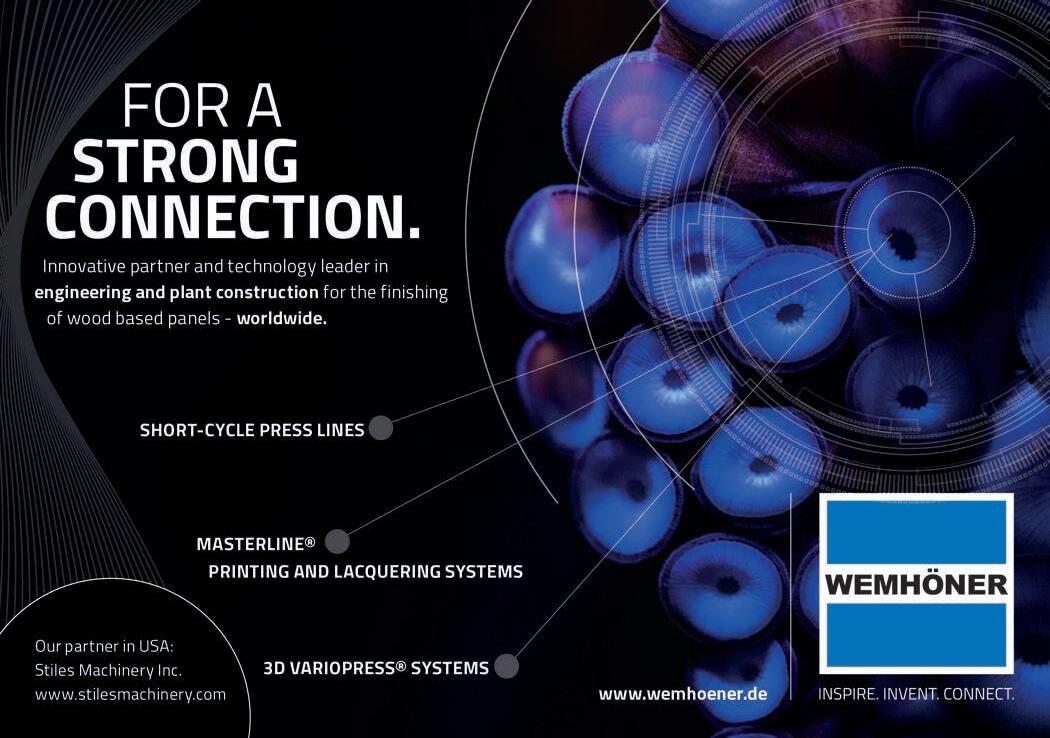
17 minute read
UPDATE
Environmental Impact Statement (EIS) needed to be re-addressed by the city because of issues involving a few acres of two “public waters wetlands” that state law would require an EIS for.
The state of Minnesota requires a “responsible governmental unit,” such as a city planning body, to determine if a project requires an EAW or EIS, or both.
The appeal from Leech Lake Band of Ojibwe and Minnesota Center for Environmental Advocacy also asked the court to weigh the environmental effects potentially caused by air emissions from the new OSB plant and from the volume of timber harvesting that the plant would require. The city had determined there would be no significant environmental effects from either, given the permitting and planning requirements the project would require going in. The appeals court ruled in favor of the city as to “no significant environmental effects” and against the Band and the Minnesota environmental group.
But the court took to task the city’s determination that an EAW was enough for the project with regard to public wetlands. Huber initially submitted an EAW and then, at the city’s request—following additional consultation and review from local citizens, state agencies, and other interested parties, and providing more information about the health of Minnesota’s forests and their ability to sustainably supply the facility, and providing more detail on the project’s carbon footprint, especially regarding the effects of generating much of the facility’s energy needs through wood fuels, and the carbon sequestration effects of the finished wood products—re-submitted the EAW, which the city accepted while deciding an EIS wasn’t necessary.
The Leech Lake Band of Ojibwe appealed, and the appeals court agreed, that the facility “falls into categories” for which an EIS is mandatory under Minnesota law, specifically as to the elimination of public waters wetland.
The city had determined that the project would not eliminate public water wetlands. But the court focused on two small public waters wetlands, which the court said are “accorded greater protection under state law” and should require an EIS beyond an EAW.
