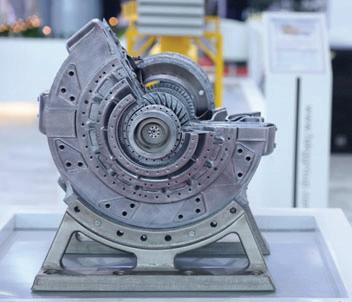
36 minute read
Casting Quality Steel in the World: Fu-an Brings Star Prod- uct to Shenyang Foundry Expo
Casting Quality Steel in the World: Fu-an Brings Star Product to Shenyang Foundry Expo “铸世界好钢”——福鞍携明星产品亮相沈阳铸造展
A council member of China Foundry Association, Liaoning Fu-an Heavy Industry Co., Ltd. was established in July 2004. The company's leading products are the key core components of major technology and equipment for energy and electric power, rail transportation, heavy machinery, marine and other industries.
Advertisement
Over the years, Fu-an has always adhered to the development of "high-end manufacturing" and the brand strategy of "creating Fu-an brand and casting quality steel in the world", which has won high praise from customers. In recent years, the company has won the only "Best Quality Award" and "Excellent Supplier Award" among GE's many global suppliers. In 2018, it won the "Best Supplier Award" of Harbin Turbine Company Limited. In 2021, it was awarded the title of "Baihetan Million kW Hydropower Unit Large Casting Excellent Supplier" by Harbin Electric Machinery Company Limited.
At present, Fu-an Heavy Industry has become the excellent suppliers of domestic and international major energy and electric power, rail transportation, heavy machinery and other equipment manufacturers .The main domestic customers are: Harbin Electric Corporation, Dongfang Electric Corporation, Shanghai Electric and other domestic key main engine plants. The main foreign customers are: TOSHIBA of Japan, General Electric of the United States, GE Transportation of the United States, SIEMENS of Germany, Mitsubishi of Japan, ALSTOM of France, VOITH Hydropower of Germany and many other Fortune 500 enterprises. Fu-an has obtained the factory certification of qualified suppliers of these international famous enterprises, and realized the batch ordering, and formed a stable international market. ■
中国铸造协会理事单位辽宁福鞍重工股份有限公司成 立于2004年7月,公司主导产品为能源电力、轨道交通、 重型机械、船舶等行业重大技术装备的关键核心部件。 多年来始终坚持“高端制造”的发展道路,坚守“创 福鞍品牌、铸世界好钢”的品牌战略,赢得了客户的好 评。近年来荣获美国GE公司全球多家供货商中唯一的“ 最佳质量奖”和“卓越供应商奖”荣誉;2018年荣获哈 尔滨汽轮机有限公司“最佳供应商奖”。2021年被哈尔 滨电机厂有限责任公司授予“白鹤滩百万千瓦水电机组 大型铸件优秀供应商称号”。 目前,福鞍重工已成为国内和国际主要能源发电、轨 道交通、重型机械等设备制造厂家的优秀供货商。国内客 户主要有:哈尔滨电气集团、东方电气集团、上海电气集 团等国内重点主机厂;国外客户主要有:日本东芝、美国 GE通用电气、美国GE轨道、德国西门子、日本三菱、法 国阿尔斯通、德国福伊特水电等多家世界500强企业。福 鞍获得了这些国际知名企业的合格供应商工厂认证,并且 实现了批量订货,形成了稳定的国际市场。 ■
Improving Corrosion Resistance on Surface-Alloyed Butterfly Valves
A recent study explored how to improve cast surface-alloying to impart high local wear and corrosion resistance to less expensive, common industrial materials.
kaustubh rane, michael beining, swaroop behera, amir kordijazi, ajay kumar p., and pradeep rohatgi, university of wisconsin (milwaukee) 提高蝶阀表面合金化的耐腐蚀性
Kaustumbh Rane、minchail benning、swaRoop beheRa、aamiR KoRdizzi、ajay KumaR p.和pRadeep Rohatgi,威斯康星大学(密尔沃基)
Many metallic components used in applications involving exposure to corrosive aqueous and atmospheric conditions suffer from degradation of the surface, such as corrosion and wear. These problems are especially widespread for castings used in the water supply industry, including pumps, butterfly valves, valve seats, faucets and flanges. To prevent corrosion on the surface of these components, water industries rely on coatings or specify cast stainless steel components. The oxide layer formed on the surface of stainlesssteel acts as a protective barrier between the environment and the sample surface.
Over the years, various techniques have been used to develop surface alloy coatings on steel to improve properties like corrosion and wear; however, these techniques are costly and often it is not feasible to use these coating methods on complex-shaped, hollow components—especially where there is no line of sight.
Because corrosion is a surface phenomenon, mainly the 在暴露于腐蚀性水和大气中的很多金属部件会 面临表面破损的问题,例如腐蚀和磨损。这 些问题在供水行业使用的铸件中尤其普遍存 在,包括泵、蝶阀、阀座、水龙头和法兰件。为了防止 这些部件的表面腐蚀,供水行业依赖涂层或特殊的不锈 钢部件。不锈钢表面形成的氧化层充当环境和产品表面 之间的保护屏障。 多年来,已开发出各种技术应用于铸钢表面的合金 涂层,以改善腐蚀和磨损性能;然而,这些技术成本高 昂,而且通常在形状复杂的空心部件上使用这些涂层方 法是不可行的——尤其是在看不见的地方。 腐蚀是一种表面现象,部件表面需要耐腐蚀。因此, 如果部件内部或芯部由不同的材料制成,而且外表面层
Fig 1. Butterfly valve molds for industrial casting (a,c): Bare and cleaned surface coated with zircon; (b,d): Multielement powder-coated mold surface using sodium polyacrylate.
Fig 2. Schematic diagram of the sand mold with the alloying powder slurry applied on the inner surface of the mold cavity. The alloying slurry is a combination of the alloying powders and the binder medium.
图1:工业铸造用蝶阀铸型(a,c):裸露和清 洁的表面涂有锆石;(b,d):使用聚丙烯酸 钠的多元素粉末涂层模具表面。
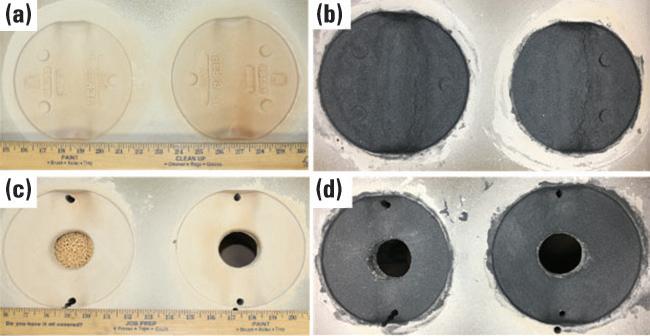
图2:在型腔内表面涂有合金粉浆的砂型示意图。合金浆是合 金粉末和粘结剂介质的组合。
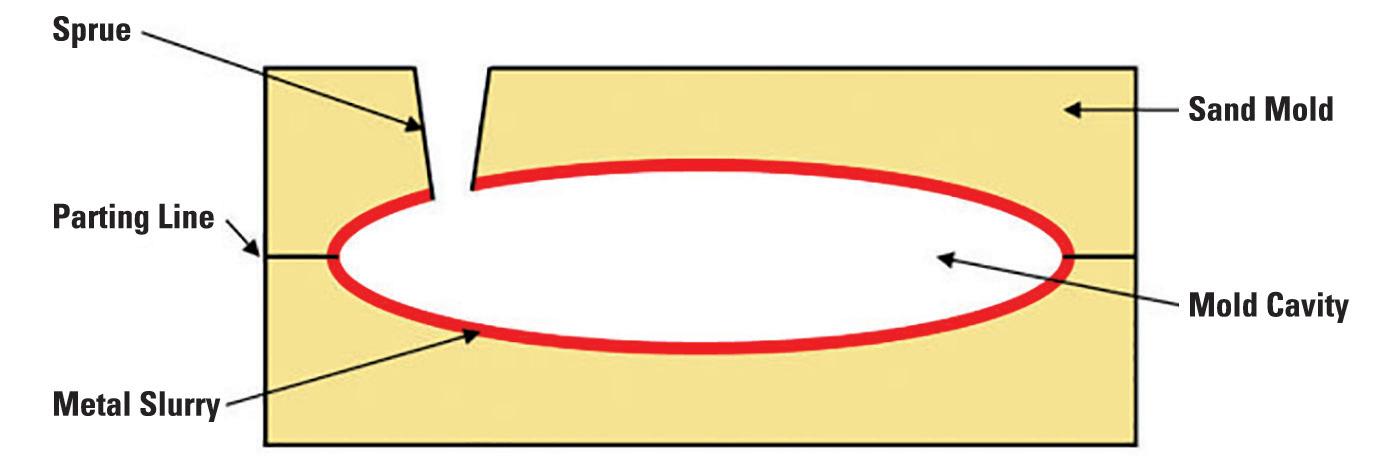
Fig 3. (a) A commercially available butterfly valve, (b) Surface alloyed butterfly valve prototypes cast at the industrial foundry and UWM.
Fig 4. Optical images of the as-cast (a) BV1 and (b) BV2.
图3:(a)市售蝶阀,(b)在铸造厂和 UWM铸造的表面合金化蝶阀原型。
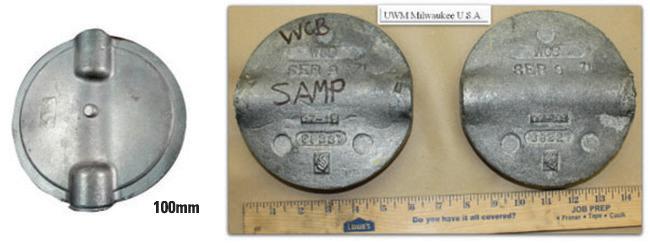
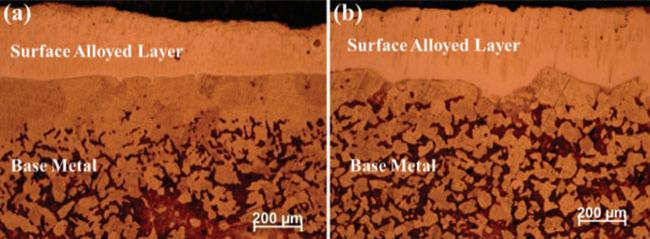
图4:铸态(a)BV1和(b)BV2 的光学 图像。
图5:三种表面合金化蝶阀铸件 表面合金化层的平均厚度。
surface of a component needs to be corrosion resistant. Thus, if the internal piece, or core, is made of a different material but the outside surface layer provides sufficient corrosion resistance, the component can perform at a level similar to a high corrosion-resistant component. This is also true for high wear-resistant applications in which a higher hardness coating will lead to high wear resistance even when the core is a softer material.
Cast surface alloying is a good solution to impart high local wear and corrosion resistance to cheaper and common industrial materials like mild steel. Some of the main characteristics of surface alloying during casting include: (1) the surface properties of materials and parts can be tailored to specific requirements (resistance against corrosion, wear, oxidation); (2) the alloyed layer is metallurgically bonded to the base metal; and (3) surface finish can be controlled, and machining allowance can be provided. Ni and Cr are frequently used alloying elements for improving the performance of wear-resistance, corrosion-resistance and thermal-resistance in iron-based components. Ni can dramatically improve the chemical stability of the iron alloys for increased corrosion resistance, and Cr leads to the formation of an oxide layer, which is highly protective against a corrosion reaction.
