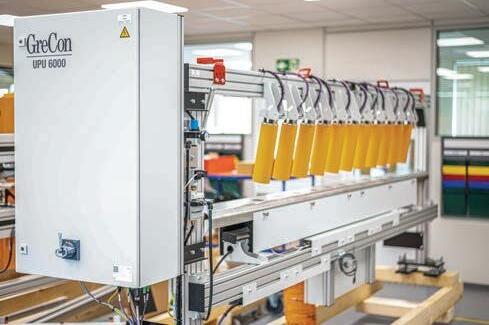
10 minute read
QC
Custom Engineering
Custom Engineering has been an ISO-9001 certified industrial metal supplier since 1997, positioning us as a worldwide leader in manufacturing high-quality products. Our comprehensive and thorough quality assurance program employs controlled documentation to communicate quality and manufacturing specifications through procedures and detailed work instructions, ensuring high-quality fabrications manufactured to exact customer requirements. Custom upholds high quality standards and procedures through monitoring and documenting nonconformities of products, evaluating the quality system itself, initiating corrective actions when necessary, and implementing preventive actions to mitigate potential quality issues. Our quality control program is backed by an ISO-9001: 2015 certification and an ASME Section VIII Division I Quality Control Program.
Maintaining platen flatness and parallelism is critical to operational efficiencies. When platens become nicked, bent, gouged or damaged, they will produce imperfections in the end product. Custom offers a complete refurbishing program to:
Re-machine platens that have been damaged in pressing accidents
Restore flat and parallel specifications to platens slightly misshaped from normal wear and tear
—Modify platens for heating with fluid instead of steam
—Upgrade hanger and guide systems to accommodate additional press openings
It is the ongoing commitment of Custom Engineering to provide the highest quality products and services achieved through careful selection of raw materials and components, well-planned production procedures, and thorough quality control testing. We have developed a thorough, comprehensive quality control system consisting of procedures and policies to ensure high-quality, certified fabrications. Our quality procedures and processes are reviewed and evaluated annually to identify any areas of improvement in order to make any adjustments necessary to ensure that the highest quality standards are upheld.
Custom Engineering employs various non-destructive examination techniques during manufacturing to evaluate materials, welds, and machined surfaces for discontinuities and defects, while maintaining the integrity of the part:
—Visual Examination
—Magnetic Particle Testing
—Liquid Penetrant Testing
—Ultrasonic Testing
—Radiographic Testing
Custom determines with diligence that its materials are free of conflict minerals in compliance as required by virtue of its customer base.
ASME Section VIII Division I maintains public safety as the number one requirement for pressure vessel design and fabrication. ASME Section VIII Division I also sets the code requirements for materials, design, fabrication, non-destructive examination, and hydro testing.
Fagus Grecon
Poor customer satisfaction, panel rejects, excessive raw material used and waste are results from delaminations and blows incurred during panel board production. The use of GreCon Delamination Control (UPU) provides production line quality assurance and significantly reduces defective panels.
The two most common defects occurring in all types of panels, including particleboard, MDF, OSB, LVL, LSL, and plywood, are delaminations and blows. Delaminations occur when glued laminate or board material doesn’t bond properly. Blows are small air pockets or voids, resulting primarily from vapor development caused by excessive moisture or excessive material. Delaminations and blows also occur when the amount of material is insufficient and the reduced thermal conductivity in the press cannot adequately heat areas. Variations in wood, inadequate drying or pressing time, or even a simple equipment malfunction can all result in defective panels as well.
GreCon’s non-contact delamination control uses ultrasonic transmissions to scan the panel. When a blow or delamination appears, the ultrasonic waves are weakened considerably, and an alarm is activated based on predetermined tolerance levels. The analysis of each panel is recorded in the SPC (Statistical Process Control) and can be recalled at any time.
GreCon Delamination Control (UPU 6000) is available for various applications and board thickness up to 6 in. Our Delamination Control can also be paired with a Thickness Gauge (DMR) and Panel Weight Scales to measure bond, thickness, weight, and also raw panel density. GreCon quality assurance systems optimize energy and resources while maximizing your production and profits.
