prices, because you are engaging with what the homeowner truly wants.
I hope that the conferences and summits that are becoming popular in our industry can address some of these issues, because I think that if we are a little more professional in our approach – doing the right things at the right time in the right way – then I think there is plenty of work out there for everybody.
With the right approach, the second half of 2024 will be better than the first.
Mike Parczuk Managing Director, Sternfenster
Comp Door Sales Director, Richard Dilberto, gives a guided tour to Glass News’ Editor, Chris Champion around their manufacturing HQ based at Newcastle Under Lyme.
Covid had a big effect on everyone and starting a business at that time may not seem the most prudent thing to do! However, it didn’t seem to cause a problem for the recently formed Comp Door business that operates out of Newcastle Under Lyme. It wasn’t as if any of the management team were new to the composite door business with decades of experience in the industry it’s clear that Pierre Mifsud and his team knew exactly what they wanted to achieve and how to succeed.
With knowledge of the composite door business, and specifically with a timber
core as opposed to polyurethane foam, the team set out to produce the best possible door from their own experience and from knowledge of other products in the market. Quality materials to their own specification has been key to their fast start in the market. Not for them re-purposing FD30 fire door blanks but high end, engineered, cross
laminated timber door blanks in the form of Albasia Falcata. This is a fast growing and sustainable timber that comes from Indonesia and is strong but light in weight and by cross laminating makes a very stable door blank. Rather than go the route of GRP or ABS skins, Comp Door uses what they call CoolSkin technology, engineered
to withstand extreme temperature changes and maintain optimum impact performance, with a colour protective layer so that it won’t get worn away or chipped. This is based on PVCu with a foiled surface. The company has looked at every angle and issue concerning composite doors, not least bowing and colour fading, and have what they believe to be the ideal composite to give strength and longevity such that a 10 year warranty is given on products.
Cleverly, and I found it impressive and a great solution, the door blank is edgebanded prior to applying the Coolskin. With most composite doors the edgebanding covers the edge of the applied skin whereas in Comp Doors’ case it’s the other way round with the skin covering the edgebanding and providing a clean look from a straight on view with no seams showing and also protecting the join from rain or the elements, generally. Comp Door refer to this edgbanding as InvisiEdge and it certainly provides a great aesthetic while protecting the door’s core from moisture penetration.
The door construction provides excellent thermal and aural properties and the tough CoolSkin facing offers maximum security with its timber core. The door is hung in a Liniar profile outerframe that boasts an industry-first TriSeal for better waterproofing and draft exclusion. Altogether it’s an impressive product and Comp Door has opted for a sales model that offers fully hung doorsets only. No slab sales: just completely finished doorsets with every doorset a unique order.
All these doors are fitted with the renowned ABS anti-snap diamond grade cylinder, as standard, for ultimate defence, and have an Auto Slam Shut lock as standard.
There are 18 skin colours to choose from and these are foiled before being pressed to the door style. When it comes to door styles, all the timeless classics are there as well as a contemporary range that are described as ‘Discovery’. On top of this are stable doors and French doors and the usual very wide range of glass options. The choice of hardware is wide with both traditional and contemporary on offer and Comp Door claim that their doors can offer 250 different colourways.
In a short time the company has built up a strong following and probably has much to do with the pedigree of the owners and staff and the fact that they are well known in the trade. They are rapidly extending their sales reach out from their Potteries base and they have a strong following throughout the Midlands and the North which is branching out throughout the country. Currently they are using 7 liveried vans for delivery and will develop the fleet as their production of 500 doors per week grows. Can they compete with the longer
established composite door manufacturers? There certainly seems no reason to doubt it, they have gathered a strong team together and currently number around 70 people and they already have plans to extend the production area and they are fortunate in having suitable options for expansion nearby. They are maintaining a sensible lead time of around 2 weeks lead time on
doorsets and everything they do appears to be measured and well planned without stretching themselves into making promises that can’t be kept.
The embracing of technology has been a key factor in Comp Doors growth and their website is excellent and provides a door builder/order taker that is sent through to an installer and, once the order is placed, is connected through to the machining centres and back through to the accounts package. All very efficient and labour saving.
The Comp Door team are determined to produce the best possible composite and select the best materials and components to enable this. Their wealth of knowledge and experience has allowed them to innovate and be confident in their product while giving a very personal service to their customers. They have three core values: “Reliability: You can always count on us to deliver on our promises. Innovation: We're constantly innovating when it comes to our product range and processes. People: We are people focused, with our customers at the heart of everything we do.”
They provide support for their customers in the form of technical and marketing back up and it seems that their customers appreciate this such that sales continue to rise, and at a pace!
The desire amongst installers to target the top end of the market has become a primary reason for seeking new quoting software, according to latest findings from Tommy Trinder.
Tom Barfield, Business Development Consultant to Tommy Trinder, has been busy; he’s carried out more than 160 demos of the firm’s market leading sales app so far in 2024, 68% more than in the same period last year. According to Tom, it’s the desire amongst installers to attract more high-end clients which is causing demand to skyrocket -
“Back in the pandemic it was all about saving time. Installers, working all hours to keep up, turned to Tommy in the need for speed; as a means to get quotes out more efficiently. Quite honestly, installers just wanted their evenings and weekends back! But the going got tough, and installers have come recognise that there’s more to winning hearts & wallets than simply getting a quote out of the door.
This year has seen a surge in the number of firms on the hunt for software that will wow homeowners; tools to help position them at the upper end of the market selling quality products to discerning customers.”
The rise and rise of Tommy Trinder is well-documented; from a standing start four years ago the firm has grown rapidly to become to go-to quoting app for over 550 window installers. The ‘flight-to-quality’ amongst installers has spurred further gains for the firm, with more than twenty installation companies now signing up to use the app every month.
Commenting on the changing market conditions, Chris Brunsdon, founder & CEO of Tommy Trinder says: “The
cost-of-living crisis has polarised the market and the difference between The Haves and Have Nots has never been more marked. The Have Nots, under 50s homeowners with mortgages and big outgoings, have been hit hard and left with little to spend on improving their properties. It’s price over quality in the bottom half of the market and it's not pretty.
Meanwhile The Haves, generally over 50s homeowners who’ve paid off or nearly paid off their mortgages, have been benefitting from 20 years of rising house prices and accumulating wealth. Price is secondary for this group because whatever they want, they can afford.
Savvy installers know that servicing The Haves is the way to a sustainable future and have been actively seeking out software that will help them sell aluminium, timber, and top end PVC-U to these discerning customers. Tommy Trinder makes it easy to sell premium materials and premium features in a professional and engaging way. It’s proving to be the tool for the job.”
Installers can find out more about Tommy Trinderand book a free demo at www.tommytrinder.com.
Unique Window Systems is preparing for the next chapter in its ongoing success story.
The award-winning company, which is one of the UK’s fastest growing fabricators of PVCu and aluminium windows, doors, and curtain walling, has rebranded, unveiling a
new identity which will help to position it for further evolution and expansion.
Sunil Patel, joint managing director at Unique, explains: “Unique’s previous brand identity has served us well having been in place since our incorporation almost 20 years ago. During that time, we have enjoyed incredible success and growth, which includes our turnover surging from
£20.8 million to £39.2 million between 2020 and 2022.
“Times and design styles change however, and it’s important for us as a business to change with them. Our new brand identity is more reflective of the company we have become and better epitomises our position as a large, highly professional, and qualityfocused organisation.”
The new Unique brand is undergoing a soft launch, being introduced gradually as existing assets and materials are replaced or updated.
The business decided to adopt this approach as part of its wider environmental policies. A hard launch had the potential to create unnecessary consumption and waste.
As part of the rebrand, the Unique Window Systems name remains and is now complemented with the addition of a distinctive U brand mark.
In addition, a new corporate font is being adopted whilst the company’s corporate colours are evolving slightly to retain a connection to the previous brand identity and to preserve existing brand equity.
A new strapline is also being introduced. ‘Our future in fenestration’ reflects the impressive breadth of the Unique offer which caters for customers in the
commercial, new build and trade sectors. It also highlights the fact the business is on a collective journey with these customers to shape a mutually beneficial future.
Unique’s new brand was developed by WeBuildBrands – the specialist marketing consultancy for the fenestration, construction, and home improvement sectors.
Concluding, Sunil adds: “The introduction of the new Unique brand is an exciting development and a clear statement of intent. We may have achieved a great deal to date but we’re not about to rest on our laurels.
“Instead, we are committed to seeking out opportunities in every area – from our brand identity to our fabrication processes – to drive enhancements that are beneficial to us, our partners, our customers, and the eventual property owners and occupiers who live with our products on a daily basis.”
"Our new brand identity is more reflective of the company we have become and better epitomises our position as a large, highly professional, and quality-focused organisation.”
Hurst has launched the new Monaco One PVC-U door panel style, which offers a contemporary composite style aesthetic, creating more opportunities for installers to sell aspirational doors to homeowners.
“Our panel range is still highly popular,”
Sales Director Mark Atkinson said. “Whilst purportedly a mature product, it accounts for a large part of our business, and customers are asking us for even more styles and colours.
“According to a customer survey we carried out at the start of the year, 62% of respondents believe that the most important factor when selling a door to an end-user is its appearance and design.
“This supports our recent product development, and our newly launched Monaco One PVC-U door style, which brings a striking modern and aspirational look to our PVC-U panel door range.”
The new Monaco One door style is featured in Hurst’s ‘You’re Home With Hurst’ PVC-U panel door brochure, which also showcase’s the company’s Harmony Glass Collection. This provides contemporary, etched effect geometric designs that feature on both sides of the double-glazed unit to create an elegant 3D effect.
“We are also expanding our Harmony glass range to be available in more door styles. Again, this broadens the available product range for installation companies, and gives them a competitive edge,” Mark said. Mark said that GRP composite door sales continue to grow, driven by modern designs and industry beating thermal and weather performance. But panel sales show no signs of diminishing.
“We are seeing some real statement composite doors leave our facility here in Hull, so it’s no surprise that other homeowners see those installations and want similar designs for their own homes,” he said.
“By extending our panel range, we are helping our customers meet the demand in all market sectors.”
“The future of entrance doors is composite based,” Mark said. “But we can’t ignore the sizeable demand and desire that still lies within the panel market, or indeed our customers who operate proactively and successfully to help satisfy that demand.
“We aim to give them the products and support to help them meet those needs.”
For more information please visit www.hurstdoors.co.uk, email info@hurstdoors.co.uk or call 01482 790790.
AluK has launched a brand new ultra-low U-Value, slim sight line Lift and Slide patio door, which it says will ‘open up’ new opportunities for customers in the higher end of the retail market, where demand and margins are both still relatively strong, and in demanding coastal applications and highrise apartment projects.
The new AluK S140 Lift and Slide has the slim sightlines and flush sash aesthetic that buyers love, coupled with impressively low U-Values of just 1.2Uw double glazed and 0.8Uw triple glazed.
It’s been designed in conjunction with AluK’s team in Italy so has all the sleek, minimalist flair you would expect, as well as clever UK engineering which delivers a compact 140mm frame depth and effortlessly smooth, double or triple track frame options.
The new door offers plenty of flexibility and can accommodate double or triple glazed units depending on the thermal
performance required and, where acoustics are a priority, has plenty of capacity for the larger glass thicknesses.
For fabricators, the S140 Lift and Slide has been designed with easy preps to make it quick to manufacture and a dedicated sub cill and simple add-on for trickle vents. It also comes with the option of AluK’s clever new Quik Clip clip-in bead system.
AluK’s Managing Director Russell Yates commented: “This is a door which ticks every box for fabricators and installers looking to get a bigger slice of the lucrative premium market. It’s easy to manufacture and, thanks to the addition of our Quik Clip system, incredibly quick to glaze.
“Crucially, it’s also available at a competitive price point which will ensure it can deliver strong and sustainable margins. With bifolds and sliders now selling at an almost 50/50 sales split, and the latest industry research indicating that Londonbased buyers actively prefer sliders, the S140 really is a great new option for AluK customers who want to win business beyond their existing bifold offering.”
The new S140 comes with AluK’s popular Novae handles and impressive security, wind and weather performance credentials. All the details, including confirmation of the convenient 15-day product lead time, are available at: bit.ly/3w4AOl3
ODL Europe has further extended its door offer with the introduction of two new contemporary door designs. Both the new Moderne Benton and the Moderne Wellington offer sleek modern aesthetics and flush door detailing, tapping into the growing trend for contemporary minimalism.
Commenting on the contemporary range extension, Suzanne Nicholl, Head of Sales and Marketing at ODL Europe, said: “In a market where product differentiation is critical, our extended range of contemporary doors will help customers stand out from the crowd and maximise the market opportunities.”
The Moderne Benton delivers contemporary door styling at every level. Suitable for homeowners wanting to achieve modern aesthetics, the Moderne Benton offers an extensive range of options and glazing positions to suit all project applications.
The Moderne Wellington is characterised by its striking glazing panel which makes a real design statement. The flush glazing panel is available in a choice of styles and options and can be positioned either left, right, or in the centre of the door.
The two new contemporary door designs come hot on the heels of the newly launched Redford Door which
is characterised by its three-section glazing and flush contemporary aesthetics.
Suzanne commented: “Contemporary door designs are becoming an increasingly popular choice for homeowners. This shift highlights a growing preference for understated design aesthetics that can effortlessly complement properties of different architectural styles.”
The two new doors are available in any RAL colour and complement the new TriSYS® Modern flush framing system.
As you would expect from an ODL Europe door, the Moderne Benton and Moderne Wellington offer impressive product durability and superior stability allowing installers to fit with confidence. They are PAS 24 accredited and backed by a ten year warranty.
Suzanne concludes: “Our extended range of contemporary door styles not only meets but exceeds the demands of today’s discerning consumers, offering fabricators and installers a valuable upsell opportunity.”
Both the Moderne Benton and Moderne Wellington Doors are available to order.
Offering three-sectional glazing, which seamlessly combines with the modern appeal of the flush door design.
• Elegant, modern flush aesthetics
• Available in any RAL colour
• Complemented with a choice of contemporary glass designs
• Suites with the TriSYS® Modern framing system
• PAS 24 compliant
• 10 year warranty
Quickslide’s Quick-Glide is a revolutionary new slim stack and slide door system that has more glass, less frame and can be slid to open however you want, explains managing director Ben Weber.
Quickslide’s newest door offering, aptly named Quick Glide, has been creatively designed to offer homeowners a fully flexible slide and stack door with a multitude of possible configurations. This flexibility is created by multiple independently sliding panels which can be configured to suit any preference or stacked entirely to create a full span, unobstructed opening. What’s more its slim sightlines – more glass, less visible profile – means that when closed, QuickGlide looks great and lets in maximum light.
“Quick-Glide is completely flexible,” says Ben. “The panels move individually and are not connected, so there is no limit to the number of configurations you can have. Which means we can give customers exactly what they want in one system.
“What’s more, it’s slim profile, and with no visible hinges or hardware when closed –other than a simple handle on the main door – makes Quick-Glide as sleek and stylish as it is flexible.”
Marrying Invisifold’s slide and stack system with the Visofold 1000 slim system from Smart Systems, Quick-Glide comes with all the added benefits of slim sightlines, contemporary square sashes, and a new slimline Quick-Glaze Bead for faster installations. It is the culmination of market testing and researching for the perfect door system that can fulfil everything homeowners are looking for.
