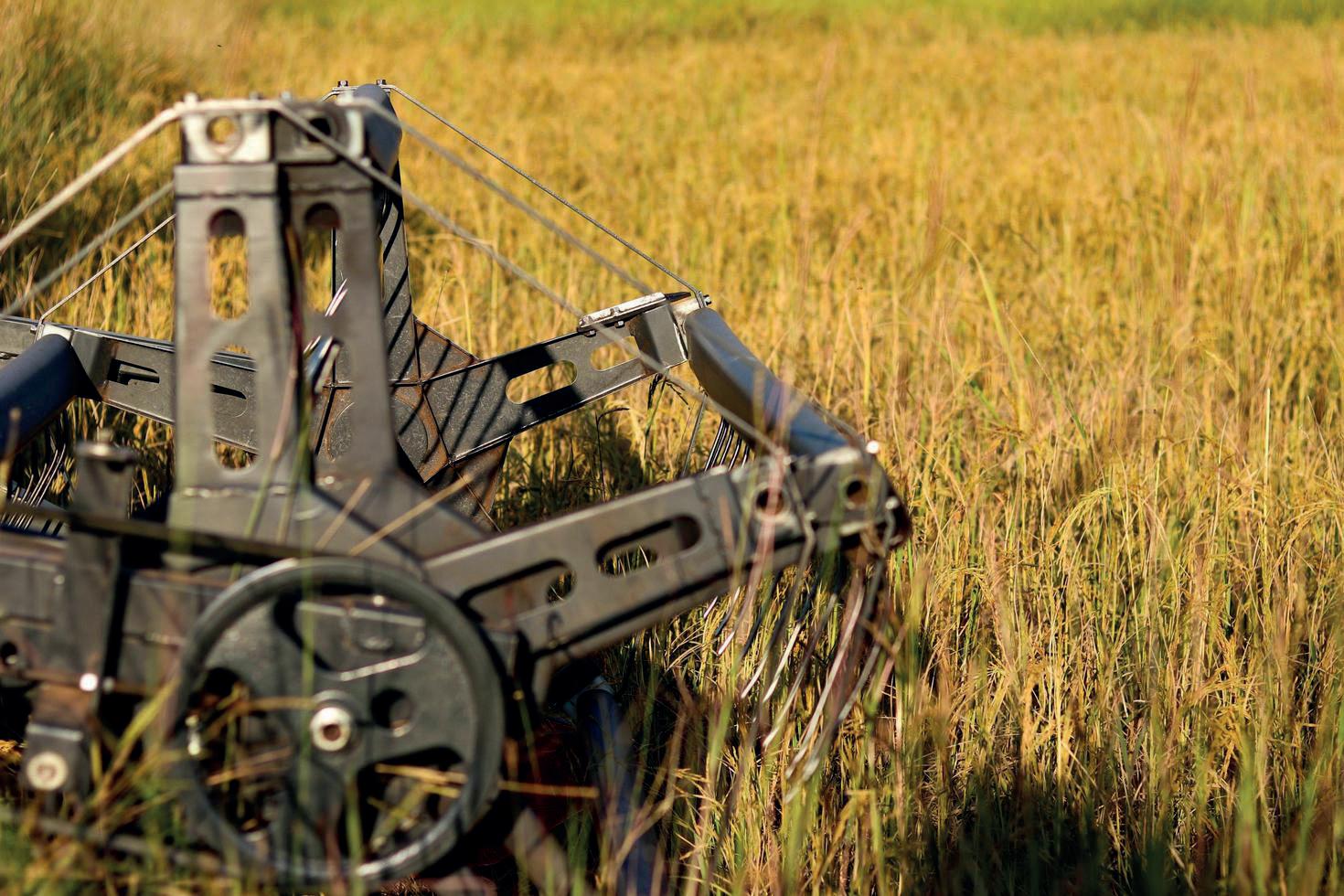
8 minute read
Colhedoras
Perdas evitáveis
Comparativo entre duas colhedoras fabricadas em 2003 e 2014 mostra os benefícios de manter a frota moderna, com sistemas tecnológicos que aumentam a eficiência da operação e reduzem as perdas
Oarroz é o segundo cereal mais cultivado no mundo e serve como base alimentar para mais de três bilhões de pessoas, sendo muito consumido em nosso país, chegando a 45kg/pessoa/ano. No Brasil, a região Sul é a maior produtora. Na safra de 2017/2018 ela foi responsável por 80% da produção nacional, seguida pelas regiões Norte com 9% e Centro-Oeste com 6% (Conab, 2020).
