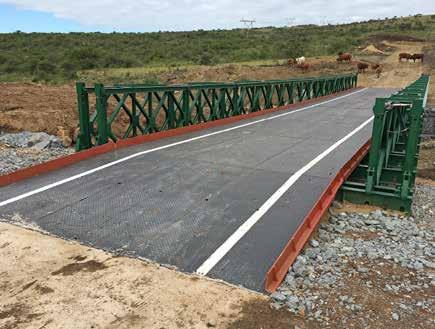
5 minute read
Closing the gap
from IMIESA August 2021
by 3S Media
Developed for deployment by military engineers during the Second World War, the modular steel-truss Bailey bridge (commonly known as the Type 100) was a highly successful invention. Through ongoing refinement by modernday manufacturers, this versatile solution for temporary pedestrian and vehicle crossings is still in use worldwide, including South Africa.
By Alastair Currie
Advertisement
Locally, BSE Engineering Group has been spearheading the widespread application of its rendition of the Type 100, delivering on key projects.
These include the manufacture and supply of bridge kits for joint Department of Public Works and Infrastructure (DPWI) and Department of
Defence and Military Veterans initiatives.
One of the most recent is the Welisizwe
Rural Bridges Programme, which was gazetted as a Strategic Integrated Project in July 2020.
This national programme serves as a disaster management response, as well as a vital link for communities, particularly schoolchildren, to reach nearby education facilities without being impeded by rivers and floods.
These single-lane bridges are being installed by South African National Defence Force (SANDF) personnel working alongside communities employed as part of the Expanded Public Works Programme (EPWP). Current projects are focused on the KwaZuluNatal (KZN) region, with the KZN Department of Transport having allocated funds for 14 bridge installations across the province.
Entering the market
Leveraging off its expertise as a specialist steel fabricator, BSE identified a gap in the market for Type 100 bridges around 2006 – a year in which an especially severe series of floods hit South Africa.
“We were also aware that there was a stockpile of Bailey bridge sections sitting in SANDF storage,” explains Elliot Marcinko, CEO at BSE. A series of discussions subsequently led to BSE being awarded an open tender to refurbish older components and start manufacturing new Type 100 units. At the time, these were mainly for projects in the Eastern Cape region.
“We subsequently won further tenders, including the fabrication and supply of all 14 bridges for the Welisizwe Rural Bridges Programme in KZN,” Marcinko continues, adding that BSE provides on-site training, logistical support, and advice on bridge abutment solutions. The latter are constructed using either gabions and gabion mattresses or reinforced concrete. Gabion systems are preferred because they can mostly be filled with readily available local materials by community-based labour.
Speed of construction is a major advantage compared to alterative building systems like cast-in-situ or precast concrete. Type 100 bridges are also arguably more pricecompetitive, when considering time and costs.
The bridge is supported on either side by gabion abutments A completed Type 100 bridge
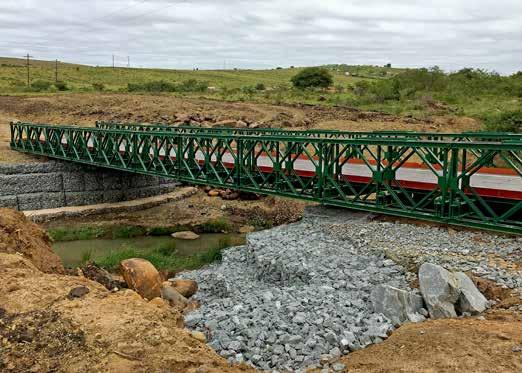
Incremental launch
Depending on the technical terrain challenges on-site, these modular steel bridges can be installed within a few days or weeks by a small team. All the components bolt together, making assembly and future disassembly straightforward.
“Although a complete bridge could be placed on its abutments in one go using a crane, this is not practical given the remote location
Preparation works in progress
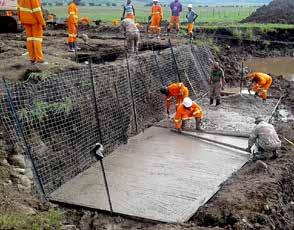
Finishing touches
Incremental launch of these sites. So, the preferred method is to incrementally launch the bridge over the river or gulley, generally without the need for scaffolding,” Marcinko explains. “Another plus is that, if a bit of extra length is required, a further extension can be bolted on.”


Research and development
While the Type 100 design has been around in minor modified formats for around 80 years, the steel used to construct them has evolved significantly since the 1940s. New steel derivatives are now stronger, which means that they can support higher live loads over shorter distances.
BSE’s single-lane bridges are typically up to 35 m in length and designed to support a 10 t live load. Bridges can also support services, like a pipeline running underneath the structure.
“Our R&D team is in the process of developing a new prototype, which we’ve coined the Type 200 bridge,” says Marcinko, adding that the Type 200 design is a joint effort between BSE and the SANDF. “The SANDF’s in-field feedback on practical design improvements is invaluable.”
On a Type 100 design, a double-sided panel is required on each side of the bridge. For the Type 200, however, only single panels will be needed on either side. In both cases, the bridge deck is composed of steel sheeting resting on a girder frame. Bridges can be galvanised to optimise the lifespan of the steel. Alternatively, a protective paint coating can be applied. The overall design can also incorporate solar-powered illumination.
Long-term durability
To determine the performance of their installations since 2009, BSE recently awarded a bursary to a Wits University PhD student to research the environmental impact and sustainability of its bridges.
“From our own observations, our first bridges in the Eastern Cape have stood the test of time well. It’s also heart-warming to see how these structures have enabled socioeconomic development,” Marcinko continues. “When most of these bridges were installed, there was no evidence of local habitation or development. Now the opposite is true, with structures such as hospitals, schools and commercial developments springing up.”
This year, BSE was tasked with developing a dedicated pedestrian-type bridge. The company’s R&D team is also working on what will be its most challenging project to date. This entails the design of a Type 200 structure to cross an 80 m gap in St Lucia, KZN. At this stage, the provisional design calls for two support pillars.
“While these modular bridges are primarily intended as a temporary measure, many could well become more permanent fixtures. This was underscored during a recent road trip to Malawi in 2015 where we crossed over functional Bailey bridges installed many decades ago,” adds Marcinko.
“Across South Africa and Africa, the potential for these bridges runs well into the thousands and we’re proud to be playing our part in delivering a 100% locally designed solution, which connects communities with the mainstream economy,” Marcinko concludes.
South Africa
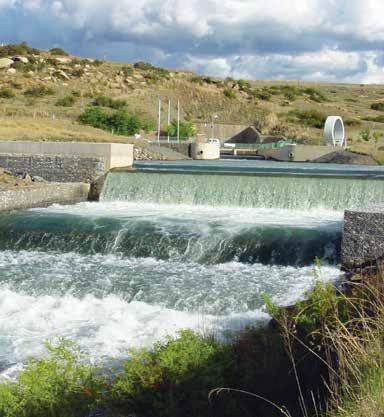