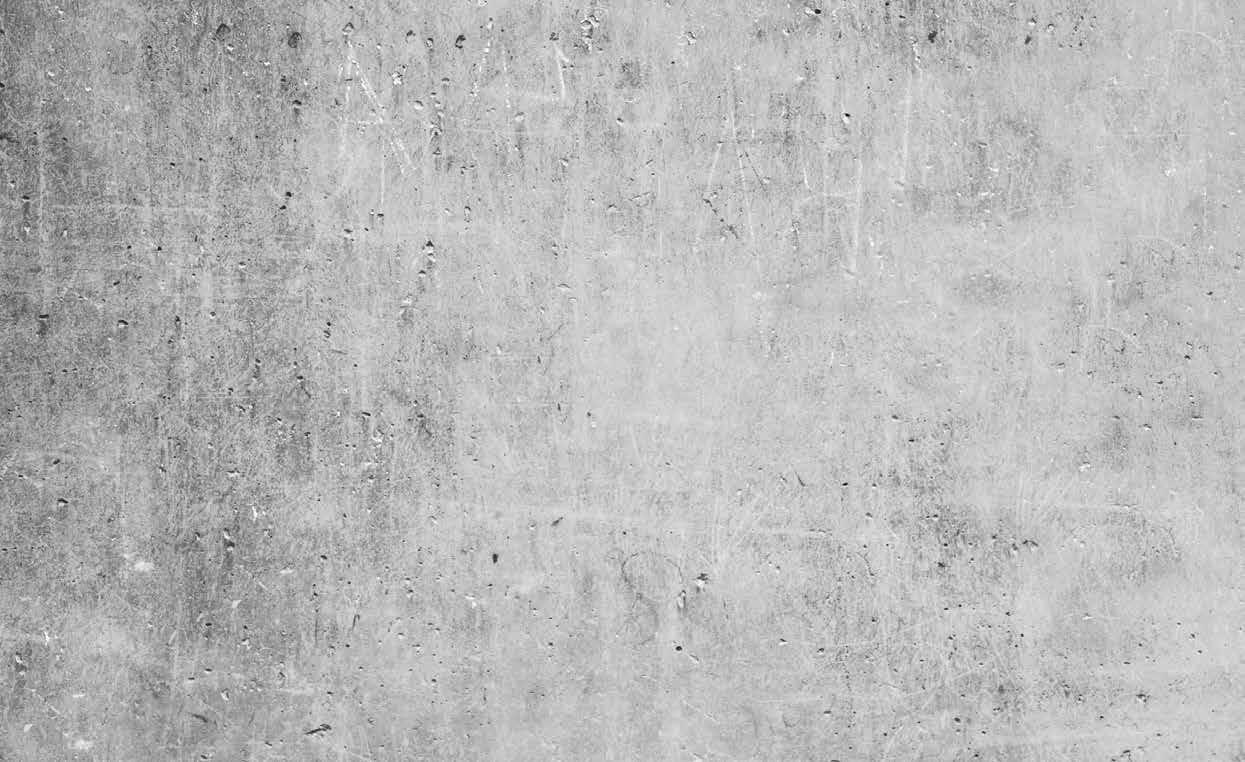
2 minute read
The smart way to monitor bridge loads
from IMIESA June 2021
by 3S Media
Keller sensors can be used to measure and record load distribution on bridges.
Mechanical indicator on the bridge bearings
Advertisement
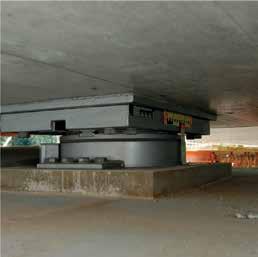
The volume of traffic on our roads is an unknown quantity and the growing proportion of trucks places increasing loads on bridges. Furthermore, plate tectonics constantly cause the ground beneath our feet to move. These two variables cause the load distribution on a bridge to change. It is therefore necessary to continuously monitor and identify changes in the load distribution with sensors. Previously, bridge loads were displayed using a mechanical indicator on the bridge bearings, which had to be read on-site. Fortunately, Keller has focused its attention on this central supporting element of the bridge and integrated a networked pressure measurement solution into the bearing.
The bridge transfers the loads to an elastomer cushion. An elastomer is a polymer with viscoelasticity (both viscosity and elasticity) and weak intermolecular forces, generally low Young’s modulus, and a high failure strain compared with other materials. Between the pressure sensor and the elastomer is a layer of grease that functions as a pressure transfer medium and makes it possible to measure the internal pressure due to loading. This change in pressure is determined by a pressure transmitter, which is customised to integrate perfectly with the bridge bearing.
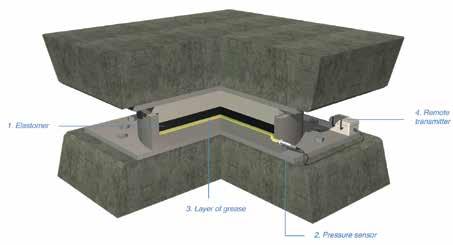
Bridge bearing with a built-in elastomer cushion, layer of grease and pressure sensor
Telemetry module
Keller has two telemetry modules: a basic version (ADT1) and a more extended highend version (ARC1). Both are battery-operated modules for the remote transmission of pressure transmitter data. The telemetry modules have been specially designed for connecting to Keller pressure and level sensors. There are several versions of both modules covering data transfer by 3G or 4G networks, as well as narrow-band and longrange internet of things (IoT). SMS and email data transfer is possible but will reduce the system’s extended features.
With bridge loads, the telemetry modules read the data directly via a digital interface and can send this data (immediately or at preset times) to the customer’s server or the Keller Kolibri Cloud Portal. The use of stainless-steelcovered pressure sensors with an especially long service life guarantees decades of reliable measurements and functional safety. With the ARC1 module, alarm alerts can be sent by SMS for immediate response.
By using IoT, bridges can be reliably and continuously monitored for changes in load distribution that pose a threat.