The court noted that the state’s definition of public waters wetlands is 10 or more acres in size in unincorporated areas and at least two and a half or more acres in incorporated areas. Huber’s EAW explained that its project would involve filling portions of two public waters wetlands, both in incorporated areas: 8.73 of 14.27 acres in one and 1.65 of 5.67 in another, and that while there would be a reduction in the size of each, it wouldn’t “eliminate” the public waters in question and only reduce the size, and thus not require an EIS. The city agreed that the partially filled public water wetlands would not fall below the 2.5 acre threshold after the partial filling.
The appeals court, however, said the state law did not explain what it means to “eliminate” a public waters wetland, and took the liberty to base its ruling that “eliminate” can also mean to “modify” the public waters wetlands, and ruled that because the project would alter the char- acteristics of the public wetlands the city should apply this legal standard and re-assess whether an EIS is necessary.
The Leech Lake Band also said the public waters wetlands fillings would have significant environmental effects that should require an EIS and that the city failed to consider these. The Band said the wetlands Huber planned to fill are a filter for water quality that nearby wild-rice beds depend upon, and removing the wetland filters would be harmful to the water quality that the rice requires. The court agreed, noting the city did not investigate or explain how wetlands replacement (as the project would entail) or stormwater controls would protect the wild-rice bed and other resources downstream.
The court said the city should reconsider given these stipulations and then issue a revised decision on the need for an EIS. Huber’s withdrawal from the project apparently now renders such an exercise as unnecessary.
“The court decision issued today is a major victory for the Leech Lake Band of
Ojibwe and serves as a powerful reminder of the importance of respecting the sovereignty and treaty rights of indigenous nations,” comments Band Chairman Faron Jackson, Sr. “The proposed OSB mill project posed a clear threat to our sacred resources, including wild rice and wildlife, while bypassing an important step in the environmental review process.”
Upon the announcement of Huber’s departure, Tamara Lowney, president of Itasca Economic Development Corp., told the Duluth News Tribune, “Today really feels like a funeral in my office, saying goodbye to the biggest opportunity that our region and our northern part of the state has seen in decades.”
The project would have replaced lost jobs and tax base as the adjacent Boswell coal-fired energy plant shuts down its coal burning units and possibly reconfigures to renewable energy sources.
The Cohasset OSB mill would have been Huber’s sixth, following facilities in Maine, Georgia, Virginia, Tennessee and Oklahoma. Had the timeline not been delayed from the outset, Huber’s construc- tion of the plant would have occurred during the current OSB market softening, possibly putting it in prime position upon startup to take advantage of the next market strengthening. PW
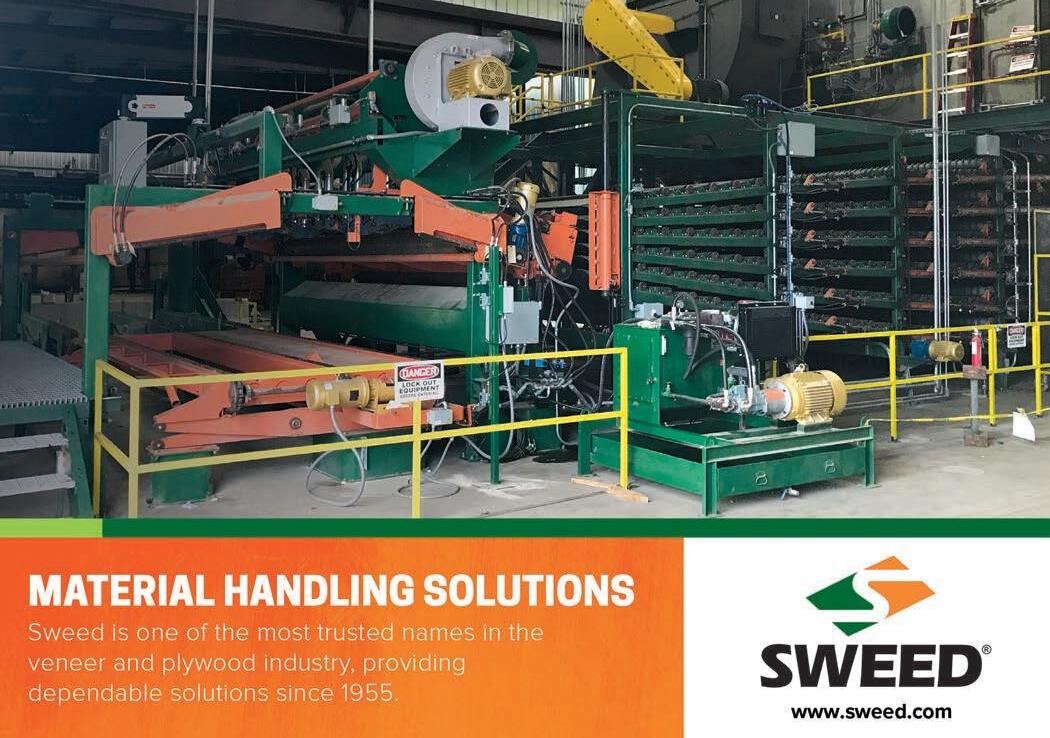
Clutter Knew Forest Economics
Dr. Michael Lee Clutter, who served as Dean of the University of Georgia Warnell School of Forestry and Natural Resources from 2007-2015, and was a noted expert in his field, died on December 24. He was 63.