“We first tested the waters for a stack and slide system by showcasing the idea at
homebuilding shows across the country,” says Ben. “It was clear straightaway that this had huge potential. We received great feedback and people loved it. But crucially, by listening to what the market told us, we realised one thing was missing: those all-important slim sightlines.
“So, we put our R&D hats back on, returned to the factory and worked with the guys at Invisifold to come up with the perfect product that would tap into all the latest home improvement trends so that these doors fit the bill when open, closed, and everything in between.
“The sashes are all operated independently so they can be positioned anywhere across the opening to provide ventilation without having the door fully open, or open up entirely for that complete indoor-outdoor living experience. Then, when closed, the slim profile and hidden hinges gives a great finish, flooding a room with natural light and making it feel spacious and bright.”
And because function is as important as form, Quick-Glide has been designed with ease of installation and maintenance in mind. There are no rollers, as the doors run on self-lubricating pads. In fact, other than the master door hinge, there are no moving parts, which means less to potentially break. And all parts of Quick-Glide other than the master door hinge are made from Nylon 66 GF30 - a 30% glass fibre reinforced and heat stabilised nylon grade that offers increased strength and wear resistance – so they wont rust or degrade over time.
Quickslide’s Quick-Glide is currently going through weather and security testing. “After which we’ll have more news,” says Ben. “So watch this space.”
Nationwide Windows and Doors has made the switch with their composite door glazing cassette system having adopted DoorCo’s pre-foamed FLiP system.
DoorCo have paved the way in the cassette world with the launch of their system in 2021, which had a rework at the end of 2023 to roll out further improvements. The system comes with Foam in Place Technology, is available in 3 different profiles, and now features a simple corner and connector system which offers improved security and weatherability.
Speaking on making the change, John Whalley, Nationwide’s Managing Director, tells us, “We’ve been impressed watching the rise of the FLiP system from DoorCo over the last couple of years. It's been a journey of innovation and has evolved into a product that addresses a lot of the complex needs of the industry.”
Dan Edwards, Nationwide’s Production Director, continued, “The system is both streamlined and extensive. The pre-foamed gasket removes the need for glazing tape and the corners and connectors coming pre-screwed makes the whole system extremely quick and easy to use. However, the simplicity of the fitting does not extend to the offering, which is vast.
“The range includes 3 different profiles and a full selection of standard colours and stains, which match the most popular door colours. This level of variety makes FLiP a system that ticks every box.”.
Talking about this new arm to their partnership, DoorCo’s Managing Director Dan Sullivan tells us “Nationwide are a much-valued customer of ours and we really respect their perspective and opinions.
“We launched FLiP around 3-years ago now and have been working hard on continually innovating the system to ensure it can be everything that everyone in our industry needs and wants.
“We’re really pleased that the team at Nationwide will be utilizing FLiP in their production lines on upcoming projects. We’re confident that the system is at a point where it’s hugely exceeding market standards and will provide Nationwide’s end customer with the best product possible. We’re looking forward to working with the team at they make the switch and hearing from their experiences of using it.”.
DoorCo’s prepped composite doors come with the FLiP cassettes as a standard, but the system is also available for purchase via their distribution arm for fabricators to glaze with in-house.
For more information on FLiP, you can download the brochure from the DoorCo website or contact a member of the team on info@door-co.com or 01625 428955.
For more information on Nationwide Windows & Doors, visit: https://nwd.co.uk/
Tamworth-based trade association, Door & Hardware Federation (DHF) is once again stressing the importance of Environmental Product Declarations (EPD). An EPD is an independently verified and registered document that communicates transparent and comparable information about the life-cycle environmental impact of products. In summary, it measures the environmental ‘footprint’ of a product. EPD demonstrate the results of a Life Cycle Assessment (LCA), detailing ‘cradle to grave’ environmental impact of all processes involved with the manufacture of a product. This can include extraction and processing of raw materials, transport, all elements of the manufacturing process, dismantling and waste disposal.
“Although it is not yet compulsory to use EPD in the UK, the market is increasingly self-regulating as manufacturers seek to demonstrate carbon transparency and market their products accordingly,” explains DHF’s Commercial Director, Patricia Sowsbery-Stevens. “Participation in the EPD programme is essential if the construction industry is to meet the growing demand for greater sustainability. We are delighted to be able to support our members by offering generic EPD.”
Back in June 2017, DHF was widely considered ‘ahead of the game’ in launching 14 generic EPD (in collaboration with ARGE) - locks, door and window handles, hinges (single axis), lock cylinders, sliding door gear, window fittings, door closers, panic exit devices, shutter hardware,
letter boxes, padlocks, glass door gear, electromechanical hardware, and push button locks - and since then, the federation has been educating and informing its members about the role and growing importance of EPD in the sustainability process; a complicated subject, DHF has been plugging the ‘information gap’. This has effectively enabled members of the Building Hardware Group to meet changing market conditions.
“EPD provide manufactures with positive credentials that are key differentiators in today’s market, and a powerful way to raise an organisation’s profile and demonstrate environmental commitments,” continues Patricia.
“DHF continues to support the green agenda and the increasing move towards green certification,” concludes Patricia. “EPD are considered crucial in demonstrating continued sustainability and providing reliable information so one product can be compared with another by looking at the various lifecycle stages.”
Currently, the UK has set a target to achieve net-zero carbon emissions by 2050.
To establish which DHF members hold EPD visit: https://bit.ly/49QaLvG
Elevate your door projects with the sleek versatility of aluminium sliding doors or the expansive qualities of bifold options , all backed by Mercury’s commitment to quality and competitive turnaround.
Bifold Doors
Sliding Doors
Designer Doors
Heritage Doors
Entrance Doors
Commercial Doors
Sam Davies, FENSA's Technical Manager advises that the ever-increasing need for formal compliance in fenestration should not rest with the window fabricator, but with the surveyor, who must adopt a formal, structured approach to the issue
The role of surveyor is all too important in fenestration installation and navigating compliance can be tricky at the best of times. In my role I have the privilege of seeing hundreds of different survey methods of varying quality. From ‘back of a fag packet’ style free hand drawings to full on CAD drawings detailing every possible intricate specification.
One very common theme seen is over-reliance on the fabricator to provide compliance with very little detail or context to work with. It’ll come as no surprise that more often than not, trickle vents are the issue.
The technical department and assessment team at FENSA regularly point out missed details in surveys. Sure, there may
have been a line drawn at the top of the window to request trickle vents – but the question always follows – what size?
Habitable rooms (this includes bedrooms, living rooms, kitchens, dining rooms, studies and media rooms!) require 8000mm2 equivalent area, or as close as is technically feasible. Bathrooms and washrooms require 4000mm2 or as close as technically feasible. If you’re not telling your supplier what you need, how are they to know?
As an installer you can save yourself the hassle of a noncompliance and note down on the survey what level of ventilation you require in the window/door. Habitable room with one window? 8000mm2. Habitable room with two windows? 4000mm2 in each window.
COMPLIANCE WITH APPROVED DOCUMENT L
We’re currently seeing little change in the industry with the approach to demonstrating Approved Document L compliance. Energy efficiency of replacement windows and doors is an increasingly important matter and whilst we are
confident that most products in the market are compliant, the only way to demonstrate that compliance is through documentation.
There are two routes to demonstrating complianceU-value simulation reports or Energy ratings. Whichever the installer chooses to demonstrate it is imperative that the customer receives this information, not just for the satisfaction of building regulation compliance but also to empower the homeowner with the relevant information that their replacement windows/doors play a large part in the overall EPC rating of the property. Did you know that without knowledge of the window/doors performance the default rating given to an EPC calculator for double glazing is 2.0 W/m²∙K? Quite the difference when we know the windows/doors meet 1.4 W/m²∙K and in many configurations, much better!
That alone proves the value in providing the customer with this information – not to mention the administrative work that goes into providing this information to your CPS or building control retrospectively if the information is not available on site.
We are still seeing instances of signed disclaimers being provided as a means of avoiding compliance to building regulations in replacement windows and/or doors. Without anyone believing that this is acceptable practice. It is clear that the ill-informed advice previously given to the industry is still hanging over us and it is important that installers do not leave themselves at risk of the consequences of following this poor advice.
The department for levelling up, housing and communities made it very clear upon the enforcement of the 2021 version of Approved Document F via a published FAQ that; “A disclaimer signed by the homeowner stating that they do not wish to have background ventilators or that they will be installed in future is not a suitable way of complying with the Building Regulations. Work must comply with the Building Regulations and competent person schemes must monitor their registrants and take action against any registrant who is found to have carried out non-compliant work.”
https://www.gov.uk/guidance/approved-document-fvolume-1-dwellings-frequently-asked-questions
The latest total value sales from the Builders Merchant Building Index (BMBI) reveals that in Q1 2024 sales were -7.2% lower than Q1 2023, with volume sales falling -8.7% and prices edging up +1.6%. With one less trading day in Q1 2024, like-forlike sales (which take the number of trading days into account) were -5.7% lower.
The two largest categoriesTimber & Joinery Products (-10.6%), which includes windows and doors of all materials, and Heavy
Building Materials (-9.4%) – were significantly down.
BMBI is the closest measure available for residential RMI (Repair, Maintenance, and Improvement) and home improvements markets nationally. That’s why BMBI reports are included in the Department of Business & Trade’s Monthly Construction Update.
Total value sales for Q1 2024 were up +3.5% compared to Q4 2023. Volume sales were +3.9% higher and prices were flat (-0.4%). With three
additional trading days in the most recent period, like-for-like sales were -1.4% lower.
YEAR-ON-YEAR
Total value sales for March 2024 fell -13.6% compared to March 2023. Volume sales dropped -14.0% while prices edged up +0.5%. With three less trading days in March this year, like-forlike sales were -0.6% lower.
The two largest categories - Heavy Building Materials (-15.2%) and Timber & Joinery Products (-17.7%)were significantly down on the same month last year.
Total Merchants sales in the 12 months from April 2023 to March 2024 were -5.9% lower than the same 12-month period a year earlier. Volume sales dropped -11.8% while prices climbed +6.6%. The three largest categories, Heavy Building Materials (-5.7%), Landscaping (-8.4%) and Timber & Joinery Products (-13.2%) sold less.
Mike Rigby, CEO of MRA Research who produce this report, said: “Exceptionally wet weather in Q1 and a hold on interest rates did little to revive the faltering newbuild market. The National House Building Council (NHBC) recently confirmed that new home registrations in Q1 were down 20% on last year, and this drop in demand has been felt throughout the supply chain.
entertainment premises, while GfK’s Consumer Confidence Index shows another 2-point increase in consumer confidence in April, following a positive March. Could lower inflation, the prospect of interest rate relief and a new Government be boosting consumer confidence? If so, it could be a welcome shot in the arm for the housing and home improvement markets as we head into summer.”
“Despite clouds hanging over the sector –figuratively and literally –there may be a break ahead. The latest ONS data for Q1 shows a marked increase in new construction orders (+15.9% quarteron-quarter), buoyed by private commercial orders for offices, health, and
For the full report, Expert comments and Round Table Debates, visit www.bmbi.co.uk.
GfK’s Builders Merchant Panel GfK’s Merchant Panel includes national, multi-regional and regional merchants such as Buildbase, Jewson, Travis Perkins, EH Smith, Gibbs & Dandy, MKM and Bradfords. GfK’s Builders’ Merchant Point of Sale Tracking Data represents 88% of the value of the builders’ merchant market. GfK insights can trace product group performance and track relevant features. GfK can also produce robust like-for-like market comparability, tailored to the requirements of an individual business.
The Builders Merchant Building Index (BMBI)
Builders Merchant Building Index (BMBI) appears every month, in print and online. A full quarterly report is published every three months. The BMBI is a brand of the Builders Merchant Federation. Launched and produced by MRA Research, it uses sales-out data from GfK’s Builders Merchant Panel. BMBI includes a panel of leading industry Experts, who speak exclusively for their markets.
Specialist aluminium fabricator CDW Systems has seen the popularity of its Smart Alitherm Heritage Range increase despite the current market slowdown.
CDW Systems added the modern thermal aluminium range to its offering three years ago due to demand from customers and it has proved a fantastic decision.
Specifically developed to meet the requirements of refurbishment renewal projects, particularly in sensitive planning areas, the range is ideal for Victorian and Art Deco projects. It has also provided the ideal solution for many heritage projects across the UK.
Managing Director Jeremy Phillips said:
“We had a strong start when we initially introduced the Heritage Range, with success in our local Gloucestershire area where there are many older properties in need of refurbishment. That has continued thanks to its slim profiles and sightlines, which are the ideal solution for building renovations as well as new projects.
“The popularity of aluminium domestically combined with the industrial steel look being hugely desirable now is why the Heritage Range is becoming more and more specified.”
The Alitherm Heritage door and window ranges both feature slim profiles and sightlines that are associated with traditional steel doors and windows for timeless elegance while offering the thermal performance of a modern aluminium system with each delivering a ‘B’ Energy Rating.
The window range, which is security tested to PAS 24:2016 and comes with both Heritage and Art Deco hardware options, is
available in several formats, including fixedpane, top-hung and side-hung casement, pivot, and tilt and turn and these may be installed in a combination of horizontal modules, which are stacked using Smart’s coupling options to form a multi-part window featuring a specially designed drip bar between modules.
CDW Systems recent merger with its sister company, supplier and installer Clearway Doors & Windows, means that the manufacturing of the Heritage Range will move to CDW Systems’ Gloucester headquarters, which will house all production moving forward due to space and the machinery available.
“Moving Heritage, and Smarts AluSpace, which is also becoming more popular, to our Gloucester site will help meet the demand,” added Jeremy. “We still think of both as niche products, but that is becoming less of the case in today’s market. And offering both means we can offer customers the best of both – Heritage for external and AluSpace for internal.”
For more information visit www.cdwsystems.co.uk or call 01452 414853.
Fentrade has recently manufactured and supplied 55 casement windows for Llanidloes High School in Powys as part of the school’s refurbishment programme. Working alongside trade customer Window-Tec based in Builth Wells, Fentrade has helped to upgrade the school with high-quality, energyefficient aluminium windows.
The school’s original windows were single-glazed and in a poor state of repair. The single glazing meant poor thermal performance which contributed to higher energy bills and excessive carbon emissions. Similarly, the original windows had limited ventilation which negatively impacted the learning environment.
Recognising the need for a comprehensive solution, Fentrade and Window-Tec worked closely with Llanidloes High School addressing several design options to meet the project’s requirements. Together, they selected white high gloss frames to emulate the existing window design whilst ensuring maximum thermal efficiency. The 55 aluminium casement windows were manufactured from Aluk’s 58BW HI thermally efficient system for optimum performance, contributing to a comfortable and sustainable learning environment for the students.
Safety was also a top priority throughout the project, with several opening casements featuring Tri-hinges, enhancing pupil safety and providing peace of mind for the school community. And to further enhance the learning experience and ensure a conducive environment, soundreducing laminated units were specified across various project phases.