In the present study, targeted, multielement Ni, Cr, Fe-Mn, Fe-Si, and Mo enriched surface alloyed layers were developed and tested for a WCB steel butterfly valve on an industrial scale using the gravity sand casting process. A butterfly valve is a quarter-turn rotational motion valve, which is used to stop, regulate and start the flow. The alloying elements were picked for their presence in super duplex stainless steel components, which have very high corrosion resistance but are expensive.
Casting Procedure
The industrial butterfly valves casting molds (Fig. 1) were obtained from an industrial foundry to demonstrate surface alloying. The molds were made from 80-grain fineness silica sand. A phenolic urethane organic binder system 具有足够的耐腐蚀性,则该部件可以在类似于高耐腐蚀 部件的环境下运行。对于高耐磨应用也是如此,即使芯 部是较软的材料,更高硬度的涂层也会具有高耐磨性。 铸件表面合金化是一种很好的解决方案,可以为低 碳钢等较便宜的普通工业材料赋予较高的局部磨损和 耐腐蚀性。铸造过程中表面合金化的一些主要特性包 括:(1)材料和零件的表面特性可以根据特定要求进行定 制(抗腐蚀、耐磨、抗氧化);(2)合金层与母材冶金结 合;(3)表面光洁度可控,可提供加工余量。Ni和Cr是 常用的合金元素,用于提高铁基铸件的耐磨、耐腐蚀和 耐热性能。Ni可以显著提高铁合金的化学稳定性,以提 高耐腐蚀性,而Cr会导致形成氧化层,对腐蚀反应具有 很强的保护作用。 在本研究中,针对WCB钢蝶阀使用重力砂型铸造工 艺开发和测试了有针对性、Ni、Cr、Fe-Mn、Fe-Si和 Mo多元素富集的表面合金层。蝶阀是一种四分之一圈 旋转运动阀,用于停止、调节和启动流量。选择合金元 素是因为它们存在于超级双相不锈钢部件中,这些部件 具有非常高的耐腐蚀性,但价格昂贵。
铸造步骤
工业蝶阀铸型(图 1)从铸造厂获得,以论证表面合 金化。铸型由80目细度的硅砂制成。使用酚醛聚氨酯有
Fig 5. Average thickness of the surface alloyed layer in three castings of surface alloyed butterfly valves.
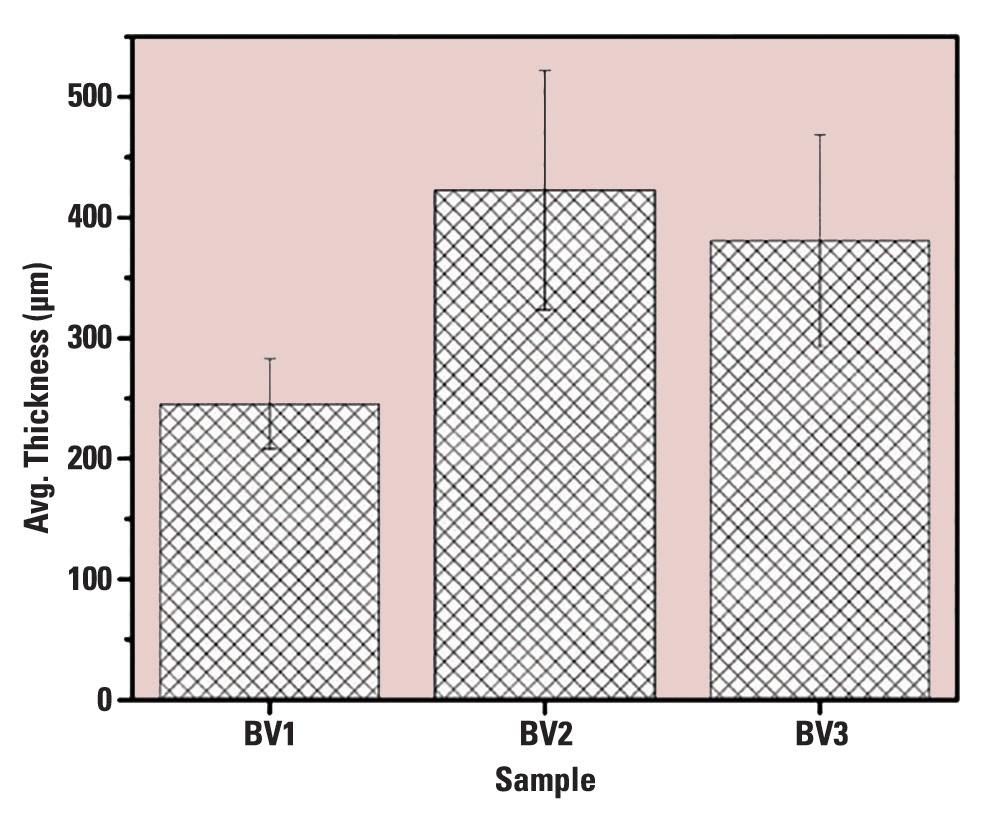
Fig 6. SEM micrograph of (a) base metal (b & d) BV1 surface alloyed layer, (c) BV2 surface alloyed layer in as-cast condition, (e) Austenite-Ferrite microstructure of the surface alloyed layer, (f) The interface layer between surface alloyed layer and the base metal. All samples were in the as-cast condition.
Fig 7. (a) Location of the EDS line scan on the cross-section of the BV3 surface alloyed sample across the base metal and surface alloyed layer. (b) Plot of elemental intensity vs. distance in the EDS line scan.
图6:(a)基体金属(b & d)BV1表面合 金层,(c)BV2铸态表面合金层的SEM 显微照片,(e)表面合金层的奥氏体-铁 素体微观结构,(f)表面合金层与基体 金属之间的界面层。所有样品都处于 铸态。
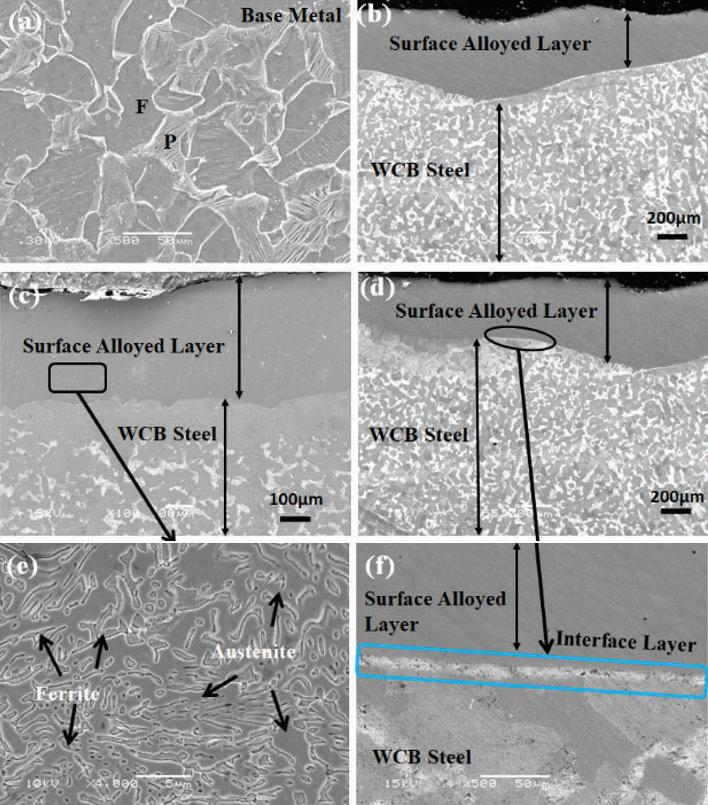
图7:(a)EDS行扫描 在BV3表面合金样品 横断基底金属和表面 合金层的横截面上的 位置。(b)EDS行扫 描中元素强度与距离 的关系图。
(binder level ~1.2%) was used to ensure good gas permeability and surface finish during casting. The catalyst used was set to allow for an eight- to 10-minute work-strip time. The sand and binder/catalyst chemicals were mixed in an industrial mixer and then dumped onto the pattern. The sand was manually smoothed, as well as with a strike-off bar, and allowed to set for 10 minutes. After the curing was complete and the mold halves were extracted from the pattern by flipping inversion of the pattern using a manipulator crane. The mold cavities were coated with a refractory wash to avoid any reaction between the molten metal and the sand. After applying binder and surface alloying elements on the mold and allowing the slurry to dry and harden, the molds were closed, and a zircon filter was placed in the down sprue of the mold.
Next, three samples were made using two different techniques. The first two samples were prepared by adding the Ni and Cr powders onto a wet refractory wash coating, and the third sample was made using a slurry containing Ni, Cr, Fe-Mn, Fe-Si, and Mo mixed with a sodium polyacrylate (NaPA) binder. Figure 2 shows a schematic representation of the sand mold before the WCB steel melt is poured. Once the mold surfaces were coated, they were sealed using a core and mold adhesive. The molds then were transported back to the industrial foundry for casting. Once the castings were poured, they were shaken out, shot blasted with steel shots, de-gated at the foundry and then transported back to the university lab for analysis.