No estado de Mato Grosso, 95% do arroz cultivado é da forma sequeiro, uma das principais formas para recuperação de áreas degradadas principalmente por sistemas extensivos de criação de bovinos, onde é cultivado por uma ou duas safras antes da cultura predefinida soja/milho ou pasto novamente.
A produção de arroz no Mato Grosso só é possível em função de conhecimentos técnicos aplicados no campo. Um dos pontos-chave para manter a boa produtividade é a eficiência da colheita, seja ela mecanizada ou não. As perdas na colheita mecanizada podem ser significativas quando mal reguladas e não trabalhada nas condições ideais.
As colhedoras podem apresentar perdas internas e externas. Geralmente, cerca de 73,2% dos grãos perdidos ocorrem no sistema de alimentação e 22,8% nos mecanismos internos, além de 4% antes da colheita. Cada máquina possui suas peculiaridades, entretanto um padrão recomendado por fabricantes para minimizar as perdas no sistema de alimentação é que a velocidade de molinete seja 20% maior que a velocidade de operação. Quando operado em velocidades inferiores o molinete não suporta a velocidade da máquina e acaba atropelando a planta, resultando em um acúmulo de plantas, consequentemente problemas no
Fendt
Fotos Leandro Ricardo Brunetto
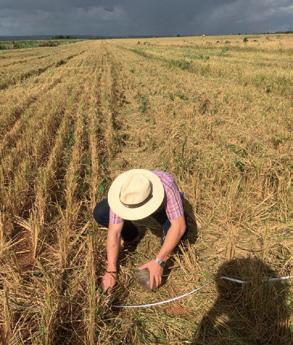

Delimitação da área e coleta amostral em lavoura de arroz sequeiro
sistema por excesso de massa. Se o molinete estiver em velocidade superior a 20% ocasiona um atrito muito forte com a planta, resultando em uma debulha, aumentando as perdas.
Outros modelos mais modernos de sistemas de alimentação já são produzidos para minimizar estas perdas. Hoje em dia as plataformas Draper vêm com sistemas de flutuação, barra de corte, molinetes mais tecnológicos e com a inovadora esteira de borracha a qual auxilia a alimentação de forma contínua e uniforme.
Para aprimorar ainda mais a operação de colheita mecanizada pode-se analisar a qualidade do processo de colheita como auxílio do controle estatístico, com intuito de melhorar a qualidade da operação por meio de levantamento de dados. Com o objetivo de avaliar o desempenho dos dois sistemas de alimentação (caracol e Draper), verificando qual apresenta melhor qualidade e eficiência, pesquisadores da Universidade do Estado do Mato Grosso e da Universidade do Estado de Minas Gerais desenvolveram um trabalho de campo com duas colhedoras com diferentes características.
O experimento foi realizado na propriedade São Eduardo, em Tabaporã (MT). A propriedade conta com uma área de cultivo de 1.000ha de grãos, a qual é distribuída em vários talhões no raio de 15km em torno do distrito. A área do experimento tinha como vegetação o cerrado, onde passou a ser cultivada por gramíneas para alimentação animal nos últimos cinco anos e, por fim, no ano de 2018, passou pelo processo de mecanização, sendo então o primeiro cultivo de grãos nesta área, com arroz cultivar Cambará Comum.