IMAL-PAL GROUP
Imal-Pal Group offers major innovations in quality control, including a complete range of online and laboratory quality control equipment: l FBC200 (Full Blister Control) detector: Utilizing a limited number of control channels to detect panel delamination, the newly designed FBC is able to control the whole width of the board. A lite version of this system is also available, the LBC100 (Lite Blister Classifier), which does not have as many sensors as the FBC system, but its coverage is three times greater than any standard channel system. The center-center distance between two consecutive channels is only 1 in. l Thickness gauging system: highly accurate and reliable system for installation at press outfeed and sanding line with excellent all-round performance. Three-year warranty on the Imal measuring sensors. Also supplied in combination with the LBC100 on the same supporting beam. The center-center distance between two consecutive channels is only 3 in. l CDP800: Essential for controlling MDF quality, is a rapid and extremely accurate online density profile analyzer, able to analyze thicknesses from 2 mm to 60 mm, a range which no other system can equal. Unlike other analyzers, the CDP800 installs both sensors below the board, a technical solution which protects the sensors from the vapors released by the board, hence they last longer and performance is not affected. l PSD400 (Press Security Device): Designed to protect continuous presses from foreign objects (stones, wire, chunks of resin, plastic etc.) and other dense objects that could damage the belt; particularly important when producing thin panels. The X-ray system provides full mat width coverage and mat density is accurately displayed in 3D. l ISO30X (On-Line X-ray mat density gauge): Performs an accurate on-line weight per surface unit analysis and is an essential device for managing and controlling mat formation. l MMW (Millimetre Wave Scanner): Controls mat weight distribution online as well as moisture content, thickness and board weight after the press (the details are supplied for each layer in the case of PB and OSB production and not just for the board itself). Extremely accurate, rapid and safe scanning process without the application of X-rays or radioactive sources. l Online moisture meters: UM300—a true thermal weighing scale which applies the loss-in-weight principle; UM700—which utilizes infrared rays to measure moisture content; UM900—microwave-operated analyzer for determining the amount of moisture present in chips, wood fiber or pellets.
The group also manufactures a full range of laboratory equipment such as the IB800 board property tester, DPX density profile meter, Lab Formaldehyde Tester, Fibercam and Screencam for analyzing the granulometry of wood particles and fiber.
Limab
An increasing number of companies have chosen the LIMAB PanelProfiler for accurate in-line quality control of panel thickness. We have many installations in both single, multi-opening and continuous press lines as well as sanding and finishing lines. The PanelProfiler measures all types of wood panels from thin MDF/HDF, particleboard, plywood, OSB, hardboard up to big size glulam panels.
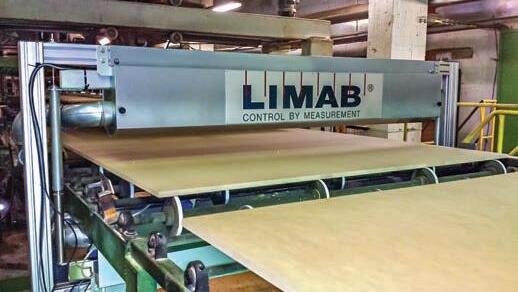
The system works non-contact with laser-based measurement technology. This gives many advantages. The careful design and material selection of our sensor frames gives both temperature and mechanical stability, and this means that there’s no need for constant calibrations between panels, like with mechanical contact roller systems.
The PanelProfiler maintains its high accuracy over long periods and changing ambient temperature, especially important in high speed and continuous/endless production lines. The high measurement frequency, 4000 measurements/sec, enables thickness control already from the very front edge of panels. No panel contact eliminates dirt and scratch marks on sanded panels. With no moving system parts, maintenance costs are low as well as total cost of ownership.
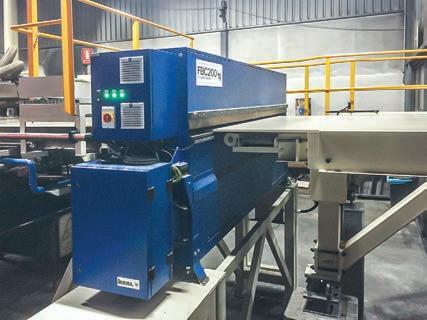
We have PanelProfiler versions to fit various process lines. A system can have a selectable number of fixed measurement tracks; the outer measurement tracks can automatically adapt to different product widths. For endless/continuous press lines, we can offer a traversing system, giving complete thickness cross profiles. We also supply multi versions systems with up to four measurement stations in one package, useful in before and after sander installations.