Figure 3 shows a commercially available butterfly valve, and the surface alloyed butterfly valve prototypes cast at the industrial foundry in the present study. The objective was to 机粘结剂(粘结剂含量约1.2%),确保铸造过程中良好 的透气性和表面光洁度。使用的催化剂设置为允许8到 10分钟的工作时间。砂子和粘结剂/催化剂在混砂机中 混合,然后倒在模具上。砂子经手动铺平,并使用刮刀 棒,让其凝固10分钟。固化完成后,通过使用机械臂起 重机翻转铸型,从模具中取出半模。铸型型腔涂有耐火 涂料,以避免熔融金属与砂之间发生任何反应。在铸型 上施加粘结剂和表面合金元素并让浆料干燥和硬化后, 闭合铸型,并将锆石过滤器放置在铸型的直浇口中。 接下来,使用两种不同的技术制作了三个样品。前两 个样品是通过将Ni和Cr粉末添加到湿耐火涂层上来制备 的,第三个样品是使用含有Ni、Cr、Fe-Mn、Fe-Si和 Mo的浆料与聚丙烯酸钠混合制成的(NaPA)粘结剂。 图2显示了浇铸WCB钢熔体之前的砂型示意图。一旦铸 型表面被涂覆,就使用型芯和铸型粘结剂将它们密封。 然后将铸型运回铸造厂进行浇注。浇注完成后,进行落 砂处理并用钢丸进行喷丸,在铸造厂去除浇口,然后运 回大学实验室进行分析。 图3显示了商用蝶阀以及本研究中的表面合金化的蝶 阀原型。目标是量化在工业环境中可以实现的富集水
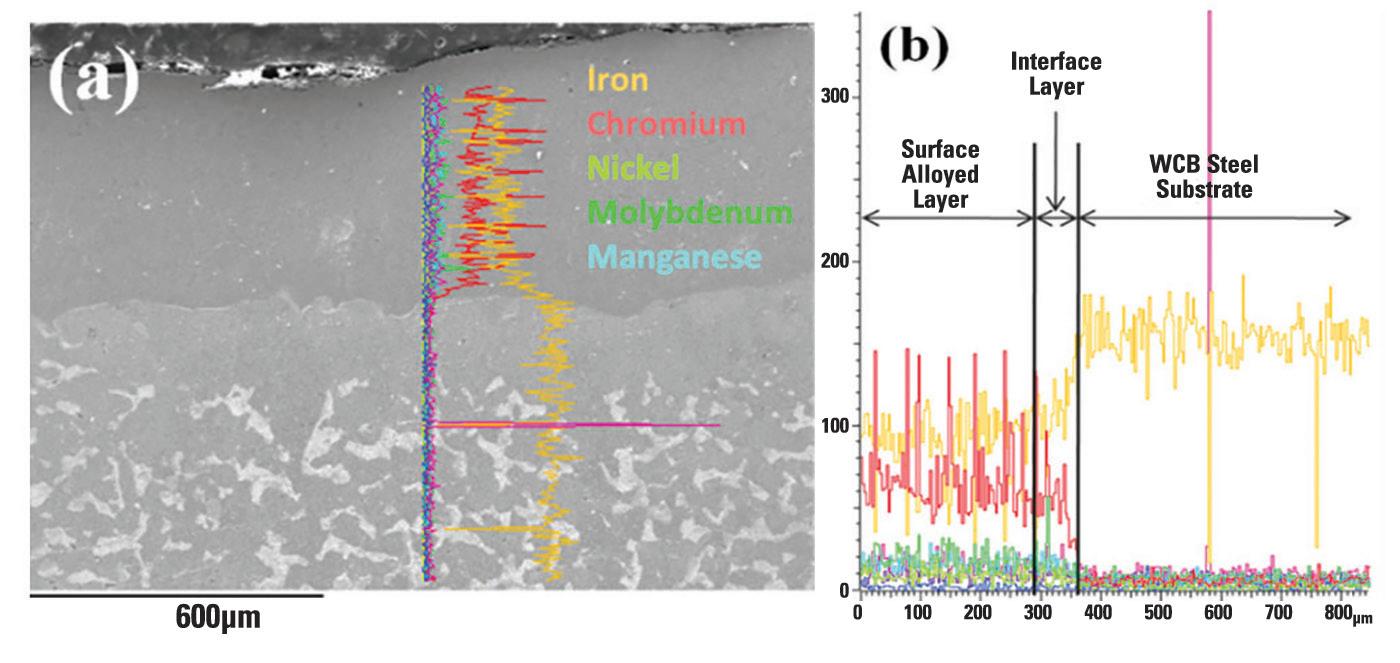
quantify the levels of enrichment that could be achieved in an industrial setting for casting a component that requires high quantities of alloying elements on the surface for wear and corrosion resistance. The chemical composition of the WCB base alloy is presented in Table 1. Table 2 presents the compositions of the alloying elements and alloys used for surface alloying of industrially cast butterfly valves.
Microstructural and Phase Analysis
Optical micrographs of the cross-section of surface alloyed as-cast samples are shown in Fig. 4. A relatively uniform and continuous surface alloyed layer was observed in all samples.
Electro-etching of the surface alloyed layer was performed using an etchant made with 15% HCl and 85% Ethanol and passing a 2 Amp current using an electrode placed on the surface alloyed layer. The base metal (Fig. 6a) shows a ferrite and pearlite microstructure, which is typical of WCB steel. Figure 6 (views b-d) demonstrates the cross-section macromorphology of the surface-alloyed layer, indicating a surface alloyed layer free of cracks or porosity. The interface layer between the base metal and the surface alloyed layer does not show the presence of cracks.
The microstructure at the interface of the surface alloyed layer and the base metal suggests a good metallurgical bond. The microstructure in a typical surface alloyed layer (Fig. 6e) is composed of austenite (γ) phases in the shape of elongated islands dispersed in the ferritic (α) matrix and free of precipitates.
The EDS line scan results of surface alloyed sample BV3 (Fig. 7) shows the change in the gradient in compositions of various alloying elements from the substrate to the surface alloyed layer. Table 3 lists the composition of the surface-alloyed layer and the interface. Compared with the original composition of the WCB steel, significant increases in concentrations of nickel, chromium, Mo, Mn, and Si have been detected in a surface alloyed layer. The analyses were performed in regions ferrite (α phase) and austenite (γ phase) indicated in the micrographs (Fig. 6e). Chromium and molybdenum were observed in a higher percentage in the ferrite phase, since they are ferritizing elements, and nickel was present in a higher percentage in the austenite phase since it dissolves and stabilizes austenite.
The dissolution of alloying elements added to the slurry coated on molds leads to the formation of the surface alloyed layer. The weight percentages of Ni and Cr drop at the interface while that of Fe increases sharply as one moves from the surface
Table 1. Elemental Composition of WCB Steel From Experimental Heat 表1:来自热实验的WCB钢的元素组成
Element Weight % C 0.22 Mn 0.84 平,用于需要大量合金元素使铸件表面合金化以实现 耐磨和耐腐蚀的部件。表1显示了WCB基合金的化学 成分。表2显示用于工业铸造蝶阀表面合金化的合金成 分。
微观结构和相分析
表面合金铸态样品横截面的光学显微照片如图4所 示。在所有样品中都观察到相对均匀和连续的表面合金 层。 表面合金层的电腐蚀使用由15%HCl和85%乙醇制成 的蚀刻剂进行,并使用放置在表面合金层上的电极通过 2安培的电流。母材(图6a)显示铁素体和珠光体显微 组织,这是WCB钢的典型特征。图6(b-d视图)展示 了表面合金层的横截面宏观形态,表明表面合金层没有 裂纹或孔隙。母材与表面合金层之间的界面层没有出现 裂纹。 表面合金层与基体金属界面处的微观结构表明良好的 冶金结合。典型表面合金层中的微观结构(图 6e)由 奥氏体(γ)相组成,呈细长岛状,分散在铁素体(α) 基体中,没有沉淀物。 表面合金化样品BV3的EDS线扫描结果(图 7)显示 了从基底到表面合金化层的各种合金元素组成的梯度变 化。表3列出了表面合金层和界面的组成。与WCB钢的 原始成分相比,在表面合金层中检测到镍、铬、钼、锰 和硅的浓度显著增加。在显微照片中指示的铁素体(α 相)和奥氏体(γ相)区域进行分析(图6e)。在铁素 体相中观察到更高百分比的铬和钼,因为它们是铁素体 化元素,而镍在奥氏体相中以更高的百分比存在,因为 它能溶解并稳定奥氏体。 涂在铸型上的浆料中的合金元素的溶解导致表面合金 层的形成。Ni和Cr的重量百分比在界面处下降,而铁的 重量百分比随着从表面合金层移动到基体合金中而急剧 增加,如图7所示。表面合金层中界面附近的区域具有 层状结构(图6b)。母材保留其α相和珠光体相组织,
P 0.021
S 0.019 Si 0.41
Fe Balance
Table 2. Weight of Alloying Elements Used for Surface Alloying of Butterfly Valves 表2:用于蝶阀表面合金化的合金元素重量
Sample Binder Medium Ni (gm) Cr (gm) Fe-Mn (gm) Fe-Si (gm) Mo (gm) Powder/Area (gm/cm2)
BV1 REFCOHOL 1010 0.51 1.19 - - - 0.106
BV2 REFCOHOL 1010 0.8 1.84 - - - 0.165
BV3 NaPA Binder 0.56 2.19 0.11 0.12 0.30 0.205
alloyed layer into the base substrate alloy, as seen in Fig. 7. The area near the interface in the surface alloyed layer has a lamellar structure (Fig. 6b). The base metal retains its α and pearlite phase microstructure, and the region immediately below the interface shows primarily an α phase with some pearlite.
XRD analysis of the surface alloyed layer of the surface alloyed sample BV3 confirmed the presence of ferrite, austenite and chromium oxide (Cr2O3) in the surface alloyed layer. The presence of Cr2O3 is known to improve the corrosion resistance of the alloy. This oxide can form in ambient conditions; however, heat treatment of the alloy leads to the acceleration of the formation of oxide. 界面正下方区域主要显示含有一些珠光体的α相。 表面合金化样品BV3的表面合金层的XRD分析结 果证实了表面合金层中存在铁素体、奥氏体和氧化铬 (Cr2O3)。已知Cr2O3的存在可以提高合金的耐腐蚀 性。这种氧化物可以在环境中形成;然而,合金的热 处理会加速氧化物的形成。
硬度测量
使用维氏显微硬度测试法测量铸态下表面合金层 和母材的硬度。合金元素Ni、Cr、Mn、Si和Mo富 集表面合金层导致表面合金层硬度增加。其他研究人 员此前曾报道,在整个截面中添加Mo、Si、Cr会导 致铁基体的硬度增加、屈服强度增加0.2%和拉伸强 度增加。 样品在铸态条件下进行测试,每个样品通过横截面 进行多次测量,以确保对样品取平均值。硬度测量没 有显示表面合金层内有任何明显的分散,表明合金元 素在表面合金层中的分布非常均匀。
耐腐蚀性能
铁基合金的耐蚀性可以通过两种方式提高:(1) 通过在固溶体中加入一些热力学稳定性较高的合金元 素,如Ni和Cr,提高其电极电位,降低阳极活化,提 高其热力学稳定性;(2)通过添加Cr、Mo等元素促进 表面稳定钝化层的形成,提高其抗腐蚀能力。因此, 表面合金化导致表面合金层中Ni和Cr含量大幅增加, 可显著提高其耐腐蚀性。 此外,合金层显微组织中奥氏体含量的增加也会提
Hardness Measurements
The hardness of the surface alloyed layer and the base metal in the as-cast condition was measured using the Vicker’s microhardness test. The enrichment of the surface alloyed layer by alloying elements Ni, Cr, Mn, Si, and Mo led to an increase in the hardness of the surface alloyed layer. It has been previously reported by other researchers that the addition of Mo, Si, Cr throughout the section leads to an increase in the hardness, 0.2% proof stress, and tensile strength of the iron matrix.
The samples were tested in an as-cast condition, with each sample undergoing multiple measurements through the cross-section to ensure the average value is taken over the sample. The hardness measurements did not show any significant scatter within the surface alloyed layer, suggesting that the distribution of alloying elements in the surface alloyed layer is quite uniform.
Corrosion Resistance
The corrosion resistance of iron-based alloys can be improved two ways: (1) improve its thermodynamic stability by adding some alloying elements with higher thermodynamic stability like Ni and Cr to the solid solution to increase its electrode potential and to decrease the anodic activation, and (2) promote the formation of stable passivation on the surface and improve its resistance on corrosion reaction by adding elements like Cr and Mo. Therefore, the large increases in the Ni and Cr content in the surface alloyed layers as a result of surface alloying can significantly improve its corrosion resistance.
In addition, the rise in austenite content in the microstructure of the alloyed layer will also improve the corrosion resistance. The fine microstructure as a result of relatively rapid solidification in the surface-alloyed layer can also decrease the corro-
Fig 8. Comparison of the hardness of the surface alloyed layer and the base metal indicating a consistent increase in the ascast condition.
