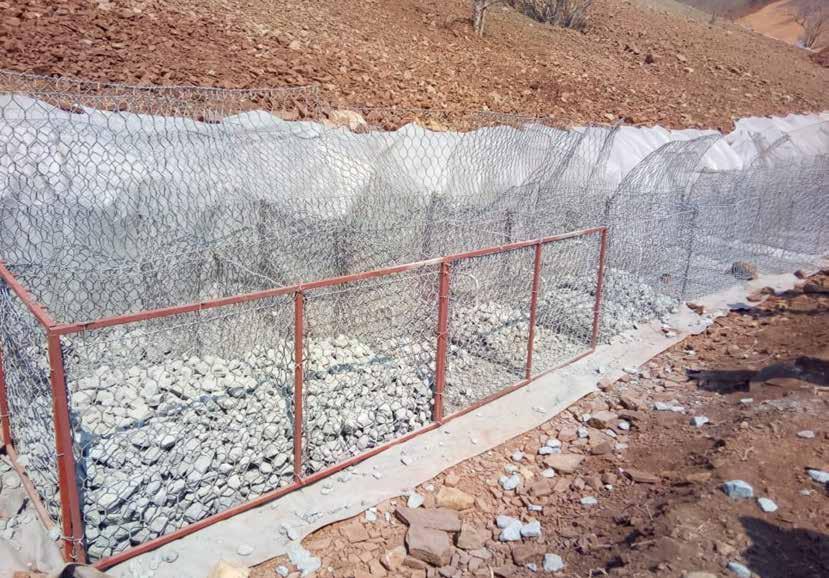
4 minute read
Gabion systems need geotextiles
from IMIESA June 2021
by 3S Media
As soil separation, drainage, water filtration and allied protection interventions, geotextiles play crucial roles in the overall integrity and performance of gabion systems. The starting point is a soil analysis, followed by optimal design, correct product specification, and best practice installation techniques, says Louis Cheyne, managing director,
Gabion Baskets.
Advertisement
By Alastair Currie
There are two main types of geotextile employed in the construction of gabion structures that enhance their structural stability – namely woven or needle-punched non-woven, which are produced using materials like polyester and polypropylene. Both materials are designed to provide some form of controlled permeability since a typical gabion basket is composed of 35% voids and 65% rock.
Non-woven mesh products are ideally suited for sandy soil-type environments, plus riverine structures. Examples include bridge abutment protection, weirs, riverbank erosion control and retaining walls. Here, these non-woven geotextiles are highly effective in countering the migration of fines that would otherwise undermine these structures. They can also perform optimally in reducing water velocity below and around submerged gabion systems.
In contrast, woven geotextiles are better suited to soils with a high plasticity. Clayey soils are a prime example. Where the plasticity is very high, however, a geotextile may not be required, but the soil analysis will determine this.
“Installing a non-woven mesh in a clayey scenario will result in progressive clogging of the liner via fine particle build-up over time. This will make the geotextile progressively impermeable. Subsequent water pressure build-up could then potentially push over the structure,” Cheyne explains.
Gabion Baskets provides turnkey solutions for all projects. This scope encompasses the manufacture of gabion baskets and/or gabion mattresses, the supply of specialist geotextiles, plus the rock fill material. Design recommendations, plus contractor and installer training are also provided.
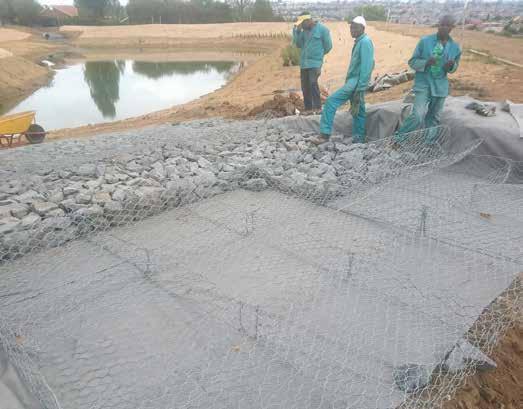
Laying geotextile sheets is the essential starting point for ensuring a sound base on which to build gabion basket and/or gabion mattress structures
Geotextile installed behind and below this gabion wall structure helps to prevent soil loss that could potentially undermine the structure
Selecting the right liner specification
Choosing the right geotextile layer thicknesses and strength is essential. The general specification supplied by Gabion Baskets ranges between 200 g/m2 and 270 g/m2 .
As Cheyne points out, lighter-weight fabrics at around 140 g/m2 are fine for roadway and sports field subsoil drainage, but far too thin and lightweight for gabion installations.
“The most common fill source is blasted rock from a commercial quarry,” Cheyne explains. “These rock fragments tend to be angular in shape, often with sharp edges that
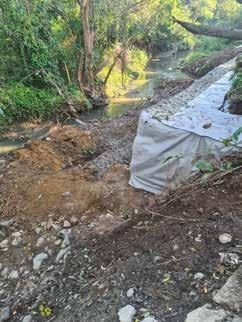

Geotextiles form an especially important role in ensuring the stability of gabions installed as part of a river erosion system prevents the sand washing through and subsidence occurring behind and below the structure. In this application, the general rule is to use 1 m² to 2 m² of geotextile per m³ of gabion.
Installation
All gabion installations placed directly on to sandy in situ soils should rest on a primary geotextile separation liner. To further prevent any soil ingress, it’s also important to ensure that there’s a minimum overlap of 30 cm between laid-out geotextile sections.
Where gabions are submerged in a riverine environment, the rock within the gabion systems should be entirely wrapped in a non-woven geotextile to prevent silt build-ups
that could eventually lead to failures. The foundation – often a gabion mattress with apron – must also be placed on a non-woven geotextile to cater for soil movement below.
Geotextiles are also ideal for protecting gabions and gabion mattresses exposed to constant fast-flowing water. Without a liner, the ensuing water velocity causes a sucking effect through the mattress. The riverbed soils are then sucked through, which causes hollows underneath. The supported gabion retaining wall will then start to lean over and eventually collapse.
“As these and other examples mentioned illustrate, the use and extent of geotextiles will vary with every gabion installation; however, it’s the basics that are non-negotiable,” adds Cheyne.
“Interestingly, geotextiles only started to gain traction in South Africa in the early 1990s. But, since then, have become the standard for professionally engineered structures,” Cheyne concludes.
OPTION 1 Examples of subsoil drainage system designs OPTION 2
could puncture a thinner geotextile during the gabion basket filling process. Then the fines will start to pass through.”
For specialist applications, the geotextile layer thickness can go as high as 1 kg/m2. This is typically used for layer works separation during road construction where the geotextile serves as a bridge over poor in situ soils, like black turfs. The geotextile liner, covered by an aggregate layer, allows the water to pass through but stops soil movement below. Where the latter occurs, potholes are among the end results.
The same principle applies for gabion retaining walls built in a sandy soil environment. Here, a non-woven geotextile
A gabion river wall failure. Contributing factors include poor installation and founding, as well as inadequate use of geotextiles to prevent soil erosion behind and below the structure
