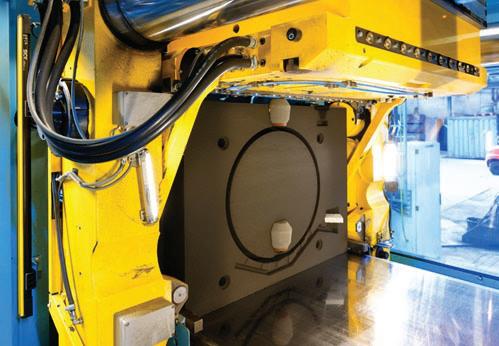
7 minute read
New DISAMATIC D5 completes foundry modernisation at LEDA
Ningbo Beilun is an important step for MAGMA to better serve their local customers, and substantially facilitate technical support in Ningbo and surrounding areas. MAGMA will adhere to its original vision: committed to casting excellence. Together with their partners, MAGMA will contribute to the development of the local economy as well as support the metal casting industry. ■
6月30日,迈格码举行了宁波分公司开业庆典仪 式。在宁波北仑开设新办事处是迈格码更好地服务当 地客户的重要一步,将极大地促进宁波及周边地区的 技术支持。迈格码将秉承其最初的愿景:致力于铸造 卓越。迈格码公司将与合作伙伴一起支持铸造行业的 发展,为当地经济发展做贡献。 ■
Advertisement
New DISAMATIC D5 completes foundry modernisation at LEDA 新款DISAMATIC D5完美成就了LEDA公司现代化铸造厂
High-end domestic stove and fireplace brand and foundry LEDA Werk GmbH & Co KG in Leer, Northern Germany, has commissioned a DISAMATIC D5 moulding line from DISA. It completes a programme of significant investment that saw LEDA’s foundry operations modernised from the ground up. It’s the first machine in the new DISAMATIC D5 range to be delivered to a customer.
Installation and commissioning were completed on schedule between December 2020 and January 2021, despite both the LEDA and DISA teams having to work around coronavirus lockdown and travel restrictions in Denmark and Germany.
德国北部利尔市的高端家用炉灶和壁炉制造商LEDA Werk GmbH & Co KG从迪砂采购了DISAMATIC D5造 型线。这是一个高明的决策,同时也是一项重大的投资计 划,使LEDA公司的铸造业务从一开始就实现了现代化。 这是首台交付给客户的全新DISAMATIC D5造型设备。 尽管LEDA团队和迪砂团队都不得不面对丹麦和德国的 新冠疫情引起的封锁和旅行限制,但安装和调试工作仍按 计划在2020年12月至2021年1月期间完成。
关于LEDA铸造厂:小批量、高品质
LEDA在利尔生产铸件已有近150年的历史。长期以 来,迪砂的成型设备一直是LEDA获得成功的一部分,第 一台DISAMATIC成型机于1977年投入使用。 该铸造厂主要生产自有品牌的家用壁炉和炉灶零件, 也包括更广泛的铸件生产、加工。公司对铸造工艺的坚 定承诺甚至构成LEDA以消费者为导向的营销组成,铸造 工艺的质量和标准是利尔团队的骄傲。 这就是为什么在过去十年中,LEDA持续进行着现代 化改造,投资于新的熔炼和混砂设备,并在2019年用 DISAMATIC D1替换了两条造型线中较小的一条,而现 在又用DISAMATIC D5替换了较大的一条。
Folkmar Ukena,LEDA营运总监说道:“高效和高 质量的铸件生产对我们来说至关重要。我们的生产规模 较小,所以我们需要造型线 提供非常稳定的工艺,即多 次更换型板。DISAMATIC 造型线从第一个铸型开始就 提供一致、可重复、高质量 的产品,这正是我们所需要 的。” 铸造厂经理Rochus Hiller 兴奋不已,他说:“通过这
About the foundry: highest quality in small series
LEDA has been producing castings in Leer for nearly 150 years. Moulding equipment from DISA has long been a part of the LEDA success story, with the first DISAMATIC moulding machine beginning service in 1977.
The foundry mainly produces domestic fireplace and stove parts under its own brand, but also acts as a jobbing foundry covering a broad range of castings. Its strong commitment to the casting process even forms part of LEDA’s consumerfacing marketing, and the quality and standard of the casting process is a source of pride for the team in Leer.
That is why, over the last decade, LEDA has been in continuous modernisation mode, investing in new melting and sand mixing equipment, as well as replacing the smaller of its two moulding lines with a DISAMATIC D1 in 2019 and now the larger one with a DISAMATIC D5.