图8:表面合金层和母材硬度 的比较表明铸态条件增加的一 致性。
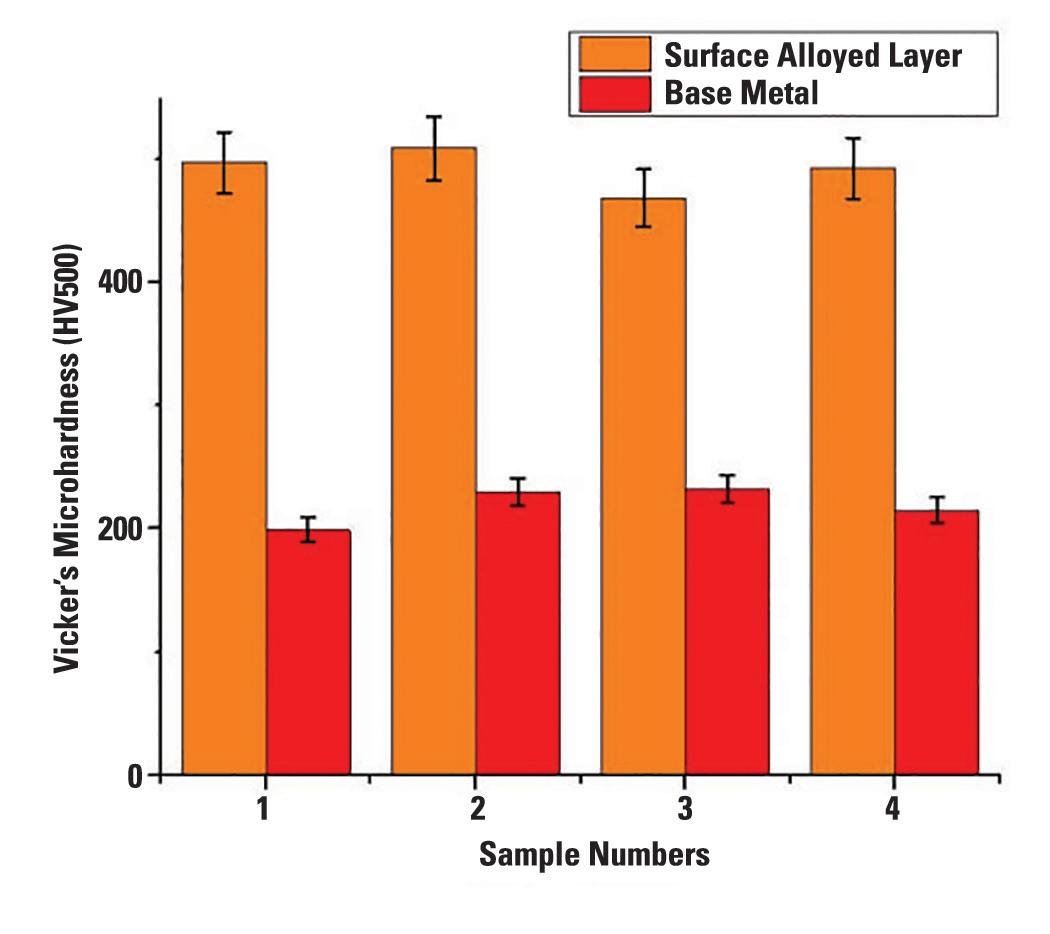
Fig 9. (a) The absence of the phase in the surface alloyed layer of surface alloyed sample BV3 after solution annealing at 850C for a period of 100 seconds (b) The presence of intermetallic phase in the surface alloyed layer of surface alloyed sample BV3 before heat treatment.
图9:(a)850℃固溶退火100秒后,表 面合金试样BV3表面合金层中不存在σ 相;(b)热处理前样品BV3表面合金的表 面合金层中存在金属间σ相。
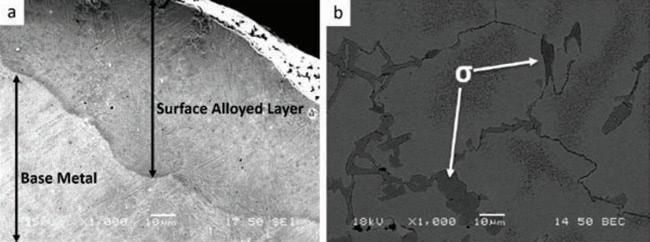
sion by the micro-cell effect.
Table 4 lists the corrosion rates of surface-alloyed butterfly valves samples and the base WCB steel. The heat-treated (normalized and tempered) surface alloyed sample shows a half corrosion rate compared to heat-treated (normalized and tempered) WCB steel. The base metal WCB steel has a higher pearlite content. Surface alloying and subsequent heat treatment transforms the microstructure to predominantly ferrite and austenite.
The as-cast microstructure of the surface alloyed layer showed the presence of intermetallic σ, which can be detrimental to the corrosion resistance of the surface alloyed layer. The solution annealing treatment led to the dissolution of the intermetallic phase, as seen in Fig. 9, which is expected to improve the corrosion resistance of the surface alloyed layer.
Applications
The novel cast surface alloying process in the study produced a surface alloyed layer enriched in several elements (including Ni Cr Mo Mn) on butterfly valve WCB steel sand castings. While the surface-alloyed WCB castings are slightly more expensive compared to WCB steel castings, they are much lower in cost than through section stainless steel (by as much as $10-$12 per lb.). The scalable and more economical techniques for coating sand molds and cores with a refractory wash containing metal and ferroalloy powder for surface alloying could include flowcoating, spray-coating, dipping and brush-coating.
This demonstrates the potential cost savings of using surface-alloyed WCB steels compared to through-section stainless steel components. It also demonstrates that surfacealloyed steel castings provide much more improved corrosion resistance, with only a marginal increase in the cost over plain WCB steel castings. This suggests several other potential applications of surface alloyed WCB castings in addition to butterfly valves, where corrosion and wear resistance higher than that of WCB steel are required. ■ 高耐蚀性。由于表面合金层中相对快速凝固而产生的精 细微观结构也可以减少微电池效应引起的腐蚀。 表4列出了表面合金化蝶阀样品和基础WCB钢的腐蚀 速率。与热处理(正火和回火)WCB钢相比,热处理( 正火和回火)表面合金样品显示出一半的腐蚀速率。母 材WCB钢珠光体含量较高。表面合金化和随后的热处理 将微观结构转变为主要是铁素体和奥氏体。 表面合金层的铸态显微组织显示存在金属间化合物 σ,这对表面合金层的耐腐蚀性是有害的。固溶退火处 理导致金属间相的溶解,如图9所示,这有望提高表面 合金层的耐腐蚀性。
应用
研究中的新型铸件表面合金化工艺在蝶阀WCB钢砂 铸件上产生了富含多种元素(包括Ni、Cr、Mo、Mn) 的表面合金层。虽然表面合金化WCB铸件比WCB钢铸 件稍贵,但它们的成本比通截面不锈钢低得多(每磅低 10-12美元)。用于表面合金化的含有金属和铁合金粉 末的耐火涂料涂覆在砂型和砂芯的技术包括流涂、喷 涂、浸涂和刷涂,这项技术可扩展,而且更经济。 这表明与全截面不锈钢部件相比,使用表面合金化 WCB钢具有潜在的成本节约优势。还表明,与普通 WCB 钢铸件相比,表面合金钢铸件具有更高的耐腐蚀 性能,成本仅略有增加。这表明除了蝶阀之外,表面合 金化WCB铸件还有其他几种潜在应用,这些应用需要有 比WCB钢更高的耐腐蚀性和耐磨性。 ■
Table 3. Chemical Composition of Surface Alloyed Layer and Interface Layer in Sample BV3 (Table 2 as Determined Using Spark Spectrometer) 表3:样品BV3中表面合金层和界面层的化学成分(表2使用火花光谱仪测定)
Elemental Composition (wt %) Cr Ni Mo Mn Si Fe Surface Alloyed Layer 23.2 6.4 3.3 1.1 0.7 Balance Interface layer 3.80 3.89 1.04 0.54 Balance WCB base metal < 0.5 < 0.5 < 0.2 < 1 0.6 Balance
Table 4. Corrosion Rate Values for Surface-Alloyed Samples and WCB 表4:表面合金样品和WCB的腐蚀速率值
Sample WCB base metal heat-treated (normalized and tempered) Normalized and tempered surface alloyed sample BV1 Corrosion Rate (mm/year) 0.12 0.06
Product News Table of Contents 产品新闻目录
MOLD, CORE & SAND PREPARATION
Fuyao Group: High-quality natural high-silica sand for environmental protection 34 福耀高品质天然高硅砂致力于环保事业 New Digital Tools Unlock Quick-Win Cost Savings For Blast Machine Operators 36 全新的数字化工具为抛丸设备操作员解锁快 速致胜的节省成本技能 Weijing Unique Auto Grinding Machine Customized For Round Castings 41
微晶独特的圆形铸件双工位自动打磨机
MELTING, POURING & HEAT TREATMENT
Energy-saving pioneer: Fuji Electric IGBT Technology 33 节能先锋:富士电机IGBT中频感应加热电炉 Success Story At Kovolis Hedvikov A.s. 40
科沃利斯•赫德维科夫公司的成功案例
The production of highly stressed castings places high demands on the inoculation technology and inoculants used. With the new generation of cut inoculants, the company offers an improved solution characterized by tighter tolerances and higher specificity.
GERMALLOY C is used to improve the sphericity of the graphite and to optimize the mechanical properties of the casting. With OPTIGRAN C, casters achieve a finer, evenly distributed A-graphite in the gray iron.
Mold inoculation is the addition of inoculant as late as possible and hence also the inoculation method in which the fading effect is reduced to a minimum. This is particularly relevant for the production of thick-walled parts. In mold inoculation, the inoculant is introduced in the pouring basin or directly into the gating system of the mold. The dissolution therefore occurs under air exclusion directly in the iron over the entire pouring time. Casted inoculation blocks such as GERMALLOY C and OPTIGRAN C should be preferably used for mold inoculation, otherwise there is a risk of flowing in of non-dissolved inoculant grains with negative consequences for the cast structure.
While serial cast parts with normal wall thicknesses of 5 to 50 mm solidify in seconds up to a few minutes in casting production, the crystallization of thick-walled, heavy castings with wall thicknesses larger than 60 mm can take hours, depending on the casting temperature. A constant inoculation effect as offered by GERMALLOY C and OPTIGRAN C is important for a good casting result. The machined surfaces guarantee a good and uniform dissolution into casting.
Thanks to the close-tolerance manufacturing process, the inoculants have high dimensional, contour and weight accuracy and are therefore also suitable for robot-assisted handling and automatic insertion into the mold.
The dimensions of the inoculations are chosen in such a way that existing core markers can generally be used unchanged as placeholders for the inoculant inserts.
