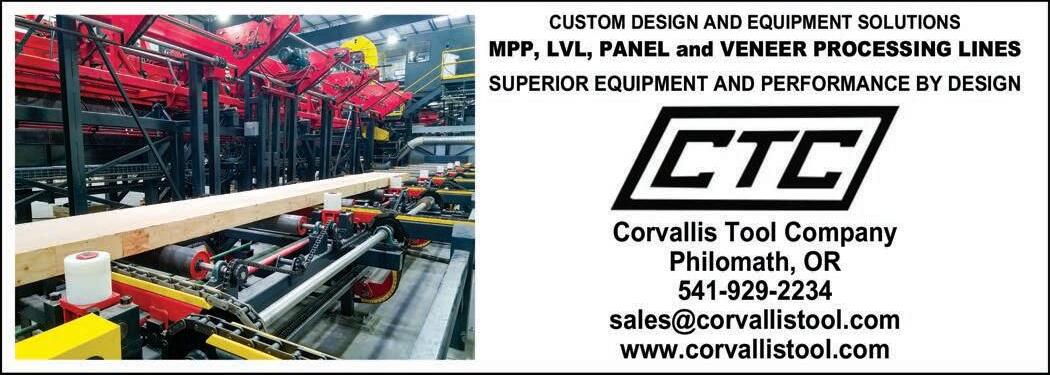
5 minute read
PROJECTS
says Fred Chinn, Vice President StrandBased Business at Tolko. “Once we rebuild, High Prairie will be better than ever, and our new CEBRO smart plant will be a big part of that.”
Chinn believes the plant will produce its first new board by year’s end. Once operational, the plant’s annual production capacity will reach up to 734,000 m³.
Royomartin Plans More Work At Chopin
Tolko Industries Ltd. has commissioned Dieffenbacher to supply the core components of a new OSB line at High Prairie, Alberta, Can. On May 20, 2022, a fire in the press building damaged beyond repair a Dieffenbacher 12-opening press, which Tolko had commissioned in 1995, and much of the surrounding equipment. A Dieffenbacher CPS+ continuous press will replace the previous press.
Dieffenbacher’s scope of supply for the rebuild also includes the forming station and forming line, and the raw board handling system. In line with Dieffenbacher’s CEBRO smart plant concept, the Press Emission Control System and the Intelligent Air Management System will improve the plant’s sustainability by creating cleaner air inside and outside the production hall. Dieffenbacher’s new digitalization solution, EVORIS, and the digital service platform, MyDIEFFENBACHER, will help make Tolko’s new plant a truly “smart one.”
“It’s great that Dieffenbacher stepped up so quickly to help us after the fire,”
Martco, LLC announced it will invest $9.5 million to install production equipment at its lumber and plywood facility in Chopin, La. The expansion will allow the company to retain approximately 684 existing jobs through 2035.
The Chopin plant began production in 1996 and has undergone multiple expansions that established it as one of the largest single-site plywood production facilities in North America.
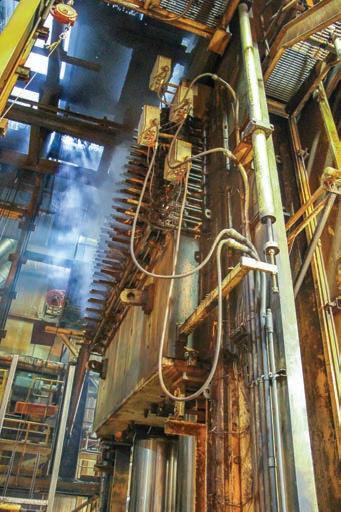
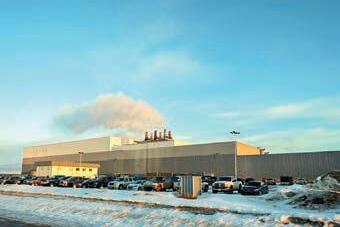
The brunt of this work will be around the plywood finishing end, including the installation of new scanning technologies as well as robotic repair and patch.
“RoyOMartin-Plywood manufacturing facility continues to modernize its operations to be competitive in the future,” RoyOMartin Chairman, CEO and CFO Roy O. Martin III says. “The plywood mill has been in continuous operation since 1996 and has survived the Great Recession, COVID pandemic and other harsh obstacles without downtime. The team leaders and team members at this facility deserve the job sustainability and security that this project and previous modernization projects provide.”
Southern Veneer Upgrades Pendulum
Southern Veneer Specialty Products is receiving a new USNR (Coe) 760 pendulum to breathe new life into its lathe system at Moncure, NC.
The USNR pendulum features a heavy-duty tube steel design to precisely transfer blocks to the lathe spindles. It prevents slow-downs during the process and works seamlessly with the charger and lathe to keep things moving.
Once the pendulum is installed, Southern Veneer Specialty Products will have a fully-optimized lathe system designed to provide the highest quality veneer.
Wisewoods Orders Refining System
Andritz has received an order from Wisewoods Co., Ltd. to supply another pressurized refining system—the second from Andritz—to its mill in Phetchaburi, Thailand. Startup is scheduled for the first half year of 2024.
The new fiber preparation system will feature a capacity of 30 tons per hour and process rubberwood for production of high-quality MDF.
