
6 minute read
HOT SEAT: The masters in fluid control
from IMIESA July 2020
by 3S Media
APE Pumps and Mather+Platt have led the market in South Africa since 1952, building on a proud legacy dating back to the world’s first industrial revolution. John Montgomery, general manager, speaks to IMIESA about the challenges and opportunities within the South African and broader African markets.
What are the Group’s core areas of specialisation?
Advertisement
JM APE Pumps has been an innovator in the field of fluid transfer solutions since 1952 across industries that include water utilities, mining, municipalities and the energy sector. This comprehensive skill set is aligned with
John Montgomery, general manager, APE Pumps and Mather+Platt sister company Mather+Platt, which traces its own heritage back to England in 1845.
Mather+Platt manufactures horizontal multistage pumps designed for high-pressure applications and split-case pumps chiefly for high volumes. In turn, APE Pumps specialises in the design and manufacture of vertical industrial turbine pumps, split-case and endsuction pumps for most industries.
What sets APE Pumps and Mather+Platt apart from the competition?
A major distinction is that we are both an OEM and a CIDB 8 ME registered contractor. In addition, we have one of the few pattern shops left in Africa, where our specialist artisans produce wooden patterns in the age-old tradition, alongside the latest trends in 3D printing. Our unsurpassed skill in patternmaking enables us to produce specialised patterns for our components on a breakdown basis.
APE Pumps and Mather+Platt have completed major turnkey projects that include a complete overhaul of the Blantyre Water Board’s pump station and pipeline infrastructure in Malawi.
We are currently working on some largescale installations in South Africa where we are responsible for delivering all the mechanical, electrical and civil components as an integrated turnkey solution. That covers the design, installation and commissioning for variable-speed drives (VSDs), low- and medium-voltage switchgear, distribution boards, cabling, motors, pipe work and pipelines, and, of course, pumps.
Another strategic advantage is our ability to turn solutions around quickly with a combination of project management acumen, technical know-how and a workshop equipped with the latest technologies. In a recent example, we completed a pump refurbishment for a client during a tight, fiveday shutdown window. Our team worked two shifts per day to accelerate the repair – delivering, installing and commissioning the pump ahead of schedule.
How are your solutions helping to sustain the energy sector?
APE Pumps and Mather+Platt have been part of South Africa’s power station landscape from inception. Our cooling water pumps are installed at every Eskom power station except Medupi and Kusile.
Refurbishing older power stations is an ongoing process. Some of them date back to the 1970s. The upside is that we have the capability to restore any pump or fluid transfer process. Keeping power stations online is essential for a smooth-running economy.
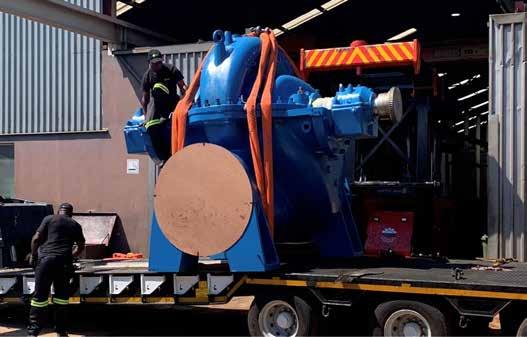
What are your views on promoting local content and manufacturing?
We are registered as a Proudly South African company. That symbolises our absolute commitment to local fabrication and local industry.
Having an extensive inventory of locally manufactured pumps and allied electromechanical systems on hand was a vital factor when South Africa entered the Covid-19 lockdown in March. From the onset, we were able to continue uninterrupted operations. Simply put, we were not dependent on imports from overseas territories. Every component we needed was made in South Africa.
Keeping our operations running during the lockdown has helped sustain our essential industries, which include the water, wastewater, energy and petrochemical sectors. Keeping the supply chain open has also sustained many of our suppliers and kept their workshops running.
Since our local foundries are critical for our business, we ensured that they were kept busy with orders to keep their furnaces on.
How are pump systems evolving?
If you travel back in time 100 years, you’ll find that the skeleton of a pump – the main components – has not changed significantly. However, there have been major advances in metallurgy that provide unsurpassed durability. These include high-abrasion steels like CA6NNM, suited to very demanding environments like mining and wastewater, and Super Duplex for seawater applications.
Pump sizes are also now more compact, but they yield far greater performance. On top of this, our new pumps are more maintenance friendly in terms of access. Additionally, the introduction of VSDs has added huge benefits, as have advances in instrumentation and telematics.
When we rebuild older pumps, we apply the latest technologies. Examples include impeller designs, anti-corrosive coatings, better-suited materials, and gauges.
We are also currently working on a mobile app, which will enable remote monitoring of pump performance via smartphone. Technology is moving at a rapid pace and we need to make sure we advance along with it. If you don’t, you will get left behind.
Are pirate parts posing a threat?
Pirate parts pose a business risk, first and foremost, to downstream industries, municipalities and public utilities. It’s also important to note that whether the part is made locally or imported, it’s still noncompliant and unproven. Pirate parts are the weakest link. Most of the time, pirate parts fail unexpectedly and catastrophically.
We’ve experienced many situations where we’ve been asked to intervene after the fact. A case in point was a client who scheduled a critical pump shutdown for emergency maintenance. Once stripped, the technical team discovered that the non-OEM sourced part wouldn’t fit. This is a part that typically takes up to six weeks just to ship if sourced from an overseas OEM.
In another recent example, we resolved a downtime issue at a municipality’s water treatment works. Motivated by the need to save costs, pirate parts were specified for their vertical turbine pumps. These are 1980s-era units supplied at the time by APE Pumps. They were specifically designed for the plant’s raw water intake.
Thanks to the use of pirate parts, the pumps failed because the valves became defective. We were commissioned by a water authority to completely overhaul the mechanical items at the treatment plant. We installed new pumps, as well as new motors running on VSDs, which, in addition to fluid optimisation, reduce electricity consumption. APE Pumps has also redesigned the pipe works, which includes new 400 mm and 600 mm diameter manifolds, plus valves and flow meters.
The upside is that we are seeing a major shift back to OEMs. This applies to water and wastewater utilities, power stations, the petrochemical industry and all other missioncritical industries. Predictive and preventative maintenance have become paramount to optimally sustain essential infrastructure. This was already a priority in the constrained macroeconomic environment prior to the Covid-19 lockdown. The deepening crisis has now made asset management and optimum life-cycle costing even more crucial.

Is outsourcing operations and maintenance (O&M) a more viable option for municipalities?
The findings of the Auditor-General’s 2018/19 audit outcomes for local government have again highlighted serious shortfalls. A number of these are in the infrastructure space. Water and wastewater plants and associated pump and pipeline systems are falling into disrepair, while allocated costs for maintenance are constrained.
Some years ago, the private sector started outsourcing non-core areas, like water and wastewater treatment, and APE Pumps and Mather+Platt have various service-level agreements in place with key clients. This has now also become a common trend within the public sector.
How has Covid-19 influenced your business model?
As an OEM, we’ve been ahead of the curve for years, so, when the pandemic hit, we didn’t falter for a second. However, the demands on our business have grown exponentially. In response, we’re increasing our inventory volumes to reduce turnaround times even further. Every essential infrastructure project is now ‘Priority One’.
What’s the outlook for the next 12 months?
We have an excellent order book, particularly for turnkey projects. We also expect our OEM business to grow significantly in the coming months. As a Proudly South African company, we’re here to add value and we remain committed to sustaining and supporting local industry, whether public or private.