A colheita foi realizada com duas colhedoras automotrizes. Uma fabricada no ano de 2003, largura de plataforma de 23 pés (7m), com sistema caracol, a qual realizou a operação com as seguintes regulagens fixas: rotação do ventilador de 750rpm, rotação do cilindro de 500rpm, abertura de côncavo de 0,7cm, abertura da primeira peneira de 0,9cm, abertura da segunda peneira de 0,8cm, velocidade de operação de 2,5km/h a 3km/h.
A outra colhedora é ano 2014, plataforma Draper de 35 pés (10,7m), a qual também realizou a operação em regulagem fixa: rotação do rotor de 670rpm, rotação do ventilador de 940rpm, abertura de côncavo de 0,4cm, abertura da primeira peneira de 1,2cm, abertura da segunda peneira de 1cm e velocidade da máquina de 3,5km/h.
Antes da colheita foram medidas a altura das plantas antes da colheita, com auxílio de uma fita métrica, e em seguida a altura da panícula da mesma (altura até o início do cacho), após a colheita foi determinada a altura de corte das plantas, com intuito de caracterizar a área para verificar a influência sob a colheita mecanizada.
A demarcação da área para a coleta dos grãos foi utilizando fita métrica, corda e régua, em que foram utilizadas medidas diferentes para cada máquina, entretanto com a mesma quantidade de área, no qual se formou um retângulo alcançando toda a plataforma. Para a colhedora ano 2003 foi usada a medida de 0,287m x 7m, somando 2m², e para a colhedora ano 2014, a medida de 0,187m x 10,7m, totalizando 2m², posteriormente as amostras foram pesadas com balança digital.
Os dados foram submetidos à comparação de médias pelo teste de Tukey, a 5% de probabilidade, e verificada a qualidade da colheita por meio do controle estatístico de processo, utilizando-se as cartas de controle de valores individuais, que possuem linhas centrais (média geral), bem como os limites superior e inferior de controle estatístico, definidos como UCL e LCL, calculados com base no desvio padrão das variáveis (para UCL, média mais três vezes o desvio padrão, e para LCL, média menos três vezes o desvio, quando maior que zero).
Para altura de planta não houve diferença significativa no teste de Tukey a 5%, e é entendido como um bom porte de planta para a colheita, por volta dos 100cm a 105cm que é descrito pelo fabricante e identificado no experimento. Além do mais, uma das características da variedade é moderada resistência ao acamamento, no qual possibilita uma colheita mais eficiente com menores índices de perdas.
A altura da panícula, característica de cada variedade, é o mecanismo que vai determinar a altura de corte feita pela máquina, ou seja, quanto menor a altura da panícula mais rente ao solo será o corte. Dependendo da altura, pode ocasionar maiores perdas pela topografia do terreno, princi-
2003 2014 CV % DMS F
Tabela 1 - Média dos parâmetros analisados Alt. de planta (m) Alt. de panícula (m) Alt. de corte (m) Perdas (Kg) 1,01 a 0,80 a 0,30 a 299,58 a 1,00 a 0,81 a 0,29 a 199,17 b 5,01 5,15 8,04 10,37* 0,04 0,04 0,02 21,90 0,06NS 0,29NS 0,27NS 90,46**
Letras diferente na coluna se diferem entre si. NS- Não significativo.
Figura 1 - Cartas de controle altura de plantas (A); altura da inserção da panícula (B); altura de corte (C); e perdas (D) durante a colheita mecanizada de arroz. UCL: Limite superior de controle; LCL: Limite inferior de controle. X=: Média dos valores amostrais
A 2003 2014 B 2003 2014
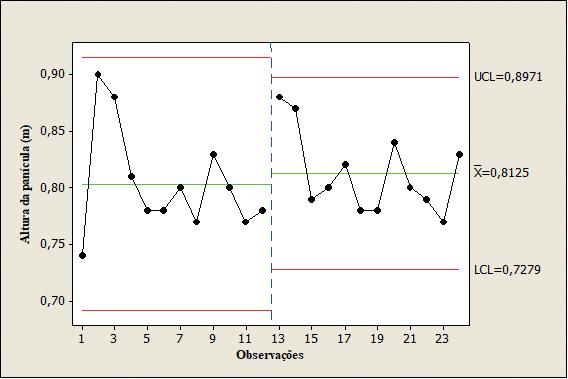
C 2003 2014 D 2003 2014
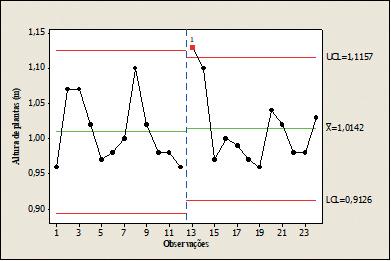
palmente por que o cultivo de arroz sequeiro geralmente é cultivado na primeira safra, condição onde a irregularidade é maior.