The six week project ran smoothly, and the attention to detail was evident throughout
Epwin’s Vertical Sliding Sash Windows have been used to transform a high-end private apartment development overlooking Kings Hill Golf Club in West Malling, Kent. The original timber sash windows had deteriorated considerably and were no longer fit for use. The development’s residents appointed Kestrel Home Improvements to undertake the replacement project throughout the property’s six apartments. Mark Ramsey, Managing Director of Kestrel, said: “We weren’t the cheapest contractor, but we offered the authentic window solution the residents wanted. We were able to offer sash windows that maintained all the building’s original aesthetics, including the arched detailing on four of the windows. The competing contractor had proposed making the arched windows square, which might have been simpler but would have compromised on the building’s aesthetic appeal.”
Kestrel was able to offer the arched window detailing thanks to the expertise of fabricator of choice Mercury Glazing Supplies and the versatility of Epwin’s Sliding Sash Window System.
In total, Mercury manufactured 32 PVC-U Vertical Sliding Sash Windows, four of which had arched tops. All the windows were manufactured in white on both sides and featured run-through horns and astragal bars to retain the aesthetics of the original windows.
The installation of the windows took under three weeks to complete, and the Kestrel team liaised closely with the building’s residents to keep disruption to a minimum.
The finished result is impressive. Mark commented: “The new Sliding Sash windows have restored the building’s high-end architecture and improved the thermal efficiency. Compared to the original
every stage. Chris Reeks, Managing Director at Fentrade, said: “Understanding the importance of minimising disruption to the school’s operation was imperative. Hands-on project management and tight communication with Window-Tec were critical at every stage as we delivered products to site, in full, to meet the phased installation schedule set out by our customer.”
Reflecting on the success of the project, Dave Evans, Director at Window-Tec, said: “As a refurbishment job, this is one of the largest we have undertaken. Fentrade’s support throughout the tender, ordering and manufacturing stages was invaluable. Despite the need for competitive pricing, Fentrade ensured that the product met our client’s requirements. Since winning the contract, Fentrade has consistently delivered according to our weekly schedule, keeping us on track with the programme.”
Fentrade is proud to have been part of this transformative project at Llanidloes High School. Chris concluded: “This project has been a great success and a testament to all parties involved. The professionalism and skill of the installation team at WindowTec was exceptional and we are delighted to have helped them deliver this first-class school refurbishment project.”
Tel: 01633 547787
www.fentradealuminium.co.uk
timber frames, the slimmer profile of the new windows lets more natural light into the building, something that the residents have welcomed. All credit goes to Mercury for the quality of the manufacture and our installation team for their attention to detail and exceptional working practices.”
Kestrel Home Improvements is based in Kent. It has three highly experienced installation teams and sells windows, doors and conservatories in PVC-U, aluminium and timber, as well as guttering and roofline.
Mercury Glazing Supplies has been a long-standing fabricator of Epwin’s Vertical Sliding Sash Window System for over two decades. The company has built its name on providing specialist window and door products that enhance a portfolio, and a commitment to customer service that goes above and beyond—a commitment clearly demonstrated in this project.
Steve Cross, Director at Mercury, concludes: “Our commitment is to always add distinct value to our customers’ projects. This project was no exception and demonstrates our manufacturing capabilities and the authentic appeal of Epwin’s Vertical Sliding Window when it comes to sash window replacement. We are delighted with the result.”
Tel: 0808 101 4143
www.epwinwindowsystems.co.uk
• Windows
• Doors
• Conservatories
• Conservatory Roofs
• Flush Sash Windows
• P atio and Bi-Folding Doors
• Leka and Leka xi Roofing Systems
• Ultraframe and Wendland Roofs
• Carports & Canopies
• ecotech Roofing System
• Skylite Roof Glass Unit
The designer behind OMNIA, the window system that will ‘set the standard for windows over the next 10 years’, has revealed it was customer feedback that drove him to create the revolutionary new system.
Phil Gregory, Design and Development Manager for VEKA plc, began visualising the system that would later become OMNIA when a customer challenged the finished look of her new windows.
“This particular customer had purchased flush-fitting windows, but as we all know, existing systems in the UK are only flush on the outside,” Phil said. “She told me she didn’t buy the windows for her neighbours, but for herself – so why weren’t they flush inside? The conversation stuck with me and was the inspiration behind OMNIA – it was our starting point.”
What followed was a three-year-long period of research and development which would result in the UK’s first doublerebated, double-flush system, which offers a complete suite of design opportunities for casement windows, tilt and turn windows, residential and French doors using just nine different profiles. OMNIA also looks set to transform fabrication by offering the highest levels of technical performance, with a hidden co-extruded gasket system that is automatically mated with the extrusions during manufacture, meaning no more time-consuming fitting by hand.
Here, Phil talks through his backstory and that of OMNIA, the processes he and his team went through to create such game-changing technology and shares the response from the industry so far.
Phil began his career in a window and door fabrication business at the age of 16. He then spent 12 years working for several PVCu fabricators in a variety of roles before joining a large composite door manufacturer, initially working within production, then progressing into a technical role.
Joining VEKA in 2013, his first position was as a Technical Support Officer providing technical support to internal and external customers and partners. Between dealing with enquiries, he was responsible for authoring and maintaining VEKA plc technical manuals and documents. However, product design was calling, appealing to
Phil’s natural appreciation for aesthetic and function. It wasn’t long before he started to become more involved in the development of VEKA products - earning a role as Design Engineer, and eventually progressing to Design & Development Manager.
“I’ve always been appreciative of good design – not only in function but form also,” he said. “One detail of PVCu windows that I always found puzzling is how many aspects don’t line through – particularly sight lines on glazing – so I’d often be found looking at the dimensions of systems to see if you could produce them in new ways to improve this.
“I’m also really interested in modular design capability; products that work together seamlessly in different ways to create new opportunities and outcomes, which is something that influenced me throughout the development of OMNIA.”
Following that influential customer interaction, Phil pulled together a small team of experts to come up with a new solution – one which would not only provide the industry with a double-flush system, but one which also eased the challenges of fabricators.
“We initially began looking at the next evolution of our systems in 2019, building a brief for what this solution could be,” he said. “In 2020, we began looking into trends and legislation to see what the future might hold for windows and doors, because we
“Working collaboratively at every step means we’ve produced a solution that can be rolled out smoothly without barriers or surprises.”
wanted to ensure longevity of the system – though changing standards are not easy to predict. In 2021 we presented our first concept for OMNIA to the board.
“One of the most important considerations was to produce a solution that could be integrated into any fabrication facility, including existing production methods and third-party products such as hardware. Once we had a concept we believed in, and which would achieve this, we began to involve more stakeholders to understand how OMNIA could benefit them. We sought their feedback and implemented it, to make sure the solution could work for as many people as possible.
“What we have created here is all you need, together in one place – for the first time in the industry, there is a full suite to make all the different window and door types. And they will all match in their appearance.”
The finished product from Phil and his team ticks the boxes of several other industry firsts.
As well as the automatically mated co-extruded gasket system, OMNIA also
supports various mechanical jointing techniques, including timber weld and VEKA’s patented, highly-cost effective ProJoin Gen 2 method. In practice, this means that recreating the look of a classic mortice and tenon joint is easy – ideal for when it comes to projects in conservation areas and the increasing demand for authentic detailing.
VEKA’s time tested profile details reduce bespoke tooling requirements – another big industry win – while for installers, the suite’s 70mm depth makes for an easy swap out of old units. Crucially, it offers full compliance with 2025 building regulations.
Harking back to his love of modular design, Phil said: “I have tried to incorporate as many common design facets in the range as possible, as well as thinking about what could be added in the future, to create a wealth of different combinations, styles and solutions that give homeowners everything they need but also make life simple for the fabricator and installer.
“There have been challenges throughout this project, just as there always is in product development, but involving industry experts and sharing ideas and concepts along the way has been a huge benefit. Working collaboratively at every step means we’ve produced a solution that can be rolled out smoothly without barriers or surprises.”
Described by VEKA as a ‘trailblazing, quantum leap in fabrication’, OMNIA has received a thoroughly positive response since its launch to the industry in April – something Phil anticipated but is nonetheless thrilled to see.
“We believed we had a good idea when we presented OMNIA for the first time, but the enthusiasm and belief we’re seeing today is overwhelming,” he said. “It makes me so pleased to know we worked on problems until we found solutions, to meet the high expectations that we put on ourselves.
“This has been the most challenging design project I have ever been involved in, but as we move into the next stages of the journey and launch into the market I – like many others who have been involved along the way – am excited to see the products installed, starting a new chapter in the range of systems, solutions, and services VEKA offers.
“We’ve built more than five decades of market-leading experience and expertise into OMNIA, and it is the right design at the right time.”
www.vekauk.com
As the UK’s largest privately owned aluminium fenestration systems house, Senior Architectural Systems can work with you to achieve your sustainability targets.
“From continuously improving our manufacturing methods, to utilising low carbon and fully recyclable aluminium across our full range of Part L compliant products, we are proud to do things differently.”
Mark Wadsworth, Managing DirectorChris Champion, Editor of Glass News, speaks exclusively to Tim Smith, Commercial Director of REAL Aluminium.
Chris and Tim talk about homeowner appeal of aluminium products, the vast amount of colour options available, as well as new products, recycling and the whole impressive portfolio that REAL Aluminium have to offer installers.
You have been fabricating aluminium windows for around ten years – have you always fabricated the Smart system?
We have a long standing strategic partnership with Smarts and have been fabricating the system for many years. Over this time we have developed and improved our proposition to make REAL Aluminium
firmly the first pick when it comes to Smarts aluminium products within the fenestration industry. We have done this by making the customer experience paramount with tools such as our online quoting and ordering. We give access to training on products and software and have experienced order processing and technical aftercare team members on hand to answer any questions that may arise. Over time our product offering has developed significantly, lead by customer demand, regulation changes, and our desire to widen our stock range to improve variety and lead times. We take great care and attention during fabrication and handling and the product is heavily wrapped before despatch to ensure it is received by our customer in pristine condition.
In that 10 years many new aluminium systems have been developed….have you been tempted to source a different system or are you content with what is on offer from Smarts?
Here at REAL Aluminium and the wider Customade group, we always have a finger on the pulse of “what’s next” and what developments are inbound within our
industry. This helps us shape our offering and proposition and we are constantly working on product development to keep at the front of the pack. With REAL specifically, our current up to date offering, wide range of finishes and styles, ease of use, fast lead times and consistent quality mean we have all the bases covered to give our customers the best possible chance of securing business in this challenging market. REAL Aluminium partnered with Smarts systems is a strong, reliable and respected partnership.
Over those ten years has your emphasis been on architects and specifiers working on commercial contracts?
At REAL and the wider group our typical customer profile leans towards medium to large retail installation business and trade counter outlets, with some specific newbuild and commercial specialists. When it comes to architects and specifiers the system houses, Smarts in this case, do lots of the hard yards here, allowing REAL to build upon this with tenders quoted and secured via our extensive customer base.
My previous question is based on aluminium, only now, being popularised for the homeowner. Is that correct or has there been a ‘high end homeowner’ market for a while?
In my view Aluminium has been an indemand product with homeowners and a sizable market for at least the last decade, with awareness coming from TV home improvement programs and significant consumer marketing from system houses and large fabricators. The home renovation live shows regularly showcase the credentials and benefits of Aluminium, focussed mainly around the visual impact of such slim, sleek looking products.
I see you talk about remakes or replacements being on a one week
lead time but what is the normal lead time for your aluminium products?
As we hold large amounts of stock, and in a large range of colours it allows us to offer swift lead times. We work hard to keep a high level of consistency in our quality and service so typically we offer a lead time of 8 to 10 days across Windows, Doors, Sliders and Bi-Folds. Any remakes are made as fast as possible.
You have a wide range of customers for other products offered by the Customade Group. Do those customers source both PVCu and aluminium from you or are aluminium customers completely separate and a different market?
The benefit of buying from a large multi product fabricator is that customers can simplify their supply chain as we have most solutions our customers will ever need. We offer Atlas Roofs, REAL Aluminium, Polyframe Rehau, Polyframe Euorcell and Virtuoso Doors. We work hard to make buying across our group a uniform service and experience. For example, Polyframe customers starting to buy aluminium products for the first time will have a smooth transition due to a very similar online ordering platform. They can also speak with sales and technical people that they have worked with for support on PVC previously. With our typical customers being trade and retail the markets are shared in my view. Most of our group customers offer aluminium products along side PVC.
What are the most popular colours for aluminium windows?
Anthracite Grey, Black, and White and combinations of these remain the most popular colours in Aluminium products, although we are seeing an increasing demand for alternate shades of grey. We also offer any RAL colour option on our full range of products should the standard range not cover what’s required and we have made the products in a huge variety of colours over the years. More and more customers are looking to personalise their home through use of alternative colours and this is a service we are happy to provide.
Do you offer both painted and foiled profile and, with aluminium, is there an advantage to one or the other?
We offer a powder coated paint finish on our REAL Aluminium range. The powder
coating is marine grade as standard so it’s a tough and resilient finish that looks great. Foil on aluminium is a very niche product and in our experience customers are almost always looking for a flat smooth surface finish. This almost always makes the powder coated painted finish the preferred choice.
Can we talk about the new products you are introducing? You are offering a tilt ‘n’ turn – these have always been a product that is peculiar to Scotland. Is that your target or is tilt ‘n’ turn becoming popular elsewhere?
In REAL Aluminium our recently released products include a brand new slim sash 400 series casement window, with a large reduction in sight line of over 20% on the previous system. We expect this new slim window system to be very well received and become a default choice for customers. We have also released a 400 series flush slim sash window and most recently the tilt and turn. The tilt and turn will support our customers efforts with commercial tenders and the Scottish market where we see strong potential to build on our already strong position. We have reintroduced the Heritage (Crittal replacement) system and that is available to order now.
How do you go about supporting your customers from both a technical and marketing standpoint?
We have extensive experience and support in both of these areas as they are a critical
part of being a good strategic partner to our customers. We have technical support functions for all our brands, and a very experienced order processing and quotes team that have the knowledge to support when it’s needed. Available marketing support is extensive for our customers. We have a range of collateral to support everything from retail POS through to technical information which customers can access online digitally or have in a physical format. We are also on hand to support customers with their own marketing initiatives and PR articles etc.
You are updating your website. Does this include the ability for your customers to order online and for the information received to be used to programme, CNCs and saws, automatically? Is the system integrated with an accounts package?
The website updates will include a resource of downloadable information to support our customers both with POS and technically. We already offer as standard the ability for our customers to quote and order products and get glass sizes online with our ordering portal. This is supplied free of charge with full training given as needed.
Can aluminium windows outsell PVCu in the future or will it always remain a premium product?
I think there is always going to be a place for both. With increasing regulatory demand for better and better thermal performance,
this inherently means Aluminium product development has to work harder to keep ahead meaning the price difference between PVC and Aluminium will remain. As such there will always be a market for both, although I think Aluminium is definitely growing its market share and will continue to do so.. to a point.
Are you involved with recycling or are most of your aluminium windows replacing PVCu?
We recycle as much of our waste material as possible via specialists to minimise our environmental impact, but yes I would agree that most of our Aluminium products are replacing, PVC or Timber windows. Many of our products like Bi-Folds will be installed into a new aperture or extension.
You have an impressive portfolio of products with sliders, bifolds, windows and the new products being introduced. What next for REAL Aluminium? Are there new products being developed?