Clutter was considered an authority on the economics of the forestry industry, including finance, budgeting, timberland management and timber supply and sizing trends. Early in his career he held various management positions with GeorgiaPacific Corp. and Union Camp Corp. in Savannah. Joining Warnell’s faculty in 2001, he was later named the Hargreaves Distinguished Professor of Forest Finance and received the Warnell School’s Faculty Award for Outstanding Teaching.
Richie LeBlanc provides insights on himself, Hunt Forest Products and the wood products industry in this question-and-answer exchange with Panel World.
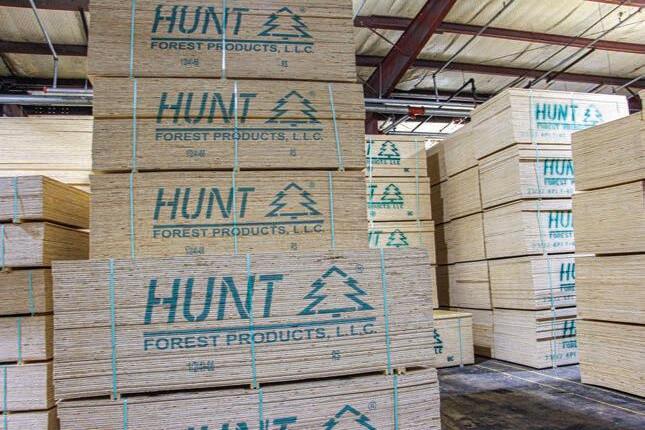
EDITOR’S NOTE: Since this is the March issue of Panel World, and March means baseball (to some people), what better person to interview than Richie LeBlanc, president and CEO of Louisiana-based Hunt Forest Products, LLC? No, we’re not interviewing him about baseball, because his insights into the forest products industry take center stage here. But before we get to that…a belated congrats goes to LeBlanc for being inducted into the Louisiana Tech 2021 Athletics Hall of Fame. LeBlanc, from Lafayette, was the Southland Conference Pitcher of the Year in 1986 and 1987 and led Ruston-located La Tech to the NCAA Regionals both seasons. His 12 wins in 1986 is still tied for the school’s most wins in a season, and his 29 career wins is second. He also completed 18 games, nearly unheard of today. They still talk about his 10-inning 5-4 win over perennial power LSU at J.C. Love Field in 1987. The Kansas City Royals drafted LeBlanc and he proceeded to pitch well as he moved up the minor league ranks, but he decided to start the next phase of his life, wrapping up his business degree at La Tech and working with an insurance agency as vice president in Ruston for 10 years, before joining Willamette Industries in Ruston and then Weyerhaeuser after Weyerhaeuser acquired Willamette in early 2002 following a prolonged takeover battle. He initially served on the integration team, charged with merging the cultures of Willamette and Weyerhaeuser. He became the land adjustment program manager of Weyerhaeuser’s North Louisiana timberlands organization. In 2015, he was named director of U.S. real estate operations for Weyerhaeuser. Legendary familyowned Hunt Forest Products appointed LeBlanc as president in 2016. In addition to its timberland assets, the compa- ny continues to operate a plywood mill in Pollock, La. and in recent years has partnered with Tolko Industries at a newly constructed sawmill in Urania, La. and also at a sawmill under construction in Taylor, La.
PW: You have a broader perspective, given your company’s (and your own career) involvement in panel, lumber and timberland. We keep hearing about softening of markets, but then again, we’re moving into spring; overall, what’s your take and expectations on the building products marketplace through this year and into next? The forecasts at the recent APA meeting were pretty soft.
