
6 minute read
Plastic pipelines add value
from IMIESA July 2020
by 3S Media
Maintaining functional and efficient water and sewer networks requires an adherence to stringent design and product standards that extend the life of these vital assets. Alastair Currie asks leading industry experts to share some snapshots.
How is SAPPMA/IFPA spearheading the change we need to see in public infrastructure?
Advertisement
Ian Venter Through our well-balanced membership structure, we can add value to a wide variety of key pipe system performance areas. Differentiation is of great importance and will play a more prominent role going forward. Our national and international footprint and alliances position us well to offer guidance and assistance in the following areas: • system design • product design • standards • specifications • manufacturing • quality management and control • handling and storage • installation and jointing • pre-commissioning testing • commissioning • maintenance and repairs. SAPPMA/IFPA selects its members through carefully controlled supplier evaluation. This is not a ‘one-size-fits-all process’. A degree of factory profiling and auditing needs to take place. In addition to product quality, ethics and a willingness to adhere to a code of conduct are just some of the criteria.
This important initial supplier evaluation is part of a long-term partnership and supplier development programme. Ongoing manufacturer
Ian Venter, technical manager, Southern African Plastic Pipe Manufacturers Association (SAPPMA), incorporating the Installation & Fabrication Plastic Pipe Association (IFPA)



Albert Vaartjes, global sales manager: RBlue PVC-O, Rollepaal
Vollie Brink, consulting engineer

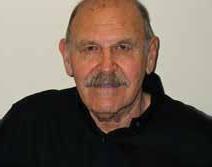
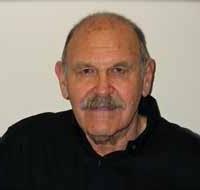
product and process audits ensure that quality is never compromised.
We have developed a list of commonly required procedures, documents and process controls that can be assessed during our manufacturing process audit to achieve consistent and repeatable results. That’s vital for specifiers when they order products for infrastructure projects.
From a design and standards perspective, where is the industry falling short?
Vollie Brink The objective of development is to uplift communities, which, in the South African context, means bridging poverty and inequality gaps. Water and sanitation infrastructure as well as housing are pressing priorities. Municipalities have a responsibility to adhere to engineering and product standards that deliver the best result. Embracing technology translates into more efficient construction processes and more durable structures.


Johann Wessels, consulting engineer Government and other statutory bodies play a vital role in enabling and supporting development. This includes their regulatory responsibility to approve standards that are practical and cost-effective. In this respect, PVC, HDPE and equivalent pipe materials are long-lasting. Due to their relatively light weight compared to steel, GRP and concrete, plastic pipes are well suited to labour-intensive construction techniques. Unlike steel, there are no concerns about costly cathodic protection requirements.
In terms of PVC pipe manufacturing, where is the R&D focus right now?
Albert Vaartjes The key areas of focus are non-pressure systems (multilayer pipe) and pressure systems (PVCO pipe). Sustainability is of utmost importance and plays a key role in the conceptual approach. The ability to reuse postconsumer, recycled material in multilayered systems is also a priority to promote circular economies.
Efficient water metering and the reduction of leaking pipes are another worldwide focus, with R&D departments developing more effective pressure and non-pressure pipe joints for their pipe components. All of this and more is achieved through effective design teams, modern, low-volume die-heads, automatic thermal centring, inline production systems, and continuous process improvements that deliver reliable pipe systems. This presents a viable alternative to traditional steel and GRP pipe systems, with all the added benefits of PVC pipe. The lower environmental impact of multilayer sewer PVC pipes also has the right properties to exceed design life. This has been achieved through innovative manufacturing processes that include effective foaming (foamed core with scrap) and by using filler and recyclates.
When conventional solutions don’t work anymore, what are the alternatives?
Johann Wessels For the nonconventional construction of new pipelines, one can consider using pipe jacking, microtunnelling, auger boring, horizontal directional drilling, pipe ramming or impact molling as alternative trenchless techniques, rather than conventional open excavation.
Further rehabilitation options include pipe bursting, slip lining, spirally wound lining, and cured-in-place pipe. These are all trenchless options that complement

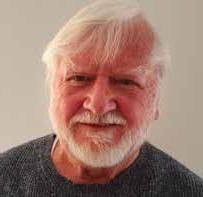
Alaster Goyns, consulting engineer
conventional, open-cut methods to install new pipe.
When should lining systems be installed on sewer pipelines?
Alaster Goyns When water is extracted from natural resources, it is usually supplied in pipelines that flow full, under pressure and which are placed in shallow trenches. This means that most of the time it is just water being transported and the major stresses in the pipe walls are due to internal pressure. Wastewater is generally conveyed in pipelines that flow partly full, under gravity and frequently placed in deep trenches. This means that water and air are being transported and the major stresses in the pipe walls are due to external loads.
All pipelines are potentially subject to corrosion, which will depend upon the materials being used and what is being transported through the pipeline. Highpressure pipelines were traditionally steel. Effective ways of protecting them include coatings that can be bonded to the steel.
Sewers 300 mm in diameter and larger were traditionally concrete. Under certain combinations of hydraulic performance and the effluent being conveyed, these sewers were subject to biogenic corrosion. This is due to the formation of hydrogen sulfide within the effluent and its subsequent release into the sewer atmosphere, where it is biologically converted into sulfuric acid. The latter then attacks the alkalinity of the concrete, causing its deterioration.
Precautions need to be taken to prevent this. Examples include providing a control layer of more corrosionresistant concrete or an inert lining. Where precautions aren’t taken, the corrosion attack can occur within a few decades, rendering the sewer structurally unsound and no longer watertight. However, if these problems

are timeously identified, the sewer can be rehabilitated at much less cost than replacement.
Another point to note about sewers is that they are generally placed at depth and follow natural water courses, where they are subjected to external water pressures. This poses a problem for their rehabilitation, as concrete is permeable, although the rate is very slow. Unlike steel pipelines, where very thin coatings can be effectively bonded on to the host pipe to provide corrosion protection, this cannot be done on a concrete pipe. The bond between the coating and the host pipe is not strong enough to resist the external groundwater pressure. For this reason, the protective layer on either a new or rehabilitated pipe must be designed to withstand these conditions for their envisaged design life of 100 years or more.
Conclusions
As with all water and wastewater pipeline designs, the conclusion from the various speakers is that each application should be fit for purpose, with a major emphasis on minimising maintenance and a corresponding focus on optimising life-cycle costs. Within the mix, plastic pipes present a longlasting solution.