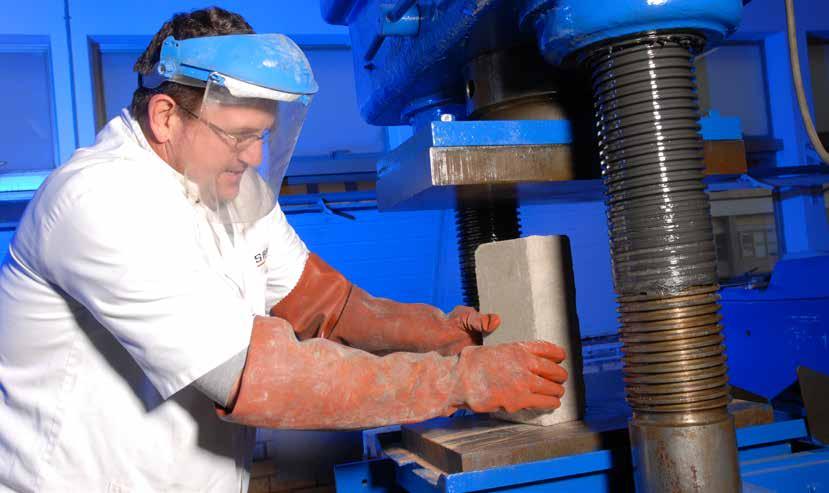
6 minute read
Thought Leadership
from IMIESA July 2020
by 3S Media
South Africa’s quality gatekeeper
The South African Bureau of Standards (SABS) is being remodelled and realigned. Alastair Currie speaks to Jodi Scholtz, lead administrator, SABS, about the key steps being
Advertisement
management, the SABS has successfully are many opportunities for a change in direction.
taken to bring the organisation What are the key
elements of the SABS’s
back on track following turnaround strategy? a period of sustained Dr Rob Davies, the former Minister of Trade and Industry, cited various financial losses. governance and performance issues, which subsequently led to the SABS being placed under administration. This process began in July 2018 and, from the How does the SABS rank against other Stabilise, Fix and Chart a New Course. international standards bodies? We’ve reached the stabilisation JS The SABS celebrates its 75th anniversary stage, which has entailed undertaking in September 2020 and remains a respected a comprehensive organisational review brand worldwide. Internationally, there to ensure a fit-for-purpose SABS. As we are two standards bodies – namely emerge out of Covid-19, we’re going to need the International Organisation for different types of skill sets. Standardisation (ISO) and the International Traditionally, the SABS received around Electro-Technical Commission (IEC). The 30% of its funding from the Department of SABS is a member of both. In fact, the SABS Trade, Industry & Competition (DTIC). The is a founding member of ISO. balance was sourced via our conformity
We also play a pivotal role on the African assessment services. This DTIC funding has continent. For example, we are affiliated to now been reduced even further, which the African Organisation for Standardisation, means that the SABS must rethink and and the African Electro-Technical reposition itself to remain commercially Standardisation Commission. viable. For this reason, we’re engaging
In terms of reputation and brand extensively with our external stakeholders. beginning, we had a three-pronged strategy: evolved through many testing years of What assurances are in place for clients? technological change. With Covid-19, there Concrete steps so far include major investments in our laboratory testing infrastructure, which is the backbone of our technical capability. We’ve made infrastructure investments in the humidity chamber for fibre and polymers, the rubber and plastics laboratories, in the pharmaceutical chemistry laboratory, as well as in the chromatographic services laboratory, to name but a few of the investments that have been made.
We’re also shifting the organisation towards a more sector-focused approach. Once you have a sector focus, you’re able to deepen the technical know-how, skills and understanding within a specific industry. Standards are developed from an industry perspective, so maintaining a win-win partnership is essential. Tertiary institutions must also be part of the process.

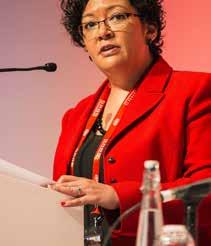
Jodi Scholtz, lead administrator, SABS
There have been some missed opportunities in the past. We are now committed to providing shared value. For example, there have been issues raised concerning the affordability of our testing services. In response, we recently reviewed our pricing strategy to make us more cost-competitive against other local and international standards bodies.
