
3 minute read
Producing water reticulation hardware post Covid-19
from IMIESA July 2020
by 3S Media
Producing water reticulation hardware post Covid-19
Davis & Deale and Conver-Tek have been in the water supply and plastic injection moulding business for over 40 years, but have been forced into a serious dilemma by Covid-19 and the subsequent lockdown.
Advertisement
By Bevan Davis, founder, Conver-Tek
Moving forward, we don’t know what final effects the government lockdown will have, but it is clear that many businesses will not survive the debilitating lockdown. Our plastics industry has been seriously compromised, and many companies – from small to large – will shut their doors.
From concept to finished, produced and tested product
Production, in future, will be radically affected. People and stable staffing are already a massive problem due to power outages. After power outages, we take four to five hours to get up and running in our production. The costs to reset machines, recheck quality, wastage of purged materials, first samples, etc. costs us over R11 000 per hour, which is a crippling cost that can’t be sustained or recuperated.
At Davis & Deale, we design the concepts, develop the products, build the tools and run production from concept to finished product, all under one roof. This is a unique benefit to our customers. We then assemble and test all the products used to supply the water industry and to many other key industries needing specialised injection moulding.
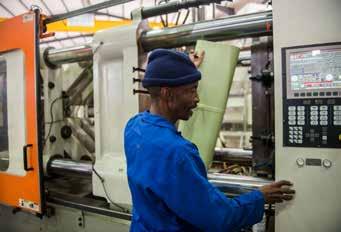
Some materials, at roughly R300/kg, are devastating to our injection moulding machines during a power outage and can cause damage of more than R300 000 to a single machine. We cannot risk running these materials with the outages we have, given the potential damage to our machines. Continuous electricity supply is critical to the survival of our plastics converting industry. It was recently announced that the boiler tubes in the new generating plants will all need to be replaced due to quality and design issues. What happens then?
Combating power outages
It is sad, but a simple fact, that, as an SMME, we will have to spend capital – not necessary or budgeted for – of R5.3 million to stay in business and shift off the Eskom grid, to be able to operate effectively. The only good result of the Eskom power outages and price increases is that the ridiculously inflated cost of electricity will pay off our unnecessary investment in a maximum of four years.
It is a reality that any key manufacturing industry SMME has two options, namely: 1) Get off the grid at a huge cost and risk. 2) Liquidate and shut down. Our junk status can’t get any worse. This is simply the reality we face, and continue to face, given the gross mismanagement, corruption and implosion of Eskom. This has had the most devastating impact on all businesses, especially industries needing 24/7, reliable, cost-effective power. Instead, we’re being fleeced on taxes and still paying R5.3 million to be able to keep the lights on to stay in business.

Instead of fixing the problems, corruption and mismanagement, the price of power continues to increase. We pay three times our normal rate in peak periods and are then charged the full peak period rates. This is simply not sustainable for industry and cannot be passed on to the customer.
Eskom is busy crippling SMMEs, which are major tax contributors and employers in South Africa. We, as a manufacturer, should be spending R5.3 million on new, modern production machines that generate new jobs, pay more taxes and boost our economy. The government, via Eskom, is in fact killing the golden goose. The cost of importing opposition products – due to our junk status and exchange rate – is the only thread of hope keeping us competitive as manufacturers.