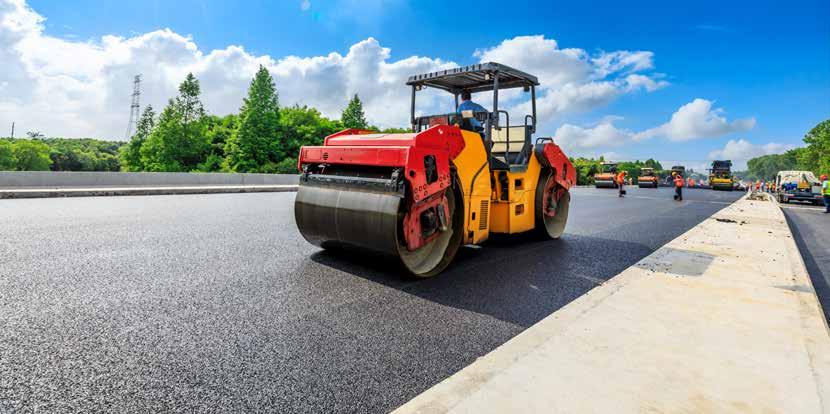
9 minute read
Implementation of PG binder specification in South Africa
from IMIESA August 2021
by 3S Media
The publication of the SATS 3208 technical specification for a performance-grade (PG) binder specification in South Africa coincided with CAPSA 2019. This milestone has its roots in CAPSA ’15, following a master class sponsored by Sabita, whereby John D’Angelo introduced the principles of a performance-based binder specification to a wider audience of practitioners. By Steph Bredenhann*
Advertisement
The purpose of the SATS 3208 was to provide a path towards complete acceptance of the PG specification and a path to a full SANS 4001 specification. The objective is to use SATS 3208 in parallel with the SANS 4001 specifications.
As only one specification can be in force at a time, it is necessary to specify which one is applicable on a contract. Since CAPSA, some authorities decided to implement SATS 3208 as the specification on a per-project basis and test according to SANS 4001 simultaneously. In this article, the PG implementation so far will be discussed and pertinent issues that have arisen will be highlighted.
PG specification in a nutshell
The purpose of this article is not to describe the PG specification in detail; it is to address implementation aspects that require attention. A summary of the most important points contained in the SATS 3208 specification is shown in Table 1. The PG specification was discussed in detail by Bredenhann et al. in the September 2019 issue of the SAICE Journal 1 .
A PG specification is a purchase specification that allows for the selection of a binder that can be expected to perform well in an asphalt mix or spray seal application. The real test for performance will always be the asphalt mix itself; the mere choice of a binder will not guarantee performance.
The PG specification is an improvement on the current penetration-grade specification in that environment, traffic and ageing are considered.
Definitions for Tmax and Tmin are given in Table 1 and the question is often raised why the UTI (useful temperature interval) of 80°C must be maintained. Minimum temperatures of -22°C are not experienced in South Africa. The lowest temperature is in the region of -6°C in a remote area where traffic is light at best. The choice of UTI = 80°C was introduced to bring the intermediate temperature, TIT, in line with the temperatures where fatigue is experienced. Researchers had noted that the pavement temperature associated with fatigue was somewhat higher than the MAAT (mean annual air temperature) and +4°C was seen as a reasonable estimate. TIT is calculated as (Tmax + Tmin)/2 + 4°C = 22°C for a PG58-22 binder.
Selecting specification criteria to ensure satisfactory resistance to fatigue cracking is a difficult challenge. The larger part of South Africa falls in the PG58 high-temperature zone, including the highly trafficked roads of southern Gauteng, up the southern coastline from Cape Town to Durban. The 22°C intermediate temperature is, compared to experience in the USA and Europe, a very reasonable temperature for fatigue criteria in this area. The ΔTc ≥ -5°C requirement addresses the fatigue to a certain extent, but no specific criteria are included in SATS 3208. However, it is required that an isotherm at TIT is reported to allow for further analysis and research into fatigue and durability. This is perhaps the research area that is the most important and hopefully the universities will respond.
The first step in specifying an appropriate binder is to define the environment and traffic level for the operating region where the binder will be used. The environment is defined by the maximum and minimum pavement temperatures and the traffic level by the equivalent number of 80 kN axles and traffic speed.