We are always developing and improving our offering across the group. It’s a constant requirement to keep ahead of the field and in-tune with market demands. This year already we have released a new Atlas Flat roof system, three new aluminium window suites, advancements in our Bi-Fold door with many new options added such as flush fitting trickle vents in the sash. We are working on the next big thing, well two actually... watch this space.
Dynamic Hardware has launched its Dynamic Letterplate, which has all the benefits of the hardware manufacturer’s expertise and experience.
Tony Chadwick, Dynamic Hardware’s CEO, said: “Like all the products in our range, the Dynamic Letterplate is precision-manufactured and independently tested to surpass industry standards, ensuring reliable operation and a prolonged service life.”
Part of Dynamic Hardware’s Premium Stainless Steel Door Hardware Collection, the Dynamic Letterplate delivers a seamless blend of contemporary elegance and robust functionality.
The Dynamic Letterplate features a one-piece letterplate flap for a clean and sophisticated appearance and is available in a choice of colours and finish options. It’s suitable for use on PVC-U, timber and composite doors and suites seamlessly with Dynamic Hardware’s high-quality door furniture collection, ensuring a cohesive aesthetic across all door projects.
For security and functionality, the letterplate has a 180-degree flap opening with robust zinc pivot points for enhanced security. It is manufactured from high-strength 304 Grade Stainless Steel and uses Galvanised Steel for painted finishes. It features a full thermal acoustic barrier for insulation and an improved weather seal to withstand the elements.
Reflecting Dynamic Hardware’s understanding of the market, the Dynamic Letterplate is 300mm wide and is suitable for doors from 20mm to 80mm thickness. Tony comments: “By offering a single size that suits various door depths, we can help fabricators and installers reduce their stockholding.”
As an indication of the confidence Dynamic Hardware has in the quality of the letterplate, it comes with a 10 year mechanical guarantee and a 20 year surface finish guarantee.
Like all Dynamic Hardware’s products, the Dynamic Letterplate is manufactured in Dynamic Hardware’s own state-of-the-art 50,000 sqm manufacturing centre in South East Asia, ensuring reliable control and quality.
Dynamic Hardware combines hardware expertise and experience with a relentless focus on excellence to give its customers the products that make the difference. Tony concludes: “The letterplate is an integral requirement of every front door. The Dynamic Letterplate elevates the requirement on every level.”
To find out more about the Dynamic Letterplate and Dynamic Hardware, visit dynamichardware.co.uk or call 01922 907776.
The Sovereign Group is one of independent hardware supplier Carl F Groupco’s longest-standing customers of over 44 years.
David Fitton, Operations Director at the Sovereign Group says: “Carl F Groupco is one of our top and most valued suppliers. Communication is key in our business and the standard of communication and commitment from Carl F Groupco is exemplary. They offer us bespoke solutions to hardware purchases, complemented by excellent technical support and customer service. We know we can rely on Carl F Groupco.”
Sovereign is loyal to the Roto hardware that Carl F Groupco supplies, in particular the Roto FRH UNI Reversible Window Hinge System, Roto NT Tilt and Turn Gearing and TSL espagnolettes.
Julie Warner, Roto Product Manager at Carl F Groupco, comments: “Roto hardware is renowned for its quality and innovation, and we are proud that our relationship with Sovereign continues to flourish. Long term partnerships with customers and manufacturers are the backbone of Carl F Groupco. Working together ensures the success of our customers and over four decades this has strengthened our relationship with Sovereign.”
Carl F Groupco stocks a comprehensive range of Roto hardware and the two companies collaborate on product development, helping to give UK fabricators and installers the hardware features they need. The impressive reliability of deliveries upon which fabricators such as Sovereign rely also contributes to the strength of the relationship.
Formed in 1973, the Sovereign Group has grown substantially, investing heavily in training and technology, to improve and grow its business to meet its clients’ ever-increasing challenges. Its core business is the manufacture of PVC-U windows, doors, composite doors and sealed units and it has over 180,000 square feet of manufacturing and warehousing facilities in Lancashire.
Carl F Groupco is one of the industry’s longestestablished names in hardware. The success of its business founded on the strength and longevity of its relationships with customers and manufacturing partners as displayed by the Sovereign Group and Roto show.
Tel: 01733 393 330 – www.carlfgroupco.co.uk www.smartsecure.co.uk – www.carlfdirect.co.uk
Hardware specialist Carl F Groupco is highlighting the practical advantages of its SmartSecure solutions, especially its suitability for care home and assisted living installations. With a focus on safety and convenience, the electromechanical door locking systems offer the impressive security solutions needed for these specialised environments.
John Mitchell, Technical Manager at Carl F Groupco, said: “Our SmartSecure range brings huge value to care home providers, retirement villages, assisted living environments and more. The products provide the practical functionality that’s vital in these settings, and it’s clear that the market understands this. We’ve seen sales of our electronic and automatic door lock ranges increase by almost 60% in recent months.”
John says the FUHR multitronic 881 electromechanical door lock perfectly demonstrates the diverse benefits the SmartSecure range brings.
The electromechanical locking system offers versatile integration options. It works with virtually any third-party access control or building management system, so is easy to retro-fit and can be supplied to suit most project requirements. John said: “This versatility has been an important component in many of our customers’ recent projects, especially where existing solutions such as push-pad releases and intercoms are already in place and positioned away from the door.”
Enhanced features of the system, particularly valuable in the care home sector, include elements such as spring-loaded contacts. These facilitate seamless wireless power and data transfer between the frame and the door sash that are fully concealed when the door is closed. John comments: “This eliminates the risk of a cable breaking by door movement or tampering, a common concern with traditional setups fitted in these settings.”
To ensure the system ticks every box, there are Emergency Exit (BS EN 179) or Panic Exit (BS EN 1125) options too.
The Secured by Design accredited hardware provides impressive security benefits, including locking automatically when the door is closed.”
John concludes: “Our customers value the fact that the options on the FUHR multitronic 881 electromechanical door lock are almost endless, making the system suitable across a variety of sectors.”
Carl F Groupco has led the way in promoting the benefits of electronic and automatic door lock options for many years. It’s just one example of how the company’s hardware expertise adds value to its customers.
Tel: 01733 393 330 – www.carlfgroupco.co.uk www.smartsecure.co.uk – www.carlfdirect.co.uk
Leading window and door specialist, Winkhaus UK, are delighted to announce that they have become finalists in 5 categories in the National Fenestration Awards 2024, including Hardware Company of the Year and New Product of the Year.
Andrew Wilkins, Business Strategy Manager for Winkhaus UK, said: “The NFAs have stood for inclusion and representation for years and has sought to bring the whole of the sector together to find the very best people and companies for the last decade, and as a main sponsor for the event we are proud to see so many worthy companies and products becoming finalists in this year’s awards.”
“As a long standing supporter of the NFAs, we recognise and appreciate the honour of becoming a finalist in so many categories, and we wholeheartedly thank everyone who voted in favour of our products and our company.”
At Winkhaus UK, everything we do is centred around guaranteeing the success of our customers, providing added value services and solutions to ensure they have maximum competitiveness. The recognition of the products and services we offer by becoming a finalist in the National Fenestration Awards’ Hardware of the Year category is a testament to the hard work that’s been done in all areas of our business.
From the quality and reliability that is consistently measured through the manufacturing process, ensuring timely delivery and a dedicated customer service team, to the bespoke development and testing of our technical and laboratory teams, Winkhaus offers a comprehensive service to our customers that doesn’t end once our products are sold.
Since they introduced the first hooked autoLock almost 20 years ago, Winkhaus has endeavoured to expand and develop its renowned AV range in an innovation timeline of industry firsts. The high-security solution has now been nominated for three categories in this year’s awards: New Product of the Year, Door Component of the Year and Digital Marketing Campaign of the Year.
Andrew said: “We are thrilled to see that our newest autoLock has become a finalist for three categories in the National Fenestration Awards this year. Introduced to a
great reception last year, AV4 has introduced a host of new features and improvements suitable for multiple markets and applications. With a low force to operate and wider operational tolerances, it reduces the need to revisit sites and make adjustments, saving lost time and increasing customer satisfaction.”
The autoLock AV4 range consists of the AV4, AV4 Heritage, AV4 EntryGuard, AV4 M4 with blueMatic EAV4, blueMatic EAV4+ motors controllable with the Winkhaus doorControl application. The new AV4 product family is available in a range of backsets and faceplate sizes including U-rail, providing suitability for all door constructions.
ALUPILOT: REVOLUTIONISING ALUMINIUM WINDOW PRODUCTION WITH ENHANCED EFFICIENCY
Winkhaus UK has also become a finalist in the 2024 for the innovative aluPilot system, with a nomination for Window Component of the Year.
Launched in the UK in 2022, aluPilot allows Aluminium fabricators to save up to 10 minutes of production time per window with aluPilot, compared to traditional systems available on the market. Winkhaus has confirmed the result of 10 minutes time saving in tests conducted with manufacturers during aluPilot’s development and subsequent roll-out to European systems houses. When multiplied across weekly production, these time savings really start to add up.
In addition to efficiency gains, aluPilot offers impressive weight capabilities, catering to various applications. With options to support sash weights ranging from 130kg to 300kg, our aluPilot system is versatile and adaptable to diverse needs.
Andrew said: “At Winkhaus, we pride ourselves in developing innovative solutions to meet the requirements of our customers and guarantee their success. One of the most critical factors in manufacturing is time, and our aluPilot fitting system is designed to streamline the production process of aluminium windows. This will contribute to a more efficient and production-friendly system, saving time and increasing our customers’ productivity.”
As a main sponsor of the National Fenestration Awards 2024, Winkhaus UK would like to congratulate all finalists, and wish them good luck for the event. To vote for your favourites in this year’s awards, visit the NFA website: https://www.fenestrationawards.co.uk/nfa24/
To learn more about the products and services that Winkhaus offers, visit https://www.winkhaus.co.uk/en/ or contact marketing@winkhaus.co.uk.
Introducing the new AV4 range of autoLocking solutions and the benefits they provide for modern entrance doors including 2 hook, 4 hook, Heritage, Entry Guard and U-rail variants.
Introducing the new AV4 range of autoLocking solutions and the benefits they provide for modern entrance doors including 2 hook, 4 hook, Heritage, Entry Guard and U-rail variants.
Precision engineered and manufactured in Germany with reduced operational force for ease of use, increased operational tolerances to eliminate issues with doors that warp, non-handed to simplify your ordering and inventory management, with the optional flexibility of day/night mode for re-entry off a latch.
Precision engineered and manufactured in Germany with reduced operational force for ease of use, increased operational tolerances to eliminate issues with doors that warp, non-handed to simplify your ordering and inventory management, with the optional flexibility of day/night mode for re-entry off a latch.
Precisely what you would expect from a Winkhaus door locking system.
Precisely what you would expect from a Winkhaus door locking system.
For further information please visit winkhaus.co.uk or contact marketing@winkhaus.co.uk
For further information please visit winkhaus.co.uk or contact marketing@winkhaus.co.uk
Safeware, the specialist hardware division of Epwin Window Systems is celebrating the 21st anniversary of its iconic Safeware range of multi-point door locks. Since the inception in June 2003, the Safeware range of feature rich door locking solutions remain a popular choice with Epwin fabricators, demonstrating their timeless appeal and innovative design.
With an impressive record of over 1.5 million sold to date, Safeware door locks have retained their popularity over the years. Specifically designed for use on PVC-U and composite doors, its reputation for high-quality mechanisms and precision design ensures ease of use, reliability and durability.
During its 21-year tenure, the lock has developed into a suite of multi-point door locks, suitable for all market sectors. Paul Hinds, Head of Sales at Safeware, said: “The family of Safeware multipoint locks is renowned for prioritising security. Over the years, the range has evolved in line with market demands but the fundamental design principles have remained the same, demonstrating how ahead of its time it was when we launched it in 2003.”
"Yale SensCheck allows homeowners the option of being able to check the status of their doors on their smart devices and mobile phones with instant connected security status for peace of mind. Since the launch, Yale SensCheck has proved popular with our customers, helping them to tap into this growing domestic interest and creating valuable upselling opportunities."
The exclusive Safeware 7 multi-point lock was designed in collaboration with Yale. Paul said: “The Safeware 7 is a sevenpoint lock incorporating three hooks and four precompression rollers. It is designed to give optimum security with ease of operation. The lock is supplied with a one piece keep which features several innovations that are unique to Safeware, saving on manufacturing time and allowing simple, quick and effective installation.”
The latest addition to the range is the development of SensCheck, an integrated smart door sensor, in collaboration with Yale.
Paul said: “We were the official launch partner of Yale SensCheck back in 2022. Yale SensCheck allows homeowners the option of being able to check the status of their doors on their smart devices and mobile phones with instant connected security status for peace of mind. Since the launch, Yale SensCheck has proved popular with our customers, helping them to tap into this growing domestic interest and creating valuable upselling opportunities.”
As you would expect from an Epwin product, all of Safeware multi-point locks are fully tested to current security standards and supported by a 10 year warranty.
In a sector where innovation is rightly valued, it’s sometimes important to remember that some products will always stand the test of time. The Safeware multipoint lock is one of those products, which is why it’s celebrating its impressive 21 year milestone.
Tel: 0845 340 3968 www.epwinwindowsystems.co.uk
In today’s competitive landscape, where speed and cost often dominate decisionmaking, leading hardware supplier AT Precision stands firm in its belief that precision manufacturing is the cornerstone of long-term success. We speak to Sales Director Michael Hewitt…
While some manufacturers prioritise shortterm gains, at AT Precision, we understand the true value of precision-crafted components, something which has set us apart in years gone by.
It’s also a commitment to long-term reduced costs, enhanced safety and reliability, improved sustainability, and customer satisfaction that has seen us forge ahead.
At AT Precision, we manufacture the Everglide range of bi-fold hardware and aluminium profile, as well as the Everseal range of high-quality gaskets.
These products are meticulously manufactured and built to last, and because they’re made in-house, come at a more affordable price compared to other suppliers, ultimately saving our customers money down the line.
But a lower price doesn’t mean a compromise on quality – we prioritise building parts that are not just functional, but exceptional, with our rigorous quality control processes ensuring minimal defects and extended product lifespans, saving our customers significant resources in the long run.
At AT Precision, we recognise that that quality doesn’t come at the expense of the environment, and we therefore prioritise using recycled materials and minimising waste throughout our manufacturing processes.
This commitment to sustainable practices is further exemplified through our new in-house recycling plant, where our new Recycled Thermal Reinforcement (RTR) bars are manufactured.
Made from 100% recycled uPVC, the RTR bars add strength and increased thermal performance to windows, are quick and
easy to install, and boast a minimum lifespan of 35 years.
At AT Precision, our dedication to customer satisfaction goes beyond just the quality of our products. We believe in building strong relationships with our customers, and that means providing exceptional service throughout the entire buying process. Our team is available to answer questions and offer expert advice, no matter how complex the project. We also travel directly to customers throughout the UK to provide on-site product support and training, ensuring they get the most out of our hardware.
This commitment to comprehensive service ensures our customers not only receive high-performing products, but that they also have the knowledge and support to use them effectively.
AT Precision is more than just a manufacturer – we are a trusted partner dedicated to helping businesses achieve their goals. By prioritising long-term value over short-term gains, we empower our customers to build better, more sustainable products.
