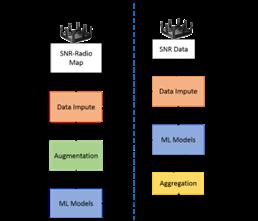
4 minute read
Student Feature: Millimeter-Wave Robot Localization for Intelligent Material Handling
Millimeter-Wave Robot Localization for Intelligent Material Handling
by Abhishek Vashist, Ph.D. Candidate, Rochester Institute of Technology
Intelligent material handling (iMH) systems represent the next major step in the advancement of warehouse productivity and safety. Our vision is to establish a center for state-of-the-art research, application, and demonstration of iMH systems consisting of a fleet of autonomous material handling agents (forklifts, picking robots, etc.) capable of maximizing productivity while safely interacting with people and objects in a warehouse or production environment. One of the major technological challenges is the estimation of an autonomous agent’s location in a warehouse environment. To address the challenge of indoor localization, in our approach, we deploy 60 GHz based millimeterwave (mmWave) routers as Access Points (APs) on the ceiling of the warehouse and one router on the robotic agent acting as a Client. To localize the client, we use machine learning (ML) modeling to learn the complex relationship between the wireless features and the distances. The overall setup for the data collection and the test time inference is shown in Fig. 1. The robot setup with mmWave router is shown in Fig. 2.
The approach consists of two phases: offline phase and inference phase. In the offline phase, we construct the radio map of the warehouse aisle where the features are the Signal-to-Noise Ratio (SNR) values from the AP routers received at the Client. Before training the ML models we implement a data imputation and synthetic data augmentation on the collected training dataset. Performing augmentationbased training train our localization system to be more robust in the event of single or multiple AP failure.

Figure 1: Localization train and test setup
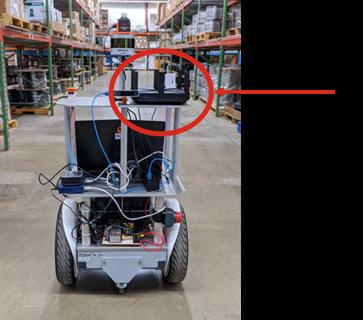
Figure 2: Robot setup in a test warehouse
In our framework, we have designed a two-level ML learning approach for location prediction within the two aisles of the warehouse. The first ML model performs the aisle level classification and the second ML model takes the signal information to regress the position of the agent within the aisle. Further, the predictions from both the ML models are combined to predict the position in 2-dimension space within

Figure 3: Prediction plot between the actual (blue) and the predicted (orange) locations
We evaluate different classes of ML models using our approach. For aisle level classification SVM achieves a very high accuracy of 99.55% and for the regression Multi-Layer Perceptron (MLP) model achieves high accuracy with the Root Mean Square Error of 0.19m and 0.92m in x and y positions respectively.
In Table I, we evaluate different ML models for continuous location estimation. We observe that MLP achieves highest accuracy compared to simple linear regression and support vector regression models. Further, Table II shows the performance using the aisle level classification for different ML models and we obtain the highest accuracy using a support vector machine (SVM) compared to a simple approach as KNN. This also illustrates the need of using machine learning to provide an accurate positioning system for an indoor warehouse environment.

Table I: ML regression performance comparison
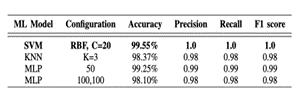
Table II: ML Classification performance comparison
Our work also received Best Paper Award at IEEE International Conference on Consumer Electronics (ICCE) 2020, Las Vegas, 2020. q
Author Bio:
Abhishek Vashist is currently pursuing his Ph.D. degree in the Department of Computer Engineering at Rochester Institute of Technology, Rochester, NY. He previously received his BS in electronics and communication engineering in 2010 and MS in electrical engineering in 2017. His research interest includes millimeter wave communication, machine learning, CPU design, and interconnection networks. His work has also won the best paper award at ICCE 2020. Contact him at av8911@rit.edu.