LeBlanc: You are correct. The APA forecast was somewhat soft. However, we have and will continue to be optimistic that markets—albeit, not like we had experienced since May of 2020— will continue to be good. During the last several years we have witnessed very strong market takeaway. Our focus during that time was to capitalize our mill to ensure when the markets returned to “normal” pricing, we would continue to operate efficiently. We never lost sight of where the markets had been and would return.
PW: We hear about labor issues affecting operations across so many industries. Is Hunt seeing this as well, and what initiative is Hunt taking to attract, train and retain employees, and also to procure younger talent into the industry?
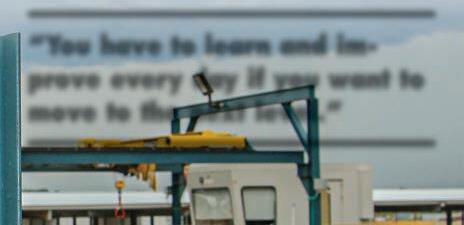
LeBlanc: Labor issues are a common theme at many industry events across the U.S. In the last several years we have experienced many challenges that impacted our work force…Covid, hurricanes, ice and snow storms. Our owners and partners agreed with the company’s leadership to pay all hourly employees during these events that caused extended downtime at our mills. I feel strongly that how we treat our employees during these uncertain times has helped us retain our talent during these trying times. We were able to take advantage of the favorable markets and provide additional bonuses to our employees. We recognize that it is both a business and strategic imperative that talent must be developed from within the organization. Our owners and leadership are committed to helping develop employees and give them the tools and skills necessary to increase employee engagement, thereby enhancing performance.
PW: Developing a company culture continues to be a growing theme. Is Hunt invested in this and what are the keys to its successful implementation?
LeBlanc: When we took over in 2016, we started molding the company’s culture into a system that is proactive with respect to safety, capitalization, automation, growth, and development of people. This was a tremendous change from where the company was prior to the change of ownership within the Hunt family. Trott and Jimmy Hunt have and continue to advocate growth both within existing assets and new projects like the greenfield lumber mill in Urania, La. and the most recent announcement of the new mill in Taylor, La.
PW: Given your experience with timberlands, there has been discussion about potential conflicts with carbon credit programs that could essentially take forestland out of timber production. How closely does that bear watching?
LeBlanc: I am by no means an expert in the carbon credit markets. I do believe there are areas that can be set aside without much impact to timber production. As we have seen, this is a very dynamic space that will continue to evolve.
PW: Is there a possibility that Hunt will enter mass timber production, again give the company’s combined panel and lumber expertise? And what about any expansion plans the company may have in panel?

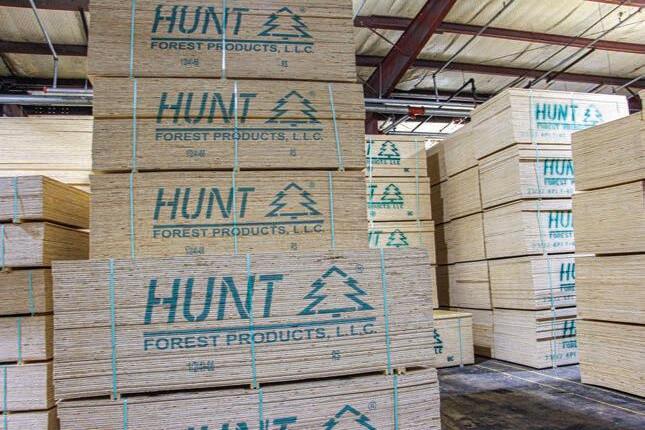
LeBlanc: We have and will continue to grow our business within our core competencies. As with carbon markets, finding new ways to utilize the renewable resource we have in wood products the table with respect to any growth opportunities within this space.
PW: Given your recent appointment to the board of APA—The Engineered Wood Assn. and the everevolving dynamics of the building products industries, how do you see APA’s role moving forward and what would you like to contribute to it?
LeBlanc: For those in our industry, they understand that the APA has a long history of dedicated scientists and engineers who through their research efforts continue to provide new solutions and improved processes that benefit our industry. I want to be part of the group that continues to tell the story and to help ensure that standards are maintained.