Folkmar Ukena, Managing Director at LEDA explains: “Efficient and high-quality casting production is key for us. We produce in small series, so we need moulding lines that deliver an extremely stable process despite multiple pattern changes per shift. DISAMATIC moulding lines deliver consistent, repeatable and high quality right from the first mould – exactly what we need.”
LEDA use the automatic core setter not just to place cores but also exothermic risers and filters. LEDA使用自动下芯机不仅可以 放置芯子,还可以放置发热冒口 和过滤片。

LEDA Werk mainly produces domestic fireplace and stove parts like this one, but is also a jobbing foundry.
Rochus Hiller, Foundry Manager, is thrilled: ”With this latest upgrade, we have now replaced all our vertical moulding machines with the latest D-series DISAMATICs and have future-proofed our processes. The investment in new state-of-the-art equipment has enabled us to reduce our operating and maintenance costs, improve our energy costs and achieve high machine availability.”

LEDA Werk主要生产家用壁炉和炉灶零 件,也是一家小批量的铸造厂。
次最新的升级改造,我们现在用最新的 D系列DISAMATIC造型机替换我们原有 的立式成型机,并使我们的工艺面向未 来。对最新最先进设备的投资使我们能 够降低运营和维护成本,降低能源消耗 并实现较高的机器利用率。”
关于新造型线:高效率的实现复杂
About the new moulding line: efficiency in complexity
LEDA’s DISAMATIC D5 is the latest in DISA’s flagship ‘D’ range of vertical moulding lines, which started with the D3 and its host of innovations which were then rolled out across the smaller and larger mould sizes with the D1 and D5 respectively.
The D5 replaces the old DISA 240 and 250 in the DISA range – and also at LEDA. The D5 range of three machines with mould sizes of 600 x 775mm, 600 x 850mm and 650 x 850mm achieves speeds of up 450 uncored moulds per hour.
Rochus Hiller comments on the upgrade: “The high degree of automation on the D1 and D5 offers us the features and settings to make more complex moulds efficiently. An example is adjustable squeeze distribution, a new feature we have not had before.”
Adjustable squeeze distribution ensures squeeze distances are optimised across the pattern, for swing plate and pressure plate, to adjust for asymmetric patterns or very deep pockets. This achieves the most consistent and even moulds and the best mould surface. The result are castings with a great surface quality that require little extra finishing work or machining.
R. Hiller explains further: “Similarly, both the D1 and D5 have automatic core setters that enable us to produce more economical and save resources. We use the automatic core setter not just to place cores but also exothermic risers and filters. The efficiency gains we get through the higher level of automation and precision mean we maintain our competitive edge, but this also enables us to pass the benefits of more productive and sustainable production on to our customers.”
Sustainability is important to the team at LEDA, who had already introduced an energy management system across the foundry and are looking to reduce annual energy consumption continuously over time. The new moulding lines use less energy – directly and indirectly. Indirect energy savings are made through the avoidance of scrap and highly accurate castings that require minimal finishing work, but also through short cycle times, with less idle time between moulds required for core setting and other manual tasks. And it’s not just energy that is being saved. For example, the new machines also use less hydraulic oil.
The new D5 at LEDA is a D5-Z which can produce up to 355 moulds per hour. This high speed, in addition to uncomplicated and fast pattern changes up to 30 times per day, gives LEDA the flexibility and responsiveness they need to
造型
LEDA的DISAMATIC D5是迪砂旗舰“D”系列垂直造 型线中的最新款,该系列从D3开始,然后分别推出从较 小到较大模具的D1和D5。
D5取代了迪砂系列中原来的DISA 240和250,LEDA 也使用过。D5系列的三台机器的铸型尺寸分别为 600x775mm、600x850mm和650x850mm,可实现 速度为每小时处理450个无芯铸型。
Rochus Hiller针对此次升级表示:“D1和D5的高 度自动化为我们提供了高效制造更复杂模具的功能和设 置。例如可调节挤压分布,这是我们以前从未有过的新 功能。” 可调节的挤压分布可确保优化整个模具的挤压距离, 用于摆动板和压力板,以调整非对称模具或非常深的口 袋,以此实现最佳的一致性和均匀的模具,以及最好的 模具表面效果。结果是,铸件具有出色的表面质量,几 乎不需要额外的精加工或机加工。
R. Hiller进一步解释说:“同样,D1和D5都具有自动 下芯机,使我们能够更经济地生产并节省资源。我们使用 自动下芯机,不仅可以放置芯子,还可以放置发热冒口和 过滤器。我们通过更高水平的自动化和精度获得的效率提 升意味着我们保持了竞争优势,但这也使我们能够将更 具生产力和可持续性的生产优势传递给我们的客户。” 可持续性对LEDA的团队很重要,他们已经在整个铸 造工厂引入了能源管理系统,并希望随着时间的推移不 断降低每年的能源消耗。新造型线直接和间接使用更少 的能源。通过避免废料和需要最少精加工操作的高精度 铸件,以及通过较短的周期时间,减少下芯和其他手动 任务所需的模具之间的空闲时间,实现间接节能。节省 的不仅仅是能源,例如,新机器也使用较少的液压油。
LEDA采购的新D5是D5-Z,每小时最多可生产355个 模具。除了每天30多次的简单和快速换模具之外,高速 还为LEDA提供了他们所需的灵活性和响应能力,高效地 进行小批量生产,适合于一周5 天、每天2班次的操作。

run smaller series efficiently and fit different runs into their 5-day, 2-shift operation.