For larger requirements, it is also possible to deviate from the standard dimensions within certain limits. ■
更小公差,更高特性的切块孕育剂
高应力铸件的生产对孕育技术和所使用的孕育剂 提出了很高的要求。随着新一代的切割孕育剂,公司 提供了改进的解决方案,其特点是更小的公差和更高 的特性。
GERMALLOY C用于改善石墨的球形度和优化铸 件的力学性能。使用OPTIGRAN C,铸造厂可以在灰 铸铁中获得更精细、均匀分布的A型石墨。 型内孕育是尽可能晚地加入孕育剂,因此也是孕 育衰退降到最低的孕育方法。厚大零件的生产需要 特别注意这一点。在型内孕育中,孕育剂被放入浇口 杯或直接进入铸型的内浇口。因此,在整个浇注时 间内,孕育块在无空气接触下熔解。切块孕育块,如 GERMALLOY C和OPTIGRAN C,最好用于造型铸型 孕育,否则会有未溶解的孕育颗粒流入的风险,对铸 态组织结构造成负面后果。 而常规壁厚为5-50mm的系列铸件在铸造生产 中可在几秒钟至几分钟内凝固。GERMALLOY C和 OPTIGRAN C提供的持续孕育效果对良好的铸造效果 很重要。经过加工的表面保证了孕育块在铸件中良好 而均匀的熔解。 由于采用精密制造工艺,孕育剂具有较高的尺 寸、轮廓和重量精度,因此也适合机器人辅助操作和 自动插入型腔。 孕育块的尺寸是这样选择的:现有的砂芯标记位 置通常可以不变地用作孕育块的安放处。 对于较大孕育块的要求,也可能在一定范围内偏 离标准尺寸。 ■
Fuji Electric Co., Ltd. is a comprehensive electromechanical manufacturer established in 1923, with 438,690 products. Among them, the power semiconductor IGBT, which has affected the nerves of the world in recent years, is the core device of industrial transformation, energy conservation and environmental protection, even more, it is ranked top three in the world.
富士电机株式会社,是一家成立于1923年的综合机 电类厂家,拥有438,690种产品之多;其中,近几年牵 动全世界神经的,作为产业转型、节能环保的核心器 件—功率半导体IGBT,更是排名世界前三。 富士电机的中频感应电炉从1963年开发,至今已 走过了将近60年的生产历程,基于自身半导体元器件
Fuji Electric’s intermediate frequency induction furnace was developed in 1963, and has gone through nearly 60 years history of intermediate frequency furnaces. IGBT series resonance intermediate frequency electric furnaces are developed based on the rapid development of its own semiconductor components IGBT and the advanced instantaneous control technology. Fuji Electric’s IGBT intermediate frequency induction heating furnace has the characteristics of energy saving, reliability and easy operation. It helps Fuji Electric IGBT intermediate frequency furnace to occupy nearly 70% of the Japanese market. It is widely praised by many customers in China, China Taiwan, South Korea, Southeast Asia and other regions.
Now, energy conservation, emission reduction and carbon reduction have become the development goals of the world. The Chinese government has clearly set a long-term goal of carbon peak in 2030 and carbon neutrality by 2060. The government has clearly pointed out at multiple levels that power devices, especially IGBTs, play an irreplaceable important role in the fields of energy saving and emission reduction, new energy, high-speed rail, as well as smart grids, and are the key “core” of a low-carbon economy. The development of IGBT technology is changing with each passing day. Fuji Electric began to produce the first generation of IGBTs in 1987 and now the seventh generation of IGBTs have come out, which are widely used in various fields of social development, making contributions to the development of the industry.
The advantages of Fuji’s intermediate frequency furnaces are: IGBT的飞速发展及富士高压产品先进的瞬时控制技术, 开发出了IGBT串联谐振中频电炉。富士的IGBT中频感 应加热电炉具有节能、可靠、易操作等特点,助力富士 电机IGBT中频炉在日本市场占有率接近70%,受到中 国、中国台湾、韩国、东南亚等区域众多客户的广泛好 评。 时至今日,节能减排、绿色降碳已成为全世界的发 展目标,中国政府明确制定了2030年碳达峰、2060年 碳中和的长远目标。国家在多个层面明确指出:功率 器件特别是IGBT在节能减排、新能源、高铁、智能电 网领域发挥着不可替代的重要作用,是低碳经济的关键 核“芯”。IGBT技术发展日新月异,富士电机从1987 年开始生产第一代IGBT,历经变革目前已经是第七代 IGBT,广泛应用于社会发展的各个领域,是世界排名领 先的IGBT厂家之一,为中国乃至世界的工业发展做出了 贡献。 从中频炉设备角度来说,富士电机有以下两个核心 优势:
一、节能、熔炼速度快
富士引以为傲的IGBT电源技术,区别于中频炉业内 传统的可控硅电源设计,更能实现节能且灵敏高效的要 求。IGBT电源的先进性可以有效的提高熔化效率,从 而缩短熔炼时间,降低能耗。其它如富士中频炉在设计 中基本保证线圈高度与额定金属液面持平,使有用功率 最大化,避免只通水不通电的“假线圈”带来的无谓损 耗;富士采用业内独有的一体型线圈设计,线圈密度大 大增加,从而提高了利用效率;通过技术革新,在安全 范围内尽量降低电流值,尽量避免热损等等。富士特有 的技术使得富士电机的中频感 应电炉在能耗方面处于领先水 平,每吨每小时耗电量比一般 高端电炉节能30~40度以上( 变压器一次侧测量值),为用 户节省了用电开支。
二、稳定可靠
中频炉是集高压、高温、水 冷于一体的成套设备,风险性
1. Energy saving and fast melting speed
Fuji’s proud IGBT power supply technology is different from the traditional thyristor power supply design in the intermediate frequency furnace industry, and it can meet the requirements of energy-saving, sensitive and high-efficiency. The IGBT power supply can effectively improve the melting efficiency, thereby shortening the melting time and reducing energy consumption. Besides, Fuji intermediate frequency furnaces basically ensure that the coil height is equal to the rated metal level in the design to maximize the useful power and avoid the unnecessary loss caused by the “false coil” that only passes water but does not supply electricity; Fuji adopts a unique design with integrated coil, which is greatly increased, thereby improving the utilization efficiency; through techno-
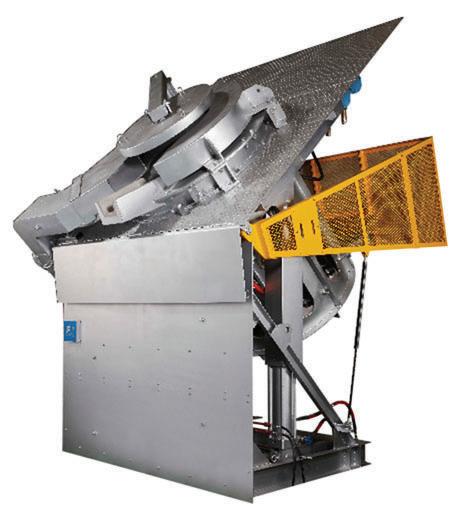
logical innovation, the current value is reduced as much as possible within a safe range, and the heat loss is avoided as much as possible. Fuji Electric’s unique technology makes its medium frequency induction furnace at a leading level in terms of energy consumption. The power consumption per ton per hour is 30-40 degrees more than that of ordinary high-end furnaces (measured on the primary side of the transformer), saving users electricity expenditure.
2. Stable and reliable
Intermediate frequency furnace is a complete set of equipment that integrates high pressure, high temperature, and water cooling. The risk is high, so that safety is definitely the first priority for intermediate frequency furnace products. Fuji Electric has not only considered complete safety protection measures in all aspects, but even some environment elements other companies have ignored, Fuji Electric will not hesitate to respond. For example, Fuji Electric’s medium frequency induction furnace adopts world-class seismic design, and the maximum seismic rating has reached Level 7 on the Richter scale. In addition, it is also equipped with a sensitive anti-furnace leakage warning system. When the furnace lining has a risk of leakage, it can issue an early warning immediately to prevent major production accidents; when the electric furnace is tilted, it is equipped with anti-falling grid and pipeline protection device; it adopts parallel coil structure design, which enhances stability and prolongs the life of the furnace lining. The coil part adopts a dust-proof and moisture-proof coil design method, which is integrally formed, so there is no need to worry about condensation due to moisture and dust. The coil is short-circuited; at the same time, the integrated structure keeps the coil refractory material strong, stable and prolongs the life of the furnace lining. The above-mentioned equipment fully considers the safety of the customer, so as to achieve reliability. ■ 较大,安全肯定是中频炉产品的第一要务。富士电 机不仅在各个环节考虑到了完备的安全保护措施, 而且连一些其它企业忽略的环境,富士电机也不惜 成本进行对应。例如富士电机中频感应电炉采用 世界一流的抗震设计,最大抗震等级达到了里氏7 级。除此以外,还配备了灵敏的防炉漏预警系统, 在炉衬有漏炉风险发生时,可第一时间发出预警, 从而防止重大生产事故的发生;在电炉倾倒作业 时,设有防落下安全栅,管道保护装置;其采用的 平行线圈构造设计,稳定性增强,炉衬寿命延长, 线圈部分采用抗尘、防湿的线圈设计方式,一体成 形,不必担心因存在水分而结露,以及由粉尘引起 线圈短路;同时,一体结构保持线圈耐火材料牢 固,稳定与延长炉衬寿命,以上种种设备充分为客 户安全考虑,从而达到可靠。
Fuyao Group was founded in Fuzhou, China in 1987. It is a large multinational company specializing in the manufacture of automobile safety glass and industrial technical glass. After more than three decades of development, Fuyao Group has established 57 research, production and sales bases in 11 countries around the world and 16 provinces and municipalities in China. The global market share of its product exceeds 28%, and the domestic market share exceeds 68%, which has become a business card for Chinese manufacturing to go global.
Fuyao owns five major silica sand deposits in Wenchang in Hainan, Benxi in Liaoning, Tongliao in Inner Mongolia, Xupu in Hunan, and Zunyi in Guizhou. A full coverage mineral source layout spanning east-west and north-south has been constructed, with diverse and high-quality silica sand resources such as sedimentary sand, aeolian sand and high-quality sandstone sand.
福耀集团1987年成立于中国福州,是专注于汽车安 全玻璃的大型跨国集团。经三十余年发展,福耀集团 在全球11个国家和中国16个省区市设立57处研产销基 地,产品全球市场占有率超28%,国内市场占有率超 68%,成为中国制造走向世界的一张名片。 福耀拥有海南文昌、辽宁本溪、内蒙通辽、湖南溆 浦、贵州遵义五大硅砂矿,构建起横跨东西、纵贯南北 的全覆盖式矿源布局,具备沉积砂、风积砂及优质砂岩 砂等多样性、高品质硅砂资源。 得天独厚的矿源优势,是福耀硅砂的品质保证。截
The unique advantage of mineral resources is the quality assurance of Fuyao silica sand. Up to now, Fuyao has developed high-performance, high-stability, high-reusability high-silicon scrubbing sand, roasting phase change sand, 3D printing sand and other series, which can be widely used in different processes in cast steel, steel and other non-ferrous metals, which has significantly reduced overall production costs and improved quality and efficiency for customers.
Fuyao High Silicon Scrubbing Sand
Fuyao silica sand with a silicon content of over 99% can withstand high temperature casting of up to 1750°C, fully satisfying customers’ physical and chemical indicators such as particle size, angle coefficient, SiO2 content, loss on ignition, mud content, acid consumption value, etc.. It is the best solution for manufacturing precision molds, core castings, high wear resistance and high corrosion resistance castings, as well as other special assembly parts.