PW: Given your diverse experience in the industry through the years, provide a few reflections on what the industry has meant to your development of character and professionalism?
LeBlanc: It certainly has been an interesting ride. I joined Willamette in 2000 not knowing much about wood products. My role was more administrative than operational. Shortly, after joining the Willamette team, Weyerhaeuser announced their bid to acquire Willamette. I was asked to be part of the integration team that would bring the two companies together. It was an incredible experience, some good and some not so good. As with any merger, there are many people that were displaced. That was a difficult time because Willamette had such a significant presence in Ruston, Louisiana. However, with Hot Springs, Arkansas just to our north, the redundancy in services was unnecessary.
I made mistakes along the way, but fortunately worked for leaders that supported me through some of those events. I learned from those experiences and one of the most important lessons I learned was what type of leader I wanted to be.
PW: How did you come to be with Hunt Forest Products?
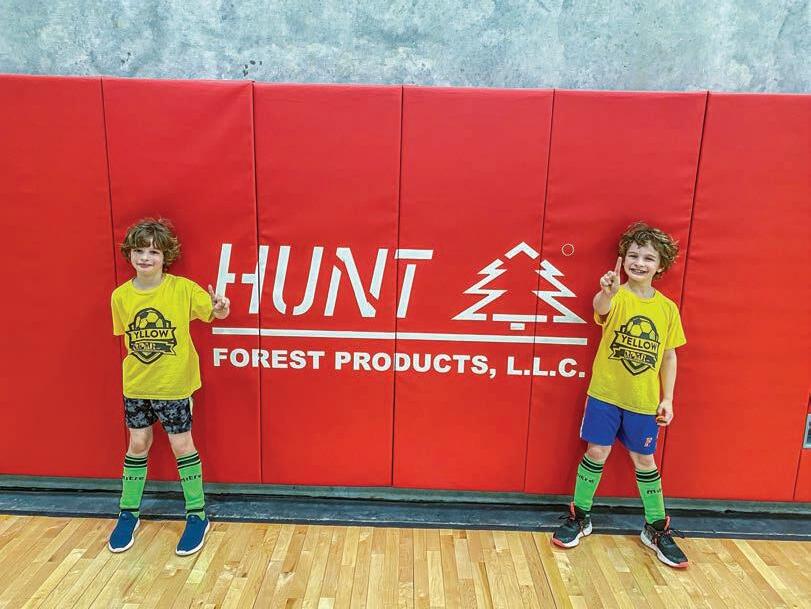
LeBlanc: Joining the Hunt team was all about timing. The Hunt Brothers needed someone to oversee the company and I was in Seattle with Weyerhaeuser at the time. My son became very ill and my wife had already returned to Ruston. I remember telling my team at Weyerhaeuser, “It’s easy to say that family comes first right up until that time when you have to make the decision to leave Weyerhaeuser and return to Ruston to take care of family matters.” I also remember the day Trott Hunt called…same day I found out that my son was ill.
PW: What’s it like to lead a familyfounded company like Hunt, and what lessons learned perhaps through your sporting days do you continue to bring to the leadership table today?
LeBlanc: The Hunt family has a long history of success in the North Louisiana Piney Woods. Being part of that history is certainly special. In the seven years I have been part of this company, we have experienced the peaks and the valleys. I tell my team it is our responsibility to leave this company in better shape than we found it for the next generation of Hunts.
When people ask about working with family companies, I tell them that the biggest difference is that your shareholders are sitting in church with you— it’s hard to hide from them in our small town. Therefore, we have to ensure our actions are sound business decisions and what will be the effect. It is similar to playing minor league baseball: You have to learn and improve every day if you want to move to the next level. Once you stop wanting to learn and improve, your career is over.
PW: If you had to pick out a major challenge the industry (and Hunt) faces moving forward, what would it be?
LeBlanc: I believe labor will continue to be challenging in the future—not only from the employment side but also from the knowledge side of our business. We are seeing employees retire after working for the Hunt family for 40+ years. That is quite a bit of knowledge walking out the door. We have to transfer that knowledge and train our people to make sure what we are doing is sustainable over time. PW
EDITOR’S NOTE: The following companies submitted these editorial profiles and images to complement their advertisements placed elsewhere in this issue. Please refer to those advertisements for web site and contact information. All statements and claims are attributable to the companies.