In an industry that prioritises speed and cost, AT Precision offers a refreshing alternative. We believe that precision manufacturing is the foundation for longterm success, and by investing in quality, we deliver products that are built to last, reducing overall costs and environmental impact.
Our commitment extends beyond the products themselves – our exceptional service ensures our customers have the knowledge and support they need to thrive.
Choose AT Precision today, and choose a partner for long-term success. www.atprecision.co.uk
“We believe in building strong relationships with our customers, and that means providing exceptional service throughout the entire buying process.”
Leading window and door specialist Winkhaus UK offers a comprehensive range of multi-point locking solutions to suit a variety of aesthetic and security requirements. Designed and developed for use in all types of applications and a range of doors, Cobra has been distributed throughout the UK and Ireland since the year 2000.
There is a range of variants available: Lever Operated, Key Operated or Split Follower (with latch withdrawal by key only on the outside). Cobra is manufactured using high grade steel and is plated to comply with the highest Grade 4 corrosion resistance requirement of BS EN1670. Smooth to operate, Cobra is designed with an
enhanced tapered hook and weather seal compression adjustment in the keeps, featuring ±2mm adjustment to aid with a number of installation and operation scenarios.
Stylish and secure, Cobra features anti ‘push-back’ hooks located behind the steel keeps for optimum security, and a sprung gearbox which helps to prevent handle ‘droop’. Tested to comply with PAS:24 and the Police ‘Secured by Design’ initiative, Cobra is available with square or rounded faceplate options in 20mm for timber and composite doors and 16mm for UPVC, with a u-rail option for aluminium doors.
Like all our multi-point locking systems, Cobra features our
innovative Nano Protect coating as standard, which protects the hardware from corrosion and the ability to recover from everyday wear and tear. Cobra is part of Winkhaus’ ‘Family of Locks’ range, which makes it easier for fabricators and installers to interchange one of Winkhaus’ locks for another based on customer requirements. Using the AV4 routing, Cobra, Thunderbolt, TruLock and autoLock AV2 can be fitted to all door materials and interchanged on-site, thereby reducing the time spent by, and cost of, property services and maintenance contractors.
Winkhaus Meiningen is a state of the art design and manufacturing facility dedicated to our locking solutions,
Hardware specialist
Carl F Groupco has seen an increase in demand for acoustic vents, highlighting the real-world impact of the changes to Building Regulations in 2022.
John Mitchell, Technical Director at Carl F Groupco, explains: “Sales volumes of acoustic vents have doubled year on year, with the majority of sales going to new customers. This clearly demonstrates the anticipated impact from the recent changes to Document F of Building Regulations, which relate to the ventilation in new and existing buildings.
He continued: “The 2022 amendment was particularly significant regarding testing requirements, which is why we were proactive in educating our customer base on the regulatory changes. At the same time, we were acutely aware of the importance of collaboration within the supply chain. For us, that meant leveraging our strong supplier relationships to secure a consistent supply of compliant-ready products, whilst also expanding our product range and providing inhouse technical support. This ensured our customers
could depend on us as the new regulations become mandatory. Today, our approach remains unchanged; our customers can always rely on us to provide as much support as we are able.”
Document F of Building Regulations sets the ventilation requirements to maintain indoor air quality and, following the 2022 changes, Local Authority Building Control (LABC) is now in charge of policing new build projects, requiring confirmation that each building complies.
By far the most economical and practical solution to meet the ventilation requirements of Document F is to use trickle vents and, as John highlights, it seems this is the route that most installers prefer.
Carl F Groupco’s trickle vent options include the EAW42W ventilator from ventilation experts Greenwood and the Acoustic Ventilator from RW Simon. For powered acoustic ventilation there’s the AERO range from Siegenia.
Carl F Groupco has a welldeserved reputation for its impressive commitment to customer service that means it’s a value-added hardware partner to its customers. Its supportive approach to the changes to Document F of Building Regulations and intelligent understanding of market forces, is a perfect example of its commitment in action.
Tel: 01733 393 330 www.carlfgroupco.co.uk www.smartsecure.co.uk www.carlfdirect.co.uk
where our team designs, develops and produces solutions that focus on quality, durability, ease of use and also offer the ability to tailor solutions to meet your requirements.
Winkhaus mechanical locking systems have a long tradition and have always stood for high levels of functional safety, user-friendly convenience and reliable protection. Our mechanical technologies can be used for a range of buildings from individual entrance or apartment doors to larger offices and buildings.
To learn more about the features and benefits of our Cobra multipoint locking solution, visit our website, https://www.winkhaus.co.uk/en/cobra or contact marketing@winkhaus.co.uk.
Hardware innovators, Dynamic Hardware has launched its range of contemporary Pull Bar handles.
The Dynamic Pull Bar handles are part of the company’s premium Stainless Steel Door Hardware Collection and deliver the perfect fusion of sleek, contemporary handle design and superior product performance. They are available in a choice of style options, including round or rectangular designs to complement modern entrance doors.
Speaking on the introduction, Tony Chadwick, CEO at Dynamic Hardware, said: “Sleek door designs are a clear trend at the moment. Our Pull Bar handles offer the contemporary styling that elevates the aesthetics of modern doors whilst delivering reliable handle performance.”
Suitable for use on PVC-U, timber and composite doors, the Dynamic Pull Bar handles are manufactured from premium 316 Stainless Steel offering superb resistance to corrosion. The handles have been corrosion tested to 1000+ hours and come with a 20 year anti-corrosion guarantee and 10 year mechanical guarantee, offering optimum levels of performance and reliability.
The Dynamic Pull bars are available in a stylish brushed stainless steel finish in addition to Matt Black and Gold. There is also a choice of inline and offset (cranked) variations. Bolt through or back-to-back fixing options are available to suit the door application, with all fixing screws supplied in addition to a clear cover washer to protect the door surface.
Like all Dynamic Hardware products, the Pull Bar handles are manufactured in Dynamic Hardware’s 50,000 sqm manufacturing facility in South East Asia and despatched from its headquarters and
The Dynamic Pull bar handles are part of a wider collection of premium stainless steel door furniture which includes door handles, letterplates, door knockers, numerals and letters, spyhole viewers, cylinder pulls and door restrictors for a seamless design solution.
Tony concludes: “Hardware plays a crucial role in the aesthetics of any installation. For contemporary door designs, our Pull Bar handles provide the perfect finishing touch. They are an ideal addition to any contemporary door portfolio.”
The Dynamic Pull Bar handles are available from stock.
Tel: 01922 907776
www.dynamichardware.co.uk
Our new advanced hardware technology stops the spread of 99.9% of infections, so you can keep your germs to yourself.
Our new advanced hardware technology stops the spread of 99.9% of infections, so you can keep your germs to yourself.
www.uapcorporate.com/armasmart
www.uapcorporate.com/armasmartwww.uapcorporate.com/armasmart
Mark Alton – Head of Product Management at Winkhaus UK guides us through the changes to fire doorset legislation and the requirements for a compliant residential fire doorset.
Fire safety and fire door legislation has changed significantly in recent years, with changes impacting every stage and aspect of a fire doorsets lifecycle, from design and testing to ongoing inspection and maintenance. The most recent changes include defining the role and responsibilities of responsible persons (RB’s) and accountable persons as covered in the Fire Safety Order (October 2023) and Social Housing acts (April 2024), which completes the sequence of changes identified by the Grenfell enquiry.
For RBs to meet their responsibilities, it’s appropriate to remind specifiers of the initial legislation changes that changed the way fire doorsets are designed, tested and how this test evidence is verified. This critical first stage in a fire doorsets specification becomes the thread of evidence that must be maintained through the lifecycle of a doorset, the Golden Thread. Mistakes at this initial stage mean a non-compliant solution will be specified, manufactured, installed, and maintained.”
The 2019 MHCLG (Ministry of Housing, Communities and Local Government) guideline identified the 3 critical performances for a fire doorset as Fire, Smoke & Security. The MHCLG guideline, along with the independent review of building regulations and
fire safety, also states that these critical performances should be 3rd party audited and certified.
These are a specific standard’s that fire doorsets should be tested against:
• Fire Performance – EN 1634-1 or BS 476-22
• Smoke Performance – EN 1634-3 or BS 476-3
• Enhance Security Performance – PAS24
All Winkhaus fire and smoke testing is caried out using EN 1634 as this is viewed as the more onerous of the two standards.
Earlier this year the Home Office published the latest detailed information on incidents attended by the Fire & Rescue Services, which provides a stark reminder of the importance of smoke as a key performance for a fire doorset. From the recorded fatalities just over half were overcome by smoke or the combination of burns and overcome by smoke.
As a business we have always tested our fire doorset solutions against all three performances, becoming the first to achieve three separate 3rd party accreditations for these performances and the first to receive this for mirrored Smoke performance. For smoke we are further seeking improvements in the standard as it currently allows for the door threshold to be taped during testing, an inclusion we do not agree with or follow in our own testing, as this blocks a gap at the bottom of the door sealing or hiding a potential weakness. All Winkhaus smoke test evidence captures fully assembled doorsets including all hardware and thresholds installed as they will be on site.
To create a compliant scope of accredited solutions its critical to test the range of solutions to the required standards for each of these three key performances, but also that the evidence is mirrored across the proposed range.
It is critical that testing reflects the range of products a fabricator wants in their scope of certification. As an example: If testing is completed for one door design, with identical hardware and fittings, this is the only door that evidence should be used for. The evidence from these tests cannot be used to show compliance for a new design with different hardware and fittings as there is no evidence to support the performances following these changes, so multiple tests must be carried out in order to build a compliant range of solutions.
In addition to testing our fire doorset solutions against all three performances, each performance now has its own mirrored FoAp (Field of Application) that identifies the design and range of products that are covered.
The introduction of 3rd party certification across the lifecycle of fire doorset was one of the main requirements of the new legislation. For RBs and tenants this provides confidence in the information provided and peace of mind that a compliant solution is being specified and installed. 3rd party certification schemes bring together the test evidence from these field of applications and consolidates the approved design range within the door manufacturers “Scope of Certification”.
UKAS accredited 3rd Party auditing is not just required to verify test data for fire doors, it is a critical requirement throughout the Golden Thread or lifecycle of a fire doorset. Every stage from
manufacture, through survey and installation, annual inspection and any remedial maintenance, must be 3rd party audited. All these stages within the Golden Thread refer back to the original Design and Testing, ensuring the correct components are being used to make or maintain a door.
Over the past decade the Winkhaus UK Technical Team have been involved in the creation and implementation of the latest standards and guidance for fire doorsets. Winkhaus fire doorset solutions are manufactured through our partner network of over sixty 3rd Party certified companies. With our partner fabricators, we have one of the largest evidence banks of compliant solutions for both timber and composite internal and external fire doorsets, all independently audited by BM Trada as part of their Q Mark scheme. This not only ensures our test evidence is always compliant, but always expanding to provide the most comprehensive range of options for all your project requirements.
Our continued investment in testing not only ensures our
continued compliance, it provides specifiers with the widest range of solutions to meet all residential and social housing requirements. As an example, our evidence bank now contains over 170 primary fire tests, evidence that was further expanded with the launch of the external composite and timber fire doorset ranges earlier this year. These external solutions have been 3rd party UKCA certified for Fire and Smoke a requirement for external and communal flat entrance doors.
Our range of solutions includes both 30 minute and 60 minute fire doorset solutions, with our internal 30 minute solutions averaging 47 minutes performance, an average over 50% higher than the minimum allowed results and with several tests achieving over an hours performance.
Creating compliant fire doorset specifications can be challenging for specifiers especially with the number and significance of changes in recent years. To support specifiers, we have created a series of checklists to simplify these changes and can further support specifiers in creation of their specifications and training to support their compliance journey.
For further information on how we can help with your specifications, to request copies of our checklists, for information on the new ranges of external timber and composite fire doorset solutions or our expanded ranges of internal timber and composite fire doorset solutions, please visit www.winkhaus.co.uk/en/ firedoorsets or email
marketing@winkhaus.co.uk.
Glass News’ Editor Chris Champion questions
Warmcore’s Mark Frain about the product, its future and how it fits in profine’s product line up.
Mark, you have a wide experience in our industry, from hardware in various companies and also with developers of aluminium products. Can you tell us a bit more about your background?
Like many people in our fantastic industry, I arrived without a conscious effort or plan to make my career in fenestration. I left school with the basic qualifications and worked in an engineering factory making car
components. My interests at the time where all around playing rugby on a Saturday and having fun with friends.
After a year or so I realised I had made a mistake and wanted more. I spent a year in college after work topping up the qualifications I needed and on completion was accepted for a Business Degree at Nottingham Trent University. I made some life long friends during that period and after graduation I was offered a job at Brunel Hardware, part of the Heywood Williams group as quality manager, the rest they say is history.
What is the motivation in joining profine UK?
From my German colleagues who helped with translation to meeting the team from Kömmerling Australia who have a fabricator customer in Perth who I went to school with, it’s been a wonderful start! profine and Kömmerling have always had a strong brand identity in the U.K and identified by many for delivering top quality products. Having visited Fensterbau many times over the years, I understood their global reach and WarmCore I believe has vast potential that I’m hoping to help realise with the team.
WarmCore is now part of profine and Kömmerling and the product is very much in your remit. Is the fusion of aluminium and PVCu an exciting product for you to promote?
Absolutely, I have so many strong features and benefits to promote to customers and it offers a point of difference and a differentiation advantage for fabricators and installers.
WarmCore was launched some time ago. Under the profine flag, is this a relaunch of the product or is it a continuation of support for WarmCore fabricators.
A good point as many see WarmCore as merely a bi-fold and the customers I am visiting are surprised that WarmCore is a family of products, incorporating a window system with standard open out casement, a tilt an turn window and a flush casement. As far as the future is concerned, this is very much a start of new journey, I have a host of ideas as do my product development colleagues, which we will hopefully share with you soon
Sadly, the WarmCore brand was tarnished by some of the choices and commercial performance of Synseal as a business. We will always support our WarmCore fabricators, but this is also an introduction to new customers who are unaware of the unique hybrid product range.
Working with over 200 Kömmerling staff on the recent Fensterbau stand and in talking to a number of potential customers in the UK and further afield made this very real. Some of the key staff from the Aperture and Synseal businesses is also a major plus for me and I am proud and excited to return and work with these great people again.
People may not realise that WarmCore is a complete suite of products. Can you tell us about those products within the suite and whether any will be added in the future?
One of the main attractions of WarmCore is thermal properties within an aluminium profile. Can you tell us about the thermal advantages and whether WarmCore can also boast sound insulation properties?
We are justifiably proud of the thermal performance of WarmCore products with it being a 70mm aluminium hybrid system. WarmCore products typically achieve a U value of 1.3 with double glazing and 0.9 triple glazed and the patio can achieve 1.4 with double and 1.0 on triple too.
These values are also honestly achieved with adherence to the sample size and style which are determined in BS EN 14351-1 standard. For sound insulation we have also carried out acoustic testing to BS EN ISO 717-1 with the best result achieving a 45dB using acoustic rated triple glazing.
We also carried out the same testing with consideration to a standard double glazed option (4/20/4) where we achieved a 34dB and with inclusion of P1A laminate for security and this improved performance up to 37dB.
Is WarmCore a contemporary style product or is it aimed at renovation work?
In my opinion think WarmCore can be used in both situations, although I may be somewhat biased!