A altura de corte também não apresentou diferença significativa, o que mostra uma igualdade na operação das duas máquinas, com altura de aproximadamente 30cm. As colhedoras mais recentes com sistema flutuante conseguem colher abaixo de 10cm de altura. No entanto, o arroz não é uma cultura que exige corte tão baixo pelas suas características morfológicas.
Para as perdas de grãos houve diferença significativa, no qual a colhedora 2014 obteve menor perda comparado com a 2003. O que pode ser explicado pela diferença dos sistemas alimentadores, os quais são o principal mecanismo de perdas.
Com o auxílio das cartas de controle, pode-se observar na Figura 1A que não houve uma grande homogeneidade entre a altura das plantas, no qual uma amostra ocorreu fora do limite aceitável. A oscilação na altura das plantas pode ser justificada por alguns fatores, chamados de 6 Ms (mão de obra, medição, matéria-prima, máquina, meio ambiente e métodos), em que o principal fator que pode ocasionar isso é matéria-prima, a qual está ligada à uniformidade da variedade e também ao meio ambiente, como declividade do terreno e deformações da área. Na altura da inserção da panícula e altura de corte (Figura 1B e 1C), não houve medidas fora dos limites, entretanto as amostras coletadas durante a colheita da colhedora 2014 mostraram uma maior homogeneidade perante as amostras da 2003. A variação da altura de corte é definida pelo operador, a qual é estabelecida durante o processo que, por sua vez, também é afetado pela topografia e irregularidades do terreno.
A Figura 1D representa as perdas durante o processo de colheita, percebe-se que a colhedora 2003 além de apresentar maiores perdas, apresentou maior variabilidade nas amostras, ou seja, menos homogênea. Este fator pode ser explicado pela idade da máquina. De acordo com alguns pesquisadores, as colhedoras até cinco anos apresentaram perdas semelhantes e menores que as com mais de seis anos, esse fator é explicado por desgastes internos e externos da colhedora.
Como observado nos resultados, a colhedora 2014, por ser mais nova e por possuir sistema mais tecnificado comparado ao da colhedora 2003, apresentou menores perdas.
Percebe-se que é importante o produtor estar sempre acompanhando e adquirindo máquinas mais modernas e tecnológicas, pois estes novos sistemas proporcionam uma maior eficiência e confiabilidade, trazendo resultados satisfatórios.
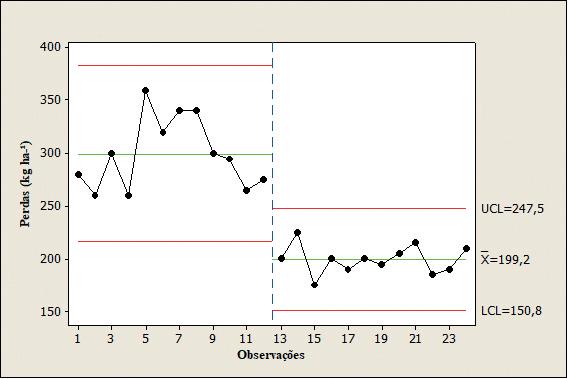
Leandro Ricardo Brunetto, Unemat, Alta Floresta Antonio Tassio S. Ormond, Uemg