All systems are supplied with mechanical dimensions to fit each production line and have powerful air cleaning and sensor protection boxes to work with a minimal maintenance, even in harsh production environments.
The system software has an easy to understand real time graphical and numerical display of each produced panel. All out-of-tolerance conditions will immediately alert the operators. Database logging of panels, with thickness variations for each track, recipe handling, remote systems diagnosis and more is included as standard in the PanelProfiler.
Raute
Maximum recovery is a must for manufacturers in all veneer-based industries. So is operating at consistently high efficiency. But these can often feel like competing priorities.
With Raute’s R7-Series analyzers and MillSIGHTS software, you can automate and optimize the processes that most impact your operation’s bottom line.
Your peeling line is your first, best opportunity to get the most value out of your forest assets. By minimizing the width of your wet clipped sheets, you can produce more full-size veneer sheet per log and realize cost savings throughout the entire production process.
Raute’s Veneer Visual, Moisture and Strength Analyzer R7 – Peeling is an industry first: a compact, integrated unit that can accurately estimate how much each sheet will shrink during the drying process.
High-resolution color cameras ensure that each sheet is clipped according to a precise drying shrinkage estimation. A combination of microwave and x-ray density measuring technology determines the sheet’s moisture content, allowing you to sort your wet veneer into up to four different moisture classes. This additional moisture grading can increase your drying line’s capacity by up to 20%.
Optimizing the drying process is more than a matter of controlling energy and labor costs. It also requires making grading decisions that consistently improve your end products’ quality and profitability.
—Raute’s integrated Veneer Visual, Moisture and Strength Analyzer R7 – Drying unlocks multiple benefits.
l High-resolution defect detection supports automatic veneer grading, eliminating the need for manual sorting.
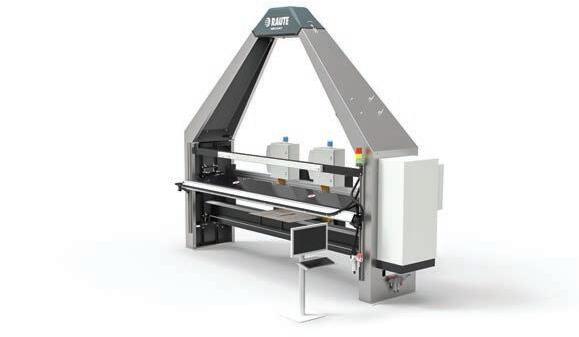
l Accurate moisture measuring, using multiple data points, reduces the risk of over-drying, delamination, and warping.
l Automatic dryer speed controls increase dryer efficiency and improve dry veneer quality.
l Industry-standard veneer strength grading processes identify the highest value of every sheet, especially those destined for use in structural products.
l Data captured on the drying line can drive continuous improvements and increase agility. For example, this data can feed simulations, turning a month-long recipe change test into a pilot project that can be completed within hours.
Visit the Raute website to learn more about the power, versatility and intelligence of the R7-Series analyzers.
Siempelkamp
Internal bond and bending strength, thickness swelling, and surface soundness—these are essential quality parameters of a wood-based panel. More than ever, plant operators aim to ensure these quality characteristics in an autonomous control loop. In this context, Siempelkamp supports plant operators with a coherent concept from online trend display to quality-assuring optimization.
“From data to resource” is the principle of the higher-level MES system Prod-IQ made by Siempelkamp. The digital system draws valuable resources from plant data that allow the evaluation of the efficiency of a wood-based panel plant and the quality of the boards with pinpoint accuracy.
The module Prod-IQ.quality, which calculates the quality of the central board characteristics online, particularly contributes to the topic of “quality control.” This module, which is already running in more than 50 plants, uses machine learning methods for online quality control by determining the quality of the board on the basis of current process settings and displaying it in a trend diagram. This also includes the minimum quality reserve required to reliably maintain the specified quality limit.
“This ensures a narrow fluctuation range, so production can run much closer to maximum capacity. The result is more productivity with assured quality; the production processes are modeled as efficiently as possible,” explains Gregor Bernardy, Head of MES & Industrial IT at Siempelkamp Logistics & Service GmbH. Designed according to the principle of self-adaptive machine learning, ProdIQ.quality uses each laboratory control to automatically adjust the process model.