Test methods in the SATS 3208 specification are performed according to the ASTM standard specification series.
An example: traffic load is 40 million E80axles, traffic speed on the design section is 80 km/h in Cape Town, thus the PG grade is PG58V-22 and PG58E-22 on inclines where truck speeds will drop below 80 km/h.
PG BINDER-GRADES
PG58-22, PG64-16, PG70-10 TRAFFIC CLASSES
S = Standard H = High V = Very high E = Extreme
Tmax for asphalt is based on the 97.5% confidence level of the average seven-day (consecutive) temperature at a depth of 20 mm. Tmin is the minimum surface temperature, but UTI≥80°C (Tmin – Tmax) must be maintained.
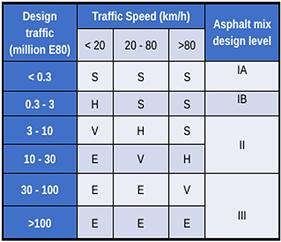

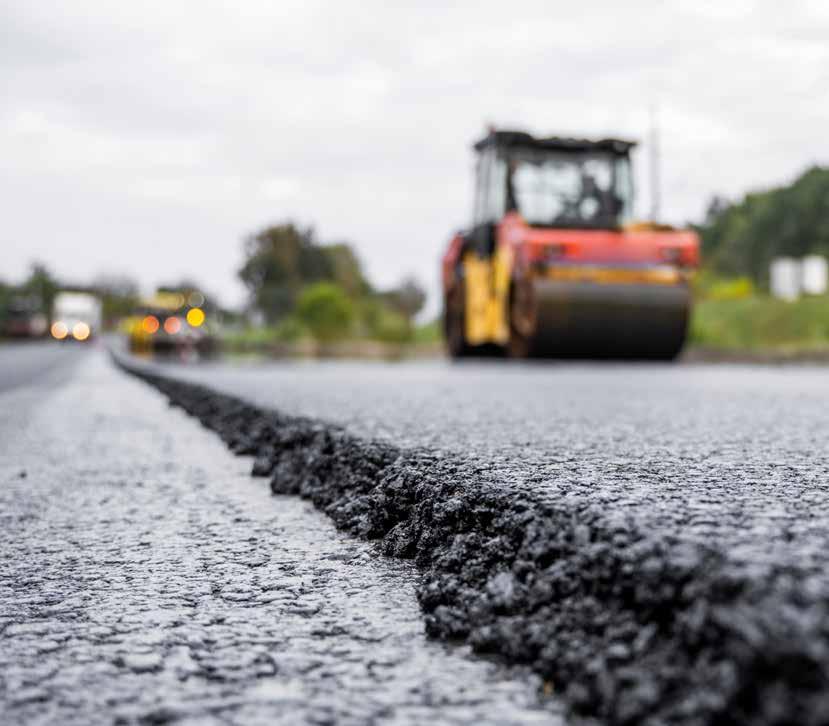
Equivalent grades: Penetration vs PG
Laboratory tests have shown that PG grades of currently available South African bitumen are as shown in Table 2. It should be noted that equivalent grades may differ between refineries and the designer must establish the PG grade with proper testing according to SATS 3208. The values in Table 1 are only given as a guideline.
Continuous grading
The continuous grading of a binder, also
TABLE 2 Equivalent penetration and PG grades
SANS 4001: BT1 SATS 3208
10/20 PG76-10 35/50 PG64-16 50/70 PG64-16 700/100 PG58-22
referred to as the ‘true grade’ of a binder, is the maximum and minimum temperatures where the PG specification requirement is met. The continuous grades are determined according to ASTM D7643 and ASTM D6816. South African PG requirements to be used are: • Tmax is the temperature where Jnr = 4.5, the requirement for S-class traffic. • Tmin is the maximum of the temperatures where S (60) = 300 MPa and m (60) = 0.3. A word of warning: software included in the DSR will report a continuous grade based on G*/sin δ = 2.5 (Tmax) and G*sin δ = 4 500 (Tmin). These are old USA specifications that are not included in the South African PG specification.

Project specifications and special needs
The PG specification requirements as set out in SATS 3208 are general and applicable to all binders, as the specification is intended to be binder blind – i.e. performance requirements to be met are specified and the binder supplier must manufacture a product that will meet those requirements. The straightforward method to incorporate the PG specification into the project specification (PS) is to include a clause that SATS 3208 will be the binder specification applied on the project. As it is still the implementation phase, one should also specify that all tests required by the applicable SANS 4001 specification must be included as compulsory items.