Argos Solutions
It has been more than 10 years since Argos developed and delivered its first Panel Repair System (PRS). The advanced system was delivered to one of the major panel producers in Finland, allowing them to repair wooden surfaces more efficiently and accurately, while maintaining high production speed.
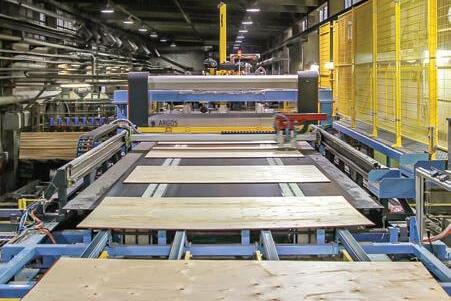
Now, Argos Solutions is the leading developer and producer of both Automatic Surface Grading and Panel Repair Systems. With a demonstrated record of providing efficient and trustworthy solutions to the industry, they have established themselves as an innovative and reliable supplier and partner to panel manufacturers all over the world.
Over the past year, the company has secured deliveries to major companies in Chile, the U.S., Canada and France, and there are several prospects in the pipeline.
“We see a growing demand in the market for PRS systems,” says Richard Lepine, General Manager for Argos Solutions, North America. “The reasons for this are many, but I believe that our reputation in the market, the reliability and accuracy of our systems combined with an outstanding service team make us an attractive partner when producers are looking to address the shortage in labor forces, reduce downgrade and rework, enhance quality, reduce cost and optimize their production processes.”
The lack of personnel, combined with increased production speed and increasing quality requirements, forces many producers to think differently about how they best can utilize the resources they have, and how they can create an attractive workplace that motivates their people to stay and further develop themselves, as well as the company. By installing automatic repair systems that are faster, more accurate, and more reliable than the human eye, panel manufacturers can be sure to deliver the quality their customers expect. It also allows them to relocate their valuable human resources to other operations.
Oregon-based Swanson Group is one of the companies that has benefited from an Argos Panel Repair System. Quality Control Manager Shawn Crager is very positive about the system:
“Part of what makes our company unique is that we handle many different types of hardwood, and the specifications for repairs and grain pattern complexity varies. We needed a system that could handle our many requirements. This PRS system is awesome, and the quality of repairs is unmatchable. In addition to being a reliable and sturdy system, the cost savings have been remarkable. The Argos system uses only a fraction of the poly and putty, reducing the cost compared to how we worked earlier.”
Argos Solutions has delivered more than 300 systems to more than 40 countries across the world.
Baumer
Baumer ColourBrain CPL 4.0 is a state-of-the-art inspection system developed for hybrid manufactured CPL decorated both digitally and in gravure. The special features of both manufacturing worlds are combined in one system and can detect all significant deviations. Furthermore, with the improved evaluation of the overlay paper, even minor, weakly visible defects are detected in all decorations. A special process ensures that the actual decor, as opposed to defects, is almost completely suppressed.
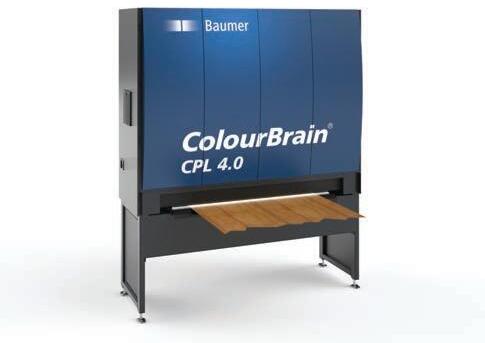
Thanks to the patented FlashingSky and other high-performance evaluation channels, process defects such as bubbles, decor particles (also of the same color as the actual decor), milkiness, gloss deviations, breaks and cracks can be reliably detected. The system also detects typical digital printing defects such as nozzle or printhead failures.
Detected defects are directly marked, alarmed and, if required, recorded in a roll log. This enables the press operator to immediately identify and eliminate the causes of process-related defects. On the other hand, the roll log enables him to remove defective areas in a targeted manner in later process steps.
The CPL 4.0 system features a new, intuitive touch user interface. The Baumer “Dashboard” provides an overview of the current production. The inspection results with defect logs as well as the production statistics are displayed scalable in different zoom levels over different production sections—from a single to several hundred running meters.
By using templates, Baumer Inspection creates order and clarity in product data management. Similarly structured products are grouped together so that suitable inspection settings do not have to be found for hundreds or thousands of different CPL items, but only for a handful of templates.