Fuyao roasting phase change sand
The new high-temperature roasting process is adopted to reasonably control the phase change expansion of silica sand, which greatly improves the near-net forming accuracy of castings. The comprehensive performance and some indicators have reached or surpassed similar international silica sand.
Fuyao 3D printing sand
On the basis of high-quality raw sand, the performance of silica sand is further improved through advanced technology, showing the characteristics of customized particle size, high concentration rate, and lower acid consumption. During the printing process, the sand laying is smooth, without sand leakage or sand pulling, and the surface quality of the molded parts is high.
Fuyao relies on the nationwide mining source layout and automobile glass transportation and sales network to minimize the transportation distance between the mine source and the client, and provide customers with fast transportation, JIT (Just In Time) service.
Regarding sustainable development as the development keynote of the silica sand industry, Fuyao promises to “provide customers with high-quality natural high-silica sand with stable mineral resources, stable quality and stable supply”, and is committed to building a higher level of resourcesaving environment-friendly enterprise. ■ 至目前,福耀已开发出高性能、高稳定性、高复用 性的高硅擦洗砂、焙烧相变砂、3D打印砂等丰富品 类序列,可广泛应用于铸钢、铸铁及其它有色金属 的不同工艺用砂需求,显著降低综合生产成本,为 客户提质增效。
福耀高硅擦洗砂
含硅量超99%的福耀硅砂,能够抵受最高1750°C 的高温浇铸,充分满足客户在粒度粒径、角形系 数、SiO2含量、烧失量、含泥量、酸耗值等理化指 标需求,是制造精密模具、核心铸件、高耐磨、高 耐蚀件等特殊装配件的最佳解决方案。
福耀焙烧相变砂
采用全新高温焙烧工艺,合理控制硅砂相变膨胀 量,大幅提升铸件近净成形精度,综合性能及部分 指标已达到或赶超国际同类硅砂。
福耀3D打印砂
在优质原砂基础上,通过先进工艺进一步提升硅 砂性能,呈现粒度定制化、高集中率、更低酸耗等 特点。打印过程中铺砂平整流畅,无漏砂、拉砂现 象,成型件表面质量高。 福耀依托覆盖全国的矿源布局及汽车玻璃运销网 络,最大限度缩短矿源地与客户端运输距离,以最 快运输速度、最优供货方案、最低物流成本向客户 提供快捷运输、JIT(Just In Time)计时服务。 福耀以可持续发展作为硅砂产业的发展基调,承 诺“为客户提供矿源稳定、质量稳定、供应稳定的 高品质天然高硅砂”,致力于建设更高水平资源节 约的环境友好型企业。 ■
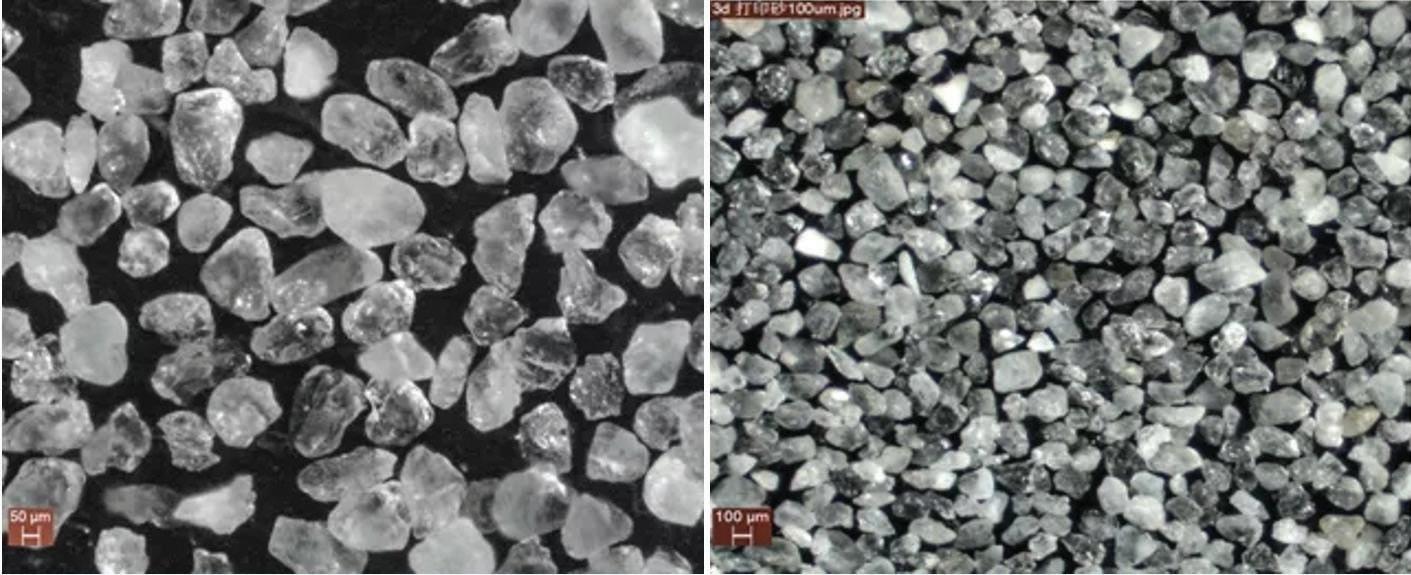
New Digital Tools Unlock Quick-Win Cost Savings For Blast Machine Operators 全新的数字化工具为抛丸设备操作员解锁快速致胜的节省成本技能
Wheelabrator has launched new digital tools that were developed specifically to help customers reduce cost around three key areas of the blast process: • abrasive consumption • energy use • maintenance and downtime
The tools were built using Norican’s Monitizer software and NoriGate hardware, both already proven on equipment at sister companies DISA and StrikoWestofen, and are available for many existing and all new Wheelabrator machines.
Heinrich Dropmann, Senior Vice President Global Wheel at Wheelabrator, explains: “Digital technologies allow us to make the blast process more transparent than ever before and optimise it accordingly. We’ve been working with a select group of pilot customers to identify the applications that would make the biggest difference to their productivity and profitability and quickly zeroed in on these three.” Tests showed that tackling abrasive consumption alone, using digital analysis and monitoring, can unlock €200-250 in annual savings per kilowatt blast power installed. For a typical hanger-type machine with four 11 kW blast wheels, this means up to €10,000 saved per year. Over the course of 20 years, savings generated by this one digital tool could pay for a new machine. Heinrich continues: “The digital tools we’ve developed enable customers to really pinpoint the parameters that are driving abrasive consumption, energy use and wear in their specific operational setting – and then do something about it. They can very quickly get a much better handle on their blasting cost, without impacting the volume or quality of their outputs – or even improving them.” The three tools can be deployed as standalone solutions or plugged into a wider Industry 4.0 system – be it from Norican, customer-built or from another supplier. The NoriGate data gateway is used to extract data from each machine – from the control system and from sensors – while the Monitizer software collects, visualises and analyses it in customizable dashboards. Heinrich explains the Wheelabrator approach: “This is not about collecting data for the sake of it. As experts on the blast process, we can select the right data points to track, so we can combine them meaningfully and in a way that gives us insights into what’s running at optimum and what isn’t. It gives customers the data they need to continuously improve the process and save some money along the way.”
Reducing abrasive consumption – a significant cost factor
Abrasive costs represent a major part of the overall running cost of a blast machine and the volume of abrasive going through the machine, relative to the blast result
维尔贝莱特推出了新型数字工具,专门用于帮助 客户降低抛丸工艺中三个关键领域的成本: • 丸料损耗 • 能源利用率 • 维护和停机时间 这些数字化工具使用诺瑞肯的Monitizer软件和 NoriGate硬件构建,这两者都已经在集团旗下姐妹 公司迪砂和史杰克西的设备上得到验证,并可用于 许多现有及所有新型维尔贝莱特设备。 维尔贝莱特全球抛丸高级副总裁Heinrich Dropmann说:“数字技术让我们能够使抛丸工艺比以往 任何时候都更加透明,并相应地对其进行优化。我 们一直在与一组精选的试点客户合作,以确定哪些 应用会对其生产力和盈利能力产生最大影响,并迅 速将注意力集中这三款应用上。” 测试表明,单独解决磨料损耗问题,使用数字分 析和监控,每千瓦抛丸功率,每年可以节省200250欧元。对于带有4个11kW抛丸设备的典型悬挂 式机器,这意味着每年最多可节省10,000欧元。在 20年的时间里,这个数字化工具节省的费用可以用 于购买新机器。 Heinrich 继续说道:“我们开发的数字工具使客 户能够真正确定在其特定运行环境中丸料损耗、能 源利用率和磨损的参数,然后采取相应措施。他们 可以非常迅速地更好地控制其抛丸成本,而不影响 其产量或质量。” 这三款工具可以作为独立的解决方案进行部署, 也可以插入到更广泛的工业4.0 系统中——无论是来 自诺瑞肯旗下品牌、客户自建还是来自其他供应商 的。NoriGate数据网关用于从每台设备(从控制系 统和传感器)提取数据,而 Monitizer软件则在可定 制的仪表板中收集、可视化和分析数据。 Heinrich继续说道:“这不是为了收集数据 而收集数据。作为抛丸工艺的专家,我们可以选择 正确的数据点进行跟踪,这样我们就可以将它们有 意义地结合起来,让我们洞悉哪些是以最佳状态运 行,哪些并没有以最佳状态运行。它为客户提供了 所需的数据,以不断改进工艺,并在此过程中节省 一些资金。”
achieved, is a key determinant of wear inside the machine. Using less abrasive to achieve the same blast result in the same time therefore is the holy grail of blast process optimisation.
And while modern blast machines have evolved considerably to improve this equation, real-time tracking and analysis of abrasive throughput and other process parameters can push this further. Yet again, this is not something that can easily be done without digital help. Wheelabrator’s first new digital tool gives an accurate picture of abrasive use over time and relates it to other metrics, so root causes of high use can be identified quickly. Even complex or more subtle causes of increased abrasive throughput can be unpicked and resolved. The costs of monitoring and analysis are low compared to manual methods.
In numbers: For a hanger-type machine with four 11kW blast wheels, the tool helped reduce abrasive consumption (and spend!) by 17% and cycle time by 20%. On a roller conveyor machine with six 15kW turbines, through-feed speed could be increased by 20% and abrasive spend reduced by 8%. Reducing or optimising abrasive consumption doesn’t just save money on abrasive, it also reduces energy use. Less wear means less maintenance and reduced spend on wear parts – by around 10%, according to Wheelabrator estimates.