Do you consider WarmCore to have slim sightlines in comparison to other profiles? Do you compare those sightlines against aluminium or PVCu profiles?
In fairness I do not consider WarmCore to have slim sightlines although it does compare with some other aluminium and PVCu systems on the market well. End users and some systems companies are in a race for the slimmest sightlines, regardless of the effects that this inevitably has on air, wind and water, along with security and U value performance.
Being a hybrid system what is WarmCore competing with, is it aluminium systems or PVCu systems?
It was designed to compete with aluminium systems and to be a product people would use when replacing PVC.
Why have you now included foiled finishes? Is it to match with existing foiled PVCu systems so, for instance, original foiled PVCu windows will match with, say, a foiled WarmCore bifold?
Absolutely, we were recently able to help a customer complete a project where they installed Irish Oak PVCu windows and doors throughout the property but needed a bi-fold for the rear and WarmCore was able to match seamlessly.
WarmCore is very different from profine and Kömmerling PVCu
systems. Does it sit comfortably within the portfolio? Indeed, does it enhance the offering?
One hundered percent it does, as we recently launched WarmCore 76 (a 76mm system for the European market) at Fensterbau and we are also looking to sell WarmCore globally through Kömmerling operations around the world. We have a number of international enquires already from Europe, South America and beyond.
Can we talk about dual colouring? Historically, aluminium systems have shied away from dual colouring even though
homeowners like the option. Is this an option for WarmCore?
Indeed it is and we are able to offer a range of dual colours on a two week lead time. Should demand increase we will work to reduce this lead time further in the future.
How do you position WarmCore…. as a replacement product for homeowners, as a new build product albeit for high end builds, or as a commercial offering?
WarmCore is relevant in all of those sectors. Foiled woodgrain finishes for homeowners and excellent U values and security for both new build and commercial.
What are architects and specifiers reactions to a hybrid product like WarmCore?
We’re at the early stages at this point, but we do have a large customer selling WarmCore into this sector with considerable success, thanks to the U-values and sound reduction properties.
Where do you see WarmCore going in the future? Is it a forerunner of other hybrid systems that will compete with you? Will it become a mainstream system that sits alongside PVCu, aluminium and timber?
Without question WarmCore will be a success and we’re investing considerably in the marketing and in a research and development programme at group level.
With Building Regulations set to get ever tighter in the years to come, WarmCore will prove to be the perfect solution across all market sectors.
Colour plays a big part in everyday life from clothing to interior decor, to cars and furniture and so on. In the window and door industry, colour is becoming increasingly important as homeowners expect the perfect finish to their property whatever type of window or door is being installed.
With colour being such a decisive factor for homeowners, window manufacturers and installers have to be flexible to make sure their products are either available in a range of different colours or can be made to an exact colour specified by their customers.
In view of homeowners’ diverse tastes, it is key for companies in the glazing supply chain to be working closely with reliable and flexible component suppliers that can deliver the right matching or complementary colours to complete the installation to the homeowners’ satisfaction.
As the marketplace becomes more competitive, combined with the consumer’s focus on aesthetics, Glazpart the leading plastic component manufacturer has planned meticulously to stay ahead of the competition by supplying components that more than meet their customers’ requirements when it comes to colours and finishes.
For the last ten years, Glazpart has consistently invested in state-of-the-art machinery, systems and tooling to provide a vast spectrum of colours and finishes of its award-winning trickle vent - the Link Vent range. It is therefore no surprise the company is in pole position to supply all colours and/or decorative finishes of trickle vents for any type (wood, uPVC, aluminium ) of window or door profile.
As demand increases due to the consumer choice of windows and doors and aligned with regulatory changes, Glazpart has led the way with the development and easy availability of trickle vents that come in more than just the most common colours (white and grey).
Some of the most popular colours in the Link Vent range include, Chartwell Green, Anthracite Grey, Redwood, Black and Cream. Link Vents can also be camouflaged on window profiles in over 40 moulded system house colours, with finishes that can also match embossed and woodgrain patterned foils. Glazpart’s trickle vents can even be sprayed at source to match aluminium RAL colours.
Glazpart launched the innovative Link Vent in 2013 in sizes 2500 and 5000 EQA and since then, with addition of the Link Vent 4000 (in 2022), the Link Vent with its vast array of colours, has become the leading ventilation solution for fabricators and installers to ensure compliance with Building Regulations, Approved Document F1 (means of ventilation).
Smart design, easy fitting, and functionality are fundamentals but it is the huge choice of colours and decorative finishes that sets Glazpart apart from the competition.
Glazpart is an approved colour paint sprayer for many paint systems developed for application onto plastic. The spray systems are special coatings designed to paint uPVC and other hard plastic such as ABS, polycarbonate and acrylic where the systems form a molecular cross bond with the plastic surface.
As well as standard RAL (European Colour Systems) and BS (British Standards) colours, Glazpart can also match to most other colour systems. In addition, the company has a specialist colour matching service that can match non-standard colours and supplied colour samples.
For homeowners, the benefits of Glazpart’s colours go beyond simple aesthetics but also durability. The colours are extremely stable and resistant to UV rays, so homeowners can be safe in the knowledge that the vents will hold their colour in extreme weather conditions and constant exposure to the elements of weather, without noticeable fading. Glazpart’s systems and products also do not contain lead, cadmium, zinc, formaldehyde or isocyanates so they are kinder to the environment and are recyclable.
Dean Bradley, Glazpart Sales Director summarises, “When it comes to choosing windows and doors, homeowners have become more particular and it’s often all about colour and finish. To meet homeowners’ demands fabricators and installers have to get the colour right. Over the last ten years, Glazpart has appreciated the increasing importance of colour and that is why we have invested in modern machinery, to ensure we can offer the widest possible choice of colours and finishes for trickle vents.”
For more information on the Link Vent’s range of colours and finishes please visit www.glazpart.com/colour-options/
Leading trade fabricator Dekko Window Systems has announced a new partnership with SaintGobain to install an on-site glass recycling unit at their Lancashire headquarters.
The new initiative will enable Dekko to collect and recycle old and unwanted glass units from customers, diverting waste from landfill and reusing the materials in their manufacturing processes.
This commitment to sustainability aligns with Dekko’s longstanding focus on environmental responsibility and reflects a growing trend within the industry.
“We’re thrilled to partner with Saint-Gobain on this important project,” comments Dekko Sales Director Kurt Greatrex.
“The new on-site glass recycling unit represents a significant step forward in our sustainability efforts, allowing us to reduce our environmental impact and offer our customers a more eco-friendly solution for waste glass disposal.
“Sustainability is a major priority for Dekko, and we believe it’s crucial for the wider industry to embrace more sustainable practices.
“This partnership with SaintGobain demonstrates our commitment to leading the way in this area and providing our customers with products that are not only high performing, but also environmentally responsible.”
Dekko is a leading trade fabricator of uPVC and aluminium windows and doors, supplying a comprehensive range of marketleading products to trade installers across the UK.
Their product portfolio includes uPVC windows and doors from Deceuninck, Residence Collection windows, and aluminium windows and doors from Reynaers and Decalu.
For more information, visit www.dekkowindows.com.
Engineered to maximise production capacity and efficiency while maintaining the highest quality standards.
Thermoseal Group has invested in a new recycling plant that will reduce the amount of manufacturing waste going to landfill.
Situated at the company’s Wigan factory, the recycling plant can handle all lengths of Thermobar warm edge, turning them back in pellets that can be reused in the manufacturing process.
“We have always been able to recycle the core material of Thermobar – polypropylene – but if it had the barrier tape attached, it would have to go to landfill,” Sales Director Mark Hickox said.
“Our new recycling equipment can remove the backing tape from the finished Thermobar, which means that any waste created during the extrusion setup process can now be shredded and reused.
“We can add up to 20% of the normal compound without any loss of performance, and it means that we send zero plastic waste in all the Thermobar production.
“Plus, the plant is also powered by a Solar PV System that we installed last year, so we are minimising our emissions in the process.”
This new investment forms part of the company’s ongoing sustainability strategy.
In 2023, new automated production lines reduced energy usage in Thermobar’s manufacture by almost 40%, and the company is expanding its steel stillage scheme, where Thermobar is delivered to customers without the need for cardboard packaging.
Also, the company’s Thermoflex flexible spacer bar is supplied coiled onto plastic reels, in a plastic bag, inside a cardboard box. To prevent this packaging from being scrapped, the company has developed a system where, similar to Thermobar’s metal stillages, the packaging is collected and reused.
This unique packaging method has successfully diverted 80%
of packaging away from landfill and has kept the price point of Thermoflex lower for customers.
“We manufacture over 50 million metres of spacer bar a year,” Mark said. “Imagine how much packaging is required for that amount of product. But with our recycling processes, we significantly cut the amount of packaging that we use, and we use everything until its lifespan is completely over, limiting the amount of waste we’re sending to landfill.”
Tel: 0121 331 3955
www.thermosealgroup.com
Avantek Machinery is excited to introduce the latest development in its inline PVCu window and door manufacturing range. The Wegoma 6-head Inline Hybrid Welder has been engineered to maximise production capacity and efficiency while maintaining the highest quality standards.
Understanding the primary differences between fully automatic and universal welders is crucial in deciding which inline welding machine will best suit your manufacturing needs.
Avantek Sales Director, Jamie Munday explains, “Auto welders are equipped with features which include: colour PLC with touch screen control of all welding functions, a quick release profile support block system, pneumatic transom self-centring systems, and a servo motor-controlled head alignment system, plus much more.
“All of this greatly increases the speed and accuracy of the welder compared to a standard inline universal (or uni) welder.”
Discussing the design of Avantek’s 6-head Inline Hybrid Welder, Jamie Munday states, “This unique six-head inline configuration features four fully automatic heads, plus two additional universal heads which have been specially adapted to produce H-welds as narrow as 370mm when turreted.”
He continues, “The cutting-edge addition to Avantek’s range reaches new heights in versatility allowing many welding combinations in one, cost-effective machine.
“This brand-new model allows the operation of four fully automatic heads, while simultaneously using the two additional universal heads in a turreted position independently - essentially providing the functionality of two machines in one.
“It’s a groundbreaking design that maximises efficiency by reducing the total number of welding cycles without compromising working with steel reinforcements.
"By incorporating user input, we’ve designed and built a welder unlike anything else currently available on the market."
Furthermore, it can be used as an inline 6-head welder when not using the turreting capacity of the two universal heads.”
The Avantek Machinery team understand that drawing on customer feedback during new product development allows needs and preferences to be identified, ideas to be validated, and helps refine new features.
Jamie explains, “In our pursuit of design innovation, we work closely with our customers to fully understand their requirements and get a clear idea of the user experience.
“This allows us to communicate insights to our suppliers and engineer manufacturing solutions from the ground up. It’s a collaborative approach that ensures we continuously redefine the benchmarks of machinery performance.
“By incorporating user input, we’ve designed and built a welder unlike anything else currently available on the market. We’ve also listened to what Avantek fabricatorcustomers are saying about market trends, carefully designing the two, turreting universal heads so that they can produce narrower sashes and smaller openings, catering to strong consumer demand for these types of windows and doors.”
Jamie concludes, “At Avantek we’re proud to offer our customers a wide range of machinery solutions that meet a diverse range of manufacturing requirements. Our Wegoma 6-head inline welder range is now available in 6-head auto, 6-head uni and 6-head hybrid configurations. This means we have a comprehensive armoury for our customers to choose from.
For more information and to arrange a face-to-face demonstration contact sales@avantekmachinery.co.uk.
Specialist door manufacturer UK Doors Online has just invested in new machinery from Haffner to support its continued business growth.
The new machinery includes a FMC 120 CNC Machining Centre, marking the company’s second investment in a FOM Industrie machining centre from Haffner. Additionally, the company has purchased a new TT 415 Double Mitre saw, while fellow group business Trade Window Centre, has invested in a new TT 405 Double Mitre Saw.
Andrew Glover, Managing Director at UK Doors Online, is clear why the companies have turned to Haffner for their latest purchases. “We know from experience that machines from Haffner deliver the quality of output that our customers have come to expect. We also appreciate the reliability and service support we get from the Haffner team which adds value to our business.”
Together, the machines will give both UK Doors Online and Trade Window Centre the quality and capacity they need to meet growing demand for their products, which include aluminium bifold, lift-and-slide, sliding patio doors and aluminium windows.
Andrew comments: “Despite tough trading conditions, UK Doors Online has achieved year-on-year growth of 8% and 16% in the past two years. We couldn’t have kept pace with demand without the skill and commitment of our team – or the exceptional quality and efficiency of the machines we’ve purchased from Haffner. Our latest machine investment will help us continue to capitalise on our growing
presence in the market.”
Matthew Thomas, Managing Director at Haffner, is confident that the new machinery will give both UK Doors Online and the Trade Window Centre the solutions they need to continue their impressive growth trajectory. He says: “We always take time to understand every customer’s plans and requirements so we can recommend the machines that will best suit their needs. This approach ensures that our customers receive tailored solutions that align with their business objectives and facilitate their ongoing success.”
The FOM Industrie FMC 120 CNC Machining Centre has been designed to carry out drilling and milling operations on aluminium and steel profiles. Features include three independently controlled axes and a worktable with pneumatic positioning at 0°, 90° and 180°. At the same time, the machining head allows machining on three sides of the profile and on the two ends with the aid of milling disks and blades. Both the TT 405 and TT 415 Double Mitre Saws streamline profile cutting, making the process more efficient.
Together, UK Doors Online and Trade Window Centre have a strong presence in the trade, commercial and domestic markets thanks to their commitment to putting the customer first. They offer their markets proactive service and the highest quality products at competitive prices. The addition of the new machinery package and the continued support of the Haffner team seems certain to ensure their continued success.
Tel: 01785 222421 – www.haffnerltd.com
+Quadra is the next generation of Emmegi’s iconic 20-axis modular Quadra CNC, which can cut, drill and machine all in one single operation.
Designed to deliver even more volume, bigger capacity and faster speeds, it represents a significant leap from the L0, L1, L2 and L3 versions of the original Quadra, which have long set the standard for precision engineering in aluminium and are installed at many of the UK’s leading fabricators.
Emmegi states that the new +Quadra with its 360° rotary based milling, drilling and tapping on 4 faces of the profile and 360° rotary cutting blade does everything that the original Quadra can do – and more.
As previously, there are four high frequency electro spindles for +Quadra L0 and six and eight for +Quadra L1 and +Quadra L2, all housed within a soundproofed cabin. Amongst the most eye catching new features though are dynamic counterblocks which can be programmed to recognise the profiles being selected and automatically adjust and set the vices without the need to set up individual counterblocks each time.
There is also a new head and tail end milling module and cutter unit with variable rotation speed up to 8000rpm and an automatic labelling module which can position the label on 3 sides of the profile.
In terms of volume and capacity, there are clever new additions to the loading and bar feed system which allow for extended unmanned cycles. This includes a profile
Sternfenster has installed its new Forel high-speed automatic glass line, promising increased output, greater accuracy, and will future-proof the leading trade fabricator for an expected increase in demand for triple glazing.
“It’s a very clever piece of machinery,” Einars Kalva, Glass Production Manager, said. “It constantly monitors the glass production, and it will tell you immediately if the glass is the wrong size, of if you have put the glass coating the wrong way round.