Pit stop in Leer: a smooth transition in challenging circumstances
LEDA’s old DISA 250-C was replaced by the new D5 between the middle of December 2020 and the start of the new year. Despite a local lockdown and travel restrictions in Germany, a joint team comprising LEDA and DISA, plus transport and crane suppliers worked in shifts to deliver a smooth transition from old to new.
In the end, the meticulously planned changeover happened super-fast and exactly on schedule – despite the numerous challenges the pandemic brought – but not without nail-biting moments. Would the DISA team be allowed to travel into Germany from Denmark? Would hotels be open for them to stay in?
Right to the last moment, the old DISA 250-C was still working reliably. Therefore, after it had been running for LEDA for 20 years, the moulding line was taken back to DISA for reconditioning, so it could continue its service in a new home.
One key part of the old machine, however, stayed in Leer. The DISA team was able to reuse the existing synchronized belt conveyor (SBC) and rebuild it on site to work with the new automatic mould conveyor (AMC).
The new D5 was designed to slot straight into the gap left by a DISA 240 or 250 with key dimensions retained to enable an easy transition to the new technology, not just at LEDA.
LEDA’s new D5 produced its first mould on the 31th of December and started normal production on the 4th of January 2021.
R. Hiller on the milestone: “We are proud to welcome the second of our two new DISAMATIC moulding lines into the LEDA family. Both are at the heart of our production and will ensure the highest quality castings are delivered reliably and responsively for our customers.”
Ready for what’s next