Prod-IQ.quality thus lays a central foundation for being able to predict the quality of the wood-based panel precisely and at an early stage. However, there is still an important process step to be taken from trend indication to the actual doing, namely setting up the process in the best possible way, which thus far has primarily been the responsibility of the operating personnel. “What should I do? How can I improve the process?” are the questions operators ask. “Can the system tell me what to do?” The answer is “Absolutely!”
Siempelkamp is now solving this question in cooperation with the Israeli high-tech company, SMARTECH. Both partners have been offering the closed-loop solution Prod-IQ · SmartPress for wood-based panel presses since October 2022—a groundbreaking autonomous process control.
Prod-IQ · SmartPress uses AI and machine learning algorithms, as well as real-time data, to immediately increase press performance and reduce production costs while ensuring board quality at the same time. The Prod-IQ · SmartPress architecture combines real-time production parameters with contextual operator input. This enables the performance level of the plant to be increased at all levels.
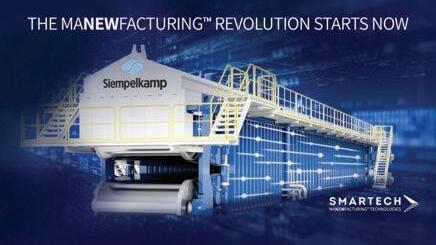
Whereas the decision-making process used to lie with the operator, Prod-IQ · SmartPress shifts autonomous decision-making to the plant itself. Less manual intervention is required, and performance can also be harmonized between shifts. It is easier for new operators to run the plant optimally: Prod-IQ · SmartPress takes the burden off the operator and indicates the best settings to increase press speed while saving material and ensuring quality at the same time.
The “self-optimizing plant” has become a reality with this solution, which has been tested several times—and the Prod-IQ software family is given the finishing touch.
Taihei Machinery
Taihei Machinery has some of the best quality control in the industry due to our test building and commissioning system. When one of our machines is ordered, we first install it on our own factory floor. This allows us to ensure that the machine meets the specific qualifications and standards of the customer, ensure there will be no logistical issues with the customer-customized design, and, lastly, test out any new innovations requested by the customer prior to shipping. We also commission the machine prior to shipping, ensuring not only that the machine meets the physical qualifications, but the production qualifications as well.
Through the test building and commissioning system, we are firstly able to install at the customer’s location in a much shorter timeframe than other competitors. Ultimately, our quality control system aims and succeeds at ensuring that the best quality machine is installed at the customer’s site, every time.
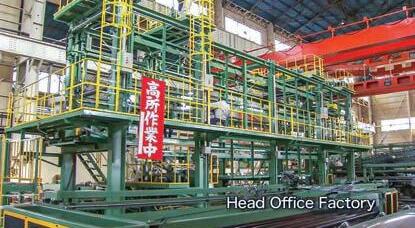
Usnr
USNR has taken its deep learning AI technology developed over years and proven in its sawmill grade optimizers and applied it to its NV4g green-end and GSc2000 dry-end veneer grading platforms. The result is a paradigm shift in solution accuracy achieving a new level of defect detection that makes grading solutions more accurate and more profitable.
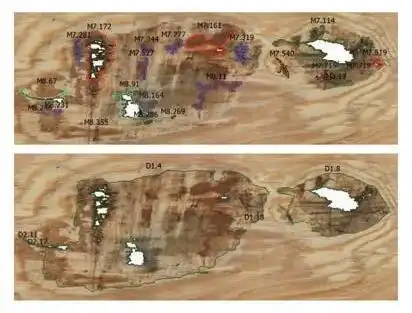
USNR’s traditional neural net defect classifier can be time consuming to configure and can struggle to accurately identify certain defects. In the image you can see that the traditional classifier sees the single large defect as several smaller defects, identifying and classifying them individually. The deep learning classifier correctly identifies this defect as a single large defect.
With current market conditions, getting every bit of value out of your raw materials counts. USNR has several deep learning systems installed and operating with impressive results. Mills are reporting improved grading accuracy and more higher-grade finished products.
Deep learning is the ultimate defect classifier! Faster to start up, more accurate, and easier to use than a traditional neural net classifier, deep learning is available as part of a new system or an upgrade to an existing system. Contact us today to learn how your operation would benefit from deep learning.