“Small missteps like these can have a big impact on glass production, because it takes time to remake a unit. The quality of the finished product is also exceptional. Fewer units are being picked up by my QC guys, and our customers can install our windows confident that they will be the best they can be.”
The new 42m Forel line represents a £1 million investment, and includes a dual super spacer reel station, air cushion conveying system, georgian bar processing, diagnostic supervision module, hot melt robot, anti-static bar with quality scanner, and quality check and frame positioning station.
The line is complemented by a new £40,000 Atlantic sixbrush vertical glass washer with demineraliser, and a new £40,000 glass cutting table.
“Our glass shop is a key element of our manufacturing process, so it is vital we keep up to date with the latest, most efficient machinery,” Einars said. “For example, we see that demand for triple glazing is increasing, as homeowners learn that a small increased investment in their new windows will mean much lower energy bills for many more years.
lifting system which picks up the profile and automatically transfers it to the operating section, and the option of a high capacity belt loading magazine which can accommodate upwards of 8 profiles at a time. There is also a high capacity unloading magazine which automatically aligns all the machined pieces from one section before they are transferred to the unloading belt and, with 4m, 7.5m or 9m options, allows the entire volume of profiles from the loading magazine to accumulate without any operator intervention.
Ian Latimer, Emmegi (UK)’s Managing Director commented: “Like the original Quadra, the key benefit of +Quadra for fabricators is the fact that it does the work of a team of operators. That’s where the real payback comes in, as well as in the precision and accuracy it achieves on cuts and preps which mean there’s never any need for reloading or repositioning.
“The new +Quadra machine is available now as a modular offering with a number of pre-packaged options which we think make it easy and cost effective for fabricators to choose the features which matter most to them. They can still choose from a long list of individual options though if they want something even more bespoke and we can provide all the help and advice they need.”
All the details of the new +Quadra are at: bit.ly/4amIxtJ and there is a video showing the machine in action at: https://www. youtube.com/watch?v=f-Y5UkNMbKQ Tel: 02476 676192 – www.emmegi.com
“By investing in this new Forel high-speed line, we are creating more opportunities for our customers to capitalise on that demand across both our PVC-U and aluminium product lines.” For more information visit www.sternfenster.com, email sales@sternfenster.co.uk or call 01522 512525. Alternatively, join the conversation on LinkedIn: www.linkedin.com/ company/sternfenster.
As installers navigate the digital landscape, the significance of a strong online presence cannot be emphasised enough. For installers, creating one-stop shop websites can not only boost their brands but also drive business growth.
The Residence Collection uses its website to display recent installations and offer all the information homeowners, installers, and fabricators require. They also provide expert advice to help boost business growth in the long run by
creating key lead generation for all Residence Collection installers and fabricators.
Jo Trotman, Marketing Manager at The Residence Collection and Window Widgets has provided a comprehensive guide on how installers can transform their website into a one-stop shop.
At the heart of every successful website is a deep understanding of the target audience. Installers must anticipate customer needs and frustrations to deliver tailored solutions effectively. Personalization, intuitive navigation, and clear communication are key to enhancing user experience.
“Installers must prioritise mobile responsiveness to provide a seamless experience across platforms, allowing customers to access information anytime, anywhere.”
A comprehensive range of products and services should take centre stage on the website. Installers need to make it easy for customers to explore their offerings, with clear filtering options and engaging content that highlights the benefits of each product or service.
With the rise of mobile browsing, ensuring websites are optimised for all devices is paramount. Installers must prioritise mobile responsiveness to provide a seamless experience across platforms, allowing customers to access information anytime, anywhere.
Exceptional customer support is a cornerstone of a successful website. Installers must provide accessible channels for assistance and ensure prompt responses to enquiries, building trust and loyalty among customers.
User experience (UX) is a critical factor in achieving website goals. Installers should focus on simplifying navigation, optimising loading times, and delivering engaging content to captivate visitors and drive conversions.
To stay ahead of the curve, installers must continuously adapt to changing user needs and market trends. Ongoing maintenance, user feedback collection, and competitor analysis are vital for ensuring the website remains current and effective.
Tracking key metrics such as website traffic, conversion rates, and customer engagement provides valuable insights into the effectiveness of the website. Installers can use this data to refine their strategies and optimise performance over time. For window and door installers looking to elevate their online presence and drive business success, building a comprehensive website is essential. By implementing these strategies and embracing emerging technologies, installers can create compelling online experiences that resonate with customers and set their businesses apart from the rest in the digital landscape.
To find out more about The Residence Collection, please visit: https://www.residencecollectiontrade.co.uk/
• Alitherm 400i - NOW EVEN SLIMMER!
• Alitherm 400i - NOW EVEN SLIMMER!
• Alitherm 400i - NOW EVEN SLIMMER!
• Alitherm 400 Flush Sash WIndows
• Alitherm 400i - NOW EVEN SLIMMER!
• Alitherm 400 Flush Sash WIndows
• Alitherm 400 Flush Sash WIndows
• Alitherm 400 Tilt and Turn Windows
• Alitherm 400 Flush Sash WIndows
• Alitherm 400 Tilt and Turn Windows
• Alitherm 400 Tilt and Turn Windows
• Alitherm Heritage Windows and Doors!
• Alitherm 400 Tilt and Turn Windows
• Alitherm Heritage Windows and Doors!
• Alitherm Heritage Windows and Doors!
• Alitherm Heritage Windows and Doors!
The Double Glazing & Conservatory Ombudsman Scheme (DGCOS) has published their Spring 2024 newsletter, which rounds up the news and initiatives the organisation has been involved with recently to offer valuable insights for installers and the wider industry.
“The DGCOS Newsletter is an important tool for us as a membership organisation to keep our stakeholders up to date with what’s happening, both at DGCOS and in the wider industry”, says Faisal Hussain, DGCOS Chief Executive. “From producing a mental health focused podcast series with the National Home Improvement Council (NHIC) to adapting our registration options to include two and six year registrations, our latest newsletter is packed with information for the industry.
“As well as positive news, such as gaining the ISO 9001 certification for Quality Management, we’re never afraid to discuss the more difficult issues that we collectively face. It’s been a turbulent market for a while now and in the newsletter we discuss serious issues like the real implications of when an installer ceases to trade, as well as the impact the lack of skilled installers coming into the industry has had on the quality of products and installations.
“On the other side, we discuss the powerful tools we have available to our members: data, benefits of teamwork and communication, and the importance of top-level customer service.
“DGCOS is committed to supporting our members through a wide range of initiatives, including our comprehensive Installer Journey Benefits, designed to help and support with their businesses, and our newsletter is a great example of the work we do.
“The DGCOS newsletter is available to view online here: https://shorturl.at/HLOSX”
For more information on DGCOS, visit: https://installers.dgcos.org.uk/
On 21 April 2024, Epwin Window Systems’ Commercial Director Ray McGrady and Customer Service Advisor Tony Lloyd took on the iconic London Marathon course to raise funds for charities close to their hearts.
Ray McGrady said: “It was incredible to be able to join 53,000 runners on the start line. The crowds along the route were amazing and crossing the finish line was a special moment I’ll always remember. It was a privilege to run the event to raise funds for British Heart Foundation. Without their amazing work, my dad wouldn’t be with us today.”
Tony Lloyd said: “It’s the London Marathon! A marathon is always tough, but all the training paid off on the day. It was an honour to run this world-famous course on behalf of SpecialEffect, who I’m an ambassador for.”
Ray McGrady finished the course in 04:27:54, raising £2,131 for his charity, British Heart Foundation, which funds around £100 million of research each year into all heart and circulatory diseases and the things that cause them.
Tony Lloyd completed the course in 04:56:22 and raised £3,618 for SpecialEffect, which transforms the lives of physically disabled people right across the world through the innovative use of technology.
Gerald Allen, Head of Marketing at Epwin Window Systems, said: “Everyone at Epwin Window Systems sends their congratulations and respect to Ray and Tony for taking on the challenge of the London Marathon. We should also salute their fundraising efforts: between them, they raised nearly £5,750 for charity – a phenomenal effort in itself!”
Epwin Window Systems is a proudly British business based in Shropshire. It’s the UK’s largest systems house and offers the widest portfolio of fully integrated window and door systems with unrivalled expertise and support to add value to every business. Its success is driven by its people and their commitment to going above and beyond in everything they do. It’s an ethos that Ray and Tony demonstrated very clearly on Sunday 21 April!
To donate to Ray’s fundraising for the British Heart Foundation, visit https://2024tcslondonmarathon.enthuse. com/pf/raymond-mcgrady.
To donate to Tony’s fundraising for SpecialEffect, visit https://2024tcslondonmarathon.enthuse.com/pf/tony-lloyd. Tel: 0845 340 3968 www.epwinwindowsystems.co.uk
Balancing building safety with aesthetic appeal continues to be in demand with smoke control solutions rising in popularity. To support this, Pyroguard is delighted to announce the release of its new Smokeguard brochure, providing customers with valuable information on its toughened glass solution.
When it comes to smoke control, an important part of a building’s passive fire protection strategy, the industry is increasingly moving away from mechanical or obstructive smoke control curtains to contemporary glazed solutions. Smokeguard is Pyroguard’s smoke control solution, offering 30-60 minutes fire protection. Manufactured from a sheet of toughened glass, it’s designed to be suspended from the ceiling to offer a contemporary and visually appealing solution.
The new brochure is designed to be an informative resource for architects and specifiers and is available to download from Pyroguard’s website. Containing all the latest product information, technical drawings and details on fixings, the brochure also features recent project case studies from around the world.
Speaking about the brochure, Andy Lake, Pyroguard’s UK & IRE Sales Director said: “While the conversation around passive fire protection often focuses on fire safety glass, smoke control is just as important, having a real impact on the ability of occupants to safely evacuate a building. With this in mind, Smokeguard is the ideal solution, helping architects to meet the required safety regulations without compromising on design.
“Our new brochure provides architects and specifiers with easy access to the information they need and is just one example of the comprehensive technical and product support we offer to our customers.”
Available in 8 mm thicknesses and with glass pane sizes up to 2500 x 1200 mm, Smokeguard can seamlessly blend into the background of a building. Available as a complete system - supplied with the glass, slimline steel brackets and fixings - once installed it can form a channel that stretches the length of a corridor or building.
As the world’s leading independent provider of fire safety glass solutions for timber, steel and aluminium applications, Pyroguard has been helping architects to achieve safe and beautiful living and working spaces for over 35 years. With a dedicated technical team and comprehensive bank of test evidence, a range of support and resources are also readily available on its website.
For more information, and to download a free copy of the brochure, please visit: www.pyroguard.eu.
Leading glass manufacturer, TuffX, is committed to helping customers meet the market and legislative demand for greener buildings with its low-carbon glass balustrades.
Paul Higgins, Commercial Director of TuffX, explains why low-carbon building materials need to become the norm:
“Despite the fact the government seems to be to-ing and fro-ing about how we get there, the ultimate goal of achieving Net Zero by 2050 is unchanged. This means manufacturers must innovate and deliver home improvement products that lower the carbon footprint of a property, whether commercial or residential, sooner rather than later. We all need to play our part to achieve Net Zero and our low carbon glass ensures we are doing just that.
“Low carbon glass balustrades are particularly useful because balustrades are often required in relatively large volumes, particularly in new build estates, renovations, and commercial properties. As a result, the difference in the carbon footprint between using standard glass balustrades and low-carbon glass balustrades is significant.”
Paul continues: “Specifiers are already seeking out lower carbon building material options for their commercial projects, but there is no doubt in my mind that demand among homeowners will become increasingly prevalent as we near the 2050 deadline.”
The TuffX low carbon glass balustrade looks identical to other glass balustrade products and performs in the same way but has up to 50% lower carbon content. This is because there is more glass cullet added into the mix during production. Using more recycled crushed glass in the manufacturing process reduces the carbon footprint of the product significantly because the required temperature to melt glass cullet is lower than sand.
“The market is only going to become more focussed on delivering low carbon buildings,” concludes Paul, “which is why we are pleased to be able to offer customers our low carbon glass solution sooner rather later.”
www.tuffxglass.co.uk
Winter Gardens are an ideal way of offering high-rise residents access to a contemporary, all-weather outdoor space. They also require a specific set of building materials that meet the required fire safety regulations. It’s for this reason that Pyroguard Balustrades was recently chosen for London’s Deanston Wharf development.
Deanston Wharf is a vibrant new development located on the curve of the River Thames, adjacent to the flagship River Wharf. Featuring four separate building plots, ranging from 9 to 17-storeys, Deanston Wharf will bring over 760 new homes to the local area, comprising a mixture of one, two and three-bedroom apartments; in addition to commercial space, leisure facilities and a luxury sky lounge.
Developed by Oxley Holdings and Ballymore Construction, Elite Architectural Systems was brought onto the project to design, supply and install a series of glazed winter gardens on select apartments. Winter gardens are an architectural trend that has significantly grown in popularity over recent years, formed of an enclosed, glazed and ventilated balcony. As well as offering a modern and striking external feature, winter gardens are ideal for providing residents with access to a garden space that they can enjoy year-round, helping to bring the outside in, and vice versa. They can also offer a safer alternative to balconies on high-rise residential buildings, occasionally recommended by London planning guidelines due to the increased wind speed and noise that can be experienced several stories above ground.
On the Deanston Wharf development, the winter gardens featured a glazed balcony with a folding partition, enabling
When it came to sensitively renovating the historic Northcote House into a luxury retirement complex, fire safety glass was an integral part of combining safety with the building’s impressive architecture, with Pyroguard Infinity the ideal solution.
residents to open up the space in the warm, sunnier months and then close it up during winter.
Speaking on the project, Noel Gilmartin, Operations Manager at Elite Architectural Systems, said: “Due to the high-rise setting, fire safety glass was a critical requirement for the construction of the glazed balcony space. Knowing that Pyroguard was one of few manufacturers to have a fire-rated glass solution that met the amended building regulations, we came to the conclusion with Q-Railing that Pyroguard Balustrades was the perfect product for this project.”
Pyroguard Balustrades is a range of laminated fire safety glass, developed specifically for use in balustrade applications over 11 metres when installed as part of a certified system. Manufactured to Reaction to Fire classification A2-s1, d0 (according to BS EN13501), Pyroguard Balustrades also offers excellent light transmission and is certified to 1B1 impact resistance rating (according to EN12600).
Noel continued: “Working with Pyroguard on the Deanston Wharf project was a great success, especially with regards to the technical support they offered. Given the stringent fire safety regulations and the emphasis on traceability, we had to supply our client with comprehensive datasheets, test evidence and certifications. Thanks to the support from Pyroguard and Q-Railing, we were able to deliver all of this to the client, smoothly and efficiently.”
Elite Architectural Systems has successfully installed over 80 winter gardens on site, with the overall Deanston Wharf development expected to be completed by December 2023.
For more information, please visit: www.pyroguard.eu.
Sunningdale Park is one of Audley’s latest luxury retirement villages, set in the village of Sunningdale. With acres of gardens, lakes and natural woodland, the village features 103 one, two and threebedroom apartments. At the centre of the development is Northcote House, a Grade II listed Neo-Georgian mansion, which was sympathetically restored as part of the works to offer residents various facilities, including a library, restaurant and bar, swimming pool and luxury health club.
Alongside main contractor Zenith Ltd and architect Gaunt Francis, Optima Systems created a bright and beautiful atrium that looks over the central lobby and bar area, bringing natural light to the historic heart of Northcote House.