Saving energy – not as simple as it sounds
Shot blast machines – wheel blast ones in particular – use a lot of energy due the power required to accelerate the abrasive. Bringing that energy consumption down while maintaining a stable blast process could unlock savings and support sustainability agendas. However, most blast machine users do not and cannot currently record energy use of their machines alongside other process parameters to identify periods of high usage or unproductive time. Without this data, there is no way of improving a machine’s energy performance in a targeted way. The second of the three digital tools from Wheelabrator does just that – it tracks the right parameters to strategically optimise standby and idle times, turbine rpms and more. This means operators and managers can instantly see if their machines are using unusually high amounts of energy, find the cause and tweak the process. Over time, the running of the machine can be adapted for ever better energy efficiency without negatively affecting blast results or throughput (in fact, both may be improved as a side-effect of energy reduction efforts). In numbers: Just by reducing idle time by 1 hour per day, the tool was able to unlock €14,000 annually in energy cost savings for a roller-conveyor machine with eight 45kW blast wheels. Doing the same on a less powerful pass-through monorail machine with eight 15kW blast wheels still achieved a saving of €4,000 per year. Both machines were operating in three shift 240 days per year.
减少丸料消耗——一个重要的成本因素
丸料成本是抛丸机总体运行成本的主要部分,通 过抛丸机的丸料量相对于达到的抛丸效果,是决定抛丸 机内部磨损的关键因素。因此,使用较少的丸料在相同 的时间内达到同样的抛丸效果,是抛丸工艺优化的“圣 杯”。 虽然现代抛丸机的发展已经大大改进了这一方程式, 但对丸料产量和其他工艺参数的实时跟踪和分析,可以 进一步推动这一进程。然而,没有数字化的帮助,这不 是一件容易做到的事情。 维尔贝莱特的第一款新型数字工具,可以准确显示 丸料随时间推移的使用情况,并将其与其他指标联系起 来,因此可以快速确定高用量的根本原因。即使是复 杂或更微妙的原因导致丸料用量增加,也可以剖析和解 决。与手动操作相比,监测和分析的成本很低。 数据:对于带有4个11kW抛丸器的悬挂式机器,该 数字化工具帮助将磨料损耗(和花费)减少了17%,循 环时间减少了20%。在配备六个15kW涡轮机的滚筒输 送机上,通过进料速度可提高20%,磨料损耗减少8% 。减少或优化磨料损耗不仅可以节省磨料成本,还可以 减少能源使用。维尔贝莱特预计,更少的磨损意味着维 护和磨损部件的支出减少约 10%。
节省能源——不像听起来那么简单
抛丸机(尤其是抛丸器)由于加速丸料所需的动力, 会消耗大量的能源。在保持稳定的抛丸工艺的同时降低 能源消耗,可以实现节约,并支持可持续发展议程。 然而,大多数抛丸机用户目前没有也不能将其设备的 能源使用情况与其他工艺参数一起记录下来,以确定高 使用率期间或非生产时间。没有这些数据,就无法有针 对性地提高设备的能源性能。 维尔贝莱特第二款数字工具中的第一款就可以实现这 一点——它跟踪正确的参数,以战略性地优化待机和闲 置时间、涡轮转速等等。这意味着操作人员和管理人员 可以立即看到其设备是否在使用异常高的能源,找到原 因并调整工艺。随着时间的推移,设备的运行可以适应 更高的能源效率,而不会对抛丸效果或产量产生负面影 响(事实上,这两者都可能可以作为节能工作的附带结 果而得到提升)。 数据:仅通过每天将闲置时间减少1小时,数字化 就能够为配备8个45kW抛丸机的滚筒输送机每年节省 14,000欧元的能源成本。在配备8个15kW抛丸机的功 率较小的直通式单轨设备上执行相同操作后,每年仍可 节省4,000欧元。两台机器实行每年240天,每天三班 的运行。
Taming a violent beast – preventive maintenance
Lastly, the inside of shot blast machines is a violent place. Wear comes with the territory. As with all equipment, keeping unplanned downtime to a minimum saves money and resources – as well as ensuring production targets and deadlines are met. Yet monitoring operating status and condition of a shot blast machine is still a manual, occasional process. Here too, digital can help. By tracking things like turbine vibration levels, pressure differentials in filters and key performance metrics, Wheelabrator’s third digital tool can present a real-time picture of the machine condition and offer an early warning system for wear and drops in performance. This enables preventative maintenance at the optimum point, not too soon, not too late, preventing unscheduled downtime without overspending on parts. In numbers: The tool helps prevent sudden or undetected parts failure, which causes expensive damage. For example, pre-empting blade breakage through early detection and timely, planned exchange cost €1,500 at a reference customer, whereas letting the blade break incurs costs of at least €4,500, depending on the extent of the damage. Blocked filters at one customer resulted in extra cost of €7,500 for clean-up and increased wear. An extreme example of a preventable fault are cracked filter cartridges, which allow fine dust to escape unnoticed and settle on surrounding machinery or even further afield. On one occasion, ferrous dust damaged the paint on cars parked in an adjacent carpark. The cost for repainting exceeded €25,000.
It’s only the beginning
The three tools were designed with quick payback for customers in mind, solving the most common issues and cost drivers machine owners are faced with. But these very specific applications are only the start of the journey. NoriGate and the Monitizer platform are highly flexible, powerful and adaptable. What customers can do with the system can be evolved and expanded over time, with more tools and capabilities already in the pipeline, backed by Norican’s commitment to digital innovation.
Heinrich concludes: “Customers who start collecting blast process data now, using one, two or all three of our new tools, are at the same time building up their digital database of historical data that can be analysed in new ways in future. So even if you want to take things slowly, you will have a wealth of data to learn from as new capabilities, like AI and automated process intervention, become available. It’s a highly sensible, pragmatic way of approaching all things digital. And if you’re ready for more straightaway, we invite you to get in touch, so we can show you what we’re working on!” ■
For more information on Monitizer please visit https://www.wheelabratorgroup. com/en-gb/equipment/digital-solutions/monitizer for more on Wheelabrator’s digital offering. 预防性维护
最后,抛丸机内部运行非常剧烈。磨损在所难免。与 所有设备一样,将计划外停机时间保持在最低限度,可 以节省资金和资源。然而,监测抛丸机的运行状态和条 件仍然是一个手动、偶发的过程。 在这方面,数字化也可以提供帮助。通过跟踪涡轮振 动水平、过滤器压差和关键性能指标,维尔贝莱特的第 三款数字工具可以实时呈现设备状况,并提供磨损和性 能下降早期预警系统。这样就可以在最佳时间点进行预 防性维护,不会太早,也不会太晚,防止计划外停机, 而不会在部件成本上超支。 数据:数字化工具有助于防止突发或未检测到的零件 故障,这会导致昂贵的损坏成本。例如,在推荐的客户 中,通过早期检测和及时、有计划的更换预防刀片破损 的成本为1,500欧元,而让刀片破损至少会产生4,500欧 元的成本,具体取决于损坏的程度。一位客户的过滤器 堵塞导致清理费用和损耗增加7,500欧元。可预防故障 的一个极端例子是破裂的过滤器滤芯,它会使细小的灰 尘在不被注意的情况下逸出并落在周围的机器上,甚至 更远的地方。有一次,铁粉尘损坏了停在相邻停车场的 汽车油漆。重新粉刷的费用超过了25,000欧元。
这仅仅只是开始...
这三款工具的设计考虑到了为客户提供快速的投资回 报,解决了设备所有者所面临的最常见问题和成本驱动 因素。但这些非常具体的应用只是旅程的开始。
NoriGate和Monitizer平台具有高度的灵活性,功 能强大,适应性强。在诺瑞肯对数字创新的承诺的支持 下,随着更多的工具和功能已经在开发之中,客户可以 利用该系统所做的事情可随着时间的推移而不断发展和 扩展。
Heinrich Dropmann总结道:“现在使用我们的一 款、两款或全部三款新型工具开始收集抛丸工艺数据的 客户,同时也在建立其历史数据的数字数据库,可以在 将来以新的方式进行分析。因此,即使您想慢慢来,随 着 AI 和自动化流程干预等新功能的出现,您也会有大 量的数据可供学习。数字化处理是一种非常明智、务 实的方式。如果您已经准备好马上开始,我们邀请您与 我们联系,这样我们就可以向您展示我们正在进行的工 作!” ■
有关 Monitizer及Wheelabrator数字产品的更多信息,请访问https:// www.wheelabratorgroup.com/en-gb/equipment/digital-solutions/ monitizer
Success Story At Kovolis Hedvikov A.s. 科沃利斯•赫德维科夫公司的成功案例
Introduction to our Company
KOVOLIS HEDVIKOV a. s. was founded as ironworks in 1816. In 1930, Polak’s patent for a cold chamber machine was purchased, and the company became the leading foundry in HPDC in the Czech Republic.
KOVOLIS HEDVIKOV a. s. is a family-owned, highpressure die casting foundry of aluminium alloys with a long and rich history. It offers its customers complete solutions to their needs, including but not limited to the complex development of parts, design, and production of tools, production of castings, including mechanical machining, surfacing, subassembly, and welding if required. The company currently employs over 800 workers. Thanks to their skill and hard work, it reaches an annual production level of over 12,000 metric tons and sales of over € 80 million.
The high level of automated production, usage of new technologies, and a sharp focus on the automotive industry help rank KOVOLIS HEDVIKOV a.s. among the most prominent foundries on the Czech and European markets.
Mainly Product Groups
KOVOLIS HEDVIKOV a.s. serves the following areas of the automotive industry: Powertrain, Brake Systems, Thermal Control, Turbo Chargers, Drive Systems, Brackets, AC compressors, Belt tensioners, Steering systems, and others. Seven different, both hypo and hypereutectic alloys, are melted in 10 melting furnaces with a total melting capacity of over 10 tons/hour. Casting runs on fully automated die casting cells with real-time shot-controlled casting machines, equipped by vacuum-assisted casting, jet cooling and squeeze, subsequent operations are also partially automated. The majority of castings are machined on a number of milling and turning machines, including special dedicated machines, and further proceeded by surface finish, subassembly, and welding (EBM and FSW).
Vision of Nowadays Industry
KOVOLIS HEDVIKOV a.s. tracks and follows the current trends in the automotive industry, offers their customers the parts with high complexity, reduced weight, improved functionality, and also special parts for hybrid and electric vehicles. Further development is forecasted as well. That is the reason why KOVOLIS HEDVIKOV a.s. introduced the semisolid casting, rheocasting method SEED, in 2013. Nowadays, it is beginning to use friction stir welding technology. As a point appreciated by our customers, we are able to fully develop parts just based on functional volume, including finite element calculations, prototypes manufacture and physical tests. Although KOVOLIS HEDVIKOV a.s produces a considerable amount of parts that are presented both in internal combustion engine vehicles and electric
公司介绍
科沃利斯•赫德维科夫公司成立于1816年,前身 是钢铁厂。1930年,公司购买了Polak专利冷室压铸 机,成为捷克共和国高压压铸领域的领先铸造厂。 科沃利斯•赫德维科夫公司是一家历史悠久的铝合 金高压压铸家族企业。公司为客户提供满足其需求 的完整解决方案,包括但不限于复杂零件的开发、 模具的设计和生产、铸件的生产,以及机械加工、 表面处理、装配和焊接等。 该公司目前拥有800多名员工。由于他们的技术 和努力,铸件年产量达到12,000多吨,销售额超过 了8000万欧元。 高水平的自动化生产、新技术的使用以及对汽车 行业的高度关注有助于将科沃利斯赫德维科夫公司 成为捷克和欧洲市场最著名的铸造企业之一。
主要产品
科沃利斯•赫德维科夫公司服务于汽车行业的相关 领域:动力总成、制动系统、热控制、涡轮增压器、 驱动系统、支架、空调压缩机、传动带张紧器、转向 系统等。7种不同的亚共晶和过共晶合金在10个熔炼 炉中熔炼,总熔炼能力超过10吨/小时。铸造过程在 全自动压铸单元上运行,配备实时压射系统的铸造设 备、真空辅助铸造、喷射冷却和挤压设备,后续操作 也实现部分自动化。大多数铸件在多个铣床和车床上 进行加工,包括专用设备,并进一步进行表面处理、 分装和焊接(包括EBM和FSW)。
行业前景
科沃利斯•赫德维科夫公司跟踪并紧随汽车行业 的当前发展趋势,为客户提供复杂程度高、重量更 轻、功能更完善的零件,以及用于混合动力和电动 汽车的特殊零件。同时也对未来发展做了预测。这 就是为什么科沃利斯•赫德维科夫公司于2013年引进 了半固态铸造、流变铸造法SEED,现在已采用了搅 拌摩擦焊接技术。公司能够仅仅基于功能体积实现
vehicles as well (e.g. AC compressors, steering systems …), the company is fully aware that projects for electromobility are important for the future, even though it is hard to say what the real share of electric vehicles in the following years will be. Parts for independent heating have been in the company portfolio since 1996. In 2012, we started making prototypes of heat exchangers for electric independent heating for plug-in-hybrids and electric vehicles and went to serial production in 2015.