The ColourBrain CPL 4.0 system is ready for Q-Live. This enables consistent data management to systematically compare several CPL 4.0 systems in a plant or group, thus ensuring that the same article is assessed with the same criteria in different lines or locations.
The CPL 4.0 systems are calibrated and preset in a standardized manner at Baumer so that commissioning can be carried out quickly and with the shortest possible line downtime.
A high level of operational reliability is achieved through the self-monitoring functions and the reporting of changes such as temperature increases, illumination losses, failure of computers, cameras, luminaires or deposits on luminaires or mirrors.
For years, Baumer Inspection has followed the strategy of developing and manufacturing the critical core components such as cameras, computers, illumination and control modules in close cooperation with the resources in the Baumer Group. This pays off several times over. The success is the control of the supply chains and the adherence to the promised delivery dates.
Biele Group

Biele Group has been developing and supplying its self-developed Quality Control System for many years in order to give additional value to its complete turnkey lines supplied to customers.
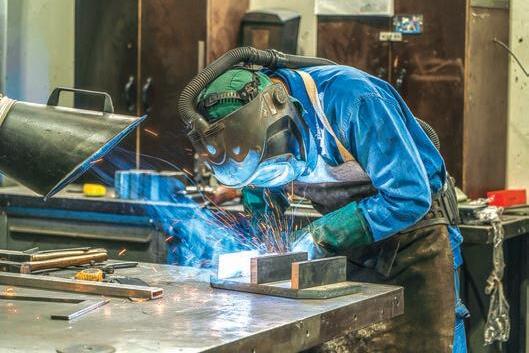
In recent years Biele has been focusing its efforts on providing these vision solutions in various lines in multiple sectors, including:
—Door Press and Trimming lines
—HPL Trimming lines
—Furniture Packaging lines
—Embossed in Register (EIR) Pressing lines for panel and for flooring
—Veneer Sheets Processing lines
Moreover, Biele Group is providing customized high-end handling solutions that synchronized with its Quality Control System maximizes the optimization of different processes, including automatic outsorting and insorting systems of panels and sorting and stacking of different quality panels.
One of the latest examples is a complete manufacturing line for residential doors, where Biele has included a brand new quality control technology. This cutting-edge technology integrates in a small form factor vision system (only 750 mm wide) 14 cameras to detect defects in all six sides of the doors.
The artificial vision equipped in this line enables the system to detect up to 40 different types of defects. These imperfections include knot holes, resin pockets, skin delaminating, split timber, glue on face, water marks, trim damage, poor trim, loose lip, open joint or face decoloration.
The key to this technology is to merge and synchronize in only one vision system what normally would be done by means of three or four different systems. The other key remains on how easily this quality control solution can be adapted to layout restrictions that each customer may have.
Another clear example of how Biele vision systems can take automation a step further is the solution installed on plywood/veneer patching lines. A unique vision system detects the imperfections on the veneer so that afterwards, the robot’s performance is optimized to handle the veneer to patch all the defects.
Furthermore, Biele Group is able to develop this quality control solution without losing the hallmark that characterizes its engineering: the customization of its production lines. Biele Group adds the feature of advanced customization in all the projects, no matter what product is manufactured and no matter what wood-based raw material is used.
Cmc Texpan
CMC Texpan, a subsidiary of the Siempelkamp Group and located in Northern Italy, is a worldwide leader in the production of wood-based panel machinery and plants. One of the main purposes of CMC Texpan has always been to respond promptly to an ever-changing market and to the customers’ needs through customized imachinery, services and plants.
CMC Texpan has invested and continues to invest in training staff and in new technologies in order to ensure and maintain a high level of quality of its products. For example, LYNX sorter, which is a compact and versatile technology for the detection and removal of contaminants, based on advanced proprietary technology developed by CMC Texpan, can be equipped with one of its latest innovative tehnologies: the Speed Classifier. It is a system that allows the classification of different wood composites, such as PB, MDF, wood chips and OSB. It is also able to predict the area and geometric barycentre of the examined samples while they are carried on the conveyor belt.
Another system, based on THz technology, has been developed in the last year. It measures the density profile of the wood panels and mats in real time and with non-contact technology. It can be applied for various types of wood and mat heights. In addition, it is possible to install another new device that has the capacity to identify humidity gradient. With all these systems is possible to collect information regarding the repeatability and quality of the panels.