With LEDA’s strong focus on innovation, it was important to the team that any new equipment was digitally enabled and ready for Industry 4.0. The digital capabilities that come as standard with the two DISAMATICs mean LEDA can continue its digital journey seamlessly and is ready for the future.
F. Ukena concludes: “Digitalisation is an important tool in the continuous improvement of our products and processes. It’s therefore important to us to capture the digital state of the art when we buy any new equipment. DISA moulding lines are digitally enabled, allowing us to introduce digital tools in a way and at a pace that suits us.”
“For us, that means combining digitalisation with the incredible wealth of knowledge and experience we’ve got in our workforce. That’s the winning formula for staying ahead of the competition as a foundry in Germany.” ■
For more information on the new DISAMATIC D5, please visit: https://www.disagroup.com/en-us/d5 利尔铸造车间:在充满挑战的环境中平稳转换
LEDA的旧DISA 250-C在2020年12月中旬至2021年初 被新的D5取代。尽管德国实施了本地封锁和旅行限制, 但由LEDA、迪砂以及运输和起重机供应商组成的联合团 队轮班工作,实现了新旧设备的平稳过渡。 最终,精心设计的设备转换进行的非常快且准时—— 但是由于新冠疫情大流行带来了很多挑战,也有令人痛 苦的时刻。例如,是否允许迪砂团队从丹麦前往德国? 酒店允许他们入住吗? 直到最后一刻,旧的DISA 250-C仍在正常工作。LEDA 使用了20年后,该造型线被退回到迪砂进行翻新,以便 在新工厂继续服务。 然而,旧机器的一个关键部件留在了利尔。迪砂团队 能够重复使用现有的同步带式传输机(SBC)并在现场重 建,以与新的自动模具传输机(AMC)配合使用。
LEDA在2020年12月中旬到2021年初的这段时间里, 将旧的DISA 250-C替换为全新DISAMATIC D5垂直造型 线。新一代的D5造型线设计旨在直接填补DISA240或 250所留下的缺口,保留住关键尺寸,使客户能够轻松 过渡到新的技术,这不仅仅只是针对LEDA。
LEDA的这台全新D5造型线于2020年12月31日生产 了第一个铸型,在2021年1月4日就开始全面投入正常 生产。
R. Hiller发表了重要看法:“我们很自豪地欢迎我们的 第二条迪砂的全新DISAMATIC造型线进入LEDA家族。这 两条造型线都是我们生产的核心,随时能够确保为我们的 客户可靠和及时地交付最高质量的铸件。”
为下一步做好准备
LEDA非常注重创新,新设备实现数字化并为工业4.0 做好准备对其团队来说非常重要。两条DISAMATIC造型 线标配的数字化功能意味着LEDA可以无缝地继续其数字 化旅程,并为未来做好准备。
F. Ukena总结道:“数字化是持续改进我们的产品和 工艺的重要工具。因此,当我们购买任何新设备时,发 掘最先进的数字技术对我们来说很重要。迪砂造型线实 现了数字化,使我们能够以适合的方式和速度引入数字 化工具。”
“对我们来说,这意味着将数字化与我们员工队伍中 的丰富知识和经验相结合。这是德国铸造企业在竞争中 保持领先地位的制胜法宝。” ■
有关新型DISAMATIC D5的更多信息,请访问:https://www.disagroup. com/en-us/d5
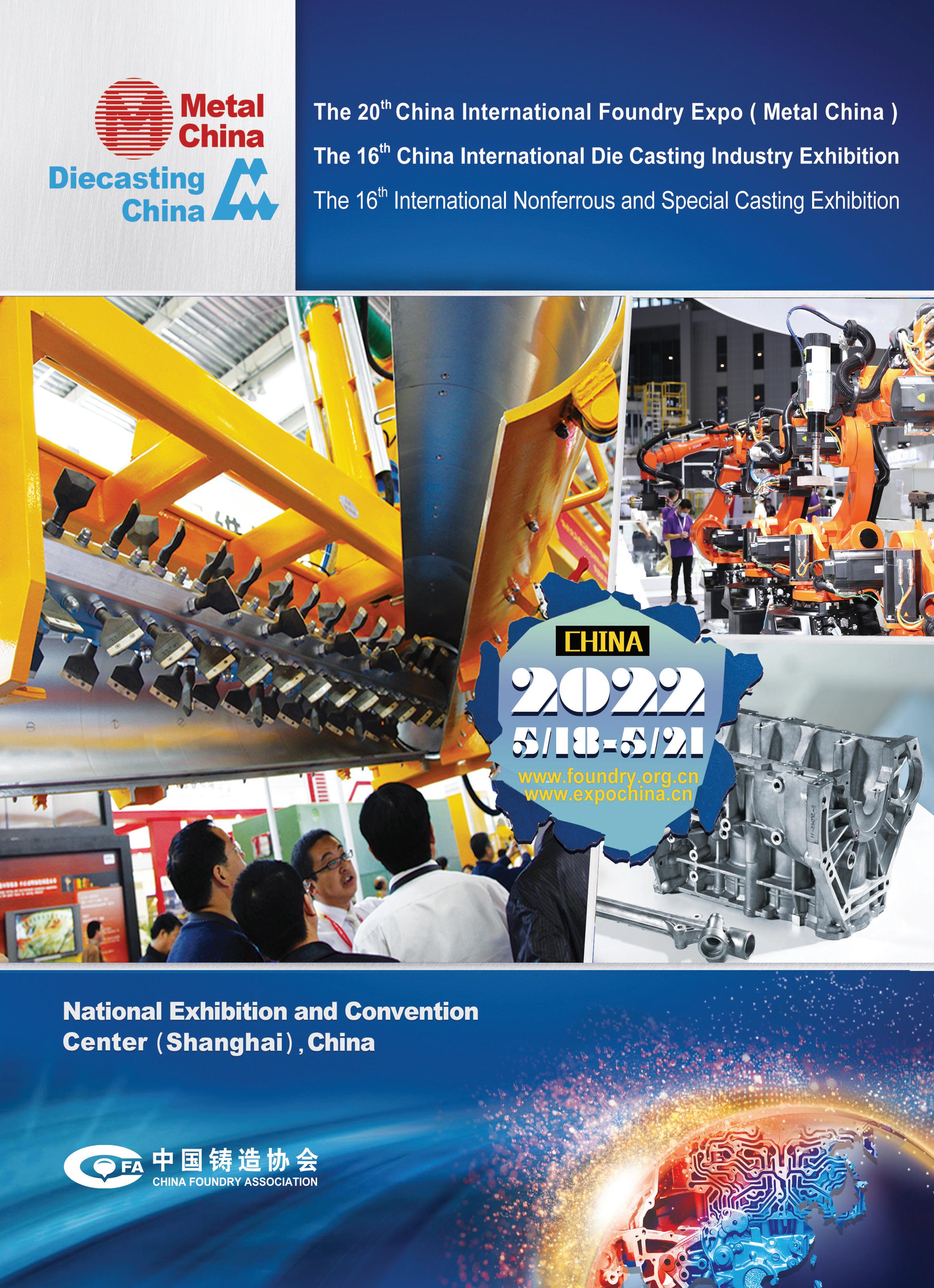