In order to meet the required safety regulations for the atrium application, Pyroguard Infinity fire safety glass was installed in Optima’s Technishield 70 fire-rated screens for partitions around the striking first-floor gallery, delivering EI60 (Integrity and Insulation) protection.
Andy Lake, UK & IRE Sales Director at Pyroguard said: “It was great to work with Optima on this project, with our Pyroguard Infinity glass the ideal solution, helping to combine ‘wow factor’ architecture with fire safety. Certified for butt-joint applications and corner solutions, no intermediate vertical profiles were required, meaning we could deliver the desired sleek, contemporary look that complemented the grand history and design of the interior space.”
Delivering EI fire protection, Pyroguard Infinity also offers 1B1 impact classification according to EN 12600:2002 and excellent light transmission.
For more information, please visit: www.pyroguard.eu.
Each month our special correspondent Danny Williams* replies to a reader’s letter...
“Everest has gone bust: coupled with Safestyle going under, if the bestknown name in the market has gone to the wall, what sort of effect will that have on the reputation of the whole industry?”
JH, Greater London
Absolutely nothing JH, don’t worry yourself.
From our brief chat I note that you are a man of a certain age, able to remember Ted Moult’s insistence that we should ‘Fit the Best, Fit Everest’. But those of us that remember his sage advice, are a dying breed, many literally, with Ted himself turning up his toes nearly 40 years ago! And to my mind thereby hangs the tale. Everest, even by the time of its first crash in 2020, was a shadow of its former self.
We should remain grateful to Everest however, because it and its primary retail competitor Anglian, whilst presenting two powerful adversaries in the market spent millions on what was, in the early decades at least, highly effective marketing and memorable advertising, that literally grew the size of the cake for the rest of us. When I was running double glazing operations in the ‘Eighties, I followed their vans around and picked off the neighbours of the houses being installed, knowing that we could undercut whatever those two were charging next door.
So powerful were their marketing machines and the volumes of leads that they and their canvassers generated, they could never sweep up every enquiry. I was happy to catch the drips, especially from Everest, who charged huge sums for what were mediocre products. Back in the day, they were damned good.
But that was a long time ago. And whilst Anglian is itself sweeping up leads and orders from the debris left by Everest and Safestyle, that’s all it is: debris. Ask anyone if they remember any of Everest’s more recent campaigns and the younger members of our society won’t be able to tell you, whilst the oldies will still hark back to Ted and one of the advertising industry’s greatest ever campaigns. For some time now our broader industry has become significantly smarter and more
SIEGENIA is proud to have made the final shortlist for 6 National Fenestration Awards this year. The company is up for the prestigious Hardware Company Of The Year award, while three new products have also made category shortlists. Their PORTAL ECO SLIDE CO sliding window and door hardware is up for New Product 2024, the concealed axxent door hinge for Door Component Of The Year, and the smart window handle for Window Component Of The Year.
with customers and provides technical advice and support daily not just to external partners but to internal sales staff as well.
SIEGENIA’s Busines Support Manager, Claire Wainwright, said, “We are extremely proud that people have taken the time to vote for us and our colleagues and to make the final list in so many categories. Chantelle and Matt are extremely deserving finalists and demonstrate the high level of customer service and product knowledge that we strive for across the company.
professional, with even small operators running smart social media and digital marketing campaigns. And whilst we still have our fair share of clowns running around cocking up the most basic installations, I do believe that in broad terms, you have to look increasingly hard to find a badly made window.
In short, we have long moved out of the shadow of these giants, doing our own thing and doing it, generally, remarkably well. And not only do I not believe that the loss of these once great brands will have any negative effect on the market, I believe we will all benefit because there will, quite literally, be more for the rest of us, and with brighter prospects on the horizon too.
In fact my good friend Ryan Johnson, he of Emplas fame, made such assertions recently in this very publication. Whilst the market has been, says Ryan, down from beween 10 to 16%, a figure that I would say is a little on the conservative side, Ryan rightly suggests that these figures are hardly catastrophic, ‘…but for those companies that haven’t invested…’.
Ryan points to a number of factors that suggest that if we are not exactly emerging from the swamp, the alligators are less likely to bite us. Might we be on the brink of an upturn he asks? I would say so.
House prices are up, and construction is moving in the right direction, if by small percentages. Add in that inflation is coming down and with it the hint by the Bank of England that if it remains on the downward trajectory, then interest rate cuts will follow. Still looming of course is the question of which idiot-government will replace the current idiot-government, and when that is decided, after a few weeks to settle, I believe we will all be back in business.
All except Everest, Safestyle and a few others of course. Their loss is our gain JH.
* Danny Williams is managing director of Chelmsford based Pioneer Trading and has been involved with all aspects of the windows and doors industry for 35 years. His activities include manufacturing a full range of windows and doors in PVC-U and aluminium, an IGU facility, retailing and commercial contracting.
Two individual staff members have also achieved finalist status. Customer Service Administrator Chantelle Shipley has been nominated for Customer Service/ Operations Person Of The Year, while Technical Assistant Matthew Hayes is up for Young Person of the Year. Both colleagues are vital members of the SIEGENIA UK team and work on the front line dealing with business partners and customers daily.
Chantelle has been with SIEGENIA for 6 years and has built great relationships both internally and externally, working diligently to deliver for customers even during times of supply shortage which were felt industry wide. Matthew joined SIEGENIA in 2022 as a trainee in the technical department and picked up the product knowledge and technical skills extremely quickly. Still only 23, he has already led a number of site visits
“The recognition of our new products is also a reflection of the emphasis that SIEGENIA has placed on innovation and product development over recent times and shown on our FENSTERBAU stand. This continues to be a priority for us, with more new products due to launch later this year and into next.”
Winners for all categories are selected by a public vote via the National Fenestration Awards website and voting is now live until 20th September at 5pm. The winners will be announced at the awards ceremony at Doncaster Racecourse on 26th October. Tel: +4424 7662 2000 – www.siegenia.com
Sheerline is delighted to announce it is a finalist in nine categories for this year’s National Fenestration Awards. Being finalists in so many categories is testimony to how busy the last year has been for the company, from strengthening internal communications to launching a host of new products.
As well as being nominated for Aluminium Systems Company of the Year and Systems Company of the Year, three members of the team have nominations, including CEO Roger Hartshorn for Director/Managing Director of the Year.
Unveiled at the FIT Show 2023, two of Sheerline’s newest innovations are also up for awards. SheerVent® – a revolutionary approach to intelligent roof lantern ventilation combining practical features with the
company’s signature sleek styling and S2, which offers a fresh approach to glazed conservatory roof systems. Built on the foundations of the K2, the S2 has been updated for a contemporary audience while also tackling issues such as thermal efficiency and leak-proof ventilation.
S2 is in the running for Conservatory Product of the Year, which shows how popular it has become in a short period and that there is room for new and innovative products. In addition, the company has been nominated for Best Use of Video and Colour Specialists of the Year.
Roger Hartshorn, Sheerline CEO, commented: “Being nominated in nine award categories is brilliant! It’s a testament to the hard work and commitment of everyone at Sheerline and shows what you can achieve with strategic vision, the right investment, and the right people.”
“Good luck to everyone who has been shortlisted. We’re looking forward to the awards night,” he added.
View the full list of finalists and vote for Sheerline here: https://www.fenestrationawards.co.uk/nfa24
Premium window and door designer,
The Residence Collection and Window Widgets, has been named as a finalist in five categories at one of the most recognised fenestration industry awards.
Founded more than a decade ago, The National Fenestration Awards has been recognising individuals and businesses in the fenestration industry for their outstanding work.
The awards is an independent and allinclusive event, where industry professionals act as judges and decide the best-in-class across 35 categories through a voting system.
The Residence Collection has been shortlisted for four awards: Best Use of Video, Digital Marketing Campaign of the Year: PVCu Systems Company of the Year and Timber Alternative of the Year.
Window Widgets’ product, Werbar, has been nominated for the Window Component of the Year category.
Last year marked the sixth time The Residence Collection won the Timber Alternative Company of the Year award since The National Fenestration Awards launched in 2013.
This achievement underscores their versatile range of styles offered throughout three collections: R9, R7, R², which blend
conventional values with contemporary techniques to thoughtfully enhance various types of properties. Boasting a palette of 26 colour options, including dual-colour selections, alongside a bespoke hardware range, The Residence Collection’s designs align seamlessly with modern interior trends, while accentuating the timeless aesthetics of period properties.
Jo Trotman, Marketing Manager at The Residence Collection and Window Widgets commented: “We’re really proud to see The Residence Collection and Window Widgets named as finalists for five outstanding categories in the National Fenestration Awards this year.
“We’ve worked hard this year to diversify our efforts with The Residence Collection and Window Widgets brands to ensure installers and fabricators alike are continually trusting us as their go-to companies for premium windows and ancillary products.
“There are lots of deserving finalists in all categories of the awards this year and we look forward to the ceremony in October.”
To find out more about The Residence Collection, please visit https://www.residencecollection.co.uk/ or for Window Widgets visit https://www.windowwidgets.co.uk/
Summer 2024 Digital Edition will be in your inboxes by now! To book Autumn 2024 Digital –deadline date is 1st August. To book the Print Edition (out in September) – deadline date is 19th July. Digital or print, the choice is yours!
Leading glazing component manufacturer Glazpart was delighted at the announcement from the National Fenestration Awards (NFA) 2024 that Glazpart products, initiatives and employees have been shortlisted for a total of six awards.
The award nominations include:
• Component of the Year: The Link Vent product
• Customer Service / Operations Person of the Year: Linda Lewis (Customer Relations Co-ordinator)
• Office Manager of the Year: Belinda White (Customer Relations Manager)
• Social Networker of the Year: James Lee (Marketing Consultant)
• Digital Marketing Campaign of the Year: Glazpartners (customer support programme)
• Best BDM/Sales Executive of the Year: Andy Lobban (Sales Manager, Fenestration Products)
On receiving the news, Dean Bradley, Glazpart Sales Director, commented, “All at Glazpart are thrilled with the news of these nominations which recognises and rewards the best of the fenestration industry.”
The National Fenestration Awards are the industry’s fastest growing and most inclusive awards event. Launched in 2013 and now into its 11th campaign, the National Fenestration Awards are decided completely by the participation of the industry. All in the industry are invited to vote on their choice of deserving winner.
To cast your vote in this unique competition, please visit the NFA website voting page here: https://www.fenestrationawards.co.uk/nfa24/.
Dean Bradley added, “We are very excited at being finalists in six categories and we encourage all our customers and colleagues to vote for Glazpart. We look forward to the awards event later in the year. In the meantime, best of luck to all those shortlisted.”
The winners will be announced at the awards ceremony on Saturday 24 October at the London Hilton Garden Inn at Doncaster Racecourse. To book tickets for this event please visit the NFA events page here: https://www.fenestrationawards.co.uk/ winners-event/
www.glazpart.com
Experience superior performance, energy efficiency, and security with the new Regal Bifold Plus door from Regal Aluminium.
Superior slimline aesthetics
Pre-gasketed, knock-in beads for quick fitting
Excellent thermal and acoustic performance
Glazing capacity up to 48mm
Slim central section of 100mm, maximising the glazed area
Can accommodate up to 14 sashes
Customisable options
PAS 24 approved
Choice of powder coating finishes
Seven-day turnaround from order confirmation
To discover how the new Regal Bifold Plus Door from Regal Aluminium can add value to your portfolio call 01773 483090
sales@regaluk.co.uk
www.regalaluminium.uk
Fill
your answer and your contact details below and send your competition entry to: FAO:
Close,
in your answer and your contact details below and send your competition entry to: FAO: Christina Lazenby, Glass News Competitions, 19 Heather Close, Tickhill, Doncaster, DN11 9UU or Email: christina@glassnews.co.uk. Entry deadline: 20/06/24.
Connaught
Structural
Quick
Professional
Free
Training
7
British Plastics Federation (BPF)
Tel: 0207 457 5000
British Standards Institution (BSI)
– Standards & Publications
Tel: 0208 996 9001
BSI – Assessment & Certification
Tel: 0845 080 9000
BSI – Product Certification & Testing
Tel: 08450 765600
BBSA (British Blind & Shutter Association)
Tel: 01449 780444
Building Research Establishment (BRE)
Tel: 01923 664000
Council for Aluminium in Building (CAB)
Tel: 01453 828851
Dekura
Tel: 01952 201631
Door & Hardware Federation (DHF)
Tel: 01827 52337
Double Glazing & Conservatory Ombudsman Scheme (DGCOS)
Tel: 0345 053 8975
Fenestration Self-Assessment Scheme (FENSA)
Tel: 0207 645 3700
Get Britain Building (GBB)
Tel: 0870 162 0936
Glass & Glazing Federation (GGF)
Tel: 0207 939 9101
GQA Qualifications (formerly Glass Qualifications Authority)
Tel: 0114 2720033
christina@improve-magazine.co.uk www.improve-magazine.co.uk
Health & Safety Executive (HSE)
– Glass & Related Industries
Phil Smith, HM Principal Inspector
Tel: 01782 602300
David Appleton, HM Inspector
Tel: 0115 9712800
Proskills – Head Office
Tel: 01235 833844
Proskills – Glass & Related Industries
Neil Robinson Tel: 07917 015 322
Recovinyl (via Axion Consulting)
Tel: 0161 355 7618
The Glazing Ombudsman (TGO)
Tel: 020 7397 7200
UK Green Building Council
Tel: 0207 580 0623
Veka Recycling
Tel: 01322 38721
Waste & Resources Action Programme (WRAP)
Tel: 01295 819 900
Wood Window Alliance (WWA)
Tel: 0844 209 261
Maintenance-free PVCu fascia boards are 20mm thick (instead of the usual 16mm) for superb strength.
Not
Distribution
Improve is distributed as follows:
•
•
•
•
•
Summer 2024 Digital Edition will be in your inboxes by now! To book Autumn 2024 Digital –deadline date is 1st August. To book the Print Edition (out in September) – deadline date is 19th July. Digital or print, the choice is yours!
Improve is distributed as follows:
• 30,000
We’ve featured TV legend Kevin McCloud, gardening gurus’ David Domoney and Huw Richards as well as a double act from George Clarke & Max McCurdo, not to mention interior designer to the stars Kelly Hoppen and master of the home makeover Georgina Burnett and Laurence Llewelyn Bowen! To mention a few!
Every Edition contains expert advice from people within the fenestration and surrounding industries, to ensure our readers are not only entertained but also kept informed of subjects such as planning permissions, building regulations and the latest trends and style.
Facebook users per quarter
• We target homeowners/gardeners and people interested in DIY (age 27 - 65+)
Forget Google, old customer lists, or even directories. Insight Data is the industry’s most powerful business device.
With access over 80,000 key decision-maker contacts and verified email addresses, transform your sales and marketing strategy and make sure your business stays ahead of the competition.
To find and win new customers, just ask Insight.
DATABASE OVER 20,800 CONTACTS
LOCAL BUILDERS DATABASE OVER 27,300 CONTACTS
DATABASE OVER 18,200 CONTACTS BUILDERS MERCHANTS DATABASE OVER 10,800 CONTACTS
MAIN CONTRACTORS DATABASE OVER 6,500 CONTACTS