Visarut Palarit, Deputy Director, Wisewoods, comments: “Our first line from Andritz has been showing excellent performance since its installation in 2016. The new line will enable us to enlarge our production capacity significantly. In parallel, Andritz technology ensures that we receive top fiber quality—a precondition for our MDF board to deliver lighter color and smoother surface properties.”
Wisewoods Co., Ltd. is a renowned player in the wood panel industry for four decades and manufactures MDF products for the Middle East and Asian region.
STEVES & SONS ORDERS DOOR SKIN LINES
U.S. door manufacturer Steves & Sons, Inc. has placed an order for two Siempelkamp forming and press lines for the production of door skins. The San Antonio, Texas-based customer also placed an order with Siempelkamp subsidiary Büttner for two fiber dryers and an energy plant. Steves & Sons is entering the door skins manufacturing business with this project.
The two press lines each consist of a fiber classifier, mat forming, forming line and the multi-daylight press yielding millions of door skins per year. For the press line design, the focus was specifically on the wide product variety, combined with the minimization of trim waste. For the process heat supply of the mill, Büttner contributes an energy system based on biomass combustion, including flue gas precleaning as well as two fiber drying systems. The energy system not only supplies thermal energy to the drying systems, it also heats ther- mal oil for press heating and generates steam for wood defibration.
Commissioning and startup is scheduled for 2024.
Siempelkamp has proven its experience in door skin production with a high-performance plant operated by a Turkish customer.
“Our experience in the North American market, our competence in being able to adapt technical designs very specifically to local requirements convinced Steves & Sons. This ensures an optimal process technology and operating cost design, for example in the form of low maintenance and energy costs, a minimized use of raw materials, and a high degree of automation,” say Dirk Koltze, President Siempelkamp LP/Büttner in Charlotte, NC.
CON-VEY PROMOTES GOEBEL TO VP
Con-Vey LLC, manufacturer of automated material handling equipment for engineered wood products, announced the promotion of Jeremy Goebel to Vice President.
Goebel joined Con-Vey as a sales representative in 2013 and quickly rose through the ranks, becoming the sales manager in 2017. With exceptional technical skills and personable nature, Goebel has been instrumental in driving Con-Vey’s success and growth.
“We are thrilled to have Jeremy take on this new role of Vice President at Con-Vey,” says Dave Larecy, CEO and President, “His vision, commitment and strengths make him the right guy for the job, and we are confident he will help us achieve our strategic initiatives and continue to grow Con-Vey into the future.”
As Vice President, Goebel will continue to lead the sales team, while also managing other department operations. This promotion is part of Con-Vey’s growth plan and the next step in expanding its management team.
B Ttner Expands Product Range
As a globally operating supplier of burners as well as drying and energy plants, Büttner—a member of the Siempelkamp Group—is taking the next logical step by establishing a new environmental technology competence center in Kaiserslautern, Germany, and expanding its product range in the field of environmental technology.
Büttner will now be designing and manufacturing dry electrostatic filters to separate ash from hot flue gases in energy plants and wet electrostatic precipitators (WESP) to reduce particles and volatile emissions from the waste air emitted by drying and press systems.
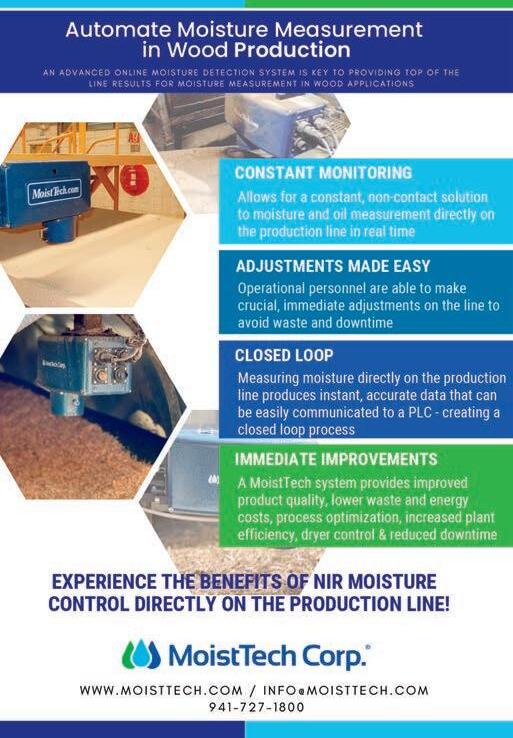
This gives new customers the opportunity to focus on energy efficiency and the reduction of emissions during the planning and design stages of their plants. But the new competence team will also be able to help current customers in regard to the modernization, conversion and extension of their existing plants.
“The environmental technology sector will continue to grow in importance. We’re proud that we’ve been able to expand our range of services in the field of integrated environmental technology on a contemporary and competent basis, which will also enable us to continue to deliver adapted solutions for all requirements in the future,” says Andreas Klug, Managing Director at Büttner Energie- und Trocknungstechnik GmbH in Krefeld.
Dieffenbacher Buys Energy Firm
Germany-based Dieffenbacher has acquired the key assets of BERTSCHenergy, based in Bludenz, Western Austria, through the newly formed Dieffenbacher Energy GmbH subsidiary. Dieffenbacher states that the acquisition accelerates its