The Case Study
A heat exchanger is made of two castings welded together by electron beam welding. Welding is made both by butt weld and overlap weld. For good heating efficiency, the heat-transmitting surface must be of perfect surface quality without any flow mark, etc. Finally, the whole assembly is leak tested by helium high pressure. To combine excellent inner quality with a perfect surface, a standard vacuum system is not enough.
Why the choice of fondarex as partner for vacuum?
That is the reason why KOVOLIS HEDVIKOV a.s. has decided to use the Fondarex HighVac Premium machines for this product. The measurement showed a considerable increase of vacuum level in the die, which was confirmed by CT scans, cuts, and finally by welding results. Transmitting surface quality has increased, and the problems with flow marks and small blisters disappear. Moreover, the Fondarex HighVac Premium machine offers very good process control and parameter check for process stability and repeatability. ■ 零件的完全开发,包括有限元计算、原型制造和物理测 试,因此受到客户的赞赏。科沃利斯赫德维科夫公司 生产了大量用于内燃机车和电动汽车的零件(例如空调 压缩机、转向系统),但该公司充分意识到电动汽车项 目对未来很重要,尽管很难预测未来几年电动汽车的真 正份额是多少。 自1996年以来,独立的加热系统一直包含在公司产 品组合中。2012年,公司开始制造用于插电式混合动 力汽车和电动汽车的独立电加热热交换器的原型,并于 2015年开始批量生产。
案例研究
热交换器由两个铸件通过电子束焊接而成。焊接分为 对接焊和重叠焊接。为了获得良好的加热效率,传热表面 必须具有完美的表面质量,没有任何焊接流痕。最后,整 个组件通过氦高压进行泄漏测试。将卓越的内在品质与完 美的表面质量相结合,标准的真空系统是不够的。
为什么选择方达瑞作为真空系统合作伙伴?
科沃利斯赫德维科夫公司决定采用方达瑞的HighVac Premium高真空系统。测量结果表明,模具中的 真空度显著增加,CT扫描、切割和焊接结果证实了这 一点。传输表面质量提高、流痕和小水泡问题消失。 此外,方达瑞HighVac Premium高压真空系统为工艺 稳定性和可重复性提供了非常好的过程控制和参数检 查。 ■
Weijing Unique Auto Grinding Machine Customized For Round Castings 微晶独特的圆形铸件双工位自动打磨机
Customized For Perfectly Circular Castings. Usually The Place Where You Need To Grind The Parting Line And End Gate Projection In Your Round Castings
Earlier foundry men used a robot fettling station for this application. Robot is quite limited when using many circular parts. A lot of technical expertise is required to program different sizes each time.
A simpler machine, lower in cost and very versatile is Weijing two axis grinding machine which could be with two grinding stations needing only one operator to load and unload the part.
This loading, unloading can also be integrated with a simple pick and place robot later. Usually offered with manual loading and unloading of part.
Diameter variation is sensed by the machine. 3 grinding models already inbuilt for foundries to select. PLC programming is much more simple than robotic programming.
We have other features like pneumatic holding of part,
圆形铸件上,您通常需要打磨合模线和浇口端部。微 晶圆形铸件双工位打磨机,为圆形铸件完美量身定制。 早期的铸造工人在此领域应用中使用了机器人打磨 站。机器人在使用许多圆形零件时非常有限。每次编程 不同的尺寸都需要大量的技术专长。 微晶两轴打磨机,是一种更简单、成本更低且用途广 泛的机器,它可以配备两个打磨站,只需要一个操作员 来上下料。 这种打磨方式,也可以与自动化流水线集成。上下料 都可以自动化操作完成。 机器检测直径变化。已内置3种打磨模型供铸造厂选 择。 PLC编程比机器人编程简单得多。 我们还有其他特色功能,例如铸件的气动保持、打磨 过程中铸件液压旋转、砂轮补偿组合,内置七个传感器 以进行各种运动检测。
hydraulic rotation of parts during grinding, wheel wear composition with seven sensors in built for various movements.
Diamond wheels made by Weijing, lowers repetitive cost of wheel and can be used for steel castings too. A simple tool for circular parts needing Outer diameter grinding maximizing outputs and releasing bottleneck from the fettling grinding area. Shorter pouring to dispatch time, reduces foundry inventory drastically.
A handy machine a foundry badly needs now, comes at an attractive price? Any requirements on the castings?
First, the casting should be absolute round, not looks like circular.
Second, the grinding places should be at same level on the round surface of the castings.
Third, the casting weight should be less than 30 kg, the casting diameter should be between 107 mm to 340 mm, the casting height should be lower than 170 mm. ■
Round Casting Grinding, Why Not Weijing 2 Axis Grinder? Watch the video on Youtube at https://www.youtube.com/watch?v=GO4FbAgQIyE For more details about Weijing Grinding Machines, visit Weijing website at www. weijingsz.com
微晶提供的金刚石砂轮,降低了砂轮的重复成本,也 可用于铸钢件。一种用于需要外径磨削的圆形零件的简 单工具,可最大限度地提高产量并从修整磨削区域释放 瓶颈。更短的浇注到发货时间,大大减少了铸造库存。 铸造厂现在急需的便携式机器,价格诱人吗? 对铸件有什么要求吗? 首先,铸件应该是绝对的圆形,而不是看起来像圆形。 其次,磨削处应在铸件圆面上的同一水平面上。 第三,铸件重量应小于30公斤,铸件直径应在107毫 米至340毫米之间,铸件高度应低于170毫米。 观看Youtube上视频https://www.youtube.com/ watch?v=GO4FbAgQIyE ,感受效率! 圆形铸件打磨,为何不考虑微晶? 你假如有兴趣了解更多微晶打磨机信息,请访问微晶 官网或者通过以下方式联系我们。谢谢您的阅读。 ■
网站:www.weijingsz.com 电话:+86 512 6610 2545 手机/微信:+86 153 0612 4775 邮箱: roc.hang@weijingsz.com
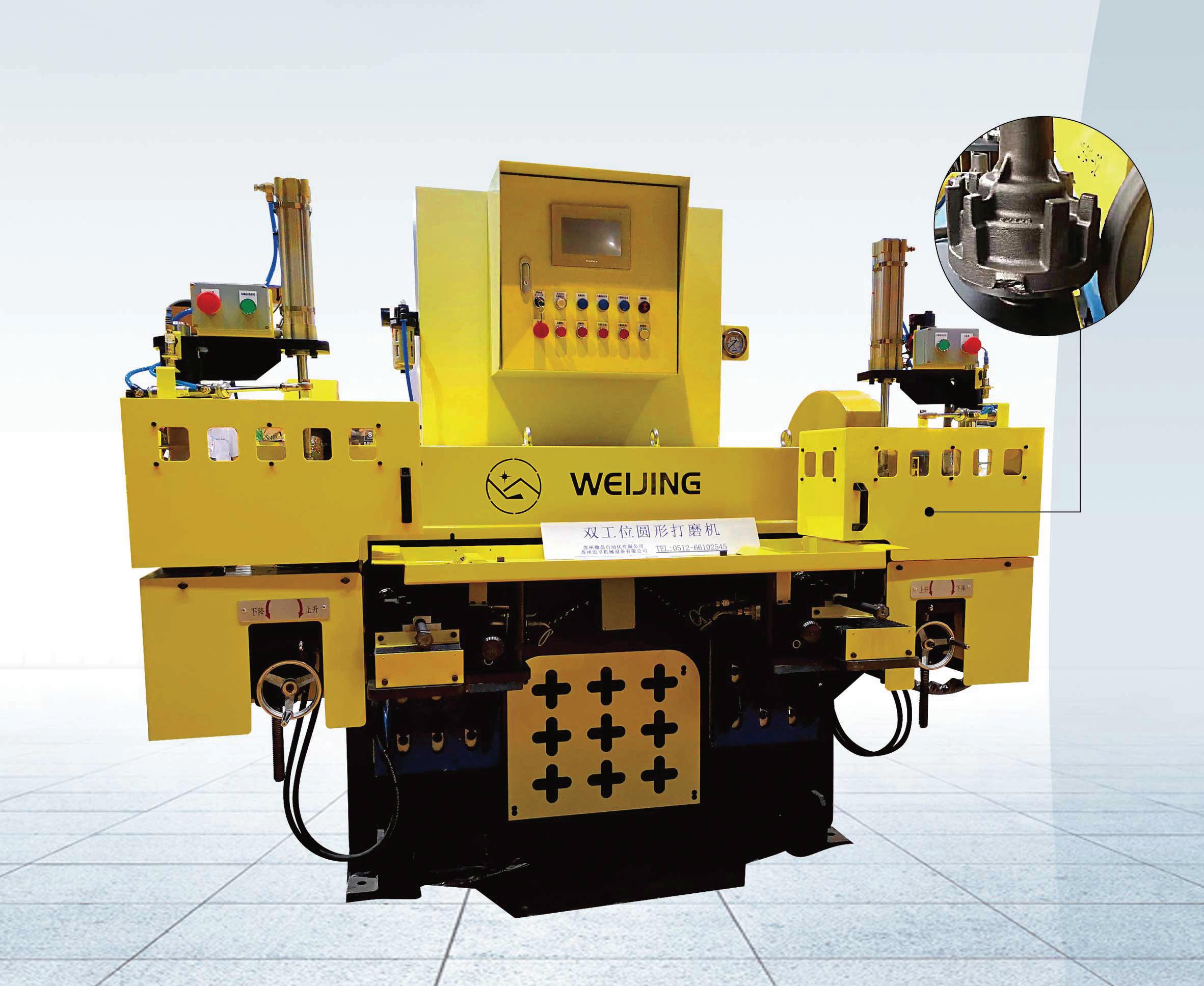