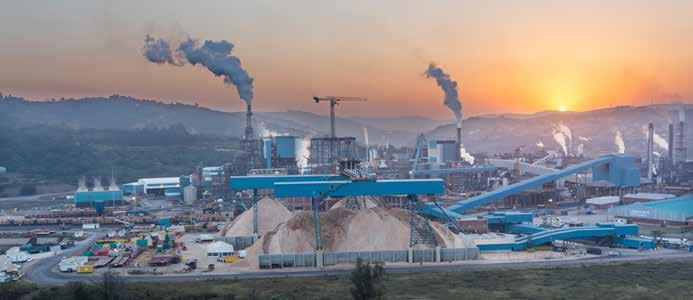
2 minute read
SiVEST SA – Sappi Saiccor Mill – Woodyard Upgrade, Umkomaas
SiVEST SA for Sappi Saiccor Mill – Woodyard Upgrade, Umkomaas
PROJECT TEAM Client: Sappi Saiccor Mill Owner’s engineer: SiVEST SA
Advertisement
In 2018, Sappi Saiccor Mill decided to increase production volumes from 783 000 air dry tonnes per annum (adt/a) to 890 000 adt/a through various expansion project investments throughout the mill. In line with the vision, Sappi Saiccor upgraded equipment in the woodyard, chemical and recovery areas, fibre line and the uptake machine.
Project Vulindlela was approved in principle, enabling a planned phased construction completion in July 2020. In order to make space for Project Vulindlela, the entire woodyard at the Sappi Saiccor Mill needed to be rearranged.
This involved the decommissioning of two of the existing chipping lines and stockpile area, and the installation of a new 300 t/h chipper to replace the decommissioned capacity. A new completely automated woodchip stockpile system had to be erected in the area previously used as a timber stockpile area.
The rail system required a complete redesign to enable the offloading of timber directly to the new chipper and existing chipper No. 6. This project, titled the Woodyard Upgrade Project, preceded the start of the Vulindlela Project and was completed in April 2019.
The woodyard included various new equipment installations, which required design and engineering across the various engineering and construction and related disciplines. Sappi Saiccor required an owner’s engineer to perform the services
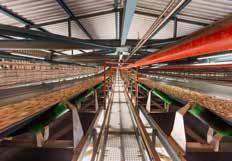

to assist Sappi Saiccor’s internal project management team, by carrying out the design, engineering, technical adjudication, technical construction support, and commissioning support of the project.
SiVEST was appointed to provide design, engineering and management advisory support services for the civil, structural, mechanical, electrical, controls, instrumentation, scheduling, and draughting works required in the woodyard area.
The key challenges included the congested operation and project interface,
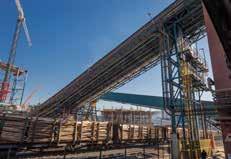
as well as the limited space on-site for new development. SiVEST’s use of advanced 3D scanning technology and 3D modelling enabled the accurate design of the new project’s interface to the existing factory infrastructure. Through detailed planning, a proactive approach and close collaboration, the SiVEST team was able to complete the works with very little disruption to Sappi’s operations.
The project commenced in August 2017 and was successfully completed and handed over to the client in April 2019 in line with Sappi Saiccor's requirements.