Practices such as ‘overspecification’ must be guarded against, but a designer, either based on their own experience or on the preference of the client, may want to specify that a certain modifier must be used – e.g. bitumen rubber. This can be achieved by adding an acronym, CRM (for crumb rubber modified), to the specification – e.g. PG58V-22(CRM). A similar approach can be taken to ensure that a binder is modified with a polymeric modifier – e.g. PG58H-22(PMB). The designer must always endeavour to keep things as simple as possible. In South Africa, we have the A-E1 and A-E2 binder grades. One should not try to go further than just PMB (polymer modified bitumen) for a polymer modified binder. The manufacturer must be allowed to offer a product for the circumstance required and the difference in binder content between an A-E1 and A-E2 is not significant.
Statistics show that more than half of the asphalt manufactured in Gauteng is still straight bitumen, unmodified. It was never the intention of implementing the PG standard to create a proliferation of modified binder grades. Neither was it the intention to favour modified binders over a straight bitumen that performed well over many years.
Special clauses in the PS
It is known that some polymer-modified binders as well as bitumen rubber (manufactured with neat bitumen from some refineries) do not meet the ΔTc ≥ -5°C requirement. In South Africa, it seems that such binders are still soft enough to have good fatigue performance, so it would be beneficial to retain these binders in the mix. This is where the designer needs some specialist knowledge and to apply themselves. There are more parameters that can be used to assess binder performance, such as the Glover-Rowe (G-R) parameter. The G-R parameter is calculated as G*(Cos δ)2/Sin δ and it was shown that at G-R = 180 kPa the potential for the onset of cracking is indicated. A possible specification requirement can then be that a relaxation of ΔTc ≥ -7°C is allowed, provided that G-R ≤ 180 kPa.
In the MSCR test, more than the Jnr is reported – e.g. the %R (recovery, known from the Jnr report SATS 3208, Table 3). %R is not a requirement in SATS 3208 but can be included in the PS to ensure modification; a %R greater than or equal to 30% is a good choice.
A further requisite clause is to specify a 10/20 penetration bitumen (for use in EME). In PG terms, two requirements must be added in the PS: • G*/Sin δ greater than or equal to 4 kPa, measured at temperature Tmax and rotational frequency ω = 10 radians/sec • %R as determined by the MSCR method of less than or equal to 10%. The G*/Sin δ ≥ 4 kPa is determined from laboratory tests and relates to penetration and softening-point values of the bitumen. The designer must confirm this limit with bitumen in their own area. The %R requirement is to ensure that no modifier is present in the bitumen. Initiative and out-of-the-box thinking are certainly encouraged.
How to handle penetration-grade bitumen in EME
A 10/20 penetration-grade bitumen will most likely have a PG76-10 continuous grading, but let us investigate 10/20 to be used in an EME for the above example where a PG58V-22 binder is required. The first reaction would be to specify a PG58V-10 as in the area a Tmin of -10°C is most probably safe. But the TIT will now be 28°C and this is too high to assess fatigue resistance.
The design engineer should assess the fatigue-resistant properties of the 10/20 bitumen and the EME mix. EME is used in a base course with a wearing course. If the wearing course is of adequate thickness, the effective maximum temperature in the EME will be lower – reducing strain in the pavement. That will assist with fatigue resistance.
The relaxation properties of the bitumen must be assessed. The m(60) will be a good indication. However, with the higher binder content of the EME, fatigue resistance is increased. The message should be clear: do not just accept that PG grades can be adjusted to suit the situation. The consequences of the changes should be considered carefully.
Reference:
Bredenhann, Myburgh, Jenkins, O’Connell, Rowe and D’Angelo (2019. ‘Implementation of a performance-grade binder specification in South Africa’. SAICE Journal of Civil Engineering, Vol 61, No 3, pp 20-31.
Acknowledgement:
Dr Geoffrey Rowe and Dr John D’Angelo, both from the USA, were consulted on some discussion points, thus their kind assistance as friends of South Africa is acknowledged herewith.
*Steph Bredenhann is a principal specialist at Naidu Consulting.