For the public at large, the SABS mark is about providing quality assurance: that products have been manufactured and tested according to strict criteria. Carrying the SABS mark, also known as ‘SABS Approved’, is a hallmark that most people still ask for by name.
How can the SABS help to promote local content and manufacturing?
Local content verification is crucial in building Brand South Africa. The SABS has been appointed to assist, with some funding provided by the DTIC. We’re also in talks with Proudly South African to explore synergies.
Companies that are producing and verifying locally should be recognised and rewarded. For example, the SABS is currently offering testing services discounts to those manufacturing PPE for Covid-19.
Where it affects public health and safety, then the South African National Standard is referenced in the compulsory specification and this then becomes compulsory for the National Regulator for Compulsory Specifications (NRCS). It is also generally a requirement for public sector tenders in terms of the Public Finance Management Act (No. 1 of 1999), and wherever stipulated by the NRCS. In all other cases, the mark is voluntary. But who would buy a product today without a widely recognised quality standard?
The SABS doesn’t have regulatory powers; however, where manufacturers abuse the SABS mark, such as through making false claims, we do engage from a legal viewpoint and issue cease and desist letters to those manufacturers. We’ve always been acknowledged for fiercely protecting our mark.
From a business perspective, all SABS Approved products are listed on our website. For instance, we currently have some 24 approved manufacturers/suppliers of medicalgrade hand sanitisers listed. For marketers, that’s a great lever when promoting their product to potential buyers.
The SABS is also aligning with sectors that the DTIC is keen to promote. That includes supporting black industrialists.
How will the SABS remain relevant?
We want to broaden our basket of services. We’re looking at using our space differently to make better use of SABS labs that are not always fully utilised. That could include partnering with SMME laboratory specialists.
During 2019, we also engaged with a number of our local and international competitors. One of the interesting things that emerged was the ideal of co-competition. There’s a definite interest in partnering with the SABS on international projects. For example, international donor funding is available to set up standards bodies in various African countries for specific industries or sectors.
The UK-based standards organisation, BSI, works across the African continent and has indicated its willingness to enter into possible partnership opportunities. It recognises the SABS’s technical skills.
Additionally, we’re forging closer relationships within SADC. These include signed agreements with the Namibian Standards Institution (NSI), as well as with the Botswana Bureau of Standards. In terms of our mutual recognition agreement with the NSI, we’re currently verifying PPE products manufactured by South African companies intended for export to Namibia.
We’re also looking at digital platforms that can help us, including the way we have already set up our internal and external

technical committees online. To further ensure relevance, we are accredited with the RVA, the Dutch accreditation agency, which conducted a virtual audit in May 2020 where one or two areas for improvement were picked up. In response, we’ve submitted our action plan as part of the reassessment process.
We’ve also reintroduced the old Customer Partial Testing offering. This enables customers to innovate parts of their product range instead of the entire process. This will help fast-track new products to market.
What is the financial outlook for the current financial year?
National Treasury recently cut the SABS’s funding for the current financial year by a further R64 million as government reallocates spending to meet Covid-19 priorities. And part of the envisaged R500 billion stimulus package had to come from existing funding.
Despite our cost-cutting efforts to date, we will be reporting a financial loss for the year ending 31 March 2020. Clearly, the economic downturn before and after Covid-19 will be compounding factors. Some 60% of our customers are SMMEs and they’ve been hit hard by the pandemic.
On a positive note, we’re making positive gains in terms of business process optimisation, reducing costs and creating new revenue streams. The DTIC remains committed and sees the SABS as part of its industrial policy toolkit.
Any concluding remarks?
In countries like Germany, standards permeate every aspect of daily life. In fact, German companies pay to serve and participate on such technical committees. They recognise the importance of standards. Most South African companies do too. It’s a proven fact that adhering to standards keeps companies and countries competitive.
When we started the administration process, we weren’t planning to execute a ‘big bang’ approach. We’re effecting a culture change where SABS employees have the freedom to be a lot more agile and responsive to customers. The SABS – first and foremost – is a business that serves South Africa.